生物质气化发电技术
生物质能发电原理

生物质能发电原理生物质能发电是一种利用生物质作为燃料来发电的技术。
生物质包括植物、动物等有机物质,如木材、农作物废弃物、食品废料等。
利用这些生物质作为燃料来发电,不仅可以有效回收利用有机废弃物,还可以减少对传统化石燃料的依赖,降低温室气体排放,具有重要的环境和经济效益。
一、生物质能燃烧发电原理生物质能燃烧发电是目前最常用的生物质能发电技术。
其基本原理是通过燃烧生物质燃料释放的热能来获得蒸汽,进而驱动涡轮发电机发电。
其具体过程如下:1. 原料处理:生物质燃料经过破碎、干燥等处理工序,得到适合燃烧的小颗粒物。
2. 燃烧过程:将处理后的生物质颗粒物送入锅炉,进行燃烧。
在燃烧过程中,生物质燃料中的可燃物质在氧气的存在下发生反应,产生高温和燃烧产物,其中最主要的产物是二氧化碳和水蒸气。
3. 热能转化:锅炉中的燃料燃烧释放的热能被传递给水,使水转化为高温高压的蒸汽。
4. 涡轮发电机组:高温高压的蒸汽推动涡轮发电机组转动,通过转动的涡轮产生电能。
5. 发电输送:发电机组产生的电能通过输电网输送到用户端,为人们的生活和生产提供电力支持。
生物质能燃烧发电技术具有成熟的产业化应用,其中关键的环节是燃烧过程和热能转化。
优化燃烧过程和提高热能转化效率是提高生物质能发电效率的重要手段。
二、生物质气化发电原理除了燃烧发电,生物质气化发电是另一种常见的生物质能发电技术。
该技术通过将生物质颗粒物在高温和缺氧条件下转化为可燃气体,再利用气体发电。
其具体过程如下:1. 生物质气化:生物质燃料经过粉碎、干燥等处理工序后,进入气化炉。
在气化炉中,生物质在高温和缺氧条件下发生热解和干馏反应,生成可燃的合成气体,主要成分为一氧化碳、氢气和甲烷等。
2. 合成气净化:气化产生的合成气中含有较多的杂质,需要进行除尘、脱硫、脱氮等处理,以便保护后续设备的正常运行。
3. 合成气发电:经过净化后的合成气进入内燃机或燃气轮机,产生动力,驱动发电机发电。
生物质气化技术的应用案例分析
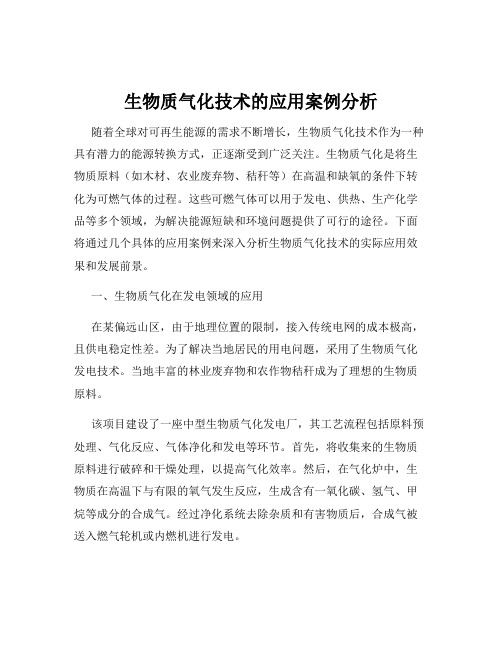
生物质气化技术的应用案例分析随着全球对可再生能源的需求不断增长,生物质气化技术作为一种具有潜力的能源转换方式,正逐渐受到广泛关注。
生物质气化是将生物质原料(如木材、农业废弃物、秸秆等)在高温和缺氧的条件下转化为可燃气体的过程。
这些可燃气体可以用于发电、供热、生产化学品等多个领域,为解决能源短缺和环境问题提供了可行的途径。
下面将通过几个具体的应用案例来深入分析生物质气化技术的实际应用效果和发展前景。
一、生物质气化在发电领域的应用在某偏远山区,由于地理位置的限制,接入传统电网的成本极高,且供电稳定性差。
为了解决当地居民的用电问题,采用了生物质气化发电技术。
当地丰富的林业废弃物和农作物秸秆成为了理想的生物质原料。
该项目建设了一座中型生物质气化发电厂,其工艺流程包括原料预处理、气化反应、气体净化和发电等环节。
首先,将收集来的生物质原料进行破碎和干燥处理,以提高气化效率。
然后,在气化炉中,生物质在高温下与有限的氧气发生反应,生成含有一氧化碳、氢气、甲烷等成分的合成气。
经过净化系统去除杂质和有害物质后,合成气被送入燃气轮机或内燃机进行发电。
通过这个项目,不仅为当地居民提供了稳定可靠的电力供应,还减少了对传统化石能源的依赖,降低了碳排放。
同时,利用当地的废弃物作为原料,还为农民增加了额外的收入,促进了当地经济的发展。
然而,在实际运行中也面临一些挑战。
例如,生物质原料的供应具有季节性,需要合理规划储存和采购;气化过程中产生的焦油会对设备造成腐蚀和堵塞,需要定期维护和清理;发电效率相对较低,需要进一步优化工艺和设备以提高能源转化效率。
二、生物质气化在供热领域的应用在北方的一个城镇,冬季供暖是一个重要的民生问题。
为了减少对煤炭等传统能源的依赖,降低供暖成本和环境污染,引入了生物质气化供热系统。
该系统以周边农村的农作物秸秆为主要原料,通过生物质气化炉将其转化为可燃气体。
这些气体经过简单的净化处理后,直接送入供热锅炉燃烧产生热能,然后通过热力管网输送到居民家中。
生物质气化耦合发电

生物质气化耦合发电
生物质气化耦合发电是一种新型的能源利用方式,它将生物质气化和发电技术相结合,实现了生物质资源的高效利用和能源的可持续发展。
生物质气化是将生物质材料在高温、高压和缺氧的条件下转化为可燃气体的过程。
这种气体主要由一氧化碳、氢气、甲烷等组成,可以作为燃料用于发电、供热等领域。
与传统的燃煤发电相比,生物质气化发电具有环保、低碳、可再生等优点,可以有效减少温室气体排放,降低能源消耗。
生物质气化耦合发电技术是将生物质气化和发电技术有机结合起来,实现了生物质资源的高效利用和能源的可持续发展。
在生物质气化过程中,产生的可燃气体可以直接用于发电,也可以通过气体净化、气体液化等处理方式得到更高品质的燃料,提高发电效率。
同时,生物质气化耦合发电技术还可以实现废弃物的资源化利用,将农业废弃物、城市垃圾等转化为可再生能源,减少环境污染和资源浪费。
生物质气化耦合发电技术在我国的应用前景广阔。
我国是一个农业大国,生物质资源丰富,尤其是农业废弃物、林业废弃物等资源的利用率较低,生物质气化耦合发电技术可以有效解决这些问题。
同时,生物质气化耦合发电技术还可以促进农村经济发展,提高农民收入,实现农业可持续发展。
生物质气化耦合发电技术是一种具有广阔应用前景的新型能源利用方式,可以实现生物质资源的高效利用和能源的可持续发展,对于促进我国能源结构调整和环境保护具有重要意义。
