模具验收检查表
模具验收检查表
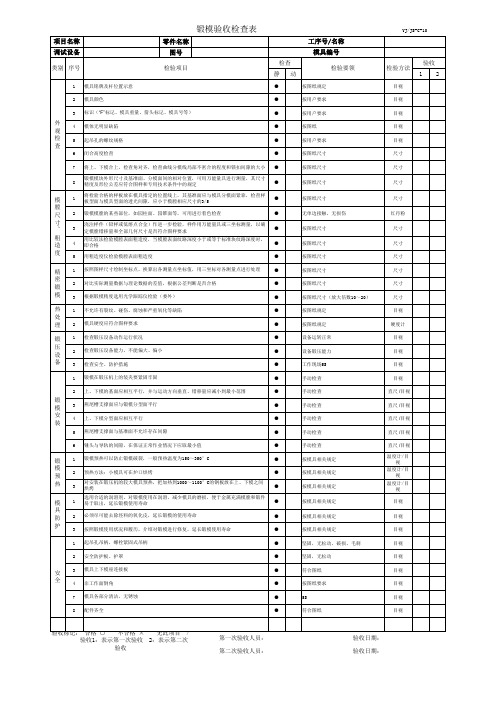
验收 1 2
外 观 检 查
4 5 6 7 8
模 膛 尺 寸 、 粗 造 度 精 密 锻 模 热 处 理 锻 压 设 备
1 2 3 4 5 1 2 3 1 2 1 2 3 1 2
锻 模 安 装
3 4 5 6
锻 模 预 热 模 具 防 护
1 2 3 1 2 3 1 2
安 全
3 4 7 8
验收标记: 合格 ○ 不合格 × 无此项目 / 验收1:表示第一次验收 2:表示第二次 验收
第一次验收人员: 第二次验收人员:
验收日期: 验收日期:
检验要领
检验方法
目视 目视 目视 目视 目视 尺寸 尺寸 尺寸 尺寸 红丹粉 尺寸 尺寸 尺寸 尺寸 尺寸 尺寸 目视 硬度计 目视 目视 目视 目视 直尺 /目视 直尺 /目视 直尺 /目视 直尺 /目视 直尺 /目视 温度计/目 视 温度计/目 视 温度计/目 视 目视 目视 目视 目视 目视 目视 目视 目视 目视
锻模验收检查表
项目名称 调试设备
类别 序号
1 2 3 模具铭牌及杆位置示意 模具颜色 标识(“F”标记、模具重量、箭头标记、模具号等) 模体无明显缺陷 起吊孔的螺纹规格 闭合高度检查 将上、下模合上,检查角对齐,检查曲线分模线局部不密合的程度和锁扣间隙的大小 锻模模块外形尺寸及基准面、分模面间的相对位置,可用万能量具进行测量,其尺寸 精度及形位公差应符合图样和专用技术条件中的规定 将检验合格的样板放在模具指定的位置线上,其基准面应与模具分模面紧靠,检查样 板型面与模具型面的透光间隙,应小于模膛相应尺寸的3/5 锻模模膛的某些部位,如园柱面、园锥面等,可用进行着色检查 浇注样件(铅样或低熔点合金)作进一步检验,样件用万能量具或三坐标测量,以确 定模膛错移量和全部几何尺寸是否符合图样要求 用比较法检验模膛表面粗造度,当模膛表面纹路深度小于或等于标准块纹路深度时, 即合格 用粗造度仪检验模膛表面粗造度 按照图样尺寸绘制坐标点,换算出各测量点坐标值,用三坐标对各测量点进行处理 对比实际测量数据与理论数据的差值,根据公差判断是否合格 根据锻模精度选用光学跟踪仪检验(委外) 不允许有裂纹、碰伤、腐蚀和严重氧化等缺陷 模具硬度应符合图样要求 检查锻压设备动作运行状况 检查锻压设备能力,不能偏大、偏小 检查安全、防护措施 锻模在锻压机上的装夹要紧固牢固 上、下模的基面应相互平行,并与运动方向垂直、错移量应减小到最小范围 燕尾槽支撑面应与锻模分型面平行 上、下模分型面应相互平行 燕尾槽支撑面与基准面不允许存在间隙 锤头与导轨的间隙,在保证正常作业情况下应取最小值 锻模预热可以防止锻模破裂,一般预热温度为150~350°C 预热方法:小模具可在炉口烘烤 对安装在锻压机的较大模具预热,把加热到1000~1100°C的钢板放在上、下模之间 烘烤 选用合适的润滑剂,对锻模使用在润滑,减少模具的磨损,便于金属充满模膛和锻件 易于取出,延长锻模使用寿命 必须尽可能去除坯料的氧化皮,延长锻模的使用寿命 按照锻模使用状况和履历,介绍对锻模进行修复,延长锻模使用寿命 起吊孔吊柄,螺栓紧固式吊柄 安全防护板、护罩 模具上下模座连接板 非工作面倒角 模具各部分清洁,无锈蚀 配件齐全
模具验收表格

制造商:
送检日期:
3、* 模胚冷却水道接口是否有“in”和“out”标识?水道是否畅通无漏水? 水咀牙是否完好? 4、 码模槽是否按标准做?
5、* 限位开关(强行复位)是否按需要和标准做? 6、 拉杆和拉杆螺丝是否按标准做?
7、* 唧嘴是否做定位,定位环? 8、 9、 双托的唧嘴法兰是否压住唧嘴,且法兰和唧嘴之间是否有倒扣? 密封圈是否做成环形?
