浙江聚龙石油化工有限公司年产45万吨丙烯项目
年产万吨丙烯酸及丙烯酸酯扩建项目环境影响报告书
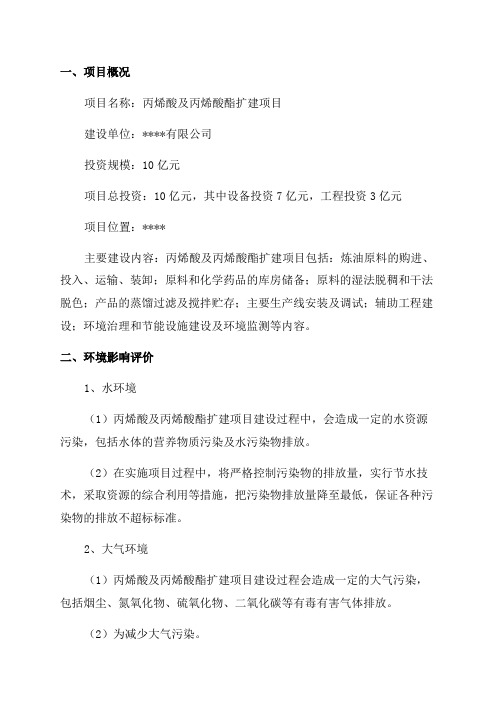
一、项目概况
项目名称:丙烯酸及丙烯酸酯扩建项目
建设单位:****有限公司
投资规模:10亿元
项目总投资:10亿元,其中设备投资7亿元,工程投资3亿元
项目位置:****
主要建设内容:丙烯酸及丙烯酸酯扩建项目包括:炼油原料的购进、投入、运输、装卸;原料和化学药品的库房储备;原料的湿法脱稠和干法脱色;产品的蒸馏过滤及搅拌贮存;主要生产线安装及调试;辅助工程建设;环境治理和节能设施建设及环境监测等内容。
二、环境影响评价
1、水环境
(1)丙烯酸及丙烯酸酯扩建项目建设过程中,会造成一定的水资源污染,包括水体的营养物质污染及水污染物排放。
(2)在实施项目过程中,将严格控制污染物的排放量,实行节水技术,采取资源的综合利用等措施,把污染物排放量降至最低,保证各种污染物的排放不超标标准。
2、大气环境
(1)丙烯酸及丙烯酸酯扩建项目建设过程会造成一定的大气污染,包括烟尘、氮氧化物、硫氧化物、二氧化碳等有毒有害气体排放。
(2)为减少大气污染。
福建省工业和信息化厅关于福州万景石化有限公司年产丙烷脱氢制丙烯90万吨项目节能报告的审查意见

福建省工业和信息化厅关于福州万景石化有限公司年产丙烷脱氢制丙烯90万吨项目节能报告的审查意见文章属性•【制定机关】福建省工业和信息化厅•【公布日期】2022.02.14•【字号】闽工信行政服务〔2022〕57号•【施行日期】2022.02.14•【效力等级】地方规范性文件•【时效性】现行有效•【主题分类】节能管理正文福建省工业和信息化厅关于福州万景石化有限公司年产丙烷脱氢制丙烯90万吨项目节能报告的审查意见闽工信行政服务〔2022〕57号福州万景石化有限公司:你公司《关于申请福州万景石化有限公司年产丙烷脱氢制丙烯90万吨项目节能审查的请示》(福州万景石化有限公司〔2022〕001号)及有关材料收悉,项目编码2111-350181 -07-02-427601。
项目新建一套年产90万吨丙烯装置,以及厂房、配电房、空压站、给排水站、循环冷却水站、低温水站、蒸汽管廊等公用工程设施和辅助生产设施。
项目建成后将新增年产90万吨丙烯的生产能力。
根据《中华人民共和国节约能源法》第十五条和《福建省固定资产投资项目节能审查实施办法》(闽节能办〔2018〕1号)等有关法律法规,经审查,具体意见如下:一、根据你公司提供的节能报告,该项目为新建项目,内容深度符合《固定资产投资项目节能审查办法》(国家发展和改革委员会令〔2016〕第44号)第七条等相关要求。
项目采用美国LUMMUS公司Catofin催化脱氢工艺,利用固定床反应器和铬-氧化铝催化剂,采取负压操作将丙烷转化为丙烯。
项目各生产工艺技术成熟可靠,根据工艺流程的特点配备高效节能的生产设备,未采用国家明令禁止和淘汰的用能设备。
项目拟于2023年12月建成投产,项目投产后,年新增综合能源消费量1608894.09tce(当量值)、1743145.42tce(等价值),含原料用能1406610tce;其中,年消耗电力77413.98万kWh、蒸汽133640t、天然气4336.8万Nm3、原料丙烷1073136t,输出蒸汽凝液819200t、氢气41018.43t、C4+重组分45024t。
未来三年我国新建PTA项目情况

未来三年我国新建PTA项目情况
浙江逸盛石化公司150万吨/年的3号PTA生产线和江苏三房巷集团90万吨/年PTA装置将于2011年第二季度和第三季度完成建设。
中国厦门翔鹭石化公司位于福建漳州的一套200万吨/年PTA装置已于2010年初破土动工,该装置的设计产能高于先前宣布的150万吨/年。
中国桐昆集团150万吨/年PTA项目已经在2009年底获得批准,当前正处于签署建设和设备供应合同过程中。
这两家公司预计在2011年前完成装置的机械建设部分,预计在2012年上半年正式投产。
江苏恒力化纤有限公司200万吨/年PTA装置和台湾亚东石化公司200万吨/年PTA装置有望在2012年下半年分别投产。
这两家公司当前已开始项目的基础设施建设,并正在等待政府最后的批文。
中国浙江远东化纤集团120万吨/年PTA装置将于2013年完成;当前已基本完成可研,正在进行审批和融资。
石化8.5万吨年丙烷资源化利用项目9-环境影响评价报告
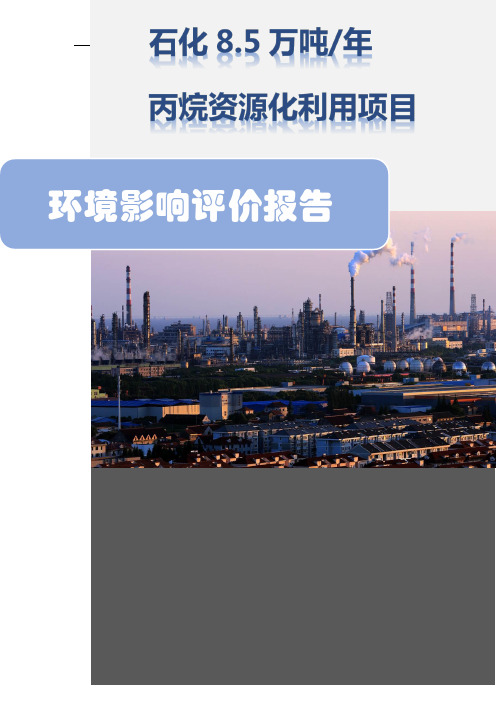
环境影响评价报告目录第一章总论 (1)1.1 编制项目由来 (1)1.2 评价目的 (1)1.3 编制依据 (2)1.3.1 环境保护法律法规及有关政策 (2)1.3.2 环境评价技术规范 (3)1.3.3 相关产业政策 (4)1.4 编制目的及原则 (4)1.4.1 编制目的 (4)1.4.2 编制原则 (5)1.5 评价的目的和原则 (5)1.5.1 评价的目的 (5)1.5.2 评价的原则及技术路线 (6)1.6 项目评价类型及重点 (7)1.7 评价标准 (8)1.7.1 环境质量标准 (8)1.7.2 污染物排放标准 (11)1.8 环境影响评价等级 (14)1.8.1 评价等级 (14)1.8.2 评价范围及主要保护目标 (17)第二章建设项目所在地自然社会环境概况 (18)2.1 自然环境概况 (18)2.1.1 地理位置 (18)2.1.2 地质、地貌 (19)2.1.3 水文地质 (19)2.1.4 气象条件 (20)2.2 社会环境概况 (21)2.2.1 经济概况 (21)2.2.2 交通状况 (21)2.2.3 基础设施 (24)2.3 区域规划 (24)2.3.1 市石化集聚区发展规划 (24)2.3.2 工业区总体规划 (26)2.3.3 园区产业链规划 (31)3.1 项目概况 (33)3.2 原料来源及产品方案 (34)3.3 工艺流程 (35)3.4 总图运输 (35)3.5 公用工程和辅助设施 (35)3.5.1 给水 (35)3.5.2 排水 (35)3.5.3 供电、通讯及报警 (36)3.5.4 储运 (36)3.6 主要生产设备 (36)第四章环境质量现状调查与评价 (37)4.1 地表水环境质量现状调查及评价 (37)4.1.1 采样点布设 (37)4.1.2 监测结果及分析 (38)4.2 大气环境现状调查及评价 (38)4.2.1 监测布点 (38)4.2.2 监测结果 (39)4.3 声环境现状调查及评价 (40)4.3.1 监测布点 (40)4.3.2 监测结果 (41)第五章项目施工期环境影响评价 (42)5.1 施工期的主要环境问题 (42)5.2 施工期大气影响分析 (42)5.2.1 施工期大气主要污染 (42)5.2.2 影响分析 (45)5.2.3 对策措施 (45)5.3 施工期声环境影响分析 (46)5.3.1 噪声污染源 (46)5.3.2 噪声影响分析 (47)5.3.3 对策措施 (48)5.4 施工期污水排放影响分析 (49)5.4.1 污水源及分布 (49)5.4.2 施工期污水排放影响 (49)5.4.3 对策措施 (50)5.5 施工期固废对环境影响分析 (50)5.5.1 固废来源 (50)5.5.2 固废影响 (50)5.5.3 对策措施 (51)5.6 施工期生态影响分析 (51)第六章环境风险评价 (52)6.1 评价等级和范围 (52)6.2 环境风险预测结果 (52)6.3 风险管理 (53)6.3.1 风险防范措施 (53)6.3.2 应急预案 (54)6.3.3 应急系统组织 (54)6.4 结论 (55)第七章环境保护措施 (56)7.1 废气 (56)7.2 废水 (57)7.2.1 排水系统设置 (57)7.2.2 处理工艺 (57)7.2.3 雨水工程设计 (61)7.3 废固 (62)7.4 噪声 (63)7.5 非正常工况污染物 (63)第八章环境影响经济损益分析 (64)8.1 概述 (64)8.2 环境保护投入费用 (64)8.3 环境保护效益 (64)8.4 环境影响经济损益分析 (65)8.5 小结 (65)第九章清洁生产分析 (66)9.1 清洁生产概述 (66)9.2 本项目清洁生产分析 (67)9.3 清洁生产的措施 (67)9.3.1 实施产品绿色设计 (67)9.3.2 实施生产全过程控制 (68)9.3.3 实施材料优化管理 (68)第十章总量控制 (69)10.1 总量控制概述 (69)10.2 总量控制建议 (69)第十一章公众参与调查 (70)11.1 公众调查的目的 (70)11.2 公众调查的必要性 (70)11.3 指导思想和基本原则 (71)11.4 公众参与调查概况 (71)11.4.1 公众参与调查方法 (71)11.4.2 公众参与的范围和对象 (71)11.4.3 公众参与调查的内容及汇总与分析 (72)11.4.4 公众参与调查问卷 (72)第十二章环境管理与监测制度分析 (74)12.1 环境管理 (74)12.1.1 环境管理机构建议 (74)12.1.2 健全各项环保制度 (74)12.1.3 加强职工教育、培训 (75)12.1.4 加强环保管理 (75)12.2 环境监测 (76)12.2.1 对建立监测制度建议 (76)12.2.2 环境评价制度 (76)12.2.3 环境监理制度 (77)第十三章结论和建议 (79)13.1 建设项目的环境可行性 (79)13.2 总结论 (79)。
