浮法玻璃熔窑设计的改进
浮法玻璃退火窑的尺寸与结构优化设计

浮法玻璃退火窑的尺寸与结构优化设计引言:随着现代建筑、汽车、光电等行业的快速发展,对于玻璃的需求量也越来越大。
浮法玻璃作为一种广泛应用于各个领域的玻璃类型,其生产工艺和设备起到了至关重要的作用。
浮法玻璃退火窑作为浮法生产线的关键设备之一,尺寸与结构的优化设计是确保玻璃熔化和退火过程的顺利进行的重要因素之一。
1. 退火过程对浮法玻璃的影响退火过程对浮法玻璃的性能和质量有着重要的影响。
在退火过程中,玻璃会被加热至高温,然后缓慢冷却以达到消除内部应力、提高光学性能、改善表面平整度等目的。
合理的退火过程能够保证玻璃的机械性能和稳定性,同时降低开裂率,提高玻璃的品质。
2. 浮法玻璃退火窑的尺寸优化2.1 窑室的尺寸设计窑室的尺寸设计直接关系到退火过程中玻璃的受热和冷却速率。
一般来说,窑室的尺寸应十分均匀地加热玻璃,并确保能够容纳需处理的玻璃板数量。
尺寸不当会导致部分玻璃板受热过度,使得退火效果不均匀。
2.2 窑室的高度设计窑室的高度设计直接影响到玻璃板在退火过程中的变形和应力消除。
窑室过高会导致玻璃板下弯,而窑室过矮会导致玻璃板上弯,都会影响玻璃的平整度和质量。
因此,合理的窑室高度设计是非常重要的。
3. 浮法玻璃退火窑的结构优化3.1 顶部结构设计顶部结构通常由隔热层和电加热系统组成。
对于隔热层的优化设计,应选用高效的保温材料,减少热量损失。
电加热系统应合理布置,确保窑室内的温度分布均匀,避免温度集中和冷热点的出现。
3.2 底部结构设计底部结构主要包括底样、输送系统和冷却系统。
优化设计底样和输送系统能够确保玻璃板的稳定输送和定位,减少进出窑室的阻力和损失。
冷却系统应具备良好的冷却性能,确保玻璃板能够在最短时间内进行均匀冷却。
3.3 侧壁结构设计侧壁结构设计主要包括隔热层和加热系统。
隔热层的设计应具有良好的隔热性能,并且能够抵抗窑内高温的侵蚀作用。
加热系统应合理分布在侧壁上,以确保窑室内的温度分布均匀。
4. 浮法玻璃退火窑结构的优化方法4.1 借助数值模拟软件进行优化设计利用数值模拟软件,如有限元分析软件,可以对退火过程进行模拟,预测玻璃板的温度分布和应力分布,进而确定合理的尺寸和结构参数。
浅谈提高浮法玻璃工艺水平的技术改造策略
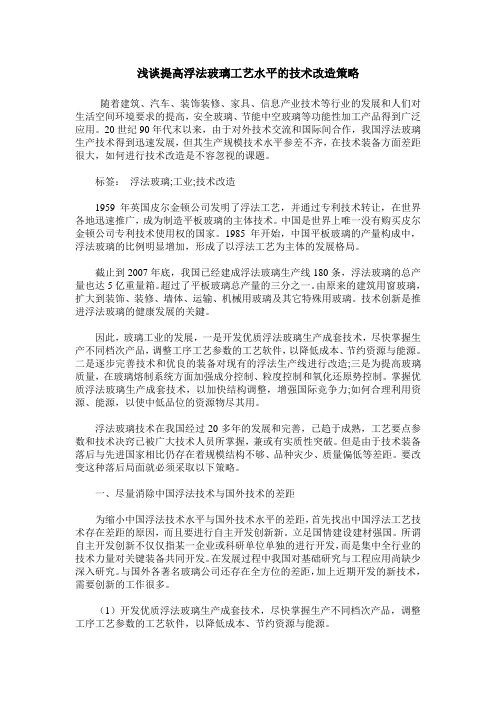
浅谈提高浮法玻璃工艺水平的技术改造策略随着建筑、汽车、装饰装修、家具、信息产业技术等行业的发展和人们对生活空间环境要求的提高,安全玻璃、节能中空玻璃等功能性加工产品得到广泛应用。
20世纪90年代末以来,由于对外技术交流和国际间合作,我国浮法玻璃生产技术得到迅速发展,但其生产规模技术水平参差不齐,在技术装备方面差距很大,如何进行技术改造是不容忽视的课题。
标签:浮法玻璃;工业;技术改造1959年英国皮尔金顿公司发明了浮法工艺,并通过专利技术转让,在世界各地迅速推广,成为制造平板玻璃的主体技术。
中国是世界上唯一没有购买皮尔金顿公司专利技术使用权的国家。
1985年开始,中国平板玻璃的产量构成中,浮法玻璃的比例明显增加,形成了以浮法工艺为主体的发展格局。
截止到2007年底,我国已经建成浮法玻璃生产线180条,浮法玻璃的总产量也达5亿重量箱。
超过了平板玻璃总产量的三分之一。
由原来的建筑用窗玻璃,扩大到装饰、装修、墙体、运输、机械用玻璃及其它特殊用玻璃。
技术创新是推进浮法玻璃的健康发展的关鍵。
因此,玻璃工业的发展,一是开发优质浮法玻璃生产成套技术,尽快掌握生产不同档次产品,调整工序工艺参数的工艺软件,以降低成本、节约资源与能源。
二是逐步完善技术和优良的装备对现有的浮法生产线进行改造;三是为提高玻璃质量,在玻璃熔制系统方面加强成分控制、粒度控制和氧化还原势控制。
掌握优质浮法玻璃生产成套技术,以加快结构调整,增强国际竞争力;如何合理利用资源、能源,以使中低品位的资源物尽其用。
浮法玻璃技术在我国经过20多年的发展和完善,已趋于成熟,工艺要点参数和技术决窍已被广大技术人员所掌握,兼或有实质性突破。
但是由于技术装备落后与先进国家相比仍存在着规模结构不够、品种灾少、质量偏低等差距。
要改变这种落后局面就必须采取以下策略。
一、尽量消除中国浮法技术与国外技术的差距为缩小中国浮法技术水平与国外技术水平的差距,首先找出中国浮法工艺技术存在差距的原因,而且要进行自主开发创新新。
浮法玻璃熔窑中溢流液面高度的控制与优化
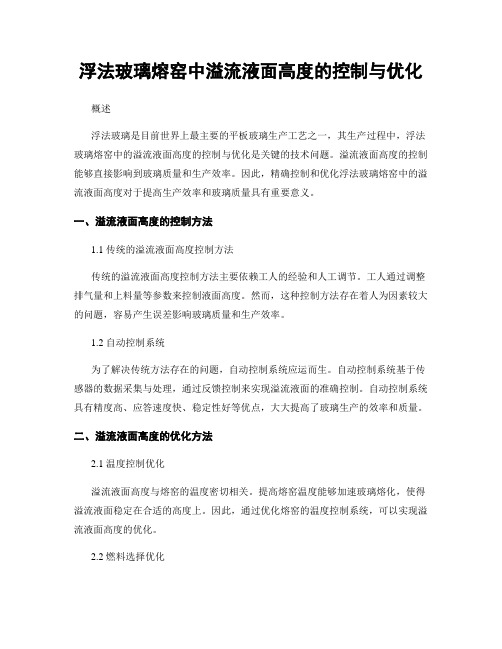
浮法玻璃熔窑中溢流液面高度的控制与优化概述浮法玻璃是目前世界上最主要的平板玻璃生产工艺之一,其生产过程中,浮法玻璃熔窑中的溢流液面高度的控制与优化是关键的技术问题。
溢流液面高度的控制能够直接影响到玻璃质量和生产效率。
因此,精确控制和优化浮法玻璃熔窑中的溢流液面高度对于提高生产效率和玻璃质量具有重要意义。
一、溢流液面高度的控制方法1.1 传统的溢流液面高度控制方法传统的溢流液面高度控制方法主要依赖工人的经验和人工调节。
工人通过调整排气量和上料量等参数来控制液面高度。
然而,这种控制方法存在着人为因素较大的问题,容易产生误差影响玻璃质量和生产效率。
1.2 自动控制系统为了解决传统方法存在的问题,自动控制系统应运而生。
自动控制系统基于传感器的数据采集与处理,通过反馈控制来实现溢流液面的准确控制。
自动控制系统具有精度高、应答速度快、稳定性好等优点,大大提高了玻璃生产的效率和质量。
二、溢流液面高度的优化方法2.1 温度控制优化溢流液面高度与熔窑的温度密切相关。
提高熔窑温度能够加速玻璃熔化,使得溢流液面稳定在合适的高度上。
因此,通过优化熔窑的温度控制系统,可以实现溢流液面高度的优化。
2.2 燃料选择优化燃料选择也对溢流液面高度有一定的影响。
不同的燃料在燃烧过程中会产生不同的热量和气体排放。
