连铸简介
水平连铸铸铁型材简介

水平连铸铸铁型材1.总体概况:铸铁型材水平连铸已有30多年历史,铸铁型材在国外称之为致密铁棒(Dense Bars),这种材料组织致密、耐压气密性好、机械性能优良、出品率高、生产成本低、节材、节能,是砂型铸造无法比拟的。
铸铁型材的推广应用对提高机械工业整体水平,特别是提高基础件的质量,无疑具有十分重要的意义。
国外众多工业发达国家在各个领域已广泛应用铸铁型材。
主要应用在机床、液压及气动、纺织及印刷等通用机械、模具、汽车及动力、制冷等行业,并且,这些国家在使用铸铁型材代替砂铸铸铁、钢、铜基合金等材料的过程中已经取得了良好的效果。
2.水平连铸铸铁型材生产特点:水平连铸铸铁型材的制造方法(原理图见图1)是将严格选择的原辅料经冲天炉或感应炉熔化处理后的铁水,倒入保温炉内,铁水流入安装在保温炉下方的短结晶器中,并被激冷凝固成一定强度的外壳后,用牵引机拉拔成型材。
保温炉内的熔融铁水,在牵引机拉拔的同时,又不断地补充到结晶器内冷却凝固,如此不断运作,生产出铸铁型材。
不同形状的结晶器和不同的生产工艺,可以生产不同截面,不同材质的铸铁型材。
3.水平连铸铸铁型材的组织及力学性能特点:(1). 灰铸铁型材的显微组织为细小片状石墨(外围为一层细小的D型石墨,内部为细小的A型石墨)和铁素体及珠光体基体。
σb=250~350Mpa,HB=150~240,E=1.1~1.7×105Mpa(2). 球墨铸铁型材组织中石墨球细小圆整,球化率高,球数多,无晶间碳化物,机械性能兼有高强度和高塑性。
球墨铸铁型材经热处理后更可以获得各种需要的基体组织及性能,与砂铸球铁相比,在强度相同时,其延伸率提高50%~100%。
(3). 采用水平连铸和封闭结晶器的工艺使型材表面质量好,尺寸精度高,无夹砂、夹渣、气孔、缩孔等铸造缺陷,加工成品率大大高于砂铸件。
(4). 弹性模数高,铸铁型材弹性模数全断面各部位比一般砂型铸铁件高且均匀。
(5). 疲劳极限强度较高,疲劳比与一般砂型铸铁相比约高50%。
连铸连轧技术
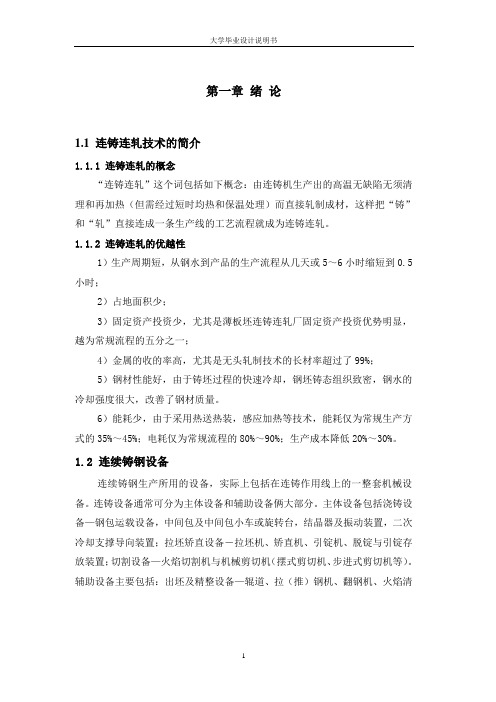
第一章绪论1.1 连铸连轧技术的简介1.1.1 连铸连轧的概念“连铸连轧”这个词包括如下概念:由连铸机生产出的高温无缺陷无须清理和再加热(但需经过短时均热和保温处理)而直接轧制成材,这样把“铸”和“轧”直接连成一条生产线的工艺流程就成为连铸连轧。
1.1.2 连铸连轧的优越性1)生产周期短,从钢水到产品的生产流程从几天或5~6小时缩短到0.5小时;2)占地面积少;3)固定资产投资少,尤其是薄板坯连铸连轧厂固定资产投资优势明显,越为常规流程的五分之一;4)金属的收的率高,尤其是无头轧制技术的长材率超过了99%;5)钢材性能好,由于铸坯过程的快速冷却,钢坯铸态组织致密,钢水的冷却强度很大,改善了钢材质量。
6)能耗少,由于采用热送热装,感应加热等技术,能耗仅为常规生产方式的35%~45%;电耗仅为常规流程的80%~90%;生产成本降低20%~30%。
1.2 连续铸钢设备连续铸钢生产所用的设备,实际上包括在连铸作用线上的一整套机械设备。
连铸设备通常可分为主体设备和辅助设备俩大部分。
主体设备包括浇铸设备—钢包运载设备,中间包及中间包小车或旋转台,结晶器及振动装置,二次冷却支撑导向装置;拉坯矫直设备-拉坯机、矫直机、引锭机、脱锭与引锭存放装置;切割设备—火焰切割机与机械剪切机(摆式剪切机、步进式剪切机等)。
辅助设备主要包括:出坯及精整设备—辊道、拉(推)钢机、翻钢机、火焰清理机等;工艺设备—中间包烘烤装置、吹氖装置、脱气装置、保护渣供给与结晶润滑装置等;自动控制与测量仪表—结晶器液面测量与显示系统、过程控制计算机、测温、测重、测长、测速、测压等仪表系统。
在连续铸钢的生产线上,出拉坯矫直机脱锭后的连铸坯需按用户或下部工序的要求,将铸坯切成定尺或倍尺。
因此在所有的连铸设备中,切割设备是非常重要的一种设备。
由于连铸坯必须在连续的运动过程中实现切割,因而连铸工艺对切割设备提出了特殊的要求,既不管采用什么型式的切割设备都必须与连铸坯实行严格的同步运动。
连铸连轧工艺流程简介
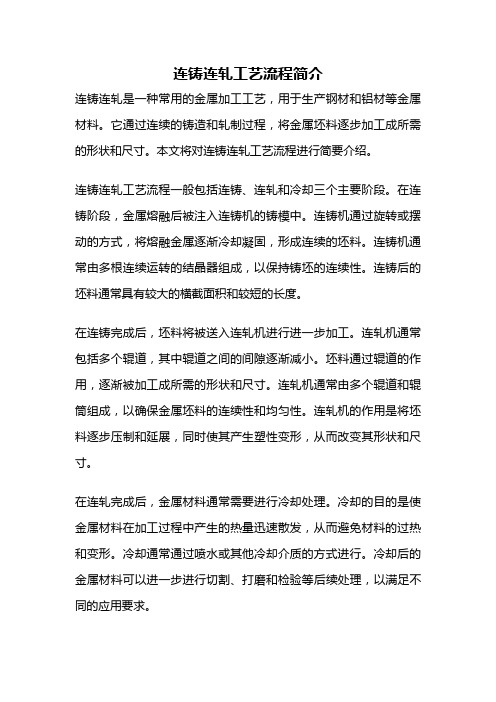
连铸连轧工艺流程简介连铸连轧是一种常用的金属加工工艺,用于生产钢材和铝材等金属材料。
它通过连续的铸造和轧制过程,将金属坯料逐步加工成所需的形状和尺寸。
本文将对连铸连轧工艺流程进行简要介绍。
连铸连轧工艺流程一般包括连铸、连轧和冷却三个主要阶段。
在连铸阶段,金属熔融后被注入连铸机的铸模中。
连铸机通过旋转或摆动的方式,将熔融金属逐渐冷却凝固,形成连续的坯料。
连铸机通常由多根连续运转的结晶器组成,以保持铸坯的连续性。
连铸后的坯料通常具有较大的横截面积和较短的长度。
在连铸完成后,坯料将被送入连轧机进行进一步加工。
连轧机通常包括多个辊道,其中辊道之间的间隙逐渐减小。
坯料通过辊道的作用,逐渐被加工成所需的形状和尺寸。
连轧机通常由多个辊道和辊筒组成,以确保金属坯料的连续性和均匀性。
连轧机的作用是将坯料逐步压制和延展,同时使其产生塑性变形,从而改变其形状和尺寸。
在连轧完成后,金属材料通常需要进行冷却处理。
冷却的目的是使金属材料在加工过程中产生的热量迅速散发,从而避免材料的过热和变形。
冷却通常通过喷水或其他冷却介质的方式进行。
冷却后的金属材料可以进一步进行切割、打磨和检验等后续处理,以满足不同的应用要求。
连铸连轧工艺具有高效、快速和节能的特点,广泛应用于钢铁和有色金属行业。
它可以将金属原料迅速转化为所需的成品,并具有较高的生产效率和质量稳定性。
连铸连轧工艺还可以通过控制温度、压力和速度等参数,实现对金属材料力学性能和表面质量的调控。
