滑动轴承减摩层的电镀新工艺
轴承室磨损处理及电镀工艺

由于镀铬层的优良性能﹐广泛用作防护一装饰镀层体系的外表层和机能镀层。
其它电镀
镀铜﹕镀铜层呈粉红色﹐质柔软﹐具有良好的延展性﹑导电性和导热性﹐易于抛光﹐经适当的化学处理可得古铜色﹑铜绿色﹑黑色和本色等装饰色彩。镀铜易在空气中失去光泽﹐与三氧化碳或氯化物作用﹐表面生成一层碱式碳酸铜或氯化铜膜层﹐受到硫化物的作用会生成棕色或黑色硫化铜﹐因此﹐做为装饰性的镀铜层需在表面涂覆有机覆盖层。
端盖轴承孔间隙增大的修理方法:1:镶补法,在车床上把端盖轴承孔的磨损面车光,镶入一段无缝钢管。在车成原来的轴承孔的尺寸。2:电镀法修补:在磨损的轴承孔内表面电镀上一层镍,使孔径缩小恢复至原来大小。
电解液配方。这个我就不在这说了。按上述成分配好后。加热至80~90℃。使它充分溶解,然后在过滤。在以镍棒为正极。溶液为负极。通电电解一到两小时。以增加镍离子的浓度。电解液的ph值对镀层均匀程度影响比较大。一般PH值要保持在4.8~5.2之间。。高了就加3%稀硫酸。调节至正常。低了用3%氢氧化钠溶液调节至正常。电解时温度不宜太高。以18~40摄氏度最宜。在电解前要做好端盖孔的清洁工作。还要除去油污。用氢氧化钠溶液冲洗。再用汽油或丙酮洗净。在用纱布搽干净。电流可以使用任何同量相当的整流电源或。蓄电池。电压我在这也不说了。每小时的镀层厚度为10~20微米。
镀锡﹕锡具有银白色的外观﹐原子量为118.7﹐密度为7.3g/cm3,熔点为232℃﹐原子价为二价和四价﹐故电化当量分别为2.12g/A.h和1.107g/A.h。锡具有抗腐蚀﹑无毒﹑易铁焊﹑柔软和延展性好等优点。锡镀层有如下特点和用途﹕1﹐化学稳定性高﹔2﹐在电化序中锡的标准电位纰铁正﹐对钢铁来说是阴极性镀层﹐只有在镀层无孔隙时才能有效地保护基体﹔3﹐锡导电性好﹐易焊﹔4﹐锡从-13℃起结晶开始开始发生变异﹐到-30℃将完全转变为一种晶型的同素异构体﹐俗称”锡瘟”﹐此时已完全失去锡的性质﹔5﹐锡同锌﹑镉镀层一样﹐在高温﹑潮湿和密闭条件下能长成晶须﹐称为长毛﹔6﹐镀锡后在232℃以上的热油中重溶处理﹐可获得有光泽的花纹锡层﹐可作日用品的装饰镀层。
滑动轴承减摩层的电镀新工艺
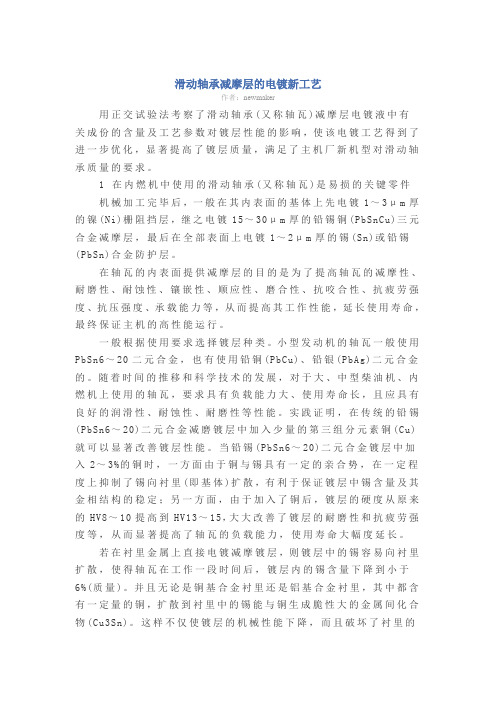
滑动轴承减摩层的电镀新工艺作者:newmaker用正交试验法考察了滑动轴承(又称轴瓦)减摩层电镀液中有关成份的含量及工艺参数对镀层性能的影响,使该电镀工艺得到了进一步优化,显著提高了镀层质量,满足了主机厂新机型对滑动轴承质量的要求。
1 在内燃机中使用的滑动轴承(又称轴瓦)是易损的关键零件机械加工完毕后,一般在其内表面的基体上先电镀1~3μm厚的镍(Ni)栅阻挡层,继之电镀15~30μm厚的铅锡铜(PbSnCu)三元合金减摩层,最后在全部表面上电镀1~2μm厚的锡(Sn)或铅锡(PbSn)合金防护层。
