表面处理标准对照表
钢铁表面处理标准说明及各标准比较

钢铁表面主要表面处理标准GB8923-88 中国国家标准ISO8501-1:1988 国际标准化组织标准SIS055900-1967 瑞典标准SSPC-SP2,3,5,6,7和10 美国钢结构涂装协会表面处理标准 BS4232 英国标准DIN55928 德国标准JSRA SPSS 日本造船研究协会标准国标GB8923-88 对除锈等级描述:喷射或抛射除锈以字母“Sa”表示。
本标准订有四个除锈等级:Sa1 轻度的喷射或抛射除锈钢材表面应无可见的油脂和污垢,并且没有附着不牢的氧化皮,铁锈和油漆涂层等附着物。
Sa2 彻底的喷射或抛射除锈钢材表面应无可见的油脂和污垢,并且氧化皮,铁锈和油漆涂层等附着物已基本清除,其残留物应该是附着牢固的。
Sa2.5 非常彻底的喷射或抛射除锈钢材表面应无可见的油脂,污垢,氧化皮,铁锈和油漆涂层等附着物,任何残留的痕迹应仅是点状或条纹状的轻微色斑。
Sa3 钢材表面外观洁净的喷射或抛射除锈钢材表面应无可见的油脂,污垢,氧化皮,铁锈和油漆涂层等附着物,该表面应显示均匀的金属色泽。
手工和动力工具除锈以字母“St”表示。
本标准订有二个除锈等级:St2 彻底的手工和动力工具除锈钢材表面应无可见的油脂和污垢,并且没有附着不牢的氧化皮、铁锈和油漆涂层等附着物。
St3 非常彻底的手工和动力工具除锈钢材表面应无可见的油脂和污垢,并且没有附着不牢的氧化皮、铁锈和油漆涂层等附着物。
除锈应比St2更为彻底,底材显露部分的表面应具有金属光泽。
我国的除锈标准与相当的国外除锈标准对照表:注:SSPC中的Sp6比Sa2.5 略为严格,Sp2为人工钢丝刷除锈,Sp3为动力除锈。
表面粗糙度及其评定喷砂、抛丸、手工和动力除锈,其目的除达到前述一定的表面清洁度外,还会对钢铁表面造成一定的微观不平整度,即表面粗糙度。
对于涂漆前钢铁表面的粗糙度通常以一些主要的波峰和波谷间的高度值来表示。
钢铁表面粗糙度对漆膜的附着力,防腐蚀性能和保护寿命有很大影响。
表面处理符合对照表
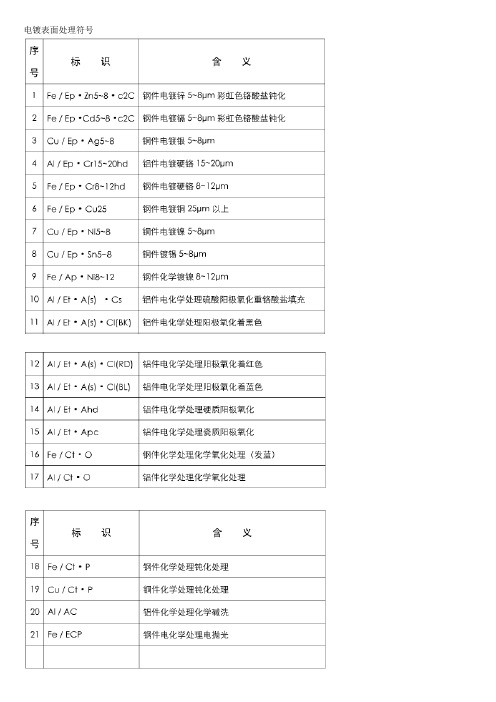
最后镀银12~18μm
镀金
Ep.Au1
D.Au1
电镀金1~3μm
镀硬铬
Ep.Cr5hd
D.yCr5
电镀硬铬5~8μm
镀镍
Ep.Ni8
D.Ni8
电镀镍8~12μm
镀锡
Ep.Sn5
D.Sn5
电镀锡5~8μm
镀锡铅合金
Ep.Sn(60)-Pb8
D.60SnPb8
电镀含锡60%的铅铝合金8~12μm
钢质零件,使用条件为极严酷,由铜、光亮镍、乳白铬组成的多层镀覆电镀层
EP.Cu20Ni25bCrOWJ456-1995
/EP.Cr(45)OWJ456-1995
注:“mc”符号表示微裂纹,“hd”符号表示硬质
镉电镀层
钢质零件,使用条件为中等,彩色钝化处理的无光缎面镉镀层
EP.Cd12St3.c2CWJ457-1995
铜质零件,使用条件为轻度,采用细光缎面镀镍
EP.Ni5St1WJ455-1995
铬电镀层
钢质零件,使用条件为轻度,采用低锡青铜为底层的粗光缎面镀镍
EP.Cu(85)-Sn(15)Ni10St2WJ455-1995
铜质零件,使用条件为轻度,采用细光缎面镀铬
Ep.Cr5St1WJ456-1995
铜质零件,使用条件为轻度,采用无光缎面镀铬
无光缎面化学氧化
Ct.OSt3WJ461-1995
半光亮化学氧化
Ct.OSWJ461-1995
光亮化学氧化
Ct.ObWJ461-1995
黑镍电镀层
钢质零件采用镀锌底层后无光缎面镀黑镍
EP.NibkSt3WJ454-1995
表面处理表示方法及选择
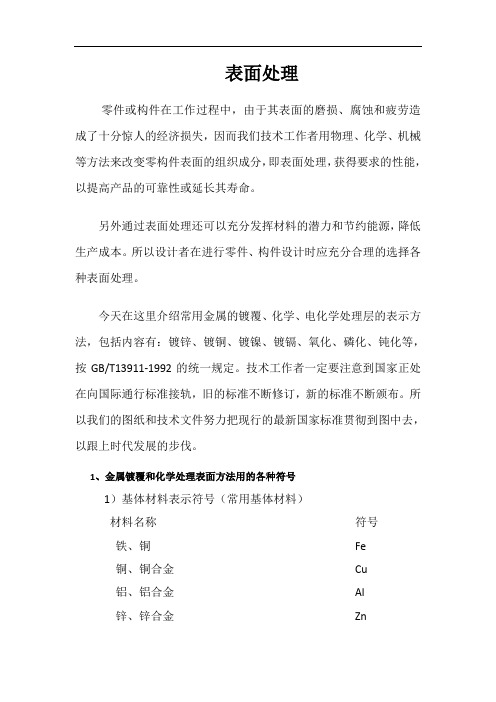
表面处理零件或构件在工作过程中,由于其表面的磨损、腐蚀和疲劳造成了十分惊人的经济损失,因而我们技术工作者用物理、化学、机械等方法来改变零构件表面的组织成分,即表面处理,获得要求的性能,以提高产品的可靠性或延长其寿命。
另外通过表面处理还可以充分发挥材料的潜力和节约能源,降低生产成本。
所以设计者在进行零件、构件设计时应充分合理的选择各种表面处理。
今天在这里介绍常用金属的镀覆、化学、电化学处理层的表示方法,包括内容有:镀锌、镀铜、镀镍、镀镉、氧化、磷化、钝化等,按GB/T13911-1992的统一规定。
技术工作者一定要注意到国家正处在向国际通行标准接轨,旧的标准不断修订,新的标准不断颁布。
所以我们的图纸和技术文件努力把现行的最新国家标准贯彻到图中去,以跟上时代发展的步伐。
1、金属镀覆和化学处理表面方法用的各种符号1)基体材料表示符号(常用基体材料)材料名称符号铁、铜Fe铜、铜合金Cu铝、铝合金Al锌、锌合金Zn镁、镁合金Mg钛、钛合金Ti塑料PL(国际通用缩写)金属材料化学元素符号表示:合金材料用其主要成分的化学元素符号表示,非金属材料用国际通用缩写字母表示。
2)镀覆方法处理方法表示符号:方法名称符号(英文缩写)电镀Ep化学镀Ap电化学处理Et化学处理Ct3)化学和电化学处理名称的表示符号处理名称符号钝化P(不能理解为元素符号磷)氧化O电解着色Ec磷化Ph阳极氧化 A电镀锌铬酸盐处理 Ca.电镀锌光亮铬酸盐处理C1Ab.电镀锌彩虹铬酸盐处理C1B (漂白型)常用c.电镀锌彩虹铬酸盐处理C2C (彩虹型)常用d.电镀锌深色铬酸盐处理C2D(符号-C;分级1、2;类型:A.B.C.D)2、金属镀覆和化学、电化学的表示方法(在图纸上的标记)1)金属镀覆表示方法:示例:例1.Fe/Ep.CuN15bCy0.3mc.(钢材,电镀铜10μm,光亮镍15μm,微裂纹铬0.3μm)例2. Fe/Ep.Zn7.C2C(钢材。
