新能源汽车线束DVP测试计划
新能源高压动力线束 DVP测试计划(2016年版)
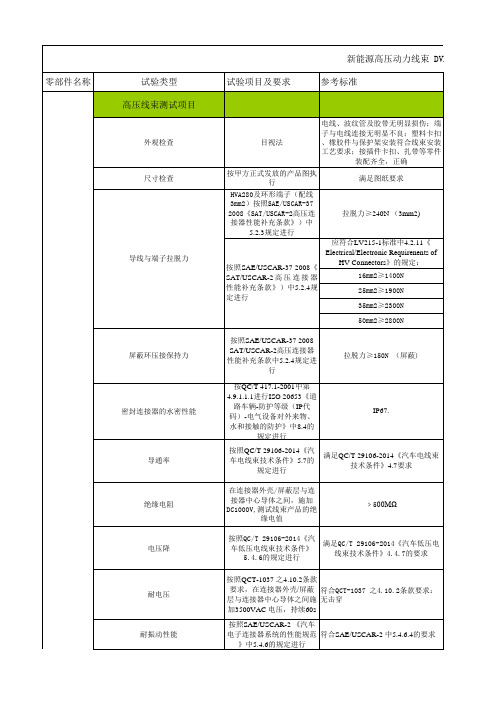
拉脱力≥150N (屏蔽)
按QC/T 417.1-2001中第 4.9.1.1.1进行ISO 20653《道
路车辆-防护等级(IP代 码)-电气设备对外来物、 水和接触的防护》中8.4的
规定进行
IP67.
按照QC/T 29106-2014《汽 车电线束技术条件》5.7的
规定进行
满足QC/T 29106-2014《汽车电线束 技术条件》4.7要求
拉脱力≥240N ຫໍສະໝຸດ 3mm2)应符合LV215-1标准中4.2.11《 Electrical/Electronic Requirenents of
HV Connectors》的规定: 16mm2≥1400N 25mm2≥1900N 35mm2≥2300N
50mm2≥2800N
按照SAE/USCAR-37 2008 SAT/USCAR-2高压连接器 性能补充条款中5.2.4规定进
标志的耐久性 耐臭氧
耐温度和湿度交变 抗延燃
波纹管原材料测试项目 3000H 热老化 热时效 低温冲击 柔韧性 抗延燃 抗紫外线
按照QCT-1037 中之5.23的 规定进行
符合QCT-1037 中之4.10.15的要求
按照QCT-1037 中之5.24的 规定进行
符合QCT-1037 中之4.10.16的要求
热过载
按照QCT-1037 中之5.3的规 定进行
符合QCT-1037 中之4.3的要求
按照QCT-1037 中之5.3的规 定进行
符合QCT-1037 中之4.7.1的要求
按照QCT-1037 中之5.4的规 定进行
符合QCT-1037 中之4.10.1的要求
按照QCT-1037 中之5.5的规 定进行
新能源汽车高压线束实验要求DVP
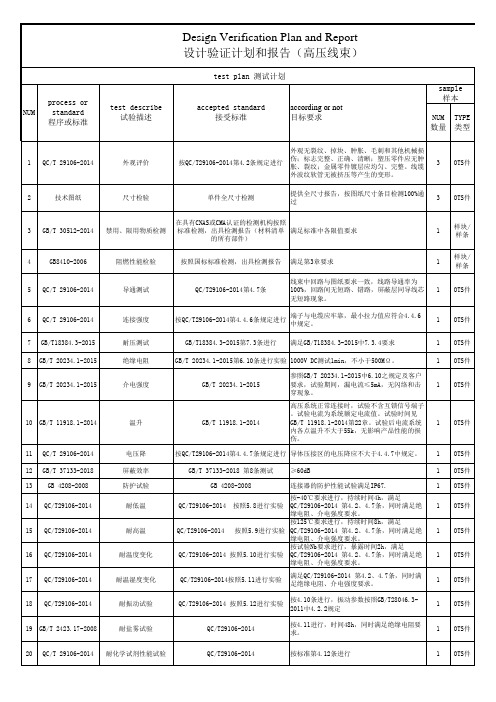
耐振动试验
19 GB/T 2423.17-2008
耐盐雾试验
GB/T 37133-2018 第8条测试 ≥60dB
1 OTS件
GB 4208-2008
连接器的防护性能试验满足IP67.
1 OTS件
按-40℃要求进行,持续时间4h,满足 QC/T29106-2014 按照5.8进行实验 QC/T29106-2014 第4.2、4.7条,同时满足绝 1 OTS件
Design Verification Plan and Report 设计验证计划和报告(高压线束)
process or NUM standard
程序或标准
test describe 试验描述
test plan 测试计划
accepted standard 接受标准
according or not 目标要求
sample 样本
NUM TYPE 数量 类型
1 QC/T 29106-2014
2
技术图纸
外观评价 尺寸检验
外观无裂纹、掉块、肿胀、毛刺和其他机械损
按QC/T29106-2014第4.2条规定进行
伤;标志完整、正确、清晰;塑压零件应无肿 胀、裂纹;金属零件镀层应均匀、完整。线缆
3
外波纹软管无被挤压等产生的变形。
导通测试
按照国标标准检测,出具检测报告 满足第3章要求
1
QC/T29106-2014第4.7条
线束中回路与图纸要求一致,线路导通率为 100%,回路间无短路、错路,屏蔽层同导线芯 1 无短路现象。
样块/ 样条
OTS件
6 QC/T 29106-2014
连接强度
按QC/T29106-2014第4.4.6条规定进行
DVP试验计划书模板

DVP试验计划书模板1. 引言本试验计划书旨在详细描述DVP试验的目的、范围、方法和安排,以确保试验的顺利进行和结果的可靠性。
本模板可以帮助团队成员快速编写DVP试验计划书,确保试验工作的有效开展。
2. 试验目的明确试验的目的,包括但不限于以下几个方面:•验证产品是否满足设计要求和性能指标;•确定产品的可靠性和耐久性;•发现并解决潜在的问题和风险。
3. 试验范围详细描述试验的范围,包括所测试的功能、性能指标、环境条件以及相关的试验输入和输出。
试验范围需要与产品设计要求和技术规范一致。
4. 试验方法描述试验所采用的方法和步骤,包括但不限于以下几个方面:4.1 试验设备和工具列出试验所需的设备和工具清单,并说明其规格和性能要求。
4.2 试验环境描述试验所需的环境条件,包括温度、湿度、气压等因素,并与产品的使用环境相匹配。
4.3 试验样品说明试验所使用的样品来源、数量以及选取的依据。
如果涉及多个样品,需要说明其相似性和差异性。
4.4 试验步骤按照一定的逻辑顺序,详细描述试验的各个步骤,包括样品准备、试验参数设置、数据采集和处理等。
4.5 试验数据和结果分析说明如何采集和记录试验数据,并对试验结果进行合理的分析和解释。
5. 试验安排根据试验目的和时间要求,制定试验的安排计划,包括但不限于以下内容:•试验开始和结束时间;•各个试验步骤的时间安排;•试验人员的职责和工作分配;•试验设备和环境的预约和准备;•试验过程中的沟通和协调。
6. 风险评估识别和评估试验过程中可能存在的风险和不确定性,制定相应的风险管理计划,并采取预防和控制措施,以减少风险对试验结果的影响。
7. 试验质量控制描述如何确保试验过程和结果的质量,包括但不限于以下几个方面:•试验人员的培训和资质要求;•试验设备和工具的校准和维护;•试验数据的准确性和完整性控制;•试验过程和结果的审查和验证。
8. 试验报告概述试验报告的内容和格式要求,以便在试验结束后及时撰写和提交。
新能源汽车交流充电枪试验测试要求