新2010年浙江省重点建设项目名单
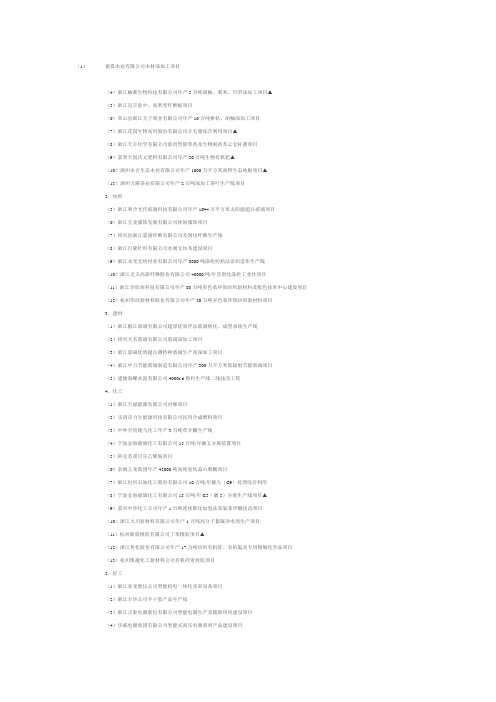
(1)德嘉木业有限公司木材深加工项目(4)浙江柚都生物科技有限公司年产5万吨胡柚、菊米、竹笋深加工项目▲(5)浙江迈尔泰中、高密度纤维板项目(6)常山县浙江天子果业有限公司年产10万吨柑桔、胡柚深加工项目(7)浙江花园生物高科股份有限公司羊毛脂综合利用项目▲(8)浙江天丰化学有限公司新剂型除草剂及生物制剂苏云金杆菌项目(9)嘉善天创沃元肥料有限公司年产20万吨生物有机肥▲(10)湖州永吉生态木业有限公司年产1000万平方米高档生态地板项目▲(13)湖州方路茶业有限公司年产2万吨深加工茶叶生产线项目2、纺织(5)浙江和合光伏玻璃科技有限公司年产1644万平方米太阳能超白玻璃项目(6)浙江宝龙服饰发展有限公司休闲服饰项目(7)绍兴县浙江嘉盛纤维有限公司差别化纤维生产线(8)浙江百隆针织有限公司水刺无纺布建设项目(9)浙江永光无纺衬业有限公司年产8000吨涤纶纺粘法非织造布生产线(10)浙江尤夫高新纤维股份有限公司40000吨/年差别化涤纶工业丝项目(11)浙江华欣高科技有限公司年产80万吨多色系环保纺织新材料及配色技术中心建设项目(12)杭州华欣新材料股份有限公司年产20万吨多色系环保纺织新材料项目3、建材(1)浙江椒江玻璃有限公司超厚优质浮法玻璃熔化、成型系统生产线(2)绍兴大名玻璃有限公司玻璃深加工项目(3)浙江嘉福优质超白薄特种玻璃生产及深加工项目(4)浙江中力节能玻璃制造有限公司年产300万平方米低辐射节能玻璃项目(5)建德海螺水泥有限公司4000t/d熟料生产线二线技改工程4、化工(1)浙江天禄能源发展公司丙烯项目(2)乐清市力生能源科技有限公司民用合成燃料项目(3)中外合资捷马化工年产3万吨草甘膦生产线(4)宁波金海德旗化工有限公司15万吨/年碳五分离装置项目(5)阿克苏诺贝尔乙烯胺项目(6)余姚王龙集团年产45000吨高纯度结晶山梨酸项目(7)浙江恒河石油化工股份有限公司10万吨/年碳九(C9)处理综合利用(8)宁波金海德旗化工有限公司15万吨/年C5(碳5)分离生产线项目▲(9)嘉兴中华化工公司年产1万吨连续催化加氢法邻氨苯甲醚技改项目(10)浙江大川新材料有限公司年产1万吨高分子絮凝净水剂生产项目(11)杭州浙晨橡胶有限公司丁苯橡胶项目▲(12)浙江传化股份有限公司年产17万吨纺织有机硅、有机氟及专用精细化学品项目(13)杭州凯越化工新材料公司有机硅密封胶项目5、轻工(1)浙江亚龙教仪公司智能机电一体化实训设备项目(2)浙江丰华公司不干胶产品生产线(3)浙江正泰电器股份有限公司智能电器生产及辅助用房建设项目(4)华威电器集团有限公司智能式高压电器系列产品建设项目(5)大好大食品有限公司休闲食品和饮料生产线项目(6)浙江中煤矿业有限公司综采设备液压支架电液阀和软启动器项目(7)省高低压电器产品质量检验中心(乐清)(8)浙江永太科技股份有限公司TFT-LCD混合液晶用单体液晶和中间体产业化项目▲(9)浙江奋飞橡塑制品有限公司年产4000万平方输送带项目(10)台州市绿田机械有限公司动力喷雾器及高压清洗机项目(11)中捷缝纫机股份有限公司无油润滑电子控制高速平缝机项目(12)星星集团智能控制冰箱生产线技改项目(13)台州市浙江新东方集团PCB液态感光阻焊高分子屏蔽材料高技术产业化示范工程(14)激光优创光能科技有限公司年产75MWP晶体太阳能电池片及组件项目(15)绍兴杰龙玻璃有限公司年产2.4亿套高档玻璃器皿项目(16)会稽山绍兴酒有限公司扩建年产4万吨黄酒生产线项目(17)浙江欧亚薄膜材料有限公司农膜、多功能膜项目(18)绍兴吉利尔科技发展有限公司年产3万台超低能耗环保湿能空调器项目(19)浙江恒鼎科技能源公司锂离子动力电池正极材料建设项目(20)常山县兴宇单晶硅棒及太阳能硅片、电池组件生产项目▲(21)浙江绿洲节能科技有限公司年产节煤助剂4万吨,节煤应用设备大、中、小格100套项目(22)维达纸业(浙江)有限公司年产8万吨高档生活用纸生产线(23)龙游国孚能源科技有限公司车用环保甲醇燃料(24)浙江明凯投资有限公司高效节能照明灯具产品建设项目▲(25)金华嘉远格隆能源有限公司200MW镉碲薄膜太阳能电池生产线(26)浙江中佳包装材料有限公司真空镀铝转移纸生产线项目(27)中外合资浙江泰科石化公司60吨/年重交沥青及配套工程(28)浙江振龙电源股份有限公司8000只/日固胶态聚合物锂离子电池产业项目▲(29)浙江超威电源公司年产800万只助力车蓄电池技改项目▲(30)浙江省机电设计研究院有限公司浙江省机电产品中试与检测基地建设项目(31)德清东大新材料照明电器有限公司年产5000万片日光灯芯片、200万只无极灯项目(32)松源机械食品饮料制造设备项目(33)杭州钱江万胜新型冷机有限公司大功率制冷压缩机生产线扩建工程(2)医药(1)温州海螺集团有限公司原料血浆及植酸酶产品生产线技改项目(2)浙江海翔药业川南分公司4-AA产品生产线(3)上虞京新药业有限公司二期建设项目(4)浙江博士达药业年产2000万盒中成药(片剂、胶囊、颗粒剂)项目▲(5)宁波鑫高益磁材有限公司生物医药高技术产业化项目7、汽车(1)平阳合信汽车零部件公司汽车刹车系统总成生产建设项目(2)温州市恒驰汽车配件有限公司汽车空调压缩机总成及刹车片项目(3)浙江海中天橡塑有限公司年产2600万条二期高性能车辆正时带固定资产投资项目▲(4)浙江银轮机械股份有限公司年产120万只轻型柴油发动机油冷器和年产1.5万只火车机车冷却器生产项目▲(5)浙江铁马汽车零部件有限公司年产1000万米车用钢丝液压软管项目▲(6)彪马集团新建5万台变速箱及1.5万台沼液沼渣清理设备项目(7)三门县浙江紫金港胶带有限公司高性能车辆传送带改造项目(8)台州浙江吉奥汽车有限公司年产20万台SUV汽车变速箱项目(9)台州本能汽车有限公司年产10万套SUV汽车车身建设项目(10)绍兴索密克有限公司年产100万套汽车转向拉杆悬架拉臂球头总成项目(11)横店集团控股有限公司年产50万套电控喷油系统建设项目(12)湖州金泰新材料有限公司年产200万件干法镀膜铝合金轮毂生产线项目8、机械(1)浙江青山控股集团有限公司不锈钢焊管建设项目(2)大众阀门有限公司水轮机流量控制阀建设项目(3)凯喜姆阀门有限公司核能阀门生产项目(4)浙江华光电力成套设备有限公司气力输灰系统建设项目(5)慎江阀门有限公司大口径液气联动阀、汽轮机主汽阀系列产品建设项目(6)温州伯威阀门成套设备有限公司气动控制阀和船舶专用阀项目(7)浙江浦大电缆有限公司电缆生产项目(8)浙江通宇园林机械生产项目(9)浙江杰克机床有限公司数控与精密外园磨床项目(10)浙江金龙电机公司以冷代热高效节能特种出口电机项目(11)诸暨市中天工业公司年产25000吨大型塑料机械配套哥林柱产品生产线项目(12)万丰奥特控股集团年产200套铸造设备自动化单元产业化项目▲(13)浙江乐丰电器有限公司年产2000万台串励电机、汽车电机扩大出口项目(14)韵升控股集团有限公司综合项目(15)浙江新元焊材有限公司年产20万吨气保焊丝生产线(16)横店集团控股有限公司年产20万台工业特种阀建设项目(17)中国南龙集团高速低噪声数控机床高技术产业化项目(18)浙江莱茵电梯有限公司电梯制造及关键零部件加工▲(19)浙江富钢金属制品有限公司年产25万吨大型核电专用阀门和大型船舶配件项目▲(20)上海电器科学研究所湖州电器(机)检测中心及产业基地项目▲(21)浙江振兴阿祥集团有限公司高效节能紧凑式换热器及数控重型机械配件生产线项目(22)浙江净野科技有限公司年产风力发电机组12333台生产项目(23)杭州双华科技有限公司管状电机项目(24)美欣达集团有限公司年产33台(套)环保机械设备生产线项目(25)浙江力龙液压公司高压大流量液压件项目(26)杭州联源重工有限公司电站设备核心部件项目▲(27)杭州富生电器有限公司高效节能感应电机及专用设备生产线(28)浙江舜飞机电设备有限公司年产6台水轮发电机组及配套产品生产项目9、信息产业(1)温州一立高新技术有限公司高新技术纳米电子墨水显示器项目(2)浙江新宏电子实业有限公司ITO玻璃、集成电路建设项目(3)天通浙江精电科技有限公司年新增1720万套高速宽带及高清数字电视网络接入单元产品生产线技改项目(4)天通浙江精电科技有限公司年新增20万套通信网络基站产品技改项目▲(5)国家兵器工业集团上海大晨光电科技有限公司LED芯片及产业化项目(6)湖州南方光通信公司光通信器件生产线项目(7)富通集团与日本住友电工合资生产光纤及光纤预制棒项目▲(8)嘉兴斯达微电子有限公司IGBT芯片和模块产业化项目10、船舶(1)舟山长白岛海洋工程装备和船舶制造项目(2)苍南北关岛船舶修理厂工程(3)温州中欧船业有限公司7万吨散货船船台船坞项目11、其他(1)上海交大嘉兴科技园二期工程▲(2)嘉兴市实达投资有限公司嘉兴都市型工业园区建设项目(3)温州宏阳铜业有限公司精密铜合金带生产线项目(4)浙江健力企业公司年产50万吨石油钻杆及石油专用管生产线(5)浙江嵊州一百岁置业有限公司标准厂房建设项目(6)绍兴万成金属薄板有限公司年产28万吨热镀锌钢板项目(7)浙江日盛公司炭纤维型材生产线(8)盛基工业(嘉善)有限公司扩建工程(9)