精益管理之快速换线课件
精益生产之快速换线概论
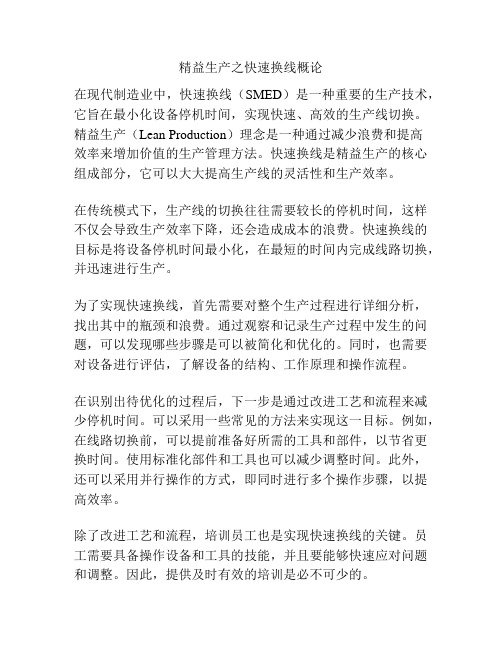
精益生产之快速换线概论在现代制造业中,快速换线(SMED)是一种重要的生产技术,它旨在最小化设备停机时间,实现快速、高效的生产线切换。
精益生产(Lean Production)理念是一种通过减少浪费和提高效率来增加价值的生产管理方法。
快速换线是精益生产的核心组成部分,它可以大大提高生产线的灵活性和生产效率。
在传统模式下,生产线的切换往往需要较长的停机时间,这样不仅会导致生产效率下降,还会造成成本的浪费。
快速换线的目标是将设备停机时间最小化,在最短的时间内完成线路切换,并迅速进行生产。
为了实现快速换线,首先需要对整个生产过程进行详细分析,找出其中的瓶颈和浪费。
通过观察和记录生产过程中发生的问题,可以发现哪些步骤是可以被简化和优化的。
同时,也需要对设备进行评估,了解设备的结构、工作原理和操作流程。
在识别出待优化的过程后,下一步是通过改进工艺和流程来减少停机时间。
可以采用一些常见的方法来实现这一目标。
例如,在线路切换前,可以提前准备好所需的工具和部件,以节省更换时间。
使用标准化部件和工具也可以减少调整时间。
此外,还可以采用并行操作的方式,即同时进行多个操作步骤,以提高效率。
除了改进工艺和流程,培训员工也是实现快速换线的关键。
员工需要具备操作设备和工具的技能,并且要能够快速应对问题和调整。
因此,提供及时有效的培训是必不可少的。
在实践中,快速换线可以带来许多好处。
首先,它能够增加生产线的灵活性。
当市场需求发生变化时,可以快速切换生产线,满足不同产品的需求。
其次,快速换线可以减少生产线的停机时间,提高生产效率。
这将减少生产成本,并增加企业竞争力。
最后,快速换线也有助于提高产品质量。
通过减少故障和人为错误的发生,可以提高产品的一致性和可靠性。
综上所述,快速换线是精益生产中的重要技术,它通过最小化设备停机时间来实现快速、高效的生产线切换。
它可以增加生产线的灵活性,提高生产效率,并且有助于提高产品质量。
通过改进工艺和流程,并提供适当的培训,企业可以实现快速换线,并在竞争激烈的市场中获得优势。
SMT快速换线 ppt课件
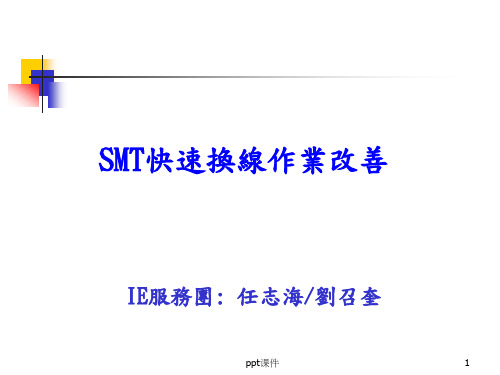
返回
ppt课件
9
三. 問題分析
答B﹕確認feeder是否放在正確的位置(料軌)﹔ 問﹕為什么feeder 會放錯位置? 答﹕物料多,作業員不小心﹔ 問﹕有無更好的方法? 答﹕作業員按順序將feeder上料軌;作業員掃All
Parts系統, 檢查是否錯。
返回
ppt课件
OP領 料
料單 與機 器程 式比 對
6’
3‘
上架
停機 下料
1’
打首件
OP測
3’
元件值 3’
換正式 用頂PIN
正式生產
掃描,IPQC核 對
7’ 3’
換首件 頂PIN
換線時間 長20分鐘
ppt课件
19
六. 可推廣性
所有SMT線都可應用,但應對不同的SMT機 和換線模式進行具體分析.以找出合理的快 速換線方案.