(完整版)表面处理标准汇总

试验方法标准 醋酸-盐雾试验
ASTM B287
44
试验方法标准 铜加速的醋酸-盐雾试验(CASS试验)
ASTM B368
45
试验方法标准 用锥形挠曲机试验附着的有机涂层的伸长
ASTM D522
46
试验方法标准 镜面光泽
ASTM D523
47
方法标准 试验色漆、清漆、喷漆和有关产品用钢板的制备
ASTM D609
ISO 8130-9
38
金属的磷酸盐转化膜-确定要求的方法
ISO 9717
39
化学转化膜-铝及铝合金上的漂洗和不漂洗铬酸盐转化膜
ISO 10546
40
人造气氛腐蚀试验-盐雾试验
ISO 9227
41
金属材料上的转化膜-单位面积上膜层质量的测量-重量法
ISO 3892
42
试验方法标准 盐雾试验
ASTM B117
GB 14443
6
污水综合排放标准
GB 8978
国际标准部分
序号
标准名称
标准号
1
色漆和清漆-试验用标准样板
ISO 1514
2
色漆和清漆-划痕试验
ISO 1518
3
色漆和清漆-弯曲试验(圆柱轴)
ISO 1519
4
色漆和清漆-压痕试验
ISO 1520
5
色漆和清漆-摆杆阻尼试验
ISO 1522
6
色漆和清漆、石油和有关产品闪点的测定-闭杯平衡法
ASTM E376
69
试验方法标准 管道涂层的耐冲击性(石灰石落降试验)
ASTM G13
70
试验方法标准 管道涂层的耐冲击性(落锤试验)
表面处理符合对照表
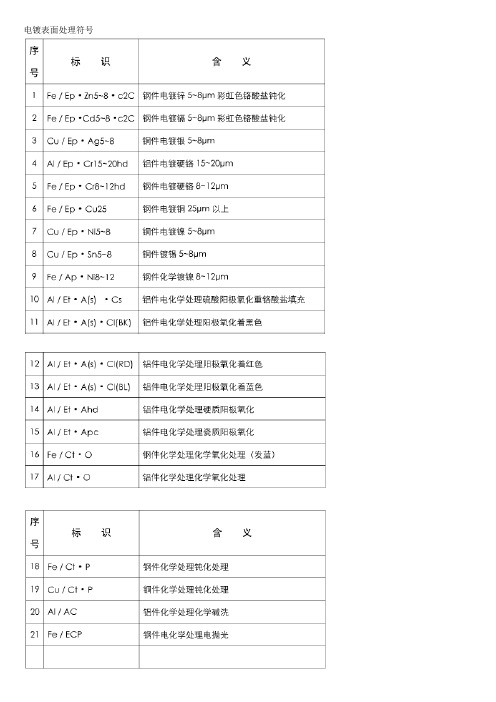
O(A)
过硫酸盐氧化
O(G)
电解氧化
O(E)
硫酸阳极氧化
A(S)
铬酸阳极氧化
A(Cr)
磷酸阳极氧化
A(P)
草酸阳极氧化
A(O)
阳极氧化
A
硬质阳极氧化
D.YY
处理名称
后处理名称
符号
钝化
P
磷化(磷酸盐处理)
Ph
氧化
O
乳化
E
着色
CI
热熔
Fm
扩散
Di
涂装
Pt
封闭
S
防变色
At
铬酸盐封闭
Cs
其它镀覆层特征、处理特征
黑色无光缎面阳极氧化
Et.ASt3.CI(BK)WJ463-1995
黑色硫酸阳极氧化
Et.A(S).CI(BK)WJ463-1995
黑色光亮硫酸阳极氧化
Et.A(S)b.CI(BK)WJ463-1995
黑色半光亮硫酸阳极氧化
Et.A(S)S.CI(BK)WJ463-1995
黑色暗面硫酸阳极氧化
Et.A(S)m.CI(BK)WJ463-1995
Et.A(Cr)St2.CI(BK)WJ463-1995
黑色无光铬酸阳极氧化
Et.A(Cr)St3.CI(BK)WJ463-1995
黑色磷酸阳极氧化
Et.A(P).CI(BK)WJ463-1995
黑色光亮磷酸阳极氧化
Et.A(P)b.CI(BK)WJ463-1995
黑色半光亮磷酸阳极氧化
Et.A(P)S.CI(BK)WJ463-1995
无光缎面化学氧化
Ct.OSt3WJ461-1995
半光亮化学氧化
各类管道表面处理对照表

各类管道表面处理对照表以下是各类管道表面处理的对照表,用于比较不同处理方式的优缺点以及适用情况。
1. 喷砂处理- 简介:喷砂是一种机械处理方法,通过将磨料高速喷射到管道表面,以去除污垢、油漆或氧化层等。
- 优点:- 拥有良好的清洁效果,可去除大部分污垢;- 提供粗糙表面,有利于涂覆或粘接材料的附着性;- 可以应用于各种类型和尺寸的管道;- 是一种经济高效的处理方式。
- 缺点:- 会产生大量的粉尘和噪音,对环境和操作人员健康有一定影响;- 可能造成管道表面变形或损坏;- 需要使用专业的喷砂设备和材料。
- 适用情况:- 需要彻底清洁管道表面的情况;- 需要提供粗糙表面以增加涂覆或粘接材料的附着性的情况;- 对处理时间和成本有一定要求的情况。
2. 酸洗处理- 简介:酸洗是一种化学处理方法,通过使用酸性溶液来去除管道表面的氧化层和其他污垢。
- 优点:- 能够去除管道表面的铁锈、氧化层等;- 清洗效果好,可以获得光洁度较高的表面;- 适用于各种材料的管道。
- 缺点:- 酸洗液对操作人员有一定的腐蚀性,对环境有污染风险;- 需要专业的设备和技术来执行酸洗过程;- 一般需要中性化处理,以防止酸残留。
- 适用情况:- 需要去除管道表面的铁锈、氧化层等的情况;- 需要获得光洁度较高的管道表面的情况;- 对酸洗过程的专业要求较高的情况。
3. 涂层处理- 简介:涂层处理是在管道表面涂覆一层保护性涂层,用于防腐、防护和美化。
- 优点:- 可以提供持久的防腐和防护效果;- 可以根据不同需求选择不同类型的涂层材料;- 可以美化管道表面,提高外观质量。
- 缺点:- 涂层施工复杂,需要专业的设备和技术;- 涂层材料成本较高;- 涂层可能会受到损坏或老化,需要定期维护。
- 适用情况:- 需要对管道进行防腐、防护和美化的情况;- 对涂层材料和施工要求较高的情况;- 需要长期保护和维护管道表面的情况。
以上是各类管道表面处理的对照表,根据不同的需求和情况选择适合的处理方式能够提高管道的耐用性和外观质量。
表面处理表示方法及选择
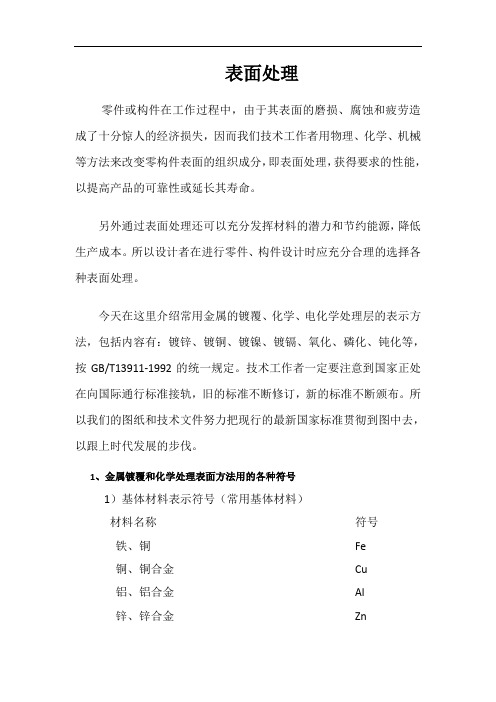
表面处理零件或构件在工作过程中,由于其表面的磨损、腐蚀和疲劳造成了十分惊人的经济损失,因而我们技术工作者用物理、化学、机械等方法来改变零构件表面的组织成分,即表面处理,获得要求的性能,以提高产品的可靠性或延长其寿命。