选用合适的燃料,可以控制溢流液面高度,并达到优化的效果。
2.3 上料量控制优化上料量直接影响熔窑中的液面高度。
合理控制上料量可以实现液面高度的优化。
通过对上料量进行监测和调节,可以使得液面高度保持在理想的状态。
2.4 气氛控制优化熔窑内的气氛对溢流液面高度也有一定的影响。
通过控制氧气含量、燃烧气体的流速和排放气体的排放速度等,可以优化熔窑内的气氛,从而控制和优化液面高度。
2.5 自动化技术优化自动化技术在溢流液面高度的控制与优化中扮演着关键的角色。
通过引入先进的传感器、仪表和控制算法,可以实现自动化的溢流液面控制,提高生产的稳定性和质量。
浮法玻璃熔窑中沉降池设计与优化
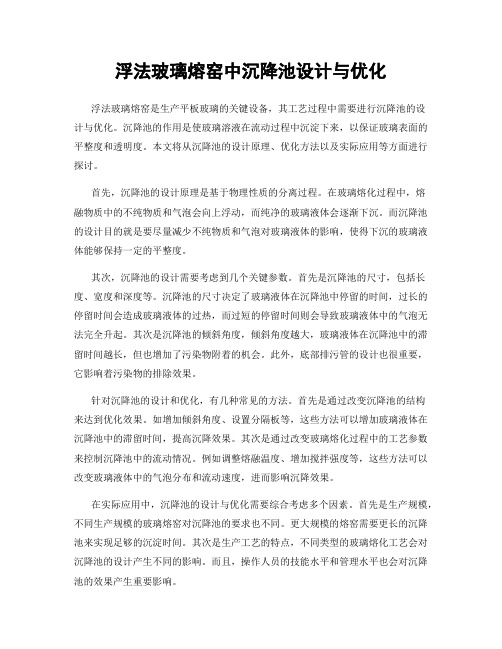
浮法玻璃熔窑中沉降池设计与优化浮法玻璃熔窑是生产平板玻璃的关键设备,其工艺过程中需要进行沉降池的设计与优化。
沉降池的作用是使玻璃溶液在流动过程中沉淀下来,以保证玻璃表面的平整度和透明度。
本文将从沉降池的设计原理、优化方法以及实际应用等方面进行探讨。
首先,沉降池的设计原理是基于物理性质的分离过程。
在玻璃熔化过程中,熔融物质中的不纯物质和气泡会向上浮动,而纯净的玻璃液体会逐渐下沉。
而沉降池的设计目的就是要尽量减少不纯物质和气泡对玻璃液体的影响,使得下沉的玻璃液体能够保持一定的平整度。
其次,沉降池的设计需要考虑到几个关键参数。
首先是沉降池的尺寸,包括长度、宽度和深度等。
沉降池的尺寸决定了玻璃液体在沉降池中停留的时间,过长的停留时间会造成玻璃液体的过热,而过短的停留时间则会导致玻璃液体中的气泡无法完全升起。
其次是沉降池的倾斜角度,倾斜角度越大,玻璃液体在沉降池中的滞留时间越长,但也增加了污染物附着的机会。
此外,底部排污管的设计也很重要,它影响着污染物的排除效果。
针对沉降池的设计和优化,有几种常见的方法。
首先是通过改变沉降池的结构来达到优化效果。
如增加倾斜角度、设置分隔板等,这些方法可以增加玻璃液体在沉降池中的滞留时间,提高沉降效果。
其次是通过改变玻璃熔化过程中的工艺参数来控制沉降池中的流动情况。
例如调整熔融温度、增加搅拌强度等,这些方法可以改变玻璃液体中的气泡分布和流动速度,进而影响沉降效果。
在实际应用中,沉降池的设计与优化需要综合考虑多个因素。
首先是生产规模,不同生产规模的玻璃熔窑对沉降池的要求也不同。
更大规模的熔窑需要更长的沉降池来实现足够的沉淀时间。
其次是生产工艺的特点,不同类型的玻璃熔化工艺会对沉降池的设计产生不同的影响。
而且,操作人员的技能水平和管理水平也会对沉降池的效果产生重要影响。
综上所述,浮法玻璃熔窑中沉降池的设计与优化对于保证玻璃产品的质量至关重要。
设计和优化沉降池需要考虑多个因素,包括沉降池的尺寸、倾斜角度和底部排污管等参数。
提高玻璃液熔化质量的几个措施
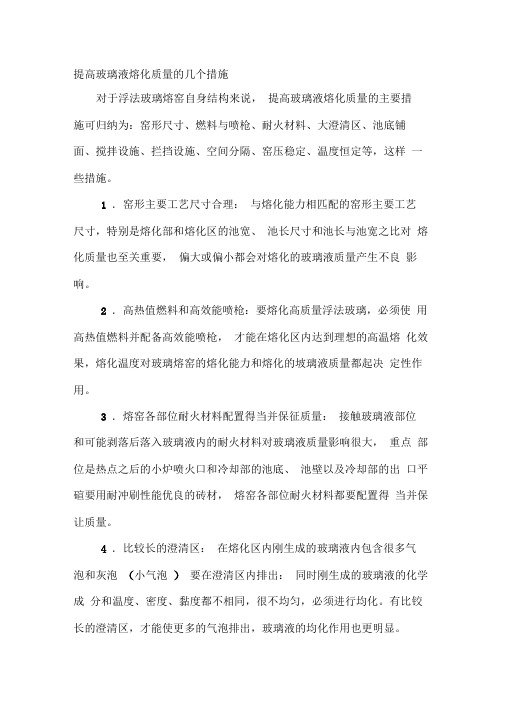
提高玻璃液熔化质量的几个措施对于浮法玻璃熔窑自身结构来说,提高玻璃液熔化质量的主要措施可归纳为:窑形尺寸、燃料与喷枪、耐火材料、大澄清区、池底铺面、搅拌设施、拦挡设施、空间分隔、窑压稳定、温度恒定等,这样一些措施。
1.窑形主要工艺尺寸合理:与熔化能力相匹配的窑形主要工艺尺寸,特别是熔化部和熔化区的池宽、池长尺寸和池长与池宽之比对熔化质量也至关重要,偏大或偏小都会对熔化的玻璃液质量产生不良影响。
2.高热值燃料和高效能喷枪:要熔化高质量浮法玻璃,必须使用高热值燃料并配备高效能喷枪,才能在熔化区内达到理想的高温熔化效果,熔化温度对玻璃熔窑的熔化能力和熔化的坡璃液质量都起决定性作用。
3.熔窑各部位耐火材料配置得当并保征质量:接触玻璃液部位和可能剥落后落入玻璃液内的耐火材料对玻璃液质量影响很大,重点部位是热点之后的小炉喷火口和冷却部的池底、池壁以及冷却部的出口平碹要用耐冲刷性能优良的砖材,熔窑各部位耐火材料都要配置得当并保让质量。
4.比较长的澄清区:在熔化区内刚生成的玻璃液内包含很多气泡和灰泡(小气泡)要在澄清区内排出:同时刚生成的玻璃液的化学成分和温度、密度、黏度都不相同,很不均匀,必须进行均化。
有比铰长的澄清区,才能使更多的气泡排出,玻璃液的均化作用也更明显。
5. 窑池底部的池底铺面结构:玻璃液在窑池底部的流动(常与表面流动方向相反)会对池底产生冲刷,被冲刷掉的池底耐火材抖粉末都要进入玻璃液内,而且不易熔化掉,是产生玻璃液熔化缺陷的重要原因之一,池底采用耐冲刷性能好的耐火材料就可比较好地解决这一问题。
6 .玻璃液搅拌装置:搅拌作用能明显地提高玻璃液的均匀性,减少由于玻璃液的化学成分、温度、密度、黏度等不均匀造成的玻璃缺陷。
常见的搅拌装置有水平搅拌器和垂直搅拌器,相比较而言,水平搅拌器结构简单,比较耐用,而垂直搅拌器的搅拌作用更好一些。
7.玻璃液表面漂浮物拦挡装置:在玻璃熔窑内,玻璃液表面有时会出现一些漂浮物,这些漂浮物主要来自两个原因:一是未熔化的玻璃配合料渣滓;二是熔窑运行中窑体结构上剥落或掉落的耐火材料颗粒或碎块。
浮法玻璃熔窑的合理设计(连载二)
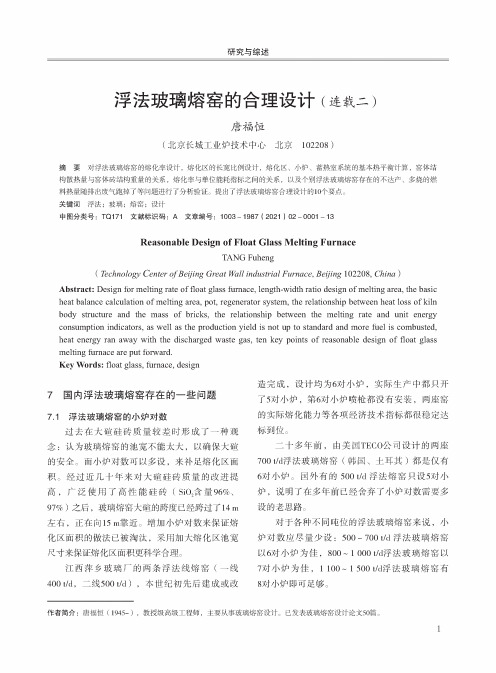
浮法玻璃熔窑的合理设计(连载二)唐福恒(北京长城工业炉技术中心北京102208)摘要对浮法玻璃熔窑的熔化率设计,熔化区的长宽比例设计,熔化区、小炉、蓄热室系统的基本热平衡计算,窑体结构散热量与窑体砖结构重量的关系,熔化率与单位能耗指标之间的关系,以及个别浮法玻璃熔窑存在的不达产、多烧的燃料热量随排岀废气跑掉了等问题进行了分析验证。
提岀了浮法玻璃熔窑合理设计的10个要点。