防触电保护
GB/T
20234.1-2015 《电动汽车传导充电用连 接装置 第1部分:通用要求》6.5
GB/T
20234.1-2015
《电动汽车传导充电用连接装置
第1部分:通用要求》6.5
接地措施
GB/T
20234.1-2015 《电动汽车传导充电用连 接装置 第1部分:通用要2015
GB/T 18487.1-2015
28
GB/T 18487.1-2015
29
GB/T 18487.1-2015
30
GB/T 18487.1-2015
欠压保护
过流保护 接地保护 过温保护
GB/T 20234.1-2015-6.21
将带有制造商推荐的电缆的供电插头和车辆插头随意地放在水泥地上,用P225/75R15或同等负载的 传统汽车轮胎以(5000±250)N的压力,以(8±2)km/h的速度压过供电插头或车辆插头(轮胎充气压 力220±10kPa)。 试验后,应满足如下要求: ——在与保护盖连接后,供电插头、车辆插头的防护等级应分别达到IP54;供电插头和供电插座、 车辆插头和车辆插座插合后,其防护等级应分别达到IP55。 ——爬电距离、电气间隙和穿透密封胶距离应该满足GB/T20234.1中6.17的要求; ——介电强度试验应无闪络和击穿。
GB/T
20234.1-2015
《电动汽车传导充电用连接装置
第1部分:通用要求》6.2
3
GB/T 20234.1-2015
锁止装置
GB/T
20234.1-2015 《电动汽车传导充电用连 接装置 第1部分:通用要求》6.3
在锁止状态下,施加200N的拔出外力时,连接不应断开,且锁止装置不得损坏。
汽车电子电气部件试验DVPV验证试验

汽车电气和电子部件验证试验〔DV/PV试验〕汽车零部件从设计归属上分为两类:1.主机厂设计的零部件;2.供给商设计的零部件;主机厂设计的零部件通常的DFME般计失效模式分析和DV股计验证方案都是有主机厂工程师来写的.供给商设计的零部件通常也叫黑匣子件,DFME股计失效模式分析和DVP设计验证方案都是有供给商来写的.主机厂的会有各种系统级和部件级的设计标准和试验方法.试验方法里面会有具体的试验方法要求,试验设备要求和试验次数要求.供给商的各类试验标准和试验方法要求通常不会直接发给主机厂,尤其国际供给商是DFME勰本只能到供给商处看,比方以前我看博世的DFMEAg至只能到德国总部才让看,不能拍照.验证试验分为DV和PV,DV是DesignVerification设计验证,此时可以是手工件或者模具彳PV是ProductVerification产品验证,必须是模具件,并从供给商的量产生产线上做出来的零件.PV之后的零件再完成PPAP审核,就具备了量产供货资格了.测试要求一般是通过对产品的需求分解而来,这个在整车和部件上都是通用的,这里的需求包含了对市场的预期、国家的法律法规,用户的需求等等.整车方面,中国有针对乘用车的强制检验标准,大概40余项,对于可以在市场售卖的车辆而言,这些试验是必须通过的,大家也可以百度的到,这里不去多说.个别厂商也会对产品做一些其他要求,比方说噪音,振动等,所以这些试验也不可预防.试验根据工程阶段的不同也分为开发性试验和批量批准的试验,两者或有重叠,但是不完全相同,目的也不同.零部件方面,根据位置的不同,所处环境的不同,功能要求的不同以及寿命要求的不同,试验的工程、方法与指标也略有不同.针对车上的每一个零件,都会有经过需求分解,标准〔国家标准、行业标准和企业标准〕分析后得到的试验工程列表,下面我试着就几个方面举些例子:1、车用外饰,下面仅用保险杠作为例子来尝试分析:a、功能方面,汽车保险杠是吸收和减缓外界冲击力、防护车身前后部的平安装置.针对此部件国家有车辆通过性能,行人保护,外部突出物等方面的要求.上面的这些需求决定了保险杠的外形及材料要求,这对这些需求需要进行在强度,韧性,总成的碰撞方面进行验证,不过这些试验的周期一般较短,并且常见于开发阶段.b、由于保险杠位于车辆外部,常年接受阳光照射,风沙侵蚀,石子打击,温湿度变化等方面的影响,所以需要进行类似于阳光辐射,湿热或枯燥气候下的耐久,耐气候循环,石击等方面的试验.耐久试验一般根据寿命要求进行规划.c、由于道路环境的复杂,汽车行驶过程中不可预防的会受到振动的影响,这些影响大致会影响两个方面,一是零件的结构强度方面,另外就是零件的连接强度方面.连接强度就是指零件固定在车身上的方式,比方说卡脚,螺栓,镶嵌以及粘贴等等.2、内饰件,例如仪表板,仅指塑料局部,不涉及仪表显示等部件.a、功能方面,仪表板主要承当了装饰及作为其他零件的基座的功能,因此,零件的颜色要求,尤其是经过环境长时间影响下的颜色变化等尤为重要,当然,这也同产品的定义的寿命有相当大的关系.由于同车身的连接及连接b、虽然内饰件是处于车辆内部,但是还是受到光照,温变乃至湿度变化的影响〔个别企业会把霉变也列入试验工程〕,所以,内饰件也要根据寿命要求及定义的环境进行温湿度变化,光照辐射等试验,但是由于车内的内饰件日光照射的时间及强度不同,其试验指标也不同,大局部分为三个区,直接照射,间接照射及完全照射不到的情况〔有时还会跟车窗的颜色有关系〕.c、同外饰不同的是,由于车内环境是人长时间所处的环境,并且塑料零件在原料或成型的过程中可能引入有毒有害的散发气体,所以内饰件还需要进行例如甲醛,总碳,冷凝,气味等方面的试验.其中,如果我没记错的话,冷凝是针对内饰件的散发物会沉积到车窗上,导致车窗模糊的情况;气味试验是个别厂商会进行的试验,国标暂时对此无要求,但是好似有意见征询.d、另外,内饰件对材料的燃烧性能也有要求,总之不要烧的太快啦.3、电子电气类,这个分类比拟复杂,有例如发动机限制器此类的电子部件,也有例如导航或者CD机这类的舒适性部件,另外还有整车线束和大灯.a、ECU发动机限制器这个部件实在是太复杂了,我这个小学生也只能是道听途说.首先是针对功能方面,整个发动机的性能〔功率,排放等〕都受其限制,那么所有的发动机台架试验根本都是在针对ECU中的程序进行,这是其特殊性,另外,由于其安装位置的关系,可能会接收到较大的振动,并且环境温度较高〔发动机周围〕,这里也影响其零部件的稳固及安装方式的稳固,所以振动,可能是不同温度下的振动就需要特别关注.b、导航,由于导航需要的操作及屏幕的关系,开发人员可能对其屏幕的性能等方面内容进行测试,但这些根本属于开发试验的范畴,以便开发人员确定其型号.c、车用线束的功能为提供能量及传递信号,对于能量而言,例如能量的消耗情况,或者说电压降就是必须关注的内容,对于信号传递而言,减少外界干扰就是重中之重.另外,线束中的塑壳是塑料件,要求阻燃乃至不可燃烧.d、以上是一些专用产品的试验关注方向,主要是一些针对功能及特性的试验,另外,电子器件还有一些根本上都有遵从的试验要求:电子电气试验以及万恶的EMC先说电子电气方面,由于车辆电源在不同阶段〔汽车的启动,怠速,正常运行〕存在不同的变换,个别零部件会受到由于发电机带来的交流变化的影响,另外其他相关负载也可能发生变化,在这些变化中,零部件要求能够正常工作或者正常复位〔根据功能要求确定〕,所以,大致会有一些跃变启动,长时高压,长时低压,甩负荷,交流影响,负载突降等方面的试验内容.e、再说EMC方面,电磁兼容性EMC〔ElectroMagneticCompatibility〕,是指设备或系统在其电磁环境中符合要求运行并不对其环境中的任何设备产生无法忍受的电磁干扰的水平.因此,EMC&括两个方面的要求:一方面是指设备在正常运行过程中对所在环境产生的电磁干扰不能超过一定的限值;另一方面是指器具对所在环境中存在的电磁干扰具有一定程度的抗扰度,即电磁敏感性.〔引自百度〕,EMC式验中包含了预防干扰其他零件以及预防其他零件干扰的试验,具体可参照标准GB/T4365—1995〔电磁兼容术语〕,CISPR等标准.对了,还有防尘防水等.另外,由于所有的产品逃不开材料这个字眼,比方说外饰件或者内饰件的塑料,线束的导线,电子器件的外壳及针脚等.所以,在设计部门定义好材料的要求之后,所有的材料也需要经过材料试验,比方说强度,韧性,热形变等等.对于设计金属的零部件〔例如车身,单片机〕而言,防腐蚀试验也是必须的,大多采用中性盐雾或酸性盐雾加速试验.关于产品的储存,运输也有一些试验标准,总是是覆盖了产品的整个过程.以上也只是介绍了一些常见的试验,事实上,每一个零件都有其试验标准,但是不妨从功能〔需求〕,耐久〔寿命〕,环境〔温度,湿度,光照,振动,电磁,人〕等方面进行分析与归纳.问题二,测试次数或者拓展一下,测试时长是怎么得来的,依我所知有两种途径:a、从实践出发,很多企业的企标都是根据其经验得来,在其公司几十年甚至几百年的开展过程中,肯定也会碰到形形色色的问题,厂商也会根据这些问题的一些数据确定之后产品的试验标准,这也是一家公司的核心啊.b、理论计算,举个简单的例子,一个开关一天会开关一次,那么一年就是365次,3年就是365*3次.当然,这个数据不会这么简单的制定,肯定也会掺进去经验修正的.另外,关于产品的寿命或耐候还存在一些理论,例如金属疲劳的寿命-应力曲线,例如加速寿命试验(采用加大应力的方法促使样品在短期内失效,以预测在正常工作条件或储存条件下的可靠性),对于不同影响效应对产品的影响有不同的函数,例如以温度为变量的加速变量的Arrhenius模型,dM/dt=Ae A(-E0/kT)式中,dM/dt是化学反响速率,A是常数,Ea是引起失效或退化过程的激活能,k是玻尔兹曼常数,T是绝对温度.就可以配合全因子试验方法确定温度试验的时长要求.。
汽车电子电气部件试验 DV V验证试验

