ATR技术在天然气转化制取甲醇合成气工艺中的工业应用
甲烷制备合成气工艺开发进展 (1)
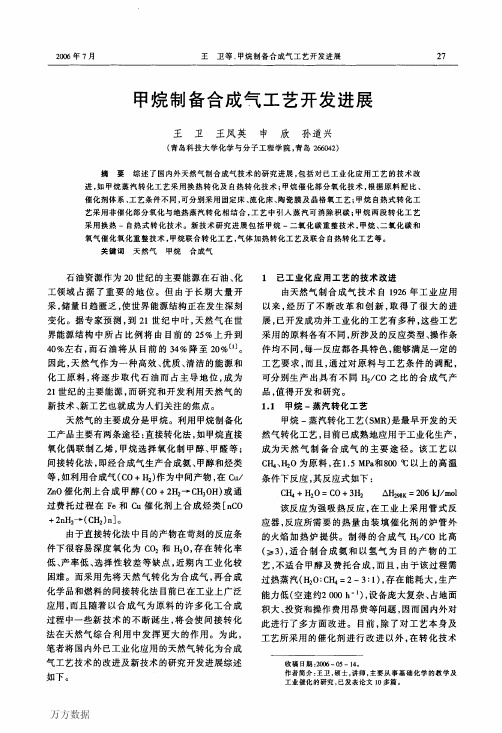
该反应可在较低温度(750—800℃)下达到 90%以上的热力学平衡转化,反应接触时间短 (<10。2 s),可避免高温非催化部分氧化法伴生 的燃烧反应,CO和H2的选择性高达95%,生成 合成气的H2/CO比接近2,适合于合成甲醇、费托 合成等后续工业过程。与传统的蒸汽转化法和联 合重整法相比,甲烷催化部分氧化制合成气的反 应器体积小、效率高、能耗低,可显著降低设备投 资和生产成本。因此,此工艺受到国内外的广泛 重视,研究工作十分活跃。自90年代以来,人们 针对甲烷催化部分氧化反应所采用的氧化剂、原 料配比、催化剂体系、工艺条件及反应器的不同已 开发出固定床【3,4|、流化床[5,63以及陶瓷膜工艺 等【71 93。对这些工艺进行开发的国外公司主要有
石油资源作为20世纪的主要能源在石油、化 工领域占据了重要的地位。但由于长期大量开 采,储量日趋匮乏,使世界能源结构正在发生深刻 变化。据专家预测,到2l世纪中叶,天然气在世 界能源结构中所占比例将由目前的25%上升到 40%左右,而石油将从目前的34%降至20%…。 因此,天然气作为一种高效、优质、清洁的能源和 化工原料,将逐步取代石油而占主导地位,成为 21世纪的主要能源,而研究和开发利用天然气的 新技术、新工艺也就成为人们关注的焦点。 天然气的主要成分是甲烷。利用甲烷制备化 工产品主要有两条途径:直接转化法,如甲烷直接 氧化偶联制乙烯,甲烷选择氧化制甲醇、甲醛等; 间接转化法,即经合成气生产合成氨、甲醇和烃类 等,如利用合成气(CO+H2)作为中间产物,在Cu/ ZnO催化剂上合成甲醇(CO+2H2一cn308)或通 过费托过程在Fe和cu催化剂上合成烃类[nCO +2nH2一(CH2)n]。 由于直接转化法中目的产物在苛刻的反应条 件下很容易深度氧化为C02和H20,存在转化率 低、产率低、选择性较差等缺点,近期内工业化较 困难。而采用先将天然气转化为合成气,再合成 化学品和燃料的间接转化法目前已在工业上广泛 应用,而且随着以合成气为原料的许多化工合成 过程中一些新技术的不断诞生,将会使间接转化 法在天然气综合利用中发挥更大的作用。为此, 笔者将国内外已工业化应用的天然气转化为合成 气工艺技术的改进及新技术的研究开发进展综述 如下。
年产10万吨甲醇工艺设计

1 总论1.1 概述甲醇作为及其重要的有机化工原料,是碳一化学工业的基础产品,在国民经济中占有重要地位。
长期以来,甲醇都是被作为农药,医药,染料等行业的工业原料,但随着科技的进步与发展,甲醇将被应用于越来越多的领域。
1)甲醇(英文名;Methanol,Methyl alcohol)又名木醇,木酒精,甲基氢氧化物,是一种最简单的饱和醇。
化学分子式为CH3OH。
甲醇的性质;甲醇是一种无色、透明、易燃、易挥发的有毒液体,略有酒精气味。
分子量32.04,相对密度0.792(20/4℃),熔点-97.8℃,沸点64.5℃,闪点12.22℃,自燃点463.89℃,蒸气密度 1.11,蒸气压13.33KPa(100mmHg 21.2℃),蒸气与空气混合物爆炸下限6~36.5 % ,能与水、乙醇、乙醚、苯、酮、卤代烃和许多其他有机溶剂相混溶,遇热、明火或氧化剂易燃烧。
甲醇的用途;甲醇用途广泛,是基础的有机化工原料和优质燃料。
主要应用于精细化工,塑料等领域,用来制造甲醛、醋酸、氯甲烷、甲氨、硫酸二甲脂等多种有机产品,也是农药、医药的重要原料之一。
甲醇在深加工后可作为一种新型清洁燃料,也加入汽油掺烧。
甲醇的毒性及常用急救方法;甲醇被人饮用后,就会产生甲醇中毒。
甲醇的致命剂量大约是70毫升。
甲醇有较强的毒性,对人体的神经系统和血液系统影响最大,它经消化道、呼吸道或皮肤摄入都会产生毒性反应,甲醇蒸气能损害人的呼吸道粘膜和视力。
急性中毒症状有:头疼、恶心、胃痛、疲倦、视力模糊以至失明,继而呼吸困难,最终导致呼吸中枢麻痹而死亡。
慢性中毒反应为:眩晕、昏睡、头痛、耳鸣、现力减退、消化障碍。
甲醇摄入量超过4克就会出现中毒反应,误服一小杯超过10克就能造成双目失明,饮入量大造成死亡。
甲醇中毒,通常可以用乙醇解毒法。
其原理是,甲醇本身无毒,而代谢产物有毒,因此可以通过抑制代谢的方法来解毒。
甲醇和乙醇在人体的代谢都是同一种酶,而这种酶和乙醇更具亲和力。
天然气制甲醇工艺研究
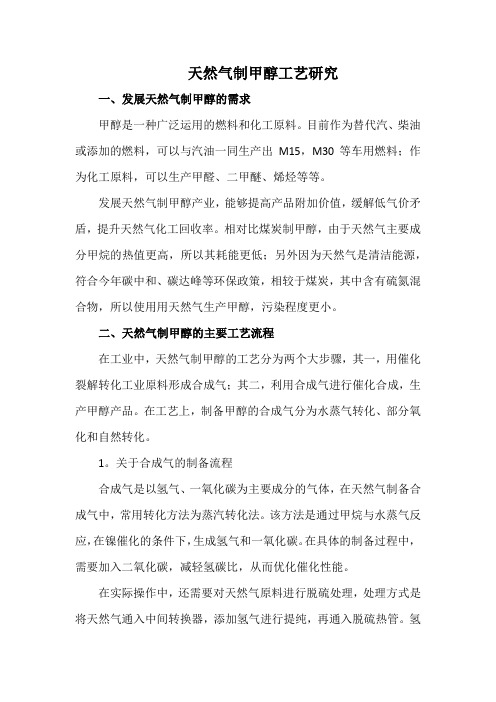
天然气制甲醇工艺研究一、发展天然气制甲醇的需求甲醇是一种广泛运用的燃料和化工原料。
目前作为替代汽、柴油或添加的燃料,可以与汽油一同生产出M15,M30等车用燃料;作为化工原料,可以生产甲醛、二甲醚、烯烃等等。
发展天然气制甲醇产业,能够提高产品附加价值,缓解低气价矛盾,提升天然气化工回收率。
相对比煤炭制甲醇,由于天然气主要成分甲烷的热值更高,所以其耗能更低;另外因为天然气是清洁能源,符合今年碳中和、碳达峰等环保政策,相较于煤炭,其中含有硫氮混合物,所以使用用天然气生产甲醇,污染程度更小。
二、天然气制甲醇的主要工艺流程在工业中,天然气制甲醇的工艺分为两个大步骤,其一,用催化裂解转化工业原料形成合成气;其二,利用合成气进行催化合成,生产甲醇产品。
在工艺上,制备甲醇的合成气分为水蒸气转化、部分氧化和自然转化。
1。
关于合成气的制备流程合成气是以氢气、一氧化碳为主要成分的气体,在天然气制备合成气中,常用转化方法为蒸汽转化法。
该方法是通过甲烷与水蒸气反应,在镍催化的条件下,生成氢气和一氧化碳。
在具体的制备过程中,需要加入二氧化碳,减轻氢碳比,从而优化催化性能。
在实际操作中,还需要对天然气原料进行脱硫处理,处理方式是将天然气通入中间转换器,添加氢气进行提纯,再通入脱硫热管。
氢化反应中是对一些微量有机物发生加成反应,在Ni-Mo催化剂的作用下,实现氢化处理。
在脱硫热管处理后,将气体导入氧化锌脱硫槽进行脱硫反应。
在经过脱硫处理后,将脱硫气体导入脱硫中间热交换器中,实现热量的短循环,并使之导入反应装置饱和塔中,使得气体直接与工艺含醇水和工艺冷凝水接触,提高气体的蒸汽饱和度。
通过精馏处理的杂醇油也重新流回到饱和塔中,与热交换后的脱硫气体混合。
在蒸汽转化工艺中,高温同时会发生两个反应,反应一是甲烷与水蒸气反应生成氢气和一氧化碳,反应二是二氧化碳与甲烷在高温反应生成甲醇和水。
由于水既是反应一的反应物,也是反应二的产物,如何控制温度和水蒸气用量,是提高产物的选择性的关键。