然而,连铸连轧工艺也存在一些问题和挑战。
例如,金属材料在连轧过程中容易产生内应力和组织不均匀等问题,这可能会影响材料的机械性能和加工性能。
此外,连铸连轧工艺对设备的要求较高,需要保证设备的稳定性和可靠性,以确保加工过程的连续性和一致性。
连铸连轧工艺是一种重要的金属加工工艺,通过连续的铸造和轧制过程,将金属坯料加工为所需的形状和尺寸。
它具有高效、快速和节能的特点,广泛应用于钢铁和有色金属行业。
精炼-连铸主要设备介绍

主要设备构成:LF炉主要由钢包炉体、钢 LF炉主要由钢包炉体、钢
包车(分单工位和双工位)电极加热 系统、吹氩搅拌系统、合金加料系统以 及测温取样系统、高压室、操作室、液 压站(实现电极、炉盖的升降)等部分 组成。
LF炉主要冶金功能及精炼手段 LF炉主要冶金功能及精炼手段 LF炉具有的主要冶金功能有: LF炉具有的主要冶金功能有 炉具有的主要冶金功能有: 钢水升温、 钢水升温、调温及保温功能 强化脱氧、脱硫功能 强化脱氧、 合金微调功能 采用的精炼手段有: 采用的精炼手段有: 吹氩搅拌 埋弧加热 造强还原气氛 造碱性合成渣
三、各种精炼设备介绍: (一)吹氩:分为底吹、顶吹两种方式。
(二)喷粉及喂丝
合金的喂入与喷粉工艺示意图
(三)LF炉 (三)LF炉 钢包处理型处理钢水过程中,因钢水的温降而使 渣及合金成分的调整以及处理时间等都受到限制。 如果用提高初炼炉出钢温度的办法保证渣熔化及 足够的精炼时间,势必加重初炼炉的负担,降低 炉衬寿命,命中率也比较低,不具备工业性连续 生产的条件。 1971年,日本特殊钢公司开发的Ladle Furnace, 1971年,日本特殊钢公司开发的Ladle Furnace, 简称“LF” 简称“LF”、“LF炉”、“LF钢包炉”、“LF钢 LF炉 LF钢包炉” LF钢 包精炼炉” 包精炼炉”、 “钢包炉”、“钢包精炼炉”等。 钢包炉” 钢包精炼炉” 该炉采用碱性合成渣,埋弧加热,吹氩搅拌,在 还原气氛下精炼,钢包炉的原理图见图
6、中间罐预热站及水口烘烤 功能及结构: 中间罐预热站,用浇注平台上,对砌筑好内衬并 经烘烤干燥的中间罐进一步加热升温,使其在大 约90min左右升温至~1100摄氏度。有利于浇注 90min左右升温至~1100摄氏度。有利于浇注 时减少钢水温度损失和提高铸坯质量。 中间罐预热站由支架、电动推杆、助燃风机、蝶 阀、燃气管及烧嘴等主要部件组成。 浸入式水口预热装置放在浇注平台上,每个人中 间罐预热位中间罐底部,采用中间罐预热废气预 热。
连续铸造原理和连铸设备简介
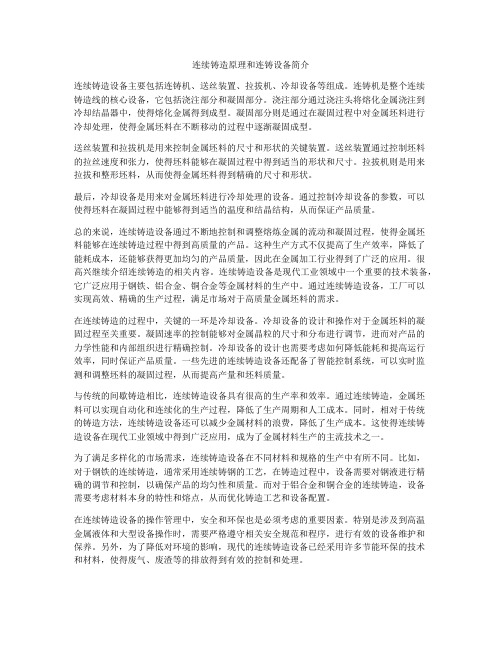
连续铸造原理和连铸设备简介连续铸造设备主要包括连铸机、送丝装置、拉拔机、冷却设备等组成。
连铸机是整个连续铸造线的核心设备,它包括浇注部分和凝固部分。
浇注部分通过浇注头将熔化金属浇注到冷却结晶器中,使得熔化金属得到成型。
凝固部分则是通过在凝固过程中对金属坯料进行冷却处理,使得金属坯料在不断移动的过程中逐渐凝固成型。
送丝装置和拉拔机是用来控制金属坯料的尺寸和形状的关键装置。
送丝装置通过控制坯料的拉丝速度和张力,使得坯料能够在凝固过程中得到适当的形状和尺寸。
拉拔机则是用来拉拔和整形坯料,从而使得金属坯料得到精确的尺寸和形状。
最后,冷却设备是用来对金属坯料进行冷却处理的设备。
通过控制冷却设备的参数,可以使得坯料在凝固过程中能够得到适当的温度和结晶结构,从而保证产品质量。
总的来说,连续铸造设备通过不断地控制和调整熔炼金属的流动和凝固过程,使得金属坯料能够在连续铸造过程中得到高质量的产品。
这种生产方式不仅提高了生产效率,降低了能耗成本,还能够获得更加均匀的产品质量,因此在金属加工行业得到了广泛的应用。
很高兴继续介绍连续铸造的相关内容。
连续铸造设备是现代工业领域中一个重要的技术装备,它广泛应用于钢铁、铝合金、铜合金等金属材料的生产中。
通过连续铸造设备,工厂可以实现高效、精确的生产过程,满足市场对于高质量金属坯料的需求。
在连续铸造的过程中,关键的一环是冷却设备。
冷却设备的设计和操作对于金属坯料的凝固过程至关重要。
凝固速率的控制能够对金属晶粒的尺寸和分布进行调节,进而对产品的力学性能和内部组织进行精确控制。
冷却设备的设计也需要考虑如何降低能耗和提高运行效率,同时保证产品质量。
一些先进的连续铸造设备还配备了智能控制系统,可以实时监测和调整坯料的凝固过程,从而提高产量和坯料质量。
与传统的间歇铸造相比,连续铸造设备具有很高的生产率和效率。
通过连续铸造,金属坯料可以实现自动化和连续化的生产过程,降低了生产周期和人工成本。
连续铸造原理和连铸设备简介
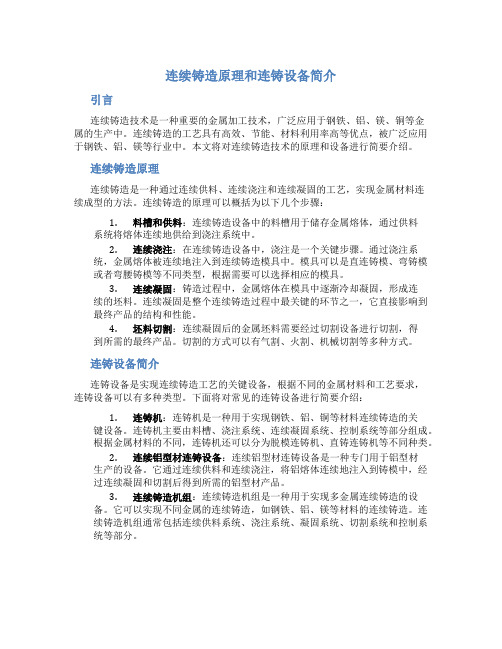
连续铸造原理和连铸设备简介引言连续铸造技术是一种重要的金属加工技术,广泛应用于钢铁、铝、镁、铜等金属的生产中。
连续铸造的工艺具有高效、节能、材料利用率高等优点,被广泛应用于钢铁、铝、镁等行业中。
本文将对连续铸造技术的原理和设备进行简要介绍。
连续铸造原理连续铸造是一种通过连续供料、连续浇注和连续凝固的工艺,实现金属材料连续成型的方法。
连续铸造的原理可以概括为以下几个步骤:1.料槽和供料:连续铸造设备中的料槽用于储存金属熔体,通过供料系统将熔体连续地供给到浇注系统中。
2.连续浇注:在连续铸造设备中,浇注是一个关键步骤。
通过浇注系统,金属熔体被连续地注入到连续铸造模具中。
模具可以是直连铸模、弯铸模或者弯腰铸模等不同类型,根据需要可以选择相应的模具。
3.连续凝固:铸造过程中,金属熔体在模具中逐渐冷却凝固,形成连续的坯料。
连续凝固是整个连续铸造过程中最关键的环节之一,它直接影响到最终产品的结构和性能。
