无损检测规定
无损检测管理规定

无损检测管理规定1. 背景无损检测是指非破坏性的材料或构件的缺陷检测方法。
它具有广泛的应用范围,例如机械制造、核工业、航空航天、船舶建造等领域。
无损检测技术的逐步发展,为生产制造和质量控制提供了重要的支持。
为了保证无损检测的有效性和准确性,制定无损检测管理规定具有重要的意义。
2. 管理要求2.1 无损检测人员无损检测人员需持有相应的资格证书或证明文件,并符合以下条件:•有专业的无损检测技能;•熟悉相应的无损检测标准;•高度负责,有良好的职业道德和技术素质;•服从工作安排,不能被其他工作干扰;•操作设备时,遵守操作规程和安全规定。
2.2 设备和仪器无损检测设备和仪器应满足相应的技术标准和检定要求。
检测设备应定期进行检定和维护,确保其准确度、稳定性和可靠性。
新购设备和仪器应验收合格,加装抵用部件应按相应规定和标准进行。
2.3 检测工艺无损检测应根据相应的规程和标准进行,并记录检测过程中的关键参数和结果。
检测时,应确保检测的位置、方式和时间符合要求,不影响被测构件的使用和使用寿命,并保证检测结果的准确性和可靠性。
若检测发现需修理的缺陷,应在得到修理方案和方案的批准后,进行修理和重检。
2.4 检测记录无损检测记录是验证检测结果的重要依据。
检测记录应符合相应的规范和标准,内容应完整、准确、可读、可追溯,如检测位置、日期、检验员、检测设备和检测结果等。
检测过程中产生的文档、证书等,也应按要求妥善保存。
2.5 质量管理无损检测的质量管理应按照质量管理体系进行,以保证无损检测具有可靠、准确、可重复和实效性。
应根据检测生产领域的实际情况,制定质量管理方案,包括检测质量目标、检测标准、检测技术和质量记录管理等。
应定期进行质量管理评审,总结经验和不足之处,及时进行改进。
3. 结论无损检测在工业生产中得到了广泛的应用。
管理无损检测必须按照相关要求和标准进行,以保证无损检测结果的准确性和可靠性,及时发现和处理缺陷,降低事故和损失的发生。
无损检测质量管理规定

1.1目的1.1.1无损检测是确保焊接件,锻件制造质量的重要检验手段,为了规范无损检测的控制程序、内容和活动,保证和提高产品质量,特制定本管理制度。
1.1.2本制度适用于公司产品无损检测系统的质量管理。
1.1.3公司产品采用的无损检测方法主要是超声波检测(UT)。
2.2无损检测人员2.2.1公司无损检测人员应按国家质检总局《中国无损检测学会标准CHSNDT001-2007》的规定,经培训考核取得《中国机械工程学会无损检测学会NDT证书》(无损检测)。
2.2.1.1公司无损检测人员技术资格按国家质检总局《中国无损检测学会标准CHSNDT001-2007》的规定分为超声波检测(UT)、磁粉检测(MT)及渗透检测(PT)三种方法和Ⅱ、Ⅱ、Ⅱ级别。
2.2.1.2无损检测人员只能从事与其证书所注明的方法与级别相适应的无损检测工作,其中:Ⅰ级人员可在Ⅱ、Ⅲ级人员指导下进行无损检测操作,记录检测数据,整理检测资料。
Ⅱ级人员可编制一般的无损检测程序,按照无损检测工艺规程或在Ⅲ级人员指导下编写工艺卡,并按无损检测工艺独立进行检测操作,评定检测结果,签发检测报告。
Ⅲ级人员可根据标准编制无损检测工艺,审核或签发检测报告,协调Ⅱ级人员对检测结论的技术争议。
2.3无损检测设备2.3.1公司无损检测设备的性能均应符合国家有关标准的规定。
2.3.2公司无损检测设备需计量的器具应按规定做好检定工作。
2.3.3无损检测人员应正确使用检测设备并做好维护保养工作。
2.4无损检测工作过程的质量控制2.4.1无损检测委托2.4.1.1产品列入生产计划后,由施工员填写《无损检测委托单》送交质量部。
无损检测委托单应详细记入有关产品试件的编号、名称、规格、材质、焊接方法和检测方法、检测比例、检测部位、检测标准、合格级别等内容。
2.4.1.2无损检测前,经过自检和专检确认外观质量合格(影响无损检测评定结论的表面)。
2.4.2无损检测准备2.4.2.1无损检测人员根据委托单按照有关标准规范的要求做好检测准备。
无损检测规定

无损检测规定无损检测规定无损检测是一种能够检测材料或构件内部的缺陷或损伤的非破坏性检测方法。
它通过使用各种物理、化学或其他方法,来检测和分析材料或构件内部的缺陷,以判断其性能、品质和可使用性。
为了保证无损检测的准确性和一致性,制定了以下无损检测规定。
1.无损检测人员资质和培训要求无损检测人员应具备相关领域的知识和技能,并通过相关培训和考试,获得相应的资质证书。
无损检测人员应定期参加进修和培训,更新知识和技术。
2.无损检测设备和工具要求无损检测设备和工具应具备相应的性能指标和质量要求。
具体要求包括设备的准确度、灵敏度、分辨率等。
设备和工具应有有效的检定和校准证书,定期进行检验和维护。
3.无损检测方法选择针对不同材料和构件的不同要求,应根据相关标准和规程选择合适的无损检测方法。
对于特殊材料和特殊构件,应进行相关前期试验和验证,确定最合适的无损检测方法。
4.无损检测操作规程无损检测应按照相关操作规程进行。
操作规程应包括检测前的准备工作、设备和工具的校验和检定、操作流程和步骤、数据处理和分析等内容。
操作规程应经过审批和授权,定期进行评审和更新。
5.无损检测记录和报告无损检测应进行记录和报告。
检测记录应包括检测日期、地点、设备和工具、材料和构件信息、操作步骤和结果等。
检测报告应包括检测结果、缺陷或损伤的类型、位置和大小、评估和分析、建议的修复和维护措施等内容。
检测记录和报告应签字确认,并妥善保存。