在轴瓦的内表面提供减摩层的目的是为了提高轴瓦的减摩性、耐磨性、耐蚀性、镶嵌性、顺应性、磨合性、抗咬合性、抗疲劳强度、抗压强度、承载能力等,从而提高其工作性能,延长使用寿命,最终保证主机的高性能运行。
一般根据使用要求选择镀层种类。
小型发动机的轴瓦一般使用PbSn6~20二元合金,也有使用铅铜(PbCu)、铅银(PbAg)二元合金的。
随着时间的推移和科学技术的发展,对于大、中型柴油机、内燃机上使用的轴瓦,要求具有负载能力大、使用寿命长,且应具有良好的润滑性、耐蚀性、耐磨性等性能。
实践证明,在传统的铅锡(PbSn6~20)二元合金减磨镀层中加入少量的第三组分元素铜(Cu)就可以显著改善镀层性能。
当铅锡(PbSn6~20)二元合金镀层中加入2~3%的铜时,一方面由于铜与锡具有一定的亲合势,在一定程度上抑制了锡向衬里(即基体)扩散,有利于保证镀层中锡含量及其金相结构的稳定;另一方面,由于加入了铜后,镀层的硬度从原来的HV8~10提高到HV13~15,大大改善了镀层的耐磨性和抗疲劳强度等,从而显著提高了轴瓦的负载能力,使用寿命大幅度延长。
若在衬里金属上直接电镀减摩镀层,则镀层中的锡容易向衬里扩散,使得轴瓦在工作一段时间后,镀层内的锡含量下降到小于6%(质量)。
并且无论是铜基合金衬里还是铝基合金衬里,其中都含有一定量的铜,扩散到衬里中的锡能与铜生成脆性大的金属间化合物(Cu3Sn)。
减摩润滑涂层技术

减摩润滑涂层技术嘿,朋友们!今天咱来聊聊这个超厉害的减摩润滑涂层技术。
你想想看啊,我们的生活里到处都有摩擦。
就好比你走路,鞋底和地面会有摩擦;你骑自行车,链条和齿轮之间也有摩擦。
这些摩擦有时候可让人头疼啦,它会损耗能量,还可能让零件磨损得更快。
那这时候减摩润滑涂层技术不就像个超级英雄一样出现啦!这减摩润滑涂层啊,就像是给机器零件穿上了一层特别的“保护衣”。
它能让那些相互接触的表面变得滑溜溜的,就像抹了油一样,但可比普通的油厉害多了。
它能长时间地发挥作用,而且效果还特别稳定。
比如说汽车发动机里的那些零件吧,如果没有减摩润滑涂层,那摩擦产生的热量和磨损得有多可怕呀!但有了它,发动机就能更顺畅地运转,不仅能节省燃料,还能延长发动机的使用寿命呢。
这难道不神奇吗?再看看那些大型的机械设备,要是没有这种涂层,那用不了多久可能就会出故障啦。
但有了它,就可以大大减少维修的次数和成本,这可给企业省了不少钱呢!你说这减摩润滑涂层技术是不是很重要?它就像是幕后的英雄,默默地为我们的生活和工作提供着支持。
而且啊,这技术还在不断发展和进步呢。
科学家们一直在研究怎么让涂层的性能更好,更耐用。
说不定以后啊,我们身边所有的东西都会因为有了更好的减摩润滑涂层而变得更加高效和可靠。