关键词浮法;玻璃;熔窑;设计中图分类号:TQ171文献标识码:A文章编号:1003-1987(2021)02-0001-13Reasonable Design of Float Glass Melting FurnaceTANG Fuheng(Technology Center ofBeijing Great Wall industrial Furnace,Beijing10220&China) Abstract:Design for melting rate of float glass furnace,length-width ratio design of melting area,the basic heat balance calculation of melting area,pot,regenerator system,the relationship between heat loss of kiln body structure and the mass of bricks,the relationship between the melting rate and unit energy consumption indicators,as well as the production yield is not up to standard and more fuel is combusted, heat energy ran away with the discharged waste gas,ten key points of reasonable design of float glass melting furnace are put forward.Key Words:float glass,furnace,design7国内浮法玻璃熔窑存在的一些问题7.1浮法玻璃熔窑的小炉对数过去在大確硅砖质量较差时形成了一种观念:认为玻璃熔窑的池宽不能太大,以确保大確的安全。
燃煤气浮法玻璃熔窑经过改进也具备优点

燃煤气浮法玻璃熔窑经过改进也具备优点一、概述目前我国的浮法玻璃熔窑以重油为燃料的居多,主要是重油的热值高,火焰刚性好,射程远,适合浮法玻璃熔窑不断扩大的发展趋势,而且使用重油为燃料的玻璃熔窑构造简单,工艺流程简洁,附属设施少,操作控制容易,尤其是烤窑至过大火,此后室内温度较之烧煤气窑容易控制。
然而,以煤气为燃料的玻璃熔窑历史悠久,在我国早期的平板玻璃熔窑中,大部分是以煤或发生炉煤气为燃料的。
随着煤气发生炉的不断改良,如二段炉,燃煤气熔窑的低成本优势日益表达出来。
目前平板玻璃市场竞争日趋激烈,市场低迷,而重油价格见涨(1700元/吨),各生产厂家在提高玻璃质量的同时,也在想方设法降低玻璃的生产成本,努力使企业安然度过平板玻璃市场的萧条期。
在这种形势下,一些以发生炉煤气为燃料的浮法玻璃熔窑开始开展技术改造,在满足生产要求的同时,要使熔窑的各项指标与燃油的熔窑相接近,以表达出燃煤气熔窑低成本的优势,使企业立于不败之地。
二、箱式蓄热室在上世纪九十年代以前,我国的燃煤气熔窑的空、煤气蓄热室均为上升道构造。
此类蓄热室的空、煤气预热温度较低,蓄热室热效率差,熔窑的能耗很高,一般每公斤玻璃液需耗0.50~0.65公斤标准煤[1].九十年代初,杭玻率先在浮法一线上尝试将上升道空气蓄热室改成箱式蓄热室,并获得成功。
从而将燃煤气熔窑的能耗降低了约10%.由于箱式蓄热室取消了空气蓄热室的半圆碹和承重碹,使蓄热室的构造更简单,寿命更长。
如杭玻的燃煤气350t/d浮法熔窑在不热修格子体的情况下寿命到达了六年,能耗约为0.40公斤标准煤/每公斤玻璃液。
三、小炉蓄热室的设计燃煤气浮法玻璃熔窑技改设计中的最大难点就是小炉和蓄热室的设计,这也是燃油熔窑和燃煤气熔窑的根本区别。
小炉的设计在浮法玻璃熔窑的煤气小炉设计中,目前已形成了一些定式,如小炉斜坡碹的下倾角是25°,底板上倾角约3°,小炉舌头伸出长度为400~450mm等。
浮法玻璃退火窑的工作条件与工艺优化
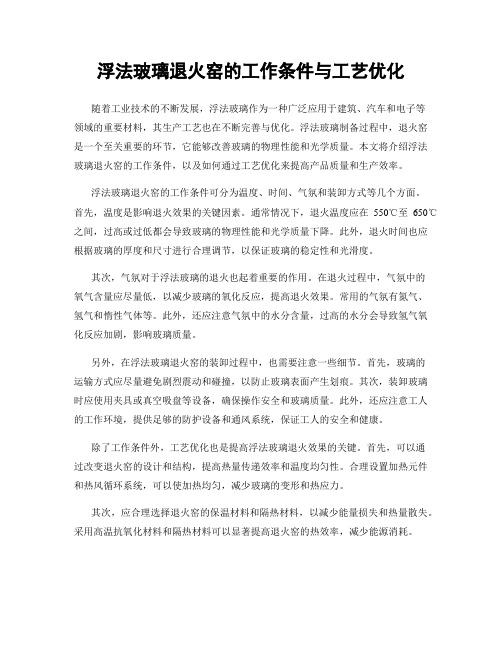
浮法玻璃退火窑的工作条件与工艺优化随着工业技术的不断发展,浮法玻璃作为一种广泛应用于建筑、汽车和电子等领域的重要材料,其生产工艺也在不断完善与优化。
浮法玻璃制备过程中,退火窑是一个至关重要的环节,它能够改善玻璃的物理性能和光学质量。
本文将介绍浮法玻璃退火窑的工作条件,以及如何通过工艺优化来提高产品质量和生产效率。
浮法玻璃退火窑的工作条件可分为温度、时间、气氛和装卸方式等几个方面。
首先,温度是影响退火效果的关键因素。
通常情况下,退火温度应在550℃至650℃之间,过高或过低都会导致玻璃的物理性能和光学质量下降。
此外,退火时间也应根据玻璃的厚度和尺寸进行合理调节,以保证玻璃的稳定性和光滑度。
其次,气氛对于浮法玻璃的退火也起着重要的作用。
在退火过程中,气氛中的氧气含量应尽量低,以减少玻璃的氧化反应,提高退火效果。
常用的气氛有氮气、氢气和惰性气体等。
此外,还应注意气氛中的水分含量,过高的水分会导致氢气氧化反应加剧,影响玻璃质量。
另外,在浮法玻璃退火窑的装卸过程中,也需要注意一些细节。
首先,玻璃的运输方式应尽量避免剧烈震动和碰撞,以防止玻璃表面产生划痕。
其次,装卸玻璃时应使用夹具或真空吸盘等设备,确保操作安全和玻璃质量。
此外,还应注意工人的工作环境,提供足够的防护设备和通风系统,保证工人的安全和健康。
除了工作条件外,工艺优化也是提高浮法玻璃退火效果的关键。
首先,可以通过改变退火窑的设计和结构,提高热量传递效率和温度均匀性。
合理设置加热元件和热风循环系统,可以使加热均匀,减少玻璃的变形和热应力。
其次,应合理选择退火窑的保温材料和隔热材料,以减少能量损失和热量散失。
采用高温抗氧化材料和隔热材料可以显著提高退火窑的热效率,减少能源消耗。
另外,在退火过程中,可以引入自动化控制系统,实现温度、时间和气氛等参数的自动控制和监测。
通过精确的温度控制和及时的数据反馈,可以提高工艺的稳定性和一致性,减少人为因素对退火效果的影响。
浮法玻璃熔窑节能技术及途径.