10、 模芯、压板、压块、行位等上的字码是否铣1mm深的槽,再打钢字? 11、 堵模芯水道是否用螺丝堵? 12、 模胚的导柱孔开排气是否上铣床铣或磨床开10*1mm槽? 13、 分型面是否开过排气?排气位置是否合理? 14、 分型面打磨机飞过的地方是否用油省过?是否光滑? 15、 所有模具配件的倒角,是否用机器倒角? 16、 所有的加工是否按照加工工艺加工? 17、 淬火硬度是否按标准? 凡是要淬火的材料,是否有材料名和淬火硬度? 18、 浇口开的是否合理? 19、 后模是否晒模腔号和材料标记? 20、 热流道模具,热嘴是否固定在模板上?热嘴是否做定位?热咀电源线和感温线是否固定好? 21、 热流道模具前模板是否加装隔热板? 22、 抽芯绞牙,吹气等辅助装置是否能够使用? 23、* 凡是容易装错的字唛,是否有做定位? 24、* 模腔是否有锈迹,是否喷有防锈油? 25、 是否有吊环螺丝孔? 26、* 导柱、导套、顶针、顶针板回针、行位、斜顶是否完好?是否有油?是否顺畅? 27、 其它各部件是否齐全、无损伤、无质量问题? 28、* 共用模胚的模仁上要晒序号。 检查合格的项,在结论框内划“√”,不合格的划“×”,没有的项 □ 备注:
检验人:
日期:
确认:
试模结果〈详细请见试模报告〉: □OK □可生产,但需改进 Prepared by: 结论: □OK □暂收,后续改进
ZAE-ME-006 Mold Inspection Sheet(模具验收检查表)
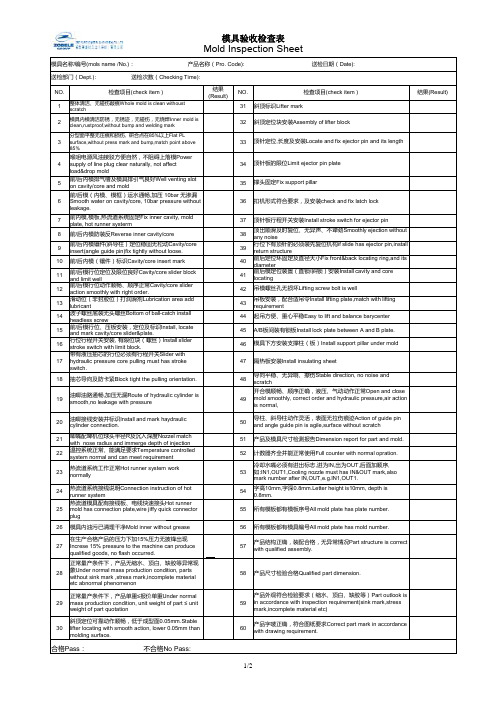
NO.检查项目(check item )结果(Result)NO.结果(Result)1整体清洁、无碰伤敲痕Whole mold is clean withoustscratch312模具内模清洁防锈,无锈迹,无碰伤,无烧焊Inner mold isclean,rustproof,without bump and welding mark323分型面平整无压痕和损伤, 研合点在85%以上Flat PLsurface,without press mark and bump,match point above85%334喉咀电源风油接驳方便自然,不阻碍上落模Powersupply of line plug clear naturally, not affect load&dropmold345前/后内模排气槽及模具排引气良好Well venting sloton cavity/core and mold356前/后模(内模、模框)运水通畅,加压 10bar 无渗漏Smooth water on cavity/core, 10bar pressure withoutleakage.367前内模,模板,热流道系统固定Fix inner cavity, moldplate, hot runner systerm378前/后内模防装反Reverse inner cavity/core389前/后内模镶件(斜导柱)定位稳固无松动Cavity/coreinsert(angle guide pin)fix tightly without loose.3910前/后内模(镶件)标识Cavity/core insert mark4011前/后模行位定位及限位良好Cavity/core slider blockand limit well4112前/后模行位动作顺畅、顺序正常Cavity/core slideraction smoothly with right order.4213滑动位(非封胶位)打润滑剂Lubrication area addlubricant4314波子螺丝底装无头螺丝Bottom of ball-catch installheadless screw4415前/后模行位、压板安装,定位及标识Install, locateand mark cavity/core slider&plate.4516行位行程开关安装, 有限位块(螺丝)Install sliderstroke switch with limit block.4617带有液压抽芯的行位必须有行程开关Slider withhydraulic pressure core pulling must has strokeswitch.4718抽芯导向及防卡紧Block tight the pulling orientation.4819油唧油路通畅,加压无漏Route of hydraulic cylinder issmooth,no leakage with pressure4920油唧接线安装并标识Install and mark haydrauliccylinder connection.5021唧嘴配啤机位球头半径R及沉入深度Nozzel match withnose radius and immerge depth of injection machine5122温控系统正常、能满足要求Temperature controlledsystem normal and can meet requirement5223热流道系统工作正常Hot runner system work normally5324热流道系统接线说明Connection instruction of hotrunner system5425热流道模具配有接线板、电线快速接头Hot runnermold has connection plate,wire jiffy quick connectorplug5526模具内油污已清理干净Mold inner without grease5627在生产合格产品的压力下加15%压力无披锋出现Increse 15% pressure to the machine can producequalified goods, no flash occurred.5728正常量产条件下,产品无缩水、顶白、缺胶等异常现象Under normal mass production condition, partswithout sink mark ,stress mark,incomplete material etcabnormal phenomenon5829正常量产条件下,产品单重≤报价单重Under normalmass production condition, unit weight of part ≤ unitweight of part quotation5930斜顶定位可靠动作顺畅,低于成型面0.05mm.Stablelifter locating with smooth action, lower 0.05mm thanmolding surface.60送检部门(Dept.): 送检次数(Checking Time):合格Pass:不合格No Pass:撑头固定Fix support pillar扣机形式符合要求,及安装check and fix latch lock顶针板行程开关安装Install stroke switch for ejector pin顶出顺滑及时复位、无异声、不犟劲Smoothly ejection without any noise检查项目(check item )斜顶标识Lifter mark斜顶定位块安装Assembly of lifter block顶针定位,长度及安装Locate and fix ejector pin and its length顶针板的限位Limit ejector pin plate行位下有顶针的必须装先复位机构if slide has ejector pin,install return structure前后定位环固定及直径大小Fix front&back locating ring,and its diameter前后模定位装置(直锁/斜锁)安装Install cavity and corelocating吊模螺丝孔无损坏Lifting screw bolt is well吊板安装,配合适吊令Install lifting plate,match with liftingrequirement起吊方便、重心平稳Easy to lift and balance barycenter所有模板都有模具编号All mold plate has mold number.A/B板间装有锁板Install lock plate between A and B plate.模具下方安装支撑柱(板)Install support pillar under mold隔热板安装Install insulating sheet导向平稳、无异响、擦伤Stable direction, no noise and scratch 开合模顺畅、顺序正确,液压、气动动作正常Open and closemold smoothly, correct order and hydraulic pressure,air action is normal,导柱、斜导柱动作灵活,表面无拉伤痕迹Action of guide pinand angle guide pin is agile,surface without scratch产品结构正确,装配合格,无异常情况Part structure is correct with qualified assembly.产品尺寸检验合格Qualified part dimension.产品外观符合检验要求(缩水、顶白、缺胶等)Part outlook is in accordance with inspection requirement(sink mark,stressmark,incomplete material etc)产品字唛正确,符合图纸要求Correct part mark in accordance with drawing requirement.产品及模具尺寸检测报告Dimension report for part and mold.计数器齐全并能正常使用Full counter with normal opration.冷却水嘴必须有进出标志,进为IN,出为OUT,后面加顺序,如:IN1,OUT1,Cooling nozzle must has IN&OUT mark,alsomark number after IN,OUT,e.g.IN1,OUT1.字高10mm,字深0.8mm.Letter height is10mm, depth is 0.8mm.所有模板都有模板序号All mold plate has plate number.1/2NO.检查项目(check item )结果(Result)NO.结果(Result)送检部门(Dept.): 送检次数(Checking Time):检查项目(check item )2/2。
模具检查表

零件号:
总成号:
车型:
G.D&T图号:
产品图纸更改级别:
工装编号及零件名称:
工装设计图纸图号:
制造地点:
联系人:
电话:
分类
项目
验收检查项目
验收检查依据
验收检查方法
模具工程师(供应商)
SQE
(HADF)
型腔尺寸
1
型腔形状是否与X向卡板、Y向卡板符合
产品图
卡板、尺子
2
模具பைடு நூலகம்腔表面过渡是否平滑
产品图
钢板尺
10
骨架定位是否可靠,限位结构是否合理
产品图、模具规范
目测、
钢板尺
整体结构
11
计有无考虑现有载模架的特点,有无开合模干涉
模具规范
钢板尺、角度尺
12
分型面高度选择及尺寸是否满足要求
产品图
目测
13
分型面是否合理,有无错箱
模具规范
钢板尺
14
开模方向是否合理?