另外通过表面处理还可以充分发挥材料的潜力和节约能源,降低生产成本。
所以设计者在进行零件、构件设计时应充分合理的选择各种表面处理。
今天在这里介绍常用金属的镀覆、化学、电化学处理层的表示方法,包括内容有:镀锌、镀铜、镀镍、镀镉、氧化、磷化、钝化等,按GB/T13911-1992的统一规定。
技术工作者一定要注意到国家正处在向国际通行标准接轨,旧的标准不断修订,新的标准不断颁布。
所以我们的图纸和技术文件努力把现行的最新国家标准贯彻到图中去,以跟上时代发展的步伐。
1、金属镀覆和化学处理表面方法用的各种符号1)基体材料表示符号(常用基体材料)材料名称符号铁、铜Fe铜、铜合金Cu铝、铝合金Al锌、锌合金Zn镁、镁合金Mg钛、钛合金Ti塑料PL(国际通用缩写)金属材料化学元素符号表示:合金材料用其主要成分的化学元素符号表示,非金属材料用国际通用缩写字母表示。
2)镀覆方法处理方法表示符号:方法名称符号(英文缩写)电镀Ep化学镀Ap电化学处理Et化学处理Ct3)化学和电化学处理名称的表示符号处理名称符号钝化P(不能理解为元素符号磷)氧化O电解着色Ec磷化Ph阳极氧化 A电镀锌铬酸盐处理 Ca.电镀锌光亮铬酸盐处理C1Ab.电镀锌彩虹铬酸盐处理C1B (漂白型)常用c.电镀锌彩虹铬酸盐处理C2C (彩虹型)常用d.电镀锌深色铬酸盐处理C2D(符号-C;分级1、2;类型:A.B.C.D)2、金属镀覆和化学、电化学的表示方法(在图纸上的标记)1)金属镀覆表示方法:示例:例1.Fe/Ep.CuN15bCy0.3mc.(钢材,电镀铜10μm,光亮镍15μm,微裂纹铬0.3μm)例2. Fe/Ep.Zn7.C2C(钢材。
(完整版)表面处理标准汇总.doc
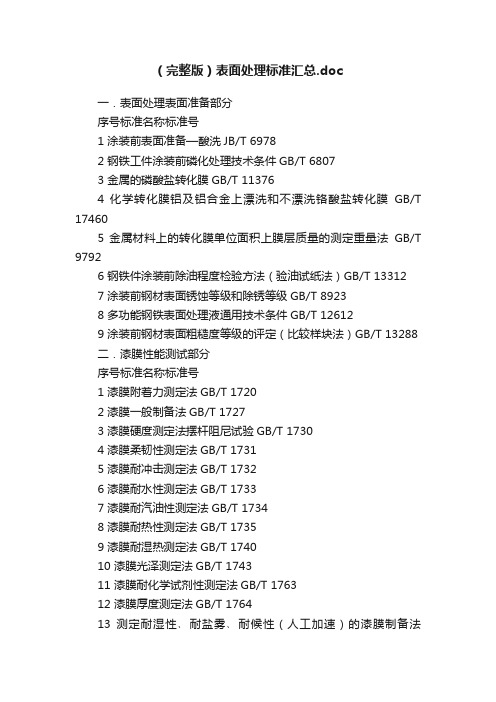
(完整版)表面处理标准汇总.doc一.表面处理表面准备部分序号标准名称标准号1 涂装前表面准备—酸洗JB/T 69782 钢铁工件涂装前磷化处理技术条件GB/T 68073 金属的磷酸盐转化膜GB/T 113764 化学转化膜铝及铝合金上漂洗和不漂洗铬酸盐转化膜GB/T 174605 金属材料上的转化膜单位面积上膜层质量的测定重量法GB/T 97926 钢铁件涂装前除油程度检验方法(验油试纸法)GB/T 133127 涂装前钢材表面锈蚀等级和除锈等级GB/T 89238 多功能钢铁表面处理液通用技术条件GB/T 126129 涂装前钢材表面粗糙度等级的评定(比较样块法)GB/T 13288二.漆膜性能测试部分序号标准名称标准号1 漆膜附着力测定法GB/T 17202 漆膜一般制备法GB/T 17273 漆膜硬度测定法摆杆阻尼试验GB/T 17304 漆膜柔韧性测定法GB/T 17315 漆膜耐冲击测定法GB/T 17326 漆膜耐水性测定法GB/T 17337 漆膜耐汽油性测定法GB/T 17348 漆膜耐热性测定法GB/T 17359 漆膜耐湿热测定法GB/T 174010 漆膜光泽测定法GB/T 174311 漆膜耐化学试剂性测定法GB/T 176312 漆膜厚度测定法GB/T 176413 测定耐湿性﹑耐盐雾﹑耐候性(人工加速)的漆膜制备法GB/T 176514 色漆和清漆涂层老化的评级方法GB/T 176615 色漆和清漆耐中性盐雾性能的测定GB/T 177116 色漆和清漆人工气候老化和人工辐射暴露(滤过的氙弧辐射)GB/T 186517 漆膜颜色标准GB/T 318118 色漆和清漆耐水性的测定浸水法GB/T 520919 涂层附着力的测定法拉开法GB/T 521020 涂膜硬度铅笔测定法GB/T 673921 涂膜弯曲试验(圆柱轴)GB/T 674222 色漆和清漆划痕试验GB/T 927923 色漆和清漆漆膜的划格试验GB/T 928624 色漆和清漆杯突试验GB/T 975325 色漆和清漆不含金属颜料的色漆漆膜之20°﹑60°和85°镜面GB/T 9754光泽的测定26 人造气氛腐蚀试验盐雾试验GB/T 1012527 金属和其他非有机覆盖层通常凝露条件下的二氧化硫腐蚀试验GB/T 978928 色漆和清漆漆膜厚度的测定GB/T 13452.229 色漆和清漆钢铁表面上的丝状腐蚀试验GB/T 13452.430 色漆和清漆耐湿性的测定连续冷凝法GB/T 1389331 色漆涂层粉化程度的测定方法及评定GB/T 1482632 绝缘漆漆膜击穿强度测定法HG/T 2-57三.部分涂料标准序号标准名称标准号1 电泳漆漆膜制备法HG/T2 —10462 电泳漆电导率测定法HG/T 2-10473 电泳漆泳透力测定法HG/T 2-10484 电泳漆库仑效率测定法HG/T 2-10495 电泳漆沉积量测定法HG/T 2-10506 电泳漆泳透力测定法(钢管法)HG/T 2-10517 涂料粘度测定法GB/T 17238 涂料细度测定法GB/T 17249 涂料固体含量测定法GB/T 172510 涂料遮盖力测定法GB/T 172611 涂料流平性测定法GB/T 175012 涂料产品分类,命名和型号GB/T 270513 涂料产品的取样GB/T 318614 色漆和清漆词汇第一部分通用术语GB/T 5206.115 色漆和清漆词汇第二部分树脂术语GB/T 5206.216 色漆和清漆词汇第三部分颜料术语GB/T 5206.317 色漆和清漆词汇第四部分涂料及涂膜物化性能术语GB/T 5206.418 色漆和清漆词汇第五部分涂料及涂膜病态术语GB/T 5206.519 色漆和清漆用漆基皂化值的测定法GB/T 674420 色漆和清漆密度的测定GB/T 675021 色漆和清漆挥发物和不挥发物的测定GB/T 675122 涂料及有关产品闪光测定法闭口杯平衡法GB/T 6753.523 色漆流挂性的测定GB/T 926424 色漆和清漆用原材料取样GB 928525 饰面型防火涂料防火性能分级及试验方法防火性能分级GB 15442.126 饰面型防火涂料防火性能分级及试验方法大板燃烧法GB/T 15442.227 饰面型防火涂料防火性能分级及试验方法隧道燃烧法GB/T 15442.328 饰面型防火涂料防火性能分级及试验方法小室燃烧法GB/T 15442.429 粉末涂料烘烤时质量损失的测定GB/T 1659230 涂料产品检验 , 运输和储存通则HG/T 2458四.