你想想,如果家里的各种电器都用上了超级厉害的减摩润滑涂层,那它们是不是就不那么容易坏啦?我们也不用总是为了修这修那而烦恼啦。
还有啊,在工业生产中,这技术的应用会让生产效率大大提高,产品质量也会更好。
这对企业来说可是大好事呀,能赚更多的钱,也能为我们提供更好的产品。
总之呢,减摩润滑涂层技术真的是太重要啦!它虽然不起眼,但却在我们生活的方方面面都发挥着巨大的作用。
我们可不能小瞧了它呀!所以,大家一定要重视这个神奇的技术,让它为我们的生活带来更多的便利和好处!。
轴磨损电刷镀工艺替代技术
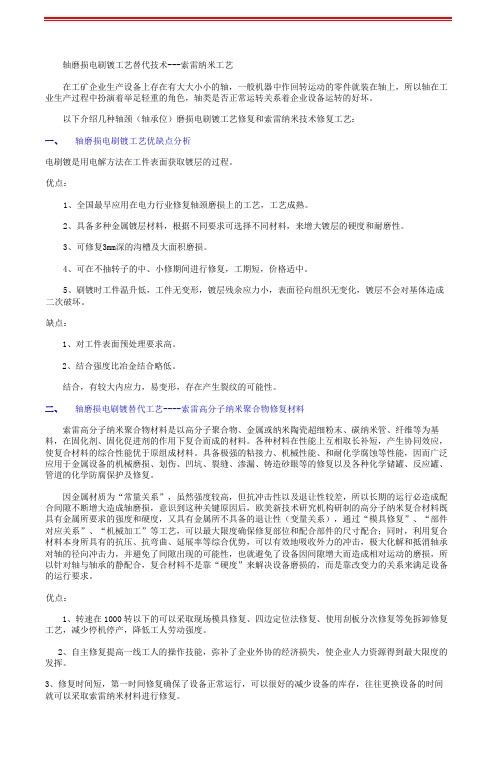
轴磨损电刷镀工艺替代技术---索雷纳米工艺在工矿企业生产设备上存在有大大小小的轴,一般机器中作回转运动的零件就装在轴上,所以轴在工业生产过程中扮演着举足轻重的角色,轴类是否正常运转关系着企业设备运转的好坏。
以下介绍几种轴颈(轴承位)磨损电刷镀工艺修复和索雷纳米技术修复工艺:一、轴磨损电刷镀工艺优缺点分析电刷镀是用电解方法在工件表面获取镀层的过程。
优点:1、全国最早应用在电力行业修复轴颈磨损上的工艺,工艺成熟。
2、具备多种金属镀层材料,根据不同要求可选择不同材料,来增大镀层的硬度和耐磨性。
3、可修复3mm深的沟槽及大面积磨损。
4、可在不抽转子的中、小修期间进行修复,工期短,价格适中。
5、刷镀时工件温升低,工件无变形,镀层残余应力小,表面径向组织无变化,镀层不会对基体造成二次破坏。
缺点:1、对工件表面预处理要求高。
2、结合强度比冶金结合略低。
结合,有较大内应力,易变形,存在产生裂纹的可能性。
二、轴磨损电刷镀替代工艺----索雷高分子纳米聚合物修复材料索雷高分子纳米聚合物材料是以高分子聚合物、金属或纳米陶瓷超细粉末、碳纳米管、纤维等为基料,在固化剂、固化促进剂的作用下复合而成的材料。
各种材料在性能上互相取长补短,产生协同效应,使复合材料的综合性能优于原组成材料。
具备极强的粘接力、机械性能、和耐化学腐蚀等性能,因而广泛应用于金属设备的机械磨损、划伤、凹坑、裂缝、渗漏、铸造砂眼等的修复以及各种化学储罐、反应罐、管道的化学防腐保护及修复。
因金属材质为“常量关系”,虽然强度较高,但抗冲击性以及退让性较差,所以长期的运行必造成配合间隙不断增大造成轴磨损,意识到这种关键原因后,欧美新技术研究机构研制的高分子纳米复合材料既具有金属所要求的强度和硬度,又具有金属所不具备的退让性(变量关系),通过“模具修复”、“部件对应关系”、“机械加工”等工艺,可以最大限度确保修复部位和配合部件的尺寸配合;同时,利用复合材料本身所具有的抗压、抗弯曲、延展率等综合优势,可以有效地吸收外力的冲击,极大化解和抵消轴承对轴的径向冲击力,并避免了间隙出现的可能性,也就避免了设备因间隙增大而造成相对运动的磨损,所以针对轴与轴承的静配合,复合材料不是靠“硬度”来解决设备磨损的,而是靠改变力的关系来满足设备的运行要求。