汽车电气和电子部件验证试验(DV/PV试验)汽车零部件从设计归属上分为两类:1.主机厂设计的零部件;2.供应商设计的零部件;主机厂设计的零部件通常的DFMEA设计失效模式分析和DVP设计验证计划都是有主机厂工程师来写的。
供应商设计的零部件通常也叫黑匣子件,DFMEA设计失效模式分析和DVP设计验证计划都是有供应商来写的。
主机厂的会有各种系统级和部件级的设计规范和试验方法。
试验方法里面会有具体的试验方法要求,试验设备要求和试验次数要求。
供应商的各类试验规范和试验方法要求通常不会直接发给主机厂,尤其国际供应商是DFMEA基本只能到供应商处看,比如以前我看博世的DFMEA甚至只能到德国总部才让看,不能拍照。
验证试验分为DV和PV,DV是DesignVerification设计验证,此时可以是手工件或者模具件。
PV是ProductVerification产品验证,必须是模具件,并从供应商的量产生产线上做出来的零件。
PV之后的零件再完成PPAP审核,就具备了量产供货资格了。
测试要求一般是通过对产品的需求分解而来,这个在整车和部件上都是通用的,这里的需求包含了对市场的预期、国家的法律法规,用户的需求等等。
整车方面,中国有针对乘用车的强制检验标准,大概40余项,对于可以在市场售卖的车辆而言,这些试验是必须通过的,大家也可以百度的到,这里不去多说。
个别厂商也会对产品做一些其他要求,比方说噪音,振动等,所以这些试验也不可避免。
试验根据项目阶段的不同也分为开发性试验和批量批准的试验,两者或有重叠,但是不完全相同,目的也不同。
零部件方面,根据位置的不同,所处环境的不同,功能要求的不同以及寿命要求的不同,试验的项目、方法与指标也略有不同。
针对车上的每一个零件,都会有经过需求分解,标准(国家标准、行业标准和企业标准)分析后得到的试验项目列表,下面我试着就几个方面举些例子:1、车用外饰,下面仅用保险杠作为例子来尝试分析:a、功能方面,汽车保险杠是吸收和减缓外界冲击力、防护车身前后部的安全装置。
新能源汽车VCU整车控制器实验要求DVP

试验步骤:
1、根据 ISO 16750-2-单线中断规定的方法进行试验。该步骤适用于所有的I/O。对于电源线和地线,中断时长应为15min。
2、连接并运行DUT。断开DUT的连接,然后恢复连接。观察装置断路期间和其后的情况。在DUT系统接口的每条电路分别重复进行。实
验条件如下:
17
开路-单线断线
断开时间:10s±1s
试验名称
试验条件/判断标准
Test Name
试验步骤:
Test conditions / Acceptance Criteria
1、对部件施加Umin
2、相对于部件功率,对典型的I/O模拟装置的电源线施加+1.0 V偏移。
3、对下一个合适的I/O模拟装置重复步骤(2)。
电源偏移
代码丢失。不应出现永久失效的代码。
试验步骤:
1、设置如图11所示的蓄电池电压降曲线。
2、浸润未通电的部件,直至其温度稳定在Tmin。
11
蓄电池电压降
3、部件上电,按照表20变量‘A’的参数绘制蓄电池电压降试验曲线。 4、按照B、C和D,另外重复步骤(3)三次。
5、在Tmax下重复步骤(2)-(4)。参数见附页A11
7
状态变化波形特征
2、在状态变化前、中和后,记录所有输出波形。采用示波器验证输出信号是否完整和部件性能是否正常。 3、对所有可能会发生其他状态变化的部件重复步骤(1)和(2)。
试验标准:
功能状态分类应为Fsc_A。状态瞬变不应损坏下游部件。分析波形时,应考虑意外输出行为和浮动输入。
试验步骤:
1、将部件接在LoadBox上,系统供电电压为12Vdc,将5µH 电感器置于台架试验装置的接地线路上。
DVP计划_汽车电子企业模板文件