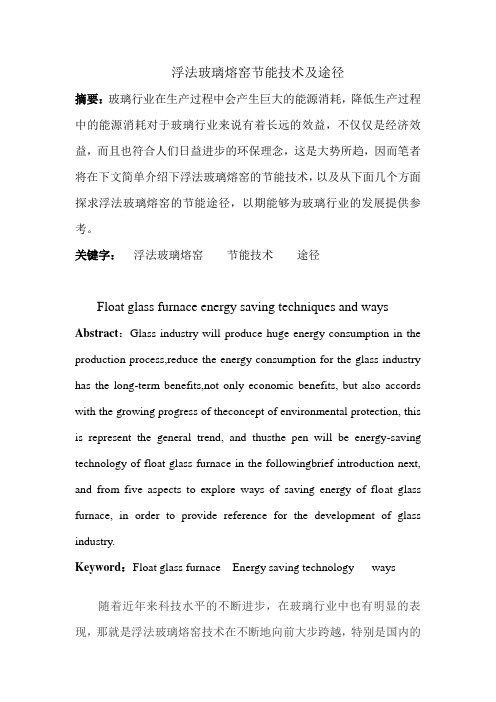
浮法玻璃熔窑节能技术及途径摘要:玻璃行业在生产过程中会产生巨大的能源消耗,降低生产过程中的能源消耗对于玻璃行业来说有着长远的效益,不仅仅是经济效益,而且也符合人们日益进步的环保理念,这是大势所趋,因而笔者将在下文简单介绍下浮法玻璃熔窑的节能技术,以及从下面几个方面探求浮法玻璃熔窑的节能途径,以期能够为玻璃行业的发展提供参考。
关键字:浮法玻璃熔窑节能技术途径Float glass furnace energy saving techniques and ways Abstract:Glass industry will produce huge energy consumption in the production process,reduce the energy consumption for the glass industry has the long-term benefits,not only economic benefits, but also accords with the growing progress of theconcept of environmental protection, this is represent the general trend, and thusthe pen will be energy-saving technology of float glass furnace in the followingbrief introduction next, and from five aspects to explore ways of saving energy of float glass furnace, in order to provide reference for the development of glass industry.Keyword:Float glass furnace Energy saving technology ways 随着近年来科技水平的不断进步,在玻璃行业中也有明显的表现,那就是浮法玻璃熔窑技术在不断地向前大步跨越,特别是国内的保温材料和耐火材料都在原基础上取得了巨大的进步,有进步虽然可喜,但是尚不足以与国外同领域的技术相比肩,或许通过以下数字大家能够更直观地看出差距所在,国外较先进的浮法玻璃熔窑技术最高产生55%的热效率,而我国最高产生40%。
浮法玻璃熔窑中玻璃液流动模拟及工艺优化

浮法玻璃熔窑中玻璃液流动模拟及工艺优化随着现代工业的快速发展,浮法玻璃成为了广泛应用于建筑、汽车和电子等领域的重要材料。
而浮法玻璃的质量和性能很大程度上取决于熔窑生产过程中玻璃液的流动情况。
因此,对于浮法玻璃熔窑中玻璃液流动进行模拟和优化,对于提高产品质量和生产效率具有重要意义。
一、浮法玻璃熔窑中玻璃液流动模拟1. 熔窑结构与玻璃液流动特性浮法玻璃熔窑通常由玻璃池、料斗、罩头、分区部分等组成。
玻璃液在池中融化,并从料斗中流出,进入罩头。
在罩头的作用下,玻璃液慢慢变平,形成连续平整的玻璃带。
在这个过程中,玻璃液的流动受到多个因素的影响,例如重力、表面张力、罩头结构等。
2. 流动模拟方法为了更好地理解浮法玻璃熔窑中玻璃液的流动特性,可以使用数值模拟方法。
数值模拟方法可以将复杂的流动过程简化为数学方程组,并通过计算机模拟求解得到详细的流动信息。
目前,常用的数值模拟方法包括有限元方法和有限体积方法等。
通过这些方法,可以计算得到玻璃液的速度场、温度场等信息。
二、浮法玻璃熔窑工艺优化1. 生产质量优化浮法玻璃的生产质量直接关系到产品的市场竞争力。
通过模拟玻璃液流动过程,可以找到工艺中存在的问题,并进一步优化工艺参数以提高产品质量。
例如,通过调整罩头结构、控制熔窑温度分布等,可以减少玻璃中的气泡和其他缺陷,提高产品的透明度和均匀性。
2. 能耗降低优化浮法玻璃熔窑通常需要消耗大量的能源。
优化工艺参数可以帮助降低能源消耗,提高能源利用效率。
例如,通过优化玻璃液的流动速度和温度分布,可以减少能源的损耗。
此外,还可以采用其他节能措施,例如使用高效燃烧器、优化加热方式等。
3. 生产效率提高优化浮法玻璃的生产效率对于企业的经济效益至关重要。
模拟玻璃液流动过程可以帮助优化生产工艺,提高生产效率。
例如,通过优化料斗结构,可以使玻璃液在流动过程中更加顺畅,减少停机时间。
此外,还可以采用自动控制系统,实现生产过程的智能化管理,提高生产效率。
浮法玻璃退火窑的多功能化与智能化发展
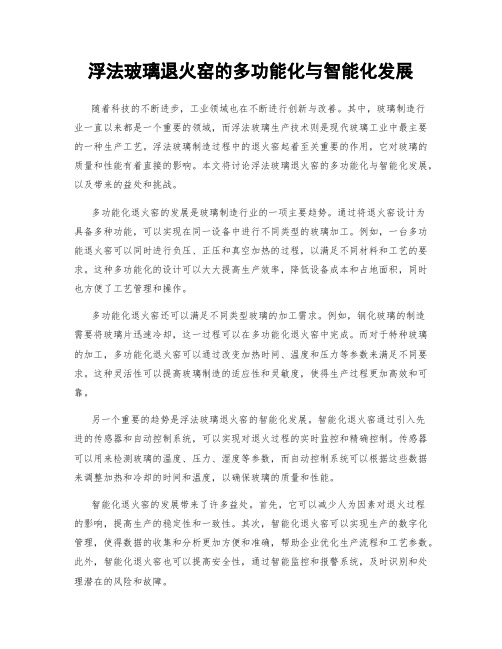
浮法玻璃退火窑的多功能化与智能化发展随着科技的不断进步,工业领域也在不断进行创新与改善。
其中,玻璃制造行业一直以来都是一个重要的领域,而浮法玻璃生产技术则是现代玻璃工业中最主要的一种生产工艺。
浮法玻璃制造过程中的退火窑起着至关重要的作用,它对玻璃的质量和性能有着直接的影响。
本文将讨论浮法玻璃退火窑的多功能化与智能化发展,以及带来的益处和挑战。
多功能化退火窑的发展是玻璃制造行业的一项主要趋势。
通过将退火窑设计为具备多种功能,可以实现在同一设备中进行不同类型的玻璃加工。
例如,一台多功能退火窑可以同时进行负压、正压和真空加热的过程,以满足不同材料和工艺的要求。
这种多功能化的设计可以大大提高生产效率,降低设备成本和占地面积,同时也方便了工艺管理和操作。
多功能化退火窑还可以满足不同类型玻璃的加工需求。
例如,钢化玻璃的制造需要将玻璃片迅速冷却,这一过程可以在多功能化退火窑中完成。
而对于特种玻璃的加工,多功能化退火窑可以通过改变加热时间、温度和压力等参数来满足不同要求。
这种灵活性可以提高玻璃制造的适应性和灵敏度,使得生产过程更加高效和可靠。
另一个重要的趋势是浮法玻璃退火窑的智能化发展。
智能化退火窑通过引入先进的传感器和自动控制系统,可以实现对退火过程的实时监控和精确控制。
