注塑成型充填过程的数值模拟技术
汽车塑料油底壳注塑成型数值模拟与结构优化研究
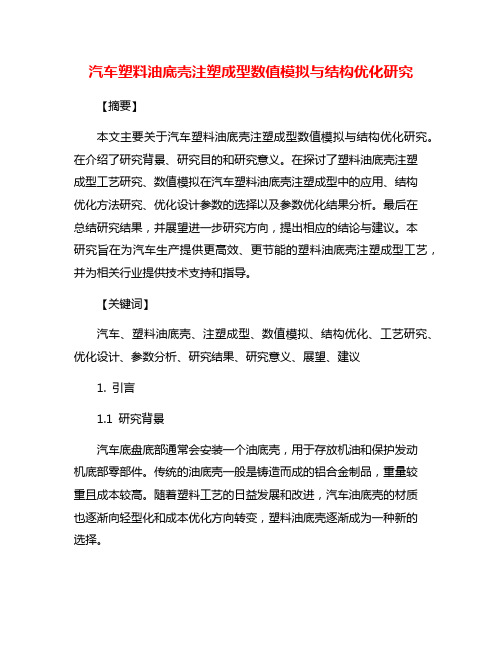
汽车塑料油底壳注塑成型数值模拟与结构优化研究【摘要】本文主要关于汽车塑料油底壳注塑成型数值模拟与结构优化研究。
在介绍了研究背景、研究目的和研究意义。
在探讨了塑料油底壳注塑成型工艺研究、数值模拟在汽车塑料油底壳注塑成型中的应用、结构优化方法研究、优化设计参数的选择以及参数优化结果分析。
最后在总结研究结果,并展望进一步研究方向,提出相应的结论与建议。
本研究旨在为汽车生产提供更高效、更节能的塑料油底壳注塑成型工艺,并为相关行业提供技术支持和指导。
【关键词】汽车、塑料油底壳、注塑成型、数值模拟、结构优化、工艺研究、优化设计、参数分析、研究结果、研究意义、展望、建议1. 引言1.1 研究背景汽车底盘底部通常会安装一个油底壳,用于存放机油和保护发动机底部零部件。
传统的油底壳一般是铸造而成的铝合金制品,重量较重且成本较高。
随着塑料工艺的日益发展和改进,汽车油底壳的材质也逐渐向轻型化和成本优化方向转变,塑料油底壳逐渐成为一种新的选择。
塑料材质具有一定的物理机械性能限制,在注塑成型过程中可能会出现熔体流动不畅、残余应力过大和收缩变形等问题,影响油底壳的质量和性能。
对汽车塑料油底壳的注塑成型工艺进行研究和优化显得尤为重要。
目前,数值模拟技术在塑料制品的成型工艺中得到了广泛应用,可以模拟流动场、熔体充填和固化过程,为工程师提供重要的参考依据。
结构优化方法可以通过优化设计参数,实现对塑料油底壳结构的轻量化和性能优化。
通过对汽车塑料油底壳注塑成型数值模拟与结构优化的研究,有助于提高油底壳的生产效率和质量稳定性,促进汽车轻量化和节能减排,具有重要的工程应用价值和研究意义。
1.2 研究目的汽车塑料油底壳是车辆发动机的重要部件,其注塑成型工艺直接影响着整个车辆的性能和质量。
由于油底壳形状复杂、受力特性复杂等因素,传统的注塑成型工艺存在一些问题,比如产品质量不稳定、生产效率低下等。
本研究旨在通过数值模拟与结构优化的方法,对汽车塑料油底壳注塑成型进行深入研究,从而提高产品质量和生产效率。
《汽车三角窗密封件注塑成型数值模拟及模具结构改进》

《汽车三角窗密封件注塑成型数值模拟及模具结构改进》篇一一、引言汽车行业近年来随着技术的不断创新与进步,对于零部件的生产质量与效率要求日益提高。
其中,汽车三角窗密封件作为汽车车身的重要组成部分,其性能的优劣直接关系到汽车的安全性能与使用体验。
本文旨在通过对汽车三角窗密封件注塑成型过程的数值模拟,以及模具结构的改进,来提高其生产效率与产品质量。
二、汽车三角窗密封件注塑成型数值模拟1. 模拟软件与建模利用现代计算机辅助工程(CAE)软件,如Moldflow等,对汽车三角窗密封件的注塑成型过程进行数值模拟。
首先,根据实际产品尺寸与要求,建立三维模型,并设定相应的材料属性、工艺参数等。
2. 注塑成型过程分析通过模拟软件,对注塑成型的填充、保压、冷却等过程进行详细分析。
包括填充速度、压力分布、温度场等关键参数的监测与分析,以了解成型过程中可能存在的问题。
3. 结果评估与优化根据模拟结果,评估汽车三角窗密封件的成型质量,如是否存在缩痕、气孔、翘曲等问题。
通过调整注塑工艺参数、改变模具结构等方式,对成型过程进行优化,以提高产品质量。
三、模具结构改进1. 模具结构设计现状分析针对现有模具结构在注塑成型过程中存在的问题,如注塑口设计不合理、冷却系统不完善等,进行详细分析。
了解这些问题对产品质量的影响,为模具结构改进提供依据。
2. 模具结构改进方案根据分析结果,提出模具结构改进方案。
包括优化注塑口设计、完善冷却系统、调整模具各部分尺寸与位置等。
通过改进模具结构,提高注塑成型的稳定性与产品质量。
3. 改进后模具的应用与效果评估将改进后的模具应用于实际生产中,对生产效率、产品质量等进行评估。
通过实际生产数据与模拟结果的对比,验证模具结构改进的效果。
四、结论通过对汽车三角窗密封件注塑成型过程的数值模拟及模具结构的改进,可以有效提高生产效率与产品质量。
数值模拟能够帮助我们了解注塑成型过程中的关键参数与问题,为优化注塑工艺提供依据。
注塑成型数值模拟报告
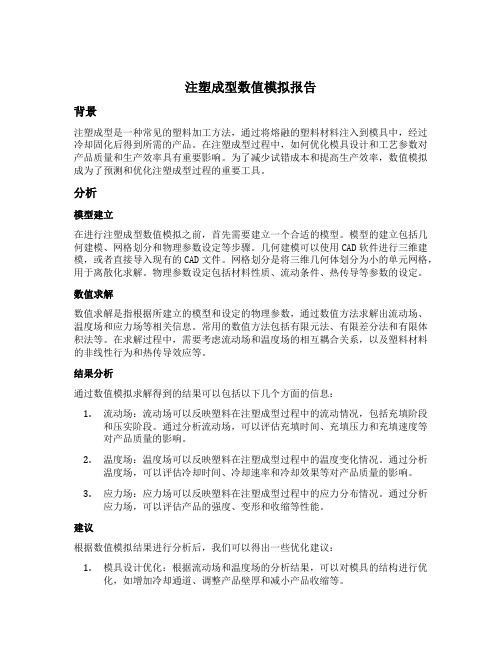
注塑成型数值模拟报告背景注塑成型是一种常见的塑料加工方法,通过将熔融的塑料材料注入到模具中,经过冷却固化后得到所需的产品。
在注塑成型过程中,如何优化模具设计和工艺参数对产品质量和生产效率具有重要影响。
为了减少试错成本和提高生产效率,数值模拟成为了预测和优化注塑成型过程的重要工具。
分析模型建立在进行注塑成型数值模拟之前,首先需要建立一个合适的模型。
模型的建立包括几何建模、网格划分和物理参数设定等步骤。
几何建模可以使用CAD软件进行三维建模,或者直接导入现有的CAD文件。
网格划分是将三维几何体划分为小的单元网格,用于离散化求解。
物理参数设定包括材料性质、流动条件、热传导等参数的设定。
数值求解数值求解是指根据所建立的模型和设定的物理参数,通过数值方法求解出流动场、温度场和应力场等相关信息。
常用的数值方法包括有限元法、有限差分法和有限体积法等。
在求解过程中,需要考虑流动场和温度场的相互耦合关系,以及塑料材料的非线性行为和热传导效应等。
结果分析通过数值模拟求解得到的结果可以包括以下几个方面的信息:1.流动场:流动场可以反映塑料在注塑成型过程中的流动情况,包括充填阶段和压实阶段。
通过分析流动场,可以评估充填时间、充填压力和充填速度等对产品质量的影响。
2.温度场:温度场可以反映塑料在注塑成型过程中的温度变化情况。
通过分析温度场,可以评估冷却时间、冷却速率和冷却效果等对产品质量的影响。
3.应力场:应力场可以反映塑料在注塑成型过程中的应力分布情况。
通过分析应力场,可以评估产品的强度、变形和收缩等性能。
建议根据数值模拟结果进行分析后,我们可以得出一些优化建议:1.模具设计优化:根据流动场和温度场的分析结果,可以对模具的结构进行优化,如增加冷却通道、调整产品壁厚和减小产品收缩等。
2.工艺参数优化:根据流动场和温度场的分析结果,可以对注塑成型过程中的工艺参数进行优化,如调整充填时间、充填压力和冷却时间等。
3.材料选择优化:根据应力场的分析结果,可以对材料的选择进行优化,以满足产品的强度和变形要求。
大型模具系统注塑成型过程中传热行为的数值模拟

大型模具系统注塑成型过程中传热行为的数值模拟王犇;李旭东【摘要】为了研究大型整体式模具系统在注塑成型工艺流程中各个阶段内模具表面温度分布规律以及相应的模具系统内各个部分的热交换效应,基于ABAQUS有限元分析平台对注塑成型用的大型整体式模具系统进行拟实性传热行为的数值模拟.结果表明:高温塑料熔体在型腔内流动的过程中,模具表面温度沿熔体流动方向呈梯度分布,注射结束后,透明预制件表面温度分布不均匀且低于芯部温度.此外,随形管道造成透明预制件内外表面冷速不同,对制件区域性能的一致性有显著影响.通过对模具系统注塑过程热交换效应的模拟再现,为工程实际中模具系统结构上的设计优化提供理论依据.【期刊名称】《甘肃科学学报》【年(卷),期】2018(030)004【总页数】7页(P119-125)【关键词】模具系统;注塑成型;传热行为;模具温度;数值模拟【作者】王犇;李旭东【作者单位】兰州理工大学省部共建有色金属先进加工与再利用国家重点实验室,甘肃兰州 730050;兰州理工大学省部共建有色金属先进加工与再利用国家重点实验室,甘肃兰州 730050【正文语种】中文【中图分类】TQ320.66注塑成型是将热塑性或热固性塑料加热转变为熔融状态,然后将熔体注射到型腔中并经过一定的工艺条件或工艺设置,将熔体冷却为各种复杂结构的制件的成型过程。
注塑成型是重要的塑料制品成型方式,适于大批量生产形状复杂、尺寸要求精确的塑料制品,注塑成型工艺非常复杂,成型制品质量受到模具设计参数,材料性能参数及充填、保压和冷却过程中工艺参数等许多因素的影响[1]。
传热过程是注塑成型过程中最重要的部分之一[2],其中注塑模具的温度大小及其分布是影响制品品质的重要因素,尤其是型腔壁面温度,模具的预热及冷却系统设计和注塑工艺设置都会考虑该重要参数,制品的形变量、尺寸精度、力学性能以及表面质量都受到模具温度的影响[3]。
模具温度过高,会使塑料制品收缩率增大,尺寸精度下降,表面产生花斑,并导致脱模困难;模具温度过低,使得塑料熔体粘度降低,流动阻力增大,导致物料交联固化不充分,机械强度受影响。
精密注塑成型过程模拟及优化分析
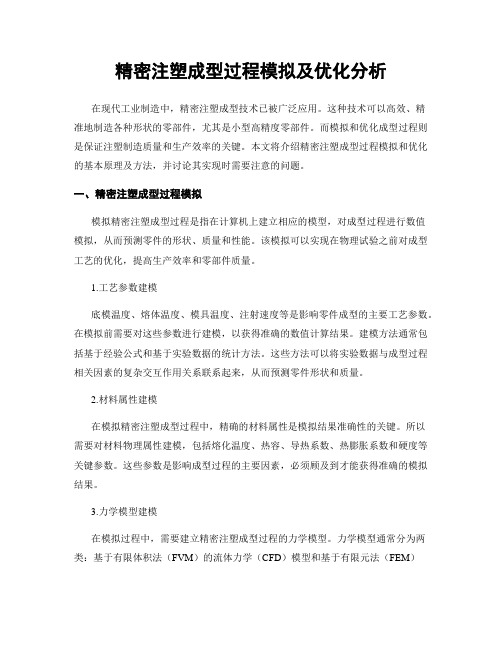
精密注塑成型过程模拟及优化分析在现代工业制造中,精密注塑成型技术已被广泛应用。
这种技术可以高效、精准地制造各种形状的零部件,尤其是小型高精度零部件。
而模拟和优化成型过程则是保证注塑制造质量和生产效率的关键。
本文将介绍精密注塑成型过程模拟和优化的基本原理及方法,并讨论其实现时需要注意的问题。
一、精密注塑成型过程模拟模拟精密注塑成型过程是指在计算机上建立相应的模型,对成型过程进行数值模拟,从而预测零件的形状、质量和性能。
该模拟可以实现在物理试验之前对成型工艺的优化,提高生产效率和零部件质量。
1.工艺参数建模底模温度、熔体温度、模具温度、注射速度等是影响零件成型的主要工艺参数。
在模拟前需要对这些参数进行建模,以获得准确的数值计算结果。
建模方法通常包括基于经验公式和基于实验数据的统计方法。
这些方法可以将实验数据与成型过程相关因素的复杂交互作用关系联系起来,从而预测零件形状和质量。
2.材料属性建模在模拟精密注塑成型过程中,精确的材料属性是模拟结果准确性的关键。
所以需要对材料物理属性建模,包括熔化温度、热容、导热系数、热膨胀系数和硬度等关键参数。
这些参数是影响成型过程的主要因素,必须顾及到才能获得准确的模拟结果。
3.力学模型建模在模拟过程中,需要建立精密注塑成型过程的力学模型。
力学模型通常分为两类:基于有限体积法(FVM)的流体力学(CFD)模型和基于有限元法(FEM)的结构力学模型。
这些模型可以预测零件的形状和质量等关键参数,为注塑工艺优化提供参考。
4.成型过程数值模拟在完成上述工作后,可以对注塑成型过程进行数值模拟。
模拟可以实现在物理试验之前对成型工艺的优化,并预测成型过程中各个参数的趋势和偏差,以及零件的形状和质量,从而为实际生产提供指导意义。
二、精密注塑成型过程优化通过模拟精密注塑成型过程,可以对注塑工艺进行优化,以提高成型过程质量和生产效率。
1.注塑成型参数优化对注塑成型参数进行优化可以使生产过程效率高,并降低零件的质量问题。
聚合物加工中的数值方法