4.坯料切割:连续凝固后的金属坯料需要经过切割设备进行切割,得到所需的最终产品。
切割的方式可以有气割、火割、机械切割等多种方式。
连铸设备简介连铸设备是实现连续铸造工艺的关键设备,根据不同的金属材料和工艺要求,连铸设备可以有多种类型。
下面将对常见的连铸设备进行简要介绍:1.连铸机:连铸机是一种用于实现钢铁、铝、铜等材料连续铸造的关键设备。
连铸机主要由料槽、浇注系统、连续凝固系统、控制系统等部分组成。
根据金属材料的不同,连铸机还可以分为脱模连铸机、直铸连铸机等不同种类。
2.连续铝型材连铸设备:连续铝型材连铸设备是一种专门用于铝型材生产的设备。
它通过连续供料和连续浇注,将铝熔体连续地注入到铸模中,经过连续凝固和切割后得到所需的铝型材产品。
3.连续铸造机组:连续铸造机组是一种用于实现多金属连续铸造的设备。
它可以实现不同金属的连续铸造,如钢铁、铝、镁等材料的连续铸造。
连续铸造机组通常包括连续供料系统、浇注系统、凝固系统、切割系统和控制系统等部分。
最新兴澄特殊钢连铸技术概述
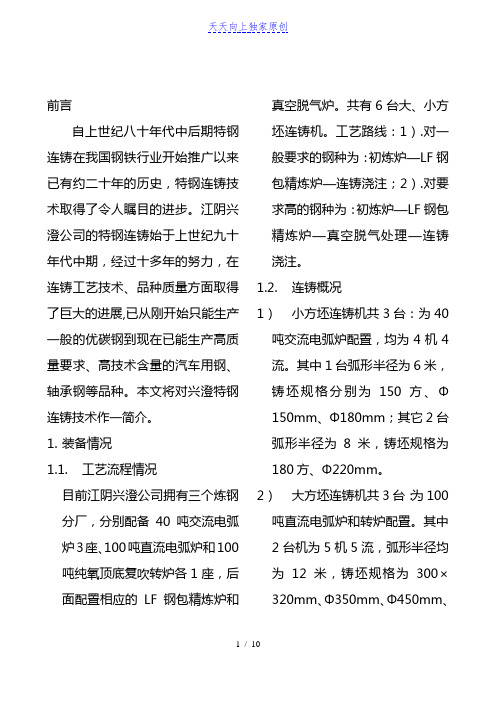
天天向上独家原创前言自上世纪八十年代中后期特钢连铸在我国钢铁行业开始推广以来已有约二十年的历史,特钢连铸技术取得了令人瞩目的进步。
江阴兴澄公司的特钢连铸始于上世纪九十年代中期,经过十多年的努力,在连铸工艺技术、品种质量方面取得了巨大的进展,已从刚开始只能生产一般的优碳钢到现在已能生产高质量要求、高技术含量的汽车用钢、轴承钢等品种。
本文将对兴澄特钢连铸技术作一简介。
1.装备情况1.1.工艺流程情况目前江阴兴澄公司拥有三个炼钢分厂,分别配备40吨交流电弧炉3座、100吨直流电弧炉和100吨纯氧顶底复吹转炉各1座,后面配置相应的LF钢包精炼炉和真空脱气炉。
共有6台大、小方坯连铸机。
工艺路线:1).对一般要求的钢种为:初炼炉—LF钢包精炼炉—连铸浇注;2).对要求高的钢种为:初炼炉—LF钢包精炼炉—真空脱气处理—连铸浇注。
1.2.连铸概况1)小方坯连铸机共3台:为40吨交流电弧炉配置,均为4机4流。
其中1台弧形半径为6米,铸坯规格分别为150方、Φ150mm、Φ180mm;其它2台弧形半径为8米,铸坯规格为180方、Φ220mm。
2)大方坯连铸机共3台:为100吨直流电弧炉和转炉配置。
其中2台机为5机5流,弧形半径均为12米,铸坯规格为300×320mm、Φ350mm、Φ450mm、Φ500mm、Φ600mm。
另1台为3机3流,弧形半径为16.5米,铸坯规格为370×490mm。
2.特殊钢连铸面临的技术课题[1]兴澄公司主要生产轴承钢、弹簧钢、齿轮钢、易切削非调钢、高压管坯钢、油田用钢、系泊链钢、硬线钢等特殊钢。
这些钢种比普通碳素钢对钢质有更高要求。
⑴由于特殊钢中的合金元素较多,含量较高,碳含量控制范围大(0.02%~1.1% C),因此其凝固特性与普通碳素钢有所不同。
⑵特殊钢的纯净度(气体含量、夹杂物数量及形态)、均匀性(低倍组织、微观组织)等要求比普通碳素钢高。
⑶特殊钢中常含有V、Ti、Nb、Al 等活泼元素,极易与氧、氮反应生成高熔点化合物;某些特殊钢中含有S、Al、N元素在浇注、凝固过程中极易形成脆性区或者坚硬质点,这给铸坯质量尤其是表面及内在质量带来一定危害。
连铸历史简介。
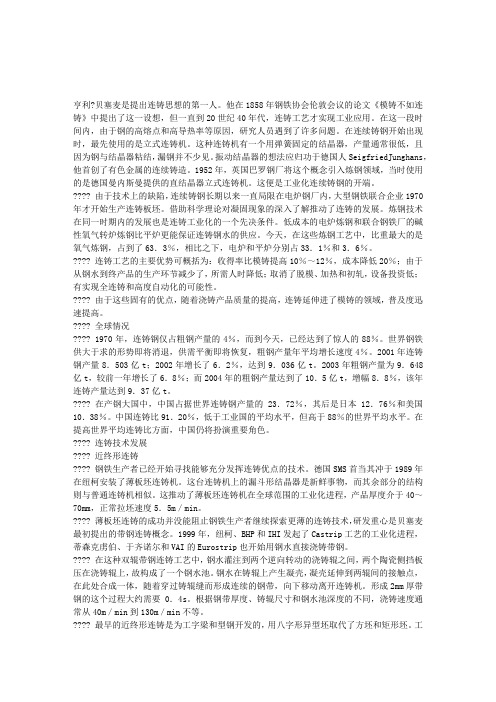
亨利?贝塞麦是提出连铸思想的第一人。
他在1858年钢铁协会伦敦会议的论文《模铸不如连铸》中提出了这一设想,但一直到20世纪40年代,连铸工艺才实现工业应用。
在这一段时间内,由于钢的高熔点和高导热率等原因,研究人员遇到了许多问题。
在连续铸钢开始出现时,最先使用的是立式连铸机。
这种连铸机有一个用弹簧固定的结晶器,产量通常很低,且因为钢与结晶器粘结,漏钢并不少见。
振动结晶器的想法应归功于德国人SeigfriedJunghans,他首创了有色金属的连续铸造。
1952年,英国巴罗钢厂将这个概念引入炼钢领域,当时使用的是德国曼内斯曼提供的直结晶器立式连铸机。
这便是工业化连续铸钢的开端。
???? 由于技术上的缺陷,连续铸钢长期以来一直局限在电炉钢厂内,大型钢铁联合企业1970年才开始生产连铸板坯。
借助科学理论对凝固现象的深入了解推动了连铸的发展。
炼钢技术在同一时期内的发展也是连铸工业化的一个先决条件。
低成本的电炉炼钢和联合钢铁厂的碱性氧气转炉炼钢比平炉更能保证连铸钢水的供应。
今天,在这些炼钢工艺中,比重最大的是氧气炼钢,占到了63.3%,相比之下,电炉和平炉分别占33.1%和3.6%。
???? 连铸工艺的主要优势可概括为:收得率比模铸提高10%~12%,成本降低20%;由于从钢水到终产品的生产环节减少了,所需人时降低;取消了脱模、加热和初轧,设备投资低;有实现全连铸和高度自动化的可能性。
???? 由于这些固有的优点,随着浇铸产品质量的提高,连铸延伸进了模铸的领域,普及度迅速提高。
???? 全球情况???? 1970年,连铸钢仅占粗钢产量的4%,而到今天,已经达到了惊人的88%。
世界钢铁供大于求的形势即将消退,供需平衡即将恢复,粗钢产量年平均增长速度4%。
2001年连铸钢产量8.503亿t;2002年增长了6.2%,达到9.036亿t。
2003年粗钢产量为9.648亿t,较前一年增长了6.8%;而2004年的粗钢产量达到了10.5亿t,增幅8.8%,该年连铸产量达到9.37亿t。
连续铸造简介

连续铸造是一种先进的铸造方法,其原理是将熔融的金属,不断浇入一种叫做结晶器的特殊金属型中,凝固(结壳)了的铸件,连续不断地从结晶器的另一端拉出,它可获得任意长或特定的长度的铸件。