6.无损检测质量控制无损检测应建立完善的质量控制体系。
质量控制包括检测设备和工具的校验和检定、操作规程的评审和更新、人员资质的管理和培训等。
质量控制应定期进行内部和外部的审核和评估。
7.无损检测标准和规程的遵守无损检测应符合相关的国家标准和规程要求。
无损检测人员应了解和遵守相关的标准和规程,确保检测结果的准确性和可靠性。
以上是无损检测的规定,根据这些规定,可以保证无损检测的准确性和一致性。
无损检测在工业生产和质量控制中起着重要的作用,能够发现材料和构件内部的缺陷和损伤,预防事故的发生,保障产品质量和安全性。
常用无损检测国家标准
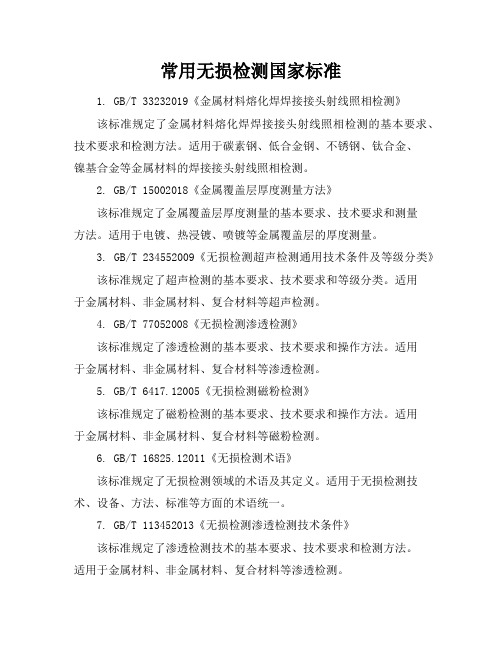
常用无损检测国家标准1. GB/T 33232019《金属材料熔化焊焊接接头射线照相检测》该标准规定了金属材料熔化焊焊接接头射线照相检测的基本要求、技术要求和检测方法。
适用于碳素钢、低合金钢、不锈钢、钛合金、镍基合金等金属材料的焊接接头射线照相检测。
2. GB/T 15002018《金属覆盖层厚度测量方法》该标准规定了金属覆盖层厚度测量的基本要求、技术要求和测量方法。
适用于电镀、热浸镀、喷镀等金属覆盖层的厚度测量。
3. GB/T 234552009《无损检测超声检测通用技术条件及等级分类》该标准规定了超声检测的基本要求、技术要求和等级分类。
适用于金属材料、非金属材料、复合材料等超声检测。
4. GB/T 77052008《无损检测渗透检测》该标准规定了渗透检测的基本要求、技术要求和操作方法。
适用于金属材料、非金属材料、复合材料等渗透检测。
5. GB/T 6417.12005《无损检测磁粉检测》该标准规定了磁粉检测的基本要求、技术要求和操作方法。
适用于金属材料、非金属材料、复合材料等磁粉检测。
6. GB/T 16825.12011《无损检测术语》该标准规定了无损检测领域的术语及其定义。
适用于无损检测技术、设备、方法、标准等方面的术语统一。
7. GB/T 113452013《无损检测渗透检测技术条件》该标准规定了渗透检测技术的基本要求、技术要求和检测方法。
适用于金属材料、非金属材料、复合材料等渗透检测。
8. GB/T 12604.12010《无损检测术语》该标准规定了无损检测领域的术语及其定义。
适用于无损检测技术、设备、方法、标准等方面的术语统一。
9. GB/T 126062010《无损检测磁粉检测技术条件》该标准详细规定了磁粉检测技术的基本要求、技术要求和操作方法。
适用于铁磁性材料如碳钢、合金钢、铸铁等的表面和近表面缺陷的检测。
10. GB/T 50972018《无损检测超声波探伤》该标准适用于金属材料和部分非金属材料的超声波探伤,规定了超声波探伤的基本要求、技术要求和操作方法。
工程施工项目无损检测管理规定
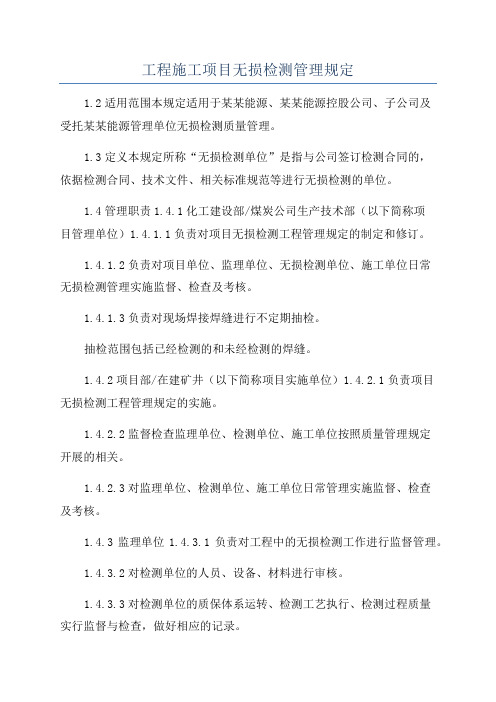
工程施工项目无损检测管理规定1.2适用范围本规定适用于某某能源、某某能源控股公司、子公司及受托某某能源管理单位无损检测质量管理。
1.3定义本规定所称“无损检测单位”是指与公司签订检测合同的,依据检测合同、技术文件、相关标准规范等进行无损检测的单位。
1.4管理职责1.4.1化工建设部/煤炭公司生产技术部(以下简称项目管理单位)1.4.1.1负责对项目无损检测工程管理规定的制定和修订。
1.4.1.2负责对项目单位、监理单位、无损检测单位、施工单位日常无损检测管理实施监督、检查及考核。
1.4.1.3负责对现场焊接焊缝进行不定期抽检。
抽检范围包括已经检测的和未经检测的焊缝。
1.4.2项目部/在建矿井(以下简称项目实施单位)1.4.2.1负责项目无损检测工程管理规定的实施。
1.4.2.2监督检查监理单位、检测单位、施工单位按照质量管理规定开展的相关。
1.4.2.3对监理单位、检测单位、施工单位日常管理实施监督、检查及考核。
1.4.3监理单位1.4.3.1负责对工程中的无损检测工作进行监督管理。
1.4.3.2对检测单位的人员、设备、材料进行审核。
1.4.3.3对检测单位的质保体系运转、检测工艺执行、检测过程质量实行监督与检查,做好相应的记录。
1.4.3.4无损检测单位在实施超声波检测、磁粉检测、渗透检测、电火花测试、材料光谱分析、硬度测试、防腐涂层测试等无损检测时,监理工程师应到场检查、监督实施检测过程,并作好检查记录。
1.4.3.5对重要检测部位(例如黄金焊口)及首次检测焊口,工程师须旁站并填写旁站记录。
旁站记录应包括旁站时间、地点、检测方法、检测部位、检测数量、检测人员是否持证作业。
1.4.3.6对现场焊口标识进行检查和核实,保证无损检测工作的可追朔性。
1.4.3.7对压力容器(容器、管道)的所有底片及TOFD图谱进行复评,复评后督促施工单位送锅检所100%复评验收。
1.4.3.8督促检查各施工单位及检测单位,按图纸进行管线号、焊口号、焊工号及探伤标记的标注,且应醒目、不易脱落。
有关规程标准中有关无损检测的规定

有关规程和标准中 有关无损检测的规定有关承压设备的规程和标准比较多,这里只重点介绍以下规程和标准中有关无损检测的规定: 1. TSG G0001-2012《锅炉安全技术监察规程》(以下简称《锅规》); 2. TSG R0004 -2009《固定式压力容器安全技术监察规程》 (以下简称《固定式容规》); 3. TSG D0001-2009《压力管道安全技术监察规程 工业管道 》 (以下简称《管规》); 4. GB150.4-2011《压力容器 第 4 部分:制造、检验和验收》 (以下简称“ GB150” )。