安全与环保标准序号标准名称标准号1 涂装作业安全规程涂漆前处理工艺安全及其通风净化GB 76922 涂装作业安全规程静电喷枪及其辅助装置安全技术条件GB 147733 涂装作业安全规程涂漆工艺安全及其通风净化GB 65144 涂装作业安全规程喷漆室安全技术规定GB 144445 涂装作业安全规程涂层烘干室安全技术规定GB 144436 污水综合排放标准GB 8978国际标准部分序号标准名称标准号1 色漆和清漆 - 试验用标准样板ISO 15142 色漆和清漆 - 划痕试验ISO 15183 色漆和清漆 - 弯曲试验(圆柱轴)ISO 15194 色漆和清漆 - 压痕试验ISO 15205 色漆和清漆 - 摆杆阻尼试验ISO 15226 色漆和清漆、石油和有关产品闪点的测定- 闭杯平衡法ISO 15237 色漆和清漆 - 研磨细度的测定ISO 15248 色漆和清漆 - 划格试验ISO 24099 色漆和清漆 - 漆膜厚度的测定ISO 280810 色漆和清漆 - 密度的测定ISO 281111 色漆和清漆 - 在20°、60°和85°非金属色漆漆膜镜面光泽的测定ISO 281312 色漆和清漆 - 巴克霍尔压痕试验ISO 281513 色漆和清漆 - 在高剪切速率下粘度的测定ISO 288414 色漆和清漆 - 色漆和清漆以及色漆和清漆用漆基的不挥发物的测定ISO 325115 色漆和清漆–色漆的目视比色ISO 366816 色漆、清漆、石油和有关产品- 闪点的测定- 快速平衡法ISO 367917 色漆、清漆、石油和有关产品- 闪点 / 非闪点试验 - 快速平衡法ISO 368018 色漆和清漆用漆基 - 皂化值的测定 - 滴定法ISO 368119 色漆和清漆用漆基 - 酸值的测定 - 滴定法ISO 368220 色漆和清漆–术语对照表 - 第 1 部份:通用术语双语种版本ISO 4617-121 色漆和清漆–术语对照表- 第 2 部份:三语种版本ISO 4617-222 色漆和清漆–术语对照表- 第 3 部份:三语种版本ISO 4617-323 色漆和清漆–术语对照表- 第 4 部份:三语种版本ISO 4617-424 色漆和清漆–词汇 - 第 1 部份:通用术语三语种版本ISO 4618-125 色漆和清漆–词汇 - 第 2 部份:薄膜在老化过程中不良变化及其原始缺ISO 4618-2陷术语三语种版本26 色漆和清漆–词汇 - 第 3 部份:树脂术语三语种版本ISO 4618-327 色漆和清漆–钢面的丝状腐蚀试验ISO 462328 色漆和清漆–粘合力拉开试验ISO 462429 色漆和清漆用漆基 - 羟基值的测定 - 滴定法ISO 462930 色漆和清漆用漆基- 耐湿性能的测定(连续冷凝作用)ISO 627031 色漆和清漆 - 落锤试验ISO 627232 色漆和清漆 - 压痕试验(球体或棱锥体)ISO 644133 色漆和清漆用漆基 - 遮盖力的测定 - 第 1 部份:用于白色和浅色色漆的ISO 6504-1Kubelka-Munk 法34 色漆和清漆 - 弯曲试验(圆锥形心轴)ISO 686035 色漆和清漆 - 耐中性盐雾的测定ISO 725336 粉末涂料 - 第 7 部份:烘烤质量损失的测定ISO 8130-737 粉末涂料 - 第 9 部份:取样ISO 8130-938 金属的磷酸盐转化膜 - 确定要求的方法ISO 971739 化学转化膜 - 铝及铝合金上的漂洗和不漂洗铬酸盐转化膜ISO 1054640 人造气氛腐蚀试验 - 盐雾试验ISO 922741 金属材料上的转化膜- 单位面积上膜层质量的测量- 重量法ISO 389242 试验方法标准盐雾试验ASTM B11743 试验方法标准醋酸 - 盐雾试验ASTM B28744 试验方法标准铜加速的醋酸 - 盐雾试验( CASS试验)ASTM B36845 试验方法标准用锥形挠曲机试验附着的有机涂层的伸长ASTM D52246 试验方法标准镜面光泽ASTM D52347 方法标准试验色漆、清漆、喷漆和有关产品用钢板的制备ASTM D60948 方法标准评定涂漆钢材表面生锈等级ASTM D61049 方法标准外用色漆粉化程度的评定ASTM D65950 方法标准色漆起泡程度的测定ASTM D71451 方法标准有机涂层干膜厚度的测定ASTM D100552 方法标准在钢板上油漆的户外暴露试验ASTM D101453 方法标准在非磁性金属底材上的色漆、清漆、喷漆及有关产品的非ASTM D1400金属涂层干膜厚度的测定54 试验方法标准清漆的弹性或柔韧性ASTM D164255 试验方法标准清漆干膜的耐水性和耐碱性ASTM D164756 方法标准涂漆用铝与铝合金表面的处理ASTM D173057 方法标准涂漆用热浸铝表面处理ASTM D173158 