连续铸造的优点连续铸造在国内外已经被广泛采用,如连续铸锭(钢或有色金属锭),连续铸管等。
连续铸造和普通铸造比较有下述优点:[1]1、由于金属被迅速冷却,结晶致密,组织均匀,机械性能较好;2、连续铸造时,铸件上没有浇注系统的冒口,故连续铸锭在轧制时不用切头去尾,节约了金属,提高了收得率;3、简化了工序,免除造型及其它工序,因而减轻了劳动强度;所需生产面积也大为减少;4、连续铸造生产易于实现机械化和自动化,铸锭时还能实现连铸连轧,大大提高了生产效率。
利用贯通的结晶器在一端连续地浇入液态金属,从另一端连续地拔出成型材料的铸造方法。
结晶器一般用导热性较好,具有一定强度的材料,如铜、铸铁、石墨等制成,壁中空,空隙中间通冷却水以增强其冷却作用。
铸出的成型材料有方形、长方形、圆形、平板型、管形或各种异形截面。
连续铸造方法的设想是英国人H.贝塞麦于1857年提出的,在当时的技术条件下未能实际应用,直到20世纪30年代,这种方法才成功地用于铜、铝合金的铸造。
到50年代,连续铸造在各国的钢厂正式用于铸钢。
根据铸造出的成型材料不同,连续铸造有铸锭、铸管、铸板等。
图1为连续铸钢锭示意图,有水平式、垂直式和圆弧式 3种。
结晶器在钢水包下部,钢水通过结晶器被连续地拉出成锭,表面固化的锭材在结晶器下面受到喷射水的二次冷却而完全凝固。
当锭料被拉至一定长度时,由切割机切断成段料,供进一步加工使用。
为了缩小锭材中的柱状晶区域,以便减少锭材轴心区的成分偏析和非金属夹杂,可在结晶器下部装一电磁装置。
70年代出现一种电磁结晶器,即利用成形的电磁场代替结晶器围住液态金属,铸锭在结晶器下部被水强烈冷却。
另外还有一种离心连续铸造方法,工作时结晶图2为铁管连续铸造。
铸造机上安有内、外结晶器。
连铸工艺简介
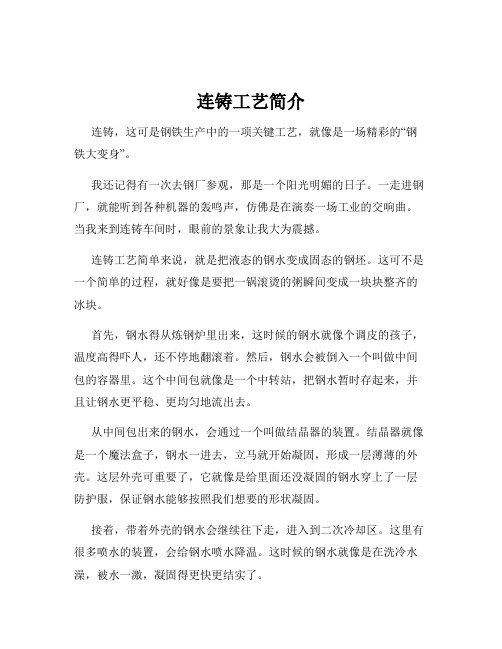
连铸工艺简介连铸,这可是钢铁生产中的一项关键工艺,就像是一场精彩的“钢铁大变身”。
我还记得有一次去钢厂参观,那是一个阳光明媚的日子。
一走进钢厂,就能听到各种机器的轰鸣声,仿佛是在演奏一场工业的交响曲。
当我来到连铸车间时,眼前的景象让我大为震撼。
连铸工艺简单来说,就是把液态的钢水变成固态的钢坯。
这可不是一个简单的过程,就好像是要把一锅滚烫的粥瞬间变成一块块整齐的冰块。
首先,钢水得从炼钢炉里出来,这时候的钢水就像个调皮的孩子,温度高得吓人,还不停地翻滚着。
然后,钢水会被倒入一个叫做中间包的容器里。
这个中间包就像是一个中转站,把钢水暂时存起来,并且让钢水更平稳、更均匀地流出去。
从中间包出来的钢水,会通过一个叫做结晶器的装置。
结晶器就像是一个魔法盒子,钢水一进去,立马就开始凝固,形成一层薄薄的外壳。
这层外壳可重要了,它就像是给里面还没凝固的钢水穿上了一层防护服,保证钢水能够按照我们想要的形状凝固。
接着,带着外壳的钢水会继续往下走,进入到二次冷却区。
这里有很多喷水的装置,会给钢水喷水降温。
这时候的钢水就像是在洗冷水澡,被水一激,凝固得更快更结实了。
在整个连铸过程中,对温度、速度的控制那是相当严格的。
温度太高了,钢水凝固不好;温度太低了,又容易出现裂纹。
速度快了不行,慢了也不行,得恰到好处。
这就像是做饭的时候掌握火候,多一分少一分都不行。
而且,为了保证铸出来的钢坯质量好,还得时刻监测钢水的成分和纯净度。
要是里面有杂质,就像我们吃饭吃到沙子一样,会影响整个钢坯的品质。
连铸出来的钢坯,表面光滑,形状规整,就像是刚刚从生产线上下来的“钢铁士兵”,排列整齐,等待着被送去加工成各种钢材制品。
想象一下,这些钢坯最后会变成高楼大厦里的钢梁、汽车上的零部件、家里的厨具等等。
连铸工艺就像是钢铁世界的源头,为我们的生活提供了各种各样坚固耐用的钢铁产品。
总之,连铸工艺虽然看似复杂,但其实每一个步骤都有它的道理和妙处。
它就像是一场精心编排的舞蹈,每个环节都紧密配合,最终为我们呈现出优质的钢铁成果。
转炉炼钢、炉外精炼、连铸
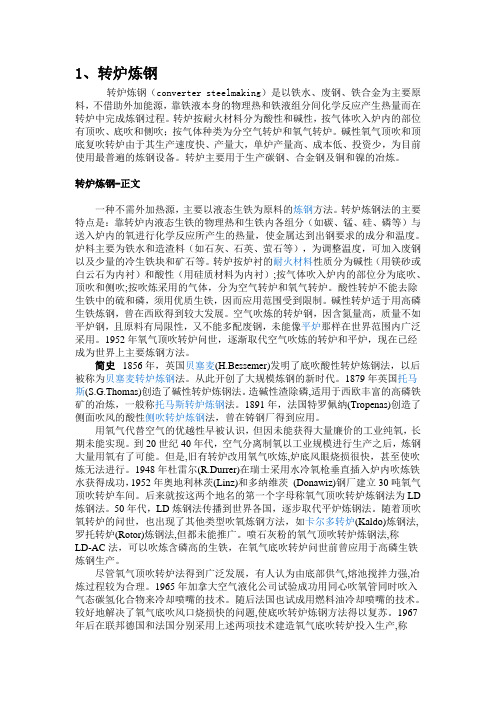
1、转炉炼钢转炉炼钢(converter steelmaking)是以铁水、废钢、铁合金为主要原料,不借助外加能源,靠铁液本身的物理热和铁液组分间化学反应产生热量而在转炉中完成炼钢过程。
转炉按耐火材料分为酸性和碱性,按气体吹入炉内的部位有顶吹、底吹和侧吹;按气体种类为分空气转炉和氧气转炉。
碱性氧气顶吹和顶底复吹转炉由于其生产速度快、产量大,单炉产量高、成本低、投资少,为目前使用最普遍的炼钢设备。
转炉主要用于生产碳钢、合金钢及铜和镍的冶炼。
转炉炼钢-正文一种不需外加热源,主要以液态生铁为原料的炼钢方法。
转炉炼钢法的主要特点是:靠转炉内液态生铁的物理热和生铁内各组分(如碳、锰、硅、磷等)与送入炉内的氧进行化学反应所产生的热量,使金属达到出钢要求的成分和温度。
炉料主要为铁水和造渣料(如石灰、石英、萤石等),为调整温度,可加入废钢以及少量的冷生铁块和矿石等。
转炉按炉衬的耐火材料性质分为碱性(用镁砂或白云石为内衬)和酸性(用硅质材料为内衬);按气体吹入炉内的部位分为底吹、顶吹和侧吹;按吹炼采用的气体,分为空气转炉和氧气转炉。
酸性转炉不能去除生铁中的硫和磷,须用优质生铁,因而应用范围受到限制。
碱性转炉适于用高磷生铁炼钢,曾在西欧得到较大发展。
空气吹炼的转炉钢,因含氮量高,质量不如平炉钢,且原料有局限性,又不能多配废钢,未能像平炉那样在世界范围内广泛采用。
1952年氧气顶吹转炉问世,逐渐取代空气吹炼的转炉和平炉,现在已经成为世界上主要炼钢方法。
简史1856年,英国贝塞麦(H.Bessemer)发明了底吹酸性转炉炼钢法,以后被称为贝塞麦转炉炼钢法。
从此开创了大规模炼钢的新时代。
1879年英国托马斯(S.G.Thomas)创造了碱性转炉炼钢法。