传感器可以用来检测玻璃的温度、压力、湿度等参数,而自动控制系统可以根据这些数据来调整加热和冷却的时间和温度,以确保玻璃的质量和性能。
智能化退火窑的发展带来了许多益处。
首先,它可以减少人为因素对退火过程的影响,提高生产的稳定性和一致性。
其次,智能化退火窑可以实现生产的数字化管理,使得数据的收集和分析更加方便和准确,帮助企业优化生产流程和工艺参数。
此外,智能化退火窑也可以提高安全性,通过智能监控和报警系统,及时识别和处理潜在的风险和故障。
然而,浮法玻璃退火窑的多功能化与智能化发展也面临着一些挑战。
首先,制造一台多功能化退火窑的成本较高,需要投入大量的资金和技术。
浮法玻璃退火窑的冷却系统优化与节能改善

浮法玻璃退火窑的冷却系统优化与节能改善浮法玻璃是目前广泛应用于建筑和汽车行业的一种常见玻璃制造工艺。
退火窑是这一工艺中至关重要的一个环节,它的冷却系统对于玻璃质量的稳定性以及能源消耗起着至关重要的作用。
因此,对浮法玻璃退火窑的冷却系统进行优化与节能改善具有重要意义。
浮法玻璃退火窑在制造过程中必须经历一个复杂的冷却阶段。
冷却的目的是降低玻璃温度以提高其稳定性,防止玻璃出现内部应力和变形。
然而,目前存在的一些冷却系统在效率和能源消耗方面存在一些问题,因此有必要对其进行优化和改善。
优化退火窑的冷却系统可以从以下几个方面进行考虑。
首先,可以通过改进冷却系统的结构来优化其热量传递效率。
例如,增加冷却风机数量、优化风机的布局和位置,以提高空气对玻璃的冷却效果。
其次,可以探索使用新型冷却介质,如高效换热器、水冷却冷却器等,以提高冷却效果。
此外,应优化冷却过程中的控制策略,减少能源浪费,例如合理调整风速、降低冷却时间等。
另一方面,节能改善是优化退火窑冷却系统的重要目标之一。
一种可能的节能方法是利用余热回收技术。
在玻璃退火过程中,有大量热量会被废气带走,通过安装余热回收设备,并将废气中的热能转换为可再利用的能源,可以有效降低能源消耗。
此外,对于冷却系统中水的使用也可以进行优化。
例如,使用循环冷却水系统,对冷却水进行循环利用,减少了用水量,降低了能源消耗。
同时,定期的设备维护和管理也是保障退火窑冷却系统高效运行和节能的重要措施。
定期检查和维护设备,保证风机和换热器的正常运转,以减少能源浪费和故障的发生。
此外,应建立良好的系统监控和自动化控制系统,根据玻璃生产的需求动态调整冷却系统的运行参数,以实现最佳的节能效果。
改进浮法玻璃退火窑的冷却系统不仅可以提高玻璃的品质稳定性,还可以实现能源的节约和减排。
通过优化冷却系统的结构和调整冷却过程中的参数,提高热量传递和冷却效果。
同时,通过余热回收和水资源的合理利用等手段,实现能源的节约和循环利用。
浮法玻璃退火窑的热损失与节能改善措施

浮法玻璃退火窑的热损失与节能改善措施浮法玻璃退火窑在玻璃生产过程中起到至关重要的作用。
然而,退火窑的运行也伴随着能源的消耗和热损失。
为了提高能源利用率和降低生产成本,制定出有效的节能改善措施成为了当务之急。
一、浮法玻璃退火窑的热损失原因1. 窑内外温差导致的热交换损失:退火窑内外温差较大时,会产生热交换,导致热量的损失。
2. 窑壁和窑门散热损失:退火窑的窑壁和窑门受到了窑内高温的热传导作用,导致热量的散失。
3. 排烟和烟气损失:在退火窑的运行过程中产生的烟气需要通过排烟系统排出,这也带走了一部分热量。
4. 辅助设备能耗过高:如风机、泵等辅助设备的能耗过高,也会导致热能的浪费。
二、节能改善措施1. 加强窑壁和窑门的保温性能:采用高效的隔热材料,如耐高温隔热板、耐火砖等,以减少热量的散失。
此外,可以在窑壁和窑门附近设置适当的隔热层,减少热传导。
2. 控制窑内外温差,减少热交换损失:可以采用双层窗户或保温门,减少室外冷空气和窑内热空气的接触,减少热量的散失。
此外,合理调整窑内外的温度和湿度,减少热交换。
3. 提高烟气利用率:通过对烟气的预处理和回收利用,可有效地降低烟气带走的热量。
可以采用热交换器对烟气进行余热回收,用于预热进入窑内的新鲜空气或水。
4. 优化辅助设备的能效:对于风机、泵等辅助设备,可通过升级换代,选择更加节能高效的设备,减少能源的浪费。
5. 合理控制窑内温度:通过合理控制窑内温度,避免过高的温度造成热能的浪费。
可以安装恒温装置或增加自动控制系统,及时调整燃料供给和通风风量。
6. 转变燃料类型或混合燃料:选择更加清洁和高效的燃料,如天然气、液化石油气等,以减少燃烧过程中的环境污染和能源消耗。
7. 加强设备的维护与管理:定期对退火窑进行检修和清洗,清理窑内积灰,保证设备的正常运行。
同时,加强对设备性能的监测和数据分析,及时发现问题并采取措施加以解决。
三、节能效果评估和监测引入节能措施后,需要对其节能效果进行评估和监测,以确保实际的节能效果。
浮法玻璃熔制理论在熔窑设计中的应用
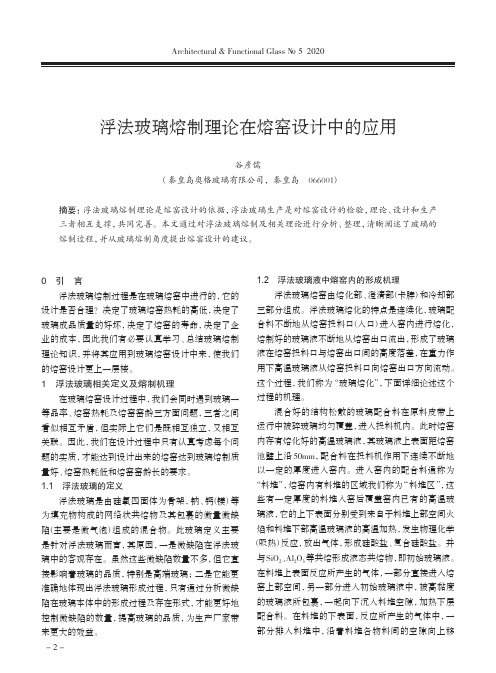
0 引 言浮法玻璃熔制过程是在玻璃熔窑中进行的,它的设计是否合理?决定了玻璃熔窑热耗的高低,决定了玻璃成品质量的好坏,决定了熔窑的寿命,决定了企业的成本,因此我们有必要认真学习、总结玻璃熔制理论知识,并将其应用到玻璃熔窑设计中来,使我们的熔窑设计更上一层楼。
1 浮法玻璃相关定义及熔制机理在玻璃熔窑设计过程中,我们会同时遇到玻璃一等品率、熔窑热耗及熔窑窑龄三方面问题,三者之间看似相互矛盾,但实际上它们是既相互独立,又相互关联。
因此,我们在设计过程中只有认真考虑每个问题的实质,才能达到设计出来的熔窑达到玻璃熔制质量好、熔窑热耗低和熔窑窑龄长的要求。
1.1 浮法玻璃的定义浮法玻璃是由硅氧四面体为骨架,钠、钙(镁)等为填充物构成的网络状共熔物及其包裹的微量微缺陷(主要是微气泡)组成的混合物。
此玻璃定义主要是针对浮法玻璃而言,其原因,一是微缺陷在浮法玻璃中的客观存在。
虽然这些微缺陷数量不多,但它直接影响着玻璃的品质,特别是高端玻璃;二是它能更准确地体现出浮法玻璃形成过程,只有通过分析微缺陷在玻璃本体中的形成过程及存在形式,才能更好地控制微缺陷的数量,提高玻璃的品质,为生产厂家带来更大的效益。
