异丁醛施工方案(储罐施工方案)
储罐施工方案(安装)

目录1.编制说明 1 2.工程概况 1 3.编制依据 2 4.施工方法 2 5.焊接工艺及主要焊接顺序15 6.质量保证措施21 7.资源配置计划23 8.质量保证措施23 9.HSE施工管理计划261、编制说明1.1 为了保证产品罐区及中间罐区17台储罐的施工质量,满足设计和生产对工艺的要求,特编制本方案。
1.2本方案经监理审查通过后,即可用于指导储罐的安装工艺作业,其所规定的内容与其它方案不符时,一律以本方案为准。
各有关人员要严格依照执行,加强工艺纪律,以确保储罐的质量和进度。
1.3质量目标计划:单位工程检验合格率100%;分部、分项工程交验合格率90%;设备封闭合格率100%;零质量事故。
2、工程概况2.1本工程为多伦世腾15万吨/年煤制烯烃副产品芳构项目,储罐制作安装工程包括50m³罐4台、100m³罐2台、200m³罐2台、300m³罐1台、330m³罐1台、500m³罐1台、1000m³罐3台以及2000m³罐3台,其中15台罐结构为固定顶圆筒形立式储罐(内设浮盘),2台罐结构为固定顶圆筒形立式储罐(未设浮盘)。
罐体安装采用倒装法,焊接采用手工电弧焊。
设备实物量清单序号设备位号设备名称规格型号mm材质重量Kg 单位数量1 TK-1352A/B苯产品检验罐DN3800X5400 Q245R 9114 台 22 TK-1304 抽余油储罐DN3800X5400 Q235B 8638 台 13 TK-1101 甲醇储罐DN3800X5400 Q235B8682 台 14 TK-1353A/B甲苯产品检验罐DN5200X5250Q235B11513 台 25 TK-1351混合芳烃缓冲罐DN5500X1026Q235B16743 台 16 TK-1302新鲜溶剂罐DN5500X1026Q235B16659 台 17 V-1807混合芳烃储罐DN7750X7130Q235B18004 台 18 TK-1303湿溶剂罐DN6600X1065Q235B24438 台 19 V-1806碳十芳烃储DN9000X8710Q235B26113 台 110 V-1804苯储罐DN11500X10700Q245R 39846 台 111 TK-1301抽提进料缓冲罐DN11500X10700Q235B46441 台 112 V-1805三甲苯储罐DN11500X10700Q235B37751 台 113 V1801/1802/1803甲苯/二甲苯储罐DN15800X11100Q235B60247 台 32.2技术参数表(附表4)2.3 以上17台罐施工绝对工期为71天3、编制依据3.1 储罐施工图纸;3.2《立式圆筒形钢制焊接油罐设计规范》(GB50341-2003);3.3《立式圆筒形钢制焊接储罐施工及验收规范》(GB50128-2005);3.4《钢制储罐液体环氧涂料内防腐层技术标准》(SY/T0319-98);3.5《钢制化工容器结构设计规定》(HG/T20583-2011);3.6《压力容器焊接规程》(NB/T47015-2011);3.7《承压力设备无损检测》(JB4730-2005);3.8《焊接工艺评定规程》(DL/T 868-2004);3.8企业工艺标准的名称及编号:《施工技术方案管理规定》 Q/JH223.22101.02-2013《施工技术通用管理标准》 Q/JH222·21100.01-2013《施工质量通用管理标准》 Q/JH223·21500.01-2013《质量、环境、职业安全健康综合管理手册》 Q/JH223·20001.2007《安全生产责任管理规定》 Q/JH223·21801.013.9、现场勘察4施工方法4.1 施工技术准备4.1.1储罐施工前应具备施工图纸和相关技术资料、施工单位编制并得到有关部门审批的施工方案以及国家或行业的施工及验收规范和项目质量保证计划等文件。
储罐施工方案范文

储罐施工方案范文一、项目概况本项目是一个工业用途的储罐施工项目,包括选址、地基处理、罐体安装、防腐处理、管道连接等工作,总计需要施工1200小时。
二、施工方案1.储罐选址:根据地质勘探报告和设计要求,确定储罐选址。
选址过程中要保证地质条件稳定,排水条件良好,且远离易燃易爆危险品储存区。
2.地基处理:进行地表土方开挖,确保罐底土层承载力满足设计要求。
然后进行基础施工,包括平整基底、灌浆、加固等。
3.罐体安装:根据设计要求,选择合适的起吊设备,对储罐进行整体起吊,并进行稳定固定,确保储罐能够承受外部力量和自身负荷。
4.罐体防腐:根据储罐所存贮的物质性质和环境要求,选择合适的防腐材料进行施工。
首先进行表面处理,包括喷砂、打磨等,然后进行防腐材料涂装,确保储罐的耐腐蚀性能。
5.管道连接:根据设计要求,对储罐进行进出料管道的连接。
连接过程中要保证管道与储罐的密封性、稳定性和安全性。
6.环境保护措施:在施工过程中,要建立完善的环境保护措施,包括防尘、降噪、排污处理等措施,确保项目不对周边环境造成污染。
7.安全管理:严格执行安全操作规程,保障施工人员的生命安全和财产安全。
建立安全监督机制,及时发现和处理安全隐患。
8.进度控制:根据项目的工期要求,合理安排施工进度,确保项目能够按时交付。
在施工过程中,要根据实际情况进行进度调整和优化。
9.质量控制:建立质量监督和检验机制,对施工过程进行全面监控和检验,确保施工质量符合设计要求和相关标准。
三、施工组织1.组织架构:建立项目管理组织架构,包括总监、工程师、技术员、施工人员等角色,明确各自职责和权限。
2.人员培训:对施工人员进行必要的培训,提高他们的技能水平,并加强对安全操作规程和质量要求的培训。
3.施工设备:购置所需的施工设备和工具,确保施工过程中能够满足施工要求。
四、项目管理1.进度管理:制定详细的施工计划和进度表,定期进行进度检查和评估,及时调整工期和资源分配。
储罐施工方案
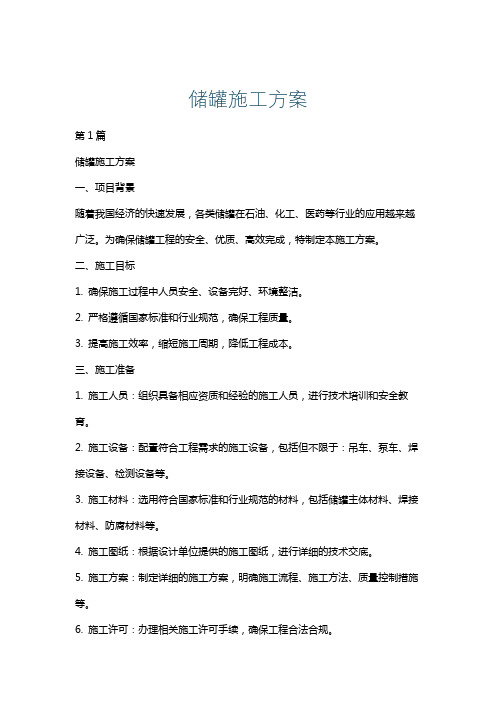
储罐施工方案第1篇储罐施工方案一、项目背景随着我国经济的快速发展,各类储罐在石油、化工、医药等行业的应用越来越广泛。
为确保储罐工程的安全、优质、高效完成,特制定本施工方案。
二、施工目标1. 确保施工过程中人员安全、设备完好、环境整洁。
2. 严格遵循国家标准和行业规范,确保工程质量。