《锅规》有关无损检测的规定4.5.4 无损检测 4.5.4.1 无损检测人员资格 无损检测人员应当按照有关安全技术规范进行考核,取得资格证书后,方可从事相应方法和技术等级 的无损检测工作。
4.5.4.2 无损检测基本方法 无损检测方法主要包括射线(RT)、超声(UT)、磁粉(MT)、渗透(PT)、涡流(ET)等检测方法。
制造单位 应当根据设计、工艺及其相关技术条件选择检测方法并且制定相应的检测工艺。
当选用超声衍射时差法(TOFD)时,应当与脉冲回波法(PE)组合进行检测,检测结论以 TOFD 与 PE 方 法的结果进行综合判定。
4.5.4.3 无损检测标准 锅炉受压部件无损检测方法应当符合 NB/T 47013 (JB/T 4730)《承压设备无损检测》的要求。
管子对接 接头 X 射线实时成像,应当符合相应技术规定。
4.5.4.4 无损检测技术等级及焊接接头质量等级 (1) 锅炉受压部件焊接接头的射线检测技术等级不低于 AB 级,焊接接头质量等级不低于 II 级; (2) 锅炉受压部件焊接接头的超声检测技术等级不低于 B 级,焊接接头质量等级不低于 I 级; (3) 表面检测的焊接接头质量等级不低于 I 级。
4.5.4.5 无损检测时机 焊接接头的无损检测应当在形状尺寸和外观质量检查合格后进行,并且遵循以下原则: (1) 有延迟裂纹倾向的材料应当在焊接完成 24h 后进行无损检测; (2) 有再热裂纹倾向材料的焊接接头,应当在最终热处理后进行表面无损检测复验; (3)封头(管板)、波形炉胆、下脚圈的拼接接头的无损检测应当在成型后进行,如果成型前进行无损检 测,则应当于成型后在小圆弧过渡区域再次进行无损检测; (4) 电渣焊焊接接头应当在正火后进行超声检测。
无损检测控制规定

更改记录1 目的规定了无损检测的人员、检测工艺、检测过程控制。
2 适用范围适用于金属原材料﹑零配件及焊缝的无损检测。
3 要求3.1无损检测工艺要求3.1.1无损检测通用工艺规程应根据相关法规、技术规范标准的要求,并针对公司的特点和设备技术条件进行编制。
3.1.2无损检测工艺规程应详细、明确、便于操作,检测的操作人员应严格执行工艺规程。
3.1.3无损检测通用工艺规程应有具备无损探伤资格的II人员编制和审核,必须由III级人员批准。
3.2 检测过程的实施3.2.1 无损探伤操作人员必须至少I级以上,报告评审人员必须至少II级以上人员;3.2.2对从事API规范产品的无损探伤人员,必须还按SNT-TC-1A标准进行资格评定;3.2.3无损检测工作必须在外观检查合格并经检查员对检测工件进行确认后进行。
3.2.4 检测人员要明确检测项目和检测方法,对易产生延迟裂纹材质的焊缝的无损检测时间,一般应在焊后24小时以后。
3.2.5 焊缝返修部位的重新检测应由检查员确认返修后,方可重新委托检测,并加注返修次数。
3.2.6 检测人员要完全理解并掌握检测项目的实施细则和设备仪器操作规程,无损检测人员应严格按照工艺卡确定的检测工艺进行现场检测。
3.2.7 检测人员要加强自检和互检,当发现自己和他人的工作出现问题时,应及时纠正。
每次作业前,要清理作业现场,划定安全作业区(警戒绳、警示灯、警示牌)并再次检查现场后方可进行作业,以免误伤他人。
从事x、γ射线作业人员必须携带个人剂量报警仪。
3.2.8 检测中有争议的问题应相互协商,向及时反映,由无损检测质控负责人协调处理。
检测结果评为返修部位者,射线检测下发返修通知单,超声波.磁粉.着色检测在实物上标注缺陷位置。
对检测委托书上注明检测方法、数量、执行标准、合格级别、工件的材质和规格及焊工代号等进行复核,返修委托书还应说明扩检内容。
3.2.9 无损检测焊口的选取根据现场情况确定,对“T”形接头应优先选作检测对象。
无损检测安全管理规定

无损检测安全管理规定(CCESCC/WI-44)1 目的保证无损检测作业人员的健康安全,避免发生辐射伤害,特制定本规定。
2 适用范围本规定适用于公司所属各分(子)公司、项目部的无损检测作业场所。
3 职责3.1 公司质量安全部对本规定实施监督。
3.2 无损检测工程技术有限公司(简称检测公司)负责执行本规定。
3.3 各分(子)公司、项目部安全科负责监督本规定在施工现场作业时的执行。
4 工作程序4.1 现场从事γ射线或X射线的操作人员必须持由国家、省环保核准签发的放射线工作人员上岗操作证。
4.2 放射线作业区应用专门的放射线警戒标志予以隔离,警戒区外应有专人进行巡视,以防无关人员误入警戒区,夜间工作应有灯光警戒标志。
4.3 警戒区范围应使用X射线或γ射线巡测仪进行划定,警戒区外的射线剂量当量应小于国家放射卫生防护标准规定的公众中个人允许受到的年剂量当量(0.5rem)4.4 巡测仪必需每年由法定计量部门进行周期检定以确保计量的准确性。
4.5 X射线机操作时必须有良好的接地,以防电击。
4.6 现场作业的放射线工作人员必须穿戴射线防护服并佩带个人剂量笔。
4.7 剂量笔必须委托通过计量认证的单位进行核定起始数据,并按人名对号发放,个人剂量笔必须本人佩带不得串用。
4.8 个人剂量笔每年必须由取得省级以上人民政府卫生行政部门资质认证的职业卫生技术服务机构核准一次,并建立放射工作人员个人剂量档案。
4.9 新购置的γ源由供方保运到使用地点,并办理交接手续,检测公司中途改变使用地点时,应指派专人、专车运输,并配置报警、防护措施,并有交接手续。