注塑模充填和保压阶段的数值方法摘要:注塑成型的充填过程是一个对流占优的能量传递过程。
其中采用有限差分法对注塑过程中充填阶段的温度场进行数值分析,建立基于非牛顿流体在非等温状态下广义Hele - Shaw流动的数学模型,来预测非牛顿流体在任意形状薄壁型腔内流动时的温度场,采用分步法将该能量守恒方程分解为一个对流方程和一个热传导方程,可分别选择不同的时间步长和求解方案独立进行求解,可以得到合理的模拟结果。
在保压过程中,基于粘性流体力学的基本理论,建立可压缩、非牛顿粘性流体在模具型腔中非等温流动的数学模型,选用了恰当的材料性质模型,确定合理的初始条件和边界条件,采用有限元/有限差分耦合解法求解数学模型实现对保压过程的模拟。
关键词:注射成型充填数值模拟温度场保压Numerical Method in Filling Stage andPacking Stage of Injection MoldingAbstract : Injection molding filling process is a convection dominant energy transfer process.Numerical analysis of temperature field during filling stage of injection molding is investigated by using FDM method here. The model is based on the generalized Hele-Shaw flows of Non-Newtionian fluid under nonisothermal condition. The temperature field of Non-Newtonian fluid within thin cavities of arbitrary shape can be predicted.The energy equation was solved by an operator-splitting method.First, the convective part of the problem was solved, and then the conduction term and source term were solved.In this way,particularly effective numerical schemes were used.In the packing stage, an at tempt is made to derive a mathematical model describing the packing behavior based on generalized Hele-Shaw flow for a purely viscous and compressible fluid in thin cavity under nonisothermal conditions.The material properties are described accurately as well.The finite-elementtechnique is employed to treat the pressure and temperature field in the stream-wise direction, how ever, an implicit finite- difference scheme is used to obtain temperature distribution in the gap wise direction.Keywords : injection molding ;filling stage; numerical simulation ; temperature field; packing stage ;注射成型是高分子材料加工成型的主要方式之一。
注塑成型过程中的黏弹性模型流动的模拟
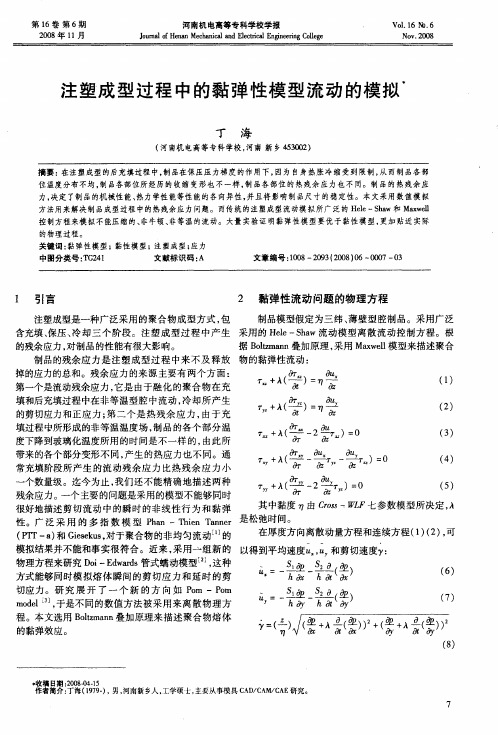
丁 ( 警 0 A 誓一 警 州誓- - 2 0 警
打
( 4 ) ( 5 )
二 : 模拟结果并不能和事实很符合。近来 , 采用一组新的 以得到平均速度:, 和剪切速度 物理方 程来研究 D i d a s管式蠕动模型 J这 种 o—E wr d , 塑 五 = 一 hO 一 h 旦 r 、 x O O t x 方式 能够同时模 拟 熔体 瞬 间 的剪 切应 力 和延 时 的 剪 切应 力 。研 究 展 开 了 一 个 新 的方 向 如 P m —Pm o o “ 一 一 ) 五: 粤一 ( , 百 一 m d lE] 于是不 同的数值 方 法被采 用 来离 散物 理 方 o e 3 程。本 文选 用 Bhm n oz an叠加原理来 描述 聚合 物熔 体
方法用来解决制 品成型过程中的热残余应力 问题 。而传统的注塑成型流动模拟所广 泛的 H l S a e e— hw和 Maw l x e l 控制方程来模拟不能压缩的、 非牛顿 、 非等温 的流动。大量实验证明黏弹性模型要优于黏性模型, 更加贴近 实际
的 物理 过 程 。
关键词 : 弹性模型;黏性模型;注塑成型; 黏 应力
( 0 Z) 2 U J
( 1 二J 2) -
鲁 温 表 : 和度 示
害( r+ ) = ) ( 砉害 券O T
2rou r r' d :Q Jr R
NO 2 8 V. OO
注塑成 型 过程 中的黏弹 性模型 流动 的模 拟
丁 海
( 河南机 电高等专科学校 , 河南 新 乡4 30 ) 5 02
摘要 : 在注塑成型的后充填过程中, 品在保压压力梯度的作用下, 制 因为自身热胀冷缩 受到限制, 从而制 品各部
位温度分布不均 , 品各部位所经历 的收缩 变形也不一样, 品各部位 的热残余 应力也不同。制 品的热残余应 制 制 力, 决定 了制品的机械性能、 热力学性能等性能的各 向异性, 并且将影响制品尺 寸的稳定性。本文采用数值模拟
考虑压力对黏度影响的注塑填充过程数值模拟
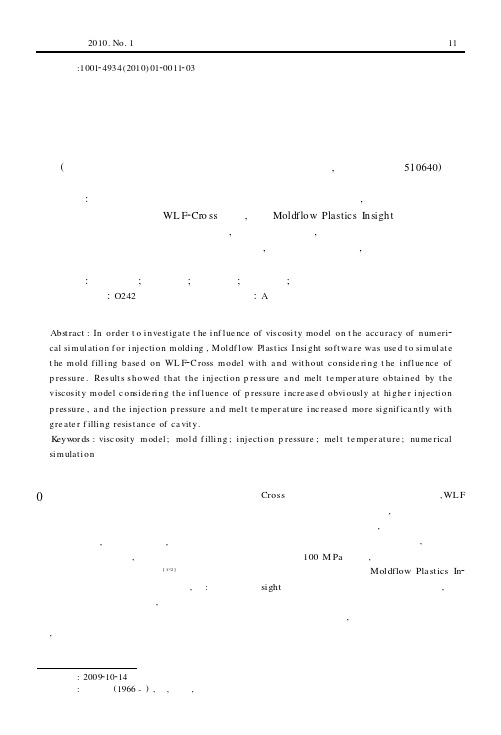
收稿日期22作者简介麻向军(66),男,博士,副教授。
文章编号:100124934(2010)0120011203考虑压力对黏度影响的注塑填充过程数值模拟麻向军(华南理工大学 聚合物新型成型装备国家工程研究中心,广东 广州 510640)摘 要:为了研究熔体黏度模型对注塑成型数值模拟精度的影响,采用不考虑压力和考虑压力对黏度影响的WL F 2Cro ss 模型,利用Moldflow Plastics Insight 软件对制品填充过程进行了数值模拟。
结果表明,注射压力较高时,采用考虑压力影响的黏度模型计算得到的注射压力和熔体温度显著增加,型腔填充阻力越大,注射压力和熔体温度增加越大。
关键词:黏度模型;填充过程;注射压力;熔体温度;数值模拟中图分类号:O242 文献标识码:AAbstract :In order t o i nvest igat e t he i nf l ue nce of vis cosi t y model on t he accuracy of num eri 2cal si m ul ati on f or i nj ecti on m oldi ng ,M ol df l ow Pl as t ics I nsi ght soft wa re was use d t o si m ul at e t he m ol d fill i ng base d on WL F 2C ross m odel wit h a nd wit hout cons ide ri ng t he i nfl ue nce of p res sure.Res ult s s howed t hat t he i nj ecti on p ress ure a nd melt t e mper at ure obtai ned by t he viscos it y m odel c ons i de ri ng t he i nf l uence of p res sure i ncre as e d obvi ousl y at hi ghe r i nj ecti on p res sure ,a nd t he i nj ect ion p ressure a nd mel t t e mper at ure i nc rease d more si gnif ica ntl y wi t h gre ate r f illi ng resis t ance of ca vit y.K eyw or ds :visc osit y m odel ;mol d f illi ng ;i nj ecti on p ressure ;mel t t e mper at ure ;nume ricalsi m ulat i on0 引言注塑成型过程的数值模拟对于提高模具设计质量和效率,减少修模次数,缩短新产品开发周期等具有重要作用,广泛用于优化制品设计和模具设计及注塑工艺参数[122]。
液态成型充型过程数值模拟仿真技术共26页

在铸件充型过程的数值模拟计算中,求解压力场是最
耗费时间的,实际工程应用中,计算时间有时会很长,满 足不了工艺分析人员的要求,因此研究如何提高压力方程 的求解速度就成了一个非常重要的问题。致力于铸件充型 过程数值模拟的研究人员,不断跟踪计算流体力学、数学 和计算机等相关学科的新发展,力图以最新的研究成果来 提高充型模拟的计算精度。研究者主要在压力场一速度场 的迭代方法上和稀疏矩阵方程组的求解方面进行研究探索, 并提出了许多提高计算速度的有效方法。
程序,进行模拟计算。
6. 数据处理和模拟计算结果的图形显示输出。
1.3铸件充型过程数值模拟的基本问题
铸件充型过程的数值热学、计算机图形学、计
算方法、偏微分方程的数学理论和铸造工艺理论等。铸件
充型过程的流场温度场模拟包括很多内容,如几何实体造
型、计算域的网格划分、流场中速度和压力的求解、充型
此外,区域分解法、并行计算法、多重网格法等也引起
了研究者的兴趣。区域分解法目前在理论上还没有完全成
熟,距离应用到实际数值计算还有一段距离。并行计算法
通过计算空间的分配来换取时间的缩短,但往往由于硬件 设备的昂贵而失去实用性。多重网格技术是提高计算求解 效率的一个有效方法。早期,Brandt等人在研究中对压力 项进行迭代求解时利用了多重网格法,后来尼(Ni)利用多 重网格技术求解了欧拉方程,近年来詹姆生等人在多重网 格法的研究方面做了很多工作。