1.2 浮法玻璃液中熔窑内的形成机理浮法玻璃熔窑由熔化部、澄清部(卡脖)和冷却部三部分组成。
浮法玻璃熔化的特点是连续化,玻璃配合料不断地从熔窑投料口(入口)进入窑内进行熔化,熔制好的玻璃液不断地从熔窑出口流出,形成了玻璃液在熔窑投料口与熔窑出口间的高度落差,在重力作用下高温玻璃液从熔窑投料口向熔窑出口方向流动。
这个过程,我们称为“玻璃熔化”,下面详细论述这个过程的机理。
混合好的结构松散的玻璃配合料在原料皮带上运行中被碎玻璃均匀覆盖,进入投料机内。
此时熔窑内存有熔化好的高温玻璃液,其玻璃液上表面距熔窑池壁上沿50mm,配合料在投料机作用下连续不断地以一定的厚度进入窑内。
进入窑内的配合料通称为“料堆”,熔窑内有料堆的区域我们称为“料堆区”,这些有一定厚度的料堆入窑后覆盖窑内已有的高温玻璃液,它的上下表面分别受到来自于料堆上部空间火焰和料堆下部高温玻璃液的高温加热,发生物理化学(吸热)反应,放出气体,形成硅酸盐、复合硅酸盐。
浮法玻璃退火窑的环保改造与排放标准达标
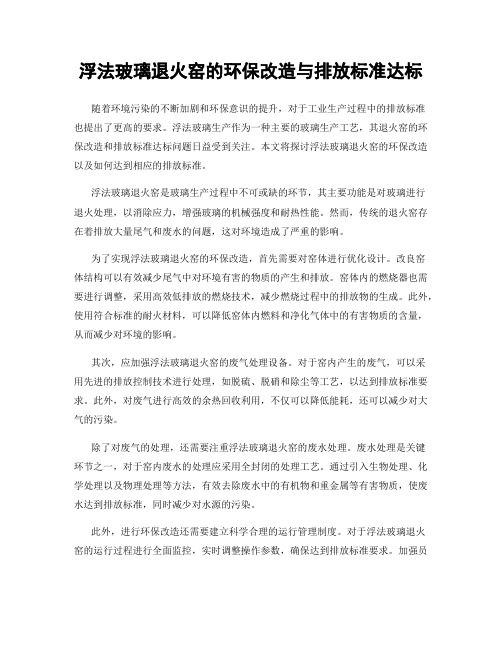
浮法玻璃退火窑的环保改造与排放标准达标随着环境污染的不断加剧和环保意识的提升,对于工业生产过程中的排放标准也提出了更高的要求。
浮法玻璃生产作为一种主要的玻璃生产工艺,其退火窑的环保改造和排放标准达标问题日益受到关注。
本文将探讨浮法玻璃退火窑的环保改造以及如何达到相应的排放标准。
浮法玻璃退火窑是玻璃生产过程中不可或缺的环节,其主要功能是对玻璃进行退火处理,以消除应力,增强玻璃的机械强度和耐热性能。
然而,传统的退火窑存在着排放大量尾气和废水的问题,这对环境造成了严重的影响。
为了实现浮法玻璃退火窑的环保改造,首先需要对窑体进行优化设计。
改良窑体结构可以有效减少尾气中对环境有害的物质的产生和排放。
窑体内的燃烧器也需要进行调整,采用高效低排放的燃烧技术,减少燃烧过程中的排放物的生成。
此外,使用符合标准的耐火材料,可以降低窑体内燃料和净化气体中的有害物质的含量,从而减少对环境的影响。
其次,应加强浮法玻璃退火窑的废气处理设备。
对于窑内产生的废气,可以采用先进的排放控制技术进行处理,如脱硫、脱硝和除尘等工艺,以达到排放标准要求。
此外,对废气进行高效的余热回收利用,不仅可以降低能耗,还可以减少对大气的污染。
除了对废气的处理,还需要注重浮法玻璃退火窑的废水处理。
废水处理是关键环节之一,对于窑内废水的处理应采用全封闭的处理工艺。
通过引入生物处理、化学处理以及物理处理等方法,有效去除废水中的有机物和重金属等有害物质,使废水达到排放标准,同时减少对水源的污染。
此外,进行环保改造还需要建立科学合理的运行管理制度。
对于浮法玻璃退火窑的运行过程进行全面监控,实时调整操作参数,确保达到排放标准要求。
加强员工培训,提高操作人员的环保意识和技能水平,从根本上保证环境污染的控制和减少。
最后,与环保改造相配套的是对排放标准的要求。
相关部门应制定更为严格的排放标准,并对其执行进行监管。
对于达到排放标准的企业给予奖励和政策优惠,对于未达标的企业进行处罚和限制,激励企业积极主动地改善生产过程,减少对环境的危害。
关于我国浮法玻璃熔窑设计的改进意见
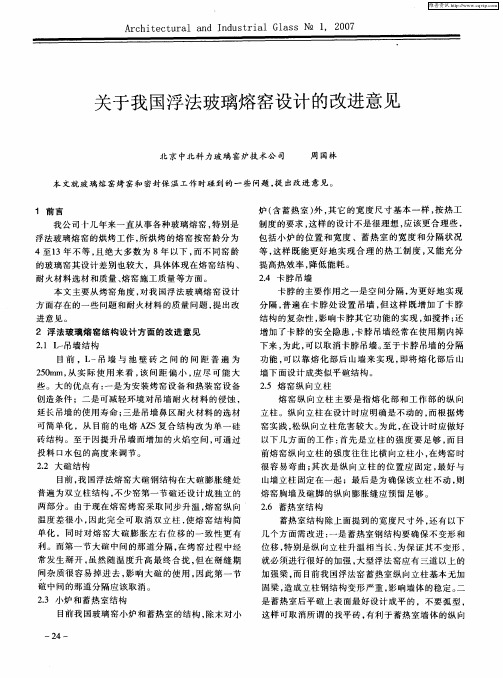
25 熔 窑纵 向立 柱 .
2 浮 法玻璃 熔 窑结构 设计 方面 的 改进 意见 21 一 . L 吊墙 结构
目 前 ,L一吊 墙 与 池 壁 砖 之 间 的 间 距 普 遍 为 2 0 m, 实 际使 用 来 看 , 问距 偏 小 , 尽 可 能 大 5m 从 该 应
问 杂 质很 容 易掉 进 去 , 响 大碹 的使 用 , 影 因此 第 一 节
碹 中 间的那 道分 隔应该 取 消 。
23 小炉 和 蓄热 室结 构 .
目前我 国玻璃 窑小 炉 和蓄热 室 的结 构 , 除末 对小
一
这样 可取 消所 谓 的找平 砖 , 有利 于蓄 热 室墙 体 的纵 向
投 料 口水包 的 高度来 调 节 。 22 大 碹结 构 . 目前 , 国浮法熔 窑 大碹 钢结 构在 大碹 膨胀 缝 处 我
前熔 窑纵 向立 柱 的强度 往 往 比横 向立柱 小 , 在烤 窑 时 很容 易 弯 曲 ; 次 是 纵 向立 柱 的位 置 应 固 定 , 其 最好 与
山墙 立柱 固定 在 一起 ;最 后是 为确 保该 立柱 不 动 , 则
普 遍 为双 立柱结 构 , 少窑第一 节 碹还设 计 成 独立 的 不 两部 分 。 由于 现在熔 窑 烤窑 采取 同步 升温 , 窑纵 向 熔 温度 差 很小 , 因此 完 全 可取 消双 立 柱 , 熔 窑结 构 简 使
单化 ,同 时对 熔 窑 大碹 膨 胀 左 右位 移 的一 致性 更 有 利 。而第 一节 大碹 中间 的那 道分 隔 , 在烤 窑 过程 中经 常 发生 掰 开 , 然 随温 度 升 高 最终 合拢 , 在 掰缝 期 虽 但
些 。大 的优点 有 : 是 为安装 烤 窑设备 和 热装 窑设 备 一 创造 条件 ;二 是可 减轻 环境 对 吊墙 耐 火材 料 的侵 蚀 ,
浮法玻璃退火窑的设计与改进
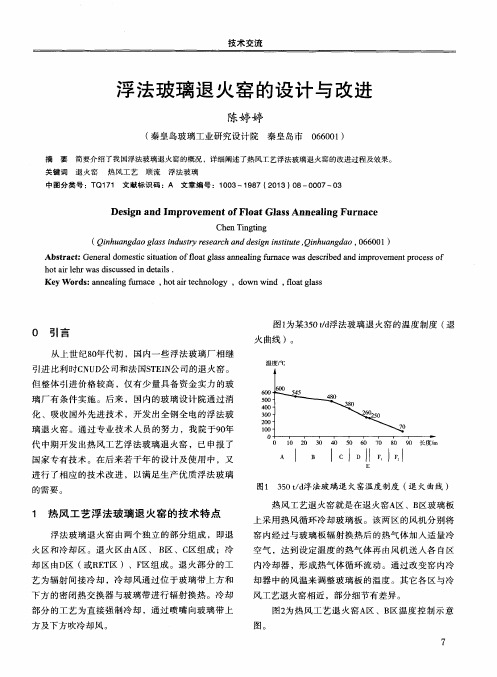
的需 要 。
5 00
0
4 0 O
3 oo 2 oo l o0 O
∞
长
良
艋
图1 3 5 0 t / d 浮法玻璃退 火窑温度制度 ( 退火曲线 )
1 热风 工艺 浮法玻 璃退 火窑 的技术特 点
Ab s t r a c t :Ge n e r a l d o me s t i c s i t u a t i o n o f lo f a t g l a s s a n ne a l i n g f U l T l a c e wa s d e s c ib r e d a nd i mpr o v e me nt p r o c e s s of h o t a i r l e h r wa s d i s c u s s e d i n d e t a i l s.
