元器件工艺要求文件
电器元件安装工艺要求
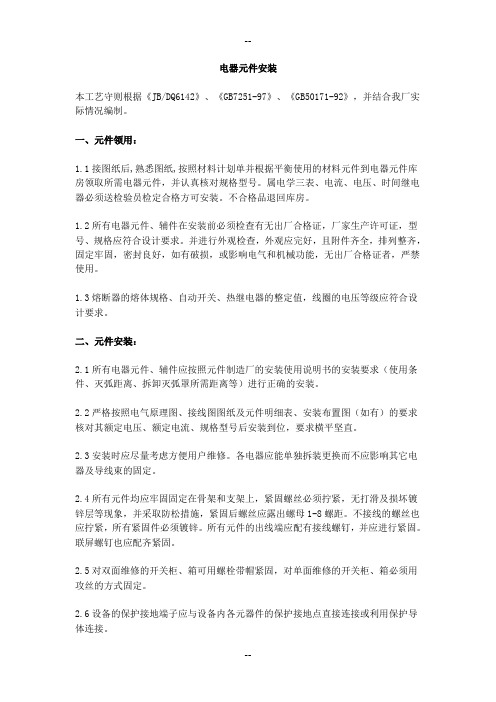
电器元件安装本工艺守则根据《JB/DQ6142》、《GB7251-97》、《GB50171-92》,并结合我厂实际情况编制。
一、元件领用:1.1接图纸后,熟悉图纸,按照材料计划单并根据平衡使用的材料元件到电器元件库房领取所需电器元件,并认真核对规格型号。
属电学三表、电流、电压、时间继电器必须送检验员检定合格方可安装。
不合格品退回库房。
1.2所有电器元件、辅件在安装前必须检查有无出厂合格证,厂家生产许可证,型号、规格应符合设计要求。
并进行外观检查,外观应完好,且附件齐全,排列整齐,固定牢固,密封良好,如有破损,或影响电气和机械功能,无出厂合格证者,严禁使用。
1.3熔断器的熔体规格、自动开关、热继电器的整定值,线圈的电压等级应符合设计要求。
二、元件安装:2.1所有电器元件、辅件应按照元件制造厂的安装使用说明书的安装要求(使用条件、灭弧距离、拆卸灭弧罩所需距离等)进行正确的安装。
2.2严格按照电气原理图、接线图图纸及元件明细表、安装布置图(如有)的要求核对其额定电压、额定电流、规格型号后安装到位,要求横平坚直。
2.3安装时应尽量考虑方便用户维修。
各电器应能单独拆装更换而不应影响其它电器及导线束的固定。
2.4所有元件均应牢固固定在骨架和支架上,紧固螺丝必须拧紧,无打滑及损坏镀锌层等现象,并采取防松措施,紧固后螺丝应露出螺母1-8螺距。
不接线的螺丝也应拧紧,所有紧固件必须镀锌。
所有元件的出线端应配有接线螺钉,并应进行紧固。
联屏螺钉也应配齐紧固。
2.5对双面维修的开关柜、箱可用螺栓带帽紧固,对单面维修的开关柜、箱必须用攻丝的方式固定。
2.6设备的保护接地端子应与设备内各元器件的保护接地点直接连接或利用保护导体连接。
2.7对于盖、门、覆板等部件,如上面没有安装电器元件,一般应用金属螺钉或金属绞链连接,以保证电连续性;如果上面装有工作电压值超过安全电压范围的电器设备时,应采用保护导体(一般为黄绿双色线),将这些器件与保护电路连接。
电子元器件安装焊接工艺设计规范
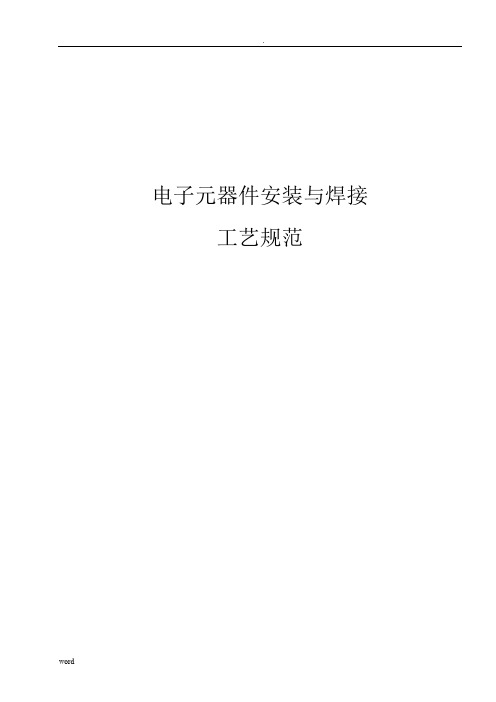
电子元器件安装与焊接工艺规范电子元器件安装与焊接工艺规范1范围本规范规定了设备电气盒制作过程中手工焊接技术要求、工艺方法和质量检验要求。
2引用标准下列文件中的有关条款通过引用而成为本规范的条款。
凡注日期或版次的引用文件,其后的任何修改单(不包括勘误的内容)或修订版本都不适用于本规范,但提倡使用本规范的各方探讨试用其最新版本的可能性。
凡未注日期或版次引用文件,其最新版本适用于本规范。
HB 7262.1-1995 航空产品电装工艺电子元器的安装HB 7262.2-1995 航空产品电装工艺电子元器的焊接QJ 3117-1999 航天电子电气产品手工焊接工艺技术要求IPC-A-610E-2010 电子组件的可接收性3技术要求与质量保证3.1一般要求3.1.1参加产品安装和检验的人员必须是经过培训合格的人员。
3.1.2环境温度要求:20℃-30℃。
3.1.3相对湿度要求:30%-75%。
3.1.4照明光照度要求:工作台面不低于500lx。
3.1.5工作场地应无灰尘,及时清除杂物(如污、油脂、导线头、绝缘体碎屑等)工作区域不得洒水。
3.2安装前准备3.2.1把安装所用的器材备齐,并放在适当位置,以便使用;3.2.2所有工具可正常使用,无油脂,按下列要求检查工具:切割工具刃口锋利,能切出整齐的切口;绝缘层和屏蔽剥离工具功能良好。
3.2.3按配套明细表检查和清点元器件、印制板、紧固件、零件等的型号规格及数量。
3.2.4凡油封的零件或部件,在安装前均应进行清洗除油,并防止已除过的零件再次糟受污染。
4元器件在印制板上安装4.1元器件准备4.1.1安装前操作人员应按产品工艺文件检查待装的各种元器件、零件及印制板的外观质量。
4.1.2元器件引线按下列要求进行了清洁处理:a、用织物清线器轻轻地擦拭引线,除去引线上的氧化层。
有镀层的引线不用织物清线器处理;b、清洁后的引线不能用裸手触摸;c、用照明(CDD)放大镜检验元器件引线清洁质量。
电子元器件插件工艺检验标准

元件插件工艺及检测标准一、目的:使LED电源PCB板组装(PCBA)工作人员掌握基本的电子元件操作工艺;规范电子元件在PCBA上的插件/焊锡等操作要求, 并为PCBA检验提供检查标准二、范围:适用于本公司PCBA(LED电源PCB的插件/焊锡)的工艺操作和检查。
三、参考文件:工艺要求参照:IPC-A-610B (Class Ⅱ)四、定义:PCBA: Printed CircuitBoard Assembly (印刷线路板组装)AX: (轴向)RD: Radial (径向)HT: Horizontal (卧式)VT: Vertical (立式)SMT: Surface Mount Technology (表面安装技术)SMD: Surface Mount Device(表面安装元件)SMC:Surface Mounting Components(表面安装零件)SIP: Simplein-line package 单列直插式封装SOJ:Small Outline J-leadpackage (具有J型引线的小外形封装) SOP: Small Outline package (小外形封装)SOT: Small Outline Transistor (小外形晶体管)IC:IntegratedCircuit (集成电路)PR: Preferred (最佳)AC: Acceptable (可接受的)RE:Reject (拒收)五、元件类别:电阻,电容, 电感, 二极管, 三极管, IC, ICSocket,晶体,整流器, 蜂鸣器, 插头,插针, PCB,磁珠等, 在此文件中, 根据本公司情况暂时定义电阻, 电容,电感, 二极管, 三极管,MOS管工艺标准六、元件插件工艺及检测标准1. 卧式(HT) 插元件卧式插元件主要是小功率,低容量, 低电压的电阻,电容,电感, Jumpe r(跳线),二极管, IC等,PCBA上的组装工艺要求和接收标准如下: 1.1元件在基板上的高度和斜度1.1.1轴向(AX)元件1.1.1.1功率小于1W的电阻, 电容(低电压,小容量的陶瓷材料),电感, 二极管,IC等元件PR:元件体平行于PCB板面且紧贴PCB板面, 如图示:AC:元件体与PCB表面之间最大倾斜距离(D)不大于3mm, 元件体与PCB表面最低距离(d)不大于0.7mm,如图示:RE: 元件体与PCB板面距离D>3mm, 或d>0.7mm1.1.1.2耗散功率大于或等于1W的元件PR: 元件体平行于PCB板面且与PCB板面之间的距离D≥1.5mm,如图示:AC:元件体与PCB板面之间的距离D≥1.5mm, 元件体与PCB板面的平行不作要求RE: 元件体与PCB板面之间的距离D≤1.5mm1.1.1.3ICPR: 元件体平行于PCB, IC引脚全部插入焊盘中, 引脚突出PCB面1.mm,倾斜度=0, 如图示:AC:IC引脚全部插入焊盘中, 引脚突出PCB面大于0.5mm, 如图:RE: IC引脚突出PCB面小于0.5mm, 或看不见元件引脚, 如图:1.1.2径向(RD)元件(电容, 晶振)PR: 元件体平贴于PCB板面,如图示:AC:元件脚最少有一边贴紧PCB板面,如图示:RE:元件体未接触PCB板面,如图示:1.2元件的方向性与基板对应符号的关系:1.2.1 轴向(AX)无极性元件(电阻,电感, 小陶瓷电容等)PR: 元件插在基板中心标记且元件标记清晰可见,元件标记方向一致(从左到右,从上到下), 如图:AC: 元件标记要求清晰,但方向可不一致, 如图:RE: 元件标记不清楚或插错孔位, 如图:1.2.2轴向(AX)有极性元件, 如二几管, 电解电容等PR: 元件的引脚插在对应的极性脚位, 元件标记清晰可看见,如图:AC:元件的引脚必须插在相应的极性脚位上,元件标记可看见, 如图:RE: 元件的引脚未按照极性方向插在相应的脚位上, 如图:1.3元件引脚成形与曲脚1.3.1引脚成形PR: 元件体或引脚保护层到弯曲处之间的距离L>0.8mm, 或元件脚直径弯曲处无损伤,如图:A元件脚直径或厚度( D半径( R )/T )≤0.8mm 1 X D0.8~1.2mm 1.5X D≥1.2mm 2 X DRE: ( 1) 元件体与引脚保护弯曲处之间L<0.8mm,且弯曲处有损伤, 如图:( 2) 或元件脚弯曲内径R小于元件直径, 如图:1.3.2屈脚PR: 元件屈脚平行于相连接的导体,如图:AC:屈脚与相间的裸露导体之间距离(H)大于两条非共通导体间的最小电气间距, 如图:RE: 屈脚与相间的裸露导体之间距离(H)大于两条非共通导体间的最小电气间距,如图:1.4元件损伤程度1.4.1元件引脚的损伤PR: 元件引脚无任何损伤, 弯脚处光滑完好, 元件表面标记清晰可见, 如图:AC: 元件引脚不规则弯曲或引脚露铜,但元件或部品引脚损伤程度小于该引脚直径的10%,如图:RE:( 1 )元件引脚受损大于元件引脚直径的10%,如图:(2)严重凹痕锯齿痕,导致元件脚缩小超过元件的10%,如图:1.4.2 IC元件的损伤PR: IC 元件无任何损伤, 如图:AC: 元件表面受损, 但未露密封的玻璃,如图:RE:元件表面受损并露出密封的玻璃, 如图:1.4.3轴向(AX)元件损伤PR: 元件表面无任何损伤,如图:AC:元件表面无明显损伤,元件金属成份无暴露,如图:RE:(1 )元件面有明显损伤且绝缘封装破裂露出金属成份或元件严重变形,如图:(2 )对于玻璃封装元件,不允许出现小块玻璃脱落或损伤.1.5元件体斜度PR:元件体与其在基板上两插孔位组成的连线或元件体在基板上的边框线完全平行,无斜度,如图:AC:元件体与其在基板上两插孔位组成的连线或元件体在基板上的边框线斜度≤1.0mm,如图:RE: 元件体与其在基板上两插孔位组成的连线或元件体在基上的边框线斜度>1.0mm,如图:2.