浙江煜辉阳光能源公司太阳能电池板项目(10)浙江安吉金冶电力铁路型材有限公司年产6万吨电力铁塔、3万吨铁路附件生产线项目▲(11)浙江久立特材科技股份有限公司年产3000吨核电站核蒸汽发生器等用镍基合金无缝管项目(3))中钢集团新型材料(浙江)有限公司年产5000吨新型石墨材料生产项目(13)浙江恒立数控科技股份有限公司年产200条精密数控金属板材剪切生产线生产项目(14)浙江直立汽配有限公司年产20000吨大型工程机械传动链条压板精加工项目(15)浙江久立集团电站配套辅件及大口径油气输送管项目(16)浙江栋梁新材股份有限公司年产3万吨高精度铝板卷及铝箔坯料生产线项目(17)浙江东南铝业集团年产十五万吨高强度铝合金板材、箔材项目(18)浙江巨力通薄板有限公司年产100万吨车用薄板生产项目(19)“山海协作”项目四、现代服务业项目(共5项)产业项目(共10项)1、宁波钢铁有限公司钢铁项目2、镇海炼化乙烯工程3、建材项目○(1)长兴玻璃有限公司超厚优质浮法玻璃生产线(2)浙江平湖玻璃有限公司日产1000吨优质超厚浮法玻璃生产线建设项目4、轻工、纺织项目○(1)绍兴新星印染集团数控针织服装建设项目(2)苍南县新雅纸塑包装印刷工程(3)浙江新聚龙化纤集团高仿真化纤面料项目(4)浙江明月化纤有限公司引进包覆纱生产线项目(5)温州市瑞新皮草有限公司新建软件家私制造项目(6)森马集团有限公司休闲服生产线项目(7)格瑞斯鞋业公司年产职业皮鞋生产线项目(8)温州天成纺织有限公司纤维纱线生产线项目(9)宁波白板纸三期项目(10)浙江中烟工业公司杭州制造部易地技改项目○(11)永义纺织(湖州)有限公司纺织项目5、机电项目○(1)杭州制氧机集团有限公司制造基地迁扩建项目(2)义乌东方缝纫设备公司特种缝纫设备生产线○(3)浙江大元泵业有限公司新建年产100万台汽车空调压缩机项目(4)浙江新柴控股集团有限公司节能环保型柴油机建设项目(5)海宁西子联合控股有限公司盾构设备制造项目(6)华为杭州二期生产基地及研发(配套)中心工程○(7)海信(浙江)空调有限公司节能变频空调器生产线○(8)杭州中新实业有限公司新建电脑羊毛织机设备、纺织CAD、电脑弹簧项目○(9)中兴杭州手机配套产业化基地项目○(10)华立“三板”项目(11)浙江佳力科技股份有限公司大型风力发电设备部件制造项目△(12)横店集团控股有限公司年产3亿只高效电子节能灯基本建设项目△(13)东方电气新能源设备(杭州)有限公司直驱式永磁风力发电机组及潮汐发电机组生产项目△(14)浙江三一装备有限公司履带起重机产品建设项目△(15)浙江佳邦数控机床有限公司年产300台大中型数控机床及零部件制造项目△(16)宁波力隆机电有限公司住宅电梯及电梯部件技改项目△(17)浙江富春江水电设备股份有限公司大型混流式水轮发电机组及大型抽水蓄能发电机组国产化制造项目6、医药、化工项目○(1)杭州海正药用植物有限公司制剂高技术项目○(2)江山市双氧水有限公司年产20万吨钯触媒双氧水生产线项目7、先进制造业(含技改)项目(1)杭钢集团20万立方米煤气柜及配套煤场项目○(2)通宇缝纫机股份有限公司特种工业缝纫机和电脑绣花机项目○(3)浙江新安化工集团有机硅项目(4)温州中科新能源科技有限公司年产10万吨生物柴油能源高科技项目8、外资项目(1)浙江巴贝领带有限公司高档面料项目○(2)上虞市浙江华孚色纺有限公司特种纤维面料项目○(3)浙江财纳福诺木业有限公司地板生产项目(4)绍兴县浙江华宇纸业有限公司年产30万吨白板纸项目(5)中外合资浙江荣成纸业有限公司年产300万吨高档箱板纸项目9、汽车及零部件项目○(1)新昌县恒通铝业制造有限公司汽摩配轻合金精密部件产品固定资产投资项目○(2)绍兴县轮胎模具有限公司年产3000套子午线轮胎模具建设项目10、其它项目(1)浙江善好酒业集团有限公司善好酒异地扩建工程(2)义乌市名媛饰品有限公司水晶钻石生产线○(3)浙江塔牌酒厂扩建项目○(4)浙江浙大佳能康生物技术有限公司肠道高能营养食品扩建项目(5)中远船务工程集团有限公司舟山分公司中远船务舟山修船基地(二期、三期工程)○(6)浙江久立集团电站配套辅件及大口径油气输送管项目(7)大鲵(娃娃鱼)工厂化繁育与养殖高技术产业示范工程(8)浙江正达船舶修造有限公司船舶修造项目(9)东邦修造船公司大衢修船基地项目(10)杭州高新区软件及服务外包生产基地(11)辻产业重工造船项目五、1、城市引、供水项目(1)杭州萧山东部区域供水工程(江东水厂一期)(2)杭州市钱塘江引水入城工程○(3)宁波市大工业供水工程○(3)白溪引水象山供水工程○(4)周公宅(皎口)水库引水及城市供水环网工程(5)奉化市溪口自来水厂(6)奉化第二水厂工程(7)温州西向水厂工程(8)平阳县城区片珊溪引供水工程○(9)平湖市广陈水厂工程○(10)海盐县城乡供水一期工程○(11)嘉善城乡供水一期工程(12)东阳市第二自来水厂工程○(13)开化县城市供水工程(14)常山县城乡供水一体化一期工程(15)舟山六横海水淡化一期工程○(16)台州供水二期工程(17)三门县城乡供水工程△(18)临海杜桥西湖水厂工程○(19)松阳县松古平原供水工程一期2、城市污水处理项目(1)杭州市七格污水处理厂三期工程(2)富阳市大源镇污水处理和再生水利用工程(3)宁波江南污水处理厂及配套管网工程○(4)慈溪市域污水治理工程(5)温州市东片排污主管网工程(6)温州市西片污水处理厂工程(7)嘉兴市污水处理二期工程(8)平湖市东片污水处理一期工程○(9)海盐县西片污水处理工程△(10)桐乡市污水处理尾水外排工程(11)绍兴污水处理三期工程(12)金华市金东区污水处理工程(一期)(13)金华婺城新区污水处理一期工程(14)金华市金西污水处理一期工程(15)义乌市污水处理工程二期○(16)浦江城市污水处理工程(二期)○(17)兰溪市污水处理工程(18)台州路桥区污水处理二期工程(19)浙海2万吨/日油污水处理与120万吨/年废油净化项目(20)海宁尖山新区污水处理工程(21)仙居县城市污水处理工程(22)椒江污水处理二期扩建工程(23)三门县城市污水处理工程△(24)丽水市水阁污水处理厂○(25)嘉善县杨庙镇污水管网工程(接入洪溪镇污水处理厂)31、城市污水处理项目(1)衢州市城东污水处理厂工程(2)龙游城北污水处理厂(一阶段)工程△(3)杭州市城西(蒋村)污水处理厂工程2△(1)德清县乾元水厂21、建材项目(1)浙江椒江玻璃有限公司超厚优质浮法玻璃熔化、成型系统生产线(2)浙江嘉福优质超白薄特种玻璃生产及深加工项目(3)绍兴县砂加气混凝土砌块生产线项目(4)浙江迈尔泰中、高密度纤维板项目(5)浙江和合光伏玻璃科技有限公司年产1644万平方米太阳能超白玻璃项目2、轻工、纺织项目(1)温州雪之梦集团有限公司年产2500万件(套)休闲服生产线项目(2)桐昆集团恒通公司年产40万吨差别化纤维项目(3)杭州华欣新材料股份有限公司年产20万吨多色系环保纺织新材料项目(4)盛基工业(嘉善)有限公司休闲制品扩建工程(5)维达纸业(浙江)有限公司年产8万吨高档生活用纸生产线(6)浙江华欣高科技有限公司年产80万吨多色系环保纺织新材料及配色技术中心建设项目(7)绍兴杰龙玻璃有限公司年产2.4亿套高档玻璃器皿项目(8)新天龙集团有限公司年产26000万米高档织物面料后整理搬迁技改项目3、机械、电子项目(1)绍兴吉利尔科技发展有限公司年产3万台超低能耗环保湿能空调器项目(2)浙江中煤矿业有限公司综采设备液压支架电液阀和软启动器项目(3)浙江乐丰电器有限公司年产2000万台串励电机、汽车电机扩大出口项目(4)华威电器集团有限公司智能式高压电器系列产品建设项目(5)中国南龙集团高速低噪声数控机床高技术产业化项目(6)浙江正泰电器股份有限公司智能电器生产及辅助用房建设项目(7)湖州南方光通信公司光通信器件生产线项目(8)浙江舜飞机电设备有限公司年产6台水轮发电机组及配套产品生产项目(9)横店集团控股有限公司年产50万套电控喷油系统建设项目(10)横店集团控股有限公司年产20万台工业特种阀建设项目(11)美欣达集团有限公司年产33台(套)环保机械设备生产线项目(12)浙江净野科技有限公司年产风力发电机组12333台生产项目(13)浙江振兴阿祥集团有限公司高效节能紧凑式换热器及数控重型机械配件生产线项目(14)浙江直立汽配有限公司年产20000吨大型工程机械传动链条压板精加工项目(15)浙江恒立数控科技股份有限公司年产200条精密数控金属板材剪切生产线生产项目4、化工、医药项目(1)浙江洪太生物工程有限公司紫苏系列产品生产项目(2)浙江天丰化学有限公司新剂型除草剂及生物制剂苏云金杆菌项目(3)上虞京新药业有限公司二期建设项目(4)浙江天禄能源发展公司丙烯项目(5)浙江传化股份有限公司年产17万吨纺织有机硅、有机氟及专用精细化学品项目(6)龙游国孚能源科技有限公司车用环保甲醇燃料(7)浙江大川新材料有限公司年产1万吨高分子絮凝净水剂生产项目5、农产品深加工项目(1)建德市农产品深加工项目(年产果蔬食品26000吨和100万平方米竹地板)(2)温州大丰农业中心(3)诸暨市农产品深加工建设项目(4)常山县浙江天子果业有限公司年产10万吨柑桔、胡柚深加工项目(5)湖州方路茶业有限公司年产2万吨深加工茶叶生产线项目(1)永康星月1号摩托车发动机高技术产业化项目(2)台州市浙江新东方集团PCB液态感光阻焊高分子屏蔽材料高技术产业化示范工程(3)浙江清华长三