物料種類多
Feeder未按順
作業不規范
序擺放(kitting) 物料裝Feeder
不到位(kitting)
料
法
快速首件檢查
ppt课件
5
三. 問題分析
作業區分及改善方向:
項目 作業內容 1 Kitting 倉備料 2 OP領料
內部作業 外部作業 改善方向 是 優化作業 是
3 停機
是
4 下料 5 上架 6 掃描
11
三. 問題分析
答﹕B.確認元件是否錯料,符合規格﹔ 問﹕為什么元件會錯料,不符合規格? 答﹕廠商混料;來料不良;IQC貼錯料號標簽﹔ 問﹕有無預防措施? 答﹕有。
1) IQC 進料檢查(測值); 2) Kitting 倉對元件測值;
返回
SMED培训课件

2拆口、心模, 3到模具房 冷模钢片,自 拿取口心模 动盖管帽机夹 安装 具
50
15
第二步
第三步
进一步选择改善点
4重装冷模、5找自动
钢片
盖管帽
机夹具
然后安
装
6模具加 热
30
25
30
第四步 第五步 第七步
PS:进一步缩小课题改善范围,选择改善对象;
三、快速换模步骤与措施
案例分析:
类别
第一步 第二步
第三步
现状把握-内部作业1
❖ 有工典作型问的题存1---在10就5E线有停改机机善台的外存管缺在加热装置
❖ 与工作是一体的,不是额外的任务和负担
❖ 不进行改善的话 工作就会落, 就永远辛
苦
有空, 改善不一定能做得好
愈是忙碌的单位, 需做改善的愈多
问题点说明:长期停产的机台,外管模具连接位加热圈没有装回相应的位置
案例分析:
程序分析
开始
计划中心下 单
计划员排产
车间接单做 准备工作
对生产设备 进行检点
人员安排
相设关设备 加热
核对信息
产品包装入 库
检测
调整 对中
挤料
换模具
152(分钟)
完成
原材料准备
后面仅仅对换
(要求总共用时是200分钟) 模展开分析
必要的操作步骤共14步,其中主要操作占了7步“蓝色标注”。
其中真正产生效益即是提高转产时间为“上述7步骤”,其他为 必要的辅助作业。
机台模具拆下多时,不知道是何情况,没有相应的说明与记录,下次排产 开机时就会影响进度。
三、快速换模步骤与措施
*是一种能有效缩短产品切换时间的理论
精益管理之快速换线课件
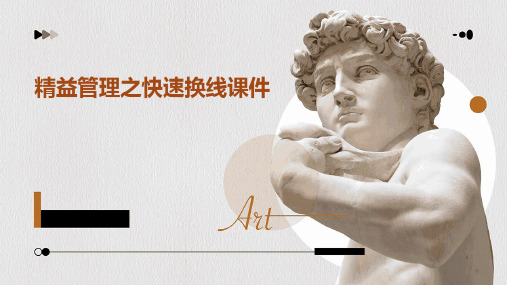
03
关注长期效益
企业应关注长期效益,而非短期成本节约,持续推进精益管理与快速换线。
01
领导力支持
企业领导应给予快速换线和精益管理足够的重视和支持。
02
实践与理论相结合
在推进快速换线和精益管理过程中,注重理论与实践相结合。
THANKS
感谢您的观看。
持续优化
将优化后的生产流程标准化,确保操作的一致性和可靠性。
标准化操作
定期评估生产流程,发现潜在问题并持续改进。
持续改进
对员工进行培训,提高员工的精益管理意识和技能,推广精益管理理念和方法。
培训与推广
04
CHAPTER
案例分析与实践
实施过程
该企业首先对生产线进行分析,识别出换线的瓶颈环节,然后制定针对性的改进措施,如标准化操作、减少换线时间等。
精益管理之快速换线课件
目录
精益管理概述快速换线的挑战与解决方案精益管理在快速换线中的应用案例分析与实践总结与展望
01
CHAPTER
精益管理概述
精益管理起源于日本丰田汽车公司的生产方式,旨在通过消除浪费、提高效率和灵活性来满足客户需求。
起源
精益管理强调价值流、流动性和价值交付,以最小成本创造最大价值,实现持续改进和卓越运营。
优化设备与工具
如5S管理、看板管理、全面生产维护等,提高生产现场的管理水平,确保快速换线的顺利进行。
采用精益管理工具
03
CHAPTER
精益管理在快速换线中的应用
找出生产流程中的瓶颈环节,如设备故障、物料短缺等。
识别瓶颈
针对瓶颈采取改进措施,如设备维护、工艺改进等。
改进措施
Байду номын сангаас
精益管理之快速换线
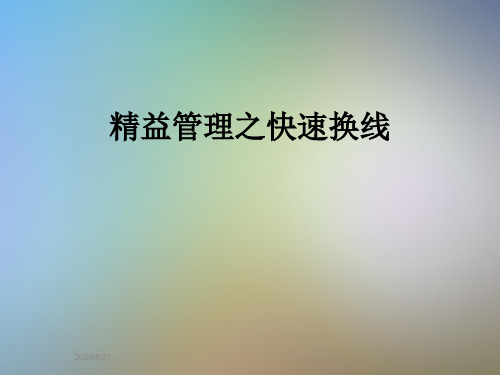
• T=T2-T1-BT*N=60(20S×30)/60=50分钟
快速换线实战演练
运用4M1E原则进行鱼骨图分析
人
机修
生产管理
品管
PMC
技术员
机
环
普通设备
性能检查
照明
提前调试
IE
特殊设备
5S 温度
作业条件
物料检测 来料追踪
重点工艺改善 物料配套
流程编排图
标准作业指导书 产前培训
组长 技转人员
品管
IE
舊款第一道工序員工完成舊款最後一件即開始正式 轉新款,长安排組內員工按照完成舊款時間先後順 序陆续把设备按編號順序擺放好 跟踪旧型体清尾工作,安排工人开始转换新型体并 指导工人操作,说明品质要求.