生物质气化发电转化废物为宝贵能源

生物质气化发电转化废物为宝贵能源随着全球能源危机的日益严重,可再生能源备受关注,生物质气化发电便是其中的一种重要利用方式。
生物质气化发电是一种将生物质资源转化为宝贵能源的过程,在当今社会中具有广泛应用和深远意义。
一、生物质气化发电的基本原理和过程生物质气化发电是一种将暖室生物质材料通过高温和缺氧条件下进行热解的过程,产生可燃气体,再通过气体发电机组发电的技术。
其基本原理是将生物质材料分解为可燃气体(主要为CO、H2、CH4等)和固体残渣(主要为残留灰分和焦炭),进而通过气体发电机组将可燃气体转化为电能,实现资源的高效利用。
二、生物质气化发电的优势和应用1. 转化废物为宝贵能源:生物质气化发电的关键在于将废弃的生物质资源进行有效利用,将其转化为宝贵能源,有利于减少废物排放和环境污染。
2. 可持续发展:生物质气化发电所使用的生物质资源广泛,包括农作物秸秆、林木废弃物、餐厨垃圾等,具有可再生的特点,有利于能源的可持续开发和利用。
3. 减少温室气体排放:相比传统燃煤发电方式,生物质气化发电过程中所产生的二氧化碳排放量较低,可以有效减少温室气体的释放,对于应对全球气候变化具有积极意义。
4. 广泛应用于乡村发电和分布式能源系统:生物质气化发电技术可以在乡村地区直接利用农作物秸秆等生物质资源发电,满足当地电力需求,缓解电力供应压力。
5. 综合利用废弃物:生物质气化发电过程中产生的固体残渣可以作为肥料或其他应用,实现废物资源的循环利用。
三、生物质气化发电的挑战和解决方案1. 生物质资源供给不稳定:生物质气化发电技术的实施面临着生物质资源供给不稳定的困难。
解决方案可以通过建立生物质贮存设施和发展生物质产业链,确保生物质资源的充足供应。
2. 废弃物管理问题:废弃物的收集、前处理和运输是生物质气化发电技术中的重要环节。
解决方案可以通过建立完善的废弃物管理体系,加强对废弃物的分类处理和运输网络的建设。
3. 气化效率的提高:生物质气化发电技术中,气化效率的提高是一个关键问题。
生物质气化技术的应用案例与分析
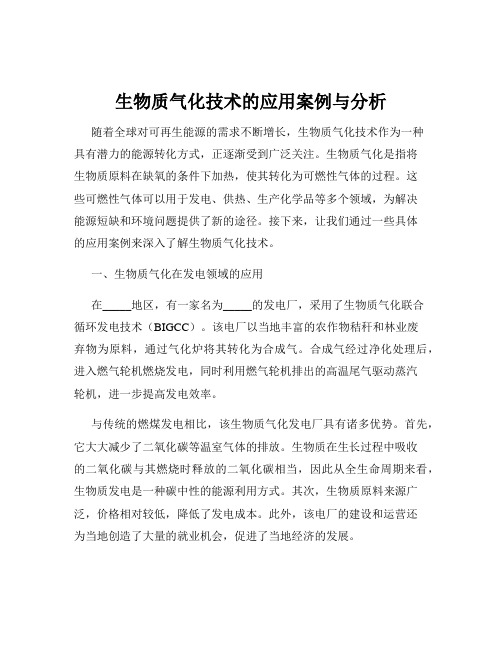
生物质气化技术的应用案例与分析随着全球对可再生能源的需求不断增长,生物质气化技术作为一种具有潜力的能源转化方式,正逐渐受到广泛关注。
生物质气化是指将生物质原料在缺氧的条件下加热,使其转化为可燃性气体的过程。
这些可燃性气体可以用于发电、供热、生产化学品等多个领域,为解决能源短缺和环境问题提供了新的途径。
接下来,让我们通过一些具体的应用案例来深入了解生物质气化技术。
一、生物质气化在发电领域的应用在_____地区,有一家名为_____的发电厂,采用了生物质气化联合循环发电技术(BIGCC)。
该电厂以当地丰富的农作物秸秆和林业废弃物为原料,通过气化炉将其转化为合成气。
合成气经过净化处理后,进入燃气轮机燃烧发电,同时利用燃气轮机排出的高温尾气驱动蒸汽轮机,进一步提高发电效率。
与传统的燃煤发电相比,该生物质气化发电厂具有诸多优势。
首先,它大大减少了二氧化碳等温室气体的排放。
生物质在生长过程中吸收的二氧化碳与其燃烧时释放的二氧化碳相当,因此从全生命周期来看,生物质发电是一种碳中性的能源利用方式。
其次,生物质原料来源广泛,价格相对较低,降低了发电成本。
此外,该电厂的建设和运营还为当地创造了大量的就业机会,促进了当地经济的发展。
然而,生物质气化发电也面临一些挑战。
例如,生物质原料的收集、运输和储存需要耗费大量的人力和物力,且原料的供应存在季节性波动,可能影响电厂的稳定运行。
此外,气化过程中产生的焦油等副产物的处理也是一个亟待解决的问题。
二、生物质气化在供热领域的应用在_____城市的_____工业园区,一家采用生物质气化供热的企业取得了显著的成效。
该企业建设了一套生物质气化供热系统,为园区内的多家工厂提供蒸汽和热水。
这套系统以木屑、稻壳等为原料,通过气化炉产生的热气体直接与水进行热交换,产生蒸汽和热水。
与传统的燃油、燃气供热方式相比,生物质气化供热具有成本低、环保等优点。
据统计,该系统每年可替代大量的化石燃料,减少了二氧化硫、氮氧化物等污染物的排放,同时为企业节省了可观的能源费用。
生物质气化发电机组

生物质气化发电机组生物质气化发电机组是一种利用生物质燃料进行气化反应,进而产生燃气发电的设备。
生物质气化发电技术是一种可再生能源利用方式,具有环保、经济和可持续发展的优势。
一、生物质气化发电技术概述生物质气化发电技术是将生物质燃料(如木屑、秸秆、稻壳等)通过气化反应转化为燃气,再利用燃气发电的过程。
生物质气化发电机组一般由气化炉、气化炉排渣系统、燃气净化系统、燃气发电机组等组成。
在气化炉中,生物质燃料经过高温和缺氧条件下的热解反应,产生可燃气体。
这些可燃气体经过净化处理后,进入燃气发电机组进行燃烧发电。
二、生物质气化发电技术的优势1. 环保:生物质气化发电过程中,生物质燃料的燃烧几乎不产生硫、氮等有害物质的排放,对环境污染较小。
而且生物质燃烧后的灰渣可以被作为有机肥料利用,实现资源的循环利用。
2. 经济:生物质燃料相对于化石燃料而言成本更低,而且生物质气化发电可以实现能源的多元化利用,降低能源供应的风险。
3. 可持续发展:生物质燃料是一种可再生能源,其资源丰富且可持续供应。
生物质气化发电技术的应用,可以减少对化石能源的依赖,推动可持续发展。