产品图
目测
标识
15
是否按照要求制作标识?标识是否正确
产品图
目测
16
标识的高度及过渡状况是否光滑
产品图、模具规范
目测、
钢板尺
其它
17
18
19
合格□
不合格□
不合格建议
返工□自修□让步接收□退货□其他□
检查验收者:验收日期:年月日
模具规范
目测
3
型腔内是否有缩孔等缺陷
模具规范
目测
外部连接
4
加热水管布置是否合理,有无漏水
模具规范
水试
5
模具验收检查单(模具自检表)

4.水嘴周边是否无干涉、妨碍码模。
其它
1.是否按照模具技术协议开模。
2.模具开合是否畅顺,开合顺序是否正确。
3.导套底部是否有排气槽。
4.电气系统是否能正常运作。
5.液压系统是否能正常运作。
验收人员
意见
验收是否合格□合格□不合格会签:
3.抽芯顺序能否可靠实现。
4.滑动面是否加工油槽或者自润滑。
顶出机构
1.顶出孔是否加工,是否与注塑机相配。
2.顶出是否畅顺,顶出顺序能否可靠实现。
3.顶出行程是否足够,顶针板是否有限位。
4.顶针是否已防转。
5.顶针是否装齐、正确。
冷却系统
1.是否已加工。
2.水嘴是否安装连接好,是否畅通,是否有标识。
5.油污、铁屑、杂物等是否清理干净。
6.各镶件是否固定好。
7.面、轮廓是否清晰、光顺无起级。
8.型芯、滑块、镶件是否有烧焊。
浇注系统
1.唧嘴球面R、小端口径、定位圈是否与啤机相配。
2.唧嘴是否已防转。
3.主流道、分流道的粗糙度是否达到要求。
4.是否有冷料井和排气槽。
抽芯机构
1.滑动是否畅顺、可靠。
2.抽芯前后是否有限位,抽芯行程是否足够。
模具验收检查单
产品名称
供应商
产品图号
版本Biblioteka 模穴数模具代码试模次数
验收日期
项目
检验内容
合格
可接受
不接受
备注
外观
1.是否清洁、无生锈、无凹陷及其它影响外观缺陷。
2.模具配件是否影响模具的吊装和存放。
型腔型芯
1.所有零件是否均已安装。
2.型腔型芯表面粗糙度是否达到要求。
模具预验收检查表及报告

1※ 模具3D数据与实物符合性 2※ 模具2D图(组装图)
3 详细油路、电路、水路、动作图 4 模具零件清单 5 模具易损件清单 6※ 模具材质质保书 7 产品自检报告书 8 模具材质处理及检测报告书 9 模具操作和保养手册 10 模具试模工艺记录及出厂检验报告
本组小计得分 本组折合得分 1 模具铭牌(包含模具重量、成型材料、顶出行程等) 2 模具前后模运水铭牌 3 模具开模动作铭牌 4 有热流道的,热流道铭牌是否安装. 5 模具是否安装油路铭牌 6 冷却水嘴是否有进出标记,进水为IN,出水为OUT, 且有对应序号 7 进出油嘴、气嘴是否有标示,并在IN、OUT前空一个字符相应地加G(气)、O 8 各模板吊环(耳)孔字体是否规范 9 产品标示、供应商代码、成型材料、(3C标示)、生产日期等是否符合吉利要求 10 模具部件(可拆卸)是否有清晰的唯一标识,是否有天地侧、操作侧与反操作侧标 本组小计得分 本组折合得分 1 冷却水嘴是否按要求 2 冷却水路是否连接正确 3 水路循环是否可靠,无漏水,易于检修(加压至2-3MPa持续5分钟无漏水现象) 4※ 模具均温性( 按规定的生产节拍连续生产不少于30模以上方可检测) 5 水道隔水片是否采用不易受腐蚀的材料 本组小计得分 本组折合得分 1※ 模具试模动作是否顺畅、可靠、无卡滞、无异响 2 模具回位是否采用强制复位 3※ 模具回位是否顺利,回位是否到位 4※ 产品顶出是否平衡、顺利 5※ 产品取件是否困难,顶出行程是否到位 6※ 顶针顶出是是否滑动,是否划伤产品 7 曲面上顶针是否止转 8※ 顶杆、顶块等顶出机构是否与滑块等干涉,若有干涉是否有强制预复位机构 本组小计得分
车型
件号
验收地 点
模具验收条件描述:
注塑模具预验收检查表(一)
模具验收点检表
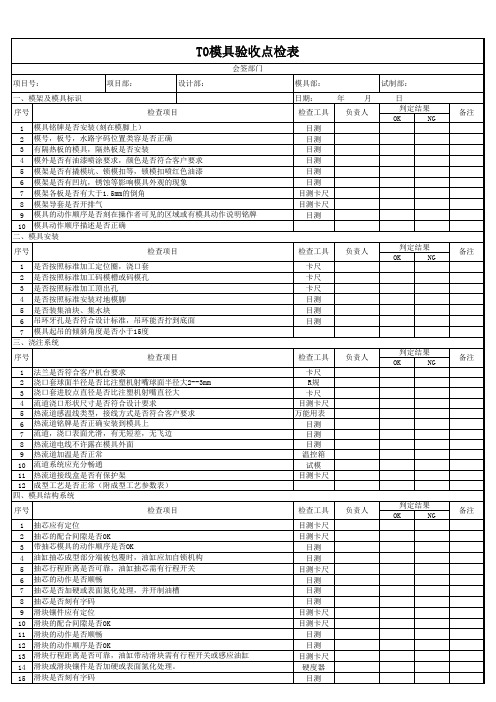
八、液压、电子、控制
检查工具 目测卡尺 目测卡尺 目测 目测 目测卡尺 目测 目测 目测 目测卡尺 目测卡尺 目测 目测 目测卡尺 硬度器 目测
负责人
判定结果 OK NG
备注