立式(VT)插元件2.1.1轴向(AX)元件PR: 元件体与PCB板面之间的高度H在0.4mm-1.5mm之间, 且元件体垂直于PCB板面, 如图:AC: H在0.4-3mm之间, 倾斜Q<15°,如图:RE: 元件体与PCB板面倾斜, 且间距H<0.4mm或H>3mm或Q>15°.2.1.2径向(RD)元件2.1.2.1引脚无封装元件PR: 元件体引脚面平行于PCB板面, 元件引脚垂直于PCB板面,且元件体与PCB板面间距离为0.25-2.0mm, 如图:AC: 元件体与PCB板面斜倾度Q小于15°, 元件体与PCB板面之间的间隙H在0.20-2.0mm之间,三极管离板面高度最高大于4.0mm,如图:RE: 元件与PCB板面斜倾角Q>15°或元件体与PCB板面的间隙H>2.0mm或三极管>4.0mm.2.1.2.2:引脚有封装元件PR: 元件垂直PCB板面,能明显看到封装与元件面焊点间有距离,如图:AC:元件质量小于10g且引脚封装刚好触及焊孔且在焊孔中不受力,而焊点面的引脚焊锡良好(单面板), 且该元件在电路中的受电压<240VAC或DC,如图:RE: 引脚封装完全插入焊孔中,且焊点面焊锡不好,可看见引脚封装料, 如图:2.2元件的方向性与基板符号的对应关系2.2.1轴向(AX)元件PR: 元件引脚插入基板时,引脚极性与基板符号极性完全吻合一致,且正极一般在元件插入基板时的上部,负极在下部,如图:AC:元件引脚插入基板时,引脚极性与基板符号极性吻合一致,但元件在插入基板时,正极在上和负极在下不作要求,如图:RE: 元件引脚插入基板时,引脚极性与基板符号极性刚好相反,如图:2.2.2径向(RD)元件AC: 元件引脚极性与基板符号极性一致,如图:RE: 元件体引脚极性与基板符号极性相反,如图:2.3元件引脚的紧张度PR:元件引脚与元件体主轴之间夹角为0°(即引脚与元件主轴平行, 垂直于PCB板面), 如图:AC: 元件引脚与元件体主轴袒闪角Q<15°,如图:RE: 元件引脚与元件体主轴之间夹角Q>15°.2.4元件引脚的电气保护在PCBA板上有些元件要有特殊的电气保护,则通常使用胶套,管或热缩管来保护电路PR:元件引脚弯曲部分有保护套,垂直或水平部分如跨过导体需有保护套且保护套距离插孔之间距离A为1.0mm-2.0mm,如图:AC: 保护套可起到防止短路作用, 引脚上无保护套时, 引脚所跨过的导体之间的距离B≥0.5mm, 如图:RE: 保护套损坏或A>2.0mm时, 不能起到防止短路作用或引脚上无保护套时,或引脚所跨过的导体之间距离B<0.5mm,如图:2.5元件间的距离PR: 在PCBA板上,两个或以上踝露金属元件间的距离要D≥2.0mm,如图:AC: 在PCBA板上, 两个或以上踝露金属元件的距离最小D≥1.6mm, 如图:RE: 在PCBA板上, 两个或以上踝露金属元件间的距离D<1.6mm,如图:2.6元件的损伤PR:元件表面无任何损伤,且标记清晰可见,如图:AC: 元件表面有轻微的抓、擦、刮伤等,但未露出元件基本面或有效面,如图:RE: 元件面受损并露出元件基本面或有效面积,如图:3. 插式元件焊锡点工艺及检查标准3.1单面板焊锡点单面板焊锡点对于插式元件有两种情形:a.元件插入基板后需曲脚的焊锡点b.元件插入基板后无需曲脚(直脚)的焊锡点3.1.1标准焊锡点之外观特点A.焊锡与铜片, 焊接面, 元件引脚完全融洽在一起, 且可明显看见元件脚B. 锡点表面光滑,细腻, 发亮C. 焊锡将整个铜片焊接面完全覆盖,焊锡与基板面角度Q<90°, 标准焊锡点如图示:3.1.2可接受标准A. 多锡焊接时由于焊锡量使用太多,使零件脚及铜片焊接面均被焊锡覆盖着,使整个锡点象球型,元件脚不能看到.AC:焊锡点虽然肥大Q>90°,但焊锡与元件脚,铜片焊接面焊接良好,焊锡与元件脚,铜片焊接面完全融洽在一起,如图:RE:焊锡与元件引脚, 铜片焊接状况差,焊锡与元件脚/铜片焊接面不能完全融洽在一起,且中间有极小的间隙, 元件引脚不能看到, 且Q>90°,如图:B. 上锡不足(少锡)焊锡、元件引脚、铜片焊接面在上锡过程中,由于焊锡量太少,或焊锡温度及其它方面原因等造成的少锡.AC: 整个焊锡点,焊锡覆盖铜片焊接面≥75%, 元件脚四周完全上锡,且上锡良好,如图:RE: 整个焊锡点, 焊锡不能完全覆盖铜片焊接面<75%,元件四周亦不能完全上锡,锡与元件脚接面有极小的间隙, 如图:C. 锡尖AC: 焊锡点锡尖, 只要该锡尖的高度或长度h<1.0mm,而焊锡本身与元件脚、铜片焊接面焊接良好,如图:RE: 焊锡点锡尖高度或长度h≥1.0mm,且焊锡与元件脚、铜片焊接面焊接不好, 如图:D. 气孔AC: 焊锡与元件脚、铜片焊接面焊接良好, 锡点面仅有一个气孔且气孔要小于该元件脚的一半, 或孔深<0.2mm,且不是通孔, 只是焊锡点面上有气孔, 该气孔没有通到焊接面上, 如图:RE:焊锡点有两个或以上气孔,或气孔是通孔, 或气孔大于该元件脚半径,如图:D. 起铜皮AC: 焊锡与元件脚、铜片焊接面焊接良好,但铜皮有翻起h<0.1mm,且铜皮翻起小于整个Pad位的30%, 如图:RE:焊锡与元件脚、铜片焊接面焊接一般, 但铜皮翻起h>0.1mm,且翻起面占整个Pad位的的30%以上, 如图:E. 焊锡点高度对焊锡点元件脚在基板上的高度要求以保证焊接点有足够的机械强度AC: 元件脚在基板上高度0.5<h≤2.0mm, 焊锡与元件脚,铜片焊接面焊接良好,元件脚在焊点中可明显看见, 如图:RE: 元件脚在基板上的高度h<0.5mm或h>2.0mm,造成整个锡点为少锡, 不露元件脚, 多锡或大锡点等不良现象,如图:注:对用于固定零件之插脚如变压器或接线端子之插脚高度可接受2.5mm为限.3.1.3不可接受的缺陷焊锡点在基板焊锡点中有些不良锡点绝对不可接收, 现列举部分如下RE: ( 1)冷焊(假焊/虚焊)如图:(2 )焊桥(短路),锡桥,连焊,如图:( 3 )溅锡, 如图:( 4 )锡球, 锡渣,脚碎,如图:(5) 豆腐渣,焊锡点粗糙, 如图:( 6 ) 多层锡, 如图:( 7)开孔(针孔),如图:3.2双面板焊锡点双面板焊锡点同单面板焊锡点相比有许多的不同点:a.双面板之PAD位面积较小(即外露铜片焊接面积)b.双面板每一个焊点PAD位都是镀铜通孔鉴于此两点, 双面板焊锡点在插元件焊接过程及维修过程就会有更高要求, 其焊锡点工艺检查标准就更高, 下面将分别详细讨论双面板之焊锡点收货标准3.2.1标准焊锡点之外观特点A.焊锡与元件脚,通孔铜片焊接面完全融洽在一起, 且焊点面元件脚明显可见.B.元件面和焊点面的焊锡点表面光滑, 细腻, 发亮.C.焊锡将两面的Pad位及通孔内面100%覆盖, 且锡点与板面角度Q<90°, 如图:3.2.2可接收标准A.多锡焊接时由于焊锡量过多,使元件脚,通孔, 铜片焊接面完全覆盖,不是使焊接时的两面元件脚焊点肥大, 焊锡过高AC:焊锡点元件面引脚焊锡虽然过多,但焊锡与元件脚,通孔铜片焊接面两面均焊接良好, 且Q<90°,如图:RE:焊锡点元件面引脚肥大, 锡点面引脚锡点肥大,不能看见元件脚且焊锡与元件脚, 铜片焊接面焊接不良, 如图:B.上锡不良AC: 焊锡与元件脚,通孔铜片焊接面焊接良好, 且焊接锡在通孔铜片内的上锡量高度h>75%·T(T: 基板厚度),从焊点面看上锡程度大于覆盖元件脚四周(360°)铜片的270°, 或从元件面能清楚的看到通孔铜片中的焊锡, 如图:RE:从焊点面看, 不能清晰的看到元件引脚和通孔铜片焊接面中的焊锡或在通孔铜片焊接面完全无焊锡或元件引脚到Pad位无焊锡或h<75%·T或上锡角度Q<270°(针对SolderPad360°而言),如左图:C. 