4.10 现场γ源的存放当有专人看守,并有报警防盗措施。
4.11 废弃γ源应由检测公司及时通知供方回收,在没有标准源库的前提下,不得擅自保存。
4.12 现场操作时,出源前,必须对驱动系统试摇三次,确定无问题方可出源。
4.13 出源和收源的全过程必须在巡视仪的监测下进行,确保出源,收源到位。
无损检测RT 评片一次性规定(定稿)

无损检测RT 评片一次性规定(定稿)为了规范特种设备无损检测人员的考核工作,提高射线检测结果的实际考核质量,特制定了本规定,以使实际考核按程序化进行。
基本要求:1.评片考核时间为60分钟(包括报告时间)。
2.底片评定数量为每袋10张,不得以任何理由拒评。
3.射线检测结果的评定和质量分级遵循NB/T .2—2015标准执行。
4.评定内容包括焊接方法、焊接型式、施焊位置、底片质量(黑度、象质指数、伪缺陷情况)、缺陷定性、缺陷定量、缺陷定位、缺陷定级等。
底片有效评定范围的确定:1.底片左上角标注了底片编号、材质及母材的厚度,底片编号为1~10号,要求与底片评定表中的序号相对应。
评片时,要求底片左上角的标签正面放在观片灯窗口的左上角。
2.底片评定范围的确定:对整张底片上焊缝影像及焊缝两侧母材和热影响区均应评定;有丁字焊缝的,纵环焊缝均应评定。
缺陷的定性、定量、定位及定级:1.缺陷定性:按六种缺陷定性:裂纹、未熔合、未焊透、夹渣、气孔、夹钨。
底片上发现的以上各种缺陷均应用汉字注明。
2.缺陷定量:底片上缺陷应确定其数量和尺寸,当存在一种以上的缺陷时应分别标出。
当在一张底片上存在多处性质相同的危险性缺陷时(如裂纹、未熔合、未焊透和条状夹渣),要分别标出其数量及尺寸,并按最严重的进行评级。
裂纹、未熔合、未焊透按长度定量;条形缺陷按长度定量;圆形缺陷按点数定量;圆形缺陷尺寸大于1/2T时,在备注栏注明。
圆形缺陷的黑度不作为这次评级的依据。
3.缺陷定位:将最严重缺陷在评片记录上准确标记,其他缺陷大致标记。
4.缺陷评级:按最严重缺陷进行评级。
圆形缺陷评定区内同时存在圆形缺陷和条形缺陷时,应进行综合评级,并在备注栏注明。
评定级别用罗马字母Ⅰ、Ⅱ、Ⅲ、Ⅳ表示。
5.对于管子对接焊缝,如果确定缺陷为未焊透,只按长度评级,不考虑深度。
如果确定为内凹,在备注中注明,不影响评级。
无损检测管理规定

无损检测管理程序1.适用范围本管理程序适用于项目工程建设、检修的无损检测管理。
2.目的明确本项目对无损检测的质量管理要求,规范无损检测的实施,并确保其结果的真实、公正。
3.定义3.1 独立无损检测单位:在本项目特指由总承包项目部直接委托,并通过业主单位认可的具有相应资质和能力的无损检测单位,其主要工作职能为按总承包项目部指令对各施工承包商委托的第三方无损检测单位的工作质量进行检查、监督和评估。
3。
2 第三方无损检测单位:在本项目特指各施工承包商按照项目管理要求委托,并通过项目认可的无损检测单位,其主要工作职能是承担委托方承包范围内内的无损检测工作。
4.职责4.1 公司项目部:4。
1.1 负责制定项目无损检测管理规定,并贯彻执行;4。
1.2 负责项目无损检测工作的质量管理和控制;4。
1。
3 负责对无损检测单位进行绩效考核;4。
1.4 负责向项目独立无损检测单位发出工作指令;4。
1.5 负责受理各施工承包商对无损检测单位和人员的投诉,组织仲裁无损检测的技术性争议。
4.1。
6 负责组织对无损检测单位进行准入审查;4.1。
7 负责无损检测人员资质的审查;4。
1.8 负责敦促施工承包商为无损检测工作创造有利条件;4。
1.9 负责协调全项目范围内施工与无损检测的交叉作业。
4。
2 第三方无损检测单位:4.2.1 建立满足项目要求的无损检测质量管理体系和相应制度、规程,编制无损检测施工方案和相应工艺;4.2。
2 配备满足工作需要的无损检测人员和设备,尽量保证检测与施工进度同步,质量、工期、服务并举;4。
2.3 强化自身管理,提高检测人员素质,及时反馈检测结果和出具检测报告,并确保其准确性;4.2。
4 积极配合总承包项目部、独立无损检测单位和监理单位的监督、检查,主动与有关部门协调解决无损检测作业中出现的问题;4.2。
5 根据项目HSE要求,妥善保管放射源,严格履行放射作业管理的相应手续;4.2.6 按项目要求及时、准确地提交无损检测统计报表。
无损检测标准要求
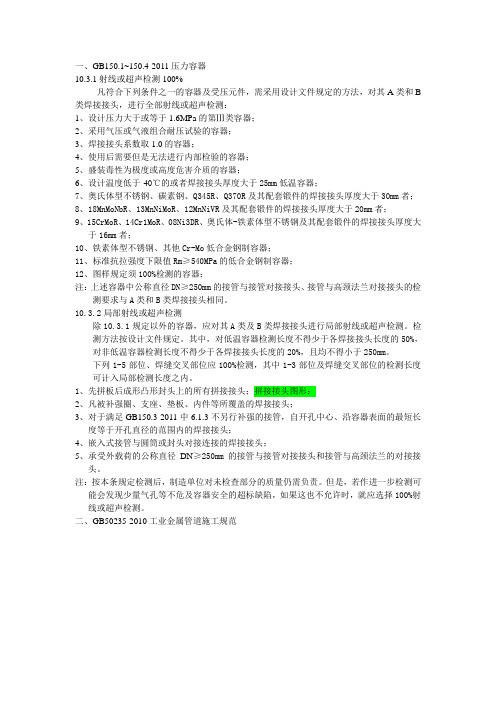
一、GB150.1~150.4-2011压力容器10.3.1射线或超声检测100%凡符合下列条件之一的容器及受压元件,需采用设计文件规定的方法,对其A类和B 类焊接接头,进行全部射线或超声检测:1、设计压力大于或等于1.6MPa的第Ⅲ类容器;2、采用气压或气液组合耐压试验的容器;3、焊接接头系数取1.0的容器;4、使用后需要但是无法进行内部检验的容器;5、盛装毒性为极度或高度危害介质的容器;6、设计温度低于-40℃的或者焊接接头厚度大于25mm低温容器;7、奥氏体型不锈钢、碳素钢、Q345R、Q370R及其配套锻件的焊接接头厚度大于30mm者;8、18MnMoNbR、13MnNiMoR、12MnNiVR及其配套锻件的焊接接头厚度大于20mm者;9、15CrMoR、14Cr1MoR、08Ni3DR、奥氏体-铁素体型不锈钢及其配套锻件的焊接接头厚度大于16mm者;10、铁素体型不锈钢、其他Cr-Mo低合金钢制容器;11、标准抗拉强度下限值Rm≥540MPa的低合金钢制容器;12、图样规定须100%检测的容器;注:上述容器中公称直径DN≥250mm的接管与接管对接接头、接管与高颈法兰对接接头的检测要求与A类和B类焊接接头相同。