由于计算速度场的真正困难在于压力场,因而研究者 们致力于寻找一种采用所谓的基本变量(即速度分量和压 力)的数值求解方法。这样的解法必须进行速度场一压力 场迭代,通过猜测值得到满意解.Patankar提出了SIMPLE 方法和SIMPLER方法,SIMPLE (Semi一Implicit Method for Pressure-Linked Equations)是求解压力连续方程的 半隐式方法,是比较全面的流场计算方法;计算出的速度 场不仅满足连续性方程的要求,也满足动量方程的要求; 其主要特点是压力场和速度场同时迭代。
注塑成形中气体反压技术的数值模拟
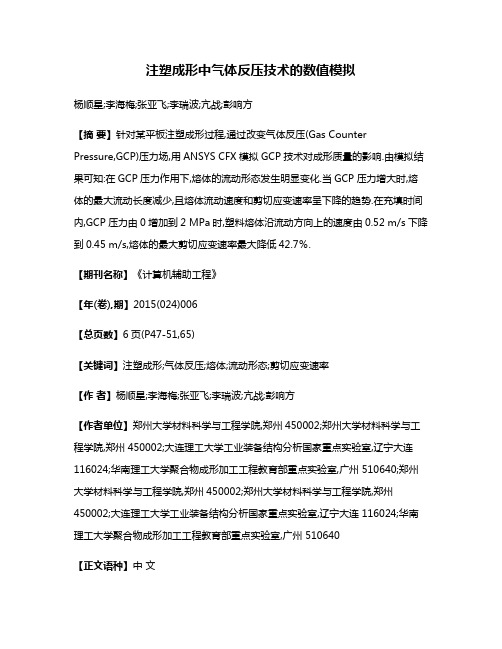
注塑成形中气体反压技术的数值模拟杨顺星;李海梅;张亚飞;李瑞波;亢战;彭响方【摘要】针对某平板注塑成形过程,通过改变气体反压(Gas Counter Pressure,GCP)压力场,用ANSYS CFX模拟GCP技术对成形质量的影响.由模拟结果可知:在GCP压力作用下,熔体的流动形态发生明显变化.当GCP压力增大时,熔体的最大流动长度减少,且熔体流动速度和剪切应变速率呈下降的趋势.在充填时间内,GCP压力由0增加到2 MPa时,塑料熔体沿流动方向上的速度由0.52 m/s下降到0.45 m/s,熔体的最大剪切应变速率最大降低42.7%.【期刊名称】《计算机辅助工程》【年(卷),期】2015(024)006【总页数】6页(P47-51,65)【关键词】注塑成形;气体反压;熔体;流动形态;剪切应变速率【作者】杨顺星;李海梅;张亚飞;李瑞波;亢战;彭响方【作者单位】郑州大学材料科学与工程学院,郑州450002;郑州大学材料科学与工程学院,郑州450002;大连理工大学工业装备结构分析国家重点实验室,辽宁大连116024;华南理工大学聚合物成形加工工程教育部重点实验室,广州 510640;郑州大学材料科学与工程学院,郑州450002;郑州大学材料科学与工程学院,郑州450002;大连理工大学工业装备结构分析国家重点实验室,辽宁大连 116024;华南理工大学聚合物成形加工工程教育部重点实验室,广州 510640【正文语种】中文【中图分类】TQ316.330 引言塑料具有质轻、加工易、精度高、成本低、成形自由度大、技术发展成熟等优点,所以应用日益广泛,但在石油资源紧张、原材料成本提高、环保要求等条件下,为提高塑料制品的附加值,除在塑料材料的改性技术上有所突破外,更需要在成形技术方面有所创新.气体反压(Gas Counter Pressure,GCP)技术[1-4]是近年来发展起来的一项新技术,其能够有效降低塑料熔体前沿的压力差,实现均匀充填,改善塑料制品的机械性能[1-2]和表面缺陷[3-4],减小翘曲变形[5]及提高制品成形质量[6]等.为提高超临界微孔发泡注射成形制品的表面质量,研发人员曾用变模温感应加热[2-3]、绝热模具层[7]、表面贴膜工艺[8-9]等方法,以拓展微孔注塑工艺的应用.在目前的工程实践中,GCP技术在超临界微孔发泡注射成形中的应用最为常见.在超临界微孔发泡注射成形时,型腔内充满一定带压气体抑制气泡生成的反压法能有效控制表面气泡流痕(见图1).当超临界流体(Super Critical Fluid,SCF)溶解于高分子熔体中,且熔体前沿受反压气体作用时,因GCP压力大小不同,可能出现3种情况:当没有GCP压力时,在熔体充填阶段发泡将自然发生而导致有银丝留痕缺陷产生于制品表面;如果GCP压力大于标准大气压但小于维持SCF所需的临界压力时,发泡将受到限制;当GCP压力大于临界压力时,熔体将在反压作用期间维持为单相泡核而无泡孔产生.[1-4]图1 GCP技术示意Fig.1 Schematic of GCP technology作为一种先进的设计手段,数值模拟技术在注塑成形加工领域应用日趋广泛.从开始仅能模拟熔体注塑充填[10],到集成化模型模拟充填、保压,再到冷却成形全过程[11],进而发展气体辅助注塑成形等双相流动的模拟[12]以及成形质量预测等.相对于注塑GCP技术的实验研究成果,反压技术的数值模拟迄今鲜有人研究.超临界微孔发泡注射成形涉及到泡孔成长的空气力学,与常规注射成形相比较复杂,为便于模拟,本文只考虑带反压的常规注塑成形工艺,用数值方法对GCP技术进行探索.利用有限元软件ANSYS CFX平台,通过二次开发,建立高分子材料的Cross-WLF七参数黏度模型,定义模拟所需要的材料,改变平板注塑制品成形过程的GCP压力,对成形充填过程进行三维数值模拟,讨论GCP压力对熔体充填流动的影响.1 模型与算法在注塑成形过程中,熔体充填阶段的数学模型满足质量守恒、动量守恒和能量守恒三大定律.熔体在充填过程中,流动前沿上受到GCP的作用,形成气-熔界面.根据工艺特点,对气-熔边界进行简化和假设:1)气体在熔体充填过程中假设为不可压缩流体;2)因为熔体黏度远大于气体黏度,假设气体黏度为0;3)气体的比热容远小于熔体,不计气体内部的能量交换;4)气体密度远小于塑料熔体,忽略其重力;5)气-熔界面两侧物质不发生能量交换.1.1 平板制件以平板注塑件为例,模拟注塑成形过程中GCP压力对塑料熔体流动的影响,制品的几何尺寸为4 mm×4 mm×1 mm,形状见图2a.浇口为侧浇口,尺寸为1mm×1 mm×1 mm.对几何模型用四面体网格单元离散,网格边长设定为0.1 mm,节点个数为7 846,单元总个数为30 246,见图2b.制品成形工艺参数见表1.图2 平板制品的尺寸及网格示意Fig.2 Schematic of size and mesh of plate product表1 注塑成形工艺参数Tab.1 Injection molding processing parameters参数值模具温度参数值模壁传热系数/(W/(m2·k))/℃ 60熔体温度25 000 GCP压力/MPa 0,1,2/℃ 230入口速率/(m/s)1在塑料熔体充填开始前,型腔内充满带压气体,然后改变GCP压力大小,采用数值方法分析塑料熔体流动前沿位置、充填时间、熔体流动速率和剪切应变速率等相关模拟结果,量化分析GCP压力对注塑成形中塑料熔体流动状态的影响.1.2 材料的黏度模型ANSYS CFX的材料库提供理想空气、水、铜、铝、钢铁和烟煤等材料参数,但没有聚合物材料.为研究聚合物材料的流动,通过软件接口添加.聚丙烯PP的Cross-WLF七参数黏度模型见式(1),材料属性用CEL语言定义完成.式中:n为非牛顿指数;为材料的玻璃化转变温度,=D2+D3P;D1,D2,D3为材料常数;τ*为剪切变稀行为开始时的剪应力;A1和为材料常数,A2=+D3P.选择Shell公司生产的牌号为XM 6700S的PP材料,式(1)中的材料参数值以及PP材料的模型参数分别见表2和3.表2 PP材料参数Tab.2 PP material parameters参数数值熔化温度/°C 135熔体密度/(kg/m3)775 2 830热传导系数/(W/m·℃)参数数值比热容/(J/kg·℃)0.19表3 PP材料的模型参数Tab.3 Model parameters of PP material七参数变量数值七参数变量数值n 0.209 8 D1/(Pa·s) 6.93 ×1011 τ*/Pa 30 354 D2/℃-10 A1 26.507 D3/(℃ /Pa)0 A~2/℃ - 221.551.3 边界条件选用流动区域内熔体-气体两相均一模型进行模拟,即熔体、气体有共同的速度场、压力场和温度场,而熔体的物理性质参数取决于两组分的变化.模拟注射成形充填过程的边界条件:1)入口为速度边界条件,熔体速度和温度已知,入口聚合物熔体组份等于1,空气为0;2)模壁处熔体速度为零,属无滑移边界条件,壁面接触处的传热系数取值为25 000 W/(m2·℃);3)出口处为压力边界条件,相对压力设置为0;4)熔体前沿仅考虑表面张力,忽略热交换;5)GCP压力通过型腔内空气压力变化表示,分别取0,1和2 MPa进行模拟,GCP压力为0相当于传统(常规)注塑成形.2 结果与讨论2.1 GCP压力对熔体前沿的影响在不同的GCP压力作用下,塑料制品熔体完成充填所需时间不同,同一时刻塑料熔体的充填体积分数也不同.为验证模拟结果的合理性,取GCP压力为0时(即传统注塑成形)PP熔体的充填体积分数随时间变化情况,见图3.图3 传统注塑成形中体积分数随充填时间的变化Fig.3 Change of volume fraction with filling time during conventional injection molding由图3可知:PP熔体在型腔中的充填体积分数随时间变化比较均匀;靠近浇口中心位置熔体的充填速度较快;靠近模具壁处,由于模具壁温度低,塑料熔体的温度接触模具壁面后迅速降低,熔体形成冷凝层,影响熔体的流动,充填较慢.改变GCP 压力为1和2 MPa,依次完成数值模拟,结果发现:当GCP压力为0时PP充填满整个型腔约0.3 s,GCP压力为1 MPa时充填时间为1.0 s,GCP压力为2 MPa 时充填时间为2.0 s.由此可知:GCP压力增大时,PP熔体充填满整个型腔所需时间也相应增加,表明反压气体会影响对塑料熔体在型腔中的流动.考虑GCP压力变化时,从模拟结果提取给定时刻PP熔体的流动前沿的位置和形状,可直观观察GCP压力对熔体流动的影响.不同GCP压力下给定时刻熔体的流动前沿见图4.由图4可知:当GCP压力增加时,熔体前沿面受的GCP压力增大,熔体流动需克服较大的压力,PP充满型腔所需的时间增加;当熔体前沿有1或2 MPa反压气体的压力作用时,熔体前沿形状发生变化,与传统注塑成形相比,曲面曲率变大,表明该截面处的速度梯度变小,利于熔体型腔的均匀充填.图4 指定时刻时不同GCP压力下的流动前沿位置Fig.4 Flow front position atgiven times under different GCP pressures流动方向截面处的SEM结果见图5.对比图3和5,发现ANSYS CFX模拟的塑料熔体充填过程与实验中熔体型腔中的流动前沿形状趋势一致,模拟结果合理.由图5b可知:当型腔有GCP压力后,熔体前沿类似抛物线形状的线条变得密集均匀,熔体前沿的曲率变小,与图4的模拟结果趋势一致.图5 不同成形工艺下熔体流动方向截面处的扫描电子显微镜观察结果Fig.5 Scanning electron microscope view results of cross section in melt flow direction under different molding processes2.2 GCP压力对熔体速度的影响为量化GCP压力对熔体速度的影响,选定浇口附近固定位置为参考点,提取模拟结果中指定位置处不同GCP压力下的熔体速度,见图6.