16 斜顶配合间隙是否OK 17 斜顶胶位面应抛光,斜顶顶面低于型芯面 18 斜顶的动作是否顺畅 19 斜顶是否刻有字码 20 模具镶件的配合间隙是否OK 21 模具镶件是否需要加硬或表面氮化处理 22 顶块配合间隙是否OK 23 顶块是否需要加硬或表面氮化处理 24 顶块是否刻有字码 25 各活动部件压条、耐磨片是否加硬处理并开制油槽 26 各导向块、导向座是否加硬或表面氮化处理 27 各装配零部件是否有字码,周边非成型边倒C角 28 所有螺牙长度是否有1.5倍螺丝直径 29 大滑块,镶件,抽芯是否有吊装螺孔 五、顶出系统 序号 1 2 3 4 5 6 7 8 检查项目 顶针与滑块是否干涉,有干涉的是否有先复位机构,是否安装行程开关 顶出时应顺畅、无卡滞、无异常声响。 顶出距离应用限位块进行限位。 所有顶杆、顶块应有止转定位,每个顶杆、顶块都应进行编号,顶杆, 顶块不应上下串动 顶杆上加倒钩,倒钩的方向应保持一致,倒钩易于从制品上去除 顶杆孔与杆的配合间隙,封胶段长度,顶杆孔的表面粗糙度应符合客户要求 制品顶出时易跟着斜顶走,顶杆上应加槽或蚀纹 固定在顶杆上的顶块,应牢固可靠,四周非成型部分应加工3-5°的斜面, 下底部周边倒角
T0模具验收点检表
会签部门 项目号: 一、模架及模具标识 序号 检查项目 项目部: 设计部: 模具部: 日期: 检查工具 目测 目测 目测 目测 目测 目测 目测卡尺 目测卡尺 目测 年 月 负责人 试制部: 日 判定结果 OK NG
备注
1 模具铭牌是否安装(刻在模脚上) 2 模号,板号,水路字码位置类容是否正确 3 有隔热板的模具,隔热板是否安装 4 模外是否有油漆喷涂要求,颜色是否符合客户要求 5 模架是否有撬模坑、锁模扣等,锁模扣喷红色油漆 6 模架是否有凹坑,锈蚀等影响模具外观的现象 7 模架各板是否有大于1.5mm的倒角 8 模架导套是否开排气 9 模具的动作顺序是否刻在操作者可见的区域或有模具动作说明铭牌 10 模具动作顺序描述是否正确 二、模具安装 序号 检查项目
模具验收标准检查表

有推板顶出的情况,顶杆是否为延迟顶出,防止顶白。 回程杆端面平整,无点焊,胚头底部无垫垫片、点焊。 斜顶在模架上的避空孔是否因太大影响外观。 固定在顶杆上的顶块是否可靠固定,四周非成型部分应加工 3-5 度的
39 斜度,下部周边倒角。 40 制品是否利于机械手取件。 三板模在机械手取料把时,限位拉杆是否布置在模具安装方向的两
外观
更多免费资料下载请进:
好好学习社区
德信诚培训网 各模板是否有零件编号, 编号在基准角符号正下方离底面 10mm 处, 要 12 求同 11 号。 模具配件是否影响模具的吊装和存放,如安装时下方有外漏的油缸、水 13 嘴、预复位机构等,应有支撑腿保护。 支撑腿的安装是否用螺丝穿过支撑腿固定在模架上, 或过长的支撑腿车 14 加工外螺纹紧固在模架上。 模具顶出孔是否符合指定的注塑机,除小型模具外, 原则上不能只用一 15 个中心顶出 (模具长度或宽度尺寸有一个大于 500mm 时) , 顶出孔直径 应比顶出杆大 5-10mm。 定位圈是否可靠固定(一般用三个 M6 或 M8 的内六角螺丝) ,直径一 16 般为¢100 或¢150mm,高出顶板 10mm。如合同有特殊要求,按全同。 17 定位圈安装孔必须为沉孔,不准直接贴在模架顶面上。 重量超过 8000KG 的模具安装在注塑机上时,是否用穿孔方式压螺丝, 18 不得单独压压板。如设备采用液压锁紧模具,也必须加上螺丝穿孔,以 防液压机构失效。 19 20 21 浇口套球 R 是否大于注塑机喷嘴球 R。 浇口套入口直径是否大于喷嘴注射口直径。 模具外形尺寸是否符合指定的注塑机。 安装有方向要求的模具是否在前模板或后模上用箭头标明安装方向, 22 箭头旁应有“UP”字样,箭头和文字均用漏板喷黄色漆,字高 50mm。 模具 模架表面是否有凹坑、锈迹,多余不用的吊环、进出水、气、油孔等 外观 23 及其他影响外观的缺陷。 24 模架各板是否都有大于 1.5mm 的倒角。
冲压模具验收动静态检查表

A
√
/
/
87
安全护板
厚度22∙Omm,操作安全
C
√
/
/
88
销钉
松紧合适,上下各销•半,安装防脱落装置
C
√
√
√
√
89
侧销孔
船销直径+0∙2mm=侧销孔宜径,无兄动
A
/
√
√
Z
90
侧销固定长度
原则上固定25mm根据直径大小现场判定
A
/
√
√
/
91
侧销锁板销钉
锁板按要求安装摞钉孔不允许人工打磨或加工
65
翻边整形刃口面
顺滑,无凸凹不平等缺陷
B
/
/
/
√
66
翻边整形块安装
间隙W0.05mm,无台阶,圆角顺滑一致
B
/
/\
/
√
67
翻边顶出器顶杆
螺钉孔与顶杆壁厚保证3-5M
B
/
/
/
√
冲压模具静态验收检查表
项目
CN200
零件名称
螺母片
备注:符合要求填写,不符合要求填写“X”,不适用填写
*7”具体问题填入“模具问题记录表”
目视
B
/
7
4
/
102
防护板涂黄色
目视
C
√
Z
/
Z
103
取出压料芯前需要先拆除的镶块涂红色
目视
A
/
√
/
/
104
模具存放块外周边涂红色.