造碱性渣除磷,适用于西欧丰富的高磷铁矿的冶炼,一般称托马斯转炉炼钢法。
1891年,法国特罗佩纳(Tropenas)创造了侧面吹风的酸性侧吹转炉炼钢法,曾在铸钢厂得到应用。
用氧气代替空气的优越性早被认识,但因未能获得大量廉价的工业纯氧,长期未能实现。
连铸连扎工艺简介

连铸连扎工艺简介连铸连轧呀,这可是个超级有趣又很厉害的工艺呢!一、连铸连轧工艺的概念连铸连轧简单来说,就是把钢水直接从炼钢炉里倒出来后,经过连铸机连续铸造成钢坯,然后这个钢坯都不带停歇的,马上就进入轧机进行轧制。
就像是一场接力赛,前面的连铸环节一完成,马上就把“接力棒”传给轧机这个“选手”。
这和传统工艺相比,可就省略了好多步骤,传统的是先铸好钢坯,得把钢坯冷却,再加热,然后才进行轧制。
这就好比传统工艺得让“运动员”休息会儿,再重新热身才能比赛,而连铸连轧是一气呵成。
二、连铸连轧的优点1. 节省能源这工艺能节省超多的能源呢。
你想啊,传统工艺里,钢坯冷却再加热,这得消耗多少能源啊。
就像你煮了一锅汤,放凉了又重新加热,多浪费火呀。
连铸连轧就不存在这个问题,从钢水到钢材成品,一路顺下来,能源损耗大大降低。
2. 提高生产效率因为是连续的过程,中间没有停顿,生产的速度就像开了挂一样。
就像一条快速流淌的河流,没有阻碍,源源不断地生产出钢材。
这可不得了,在同样的时间里,能生产出更多的产品,满足市场对钢材大量的需求。
3. 提升产品质量连铸连轧过程中的连续操作,使得钢材内部组织更加均匀。
这就好比一块蛋糕,如果是一口气做好的,那它的质地就会很均匀,要是中间停了再做,可能就会有分层之类的问题。
钢材也是一样,内部组织均匀的钢材,它的强度、韧性等性能就会更好。
三、连铸连轧的关键设备1. 连铸机连铸机可是这个工艺里的大功臣。
它负责把钢水变成钢坯。
它的构造很复杂,有结晶器,这个结晶器就像是一个神奇的模具,钢水进去就开始初步成型。
还有冷却系统,要确保钢坯在合适的温度下凝固成型。
如果冷却太快或者太慢,那钢坯可就不合格了。
2. 轧机轧机是负责把钢坯变成我们需要的钢材形状的设备。
它有不同的轧辊,通过轧辊的挤压,钢坯就会逐渐变成我们想要的形状,比如说板材、管材或者棒材。
轧机的精度要求可高了,就像一个非常精密的雕刻师,一点点地把钢坯雕琢成合适的样子。
连铸工艺与设备

b. 薄板连铸机,又省去了粗轧机组。
2)提高了金属收得率和成材率;由于在一个机组上连续 浇铸出钢坯来,可以提高金属收得率达7%-8%,成材 率提高10%-15%,成本可以降低约10%-12%;
11/52
3)降低了能源消耗。据日本资料介绍,连铸的能源消 耗仅为模铸工艺的13.5%-20.8%; 4)生产过程机械化、自动化程度高,改善劳动条件。 可以采用计算机自动控制,易于实现连续生产; 5)提高铸坯质量,扩大品种。连铸坯断面比较小,冷 却速度大,枝晶间距小,偏析程度小,尤其沿铸坯 长度方向化学成分均匀。此外,除沸腾钢外几乎所 有钢种均可以采用连铸工艺生产,而且质量很好。
8/52
随着拉坯辊缓慢地将 带液芯铸坯从结晶器 拉出,中间包内的钢 水也同时连续地注入 结晶器内,就可以得 到很长带液芯铸坯。 带液芯铸坯在二次冷却区喷水强制冷却,拉矫机与 结晶振动装置共同作用,将结晶器内铸坯拉出,当拉 到规定位置时,铸坯内部完全凝固。将铸坯切割成规 定的尺寸,由出坯装置送后续工序。
21/52
1.4 连续铸钢技术发展的概况
22/52
1.4 我国连续铸钢技术发展概况
我国是连续铸钢技术发展较早的国家之一,早在20 世纪50年代就已开始研究和工业试验工作。
1957年上海钢铁公司中心试验室的吴大柯主持设计 并建成第1台立式工业试验连铸机。
1958年由徐宝升主持设计的我国第1台双流立式连 铸机于重钢三厂建成投产。 1964年6月24日由徐宝升主持设计的我国第1台方坯 和板坯兼用弧形连铸机于在重钢三厂诞生投产,这 是世界上最早的生产用弧形连铸机之一。
连铸机可以按照多种形式分类:
1)按照连铸机结构外形或铸坯运行轨迹分:立式、立 弯式、直结晶器多点弯曲式、直结晶器弧形、弧形、 椭圆形和水平连铸机。
连铸连锻技术简介
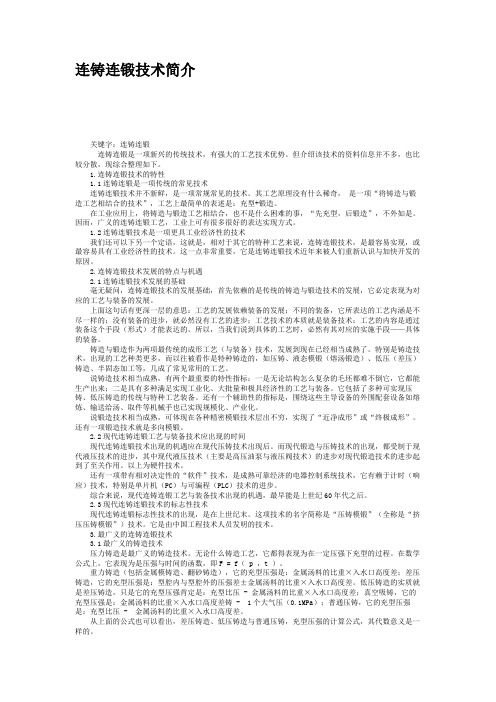
连铸连锻技术简介关键字:连铸连锻连铸连锻是一项新兴的传统技术,有强大的工艺技术优势。
但介绍该技术的资料信息并不多,也比较分散,现综合整理如下。
1.连铸连锻技术的特性1.1连铸连锻是一项传统的常见技术连铸连锻技术并不新鲜,是一项常规常见的技术。
其工艺原理没有什么稀奇,是一项“将铸造与锻造工艺相结合的技术”,工艺上最简单的表述是:充型+锻造。
在工业应用上,将铸造与锻造工艺相结合,也不是什么困难的事,“先充型,后锻造”,不外如是。
因而,广义的连铸连锻工艺,工业上可有很多很好的表达实现方式。
1.2连铸连锻技术是一项更具工业经济性的技术我们还可以下另一个定语,这就是,相对于其它的特种工艺来说,连铸连锻技术,是最容易实现,或最容易具有工业经济性的技术。
这一点非常重要,它是连铸连锻技术近年来被人们重新认识与加快开发的原因。
2.连铸连锻技术发展的特点与机遇2.1连铸连锻技术发展的基础毫无疑问,连铸连锻技术的发展基础,首先依赖的是传统的铸造与锻造技术的发展,它必定表现为对应的工艺与装备的发展。
上面这句话有更深一层的意思:工艺的发展依赖装备的发展;不同的装备,它所表达的工艺内涵是不尽一样的;没有装备的进步,就必然没有工艺的进步;工艺技术的本质就是装备技术:工艺的内容是通过装备这个手段(形式)才能表达的。
所以,当我们说到具体的工艺时,必然有其对应的实施手段——具体的装备。
铸造与锻造作为两项最传统的成形工艺(与装备)技术,发展到现在已经相当成熟了。