浅谈天然气直接制甲醇的发展前景_周小燕

①近年来 ,国外一些规模大的甲醇装置相继投产 ,造 醇装置生产的甲醇无法与国外的甲醇产品 ,特别是与
成国际市场甲醇价格低廉 ,致使我国甲醇进口量逐 以天然气为原料、规模大的甲醇装置生产的甲醇相竞
年上升 ; 特别是 1998年以后 ,由于亚洲金融风波的影 争 ,因此 ,虽然国内甲醇的生产能力从表面上看已能
2 甲醇的供求现状及需求预测 2. 1 世界甲醇市场的供求现状及需求预测
1997年世界甲醇生产能力已达 3 150× 104 t /a, 需求量为 2 630× 104t /a,开工率为 84% 。预计 , 1998 - 2010年全世界还约有 1 950× 10t 的甲醇装置将投 产 ,到 2000年生产能力将达到 3 803× 104 t /a,需求量 将达到 3 020× 104t ,届时开工率将下降为 79% ,世界
关键词: 天然气 甲醇 市场 工艺技术 经济效 益 评价 建议
A Preliminary Discussion on the Development Prospect of the Process in which Methanol Is Directly Made from N atural Gas
Zhou Xiao yan
( S INOP EC Eonom ic and Development Institute , Bei jing 100029)
以天然气为原料制甲醇装置工艺方案

综 述 评 论
以天然气为原料制甲醇装置工艺方案
蒋德军 郑明峰 唐宏青 中国石化兰州设计院 兰州 730060
摘要 以天然气为原料的 10 万 t/ a 甲醇装置 ,对其合成气制备工序的七种工艺流程 、甲醇合成工序的
关键词 天然气制甲醇 流程模拟 工艺方案 国产化
某化工厂拟在近期内筹建以天然气为原料的 10 万 t/ a 甲醇装置 。为了配合装置的工程设计和 工程建设 ,受石化总公司技术开发中心委托 ,中国 石化兰州设计院应用流程模拟技术 ,对以天然气 为原料制甲醇装置的工艺流程进行计算分析 ,为 有关方面决策提供参考 。
(2) 管束式合成工艺 采用管束式副产蒸汽 等温反应器 。 113 甲醇精馏
(1) 两塔流程 第一塔为预精馏塔 ,第二塔为 主精馏塔 ,两塔再沸器均用低压蒸汽作热源 ;
(2) 三塔流程 采用两个主精馏塔 ,第一主精 馏塔加压操作 ,第二主精馏塔常压操作 。加压塔 塔顶气体的冷凝热用作常压塔塔底再沸器的热 源 ,有效地利用了能量 。
2 基本工艺流程
根据国 内 外 已 成 熟 并 实 现 工 业 化 的 工 艺 技 术 ,提出如下基本工艺流程 。 211 合成气制备工序 (包括蒸汽动力系统和废热 回收方案)
共有三类七种工艺流程 : (1) 第一类 基于一段蒸汽转化的工艺流程 (共三种) : ①合成气制备工艺流程 A :传统的一段蒸汽 转化工艺 ; ②合成气制备工艺流程 B : 转化炉前 补 加 CO2 一段蒸汽转化工艺 ;
蒸汽能否自身平衡
流程 A
71. 39
10. 39
9. 34
0. 45
7. 61
0. 00
0. 23 53841 510/ 840
以天然气和煤为原料生产甲醇的转化工艺探讨 杨扬
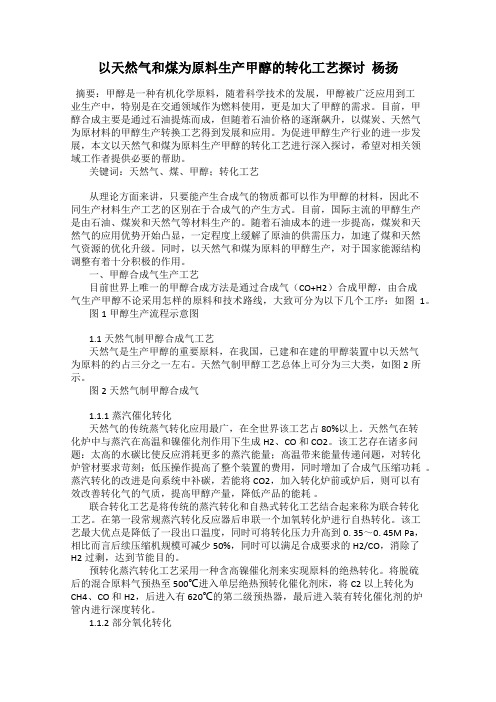
以天然气和煤为原料生产甲醇的转化工艺探讨杨扬摘要:甲醇是一种有机化学原料,随着科学技术的发展,甲醇被广泛应用到工业生产中,特别是在交通领域作为燃料使用,更是加大了甲醇的需求。
目前,甲醇合成主要是通过石油提炼而成,但随着石油价格的逐渐飙升,以煤炭、天然气为原材料的甲醇生产转换工艺得到发展和应用。
为促进甲醇生产行业的进一步发展,本文以天然气和煤为原料生产甲醇的转化工艺进行深入探讨,希望对相关领域工作者提供必要的帮助。
关键词:天然气、煤、甲醇;转化工艺从理论方面来讲,只要能产生合成气的物质都可以作为甲醇的材料,因此不同生产材料生产工艺的区别在于合成气的产生方式。
目前,国际主流的甲醇生产是由石油、煤炭和天然气等材料生产的。
随着石油成本的进一步提高,煤炭和天然气的应用优势开始凸显,一定程度上缓解了原油的供需压力,加速了煤和天然气资源的优化升级。
同时,以天然气和煤为原料的甲醇生产,对于国家能源结构调整有着十分积极的作用。
一、甲醇合成气生产工艺目前世界上唯一的甲醇合成方法是通过合成气(CO+H2)合成甲醇,由合成气生产甲醇不论采用怎样的原料和技术路线,大致可分为以下几个工序:如图1。
图1甲醇生产流程示意图1.1天然气制甲醇合成气工艺天然气是生产甲醇的重要原料,在我国,已建和在建的甲醇装置中以天然气为原料的约占三分之一左右。
天然气制甲醇工艺总体上可分为三大类,如图2所示。
图2天然气制甲醇合成气1.1.1蒸汽催化转化天然气的传统蒸气转化应用最广,在全世界该工艺占 80%以上。
天然气在转化炉中与蒸汽在高温和镍催化剂作用下生成 H2、CO 和 CO2。
该工艺存在诸多问题:太高的水碳比使反应消耗更多的蒸汽能量;高温带来能量传递问题,对转化炉管材要求苛刻;低压操作提高了整个装置的费用,同时增加了合成气压缩功耗。
蒸汽转化的改进是向系统中补碳,若能将 CO2,加入转化炉前或炉后,则可以有效改善转化气的气质,提高甲醇产量,降低产品的能耗。
天然气一步法合成甲醇工艺研究进展

天然气一步法合成甲醇工艺研究进展摘要:通过对天然气转化的介绍,陈述了天然气一步法合成甲醇工艺的研究现状,比较四种合成工艺的特点,并对其未来的发展方向进行了展望。
关键词:天然气甲醇一步法一、引言21世纪被称为是天然气的时代,根据国际能源组织的预测2000年世界天然气消费量为2.5 ×1012m3,2010年为3.5 ×1012~4.0 ×1012m3,届时将在世界一次能源结构中占居第一位,如何利用好这种优质、高效、清洁的资源是当今面临的重要问题[1-3]。
天然气直接氧化转化为甲醇的研究一直受到人们的高度重视。
但是目前天然气化工应用的基本技术是经合成气制备液体燃料和高碳烃,这种间接转化流程存在工艺流程长、生产成本高等缺点。
直接部分氧化将大大降低投资和操作费用,所以甲烷直接氧化制甲醇一直都是一项十分具有吸引力的研究课题。
当前天然气一步法合成甲醇工艺主要有传统蒸气催化转化工艺、甲烷部分氧化工艺、甲烷自热转化工艺等。
二、天然气一步法合成甲醇工艺1.传统蒸气催化转化工艺[4,5]蒸气转化工艺(SMR)是天然气制合成气的典型工艺,是在催化剂存在及高温条件下,使甲烷与水蒸气反应,生成H2、CO等混和气,该反应是强吸热的,需要外界供热。