方法标准涂漆用镁合金表面的处理ASTM D173259 方法标准色漆、清漆、喷漆及其有关产品试验用铝合金样板的处理ASTM D173360 试验方法标准用圆柱轴装置试验附着的有机涂层的伸长ASTM D173761 试验方法标准有机涂层的附着力ASTM D219762 方法标准试验色漆、清漆、喷漆及其有关产品用的热浸、非钝化镀ASTM D2201锌钢板的处理63 试验方法标准有机涂层抗快速变型(冲击)的作用ASTM D279464 试验方法标准涂层抗碎裂性ASTM D317065 试验方法标准漆膜孔隙率ASTM D325866 试验方法标准用胶带试验测定附着力ASTM D335967 试验方法标准用铅笔试验测定漆膜厚度ASTM D336368 推荐作法标准用磁场法或涡流法(电场法)测定涂层厚度ASTM E37669 试验方法标准管道涂层的耐冲击性(石灰石落降试验)ASTM G1370 试验方法标准管道涂层的耐冲击性(落锤试验)ASTM G1471 试验方法标准管道涂层的耐穿透性(圆头棒法)ASTM G17。
钢铁表面处理标准及对比说明

钢铁表面主要表面处理标准GB8923-88 中国国家标准ISO8501-1:1988 国际标准化组织标准SIS055900-1967 瑞典标准SSPC-SP2,3,5,6,7和10 美国钢结构涂装协会表面处理标准BS4232 英国标准DIN55928 德国标准JSRA SPSS 日本造船研究协会标准国标GB8923-88 对除锈等级描述:喷射或抛射除锈以字母“Sa”表示。
本标准订有四个除锈等级:Sa1 轻度的喷射或抛射除锈钢材表面应无可见的油脂和污垢,并且没有附着不牢的氧化皮,铁锈和油漆涂层等附着物。
Sa2 彻底的喷射或抛射除锈钢材表面应无可见的油脂和污垢,并且氧化皮,铁锈和油漆涂层等附着物已基本清除,其残留物应该是附着牢固的。
Sa2.5 非常彻底的喷射或抛射除锈钢材表面应无可见的油脂,污垢,氧化皮,铁锈和油漆涂层等附着物,任何残留的痕迹应仅是点状或条纹状的轻微色斑。
Sa3 钢材表面外观洁净的喷射或抛射除锈钢材表面应无可见的油脂,污垢,氧化皮,铁锈和油漆涂层等附着物,该表面应显示均匀的金属色泽。
手工和动力工具除锈以字母“St”表示。
本标准订有二个除锈等级:St2 彻底的手工和动力工具除锈钢材表面应无可见的油脂和污垢,并且没有附着不牢的氧化皮、铁锈和油漆涂层等附着物。
St3 非常彻底的手工和动力工具除锈钢材表面应无可见的油脂和污垢,并且没有附着不牢的氧化皮、铁锈和油漆涂层等附着物。
除锈应比St2更为彻底,底材显露部分的表面应具有金属光泽。
我国的除锈标准与相当的国外除锈标准对照表:注:SSPC中的Sp6比Sa2.5 略为严格,Sp2为人工钢丝刷除锈,Sp3为动力除锈。
表面粗糙度及其评定喷砂、抛丸、手工和动力除锈,其目的除达到前述一定的表面清洁度外,还会对钢铁表面造成一定的微观不平整度,即表面粗糙度。
对于涂漆前钢铁表面的粗糙度通常以一些主要的波峰和波谷间的高度值来表示。
钢铁表面粗糙度对漆膜的附着力,防腐蚀性能和保护寿命有很大影响。
表面处理表方法及选择应用

表面处理表示方法及选择应用零件或构件在工作过程中,由于其表面的磨损、腐蚀和疲劳造成了十分惊人的经济损失,因而我们技术工作者用物理、化学、机械等方法来改变零构件表面的组织成分,即表面处理,获得要求的性能,以提高产品的可靠性或延长其寿命。
另外通过表面处理还可以充分发挥材料的潜力和节约能源,降低生产成本。
所以设计者在进行零件、构件设计时应充分合理的选择各种表面处理。
今天在这里介绍常用金属的镀覆、化学、电化学处理层的表示方法,包括内容有:镀锌、镀铜、镀镍、镀镉、氧化、磷化、钝化等,按GB/T13911-1992的统一规定。
技术工作者一定要注意到国家正处在向国际通行标准接轨,旧的标准不断修订,新的标准不断颁布。
所以我们的图纸和技术文件努力把现行的最新国家标准贯彻到图中去,以跟上时代发展的步伐。
1、金属镀覆和化学处理表面方法用的各种符号1)基体材料表示符号(常用基体材料)材料名称符号铁、钢Fe铜、铜合金Cu铝、铝合金Al锌、锌合金Zn镁、镁合金Mg钛、钛合金Ti塑料PL(国际通用缩写)金属材料化学元素符号表示:合金材料用其主要成分的化学元素符号表示,非金属材料用国际通用缩写字母表示。
2)镀覆方法处理方法表示符号:方法名称符号(英文缩写)电镀Ep化学镀Ap电化学处理Et化学处理Ct3)化学和电化学处理名称的表示符号处理名称符号钝化P(不能理解为元素符号磷)氧化O电解着色Ec磷化Ph阳极氧化 A电镀锌铬酸盐处理Ca.电镀锌光亮铬酸盐处理C1Ab.电镀锌彩虹铬酸盐处理C1B (漂白型)常用c.电镀锌彩虹铬酸盐处理C2C (彩虹型)常用d.电镀锌深色铬酸盐处理C2D(符号-C;分级1、2;类型:A.B.C.D)2、金属镀覆和化学、电化学的表示方法(在图纸上的标记)1)金属镀覆表示方法:示例:例1.Fe/Ep.Cu10.Ni15b.Cr0.3mc.(钢材,电镀铜10μm,光亮镍15μm,微裂纹铬0.3μm)例2. Fe/Ep.Zn7.C2C(钢材。
表面处理标准大众13750-中文

保密,保留所有权力。
未经大众汽车集团标准部门的许可,不得复制或转换本文件的任何一部分。
合同当事方仅能通过B2B供应商平台“”获取本标准。
第2页删除了“带微小裂缝的光亮镀铬处理”表面保护类型(代码f320),(代替以Ofl-f350)。
制定了“镀锡处理”表面保护类型的涂层厚度(代码g...)。
增补了电解沉积铝和铝/猛合金涂层的表面保护类型(代码q600, q605, q610, q615)。