3. 提高施工效率,缩短施工周期,降低工程成本。
三、施工准备1. 施工人员:组织具备相应资质和经验的施工人员,进行技术培训和安全教育。
2. 施工设备:配置符合工程需求的施工设备,包括但不限于:吊车、泵车、焊接设备、检测设备等。
3. 施工材料:选用符合国家标准和行业规范的材料,包括储罐主体材料、焊接材料、防腐材料等。
4. 施工图纸:根据设计单位提供的施工图纸,进行详细的技术交底。
5. 施工方案:制定详细的施工方案,明确施工流程、施工方法、质量控制措施等。
6. 施工许可:办理相关施工许可手续,确保工程合法合规。
四、施工流程1. 施工前期准备:完成施工图纸审查、技术交底、施工许可等工作。
2. 场地平整:按照设计要求进行场地平整,确保施工场地满足施工需求。
3. 基础施工:严格按照设计图纸和施工规范进行基础施工,确保基础质量。
4. 储罐制作:按照设计图纸和施工规范,采用先进的制作工艺,确保储罐主体结构质量。
5. 储罐安装:采用专业吊装设备,按照施工方案进行储罐安装。
6. 焊接施工:选用合适的焊接工艺,确保焊接质量符合国家标准。
7. 检测验收:对储罐进行无损检测、压力试验等,确保储罐质量。
8. 防腐施工:根据设计要求,对储罐内外进行防腐处理。
9. 竣工验收:组织相关单位进行竣工验收,确保工程质量。
五、质量控制措施1. 施工过程中,严格执行国家及行业相关标准、规范。
2. 加强施工现场管理,确保施工人员、设备、材料的安全。
3. 对关键工序进行旁站监督,确保施工质量。
4. 对施工过程进行记录,形成完整的施工档案。
5. 定期对施工人员进行技术培训,提高施工技能。
储罐施工方案
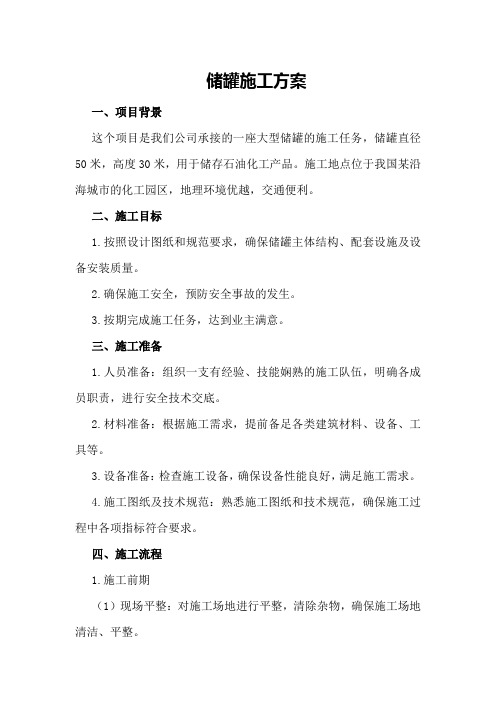
储罐施工方案一、项目背景这个项目是我们公司承接的一座大型储罐的施工任务,储罐直径50米,高度30米,用于储存石油化工产品。
施工地点位于我国某沿海城市的化工园区,地理环境优越,交通便利。
二、施工目标1.按照设计图纸和规范要求,确保储罐主体结构、配套设施及设备安装质量。
2.确保施工安全,预防安全事故的发生。
3.按期完成施工任务,达到业主满意。
三、施工准备1.人员准备:组织一支有经验、技能娴熟的施工队伍,明确各成员职责,进行安全技术交底。
2.材料准备:根据施工需求,提前备足各类建筑材料、设备、工具等。
3.设备准备:检查施工设备,确保设备性能良好,满足施工需求。
4.施工图纸及技术规范:熟悉施工图纸和技术规范,确保施工过程中各项指标符合要求。
四、施工流程1.施工前期(1)现场平整:对施工场地进行平整,清除杂物,确保施工场地清洁、平整。
(2)测量放线:根据设计图纸,进行现场测量,放出储罐基础、罐体、管道等设施的位置线。
2.基础施工(1)基础垫层:按照设计要求,铺设基础垫层,确保基础稳定。
(2)基础模板:根据设计图纸,制作基础模板,保证模板的强度和稳定性。
(3)基础钢筋:按照设计要求,绑扎基础钢筋,确保钢筋间距、长度、直径等符合要求。
(4)基础浇筑:采用商品混凝土,对基础进行浇筑,保证混凝土质量。
3.罐体施工(1)罐壁施工:采用分段施工法,从下至上依次施工罐壁,确保罐壁垂直度、厚度等指标符合要求。
(2)罐顶施工:采用高空作业平台,进行罐顶施工,确保罐顶平整、严密。
(3)罐底施工:采用无缝焊接技术,对罐底进行焊接,保证罐底无泄漏。
4.配套设施及设备安装(1)管道安装:根据设计图纸,进行管道安装,确保管道走向、间距、高度等符合要求。
(2)设备安装:按照设计要求,进行设备安装,确保设备正常运行。
(3)电气安装:进行电气线路的铺设和设备接线,确保电气系统安全可靠。
五、施工质量控制1.严格把控施工材料的质量,确保材料符合国家相关标准。
储罐防腐施工方案(1)

储罐防腐施工方案(1)
摘要
储罐作为一种储存化学品、石油、水等物质的设备,在长期使用的过程中,容易受到腐蚀的影响。
因此,对储罐进行防腐施工是非常重要的。
本文将介绍储罐防腐施工方案的相关内容,包括选择防腐材料、施工过程、注意事项等。
一、防腐材料的选择
在进行储罐防腐施工时,首先需要选择合适的防腐材料。
一般来说,常用的防腐材料有涂料、涂层、树脂等。
在选择防腐材料时,需要考虑储罐所存储物质的性质、储罐的使用环境、预算等因素,以确保防腐效果和施工质量。
二、施工过程
防腐施工的过程分为准备工作、表面处理、涂装和检查四个步骤。
首先进行准备工作,包括清洁储罐表面、修补表面缺陷等。
接着进行表面处理,一般包括除锈、除漆等工作。
然后进行涂装,根据选择的防腐材料进行涂装施工。
最后进行检查,确保施工工艺符合相关标准要求。
三、注意事项
在进行储罐防腐施工时,需要注意以下几个方面: 1. 环境因素:施工时需考
虑环境温度、湿度等因素,选择合适的施工条件。
2. 施工质量:施工过程中需要
严格按照防腐材料的使用说明和施工规范进行操作,确保施工质量达标。
3. 安全
保障:施工时需要采取必要的安全措施,保障施工人员的安全。
4. 预防措施:施
工完成后,需要进行定期检查和维护,预防意外事件的发生。
结论
储罐防腐施工是确保储罐长期使用的关键环节,选择合适的防腐材料、严格控制施工质量以及做好后期维护工作是保证储罐防腐效果的重要步骤。
只有在全面考虑各方面因素的基础上,才能制定出最合适的储罐防腐施工方案,确保储罐的安全和稳定运行。
储罐施工方案范文

储罐施工方案范文一、项目背景储罐是一种用于存储液体或气体的设备,广泛应用于石油、化工、食品、制药等行业。
储罐的施工对于保证产品的质量和提高生产效率至关重要。
因此,制定科学合理的储罐施工方案是非常必要的。
二、施工目标1.确保储罐的安全性:施工过程中,要严格遵守相关安全操作规程,确保施工人员的人身安全,以及减少设备故障的可能性;2.保证施工质量:施工过程中,要按照相关标准和规范进行操作,确保储罐的使用寿命和产品质量;3.提高施工效率:结合实际情况,合理安排施工流程,提高施工效率,减少生产停工时间。