在充填0.10 s时,GCP压力为0,1和2 MPa时的熔体速度分别为 0.52,0.48 和 0.45 m/s,最大降幅为 13.5%.此模拟结果与图5类似,即GCP压力增大时,熔体沿流动方向上的速度有减小趋势.为便于直观观察反压技术对充填的影响,通过气体辅助注塑工艺进行实验.图7a中,气体内部压力为3 MPa,外部反压气压为0,相当于常规的气体辅助注塑成形;图7b中,外部GCP压力为5 MPa,相当于2 MPa反压条件下的常规的气体辅助注塑成形.在给定的时刻,GCP压力为2 MPa(外部压力为5 MPa)时气体的流动长度(图7b)小于GCP压力为0的长度(图7a).实验结果间接证明GCP压力可降低熔体和气体的速度.由于GCP压力相当于增加熔体的保压压力,使得熔体的密度增大,在内气体积近似相等的条件下,内压力相同的气体穿透长度明显减小.图6 不同GCP压力下熔体沿流动方向的速度曲线Fig.6 Melt velocity curves along flow direction under different GCP pressures图7 不同GCP压力下充填速度的实验结果Fig.7 Experimental results of fillingvelocity under different GCPpressures2.3 GCP压力对剪切应变速率的影响剪切应变速率对熔体取向、熔体破裂和残余应力等影响显著,GCP压力对剪切应变速率的影响可作为评价成形工艺参数是否合理及GCP技术优劣的指标之一.浇口附近位置处不同GCP压力下纤维增强塑料试样中纤维取向的测量与模拟结果见图8.由此可知:在GCP压力作用下,近浇口处厚度方向的纤维取向小于无GCP压力作用下的传统注塑制品,试样性能更均匀;在GCP压力作用下,试样厚度方向的纤维取向差异更小,取向张量Azy在皮层与芯层的最大差值为0.12;无反压时,Azy在皮层与芯层的最大差值为0.21.目前无法模拟反压作用下的纤维取向.传统注塑的纤维模拟取向结果与实验结果趋势一致,但忽略材料弹性的黏性本构方程使得模拟结果偏大.图8 不同GCP压力下近浇口位置处纤维取向的测量和模拟结果Fig.8 Measurement and simulation results of fiber orientation near gate under different GCP pressures浇口附近熔体的剪切应变速率随时间的变化曲线见图9.由此可知:随着时间的增加,熔体的剪切应变速率先升高后下降,表明熔体流动前沿到达选定的参考点位置时该处熔体的剪切应变速率可认为是熔体前沿所受的最大剪切应变速率;当GCP压力为2 MPa时,熔体剪切应变速率变化相对平缓,便于成形过程中所制备产品性能的均匀性,与图8中测量的纤维取向结果一致.GCP压力为0,1和2 MPa时熔体的最大剪切应变速率分别为6.1×106,5.8×106和2.6 ×106s-1.与传统注塑成形相比,GCP压力为2 MPa时最大剪切应变速率下降42.7%,可有效改善成形加工中的分子(纤维)的取向,使垂直于流动方向的制品性能得到提高.图9 不同GCP压力下浇口附近熔体剪切应变速率-时间曲线Fig.9 Curves of shear rate variation against time of melt near gate under different counterpressures3 结束语初步实现GCP技术的数值模拟,以平板制品为例,研究GCP压力对塑料熔体充填过程中流动状态的影响.从模拟结果看:GCP压力对熔体的流动形态有明显影响;GCP压力不同,熔体的流动速度、最大剪切应变速率也发生变化,并且随着GCP压力的提高熔体的流动速度、剪切应变速率都呈下降的趋势.模拟结果与实验的趋势吻合.由于反压工艺使用方式多样,本文没有考虑GCP压力的保持时间且简化较多,为更精确模拟GCP技术,还需结合现场参数,进一步完善数学模型与模拟方法.参考文献:【相关文献】[1] CHEN S C,LIAO W H,CHIEN R D,et al.Structure and mechanical properties of polystyrene foams made through microcellular injection molding via control mechanisms of gas counter pressure and mold temperature[J].Int Commun Heat& Mass Trans,2012,39:1125-1131.[2] CHEN S C,HSU P S,HWANG S S.Effect of gas counter pressure and mold temperature variation on surface quality and morphology of microcellular polystyrene foams[J].J Appl Poly Sci,2013,127(6):4769-4776.[3] LEE J,TURNG L S,DOUGHERTY E,et al.A novel method for improving the surface quality of microcellular injection molded parts[J].Polymer,2011,52(6):1436-1446. [4] CHEN S C,HSU P S,LIN Y W.Establishment of gas counter pressure technology and its application to improve the surface quality of microcellular injection molded parts [J].Int Polym Proc,2011,26(3):275-282.[5] YOO Y E,WOO S W,KIM S K.Injection molding without prior drying process by gas counter pressure[J].Poly Eng Sci,2012,52(11):2417-2433.[6] BLEDZKI A K,KIRSCHLING H,STEINBICHLER G,et al.Microcellular moulding with gas counter pressure using physical blowing agent[M].Zurich:Trans Tech Publication,2005:257-260[7] CHEN H L,CHIEN R D,CHEN S ing thermally insulated polymer film for mold temperature control to improve surface quality of microcellular injection molded parts [J].Int Commun & Mass Trans,2008,35(8):991-994.[8] MICHAELI W,OPFERMANN D.Increasing the feasible bonding strength in micro assembly injection molding using surface modifications[J].SPE ANTEC Technol Papers,2006,64:1290-1294.[9] BLEDZKI A K,KIRSCHLING H,STEINBICHLER G,et al.Polycarbonate microfoams with a smooth surface and higher notched impact strength[J].J Cell Plascitcs,2004,40(6):489-496.[10] HAAGH G A A V,van de VOSSE F N.Simulation of three dimensional polymer mould filling processes using a pseudo-concentration method[J].Int J Numer Methods Fluids,1998,28(9):1355-1369.[11] CHIANG H H,HIEBER C A,WANG K K.A unified simulation of the filling and postfilling stages in injection molding:Part I:Formulation[J].Polymer Eng & Sci,2004,31(2):116-124.[12] CHEN W,ZHOU X H,HAN X puting gas/melt free interface of gas-assisted injection molding[J].Int J Adv Manufacturing Technol,2011,52(5-8):521-529.。
某水箱盖注塑成型数值模拟

21 0 2年
第 2 7卷
第 4期
于曝气 , 在溶解氧达到要求 的情况 下 , 以相应 减少转碟 的运行 可 时间 , 节约大量的电能 。一套氧化沟系统共有 1 组转碟 , 2 加装潜 水搅拌器后 , 能够停运 2组 A型转碟 和 1 B型转碟 , 组 停运转碟
l 5次试验 。数据整理后 , 与注塑件设计 尺寸进行对 比 , 分别作 出 注塑件端 面上的 Z向最大变形量 、 最小变形量 , 关于 中心对称 的 z向变形量半 区间平均值 以及用 z向最大变形 量与最小变形量 差值表示 的平 面度 的变化曲线线图 ,综合分析工 艺参数对注 塑 件翘 曲变形量 的影响 。 图2 是保 压压 力对 z向变形量 的影响 。可 以看 出 , z向 , 对 变形量 区间先 是缓 慢缩 小 , 到一定数值后 , 最大 变形 量与最小变 形量 向两个极端分离 , 总的翘 曲量变大 。
设置不 同的注射 时间 , 其他用得 出的最优工艺 参数 , 此组 将 参数放人 Mo f w中模拟 , ll do 在不同保压压力下的翘曲量见表 2 。
吕
表 2 不同保压压 力下的翘 曲量 注射时间() s
1 2
3
4
嘲l
翘 曲量( m m )
05 55 .5 04 7 3 .9