含六价铬Cr(VI)的“镀锌/铁合金处理”表面保护类型(代码r600, r605, r610, r620 和r630),限于可行的应用(不再允许用于新设计,有关替代类型请参见表A.1)。
增补了不含六价铬Cr(VI)的“镀锌/铁合金处理”表面保护类型(代码r301和r302)。
“镀锌/镍合金处理”表面保护类型(代码r640, r650, r660, r665, r670, r675),限于可行的应用(不再允许用于新设计,有关替代类型请参见表A.1)。
增补了不含六价铬Cr(VI)的“镀锌/镍合金处理”表面保护类型(代码r642, r643, r649, r672, r673和r677)。
增补了不含六价铬Cr(VI)的“复合镀层处理”表面保护类型(代码s611, s617, s621和s627)。
含六价铬Cr(VI)的“复合镀层处理”表面保护类型(代码s610, s615, s620和s625),限于可行的应用(不再允许用于新设计,有关替代类型请参见表A.1)。
“锌片涂层”表面保护类型(代码t300, t310, t320, t345, t600, t620和t645),限于可行的应用(不再允许用于新设计,有关替代类型请参见表A.1)。
增补了不含六价铬Cr(VI)的“锌片涂层”表面保护类型(代码t602, t611, t615和t647)。
重新增补了“表面镀黑抛光处理”表面保护类型(代码u110)。
含六价铬Cr(VI)的“渗铬处理”表面保护类型(代码v110),限于可行的应用(不再允许用于新设计,代替以Ofl-v111)。
表面处理标准标准版资料

40~60μm之间。 露SP出5 大喷多砂数出的白有处锈理斑点的钢板。
SP53 喷电砂动出工白具处理 以压下膜的 式两测个量标仪准检最测为的常速见度,较被慢广,泛不使适用合:打砂现场的随时测量,但是测得的结果可以保留存档。
粗糙度的测量工具主要有指针式测量仪和压膜式测量仪。指针式 S通S过PC喷砂:除钢去结所构有涂可装见委的员锈会迹、氧化皮、漆皮等。
为将了符达 合到要级求的打无砂色标透准明,的通胶常带采(用25-的30磨mm料宽是)抛长丸度、不钢小砂于(5棱cm角,砂紧)贴、在钢底丝材切上段,的然混后合撕物下混来合与比标例准根样据片实进际行生对产照情。况综合考虑。
测量仪对于现场检测非常方便,使用也很简单。压膜式测量仪检 S要P求5 清喷洁砂度出级白别处要理好于ISO 8502-3标准(参见我公司的清洁度标准样片)。
清洁度的检测采用在待测底材上粘贴胶带 的方法。将符合要求的无色透明的胶带 (25-30mm 宽)长度不小于5cm,紧贴在 底材上,然后撕下来与标准样片进行对照。 要求清洁度级别要好于ISO 8502-3标准(参 见我公司的清洁度标准样片)。如果底材 表面清洁度太差,油漆与底材之间的附着 力和油漆性能将会受到影响。
露出大多数的有锈斑点的钢板。
测的速度 较慢,不适合打砂现场的随时测量,但是测得的结果可
以保留存档。除此之外,还可以直接对照标准样板进行目视检测。
当用测量仪器对打砂粗糙度进行测量时,应在板面上均匀地选取
测量位置,对各不同部位的粗糙度进行检测,并针对不同的结果
对打砂设备作出适当的调整。
•
打砂清洁度标准(ISO 8502-3)
时浪费油漆的用量,而且车间底漆容易露底;粗糙度过小时影响 除一此、之外,打还砂可的以密直度接对照标准样板进行目视检测。
表面处理标准对照表
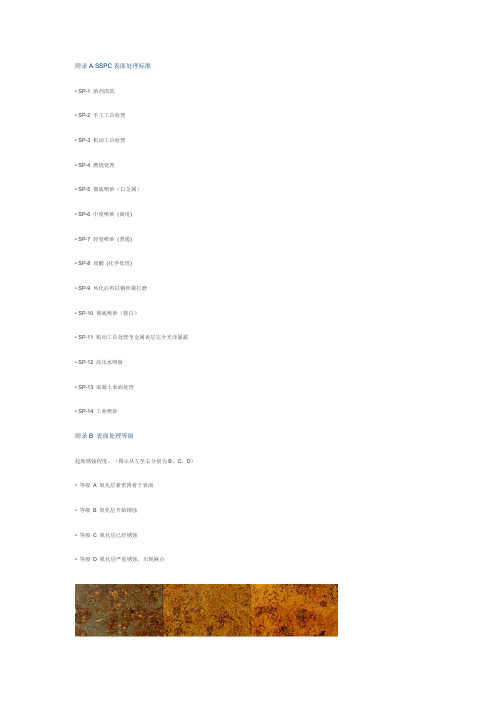
附录A SSPC表面处理标准• SP-1 溶剂清洗• SP-2 手工工具处理• SP-3 机动工具处理• SP-4 燃烧处理• SP-5 彻底喷砂(白金属)• SP-6 中度喷砂(商用)• SP-7 轻度喷砂(普通)• SP-8 浸酸(化学处理)• SP-9 风化后再以钢丝刷打磨• SP-10 彻底喷砂(接白)• SP-11 机动工具处理至金属表层完全光泽暴露• SP-12 高压水喷射• SP-13 混凝土表面处理• SP-14 工业喷砂附录B 表面处理等级起始锈蚀程度:(图示从左至右分别为B、C、D)• 等级A 氧化层紧密附着于表面• 等级B 氧化层开始锈蚀• 等级C 氧化层已经锈蚀• 等级D 氧化层严重锈蚀,出现麻点轻度喷砂:商用喷砂:近白喷砂:白金属喷砂:附录C 国际通用表面处理标准对比钢结构油漆委员会Steel Structure Painting Council (SSPC)国家防腐工程师协会National Association of Corrosion Engineers (NACE) 英国标准ISO 8501-1 / BSI BS 7079瑞典标准Swedish Standard国标GB-3092 / GB-8923-88关于表面处理等级1994年10月,NACE和SSPC发布了用于磨料清理的联合表面处理标准(这些标准大约相当于由最初的瑞典标准发展而来的ISO标准ISO8501-1SO-公布于1988年:NACE NO.I/SSPC-SP5“金属出白级喷砂” 相当于—Sa3“喷砂至可见清洁金属”NACE NO.2/SSPC-SP10“金属近于出白级喷砂” 相当于—Sa21/2“非常彻底的喷砂清理”NACE NO.3/SSPC-SP6“工业级喷砂” 相当于—Sa2“彻底的喷砂清理”NACE NO.4/SSPC-SP7“刷除锈级喷砂” 相当于—Sa1“轻喷砂清理”SSPC-SP1“溶剂清理” SSPC-SP2“手动工具清理” SSPC-SP11 “动力工具清理至裸钢”SSPC-SP8“酸洗” SSPC-SP3“动力工具清理” SSPC-SP11R “动力工具清理维修保养”一、金属(1) 新表面A.钢铁1.喷砂处理实践证明,无论是在施工现场还是在装配车间,喷砂处理都是除去锻痕的最有效方法。
