合成操作规程
有机合成反应操作规程

有机合成反应操作规程有机合成反应操作规程一、实验室准备工作1. 实验室环境整洁,确保实验区域没有杂物和易燃物。
2. 所有的仪器、设备和试剂都应处于良好的工作状态,确保能够正常操作。
3. 个人穿戴实验室所需的防护用品,包括实验服、手套、护目镜和实验室鞋。
4. 检查实验室中的应急处理设备,如消防器材和急救箱等。
二、试剂准备1. 仔细查看试剂的物质安全数据表(MSDS),了解试剂的性质、危险性和操作注意事项。
2. 使用纯度较高的试剂,避免有机杂质对实验结果的影响。
3. 将试剂按照实验所需的量准备好,并注意正确标记试剂瓶。
三、实验操作1. 在操作前,将实验步骤仔细阅读,并确保对操作流程有充分的了解。
2. 使用正确的仪器和设备进行各项操作,并确保其正常工作。
3. 按照实验步骤逐步进行反应操作,注意操作的顺序和时间控制。
4. 使用适当的容器和反应条件,避免溶剂和试剂的蒸发和挥发。
5. 在操作过程中,注意观察反应物的颜色、温度、气味等变化,并记录相关观察结果。
6. 在处理有机溶剂和有机试剂时,注意对其蒸汽的远离点燃源,并保持通风良好。
7. 使用适当的电子天平、滴定仪、分光光度计等测量仪器,确保实验结果的准确性。
8. 在反应物和产物的处理过程中,遵循环保原则,妥善处理废弃物。
四、安全注意事项1. 所有操作必须在通风良好的实验室内进行,避免有机蒸汽的积聚。
2. 当操作易燃或有毒的试剂时,注意提前做好安全隔离措施和防护措施。
3. 在操作有机物时,禁止吸烟、饮食和使用手机等不必要的行为。
4. 在发生意外或紧急情况时,及时采取相应的应急措施,并向实验室负责人报告。
5. 实验结束后,将实验台面和仪器设备彻底清洁,并将实验废弃物正确处理。
五、实验记录1. 在实验过程中,及时记录实验的所有数据和观察结果。
2. 实验记录应准确、详细,并包括实验开始和结束的时间,使用的试剂和仪器设备的规格型号等信息。
3. 实验记录应保留在实验室内,以备将来参考和查阅。
硫脲合成工序工艺操作规程及安全规定范文

硫脲合成工序工艺操作规程及安全规定范文硫脲合成是一种重要的有机化工工艺,以下是硫脲合成工序工艺操作规程及安全规定的范文,供参考:一、目的及适用范围:本操作规程适用于硫脲合成工序的生产过程,旨在规范工作人员在生产操作中的行为规范,提高生产效率,并保障工作人员的人身安全和设备设施的安全。
二、工艺操作规程:1.在进行硫脲合成之前,应检查生产设备的完好性,并确保设备具备正常运行条件。
2.汽车与要求的合成温度进行调节并设置好温度控制装置。
3.准备好所需的硫脲原料、溶剂等辅助物料,并根据工艺要求进行称量。
4.将硫脲原料和溶剂按工艺要求加入反应釜中,注意操作过程中做到精确称量,避免溢漏。
5.开始加热反应釜,控制升温速率适中,不超过工艺要求,避免因温度升高过快导致产物失控。
6.在加热过程中,保持反应釜内压力与温度的稳定,按工艺要求进行搅拌。
7.当反应达到设定的时间后,停止加热,立即冷却反应釜,以避免产物进一步热分解。
8.反应结束后,将产物进行过滤或离心分离,得到所需的硫脲产品。