1 7 l 8 1 9 2 0 21
4 4 4 4 5 5 5 5
5
5 0 8 0 1O 1 10 4 2 0 5 0 8 0 11 0
1 0 4
1 6 4 7 1 0 1 6 4 7 1 0
基于分步法的三维注塑充填温度场数值模拟
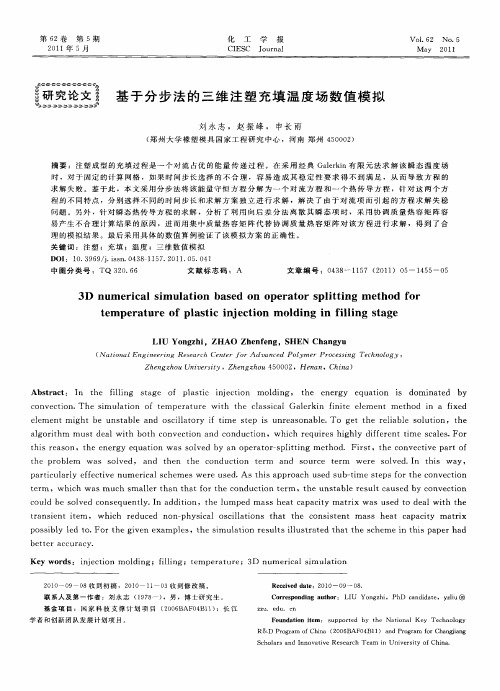
e e n i ht b u t b e nd s il t r f tme t p s nr a o b e To e he e ibl o uton,t e l me tm g e ns a l a o cla o y i i s e i u e s na l . g t t r la e s l i h
c nv c i n o e to .The s m ul ton i a i of t m pe a ur w ih he l s ia G a e ki fn t e e e t e rt e t t ca sc l l r n i ie lm n m e ho i a i e t d n fx d
a go ihm u t d a ih b h c ve to nd c duc i n,w hih r qu r s hi hl if r n i e s a e . r l rt m s e lw t ot on c i n a on to c e ie g y d fe e t tm c l s Fo t sr a on, t ne g q a i n w a ol e y a pe a o — p itn e ho . Fis , t on c i r f hi e s he e r y e u to s s v d b n o r t r s lt i g m t d r t he c ve tvepa to t p ob e wa s v d, a t e t e c nd to t r he r l m s ol e nd h n h o uc i n e m a s r e e m w e e s l d. n hi w a nd ou c t r r o ve I t s y,
3 nu e i a i u a i n b s d o pe a o plt i g m e ho o D m r c lsm l to a e n o r t r s itn t dfr
注塑成型过程仿真模拟

注塑成型过程仿真模拟注塑成型过程仿真模拟注塑成型是一种常用的塑料加工方法,通过在模具中加热和压力的作用下,将熔融的塑料材料注入模具中,形成所需的产品形状。
然而,在实际生产中,由于材料和工艺的复杂性,注塑成型过程中常常会出现一些问题,如产品缺陷、模具磨损等。
为了解决这些问题,提高生产效率和产品质量,注塑成型过程仿真模拟应运而生。
注塑成型过程仿真模拟是利用计算机技术对注塑成型过程进行数字化模拟和分析的方法。
通过建立注塑成型的数学模型,并运用计算流体力学和有限元分析等方法,可以模拟和预测材料的流动、温度分布、变形等情况,从而优化模具设计和工艺参数,提高生产效率和产品质量。
注塑成型过程仿真模拟的基本流程包括几何建模、网格划分、物理参数设定、边界条件设定、数值计算和结果分析等步骤。
首先,根据实际产品的几何形状,利用计算机辅助设计软件进行三维几何建模。
然后,将几何模型转化为计算所需的网格模型,即将几何体划分为无数小的单元格,以便进行数值计算。
接下来,根据材料的物理参数,设定模拟过程中的温度、压力、速度等参数,并确定边界条件,如模具表面的温度和压力。
然后,利用数值方法对模型进行计算,得出模拟结果。
最后,对模拟结果进行分析,评估模具设计和工艺参数的合理性,并根据需求进行优化。
注塑成型过程仿真模拟具有多方面的优势。
首先,它可以提前发现和解决注塑成型过程中可能出现的问题,如翘曲、热应力、气泡等缺陷,从而避免因产品缺陷导致的生产损失。
其次,它可以优化模具设计和工艺参数,提高生产效率和产品质量。
再次,它可以减少试模次数,节省原材料和时间成本。
此外,注塑成型过程仿真模拟还可以提供详细的数值结果和可视化的模拟图像,为工程技术人员提供参考和决策依据。
总之,注塑成型过程仿真模拟是一种有效的工具,可以帮助企业解决注塑成型过程中的问题,提高生产效率和产品质量。
随着计算机技术的不断发展和成熟,注塑成型过程仿真模拟将会得到更广泛的应用和推广。
《汽车三角窗密封件注塑成型数值模拟及模具结构改进》范文

《汽车三角窗密封件注塑成型数值模拟及模具结构改进》篇一一、引言随着汽车制造业的不断发展,对汽车零部件的质量要求也日益提高。
汽车三角窗密封件作为汽车的重要零部件之一,其质量和性能对汽车的整体性能具有重要影响。
注塑成型作为三角窗密封件的主要制造方法,其成型过程和模具结构对产品的质量有着决定性的影响。
因此,本文通过数值模拟技术对汽车三角窗密封件的注塑成型过程进行模拟,分析其成型过程中的流动行为和温度分布,同时对模具结构进行改进,以提高产品的质量和生产效率。
二、注塑成型数值模拟1. 模型建立首先,根据汽车三角窗密封件的几何形状和尺寸,建立注塑成型的三维模型。
该模型应包括注塑机、模具、材料等关键部件,并确保模型能够真实反映实际生产过程中的物理和化学特性。
2. 数值模拟方法采用先进的有限元法或有限体积法等数值模拟方法,对注塑成型过程进行模拟。
重点分析材料的流动行为、温度分布、压力变化等关键参数,以及这些参数对产品质量的影响。
3. 模拟结果分析通过对模拟结果的分析,可以得出以下结论:在注塑过程中,材料的流动行为和温度分布对产品的质量和性能具有重要影响。
在特定阶段,如充模阶段和保压阶段,应严格控制材料的流动速度、温度和压力等参数,以确保产品质量的稳定性和可靠性。
三、模具结构改进1. 模具结构分析针对现有模具结构存在的问题,如注射口设计不合理、流道布局不科学等,进行详细的分析和评估。
这些问题的存在可能导致材料流动不均匀、温度分布不均等,进而影响产品的质量和性能。
2. 模具结构改进方案根据分析结果,提出以下模具结构改进方案:(1)优化注射口设计:调整注射口的位置和大小,使材料能够更均匀地进入模具型腔。
(2)改进流道布局:优化流道的数量、长度和直径等参数,使材料在流道中能够更顺畅地流动。
(3)增加冷却系统:在模具中增加冷却系统,以控制模具的温度分布,从而提高产品的质量和生产效率。
四、实验验证与结果分析1. 实验方法与步骤为验证数值模拟结果和模具结构改进方案的可行性,进行实际生产实验。
注塑成型冷却过程的数值模拟
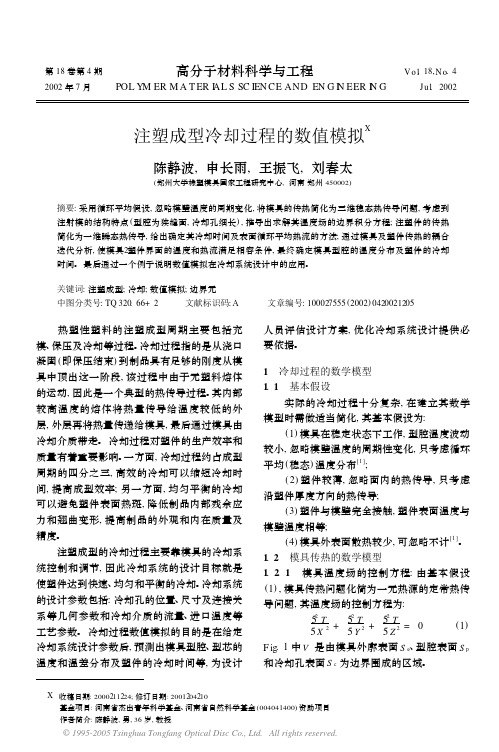
2. 1. 2 边界积分方程的离散: 一般情况下, 不 可能用解析法来求解积分方程 ( 10 ) 、( 11 ) 和 ( 12) , 而必须采用近似的数值解法。 为了求出边
F ig. 2 Nota tion for an in jection m old surface
界积分方程的数值解, 可将模具型腔表面离散 成三角形单元, 将冷却孔沿轴线离散成一维线 单元, 代入相应的边界条件, 则可得到边界积分 ( 11) 和 ( 12) 的离散形式, 单元上的积 方程 ( 10) 、 分可用解析法 ( 奇异积分) 和高斯求积法 ( 非奇 ( 11 ) 异 积分) 计算[ 4 ] , 最终边界积分方程 ( 10 ) 、 和 ( 12) 可化为一线性代数方程组:
第 4 期
陈静波等; 注塑成型冷却过程的数值模拟
23
数降低一维, 只需在边界上进行离散化, 而不像 有限元法或有限差分法需将整个求解区域离散 化, 数据难备工作量和求解计算量较小。 此外, 由于边界元法引入微分方程的基本解, 具有解 析和离散相结合的特点, 因而具有较高的求解 精度。 注射模冷却分析关心的是模具型腔表面 ( 即边界) 的温度分布, 因此利用边界元法求解 注射模冷却问题具有其它方法不可比拟的优越 性。 2. 1. 1 边界积分方程: 由 G reen 积分第二恒等 式可导出 L ap lace 方程 ( 1) 的边界积分方程
人员评估设计方案, 优化冷却系统设计提供必 要依据。
1 冷却过程的数学模型 1. 1 基本假设
实际的冷却过程十分复杂, 在建立其数学 模型时需做适当简化, 其基本假设为: ( 1) 模具在稳定状态下工作, 型腔温度波动 较小, 忽略模壁温度的周期性变化, 只考虑循环 平均 ( 稳态) 温度分布[ 1 ]; ( 2 ) 塑件较薄, 忽略面内的热传导, 只考虑 沿塑件厚度方向的热传导; ( 3) 塑件与模壁完全接触, 塑件表面温度与 模壁温度相等; ( 4) 模具外表面散热较少, 可忽略不计 [ 1 ]。 1. 2 模具传热的数学模型
塑料成型数值模拟方法简介
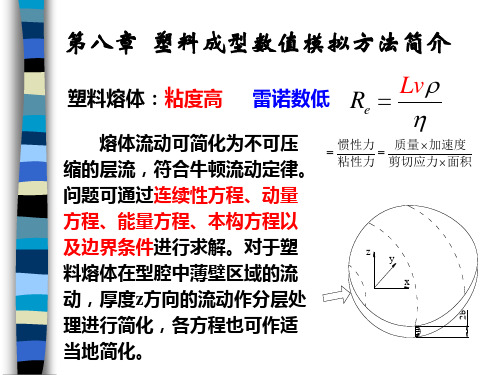
对 每一个节点的控制体积,根据质量平衡 ( 连续性 ) 方程、动量平衡方程和能量平衡方程, 以及边界条件和初始状态,可以计算得到熔体 充满型腔过程中任意时刻任意节点的温度、压 力、粘度等各场量的分布。
⑤ ④
⑦
③⑥
⑧
⑨
② ①
流动路径与单元组合
A 路径:1-2-3-4-5 B 路径:1-2-6-7-8-9 1与2为圆形管单元,3与6是圆板单元,4与7属 于圆环板单元,5、8和9属于平板单元。
三、三维流动分析
三维流动分析是对熔体在三维结构上的流动进行 模拟分析,可以在二维流动分析的基础上进行。分析 时,先将塑件的三维结构展平,并划分流动路径和单 元;然后,利用二维分析方法对型腔充填过程进行流 动分析。该方法计算量小、方法简单,但完全依赖于 设计人员的经验,且实际使用不方便。
(,
T
)
1
0 T
c(0
*
)1n
连续性方程简化
流动率
S b z2 dz
0
熔体流量
Q x
b
u dz
b
型腔宽度
型腔形状系数 x 2 x( W)
动量方程简化
圆盘型腔 长板型腔
压力梯度 p Q x 2 S
剪切速率
粘性热
z
2
熔体流速
b
u z dz
能量方程简化
能量平衡方程
有限元与控制体积法结合的方法应用于分析型腔 内熔体的流动过程,可以克服简化二维分析的缺点, 对设计人员的经验依赖甚少;因此,已成为分析熔体 流动过程有效手段。目前,实际模拟分析中将三维流 动问题分解为平面流动的二维问题和壁厚方向的一维 问题,采用有限元和有限差分耦合方法进行求解计算。
注塑件流动平衡的数值模拟分析
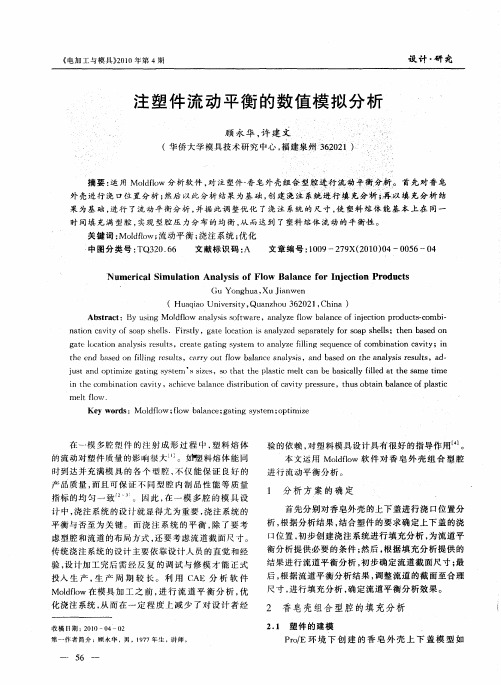
动的平 衡性 。
。
器嚣 筠
图 9
熔 接 痕 与气 穴
3 香 皂 外 壳组 合 型腔 的流 道 平 衡 分 析
3 1 初始 流道 平衡 分析 .