表面处理表示方法及选择

镍镀层
Ep.Cu10bNi5b
Ep.Cu20bNi10b
Ep.Cu30bNi15b
Ep.Cu10bNi5s
Ep.Cu20bNi10s
Ep.Cu30bNi15s
Ep.Ni5m
Ep.Cu10bNi5m
Ep.Cu15bNi15m
铬镀层
Ep.Cu10bNi5b
Cr0.3b
Ep.Cu10bNi10b
双层
d
S
三层
d
-
普层
r
-
花纹
Pt
W
乳色
O
R
密封
Se
F
硬质
没有工业、锅炉和其他有害废气,如密封装置内部或空气调节装置的实验室内。
一般
温度:-40~+55℃,
相对湿度:不大于95%,
有少量工业、锅炉和其他有害废气,如无空气调节装置的机房内或不受太阳、雨、雪、雾及水份饱和的大气直接影响的室外。
恶劣
温度:-60~+85℃,
相对湿度:达98%,
有较多工业、锅炉和其他有害废气,如受太阳、雨、雪等直接影响及有害气源的室外。
Cr0.3b
Ep.Cu15bNi15b
Cr0.3b
Ep.Cu10bNi5b
Cr0.3s
Ep.Cu10bNi10b
Cr0.3s
Ep.Cu10bNi15b
Cr0.3s
表3 铜基体上镀覆
镀覆层
种 类
镀覆标记
良好
一般
恶劣
镍镀层
Ep.Ni5b
Ep.Ni10b
Ep.Ni15b
Ep.Ni5s
Ep.Ni10s
Ep.Ni15s
表面处理表示方法及选择
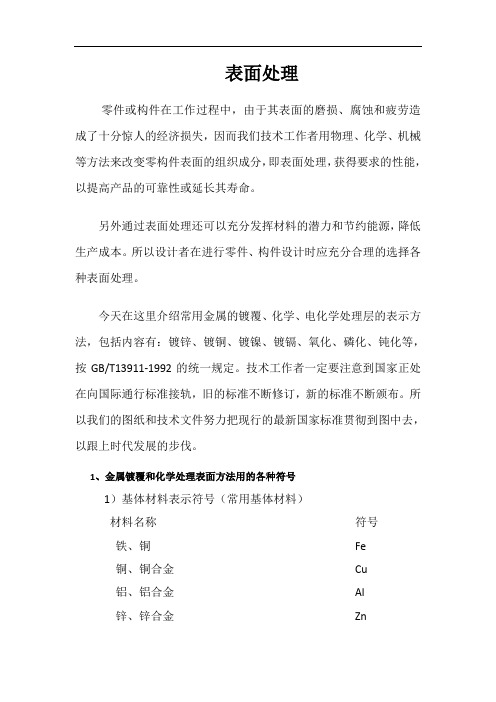
表面处理零件或构件在工作过程中,由于其表面的磨损、腐蚀和疲劳造成了十分惊人的经济损失,因而我们技术工作者用物理、化学、机械等方法来改变零构件表面的组织成分,即表面处理,获得要求的性能,以提高产品的可靠性或延长其寿命。
另外通过表面处理还可以充分发挥材料的潜力和节约能源,降低生产成本。
所以设计者在进行零件、构件设计时应充分合理的选择各种表面处理。
今天在这里介绍常用金属的镀覆、化学、电化学处理层的表示方法,包括内容有:镀锌、镀铜、镀镍、镀镉、氧化、磷化、钝化等,按GB/T13911-1992的统一规定。
技术工作者一定要注意到国家正处在向国际通行标准接轨,旧的标准不断修订,新的标准不断颁布。
所以我们的图纸和技术文件努力把现行的最新国家标准贯彻到图中去,以跟上时代发展的步伐。
1、金属镀覆和化学处理表面方法用的各种符号1)基体材料表示符号(常用基体材料)材料名称符号铁、铜Fe铜、铜合金Cu铝、铝合金Al锌、锌合金Zn镁、镁合金Mg钛、钛合金Ti塑料PL(国际通用缩写)金属材料化学元素符号表示:合金材料用其主要成分的化学元素符号表示,非金属材料用国际通用缩写字母表示。
2)镀覆方法处理方法表示符号:方法名称符号(英文缩写)电镀Ep化学镀Ap电化学处理Et化学处理Ct3)化学和电化学处理名称的表示符号处理名称符号钝化P(不能理解为元素符号磷)氧化O电解着色Ec磷化Ph阳极氧化 A电镀锌铬酸盐处理 Ca.电镀锌光亮铬酸盐处理C1Ab.电镀锌彩虹铬酸盐处理C1B (漂白型)常用c.电镀锌彩虹铬酸盐处理C2C (彩虹型)常用d.电镀锌深色铬酸盐处理C2D(符号-C;分级1、2;类型:A.B.C.D)2、金属镀覆和化学、电化学的表示方法(在图纸上的标记)1)金属镀覆表示方法:示例:例1.Fe/Ep.CuN15bCy0.3mc.(钢材,电镀铜10μm,光亮镍15μm,微裂纹铬0.3μm)例2. Fe/Ep.Zn7.C2C(钢材。
表面处理标准汇总
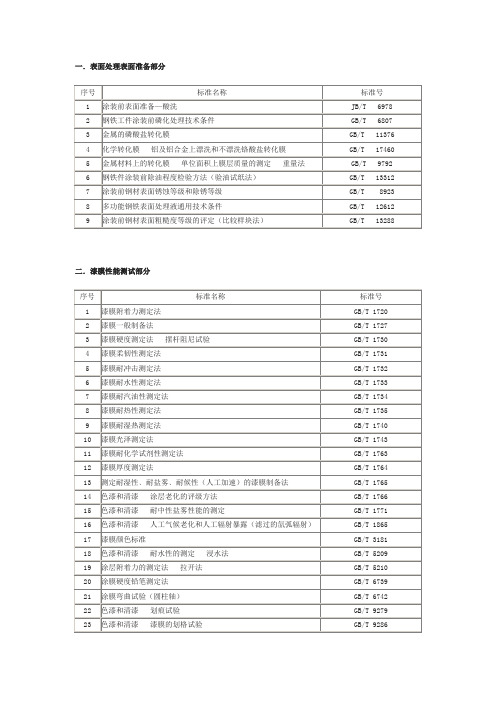
61
试验方法标准有机涂层的附着力
ASTM D2197
62
方法标准试验色漆、清漆、喷漆及其有关产品用的热浸、非钝化镀锌钢板的处理
ASTM D2201
63
试验方法标准有机涂层抗快速变型(冲击)的作用
ASTM D2794
64
试验方法标准涂层抗碎裂性
ASTM D3170
65
试验方法标准漆膜孔隙率
GB/T 9286
24
色漆和清漆杯突试验
GB/T 9753
25
色漆和清漆不含金属颜料的色漆漆膜之20°﹑60°和85°镜面光泽的测定
GB/T 9754
26
人造气氛腐蚀试验盐雾试验
GB/T 10125
27
金属和其他非有机覆盖层通常凝露条件下的二氧化硫腐蚀试验
GB/T 9789
28
色漆和清漆漆膜厚度的测定
2
电泳漆电导率测定法
HG/T 2-1047
3
电泳漆泳透力测定法
HG/T 2-1048
4
电泳漆库仑效率测定法
HG/T 2-1049
5
电泳漆沉积量测定法
HG/T 2-1050
6
电泳漆泳透力测定法(钢管法)
HG/T 2-1051
7
涂料粘度测定法
GB/T 1723
8
涂料细度测定法
GB/T 1724
9
涂料固体含量测定法
涂装作业安全规程静电喷枪及其辅助装置安全技术条件
GB 14773
3
涂装作业安全规程涂漆工艺安全及其通风净化
GB 6514
4
涂装作业安全规程喷漆室安全技术规定
GB 14444
- 1、下载文档前请自行甄别文档内容的完整性,平台不提供额外的编辑、内容补充、找答案等附加服务。
- 2、"仅部分预览"的文档,不可在线预览部分如存在完整性等问题,可反馈申请退款(可完整预览的文档不适用该条件!)。
- 3、如文档侵犯您的权益,请联系客服反馈,我们会尽快为您处理(人工客服工作时间:9:00-18:30)。