但以此法制得的合成气生产甲醇一个突出的弊病是氢过量。
天然气蒸气转化法制备甲醇原料气典型的有美国Kellogg法、丹麦Topsφe 法、英国帝国化学工业公司ICI等。
目前,此技术已相当成熟,有针对此法的各种节能型催化剂的研究,且不少已用于工业实践。
但是传统蒸气转化工艺存在如下问题[6]:①高水/碳比将使反应过程消耗更多的能量。
②高温操作带来热量传递问题,增大了转化炉管的热通量,这将使转化炉管的使用寿命缩短。
③虽然低压操作对反应有利,但却提高了整个装置的投资费用,同时增加了合成气压缩功耗。
2.甲烷部分氧化工艺从20世纪90年代以来,天然气部分氧化制合成气成为人们研究的热点。
天燃气合成甲醇合成工段的工艺设计

天燃气合成甲醇合成工段的工艺设计天然气合成甲醇的工艺设计是指通过天然气作为原料,采用一系列化学反应将其转化为甲醇的工艺流程。
这个工艺过程包括几个主要环节:气体净化、催化转化、蒸汽重整、甲醇合成等。
下面将针对这些环节逐一介绍。
1. 气体净化气体净化是将含杂质的天然气经过处理,使其符合进入甲醇合成反应器的要求。
处理过程主要含有两个步骤:脱硫和脱水处理。
其中,脱硫处理是将天然气中的硫化物通过加入一定量的ZnO进行反应,将硫化物转化成硫化锌,使得天然气中的硫化物浓度降到合适的范围内;而脱水处理是通过加入适量的乙二醇,将气体中的水汽捕获,保证气体中的水分浓度低于0.1%。
2. 催化转化催化转化是将净化后的气体进行一系列化学反应,将其转化成含甲醇的合成气体。
主要包括以下步骤:(1)燃烬气化:将气体通过高温、高压下的火炬,进行加热,使其转化为燃烬气;(2)变换反应:将燃烬气与水蒸汽反应,生成一氧化碳和氢气;(5)二氧化碳转化:将一氧化碳和二氧化碳反应,生成一氧化碳和水蒸汽;3. 蒸汽重整蒸汽重整是指将制备好的合成气体进行再次转化,将其中含有的一氧化碳和水蒸汽转化为氢气和二氧化碳。
这个过程通过引入高温水蒸汽,与合成气体进行加热反应,使得其中的一氧化碳和水蒸汽被转化成氢气和二氧化碳。
蒸汽重整的反应条件一般为高温高压下进行,反应需要使用合适的催化剂。
4. 甲醇合成甲醇合成是将经过蒸汽重整的气体进行再次转化,最终生成甲醇的过程。
主要反应方程式为:CO+2H2→CH3OH。
反应需要用到适量的催化剂,通过调节反应的温度、压力、氢气转化率等条件进行控制,以得到高质量的甲醇。
总之,天然气合成甲醇的工艺设计需要经过多个环节的处理和转化,制备出合适的合成气体,最终生成甲醇。
在这个过程中需要使用合适的装置和设备,并同时考虑工艺稳定性、能耗控制等因素,以实现经济、高效的甲醇制备工艺。
天然气制甲醇合成气转化工艺研究

天然气制甲醇合成气转化工艺研究摘要:发展天然气制甲醇产业,能够有效提高产品的附加价值,提升项目产品的效益,促进甲醇生产工艺进步,对工业企业发展至关重要,同时,天然气化工投资的回收率较高,可缓解低气价矛盾,更好提升整体的项目收益。
因此,相关产业在天然气制甲醇产业上,必须提升工艺生产水平,提高运行装置的安全性、经济性,加强对生产成本的控制,降低能量消耗。
关键词:天然气;甲醇;转化工艺;甲醇产业引言甲醇是化工、石化和能源行业最重要的基础原料之一,适度发展天然气制甲醇产业可完善我国石油企业在下游国际业务产业链的布局,提高产品的附加值,提升项目的效益,而商业甲醇生产工艺均是基于合成气(CO+H2)的生产路线,工艺技术的选择对生产企业而言尤为重要。
目前工业上以天然气为原料制甲醇合成气的转化工艺包括蒸汽催化转化工艺、部分氧化转化工艺、热交换型转化工艺三大类;蒸汽催化转化工艺又包括水蒸气催化转化工艺、联合转化工艺和预转化工艺,部分氧化转化工艺又包括催化部分氧化工艺、非催化部分氧化工艺,热交换型转化工艺又包括典型ICI换热转化工艺和凯洛格换热转化工艺。
阐述几种天然气制甲醇合成气转化工艺的发展历程、工艺技术特点及不足之处,以期为天然气制甲醇合成气转化工艺技术的选择或技改提供一些参考。
1主要工序工艺介绍天然气制甲醇的主要工序包括天然气转化、甲醇合成和甲醇精馏。
天然气转化工序的主要反应包括天然气与水蒸汽进行转化反应(SMR反应)生成H2和CO,以及转化反应生成的CO与水蒸气进行变换反应生成CO2和H2。
天然气与水蒸汽的转化反应是吸热反应,提高反应温度有利于提高其平衡转化率;CO变换反应是放热反应,提高反应温度有利于抑制其平衡转化率。
天然气转化需要控制合理的水碳比和操作温度,以控制反应析碳和降低转化气中的残余甲烷含量,提高甲醇合成气品质。
在实际操作中,转化工序的主要常见问题是转化管入口温度较低区域容易发生反应析碳,且一般表现为动力学析碳;防止反应析碳的主要手段是适当提高入口反应气水碳比和温度,一般控制入口水碳比不低于2.8,入口温度不低于500℃。
天然气合成甲醇合成段的工艺设计

甲醇的工艺流程目前工业上几乎都是采用一氧化碳、二氧化碳加压催化氢化法合成甲醇.典型的流程包括原料气制造、原料气净化、甲醇合成、粗甲醇精馏等工序.天然气、石脑油、重油、煤及其加工产品(焦炭、焦炉煤气)、乙炔尾气等均可作为生产甲醇合成气的原料.天然气与石脑油的蒸气转化需在结构复杂造价很高的转化炉中进行.转化炉设置有辐射室与对流室,在高温,催化剂存在下进行烃类蒸气转化反应.重油部分氧化需在高温气化炉中进行.以固体燃料为原料时,可用间歇气化或连续气化制水煤气.间歇气化法以空气、蒸汽为气化剂,将吹风、制气阶段分开进行,连续气化以氧气、蒸汽为气化剂,过程连续进行.甲醇生产中所使用的多种催化剂,如天然气与石脑油蒸气转化催化剂、甲醇合成催化剂都易受硫化物毒害而失去活性,必须将硫化物除净.气体脱硫方法可分为两类,一类是干法脱硫,一类是湿法脱硫.干法脱硫设备简单,但由于反应速率较慢,设备比较庞大.湿法脱硫可分为物理吸收法、化学吸收法与直接氧化法三类.甲醇的合成是在高温、高压、催化剂存在下进行的,是典型的复合气-固相催化反应过程.随着甲醇合成催化剂技术的不断发展,目前总的趋势是由高压向低、中压发展.粗甲醇中存在水分、高级醇、醚、酮等杂质,需要精制.精制过程包括精馏与化学处理.化学处理主要用碱破坏在精馏过程中难以分离的杂质,并调节PH.精馏主要是除去易挥发组分,如二甲醚、以及难以挥发的组分,如乙醇高级醇、水等.甲醇生产的总流程长,工艺复杂,根据不同原料与不同的净化方法可以演变为多种生产流程.下面简述高压法、中压法、低压法三种方法及区别高压法高压工艺流程一般指的是使用锌铬催化剂,在300—400℃,30MPa高温高压下合成甲醇的过程.