9.清洗反应器及周边设备,确保无残留物。
三、安全规定:1.操作人员应戴好防护用品,包括手套、护目镜、防护服等,以保障操作人员人身安全。
2.在操作过程中,要保持清醒,切勿酗酒或使用任何会使人失去集中注意力的物品。
3.良好的通风环境对于工艺的顺利进行和人身安全至关重要,若通风不良,应配备好通风设备。
4.严禁在工作现场吸烟、饮食或带入易燃易爆物品,以免引发火灾或爆炸事故。
5.在工艺操作中,应保持设备设施的完好性,发现异常及时汇报,不得擅自进行修理。
6.如果在操作过程中发生任何有害物质泄漏,应立即通知相关人员,并采取适当的应急措施进行处理。
7.硫脲合成工艺涉及有机物,应储存于专用区域,严禁存放与之相容性差的材料。
8.硫脲合成反应釜内部温度较高,禁止擅自打开盖子、触摸或接近反应釜,防止烫伤。
9.操作人员应参加相关培训,了解硫脲合成工艺的安全要求,并定期进行安全知识的学习。
合成作业安全操作规程(4篇)

合成作业安全操作规程1. 引言作业安全操作规程是为了保护员工的生命安全和工作环境的安全而制定的一套操作规程。
本文将详细介绍合成作业安全操作规程,希望能够提高员工的安全意识,预防事故的发生。
2. 人员管理2.1 员工应经过相关培训,熟悉工作岗位的安全操作规程;2.2 合成作业场所应有足够数量的安全员工,负责监督和管理作业现场;2.3 强调个人责任,每位员工都应对自己的安全有更高的意识。
3. 工作场所的安全设施3.1 合成作业场所应设有明显的安全警告标识,标明禁止吸烟、禁止使用明火等;3.2 消防设备应齐全,并定期进行维护和检查;3.3 定期检查和维护危险化学品储存区,确保储存区的安全。
4. 作业装备的安全使用4.1 使用任何作业装备前,应仔细阅读操作说明书,并由专人进行培训;4.2 定期检查和维护作业装备,确保其正常运行;4.3 使用作业装备时,应佩戴必要的安全防护用品,如安全帽、防护眼镜等。
5. 危险源的控制5.1 对于隐患和危险源,应及时进行评估和控制;5.2 严禁使用易燃、易爆物品;5.3 对于容易引发事故的作业区域,应进行隔离和标示。
6. 废物处理6.1 废弃物应按照规定分类和储存,并定期清理;6.2 废弃物的处理应符合相关环保法规。
7. 紧急情况下的应对措施7.1 员工应熟悉急救常识,并掌握相关急救设备的使用方法;7.2 出现火灾、泄漏等紧急情况时,应立即向上级报告,并采取有效措施进行控制。
8. 作业现场监督和检查8.1 定期进行作业现场的监督和检查,发现问题及时纠正;8.2 对于违反安全操作规程的人员,应及时予以警告和纠正;8.3 作业现场应设有安全检查记录,以备后续参考和复查。
9. 事故调查和防范9.1 发生事故后应尽快组织调查,并总结经验教训,提出改进措施;9.2 针对可能的事故隐患,应做好相应的防范措施。
10. 员工安全教育和培训10.1 定期组织员工参加安全教育和培训,提高员工安全意识;10.2 安全教育和培训内容应包括作业安全操作规程、急救知识等。
功夫酰氯合成操作规程

功夫酰氯合成操作规程功夫酰氯合成是一种重要的有机合成方法,广泛应用于有机合成领域。
下面就对功夫酰氯合成的操作规程进行详细介绍。