特别是铸造技术,出现的工艺种类更多,而以往被看作是特种铸造的,如压铸、液态模锻(熔汤锻造)、低压(差压)铸造、半固态加工等,几成了常见常用的工艺。
说铸造技术相当成熟,有两个最重要的特性指标:一是无论结构怎么复杂的毛坯都难不倒它,它都能生产出来;二是具有多种满足实现工业化、大批量和极具经济性的工艺与装备。
它包括了多种可实现压铸、低压铸造的传统与特种工艺装备。
还有一个辅助性的指标是,围绕这些主导设备的外围配套设备如熔炼、输送给汤、取件等机械手也已实现规模化、产业化。
连铸简介
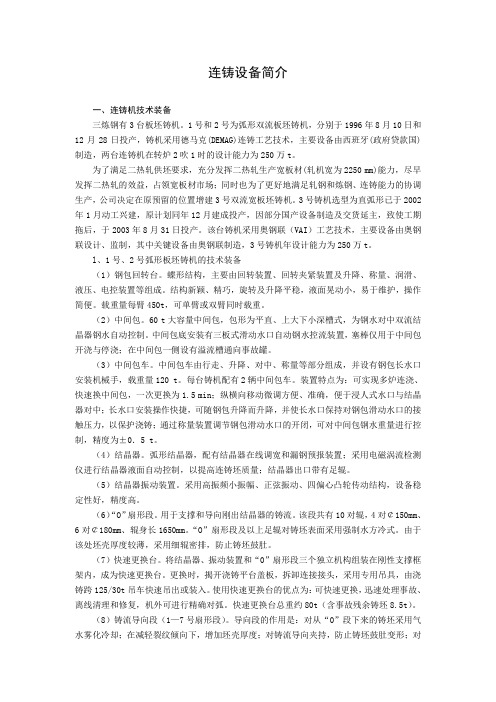
连铸设备简介一、连铸机技术装备三炼钢有3台板坯铸机。
1号和2号为弧形双流板坯铸机,分别于1996年8月10日和12月28日投产,铸机采用德马克(DEMAG)连铸工艺技术,主要设备由西班牙(政府贷款国)制造,两台连铸机在转炉2吹1时的设计能力为250万t。
为了满足二热轧供坯要求,充分发挥二热轧生产宽板材(轧机宽为2250 mm)能力,尽早发挥二热轧的效益,占领宽板材市场;同时也为了更好地满足轧钢和炼钢、连铸能力的协调生产,公司决定在原预留的位置增建3号双流宽板坯铸机。
3号铸机选型为直弧形已于2002年1月动工兴建,原计划同年12月建成投产,因部分国产设备制造及交货延主,致使工期拖后,于2003年8月31日投产。
该台铸机采用奥钢联(VAI)工艺技术,主要设备由奥钢联设计、监制,其中关键设备由奥钢联制造,3号铸机年设计能力为250万t。
l、1号、2号弧形板坯铸机的技术装备(1)钢包回转台。
蝶形结构,主要由回转装置、回转夹紧装置及升降、称量、润滑、液压、电控装置等组成。
结构新颖、精巧,旋转及升降平稳,液面晃动小,易于维护,操作简便。
载重量每臂450t,可单臂或双臂同时载重。
(2)中间包。
60 t大容量中间包,包形为平直、上大下小深槽式,为钢水对中双流结晶器钢水自动控制。
中间包底安装有三板式滑动水口自动钢水控流装置,塞棒仅用于中间包开浇与停浇;在中间包一侧设有溢流槽通向事故罐。
(3)中间包车。
中间包车由行走、升降、对中、称量等部分组成,并设有钢包长水口安装机械手,载重量120 t。
每台铸机配有2辆中间包车。
装置特点为:可实现多炉连浇、快速换中间包,一次更换为1.5 min;纵横向移动微调方便、准确,便于浸人式水口与结晶器对中;长水口安装操作快捷,可随钢包升降而升降,并使长水口保持对钢包滑动水口的接触压力,以保护浇铸;通过称量装置调节钢包滑动水口的开闭,可对中间包钢水重量进行控制,精度为±0.5 t。
薄带连铸技术简介
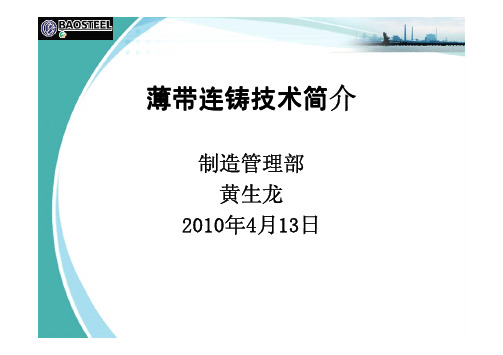
结束语
薄带连铸是尚在中试阶段的新技术, 其侧封板、连铸辊、布流器的寿命与成 本是限制该技术广泛应用的关键技术。 其存在的问题如:产品质量与规格、亚 快速凝固规律及其控制模型、 二次冷却 问题等。这些问题在工业应用中比在中 试阶段解决的速度要快,宁钢在规划中 无论400万吨还是600万吨,考虑品种与 规格拓展,炼钢—连铸—轧钢间一定程度 上存在物流不畅的问题,用薄带连铸解 决宁钢炼钢能力发挥问题是一种很好的 方式。
2.1.1侧封技术--固体侧封板
2.1.2 侧封技术--电磁侧封
2.1.3 侧封技术--直流电+静磁场电磁侧封
二 薄带连铸工艺的关键技术 与存在的主要问题
2.2 结晶辊是影响薄带连铸机拉速、薄带坯表 面质量与规格和工艺成本的关键性设备。
二 薄带连铸工艺的关键技术 与存在的主要问题
2.3 铸轧模型及其板形控制。 2.4 熔池布流器加工技术,熔池布流器液 位及波动控制。 2.5 亚快速凝固规律及其控制模型。 2.6 与大容量转炉(电炉)间的炉—机匹 配问题。 2.7 与常规连铸产品规格、质量竟争的问 题。 2.8 二次冷却问题。 2.9 熔池钢水的保护性气氛的控制问题。
薄带连铸技术简介
制造管理部 黄生龙 2010年4� 薄带连铸工艺的关键技术。 � 薄带连铸的主要质量问题。 � BAOstrip技术参数(宁钢条件 下的物流平衡)。
�
一、薄带连铸技术简介 1.1 薄带连铸技术的特征:薄带连铸技术是 指将液态钢水直接铸轧成厚度为1-10mm 的薄带坯,稍经冷轧就一次成形的带钢铸轧 生产技术。其特点是:投资成本低,改造费 用少,产品生产周期短,产品生产成本低, 原料要求宽(可实现劣质资源:高P、高S 、高Cu矿或废钢的有效综合利用)。主要用 于碳钢、硅钢、高合金钢(不锈钢等)、高 温合金及非晶材料的生产。目前研究最多是 双辊式薄带连铸机。
连铸工艺与设备-连铸的工艺流程与设备PPT演示文稿

17
2.2.9 二冷固定扇形段
功能 支撑和导向结晶器与拉矫机之间的铸坯和开浇时的引 锭杆。 位置 结晶器与拉矫机之间。 结构 二冷固定扇形段由支撑框架,热保护装置,外弧支撑 辊,内弧压辊确保各种铸坯的冷却控制。此扇形段为 固定段。 2021/3/10
202仪1/3/1表0 系统。
5
连续铸钢设备必须适应高温钢水由液态变成液-固 态,又变成固态的全过程。其间进行着一系列比较 复杂的物理化学变化。连续铸钢具有连续性强、工 艺难度大和工作条件差等特点。 ❖连铸生产对机械设备提出了较高的要求,主要有: 应具有抗高温、抗疲劳强度的性能和足够的刚度, 制造和安装精度要高,易于维修和快速更换,要有 充分的冷却和良好的润滑等。
202度1/3/1把0 引锭杆(牵着铸坯)从结晶器中拉出。
2
❖ 为防止铸坯壳被拉断漏钢和减少结晶器中的拉坯阻力, 在浇铸过程中要对结晶器内壁润滑又要它做上下往复 振动。
❖ 铸坯被拉出结晶器后,为使其更快地散热,需进行喷 水二次冷却,通过二次冷却支导装置的铸坯逐渐凝固。 铸坯不断地被拉出,钢水连续地从上面注入结晶器, 形成了连续铸坯的过程。