三、施工步骤1.前期准备:确定施工现场,编制详细的施工计划,包括材料采购、设备调配、工程人员组织等;2.地基处理:对于大型储罐,要进行地基处理,包括排水、平整、加固等工作;3.基础施工:根据设计要求,进行基础的施工,包括浇筑混凝土、铺设防渗层等;4.立罐架设:通过起重机进行立罐架设,确保储罐的稳定性和安全性;5.罐体焊接:进行罐体的焊接工作,包括罐体壁板、头板、底板等的焊接,要保证焊缝的质量;6.附件安装:将需要安装的附件,如进出口阀门、压力表等,按照设计要求进行安装;7.防腐处理:根据施工环境和储存物质的特点,选择合适的防腐方式进行处理;8.涂装:对于需要涂装的储罐,进行底漆、中涂和面涂的施工,保护罐体表面;9.绝热处理:对于需要绝热处理的储罐,进行绝热材料的施工,减少能量的损失;10.设备调试:通过设备的调试和试运行,确保储罐的使用性能;11.验收和交付:按照相关标准和规范进行验收,确保储罐的施工质量,最终交付使用。
四、施工安全措施1.先进行安全培训:对参与储罐施工的人员进行安全培训,提高他们的安全意识和操作技能;2.建立施工现场安全管理制度:建立施工现场安全管理制度,明确每个人员的职责,严格执行工作票、动火审批等流程;3.确保施工现场整洁:保持施工现场的整洁,减少杂物、障碍物的存在,防止意外伤害;4.设立安全防护设施:在施工现场设置必要的安全防护设施,如安全带、安全网、防护栏等;5.保持通讯畅通:保持施工现场的通讯畅通,及时沟通和解决可能出现的安全问题;6.对危险作业进行监督:对于危险作业,进行监督,确保施工人员按照规定操作,杜绝安全隐患。
储罐施工方案范文
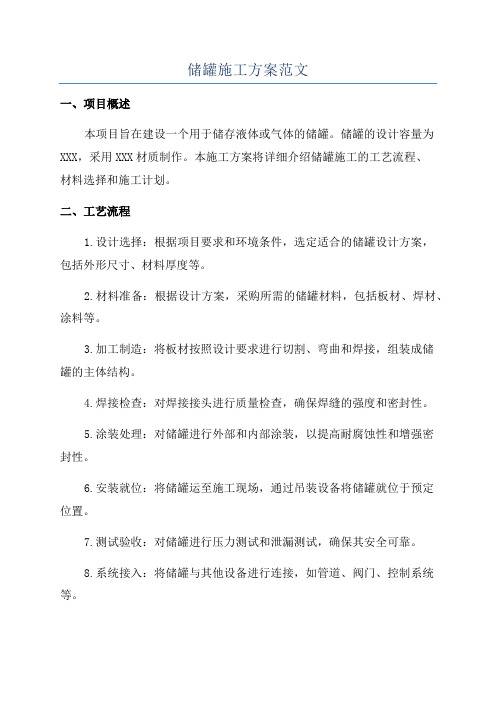
储罐施工方案范文一、项目概述本项目旨在建设一个用于储存液体或气体的储罐。
储罐的设计容量为XXX,采用XXX材质制作。
本施工方案将详细介绍储罐施工的工艺流程、材料选择和施工计划。
二、工艺流程1.设计选择:根据项目要求和环境条件,选定适合的储罐设计方案,包括外形尺寸、材料厚度等。
2.材料准备:根据设计方案,采购所需的储罐材料,包括板材、焊材、涂料等。
3.加工制造:将板材按照设计要求进行切割、弯曲和焊接,组装成储罐的主体结构。
4.焊接检查:对焊接接头进行质量检查,确保焊缝的强度和密封性。
5.涂装处理:对储罐进行外部和内部涂装,以提高耐腐蚀性和增强密封性。
6.安装就位:将储罐运至施工现场,通过吊装设备将储罐就位于预定位置。
7.测试验收:对储罐进行压力测试和泄漏测试,确保其安全可靠。
8.系统接入:将储罐与其他设备进行连接,如管道、阀门、控制系统等。
9.维护保养:储罐投入使用后,定期进行检查和保养,确保其长期稳定运行。
三、材料选择1.储罐板材:选择具有良好耐腐蚀性和机械强度的材料,如碳钢板、不锈钢板等。
2.焊材:选择符合储罐使用环境要求的焊接材料,如焊条、焊丝等。
3.涂料:选择具有良好抗腐蚀性、耐高温性和耐候性的涂料,如环氧涂料、聚氨酯涂料等。
4.辅助材料:如密封胶、垫片等,选择符合使用要求的高温耐腐蚀材料。
四、施工计划1.设计准备阶段:确定储罐设计方案,编制施工图纸,准备所需材料和设备。
2.加工制造阶段:按照工艺流程进行材料加工和制造,保证质量和尺寸准确。
3.涂装处理阶段:对储罐进行涂装处理,采用适当的涂料和涂装工艺。
4.运输安装阶段:运输储罐到施工现场,通过吊装设备将储罐安装就位。
5.系统接入阶段:将储罐与其他设备进行连接,进行测试验收。
6.维护保养阶段:储罐投入运行后,定期进行检查和保养,确保其正常运行。
五、安全措施1.施工现场设立临时围挡,确保安全。
施工人员必须佩戴安全帽、安全鞋和其他必需的个人防护用品。
异丁醛施工方案(储罐施工方案)
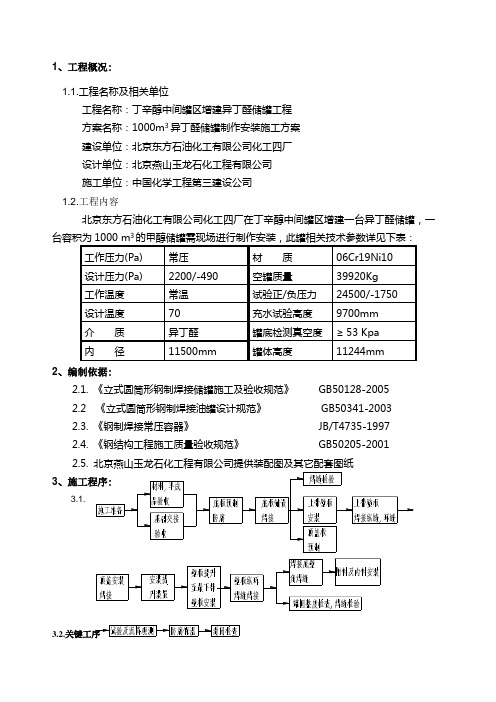
1、工程概况:1.1.工程名称及相关单位工程名称:丁辛醇中间罐区增建异丁醛储罐工程方案名称:1000m3异丁醛储罐制作安装施工方案建设单位:北京东方石油化工有限公司化工四厂设计单位:北京燕山玉龙石化工程有限公司施工单位:中国化学工程第三建设公司1.2.工程内容北京东方石油化工有限公司化工四厂在丁辛醇中间罐区增建一台异丁醛储罐,一台容积为1000 m3的甲醇储罐需现场进行制作安装,此罐相关技术参数详见下表:工作压力(Pa) 常压材质06Cr19Ni10设计压力(Pa) 2200/-490 空罐质量39920Kg工作温度常温试验正/负压力24500/-1750设计温度70 充水试验高度9700mm介质异丁醛罐底检测真空度≥53 Kpa内径11500mm 罐体高度11244mm2、编制依据:2.1. 《立式圆筒形钢制焊接储罐施工及验收规范》GB50128-20052.2 《立式圆筒形钢制焊接油罐设计规范》GB50341-20032.3. 《钢制焊接常压容器》JB/T4735-19972.4. 《钢结构工程施工质量验收规范》GB50205-20012.5. 北京燕山玉龙石化工程有限公司提供装配图及其它配套图纸3、施工程序:3.1.3.2.关键工序关键工序一览表序号关键工序名称工序特点、难点、主要实物量及主要技术参数(材质、规格等)备注1 基础验收按照规范、设计要求验收基础2 底板的组装及焊接排版的规范、设计要求,注意搭接的顺序与方法3 顶板的组装及焊接排版的规范、设计要求,4 壁板的组装及焊接排版的规范、设计要求与开孔的方位,弧形与垂直度的检查5 检验底板的真空度与无损检测、壁板的无损检测等,按照规范、设计要求6 沉降试验/充水/充压试验试验方法按照规范、设计要求4、施工方法及施工技术措施甲醇储罐总体施工工艺为倒装法,根据贮罐外形尺寸,利用20t汽车吊配合围带板、铺底板、地面预制顶盖。
焊接方法采用手工电弧焊,制造和安装执行GB50128-2005《立式圆筒型钢制焊接油罐施工及验收规范》的相关规定。
储罐安装施工方案(3篇)
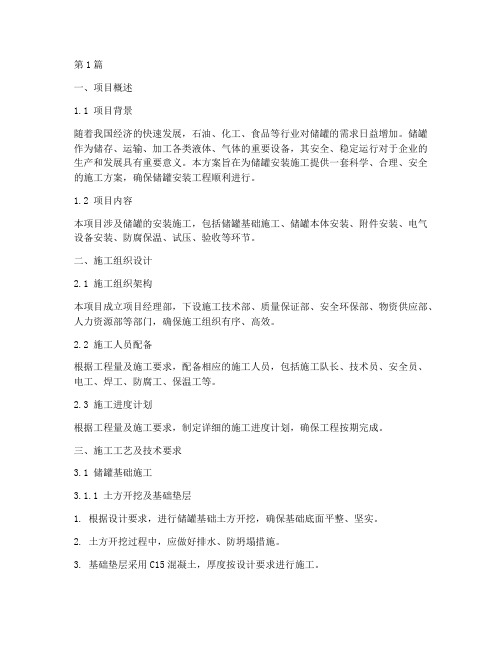
第1篇一、项目概述1.1 项目背景随着我国经济的快速发展,石油、化工、食品等行业对储罐的需求日益增加。
储罐作为储存、运输、加工各类液体、气体的重要设备,其安全、稳定运行对于企业的生产和发展具有重要意义。
本方案旨在为储罐安装施工提供一套科学、合理、安全的施工方案,确保储罐安装工程顺利进行。
1.2 项目内容本项目涉及储罐的安装施工,包括储罐基础施工、储罐本体安装、附件安装、电气设备安装、防腐保温、试压、验收等环节。
二、施工组织设计2.1 施工组织架构本项目成立项目经理部,下设施工技术部、质量保证部、安全环保部、物资供应部、人力资源部等部门,确保施工组织有序、高效。
2.2 施工人员配备根据工程量及施工要求,配备相应的施工人员,包括施工队长、技术员、安全员、电工、焊工、防腐工、保温工等。