10.3.2局部射线或超声检测除10.3.1规定以外的容器,应对其A类及B类焊接接头进行局部射线或超声检测。
检测方法按设计文件规定。
其中,对低温容器检测长度不得少于各焊接接头长度的50%,对非低温容器检测长度不得少于各焊接接头长度的20%,且均不得小于250mm。
下列1-5部位、焊缝交叉部位应100%检测,其中1-3部位及焊缝交叉部位的检测长度可计入局部检测长度之内。
1、先拼板后成形凸形封头上的所有拼接接头;拼接接头图形:2、凡被补强圈、支座、垫板、内件等所覆盖的焊接接头;3、对于满足GB150.3-2011中6.1.3不另行补强的接管,自开孔中心、沿容器表面的最短长度等于开孔直径的范围内的焊接接头;4、嵌入式接管与圆筒或封头对接连接的焊接接头;5、承受外载荷的公称直径DN≥250mm的接管与接管对接接头和接管与高颈法兰的对接接头。
无损检测持证上岗的政策依据
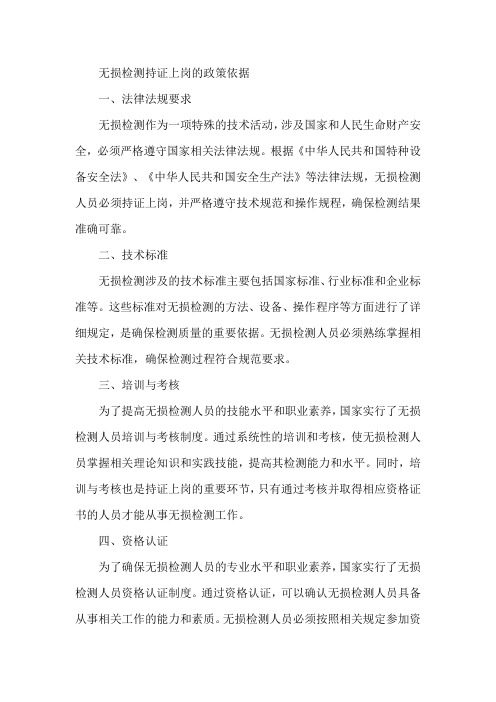
无损检测持证上岗的政策依据
一、法律法规要求
无损检测作为一项特殊的技术活动,涉及国家和人民生命财产安全,必须严格遵守国家相关法律法规。
根据《中华人民共和国特种设备安全法》、《中华人民共和国安全生产法》等法律法规,无损检测人员必须持证上岗,并严格遵守技术规范和操作规程,确保检测结果准确可靠。
二、技术标准
无损检测涉及的技术标准主要包括国家标准、行业标准和企业标准等。
这些标准对无损检测的方法、设备、操作程序等方面进行了详细规定,是确保检测质量的重要依据。
无损检测人员必须熟练掌握相关技术标准,确保检测过程符合规范要求。
三、培训与考核
为了提高无损检测人员的技能水平和职业素养,国家实行了无损检测人员培训与考核制度。
通过系统性的培训和考核,使无损检测人员掌握相关理论知识和实践技能,提高其检测能力和水平。
同时,培训与考核也是持证上岗的重要环节,只有通过考核并取得相应资格证书的人员才能从事无损检测工作。
四、资格认证
为了确保无损检测人员的专业水平和职业素养,国家实行了无损检测人员资格认证制度。
通过资格认证,可以确认无损检测人员具备从事相关工作的能力和素质。
无损检测人员必须按照相关规定参加资
格认证,取得相应资格证书后才能从事相应等级的无损检测工作。
五、监督与管理
为了确保无损检测工作的质量和安全,国家实行了无损检测监督管理制度。
各级政府和相关部门对无损检测工作进行监督和管理,确保其符合法律法规和技术标准的要求。
同时,无损检测机构也必须建立健全内部管理制度,确保检测工作的质量和安全。
无损检测管理规定

.目录 .1.编制说明: (2)2.编制依据: (2)3.管理职责 (2)4.管理内容 (2)5.射线底片质量控制 (4)6.安全、防护 (5)7.报告和记录 (5)8.附录 (6)1.编制说明:1.1为保证检测质量,保障工程质量,依据《压力容器安全技术检查规程》及相关法规、规范,特制订本规定;1.2本规定适用于宁夏煤业集团公司25万吨/年甲醇工程气化装置无损检测工作中的射线检测(r射线、x射线)、超声波检测、磁粉检测渗透检测、超声波测厚的管理。
2.编制依据:《压力容器无损检测》 JB4730 -1994《锅炉大口径管座焊缝超声波探伤》 JB3144 -1982《钢熔化焊对接接头射线照相合质量分级》 JB3323 -1987《钢制压力容器焊接规程》 JB4709 -2000《现场工业设备、管道焊接工程施工及验收规范》 GB50236-19983.管理职责由宁煤项目经理部工程部负责工程中无损检测工作的人员、组织、协调、统一标准,并对无损检测工作质量进行监督管理.4.管理内容4.1 无损检测人员4.1.1各级无损检测人员,必须取得相应等级的无损检测合格证书,持证上岗;4.1.2取得不同无损检测方法和等级证书的人员,只能从事与该方法、该等级相应的无损检测工作,并负相应的技术责任;4.1.3无损检测人员,应熟练掌握有关无损检测工作的条例、规范和标准。
严格执行探伤比例、报废比例,保证底片透照质量,确保检测结果的准确性;4.1.4无损检测人员要认真负责、实事求是、严紧降低合格标准、弄虚作假;4.1.5严格执行无损检测工艺安全操作规程和《放射卫生防护基本标准GB-4792》及公司安全管理的有关规定;4.1.6评定检测结果、审核、鉴发检测报告的无损检测人员,必须持有从事该方法Ⅱ级以上(含Ⅱ级)无损检测资格证书;4.2 无损检测委托4.2.1凡图纸技术条件中有无损检测要求的均可委托检测。
压力容器、管道焊缝检测,硬附排版图、管线图一式三份;4.2.2委托检测的工件表面应符合探伤工艺技术要求。
无损检测规章制度范本最新

无损检测规章制度范本最新第一章总则第一条为规范无损检测工作,确保设备运行安全稳定,保障人员生命财产安全,提高工作效率和质量,制定本规章制度。
第二条本规章制度适用于所有从事无损检测相关工作的人员及单位,包括但不限于无损检测技术人员、无损检测设备、无损检测单位等。
第三条无损检测是利用各种无损检测方法对被检测物体的内部缺陷、病态进行检测、评定和诊断的一种检测方法。
第四条无损检测的目的是提供客观、准确、可靠的检测结果,为设备维护、产品质量控制、故障诊断等提供依据。
第五条无损检测工作应按照国家相关法律法规和行业标准进行,遵循科学、谨慎、客观、公正的原则,保证检测结果的可靠性。
第六条无损检测工作应根据实际情况制定详细的检测方案,选择合适的无损检测方法和设备,进行有效的检测。