目视
A
√
√
模具验收点检表

供应商:XXX 已量产数: pcs 模具整体重量:234.80KG 机台吨位:180穴数:1*1材质硬度数量外形尺寸(长*宽*高)是否补焊母模仁进口S 136HRC50-521180*130*37.25否公模仁S136HRC48-501180*130*51.5否材质硬度数量公模侧实物照片母模侧实物照片母模仁镶件无无无公模仁镶件S136HRC48-505斜销S136HRC50-5212滑块S136HRC50-524材质硬度数量圆顶针SKD61HRC5421扁顶针SKD61HRC543司筒SKD61HRC541D型顶针SKD61HRC5429供应商材质母模板S50C 公模板S50C上顶出板S50C下顶出板S50C顶出审核: 模具工程师:产品确尺寸量测报告 ■合格 □不合格产品结构&外观 ■合格 □不合格图纸留档方式: □纸档 ■电子档图档保留时间: 纸档 电子档:保留5年结论保养报废模具或项目暂停模具流向及管理:滑动机构滑块底部、背部是否有耐磨块 ■有 □无滑块底部、背部、侧面是否有油槽 ■有 □无斜销侧面是否有油槽 ■有 □无保养点检表:■有 □无 保养时间: 个月保养一次保养内容:防锈保护方式:滑动机构保养方式:模具外观模具标志(铭牌)与实际内容是否相符 ■合格 □不合格表面无严重碰伤、凹陷、变形、生锈 ■合格 □不合格水嘴是否有漏水、是否堵塞 ■合格 □不合格装于模具外侧零件(热浇道接线盒、急回机构等)是否牢固固定 ■合格 □不合格装于模具外侧零件在模具平放时,是否有保护不会被压伤 ■合格 □不合格其他信息补充:外形尺寸(长*宽*高)350*300*50350*300*90350*350*40350*350*25模具信息模具设计&加工地点: 深圳市福永镇凤凰鹰星精密工业有限公司模具寿命: 50万次模具整体外形尺寸(长*宽*高)mm:350*350*321模具形式:□两板模 ■三板模 □双射模 □倒装模 ■冷浇道 □热浇道成型零件 排气方式:■分型面 ■镶件 □其它:模座模具编号:XXX 验收日期:模具当前状态: □生产中 ■待生产 □闲置中 □其他模具签核满足条件:□条件一 □条件二 ■条件三 □条件四 □条件五XXX塑胶模具验收点检表项目、零件名称:XXX底壳XXX结构负责人:。
汽车模具模具验收表
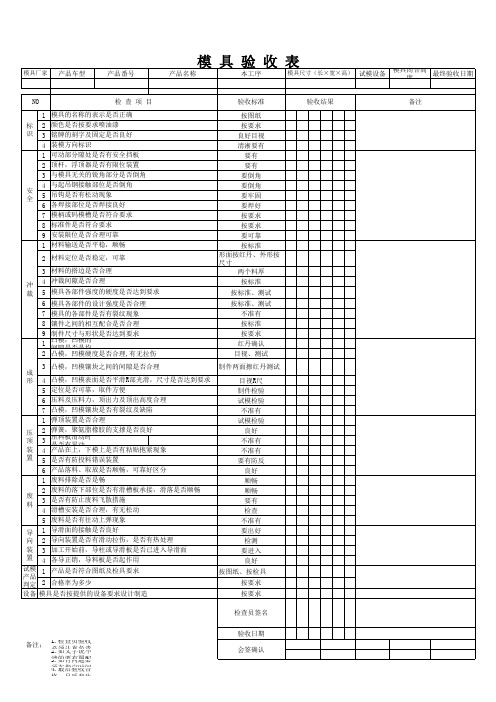
验收结果
备注
标 识
安 全
冲 裁
1 凸模,凹模的间隙是否是均匀的一个料厚 2 凸模,凹模硬度是否合理,有无拉伤 成 形 3 凸模,凹模镶块之间的间隙是否合理 4 凸模,凹模表面是否平滑R部光滑,尺寸是否达到要求 5 定位是否可靠,取件方便 6 压料及压料力,顶出力及顶出高度合理 7 凸模,凹模镶块是否有裂纹及缺陷 1 弹顶装置是否合理 2 弹簧,聚氨脂橡胶的支撑是否良好 3 4 5 6 压料板滑动时是否有晃动,异响等现象 产品在上,下模上是否有粘贴抱紧现象 是否有防投料错误装置 产品落料、取放是否顺畅,可靠好区分
验收标准 按图纸 按要求 良好目视 清淅要有 要有 要有 要倒角 要倒角 要牢固 要焊好 按要求 按要求 要可靠 按标淮 形面按红丹、外形按 尺寸 两个料厚 按标淮 按标淮、测试 按标准、测试 不准有 按标淮 按要求 红丹确认 目视、测试 制件两面擦红丹测试 目视R尺 制件检验 试模检验 不准有 试模检验 良好 不准有 不准有 要有防反 良好 顺畅 顺畅 要有 检查 不准有 要出好 检测 要进入 良好 按图纸、按检具 按要求 按要求 检查员签名 验收日期
模 具 验 收 表
模具厂家
产品车型产品番号源自产品名称本工序模具尺寸(长×宽×高)
试模设备 模具闭合高度 最终验收日期
NO
检 查 项 目 1 模具的名称的表示是否正确 2 颜色是否按要求喷油漆 3 铭牌的刻字及固定是否良好 4 装模方向标识 1 可动部分隙处是否有安全挡板 2 顶杆,浮顶器是否有限位装置 3 与模具无关的锐角部分是否倒角 4 与起吊钢接触部位是否倒角 5 吊钩是否有松动现象 6 各焊接部位是否焊接良好 7 模柄或码模槽是否符合要求 8 标准件是否符合要求 9 安装限位是否合理可靠 1 材料输送是否平稳,顺畅 2 材料定位是否稳定,可靠 3 材料的搭边是否合理 4 冲裁间隙是否合理 5 模具各部件强度的硬度是否达到要求 6 7 8 9 模具各部件的设计强度是否合理 模具的各部件是否有裂纹现象 镶件之间的相互配合是否合理 制件尺寸与形状是否达到要求
模具验收表

49 规尺的调整余量及间隙是否合适 50 规尺的位置是否恰当 51 有无防止误组装装置 52 升降机的动作是否稳定 53 制品排出滑槽宽度是否合适 54 制品有无付着在上模具,下模具 55 部件安装时升降器有无稳定性 56 END 块的接触(高度)是否合适 57 模具高度・模具尺寸是否符合规格 58 购入品有无使用指定品 59 按钮台的旋转是否能正确停止 60 吊钩有无松动 61 U构的厚度和间距对吗(符合规格书) 62 模具固定范围内有无干涉物 63 模具的定位基准是否可以 64 符合材质表示的标记是否对(刻印.其他) 65 是否满足提升规格(叉车用孔ete) 66 重量物(块)有无有眼螺杆用的螺纹 67 有无涂指定的涂装色 68 和铭版的刻印安装是否正确
表 示 ・ 梱 包
69 螺杆有无确实拧紧(涂料确认) 70 上下模具是否有加板条 71 保管PIPE的安装是否可以 72 机械加工面有无防锈 73 在滑动面有无涂布润滑油 74 2次滑槽或者通道有无固定 75 检具上确认是否OK 76 制品上有无夹痕,裂纹,开花(欠肉,伤痕) 77 制品上有无折皱,重叠
中浩精密机械(中山)有限公司 承认 确认 担当
68284785.xls
模具 完成、 模具 完成、检查确认表
大零件番号 大零件名 模具重量 上= kg 制作厂商 承认 确认 担当 下= kg 制作厂商 承认 经历 1 2 3 4 分类 № 确认项目 经历 1 2 3 4 分类 № Total kg 年 月 日 小零件番号 小零件名 模具尺寸 ( W×L×H ) 面的压力) 43 与功能无关的角倒角是否可以 44 有无冲孔模板类的落下防止措施 45 是否符合吊钩的规格
其 它
87 88 89 1. 1 2. 1 ~ 4 ~ 4 模具制作厂商填写 填写确认年月日・检查者.