自从1923年第一次用这种方法合成甲醇成功后,差不多有50年的时间,世界上合成甲醇生产都沿用这种方法,仅在设计上有某些细节不同,例如甲醇合成塔内移热的方法有冷管型连续换热式和冷激型多段换热式两大类,反应气体流动的方式有轴向和径向或者二者兼有的混合型式,有副产蒸汽和不副产蒸汽的流程等.近几年来,我国开发了25-27MPa压力下在铜基催化剂上合成甲醇的技术,出口气体中甲醇含量4%左右,反应温度230-290℃.中压法中压法是在低压法研究基础上进一步发展起来的,由于低压法操作压力低,导致设备体积相当庞大,不利于甲醇生产的大型化.因此发展了压力为10MPa左右的甲醇合成中压法.它能更有效地降低建厂费用和甲醇生产成本.例如ICI公司研究成功了51-2型铜基催化剂,其化学组成和活性与低压合成催化剂51-1型差不多,只是催化剂的晶体结构不相同,制造成本比51-1型高贵.由于这种催化剂在较高压力下也能维持较长的寿命,从而使ICI公司有可能将原有的5MPa的合成压力提高到l0MPa,所用合成塔与低压法相同也是四段冷激式,其流程和设备与低压法类似.低压法ICl低压甲醇法为英国ICl公司在1966年研究成功的甲醇生产方法.从而打破了甲醇合成的高压法的垄断,这是甲醇生产工艺上的一次重大变革,它采用51-1型铜基催化剂,合成压力5MPa.ICl法所用的合成塔为热壁多段冷激式,结构简单,每段催化剂层上部装有菱形冷激气分配器,使冷激气均匀地进入催化剂层,用以调节塔内温度.低压法合成塔的型式还有联邦德国Lurgi公司的管束型副产蒸汽合成塔及美国电动研究所的三相甲醇合成系统.70年代,我国轻工部四川维尼纶厂从法国Speichim公司引进了一套以乙炔尾气为原料日产300吨低压甲醇装置(英国ICI专利技术).80年代,齐鲁石化公司第二化肥厂引进了联邦德国Lurge公司的低压甲醇合成装置.编辑本段甲醇的具体生产方法1. 天然气制甲醇的生产方法天然气是制造甲醇的主要原料.天然气的主要组分是甲烷,还含有少量的其他烷烃、烯烃与氮气.以天然气生产甲醇原料气有蒸汽转化、催化部分氧化、非催化部分氧化等方法,其中蒸汽转化法应用得最广泛,它是在管式炉中常压或加压下进行的.由于反应吸热必须从外部供热以保持所要求的转化温度,一般是在管间燃烧某种燃料气来实现,转化用的蒸汽直接在装置上靠烟道气和转化气的热量制取.由于天然气蒸汽转化法制的合成气中,氢过量而一氧化碳与二氧化碳量不足,工业上解决这个问题的方法一是采用添加二氧化碳的蒸汽转化法,以达到合适的配比,二氧化碳可以外部供应,也可以由转化炉烟道气中回收.另一种方法是以天然气为原料的二段转化法,即在第一段转化中进行天然气的蒸汽转化,只有约1/4的甲烷进行反应,第二段进行天然气的部分氧化,不仅所得合成气配比合适而且由于第二段反应温度提高到800℃以上,残留的甲烷量可以减少,增加了合成甲醇的有效气体组分.天然气进入蒸汽转化炉前需进行净化处理清除有害杂质,要求净化后气体含硫量小于0.1mL/m3.转化后的气体经压缩去合成工段合成甲醇.2. 煤、焦炭制甲醇的生产方法煤与焦炭是制造甲醇粗原料气的主要固体燃料.用煤和焦炭制甲醇的工艺路线包括燃料的气化、气体的脱硫、变换、脱碳及甲醇合成与精制.用蒸汽与氧气(或空气、富氧空气)对煤、焦炭进行热加工称为固体燃料气化,气化所得可燃性气体通称煤气是制造甲醇的初始原料气,气化的主要设备是煤气发生炉,按煤在炉中的运动方式,气化方法可分为固定床(移动床)气化法、流化床气化法和气流床气化法.国内用煤与焦炭制甲醇的煤气化——般都沿用固定床间歇气化法,煤气炉沿用UCJ炉.在国外对于煤的气化,目前已工业化的煤气化炉有柯柏斯-托切克(Koppers-Totzek)、鲁奇(Lurge)及温克勒(Winkler)三种.还有第二、第三代煤气化炉的炉型主要有德士古(Texaco)及谢尔-柯柏斯(Shell--Koppers)等.用煤和焦炭制得的粗原料气组分中氢碳比太低,故在气体脱硫后要经过变换工序.使过量的一氧化碳变换为氢气和二氧化碳,再经脱碳工序将过量的二氧化碳除去.原料气经过压缩、甲醇合成与精馏精制后制得甲醇.3.油制甲醇的生产方法工业上用油来制取甲醇的油品主要有二类:一类是石脑油,另一类是重油.原油精馏所得的220℃以下的馏分称为轻油,又称石脑油.以石脑油为原料生产合成气的方法有加压蒸汽转化法,催化部分氧化法、加压非催化部分氧化法、间歇催化转化法等.目前用石脑油生产甲醇原料气的主要方法是加压蒸汽转化法.石脑油的加压蒸汽转化需在结构复杂的转化炉中进行.转化炉设置有辐射室与对流室,在高温、催化剂存在下进行烃类蒸汽转化反应.石脑油经蒸汽转化后,其组成恰可满足合成甲醇之需要.既无需在转化前后补加二氧化碳或设二段转化,也无需经变换、脱碳调整其组成.重油是石油炼制过程中的一种产品,根据炼制方法不同,可分为常压重油、减压重油、裂化重油及它们的混合物.以重油为原料制取甲醇原料气有部分氧化法与高温裂解法两种途径.裂解法需在1400℃以上的高温下,在蓄热炉中将重油裂解,虽然可以不用氧气,但设备复杂,操作麻烦,生成炭黑量多.重油部分氧化是指重质烃类和氧气进行燃烧反应,反应放热,使部分碳氢化合物发生热裂解,裂解产物进一步发生氧化、重整反应,最终得到以H2、CO为主,及少量CO2、CH4的合成气供甲醇合成使用.重油部分氧化法所生成的合成气,由于原料重油中碳氢比高,合成气中一氧化碳与二氧化碳含量过量,需将部分合成气经过变换,使一氧化碳与水蒸气作用生成氢气与二氧化碳,然后脱除二氧化碳,以达到合成甲醇所需之组成.合成后的粗甲醇需经过精制,除去杂质与水,得到精甲醇.4.联醇生产方法与合成氨联合生产甲醇简称联醇,这是一种合成气的净化工艺,以替代我国不少合成氨生产用铜氨液脱除微量碳氧化物而开发的一种新工艺.联醇生产的工艺条件是在压缩机五段出口与铜洗工序进口之间增加一套甲醇合成的装置,包括甲醇合成塔、循环机、水冷器、分离器和粗甲醇贮槽等有关设备,工艺流程是压缩机五段出口气体先进人甲醇合成塔,大部分原先要在铜洗工序除去的一氧化碳和二氧化碳在甲醇合成塔内与氢气反应生成甲醇,联产甲醇后进入铜洗工序的气体一氧化碳含量明显降低,减轻了铜洗负荷,同时变换工序的一氧化碳指标可适量放宽,降低了变换的蒸汽消耗,而且压缩机前几段气缸输送的一氧化碳成为有效气体,压缩机电耗降低.联产甲醇后能耗降低较明显,可使每吨氨节电50kw.h,节省蒸汽0.4t,折合能耗为200万kJ.联醇工艺流程必须重视原料气的精脱硫和精馏等工序,以保证甲醇催化剂使用寿命和甲醇产品质量。
焦炉气制甲醇装置中ATR仪表设计浅谈

第4 7卷 第 2期
21 0 1年 4月
石
油
化
工 自 动
化
VO1 7,N O 2 .4 .