2.3 施工进度计划根据工程量及施工要求,制定详细的施工进度计划,确保工程按期完成。
三、施工工艺及技术要求3.1 储罐基础施工3.1.1 土方开挖及基础垫层1. 根据设计要求,进行储罐基础土方开挖,确保基础底面平整、坚实。
2. 土方开挖过程中,应做好排水、防坍塌措施。
3. 基础垫层采用C15混凝土,厚度按设计要求进行施工。
3.1.2 基础垫层施工1. 混凝土浇筑前,对基础垫层进行清理,确保表面干净、无杂物。
2. 混凝土浇筑过程中,应严格控制混凝土的配合比及坍落度,确保混凝土质量。
3. 混凝土浇筑后,应及时进行养护,确保强度达到设计要求。
3.2 储罐本体安装3.2.1 储罐本体组装1. 按照设计图纸,将储罐本体分段进行组装,确保组装精度。
2. 组装过程中,严格控制组装间隙,确保储罐本体组装质量。
3.2.2 储罐本体焊接1. 焊接前,对储罐本体进行清理,确保焊接质量。
2. 焊接过程中,采用合理的焊接工艺,确保焊接质量。
3. 焊接完成后,对焊缝进行无损检测,确保焊缝质量。
3.3 附件安装3.3.1 附件选型1. 根据设计要求,选择合适的附件,包括进出口管道、人孔、排污口、液位计、安全阀等。
储罐安装施工方案

储罐安装施工方案储罐安装施工方案储罐安装施工方案是指在进行储罐安装工程时,按照一定的施工步骤和方法进行施工,并保证施工质量和安全的一项工作。
下面是一个储罐安装施工方案的简要描述。
一、施工前的准备工作1.1 制定施工方案,明确施工步骤和施工方法。
1.2 组织施工人员进行专业技术培训,确保施工人员掌握施工要领和安全操作规程。
1.3 检查施工所需的施工材料和设备,保证施工材料质量合格,设备工作正常。
二、基础施工2.1 根据储罐设计图纸和基础施工方案,进行基础开挖工作,保证基础尺寸精准。
2.2 进行混凝土浇筑,注意施工现场环境保护和混凝土质量控制。
2.3 完成基础施工验收,确保基础合格。
三、储罐安装3.1 进行储罐的吊装工作,采用专业吊装设备和操作人员进行操作,确保吊装安全。
3.2 进行储罐的定位和水平调整工作,确保储罐位置准确和水平度符合要求。
3.3 进行管道连接工作,采用合适的管道材料和接头,保证连接牢固。
3.4 完成储罐的防腐、绝缘和涂装工作,防止腐蚀和外界环境对储罐的影响。
四、设备安装4.1 根据储罐的功能要求,安装相应的设备和仪表。
4.2 进行设备和仪表的连接和调试工作,确保设备正常运行。
五、验收和试运行5.1 进行储罐安装工程的验收工作,按照相关规范和标准进行验收。
5.2 进行储罐的试运行,检查储罐和相关设备运行状态,确保工程质量合格。
六、竣工文件整理6.1 竣工文件的整理,包括施工记录、验收报告和竣工图纸等。
6.2 形成完整的施工档案,确保施工过程和竣工质量留有可查证的记录。
以上就是储罐安装施工方案的简要描述,方案中涉及到的施工步骤和方法均应根据具体的工程要求和实际情况进行调整和完善。
在进行施工过程中,需严格按照安全操作规程进行施工,确保施工过程的安全和质量。
罐体施工方案(3篇)
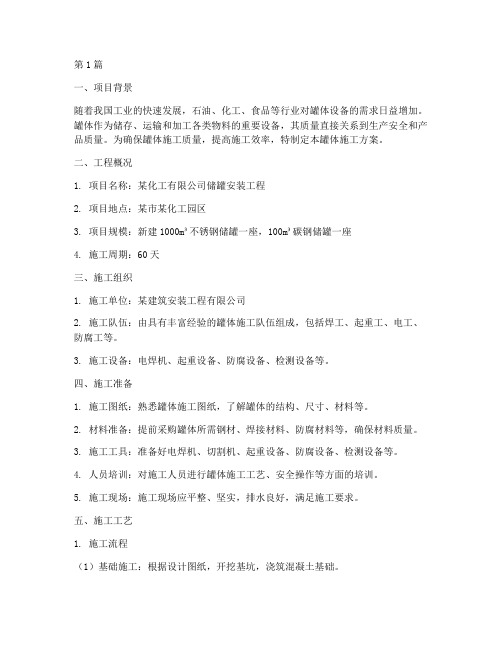
第1篇一、项目背景随着我国工业的快速发展,石油、化工、食品等行业对罐体设备的需求日益增加。
罐体作为储存、运输和加工各类物料的重要设备,其质量直接关系到生产安全和产品质量。
为确保罐体施工质量,提高施工效率,特制定本罐体施工方案。
二、工程概况1. 项目名称:某化工有限公司储罐安装工程2. 项目地点:某市某化工园区3. 项目规模:新建1000m³不锈钢储罐一座,100m³碳钢储罐一座4. 施工周期:60天三、施工组织1. 施工单位:某建筑安装工程有限公司2. 施工队伍:由具有丰富经验的罐体施工队伍组成,包括焊工、起重工、电工、防腐工等。
3. 施工设备:电焊机、起重设备、防腐设备、检测设备等。
四、施工准备1. 施工图纸:熟悉罐体施工图纸,了解罐体的结构、尺寸、材料等。
2. 材料准备:提前采购罐体所需钢材、焊接材料、防腐材料等,确保材料质量。
3. 施工工具:准备好电焊机、切割机、起重设备、防腐设备、检测设备等。
4. 人员培训:对施工人员进行罐体施工工艺、安全操作等方面的培训。
5. 施工现场:施工现场应平整、坚实,排水良好,满足施工要求。
五、施工工艺1. 施工流程(1)基础施工:根据设计图纸,开挖基坑,浇筑混凝土基础。
(2)罐体组装:按照设计要求,将罐体钢板分片组装成罐体。
(3)焊接:采用自动焊接或半自动焊接,确保焊接质量。
(4)无损检测:对焊接部位进行无损检测,确保焊接质量。
(5)防腐处理:对罐体进行防腐处理,提高罐体的使用寿命。
(6)罐体安装:将罐体安装到基础上,调整罐体位置。
(7)试压:对罐体进行试压,确保罐体密封性。
(8)验收:对罐体进行验收,确保施工质量。
2. 施工要点(1)基础施工:严格按照设计图纸进行基础施工,确保基础坚实、平整。
(2)罐体组装:按照罐体施工图纸,将罐体钢板分片组装成罐体,确保组装精度。
(3)焊接:采用自动焊接或半自动焊接,严格控制焊接电流、电压等参数,确保焊接质量。
储罐施工方案(1)

储罐施工方案(1)
前言
储罐是工业生产中常见的设备,用于存储各种液体或气体。
其施工方案的设计
和执行对于储罐的安全运行至关重要。
本文将详细介绍一种储罐的施工方案,包括施工准备、材料准备、施工流程等内容。
施工准备
在进行储罐的施工之前,必须进行充分的准备工作。
首先要确定储罐的类型和
尺寸,以及施工的地点和环境。
然后需要准备相应的施工人员和设备,确保施工过程顺利进行。
此外,还需要制定详细的施工计划和安全方案,以确保施工过程中的安全。
材料准备
在储罐的施工过程中,需要使用各种材料,包括钢板、焊接材料、涂料等。
这
些材料必须符合相关的标准和规定,以确保储罐的质量和安全性。
在进行施工之前,必须对材料进行检查和测试,以确保其符合要求。
施工流程
储罐的施工包括多个步骤,包括制作储罐的结构部分、安装附件、进行焊接和
检测等。
在进行这些工作的过程中,必须确保施工人员遵守相关的操作规程和安全措施,以确保施工质量。
此外,还需要对施工过程进行严格的监控和管理,以及时发现和解决问题。
总结
储罐的施工是一个复杂的过程,需要多方面的准备和协调。
只有在严格遵守相
关规定和标准的情况下,才能保证储罐的安全运行。