9温度循环试验DUT表面无裂纹、起皱、颜色蜕变、变形等;功能状态A级要求10温度冲击试验DUT表面无裂纹、起皱、颜色蜕变、变形等;功能状态A级要求11扫频振动DUT电气性能和功能达到A级要求;按GB/T 2423.22规定的方法进行试验。
工作模式 3.2试验参数循环次数 30 Tmin=-20℃;Tmax=80℃需要严格控制湿度,以避免冷凝:循环曲线如下图上限温度 +95℃下限温度 -40℃循环周期 最高和最低存放温度分别为0.5小时(T=1h),范围内的温度变化试验转换时间为≤60s。
循环次数 100个周期确认工作模式 1.1试验恢复时间为2h产品按下条件进行扫频振动,X、Y、Z三个方向,振动试验后,产品应能正常工作12随机振动DUT电气性能和功能达到A级要求;13机械冲击试验1. DUT不能有任何损坏;2. DUT功能状态应达到A级要求;14跌落试验1. 跌落后如果所有DUT均发生明显的外观损坏,则对DUT功能不做要求,但应报告功能检测结果;2. 试验后如果至少一个DUT没有发生外观损坏,则要求DUT满足产品技术条件中规定的所有功能技术指标;工作模式:3.2实验次数:每个方向10次;试验方法:1. 实验过程中对DUT进行通电进行相关的功能测试;2.实验相关参数:——脉冲形状:半正弦——脉冲参数:500m/s2,6ms工作模式:1.1样品状态:带包装样品数量:带包装、不带包装各3个高度:1000mm跌落次数:每个轴向正反面各一次跌落地面:水泥地面或钢板试验环境 RT工作模式:4.2分别接通Usmin和Usmax产品按下条件进行随机振动,X、Y、Z三个方向,振动试验后,产品应能正常工作,1h/axis试验划。
产品设计阶段DVP测试计划
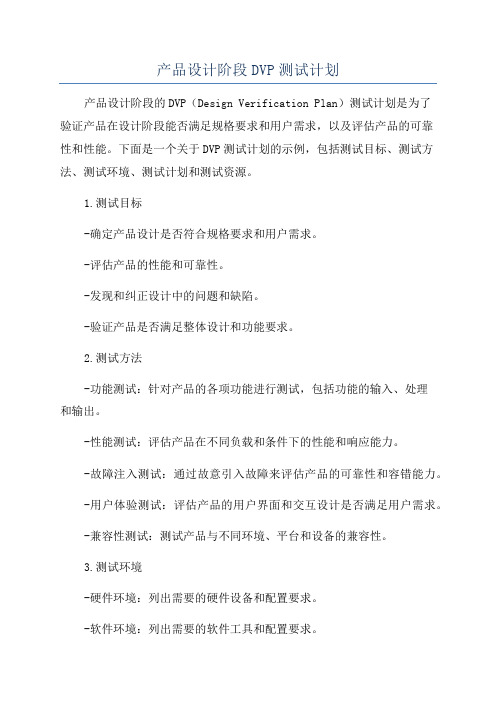
产品设计阶段DVP测试计划产品设计阶段的DVP(Design Verification Plan)测试计划是为了验证产品在设计阶段能否满足规格要求和用户需求,以及评估产品的可靠性和性能。
下面是一个关于DVP测试计划的示例,包括测试目标、测试方法、测试环境、测试计划和测试资源。
1.测试目标-确定产品设计是否符合规格要求和用户需求。
-评估产品的性能和可靠性。
-发现和纠正设计中的问题和缺陷。
-验证产品是否满足整体设计和功能要求。
2.测试方法-功能测试:针对产品的各项功能进行测试,包括功能的输入、处理和输出。
-性能测试:评估产品在不同负载和条件下的性能和响应能力。
-故障注入测试:通过故意引入故障来评估产品的可靠性和容错能力。
-用户体验测试:评估产品的用户界面和交互设计是否满足用户需求。
-兼容性测试:测试产品与不同环境、平台和设备的兼容性。
3.测试环境-硬件环境:列出需要的硬件设备和配置要求。
-软件环境:列出需要的软件工具和配置要求。
-测试数据:列出需要的测试数据和测试用例。
4.测试计划-确定测试阶段和测试周期。
-制定每个测试阶段的具体测试内容和测试要点。
-列出测试人员和责任分工。
-列出每个测试阶段的起止时间和测试任务交付时间。
5.测试资源-测试人员:确定测试团队的成员,包括测试经理、测试工程师和测试操作员。
-测试设备:确定需要的测试设备和硬件配置。
-测试工具:确定需要的测试工具和软件配置。
总结:DVP测试计划是产品设计阶段的重要一环,通过测试可以验证产品设计的可行性和准确性,发现并解决设计中的问题和缺陷,保证产品的性能和可靠性。
一个完整的DVP测试计划包括测试目标、测试方法、测试环境、测试计划和测试资源等要素。
通过制定和执行DVP测试计划,可以确保产品在设计阶段就达到预期的性能和质量要求,为后续的产品开发和生产提供坚实的基础。
DVP策划

零件号平台台架/整车
日期样件类型
试验方法描述具体实验过程测试地点
编制审核批准日期
日期
日期
建议手签,可以打
印建议手签,可以打印
必须手签,实验部门经理经理以上领导签
署
编号:FDLZC13.1.2.4-02/A0
试验目的验证何种样件的某种特性能否达到要求
零件/总成样件数量标准号及名称依据标准号及名称
机型/年责任单位/地点测试输入要求
测试时间测试人员
测试的项目测试具体产品特性
判定合格条件
规定当测试数据达到一定的范围或样件出现某种情况时判定合格,判定合格条件与吉利保持一致。
DVP 策划
试验具体要求
样件特殊要求
测试前对样件特性充分识别,如样件在某种工况下会影响性能货出现
某种情况会影响测试结果
测试条件要求。
新能源汽车DVP测试计划