模具拆模验收点检表A0
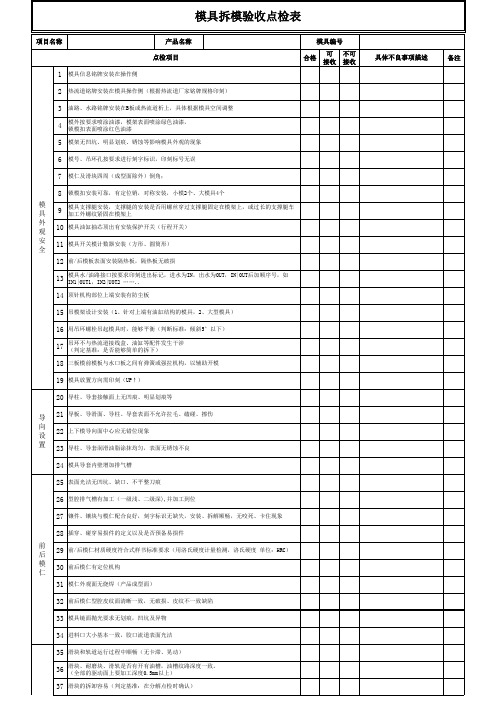
块 系
40 滑块外观面无烧焊(产品成型面)
统 41 产品外观面滑块表面皮纹面清晰、与其它滑块或前后模仁皮纹一致,无破损、不一致
模具编号合格可 接收不可 接收具体不良事项描述
备注
42 产品面及配合功能部位排气槽有加工(一级浅、二级深),并加工到位
43 滑块背面有刻字标识,安装、拆解顺畅无咬死、卡滞现象
6 模号、吊环孔按要求进行刻字标识,印刻标号无误
7 模仁及滑块四周(成型面除外)倒角;
8 锁模扣安装可靠,有定位销,对称安装,小模2个、大模具4个
模 具
9
模具支撑腿安装,支撑腿的安装是否用螺丝穿过支撑腿固定在模架上,或过长的支撑腿车 加工外螺纹紧固在模架上
外 观 10 模具油缸抽芯顶出有安装保护开关(行程开关)
55 顶针板与底板间有垃圾订
56 后模板固定柱,垃圾钉安装是否到位,零件无松动
57 复位弹簧选用标准件,两端不打磨、割断
其 他
58 所有紧固螺丝不允许松动
59 模具装配不允许漏装或装错零件
60 模具开合模具时不允许有异常响声
61 模具使用材质牌号、生产厂家与福尔达式样书指定的要求一致
责任单位
验收公司确认
16 用吊环螺栓吊起模具时,能够平衡(判断标准:倾斜5°以下)
17
吊环不与热流道接线盒、油缸等配件发生干涉 (判定基准:是否能够简单的拆下)
18 三板模前模板与水口板之间有弹簧或强拉机构,以辅助开模
19 模具放置方向需印刻(UP↑)
20 导柱、导套接触面上无凹痕、明显划痕等
导 21 导板、导滑面、导柱、导套表面不允许拉毛、磕碰、擦伤
44 镜像工件应有防错装标识
45 滑块与前后模仁安排配合接触面平整无高低
模具验收检查表

项目编号产品名称供应商
评分项目评分内容Yes No备注
一.模具外观 1.模具外观及所有的模板不能有锈蚀的痕迹,并涂油保护。
2.所有的模板棱边必须倒角且规范。
3.模具的项目号,零件编号是否按要求整齐的打在每个工件上。
4.模具上的标识,标牌是否按规定按装。
要打上天号。
5.模具外观有无严重碰伤,划伤的痕迹,及无用或加工错的孔。
6.模具上所有的吊环孔是否打上标识。
如M24,用12m高的字体。
7.冷却水孔的编号和进出标示是否整齐打在水孔的下方或右侧。
如:IN1 OUT1用12m高的字体。
8.模具上的油嘴,气嘴是否有IN ,OUT的标记。
并在前面加A(
气),O(油)字符。
二.模具分型面1.模具分型面不能有严重的打磨痕迹。
2.模具分型面非封胶面不许有打磨痕迹,且刀路清晰。
3.模具的模口及擦穿碰穿位不许有塌陷及翻边等。
三.模具型腔 1.根据3D检查型腔有无错漏加工。
2.型腔部位有无烧焊的痕迹。
(未经确认的)
C加工结束须根据3D检查型面的若干点面,并记录在案。
见附表:1
4.EDM加工结束须根据3D检查型面的若干点面,并记录在案。
见附表:1
5.模具的型腔面是否顺畅,有无刮痕,可见的火花纹,可见的刀痕。
模具检验表
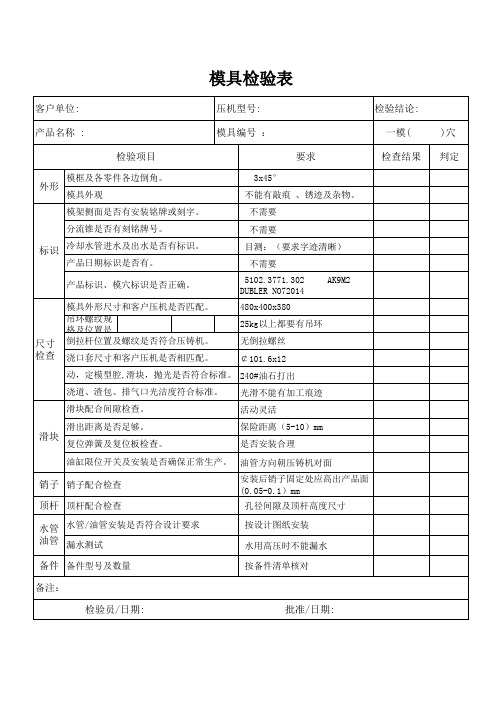
孔径间隙及顶杆高度尺寸
水管 水管/油管安装是否符合设计要求 油管 漏水测试
按设计图纸安装 水用高压时不能漏水
备件 备件型号及数量
按备件清单核对
备注:
检验员/日期:
批准/日期:
判定
模具检验表
客户单位:
压机型号:
检验结论:
产品名称 :
模具编号 :
一模(
)穴
检验项目
要求
检查结果
模框及各零件各边倒角。 外形
模具外观 模架侧面是否有安装铭牌或刻字。 分流锥是否有刻铭牌号。 标识 冷却水管进水及出水是否有标识。 产品日期标识是否有。ຫໍສະໝຸດ 产品标识、模穴标识是否正确。
尺寸 检查
模具外形尺寸和客户压机是否匹配。 吊环螺纹规 格及位置是 倒拉杆位置及螺纹是否符合压铸机。
浇道、渣包、排气口光洁度符合标准。 光滑不能有加工痕迹
滑块配合间隙检查。
活动灵活
滑出距离是否足够。 滑块 复位弹簧及复位板检查。
保险距离(5-10)mm 是否安装合理
油缸限位开关及安装是否确保正常生产。 油管方向朝压铸机对面
销子 销子配合检查
安装后销子固定处应高出产品面 (0.05-0.1)mm
顶杆 顶杆配合检查
浇口套尺寸和客户压机是否相匹配。
3x45°
不能有敲痕 、锈迹及杂物。
不需要
不需要
目测:(要求字迹清晰)
不需要
5102.3771.302 DUBLER NO72014
AK9M2
480x400x380
25kg以上都要有吊环
无倒拉螺丝
¢101.6x12
动,定模型腔,滑块,抛光是否符合标准。 240#油石打出
注塑模具检查验收表

分类成形机械结构是否符图纸 分型面基本结构浇道和浇口
侧面抽芯机构 温度控制 推顶方式 质量 整体配套 其它
模具验收检查表
检查事项 1.确认模具在选定的成型设备上的正确安装方法,紧固螺钉位置,定位圈直径,喷嘴R,浇口套孔径,推 杆孔位置及大小 2.模具尺寸和厚度等是否适合 3.成形设备注射量,注射压力,合模力 是否充分 结构是否符合图纸 分型面研合着点70%以上,制品达无毛刺
1.浇口位置及大小是否适当
2.进料口和浇道大小是否适合 3.浇口形式是否适当
1.抽芯机构设计是否合理,有无卡紧情况
2.抽芯上的重要成型材料,热处理,有无备件
1.模具预热与冷却,采用的水循环是否合理2.冷却水孔的大小位置,数量是否合适 1.所选择的推杆,成形件方式是否适当2.推杆和卸料板的位置及数量是否适当 1.对模具使用的材料,硬度,加工粘度是否符合图样要求和国家标准2.技术协议中的各项条款要逐 条落实,有无遗漏 1.吊环孔及规格大小是否合理 2.大中型模具要有锁紧板 3.液压,电气文件配套安装方便,合理, 整齐,便于操作与运输 4.易损件,备品备件数量齐全,对物验货 1.整体所需全部技术资料,图样 2.关键部件材料化验单,证明 3.备件,易损件图样及半成品图样 4.配套元件生产厂家名称,通讯地址,供货期
模具检查表[空白模板]
![模具检查表[空白模板]](https://img.taocdn.com/s3/m/9a62393ab9f3f90f77c61b54.png)