锡尖在焊接过程中由于焊锡温度过低或焊接时间过长等原因造成的锡尖AC: 焊锡点的锡尖高度或长度h<1.0mm,而焊锡本身与元件引脚及通孔铜片焊接面焊接良好,Q<90°,如图:RE:焊锡点锡尖高度或长度h≥1.0mm,且焊锡与元件引脚, 通孔铜片焊接面焊接不良, 如图:D.气孔AC:焊锡与元件脚,铜片焊接面焊接良好, 锡点面仅有一个气孔且气孔要小于该元件脚的1/2, 且不是通孔(只是焊锡点表面有气孔,未通到焊接面上), 如图:RE:焊锡点上有两个或以上气孔, 或气孔是通孔, 或气孔大于该元件脚直径的1/2,焊点面亦粗糙,如图:E.起铜皮AC: 焊锡点与元件脚, 通孔铜片焊接面焊接良好, 但铜皮翘起高度h<0.1mm,翘起面积S<30%·F (F为整个焊盘的面积)RE: 焊锡与元件脚, 通孔铜片焊接面焊接质量一般,但铜皮翘起h>0.1mm, 且翘起面积S>30%·F(F为整个焊盘的面积),如图:F.焊接点高度PR:元件脚在焊锡点中明显可见, 引脚露出高度h=0.1mm,且焊锡与元件脚,通孔铜片焊接面焊接良好,如图:AC: 元件脚露出基板的高度0.5mm<h≤2.0mm,元件脚在焊锡点中可明显看见, 且焊锡与元件脚,通孔铜片焊接面焊接良好. (但对于通孔铜片焊接面的双面PCB板, 基板厚度T>2.3mm, 则元件脚露出基板高度可接收0<h≤0.5mm),如图:RE:元件脚露出基板高度h<0.5mm或h>2.0mm (仅对于厚度T≤2.3mm的双面板), 造成整个锡点为少锡, 不露元件脚, 多锡或大锡点等不良现象,且焊接不良,如图:3.2.3 不可接收的缺陷焊锡点:在双面板(镀铜通孔铜片焊接面)焊锡点中,有些不良焊点绝对不可接收, 其不可接收程度完全同于单面板,详细请参考3.1.3。
元器件工艺技术要求
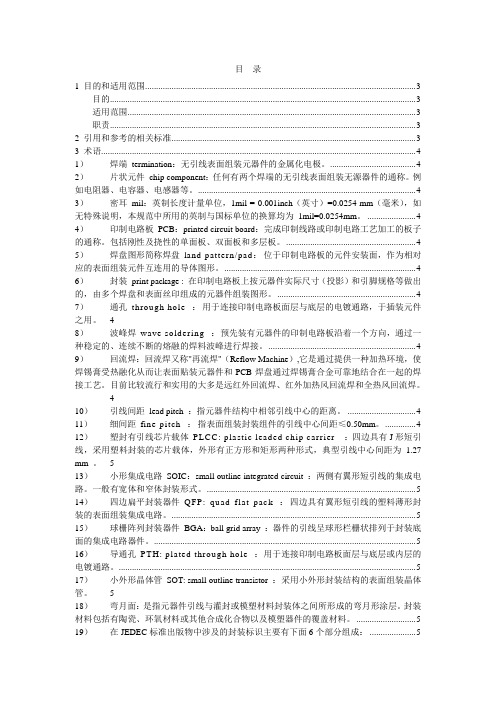
目录1 目的和适用范围 (3)目的 (3)适用范围 (3)职责 (3)2 引用和参考的相关标准 (3)3 术语 (4)1)焊端termination:无引线表面组装元器件的金属化电极。
(4)2)片状元件chip component:任何有两个焊端的无引线表面组装无源器件的通称。
例如电阻器、电容器、电感器等。
(4)3)密耳mil:英制长度计量单位,1mil = 0.001inch(英寸)=0.0254 mm(毫米),如无特殊说明,本规范中所用的英制与国标单位的换算均为1mil=0.0254mm。
(4)4)印制电路板PCB:printed circuit board:完成印制线路或印制电路工艺加工的板子的通称。
包括刚性及挠性的单面板、双面板和多层板。
(4)5)焊盘图形简称焊盘land pattern/pad:位于印制电路板的元件安装面,作为相对应的表面组装元件互连用的导体图形。
(4)6)封装print package : 在印制电路板上按元器件实际尺寸(投影)和引脚规格等做出的,由多个焊盘和表面丝印组成的元器件组装图形。
(4)7)通孔through hole :用于连接印制电路板面层与底层的电镀通路,于插装元件之用。
48)波峰焊wave soldering :预先装有元器件的印制电路板沿着一个方向,通过一种稳定的、连续不断的熔融的焊料波峰进行焊接。
(4)9)回流焊:回流焊又称"再流焊"(Reflow Machine),它是通过提供一种加热环境,使焊锡膏受热融化从而让表面贴装元器件和PCB焊盘通过焊锡膏合金可靠地结合在一起的焊接工艺。
目前比较流行和实用的大多是远红外回流焊、红外加热风回流焊和全热风回流焊。
410)引线间距lead pitch :指元器件结构中相邻引线中心的距离。
(4)11)细间距fine pitch :指表面组装封装组件的引线中心间距≤0.50mm。
电子元器件的生产工艺指导书(新版)
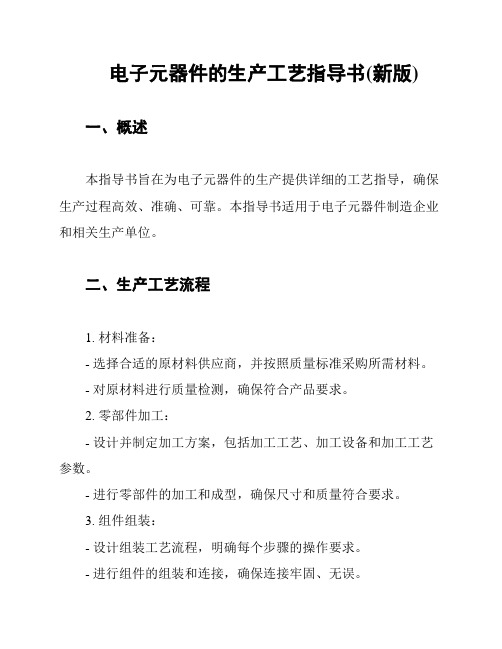
电子元器件的生产工艺指导书(新版)一、概述本指导书旨在为电子元器件的生产提供详细的工艺指导,确保生产过程高效、准确、可靠。
本指导书适用于电子元器件制造企业和相关生产单位。
二、生产工艺流程1. 材料准备:- 选择合适的原材料供应商,并按照质量标准采购所需材料。
- 对原材料进行质量检测,确保符合产品要求。
2. 零部件加工:- 设计并制定加工方案,包括加工工艺、加工设备和加工工艺参数。
- 进行零部件的加工和成型,确保尺寸和质量符合要求。
3. 组件组装:- 设计组装工艺流程,明确每个步骤的操作要求。
- 进行组件的组装和连接,确保连接牢固、无误。
4. 测试与调试:- 制定测试计划和测试方法,包括功能测试、性能测试和可靠性测试。
- 对组装后的产品进行测试和调试,确保产品符合技术要求。
5. 成品包装:- 设计合适的包装方案,确保产品的安全运输和储存。
- 进行产品的包装和标识,确保产品完好无损。
三、质量控制1. 质量管理体系:- 建立和遵守ISO 9001质量管理体系,确保质量管理规范和程序的执行。
- 设立质量管理部门,负责质量管理和质量监控工作。
2. 检测和测试:- 建立完善的检测和测试设备,对原材料、零部件和成品进行全面检测。
- 建立检测和测试记录,以备追溯和分析。
3. 不良品处理:- 建立不良品处理机制,对不合格品进行返工、修正或报废处理。
- 定期分析和总结不良品的原因,采取措施进行改进。
四、安全与环保1. 安全生产:- 遵守相关的安全生产法规,建立安全生产责任制。
- 提供员工必要的安全培训和操作指导。
- 定期进行安全巡检和隐患排查,及时消除安全隐患。
2. 环境保护:- 遵守环境保护法律法规,确保生产过程对环境无害。
- 采取措施进行废物处理和排放控制,减少对环境的污染。
- 定期进行环境监测和评估,确保环境指标达标。
五、持续改进1. 数据分析和评估:- 定期对生产过程和产品质量进行数据分析和评估。
- 基于数据和评估结果,确定改进方向和目标。
元器件工艺要求
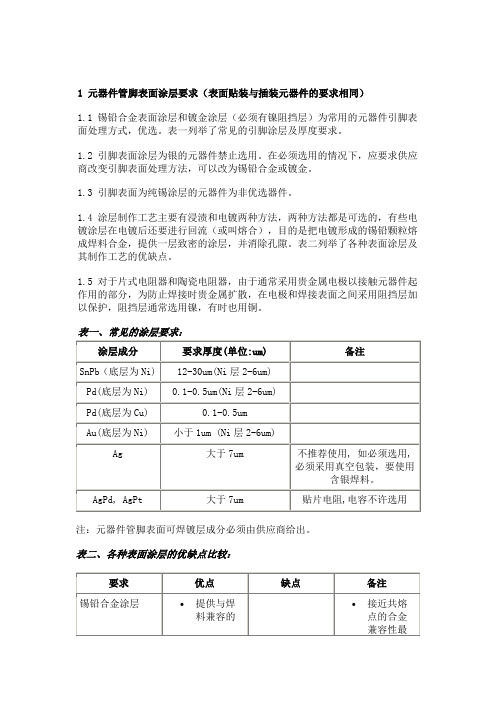
1 元器件管脚表面涂层要求(表面贴装与插装元器件的要求相同)1.1 锡铅合金表面涂层和镀金涂层(必须有镍阻挡层)为常用的元器件引脚表面处理方式,优选。
表一列举了常见的引脚涂层及厚度要求。
1.2 引脚表面涂层为银的元器件禁止选用。
在必须选用的情况下,应要求供应商改变引脚表面处理方法,可以改为锡铅合金或镀金。
1.3 引脚表面为纯锡涂层的元器件为非优选器件。
1.4 涂层制作工艺主要有浸渍和电镀两种方法,两种方法都是可选的,有些电镀涂层在电镀后还要进行回流(或叫熔合),目的是把电镀形成的锡铅颗粒熔成焊料合金,提供一层致密的涂层,并消除孔隙。
表二列举了各种表面涂层及其制作工艺的优缺点。
1.5 对于片式电阻器和陶瓷电阻器,由于通常采用贵金属电极以接触元器件起作用的部分,为防止焊接时贵金属扩散,在电极和焊接表面之间采用阻挡层加以保护,阻挡层通常选用镍,有时也用铜。
表一、常见的涂层要求:注:元器件管脚表面可焊镀层成分必须由供应商给出。
表二、各种表面涂层的优缺点比较:表三、常见金属的可焊性(仅供参考)2 可焊性要求2.1 可焊性试验有很多种方法,各种试验的目的和优缺点有所不同(见表四)。
如果供应商或器件资料上不能很好地说明可焊性测试过程和结果及依照的标准,可以认为该供应商不能很好地保证可焊性,或者考虑按照公司现有的规范对其样品进行可焊性测试。
2.2 不论供应商采用哪一种试验方法,最终插件的可焊性需要满足我公司《插装元器件引线可焊性检测规范》中的要求,表面贴装元器件的可焊性可以与供应商按照下面的2种方法之一做定性/定量的测试。
表四、可焊性试验的几种方法比较3 元器件包装及存储期限的要求。
3.1 为了保持元器件的可靠性和可焊性,避免在运输和贮存过程造成的不良影响,表五对包装的防潮性能作了要求,插装元器件与表面贴装元器件的要求相同,由焊端表面涂层和封装形式来确定应该选择的包装形式,此要求为最低要求。
3.2 元器件运输、存储时的环境条件会对可焊性造成影响,要求如表六,表面贴装与插装元器件的要求相同。
元器件引脚成型工艺
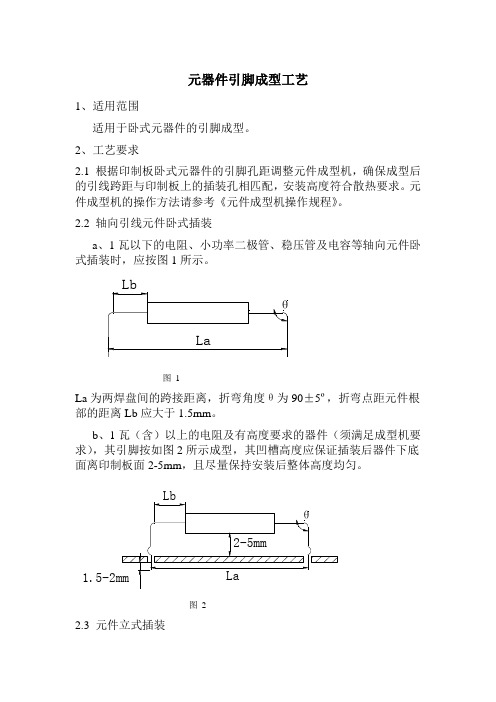
元器件引脚成型工艺1、适用范围适用于卧式元器件的引脚成型。
2、工艺要求2.1 根据印制板卧式元器件的引脚孔距调整元件成型机,确保成型后的引线跨距与印制板上的插装孔相匹配,安装高度符合散热要求。
元件成型机的操作方法请参考《元件成型机操作规程》。
2.2 轴向引线元件卧式插装a、1瓦以下的电阻、小功率二极管、稳压管及电容等轴向元件卧式插装时,应按图1所示。