日期顾客名称序号实验项目要求测试方法测量设备抽样频率测试标准备注外观符合规格书要求导体芯线股数、绝缘皮、电线颜色目视每批参照产品规格书尺寸符合规格书要求测量电线的外径、导体直径千分尺每批参照产品规格书导体电阻≤54.4Ω/KM @0.35mm2≤37.1Ω/KM @0.5mm2≤9.42Ω/KM @1.0mm2≤9.42Ω/KM @2.0mm2≤Ω/KM @4.0mm2≤Ω/KM @6.0mm2试样长度1m,常温(20℃)下测试导体的电阻低电阻测试仪每批参照ISO 6722第6.1规定/EIA 364-23B 规定,具体以产品规格书定义为准阻燃性1.任何一次供火停止后,火焰继续燃烧的时间不超过60s;2.在试验过程中或试验后,无滴落物引燃铺垫在底部的棉层试样长度457mm1按标准要求将试样垂直地夹持于燃烧试验机的金属罩中。
在罩子底部铺上一层6-25mm 厚的医用棉花,棉花层的顶面与火焰蓝色内焰尖端触及试样的那一点的距离不得大于240mm.2用喷灯向试样供火15s,停止15s,反复5循环。
如果试样上的火焰在15秒或更短时间内熄灭,那喷灯在停火15s,开始下一次供火,如果试样上的火焰超过15秒s ,则待垂直燃烧试验机每批可参照ISO 6722第12规定和GB12666.2-1990第4节规定,具体以其所用规格导线对应的标准实验方法为准热老化绝缘层卷绕后无破损,加压后无击穿现象取3段长350mm 电线悬挂在试验箱内,在131±4℃温度下加热240h,恢复到常温16h 后反向弯曲, 浸在盐水里10min 后施加1min 耐压高温试验箱每批可参照ISO 6722第10.1规定,具体以其所用规格导线对应的标准实验方法为准低温冲击绝缘层冲击后无破损,加压后无击穿现象1、从成品电线上截取长为1200mm 的试样3段,并列放置在冲击工装上.2、试样及试验装置在(-40±2)℃低温槽放置16h ,若试样及装置在试验前已达到该低温,则放置时间可降至4h 。
新能源汽车电驱动实验要求DVP

按表1选取
机应能正常工作,满足GB/T29037-2012的规定
按照GB/T18655-2010、GB/T17619-1998中规定进行试验 符合产品技术协议及相关国标要求
接地检查方法和量具要求按照GB/T 13422-2013中5.1.3进 行,量具推荐采用毫欧表
按照GB/T 3859.1-2013中7.5.3的要求进行
GB/T 18488.2-2015
2
电机控制器绝缘电阻
GB/T 18488.2-2015
3
绝缘电 阻
驱动电机定子绕组对机壳 的绝缘电阻
GB/T 18488.1-2015
4
驱动电机定子绕组对温度 传感器的绝缘电阻
GB/T 18488.1-2015
5
工频耐电压
GB/T 18488.1-2015
6
耐电压
驱动电机绕组的匝间冲击 耐电压
45 减速箱 差速可靠性试验
46
总成静扭强度试验
47
高速性能试验
QC/T1022-2015《纯电动 乘用车加速器总成技术条
件》
QC/T1022-2015《纯电动乘用车加速器总成技术条件》 满足图纸及技术协议要求,满足国标技术要求
48
加速噪音试验
49
超速性能试验
50
滑行噪声试验
51
CAN总线测试
依据通讯协议
52
可靠性
GB/T29037-2012
53
EMC
五、安全测试
1
安全接地检查
GB/T18655-2010、 GB/T17619-1998
2
电机控制器的保护功能
3
被动放电时间
4
主动放电时间
DVP试验方案模板
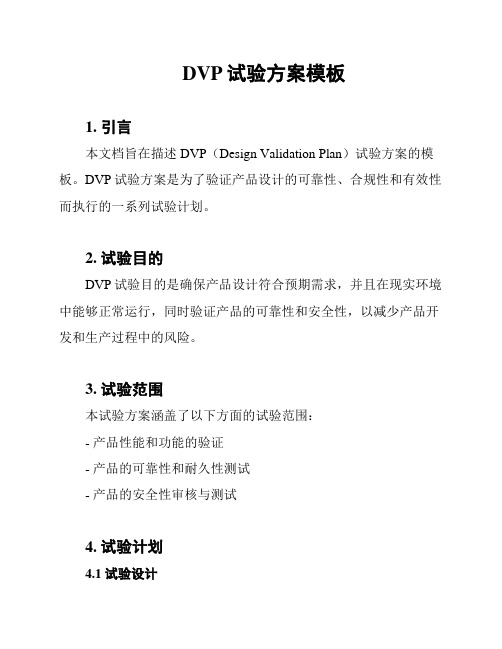
DVP试验方案模板1. 引言本文档旨在描述DVP(Design Validation Plan)试验方案的模板。
DVP试验方案是为了验证产品设计的可靠性、合规性和有效性而执行的一系列试验计划。
2. 试验目的DVP试验目的是确保产品设计符合预期需求,并且在现实环境中能够正常运行,同时验证产品的可靠性和安全性,以减少产品开发和生产过程中的风险。
3. 试验范围本试验方案涵盖了以下方面的试验范围:- 产品性能和功能的验证- 产品的可靠性和耐久性测试- 产品的安全性审核与测试4. 试验计划4.1 试验设计根据产品需求和标准要求,设计相应的试验方案和流程,包括试验环境、试验设备、试验样本和试验方法等。
4.2 试验执行按照试验计划,组织并执行试验,记录试验数据和结果,并准确记录试验过程中的任何异常情况。
4.3 试验评估基于试验结果和数据,对产品的性能、功能、可靠性和安全性进行评估和分析,确定产品的优点和改进空间,并提出相应的改进措施。
5. 质量管理试验过程应遵循质量管理体系的要求,确保试验过程的可控性和标准化,包括试验设备的校准和维护、试验人员的培训和技能提升、试验环境的控制等。
6. 安全管理试验过程中应遵守安全管理规范,确保试验人员的人身安全和试验设备的安全性,包括试验操作的风险评估和安全防护措施的采取。
7. 试验报告根据试验计划和评估结果,撰写详细的试验报告,包括试验目的和背景、试验设计和方法、试验结果和数据分析、评估和改进建议等内容。
8. 试验时间表根据产品开发和生产计划,制定试验时间表,确保试验进度和产品上市时间的协调。
9. 试验资源确定试验所需的人力、物力和财力资源,包括试验设备和设施、试验人员和试验费用等。
10. 试验风险评估对试验过程和试验结果可能出现的风险进行评估和分析,制定相应的应对措施,以最大程度地减少试验风险和不确定性。
11. 试验审批试验方案和试验报告的编制、执行和评估需要经过相关部门的审批,确保试验过程和结果的可靠性和合规性。
DVP试验大纲实验计划(发动机左右护板)