三、生物质气化发电技术的应用领域生物质气化发电技术广泛应用于农村能源供应、农业废弃物综合利用、农村环境治理等领域。
1. 农村能源供应:生物质气化发电机组可以利用农村丰富的秸秆、木屑等生物质资源,为农村地区提供可靠的电力供应,满足农村居民生活和生产的能源需求。
2. 农业废弃物综合利用:农业废弃物如秸秆、稻壳等常常成为污染环境的问题,生物质气化发电技术可以将这些废弃物转化为可再生能源,既解决了废弃物的处理问题,又为农村地区提供了经济效益和环境效益。
3. 农村环境治理:生物质气化发电技术可以有效治理农村生活垃圾和农作物秸秆等废弃物的环境问题,减少污染物的排放,改善农村环境质量。
四、生物质气化发电技术的发展现状和前景生物质气化发电技术在我国得到了广泛的应用和推广。
随着能源转型和可持续发展的需求,生物质气化发电技术将有更广阔的发展前景。
生物质能源的气化与气体发电技术

生物质能源的气化与气体发电技术生物质能源的气化与气体发电技术是一种利用生物质资源进行能源转化的重要技术途径,具有环保、可持续和高效利用资源的特点,是解决能源危机和环境问题的有效途径。
随着全球能源需求的不断增长和环境污染问题的日益加重,生物质能源的气化与气体发电技术受到了广泛关注和研究。
本文将从生物质能源的气化基础、气化过程和气体发电技术等方面进行深入探讨,旨在全面了解该技术在能源转化领域的应用和发展前景。
首先,生物质能源的气化是将固体生物质通过热解、氧化或还原等化学反应转化为气态燃料的过程。
生物质气化是一种复杂的多相反应过程,包括干馏、热解、气化和燃烧等多种反应机理。
在气化过程中,生物质原料在高温、高压和缺氧条件下,通过热解和气化反应生成气体燃料和残渣灰。
气化反应的主要产物包括一氧化碳、氢气和甲烷等可燃气体,这些气体可以用于发电、供热和工业生产等领域。
其次,生物质能源的气化过程受到多种因素的影响,包括原料性质、气化剂种类、气化温度和压力等。
原料的种类和含水率是影响生物质气化的关键因素之一,不同种类的生物质原料在气化过程中产生的气体组成和产率不同。
气化剂种类和用量也对气化效果有明显影响,氢气和二氧化碳是常用的气化剂,可以影响气化反应的速率和产物分布。
此外,气化温度和压力是调控气化反应速率和产气性能的重要参数,适当的温度和压力可以提高生物质气化的产气率和燃烧效率。
第三,生物质气化技术在生物质能源利用中具有重要意义,可以实现生物质资源的高效利用和能源转化。
生物质气化技术可以将固体生物质转化为可再生的气体燃料,取代传统的化石燃料,减少碳排放和资源消耗。
气化气体可以直接用于发电和供热,也可以作为合成天然气、合成液体燃料和化工原料等。
生物质气化技术还可以实现废弃物资源化利用,将农林废弃物和生活垃圾等转化为有用的能源产品,减少环境污染和资源浪费。
第四,生物质气化与气体发电技术的发展还面临一些挑战和问题,包括气化反应的复杂性、气化产气的稳定性和气体净化的难度等。
2024年高效生物质气化发电市场前景分析

高效生物质气化发电市场前景分析1. 引言随着全球能源需求的不断增长和可再生能源的发展,生物质气化发电作为一种环保且高效的能源转化技术逐渐受到关注。
本文将对高效生物质气化发电市场前景进行分析。
2. 市场概述在过去的几年中,高效生物质气化发电市场取得了显著的增长。
这种技术能够将生物质转化为可再生能源,如生物质气体或合成气体,用于发电和热能生产。
高效生物质气化发电可以利用农作物秸秆、森林剩余物、园林废弃物等各种生物质资源,减少对传统能源的依赖,促进可持续发展。
3. 市场驱动因素3.1 环保政策的支持在减少碳排放和应对气候变化的背景下,许多国家纷纷推出支持生物质气化发电的环保政策。
这些政策包括提供补贴和税收优惠等激励措施,推动了高效生物质气化发电市场的发展。
3.2 能源安全和可持续发展需求传统能源的供应面临着不断减少的资源和供应不稳定的问题。
高效生物质气化发电作为一种可再生能源,能够提供持续稳定的能源供应,减轻对传统能源的依赖。
3.3 技术发展和成本下降随着技术的不断进步和成本的降低,高效生物质气化发电技术逐渐变得更加成熟和经济可行。
这促使了更多投资者和能源公司对该市场的关注和投入。
4. 市场挑战和限制4.1 生物质资源供给不稳定生物质气化发电的一个主要挑战是生物质资源供给的不稳定性。
受季节、天气和地理条件等因素的影响,生物质资源的供应可能不足或不稳定,这给生产和运营带来了一定的困难。
4.2 高效气化技术的复杂性高效生物质气化发电技术相对复杂,需要高水平的技术和设备支持。
这对技术人员的要求较高,并增加了项目建设和运营的难度。
4.3 地方政策和管理的不完善地方政府在生物质气化发电项目审批和管理方面的不完善,可能导致项目推进缓慢和不确定性。
5. 市场前景高效生物质气化发电市场在未来有望继续保持快速增长的势头。
以下是市场前景的一些关键因素:5.1 增加生物质供应随着对生物质资源需求的增加,生物质供应链将进一步完善并扩大规模。
生物质气化 间接 热空气 内燃机发电技术

生物质气化间接热空气内燃机发电技术生物质气化间接热空气内燃机发电技术是一种利用生物质能源进行发电的技术。
生物质气化是将生物质材料在缺氧条件下进行热解反应,产生合成气。
而间接热空气内燃机是一种利用合成气进行燃烧的内燃机。
将这两种技术结合起来,可以实现对生物质能源的高效利用和可持续发展。
生物质气化是一种将生物质材料转化为可燃气体的过程。
在气化过程中,生物质材料首先经过预处理,如破碎、干燥等,然后在气化炉中进行气化反应。