图1La为两焊盘间的跨接距离,折弯角度θ为90±5º,折弯点距元件根部的距离Lb应大于1.5mm。
b、1瓦(含)以上的电阻及有高度要求的器件(须满足成型机要求),其引脚按如图2所示成型,其凹槽高度应保证插装后器件下底面离印制板面2-5mm,且尽量保持安装后整体高度均匀。
图22.3 元件立式插装轴向引线元件或径向引线元件立式插装时,按图3所示成型,R 应大于元件半径,r应大于引脚直径的2倍。
图3对于引脚跨距与电路板插装孔距匹配的径向引脚元件,不必成型,直接插装,如铝电解电容。
2.4元件引脚成型时,应保证插装到印制板后,其引脚端头露出板面长度为1.5-2mm。
2.5 印有型号、规格等字符的元件成型时应保证插装在印制板上后,标识明显可见,以便于检查或维修。
2.6 元件成型所造成的引脚裂纹和损伤,不得大于引脚直径的10%,不得暴露基底材料,否则作报废处理。
2.7 对于有焊点的引线,折弯处应距离焊点1.5mm以上。
2.8 集成块的成型,请参照《集成块引脚成型机操作规程J-06-005》。
3、质量标准3.1 元件成型后的跨距必须与印制板上的孔距相匹配。
3.2 折弯半径尽可能大,在折弯后不能损伤元件。
3.3 元件的两引脚折弯后应平行,并且保持折弯角度90±5℃。
3.4 元件两端折弯的部位距元件体中心的距离应相等。
3.5 将元件引脚压成“凹槽”时应保证元件插装后以规定距离平行于印制板。
3.6 成型后,保证元器件标识明显可见。
4、注意事项4.1 元件成型时须注意折弯尺寸。
电子元器件安装及焊接工艺设计规范方案精选全文

可编辑修改精选全文完整版电子元器件安装与焊接工艺规范电子元器件安装与焊接工艺规范1范围本规范规定了设备电气盒制作过程中手工焊接技术要求、工艺方法和质量检验要求. 2引用标准以下文件中的有关条款通过引用而成为本规范的条款.凡注日期或版次的引用文件,其后的任何修改单<不包括勘误的内容>或修订版本都不适用于本规范,但提倡使用本规范的各方探讨试用其最新版本的可能性.凡未注日期或版次引用文件,其最新版本适用于本规范.HB 7262.1-1995 航空产品电装工艺电子元器的安装HB 7262.2-1995 航空产品电装工艺电子元器的焊接QJ 3117-1999 航天电子电气产品手工焊接工艺技术要求IPC-A-610E-2010 电子组件的可接收性3技术要求与质量保证3.1一般要求3.1.1参加产品安装和检验的人员必须是经过培训合格的人员.环境温度要求:20℃-30℃.相对湿度要求:30%-75%.照明光照度要求:工作台面不低于500lx.工作场地应无灰尘,及时清除杂物<如污、油脂、导线头、绝缘体碎屑等>工作区域不得洒水.3.2安装前准备把安装所用的器材备齐,并放在适当位置,以便使用;所有工具可正常使用,无油脂,按以下要求检查工具:切割工具刃口锋利,能切出整齐的切口;绝缘层和屏蔽剥离工具功能良好.按配套明细表检查和清点元器件、印制板、紧固件、零件等的型号规格及数量.凡油封的零件或部件,在安装前均应进行清洗除油,并防止已除过的零件再次糟受污染.4元器件在印制板上安装4.1元器件准备4.1.1安装前操作人员应按产品工艺文件检查待装的各种元器件、零件及印制板的外观质量.4.1.2元器件引线按以下要求进行了清洁处理:a、用织物清线器轻轻地擦拭引线,除去引线上的氧化层.有镀层的引线不用织物清线器处理;b、清洁后的引线不能用裸手触摸;c、用照明<CDD>放大镜检验元器件引线清洁质量.4.2元器件成型须知a、成型工具必须表面光滑,夹口平整圆滑,以免损伤元器件;b、成型时,不应使元器件本体产生破裂,密封损坏或开裂,也不应使引线与元器件内部连接断开;c、当弯曲或切割引线时,应固定住元器件引线根部,防止产生轴向应力,损坏引线根部或元器件内部连接;d、应尽量对称成型,在同一点上只能弯曲一次;e、元器件成型方向应使元器件装在印制板上后标记明显可见;f、不允许用接长元器件引线的办法进行成型;g、不得弯曲继电器、插头座等元器件的引线.4.3元器件成型要求4.3.1轴向引线元器件引线弯曲部分不能延长到元器件本体或引线根部,弯曲半径应大于引线厚度或引线直径;见图1:图1 轴向引线元器件引脚折弯要求水平安装的元器件应有应力释放措施,每个释放弯头半径R至少为0.75mm,但不得小于引线直径.图2 元器件应力释放弯头处理要求4.3.2径向引线元器件反向安装径向引线元器件成型要求见图3:图3 径向引线元器件弯角要求4.3.3扁平封装元器件引线成型时就有防震或防应力的专门工具保护引线和壳体封接;用工具挪动扁平组件时,只允许金属工具与外壳接触;装配扁平组件时,工作台面上应垫有弹性材料.4.3.4用圆嘴钳弯曲元器件引线的方法如下:a、将成型工具夹持住元器件终端封接处到弯曲起点之间的一点上;b、逐渐弯曲元器件引线.图44.4元器件在印制板上安装的一般要求4.4.1按装配工序,将盛开好的元器件由小到大依次安装,先安装一般元器件最后再安装电敏感元器件.4.4.2当具有金属外壳的元器件需要跨接印制导线安装时,必须采取良好的绝缘措施.4.4.3安装元器件时,不应使元器件阻挡金属化孔.4.4.4质量较重的元器件应平贴在印制板上,并加套箍或用胶粘接.4.5元器件在印制板上的安装形式4.5.1贴板安装元器件与印制板安装间隙小于1mm,当元器件为金属外壳面安装面又有印制导线时,应加绝缘衬垫或绝缘管套,如图5:图5 贴板安装要求4.5.2悬空安装元器件与印制安装距离一般为3~5mm,如图6.该形式适用发热元器件的安装.图6 悬空安装要求4.5.3垂直安装元器件轴线相对于印制板平面的夹角为90°±10°,见图7.该形式适用于安装密度高的印制板俣不适用于较重的细引线的元器件.图7 元器件垂直安装要求4.5.4支架固定安装用金属支架将元器件固定在印制板上见图8:图8 元器件支架安装要求4.5.5粘接和绑扎安装对防震要求较高的元器件,巾板安装后,可用粘合剂将元器件与印制板粘接在一起,也可以用绵丝绑扎在印制板上,见图9:图9 元器件绑线安装要求4.5.6反向埋头安装反向埋头安装形式见图10:图10 元器件反向埋头安装要求4.5.7接线端子和空心铆钉的安装4.5.7.1接线端子和空心铆钉的安装要求如下:a、安装接线端子和空心铆钉时应满足正常指力下,既不转动,也不轴向移动,没有缺损或印制板基材脱落现象;b、接线端子杆不得打孔、切口、切缝和其它间断点,以免焊料和焊剂漏入孔内;c、铆接后的接线端子或空心铆钉不得有切口、切缝和其它间断点,铆接事,铆接面周围的豁口或裂缝小于90角分开,且延伸不超过铆接面时,允许有三个弧状豁口或裂缝;d、接线端子应垂直安装于印制板,倾斜角应不大于5°.4.5.7.2按以下步骤安装接线端子和空心铆钉:a、将印制板置于夹具上,将清洁的接线端子或空心铆钉从印制板的元件面插入相应的孔内,将印制板翻转,翻转时,接线端子或空心铆钉应紧靠住底板;b、用铆接器<铆压工装>接线端子或空心铆钉铆接到印制板上,应控制好压力.4.6焊接面上元器件引线处理4.6.1弯曲元器件引线焊接面上元器件引线可采用全弯曲、部分弯曲和直插式.a、全弯曲引线:引线弯曲后,引线端与印制板垂线的夹角在75°~90°之间;b、部分弯曲:引线弯曲后,引线端与印制板垂线的夹角在15°~75°之间,见下图,引线伸出长度为0.5mm~1.5mm;c、直插引线:引线端与印制板垂线的夹角在0°~15°之间,见图11,引线伸出长度为0.5mm~1.5mm.图11 焊接面元器件引脚处理要求全弯曲引线一般要求:a、引线弯曲部分的长底不得短于焊盘最大尺寸的一半或0.8mm,但不大于焊盘的直径<或长度>;b、向印制导线方向弯曲引线;c、引线全弯曲后与印制板平面允许的最大回弹角为15°;d、引线弯曲后相邻元器件的间隙不小于0.4mm;e、不许弯曲硬引线继电器、电连接器插针或工艺文件规定的其它元器件引线.4.6.2切割引线用切割器切除引线,不许损坏印制制导线;不许切割直插式集成电路、硬引线继电器插针或工艺文件规定的其它元器件引线.4.6.3固定引线用玻璃纤维焊接工具压倒已切割过的引线.4.7各类元器件在印制板上的安装4.7.1轴向引线元器件安装a、轴向引线元器件应按工艺文件规定进行近似平行安装;b、将引线穿过通孔,弯曲并焊到印制板的焊盘上.弯曲部分应满足要求.4.7.2径向引线元器件安装4.7.2.1金属壳封装的元器件反向埋头安装要求见条的要求.4.7.2.2伸出引线的基面应平行于印制板的表面,且有一定的间隙.4.7.2.3引线应从元器件的基点平直地延长,引线的弯头不应延伸到元件的本体或焊点处.4.7.2.4当元器件每根引线承重小于3.5g时,元器件可不加支撑面独立安装,此时,元器件的基面和印制板表面间距为1.3mm~2.5mm.