随时跟进各工段的品质管控
协助生产组长编排工段,记录换线时间
机修人员
协助生产组长及员工进行机器安排,换线原地待命
精益管理之快速换线
2020/8/21
快速换线概念解析
➢什么是3P流程? Production Preparation Process
生产准备流程,它是精益生产中的一个比较重要的 工具,是一个采用团队 方式的生产流程设计系统.
√1
产前准备 流程
P
2
产品生产 流程
D
3
产品检验 流程
C
4
产品入库 流程
快速换线实战演练
➢转款三天之后I E负责测时做 线平衡改善,运用ECRS四原则平 衡各工段,提高产线效率.
快速换线实战演练
快速换线活动总结
➢成果汇报
换线组别
A
换线型体
001
快速换线及Cell线介绍描述讲课讲稿

快速换线的定义和基本原理—为福什田么电换工线时间长福满中国
观念:传统的切换观念 –要求很高的知识和技巧 –只有通过经验的积累才能提高 –为了减少切换时间太长造成的影响,尽量
将生产批量扩大
这些都是基于切换时间不能大量减少的结论!
快速换线的定义和基本原理—为福什田么电换工线时间长福满中国
•混淆了内部和外部的切换操作
•作业员更换测试治具
快速换线的定义和基本原理—介福绍田电工
福满中国
•什么是SMED ? –Single Minute Exchange of Dies (快速换线/快速换模) •SMED系统是一种能有效缩短产品切换 时间的理论和方法
快速换线的定义和基本原理—历福史田电工
福满中国
• SMED在50年代初期起源于日本 • 在丰田企业发展起来 • Single的意思是小于10分钟(Minutes) • 最初使用在汽车制作厂,以达到快速的模
•法则六:基准不要变动。调整基准浪费时间。
•法则七:做好事前准备
•法则八:能简则简
SMED的五个步骤—五个步骤概述福田电工
福满中国
SMED的五个步骤—1 作业分析2 福区田分电内工外
福满中国
步骤一:对切换作业进行分析。 步骤二:区分内部与外部作业。 方法: •所有新的部件和工具必须在停机前运到现场 •所有换下的部件和工具应在切换结束后才进行清理和 转存 •提前准备好物料 •提前进行功能检查 •准备和使用检查表(防止遗漏琐碎的项目)
换线时间
上一料号生产直到停机
产线停机直到开机
下一工单正式生产
快速换线的定义和基本原理—换福线田定电义工案例 福满中国
案例:某拉线由A产品到B产品转换,换线具体时间如下表, 请问该拉线的换线时间是多少?