角研究院建设工程(4)乐清市力生能源科技有限公司民用合成燃料项目(5)浙南信息科技公司激光高能彩色打印机项目(6)浙江省机电设计研究院有限公司浙江省机电产品中试与检测基地建设项目(7)浙江海翔药业川南分公司4—AA产品生产线7、重大外资项目(1)绍兴县浙江嘉盛纤维有限公司差别化纤维生产线(2)浙江思源纺织有限公司高档织物辅料项目(3)浦江亚华水钻技术有限公司CNT水钻制造项目(4)浙江伊美薄膜工业集团非PVC医用复合膜生产线项目(5)浙江中佳包装材料有限公司真空镀铝转移纸生产线项目(6)德嘉木业有限公司木材深加工项目(7)温州伯威阀门成套设备有限公司气动控制阀和船舶专用阀项目(8)温州一立高新技术有限公司高新技术纳米电子墨水显示器项目(9)浙江宝龙服饰发展有限公司休闲服饰项目(10)浙江伟龙包装科技有限公司高科技包装材料项目(11)浙江通宇园林机械生产项目(12)舟山长白岛海洋工程装备和船舶制造项目(13)嘉兴帝人化成聚碳酸酯有限公司17.7万吨PC项目(14)杭州凯越化工新材料公司有机硅密封胶项目(15)中外合资浙江泰科石化公司60吨/年重交沥青及配套工程(16)中外合资捷马化工年产3万吨草甘膦生产线(17)浙江欧亚薄膜材料有限公司农膜、多功能膜项目8、先进制造业(含技术改造)项目(1)浙江亚龙教仪公司智能机电一体化实训设备项目(2)浙江华光电力成套设备有限公司气力输灰系统建设项目(3)慎江阀门有限公司大口径液气联动阀、汽轮机主汽阀系列产品建设项目(4)星星集团智能控制冰箱生产线技改项目(5)温州宝峰纺织机械有限公司新型纺织机械技改项目(6)温州海螺集团有限公司原料血浆及植酸酶产品生产线技改项目(7)浙江青山控股集团有限公司不锈钢焊管建设项目(8)凯喜姆阀门有限公司核能阀门生产项目(9)大众阀门有限公司水轮机流量控制阀建设项目(10)浙江新宏电子实业有限公司ITO玻璃、集成电路建设项目(11)浙江百隆针织有限公司水刺无纺布建设项目(12)台州市绿田机械有限公司动力喷雾器及高压清洗机项目(13)中捷缝纫机股份有限公司无油润滑电子控制高速平缝机项目(14)浙江杰克机床有限公司数控与精密外园磨床项目(15)宁波海天科技公司年产2000台全电动注塑机和专用液压注塑机项目(16)杭州钱江万胜新型冷机有限公司大功率制冷压缩机生产线扩建工程(17)浙江煜辉阳光能源公司太阳能电池板项目(18)国家兵器工业集团上海大晨光电科技有限公司LED芯片及产业化项目(19)德清东大新材料照明电器有限公司年产5000万片日光灯芯片、200万只无极灯项目9、汽车及零部件制造业(1)台州浙江吉奥汽车有限公司年产20万台SUV汽车变速箱项目(2)台州本能汽车有限公司年产10万套SUV汽车车身建设项目(3)平阳合信汽车零部件公司汽车刹车系统总成生产建设项目(4)温州市恒驰汽车配件有限公司汽车空调压缩机总成及刹车片项目(5)衢州青年传动系统制造有限公司车桥及制动系统生产建设项目(6)绍兴索密克有限公司年产100万套汽车转向拉杆悬架拉臂球头总成项目(7)浙江巨力通薄板有限公司年产100万吨车用薄板生产项目(8)湖州金泰新材料有限公司年产200万件干法镀膜铝合金轮毂生产线项目10、其它产业项目(1)温州宏阳铜业有限公司精密铜合金带生产线项目(2)浙江恒鼎科技能源公司锂离子动力电池正极材料建设项目(3)浙江日盛公司炭纤维型材生产线(4)浙江浦大电缆有限公司电缆生产项目(5)省高低压电器产品质量检验中心(乐清)(6)浙江恒耀实业有限公司年产90万台运动器材生产项目(7)慈溪市年产150万箱局域网数据电缆技改项目(8)大好大食品有限公司休闲食品和饮料生产线项目(9)浙江栋梁新材股份有限公司年产3万吨高精度铝板卷及铝箔坯料生产线项目(10)温州中发再生纺织综合利用工程(11)浙江丰华公司不干胶产品生产线(12)浙江环益资源利用有限公司有色金属废弃物资源化利用中心(13)杭州汽轮东风船舶制造有限公司整体迁建项目(14)温州中欧船业有限公司7万吨散货船船台船坞项目(15)浙江新元焊材有限公司年产20万吨气保焊丝生产线(16)浙江金西园科技有限公司改良西门子法年产1500吨多晶硅项目(17)中钢集团新型材料(浙江)有限公司年产5000吨新型石墨材料生产项目(18)绍兴万成金属薄板有限公司年产28万吨热镀锌钢板项目(19)激光优创光能科技有限公司年产75MWP晶体太阳能电池片及组件项目(20)宁波海伦乐器有限公司钢琴技改项目(21)宁波韵升控股集团有限公司综合项目(22)会稽山绍兴酒有限公司扩建年产4万吨黄酒生产线项目(23)嘉兴市实达投资有限公司嘉兴都市型工业园区建设项目(24)浙江嵊州一百岁置业有限公司标准厂房建设项目。
“有效防止火灾最重要的不是禁用某些材料,而是要高度重视阻燃工作”中外合作推动溴阻燃剂科学发展
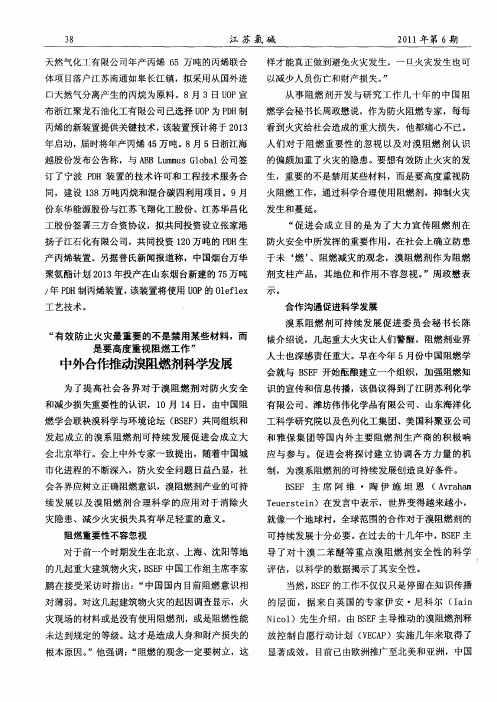
中外合作推动溴阻燃剂科学发展
根 本 原因 。 ”他 强调 :“ 阻燃 的观念 一定 要树 立 ,这
导 了对十溴二苯醚等重点溴阻燃剂安全性 的科学
评估 , 以科 学 的数据 揭示 了其 安全 性 。
当然, S F的工作不仅仅只是停留在知识传播 BE
的层面 ,据 来 自 国的专家伊 安 ・ 英 尼科尔 ( a n 1 i
N . 06 D C 2 1 E. 01 3 9
也 已经 开 始该 计 划 。“ 学 知 识非 常重 要 ,但 更 重 科
黑西哥化学公司将扩产 P C V
由于预期拉美地区需求仍将保持较高增速,墨
西 哥 聚 氯 乙烯 生产 商 墨 西 哥 化 学 公 司近 日表 示 将 扩大 P C产 能 ,到 2 1 使 PC生产 能力 再增 4 V 04年 V 6
样 才 能真正 做 到避 免 火灾发 生 ,一 旦火 灾发 生也 可
以减少 人员 伤亡和 财产 损失 。 ” 从 事 阻燃 剂 开发 与 研 究 工 作 几 十 年 的 中 国 阻
燃 学会秘 书 长周政 懋说 ,作 为防火 阻燃 专家 ,每每 看 到火 灾给 社会造 成 的重大损 失 ,他 都痛心 不 已。 人 们 对 于 阻燃 重 要 性 的 忽视 以及 对 溴 阻燃 剂 认 识 的偏颇 加重 了火 灾 的隐患 。要想 有效 防止 火 灾 的发
Nc1 io )先生介绍,由B E 主导推动的溴阻燃剂释 SF 放控制 自 愿行动计划 ( EA )实施几年来取得 了 V CP
XX年生产28万吨丙烯联产36万吨酚酮项目环境影响评价报告书

目录第1章总论 (1)1.1项目背景 (1)1.2评价目的及原则 (1)1.2.1评价目的及意义 (1)1.2.2编制原则 (2)1.3编制依据 (3)1.3.1国家有关法律和条例 (3)1.3.2评价技术导则及规范 (4)1.4评价的重点和生产制约因素 (5)1.4.1评价的重点 (5)1.4.2制约因素 (5)1.5评价范围 (6)1.6环境保护目标 (7)1.7评价工作等级 (8)1.7.1地表水评价等级 (8)1.7.2空气环境评价等级 (8)1.7.3噪声评价等级 (9)1.7.4地下水环境评价等级 (9)1.7.5风险评价等级 (9)1.8评价标准 (10)1.8.1环境质量标准 (10)1.9污染物排放标准 (13)1.9.1废气污染物排放标准 (13)1.9.2废水污染物排放标准 (14)1.9.3噪声评价标准 (14)第2章项目所在地自然社会环境概况 (16)2.1自然环境概况 (16)2.1.1地理位置与交通 (16)2.1.2地形、地质、地貌 (18)2.1.3气候、气象 (18)2.1.4水文 (19)2.1.5矿产资源 (19)2.2用电条件 (20)2.3社会环境概况 (21)2.3.1行政区划与人口 (21)2.3.2厂区规划产业布局概况 (22)2.4区域规划 (22)2.5项目工程依托设施概况 (23)第3章建设项目概况 (24)3.1基本情况 (24)3.2建设内容 (24)3.3产品质量指标及原料理化性质 (24)3.4总平面布置及合理性分析 (25)3.5主要原辅料及动力消耗 (25)3.5.1项目原辅材料消耗 (25)3.5.2项目能源及资源消耗 (25)3.6公用工程 (26)3.6.1给水 (26)3.6.2排水 (26)3.6.3供电、通讯及报警 (26)3.6.4供热 (26)3.6.5储运 (26)3.7主要生产设备 (26)第4章污染源分析 (27)4.1主要污染物与污染源 (27)4.2环境治理措施 (28)4.2.1废气 (28)4.2.2废液 (31)4.2.3废渣 (34)4.2.3.1废渣 (34)4.2.4噪声 (36)第5章总量控制 (38)5.1总量控制因子 (38)5.2总量控制建议 (38)第6章环境风险评价 (39)6.1环境评价概述 (39)6.2废气污染源及污染物 (39)6.3废水污染源及污染物 (40)6.4固体废物污染源分析 (40)6.5噪声污染源 (41)6.6环境影响因素识别 (41)6.6.1大气环境影响因子的筛选 (41)6.6.2声学环境影响因子的筛选 (41)6.6.3地表水环境影响分析 (42)第7章总量控制 (43)7.1总量控制原则 (43)7.2总量控制因子 (43)7.3总量控制建议 (43)第8章环境质量现状评价 (44)8.1环境空气质量现状评价 (44)8.1.1现状监测 (44) (45)8.2.1评价范围及评价参数 (45)8.2.2评价方法 (45)8.2.3评价标准 (46)8.3现状评价结果 (46)8.4现状评价结论 (47)8.5地表水环境现状调查与评价 (47)8.6声环境质量现状评价 (47)8.6.1现状评价 (47)8.6.2评价方法 (48)8.6.3现状评价结论及分析 (48)第9章施工期环境影响分析 (49)9.1概述 (49)9.2施工期的主要环境问题 (49)9.3施工期环境空气影响分析 (49)9.3.1施工期主要大气污染源和污染物 (49)9.3.2对策措施 (50)9.4施工期声环境影响分析 (51)9.4.1噪声污染源强 (51)9.4.2对策措施 (51)9.5施工期污水排放影响分析 (52)9.5.1污水源强及分布 (52)9.5.2对策措施 (53)9.6施工期固废对环境影响分析 (53)9.6.1固废来源 (53)9.6.2对策措施 (54)第10章环境风险分析 (55)10.1环境风险分析评价 (55) (55)10.2.1发生风险的原因 (55)10.2.2风险识别范围 (55)10.2.3生产设施风险识别 (56)10.2.4物质危险性识别 (56)10.2.5风险识别 (58)10.2.6辨识结果 (58)10.2.7环境风险评价工作等级的确定 (59)10.3环境风险防范 (61)10.4应急预案 (61)第11章清洁生产在本项目中的应用 (63)11.1概述 (63)11.2本项目清洁生产分析 (64)11.3清洁生产的措施 (64)11.3.1实施产品绿色设计 (64)11.3.2实施总量和集中控制 (64)11.3.3实施生产全过程控制 (64)11.3.4企业清洁生产管理分析 (64)11.4清洁生产分析结论 (65)11.5持续清洁生产建议 (65)第12章环境管理与监测制度分析 (66)12.1环境管理 (66)12.2环境监测计划 (66)第13章环境影响经济损益分析 (68)13.1概述 (68)13.2环境保护效益 (68)13.3环境影响经济损益分析 (68)13.4小结 (68)第14章公众参与 (70)14.1公众参与目的 (70)14.2公众调查的必要性 (70)14.3指导思想和基本原则 (71)14.4公众参与调查概况 (71)14.4.1公众参与调查方法 (71)14.4.2公众参与的范围和对象 (71)14.4.3公众参与调查的内容及汇总与分析 (72)14.4.4公众参与调查问卷 (72)第15章结论和建议 (74)15.1项目建设的环境可行性 (74)15.2建议措施 (74)15.3总结论 (74)第1章总论1.1项目背景我国丙烷的来源日益增多,但丙烷的利用方式相对单一,在国内一般是作为燃料燃烧,不仅造成资源浪费,而且在不完全燃烧的情况下会生成污染大气的CO。
年产万吨丙烯酸及丙烯酸酯扩建项目环境影响报告书

目录前言丙烯酸(AA)及丙烯酸酯类(AE) 工业为民生基础工业极重要的一环,日常生活中处处与其发生密不可分的关系,工业发达国家均将丙烯酸及丙烯酸酯工业列为工业发展的重要项目之一,合成纤维、树脂、乳化油漆、水性涂料、高吸水性树脂等均为丙烯酸及丙烯酸酯工业之下游产业。
其次丙烯酸及丙烯酸酯制品在工程、纤维、建筑及民生工业领域里亦为不可或缺的产品,如丙烯酸乳胶建筑涂料、密封胶等,丙烯酸酯类建筑乳液产品因性能优异和对环境友好,可用作内、外墙涂料,深受用户青睐。
根据预测,综上所述,预计2010年我国丙烯酸及酯需求量将达116万吨,同时丙烯酸酯需求仍将以每年5%的速度增长。
宁波市位于中国大陆海岸线中部,经济发达的长江三角洲南翼,毗邻上海、杭州,是中国十大工业城市之一,被国务院定位为重要的化工、能源、原材料及产品生产基地,是国家化工项目的重点投资区域和出口贸易加工区。
全市已形成以石油及精细化工、纺织服装、机械、电子、冶金、食品、医药等各行业协调发展的工业体系。
宁波市利用其沿海北仑深水良港的有利条件,在宁波经济技术开发区规划建设发展需要大进大出的临港性工业,目前已有多家大型化工生产厂家在此投资,已经形成台塑工业园区、青峙化工区和大榭化工专区组成的大型化工基地。
台塑丙烯酸酯(宁波)有限公司坐落于宁波经济技术开发区内的台塑工业园区内,是由属于台塑关系企业的台湾塑胶工业(开曼)股份有限公司投资组建,为外(台)商独资企业,注册资本15357万美元,主要经营范围是丙烯酸(AA)及其酯类(AE)的生产销售,是台塑关系企业宁波石化项目中的一个子项目,为30个系列工程项目之一。
该公司现有规模为年产丙烯酸16万吨和丙烯酸酯20万吨,工程于2003年8月开工建设,2006年1月建成,2006年2月申请进行了试生产,并于2008年8月通过了环保竣工验收。
为满足日益增长的国内对丙烯酸及酯类的市场需求,提升企业竞争力,台塑丙烯酸酯(宁波)有限公司拟投资25620.9万美元,于现有厂区预留用地建设实施“年产16/20万吨丙烯酸及丙烯酸酯扩建项目”,本项目年产丙烯酸16万吨和丙烯酸酯20万吨,待项目建设完成后,台塑丙烯酸酯(宁波)有限公司将会形成年产丙烯酸32万吨和丙烯酸酯40万吨的生产规模。
35万吨丙烯项目建议书

天茂实业集团股份有限公司年产3.5万吨丙烯技改工程项目建议书天茂实业集团股份有限公司技术部二零一三年七月目录1 总论 (2)2 市场分析 (7)3产品方案及生产规模 (12)4 工艺技术 (13)5原料、产品规格及质量指标 (17)6 建厂条件和选址 (19)7 总图运输及土建 (21)8节能、节水 (25)9消防 (27)10环境保护 (30)11劳动安全与工业卫生 (32)12 投资估算及资金筹措 (34)13财务评价及结论 (36)第一章总论1.1 项目名称、建设单位名称、企业性质及法人项目名称:年产3.5万吨丙烯技改工程建设单位:天茂实业集团股份有限公司企业性质:民营1.2 建设单位基本情况天茂实业集团股份有限公司(原湖北百科药业股份有限公司,于2006年7月更名),横跨化工和医药两个产业,由新能源、合成树脂、化学原料药及医药中间体、医药制剂四个板块组成,1996年公司在深交所上市(代码:000627)。
现有总资产20.3亿元,职工1600多人,其中各类技术人员549人。
公司先后被认定为国家级高新技术企业,湖北省第一家博士后医药产业基地。
公司主要生产销售医药原料药和医药制剂以及甲醇、二甲醚、聚丙烯等化工产品。
2012公司实现销售收入77937万元。
公司目前拥有年产50万吨二甲醚、3万吨聚丙烯生产装置,医药方面拥有各类符合cGMP等国际规范的吨级规模原料药生产装置十多套,公斤级特色原料药生产装置八套。
公司的解热镇痛药在国际上已有重要影响,除目前已处于亚洲第一、世界前二的产品布洛芬外,其它解热镇痛类药包括国家二类新药奥沙普秦、四类新药右旋布洛芬、三类新药赖氨洛芬等均为国内首家开发上市,它们和布洛芬一起已批量销往国外多家著名制药公司。
公司的特色原料药盐酸格拉司琼、磷酸氟达拉滨、米力农、氟马西尼等均通过了美国FDA认证,托拉塞米原料药通过了欧洲COS认证,另还有多个原料药产品也已完成了美国DMF或欧洲EDMF的研究及编制工作,正在实施欧美药政注册。
浙江聚龙石油化工有限公司年产万吨丙烯项目模板

浙江聚龙石油化工有限公司年产45万吨丙烯项目环境影响报告书( 简写本)浙江省环境保护科学设计研究院ENVIRONMENTAL SCIENCE RESEARCH DESIGN INSTITUTE OF ZHEJIANG PROVINCE国环评证: 甲字第号二○一一年十一月一、项目概况1、项目来源丙烯是仅次于乙烯的重要有机化工基础原料, 其下游衍生物主要有: 聚丙烯、环氧丙烷、丙烯腈、丙烯酸、异丙苯/苯酚/丙酮、羰基合成醇、异丙醇等有机原料。
这些衍生物由于其自身的特性正在逐步地取代传统的材料如钢铁、木材、棉及棉制品等, 被广泛运用于基础设施和城市建设、航天和航空工业、汽车制造、家用电器、生物及医药制品等各个行业。
随着中国国民经济的发展和人民生活水平的不断提高, 其应用领域还将进一步扩大, 需求还将大幅度地提升。
长期以来, 由于受原油价格和工艺技术的制约, 丙烯供应主要来自石脑油裂解制乙烯和石油催化裂化过程的副产品。
随着近年来大部分新建的乙烯装置已不再沿用陈旧的石脑油裂解工艺转而采用乙烷直接裂解工艺, 新的乙烯装置不再代产丙烯, 从而导致丙烯产能增长严重滞后。
近年开发扩大丙烯来源的生产工艺成为热点, 其中丙烷脱氢( PDH) 制丙烯工艺最备受关注。
浙江聚龙石油化工有限公司是以浙江长江能源发展有限公司为主体投资组建的独立法人单位。
浙江长江能源发展有限公司成立于1988年, 是一家从事集液化气船舶制造、运输、仓储、批发, 销售的综合企业。
浙江聚龙石油化工有限公司拟投资16.3亿元, 引进美国UOP公司Oleflex技术在平湖独山港区新建一套丙烷脱氢( PDH) 装置, 实施年产45万吨丙烯项目。
2、项目基本情况建设项目名称: 浙江聚龙石油化工有限公司年产45万吨丙烯项目建设项目性质: 新建建设地点: 浙江省平湖独山港区一期内, 项目北临老海塘路, 南侧为新海塘路及杭州湾, 西侧为散货物流区, 东侧是规划工业用地, 总占地243.34亩。
中国聚烯烃装置产能及工艺
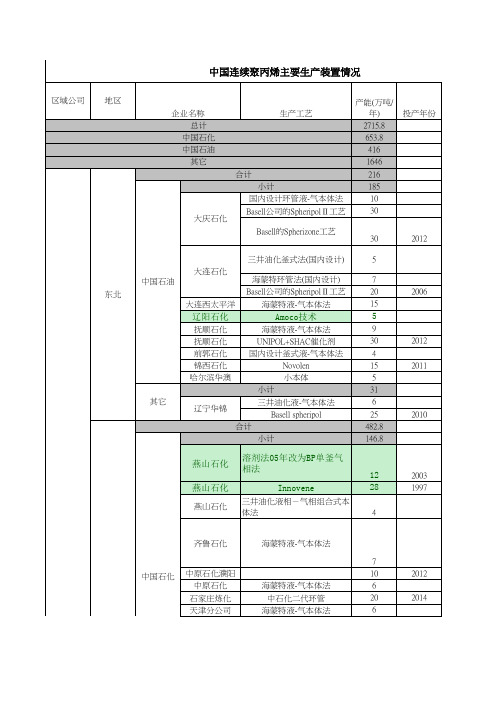
Novolen工艺
合计
小计
35
2016
27
2013
30
30
2015
30
30
35