Part Name.产品名称Ass/装配Pos.O.K N.O.K NA Remark/备注1##########2##########3##########4##########5##########6##########7所有顶针是否地有空隙可活动(0.02mm)##########8##########9##########10##########11##########12##########13##########14##########15##########16###17###18###19###20###21222324v2526272829303132333435日期章能否可以转动3637383940414243表单编号:记录保管期限:5年所有工件是否洗干净.前后模固定板是否有码模槽。
计数器是否有安装隧道铲基是否按要求配模与点检前,后模,整体拍照,检查照片是否清析XX-XXX-XX 版本:V02热咀是否会碰穿流道板。
所有运动部件是否有油槽和上油。
所有模仁工件是否有退磁。
整套模具各散件,对应位置字码是否清析明了。
排气引出槽是否有引出符合标准。
水口勾针有没装对,高度是否正确,无后退,在对应位置是否可转动。
检查PL 面。
行位与行位45度角,与前后模封胶位的FIT 模效果验证。
斜顶的高度检查,是否平胶位面。
(顶针要高出胶面0.04mm)检查斜导柱长度,行位不装弹簧是否能退到位。
顶针强行复装置是否配合到位,开合模是否正常。
进胶孔是否有倒扣,积炭,与流道板贴合位是否有错位,反倒扣。
所有铲基,反铲。
耐磨块贴合面是否做R角,油槽是否标准。
环形镶件与前模仁配合位数据是否核对(配合公差在0.00mm到-0.01mm)环形镶件与模仁外形夹口位数据是否核对清(保证夹口公差在0.01mm之内)环形镶件冬菇头精定位与模仁定位槽位置数据核对过。
回针顶面与回针支撑柱是否贴。
垃圾钉与顶针板是否贴合动模组立后必须把所有斜顶打红丹验证封胶位是否到位。
模具验收检查表
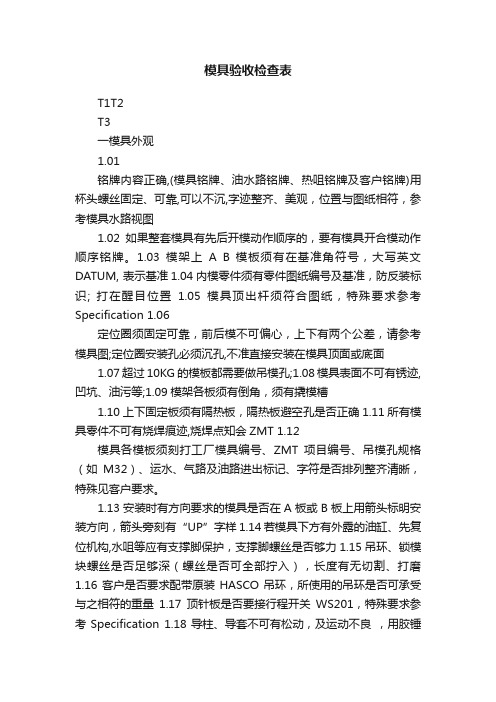
模具验收检查表T1T2T3一模具外观1.01铭牌内容正确,(模具铭牌、油水路铭牌、热咀铭牌及客户铭牌)用杯头螺丝固定、可靠,可以不沉,字迹整齐、美观,位置与图纸相符,参考模具水路视图1.02如果整套模具有先后开模动作顺序的,要有模具开合模动作顺序铭牌。
1.03模架上A B 模板须有在基准角符号,大写英文DATUM, 表示基准1.04内模零件须有零件图纸编号及基准,防反装标识; 打在醒目位置1.05模具顶出杆须符合图纸,特殊要求参考Specification 1.06定位圈须固定可靠,前后模不可偏心,上下有两个公差,请参考模具图;定位圈安装孔必须沉孔,不准直接安装在模具顶面或底面1.07超过10KG 的模板都需要做吊模孔;1.08模具表面不可有锈迹,凹坑、油污等;1.09模架各板须有倒角,须有撬模槽1.10上下固定板须有隔热板,隔热板避空孔是否正确1.11所有模具零件不可有烧焊痕迹,烧焊点知会ZMT 1.12模具各模板须刻打工厂模具编号、ZMT项目编号、吊模孔规格(如M32)、运水、气路及油路进出标记、字符是否排列整齐清晰,特殊见客户要求。
1.13安装时有方向要求的模具是否在A板或B板上用箭头标明安装方向,箭头旁刻有“UP”字样1.14若模具下方有外露的油缸、先复位机构,水咀等应有支撑脚保护,支撑脚螺丝是否够力1.15吊环、锁模块螺丝是否足够深(螺丝是否可全部拧入),长度有无切割、打磨1.16客户是否要求配带原装HASCO吊环,所使用的吊环是否可承受与之相符的重量1.17顶针板是否要接行程开关WS201,特殊要求参考Specification 1.18导柱、导套不可有松动,及运动不良,用胶锤轻敲可进为准。
1.19导柱长度是否足够(合模时比斜导柱要长)、是否弯曲、烧伤等1.20导柱导套配合是否有在底板加工排气槽1.21前、后模半边单独起吊是否平衡,是否要追加平衡吊模孔1.22是否有防锈处理(如前后模芯是否喷白色防锈油)1.23AB 板锁模块及吊模担是否按图纸加工,特殊要求参考Specification;起吊方便、重心平衡二顶出、复位、2.01顶针、顶块等顶出机构与滑块是否干涉,有无强制复位机构,顶针复位须有复位开关,特殊复位开关参考客户Specification2.02油缸抽芯、顶出须行程开关控制,特殊参考Specification 2.03撑头须比模脚高,且不与其他机构干涉2.04顶出是否顺畅、无卡滞,无异响复位杆与B 板无卡滞,EGP 的垂直度与同心度无问题,以手可推动顶针板为标准;2.05 斜顶表面须抛光、加油槽,在最大顶出状况下油槽不超过后模,过大过长的斜顶是否须氮化处理。
- 1、下载文档前请自行甄别文档内容的完整性,平台不提供额外的编辑、内容补充、找答案等附加服务。
- 2、"仅部分预览"的文档,不可在线预览部分如存在完整性等问题,可反馈申请退款(可完整预览的文档不适用该条件!)。
- 3、如文档侵犯您的权益,请联系客服反馈,我们会尽快为您处理(人工客服工作时间:9:00-18:30)。
T1T2
T3
一模具外观
1.01
铭牌内容正确,(模具铭牌、油水路铭牌、热咀铭牌及客户铭牌)用杯头螺丝固定、可靠,可以不沉,字迹整齐、美观,位置与图纸相符,参考模具水路视图
1.02如果整套模具有先后开模动作顺序的,要有模具开合模动作顺序铭牌。
1.03模架上A B 模板须有在基准角符号,大写英文DATUM, 表示基准1.04内模零件须有零件图纸编号及基准,防反装标识; 打在醒目位置1.05模具顶出杆须符合图纸,特殊要求参考Specification 1.06
定位圈须固定可靠,前后模不可偏心,上下有两个公差,请参考模具图;定位圈安装孔必须沉孔,不准直接安装在模具顶面或底面
1.07超过10KG 的模板都需要做吊模孔;1.08模具表面不可有锈迹,凹坑、油污等;1.09模架各板须有倒角,须有撬模槽
1.10上下固定板须有隔热板,隔热板避空孔是否正确1.11所有模具零件不可有烧焊痕迹,烧焊点知会ZMT 1.12
模具各模板须刻打工厂模具编号、ZMT项目编号、吊模孔规格(如M32)、运水、气路及油路进出标记、字符是否排列整齐清晰,特殊见客户要求。