第二章无损检测人员管理第七条无损检测人员应具备相关专业知识和技能,持有国家认可的无损检测人员资质证书,熟悉无损检测方法和设备的操作规程。
第八条无损检测人员应严格遵守相关法律法规和行业标准,保守职业秘密,不得利用无损检测技术和信息谋取个人私利。
第九条无损检测人员应接受定期的培训和考核,不断提高自身的技能和综合素质,保持专业能力的水平。
第十条无损检测人员在无损检测过程中应严格按照检测方案和程序进行,保证检测结果的准确性和可靠性。
第十一条无损检测人员应认真履行职责,严守纪律,禁止擅自调整检测方案或使用不合格的设备进行检测。
第三章无损检测设备管理第十二条无损检测单位应具备国家认可的无损检测设备,设备应定期进行检测、校准和维护,确保设备的正确运行。
第十三条无损检测单位应制定详细的设备管理制度,规范设备的使用、保养和维护,延长设备的使用寿命。
第十四条无损检测单位应定期对设备进行检测和校准,确保设备测量精度和准确度符合要求。
第十五条无损检测单位应配备专业技术人员对设备进行维护和维修,及时处理设备故障,确保设备正常运行。
第四章无损检测工作程序第十六条无损检测工作应制定详细的检测方案,包括检测目的、方法、程序、标准和要求等内容。
无损检测规章制度

无损检测规章制度无损检测规章制度是指对无损检测(Non-Destructive Testing,简称NDT)工作进行管理的一套规范和制度。
无损检测是一种利用物质的声学、热学、电磁学、光学等物理特性对物质进行检测的技术手段,其目的是在不破坏被检测物件的前提下,发现物件内部或外部的缺陷、病害、劣化等。
一、无损检测组织和管理1.组织设置:设立无损检测部门,负责无损检测的组织、管理和技术支持,包括人员配备、设备购买和维护等。
2.管理责任:制定无损检测的管理责任制度,明确各级管理人员的职责和权限,确保无损检测工作的高效进行。
二、无损检测人员的资格要求和培训管理1.资格认证:无损检测人员应具备相应的资格证书,包括相关的教育背景和培训经历。
2.培训计划:制定无损检测人员的培训计划,包括理论知识和实践技能的培训,定期进行培训和考核。
3.证书管理:对无损检测人员的证书进行管理,包括证书的登记、更新和维护等,确保证书的有效性和及时性。
三、无损检测设备和工具的管理1.设备购买:根据无损检测的需求,制定设备采购计划,选择适当的设备和工具,确保设备的质量和性能满足要求。
2.设备维护:建立设备维护制度,定期进行设备的检修和维护,确保设备的正常工作和准确性。
3.工具使用:规定工具的使用方法和操作规范,确保无损检测工作的准确和安全。
四、无损检测工作的程序和标准1.检测方案:根据被检测物件的要求和特点,制定相应的检测方案,包括检测方法、参数和步骤等。
2.检测报告:对检测结果进行准确记录,并制作检测报告,包括测试数据、结果分析和评价等。
3.质量控制:建立质量控制制度,确保无损检测的准确性和可靠性,包括对仪器设备的校准和检查,以及对人员的持续培训和评价。
五、无损检测的质量保证和监督体系1.质量保证:建立质量保证体系,确保无损检测的工作质量,包括对工作流程和程序的规范和监控。
2.监督管理:建立监督管理机制,定期检查和评估无损检测工作的质量和效果,及时发现和纠正问题。
无损检测相关要求
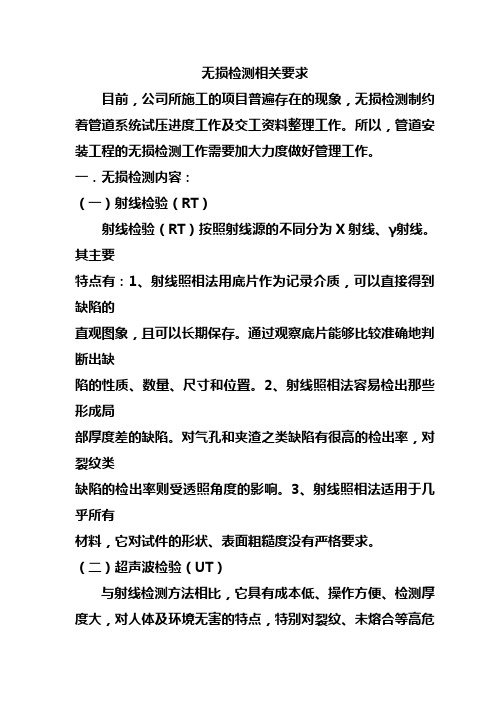
无损检测相关要求目前,公司所施工的项目普遍存在的现象,无损检测制约着管道系统试压进度工作及交工资料整理工作。
所以,管道安装工程的无损检测工作需要加大力度做好管理工作。
一.无损检测内容:(一)射线检验(RT)射线检验(RT)按照射线源的不同分为X射线、γ射线。
其主要特点有:1、射线照相法用底片作为记录介质,可以直接得到缺陷的直观图象,且可以长期保存。
通过观察底片能够比较准确地判断出缺陷的性质、数量、尺寸和位置。
2、射线照相法容易检出那些形成局部厚度差的缺陷。
对气孔和夹渣之类缺陷有很高的检出率,对裂纹类缺陷的检出率则受透照角度的影响。
3、射线照相法适用于几乎所有材料,它对试件的形状、表面粗糙度没有严格要求。
(二)超声波检验(UT)与射线检测方法相比,它具有成本低、操作方便、检测厚度大,对人体及环境无害的特点,特别对裂纹、未熔合等高危险性的面状缺陷有较高的检测灵敏度。
但也有判断缺陷不直观,难以定性和受操作者技术水平、经验、责任心的影响等缺点。
在焊接结构(产品)的质量检验与控制过程中,常常是射线与超声波配合使用,以提高检测结果的可靠性。
(三)磁粉检验(MT)磁粉检测是用来检查焊缝及热影响区的表面和近表面缺陷,磁粉检测仅适用于铁磁性材料,对于有色金属、奥氏体钢、非金属不能采用。
(四)渗透检测(PT)渗透检测包括着色法和荧光法两种。
渗透检测是检查工件或材料表面缺陷的一种方法,它不受材料磁性的限制,除多孔材料外,几乎一切材料的表面缺陷都可以采用此法,但操作工序比较复杂。
二、与无损检测相关的规范及要求GB50235-1997《工业金属管道工程施工及验收规范》根据其7.4.3条要求:管道焊缝检验的射线检测数量应符合下列规定:(一)100%检测比例的对接焊缝,质量等级不低于Ⅱ级:1.输送剧毒液体的管道;2.输送设计压力≥10 Mpa或设计压力≥4Mpa且设计温度≥400℃的可燃流体、有毒流体的管道;3.输送设计压力≥10 Mpa且设计温度≥400℃的非可燃流体、无毒流体的管道;4.设计温度<-29℃的低温管道;5.设计文件要求进行的100%检测比例的管道。
现场设备无损检测管理规定