2015
40
2014
40
2016
30
2013
45
2008
547.5
273.5
广州分公司 广州分公司
茂名分公司
三井HYPOL 中石化二代环管
Innovene
14
20
2013
30
2014
中国石化
茂名分公司
海蒙特
17
பைடு நூலகம்国产环管二代
国内设计
0.2 0.5 0.75 2 1 0.7 0.5 0.45 0.2 0.5 3 4.5 1.07 1.2 7 6 39.97 2
42
43 44 45 46 47 48
49 50 51 52 53 54 东北 55
56
57
58 59 60 61 62
抚顺石油化 工公司石油 二厂
锦西炼达石 油化工有限 公司
J700 纤维料BH,,S900
T38F
1PP装置;2PP装置F800E; 3PP装置M2600R,Y1600。 K8303 T30S,F280Z
民营企业 拟建以煤化工甲醇制
丙烯
A线F400H,J641,B线 CJS700
EPC30R,HHP6 T30S,F280M
T36F
T36F 双环管液相本体法 (ST),双釜式气相本体
30
投产年份 2012
三井油化釜式法(国内设计)
5
大连石化
中国石油
海蒙特环管法(国内设计)
建设单位浙江绍兴三圆石化有限公司
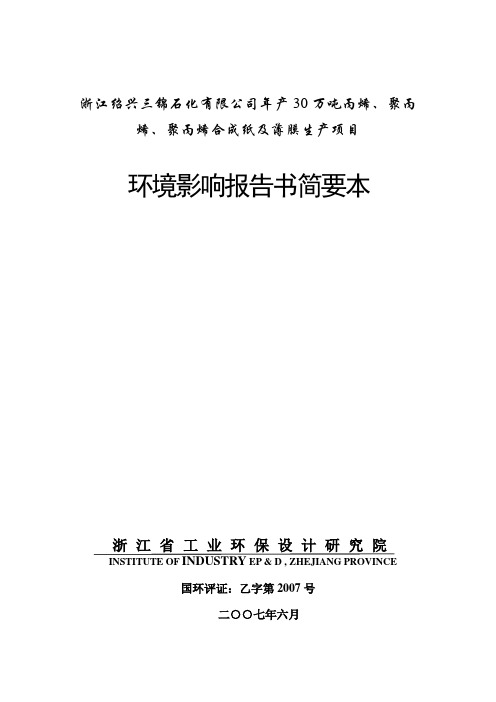
序号
废水名称
排放量(万t/a)
废水水质
1
生产废水
1.353
pH8.13~8.32、SS30mg/L、CODcr47.5 mg/L、石油类1.68mg/L、氨氮0.26mg/L、总磷1.32mg/l
2
生活污水
0.630
pH值范围为8.46~8.51、SS31mg/L、CODCr124mg/L、石油类2.59mg/L、氨氮114mg/L、总磷7.99mg/l
经营范围:丙烯精制、聚丙烯生产、聚丙烯合成纸生产、聚丙烯簿膜生产。
二、工程内容及污染因素分析
1、基本内容
(1)产品方案及生产规模
项目将建成产量为30万t/a丙烯精制和聚丙烯生产线,同时建成5万t/a聚丙烯合成纸和10万t/a聚丙烯薄膜生产线,其最终产品为聚丙烯粒子、聚丙烯合成纸和薄膜(BOPP)。
项目最终产品方案及生产规模见表2-1。
只
2
与合成纸生产线合用
四
聚丙烯合成纸
条
3
5万t/a聚丙烯合成纸
1
串联挤出机
台
3
2
辅助挤出机
台
3
3
电晕设备
台
3
4
分切机
台
3
五
罐区
1
2000 m3丙烯储罐
只
4
依托三圆石化公司
2
150 m3乙烯储罐
只
2
依托三圆石化公司
3
表2-6建设项目主要原辅料消耗
序号
原辅料名称
单位
用量
备注
一
丙烯精制
1
化学级丙烯
t/a
316114
丙烷脱氢介绍

丙烷脱氢介绍
“丙烷脱氢”是现今国内丙烯生产新工艺的热点之一,备注市场的关注和青睐。
国内丙烯市场存在较大的需求缺口,为了使得下游产品市场更健康长久发展,解决原料丙烯的缺量问题,市场中跃跃欲试的企业越来越多。目前有两个热点,其一煤化工路线,煤制烯烃;其二,丙烷脱氢。
丙烷脱氢工艺因其丙烯收率相对较高,目前备受市场关注和青睐。目前较为成熟的丙烷脱氢工艺主要有三种:Oleflex 工艺、Catofin 工艺和 PDH 工艺。 Oleflex 工艺由 UOP 公司开发并于 1990 年实现工业化生产,工艺主要采用催化剂连续再生方法,该工艺制取丙烯的产率约为 86×4%,氢气产率约为 3×5%。 Catofin 工艺是由鲁姆斯等公司联合开发,可生产丙烯、异丁烯、正丁二烯等产品。该工艺采用固定床催化反应器,并用取切换操作的方法,丙烯转化率高达 90%左右。PDH 工艺是由德国林德公司和巴斯夫公司合作开发,主要生产丙烯和异丁烯。该工艺采用装填催化剂的管式反应器。 目前该项目在国内仍是一片空白。
丙烷脱氢

一、概述丙烯主要用于生产聚丙烯、丙烯腈、丁辛醇、丙烯酸等产品,目前,丙烯供应主要来自石脑油裂解制乙烯和石油催化裂化。
2004-2010年间,乙烯产能增长34%,而丙烯产能仅增长25%。
随着丙烯下游产品需求量不断增长,丙烯资源短缺的状况还会进一步加剧。
因此,近年开发扩大丙烯来源的丙烷脱氢(PDH)制丙烯生产工艺成为备受关注的热点。
二、丙烷脱氢制丙烯技术情况丙烷脱氢制丙烯技术主要包括催化脱氢制丙烯、氧化脱氢制丙烯、膜反应器脱氢制丙烯以及CO2逆水煤气法脱氢制丙烯技术[2]。
2.1 丙烷催化脱氢技术丙烷催化脱氢技术根据催化剂体系的不同主要有铬系催化剂、铂系催化剂。
2.1.1 铬系催化剂丙烷催化脱氢的Catofin 工艺就采用Cr203/Al2O3催化剂,由于铬系催化剂稳定性差,且具有毒性,随着环境保护呼声的日益提高,开发低Cr含量的催化剂才有一定的前景。
2.1.2 铂系催化剂丙烷Oleflex催化脱氢工艺,采用贵金属Pt催化剂,Pt催化剂对热更稳定,可在更苛刻条件下操作。
铂催化剂对环境友好,活性较高,但其稳定性选择性还不是很理想。
2.2 丙烷氧化脱氢技术丙烷氧化脱氢为放热反应,无需外界加热,不必向过程提供热能,可节省能源,同时反应不受热力学平衡的限制。
因此氧化脱氢具有诱人的前景。
但该技术面临的困难之一是在氧化脱氢的反应条件下,很容易发生丙烷的完全氧化反应,一旦发生完全氧化反应,将放出大量热量,使温度急剧上升,不仅丙烷完全氧化,而且所产生的丙烯更容易氧化成CO~CO2(因为丙烯比丙烷更不稳定)。
因此,开发低温型高选择性催化剂是丙烷氧化脱氢的研究方向。
两种技术比较丙烷催化脱氢的选择性较高,其缺点是要耗费大量的能量。
若能把催化脱氢和氧化脱氢的优点结合起来,设计双功能型催化剂。
在催化脱氢体系引入少量氧,氧在活化丙烷的同时实现对氢气高选择性氧化,实现化学平衡移动的同时自身提供热量。
这个过程可能打破脱氢反应热力学限制,同时解决氧化脱氢反应在高烷烃转化率下的低碳烯烃选择性问题。
浙江石油化工公司炼化一体化项目环境影响评价公众参与第二次信息公开
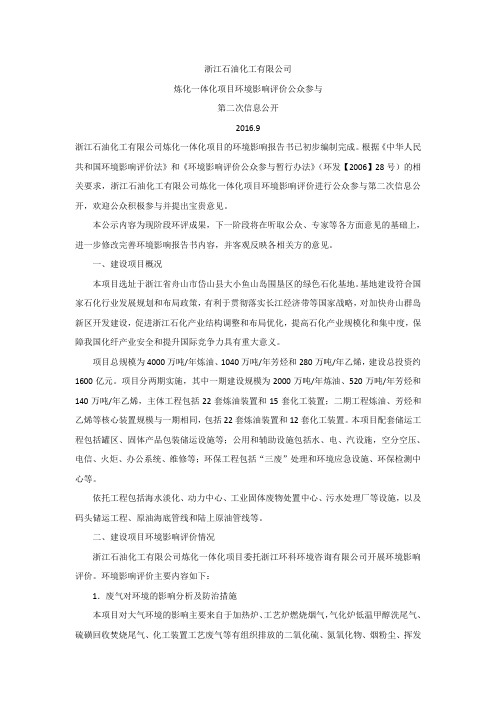
浙江石油化工有限公司炼化一体化项目环境影响评价公众参与第二次信息公开2016.9浙江石油化工有限公司炼化一体化项目的环境影响报告书已初步编制完成。
根据《中华人民共和国环境影响评价法》和《环境影响评价公众参与暂行办法》(环发【2006】28号)的相关要求,浙江石油化工有限公司炼化一体化项目环境影响评价进行公众参与第二次信息公开,欢迎公众积极参与并提出宝贵意见。
本公示内容为现阶段环评成果,下一阶段将在听取公众、专家等各方面意见的基础上,进一步修改完善环境影响报告书内容,并客观反映各相关方的意见。
一、建设项目概况本项目选址于浙江省舟山市岱山县大小鱼山岛围垦区的绿色石化基地。
基地建设符合国家石化行业发展规划和布局政策,有利于贯彻落实长江经济带等国家战略,对加快舟山群岛新区开发建设,促进浙江石化产业结构调整和布局优化,提高石化产业规模化和集中度,保障我国化纤产业安全和提升国际竞争力具有重大意义。
项目总规模为4000万吨/年炼油、1040万吨/年芳烃和280万吨/年乙烯,建设总投资约1600亿元。
项目分两期实施,其中一期建设规模为2000万吨/年炼油、520万吨/年芳烃和140万吨/年乙烯,主体工程包括22套炼油装置和15套化工装置;二期工程炼油、芳烃和乙烯等核心装置规模与一期相同,包括22套炼油装置和12套化工装置。
本项目配套储运工程包括罐区、固体产品包装储运设施等;公用和辅助设施包括水、电、汽设施,空分空压、电信、火炬、办公系统、维修等;环保工程包括“三废”处理和环境应急设施、环保检测中心等。
依托工程包括海水淡化、动力中心、工业固体废物处置中心、污水处理厂等设施,以及码头储运工程、原油海底管线和陆上原油管线等。
二、建设项目环境影响评价情况浙江石油化工有限公司炼化一体化项目委托浙江环科环境咨询有限公司开展环境影响评价。
环境影响评价主要内容如下:1.废气对环境的影响分析及防治措施本项目对大气环境的影响主要来自于加热炉、工艺炉燃烧烟气,气化炉低温甲醇洗尾气、硫磺回收焚烧尾气、化工装置工艺废气等有组织排放的二氧化硫、氮氧化物、烟粉尘、挥发性有机物等,以及在生产过程、物料的储存和装卸过程中无组织排放的挥发性有机物等。
丙烷的工业应用

丙烷的工业应用一、丙烷的工业应用图1:二、丙烷的工业应用:1.丙烷的主要用途:丙烷常用作烧烤、便携式炉灶和机动车的燃料。
丙烷通常被用来驱动火车,公交车,叉车和出租车,也被用来充当休旅车和露营时取暖和做饭的燃料。
在北美的一些农村,人们用丙烷来填充炉灶、热水器和干手机等产热的器具。
截至2000年,690万美国家庭以丙烷作为主要燃料。
商用的“丙烷”燃料,或称液化石油气,是不纯的。
在美国和加拿大,其主要成分是90%的丙烷外加最多5%的丁烷和丙烯以及臭味剂。
这是美国和加拿大的国内标准,通常写作HD-5标准。
需要注意的是,从甲烷(天然气)制备的液化石油气不包含丙烯,只有从原油精炼过程中得到的丙烷才含有。
同样,在一些其他国家,比如墨西哥,丁烷的标准含量会高一些。
目前随着工业的发展,丙烷逐渐成为一种重要的石油化工原料。
在石油化工上,丙烷可作为蒸汽裂化制备基础石化产品的给料;由于丙烷与丙烯之间存在着巨大的价格差,而且丙烷资源丰富,目前全球很多公司纷纷研究用丙烷作原料生产丙烯和丙烯腈的工艺。
三、丙烷一次氨氧化制丙烯腈:丙烷氨氧化工艺早在20世纪50年代和60年代初就开始被研究。