在缺氧条件下,生物质材料发生热解反应,生成合成气。
合成气主要由一氧化碳、氢气、甲烷等组成,可以作为燃料用于发电或其他能源利用。
间接热空气内燃机是一种利用合成气进行燃烧的内燃机。
合成气在燃烧过程中释放能量,驱动内燃机工作。
燃烧产生的高温高压气体通过活塞的工作,驱动发电机转动,产生电能。
与直接热空气内燃机不同,间接热空气内燃机通过燃烧室与发电机分离,使得燃烧过程更加稳定,减少了燃烧室的磨损和冷却问题。
生物质气化间接热空气内燃机发电技术具有许多优点。
首先,生物质作为可再生能源,具有丰富的资源和广泛的分布,可以有效替代传统的化石燃料,减少对环境的影响。
其次,生物质气化技术可以实现对生物质能源的高效利用,提高能源利用效率。
再次,间接热空气内燃机的分离设计使得燃烧过程更加稳定,提高了发电机的工作效率和可靠性。
此外,生物质气化间接热空气内燃机发电技术还可以实现废弃物的资源化利用,减少了废弃物的排放和处理成本。
然而,生物质气化间接热空气内燃机发电技术也面临一些挑战和问题。
首先,生物质气化过程中产生的合成气中可能含有一些有害物质,如灰分、硫、氯等,需要进行净化处理,以减少对环境和设备的影响。
其次,生物质气化技术的工艺复杂,需要考虑气化温度、气化剂、气化时间等因素,以获得高质量的合成气。
再次,合成气的燃烧特性与传统燃料有所不同,需要对燃烧过程进行优化设计,以提高燃烧效率和降低排放物的产生。
为了克服这些挑战,需要进一步研究和开发相关技术。
生物质气化发电技术

生物质气化发电技术1.气化发电的工作原理及工艺流程1.1气化发电工作原理生物质气化发电技术的基本原理是把生物质转化为可燃气,再利用可燃气推动燃气发电设备进行发电。
它既能解决生物质难于燃用而又分布分散的缺点,又可以充分发挥燃气发电技术设备紧凑而污染少的优点,所以是生物质能最有效最洁净的利用方法之一。
气化发电过程包括三个方面,一是生物质气化,把固体生物质转化为气体燃料;二是气体净化,气化出来的燃气都带有一定的杂质,包括灰份、焦炭和焦油等,需经过净化系统把杂质除去,以保证燃气发电设备的正常运行;三是燃气发电,利用燃气轮机或燃气内燃机进行发电,有的工艺为了提高发电效率,发电过程可以增加余热锅炉和蒸汽轮机。
生物质气化发电技术是生物质能利用中有别于其他可再生能源的独特方式,具有三个方面特点:一是技术有充分的灵活性,由于生物质气化发电可以采用内燃机,也可以采用燃气轮机,甚至结合余热锅炉和蒸汽发电系统,所以生物质气化发电可以根据规模的大小选用合适的发电设备,保证在任何规模下都有合理的发电效率。
这一技术的灵活性能很好地满足生物质分散利用的特点;二是具有较好的洁净性,生物质本身属可再生能源,可以有效地减少CO2、SO2等有害气体的排放。
而气化过程一般温度较低(大约在700-900oC),NOx 的生成量很少,所以能有效控制NOx的排放;三是经济性,生物质气化发电技术的灵活性,可以保证该技术在小规模下有效好的经济性,同时燃气发电过程简单,设备紧凑,也使生物质气化发电技术比其他可再生能源发电技术投资更小,所以总的来说,生物质气化发电技术是所有可再生能源技术中最经济的发电技术,综合的发电成本已接近小型常规能源的发电水平。
典型的生物质气化发电工艺流程如图1-1所示。
图1-1气化发电系统流程图生物质循环流化床气化发电装置主要由进料机构,燃气发生装置,燃气净化装置,燃气发电机组、控制装置及废水处理设备六部分组成:进料机构:进料机构采用螺旋加料器,动力设备是电磁调速电机。
生物质气化发电原理

一、概况生物质气化发电技术,简单地说,就是将各种低热值固体生物质能源资源(如农林业废弃物、生活有机垃圾等)通过气化转换为燃气,再提供发电机组发电的技术。
寻求利用生物质气化发电的方法,既可以解决可再生能源的有效利用,又可以解决各种有机废弃物的环境污染。
正是基于以上原因,生物质气化发电技术得到了越来越多的研究和应用,并日趋完善。
生物质气化发电,可归纳为下列几种方式:从上图可以看出,生物质气化发电可通过三种途径实现:生物质气化产生燃气作为燃料直接进入燃气锅炉生产蒸汽,再驱动蒸汽轮机发电;也可将净化后的燃气送给燃气轮机燃烧发电;还可以将净化后的燃气送入内燃机直接发电。
在发电和投资规模上,它们分别对应于大规模、中等规模和小规模的发电。
今天,在商业上最为成功的生物质气化内燃发电技术,由于具有装机容量小、布置灵活、投资少、结构紧凑、技术可靠、运行费用低廉、经济效益显著、操作维护简单和对燃气质量要求较低等特点,而得到广泛的推广与应用。
二、生物质气化内燃发电系统主要组成部分生物质气化内燃发电系统主要由气化炉、燃气净化系统和内燃发电机等组成:气化炉是将生物质能由固态转化为燃气的装置。
生物质在气化炉内通过控制空气供应量,而进行不完全燃烧,实现低值生物质能由固体向气态的转化,生成包含氢气(H2)、一氧化碳(CO)、甲烷(CH4)、多碳烃(C n H m)等可燃成分的燃气,完成生物质的气化过程。
气化产生的燃气出口温度随气化炉型式的不同,在350℃~650℃之间,并且燃气中含有未完全裂解的焦油及灰尘等杂质,为满足内燃机长期可靠工作的要求,需要对燃气进行冷却和净化处理,使燃气温度降到40℃以下、焦油灰尘含量控制在50mg/Nm3以内,燃气经过净化后,再进入内燃机发电。
在内燃机内,燃气混合空气燃烧做功,驱动主轴高速转动,主轴再带动发电机进行发电。
生物质气化内燃发电就是通过以上过程,将各种废弃物化废为宝,转化为优质电能,解决废弃物的污染和能源的合理利用问题。