1.13安装时有方向要求的模具是否在A板或B板上用箭头标明安装方向,箭头旁刻有“UP”字样1.14若模具下方有外露的油缸、先复位机构,水咀等应有支撑脚保护,支撑脚螺丝是否够力1.15吊环、锁模块螺丝是否足够深(螺丝是否可全部拧入),长度有无切割、打磨1.16客户是否要求配带原装HASCO吊环,所使用的吊环是否可承受与之相符的重量1.17顶针板是否要接行程开关WS201,特殊要求参考Specification 1.18导柱、导套不可有松动,及运动不良 ,用胶锤轻敲可进为准。
1.19导柱长度是否足够(合模时比斜导柱要长)、是否弯曲、烧伤等1.20导柱导套配合是否有在底板加工排气槽
1.21前、后模半边单独起吊是否平衡,是否要追加平衡吊模孔1.22是否有防锈处理(如前后模芯是否喷白色防锈油)
1.23AB 板锁模块及吊模担是否按图纸加工,特殊要求参考Specification;起吊方便、重心平衡
二顶出、复位、
2.01
顶针、顶块等顶出机构与滑块是否干涉,有无强制复位机构,顶针复位须有复位开关,特殊复位开关参考客户Specification
2.02油缸抽芯、顶出须行程开关控制,特殊参考Specification 2.03撑头须比模脚高,且不与其他机构干涉
2.04顶出是否顺畅、无卡滞,无异响复位杆与B 板无卡滞,EGP 的垂直度与同心度无问题,以手可推动顶针板为标准;2.05
斜顶表面须抛光、加油槽,在最大顶出状况下油槽不超过后模,过大过长的斜顶是否须氮化处理。
斜顶有导滑板,材料为青铜,定位在B 板底部,特殊情况请参考图纸 。
2.06所有滑动部件须有开油槽,装模时是否涂耐高温润滑油,是否须做氮化处理,特殊见客户Specification 2.07所有螺丝要求固定良好,且长度一致,斜顶固定螺丝底板上也要有过孔方便拧紧。
2.08所有顶针须做有定位,并有编号,顶针孔光滑;2.09客户是否同意试模时在复位杆中加弹簧 ;
2.10顶针运动顺畅,不可上下串动,顶针避空孔大小是否合适,B 板过孔比顶针单边大0.5MM;顶针板过孔比顶针单边大0.1MM 2.11固定在顶杆上的顶块固定可靠,须做防转处理 ,顶出块回位于内模配合处需有斜度2.12模具有二次顶出的,二次顶出的行程是否按照图纸要求制做2.13顶针顶出是否顺畅,有无变形和烧伤
2.14顶针胶位面为异形和斜面时,是否有做定位和胶位面有晒纹2.15顶针杯头直径和厚度是否符合图纸标准2.16顶杆及二次顶出装置无偏心;2.17顶针和顶针孔中心是否有偏差
2.18顶针避空孔深度是否合适(从产品面开始30mm)2.19延时顶针动作有无问题
2.20是否使用了特殊型号的顶针(扁形,极细,阶梯,其他),是否可满足生产的要求
2.21回针端面是否平整,无焊点,打磨痕,是否倒角。
A板与回针端面有垫块。
复位杆比平衡块低0.05MM.2.22推块顶出是否顺畅,顶杆是否有避空
2.23顶出距离是否用限位块进行限位,复位时是否到底
No.检查项目
ZMT 项目号(ZMT Project No.): 工厂模号(Supplier Tooling No.): 检查日期(Checking Date):项目工程师(Projekt Engineer): 检查责任人(Check Person): 工厂负责人(Responsible Person):
品质 Qualitaet
备注Bemerkung
T1T2
T3
No.
检查项目
ZMT 项目号(ZMT Project No.): 工厂模号(Supplier Tooling No.): 检查日期(Checking Date):项目工程师(Projekt Engineer): 检查责任人(Check Person): 工厂负责人(Responsible Person):
品质 Qualitaet
备注Bemerkung
T1T2
T3
No.
检查项目
ZMT 项目号(ZMT Project No.): 工厂模号(Supplier Tooling No.): 检查日期(Checking Date):项目工程师(Projekt Engineer): 检查责任人(Check Person): 工厂负责人(Responsible Person):
品质 Qualitaet
备注Bemerkung
T1T2
T3
No.检查项目
ZMT 项目号(ZMT Project No.): 工厂模号(Supplier Tooling No.): 检查日期(Checking Date):项目工程师(Projekt Engineer): 检查责任人(Check Person): 工厂负责人(Responsible Person):
品质 Qualitaet
备注Bemerkung
备注Bemerkung:
1.00合格 " √ ", 不合格 " × ", 让步接收 " ○ ", 不适合项 " / "
Annehmbar " √ ", Nicht annehmbar " × ", Annehmen " ○ ", Sonst " / "
2.00有备注参考客户Specification 的项,须附上客户Specification 给相关检查人员;
Wenn es eine Spezifikation vom Kunden gibt, muss die Spezifikation an die entsprechende Kontrollperson geschickt werden.3.00以上检查项不可将所有检查项目等到走模时检查,须在模具试模后开始检查,以缩短制模周期;
Die oben genannten Teile muessen geprueft werden vor der Verfrachtung des Wkz, sie sollen nach der Abmusterung geprueft werden, um Zeit zu sparen.
4.00模具检查,须逐一拆开模具,逐项检查。
Das Wkz soll demontiert werden, um alle Teile zu ueberpruefen.
检查责任人(Kontrollperson): T1 T2
T3。