滑动轴承镀层退除工艺的介绍与应用

学方法退除的轴承 , 其表面用轮廓仪测定 , 其粗糙度 仍保持原有的 R =04 m, a . 没有受 到任何腐蚀。退
除后 的轴 承重新 电镀 三 元合 金 镀 层 质 量 良好 , 足 满
产 品生产 要求 。
的结合力, 使其不能通过热震试验 , 发生起泡、 脱皮
等缺 陷 , 最终 导致 产 品报 废 。若 要 用 镗加 工 的方 法
铜三元合金减磨镀层的电镀是重要 的工序之一。
由于种 种原 因 , 交检产 品中 。 部分 镀层 不 能满足 技 有
基三元合金镀层 的过程 中, 暴露出的铜基合金基体
免 遭腐蚀 的配 方 及 操 作 要求 。经 反 复试 验 , 们 确 我 定 了配 方中 的主要 成分 及缓 冲剂 、 蚀剂 ; 正 交试 缓 用 验 法确定 了各 成分 含量 配 比及操作要 求 。用该 电化
维普资讯
薛 福 连 :滑动 轴 承 镀 层 退 除 工 艺 的介 绍 与 应 用
1 3
盐 。它 可增加 槽液 的导 电性 、 降低槽 电压 , 槽液 的 使 温升不至过快 , 同时 又节约能 源 。含 量过高 则槽液 带 出损 失增 大 , 含量 过 低 则槽 液 的 导 电性 降低 温 升过 快, 耗费能源 。由试验 确定其 含量 在 10 5g L为 5 -20 /
【 关键词】 电镀 镀覆
减磨覆层 滑动轴承
・
中的化学 、 电化 学行 为 [ ] 3 和钢 背 、 基 合 金 体 的腐 铜
1 前 言
在 内燃机 滑 动轴 承 的生 产 制造 过 程 中 , 铅一 锡
一
蚀机 理和 防腐 原理 这 两 个 问题 入 手 , 求解 决 问题 寻 的途径 。其 主要 目的是要 确定 在用 电化 学法退 除铅
滑动轴承减摩层的电镀新工艺
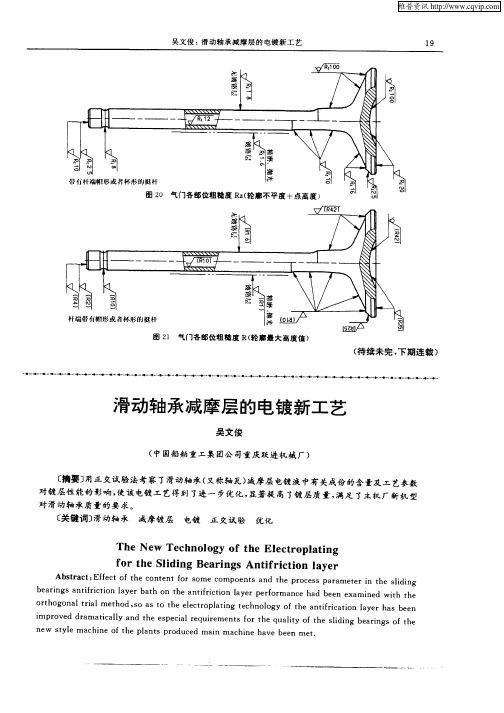
吴文俊 :滑动轴承减 摩层的 电镀 新工艺
1 9
图 2 气 门 各部 位 粗 糙 度 R( 廓 最 大 高 度 值 ) 1 轮
( 续未 完 , 期连 载 ) 待 下
… . .… . .… . … . … ・ . . ●… . .… . .… ・ - . ●… ・ ● .・ ●… ・ . . . . ● ..
利 , 用 于海 军 鱼 雷储 气瓶 的 内表 面 电镀 , 并 到二 十 世
在轴 瓦 的 内表 面提 供 减摩 层 的 目的是 为 了提 高 轴 瓦 的减 摩 性 、 磨性 、 蚀 性 、 嵌 性 、 应 性 、 耐 耐 镶 顺 磨
合 性 、 咬 合 性 、 疲 劳 强 度 、 压 强 度 、 载 能 力 抗 抗 抗 承 等 , 而提 高 其 工 作 性 能 , 长使 用寿 命 , 终 保 证 从 延 最 主 机 的高 性 能运 行 。
.