生物质气化耦合燃煤发电技术应用
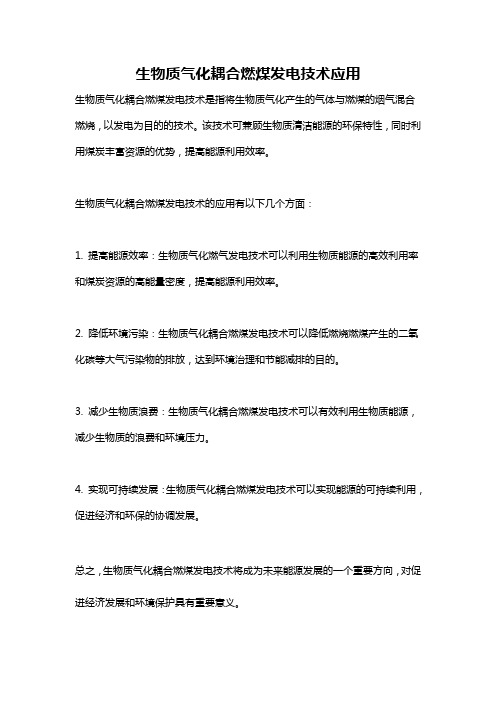
生物质气化耦合燃煤发电技术应用
生物质气化耦合燃煤发电技术是指将生物质气化产生的气体与燃煤的烟气混合燃烧,以发电为目的的技术。
该技术可兼顾生物质清洁能源的环保特性,同时利用煤炭丰富资源的优势,提高能源利用效率。
生物质气化耦合燃煤发电技术的应用有以下几个方面:
1. 提高能源效率:生物质气化燃气发电技术可以利用生物质能源的高效利用率和煤炭资源的高能量密度,提高能源利用效率。
2. 降低环境污染:生物质气化耦合燃煤发电技术可以降低燃烧燃煤产生的二氧化碳等大气污染物的排放,达到环境治理和节能减排的目的。
3. 减少生物质浪费:生物质气化耦合燃煤发电技术可以有效利用生物质能源,减少生物质的浪费和环境压力。
4. 实现可持续发展:生物质气化耦合燃煤发电技术可以实现能源的可持续利用,促进经济和环保的协调发展。
总之,生物质气化耦合燃煤发电技术将成为未来能源发展的一个重要方向,对促进经济发展和环境保护具有重要意义。
生物质气化发电
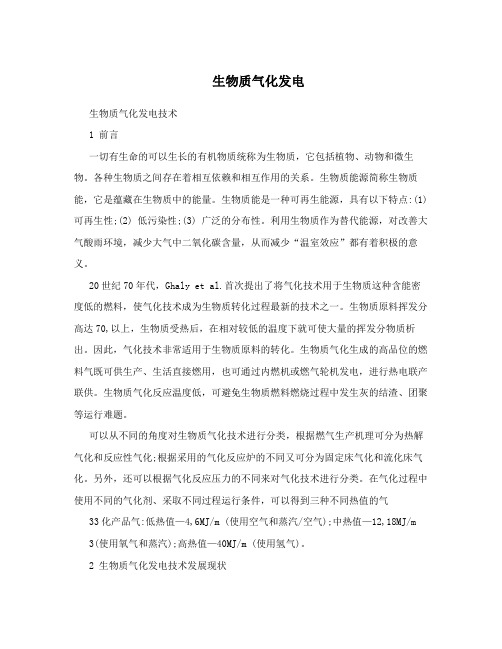
生物质气化发电生物质气化发电技术1 前言一切有生命的可以生长的有机物质统称为生物质,它包括植物、动物和微生物。
各种生物质之间存在着相互依赖和相互作用的关系。
生物质能源简称生物质能,它是蕴藏在生物质中的能量。
生物质能是一种可再生能源,具有以下特点:(1) 可再生性;(2) 低污染性;(3) 广泛的分布性。
利用生物质作为替代能源,对改善大气酸雨环境,减少大气中二氧化碳含量,从而减少“温室效应”都有着积极的意义。
20世纪70年代,Ghaly et al.首次提出了将气化技术用于生物质这种含能密度低的燃料,使气化技术成为生物质转化过程最新的技术之一。
生物质原料挥发分高达70,以上,生物质受热后,在相对较低的温度下就可使大量的挥发分物质析出。
因此,气化技术非常适用于生物质原料的转化。
生物质气化生成的高品位的燃料气既可供生产、生活直接燃用,也可通过内燃机或燃气轮机发电,进行热电联产联供。
生物质气化反应温度低,可避免生物质燃料燃烧过程中发生灰的结渣、团聚等运行难题。
可以从不同的角度对生物质气化技术进行分类,根据燃气生产机理可分为热解气化和反应性气化;根据采用的气化反应炉的不同又可分为固定床气化和流化床气化。
另外,还可以根据气化反应压力的不同来对气化技术进行分类。
在气化过程中使用不同的气化剂、采取不同过程运行条件,可以得到三种不同热值的气33化产品气:低热值—4,6MJ/m (使用空气和蒸汽/空气);中热值—12,18MJ/m 3(使用氧气和蒸汽);高热值—40MJ/m (使用氢气)。
2 生物质气化发电技术发展现状2.1 生物质气化发电技术在国外的发展及现状1生物质气化及发电技术在发达国家已受到广泛重视,如奥地利、丹麦、芬兰、法国、挪威、瑞典和美国等国家,生物质能在总能源消耗中所占的比例增加相当迅速。
奥地利成功地推行了建立燃烧木材剩余物的区域供电站的计划,生物质能在总能耗中的比例由原来的3%增到目前的25%,已拥有装机容量为1,2MW的区域供热站90座。
生物质气化发电系统的技术介绍及参数

生物质气化发电系统的技术介绍及参数一,技术介绍本生物质气化发电系统是一种将生物质气化处理的供气发电系统。
1,技术背景石油、天燃气、煤等化石能源在燃烧过程中排放出大量温室气体而使用全球的气温逐步暖化而产生温室效应。
鉴于此,《京都协议书》规定了各成员国应当在未来逐渐减少二氧化碳等温室气体的排放。
今后全世界所有粉煤电站多要采用气化发电的新工艺主要是(减少二氧化碳等温室气体的排放),这种历史背景下,人们开始寻找可能替代化石能源的可再生能源,生物质能、太阳能、风能、地热能以及曾在历史短暂辉煌的生物质能被人们重新重视,我国在2006年1月1日执行(可再生能源法) 对生物质发电补贴0.25元人民币/每1度电(1KW)。
2,概述该系统具有占地小、环保、易操作、易运输、易安装、功能完善、维修快捷的特点。
可将目前各种生物质能秸秆:稻秆、稻壳、果壳、棉花杆、玉米秆、小米秆、木屑、甘蔗渣、麦杆、棕榈壳等生物质进行气化处理,达到冷却、净化的燃气为目的。
该系统在较小的空间内对生物质进行气化、冷却、除尘、除焦处理;同时,最大限度的降低了用户在使用过程中的维修及零配件更换时间,从而减少了使用成本。
并采用半自动方式控制并配置自动保护装置,保证了环保型气化系统的使用过程中的稳定性、安全性。
3,设计原则选择先进成熟可靠的技术及装备,能充分满足产品要求及环保要求,保证工艺的合理性及长期运行的稳定性,实用与节约投资相结合。
二,设备组成生物质循环气化发电装置主要由进料机构、燃气发生装置、燃气净化装置、燃气发电机组、控制装置及废水处理设备六部分组成.三、技术参数产气量:300m3/h以上发热量:1100-1350大卡气化效率:70%发电功率:100KW以上发电效率:30%-40%原文地址:/tech/9184.html。
生物质气化发电技术废物转化为可再生能源之道

生物质气化发电技术废物转化为可再生能源之道随着全球能源需求的增长和环境问题的日益凸显,对可再生能源的需求不断提升。
生物质气化发电技术以其高效、环保的特点,成为了转化废物为可再生能源的一种重要途径。
本文将介绍生物质气化发电技术以及废物转化为可再生能源的过程。
一、生物质气化发电技术简介生物质气化发电技术是指利用生物质废物作为原料,通过氧化和热解的过程将其转化为可燃性气体,并利用气体发电。