由丙烷氨氧化直接生产丙烯腈关键在于开发使丙烷活化的催化剂(钒/锑氯化物),丙烯腈收率可望达到约55%。
进行丙烷制丙烯腈工艺开发的有旭化成、BP和三菱化学公司,三井东压化学、罗纳-普朗克、巴斯夫、空气产品和日本触媒化成等公司也在开发此工艺。
浅野化学公司已将小试放大到中试。
三菱化学公司和BOC气体公司也在日本建设了中试装置,三菱化学开发的催化剂以钼、钒、碲的氧化物为基础,其中含少量铌和锑。
旭化成和三井公司也在投入研究。
BP公司也在开发丙烷生产丙烯腈工艺,并在美国得州绿湖中试成功,BP开发的催化剂以钒和锑的氧化物为基础,以锡和钛为助剂。
可望在7~8年内建成20-25万吨/年装置。
国内外丙烷一次氨氧化制丙烯腈工业化如下表:表1. 国内外丙烷一次氨氧化制丙烯腈的生产能力(万吨/年)表2丙烯腈生成方法的经济概况注:1. 美国Guif Coast,1997年二季度27.22万t/a;2. 丙烯43.54美分/kg,丙烷18.1美分/kg,氨24.80美分/kg,HCN 49.16美分/kg。
丙烷的工业应用

丙烷的工业应用一、丙烷的工业应用图1:二、丙烷的工业应用:1.丙烷的主要用途:丙烷常用作烧烤、便携式炉灶和机动车的燃料。
丙烷通常被用来驱动火车,公交车,叉车和出租车,也被用来充当休旅车和露营时取暖和做饭的燃料。
在北美的一些农村,人们用丙烷来填充炉灶、热水器和干手机等产热的器具。
截至2000年,690万美国家庭以丙烷作为主要燃料。
商用的“丙烷”燃料,或称液化石油气,是不纯的。
在美国和加拿大,其主要成分是90%的丙烷外加最多5%的丁烷和丙烯以及臭味剂。
这是美国和加拿大的国内标准,通常写作HD-5标准。
需要注意的是,从甲烷(天然气)制备的液化石油气不包含丙烯,只有从原油精炼过程中得到的丙烷才含有。
同样,在一些其他国家,比如墨西哥,丁烷的标准含量会高一些。
目前随着工业的发展,丙烷逐渐成为一种重要的石油化工原料。
在石油化工上,丙烷可作为蒸汽裂化制备基础石化产品的给料;由于丙烷与丙烯之间存在着巨大的价格差,而且丙烷资源丰富,目前全球很多公司纷纷研究用丙烷作原料生产丙烯和丙烯腈的工艺。
三、丙烷一次氨氧化制丙烯腈:丙烷氨氧化工艺早在20世纪50年代和60年代初就开始被研究。
由丙烷氨氧化直接生产丙烯腈关键在于开发使丙烷活化的催化剂(钒/锑氯化物),丙烯腈收率可望达到约55%。
进行丙烷制丙烯腈工艺开发的有旭化成、BP和三菱化学公司,三井东压化学、罗纳-普朗克、巴斯夫、空气产品和日本触媒化成等公司也在开发此工艺。
浅野化学公司已将小试放大到中试。
三菱化学公司和BOC气体公司也在日本建设了中试装置,三菱化学开发的催化剂以钼、钒、碲的氧化物为基础,其中含少量铌和锑。
旭化成和三井公司也在投入研究。
BP公司也在开发丙烷生产丙烯腈工艺,并在美国得州绿湖中试成功,BP开发的催化剂以钒和锑的氧化物为基础,以锡和钛为助剂。
可望在7~8年内建成20-25万吨/年装置。
国内外丙烷一次氨氧化制丙烯腈工业化如下表:表1. 国内外丙烷一次氨氧化制丙烯腈的生产能力(万吨/年)表2丙烯腈生成方法的经济概况注:1. 美国Guif Coast,1997年二季度27.22万t/a;2. 丙烯43.54美分/kg,丙烷18.1美分/kg,氨24.80美分/kg,HCN 49.16美分/kg。
平湖:实施企业兼并实现退低进高
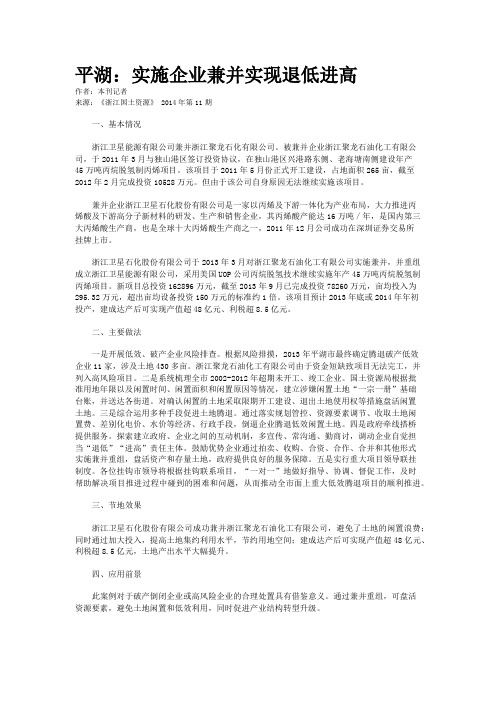
平湖:实施企业兼并实现退低进高作者:本刊记者来源:《浙江国土资源》 2014年第11期一、基本情况浙江卫星能源有限公司兼并浙江聚龙石化有限公司。
被兼并企业浙江聚龙石油化工有限公司,于2011年3月与独山港区签订投资协议,在独山港区兴港路东侧、老海塘南侧建设年产45万吨丙烷脱氢制丙烯项目。
该项目于2011年5月份正式开工建设,占地面积265亩,截至2012年2月完成投资10528万元。
但由于该公司自身原因无法继续实施该项目。
兼并企业浙江卫星石化股份有限公司是一家以丙烯及下游一体化为产业布局,大力推进丙烯酸及下游高分子新材料的研发、生产和销售企业,其丙烯酸产能达16万吨/年,是国内第三大丙烯酸生产商,也是全球十大丙烯酸生产商之一,2011年12月公司成功在深圳证券交易所挂牌上市。
浙江卫星石化股份有限公司于2013年3月对浙江聚龙石油化工有限公司实施兼并,并重组成立浙江卫星能源有限公司,采用美国UOP公司丙烷脱氢技术继续实施年产45万吨丙烷脱氢制丙烯项目。
新项目总投资162896万元,截至2013年9月已完成投资78260万元,亩均投入为295.32万元,超出亩均设备投资150万元的标准约1倍。
该项目预计2013年底或2014年年初投产,建成达产后可实现产值超48亿元、利税超8.5亿元。
二、主要做法一是开展低效、破产企业风险排查。
根据风险排摸,2013年平湖市最终确定腾退破产低效企业11家,涉及土地430多亩。
浙江聚龙石油化工有限公司由于资金短缺致项目无法完工,并列入高风险项目。
二是系统梳理全市2002-2012年超期未开工、竣工企业。
国土资源局根据批准用地年限以及闲置时间、闲置面积和闲置原因等情况,建立涉嫌闲置土地“一宗一册”基础台账,并送达各街道。
对确认闲置的土地采取限期开工建设、退出土地使用权等措施盘活闲置土地。
三是综合运用多种手段促进土地腾退。
通过落实规划管控、资源要素调节、收取土地闲置费、差别化电价、水价等经济、行政手段,倒逼企业腾退低效闲置土地。
华联三鑫石化年产45tPTA工程环境影响报告书
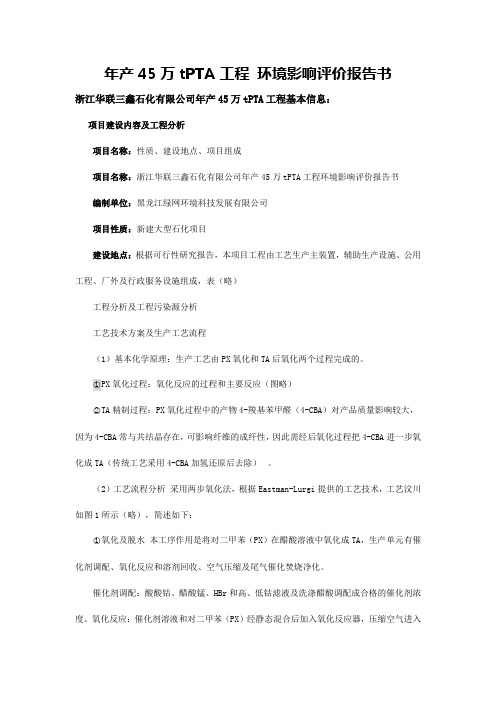
年产45万tPTA工程环境影响评价报告书浙江华联三鑫石化有限公司年产45万tPTA工程基本信息:项目建设内容及工程分析项目名称:性质、建设地点、项目组成项目名称:浙江华联三鑫石化有限公司年产45万tPTA工程环境影响评价报告书编制单位:黑龙江绿网环境科技发展有限公司项目性质:新建大型石化项目建设地点:根据可行性研究报告,本项目工程由工艺生产主装置,辅助生产设施、公用工程、厂外及行政服务设施组成,表(略)工程分析及工程污染源分析工艺技术方案及生产工艺流程(1)基本化学原理:生产工艺由PX氧化和TA后氧化两个过程完成的。
○1PX氧化过程:氧化反应的过程和主要反应(图略)○2TA精制过程:PX氧化过程中的产物4-羧基苯甲醛(4-CBA)对产品质量影响较大,因为4-CBA常与共结晶存在,可影响纤维的成纤性,因此需经后氧化过程把4-CBA进一步氧化成TA(传统工艺采用4-CBA加氢还原后去除)。
(2)工艺流程分析采用两步氧化法,根据Eastman-Lurgi提供的工艺技术,工艺汶川如图1所示(略),简述如下:○1氧化及脱水本工序作用是将对二甲苯(PX)在醋酸溶液中氧化成TA,生产单元有催化剂调配、氧化反应和溶剂回收、空气压缩及尾气催化焚烧净化。
催化剂调配:酸酸钴、醋酸锰、HBr和高、低钴滤液及洗涤醋酸调配成合格的催化剂浓度。
氧化反应:催化剂溶液和对二甲苯(PX)经静态混合后加入氧化反应器,压缩空气进入反应器下部分布器,通过鼓泡代替搅拌进行传质传热,氧化反应生成的TA在反应器中析出。
醋酸溶剂汽化带走反应热并和反应废气进入溶剂脱水塔,塔顶物料冷凝后送厂内污水处理系统,不凝尾气进尾气处理系统,塔釜物料进离心分离系统处理。
空气压缩及尾气焚烧净化:脱水顶部蒸汽冷凝后气水分离,冷凝液回氧化反应器,不凝尾气部分经干燥压缩后用于后继物料风送,其他部分先经膨胀透平回回收能量用于驱动空压机,回收能量后尾气与风送系统除尘后尾气混合进入RTO焚烧室,燃烧尾气再经文丘里急冷器和碱洗后排入大气。
- 1、下载文档前请自行甄别文档内容的完整性,平台不提供额外的编辑、内容补充、找答案等附加服务。
- 2、"仅部分预览"的文档,不可在线预览部分如存在完整性等问题,可反馈申请退款(可完整预览的文档不适用该条件!)。
- 3、如文档侵犯您的权益,请联系客服反馈,我们会尽快为您处理(人工客服工作时间:9:00-18:30)。
浙江聚龙石油化工有限公司年产45万吨丙烯项目环境影响报告书( 简写本)浙江省环境保护科学设计研究院ENVIRONMENTAL SCIENCE RESEA RCH DESIGN INSTITUTE OF ZHEJIANG PROVINCE国环评证:甲字第2003号二○一一年十一月一、项目概况1、项目来源丙烯是仅次于乙烯的重要有机化工基础原料,其下游衍生物主要有:聚丙烯、环氧丙烷、丙烯腈、丙烯酸、异丙苯/苯酚/丙酮、羰基合成醇、异丙醇等有机原料。
这些衍生物由于其自身的特性正在逐步地取代传统的材料如钢铁、木材、棉及棉制品等,被广泛运用于基础设施和城市建设、航天和航空工业、汽车制造、家用电器、生物及医药制品等各个行业。
随着我国国民经济的发展和人民生活水平的不断提高,其应用领域还将进一步扩大,需求还将大幅度地提升。
长期以来,由于受原油价格和工艺技术的制约,丙烯供应主要来自石脑油裂解制乙烯和石油催化裂化过程的副产品。
随着近年来大部分新建的乙烯装置已不再沿用陈旧的石脑油裂解工艺转而采用乙烷直接裂解工艺,新的乙烯装置不再代产丙烯,从而导致丙烯产能增长严重滞后。
近年开发扩大丙烯来源的生产工艺成为热点,其中丙烷脱氢(PDH)制丙烯工艺最备受关注。
浙江聚龙石油化工有限公司是以浙江长江能源发展有限公司为主体投资组建的独立法人单位。