附录A SSPC表面处理标准
• SP-1 溶剂清洗
• SP-2 手工工具处理
• SP-3 机动工具处理
• SP-4 燃烧处理
• SP-5 彻底喷砂(白金属)
• SP-6 中度喷砂(商用)
• SP-7 轻度喷砂(普通)
• SP-8 浸酸(化学处理)
• SP-9 风化后再以钢丝刷打磨
• SP-10 彻底喷砂(接白)
• SP-11 机动工具处理至金属表层完全光泽暴露• SP-12 高压水喷射
• SP-13 混凝土表面处理
• SP-14 工业喷砂
附录B 表面处理等级
起始锈蚀程度:(图示从左至右分别为B、C、D)• 等级A 氧化层紧密附着于表面
• 等级B 氧化层开始锈蚀
• 等级C 氧化层已经锈蚀
• 等级D 氧化层严重锈蚀,出现麻点
轻度喷砂:
商用喷砂:
近白喷砂:
白金属喷砂:
附录C 国际通用表面处理标准对比
钢结构油漆委员会Steel Structure Painting Council (SSPC)
国家防腐工程师协会National Association of Corrosion Engineers (NACE) 英国标准ISO 8501-1 / BSI BS 7079
瑞典标准Swedish Standard
国标GB-3092 / GB-8923-88
关于表面处理等级
1994年10月,NACE和SSPC发布了用于磨料清理的联合表面处理标准(这些标准大约相当于由最初的瑞典标准发展而来的ISO标准ISO8501-1SO-公布于1988年:
NACE NO.I/SSPC-SP5“金属出白级喷砂” 相当于—Sa3“喷砂至可见清洁金属”
NACE NO.2/SSPC-SP10“金属近于出白级喷砂” 相当于—Sa21/2“非常彻底的喷砂清理”
NACE NO.3/SSPC-SP6“工业级喷砂” 相当于—Sa2“彻底的喷砂清理”
NACE NO.4/SSPC-SP7“刷除锈级喷砂” 相当于—Sa1“轻喷砂清理”
SSPC-SP1“溶剂清理” SSPC-SP2“手动工具清理” SSPC-SP11 “动力工具清理至裸钢”
SSPC-SP8“酸洗” SSPC-SP3“动力工具清理” SSPC-SP11R “动力工具清理维修保养”
一、金属
(1) 新表面
A.钢铁
1.喷砂处理
实践证明,无论是在施工现场还是在装配车间,喷砂处理都是除去锻痕的最有效方法。
这是成功使用各种高性能油漆系统的必要处理手段。
喷砂处理的清洁程度必须规定一个通用标准,最好有标准图片参考,并且在操作过程中规定并控制表面粗糙度。
表面粗糙度取决于几方面的因素,但主要受到所使用的磨料种类及其粒径和施力方法(如高压气流和离心力)的影响。
对于高压气流,喷嘴的高压程及其对工件的角度是表面粗糙度的决定因素;而对于离心力或机械喷射方法来说,喷射操作中的速率是非常重要的。
喷砂处理完成后必须立即上底漆。
所有油脂及污染物必须在上漆前清除。
2.湿喷砂或砂洗
这种方法是使用砂浆及高压水来除去旧漆、锻痕及蚀物。
使用这种方法,极大程度上克服了普通喷砂处理中粉尘对健康的危害。
同样,表面粗糙度及清洁效率取决于水压及砂浆中磨料的浓度。
这种处理方法的一个主要缺点是清洁好的钢铁表面将立即开始生锈,因此与普通喷砂处理比较,表现出一种较次的表面。
要在水中加入阻锈剂但必须十分小心,因为有些阻锈剂会影响随后漆膜的性能。
3.车间预上底钢结构
在车间经过自动喷砂处理并在装配前预上底漆的钢结构,在施以最后的保护性油漆系统前,通常需要进行特殊处理。
所有损伤区域,会继续生锈,这些区域必须被重新喷砂处理,或用手工方法彻底清洁至可接受的标准。
在施以高性能油漆体系前,通常需要重新喷砂处理,这需要在所有可能的场合做具体的规定。
这种处理方法也通常用于焊接及焊接前无法上底漆的钢结构连接部分。
4.酸洗清洁酸洗清洁
是一种古老的车间处理方法,用于除去钢铁的锻痕。
目前仍有几个步骤在被使用,通常为一个双重体系包括酸腐蚀及酸钝化。
酸清洁的一个缺点是它将钢铁表面清洁了但没有一个粗糙度,而粗糙度则有助于提高重防腐油漆的附着力。
5.火焰清洁
当今,火焰清洁过程已经很少被使用。
与其它低标准表面处理方法如手工工具清洁或低等级喷砂处理一样,它们不能除去那些深深附(SSPC SP8)着的锻痕及锈迹,因而不适合用于尖端重防腐油漆。
火焰清洁的主要优点在于它能除去一些化学污染及保持表面温暖干燥,这有助于底漆的干燥并增强附着力。
6.电动工具清洁
这种方法是使用手持电动工具如旋转钢丝刷、砂轮或砂磨机,除去表面之疏松锻痕,损伤漆膜及锈蚀物。
瑞典标准等级SIS 055900包括了相应的图片标准。
(SSPC SP3)
7.手工工具清洁
这是一种传统的清洁方法。
它使用钢丝刷刷、砂纸打磨、刮、凿或(SSPC SP2)其组合等方法,除去表面之疏松锻痕,漆膜及锈蚀物。
8.溶剂清洗
这不是一种真正的表面处理,但是可以用溶剂或乳液除去表面的油脂及其它类似的污染物。
溶剂清洗不能完全除去油型污染物,它只能用于清洁过程的一部分并需包括水溶性清洗剂的冲洗。
(SSPC SP1)
表面处理标准比较
描述美国标准英国标准瑞典标准
SSPC SP BS 4232 SIS 055900
溶剂清洗SSPC SP1
手工清洁SSPC SP2 ST2
机械清洁SSPC SP3 ST3
气凿清洁新钢铁SSPC SP4
喷砂处理白金属SSPC SP5 一级SA3
喷砂处理近白金属SSPC SP10 二级SA2.5
喷砂处理商用级SSPC SP6 三级SA2
喷砂处理普能级SSPC SP7
化学清洁SSPC SP8。