现场设备无损检测管理规定一﹑总则第一条为提高锅炉﹑压力容器﹑压力管道以及其它受压元件安全使用性能,确保生产装置安﹑稳﹑长﹑满﹑优运行,特制定本规定。
二﹑适用范围第二条本规定适用于公司所属范围内的锅炉﹑压力容器﹑压力管道及其它受压元件的大﹑中﹑小修;日常维护检测,备品﹑备件检测等。
三、定义第三条无损检测:是指采用某种手段,在不损坏被检对象的前提下进行检验﹑评定的一种方法。
四、具体要求第四条目前我公司应用的常规检测方法有:射线探伤、超声探伤、磁粉探伤、渗透探伤、涡流探伤﹑超声测厚、声发射等。
第五条检测标准应按设计图纸规定或相应的国家及部颁规范标准执行。
第六条大中修的检测任务,应按大中修计划中检测项目执行,日常检测由设备所在部门填写申请单,报机动处检测中心。
第七条检测工件表面不得有油污、严重锈蚀、污物等,现场必须具备检测条件,检测人员有权责令设备所在部门按要求使其具备检测条件。
第八条进行х、г射线探伤时,检测部门应及时将探伤时间、地点通知被检部门及调度室。
施工现场都应设有警示绳、警示牌,特殊情况应由安环处安排专人现场监护。
调度室负责通知各岗位及相关人员,各岗位及相关人员不得以任何借口擅离岗位。
第九条现场检测应由车间技术人员指出具体位置及相应的工艺条件(如温度、介质﹑压力等)。
第十条检测人员进入现场后,必须遵守公司安全管理规定,办理相应的作业票证。
第十一条检测完毕后,检测部门应及时将检测结果通知给设备所在部门。
第十二条检测报告应由检测部门、设备所在部门分别存档。
第十三条检测工作由机动处总体负责与协商,其它要求按公司相应规定执行。
第十四条新建项目的工程检测参照此规定执行。
五、罚则第十五条违反上述规定按照经济责任制进行处罚。
六、附则第十六条本规定未尽事宜由机动处负责解释。
第十七条本规定自下发之日起施行。
无损检测规章制度范本下载

无损检测规章制度范本下载第一章总则第一条为加强无损检测工作管理,提高无损检测工作效率和质量,制定本规章制度。
第二条本规章制度适用于公司内的无损检测工作,适用范围包括但不限于设备、管道、构件、焊缝、母材等的无损检测。
第三条公司应建立健全无损检测机构,配备合格的无损检测人员,并严格遵守国家有关规定。
第四条无损检测工作应遵循“预防为主,安全第一”的原则,确保无损检测工作的安全、准确和可靠。
第五条无损检测工作应按照《无损检测程序》执行,确保无损检测结果的准确性和真实性。
第二章无损检测机构第六条公司应设立专门的无损检测机构,配备符合国家标准要求的无损检测设备和仪器。
第七条无损检测机构应配备专业的无损检测人员,人员应具备相关专业技术资格证书,并定期进行培训和考核。
第八条无损检测机构应建立健全的管理制度,明确无损检测工作的职责分工和工作流程。
第三章无损检测人员第九条无损检测人员应按照国家规定的资格要求取得相应无损检测资格证书。
第十条无损检测人员应具备扎实的专业知识和技能,熟悉无损检测设备和方法。
第十一条无损检测人员应遵守无损检测工作的相关规定,严格执行无损检测程序。
第四章无损检测程序第十二条公司应按照国家有关标准和规定制定并执行《无损检测程序》,确保无损检测工作的规范化和标准化。
第十三条无损检测程序应包括但不限于无损检测方法、设备使用、工作流程、结果评定等内容。
第十四条无损检测程序应经过管理部门审核批准后执行,未经批准不得擅自更改。
第五章无损检测工作流程第十五条无损检测工作流程包括但不限于设备检测、焊缝检测、管道检测等内容,应细化明确每项工作的具体步骤和要求。
第十六条无损检测工作应按照程序要求进行,工作人员应严格遵守操作规程,确保无损检测结果的准确性和可靠性。
第十七条无损检测工作结束后应及时整理资料,编制检测报告,并核实报告内容的真实性和准确性。
第六章无损检测结果评定和处理第十八条无损检测结果应由专业无损检测人员进行评定,评定结果应真实准确。
容规国标对检测比例的规定

新《容规》的规定1.无损检测规定压力容器设计单位应当根据本规程、本规程引用标准和JB/T4730的规定在设计图样上规定所选择的无损检测方法、比例、质量规定及其合格级别等。
2.钢板超声检测2.1 检测规定厚度大于或者等于12mm的碳素钢和低合金钢钢板(不涉及多层压力容器的层板)用于制造压力容器壳体时, 凡符合下列条件之一的, 应当逐张进行超声检测:(1) 盛装介质毒性限度为极度、高度危害的;(2) 在湿H2S腐蚀环境中使用的;(3) 设计压力大于或者等于10MPa的;(4) 本规程引用标准中规定逐张进行超声检测的。
2.2 检测合格标准钢板超声检测应当按JB/T 4730 《承压设备无损检测》的规定进行, 用于本规程2.5.1第(1)项至第(3)项的钢板, 合格等级不低于Ⅱ级, 用于本规程2.5.1第(4)项的钢板, 合格等级应当符合本规程引用标准的规定。
3.接管与壳体之间接头设计钢制压力容器的接管(凸缘)与壳体之间的接头设计以及夹套压力容器的接头设计, 可参照本规程引用标准进行。
有下列情况之一的, 应当采用全焊透结构:(1)介质为易爆或者介质毒性为极度危害和高度危害的压力容器;(2)规定气压实验或者气液组合压力实验的压力容器;(3)第Ⅲ类压力容器;(4)低温压力容器;(5)进行疲劳分析的压力容器;(6)直接受火焰加热的压力容器;(7)设计图样规定的压力容器。