该技术能够实现废物资源化利用,并产生可再生能源。
生物质气化发电技术的核心设备包括气化炉、净化设备以及发电机组等。
二、废物转化为可再生能源的过程1. 废物收集与预处理为了获得高质量的原料,首先需要对废物进行收集与预处理。
收集的废物包括农林废弃物、城市垃圾等。
预处理过程包括废物切碎、除杂和干燥等步骤,以提高气化过程的效率。
2. 生物质气化经过预处理的废物送入生物质气化炉中进行气化处理。
气化炉中通过控制氧气供应和温度,使废物在缺氧或氧限制的条件下发生热解和气化反应,生成可燃性气体。
3. 气体净化与能源转化气化产生的气体中含有一定的杂质和有害物质,需要经过净化设备进行处理,以提高气体的纯度。
净化过程主要包括除尘、除硫、除氮等处理,以保证气体的可燃性和环保性。
净化后的气体可以用于直接燃烧,也可以用于燃气发电。
对于小型规模的生物质气化系统,可以采用内燃机或燃气轮机发电;而对于大型规模的系统,则可以选择蒸汽发电或燃气联合循环发电。
三、生物质气化发电技术的优势1. 资源丰富可再生废弃的农林废物和城市垃圾等是生物质气化发电技术的主要原料,这些废物资源丰富,并呈现可持续增长的趋势。
通过废物转化为可再生能源,可以减少对传统能源的依赖,实现资源的有效利用。
2. 环境友好低碳生物质气化发电技术所产生的气体具有低污染、低排放的特点。
而且生物质气化过程中产生的二氧化碳在植物生长过程中会被吸收,形成可持续循环。
3. 多能合一高效生物质气化发电技术既可以获得燃气,也可以获得余热用于供热和生产过程中,实现多能合一的效果。
【PPT】生物质气化发电技术(精)
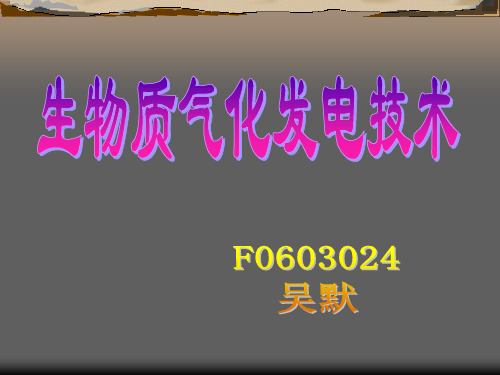
形成NO2 水洗SCR等 堵塞、难以燃 裂解、除焦 烧 、水洗 水洗化学反 腐蚀污染 应法
•燃气高温过滤 •燃气除焦技术:
焦油裂解
水洗除焦:同时有除焦、除尘和降温三方面的效果 静电除焦 :除尘、除焦效率高,一般达98%以上
结论 (1) 生物质气化技术是一项较新的技术,其技术目 前还不很成熟,还有许多方面需要完善 ; (2) 流化床生物质气化炉比固定床生物质气化具有 更大的经济性,应该成为我国今后生物质气化研究的 主要方向; (3) 与欧美国家相比,目前我国生物质气化还是以 中小规模、固定床、低热值气化为主,利用现有技术, 研究开发经济上可行、效率较高的系统,是目前发展 我国生物质气化发电技术的一个主要课题,也是我国 能否有效利用生物质的关键。
生物质气化发电技术
意义
工作原理
流程与主要设备 关键技术
意义
•处理农业废料
•减少CO2及SO2、 NOx等污染气体的排放
工作原理
生物质气化发电技术的基本原理是把生物质转化为 可燃气,再利用可燃气推动燃气发电设备进行发电。
气化发电过程包括三个方面
•生物质气化 •气体净化 •燃气发电
流下吸式 鼓泡流化床 适应不同形状尺 大块原料不 原料尺寸控制较 原料适应 寸原料、含水量 经预处理可 严,需预处理过 在15-45%间可 直接使用。 程。 性 稳定运行。 燃气特点 H 2和CnHm含量 少,CO 2含量 高,焦油含量 高,需要复杂净 后处理过 化处理。 程的简单 性 设备实用 生产强度小。 性、单炉 生产能力 结构简单、加工 、结构复 制造容易 杂程度、 制造维修 费用 H 2含量增加 。焦油经高 温区裂解, 含量减 少。 与直径相同的固 定床比,产气量 大4倍,焦油较 少,燃气成分稳 定,后处理过程 简单。
生物质能发电工作原理

生物质能发电工作原理生物质能发电是指利用生物质作为燃料进行发电的一种方式。
生物质是指由植物和动物所产生的有机物质,如木材、农作物残余物、畜禽粪便等。
生物质能发电的工作原理主要包括生物质燃烧发电和生物质气化发电两种方式。
一、生物质燃烧发电生物质燃烧发电是将生物质作为燃料,经过燃烧产生高温高压蒸汽,然后利用蒸汽驱动涡轮发电机发电。
其工作过程如下:1. 原料准备:收集和处理合适的生物质燃料,如木材、农作物残余物和废弃物等。
2. 燃烧过程:将生物质燃料送入燃烧炉中进行燃烧,在高温下释放燃料中所含的化学能,产生高温高压蒸汽。
3. 蒸汽扩压:将燃烧释放的蒸汽送入蒸汽轮机中,通过涡轮的扩张和旋转,使蒸汽的动能转化为机械能。
4. 发电:涡轮转动时,驱动连接在轴上的发电机旋转,产生电能。
5. 能量回收:蒸汽在发电过程中失去了一部分能量,但仍保持一定的热量。
利用余热回收系统,将余热转化为其他有用的能量,如供暖或加热。
生物质燃烧发电具有供应稳定、可再生、低碳排放等优点,能够有效利用生物质资源,减少对传统化石能源的依赖。
二、生物质气化发电生物质气化发电是通过将生物质燃料在缺氧或氧气限制的条件下进行热解和气化,生成合成气,再利用合成气驱动内燃机或燃气轮机发电。
1. 原料准备:收集和处理适当的生物质燃料,如农作物秸秆、木屑等。
2. 气化反应:将生物质料送入气化炉内,在高温下进行热解和气化反应,生成合成气。
反应中的产物包括一氧化碳、氢气和少量的甲烷、二氧化碳等。
3. 气体净化:将合成气经过净化处理,去除其中的颗粒物、硫化物和氯化物等有害物质,以保护后续设备的正常运行。
4. 燃烧或发电:合成气进入内燃机或燃气轮机,在高温高压条件下燃烧或扩张,转化为机械能,驱动发电机发电。
5. 废气处理:气化过程中产生的废气含有有害物质,需要进行处理,如高温焚烧、吸收和过滤等方式,以达到排放标准。