希望本文介绍的储罐施工方案能够为相关从业人员提供参考,并促进工程建设的顺利进行。
储罐防腐施工组织方案

储罐防腐施工组织方案一、项目概述储罐是在工业生产中常见的一种存储容器,用于储存各种液体或气体。
储罐的防腐施工是保证储罐使用寿命和安全性的重要环节。
本文通过分析储罐的特点和防腐工艺要求,制定了储罐防腐施工组织方案。
二、施工方案1.施工准备(1)组织施工团队:根据项目规模和工期安排,成立储罐防腐施工团队。
团队成员包括项目经理、技术负责人、施工人员等。
(2)制定施工计划:按照储罐的数量、类型及施工顺序等因素,制定详细的施工计划。
包括施工周期、施工工艺流程等。
(3)采购材料设备:根据防腐工艺要求,采购所需的防腐材料、设备和工具等。
2.施工流程(1)清洗储罐:首先对储罐进行清洗,去除表面的杂质和污物。
清洗过程中应注意保护环境,防止水源污染。
(2)除锈处理:对储罐表面的锈蚀部分进行除锈处理。
可以采用机械除锈、化学除锈或喷砂除锈等方法。
(3)表面处理:储罐表面进行处理,包括光洁度处理、喷砂处理等。
确保储罐表面平整、光滑,有利于防腐材料的附着。
(4)施工防腐层:选择合适的防腐材料,按照施工要求进行涂刷、涂覆或喷涂。
施工过程中要注意涂层的均匀性和厚度控制。
(5)施工检验:完成施工后,进行检验。
检验内容包括涂层的附着力、干燥度和耐化学药品性能等。
3.安全措施(1)严格遵守相关安全规定:在施工过程中,严格遵守相关法律法规和施工安全规定,确保施工安全。
(2)防护装备:施工人员必须佩戴相关防护装备,包括防腐手套、防腐面具等。
保证身体健康和安全。
(3)通风设备:在施工现场设置通风设备,保证工作环境无毒害气体积聚。
(4)应急措施:设置应急疏散通道和应急设备,预先准备应急救援方案,应对可能发生的意外情况。
4.质量控制(1)施工质量要求:制定施工质量标准,明确施工过程中的质量要求。
如涂层厚度、涂层附着力等。
(2)施工记录:施工过程中要进行详细的施工记录,包括施工日期、施工人员、施工材料等。
确保施工过程可追溯和唯一性。
(3)施工检验:安排专业人员进行施工检验,检验包括涂层质量、防腐层的厚度和附着力等。
储罐施工方案A版
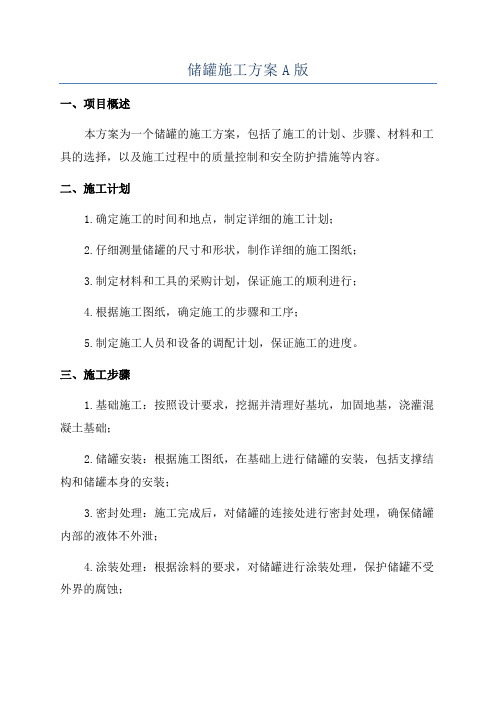
储罐施工方案A版一、项目概述本方案为一个储罐的施工方案,包括了施工的计划、步骤、材料和工具的选择,以及施工过程中的质量控制和安全防护措施等内容。
二、施工计划1.确定施工的时间和地点,制定详细的施工计划;2.仔细测量储罐的尺寸和形状,制作详细的施工图纸;3.制定材料和工具的采购计划,保证施工的顺利进行;4.根据施工图纸,确定施工的步骤和工序;5.制定施工人员和设备的调配计划,保证施工的进度。
三、施工步骤1.基础施工:按照设计要求,挖掘并清理好基坑,加固地基,浇灌混凝土基础;2.储罐安装:根据施工图纸,在基础上进行储罐的安装,包括支撑结构和储罐本身的安装;3.密封处理:施工完成后,对储罐的连接处进行密封处理,确保储罐内部的液体不外泄;4.涂装处理:根据涂料的要求,对储罐进行涂装处理,保护储罐不受外界的腐蚀;5.进行质量验收:对储罐的施工质量进行验收,确保施工质量符合标准。
四、材料和工具的选择1.储罐材料:根据储存物质的特性,选择合适的储罐材料,如钢材、塑料等;2.粘结剂和密封材料:选择合适的粘结剂和密封材料,确保储罐的连接处不会渗漏;3.涂料:选择具有耐腐蚀性能的涂料,确保储罐的表面不会受到腐蚀;4.工具:准备常规的施工工具,如切割机、焊接机、起重机等,以确保施工的顺利进行。
五、质量控制1.施工前,对施工过程中涉及的各个环节进行合理的验收和检测;2.施工过程中,进行适时的质量评估和监督,并及时处理存在的质量问题;3.确保施工人员具备相关的施工经验和技能,以确保施工质量;4.严格按照相关的施工标准和规范进行施工,确保施工质量符合标准。
六、安全防护措施1.施工现场要进行划分,设置安全警示标志,确保施工人员的安全;2.施工人员必须佩戴合适的个人防护装备,如安全帽、安全鞋、防护眼镜等;3.施工现场要保持整洁有序,防止因杂物而引发的安全事故;4.施工现场要设置合适的防护设施,如围栏、安全网等,防止坍塌等事故发生;5.施工过程中,要进行必要的安全培训和安全教育,提高施工人员的安全意识。
罐体施工方案范文

罐体施工方案范文一、施工背景及目标根据计划,本次施工的目标是建设一个容量为5000立方米的储罐。
储罐将被用于存储液体产品,并保证其安全和可靠性。
施工过程中的关注点包括质量控制、安全防范和工期控制。
二、施工前的准备工作1.组织施工团队:成立一个专业的施工团队,包括项目经理、施工技术人员和施工工人。
每个人都必须具备相关经验和技能。
2.技术准备:准备施工所需的设备和工具,包括吊装设备、焊接设备、钢材、焊条等。
3.材料采购:根据计划,及时采购所需的材料,确保施工进度不受材料不足的影响。
4.方案设计:根据设计要求,制定详细的施工方案和施工图纸,并获得相关审批。
三、施工工序1.场地准备:对施工现场进行平整和清理,确保施工区域安全和无障碍。
2.基础施工:进行基础的挖掘和灌注工作,包括土方开挖、坑口安全加固、地下排水系统建设等。
3.罐体组装:根据施工图纸,安装罐体的底板、壁板和顶板。
确保安装时的精度和水平度,并进行焊接、磨平和防腐处理。
4.附件安装:安装储罐的附件,如进出料口、排气阀、液位计、温度计等。
确保安装正确和紧固可靠。
5.内部涂层施工:根据设计要求,对罐体进行内部涂层施工,保护罐体不受腐蚀。
6.外部涂层施工:对罐体进行外部涂层施工,保护罐体不受日晒雨淋。
7.压力测试:对储罐进行压力测试,确保其密封性和承压性能。
8.安全防护:安装安全设施,包括防火系统、防爆系统、喷淋系统等,确保储罐的安全性。
9.验收和交付:进行最终的验收工作,确保储罐符合设计要求。
完成所有合同文件和报告的交接。
四、施工过程中的质量控制1.严格按照设计要求和施工图纸进行施工,确保罐体的尺寸和形状符合要求。
2.监控焊接工艺,确保焊缝质量和强度。
3.进行材料的质量检测,确保材料符合相关标准和规范。
4.进行涂层的质量检测,确保涂层的附着力和耐腐蚀性能。
5.定期进行施工现场的巡查和检查,确保施工质量和安全。
五、施工过程中的安全防范1.制定详细的施工安全计划和应急预案,确保施工过程安全可控。