10.8
2-8
落锤冲击性试验 Impact strength
QC/T 15-92(5.7.3.1)
10.8
2-9
燃烧特性 Flammability
GB 8410-1994
燃烧试验箱/试样支架
10.8
2-11
耐刮伤试验 Scratch resistance 刚性试验 Rigid test
QC/T 15-92(5.9.3.1)
试验设备 Test Equipment
样件 数量 Qty Sampl es
试验完成时间
2-13
耐水性试验 Water resistance
QC/T 15-92(5.3)
先按GB2918标准环境下预处理试样,然后浸渍在充满40±1℃水的恒温试 试验过后,产品不能出现尺寸变化以及产品外观出现 验槽中,至少放置200h后取出,用干燥的清洁布擦干,然后让其在标准环 龟裂、破裂、剥离、溶胀、释出、发白等缺陷. 境下冷却1h. 1,试验标准环境:温度20±2℃,湿度65±5℅;2,取样:(1)测试前试样需 放置在标准环境下至少24h以上;(2)试样尺寸为100×100×产品厚度,重 量在20g以上;(3)泡沫类试样尺寸为10×10×10,重量20g以上;(4)如果 满足等级不得低于第四级,即有轻微的但不明显的气味; 试样重量小于20g,则需取整个产品作为试样;3,测试:将试样放到一个密 封容器中,然后放置到温度为80±2℃的热控箱中保温3h后取出,由至少3 个人进行评价气味性程度等级.
试验计划
客户/Customer: 项目名称/Project Name: 供应商/Supplier:
협 력 업 체
序号 NO.
试验项目 Test Item
产品设计阶段DVP 测试计划

电流、负载转速、堵转力矩、堵转电流、最低启动
电压 、静态扭矩
测试电压:额定电压12V
测试环境:常温25± 5度,RH65%±20%
电压、 测试方法:
电机基本特性 扭力计 1.作动方向通电后目视,
1.启动电压:1.2V
1
测试
、转速 2.空载电流、空载转速、负载电流、负载转速、堵
2.其他参照外形图
仪 转力矩、堵转电流使用测功机测试(标准参考图纸
9
绝缘耐压
≥100MΩ, AC500V漏电
5
试仪 试绝缘耐压,
流≤1mA,
72小时后,外壳不允许
盐雾试
10
盐雾测试
按GB/T 10125-1997中NSS的规定进行盐雾试验 有红锈(冲压断面除外
5
验机
)
1.电机在跌落后,外观
不可有损伤
1.将包装好的电机从750mm高度水平跌落在水泥地 2.电机无异音及噪音值
判定要求:满足QZTB 依照QZTB 04.001-2014车辆电器电子零部件EMC
04.001-2014车辆电器 要求的实验方法,
电子零部件EMC要求;
射频辐射发射 -天线测量法
(EMI)
满足QZTB 04.001依照QZTB 04.001-2014车辆电器电子零部件EMC
2014车辆电器电子零部 要求的实验方法;
2014车辆电器电子零部 要求的实验方法;
件EMC要求;
I/O线瞬态抗 干扰(EMS)
满足QZTB 04.001依照QZTB 04.001-2014车辆电器电子零部件EMC
2014车辆电器电子零部 要求的实验方法;
件EMC要求;
静电放电抗干 扰(EMS)
DVP试验计划指南

DVP试验计划指南1. 引言本文档旨在为DVP(设计验证计划)试验的策划人员提供指南,以确保试验的有效性、可行性和准确性。
DVP试验计划旨在验证设计的可靠性,评估产品的性能和功能,并在产品进入下一阶段之前发现并解决潜在问题。
2. 背景在产品设计和开发过程中,DVP试验是非常重要的一部分。
通过对设计进行验证,可以减少产品开发中的风险和不确定性,并提高产品的质量和可靠性。
因此,制定一个详细的DVP试验计划是必要的。
3. 试验目标在制定DVP试验计划之前,需要明确试验的目标。
试验目标应该明确、具体、可以量化,并与产品的设计需求相一致。
例如,试验目标可能包括验证产品在不同环境条件下的工作性能,验证产品在预定使用寿命内的可靠性等。
4. 试验方案DVP试验方案应该详细描述试验的内容、方法和过程。
试验方案应该根据试验目标确定试验的样本数量、测试参数、测试方法和测试设备等。
同时,需要制定试验的时间计划,确保试验能够按时启动和完成。
5. 试验评估试验评估是对试验结果进行定量和定性分析的过程。
在试验评估中,需要比对试验结果与设计要求或标准的要求进行对比,并进行合理的数据处理和统计分析。
从试验结果中,可以得出结论和建议,用于指导产品的改进和优化。
6. 试验报告试验报告是对整个试验过程和结果的总结和描述。
试验报告应该包含试验目标和方法、试验结果和评估、结论和建议等内容。
试验报告的编写应遵循相关科学技术文献的规范,并表达清晰、准确、简洁。
7. 质量控制为了确保试验结果的可靠性和准确性,需要进行质量控制。
质量控制包括试验设备的校准、试验操作员的培训和资质管理、试验数据的可追溯性和可验证性等。
对于重要的试验项目,还需要进行重复试验和同行评审等措施。
8. 试验安全在进行DVP试验时,安全是一个非常重要的因素。
试验人员应该严格遵守安全操作规程,使用合适的个人防护装备,并确保试验过程中不会对人员和设备造成危害。
9. 结论通过制定和执行DVP试验计划,可以有效地验证产品的设计,并评估产品的性能和功能。
新能源汽车线束项目计划书

新能源汽车线束项目计划书一、项目背景和目的:当前,全球环境污染和能源压力日益加剧,推动新能源汽车的发展已成为全球汽车产业的重要目标之一、新能源汽车的核心技术之一是电气线束技术,它是连接车辆各个电气系统的重要组成部分。
为了满足新能源汽车市场发展的需求,本项目旨在建立一套完整的新能源汽车线束生产工艺和品质控制体系,为新能源汽车线束的大规模生产提供支持。
二、项目范围和目标:1.项目范围:本项目计划开展新能源汽车线束的设计、开发、制造和测试等工作。
2.项目目标:-建立新能源汽车线束的设计、开发、制造和测试体系,提高生产效率和品质水平;-提供符合国际标准和行业规范的新能源汽车线束产品;-提高新能源汽车线束的性能,满足市场需求。
三、项目内容和主要步骤:1.设计阶段:-分析市场需求和竞争状况,制定线束设计的技术要求和产品标准;-进行线束的结构设计和电气布局,确保各个系统之间的正常连接;-制定线束的材料选择和工艺要求。
2.开发阶段:-建立新能源汽车线束的模具和设备制造计划;-进行线束样件的制造和测试,优化设计方案;-开展适应性测试,确保线束在各种工况下的稳定性和可靠性。
3.制造阶段:-建立新能源汽车线束的生产流程和质量控制体系;-选购生产设备和制定生产计划;-开展线束的批量生产,严格控制质量,满足交付要求。
4.测试阶段:-设立线束的实验室,开展性能测试和可靠性验证;-进行线束的耐久性测试,模拟车辆使用环境;-提出改进意见和措施,优化线束的设计和制造工艺。
四、项目预算和资源规划:1.资金预算:本项目预计需要资金X万元,主要用于设备采购、人员培训和原材料采购等方面。
2.人力资源:本项目需组建一支由技术人员和生产人员构成的团队,共计X人,其中技术人员X人,生产人员X人。
3.设备资源:本项目需要购买新能源汽车线束的制造设备,包括模具、线束加工设备、测试设备等。
五、项目实施计划和风险管理:1.实施计划:本项目计划从资金申请、团队组建、设备采购、线束设计、生产组织等方面展开,并按照前期设计、中期开发、后期制造和测试的阶段进行有序推进。
设计验证计划DVP