由香 皂 外 壳组 合 型 腔 的填 充 分 析可 知 , 填 充 其
明 显 不 平 衡 。 为 了 获 取 平 衡 的 浇 注 系 统 , 要 以 之 需 前 的 分 析 为 基 础 进 行 流道 平 衡 分 析 。 考 虑 到 下 盖 的
Modl 在模 具加 工 之 前 , 行 流 道 平 衡 分 析 , lf w o 进 优 化浇 注系统 , 从而 在 一定 程 度 上 减 少 了对 设 计 者经
J F期 : 0 0—0 { 史稿 t 21 4—0 2 第一 作 者 简 介 : 永 华 ,男 ,1 7 顾 9 7年 生 , 师 。 讲
一
根据 实 际 情 况 , 照 流道 平 衡分 析 结 果 对 流道 按 以及 浇 口的尺 寸进 行 调 整 , 通往 上 盖 的浇 口尺 寸为
5 8 一
设 计 ・ 究 研
长 ×宽 ×深 =2mm x3Ii X2mm, 流道 直径 为 /T l/ 分 68 mm; 往 下 盖 的 浇 口尺 寸 为 长 X宽 ×深 =2 . 通 mmX1 5mm ×0 5mi, 流道 直 径 为 2 4II , . . n 分 . II主 TT 流道 尺寸 不 变 ( 1 ) 图 4 。在 此 浇 注 系统 下 , 合 型 腔 组 的填 充分 析 结果 见 图 1 ~图 1 。 5 7
注塑成型充填过程数值模拟的隐式算法
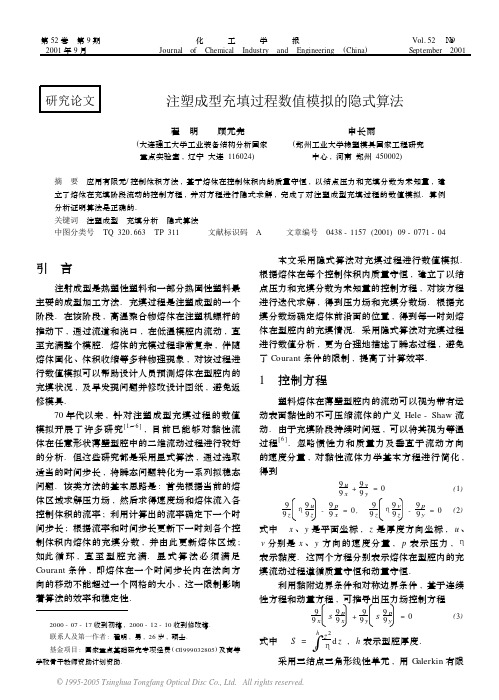
第52卷 第9期 化 工 学 报 Vol.52 №9 2001年9月 Journal of Chemical Industry and Engineering (China) September 2001研究论文 注塑成型充填过程数值模拟的隐式算法 翟 明 顾元宪 申长雨 (大连理工大学工业装备结构分析国家 (郑州工业大学橡塑模具国家工程研究 重点实验室,辽宁大连116024) 中心,河南郑州450002) 摘 要 应用有限元/控制体积方法,基于熔体在控制体积内的质量守恒,以结点压力和充填分数为未知量,建立了熔体在充填阶段流动的控制方程,并对方程进行隐式求解,完成了对注塑成型充填过程的数值模拟.算例分析证明算法是正确的.关键词 注塑成型 充填分析 隐式算法中图分类号 TQ320.663 TP311 文献标识码 A 文章编号 0438-1157(2001)09-0771-04引 言注射成型是热塑性塑料和一部分热固性塑料最主要的成型加工方法.充填过程是注塑成型的一个阶段.在该阶段,高温聚合物熔体在注塑机螺杆的推动下,通过流道和浇口,在低温模腔内流动,直至充满整个模腔.熔体的充模过程非常复杂,伴随熔体固化、体积收缩等多种物理现象,对该过程进行数值模拟可以帮助设计人员预测熔体在型腔内的充填状况,及早发现问题并修改设计图纸,避免返修模具.70年代以来,针对注塑成型充填过程的数值模拟开展了许多研究[1~6],目前已能够对黏性流体在任意形状薄壁型腔中的二维流动过程进行较好的分析.但这些研究都是采用显式算法,通过选取适当的时间步长,将瞬态问题转化为一系列拟稳态问题.该类方法的基本思路是:首先根据当前的熔体区域求解压力场,然后求得速度场和熔体流入各控制体积的流率;利用计算出的流率确定下一个时间步长;根据流率和时间步长更新下一时刻各个控制体积内熔体的充填分数,并由此更新熔体区域;如此循环,直至型腔充满.显式算法必须满足Courant条件,即熔体在一个时间步长内在法向方向的移动不能超过一个网格的大小,这一限制影响着算法的效率和稳定性.2000-07-17收到初稿,2000-12-10收到修改稿.联系人及第一作者:翟明,男,26岁,硕士.基金项目:国家重点基础研究专项经费(G1999032805)及高等学校骨干教师资助计划资助.本文采用隐式算法对充填过程进行数值模拟.根据熔体在每个控制体积内质量守恒,建立了以结点压力和充填分数为未知量的控制方程,对该方程进行迭代求解,得到压力场和充填分数场.根据充填分数场确定熔体前沿面的位置,得到每一时刻熔体在型腔内的充填情况.采用隐式算法对充填过程进行数值分析,更为合理地描述了瞬态过程,避免了Courant条件的限制,提高了计算效率.1 控制方程塑料熔体在薄壁型腔内的流动可以视为带有运动表面黏性的不可压缩流体的广义Hele-Shaw流动.由于充填阶段持续时间短,可以将其视为等温过程[6].忽略惯性力和质量力及垂直于流动方向的速度分量,对黏性流体力学基本方程进行简化,得到9u9x+9v9y=0(1) 99zη9u9z-9p9x=0,99zη9v9z-9p9y=0(2)式中 x、y是平面坐标,z是厚度方向坐标,u、v分别是x、y方向的速度分量,p表示压力,η表示黏度.这两个方程分别表示熔体在型腔内的充填流动过程遵循质量守恒和动量守恒.利用黏附边界条件和对称边界条件,基于连续性方程和动量方程,可推导出压力场控制方程99x S9p9x+99y S9p9y=0(3)式中 S=∫h0z2ηd z,h表示型腔厚度.采用三结点三角形线性单元,用G alerkin有限元方法对压力场控制方程进行离散,控制方程的余量为R (p )=(¤・¤S p )(4)根据G alerkin 法,有∫AN i R (p )d A =∫AN i (¤・¤S p )d A =0(5)式中 A 为单元面积,N i 为单元形函数.对上式进行进一步推导,有∑lS (l )∑3m =1D(l )imp N ′=∑lq (l )i (i =1,2,3)(6)式中 l 表示单元,N ′是单元l 的第m (m =1,2,3)个结点,D (l )im 是结点压力对净流率的影响系数,q (l )i为从单元l 流入单元l 的第i 个结点的控制体积中的体积流率.所谓结点的控制体积,即是将三角形单元的中心与3个边中点相连,把三角形单元分为3个子区域,与1个结点相连的所有子区域即构成该结点的控制体积[5],如图1所示.Fig.1 Schematic diagram of control volume由于在充填阶段不考虑聚合物熔体的可压缩性,根据质量守恒,对任一结点N 有V N 9F N /9t =Q N(7)式中 V N 是结点N 的控制体积,F N 是结点N 的控制体积中熔体已充填的部分占该控制体积的比例,Q N 是流入结点N 的控制体积的净体积流率.如果F i =1,该结点已被熔体充满;如果0<F i <1,该结点为前沿点,正在被熔体充填;如果F i =0,该结点为空结点,还未被熔体充填.根据式(6)、式(7)有V N 9F N /9t =Q N =∑kq (k )i=∑kS (k )∑3m =1D(k )imp N ′(8)式中 k 为包含结点N 的所有单元.对时间导数进行差分,有V N F mN=V N F m -1N +Δt∑kS (k )∑3m =1D (k )imp N ′(9)式中 上角标m 、m -1分别表示当前时刻和上一时刻.对各个结点写出上式,可以得到关于压力场p 和结点充填分数场F 的非线性方程组,该方程组用矩阵形式表示为Δt Ap =F m -1-F m +Δt B(10)式中 B 是列向量,包含了边界条件的贡献.对于充填过程,除了满足流率边界条件(浇口处流率给定)及无渗透边界条件外,对任一结点i ,如果F i <1,该结点为前沿点,其压力p i =0.此外,结点的压力和充填分数还应满足p i ≥0; 0≤F i ≤1(11)基于上述条件,对方程(10)进行求解,便可得到压力场和充填分数场.在充填阶段,熔体剪切速率较高,幂律模型可以较好描述此时熔体的剪切变稀行为[6],而且幂律模型比较简单,因此本文采用幂律模型表征熔体的黏度,即η=m γn -1exp (T a /T )(12)式中 T 表示温度,m 、T a 是常数,n 是幂律指数,γ表示剪切速率.γ可进一步表示为γ=(9u/9x )2+(9v/9y )2(13)2 隐式算法对充填过程的数值模拟最终归结为求解方程组(10).用隐式算法求解该方程组的迭代步骤如下.①首先将方程(10)改写为Δt ・(A +D )P =F m -F m +1+Δt B(14)式中 D 是由矩阵A 的对角线上的元素构成的对角阵,A =A -D .②在第n 次迭代开始,对任一点i ,如果F (n )i <1,则赋予对应的对角阵中的元素D i ,i 一非常大的值,如1016.③求解方程Δt ・(A +D )p (n )=F m -F (n )+Δt B(15)可得到第n 次迭代结点压力场p (n ).方程(15)中,上角标(n )表示第n 次迭代.④更新充填分数场F(n +1)=F m-Δt ・Ap (n )+Δt B (16) ⑤第2步到第4步反复迭代,直至收敛.收敛准则为‖F (n +1)-F (n )‖≤10-6(17)式中‖・‖表示向量的范数.这样,完成了一个时间步的计算.以上几步不・277・ 化 工 学 报 2001年9月 停循环,直至型腔充满,便完成了对充填过程的数值分析.用方程(16)更新体积分数时,计算出的体积分数可能不属于[0,1],这时所得的结果并不满足式(11),因此,需对体积分数进行修正,这是隐式算法的一个关键步骤.本文采用下式对计算出的体积分数进行修正F (n )i=max [0,min (1,F (n )i )](18)3 算 例本文给出两个算例,验证充填过程数值模拟隐式算法的正确性.算例1 矩形平板.对该平板,所选用的实验模具结构如图2所示,其型腔厚度为2.54mm.在充模时,熔体首先充满存料池,然后通过线浇口注入型腔.利用隐式算法对该平板的充模过程进行分析,并通过与实验结果[7]的对比来验证算法的正确性.Fig.2 Schematic diagram of experimental mold1,2,3—positions of pressure transducers注射时所采用的工艺参数为:注射机的注射流率Q =10.7cm 3・s -1,熔体温度T =200℃,模壁温度T w =37℃.塑料材料选用聚苯乙烯,密度ρ=940kg ・m -3,其幂律模型中有关参数为m =0.027Pa ・s n ,n =0.36,T a =6000K.利用上述参数,对熔体在型腔内的充填过程进行模拟,图3将模拟结果与实验结果进行了对比.可以看出,数值计算结果与实验结果基本上相吻合,说明所采用Fig.3 Comparison between predicted andexperimental pressure trace●Pred.1;■Pred.2;▲Pred.3———Exp.1;---Exp.2;——Exp.3的隐式算法是正确的.算例2 L 形平板.该平板的结构如图4所示.Smith 等人证明当浇口位于A 点(0.6005m ,0.3775m ),熔体同时充满型腔末端[8].对该平板注射时,采用的注射流率为10-4m 3・s -1,其他的与工艺及材料有关的参数同算例1.对该平板划分658个三角形单元,时间步长取为1.2s ,用隐式算法对该平板的充填过程进行分析.