精益生产快速换模换线培训教材
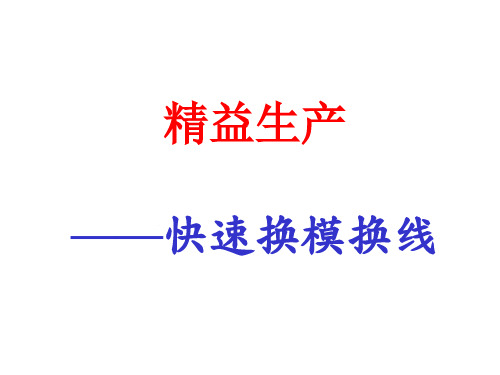
第3步骤改善:澈底改善内外作业(续)
3.排除调整 ※通常「试机、调整」占内部作业时间的50%。 ※「试机、调整」作业是将内部准备作业的「对中心、定位 置、条件设定」予以精确化调整,以防止重复试作出不 良品。因此,应将「对中心、定位置、条件设定」加以 精确化改善,则可减少不必要调整次数或时间。 ※排除调整必须依赖感觉、师傅式的作法。 4.标准化 ※作业标准书面化。(一致性与便于检讨) ※要求作业确实遵守作业标准书。 5.持续不断改善 ※公开换模 ※持续不断检讨改善,改善后立即再修改作业标准书。
查核表
机能查核 模具搬运 改善
作业状况
事先准备 机能标准化 界面具使用
改善模具、治 具、固定等作 业、储存及搬 运。 并行操作 装卸机能 降低微调 机械化
第O步骤改善:现状调查与分析
1.连续做马表现状工作调查与分析 优点:简单有效 缺点:精确度(非重复性) 2.现场作业录像分析 优点:(1)减少漏失动作分析 (2)可以与当事人互动检讨 (3)可以重复检讨 缺点:需有录像设备 3.原则:(1)告知 (2)平常心 (3)重复数次 (4)偶发异常排除 (5)不必分析太精细动作
整理,并确认功能。-----------------------30%
2.刀具等之安装、卸除。---------------------5% 3.定位、对准中心、设定加工条件。----------15% 4.试模、调整。-----------------------------
换模改善基本原则
初期状况 线内与线外 作业混杂不 清之混沌 第一阶段 首先将线内 与线外作业 作分离 第二阶段 尽可能将线 内作业转移 到线外作业 第三阶段 改善降低线 内作业与线 外作业时间
旋转式换模台车例
SMT快速换线ppt课件
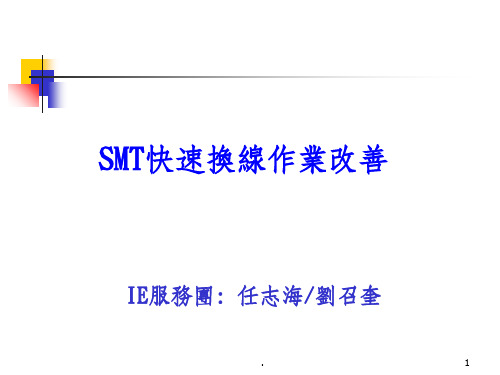
是
7 更換頂PIN(首件)
是
8 打首件(料件檢查)
是
9 OP測元件值
是
10 更換頂PIN(正式)
是
11 比對程式
是
12 IPQC測元件值
是
13 IPQC對料
是
.
取消 取消
取消
轉化為外部作業
取消或并行
取消或并行 6
三. 問題分析
運用5W1H手法追根溯源
1. 問﹕為什么 IPQC要進行對料作業 ? 答﹕A.確認所用料是否與料單一致; B.確認feeder是否放在正確的位置(料軌);
.
7
三. 問題分析
2. 問﹕為什么要快速料件檢查 ? 答﹕A.確認feeder是否放錯料軌; B.確認元件是否錯料,符合規格;
.
8
三. 問題分析
答A﹕確認所用料是否與料單一致; 問﹕為什么所用料與料單不一致? 答﹕來料不良或 IQC ,Kitting 混料﹔ 問﹕有無更好的預防措施? 答﹕1)kitting倉備料時檢查﹔
答﹕A.確認feeder是否放錯料軌﹔ 問﹕為什么會放錯料軌? 答﹕物料多,軌道多,易放錯料軌﹔ 問﹕有無更好的方法預防放錯料軌? 答﹕有。
1)Kitting備料按料單順序擺放; 2)作業員按順序將feeder上料軌; 3)作業員掃All Parts系統,檢查是否錯。
返回
.
11
三. 問題分析
答﹕B.確認元件是否錯料,符合規格﹔ 問﹕為什么元件會錯料,不符合規格? 答﹕廠商混料;來料不良;IQC貼錯料號標簽﹔ 問﹕有無預防措施? 答﹕有。
1) IQC 進料檢查(測值); 2) Kitting 倉對元件測值;
返回
.