3Байду номын сангаас
AKP-C88
不通电,接头不处于连接状态
研发部
4
高温试验
QC/T1037-2016
样品不应出现开裂、变色,变形、膨胀,功能测试满足要求
样品在105℃条件下放置1 450 h保持通电/设备:电热恒温鼓风干燥箱
3
AKP-C88
通恒定额定交流电40A
研发部
5
高温高湿试验
QC/T1037-2016
有限公司
设计验证计划
编号
XH-C2-01-08
表号
用户名称
上海捷能汽车技术有限公司
产品名称
充电座
产品图号
FSLEV-XS-047-030
产品规格
AKP-C88-030-030
序号
试验
种类
试验项目
执行标准
试验要求
重要度分级
试验设备
试样要求
实施
部门
反应
计划
备注
数量
规格
状态
1
机械
机械冲击试验
QC/T1037-2016
参照DIN 53509-1,方法A
3
AKP-C88
研发部
7
高压水喷射试验
试验结束后
自然风干样件,不应出现开裂、
变色、变形、膨胀或电化学腐蚀的情况,功能
测试需满足要求。
参照DIN 40050,IP等级为X9K
3
AKP-C88
研发部
8
防尘试验
试验结束后,样品功能需满足设定要求
参照DIN 40050,IP等级6KX
样品不应出现开裂、变色、
变形、膨胀,金属部件不应出现氧化或电化学腐蚀,功能测试满足要求。
汽车电子电气部件试验DVV验证试验