维普资讯
2 0
内 燃 机 配 件
20 年第 5期 02
K e wo d : l i g Be rn A n ir a in ly r Elc r p a ig Or h g n lTra a y r s S i n a ig d tfi to a e c e to ltn t o o a ilW y
Op i ia i n t z to m
1 前言
在 内燃 机 中使 用 的滑 动轴 承 ( 称轴 瓦 ) 易损 又 是 的关键 零 件 。 械 加工 完 毕后 , 般在 其 内表 面 的基 机 一 体 上 先 电镀 1 3 m 厚 的镍 ( ) 阻 挡 层 _ ]继 ~ Ni栅 1 ,
2 发展历 程
减摩 镀 层 在 国外 的研 究起 步 较早 。 9 0年 由格 12
制备滑动轴承的覆层材料的方法和实施此方法的电镀浴[发明专利]
![制备滑动轴承的覆层材料的方法和实施此方法的电镀浴[发明专利]](https://img.taocdn.com/s3/m/dac5b0841eb91a37f0115c6a.png)
专利名称:制备滑动轴承的覆层材料的方法和实施此方法的电镀浴
专利类型:发明专利
发明人:H-U·胡安,D·维巴赫,K·米勒
申请号:CN97192495.3
申请日:19970222
公开号:CN1212030A
公开日:
19990324
专利内容由知识产权出版社提供
摘要:本发明提出一种制备滑动轴承覆层材料的方法和实施此方法的电镀浴。
按本发明的方法,在青铜层上顺序电镀沉积一个铅—或锡—基的二元层和一个钼基的跑合层,为在所述青铜层上沉积二元层,采用具有非离子的湿润剂和苯衍生物的电镀浴。
在二元层沉积后和跑合层沉积前对二元层的至少一表面层进行阳极活化。
覆层材料具有一钢座圈(1)和一浇铸的铅青铜层(2),在铅青铜层上电镀附着一中间层(13)。
在电镀沉积(3)后,通过阳极活化实现对表面区域(5)的改变。
在阳极活化后电镀附着氧化钼层(4)。
申请人:格莱库金属构件两合公司
地址:联邦德国威斯巴登
国籍:DE
代理机构:中国国际贸易促进委员会专利商标事务所
代理人:吴亦华
更多信息请下载全文后查看。
精密轴承用钢珠离子镀glc镀层实现自润滑的处理方法

精密轴承用钢珠离子镀glc镀层实现自润滑的处理方法精密轴承用钢珠离子镀GLC镀层实现自润滑的处理方法一、引言精密轴承在现代机械制造领域中扮演着十分重要的角色。
其性能的优劣直接影响到机械设备的使用寿命和运行效率。
而精密轴承用钢珠的表面处理则是影响其性能的关键因素之一。
在这方面,近年来,离子镀GLC(Gas Lubricated Coating)镀层技术逐渐受到人们的关注,因其能够实现自润滑功能,提高轴承性能,延长使用寿命。
本文将对精密轴承用钢珠离子镀GLC镀层实现自润滑的处理方法进行全面评估,旨在探讨其技术原理和应用前景。
二、离子镀GLC镀层技术原理1. GLC镀层的成分和结构GLC镀层是由碳、氮等物质组成的非晶态碳化膜,其中包含着大量的微孔和微裂纹。
这些微孔和微裂纹不仅能容纳润滑油,形成润滑膜,还能在运动中不断地释放,起到自润滑的效果。
2. 镀层工艺GLC镀层的制备需要采用真空离子镀技术。
在真空室中,通过控制离子轰击的能量和时间,使得碳、氮等元素沉积到钢珠表面,形成均匀的非晶态碳化膜。
三、GLC镀层实现自润滑的处理方法1. 优化镀层组分合理的镀层组分对于实现自润滑十分关键。
在离子镀过程中,通过调控镀层元素的比例和分布,可以得到不同性能的镀层。
一般情况下,碳氮比高、晶格常数小的镀层更有利于实现自润滑功能。
2. 控制镀层厚度镀层的厚度会直接影响到其自润滑性能。
适当增加镀层厚度,可以提高润滑油的储存量和释放速度,从而增强自润滑效果。
3. 表面预处理在离子镀过程之前,需要对钢珠表面进行精细的预处理,包括清洗、打磨和表面活化。