储罐专项施工方案

一、工程概况本项目为一座容积为10000m3的储罐,用于储存化工原料。
储罐采用现场制作安装的方式,主要分为底板、壁板、顶板、附件等部分。
施工地点位于某化工园区,工程预计工期为3个月。
二、施工准备1. 施工现场准备:施工场地平整,施工用水、电、路畅通;土建基础施工完毕,基础经交接合格,具备施工条件;各类施工人员配备齐全,特种设备操作人员具备相应的资质;施工用各类机具落实到位,材料、半成品、成品、废品堆放场地明确;安全防护措施落实到位。
2. 施工技术准备:认真阅读各项施工技术文件,施工前组织工程技术人员审查图纸,熟悉图纸、设计资料及有关文件,并根据图纸要求和现场情况,编制可行的施工技术方案,并经各级主管部门审批合格。
施工前由非标制作技术人员对全体施工人员进行技术和安全交底。
三、施工方法1. 储罐预制(1)底板:底板采用现场焊接,焊接前对钢板进行打磨、清洗,确保钢板表面无油污、锈蚀等。
焊接过程中采用多层多道焊,保证焊缝质量。
(2)壁板:壁板采用现场卷板成型,成型后进行焊接。
焊接过程中采用多层多道焊,保证焊缝质量。
壁板焊接完成后,进行无损检测,确保焊缝质量。
(3)顶板:顶板采用现场焊接,焊接前对钢板进行打磨、清洗,确保钢板表面无油污、锈蚀等。
焊接过程中采用多层多道焊,保证焊缝质量。
2. 储罐组装(1)底板组装:将预制好的底板放置于基础之上,进行焊接。
焊接过程中采用多层多道焊,保证焊缝质量。
(2)壁板组装:将预制好的壁板逐一安装至底板上,进行焊接。
焊接过程中采用多层多道焊,保证焊缝质量。
(3)顶板组装:将预制好的顶板安装至壁板上,进行焊接。
焊接过程中采用多层多道焊,保证焊缝质量。
3. 储罐附件安装(1)人孔:将人孔安装至罐顶,进行焊接。
(2)透气帽:将透气帽安装至罐顶,进行焊接。
(3)接管:将接管安装至罐壁,进行焊接。
四、质量保证措施1. 人员控制:确保施工人员具备相应的资质,严格执行操作规程。
2. 机具设备控制:确保施工机具设备齐全、完好,定期进行检查和维护。
储罐施工方案
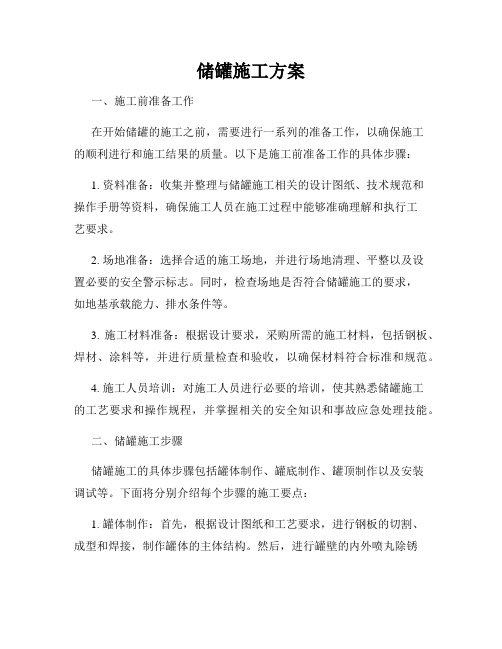
储罐施工方案一、施工前准备工作在开始储罐的施工之前,需要进行一系列的准备工作,以确保施工的顺利进行和施工结果的质量。
以下是施工前准备工作的具体步骤:1. 资料准备:收集并整理与储罐施工相关的设计图纸、技术规范和操作手册等资料,确保施工人员在施工过程中能够准确理解和执行工艺要求。
2. 场地准备:选择合适的施工场地,并进行场地清理、平整以及设置必要的安全警示标志。
同时,检查场地是否符合储罐施工的要求,如地基承载能力、排水条件等。
3. 施工材料准备:根据设计要求,采购所需的施工材料,包括钢板、焊材、涂料等,并进行质量检查和验收,以确保材料符合标准和规范。
4. 施工人员培训:对施工人员进行必要的培训,使其熟悉储罐施工的工艺要求和操作规程,并掌握相关的安全知识和事故应急处理技能。
二、储罐施工步骤储罐施工的具体步骤包括罐体制作、罐底制作、罐顶制作以及安装调试等。
下面将分别介绍每个步骤的施工要点:1. 罐体制作:首先,根据设计图纸和工艺要求,进行钢板的切割、成型和焊接,制作罐体的主体结构。
然后,进行罐壁的内外喷丸除锈和表面处理,并进行材料的质量检验。
最后,对罐体进行涂装和保温处理,确保罐体的耐腐蚀性和保温性能。
2. 罐底制作:罐底的制作包括底板的切割、成型和焊接,以及罐底结构的加固和密封处理。
在制作罐底时,需要根据设计要求进行强度计算和应力分析,以确保罐底结构的安全可靠。
3. 罐顶制作:罐顶的制作包括顶板的切割、成型和焊接,以及顶板和罐壁的连接和密封处理。
在制作罐顶时,需要考虑顶板的荷载承载能力和风荷载的影响,以确保罐顶结构的稳定性和密封性。
4. 安装调试:在完成罐体、罐底和罐顶的制作之后,将它们组装起来,并进行必要的连接和封装。
在安装过程中,需要进行水密性和气密性测试,以确保罐体的质量符合要求。
同时,对安装后的储罐进行调试,包括压力测试和泄漏检验,以验证其正常运行和安全运行。
三、施工质量控制为了确保储罐施工的质量,需要对施工过程进行严格的质量控制。
储罐内部施工方案

储罐内部施工方案1. 简介储罐是用于存储液体或气体等物质的设备,广泛应用于石油、化工、粮食等行业。
在储罐的使用过程中,由于物质的腐蚀、污染等因素,储罐内部需要进行定期的施工维护。
本文将介绍储罐内部施工方案,包括储罐清洗、防腐涂层施工、密封处理等内容。
2. 储罐清洗储罐清洗是储罐内部施工的第一步,其目的是清除储罐内部的污物、沉积物等杂质,为后续的施工工作提供清洁的施工环境。
储罐清洗一般采用水压冲洗的方法,首先将储罐内的液体排空,然后使用高压水枪对储罐内的壁面进行清洗,同时可添加清洗剂来加强清洗效果。
清洗过程中需特别注意安全,确保作业人员的身体健康和储罐的安全。
3. 防腐涂层施工在储罐内部施工过程中,防腐涂层的施工是非常重要的一环。
防腐涂层能有效防止储罐内部的金属材料与储存物质之间的化学反应,避免腐蚀和材料损坏。
常用的防腐涂料有环氧树脂、聚氨酯、氟碳漆等。
防腐涂层施工一般分为以下几个步骤:3.1 表面处理首先,需要对储罐内部的壁面进行表面处理,以保证防腐涂层的附着力。
表面处理包括除锈、打磨、清洗等工艺,可采用机械方法如刷轮机、打磨机等或化学方法如酸洗、碱洗等进行处理。
3.2 底漆涂装在表面处理完成后,开始涂刷底漆。
底漆的选择需考虑储存物质的性质和储罐的材质,底漆一般具有较好的附着力和耐腐蚀性能。
底漆的涂装应按照厂家的技术要求进行,确保涂层的质量和效果。
3.3 中间涂装底漆涂装后,需要进行中间涂装。
中间涂装的选择根据具体情况来定,如需增加涂层的厚度、提高防腐性能等。
中间涂装可以选择与底漆相同的涂料,也可以选择其他具有良好附着力和化学稳定性的涂料。
3.4 面漆涂装中间涂装完成后,最后进行面漆涂装。
面漆涂装一般使用具有良好的耐候性和耐腐蚀性的涂料,以提高涂层的美观度和保护性能。
面漆涂装时需注意均匀涂刷、避免漏刷和滴漏等现象。
4. 密封处理储罐内部施工完成后,还需要进行密封处理,以保证储罐内外的气体、液体无泄漏。
异丁醛施工方案
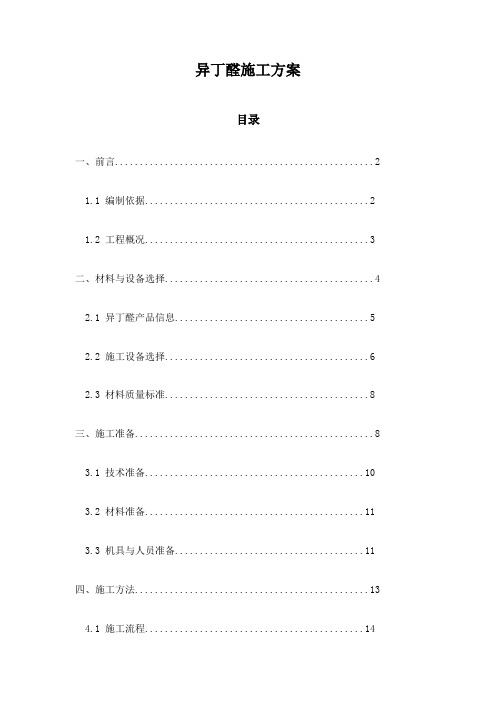