4.焊接返修焊接返修(涉及母材缺陷补焊)的规定如下:(1)应当分析缺陷产生的因素, 提出相应的返修方案;(2)返修应当按本规程4.2.1进行焊接工艺评估或者具有通过评估合格的焊接工艺规程(WPS)支持, 施焊时应当有详尽的返修记录;(3)焊缝同一部位的返修次数不宜超过2次, 如超过2次, 返修前应当通过制造单位技术负责人批准, 并且将返修的次数、部位、返修情况记入压力容器质量证明文献;(4)规定焊后消除应力热解决的压力容器, 一般应当在热解决前焊接返修, 如在热解决后进行焊接返修, 应当根据补焊深度拟定是否需要进行消除应力解决;(5)有特殊耐腐蚀规定的压力容器或者受压元件, 返修部位仍需保证不低于原有的耐腐蚀性能;(6)返修部位应当按照原规定通过检测合格。
- 1、下载文档前请自行甄别文档内容的完整性,平台不提供额外的编辑、内容补充、找答案等附加服务。
- 2、"仅部分预览"的文档,不可在线预览部分如存在完整性等问题,可反馈申请退款(可完整预览的文档不适用该条件!)。
- 3、如文档侵犯您的权益,请联系客服反馈,我们会尽快为您处理(人工客服工作时间:9:00-18:30)。
无损检测规定
《海上高速船入级与建造规范》(1996)
第124页第8章船体结构建造工艺第6节质量检验
8.6.2焊缝检验
8.6.2.1.所有完工焊缝均应经外观检查。
外观检查可用眼或5倍放大镜检查。
焊缝的尺寸应符合图纸或有关标准的要求,表面平顺,成形良好。
8.6.2.2.焊缝表面不允许有裂纹、夹渣、未填满、气孔、焊穿、过烧和焊瘤等缺陷。
板厚小于或等于3mm者,不允许存在咬边;板厚大于3mm者咬边深度应不大于0.5mm,其累积长度不得超过单条焊缝长度的10%,且不得大于100mm。
8.6.2.3.船体主要结构的焊缝应经无损检测,检测范围由工厂与验船师商定。
建议射线检查范围应不少于主船体对接焊缝的5%。
重要结构的角焊缝应经超声波检查。
缺陷的评定标准应经本社同意。
《内河小型船舶建造检验规程》(1987)
适用范围:
钢质船舶:船长不超过30m;主柴油机额定功率不超过220KW(300马力),或双机不超过440KW(600马力);发电机单机容量不超过15KW。
如船舶某部分超过规定,超过部分的
技术监督检验应按本局的《船舶建造检验规程》实施。
第258页第3章船体装配及焊接的检验
3.4焊缝无损探伤的检验
3.4.1.船体焊缝的无损探伤检验应在焊缝表面质量检验合格后进行。
无损探伤检验可采用射线透视,超声波探伤或其它有效的方法进行。
3.4.2.射线透视的底片质量和焊缝无损探伤质量的评级,应按验船部门同意的评定标准。
3.4.3.无损探伤的检查范围和位置,应经验船师同意,验船师可根据实际情况适当增加或减少检查范围或指定检查位置。
探测位置应重点选在船中部0.4L区域内的强力甲板、舷侧外板、船底板等纵横焊缝交叉点和分段大合拢的环形焊缝。
探测长度与船舶主体焊缝总长的比例,应不少于0.5%~1%,具体拍片数量应征得验船师同意。
对非机动船和船长小于20米以下的机动船,验船师可根据实际情况少探或免探。
3.4.4.经无损探伤后发现有不允许存在内在缺陷的焊缝时,应对该段焊缝中认为缺陷有可能延伸的一端或两端进行延伸探伤。
不合格的焊缝应批清重焊,返修后应再次进行无损探伤。
如仍不合格,须查明原因后才准进行第二次批清重焊。
3.4.5.验船师如对超声波探伤的检查结果有疑问时,可对有疑问的焊缝部位要求用射线透视复查。
《船舶建造检验规程》(1984)
1.2适用范围:
本规程适用于悬挂中华人民共和国国旗的下列钢质船舶:
总吨位为150及以上的海船;
船长30m及以上的内河船;或主机单机大于等于220KW(300马力),或双机大于等于440KW (600马力)的船舶。
第6页第4章船体装配及焊接检验
4.3焊缝无损探伤的检验
4.3..1.射线透视的底片质量及焊缝质量等级的评定应符合验船部门同意的标准
4.3..2.焊缝射线透视的检查范围和位置应经验船师审查批准,验船师可根据实际情况适当增加或减少检查范围及指定检查位置。
下列主要构件部位的焊缝应作重点检查:
1)船中部0.4L区域内的强力甲板、舷顶列板、舷侧外板、船底板等纵横焊缝交叉点和船体分段大合拢的环形焊缝,以及平板龙骨对接缝和圆弧形舷顶列板的对接缝;
2)强力甲板舱口角隅板;
3)船中部0.4L区域内的纵向骨架和纵舱壁扶强材的对接接头;
4)起重桅(柱)的对接缝,包括焊缝上的每个交叉点;
5)机舱内底板与机座面板的边接缝;
6)其它各层甲板、平台板、内底板的纵横舱壁的对接焊缝。
焊缝透视的长度与各焊缝总长的比例应征得验船部门同意。
4.3..3.如用超声波探伤来代替射线透视检查,则其替代部位和数量应事先征得验船师同意。
如对超声波探伤的检查结果有疑问时,则应对有疑问的焊缝部位用射线透视查验。
《内河高速船入级与建造规范》(2002)
第144页第9章船体建造工艺第6节质量检验
4.3焊缝检验
9.6.2.1.所有完工焊缝均应经外观检查。
外观检查可用眼或5倍放大镜检查。
焊缝的尺寸应符合图纸或有关标准的要求,表面平顺,成形良好。
9.6.2.2.焊缝表面不允许有裂纹、夹渣、未填满、气孔、焊穿、过烧和焊瘤等缺陷。
板厚小于或等于3mm者,不允许存在咬边;板厚大于3mm者咬边深度应不大于0.5mm,其累积长度不得超过单条焊缝长度的10%,且不得大于100mm。
9.6.2.3.船体主要结构的焊缝应经无损检测,检测范围由工厂与验船师商定。
建议射线检查范围应不少于主船体对接焊缝的5%。
重要结构的角焊缝应经超声波检查。
缺陷的评定标准应经本社同意。
9.6.2.4.当船体结构需要进行无损探测时,工厂应制定详细的检测工艺规程,并提交验船师认可,规程中至少应包括拟采用的检测方法,检测范围以及检测点的布置内容。