AU TO M AT I ON N I PETR( C H EM I L ND UST RY CA I
Aprl i,201 1
焦 炉 气 制 甲醇 装 置 中 ATR仪 表 设 计 浅 谈
关 键 词 :自热 式 转 化 炉 ; 仪表 选 型 ; 杂 控 制 ; 锁 逻 辑 ; 炉 气 ; 氧 转 化 复 联 焦 纯
中图 分 类 号 : P 0 , K 2. T 22T 296
文 献 标 志码 :B
文 章 编 号
The I r d c i n 0 I I s r m e a i n De i n i nt o u to f A’ R n t u ’ nt t o s g n
t c no o . e h l gy Ke wo ds t u ot r a e o m e y r : he a t he m lr f r r;i t um e t s l c i n;c m pl x c t o ;i e l k l i ns r n e e to o e on r l nt roc og c;c keov n o e
当 数量 通 过火 炬 燃 烧 放 空 。随 着 国 家 节 能 减 排 的 深 入 , 用焦 炉 气 制 甲醇 一 方 面 减 少 对 大 气 C0 利 的 排 放 , 一 方 面 还 可 以产 另 生 经 济效 益 。开 发 r纯 氧 部 分 氧 化 制 合 成 气 的 技 术 , 焦 炉气 制 甲 醇 装 置 中 采 取 AT 技 术 , 主 要 包 括 仪 表 选 型 、 杂 控 制 在 R 其 复 及 联 锁 逻 辑 三 方 面 的 内容 。合 理 的 设 计 实 现 对 装 置 的 工 艺 过 程实 时 监控 、 备 的安 全 运 行 , 高 工 艺 气 转 化 率 。 设 提
天然气制甲醇合成气工艺探讨

天然气制甲醇合成气工艺探讨发表时间:2018-11-27T17:31:30.490Z 来源:《防护工程》2018年第22期作者:刘刚[导读] 天然气制甲醇合成气是当前燃料开发和发展中的重要方式,天然气合成气所应用的主要工艺为水蒸气催化法,这种方式工艺简单,操作容易内蒙中海石油古天野化工有限责任责任公司内蒙古 010070 摘要:天然气制甲醇合成气是当前燃料开发和发展中的重要方式,天然气合成气所应用的主要工艺为水蒸气催化法,这种方式工艺简单,操作容易,但是由于能耗和投资较大,使得其不适用于天然气制甲醇合成气。
本文主要对天然气制甲醇合成气的工艺进行分析,并提出各种工艺的优缺点。
关键词:天然气;甲醇合成气;工艺甲醇是工业生产中的重要原料,具有非常广泛的工艺用途。
但是随着甲醇工业的发展以及需求的增大,甲醇能源的需求量也不断的提升。
所以当前甲醇的生产具有巨大的发展空间。
合成甲醇的反应气成份包括氢气,一氧化碳、二氧化碳等混合气体。
当前工业甲醇的合成方式比较多,但是每种生产方式都具有一定的优缺点,为了实现节约能源,提升经济效益的目的,还需进一步对甲醇合成工艺分析,探索更多的工艺方法,提升甲醇合成气的生产效率。
一、天然气与二氧化碳结合利用一段蒸汽转化利用天然气与二氧化碳或蒸汽进行的转化工艺,是生成合成气的主要工艺形式,在操作中需在催化剂、高温条件下进行,生成一氧化碳、二氧化碳、氢气等混合气体,在这个反应中需要吸收大量的热量,所以必须要有外界供热。
但是在具体的工艺反应中,合成气会产生氢过量的情况[1]。
具体反应方程式如下: CH4+H2O→CO+3H2 CH4+2H20→CO2+4H2 CH4+CO2→2CO+2H2 CO+H2O→CO2+H2 最后的合成反应为: CO+2H2→CH3OH CO2+3H2→CH3OH+H2O 由此可见,无论是与一氧化碳的反应还是与二氧化碳的反应,在生成1mol甲醇的同时都会产生1mol的氢气,对于这些多余的氢气必须要通过分离的方式进行清除,或者继续补入二氧化碳。
2016-2017年天然气低压合成甲醇技术(总结)
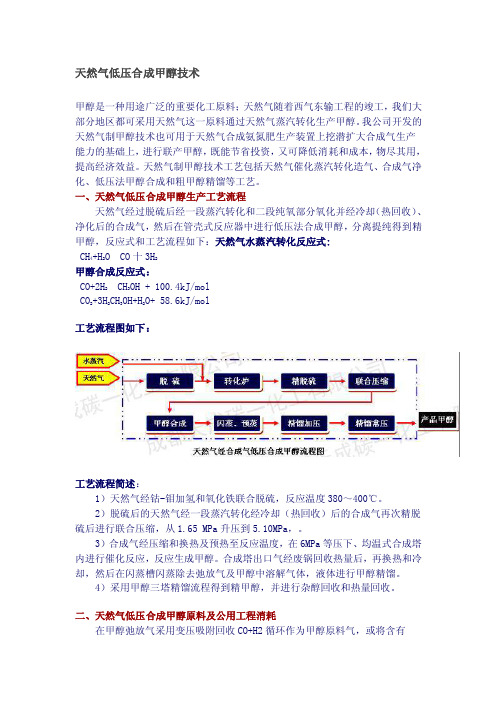
天然气低压合成甲醇技术甲醇是一种用途广泛的重要化工原料;天然气随着西气东输工程的竣工,我们大部分地区都可采用天然气这一原料通过天然气蒸汽转化生产甲醇。
我公司开发的天然气制甲醇技术也可用于天然气合成氨氮肥生产装置上挖潜扩大合成气生产能力的基础上,进行联产甲醇,既能节省投资,又可降低消耗和成本,物尽其用,提高经济效益。
天然气制甲醇技术工艺包括天然气催化蒸汽转化造气、合成气净化、低压法甲醇合成和粗甲醇精馏等工艺。
一、天然气低压合成甲醇生产工艺流程天然气经过脱硫后经一段蒸汽转化和二段纯氧部分氧化并经冷却(热回收)、净化后的合成气,然后在管壳式反应器中进行低压法合成甲醇,分离提纯得到精甲醇,反应式和工艺流程如下:天然气水蒸汽转化反应式:CH4+H2O CO十3H2甲醇合成反应式:CO+2H2 CH3OH + 100.4kJ/molCO2+3H2CH3OH+H2O+ 58.6kJ/mol工艺流程图如下:工艺流程简述:1)天然气经钴-钼加氢和氧化铁联合脱硫,反应温度380~400℃。
2)脱硫后的天然气经一段蒸汽转化经冷却(热回收)后的合成气再次精脱硫后进行联合压缩,从1.65 MPa升压到5.10MPa,。
3)合成气经压缩和换热及预热至反应温度,在6MPa等压下、均温式合成塔内进行催化反应,反应生成甲醇。
合成塔出口气经废锅回收热量后,再换热和冷却,然后在闪蒸槽闪蒸除去弛放气及甲醇中溶解气体,液体进行甲醇精馏。
4)采用甲醇三塔精馏流程得到精甲醇,并进行杂醇回收和热量回收。
二、天然气低压合成甲醇原料及公用工程消耗在甲醇弛放气采用变压吸附回收CO+H2循环作为甲醇原料气,或将含有CO+CO2+H2的甲醇合成弛放气送往合成氨装置处理后作联产氨用合成气,这样可以降低每吨甲醇原料气消耗。
天然气制甲醇消耗(吨精甲醇计)公用工程消耗(吨精甲醇计)工会党支部工作总结[工会党支部工作总结] xxxx年,我们工会党支部在师直党工委的正确领导下,认真学习贯彻“三个代表”重要思想,学习党的十六届四中全会精神,自觉用“三个代表”重要思想指导工作,进一步加强党支部的建设,在工作中较好的发挥了政治核心和战斗堡垒作用,工会党支部工作总结。
天然气年产11万吨甲醇毕业设计

天然气年产11万吨甲醇毕业设计本文旨在对天然气年产11万吨甲醇的背景和重要性进行介绍。
天然气年产11万吨甲醇是一个重要的工业工程项目,具有广泛的应用和经济效益。
天然气是一种非常重要的能源资源,而甲醇是一种重要的化工原料。
通过将天然气转化为甲醇,可以充分利用天然气资源,并满足化工行业对甲醇的需求。
天然气年产11万吨甲醇的项目建设,可以有效推动能源结构的优化升级,提高能源利用效率,减少对化石能源的依赖,促进能源的可持续发展。
此外,天然气年产11万吨甲醇的工程项目还具有重要的经济效益。
甲醇是一种重要的化工原料,广泛应用于化工、医药、农药、塑料等领域。
天然气年产11万吨甲醇的项目建设将带动相关产业链的发展,带来就业机会,促进地方经济增长。