一、操作前的准备工作:1. 安全防护:穿戴防护眼镜、实验服、手套等个人防护装备,保证实验操作安全。
2. 准备玻璃仪器:准备好所需的实验仪器,如三口瓶、磁力搅拌子、浓硫酸滴定管等。
3. 清洗仪器:使用去离子水或其他合适溶剂清洗实验仪器,保证实验无杂质。
二、合成操作步骤:1. 取一定量的苯甲酸和过量的的无水氯化亚砜放入三口瓶中。
2. 开启磁力搅拌子,将其放入三口瓶中,开始搅拌。
3. 缓慢滴加浓硫酸至三口瓶中,同时控制加热源使其保持温度在50-60℃之间。
滴加浓硫酸的速度应适度,使其与苯甲酸、氯化亚砜充分反应。
4. 在反应完成后,停止加热,继续搅拌一段时间,使反应体系充分混合,从而得到较好的反应产物。
5. 倾倒反应混合物到含稀释剂的三口瓶中,并用去离子水迅速洗涤三口瓶,将洗涤液也加入反应体系中。
6. 在洗涤液中加入适量饱和硫酸以除去水分,由于饱和硫酸比水活泼,所以水分会被吸附,保持反应产物的纯度。
7. 将混合物转移至分液漏斗中,放置一段时间,分为两层后将有机相收集到干净的干燥瓶中。
8. 使用饱和氯化钠溶液洗涤有机相,去除其中残留的无水氯化亚砜等杂质。
9. 使用无水氯化钠或其他适合的干燥剂对有机相进行干燥。
10. 进行理化性质检测,如测定产品的沸点、密度、熔点等,以确保合成的功夫酰氯达到要求。
11. 将产品存放在干燥、避光的地方进行保存,以避免与空气、水分等发生反应。
三、实验注意事项:1. 在操作前要仔细读取化学品的安全说明书,了解其危害性,并严格按照安全操作规程操作。
2. 操作过程中要注意保持反应体系的温度、pH值等,以确保反应的进行。
3. 在制备功夫酰氯过程中,硫酸是铁三氯、铁氯等的形成条件,所以要避免硫酸被水分溅溢。
4. 反应后的废液处理要按照相关规定进行处理,避免对环境造成污染。
化工公司合成工段操作规程工作流程 (一)
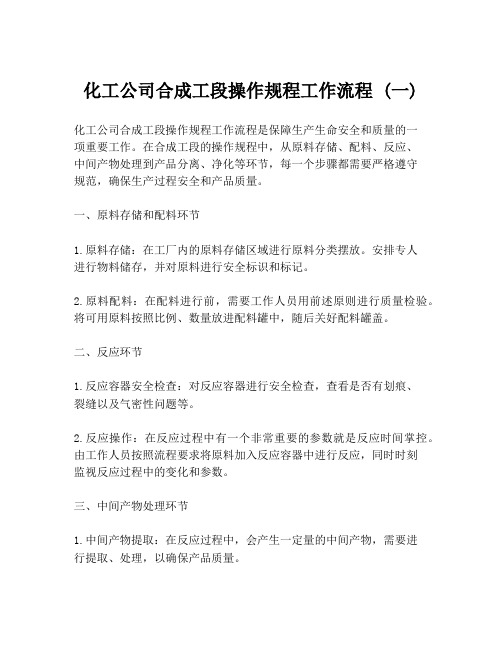
化工公司合成工段操作规程工作流程 (一)化工公司合成工段操作规程工作流程是保障生产生命安全和质量的一项重要工作。
在合成工段的操作规程中,从原料存储、配料、反应、中间产物处理到产品分离、净化等环节,每一个步骤都需要严格遵守规范,确保生产过程安全和产品质量。
一、原料存储和配料环节1.原料存储:在工厂内的原料存储区域进行原料分类摆放。
安排专人进行物料储存,并对原料进行安全标识和标记。
2.原料配料:在配料进行前,需要工作人员用前述原则进行质量检验。
将可用原料按照比例、数量放进配料罐中,随后关好配料罐盖。
二、反应环节1.反应容器安全检查:对反应容器进行安全检查,查看是否有划痕、裂缝以及气密性问题等。
2.反应操作:在反应过程中有一个非常重要的参数就是反应时间掌控。
由工作人员按照流程要求将原料加入反应容器中进行反应,同时时刻监视反应过程中的变化和参数。
三、中间产物处理环节1.中间产物提取:在反应过程中,会产生一定量的中间产物,需要进行提取、处理,以确保产品质量。
2.中间产物处理:中间产物处理方式有多种,可以采用分离提纯、萃取、结晶等方法。
根据反应体系,制定相应的处理方案。