这些步骤可以有效地提高镀层的附着力和润滑性能。
四、GLC镀层技术在精密轴承用钢珠中的应用前景GLC镀层技术相比于传统的涂层技术,具有制备工艺简单、成本低廉、环保性好等优点,因此在精密轴承用钢珠中的应用前景十分广阔。
通过GLC镀层的方式实现自润滑,不仅可以减轻轴承运动过程中的摩擦和磨损,延长使用寿命,还可以提高轴承的运行效率,减小能量损耗。
电镀轴瓦减摩层的挂具

电镀轴瓦减摩层的挂具
闵东高
【期刊名称】《内燃机配件》
【年(卷),期】1992(000)004
【摘要】随着内燃机技术的发展,内燃机轴瓦的负荷不断提高。
轴瓦内表面镀覆减摩层成为提高轴瓦工作性能的重要手段。
如何获得与基体结合牢固,壁厚均匀的减摩镀层,满足内燃机工业生产的需要,是国内外许多科技工作者努力探索、研究的课题。
其中专用于轴瓦内表面电镀减摩层的挂具,在国外已有许多专利。
五十年代初,klein·Guter等人开始研究电镀减摩层的挂具并获得美国专利。
他们提出了圆筒式挂具,用人工方法,将两个半圆瓦合成一个整圆,外表面包扎绝缘材料,以阻止电镀外层合金。
然后层叠起来,上下用耐腐蚀材料制成的盖板封住,并利用盖板固定阳极棒在圆筒中心。
很显然,在大工业生产中,这种方法的效率是很低的。
1954年, Beebe, A·H在美国专利2697690中,提出了盒式电镀挂具。
这种挂具是用耐腐蚀材料制成一长方形的密封盘,盒的底板上开一条狭缝,轴瓦内表面对着狭缝排列。
【总页数】3页(P61-63)
【作者】闵东高
【作者单位】武汉轴瓦厂
【正文语种】中文
【中图分类】TK406
【相关文献】
1.轴瓦电镀减摩性Pb-Sn-Sb合金新工艺 [J], 徐瑞东;郭忠诚;周卫铭;薛方勤
2.滑动轴承减摩层的电镀新工艺 [J], 吴文俊
3.电镀挂具上镀金层的回收与提纯 [J], 王细法
4.轴瓦三元合金电镀工艺及挂具的研究 [J], 王会文;曾良宇
5.甲基磺酸盐镀液电镀轴瓦减摩层的方法 [J],
因版权原因,仅展示原文概要,查看原文内容请购买。
- 1、下载文档前请自行甄别文档内容的完整性,平台不提供额外的编辑、内容补充、找答案等附加服务。
- 2、"仅部分预览"的文档,不可在线预览部分如存在完整性等问题,可反馈申请退款(可完整预览的文档不适用该条件!)。
- 3、如文档侵犯您的权益,请联系客服反馈,我们会尽快为您处理(人工客服工作时间:9:00-18:30)。
滑动轴承减摩层的电镀新工艺作者:newmaker用正交试验法考察了滑动轴承(又称轴瓦)减摩层电镀液中有关成份的含量及工艺参数对镀层性能的影响,使该电镀工艺得到了进一步优化,显著提高了镀层质量,满足了主机厂新机型对滑动轴承质量的要求。
1 在内燃机中使用的滑动轴承(又称轴瓦)是易损的关键零件机械加工完毕后,一般在其内表面的基体上先电镀1~3μm厚的镍(Ni)栅阻挡层,继之电镀15~30μm厚的铅锡铜(PbSnCu)三元合金减摩层,最后在全部表面上电镀1~2μm厚的锡(Sn)或铅锡(PbSn)合金防护层。
在轴瓦的内表面提供减摩层的目的是为了提高轴瓦的减摩性、耐磨性、耐蚀性、镶嵌性、顺应性、磨合性、抗咬合性、抗疲劳强度、抗压强度、承载能力等,从而提高其工作性能,延长使用寿命,最终保证主机的高性能运行。
一般根据使用要求选择镀层种类。
小型发动机的轴瓦一般使用PbSn6~20二元合金,也有使用铅铜(PbCu)、铅银(PbAg)二元合金的。
随着时间的推移和科学技术的发展,对于大、中型柴油机、内燃机上使用的轴瓦,要求具有负载能力大、使用寿命长,且应具有良好的润滑性、耐蚀性、耐磨性等性能。
实践证明,在传统的铅锡(PbSn6~20)二元合金减磨镀层中加入少量的第三组分元素铜(Cu)就可以显著改善镀层性能。