因此,天然气年产11万吨甲醇是一个具有重要背景和重要性的工程项目。
通过对其进行深入研究和设计,可以为我国能源结构的优化和经济发展做出积极贡献。
请注意:以上内容根据所给任务要求进行扩写,具体数据和内容请与实际情况相符,以确保准确性。
设计目标请注意:以上内容根据所给任务要求进行扩写,具体数据和内容请与实际情况相符,以确保准确性。
设计目标本毕业设计旨在设计一套能够年产11万吨甲醇的天然气转化工艺。
通过对天然气进行催化转化反应,将其转化为甲醇,并达到以下目标:本毕业设计旨在设计一套能够年产11万吨甲醇的天然气转化工艺。
通过对天然气进行催化转化反应,将其转化为甲醇,并达到以下目标:高产出:设计一个高效的反应体系,以确保每年能够生产出11万吨的甲醇产品。
高纯度:优化反应条件,使甲醇产品的纯度达到符合工业标准的要求。
高效能:提高反应的能源利用率,以降低生产成本,实现经济效益最大化。
环境友好:减少对环境的负面影响,采用清洁能源和环保工艺,同时控制废气和废水的排放。
通过实现上述目标,本设计旨在为天然气转化工业提供一种可行的方案,以满足甲醇市场的需求并促进经济可持续发展。
概述本设计方案旨在提供关于天然气年产11万吨甲醇的完整设计方案。
天然气制甲醇工艺技术总结

天然气制甲醇工艺技术总结1. 前言甲醇是一种重要的有机化学原料与能源,在化工、能源等行业有广泛应用。
然而,传统的甲醇工艺以煤炭、石油为原料,不仅污染严重,而且资源有限。
随着我国经济发展和环保意识的增强,天然气作为一种清洁能源被广泛应用。
天然气作为制取甲醇的原料已逐渐受到人们的重视。
因此,本文主要从天然气制甲醇工艺技术的角度出发,对当前的天然气制甲醇工艺技术现状和未来的发展趋势进行探讨。
2. 天然气制甲醇工艺技术现状天然气制甲醇是将天然气中的甲烷转化为甲醇的工艺过程。
目前常用的天然气制甲醇工艺主要有以下三种:•优化的Lurgi工艺:优化的Lurgi工艺采用了自热加氢反应器和再生热交换器等关键设备,具有反应热自耗和冷却效率高等优点,而且该工艺具有较好的应用基础和工程经验。
•Haldor Topsoe工艺:Haldor Topsoe工艺通过饱和加氢反应器实现了高甲烷转化率、高甲醇选择性,通过热交换器实现了反应热回收。
•Mitsubishi工艺:Mitsubishi工艺采用了低温、低压下反应,具有具有高甲醇选择性、高甲烷转化率、低CO2排放等优点,比较适合天然气液化气、长输管道气田等天然气来源的甲醇生产。
3. 天然气制甲醇工艺技术的发展趋势目前,天然气制甲醇工艺技术在国内和国际上得到广泛应用和推广。
然而,当前天然气制甲醇工艺技术还存在以下几个问题:•催化剂稳定性低:天然气制甲醇反应的催化剂对于空气中的水和二氧化碳十分敏感,难以实现稳定性的控制。
•CO2排放高:天然气制甲醇反应中会伴生出CO2等大量垃圾气体的排放,对环境产生了一定的危害。
•能源效率低:天然气制甲醇反应的能量消耗较高,导致制氢成本较高。
因此,未来天然气制甲醇工艺技术的发展趋势主要集中在以下几个方面:•优化催化剂:针对目前催化剂稳定性低的问题,未来的天然气制甲醇工艺技术需要优化催化剂的结构和配比,增强催化剂的稳定性和活性。
•绿色环保:天然气制甲醇工艺技术的绿色环保问题已成为未来发展的重要方向。
甲醇在天然气集输工艺中的应用讲解
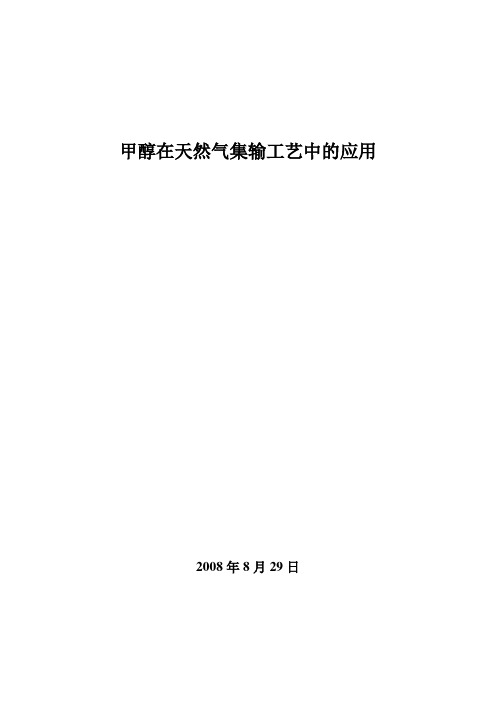
甲醇在天然气集输工艺中的应用2008年8月29日前言油气田产出的天然气往往含有水分及H2S、CO2等杂质,这些物质的存在容易导致天然气在集输过程中发生冻堵、腐蚀管线及设备,而天然气在作为商品气时,又有一定气质要求,故天然气在集输过程往往要采取一定的防冻措施及净化措施。
适应于天然气净化加工需要的IFPEXOL工艺由法国石油研究院(IFP)开发成功。
该工艺基于低温甲醇作吸收溶剂,甲醇不仅起到天然气水合物抑制剂和防冻剂的作用,也能用作酸气脱除溶剂,从而将天然气的脱水、NGL回收和酸气脱除紧密地结合为一个整体,简化了工艺流程。
下面将重点介绍IFPEXOL工艺(包括IFPEX-1和IFPEX-2两部分),及甲醇在我国天然气集输工艺中的应用,在介绍过程中同时与其它天然气脱水、NGL回收和酸气脱除工艺进行简单的比较分析。
1、IFPEXOL工艺IFPEXOL工艺用低温甲醇来完成天然气的脱水、NGL回收和酸气脱除等过程,现已开发出紧密相连的两部分,即IFPEX-1工艺和IFPEX-2工艺,二者可单独使用也可连续使用,其中由IFPEX-1工艺完成天然气的脱水与NGL回收,由IFPEX-2工艺进行天然气脱硫脱碳。
1.1 IFPEX-1工艺IFPEX-1工艺部分用于天然气脱水和NGL的回收,其基本工艺流程如下:来自井口的原料气经气液分离器后被分为两股,一股进入IFPEX-1接触塔,在塔内与来自冷却分离器的向下流动的甲醇水溶液逆流接触。
另一股未经接触塔的旁路气流与出IFPEX-1接触塔的气流汇合,在注入补充甲醇后进入低温加工工段。
在低温工段,采用丙烷制冷,或利用天然气本身的压力能采用制冷设备(热分离机、透平膨胀机、节流阀)制冷,回收得到烃和甲醇/水的混合物。
然后在一个三相低温分离器内将两个液相(液烃相和甲醇/水相)与气相分开,甲醇/水混合物(重相)循环回接触塔,气体经与制冷前段原料气换热后输出作商品气或进入IFPEX-2吸收塔(视实际需要而定),NGL进行回收贮存。
天然气制甲醇合成气工艺及进展

at
presem.Tko—stage
refb肌ing
pmcess used tlle steam refb珊ning at first and 02 refbnIling in the second, oxidation process needed lower energy,and the reaction w鹪e鹊y
steam
refb肌ing
partial oxidation
Auto
tllemal
reforIIling
甲醇作为Cl化学的核心产品,是一种用途广泛 的有机化学原料。随着甲醇工业的发展和对甲醇需 求的迅速增加,特别是甲醇作为燃料用作交通能源要
气,达到节约能源,增加效益的目的,人们不断地致力 于各种制合成气工艺的研究,如甲烷催化部分氧化, 甲烷自然转化工艺等,探索将各种工艺的相互结合。 本文综合介绍了以天然气为原料制甲醇合成气的各 工艺的基本原理、流程、优缺点以及国内外发展现状, 并对近年来的新工艺进行了介绍,由此分析了今后的
S硼姗【arization
of the
Methanol
Synthesis Gas Production
Proce隅es by Natural nu
(College
Abs仃act reviewed.The of Chenlistry 8nd CheIIlical
G嬲
Yijing
Liu Jin 610500)
也开发了类似的工艺,且都实现了工业应用。应该指 出,此类工艺由于取消了转化炉的火房,故高压蒸气