12
工厂生产排线换线技巧课件
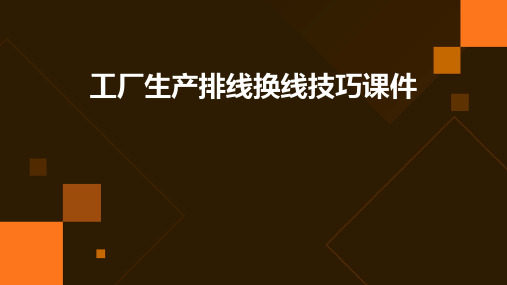
某电子制造企业采用快速换模方法后,减少了换 模过程中的浪费环节,实现了生产成本的降低。
3
案例三
某机械加工企业通过标准化操作和优化工装布局 ,将换模时间缩短了20%,提高了设备的利用率 。
03
设备调试与检查
设备调试流程
调试前准备
确保设备周围环境安全 ,准备好调试工具和检
测仪器。
通电检查
对设备进行通电检查, 观察设备运行是否正常
减少等待时间
优化物料供应和人员配备,减少设备或工人 的等待时间。
减少搬运距离
合理安排设备和物料的位置,减少搬运距离 和时间。
提高设备利用率
定期维护和保养设备,确保设备处于良好状 态,提高设备利用率。
采用自动化和智能化技术
引入自动化和智能化技术,减少人工干预, 提高生产效率。
05
安全注意事项
操作安全规范
生产排线优化
排线原则与策略
效率优先原则
在排线时,应优先考虑效率最高的设 备或工人,使其承担更多的生产任务 。
工艺流程原则
遵循产品工艺流程的顺序,合理安排 设备或工人的前后顺序。
瓶颈原则
识别生产中的瓶颈环节,优先解决瓶 颈问题,提高整体生产效率。
柔性原则
考虑未来产品变化的可能性,设计具 有一定柔性的排线方案,便于快速调 整。
调整生产线布局
U型布局
直线布局
将生产线设备按照U型排列,便于物料传递 和人员操作,减少走动距离。
将生产线设备按直线排列,便于工艺流程 的连续性,提高生产效率。
模块化布局
立体布局
将生产线设备按功能模块化分组,便于生 产管理和维护。
利用多层空间进行布局,节省占地面积, 提高空间利用率。
快速换线 PPT课件
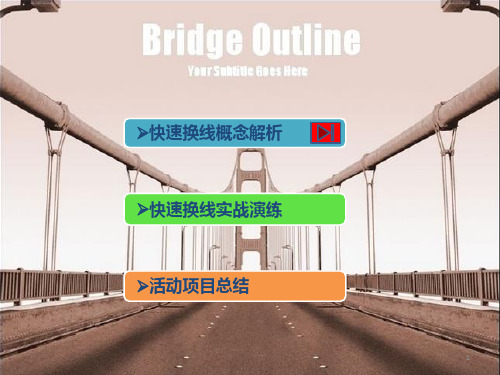
快速换线培训流程
17
快速换线实战演练
➢准备新型体换线
生产主管 生产组长
组长 技转人员
品管
IE
旧款第一道工序员工完成旧款最后一件即开始正式 转新款,长安排组内员工按照完成旧款时间先后顺 序陆续把设备按编号顺序摆放好 跟踪旧型体清尾工作,安排工人开始转换新型体并 指导工人操作,说明品质要求.
随时跟进各工段的品质管控
➢➢换线前一天
➢难度较大或复杂 工序由技转人员协 助生产组长长提前 做好线外产前培训 工作,缩短工人进行 新款生产时的学习 曲线时间
➢➢换线前30分钟
➢组长按流程图标 识好设备排布号码, 提前配好主辅料, ➢ 通知IE/品管/机修/ 技术人员提前到产 线就位. ➢将新款设备提前 安置在产线旁边,便 于快速换产, ➢组长提前组织工 人召开产前会议,讲 解工序操作方法和 品质要求
特殊设备
温度
技术员
作业条件
物料检测 来料追踪
重点工艺改善 物料配套
流程编排图
标准作业指导书 产前培训
物辅料分类
投产试制
料
法
11
快速换线实战演练
➢成立快速转款小组
参与人员 生产经理 生产主管 生产组长
生管 超市配料
IE 技转人员 设备维修 产线发料员 开发技术员 品管人员
角色 组长 成员 成员 成员 成员 成员 成员 成员 成员 成员 成员
➢➢换线前三天
➢生产组长需提前 做好新款点位板及 辅助工具,核对新 产品资料(纸板/物 料卡/样衣/制单/设 备需求单)正确. ➢ IE人员协同线长 制定好流程图及人 力编排表.