四、产品分离和净化环节1.离心操作:在该操作环节中,需要使用离心机进行分离,收集分离出来的产品2.产品净化和收集:收集后的产品需要进行净化和收集操作,包括臭味、颜色、纯度检测、盛放装罐等。
五、维护和记录环节维护和记录是操作规程中的重要一环。
需要员工在操作过程结束后对设备进行清洁和维护,以确保设备的正常运行。
同时还需要按规定记录生产批次、产品名称、产品质量指标、存储位置等信息,做好生产记录,为下一次生产提供参考依据。
总结:在化工公司合成工段操作规程工作流程中,要始终坚持安全标准、质量控制和生产效率三者平衡。
这不仅可以最大限度保障生产的顺利进行,还可以确保生产成果的品质和规范性。
药品合成岗位标准操作规程
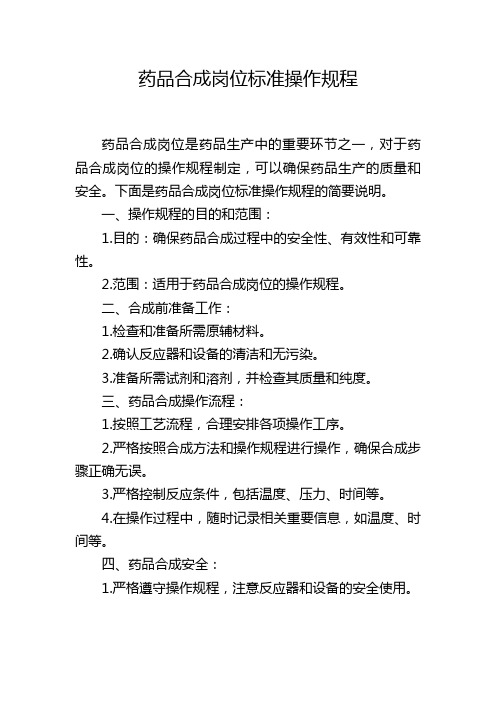
药品合成岗位标准操作规程药品合成岗位是药品生产中的重要环节之一,对于药品合成岗位的操作规程制定,可以确保药品生产的质量和安全。
下面是药品合成岗位标准操作规程的简要说明。
一、操作规程的目的和范围:1.目的:确保药品合成过程中的安全性、有效性和可靠性。
2.范围:适用于药品合成岗位的操作规程。
二、合成前准备工作:1.检查和准备所需原辅材料。
2.确认反应器和设备的清洁和无污染。
3.准备所需试剂和溶剂,并检查其质量和纯度。
三、药品合成操作流程:1.按照工艺流程,合理安排各项操作工序。
2.严格按照合成方法和操作规程进行操作,确保合成步骤正确无误。
3.严格控制反应条件,包括温度、压力、时间等。
4.在操作过程中,随时记录相关重要信息,如温度、时间等。
四、药品合成安全:1.严格遵守操作规程,注意反应器和设备的安全使用。
2.确保操作区域的通风良好,防止有害气体对操作人员的危害。
3.严格遵守防火防爆要求,禁止在操作区域内吸烟、使用明火等。
4.注意用药人员的人身安全,如穿戴个人防护装备,避免接触有毒有害物质。
5.合理安排操作人员的劳动强度,避免疲劳引起的操作失误。
五、实验室环境和设施:1.确保实验室环境和设施的清洁整洁,并定期进行检查和维护。
2.保证实验室的温度、湿度、光照等环境条件符合要求。
3.检查实验室的通风系统和安全设备的运行情况。
六、药品合成质量控制:1.合成过程中要注意反应的产率和纯度,并进行实时监测。
2.合成完成后,按照规定的方法进行产品的检验和测试。
3.及时记录和报告合成过程和产品质量的相关信息,包括不良现象和事件。
七、事故和应急处理:1.在发生事故或紧急情况时,立即采取应急措施,确保人员的安全。
2.及时报告相关人员,寻求专业人员的帮助和指导。
3.保护现场,避免事故扩大和二次污染。
八、操作规程的更新和整改:1.定期评估操作规程的有效性,并根据实际情况进行修订和更新。
2.对操作中发现的问题和不良现象,进行整改和改进。
化工合成操作规程
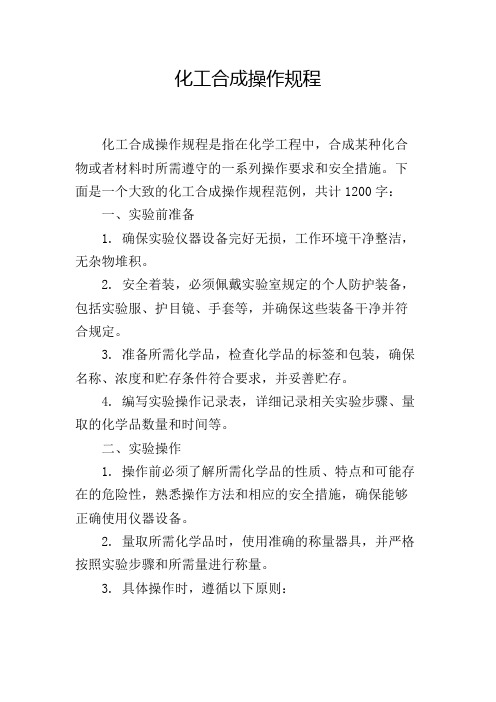
化工合成操作规程化工合成操作规程是指在化学工程中,合成某种化合物或者材料时所需遵守的一系列操作要求和安全措施。