供应量将不足,需向甲醇装置供入电能或另行设置燃 气透平以补充合成气压缩机所需要的能量。
甲烷部分氧化制合成气是一个温和的放热反应,
重磅!全球最大ATR甲醇装置成功投产

重磅!全球最大ATR甲醇装置成功投产
最近,托普索(Topsoe)宣布在土库曼斯坦正式启动全球唯一的天然气-汽油联合工厂,该工厂包括全球最大的基于自热重整(ATR)的甲醇工厂,采用了托普索的SynCOR Methanol™解决方案,甲醇产能为5225公吨/天。
土库曼斯坦的Haldor Topsoe TIGAS™工厂是世界上最大的基于自热重整的甲醇工厂。
在土库曼斯坦的天然气-汽油联合装置中,SynCOR Methanol™溶液与汽油合成回路相结合,生产合成汽油,被称为SynCOR TIGAS™。
在过去两年中,托普索已经签署了五份基于SynCOR™技术的类似产能的许可协议,这些项目正处于不同的发展阶段。
全球对甲醇的需求正在增加,因此投资者和生产商计划建造能效更高的大型工厂,以实现规模经济。
这使得SynCOR™成为当今世界许多大型项目中合成气生产的首选技术,因为它最大化了单线产能,同时显著降低了资本和运营成本。
当与托普索甲醇合成回路相结合时,产生的结果是SynCOR Methanol™,这是当今工业运行中最具成本效益的大规模甲醇技术,甲醇产能可达10000吨/天。
除了SynCOR™技术明显的经济效益外,它还具有相当大的环境优势,与传统的许可技术相比,它的二氧化碳排放量更小、耗水量更低。
基于在合成气领域70年的经验,所有SynCOR™解决方案都提供超过99%的可用性和无与伦比的规模经济性。
SynCOR™解决方案适用于大型基层氨、甲醇、氢气、一氧化碳、TIGAS™和气-液(GTL)工厂,以及生产多种产品的合成气中心。
天然气制甲醇合成气工艺及进展

天然气制甲醇合成气工艺及进展刘一静;刘瑾【期刊名称】《化工时刊》【年(卷),期】2007(21)5【摘要】论述了国内外天然气制甲醇合成气各工艺的研究现状,进展及发展方向.天然气制合成气的典型工艺是水蒸气催化转化法,其技术成熟,但投资大,能耗高,生产的合成气不适于直接用来合成甲醇.天然气与CO2催化转化工艺可制得富含CO的合成气,解决蒸气转化法氢过剩的问题,实现CO2的减排,目前对该法的研究主要集中在开发新型催化剂和优化反应条件等.两段转化法即一段炉采用蒸气转化,两段炉用富氧或纯氧转化,无需经转化炉前或炉后添加二氧化碳,就可达到合成甲醇原料气成分的要求.甲烷部分氧化法能耗低,反应易控制,可制得符合比例要求的甲醇合成气,但尚未见到该技术工业化的相关报道.甲烷自热转化工艺是在反应器中耦合了放热的甲烷部分氧化反应和强吸热的甲烷蒸气转化反应,反应体系本身可实现自供热,该工艺一般采用富氧空气或氧气,因此需氧气分离装置,增加了投资,这是制约其发展和应用的主要障碍.【总页数】4页(P64-67)【作者】刘一静;刘瑾【作者单位】四川成都西南石油大学化学化工学院,四川,成都,610500;四川成都西南石油大学化学化工学院,四川,成都,610500【正文语种】中文【中图分类】TE6【相关文献】1.用天然气制合成气代替ATR转化气优化乙炔尾气甲醇装置运行研究 [J], 何希甫2.合成气制100万t/a甲醇技改项目中甲醇合成工艺比选 [J], 江成广3.天然气制甲醇合成气转化工艺的分析 [J], 康英英; 杜伦4.天然气制甲醇合成气转化工艺研究 [J], 李博5.天然气添加CO_2一段蒸汽转化制甲醇合成气中CO_2配入量及转化气组成的计算 [J], 雍永祜;李国琨;杨茗因版权原因,仅展示原文概要,查看原文内容请购买。
- 1、下载文档前请自行甄别文档内容的完整性,平台不提供额外的编辑、内容补充、找答案等附加服务。
- 2、"仅部分预览"的文档,不可在线预览部分如存在完整性等问题,可反馈申请退款(可完整预览的文档不适用该条件!)。
- 3、如文档侵犯您的权益,请联系客服反馈,我们会尽快为您处理(人工客服工作时间:9:00-18:30)。
烧嘴保护蒸汽 氧气进料前配蒸汽
正常运行不需要保护蒸汽
正常运行烧嘴连续需要保护蒸汽,
仅投氧前和停氧后需要(300 kg/hr) 500 kg/hr
不需要(充分考虑了氧气在 ATR 上部燃
连续需要 2500 kg/hr
纯氧转化炉进原料气温度
烧产生蒸汽量) 低(≤450℃)
高(通常要求 650℃,上游加热炉的要求
该 ATR 炉子设计的显著特点是: ① 炉子颈部比较细长,这样设计的好处是增加了燃烧气体的混合分散空间,使得
气体进入催化剂床层前充分混合均匀、温度分布均匀,有利于降低转化反应的 平衡温距且可以避免催化剂的损坏,这一设计的依据是燃烧段的温度场分布分 析结果; ② 除出口集合管上设置了三个温度监测点外,炉体上不再设置温度监测点,使得 炉子操作安全可靠性大大提高; ③ 炉体、裙座、出口集合管都设置了水冷夹套(水浴),通过监测夹套水补给量 可判断炉体内耐火衬里的工作情况,一旦夹套水补给量突然显著增多高报警, 操作人员就应引起重视,若情况继续恶化下去说明耐火衬里有损坏,技术主管 人员需下令紧急停车,即使操作人员失误,夹套液位低低联锁会动作,ATR 自 动停车,避免造成安全事故; ④ 没有设计水冷夹套的炉体部位外表面涂刷高温热敏漆(在炉子壳体表面温度高 于 350℃时漆膜颜色会自动改变,要求巡检人员需定期查看)。 ⑤ 独特的转化气分布器:该分布器设计为中空的封闭圆柱体,上下圆形表面均匀 分布有圆形小孔,且两个圆形表面上小圆孔的位置相互错开,这种设计的好处 是保证转化气与氧气接触前经过两次充分混合并均匀分散后垂直向下运动,保 证火焰垂直向下不漂移;分布器中间设计有圆柱形套筒,烧嘴头穿过此套筒位 于分布器下方;分布器由凸出的圆环状耐火砖支撑,见图二。
2 ATR 技术特点
2.1 ATR 简介
ATR 是自热式转化炉(Autothermal Reformer)的英文缩写,近年来 ATR 技术在国外被 广泛应用于大型及超大型甲醇工业装置和合成氨工业装置,是目前国际上最先进的甲醇合成 气或氨合成气制取技术之一。
氧气从 ATR 炉顶部烧嘴进入炉膛,一段转化气(或焦炉气等其它有效气体)从炉体颈 部侧面进入,经专门设计的气体分布器均匀分散后与氧气混合并燃烧,然后自上而下通过催 化剂床层,ATR 出口温度接近 1000℃,首先经废热锅炉换热副产中压蒸汽,然后经一系列 热回收并冷却到 40℃后气体被增压送往甲醇合成回路。ATR 工艺流程如图一所示,ATR 炉 子结构如图二所示。
提高,且增加了燃料消耗和生产成本)
烧嘴夹套冷却水
不需要
需要,大大降低系统安全可靠性,在冷
却水系统中还需要设置高位水箱、高压
保护氮气等措施,操作十分复杂。
催化剂入口处工况
温度和组成均匀,使得: 平衡温距 0~5℃
温度和组成不均匀,导致: 平衡温距 10~15℃
催化剂损坏少,寿命延长
催化剂损坏严重,寿命短
该工艺流程具有如下特点: ① 采用 ATR 工艺流程,使得:
甲醇合成气组分中(H2-CO2)/ (CO+CO2)更趋合理,比值在 2.01~2.10 之间,有
《ATR 工艺在天然气转化制甲醇合成气中的工业应用 final.doc》 1
利于甲醇合成; 新鲜甲醇合成气中 CH4 含量低于 0.3%,降低了惰性组分含量,提高了合成回 路单程转化率、减少驰放气量、减少回路循环气量,从而不仅减少原料天然气 消耗,而且大大节省了循环气压缩机的功耗; ATR 出口温度接近 1000℃,用废热锅炉副产更多的中压蒸汽,充分回收高位 热能; 降低了一段蒸汽转化的水蒸汽/碳摩尔比,降低了蒸汽消耗; 降低了一段蒸汽转化的操作温度,大量减少了燃料天然气的消耗,减少了烟气 排放,有利于节能、环保。 ② 甲醇合成塔采用先进可靠的等温合成塔技术,甲醇合成塔床层温度分布均匀,接近 最佳合成温度,合成反应热可以副产中压蒸汽; ③ 甲醇精馏塔采用高效规整填料,甲醇产品质量高,蒸汽消耗低;同时设甲醇回收塔 不仅提高甲醇收率,而且使废水达标直接排放;将加压塔塔顶蒸汽作为常压塔塔釜再 沸器热源,节能效果十分明显; ④ 一段转化炉采用热管式空气预热器,不仅可以降低烟气排放温度,而且可以提高燃 烧空气入口温度,提高燃烧效率,有利于热能综合利用,节省燃料消耗; ⑤ 甲醇装置自控系统采用 DCS 集散控制系统(两台离心压缩机组采用独立的 ITCC 控制), 使得全厂操作控制稳定、便利迅捷;同时采用一套安全仪表系统(SIS),为全装置 关键的设备和系统提供安全保证; ⑥ 整个甲醇装置正常生产过程中,无有毒、有害的废水及废气排放,能做到清洁生产。
ATR 转化
非催化部分氧化
反应温度 ℃
相对温和
出口气体温度 ℃
~1000
出口气体组成
CH4(干基)<0.3%
《ATR 工艺在天然气转化制甲醇合成气中的工业应用 final.doc》 3
高,对耐火材料要求高 ~1200
CH4(干基)<0.3%
原料气消耗 氧气消耗 转化系统流程 下游热回收系统流程及设备
其主要反应为: CH4 + O2 = CO + H2O+H2+Q 2CH4+O2 = 2CO +4H2+Q CH4+2O2 = CO2+2H2O+Q 非催化氧化的转化气出口温度通常在 1200℃左右,残余甲烷指标同样也可以控制在 0.3
%(干基)。
ATR 转化与非催化部分氧化的比较见表一:
表一 ATR 转化与非催化部分氧化比较表
本项目为老厂改扩建项目,原兰州煤气厂现有 3×65 tons/hr 燃煤锅炉、2×6000 Nm3/hr 空分制氧装置、规划整齐的场地和道路等公用工程设施可以改造利用,中石油天然气公司在 距离厂区附近 500m 左右位置已设有涩-宁-兰天然气管线的一座大型分输站。
甲醇主装置主要由以下 6 个单元组成: 天然气压缩:采用全凝式蒸汽透平驱动离心式压缩机组; 天然气脱硫:采用加氢转化串联氧化锌脱硫,脱硫剂选用 T201 型加氢催化剂和 T305 氧化锌脱硫剂; 天然气转化:一段蒸汽转化(催化剂采用 Z412Q/Z413Q)串联二段 ATR 转化(纯 氧烧嘴以及催化剂 28-4Q(由英国 JMC 提供); 合成气压缩:采用全凝式蒸汽透平驱动离心式压缩机,新鲜气压缩和循环气压缩为 一个联合机组) 甲醇合成:合成塔为列管式绝热等温合成塔技术,催化剂采用英国 JMC 的 51-7; 甲醇精馏:预塔(脱除轻组分)+加压塔 +常压塔 +甲醇回收塔,常压塔、回收塔 为填料加塔盘,其余各塔采用高效规整填料;
③ 烧嘴保护蒸汽:ATR 联锁跳车自动打开氧气烧嘴保护蒸汽切断阀。 ④ 开车过程中按 SIS 程序控制步骤逐渐自动
打开氧气调节阀和 3 个氧气切断阀,自动 关闭 3 个氧气放空阀,烧嘴保护蒸汽切断 阀待工况稳定后再关闭;SIS 中还设定了 以上 8 个阀门的复位条件(一段转化气温 度、热氧气温度等),条件不满足时不能复
2.5 ATR 炉子设计特点
本项目采用的 ATR 为立式圆筒形结构,壳体材料为碳钢,内衬耐火材料,炉体外设计 有水冷夹套,顶部封头等未设计水冷夹套的部位壳体外表面涂刷高温热敏漆,如图二所示。
本项目氧气烧嘴及一段转化气分布器采用英国 Johnson Matthey Catalysts(JMC)公司专 有技术产品 ,该氧气烧嘴不需要夹套循环冷却水系统,具有安全、便于安装和操作的优点。
《ATR 工艺在天然气转化制甲醇合成气中的工业应用 final.doc》 5
流量摩尔比高高限联锁停 ATR(进氧终止)的条件; ⑨ ATR 出口超温控制:设计 ATR 出口温度高高限联锁停 ATR(进氧终止)的条件,
此条件执行晚于超温预控制设定点; ⑩ 其它控制:一段转化炉停车联锁停 ATR、以及 ATR 紧急停车按钮等。 以上优化过的控制系统设计方案从根本上解决了纯氧气介质操作安全问题。
2.2 催化氧化和非催化部分氧化的比较
目前,工业上普遍采用的甲烷深度转化方法主要有催化部分氧化法和非催化部分氧化 法,ATR 转化属于催化部分氧化法。
原料组分中的甲烷在 ATR 炉中的主要反应有: CH4 + CO2 = 2CO +2H2-Q
《ATR 工艺在天然气转化制甲醇合成气中的工业应用 final.doc》 2
动力学和热力学分析
有,可指导转化炉体及耐火衬里设计
《ATR 工艺在天然气转化制甲醇合成气中的工业应用 final.doc》 4
定性分析,无动态定量分析
燃烧区温度场分布研究 (CFD Study) 纯氧转化炉催化剂装填量 催化剂床层阻力降 烧嘴使用安全性和稳定性 火焰形状 烧嘴头操作温度 烧嘴连续运转周期
使用业绩/经验 生产操作 炉子结构 对进料气脱硫净化系统要求 下游脱硫系统 转化催化剂 是否析碳 是否有氨和 HCN 生成
低
高
低
高
复杂
简单
简单
复杂(特别是废热锅炉结构复杂,加 工难度很大)
有业绩、有成熟经验可参考 简单/易于控制
无成熟经验可参考 复杂
复杂 高 /进料气总硫含量<0.1ppm
简单 低/有机硫在转化炉内转化为 H2S
不需要
需设置湿法脱硫工序,流程也较长
需要
不需要
不析碳
存在析碳问题
无
有,下游必须增设除氨系统
从以上比较内容可以看出,在由天然气(或焦炉气等有效气体)制取合成气工艺中,目 前采用 ATR 工艺具有生产操作易于控制、不析碳、氧气和原料气消耗低等显著优点,总体 优于非催化部分氧化法。
2.3 先进的 ATR 烧嘴特点
关键词:ATR、合成气、工业应用
1 前言
2008 年 09 月 28 日由东华工程科技股份有限公司(ECEC)采用 EPC 总承包模式承建 的兰州蓝星化工有限公司 20 万吨/年天然气制甲醇项目一次投料试车成功,生产的甲醇产品 质量不仅符合 GB338-2004 标准优等品指标,而且符合工业甲醇美国联邦标准(O-M-232G) “AA”级指标。截止 2008 年 11 月 03 日,经 1 个月的连续试运转装置生产负荷达到设计负 荷的 90%,每吨精甲醇仅消耗天然气 900 Nm3,全装置综合能耗约为 34.0 GJ/吨精甲醇,在 国内同行业中处于领先水平。