15
快速换线实战演练
➢➢换线前二天
➢生产管理人员需 提前跟踪物辅料进 度,确保新款导入时 超市备料准确,及时, 齐全. ➢机修人员将新产 品所需设备提前调 试好并做好标识
IE基础_如何实现快速换线.pptx
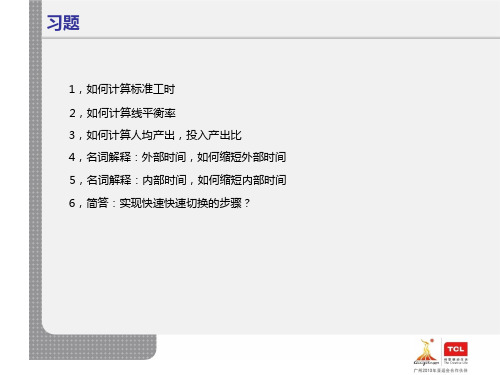
2,标准工时 例:计算生产某普通底壳产品的标准工时:
注塑机 (周期70)
包装
80s 取注塑产品+刮批峰
40s 包装
3,线平衡 用于衡量流程中各工站节拍符合度的一個综合比值﹔
单件标准时间 平衡率= ----------------------100%
瓶颈时间工位数
瓶颈时间:决定产品下线速度的工序时间
1,IE简介
IE的概念: 对人、机、料、法、环组成的集成系统进行设计、分 析及改善的一门学科。
运用数学、物理、社会科学等多方面的知识,运用工 程分析和设计的原理及方法,对该系统进行分析、评 价
IE的核心内容:提升生产效率与质量,降低成本
1,IE简介
IE的四大意识:
成本和效率意识 问题和改革意识 工作简化和标准化意识 全局和整体化意识 以人为中心的意识。
在订单逐量减少的今天,切换停机时间在设备运行时间中所占的比重越来 越大,每转换一次效率损失极大; 因为转产损失大,直接导致生产小批量订单时产出低、耗时长, 甚至导致企业不敢接收小批量订单,或使订单量不饱和。
20
快速切换的意义
缩短换模时间 增加换模次数 更具小批量生能力 更具平准化生产能力 缩短交期时间 减少资源波动 降低库存数量 增加库存周转率 减少仓储空间 减少管理工作负荷 企业更具竞争力
求:为完成2500PCS产量,需要几个人
2,标准工时
标准工时的定义: 在特定的工作环境条件下,用规定的作业方法和设备
,以普通熟练工作者的正常速度完成一定质量和数量的工作 所必需的时间
标准工时的重要性: IE的一切方法及手段都是为了保证所制定的标准时间公平合 理,因为它是衡量生产效率的基准,同时也是进行科学的效 率管理的基础。
精益生产全集_快速切换_QCO_CN
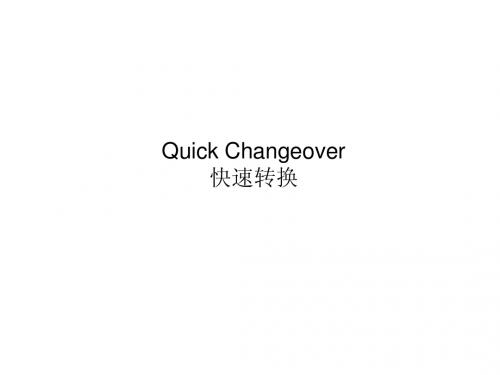
•内部时间:必须在设备停机的状态下才可执行的工作
–移开、插入工具或坏掉的传送链
•外部时间:可在设备运行同时进行的准备或清理工作
–工具和/或模具的运输 –每次运行必须做的书面工作
22
区分内外部
QCO步骤1(续)
过程:
内部转外部 运用夹具
消除调节
标准化 并行操作 机械改进
产品时间表 一个月
A B C
50 100 150
每月生产一次以上(小批量)
9
平衡生产与大批量
批量生产
生产理论 产出理论
平衡生产
市场导向理论
生产方式
大批量
周期时间
达到效率的方法
针对每个单独的工序
针对整条线提高效率 (系统焦点) 中等速度,用途单一, 体积小,价格低
关于设备
高速,广用途,体积大并且价格高
• 工具整和 – 是否每件工具都是必要的? 工具的性能是 可以合并,减少或取消?
• 专业化 – 改进手推车、工具和其他的设备以缩短转换 时间。
5S 能够在安装调试阶段实现很大的节约而又不耗费任何成本!
19
改进的关键——TPM
• TPM 可以看作为“对设备的5S” • 它提供了严格的有规律的过程,这些过程改进了 重复性并确保证设备最大的正常运行时间。 • 如果设备情况不可预测,不可能进行真正有意义 的转换时间降低。 • 通过TPM可以预测设备的运行情况,通过快速转换 实现的节约是可以持续的
使操作标准化并消除调节
• 定位 – 制定定位和夹紧定制的标准。 • 夹紧 – 每次按同样的顺序、相同的扭矩夹紧和拧紧 螺丝。 • 设置档块 – 如果必需垫片,要使用标志清楚、伸手 可及的专用间隔档块。
快速换线

2018/8/16
36
2018/8/16
37
PDCA来源
• 美国质量管理专家戴明博士首先提出,所 以又称为“戴明环”。|它是全面质量管理 所应遵循的科学程序。全面质量管理活动 的全部过程,就是质量计划的制订和组织 实现的过程,这个过程就是按照PDCA循环, 不停顿地周而复始地运转 的。
2018/8/16
2018/8/16
39
PDCA的适用领域
• PDCA精神是发现、改善各种管理困难。循 环理论存在于所有领域,大至企业的策略 管理、环保污染管理,小到部门的项目管 理、教育训练、自我管理等等。它被人们 持续地、正式或非正式地、有意识或下意 识地使用于自己所做的每件事和每项活动。
2018/8/16
40
PDCA简介
• PDCA循环作为全面质量管理体系运转的基 本方法,其实施需要搜集大量数据资料, 并综合运用各种管理技术和方法。如下图 所示,一个PDCA循环一般都要经历以下4个 阶段(图1所示)、8个步骤(图2所示)。
2018/8/16
41
如图所示:
2018/8/16
42
PDCA8个步骤
• ① 分析现状,发现问题; ② 分析问题中各种影响因素; ③ 分析影响问题的主要原因; ④ 针对主要原因,采取解决的措施; Why--为什么要制定这个措施? What--达到什么目标? Where--在何处执行? Who--由谁负责完成? When--什么时间完成? • How--怎样执行?