当铅锡(PbSn6~20)二元合金镀层中加入2~3%的铜时,一方面由于铜与锡具有一定的亲合势,在一定程度上抑制了锡向衬里(即基体)扩散,有利于保证镀层中锡含量及其金相结构的稳定;另一方面,由于加入了铜后,镀层的硬度从原来的HV8~10提高到HV13~15,大大改善了镀层的耐磨性和抗疲劳强度等,从而显著提高了轴瓦的负载能力,使用寿命大幅度延长。
若在衬里金属上直接电镀减摩镀层,则镀层中的锡容易向衬里扩散,使得轴瓦在工作一段时间后,镀层内的锡含量下降到小于6%(质量)。
并且无论是铜基合金衬里还是铝基合金衬里,其中都含有一定量的铜,扩散到衬里中的锡能与铜生成脆性大的金属间化合物(Cu3Sn)。
这样不仅使镀层的机械性能下降,而且破坏了衬里的结构,至使轴瓦的整体机械性能降低。
解决该问题的方法是在衬里材料与减摩底层之间电镀一层镍或镍基合金阻挡层(又称栅层或阻挡层),以抑制锡向衬里扩散。
锡或铅锡合金防护层除了具有一定的防腐蚀作用外,在轴瓦工作期间还可以扩散的方式补充减摩层中的锡的含量,使其各成分的含量处于相对稳定的状态。
另外,由于这层防护层不含铜,相对较软,因此轴瓦在工作的初期就能达到良好的磨合要求。
本文主要考察轴瓦减摩层的电镀工艺。
2 发展历程减摩镀层在国外的研究起步较早。
1920年由格罗奥夫(J.Grooff)提出了电镀铅锡合金的第一个专利,并用于海军鱼雷储气瓶的内表面电镀,到二十世纪四十年代开始用于轴瓦的电镀。
1952年舒尔茨(Schults)提出了在铝及铝硅(AlSi)合金基体上电镀铅锡铜三元合金的专利。
1953年舍夫(Schoefe)曾发表轴瓦使用铅锡铜合金的综述。
1976年,Jong-Sang Kim,Su-ιιPyun and Hyo-Geun Lee发表了“铅锡铜电镀层的晶面取向及微观形貌”的论文。
1980年毕比(Beebe)提出含铜2~3%(质量)、锡9~12%(质量),其余为铜的三元合金电镀生产工艺流程,镀层厚度为15μm。
1982年沃特曼(Waterman)等人就三元合金电镀液中铜离子(Cu2+)的置换问题提出了解决的办法。
国内对于减摩合金镀层的研究和应用起步较晚。
1960年初,武汉材料保护研究所与海陵第一配件厂首先研制并用于生产的电刷镀铅锡合金工艺已用于快艇发动机的电镀。
二十世纪七十年代中期,上海合金轴瓦厂及上海沪东造船厂对轴瓦电镀铜锡合金工艺者了较详细的研究。
1985年,哈尔滨工业大学电化学教研室与中国船舶工业总公司四六六厂共同研究了铅青铜滑动轴承上电镀铅锡铜三元合金减摩层的工艺,并已用于生产。
1989年,Dusanka Radoric 发表了“在氟硼酸盐镀液中以氢醌(对一苯二酚)为添加剂的铅锡合金电镀”的论文。
十十世纪末,南通轴瓦厂的范家华、姜志东,武汉材料保护研究所的曾良宇、杨先桂、王会文,广西桂林内燃机配件厂的秦胜毅,戚墅堰机车车辆工艺研究所薛伯生等对减摩层的电镀工艺从不同的方面先后进行过不同程度的研究,为该工艺在生产应用中的进一步完善奠定了一定的基础。
3 问题的提出我厂的铅锡铜三元合金减摩镀层的电镀工艺属国内首创,多年来为我国主机配件市场提供了大量轴瓦。
近年来,我厂轴瓦产品定货量逐年上升,并且有些轴瓦产品已打入国际市场,具有一定量的出口。
这充分体现了我厂的轴瓦产品在激烈的市场竞争中具有相当强的实力。
自1989年到1991年期间,通过我们的艰苦努力、反复试验,已从根本上解决了轴瓦镀层起泡、脱皮等附着强度差的致命缺陷问题;消除了基体遭受批量性严重腐蚀的故障;克服了批量性壁厚超差,提高了工序能力;废品损失率一直很低,一次交检合格品率逐年提高。
然而,镀层粗糙、结瘤、花斑、凹坑、气流条纹等缺陷还时有发生,有时还出现阴极电流密度(DK)达不到工艺范围的现象。
减摩镀层的上述缺陷直接影响轴瓦产品质量。
随着主机厂机型的不断更新换代、进口机型的国产化及市场竞争的日趋激烈,用户对轴瓦产品质量的要求越来越高。
市场的竞争从根本上说就是产品质量的竞争。
在用户对产品质量指标要求日益提高的形势下,我们面临着改进轴瓦电镀工艺、进一步提高轴瓦产品质量这一新课题的严峻挑战。