2021/3/10
6
2021/3/10
7
2.2.1 钢包回转台
❖钢包回转台:在连铸机浇铸位置上方用于运载钢包 过跨和支承钢包进行浇铸,由回转部分、固回转台是连铸机的关键设备之一,起着连接上
下两道工序的重要作用。钢包回转台的回转情况基本
上包括两侧无钢包、单侧有钢包、两侧有钢包三种情
13
2.2.4 中间包塞棒机构
❖功能:浇铸过程中能自动或手动控制钢液的流量。 ❖ 位置:在中间包上。
通过塞棒控制机构 控制塞棒上下运动, 以达到开闭水口调节 钢水流量为目的,塞 棒机构如左图所示。
- 1、下载文档前请自行甄别文档内容的完整性,平台不提供额外的编辑、内容补充、找答案等附加服务。
- 2、"仅部分预览"的文档,不可在线预览部分如存在完整性等问题,可反馈申请退款(可完整预览的文档不适用该条件!)。
- 3、如文档侵犯您的权益,请联系客服反馈,我们会尽快为您处理(人工客服工作时间:9:00-18:30)。
连铸简介1 连铸的发展及机型介绍1.1 连铸的发展历史常规连续铸钢的最早提出者可以追溯到美国炼钢工程师B.Atha(1886年)和德国工程师R.M.Dlaelen(1887年)。
前者采用了一个垂直固定、底部敞口的厚壁铁质的结晶器,并与中间包相连接来实施间歇式拉坯;后者采用固定式水冷薄壁铜质结晶器,实施连续拉坯,并进行二次冷却,同时也应用了引锭杆垂直贮放装置,飞溅切割等,显然这已经很接近今天使用的连铸机了。
连续铸钢技术经历了20世纪40年代的试验开发,50年代开始步入工业生产,60年代弧形连铸机出现,70年代由于世界能源危机推动的大发展,80年代日趋成熟的技术和90年代面临的一场新的变革,整整经历了60年的历史发展进程。
1866年:美国B.Atha提出以水冷,底部敞口固定结晶器为特征的常规连铸概念;1933年:德国S.Junghans实现了结晶器以可变的频率和振幅做往复振动的想法;1951年:世界第一台工业生产性的立式半连续式连铸机在前苏联红十月钢厂投产,断面尺寸180×600mm;1952年:世界上第一台双流立弯式连续浇注的连铸机在英国巴路钢厂投产,主要生产50×50mm和180×180mm的小方坯;1954年:加拿大阿特拉斯钢厂投入使用方板坯兼用的不锈钢连铸机,可以生产一流的168×620mm板坯和双流的150×150mm的方坯;1960年:日本新日铁钢厂引进世界第一台不锈钢宽板坯连铸机,板坯宽度为1050mm。
1.2 连铸在我国的发展历史我国是世界上开发和应用连续铸钢技术较早的国家之一。
1956年,重工业部的钢铁研究所在一台半连续铸机上浇铸了ф80的圆坯;1957年,上海钢铁公司中心实验室建造了立式连铸机,浇铸了我国第一根75mm×180mm的小方坯连铸钢。
1960年,在北京钢铁学院试验场建造了一台弧形连铸机简单的试验装置,浇铸出了200mm×200mm方坯。
从20世纪70年代后期,一些企业开始引进国外技术和设备,1978年10月、1979年2月和1979年3月武汉钢铁公司二炼钢厂共投产了3台从德国西马克-德马克公司引进的单流板坯连铸机。
20世纪90年代,我国轧钢系统完成了从模铸到连铸的改造,实现了100%的连铸比。
1.3 连铸机的基本机型立式连铸机,立弯式连铸机,弧形连铸机,椭圆形连铸机,水平式连铸机等;除此之外还有同步运动式结晶器的各种连铸机,这类机型的结晶器与铸坯同步移动,铸坯与结晶器壁间无相对运动,因而也没有相对摩擦,能够达到较高的浇注速度,适合与生产接近成品钢材尺寸的小断面或薄断面的铸坯,即近中型连铸,这类的机型有:双辊式连铸机、单辊式连铸机、双带式连铸机、单带式连铸机、轮带式连铸机等。
2 连铸的设备概况2.1 连铸的主要设备连铸的主要设备有:钢包回转台,中间包,结晶器,二次冷却系统和拉坯矫直装置等。
2.2 设备简介2.2.1 钢包回转台钢包回转台的作用那个有:短时间旋转钢包,快速向中间包供给另一炉钢水;称量并显示钢包中剩余钢水量和钢水总量,为生产调度提供基础数据;事先钢包升降,为实现保护浇铸创造条件;当连铸出现工艺事故时,迅速把剩余钢水转移到事故钢包。
以上功能通过液压驱动马达和质量传感器实现。
实物如图2.1。
图2.1 钢包回转台实物图2.2.2 中间包中间包由包盖、塞棒、包壳、永久层、工作层、包底、水口砖、水口座砖、挡渣墙和湍流控制器等部分组成。
其中,塞棒由袖砖和塞头等部分组成,图2.2。
图2.2 中间包内局部结构中间包首先承接钢包中的钢液,然后对准结晶器中心进行浇铸。
它具有减压、稳流、净化钢液、储存钢水和分流的功能。
其主要作用如下:通过调节钢水包滑动水口的开度,保持中间包中有一定深度的钢液面,为钢水能在比较稳定压力下平稳地注入结晶器,为保证连铸拉速和铸坯质量创造条件;它是一个精炼容器,钢水在其中停留5~10min,使混于钢水中的夹杂物和炉渣有一个上浮的机会,如果再在中间保重设置挡渣墙,就能为生产洁净钢创造良好的条件;在多流连铸机上,它把钢水均匀地分配到每一流结晶其中;在多炉连浇时,它能储存一定量的钢水,通过拉速调节,衔接下炉钢水,保证连铸机不断流,为多炉连浇创造条件。
图2.3 钢包-中间包-结晶器浇铸流程中间包容量为钢包容量的20%~40%,使用前需要用煤气烘烤到1000~1300℃。
在浇铸优质钢种时常使用碱性包衬和挡渣墙等。
为使夹杂物上浮,生产洁净钢和超洁净钢奠定了工艺条件。
一般采用全封闭无氧化保护浇铸系统。
全封闭的无氧化保护浇铸系统由钢水包、氩气保护环、中间包保护渣、挡渣墙、钢水、中间包包盖、结晶器保护渣、浸入式水口、结晶器、结晶器内电磁搅拌装置等组成。