图5(a )、图5(b )分别是t =7.2s 和10.8s 时,型腔内熔体的充填状况.可以看出,当浇口位于A 处时,熔体基本上同时充满型腔末端,与Smith 等人的结论一致,从而说明所采用的隐式算法是正确的.同时由于所采用的时间步长较大,已不满足Courant条Fig.4 Schematic diagram of L 2plateFig.5 Schematic diagram of filling process・377・ 第52卷第9期 翟明等:注塑成型充填过程数值模拟的隐式算法 件,因此该算例也验证了隐式算法的稳定性不受Courant 条件限制的优点.分别用显式算法和隐式算法(取不同的时间步长),对该平板的充填过程进行数值分析,所耗用的CPU 时间如表1所示.可以看出,利用隐式算法,采用适当的时间步长,可以明显减少耗用的CPU 时间,提高计算效率.T able 1 Comparison of eff iciencyExplicitalgorithm Implicit algorithmΔt =0.28sΔt =0.56sΔt =1.12sCPU time72s49s34s33s4 结 论本文基于质量守恒,建立了注塑成型充填阶段熔体流动的控制方程,并用隐式算法对该方程进行了求解,实现了对充填过程的数值分析.隐式算法避免了Courant 条件的限制,提高了算法的效率和稳定性.最后,通过两个算例验证了该算法的正确性.R eferences1K amal M R ,K enig S.Poly m.Eng.Sci .,1972,12(2):295—3082Tadmor Z ,Broyer E ,Gufinger C.Poly m.Eng.Sci .,1974,14(4):660—6653Lord H A ,Williams G.Poly m.Eng.Sci .,1975,15(5):569—5824Hieber C A ,Shen S F.J.Non -New tonian Fl ui d Mechanics ,1980,7(1):1—325Wang V W ,Hieber C A ,Wang K K.In :AN TEC ’86,SPE conference.N Y:Society of Plastics Engineers ,1986.97—1026Isayev A I.Injection and Compression Molding Fundamentals.N Y:Marcel Dekker ,19877Chiang H H.Simulation and Verification of Filling and Post -Filling Stages of the Injction Molding Process :[dissertation ].N Y:Cornell University ,19898Smith D E.Optimal Design and Analysis for Polymer Extrusion and Molding :[dissertation ].Illinois :University of Illinois at Urbana 2Champaign ,1996IMPL ICIT AL G ORITHM FOR NUMERICAL SIMU LATIONOF INJECTION MOLD FILL ING PROCESSZHAI Ming and GU Yuanxian SHEN Changyu (S tate Key L aboratory of S t ructural A nalysis f or (N ational Engineering Research Center of Polymer Indust rial Equipment ,Dalian U niversity of and R ubber Mold &Die ,Zhengz hou U niversity Technology ,Dalian 116024,L iaoning ,China ) of Technology ,Zhengz hou 450002,Henan ,China )Abstract A physically accurate and computationally effective implicit algorithm for injection mold processsimulations is presented.The governing equations involving the pressure field and fill factor which tracks the location of the front surface are developed in terms of mass conservation for each control volume.The transient equations are solved in an iterative manner for both pressure field and fill factor for tracking the progression of the resin front in the mold cavity.The present formulations accurately account for and capture the physical transient nature of the mold 2filling process while maintaining improved numerical and computational attributes.The selection of time steps is based on accuracy considerations and resolution of flow front locations ,which is free from the restrictions that exist in the traditional explicit finite 2element 2control volume based formulations.The time increments of the traditional explicit methodology are restricted so that no more than one complete control volume region is updated and filled at each time increment.In certain cases ,more than one control volume may be simultaneously filled.The present methodology does not have such a restriction and computes the position of the flow front at each of the selected discrete time intervals.The com puted position of the flow front at the end of a certain time interval is independent of the time step size used to reach that time interval.In the end ,the methodology is used successfully in two examples.K eyw ords injection molding ,filling simulation ,implicit algorithmR eceived d ate :2000-07-17.Corresponding author :ZHAI Ming.・477・ 化 工 学 报 2001年9月 。
- 1、下载文档前请自行甄别文档内容的完整性,平台不提供额外的编辑、内容补充、找答案等附加服务。
- 2、"仅部分预览"的文档,不可在线预览部分如存在完整性等问题,可反馈申请退款(可完整预览的文档不适用该条件!)。
- 3、如文档侵犯您的权益,请联系客服反馈,我们会尽快为您处理(人工客服工作时间:9:00-18:30)。
注塑成型充填过程的数值模拟技术王利霞申长雨郑州大学檬塑模具国家工程研究中心,郑州、450002注塑成型充模流动过程是一个相当复杂的物理过程,非牛顿的高温塑料熔体在压力的驱动下通过流道、浇口向温度较低的模腔充填,塑料熔体压力、温度、剪切速率等物理量在充模过程中的变化.将直接影响者塑件的最终彤状、内部结构、取向和残余应力。
模具设计人员应综合考虑这些因素,才能正确设计出合格的模具。
注射模cAE技术的出现,使人们在模具制造之前就能预测熔体的充填状况,以便及早发现问题,修改图纸而不是返修模具。
l数学模型注塑模充填模拟基于型腔内熔体充填机理和流变学基本方程,视聚合物熔体在型腔中的流动为粘性不可压流体的流动,忽略垂直于流动方向的速度分量,进行合理简化,建立了广义Hele-¥haw流动的数学模型。
连续性方程旦㈦+曼!坐尘=0n)0xay运动方程罢一导(卵要b:o(2)ujOZ口=罢一_c3(叩_dv)=o(3)vyo=口z能量方程,o(乓拿+。
导£+,要马:I要≥+口,。
(4)ul“^u,_z其中,tl、v分别为x、y方向的速度分量,P为密度,Cp、k分别是比热窖和热传导率,P、T分别代表熔体的压力和温度,x、Y为中面坐标,z为厚度方向坐标,Y为剪切速率,n为剪切粘度,可采用Cross模型。
2数值离散由于注塑件大多是薄壁件,采用中面模型处理三维问题,即沿型腔中面划分为三角形单元,对型腔厚度方向和时间采用有限差分。
计算区域离散后,引入控制体积概念,即对于每一个三角形单元,通过连结形心和边的中点而将单元划分成三个子体积,相应于每个节点的控制体积是由与此节点相连的所有子体积构成的,它是一多边形区域。
1)温度场计算:在充填过程中,聚合物熔体粘度对温度具有高度敏感性,温度分布在注塑成型模拟中十分重要。
采用有限差分法求解能量方程时,由于热传导、热对流项和粘性热项对每个控制体积结点的贡献在单元内边界处可能是不连续的,需加权平均。
为了保持数值计算稳定性,采用“上风法”处理对流项和粘性热项,从而可得到每一个结点的能量差分方程。
利用松弛法求解能量方程可得到流动区域的温度场分布。
2l压力场计算:假设流动过程中熔体不可压,根据每个结点的控制体积的质量守恒关系可建立压力场求曲8解的有限元方程,即∑s‘。
芝D凹■‘)=Q。
』ms]点N韵所有单元,Qw为结点流率。
压力方程为1迭代法求解。