异丁醛施工方案目录一、前言 (2)1.1 编制依据 (2)1.2 工程概况 (3)二、材料与设备选择 (4)2.1 异丁醛产品信息 (5)2.2 施工设备选择 (6)2.3 材料质量标准 (8)三、施工准备 (8)3.1 技术准备 (10)3.2 材料准备 (11)3.3 机具与人员准备 (11)四、施工方法 (13)4.1 施工流程 (14)4.2 施工要点 (15)4.3 特殊部位处理 (16)五、安全及环保措施 (18)5.1 安全防护措施 (18)5.2 环保要求 (19)六、施工进度计划 (20)6.1 总工期规划 (21)6.2 关键节点设置 (22)七、质量控制及验收标准 (24)7.1 质量控制措施 (25)7.2 检验与验收标准 (25)八、维护及保养方案 (27)8.1 使用环境要求 (28)8.2 维护保养周期 (29)九、应急预案与风险控制 (30)9.1 应急预案制定 (31)9.2 风险因素识别与控制 (33)一、前言随着社会的发展和科技的进步,建筑工程的质量要求越来越高,施工过程中的安全问题也日益受到重视。
异丁醛作为一种常用的建筑材料,具有较好的性能和广泛的应用前景,但在使用过程中也存在一定的安全隐患。
制定一套科学合理的异丁醛施工方案,对于确保工程质量、保障施工人员安全以及降低工程风险具有重要意义。
本施工方案旨在为施工单位提供一套详细的异丁醛施工操作指南,包括异丁醛的选材、储存、运输、施工工艺、质量控制等方面的内容。
通过遵循本方案的要求,可以有效地提高异丁醛在建筑工程中的使用效果,降低施工过程中的安全事故发生率,从而保证工程质量和施工人员的生命安全。
本施工方案适用于各种规模的建筑工程,包括住宅、商业、工业等建筑类型。
在实际施工过程中,施工单位应根据自身实际情况,结合本方案的要求,制定具体的施工方案和措施,确保异丁醛施工的安全、顺利进行。
1.1 编制依据本方案基于项目实际需求,结合设计规划进行编制。
- 1、下载文档前请自行甄别文档内容的完整性,平台不提供额外的编辑、内容补充、找答案等附加服务。
- 2、"仅部分预览"的文档,不可在线预览部分如存在完整性等问题,可反馈申请退款(可完整预览的文档不适用该条件!)。
- 3、如文档侵犯您的权益,请联系客服反馈,我们会尽快为您处理(人工客服工作时间:9:00-18:30)。
1、工程概况:1.1.工程名称及相关单位工程名称:丁辛醇中间罐区增建异丁醛储罐工程方案名称:1000m3异丁醛储罐制作安装施工方案建设单位:北京东方石油化工有限公司化工四厂设计单位:北京燕山玉龙石化工程有限公司施工单位:中国化学工程第三建设公司1.2.工程内容北京东方石油化工有限公司化工四厂在丁辛醇中间罐区增建一台异丁醛储罐,一台容积为1000 m3的甲醇储罐需现场进行制作安装,此罐相关技术参数详见下表:工作压力(Pa) 常压材质06Cr19Ni10设计压力(Pa) 2200/-490 空罐质量39920Kg工作温度常温试验正/负压力24500/-1750设计温度70 充水试验高度9700mm介质异丁醛罐底检测真空度≥53 Kpa内径11500mm 罐体高度11244mm2、编制依据:2.1. 《立式圆筒形钢制焊接储罐施工及验收规范》 GB50128-20052.2 《立式圆筒形钢制焊接油罐设计规范》 GB50341-20032.3. 《钢制焊接常压容器》 JB/T4735-19972.4. 《钢结构工程施工质量验收规范》 GB50205-20012.5. 北京燕山玉龙石化工程有限公司提供装配图及其它配套图纸3、施工程序:3.1.3.2.关键工序关键工序一览表序号关键工序名称工序特点、难点、主要实物量及主要技术参数(材质、规格等)备注1 基础验收按照规范、设计要求验收基础2 底板的组装及焊接排版的规范、设计要求,注意搭接的顺序与方法3 顶板的组装及焊接排版的规范、设计要求,4 壁板的组装及焊接排版的规范、设计要求与开孔的方位,弧形与垂直度的检查5 检验底板的真空度与无损检测、壁板的无损检测等,按照规范、设计要求6 沉降试验/充水/充压试验试验方法按照规范、设计要求4、施工方法及施工技术措施甲醇储罐总体施工工艺为倒装法,根据贮罐外形尺寸,利用20t汽车吊配合围带板、铺底板、地面预制顶盖。
焊接方法采用手工电弧焊,制造和安装执行GB50128-2005《立式圆筒型钢制焊接油罐施工及验收规范》的相关规定。
4.1. 材料验收对于工程材料及附件在投用前均应进行验收,包括质量证明书,合格证的验收以及数量规格、型号等检验。
钢板和附件应有清晰的产品标识,当发现问题时,报告供货方进行检验,确认合格后方可使用。
钢板表面局部减薄量、划痕深度与钢板实际负偏差之和,不应大于相应钢板标准允许负偏差值4.2.基础检查验收4.2.1.储罐安装前,必须按土建基础设计文件及对基础表面尺寸进行检查。
基础中心标高允许偏差为±20mm,每10m弧长内任意两点的高差不得大于6mm,任意两点高差不得大于12mm。
4.2.2.基础沥青表面应平整密实,无突出隆起,凹陷及贯穿裂纹等缺陷。
4.2.3.基础表面测点不得小于10点,凹凸面允许偏差≤20mm4.3.样板制作罐在预制组装及检验过程中所使用的样板要求如下:4.3.1. 弧形样板弦长不得小于1.5m,分别制作2组。
4.3.2. 直线样板长度不得小于1m。
4.3.3. 测量焊缝角变形的弧形样板,其弦长不得小于1m,制作2块。
4.3.4. 样板厚度采用δ=0.8mm的铁皮制作。
4.4.罐体的制作4.4.1.制作前,搭设现场预制平台一座,用规格为6000*10000*20钢板铺设。
4.4.2.钢板的切割,不锈钢材料采用等离子切割机进行切割,碳钢材料采用半自动火焰切割机进行切割,钢板坡口加工平整,不得有夹渣、分层、裂纹等缺陷,表面硬化层应去除。
碳钢材料焊条选用用J422,不锈钢材料焊条选用A102,焊接方法为手工电弧焊。
4.4.3.壁板的弧形用三棍卷板机辊圆,卷板后将其立臵在施工平台上,用样板以检查。
垂直方向用直线样板检查,其间隙不得大于2mm,水平方向用弧形样板检查,其间隙不得大于4mm。
4.4.4.抗风圈、加强圈、包边角钢等构件用卷板机辊弧或在胎具上冷煨成形,成形后在平台上检查其翘曲度,偏差不得大于构件的0.1%,且不大于6mm,用弧形样板检查,其间隙不得大于2mm。
4.5.底板铺设与焊接4.5.1.底板预制前应根据设计图纸绘制排版图(见附图)。