O
Ke y Wo r d s : a n ne a l i n g f u r n a c e, h o t a i rห้องสมุดไป่ตู้ t e c h n o l o g y ,d o wn wi n d, lo f a t g l a s s
m
A
∞
B
0 引 言
从 上世 纪8 O 年 代初 ,国 内一 些 浮法 玻璃 厂相 继
( 2 )退 火 窑壳 体 为节 能 型 的保 温 结构 。其 内
壳体 是 活动 的 ,通过 螺栓 与外壳 体相连 接 。此结 构
以前 投 产 的退 火 窑 的C 区板 下温 度 高 ,玻璃 板 上 、
下温差 大的状况 。
可保 证壳 体在 制造 时保温 材料填 充得 均匀 密实 。提
关于浮法玻璃熔窑前脸水包改进的探讨

我 厂 拥 有 三条 浮 法 玻 璃生 产 线 , 日熔 化 能 力 为 12 0td 0 / 。在相 当长 一 段 时 期 内 , 厂 一 直 采 用 在 我
投料 池池 壁上 直接 蓬放 一前 脸 大水包 的作 法 。示 意 简 图如 图 1 示 。这 种方式 存在 以下 几 种缺 点 : 所 () 1 整体 相 当于一 个跨 度 很 大 ( ≥ 8m) L 的简 支
维普资讯
全 国性 建 材 科 技 期 刊 —— 《 璃 》 2 O 玻 O 3年
第 3期 总 第 18期 6
关 于浮 法 玻 璃 熔 窑 亩 脸 水 包 改 进 的 探讨 i
邵 厚 江 赵 阳 燕先 进
( 南 省振 华玻 璃厂 商 丘市 河 4 60 ) 7 0 0
更有 利 于配合 料 的预熔 ;
陈正 树 , .浮 法 玻 璃 .武 汉工 业 大 学 出 版 社 ,9 78 等 19 .
( 接 3 页) 上 3
固定 架 。为适 应 不 同形状 、 规格 的玻 璃 及运输 片数 ,
的划 伤 。为此 本机 构设 计 在玻 璃下 面安 置 等距 牙形 胶条 , 上面玻 璃 间安 放橡 胶 泡沫 垫块 , 在 之后 用 打包 带 打包 并与 主架 固定 , 而 防止玻 璃 的前后 滑 动 , 从 消
烧 弯入 投料 池 中 的情 况 , 出弯 水 包 的 过程 既 十分 拉
I l
维普资讯
全 国 性 建 材 科 技 期 刊 —— 《 璃 》 2 0 年 玻 03
第 3期 总 第 18期 6
( ) 换 水包 时仅需 要 向两侧 拉 出水包 , 必停 1更 不
于大 水包在 更 换 时需 要 自投 料 池 向 后 拉 出 , 以 更 所
- 1、下载文档前请自行甄别文档内容的完整性,平台不提供额外的编辑、内容补充、找答案等附加服务。
- 2、"仅部分预览"的文档,不可在线预览部分如存在完整性等问题,可反馈申请退款(可完整预览的文档不适用该条件!)。
- 3、如文档侵犯您的权益,请联系客服反馈,我们会尽快为您处理(人工客服工作时间:9:00-18:30)。
浮法玻璃熔窑设计的改进宋 庆 余(蚌埠玻璃工业设计研究院 蚌埠市 233018) 近些年来,我国浮法玻璃熔窑的设计技术取得了长足的发展,20年前中国只有一座浮法玻璃熔窑,当时的熔化能力只有230t/d,窑炉的寿命只有3年,熔化率为1.13t/m2・d,热耗11675kJ/kg玻璃液,玻璃质量仅能达到当时厂标的二、三等品,总成品率为65%。
现在我国已有浮法窑61座,我国自己设计的最大吨位为600t/d的窑已投产2年,与20年前相比,熔化能力增加了2.6倍,熔化率达到2.26t/m2・d,提高了近一倍,热耗为6688kJ/ kg玻璃液,降低了43%,产品质量大幅度提高,制镜级和加工级玻璃达到90%,总成品率大于80%。
以上的浮法玻璃熔窑技术指标,我国只有少数生产线可以达到,多数浮法玻璃熔窑达不到。
这少数的浮法玻璃熔窑与国外先进的相比还有不小的差距。
本文主要讨论目前我国浮法玻璃熔窑应如何改进。
1 投料池设计的改进投料是熔制过程中的重要工艺环节之一,它关系到配合料的熔化速度、熔化区的位置、泡界线的稳定,最终会影响到产品的质量和产量。
1.1 应设计与熔化部等宽的投料池投料池越宽,配合料的覆盖面积就越大,配合料的吸热是与覆盖面积大小成正比的。
因此采用与熔化部等宽或接近等宽的投料池,有利于提高热效率,有利于节能,有利于提高熔化率。
1.2 采用无水包的45度“L”型吊墙传统的“L”型吊墙都有水包,由于水包的寿命短、易损坏、漏水,造成吊墙砖的炸裂,吊墙砖实际上在热工作状态下无法更换,这样就影响窑炉的寿命。
所谓无水包吊墙,就是水包被一排吊砖所代替,这就解决了因水包漏水所造成的吊墙砖炸裂问题,同时也解决了更换损坏水包对生产的影响。
1.3 投料口采用全密封结构投料池内的压力一般是正压,所以由窑内向外部的溢流和辐射热损失较大。
采用全密封结构,构成预熔池,将减少这部分热损失,使配合料进入熔化池之前能吸收一定的热量,将其中的水分蒸发并进行预熔,这样料堆进入熔化池后很快就会熔化摊平,因此加速了熔化过程。
同时,由于料堆表面被预熔,就减少了粉料被烟气带入蓄热室的量,也减轻了飞料对熔窑上部结构的化学侵蚀。
投料池采用全密封结构,可以防止外界的干扰,保证窑内压力制度、温度制度的稳定,保证泡界线的稳定。
特别是保证玻璃对流的稳定,有利于减少生料对池壁砖的侵蚀,延长窑炉寿命,是一条宝贵的经验。
2 熔化部设计的改进2.1 加长1#小炉至前脸墙的距离加长1#小炉至前脸墙的距离,可开大1#小炉,提高熔化效率和热效率。
从辐射传热公式可以清楚地看出这个问题。
Q=C・T11004-T21004・F式中:Q——配合料吸收的热量,kJ;T1——火焰的温度,K;T2——配合料的温度,K; C——综合辐射系数,kJ/m2h・K4;F——加热面积,m2。
配合料吸收的热量与本身温度的4次幂和火焰温度的4次幂的差成正比,在熔窑中只有1#小炉这个区域两者的温差最大。
这说明加大1#小炉的热负荷,可获得很高的热效率,合理的加长1#小炉至前脸墙的距离可提高熔化量10%以上。
这个措施除了新窑设计可采用外,特别是老窑改造更应该采用。
为了提高产量和质量,这是一个花钱不多效果明显的技术措施。
国外一些浮法玻璃熔窑1#小炉中心线至前脸墙的距离为4m至4.5m,而国内该部位尺寸最大的是洛玻一线,是3.9m。
2.2 新设计的浮法窑应合理的增加熔化部的宽度宽熔化部的设计会带来以下优点:(1)提高火焰对玻璃液的传递长度,火焰的热量被充分吸收,提高热效率。
(2)增加从热点附近返回窑头配合料底面的温度,有利于提高熔化率。
(3)减缓配合料的流动速度,从而有利于减小对池壁砖的侵蚀速度。
(4)减少对格子体的烧损和堵塞。
2.3 窑底结构设计的改进末对小炉后的池底应设计成浅池平底,这样可以减小玻璃液的回流系数,减少玻璃液的重复加热,有利于节能。