基准面应平行印制板表面,倾斜角在10度以内.4.7.2.5当元器件每根引线承重大于3.5g时,元器件基面将平行于印制板表面安装,元器件应以以下方式加支撑:a、元器件本身所具备的弱性支脚或支座,与元器件形成一个整体与底板相接;b、采用弹性或非弹性带脚支架装置,支座不堵塞金属化孔,也不与印制板上的元器件内连;c、当弹性支座或非弹性带脚支座的元器件安装到印制板时,元器件每个支脚都应与印制板相连,支脚的最小高度为0.25mm,当使用一个分离式弹性支座或分离式弹性无脚支座时,元器件基面与印制板表面平行安装的要求, 使用非弹性支座连接元器件基面并平行安装于印制板表面时,则基面应与支座完全接触,支脚应与印制板完全接触.4.7.2.6侧面或端部安装的元器件应与印制板粘接或固定住,以防因冲击或震动而松动.4.7.2.7引线带有金属涂层的元器件安装,涂层与印制板表面焊盘处距离不得小于0.25mm.禁止修整引线涂层.4.7.3双引线元器件安装要求:距印制板表面最近的元器件本体边缘与印制板表的平行角度在10度以内,且与印制板间距在1.0mm~2.3mm以内,元器件与印制板垂线成最大角度为±15°.4.7.4扁平封装元器件安装扁平封装元器件的安装要求见条.4.7.5双列直插式集成电路的安装双列直插式元器件基面应与印制板表面隔开,其间距为0.5mm~1mm或引线的凸台高度.4.8焊接方法4.8.1单面印制板的焊接图12 单面印制板的焊接4.8.2金属化孔双面印制板的焊接金属化孔双面印制板的焊接应符合图要求.对有引线或导线插入的金属孔,通孔就充填焊料,焊料应从印制电路板一侧连续流到另一侧的元器件面,并覆盖焊盘面积90%以上,焊料允许凹缩进孔内,凹缩量如图13:图13 元器件在金属化孔双面印制板上的焊接4.8.3多层印制板的焊接多层印制板的焊接应符合图14要求.严禁两面焊接以防金属化孔内出现焊接不良.图14 元器件在多层印制板上的焊接4.8.4扁平封装集成电路的焊接采用对角线焊接方法,并符合以下规定:扁平应沿印制导线平直焊接,元器件引线与印制板的焊盘应匹配;引线最小焊接长度为1.5mm且引线在焊盘中间;元器件的型号规格标识必须在正面,严禁反装;扁平封装集成电路未使用的引线应焊接在相应的印制导线上;焊点处引线轮廓可见.图15 扁平封装元器件的焊接4.8.5断电器的焊接焊接时非密封继电器应防止焊济、焊料渗入继电器内部,在接线端子之间应塞满条形吸水纸带,焊接时继电器焊接面倾斜不大于90°.焊接密封继电器时,要防止接线端子根部绝缘子受热破裂,可用蘸乙醇的棉球在绝缘子周围帮助散热.4.8.6开关元器件的焊接焊接时可采用接点交叉焊接的方法,使加热温度分散,减少损坏.5元器件焊接判定标准元器件焊接质量判定可根据附表1~附表16内的图示.附表 2 有引脚的支撑孔-焊接主面目标 可接受不可接受和孔壁润湿角=360° 焊锡润湿覆盖率=100%•引脚和孔壁润湿角≥270° •焊盘焊锡润湿覆盖率≥0•引脚和孔壁润湿角<270°附表3 有引脚的支撑孔-焊接辅面目标可接受不可接受和孔壁润湿角=360° 焊锡润湿覆盖率=100%•引脚和孔壁润湿角≥330° •焊盘焊锡润湿覆盖率≥75%•引脚和孔壁润湿角<330° •焊盘焊锡润湿覆盖率<75%附表4 焊点状况目标可接受不可接受附表1 焊点润湿目标可接受不可接受1焊点表层总体呈现光滑和与焊接零件由良好润湿;部件的轮廓容易分辨;焊接部件的焊点有顺畅连接的边缘;2表层形状呈凹面状.可接受的焊点必须是焊接与待焊接表面,形成一个小于或等于90度的连接角时能明确表现出浸润和粘附,当焊锡量过多导致蔓延出焊盘或阻焊层的轮廓时除外.1不润湿,导致焊点形成表面的球状或珠粒状物,颇似蜡层面上的水珠;表面凸状,无顺畅连接的边缘;2移位焊点; 3虚焊点.洞区域或表面瑕疵;和焊盘润湿良好;形状可辨识;周围100%有焊锡覆盖;覆盖引脚,在焊盘或导薄而顺畅的边缘. •焊点表层是凹面的、润湿良好的焊点内引脚形状可以辨识.•焊点表面凸面,焊锡过多导致引脚形状不可辨识,但从主面可以确认引脚位于通孔中;•由于引脚弯曲导致引脚形状不可辨识.附表5 有引脚的支撑孔-垂直填充目标可接受不可接受润湿角度=360°焊锡润湿覆盖率=100% •周边润湿角度≥330°•焊盘焊锡润湿覆盖率≥75%•周边润湿角度<330°•焊盘焊锡润湿覆盖率<75% 附表6 焊接异常-暴露基底金属目标可接受不可接受露基底金属·基底金属暴露于:a〔导体的垂直面b〔元件引脚或导线的剪切端c〔有机可焊保护剂覆盖的盘·不要求焊料填充的区域露出表面涂敷层·元件引脚/导体或盘表面由于刻痕、划伤或其它情况形成的基底金属暴露不能超过对导体和焊盘的要求附表7 焊接异常-针孔/吹孔目标可接受不可接受良好、无吹孔·润湿良好、无吹孔·针孔/吹孔/空洞等使焊接特性降低到最低要求以下附表8 焊接异常-焊锡过量-锡桥目标可接受不可接受·**桥·横跨在不应相连的两导体上的焊料连接·焊料跨接到非毗邻的非共接导体或元件上附表9 焊接异常-焊锡过量-锡球目标可接受不可接受现象·锡球被裹挟/包封,不违反最小电气间隙注:锡球被裹挟/包封连接意指产品的正常工作环境不会引起锡球移动·锡球未被裹挟/包封·锡球违反最小电气间隙附表10 引脚折弯处的焊锡目标可接受不可接受折弯处无焊锡·引脚折弯处的焊锡不接触元件体·引脚折弯处的焊锡接触元件体或密封端附表11 焊接异常-反润湿目标可接受不可接受良好、无反润湿现象·润湿良好、无反润湿现象·反润湿现象导致焊接不满足表面贴装或通孔插装的焊料填充要求附表12 焊接异常-焊料受拢目标可接受不可接受料受拢·无焊料受拢·因连接产生移动而形成的受拢焊点,其特征表力纹附表13 焊接异常-焊料破裂目标可接受不可接受料破裂·无焊料破裂·焊料破裂或有裂纹附表14 焊接异常-锡尖目标可接受不可接受圆润饱满没有锡尖·焊锡圆润饱满没有锡尖·锡尖违反组装的最大高度要求或引脚凸出要求1.5毫米·锡尖违反最小电气间隙附表15 镀金插头目标可接受不可接受插头上无焊锡·镀金插头上无焊锡·在镀金插头的实际连接区域有焊锡、合金以外其它金属附表16 焊接后的引脚剪切目标可接受不可接受·引脚和焊点无破裂·引脚凸出符合规范要求·引脚和焊点无破裂·引脚凸出符合规范要求·引脚与焊点间破裂。
电子工业工艺文件
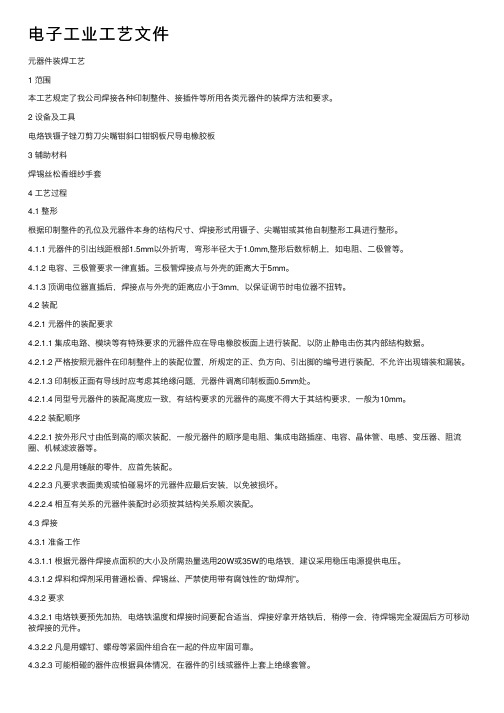
电⼦⼯业⼯艺⽂件元器件装焊⼯艺1 范围本⼯艺规定了我公司焊接各种印制整件、接插件等所⽤各类元器件的装焊⽅法和要求。
2 设备及⼯具电烙铁镊⼦锉⼑剪⼑尖嘴钳斜⼝钳钢板尺导电橡胶板3 辅助材料焊锡丝松⾹细纱⼿套4 ⼯艺过程4.1 整形根据印制整件的孔位及元器件本⾝的结构尺⼨、焊接形式⽤镊⼦、尖嘴钳或其他⾃制整形⼯具进⾏整形。
4.1.1 元器件的引出线距根部1.5mm以外折弯,弯形半径⼤于1.0mm,整形后数标朝上,如电阻、⼆极管等。
4.1.2 电容、三极管要求⼀律直插。
三极管焊接点与外壳的距离⼤于5mm。
4.1.3 顶调电位器直插后,焊接点与外壳的距离应⼩于3mm,以保证调节时电位器不扭转。
4.2 装配4.2.1 元器件的装配要求4.2.1.1 集成电路、模块等有特殊要求的元器件应在导电橡胶板⾯上进⾏装配,以防⽌静电击伤其内部结构数据。
4.2.1.2 严格按照元器件在印制整件上的装配位置,所规定的正、负⽅向、引出脚的编号进⾏装配,不允许出现错装和漏装。
4.2.1.3 印制板正⾯有导线时应考虑其绝缘问题,元器件调离印制板⾯0.5mm处。
4.2.1.4 同型号元器件的装配⾼度应⼀致,有结构要求的元器件的⾼度不得⼤于其结构要求,⼀般为10mm。
4.2.2 装配顺序4.2.2.1 按外形尺⼨由低到⾼的顺次装配,⼀般元器件的顺序是电阻、集成电路插座、电容、晶体管、电感、变压器、阻流圈、机械滤波器等。
4.2.2.2 凡是⽤锤敲的零件,应⾸先装配。
4.2.2.3 凡要求表⾯美观或怕碰易坏的元器件应最后安装,以免被损坏。
4.2.2.4 相互有关系的元器件装配时必须按其结构关系顺次装配。
4.3 焊接4.3.1 准备⼯作4.3.1.1 根据元器件焊接点⾯积的⼤⼩及所需热量选⽤20W或35W的电烙铁,建议采⽤稳压电源提供电压。
4.3.1.2 焊料和焊剂采⽤普通松⾹、焊锡丝、严禁使⽤带有腐蚀性的“助焊剂”。
4.3.2 要求4.3.2.1 电烙铁要预先加热,电烙铁温度和焊接时间要配合适当,焊接好拿开烙铁后,稍停⼀会,待焊锡完全凝固后⽅可移动被焊接的元件。
元器件成型工艺规范
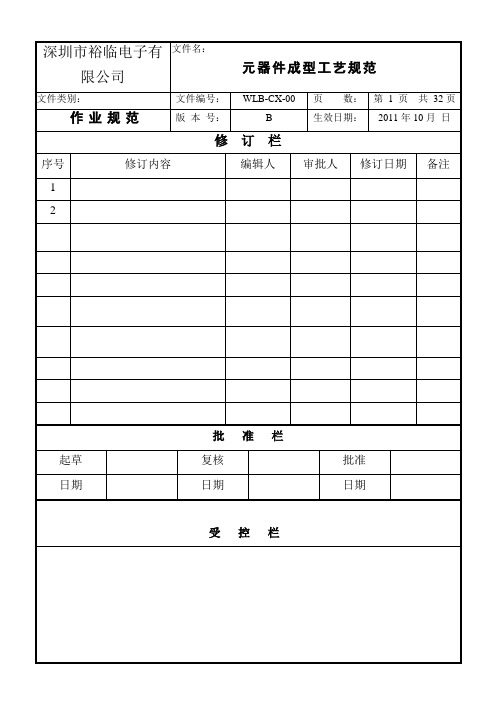
5.1.3.3 折弯角度ω折弯类型折弯角度ω(公差+3度),优选值变向折弯90度非变向折弯120度、135度或150度5.1.3.4 偏心距V偏心距是针对非变向折弯而言的参数,对偏心距不规定具体数值。
但必须要保证元器件在其丝印框内,且符合电气间隙与安规要求,同进引脚上无应力存在。