生物质气化发电技术能够高效利用生物质资源,减少传统能源消耗,减少环境负荷,具有较高的经济性和环境友好性。
- 1、下载文档前请自行甄别文档内容的完整性,平台不提供额外的编辑、内容补充、找答案等附加服务。
- 2、"仅部分预览"的文档,不可在线预览部分如存在完整性等问题,可反馈申请退款(可完整预览的文档不适用该条件!)。
- 3、如文档侵犯您的权益,请联系客服反馈,我们会尽快为您处理(人工客服工作时间:9:00-18:30)。
生物质气化发电技术1.气化发电的工作原理及工艺流程1.1气化发电工作原理生物质气化发电技术的基本原理是把生物质转化为可燃气,再利用可燃气推动燃气发电设备进行发电。
它既能解决生物质难于燃用而又分布分散的缺点,又可以充分发挥燃气发电技术设备紧凑而污染少的优点,所以是生物质能最有效最洁净的利用方法之一。
气化发电过程包括三个方面,一是生物质气化,把固体生物质转化为气体燃料;二是气体净化,气化出来的燃气都带有一定的杂质,包括灰份、焦炭和焦油等,需经过净化系统把杂质除去,以保证燃气发电设备的正常运行;三是燃气发电,利用燃气轮机或燃气内燃机进行发电,有的工艺为了提高发电效率,发电过程可以增加余热锅炉和蒸汽轮机。
生物质气化发电技术是生物质能利用中有别于其他可再生能源的独特方式,具有三个方面特点:一是技术有充分的灵活性,由于生物质气化发电可以采用内燃机,也可以采用燃气轮机,甚至结合余热锅炉和蒸汽发电系统,所以生物质气化发电可以根据规模的大小选用合适的发电设备,保证在任何规模下都有合理的发电效率。
这一技术的灵活性能很好地满足生物质分散利用的特点;二是具有较好的洁净性,生物质本身属可再生能源,可以有效地减少CO2、SO2等有害气体的排放。
而气化过程一般温度较低(大约在700-900oC),NOx的生成量很少,所以能有效控制NOx的排放;三是经济性,生物质气化发电技术的灵活性,可以保证该技术在小规模下有效好的经济性,同时燃气发电过程简单,设备紧凑,也使生物质气化发电技术比其他可再生能源发电技术投资更小,所以总的来说,生物质气化发电技术是所有可再生能源技术中最经济的发电技术,综合的发电成本已接近小型常规能源的发电水平。
典型的生物质气化发电工艺流程如图1-1所示。
图1-1气化发电系统流程图生物质循环流化床气化发电装置主要由进料机构,燃气发生装置,燃气净化装置,燃气发电机组、控制装置及废水处理设备六部分组成:进料机构:进料机构采用螺旋加料器,动力设备是电磁调速电机。
螺旋加料器既便于连续均匀进料,又能有效地将气化炉同外部隔绝密封起来,使气化所需空气只由进风机控制进入气化炉,电磁调速电机则可任意调节生物质进料量。
燃气发生装置:气化装置可采用循环流化床气化炉或其他可连续运行的气化炉,它主要由进风机,气化炉和排渣螺旋构成。
生物质在气化炉中经高温热解气化生成可燃气体,气化后剩余的灰份则由排渣螺旋及时排出炉外。
燃气净化装置:燃气需经净化处理后才能用于发电,燃气净化包括除尘、除灰和除焦油等过程。
为了保证净化效果,该装置可采用多级除尘技术:例如惯性除尘器、旋风分离器、文氏管除尘器、电除尘等,经过多级除尘,燃气中的固体颗粒和微细粉尘基本被清洗干净,除尘效果较为彻底;燃气中的焦油采用吸附和水洗的办法进行清除,主要设备是两个串联起来的喷淋洗气塔。
燃气发电装置:可采用燃气发电机组或燃气轮机。
由于目前国内燃气内燃机的最大功率只有500kW,故大于500kW发电机系统可由多台500kW的发电机并联而组成。
燃气轮机必须根据燃气的要求进行相应的改造,目前该项技术国内还未开展,国外技术也不成熟,所以成本较高。
控制装置:由电控柜,热电偶及温度显示表,压力表及风量控制阀所构成。
在用户需要实业可增加相应的电脑监控系统。
废水处理设备:采用过滤吸附、生物处理或化学、电凝聚等办法处理废水,处理后的废水可以循环使用。
1.2生物质气化发电技术的分类生物质气化发电系统由于采用气化技术和燃气发电技术的不同,其系统构成和工艺过程有很大的差别。
从气化形式上看,生物质气化过程可以分成为固定床和流化床两大类,固定床气化包括上吸式气化、下吸式气化和开心层下式气化三种,现在这三种形式的气化发电系统都有代表性的产品。
流化床气化包括鼓泡床气化、循环流化床气化及双流化床气化三种。
这三种气化发电工艺目前都有研究,其中研究和应用最多是循环流化床气化发电系统。
(另外,国际上为了实现更大规模的气化发电方式,提高气化发电效率,正在极积开发高压流化床气化发电工艺。
)从燃气发电过程上看,气化发电可分为内燃机发电系统,燃气轮机发电系统及燃气—蒸汽联合循环发电系统。
内燃机发电系统以简单的燃气内燃机组为主,可单独燃用低热值燃气,也可以燃气、油两用,它的特点是设备紧凑,系统简单、技术较成熟、可靠;燃气轮机发电系统采用低热值燃气轮机,燃气需增压,否则发电效率较低,由于燃气轮机对燃气质量要求高,并且需有较高的自动化控制水平和燃气轮机改造技术,所以一般单独采用燃气轮机的生物质气化发电系统较少。
燃气—蒸汽联合循环发电系统是在内燃机、燃气轮机发电的基础上增加余热蒸汽的联合循环,该种系统可以有效地提高发电效率。
一般来说,燃气—蒸汽联系循环的生物质气化发电系统采用的是燃气轮发电设备,而且最好的气化方式是高压气化,构成的系统称为生物质整体气化联合循环(B/IGCC)。
它的一般系统效率可以达40%以上,是目前发达国家重点研究的内容。
传统的B/IGCC技术包括生物质气化,气体净化,燃气轮机发电及蒸汽轮机发电。