组织会议事项确 认,各生产人员提前 了解新产品工艺 机修人员根据产 品要求提前准备新 款所需设备以及工 夹具等其他辅助设 备
快速换线实战演练
换线前二天
换线前一天
换线前30分钟
快速换线

换线时间=内部换线时间+外部换线 时间
• 内部换线时间指停止当前作业任务到生产下一个合格产品 的时间,这段时间,机器没有产生附加价值,Internal Changeover Time begins when the current processing task is finished and ends when the next processing task produces a defect-free product ,Throughout this time ,the machine does not add any value to the workpiece. • 外部换线时间指作业人员在线为做换线准备的时间,此时 机器在正常地工作.External Changeover Time is the time spent by the operator carrying out setup procedures independent of the machine while the machine is operating
快速切换 (Quick Change over)
课程内容Contents
• 快速换线介绍Introduction to QCO • 换线时间和换线中的浪费Change Time and Waste in Changeover Operations • 换线改善流程步骤Changeover Improvement Process Steps
何谓快速换线?What is QCO?
快速换线是一个有组织的过程:QCO is an organized process that: 1. 减少不同产品间换线时间,Reduces the time required for set-up between different parts. 2. 提高换线的可重复性,确信在X分种内换线成功 并生产出合格产品,Improves the repeatability of changeover operations ,It generates confidence that a process can be producing the next quality parts within X minutes of shutdown . •
- 1、下载文档前请自行甄别文档内容的完整性,平台不提供额外的编辑、内容补充、找答案等附加服务。
- 2、"仅部分预览"的文档,不可在线预览部分如存在完整性等问题,可反馈申请退款(可完整预览的文档不适用该条件!)。
- 3、如文档侵犯您的权益,请联系客服反馈,我们会尽快为您处理(人工客服工作时间:9:00-18:30)。
• T=T2-T1-BT*N=60(20S×30)/60=50分钟
10
➢快速换线概念解析 ➢快速换线实战演练 ➢活动项目总结
11
快速换线实战演练
运用4M1E原则进行鱼骨图分析
人
机修
生产管理
品管
PMC
技术员
机
环
普通设备
性能检查
照明
提前调试
IE
特殊设备
5S 温度
作业条件
协助生产组长编排工段,记录换线时间
机修人员
协助生产组长及员工进行机器安排,换线原地待命
精益管理之快速换线
工业工程(亚洲)精益学院公开课
分享人: Seven(小七)
用你最扎实的基础去改善企业 用你最真实的心态去创造价值
➢快速换线概念解析 ➢快速换线实战演练 ➢活动项目总结
2
快速换线概念解析
➢什么是3P流程? Production Preparation Process
生产准备流程,它是精益生产中的一个比较重要的 工具,是一个采用团队 方式的生产流程设计系统.
➢➢换线前一天
➢难度较大或复杂 工序由技转人员协 助生产组长长提前 做好线外产前培训 工作,縮短工人进行 新款生产时的学习 曲线时间
➢➢换线前30分钟
➢组长按流程图标 识好设备排布号码, 提前配好主辅料, ➢通知IE/品管/机修 /技术人员提前到产 线就位. ➢将新款设备提前 安置在产线旁边,便 于快速换产, ➢组长提前组织工 人召开产前会议,讲 解工序操作方法和 品质要求
9
快速换线概念解析
转拉时间的计算方式: • T=T2-T1-BT*N
转拉时间 怎么算呢?