浙江长江能源发展有限公司成立于1988年,是一家从事集液化气船舶制造、运输、仓储、批发,销售的综合企业。
浙江聚龙石油化工有限公司拟投资16.3亿元,引进美国UOP公司Oleflex技术在平湖独山港区新建一套丙烷脱氢(PDH)装置,实施年产45万吨丙烯项目。
2、项目基本情况建设项目名称:浙江聚龙石油化工有限公司年产45万吨丙烯项目建设项目性质:新建建设地点:浙江省平湖独山港区一期内,项目北临老海塘路,南侧为新海塘路及杭州湾,西侧为散货物流区,东侧是规划工业用地,总占地243.34亩。
项目建设地理位置图见附图一。
建设规模及产品方案:本项目设计总规模为年产丙烯45万t/a,项目装置设计年开工8000小时。
工作制度和劳动定员:依据《石油化工生产装置设计定员暂行规定》和本项目的实际情况,本项目实行四班三运制,劳动定员共134人,其中生产人员109人,管理人员25人。
建设项目工程组成:本项目主体工艺装置为45万吨/年丙烯装置,配套工程包括循环水场、脱盐水站、罐区、变电站及控制室、空压站、化验室、消防设施等。
本项目内容组成见表3.3-1。
表3.3-1 本项目内容组成一览表二、项目概括及工程分析1、生产工艺流程本项目丙烷脱氢装置设计规模为45万吨/年,采用美国UOP公司的Oleflex 工艺,通过连续催化再生的催化脱氢工艺把丙烷转化成丙烯。
本项目主要包括原料预处理、脱丙烷部分、Oleflex反应部分、脱乙烷部分、丙烷丙烯分离部分以及催化剂再生部分。
(2)工艺说明①原料预处理原料预处理部分包括原料保护床、原料干燥器和脱丙烷塔等设施。
从罐区来的丙烷原料通过原料保护床吸附脱出氮化物、金属化合物等杂质,再经过原料干燥器去除原料中含有的水份,以保护脱氢催化剂和设备。
其中原料干燥剂可以通过再生装置进行再生,重复利用,原料保护剂和干燥剂3年更换一次。
经干燥后的丙烷原料与丙烷丙烯分离塔回流的丙烷一并进入脱丙烷塔,脱丙烷塔操作压力为2.6Mpa(g)。
在脱丙烷塔顶部得到丙烷进入反应系统,底部物料进入脱丙烷汽提塔进一步回收丙烷,丙烷汽提塔下部塔盘抽出C4组分,底部得到碳四以上重组分。
汽提塔丙烷与来自反应产物干燥器的反应产物换热,然后与来自反应器的反应产物换热,再进入到Oleflex反应系统。
②反应部分在反应部分新鲜丙烷和循环丙烷通过催化脱氢反应将丙烷转化成丙烯。
反应系统由4台加热炉和4台反应器交替串联布置,加热炉提供反应所需热能,反应器提供反应所需场所。
4台反应器垂直安装,丙烷原料先经过加热炉加热到反应所需温度后进入到反应器内反应,丙烷原料在反应器内横向穿过催化剂床层进行反应,催化剂在反应器内靠重力自上而下流动。
反应器平均进料温度为644℃,第一台反应器的进料压力为0.23 Mpa(g),第四台反应器的出口压力为0.034 Mpa(g),出口温度为605℃。
最后一个反应器流出的产物与进料丙烷换热回收反应系统余热后进入反应产物冷却器冷却。
加热炉烟气进过余热锅炉回收热量后高空排放。
为了防止加热炉和反应器高温腐蚀,第一台加热炉前注入二甲基二硫化醚(DMDS), 注入量以反应产物中H2S的含量为60PPm为准。
DMDS用槽车自厂外购进,在密闭状态下用氮气压到注硫罐内,并采用隔膜泵打入反应器入口管线,整个工艺操作是在密闭状态下进行的。
DMDS进入反应器后进行高温分解,生成H2S,H2S与反应器内件(不锈钢)中的铬反应形成硫化铬,硫化铬起保护膜的作用,防止高温腐蚀,其反应式如下:CH3-S-S-CH3→H2S+CnHm →CrS+CnHm。
反应产物用压缩机压缩到1.4 Mpa(g),压缩后的物料进行冷却至43℃左右。
反应产物进入压缩机前注入二乙基苯溶剂,以去除换热器管内的污垢,提高传热系数,对二乙基苯最后随物料进入重组分。
压缩后的物料先后进入脱氯器和干燥器以除去硫化物和氯化物。
③分离部分干燥后的反应产物进入分离系统,物料通过膨胀机进行深冷(-110℃)分离,分离成液态烃和富含氢的气相组分。
液态烃去选择性加氢,富氢气体部分去PSA氢气提纯系统提纯到99.99%,部分去再生反应物干燥剂。
经PSA提纯的氢气先经选择性加氢后多余部分用于进入反应器,用于催化剂还原。
PSA尾气去燃料气管网。
④产品回收部分液态烃与丙烯—丙烷分离塔侧线抽出的双烯烃和炔烃一起进行选择性加氢,操作压力为3.8 Mpa(g),温度为60℃。
加氢后的物料进脱乙烷塔,塔顶脱出乙烷和轻组分去燃料气管网。
塔底物料去丙烯—丙烷分离塔,脱乙烷汽提塔的操作压力为3.1 Mpa(g),顶温为62℃;脱乙烷精馏塔的塔顶操作压力为2.8 Mpa(g),塔顶温度为-15℃。
丙烯—丙烷分离塔塔顶得到产品丙烯,塔底未转化的丙烷返回脱丙烷塔分离。
丙烯—丙烷分离塔塔顶压力为0.7 Mpa(g),塔顶温度为10℃左右。
⑤催化剂再生部分本项目催化剂采用连续再生,从第四反应器底部下来的待再生催化剂,使用氮气来吹扫氢气和碳氢化合物。
氢气和碳氢化合物清除干净后催化剂流入提升料斗,用氮气把催化剂提升到再生器顶部的分离料斗。
再用氮气吹除催化剂粉尘和碎末,含有催化剂粉尘和碎末的气流流进集尘器回收催化剂粉尘和碎末,从而回收贵金属铂。
除掉细粉的催化剂从分离料斗通过重力流到再生塔。
再生塔内的催化剂靠重力继续往下流,催化剂上的碳通过与氮气和氧气(约1%)情况下烧焦而再生,烧焦温度为477—550℃,并注入适量的氯气,防止铂在催化剂内部烧结。
烧焦再生后的催化剂返回反应系统,依次通过四个反应器,再回到再生器,进行连续循环再生。
再生烟气经过再生气洗涤塔用10%氢氧化钠溶液洗涤。
根据UOP提供资料,本项目催化剂对硫无吸附作用,再生烟气中基本无SO2排放。
催化剂经一段时间使用后(约3.5年)失效需返厂,系统中的Oleflex 催化剂需整体更换,换下的催化剂由UOP公司回收再生。
⑥干燥剂再生本装置设有2套物料干燥器,交替再生使用。
当干燥剂饱和(24h为一个周期)时,用230℃的富氢干气进行气提干燥,除去吸附的水份和硫化氢。
干燥后带硫化氢的干气经碱洗塔碱洗去除硫化氢后进入燃料系统。
本项目两套干燥器每24小时切换一次,干燥器气提干燥时间为24小时/次。
⑦PSA装置工艺PSA(变压吸附)装置对来自分离系统的富氢干气进行提纯,得到99.99%的氢气,该装置主要包括:5个吸附塔、1个顺放气缓冲罐和1个解吸气缓冲罐。
来自分离系统压力为0.6MPa(G)的原料气,经吸附、均压降压、顺放、逆放、冲洗、均压升压和产品气升压等步骤处理后得到纯度大于99.99%的氢气。
从原料气中吸附的烃类气体经解吸后送往加热炉作为燃料。
PSA生产过程中无废水、固废产生。
浙江卫星丙烯酸制造有限公司丙烯酸及丙烯酸酯二期、三期技改项目环境影响报告书简写本6入燃料系统W1图2.1-1 Oleflex 丙烷脱氢污染工艺流程方框图2、原辅材料及设备情况原材料消耗情况见表2.2-1,本项目二期技术改造的主要设备见表3.2-2。
表2.2-1 本项目原材料消耗情况表2.2-2 本项目的主要设备一览表3、污染源汇总表2.3-3 本项目“三废”排放汇总表三、周边环境及保护目标1、保护目标根据本项目的污染特征和周围的环境状况,本评价的重点为项目的工程分析、废气、废水和废渣排放及事故风险排放对周围环境的影响以及污染防治措施的分析,同时兼顾声环境和固废的影响分析。
水环境主要保护对象:厂区附近河道。
大气环境主要保护对象:见表1.7-1。
声环境主要保护对象:距离厂界200米范围内。
表1.7-1 主要保护目标概况最近的一类工业用地(规划)为现有的渔业村。
2、环境质量现状(1)环境空气质量现状2011年7月监测期间,该区域的SO2、NO2和PM10能满足环境空气质量功能区的要求;非甲烷总烃低于原国家环保总局的相关规范说明取值。
可见项目拟建地区域环境空气质量现状较好。
(2)水环境质量现状从监测结果来看,附近内河水体水质已不能满足相应功能区类别的要求,主要超标因子为COD、氨氮、BOD5、石油类、总磷和高锰酸钾指数等。
(3)声环境质量现状从噪声监测结果可知,项目拟建地厂界昼夜噪声均能达到《声环境质量标准》(GB3096-2008)中的3类声环境标准。
(4)地下水环境质量现状从监测结果来看,项目拟建地附近地下水的三个监测点中除了渔业村测点的氨氮指标超过Ⅲ类标准,其他所有指标都能达到《地下水质量标准》(GB/T14848-93)中III类标准要求,地下水环境质量尚可。
根据分析氨氮超标主要与地表水污染及农田径流的影响有关。
四、环境影响主要结论1、环境空气(1)正常工况下本项目SO2、NO2和非甲烷总烃排放对区域环境空气影响不大,SO2、NO2地面小时/日均/年均浓度以及非甲烷总烃地面年均浓度贡献最大值均能满足标准要求;各敏感点SO2、NO2小时/日均/年均浓度以及非甲烷总烃地面年均浓度贡献最大值均能达标。
(2)正常工况下本项目叠加背景浓度后,SO2、NO2和非甲烷总烃的排放对各敏感点环境空气影响不大,各敏感点的污染因子小时/日均浓度也均能达到相应标准限值要求。
(3)根据预测可知,非正常工况排放情况下,SO2最大落地浓度及各敏感点贡献值均未超出相应的标准要求,非正常排放下SO2对周边影响不大。
(4)本项目装置区需设置150米的卫生防护距离。
现状卫生防护距离范围内无居民等敏感点,卫生防护距离可达到保证;由于厂区内产生的无组织非甲烷总烃排放计算后得到的结果为“无超标点”,所以本项目不需设大气环境防护距离。