如果偏心距过小(主要针对功率管的引脚成型),我司的模具无法保证成型的偏心距。
给出一个通用的参考值:不小于1.5mm。
5.1.3.5 K值引脚的直径(D)或厚度(T)K值(优选值)D( T )≤0.8mm 2.5 mm0.8mm<D( T )<1.2mm 3.5 mmD( T )≥1.2mm 4.0 mm5.1.4 元器件的成型(主要根据公司的实际情况)5.1.4.1 元件的出脚(指插装后的元件伸出PCB部分的长度)控制在0.5 – 2.5 mm间。
因考虑到模具公差和波峰时的焊锡堆积和拉尖,同时为方便控制加工,将成型元件的出脚长度统一规定为2.0mm。
注意:如果客户对元件出脚有特殊要求,必须按客户要求进行元件成型加工。
如要求出脚为1.0mm,则贴板元件按:板厚+1.0mm控制,抬高元件按:H(抬高高度)+板厚+1.0mm控制;如要求出脚为1.5mm,则贴板元件按:板厚+1.5mm控制,抬高元件按:H(抬高高度)+板厚+1.5mm 控制。
5.1.4.2 具体元器件的成型要求5.1.4.2.1 对1W以下卧式插装的非功率电阻,要求贴板成型,成型尺寸如下图所示:L:电阻所对应的焊盘之孔距;H为电阻的本体的半径;X-Y≤±0.5mm;其它尺寸需满足5.1.3引脚折弯的要求。
5.1.4.2.2 对1W以下立式插装的非功率电阻,要求贴板插装,成型尺寸如下图所示:L:电阻所对应的焊盘之孔距;其它尺寸需满足5.1.3引脚折弯的要求。
5.1.4.2.3 对1W 及1W 以上卧式成型的功率电阻,我司均有要求供应商来料成型,有打K 和扁脚两种抬高方式。
电子元器件插件实用工艺要求规范

实用6.2元器件的插件检验标准6.2.1卧式零件插件的方向与极性+R1 C1Q R2D2 理想状况(Target Condition)1.零件正确组装于两锡垫中央;2.零件的文字印刷标示可辨识;3.非极性零件文字印刷的辨识排列方向统一(由左至右,或由上至下)。
+R1 C1Q R2D2 允收状况(Accept Condition) 1.极性零件与多脚零件组装正确。
2.组装后,能辨识出零件的极性符号。
3.所有零件按规格标准组装于正确位置。
4.非极性零件组装位置正确,但文字印刷的辨示排列方向未统一(R1,R2)。
+C1 拒收状况(Reject Condition)1.使用错误零件规格(错件)。
2.零件插错孔。
6.2.2立式零件组装的方向与极性6.2.3卧式电子零组件插装高度与倾斜1000μF++ + J233 ●拒收状况(Reject Condition)1.极性零件组装极性错误 (极性反) 。
2.无法辨识零件文字标示。
3.以上缺陷任何一个都不能接收。
1000μF++10μ 16● 332J允收状况(Accept Condition) 1.极性零件组装于正确位置。
2.可辨识出文字标示与极性。
6.2.4立式电子零组件浮件6.2.5机构零件浮件6.2.6机构零件组装外观(1)6.2.6机构零件组装外观(2)6.2.7零件脚折脚、未入孔、未出孔6.2.8零件脚与线路间距6.2.9元件本体斜度最佳: 元件本体与其在基板上两插孔位组成的连线或元件体在基板上的边框线完全平行,无斜度,如图: 可接受: 元件体与其在基板上两插孔位组成的连线或元件体在基板上的边框线斜度≤1.0mm,如图: 拒收: 元件体与其在基板上两插孔位组成的连线或元件体在基上的边框线斜度>1.0mm,如图:6.2.10元件引脚的紧张度最佳: 元件引脚与元件体主轴之间夹角为0°(即引脚与元件主轴平行, 垂直于PCB板面), 如图:可接受: 元件引脚与元件体主轴袒闪角Q<15°,如图:拒收: 元件引脚与元件体主轴之间夹角Q>15°.6.2.11元件引脚的电气保护在PCBA板上有些元件要有特殊的电气保护,则通常使用胶套,管或热缩管来保护电路最佳: 元件引脚弯曲部分有保护套,垂直或水平部分如跨过导体需有保护套且保护套距离插孔之间距离A为1.0mm-2.0mm,如图:可接受: 保护套可起到防止短路作用, 引脚上无保护套时, 引脚所跨过的导体之间的距离B≥0.5mm, 如图:拒收: 保护套损坏或A>2.0mm时, 不能起到防止短路作用或引脚上无保护套时, 或引脚所跨过的导体之间距离B<0.5mm,如图:6.2.12元件间的距离最佳: 在PCBA板上,两个或以上踝露金属元件间的距离要D≥2.0mm,如图:可接受: 在PCBA板上, 两个或以上踝露金属元件的距离最小D≥1.6mm, 如图:拒收: 在PCBA板上, 两个或以上踝露金属元件间的距离D<1.6mm, 如图:6.3元件的损伤6.3.1元件本体损伤最佳: 元件表面无任何损伤,且标记清晰可见,如图:可接受: 元件表面有轻微的抓、擦、刮伤等,但未露出元件基本面或有效面,如图:拒收: 元件面受损并露出元件基本面或有效面积,如图:6.3.2元件引脚的损伤最佳: 元件引脚无任何损伤, 弯脚处光滑完好, 元件表面标记清晰可见, 如图:可接受: 元件引脚不规则弯曲或引脚露铜,但元件或部品引脚损伤程度小于该引脚直径的10%,如图:拒收: ( 1 )元件引脚受损大于元件引脚直径的10%,如图:( 2 )严重凹痕锯齿痕,导致元件脚缩小超过元件的10%,如图:6.3.3 IC元件的损伤最佳: IC 元件无任何损伤, 如图:可接受: 元件表面受损, 但未露密封的玻璃, 如图:拒收: 元件表面受损并露出密封的玻璃, 如图:6.3.4轴向元件损伤最佳: 元件表面无任何损伤,如图:可接受: 元件表面无明显损伤,元件金属成份无暴露,如图:拒收:( 1 )元件面有明显损伤且绝缘封装破裂露出金属成份或元件严重变形,如图:( 2 ) 对于玻璃封装元件,不允许出现小块玻璃脱落或损伤.6.4元件应力评估,进行插件作业时,需参照以下表格对个各元件易产生应力部位进行重点检查和防护。
电子产品的工艺文件

右图是
×× 袖珍 收音 机的 工艺 文件 封面 。
路漫漫其修远兮, 吾将上下而求索
工艺文件
型 号 科宏2045 名 称 AM/FM袖珍收音机 图 号 ××× 本册内容 收音机的装配调试
共1册 第1册 共页
批准 ××× 2006年5月6
日
工艺文 件明细 表是工 艺文件 的目录 。成册 时,应 装在工 艺文件 的封面 之后, 反映产 品工艺 文件的 齐套性 。
➢工艺文件明细表(目录)
路漫漫其修远兮, 吾将上下而求索
填写文件 的简号
工艺文件目录 明细表产品名称或型号
产品图 号
序 文件 号 代号
1
2
零部件、整件 图号
3
零部件、整 件名 称
页数
4
5
备注
6
填写被 本底图 所代替 的旧底 图总号
填写 更改 事项
路漫漫其修远兮, 吾将上下而求索
使用性
旧底图 总号
底图总 号
下图给出了××收音机的导线加工表。
路漫漫其修远兮, 吾将上下而求索
导线及线扎加工表
产品名称或型号
编号
名称规格
颜 色
数 量
L全 长
1
2
34 5
1
ASTVR 黄
80
填写
2
导线 3
的编 4
号
5
6
填写 7
材料 8
使用性的名
称规
格、
旧底图总颜号 色 、数
量
黑
80
黑
40
白
90
红
60
黄
80
长度(mm) A B A剥 端端 头
生效日期
元器件在pcb插装的顺序和工艺要求

元器件在pcb插装的顺序和工艺要求PCB(Printed Circuit Board)是电子产品的重要组成部分,元器件的插装顺序和工艺要求对于PCB的性能和稳定性具有重要影响。
本文将从元器件插装的顺序分析、插装工艺要求以及影响因素三个方面详细介绍元器件在PCB插装过程中的重要性和注意事项。
一、元器件插装的顺序分析元器件插装的顺序对于PCB的性能和可靠性具有重要影响。
一般情况下,元器件插装的顺序应该是从矮小到高大的顺序进行,即从矮的元器件开始插装,然后逐渐插装高的元器件。
这样可以避免在插装高的元器件时,造成对于已插装元器件的损坏或者困难。
另外,还应该避免元器件之间产生阴影效应,影响PCB的性能。
二、插装工艺要求1.对于不同类型的元器件,插装的工艺要求也不同。
如IC插装需要注意对引脚的定位和正确性,需要使用专门的夹具和设备。
而电阻和电容的插装需要注意插装的方向和位置,避免产生短路或者插装不良的情况。
2.在插装过程中,需要严格控制温湿度和静电环境,避免对元器件产生损坏。
特别是在插装静电敏感元器件时,需要采取防静电措施,避免元器件受到静电损坏。
3.同时,对于贴片元器件的插装,需要注意粘贴剂的使用和精确度,确保元器件能够牢固地粘附在PCB上,并且不影响元器件的正常使用。
三、影响因素分析1.设计因素:在PCB设计的初期,需要考虑元器件的插装顺序和工艺要求。
合理的布局和排列可以减少插装的困难和错误,提高插装的效率和准确性。
2.环境因素:在插装过程中,温湿度和静电环境的控制对于元器件的稳定性和可靠性具有重要影响。
特别是在插装静电敏感元器件时,需要特别注意防静电措施。