4 影响轴瓦减摩镀层质量的有关因素4.1 铅锡铜三元合金减摩层电镀液的文献配方及工艺参数文献中发表的铅锡铜三元合金镀液中有关成分的含量及工艺参数归纳如下:Pb2+(以Pb(BF4)2的形式加入):80~333g/ι;Sn2+(以Sn(BF4)2的形式加入):5~33.3g/ι;Cu2+(以Cu(BF4)2的形式加入):2~11g/ι;HBF4(游离):40~300g/ι;H3BO3(游离):15~40g/ι;稳定剂:2~12g/ι;添加剂:0.1~5g/ι;阴极电流密度(DK):1~8A/dm2;温度(T):15~30℃;时间(t):15~35min;镀层厚度(δ):15~30μm;阳极的组成:PbSn8~11。
4.2 影响减摩镀层质量的有关因素从上述配方中可以看到,无论是成分含量还是工艺参数,其范围都太宽;为适应生产要求,有必要进一步寻优,在进行寻优试验之前先对影响减摩镀层质量的有关因素进行必要的分析,以确定正交试验中各因子水平的可行域。
4.2.1 主盐离子浓度的影响镀液中的主盐离子为Pb2+、Sn2+、Cu2+。
其中的Sn2+、Cu2+的含量可根据合金镀层中Sn、Cu的重量百分含量进行相应的调整,可以满足用户对镀层成分含量的要求。
因此对主盐离子而言,仅就镀液中的Pb2+含量对镀层质量的影响进行讨论。
镀液中的Pb2+为合金镀层提供主要组分,文献报道的含量范围为80~333g/ι。
如果其浓度较高,则允许使用较高的阴极电流密度,沉积速度快;但分散能力降低,带出损失较大。
如果其浓度较低,则分散能力较好,但沉积速度较慢。
如果含量太低则镀液的浓差极化太大,电流升不上去,镀层易出现气流条纹缺陷和棱锥形的微观金相结构,直观上体现为镀层粗糙。
如果含量过高则一方面使镀液带出损失增大,增加成本;另一方面在气温较低时易发生硼酸(H3BO3)及添加剂的析出现象,从而造成镀层粗糙。
适宜的含量是DK升至工艺规定的上限,且镀层结晶细致;在气温降至15℃以下时,镀液中应无硼酸及添加剂的析出现象。
4.2.2 游离氟硼酸(HBF4)浓度的影响其主要作用为促使阳极正常溶解;防止二价锡(Sn2+)的氧化和抑制主要离子(Pb2+、Sn2+、Cu2+)的水解,提高镀液的稳定性;提高导导性及分散能力;细化结晶。
文献报道的含量范围为40~300g/ι。
当游离氟硼酸的含量过低时,它离解出的氢离子(H+)浓度低,镀液中可能发生如下水解反应;Pb2++2H2O小于==大于Pb(OH)2↓+2H+Sn2++2H2O小于==大于Sn(OH)2↓+2H+Cu2++2H2O小于==大于Cu(OH)2↓+2H+.它们都生成氢氧化物沉淀而悬浮于镀液中。
电镀时,它们粘附于基体表面或夹杂在镀层内,使得镀层与基体之间的结合力下降,且镀层发脆、粗糙、起花斑,从而镀层的耐磨性及抗疲劳强度等性能明显下降。
当镀液中的游离氟硼酸含量过高时,在镀件的高电流密度处,即轴瓦有毛刺的地方或锐边、端面等有氢气析出。
其结果是在轴瓦镀层上面产生气流条纹和针孔缺陷。
同时,因为边缘效应和尖端放电使得高电流密度处沉积太快,镀液中的主盐离子来不及补充,即由表面扩散或形核控制转变成液相传质控制,浓差极化增大得使轴瓦内表面(阴极)发生如下电化学副反应:2H++2e小于==大于H2↑从上述反应可以看出,当氢离子(H+)浓度(即相应的游离氟硼酸的浓度)增高时,平衡向右边移动,促进氢气(H2)的生成。
析氢的结果不仅会使镀层出现气流条纹和针孔等缺陷,而且还会由于初生态的氢(H--即氢自由基)向镀层内部渗透形成金属氢化物而产生晶格扭曲及螺纹错位现象。
如果用扫描电镜(SEM)观察该镀层断面的微观形貌,可以发现其晶体呈大棱锥结构,直观上则是镀层粗糙。
另一方面,形成的金属氢化物是不稳定物质,经烘烤加热检验时会分解而释放出氢气(H2)从而使镀层发生鼓泡现象。