汽车电气和电子部件验证试验(DV/PV试验)汽车零部件从设计归属上分为两类:1.主机厂设计的零部件;2.供应商设计的零部件;主机厂设计的零部件通常的DFMEA设计失效模式分析和DVP设计验证计划都是有主机厂工程师来写的。
供应商设计的零部件通常也叫黑匣子件,DFMEA设计失效模式分析和DVP设计验证计划都是有供应商来写的。
主机厂的会有各种系统级和部件级的设计规范和试验方法。
试验方法里面会有具体的试验方法要求,试验设备要求和试验次数要求。
供应商的各类试验规范和试验方法要求通常不会直接发给主机厂,尤其国际供应商是DFMEA基本只能到供应商处看,比如以前我看博世的DFMEA甚至只能到德国总部才让看,不能拍照。
验证试验分为DV和PV,DV是DesignVerification设计验证,此时可以是手工件或者模具件。
PV是ProductVerification产品验证,必须是模具件,并从供应商的量产生产线上做出来的零件。
PV之后的零件再完成PPAP审核,就具备了量产供货资格了。
测试要求一般是通过对产品的需求分解而来,这个在整车和部件上都是通用的,这里的需求包含了对市场的预期、国家的法律法规,用户的需求等等。
整车方面,中国有针对乘用车的强制检验标准,大概40余项,对于可以在市场售卖的车辆而言,这些试验是必须通过的,大家也可以百度的到,这里不去多说。
个别厂商也会对产品做一些其他要求,比方说噪音,振动等,所以这些试验也不可避免。
试验根据项目阶段的不同也分为开发性试验和批量批准的试验,两者或有重叠,但是不完全相同,目的也不同。
零部件方面,根据位置的不同,所处环境的不同,功能要求的不同以及寿命要求的不同,试验的项目、方法与指标也略有不同。
针对车上的每一个零件,都会有经过需求分解,标准(国家标准、行业标准和企业标准)分析后得到的试验项目列表,下面我试着就几个方面举些例子:1、车用外饰,下面仅用保险杠作为例子来尝试分析:a、功能方面,汽车保险杠是吸收和减缓外界冲击力、防护车身前后部的安全装置。
- 1、下载文档前请自行甄别文档内容的完整性,平台不提供额外的编辑、内容补充、找答案等附加服务。
- 2、"仅部分预览"的文档,不可在线预览部分如存在完整性等问题,可反馈申请退款(可完整预览的文档不适用该条件!)。
- 3、如文档侵犯您的权益,请联系客服反馈,我们会尽快为您处理(人工客服工作时间:9:00-18:30)。
1、在不工作的状态下进行,按 GB/T2423.17的规定,将试样放在 盐水喷雾试验机试验箱内,用于 盐雾试验机 喷雾的盐溶液采用氯化钠和蒸馏 水配制,浓度为(5±0.1)%,PH 值在6.5-7.2之间.2、试验设备的 工作试验空间内的温度设置为35 ±2℃,试验时间设置为48h。 试样放在85±2℃的高温箱内,时 符合QC/T 29106-2004 耐高温 间为8h,再在常温下放置24h后, 高温试验箱 中4.7、4.8、4.10规定 检验电线束。 试样放在-40±2℃的高温箱内, 符合QC/T 29106-2004 耐低温 低温试验箱 时间为8h,再在常温下放置24h 中4.7、4.8、4.10规定 后,检验电线束。 产品按GB/T 2423.34的规定,在 耐温度、湿 符合QC/T 29106-2004 不工作状态下,在-10℃~65℃之 高温试验箱、 度循环变化 中4.7、4.8、4.10规定 间进行10个循环(每个循环为 低温试验箱 24h)的耐温度、湿度循环变化性 QC/T 29106-2004中 4.10的规定且持续时间 为48h的耐盐雾性能试验 耐盐雾试验 后,电线束中线路导通 率为100%,无短路、错 路现象。
压接高度 线束 压接剖面
符合产品设定的高度
千分尺
每批
参照VW60330规范 3.3.4.1规定
符合QC/T 29106-2004 中4.4.3的规定
金相试样抛光 机
每批
QC/T 29106-2004中5.6规定
电压降
5A ≤3mV(20AWG)
电压降测试仪
每批
QC/T 29106-2004中5.7规定
每批
参照ISO 6722第6.1规定/EIA -23B规定,具体以产品规格书 定义为准
每批
可参照ISO 6722第12规定和 GB12666.2-1990第4节规定,具 体以其所用规格导线对应的标准 实验方法为准
每批
可参照ISO 6722第10.1规定,具 体以其所用规格导线对应的标准 实验方法为准
新能源汽车线束DVP测试计划
产品名称 料号/型号 一:材料性能 序号 实验项目 外观 尺寸 要求 符合规格书要求 符合规格书要求 测试方法 导体芯线股数、绝缘皮、电线颜 色 测量电线的外径、导体直径 测量设备 目视 千分尺 抽样频率 每批 每批 测试标准 参照产品规格书 参照产品规格书 备注 BMU主线束 xxxxxxxx 日期 顾客名称 2016.07.09
1次/年 1次/年
可参照ISO 29864-2007规定,具 体以客户规定标准实验方法为准 可参照ISO 29864-2007规定,具 体以客户规定标准实验方法为准 QC/T 29106-2004中4.4.1、 4.4.3、4.4.6.1、4.5.2、4.5.3 、4.5.5、4.6、4.7、4.8、4.9 规定或客户规定的公差 QC/T 29106-2004中4.2规定或客 户规定的公差 QC/T 29106-2004中4.10规定 参照EIA-364-21C试验方法进行试 验 参照EIA-364-20C试验方法进行试 验
每批
可参照ISO 6722第8.2,具体以其 所用规格导线对应的标准实验方 法为准
每批 每批 每批
参照产品规格书 参照产品规格书 参照EIA-364-23B中试验方法进行 试验
绝缘电阻
≥1000MΩ
连接器 耐电压测试 无击穿
温升试验
≤30℃
耐高温
Δ R≤20mΩ
1.公端子与母端子对插连接;2.在 低电阻测试仪 每一对通路上加上20mV电压和 100mA的电流;3.测量公母端子接 1.在连接器的任一P脚与相邻的其 它P脚之间,施加500VDC电压;测 量两者之间的绝缘电阻值 2.在连 绝缘电阻测试仪 接器的任一P脚与外壳之间,施加 500VDC电压,测量两者之间的绝 1.在连接器的任一P脚与相邻的其 它P脚之间,施加500VAC电压,维 持1分钟的时间。2.在连接器的任 耐压测试仪 一P脚与外壳之间,施加500VAC电 压,维持1分钟的时间。 1.连接器与其对应座互配连接于 负载电路中;2.在测试电路中加上 温升测试仪 额定电流2A;3.经过96小时测试, 测量此过程中最大温升值 1.将基座公母互配,测量初始接 触电阻值 高温试验箱 2.将试样放入105±2℃的试验箱 中96小时 3.测试试样的接触电阻 目视检验产品外观 参照规格书或样品对比检验各项 尺寸 取3段长为500mm的波纹管样品, 存放于100℃的热空气中,存放时 间≥240h。 参照UL 94 V-0测试方法 目视 数显卡尺
每批
参照EIA-364-21C试验方法进行试 验
每批
参照EIA-364-20C试验方法进行试 验
每批
参照EIA-364-70C试验方法进行试 验
每批
可参照EIA-364-32C/EIA-36423B试验方法进行试验,具体以客 户规定标准实验方法为准
波纹管
无毛刺、无破损、无变 形、无油污 尺寸 尺寸符合规格要求 波纹管不可以发生脆变 。在常温下以2倍于波纹 热时效试验 管径的半径弯曲波纹管 时,不允许出现断裂和 裂纹以及影响使用的缺 外观 阻燃性 外观 尺寸 拉伸强度 符合94V-0要求
由供应商提供 测试报告验证 由供应商提供 测试报告验证
目视检验产品外观 用钢尺(卷尺)测量线束每个尺 寸或用检验工装板检验线束尺寸 用电测机(导通测试台)测量线 束的每个回路 1.在线缆组件的任一P脚与相邻的 其它P脚及地线之间,施加500VDC 电压;测量两者之间的绝缘电阻值 1.在线缆组件的任一P脚与相邻的 其它P脚及地线之间,施加500VAC 电压,维持0.1秒的时间 拉脱力:沿导线轴线方向,用示 值误差不大于1%的拉力试验机检 测,拉力试验机的位移应匀速运 动,速度为25mm/min-100mm/min 。 撕裂力:将最细 的导线夹在示值误差不大于1%的 拉力试验机的运动夹头,其余导 线夹在固定夹头,运动夹头匀速 运动,速度为25mm/min用千分尺测试端子压接后最低点 间的高度值 1、将样品从前压接翼中间位置截 断,取其中一侧作为试样,其断 面应磨平,并作化学腐蚀处理, 直至能够完全显示截面状态;2、 将做好的试样断面用显微镜观察 1、在距离端子前压接翼中间位置 至电线75mm长的为准剥开线皮并 钎焊牢固。2、测量电压降,再减 去75mm导线的电压降
目视 钢尺、卷尺、 检验工装板 用电测机、导 通测试台、万 线缆测试机
每批
全尺寸 通断 绝缘
每批 每批 每批
耐压
漏电流IA≤1mA.
线缆测试机
每批
F≥55N @0.35mm2 端子与线材 F≥70N @0.5mm2 拉脱力 F≥250N @2.0mm2
拉力试验机
每批
QC/T 29106-2004中5.5规定
每批 每批 可参照QCT413-2002中4.10.2条 规定,具体以客户规定为准 参照UL 94 V-0标准/GB84102006 第4条规定/FMVSS 302标准 进行燃烧性能试验 参照产品规格书 参照产品规格书 可参照ISO 29864-2007规定,具 体以客户规定标准实验方法为准 可参照ISO 29864-2007规定,具 体以客户规定标准实验方法为准 可参照ISO 29864-2007规定,具 体以客户规定标准实验方法为准 由供应商提供 测试报告验证 由供应商提供 测试报告验证 由供应商提供 测试报告验证
导体电阻
阻燃性 线材
热老化
低温冲击
外观 尺寸 接触电阻
≤54.4Ω /KM @0.35mm2 ≤37.1Ω /KM @0.5mm2 ≤9.42Ω /KM @1.0mm2 试样长度1m,常温(20℃)下测试 低电阻测试仪 ≤9.42Ω /KM @2.0mm2 导体的电阻 ≤Ω /KM @4.0mm2 ≤Ω /KM @6.0mm2 试样长度457mm 1按标准要求将试样垂直地夹持于 燃烧试验机的金属罩中。在罩子 1.任何一次供火停止 底部铺上一层6-25mm厚的医用棉 后,火焰继续燃烧的时 花,棉花层的顶面与火焰蓝色内 间不超过60s; 焰尖端触及试样的那一点的距离 垂直燃烧试验 2.在试验过程中或试验 不得大于240mm. 机 后,无滴落物引燃铺垫 2用喷灯向试样供火15s,停止15s, 在底部的棉层 反复5循环。如果试样上的火焰在 15秒或更短时间内熄灭,那喷灯 在停火15s,开始下一次供火,如 果试样上的火焰超过15秒s,则待 取3段长350mm电线悬挂在试验箱 绝缘层卷绕后无破损, 内,在131±4℃温度下加热240h, 高温试验箱 加压后无击穿现象 恢复到常温16h后反向弯曲, 浸 在盐水里10min后施加1min耐压 1、从成品电线上截取长为1200mm 的试样3段,并列放置在冲击工装 上.2、试样及试验装置在(-40± 绝缘层冲击后无破损, 2)℃低温槽放置16h,若试样及 低温试验箱 加压后无击穿现象 装置在试验前已达到该低温,则 放置时间可降至4h。3、拉动手柄 让砝码在100 mm高度落下冲击样 件.4、浸在盐水里10min后施加 符合规格书要求 颜色、印字、外型等 目视 符合规格书要求 ≤20mΩ 所有规格书标识尺寸 千分尺
每批/依客 户要求
QC/T 29106-2004中5.15规定
每批
QC/T 29106-2004中5.10/5.11
每批
QC/T 29106-2004中5.10/5.11
每批
QC/T 29106-2004中5.13和 QC/T413-2002中 4.11
高温试验箱
每批
燃烧试验机 目视 数显卡尺 拉力试验机 拉力试验机
每批 每批 每批 1次/年 1次/年 1次/年
无毛刺、无破损、无变 目视检验产品外观 形、无油污 参照规格书或样品对比检验各项 尺寸符合规格要求 尺寸 >100 N/25mm
胶带
断裂伸长率 >10 % 缠绕试验 无开胶,无脱落 将胶带放置于 150℃环境中 6小 时