末对小炉以前的池底,应设计成阶梯式的,池深由浅逐渐变深,投料池的池深是最大的,这样的池深变化,会加长配合料在高温带的滞留时间,有利于提高热效率,有利于提高熔化率,有利于提高玻璃液的质量。
实践证明,这是一种理想的池底结构。
2.4 熔化部大碹结构设计的改进众所周知,决定熔窑寿命的三个环节是大碹、池壁、蓄热室,其中有一个环节使用期限到头了,整个熔窑也就到期限了。
熔化部大碹受侵蚀最严重的有三个部位,第一是各种测孔,如测压孔、测温孔及压石墨挡条的压杠孔等。
因碹顶是正压,在孔洞处穿火,火力集中,孔洞越烧越大,直至无法热修而停窑。
根据国内外的实践经验,测温孔砖、测压孔砖、压杠孔砖等由硅砖改成“骨料型锆英石砖”是最好的办法。
大碹被侵蚀严重的第二个部位是三块边碹砖。
这主要是受高温环流的侵蚀,该部位责任重大,是大碹的基础,它承担大碹本身和保温层的全部重量。
根据国内外的实践经验,这三块边碹砖采用“骨料型锆英石砖”是行之有效的技术措施。
它的高温使用性能高于优质硅砖,同时它与电熔A ZS砖直接接触在高温下不共熔,而优质硅砖在高温下与电熔AZS砖严重共熔,正因为二者之间严重共熔,导致窜火烧坏钢结构,严重的会造成胸墙向窑内倾倒,无法热修而停窑。
大碹易出问题的第三个部位是膨胀缝处。
大碹膨胀缝处的碹头是自由端,没有约束,膨胀缝密封不好易窜火。
所以有时大碹塌落从此处开始。
要解决好这个问题,在施工砌筑碹头时要砌筑紧一些,砖缝要小,拉条要紧。
膨胀缝的结构设计也是很重要的,设计成台阶式的膨胀缝使用效果较好;在烤窑膨胀结束后,在台阶上湿砌标砖,然后在上面用优质硅质热补料严格密封,这样处理效果很好。
2.5 如何解决胸墙内倾问题(1)三块边碹砖用“骨料型锆英石砖”解决与电熔AZS砖的高温共熔问题。
采用广州石井特耐厂的锆砖最为可靠。
(2)设计的胸墙,其重心尽量向外。
(3)为防止挂勾砖断裂应解决以下问题:・设计挂勾砖的尺寸,长宽比要合理;・烤窑升温曲线要合理,更不能停电;・生产中不能停电,停电会造成挂勾砖炸裂。
・挂勾砖与胸墙托板之间加3mm厚的“多晶莫来石纤维板”,可减少砖炸裂。
・选择离退火质量好的挂勾砖。
(4)采用中硅球墨铸铁做胸墙托板目前浮法窑的胸墙托板一般都采用50m m厚的钢板,这种材质抗氧化性能差,易被烧损,抗弯性能差,在挂勾砖断裂后,暴露在火焰中易弯曲,易烧损,会造成胸墙内倾。
国内有的大型浮法窑的胸墙托板用60mm厚的“中硅球墨铸铁,收到了较好的效果。
2.6 熔化带池壁砖应采用“刀把砖”的结构形式池壁砖的寿命也是决定熔窑寿命的重要因素之一。
因此延长池壁砖的寿命,也就是延长窑炉寿命的重要技术措施之一。
为了延长池壁砖的寿命,一般采用风冷的办法。
众所周知,风冷的目的是为了降低池壁砖内表面温度,从而降低被侵蚀的速度。
池壁砖内表面温度的降低与本身厚度有重要的关系。
当池壁砖厚度为300mm或200mm时,其内表面温度只降低几度。
池壁砖内表面的温度,可按下列公式计算:t1=(A t3-Ks t2)(Ks+A)式中:t1,t2——分别为内外表面的温度,℃;t3——熔融玻璃液表面的温度,℃;K——导热系数kJ/m・h・℃;s——池壁砖的厚度,m;A——导热系数kJ/m・h・℃。
从计算公式可以看出,池壁砖厚度太大,冷却风的效果很差。
池壁砖厚度为150m m时才开始风冷有效果。
因此“刀把砖”上部的厚度设计成175 mm是合适的,下部厚度设计成250m m厚,帮砖可用75mm厚的砖。
当池壁厚度被侵蚀剩下20~30 mm时,冷却效果最佳,所以不过早地帮砖,可延长其寿命。
国外有的浮法窑可帮三次砖,其寿命超过十年,在设计上要考虑留有帮砖空间。
为防止池壁砖炸裂漏玻璃水,在池壁顶铁与池壁砖之间加铁篦子。
在窑的后期,为了延长其寿命,可采用风、水双冷的办法,除了在池壁砖上贴水包外,还要吹风,效果也较好。
3 冷却部设计的改进冷却部的作用是将来自熔化部已被熔化和澄清好的玻璃液降低到成形温度,且不污染玻璃,所以接触玻璃液的池底、池壁砖应选用电熔A-B Al2O3砖,因为它的发泡指数是零,污染玻璃的指数是零。
一般老窑冷修改造都要提高熔化量,这样觉得原冷却部面积小了,温度降不下来。
为了解决这个问题,可采用以下的办法。
即缩小卡脖的宽度和加大卡脖的长度,在卡脖上设置深层水包。
一般可取卡脖的宽度是熔化部宽度的28~50 %。
卡脖的长度一般可取6m,国外也有9m长的。
新设计采用窄卡脖、小冷却部也是方向,这样有利于成形部的稳定,减少投资。
4 蓄热室设计的改进玻璃熔窑的热平衡测试结果表明,废气从窑膛中带走的热量高达50%,这部分热量主要靠蓄热室回收。
所以加强蓄热室的热回收是十分重要的。
搞好蓄热室的设计要做到以下几点:(1)加强蓄热室的密封,防止冷空气吸入。
如吸入冷空气占助燃空气量的20%,就会浪费燃料16%,可见密封对节能是很重要的。
为了保证密封,施工时墙体要做到二类砌体的质量,其外面应涂上50m m厚的保温涂料。
(2)加强蓄热室的保温,减少蓄热室的散热损失。
现在蓄热室墙一般采用镁砖,其导热系数是硅砖的两倍左右,因此要加强保温,除采用优质保温砖外,还要在外层加高质量的保温涂料,成都飞峰公司的保温涂料的导热系数只有0.1675kJ/m・h ・℃,值得推广使用。
(3)选择优质的耐火材料做格子砖。
碱性耐火材料格子砖是理想的选择,其优点是耐火度高,耐碱的侵蚀性能好,蓄热能力强,容积比热大,是低气孔粘土砖的1.36倍;导热系数大,是低气孔粘土砖的两倍左右。
所以使用碱性格子砖换热效率高,可提高助燃空气的预热温度,提高火焰温度,可节能10%左右。
我国高纯镁砖的热稳定性差,用于格子体的上部易剥落。
国外研制的镁锆砖热稳定性好,用到格子体上部效果好。
我国耐火材料行业应加快研制,争取早日投放市场。
(4)合理选择格子砖的结构形式。
筒型格子砖是最佳的选择。
蓄热室热交换过程中,热废气传给空气的热量可用下列传热方程式表示:Q=R・F・$t m,kJ/周期Q——蓄热室的热回收,即每一换向周期热废气传给空气的热量,kJ/周期;R——传热总系数,kJ/m2・周期・℃;F——格子砖的传热面积,m2;$t m——平均温差,℃。
从上述方程式可以看出,蓄热室格子体换热面积越大,蓄热室的热回收就越多。
为了增加换热面积,蓄热室的格子体采用筒型砖是最佳的选择。
采用筒型砖做格子体有以下优点:¹采用筒型砖的格子体,可以获得较大的换热面积。
表1格子体砖型/mm 单位体积格体的换热面积/m2・m-3筒型砖140×140(格孔)16.0十字型砖13.7空穴式格子体300×150×6412.7编篮式格子体300×150×6410.4 下表是筒型砖与其它各种格子砖换热面积的比较。
从上表可以看出,筒型格子砖组成的格子体比传统编篮式格子体增加换热面积50%以上。