3.人为因素:插装工艺需要操作人员有一定的经验和技能,严格遵守插装规范和操作步骤。
同时需要进行不断的培训和学习,提高插装的准确性和稳定性。
综上所述,元器件在PCB插装的顺序和工艺要求对于PCB的性能和稳定性具有重要影响。
对于不同类型的元器件,插装的工艺要求也不同,需要根据具体情况进行具体处理。
电子产品的工艺技术文件

电子产品的工艺技术文件电子产品工艺技术文件电子产品作为现代生活不可或缺的一部分,需要经过复杂的工艺流程才能够顺利制造出来。
下面是一份电子产品工艺技术文件,介绍了电子产品的制造过程和技术细节。
一、工艺流程电子产品的制造过程可以简单分为三个阶段:物料准备、组装过程和调试测试。
1.物料准备:在制造过程开始之前,需要进行物料的采购和准备工作。
物料包括各种电子元件和元器件,例如电路板、电容、电阻、集成电路芯片等。
这些物料需要提前进行选择和采购,并在制造过程中合理组织和调配。
2.组装过程:组装过程是将各个物料进行拼装和连接的过程。
首先,将电路板放置在组装台上,根据电子产品的设计要求精确确定各个电子元件和元器件在电路板上的位置。
然后,使用焊接技术将电子元件和电路板连接在一起,确保电路板上各个元件之间的电路连接是正确无误的。
3.调试测试:在组装完成之后,需要对电子产品进行调试和测试。
通过专业的测试设备,检测电子产品的各项性能指标,例如功耗、主频、传输速率等。
同时,还需要对产品的外观进行检查,确保产品无瑕疵。
二、工艺技术要点1.焊接技术:电子产品的焊接是一个关键的工艺环节。
焊接技术的好坏会直接影响到电子产品的质量和可靠性。
目前,常用的焊接技术有手工焊接、波峰焊接和热风回流焊接等。
不同的焊接技术适用于不同的电子元件和元器件,需要根据产品的特点和工艺要求进行选择和应用。
2.贴片技术:随着电子产品的小型化和轻量化趋势,贴片技术在电子产品制造中得到广泛应用。
贴片技术是将电子元器件直接贴附在电路板上的一种技术。
通过贴片技术,可以大幅度减小电子产品的体积,提高产品的集成度。
3.自动化生产:为了提高生产效率和产品质量,电子产品制造过程中越来越多的环节实现了自动化生产。
例如,自动贴片机、自动焊接设备等,大幅度提高了生产效率,减少了人为因素带来的质量问题。
三、工艺技术改进为了满足市场日益增长的需求,电子产品制造过程中的工艺技术也在不断改进和创新。
元器件成形工艺标准文件
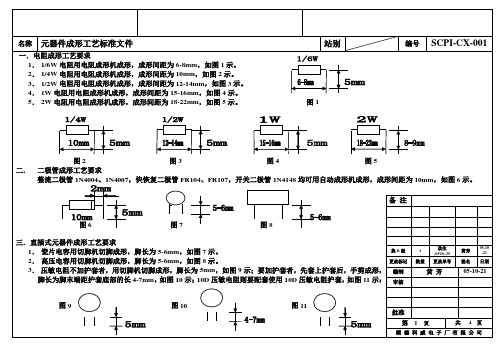
换B版
1
改生-0510-35
黄芳
05-10-21
更改标记
数量
更改单号
签名
日期
编制
黄芳
05-10-21
审核
批准
第4页
共4页
顺德科威电子厂有限公司
2.高压电容用切脚机切脚成形,脚长为5-6mm,如图8示。
3.压敏电阻不加护套者,用切脚机切脚成形,脚长为5mm,如图9示;要加护套者,先套上护套后,手剪成形,脚长为脚末端距护套底部的长4-7mm,如图10示;10D压敏电阻则要配套使用10D压敏电阻护套,如图11示:
图9图10图11
备注
换B版
1
改生-0510-35
九.发光二极管成形要求
发光二极管用切脚机成型,脚长根据具体机型而定,成型后,按相应机型,工艺要求插装到线路板后,露出板底脚长为1.5-2.5mm。
图12图13图14图15
图16图17图18
备注
换B版
1
改生-0510-35
黄芳
05-10-21
更改标记
数量
更改单号
签名
日期
编制
黄芳
05-10-21
审核
批准
第2页
共4页
顺德科威电子厂有限公司
e
名称
元器件成形工艺标准文件
站别
编号
SCPI-CX-001
十.三端稳压器安装散热器的工艺要求。
涂有均匀适量硅脂的三端稳压器用M3×6的螺丝固定在散热器上,三端稳压器应紧贴散热器,且两者应互相平行,请参见图19示:
(三端稳压器、散热器的规格请参见相应的工艺文件,螺丝规格若没有特别说明均使用M3×6的螺丝)
e
电气工艺文件

编号:HC-SC-02-2011版本:B/0发放号:合肥花冲电器开关厂工艺文件编制:审核:批准:2011年11月23日发布2011年11月23日实施文件目录元件装配工艺规程HC-SC-02-2011-11 1 、目的加强本公司低压成套设备元件装配质量。
特制定本规程。
2、范围本守则适用于各种低压柜的元件装配、成套开关柜的元器件装配。
本规则规定了成套开关柜的元器件装配的准备事项、工艺方法、检查验收和注意事项。
3、准备工作施工前,应根据图纸,检查元件的规格、数量是否符合图纸要求,如有损坏或缺少的应及时换掉和领取。
特别各元件的圈电压应与图纸一致。
4、工艺过程4.1 所安装件必须选用取得CCC认证厂家生产的合格产品,对尚未发放许可证的元件,准许选符合技术条件的合格品,并保存元件合格证书,否则不能安装。
4.2 元件的安装方式要符合元件产品说明书的规定,以保证元件的正常工作条件。
元件安装后要适当校正元件的位置,使得安装后的台面元件排列,从视觉上做到横平竖直,整齐美观。
4.3 电器元件中的指示灯及按钮的颜色的含义应符合《电工成套装置中的指示灯和安钮的颜色》中的规定。
4.4 安装在柜后的元件以及端子排,其安装位置尽量偏靠柜的上方或一方或一侧,以不妨碍其它元件的正常维修或拆装为原则。
对有绝缘要求又无绝缘底座的元件,应先固定在绝缘板上,然后再安装,或者在其底座上垫上绝缘板后,再一起安装上去。
4.5 柜后元件排列应整齐,层次分明。
元件安装后,紧固件是确实固紧,保证在支输中不致因震动脱落,使元件受损。
4.6对于长期带电发热的元件,其温升应符合本身的技术标准的要求。
安装时应尽量偏靠柜的上方,同时与周围元件应保证有不小于20mm的空间距离。
4.7 如果竖装的端子排数量较多,同一侧确需安装两排端子排时,两排间隔距离就不小于150mm。
4.8 门及面板上电器元件的安装,以元件盖住螺丝安装孔为准,不允许出现元件安装后有露孔现象存在。
元件成型的规范要求
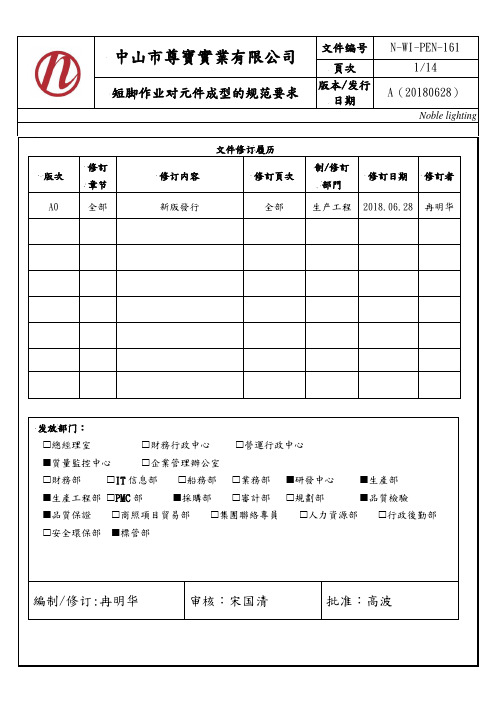
5.4未注公差均按±0.5mm。
5.5成型时不允许从元器件引线的根部直接弯折。规定弯折处距离元器件主体≥1.0mm。
5.6成型后的引线
5.6.1不得有扭曲现象,引线上不得有明显压坏和其他伤痕。
5.6.2折弯处的痕迹规定不超过0.25d的凹陷(d为引线直径)。
文件修订履历
版次
修訂章节
修订内容
修訂頁次
制/修訂部門
修訂日期
修訂者
A0
全部
新版發行
全部
生产工程
2018.06.28
冉明华
发放部门:
總經理室財務行政中心營運行政中心
質量監控中心企業管理辦公室
財務部IT信息部船務部業務部研發中心生產部
生產工程部PMC部採購部審計部規劃部品質檢驗
品質保證商照項目貿易部集團聯絡專員人力資源部行政後勤部安全環保部標管部
适用元器件
径向型(电容、发光二极管、三极管、红外接收器)
应用环境
元器件表面温升≤40℃
元器件的外形尺寸
备注
*为成型三极管类、无极性电容字符面或红外接收器类的工作面定向
6.6 ZR型
ZR型
成型代号
电容类CZR-s×h
径向二极管类VZR-s×h
三极管类VZR-s×h
电感类LZR-s×h
标定成型跨距/参数(s)
編制/修订:冉明华
审核:宋国清
批准:高波
1.0目的
规范元器件来料成型操作的方法和流程,消除元器件成型时应力造成的损伤,提高产品可靠性,提高产品质量,防止出现批次质量事故。
2.0适用范围
本规范规定了元器件引线成型生产中人、机、料、法、环的工艺要求和质量检测中的管理要求、质量控制方法、元器件引线成型方式和技术要求。本规范适用于印制板厚度为1.0~1.6mm,用手工插件的元器件(包括电阻器、电容器、电感器、二极管、三极管、集成电路、振荡器、保险丝管保险管)引线成型。适用于本公司所有产品,包括内、外发产品。
- 1、下载文档前请自行甄别文档内容的完整性,平台不提供额外的编辑、内容补充、找答案等附加服务。
- 2、"仅部分预览"的文档,不可在线预览部分如存在完整性等问题,可反馈申请退款(可完整预览的文档不适用该条件!)。
- 3、如文档侵犯您的权益,请联系客服反馈,我们会尽快为您处理(人工客服工作时间:9:00-18:30)。
合),目的是把电镀形成的锡颗粒熔成焊料合金,提供一层致密的涂层,并消除孔隙。
表 2 列举了各种表面涂层及其制作工艺的优缺点。
表 2 :各种表面涂层的优缺点比较
要求
优点
缺点
备注
锡铅合金涂层
提供与焊料兼容的金相
接近共熔点的合金
兼容性最好
焊料人工浸渍涂层 贮存寿命长
昂贵
共熔合金涂敷
难于控制表面集合几何形状
电镀涂层
较好地控制表面几何形状
锡铅比例对电镀参数敏感
细颗粒电镀可焊性
比浸渍成本低
易受氧化
比粗颗粒的长
电镀涂层回流
锡铅合金电镀
成本增加
关于这种工艺的意