3)熔体前沿及时间步长的确定:压力场确定后,采用控制体积确定熔体前aFAN的基本思想,但采用多边形控制体积代替四因子f(控制体积充填百分比),相应地定义了4l仁1;②内点,Pt:③前沿结点,o<f<l:④空时间步长的选取是使每个时间步长刚好有一此时,与其相邻的所有空结点都变成新的前沿结开始时第一个控制体积已被熔体充满,此时可近温状态,这样便获得了初始时刻的前沿位置和温求解粘度和压力。
在获得压力场数据后,计算下体豹新前沿位置,以便计算下一时刻的温度场。
个型腔被熔体充满。
3算例分析这里对天津润通彩票杌面板进行模拟分析。
量要好,没有明显的暇癖。
分析的目的是找出最目,并调整工艺参数使成型的制品达到用户要求所示为最佳设计方案的分析结果。
4结束语注塑成型充填模拟可使我们从宏观上认识充模过程中各种物理场的变化,估计一些充模特征,帮助优化产品和型腔设计,确定合理的浇口和流道设计,预测所需的注射压力和锁模力等,以尽早发现由于模具设计或工艺参数不合理而引起的塑件质量问题,及时进行修改而得到台理的模具设计和工艺参数,以提高产品质量和生产效率。
关键词:注塑成型,充填模拟,流动分析NUMERICALSlMULATIONTECHNIQUEOFFILLINGS‘rAGEINPLASTIClNJECTlONMOLDINGWANGUxiaSHENChangyuAPPTNERC,zhengzhOuUnivemRylZhengzhou,450002Am=hemaU∞lmodelingise嘲blishedbyusinggenemlizedHeIe.sh洲月awofanin翻a=icandNon.Newtonianfluidundernon-isothema|∞ndRionshasbeenpreenedtode∞n嗨thedi仃b糟n∞,fillingstageininjedionmoldinginthbpapeLAhybdd仃niteelement/tingecontml.volumenumed∞lscIIemelsappIiedtoimplememthe3D=mul=ionofthefillingstage.Ab甜雕t:pla=icinje=ionmolding.fillingsimul甜on。
nowanafysisc-79注塑成型充填过程的数值模拟技术作者:王利霞, 申长雨作者单位:郑州大学橡塑模具国家工程研究中心(郑州)1.期刊论文师平.张纹.Shi Ping.Zhang Wen基于Moldflow的注塑成型充填过程的数值研究-农业装备技术2007,33(6)由于产品的注塑成型过程非常复杂,而充填过程的模拟计算机软件在预测型腔的流动行为方面已经比较准确.采用Moldflow充模模块,对手机外壳的充模流动过程进行了动态模拟,分析和讨论了影响产品质量的主要原因和问题.2.学位论文刘恰注塑模具的保压优化设计2009注射成型是指将受热融化的塑料材料快速注入闭合的模具型腔内,经过冷却固化定型后,得到和模具型腔形状一致的塑料制品的成型方法。
信息产品和电子产品的迅速发展,对注塑制品的质量提出了更高的要求,如轻便、小巧等,这些就促使了高精密塑料模具的出现。
随着一些大型的注塑成型分析软件的发展和成熟,基于CAE技术的优化设计在注塑成型工艺中的应用极大地提高了制品成型的质量和效率。
然而,基于这些大型分析软件,实施有效的优化设计仍然是一个有挑战性的课题。
由于注塑制品在注塑成型中容易出现收缩不均、残余应力及翘曲变形等缺陷,会严重影响制品的质量。
本文从改善制品质量的角度出发,分阶段地考虑注塑成型的各个关键因素,采用系统优化方法找出各个子系统中的主要设计目标,并对影响设计目标的参数进行优化设计。
首先,阐述了注塑成型的概念与发展现状,介绍了注塑成型过程的主要工艺条件及影响产品质量的关键因素,简述了注塑成型CAE技术的发展与几种常用的优化算法。
其次,由于目前针对保压阶段的设置相对简单,主要是将保压曲线设为恒压控制。
本文对保压曲线的形式做了更多的研究调整,提出了五种不同的保压曲线形式,以有效降低注塑制品的不均匀体积收缩为主要设计目标,并利用Kriging代理模型方法来模拟设计变量与目标函数之间的近似关系,进行优化迭代计算,分别得到了在五种保压曲线形式下的优化设计方案。
本文以扫描器和手机壳为例,详细阐述了本文所提出的注塑模具保压优化设计方法,有效地解决了注塑制品的不均匀体积收缩问题。
最后,将保压曲线优化与浇口位置优化、冷却系统优化和成型工艺参数优化相结合,对整个注塑成型过程进行系统优化设计。
对于浇口位置优化,将遗传算法与注塑充填模拟程序相结合,最小化充填过程中的入口注射压力、制件温度差异、过压和磨擦热四项指标。
对于冷却系统优化,在浇口位置与保压曲线优化设计的基础上,利用分级优化方法对冷却系统进行优化设计。
最后,以成型工艺参数作为设计变量,收缩和翘曲引起的最大变形为设计目标,利用Kriging替代函数对其进行优化设计。
以手机上面板和CPU基座为例,详细阐述了注塑模具的系统优化设计方法。
结果表明系统优化方法可以更为有效地解决注塑成型各阶段的主要质量缺陷,大大提高制品的质量。
本文工作得到国家自然科学基金重大项目《高聚物成型加工与模具设计中的关键力学和工程问题》(No.10590354)的资助。
3.期刊论文申长雨.王利霞.李倩.陈静波.刘春太.SHEN Changyu.WANG Lixia.LI Qian.CHEN Jingbo.LIU Chuntai注塑成型充填过程的可压缩流动分析-化工学报2006,57(7)注塑成型过程中,熔体在型腔中的流动和传热对制品质量性能有重要的影响.为了预测注塑制品的收缩、翘曲和力学性能,精确预测充填过程的流动及传热历史是十分必要的.本文考虑熔体的可压缩性及相变的影响,将充填过程中熔体的流动视为非牛顿可压流体在非等温状态下的广义Hele-Shaw流动.采用有限元/有限差分混合方法求解压力场和温度场,采用控制体积法跟踪熔体流动前沿,并应用Visual C++实现了注塑充填过程的可压缩流动分析.为了保证能量方程各项在单元内边界的连续性,结点能量方程各项由单元形心处的离散值加权平均获得,因而,能量方程在计算区域内整体求解.对两个算例进行了分析,模拟结果与实验结果的对比,验证了本文数值算法及程序.4.学位论文王利霞基于数值模拟的注塑成型工艺优化及制品质量控制研究2004注塑成型过程中,熔体在型腔内的状态及变化历史直接影响到最终制品的性能和质量.对成型过程进行数值模拟,预测熔体在型腔内的状态及变化规律,以辅助模具设计和成型工艺设置,成为提高制品质量的重要手段.应用成型过程的数值模拟只能代替试模来反复验证工艺参数是否合适,难以得到最佳工艺设置,且由于成型中外界扰动的影响,难以保证制品质量的稳定性,因此,对成型工艺进行优化和控制,提高加工变量的稳定性以生产出高质量的制品具有重要的意义.论文在对注塑成型充填/后充填过程进行数值模拟的基础上,研究工艺条件对制品质量的影响规律,建立了注塑成型工艺优化和制品质量控制理论及算法,设计了新型注塑制品质量闭环控制系统,并基于数值模拟实现了注塑制品在线质量控制仿真.论文主要工作包括:1基于粘性可压缩流体的非等温流动,针对注塑成型过程的流动、传热机理及特点,采用适当的简化和假设,建立了三维薄壁制品注塑成型充填/后充填过程的统一数学模型,模型考虑了熔体的可压缩性及相变的影响.构造了耦合有限元/有限差分/控制体积法求解的数值模型,实现了注塑充填/后充填过程一体化数值模拟,预测充模模式、熔接线和气穴位置,以及温度、压力、密度、剪切速率等在空间和时间上的变化,并进一步预测制品质量指标如收缩、沉降斑指数、重量等.数值模拟与验证实验取得了一致的结果.2在充填/后充填模拟的基础上,分别采用材料ABS、HDPE和PP,应用TaguchiDOE技术进行正交实验,研究了工艺参数对制品沉降斑指数、体收缩率变化和制品重量三个指标的影响关系,确定了各个工艺变量对三个质量指标的影响度.3根据工艺参数对质量指标的影响度选取控制变量,以实验设计获得的近似优化解为基线条件,抽取工艺特性及制品质量特性数据,应用人工神经网络技术建立了工艺参数与制品质量之间的关系模型,克服了回归分析方法事先给定数学形式导致有可能丢失信息的缺点,且制品质量神经网络模型对工艺条件变化的适应性为制品质量控制提供了基础.4基于神经网络模型,将实数编码遗传算法与最速下降法结合,用动态惩罚函数处理遗传算法的约束优化问题,建立了实现单目标和多目标注塑成型工艺优化的理论和算法.最速下降算子的嵌入加速了遗传算法的收敛,而动态惩罚函数的引入增大了遗传算法的搜索空间,保证了成型工艺全局最优解的获得,从而为制品质量控制提供了最优的工艺设置及质量参考.数值算例中对注塑工艺的优化,使制品内的体收缩率分布和沉降斑得到了明显改善.5基于注塑成型机理,以及机器设置参数、状态参数和制品质量指标的关系,提出了工艺控制环和质量控制环串联的注塑制品质量闭环控制策略,建立了注塑制品质量闭环控制的神经网络内模控制理论.基于注塑成型模拟,在Matlab平台上实现了制品质量闭环控制仿真.仿真结果表明,工艺控制环和质量控制环串联的闭环质量控制系统比传统的层叠控制具有更好的设置点跟踪能力和抗扰性.5.学位论文谷诤巍薄壳注塑成型中熔体充填过程的模拟研究2001该论文对薄壳注塑成型中熔体充填过程进行了深入的模拟研究.基于流体力学的基本定律,建立了熔体充填流动的数学模型,确定了适合描述薄壳成型充填过程中熔体流变特性的粘度模型,并采用有限元/有限差分/控制体积法求解了压力场、温度场和移动边界问题.首次深入研究了薄壳成型的可成型性问题.通过材料物性分析和量纲分析,从充填阶段形成的"皮芯结构"出发,研究了凝固层分布和可供熔体通过的流动空间大小的影响因素,并主要研究了表征可成型性的两个主要变量即最大注射压力和最大流动长度的主要影响因素,探讨了粘度的压力依赖性等因素对注射压力和流动长度的影响,并通过实验对比加以验证.对薄壳成型充填过程中的主要成型缺陷进行了模拟研究,建立了薄壳制品熔接线强度的预测模型,并通过实验加以验证.对典型的薄壳塑料制品的充填流动过程进行了模拟研究,并和实际生产数据进行了比较,验证了薄壳成型充填模拟的有效性和正确性.6.期刊论文王利霞.申长雨.陈静波.刘春太.董斌斌注塑成型充模过程的温度场计算-计算力学学报2002,19(2)对注塑成型过程中充填阶段的非等温效应的数值模拟进行了研究,模拟了非牛顿流体在任意形状型腔内的流动.这里,数学模型是基于非牛顿流体在非等温状态下的广义Hele-Shaw流动,利用有限元/有限差分混合数值方法求解流场中的压力和温度分布.7.期刊论文王利霞.张娜.申长雨.李倩应用Taguchi实验设计法最小化注塑成型制品沉降斑-塑料工业2004,32(4)基于注塑成型充填后的充填模拟,应用Taguchi实验设计(DOE)技术,采用L9(34)正交矩阵进行实验, 并采用变量分析(ANOVA)研究了工艺参数对制品内最大沉降斑的影响,优化工艺参数以使注塑制品内的沉降斑指数最小,从而提高制品质量.8.学位论文余德启注塑模具的系统优化设计方法研究2008注塑成型是指将受热融化的材料由高压射入模腔,经冷却固化后,得到成形品的方法。