• 说明: T 1:头位下完最后一部旧型体的时刻 T 2:QC位拿到第一个产品的时刻,且 新型体已正常生产 BT:新型体的瓶颈时间 N :新型体头位到QC之间的人数(不 包括QC)
• 某生产线由007型体转008型 体,拉头第一个工位在10:25 下完007型体,拉尾QC位于 11:25分开始测试第一部008型 体,从拉头到QC共有30人, 008 型体的瓶颈时间为20秒, 那么,
15
快速换线实战演练
➢➢换线前一周
➢组织会议事项确 认,各生产人员提 前了解新产品工艺 ➢机修人员根据产 品要求提前准备新 款所需设备以及工 夹具等其他辅助设 备
➢➢换线前五天
➢生管提供样品(制 单/物料卡/样衣/纸 板)给到生产线长开 始进行首件试产样, ➢机修及相关技术 人员提供支持,确认 工艺做法. ➢品管人员进行结 果检验,并做问题总 结.
单独 分钟 切换
模具
• 以最小的设备停机时间来进行不同产品间的生产切换,最 大限度提高设备利用率的方法,也是精益生产常用到的改 善工具之一.
尽量做到少停机,多生产,将内部切换转换外部切换
8
快速换线概念解析
➢快速换线的好处
• 减少批量大小 • 縮短型体转换时间 • 提高生产效率 • 縮短操作工人新工段学习曲线 • 减少线上在制品库存 • 减少各种浪费动作 • 提高机器稼动率 • 提高生产效率 • 提升品质 • 减少断流次数
√1
产前准备 流程
P
2
产品生产 流程
D
3
产品检验 流程
C4产品入库 来自程A3快速换线概念解析
➢确保各制造部门同步化生产 ➢縮短产品换线时间,提高生产效率 ➢提前降低制造不良率,改善并提高品质 ➢平衡生产线,降低在制品库存 ➢减少换线过程中产生的过多搬运动作浪费 ➢针对难度工序提前预警并进行线外培训 ➢保证设备性能最佳状态及工夹具准备完善 ➢……..
➢➢换线前三天
➢生产组长需提前 做好新款点位板及 辅助工具,核对新 产品资料(纸板/物 料卡/样衣/制单/设 备需求单)正确. ➢ IE人员协同线 长制定好流程图及 人力编排表.
16
快速换线实战演练
➢➢换线前二天
➢生产管理人员需 提前跟踪物辅料进 度,确保新款导入时 超市备料准确,及时, 齐全. ➢机修人员将新产 品所需设备提前调 试好并做好标识
和操作后进行切换动作.如:检验/可提前 准备工作 ..等
旧型体
切线 时间
新型体 6
快速换线概念解析
1.你们的工厂有哪些切换? 2.你们的工厂型体切换时间是多久? 3.你觉得频繁切换型体有哪些不好?
倒计时 59:00
7
快速换线概念解析
快速换模之定义
----SMED-Single Minute Exchange of Die
职责担当 活动督导,组织协调各部门顺利进行 了解新型体工艺技术,组织部门会议
试制产前样,教导工人工段操作 提供订单生产计划信息及各类产品工艺文件
协助新型体物料前期准备 解析型体工艺,编制工艺流程表,协助产线平衡
协助组长产线安排,给工人做产前培训 提前调试机器,准备辅助工具,换线原地待命 物料交接,旧型体收料,新型体发料,中途配料
4
快速换线概念解析
快速换线如何去做? 为什么要快速换线? 什么是快速换线?
5
快速换线概念解析
➢换线的定义 • 前一型体和后一型体的转换生产. • 内换线和外换线两种换线形式.
➢内换线 • 在机器设备停止状态后才能做型体切换
的动作.如:设备搬运/换模具..等 ➢外换线 • 在机器不需要停止的情况下可在操作前
17
快速换线培训流程
18
快速换线实战演练
➢准备新型体换线
生产主管 生产组长
组长 技转人员
品管
IE
舊款第一道工序員工完成舊款最後一件即開始正式 轉新款,长安排組內員工按照完成舊款時間先後順 序陆续把设备按編號順序擺放好 跟踪旧型体清尾工作,安排工人开始转换新型体并 指导工人操作,说明品质要求.
随时跟进各工段的品质管控
物料检测 来料追踪
重点工艺改善 物料配套
流程编排图
标准作业指导书 产前培训
物辅料分类
投产试制
料
法
12
快速换线实战演练
➢成立快速转款小组
团队小游 戏视频
参与人员 生产经理 生产主管 生产组长
生管 超市配料
IE 技转人员 设备维修 产线发料员 开发技术员 品管人员
角色 组长 成员 成员 成员 成员 成员 成员 成员 成员 成员 成员
协助工艺技术难点指导 全程监督物料品质及制程品质
13
快速换线实战演练
运用PDCA(戴明环定理)循环分成四个阶段进行
14
快速换线实战演练
确认订单/ 了解工艺/ 组织会议
首件试产/ 确定工艺
投产准备/ 编排人力/ 确认流程
线平衡改 善/总结问
题
快速换线
准备转款/ 技术指导/ 品质跟进
备料齐全/ 设备调试/ 产前培训