气孔率降低
控制表面几何形状的能力减弱 见分歧较大
为基底金属的可焊性提供反馈
序号 1 2 3 4 5
首次修订
变更内容
版本 A/0
生效日期 2010-8-5
本要求规定了表面贴装元器件和插装元器件的工艺技术要求,以保证所选用的元器件具有良好的工艺性。
2. 适用范围 本技术要求适用于金升阳公司的所有元器件,是对元器件工艺技术的通用要求,只有满足要求的元器件才能被选
用、生产。 本要求将随工艺水平的提高而更新。
3. 引用文件 EIA/IS-47《Contact Terminations Finish for Surface Mount Device》 J-STD-001B《Requirements for Soldered Electrical and Electronic Assemblies》 IEC68-2-69《Solder ability testing of electronic components for surface mounting technology by the wetting balance methods》 EIA-481-A《表面安装器件卷带盘式包装》 IEC286《表面安装器件卷带盘式包装》 IPC-SM-786A《Procedures for Characterizing and Handling of Moisture/Reflow Sensitive Plastic ICs》 J-STD-020《Moisture/Reflow Sensitivity Classification of Plastic Surface Mount Devices》 IPC-SC-60A《Post Solder Solvent Cleaning Handbook》 IPC-AC-62A《Post Solder Aqueous Cleaning Handbook》 IPC-CH-65《Guidelines for Cleaning of Printed Boards and Assemblies 》 IPC-7711《Rework of Electronic Assemblies(Replaces IPC-R-700)》 IPC-7721《Repair and Modification of Printed Boards and Electronic Assemblies(Replaces IPC-R-700) 》 IPC-SM-780《Guidelines for Component Packaging and Interconnection with Emphasis on Surface Mounting》 J-STD-004《Requirement for Soldering Flux》 J-STD-002《solder ability test for component lead, Terminations, Lugs, Terminals and Wires》
拟制
审核
批准
文件编号: 文件名称:
MS-SOP-PE元器件工艺要求文件
版 本 号:
A
适用部门:
作业指导书
第 3 页 共 12 页
贵金属上的阻挡层 提高了浸析阻力
成本增加
4.1.5. 对于片式电阻器和陶瓷电容器,由于通常采用贵金属电极以接触元器件起作用的部分,为防止焊接时贵金属扩
散,在电极和焊接表面之间采用阻挡层加以保护,阻挡层通常选用镍,有时也用铜。
版本 A/0
生效日期 2010-8-5
拟制
审核
批准
文件编号: 文件名称:
MS-SOP-PE元器件工艺要求文件
版 本 号:
A
适用部门:
作业指导书
第 5 页 共 12 页
℃(工业温度)、-40℃~+125℃(汽车温度)】。 4.6. 可焊性要求
可焊性试验有很多种方法,各种试验的目的和优缺点有所不同(见表 5)。如果供应商或器件资料上不能很好地说 明可焊性测试过程和结果及依照的标准,可以认为该供应商不能很好地保证可焊性,或者考虑按照公司现有的规范对 其样品进行可焊性测试。
表面安装元器件的焊端经过下面的检验后,焊端表面超过 95%的面积被焊料覆盖,且无针孔。 检验条件:
首先表面安装元器件的焊端经过 8 小时蒸汽老化,将 25%的水白松香和 75%的异丙醇组成的 R 型焊剂涂抹在表 面安装元器件的焊端上,再将焊端浸入 245℃±5℃熔融的 SAC305 焊料中 3~5 秒钟,取出元器件,用 10×显微镜观察 焊端覆盖焊料的情况,焊料在焊端面积覆盖率达到 95%以上。
4.1.6. 元器件引脚金属成分和可焊镀层金属成分要与公司使用或外协厂使用的助焊剂类型相匹配。
4.1.7. 对于无铅器件,供应商需指明拆分原则,且需提供每个拆分部分的检测报告,若有豁免部分,需指出豁免理由。
4.1.8. 焊料涂层的类别;
e1-锡银铜
e2-其它锡合金(即锡铜、锡银、锡银铜 X 等)
e3-锡
4.1.4. 阻挡层 Ni:1~3μm(片式元件阻挡层 Ni:1~3μm)。
表 1 :常见的涂层要求
涂层成分
要求厚度(单位: μm)
备注
≥8
没有镍或银底层
≥2
采用镍或银底层
Sn
≥5.1
浸锡工艺
≥0.5
化学镀纯锡工艺
SnCu
≥3
Pd(底层为 Ni)
≥0.075
Pd(底层为 Cu)
0.1-0.5
Au(底层为 Ni)
表 3 :用于 IC 器件封装的材料举例
氧化铝陶瓷
烧成温度 1620℃~1670℃
高温真空封接玻璃
封接温度为 880℃~950℃
低熔封接玻璃
封接温度为 430℃~460℃
热固性模塑料(塑料材料有以高分子化合物合成树 塑模固化温度约为 170 ℃~190 ℃。
脂为基体的改性环氧)
氧化铍陶瓷
氮化铝陶瓷
序号 1 2 3 4 5
≤0.1
Au(底层为 Pd)
≤0.1
不推荐, 如必须选用, 须采用真
Ag
≥7
空包装,使用含银焊料。
AgPd, AgPt
≥7
注:A.元器件管脚表面可焊镀层成分必须由供应商给出。
B.引脚表面涂层为银的元器件禁止选用。在必须选用的情况下,应要求供应商改变引脚表面处理方法,可以改为纯
雾锡。
C.涂层制作工艺主要有浸渍和电镀两种方法,两种方法都是可选的,有些电镀涂层在电镀后还要进行回流(或叫熔
4. 工艺要求内容
4.1. 元器件管脚表面涂层要求 本项对表面贴装与插装元器件的要求相同。
4.1.1. 纯锡表面涂层和镀金涂层(必须有镍阻挡层)为常用的元器件引脚表面处理方式,优选。表 1 列举了常见的引 脚涂层及厚度要求;
4.1.2. 有引线的 SMD 和集成电路器件,引脚线金属材料要为铜、铜合金(不允许含锌)、可伐合金、42 合金材料,表面 合金涂镀均匀,厚度符合表 1 要求;
7)、采用镍或银底层时,为了确保可焊性贮存期限,雾锡的厚度最少应达到 2μm。使用镍底层的元件,无孔镍的厚
度最少为 0.5μm。使用银底层的元件,银的厚度最少为 2μm。
4.2. 表面贴装器件封装
4.2.1. 器件资料中应说明基体材料,以便全面地了解器件的工艺性,常见的用于 IC 器件封装的基体材料见表 3。
是 12~16ppm/℃。 4.2.3. 器件资料中应说明引线及引线框架材料,以便全面地了解器件的工艺性。用于制作引线框架和相关零件的金属
材料主要有(不限于)可伐合金 KAVOR(也称铁镍钴合金,相当于 GB 4J29,ASTM F15,UNS K94610);KOVAR 为 含镍 29%,钴 17%的硬玻璃铁基封接合金、铁镍合金 4J42、铜、铜铁合金等。 4.2.4. 器件资料中应说明外引线涂层及涂层制作工艺。 封装遵循的标准不同,元器件的封装尺寸可能会有所不同,常用的关于封装的几个世界标准机构有 EIA、JEDEC、IPC、 MIL-STD(美国),IECQ(欧洲),EIAJ(日本),供应商需提供元器件封装尺寸所遵循的标准,其中 EIAJ 多采用公制尺 寸封装,其余标准多采用英制尺寸封装,选择按 EIAJ 标准封装的器件需要注意正确选取相应的焊盘库。 4.3. 表面贴装器件的共面度要求 共面度定义:以零件的三个最低的引脚形成的平面为基准面,其余的引脚与之比较而得到的最大偏差。 4.3.1. 表贴器件共面度要求小于 0.10mm。 4.3.2. 引脚间距(Pitch)小于 1.0mm 的 uBGA/CSP,共面度要求小于 0.10mm。 4.3.3. 引脚间距(Pitch)小于 0.5mm 的表贴接插件,共面度要求小于 0.05mm,其余表贴接插件共面度要求小于 0.10mm。 4.3.4. LCCC、QFN、BCC 封装的底面及焊端的共面度要求小于 0.10mm。 4.4. 引脚要求 为增强焊接效果,器件选用时,应选用焊端侧面有引脚的元件,禁止选用只有底部焊端器件.如下图:
3)、采用 Sn4Ag 或 Sn/Ag/Cu 热浸焊时是一种比较有效的方法。