由于生物质燃气热值低(约1200kcal/m3),炉子出口气体温度较高(800℃以上),要使IGCC具有较高的效率,必须具备两个条件,一是燃气进入燃气轮机之前不能降温,二是燃气必须是高压的。
这就要求系统必须采用生物质高压气化和燃气高温净化两种技术才能使IGCC的总体效率达到较高水平(>40%),否则,如果采用一般的常压气化和燃气降温净化,由于气化效率和带压缩的燃气轮机效率都较低,气体的整体效率一般都低于35%。
从纯技术的角度看,生物质IGCC技术可以大大地提高生物质气化发电的总效率。
目前国际上有很多先进国家开展这方面研究,如美国Battelle (63MW)和夏威夷(6MW)项目,欧洲英国(8MW)和芬兰(6MW)的示范工程等,但由于焦油处理技术与燃气轮机改造技术难度很高,仍存在很多问题,如系统未成熟,造价也很高,限制了其应用推广。
以意大利12MW 的IGCC示范项目为例,发电效率约为31.7%,但建设成本高达25000元/kW,发电成本约1.2元/kW.h,实用性仍很差。
近年来,欧洲为了解决开展了新的气化发电工艺研究(JOULE II 项目),如比利时(2.5MW)和奥地利(TINA,6MW)开展的生物质气化与外燃式燃气轮机发电技术。
它的主要目的是发展适合于中小型规模使用的生物质气化发电技术,解决B/IGGCC过程中碰的难题,提高生物质气化发电技术的实用性,它的基本原理是生物质气化后,燃气不需经过交货除焦,直接在燃烧器中燃烧,燃烧后的烟气用来加热高压的空气,最后由高温高压空气推动燃气轮机发电,该技术路线的最大优点是避开了高温除尘及除焦两大难题,但最大的难题是高温空气供热设备的材料和工艺问题。
由于该项目的设备可靠性和造价问题,目前还很难进入实际应用(图1-2)图1-2 Free Un流程从发电规模上分,生物质气化发电系统可分为小型、中型、大型三种,小型气化发电系统简单灵活,主要功能为农村照明或作为中小企业的自备发电机组,它所需的生物质数量较多少,种类单一,所以可以根据不同生物质形状选用合适的气化设备,一般发电功率,<200KW。
中型生物质气化发电系统主要作为大中型企业的自备电站或小型上网电站,它可以适用于一种或多种不同的生物质,所需的生物质数量较多。
需要粉碎、烘干等预处理,所采用的气化方式主要以流化床气化为主,中型生物质气化发电系统用途广泛,适用性强,是当前生物质气化技术的主要方式,功率规模一般在500~3000KW之间。
大型生物质气化发电系统主要功能是作为上网电站,它可以适用的生物质较为广泛,所需的生物质数量巨大,必须配套专门的生物质供应中心和预处理中心,是今后生物质利用的主要方面。
大型生物质气化发电系统功率一般在5000KW以上,虽然与常规能源比仍显得非常小,但在生物质能发展成熟后,它将是今后替代常规能源电力的主要方式之一。
表1-1各种生物质气化发电技术的特点在中国目前条件下研究开发与国外相同技术路线的B/IGCC的大型气化发电系统,由于资金和技术问题,将更加较困难。
由于我国工业水平的限制,目前,我国小型燃气轮机(﹤5000kW)的效率仅有25%左右(仅能用于天燃气或石油,如果利用低热值气体,效率更低),而且燃汽轮机对燃气参数要求很高(进口燃气H2S﹤200mg/N m3,萘﹤100mg/N m3,HCN﹤150mg/N m3,焦油与杂质﹤100mg/N m3)。
而国外的燃汽轮机的造价很高,单位造价约达7000元/KW左右(系统造价将达15000元/ kW以上)。
另外,由于我国仍未开展生物质高压气化的研究,所以在我国如果研究传统的B/IGCC系统,以目前的水平其效率将低于30%,而且有很多一时难以解决的技术问题。
针对目前我国具体实际,采用气体内燃机代替燃气轮机,其它部分基本相同的生物质气化发电过程,不失为解决我国生物质气化发电规模化发展的有效手段。
一方面,采用气体内燃机可降低对燃气杂质的要求(焦油与杂质含量﹤100mg/N m3即可),可以大大减少技术难度。
另一方面,避免了调控相当复杂的燃气轮机系统,大大降低系统的成本。
从技术性能上看,这种气化及联合循环发电在常压气化下整体发电效率可达28%—30%左右,只比传统的低压IGCC降低3%—5%。
但由于系统简单,技术难度小,单位投资和造价大大降低(约5000元/kW);更重要的是,这种技术方案更适合于我国目前的工业水平,设备可以全部国产化,适合于发展分散的、独立的生物质能源利用体系,可以形成我国自己的产业,在发展中国家大范围处理生物质中有更广阔的应用前景。
2生物质气化发电的关键技术2.1生物质气化工艺的设计与选用生物质的气化有各种各样的气化工艺过程。
从理论上讲,任何一种气化工艺都可以构成生物质气化发电系统。
但从气化发电的质量和经济性出发,生物质气化发电要求达到发电频率稳定、发电负荷连续可调两个基本要求,所以对气化设备而言,它必须达到燃气质量稳定,燃气产量可调,而且必须参连续运行。
在这些前提下,气化能量转换效率的高低是气化发电系统运行成本的才是关键所在。
气化形式选定以后,从系统匹配的角度考虑,气化设备应满足以下要求:(1)产气尽可能干净,以减少后处理系统的复杂性,使焦油含量达到内燃机允许的程度。
如果后续净化系统选用催化裂解工艺,还要尽可能使原始气中的焦油具有易于催化裂解的特点;(2)产气热值要高而且稳定,以提高内燃机的输出功率,增大整个系统的效率;(3)设计气化炉本体及加料排渣系统,应充分考虑原料特性,实现连续运行;(4)充分利用余热,提高能量利用率。
表1-2是各种气化炉的特性,是气化发电系统选择气化炉形式和控制运行参数的制约条件。