以上系统的作用是:在浇铸过程中避免钢水与空气接触,保证钢水不受二次氧化;避免高温钢水的热辐射,在降低钢包中钢水过热度的同时又改善了工作环境;发挥了中间包的二次冶金作用,为生产洁净钢和超洁净钢创造了工艺环境。
通过模拟研究,挡渣墙能改变中间包内钢水流动状态和在中间包内的停留时间,钢水的流动又促进了其中夹杂物碰撞、形核、长大的概率;长大、上浮的夹杂物被保护渣吸收后大大提高了钢水的洁净度。
为了提高连浇炉数,中间包水口一般采用快换水口装置。
使用该机构后,可解决长时间浇铸中间包水口的扩径问题,图2.4。
图2.4 中间包快换装置2.2.3 结晶器结晶器的主要作用是冷却中间包中流出的钢水,使其外部形成一定厚度的坯壳。
这个过程中除了用循环水冷却之外。
结晶器还需要振动,以避免钢坯与结晶器壁粘结漏钢。
结晶器的振动规律演变主要经历以下几个阶段:1、矩形速度规律特点:结晶器下降时与铸坯同步运动,然后以3倍的拉坯速度上升。
问题:加速度大,对机械要求高,不便于实行高频振动。
2、梯形速度规律特点:结晶器下降过程中有较长时间的速度稍大于拉坯速度优点:可使在结晶器内断裂的坯壳压合;使粘结的坯壳强迫脱模;上升、下降转折处的速度变化较缓和,运动平稳。
3、正弦速度规律特点:结晶器与铸坯无同步运动,有一小段负滑动;速度按正弦变化,所以加速度按余弦变化,振动平稳;因为加速度小,所以频率可提高,消除粘结,提高脱模;加工制造容易,润滑密封方便,运动精度高。
优点:目前国内外应用广泛;用于方坯,板坯,薄板坯。
4、非正弦速度规律特点:负滑时间短,减轻坯表面振痕深度;正滑动时间较长,增加消耗保护渣,利于润滑结晶器;结晶器向上运动速度差小,有利于减少摩擦。
此外,为了控制钢水的流动,减少表面和皮下的夹杂物和气泡,减少表面裂纹和稳定操作,借助搅拌流动使结晶器内钢水温度均匀,从而使坯壳厚度均匀。
还要在结晶器上安装电磁搅拌装置。
结晶器外观如图2.5所示,图2.6为浇铸时结晶器内部钢水流动的情况。
图2.5 R12米连铸机300X300方坯结晶器图2.6 结晶器内部钢水流动情况2.2.4 二次冷却系统当铸坯从结晶器中被拉出之后,它的表面上只有10~25mm厚度的一层坯壳,中间充满了未凝固的钢液。
如果不以一定的方式对其进行支撑、保护和继续冷却,铸坯内部的高温钢液就会使坯壳温度回升而软化,并在钢液的静压力作用下,使铸坯变形、鼓肚,甚至出现纵裂,同时也容易发生漏钢事故。
因此,二冷区的任务是,支撑尚未凝固的铸坯,并向铸坯表面喷水进一步冷却铸坯,同时对铸坯和引锭杆的运动起到导向作用;另外还支撑了铸坯和引锭杆的部分重量,以及拉坯时产生的横向力。
因此,二次冷却系统同结晶器的作用一样,直接影响连铸机的效率和铸坯质量。
二次冷却装置采用净水压力喷嘴和汽-水雾化喷嘴。
净水压力喷嘴是用冷却水本身的压力(8~12MPa)为能量,把水雾化为小水滴喷射在铸坯表面;汽-水雾化喷嘴是利用高压空气的能量,把水雾化称为非常小的水滴喷射在铸坯表面。
不论采用何种喷嘴,在二次冷却系统中,对喷嘴的要求是:在铸坯的宽度、长度方向上,铸坯冷却要均匀;既能把水雾化成细水滴,又有较高的喷射速度,打到高温铸坯上易蒸发;能按钢种和冷却工艺要求,最大限度地调节冷却强度;到达铸坯表面的水滴,覆盖面要大且均匀;在铸坯上,未蒸发水的停留时间越短越好。
另外,二冷水的另一个任务,是对支承辊、机架和拉矫机进行冷却。
冷却喷嘴如图2.8.图2.8 适用于板坯及大方坯连铸的二次冷却喷嘴2.2.5 拉矫机设置在铸坯导向和二次冷却装置之后,将铸坯连续拉出并矫直的连铸设备。
拉矫机另一个重要功能是输送引锭杆。
对拉矫机的要求是:(1)经拉矫的铸坯无表面和内部裂纹;(2)可以方便地调整其上下辊的开口度,以适应不同的铸坯断面尺寸;(3)能灵活地调速,以适应拉速的变化;(4)具有足够的强度和刚度;(5)机架的布置要保证安装方便,易于检修和对弧准确等。
小方坯连铸机通常采用五辊拉矫机,大方坯连铸机则由3~5对辊子组成。
板坯连铸机采用多辊拉矫机。
现代板坯连铸机的拉矫机功能已在铸坯导向装置的弧形导向段和矫直段完成,不再专设拉矫机了。
拉矫机由传动装置、压下装置、辊子、机架、底座等组成。
传动装置过去采用直流电机,可以无级调速,现代连铸机的拉矫机都改用交流变频调速。
拉矫机压下装置,小方坯连铸机采用气缸或者液压方式,大方坯和板坯连铸机一般均采用液压压下。
现在的高效连铸对拉矫机的要求为:具有足够的拉坯力,能把铸坯从结晶器中顺利拉出;能在较大范围内调节拉速,并且适应改变断面、钢种和快速送引锭杆的要求,另外,拉坯系统要与结晶器振动系统、结晶器液面自控系统、二冷配水系统实现计算机闭环控制;具有足够的矫直力,能适应最大断面和最低温度的铸坯矫直,为多炉浇铸奠定基础;在结构上要考虑未矫直的冷坯能通过,为快速处理连铸事故创造条件;同时采用合理的冷却措施,保证设备在高温条件下正常使用。
3 连铸工艺概况3.1 钢水的准备首先要准备好成分、温度、脱氧程度及纯净度都合格的钢水。
3.2 浇铸温度指钢水进入结晶器时的温度.也可以指中间包内的钢水温度。
通常一炉钢水需在中间包内测温3次,即开浇后5min、浇铸中期和浇铸结束前5min,而这3次温度的平均值被视为平均浇铸温度。
3.3 浇铸温度的要求在尽可能高的拉速下,保证铸坯出结晶器时形成足够厚度的坯壳,使连铸过程安全的进行下去;在结晶器内,钢水将热量平稳的传导给铜板,使周边坯壳厚度能均匀的生长,保证铸坯表面质量。
3.3.1 浇铸温度过高的危害1、出结晶器坯壳薄,容易漏钢;2、耐火材料侵蚀加快,易导致铸流失控,降低浇铸安全性;3、增加非金属夹杂,影响板坯内在质量;4、铸坯柱状晶发达;中心偏析加重,易产生中心线裂纹。
3.3.2 浇铸温度过低的危害1、容易发生水口堵塞,浇铸中断;2、连铸表面容易产生结疱、夹渣、裂纹等缺陷;3、非金属夹杂不易上浮,影响铸坯内在质量。