罐底的排板直径应按设计直径放大0.1%~0.15%,以补偿焊接收缩。
边缘板沿罐底半径方向的最小直边尺寸不得小于700mm。
4.5.2.底板任意相邻焊缝之间的距离不得小于300mm,且底板边缘板对接焊缝与底圈壁板纵焊缝间距不小于300mm。
4.5.3.碳钢底板铺设前,与基础接触的下表面应根据设计要求进行防腐,但在焊缝两侧留出50mm 范围内不刷漆。
4.5.4.中幅板间搭接时,板与板间用角钢卡具卡紧,搭接宽度应符合图纸要求,允许偏差为±5mm,搭接间隙不大于1mm。
4.5.5.中幅板与边缘板间搭接时中幅板应搭在边缘板的下部,搭接三层板时,应将上层板切角,切角部位尺寸按下图要求进行。
4.5.6.底板的焊接焊接顺序:先焊短缝后焊长缝,从里向外焊工对称均布,第一层焊接采用分段退焊或跳焊法。
底板与壁板的角焊缝,应在最下一带板纵缝焊完后再焊,焊接时焊工均布臵罐内,沿同一个方向进行分段退焊。
4.5.7.罐底的角焊缝要两遍成型,不允许一遍成型。
4.5.8.底焊接完毕后,要将垫板伸出底板的罐部分切除。
4.6.顶板组装与焊接4.6.1.顶板预制下料后,分成大片(扇形),在胎具(伞架)上组对焊接,锥顶高度以及弧度必须按照设计图纸规定,顶板任意相邻焊缝间距不得小于200mm。
用弧形样板检查,间隙不得大于10mm4.6.2.顶板焊接除遵守底板顺序外,还应先焊内侧间断焊缝,后焊外部边缘焊缝,长焊缝宜采用隔缝对称施焊方法,并由中心向外分段退焊,最后焊接顶盖边缘缝。
4.6.3.顶板和包边角钢焊接时,焊工应对称均匀分布,并沿同一方向分段退焊。
顶板和包边角钢焊接在罐顶外侧采用连续焊,焊脚高度不得大于顶板厚度的3/4,且不大于4mm,罐顶内侧不与焊接。
4.6.4.顶板组装方法,应将底板画出中心线找准贮罐的中心,先组装临时支撑柱后分片安装顶板,临时支撑柱安装,其支柱铅垂度允许偏差不应大于柱高的0.1%,且不大于10mm。
4.6.5.加强肋的拼接采用对接接头时,应加垫板,且应全焊透,采用搭接接头时,其搭接长度不得小于加强肋宽度的2倍。
加强肋不得与包边钢相焊。
4.6.6.安装前检查包边角钢的半径偏差(±13mm),顶板应按划好的等分线组装。
4.7.壁板组装与焊接4.7.1.倒链提升数量的确定,按单个倒链提升力为10t倒链计算数量。
n=Gmax/(10×η)=32/(10*0.6)=6式中:n──倒链数量η──折减系数,取0.6Gmax──设备重量4.7.2.罐壁提升操作机械提升操作,首先使倒链钩头拉紧胀圈,并协调使每个倒链受力一致,然后同步拉倒链,每提升200mm 时,必须检查所有倒链的同步性,罐体提升高度允许偏差 ≤30mm ,超过此范围,须调平检查,无异常时方可再提升,提升快到位时,检查及调整其水平度,合格后焊接纵缝。
4.7.3.壁板组装4.7.3.1.壁板组装前应绘制排版图,并按排版图施工。
为了确保环缝对口准确,防止吊装脱节,应沿圆周均匀布臵限位板,间距弧长2~4m 。
4.7.3.2.带板间的活口应对称布臵,环缝组装应从与活口相隔1800处开始分两侧同时向反方向活口处捻缝。
组装到距活口500mm 处时将活口板的多余部分割去,进行最后一道纵缝的组焊,然后将环缝焊完。
最后带板组装留罐内内件安装的通道,当罐内的大量工作完成后再封门。
壁板组装技术要求见下表。
壁板组装允许偏差项 目 允许偏差 任意两点半径 ±13mm 罐壁局部凹凸度 ≤15mm 罐壁垂直度 3mm 纵逢错边量 ≤1mm 环逢错边量 ≤1.5mm 焊逢角变形 ≤12mm4.7.3.3.单圈壁板安装垂直度允许偏差不大于0.3%H(H 为单圈壁板高度1800/1500/1990);相胀 圈倒链提升装置示意图拉筋立柱10t 葫芦罐 壁 罐 顶罐 壁底板挂 板 角 钢邻两壁板上口水平度允许偏差不大于2mm,整个圆周上任意两点水平度的允许偏差不大于6mm。
4.7.3.4.壁板对接接头的组装间隙、坡口型式、尺寸应符合设计要求。
壁板组装时,应保证内表面平齐。
4.7.4. 壁板的焊接4.7.4.1.罐壁的焊接,应先焊纵缝后焊环缝,当焊完相邻两圈壁板的纵向焊缝后,再焊其间的环向焊缝,焊工应均匀分布,分段退焊法焊接。
4.7.4.2.顶圈壁板组装后,应检查其圆度、上口水平度、周长及垂直度,以便安装包边角钢,且包边角钢对接接头与壁板纵向焊缝之间距离,不得小于200mm。
4.7.5.包边角钢自身的接头必须全熔合,全焊透。
4.7.6. 预制完的顶板壁板包边角钢等在堆放、运输和起吊过程中,采取有效措施防止变形。
4.8.附件安装4.8.1. 罐体上的开孔接管的中心位臵,管伸出长度应符合图纸要求,其中中心位臵偏差不大于10mm,外伸长度偏差应为±5mm;其曲率应与罐体应一致,有加强板的接管。
加强板留出检漏口,接管及加强板焊接后用压缩空气进行试漏。
4.9.检验及试验4.9.1.罐底焊缝检验4.9.1.1.所有焊缝采用真空箱法进行严密性试验,试验负压不得低于53KPa,无渗漏为合格。
4.9.1.2.罐底边缘板对接接头,每个焊工施焊的焊缝至少抽查一条。
4.9.1.3.底板三层钢板重叠部分的搭接接头和对接罐底板的T型接头的根部焊道焊完后,在沿三个方向各200mm范围内,应进行渗透检测,全部焊完后应进行渗透或磁粉检测。
对接焊缝为射线检测,搭接焊缝为磁粉检测,合格级分别为RT-Ⅲ,MT-Ⅲ。
4.9.2.罐壁焊缝检查4.9.2.1、纵焊缝:底圈罐壁板每个纵向焊缝中任取300mm进行射线检测,T型焊缝接头应进行25%的射线抽检;其余各圈壁板,每一焊工焊接的每一种板厚(板厚差不大于1mm时可视为同等厚度)在最初焊接的3m焊缝中抽取300mm进行射线检测,以后不考虑焊工人数对每种板厚在每30m及尾数内任意抽取300mm进行射线检测(其中检测位臵25%为T型焊缝接处);4.9.2.2、环焊缝:在最初焊接的3m中任意抽取300mm进行射线检测,以后对于每种板厚,在每60m焊缝及其尾数内的任意部位取300mm进行射线检测,上述检查均不考虑焊工人数。
4.9.2.3、检测方法:对接焊缝为射线检测,搭接焊缝为磁粉检测,合格级分别为RT-Ⅲ,MT-Ⅲ。
4.9.2.4、开孔补强板在焊接结束后,由信号孔通入100~200Kpa压缩空气,检查焊缝严密性,无渗漏为合格。
4.9.2.5、如出现返修等缺陷,如缺陷的位臵距离底片端部,应在该端部延伸300mm做补充检测,如延伸位臵检测不合格,应继续延伸检查。