下面是一个大致的化工合成操作规程范例,共计1200字:一、实验前准备1. 确保实验仪器设备完好无损,工作环境干净整洁,无杂物堆积。
2. 安全着装,必须佩戴实验室规定的个人防护装备,包括实验服、护目镜、手套等,并确保这些装备干净并符合规定。
3. 准备所需化学品,检查化学品的标签和包装,确保名称、浓度和贮存条件符合要求,并妥善贮存。
4. 编写实验操作记录表,详细记录相关实验步骤、量取的化学品数量和时间等。
二、实验操作1. 操作前必须了解所需化学品的性质、特点和可能存在的危险性,熟悉操作方法和相应的安全措施,确保能够正确使用仪器设备。
2. 量取所需化学品时,使用准确的称量器具,并严格按照实验步骤和所需量进行称量。
3. 具体操作时,遵循以下原则:- 保持操作仪器干燥和清洁,并及时清理操作区域的杂物和废弃物。
- 在进行反应过程中,控制温度、压力和反应时间,避免产生危险性气体或生成不稳定物质。
- 加入试剂时,要注意缓慢滴注或加入,并避免产生剧烈反应。
- 在操作期间,仔细观察反应过程中的实验现象,及时调整反应条件,保证实验顺利进行。
- 在实验中要严格执行安全操作规程,按照操作规范使用通风设备、防爆设备和相关防护装置。
4. 实验结束后,对仪器设备和操作区域进行清理和消毒,彻底清除可能存在的污染物,保持实验室的清洁和整齐。
三、安全措施1. 在进行化学合成操作前,应了解所用化学品的危险性及适当的应对措施,并佩戴相应的个人防护装备。
2. 在操作前要对实验室停电按钮、紧急洗眼器、紧急淋浴等应急设备进行检查,确保其正常工作。
3. 配置酸、碱或其他有毒、易燃的试剂时,应使用专用配制设备,并注意操作过程中的防护和气体排放。
4. 在操作过程中,减少或避免进行不可逆的反应,避免或减少产生有毒气体和不稳定物质。
5. 合成反应时,要掌握温度、压力、搅拌速度等操作条件,以确保反应安全和产物质量。
合成岗位操作规程

合成岗位操作规程一、岗位任务1、岗位要紧任务本岗位是将合成气压缩岗位来的工艺气体,在一定温度、压力、催化剂作用下,在甲醇合成塔内合成粗甲醇,将生产的粗甲醇送至精馏岗位;并利用其反应热副产中压蒸汽,经减压减温送至低压蒸汽管网;合成弛放气送往能源利用公司做原料气或送往转化岗位做燃料气或送往焦化分厂做回炉煤气。
2、管辖范畴甲醇合成塔、洗醇塔、稀醇水槽、闪蒸槽、甲醇分离器、汽包、磷酸盐槽、排污膨胀器、气气换热器、水冷器、取样冷却器、蒸汽喷射器、一级过滤器、二级过滤器、稀醇水泵、磷酸盐泵等设备及其有关的外表、电气、管线、DCS。
二、差不多原理入塔合成气中的一氧化碳、二氧化碳分不与氢气在一定的压力、温度下,通过铜基催化剂的催化作用,在甲醇合成塔内生成甲醇并放出一定的热量。
放出热量的多少与反应温度、压力、入塔气体成份、合成转化率有关,一样随系统压力的升高而增大。
要紧反应方程:CO+2H2《--> CH30H+QCO2+3H2《--> CH3OH+H2O+Q 甲醇合成反应是放热的,体积缩小的反应,因此降低温度,提升压力有利于正反应的进行。
在合成甲醇的过程中,由于触媒缘故及二氧化碳和其它气体的存在,还有一些副反应发生,生成二甲醚、高级烷烃、醇、酸等杂质,如:2CH3OH《--> CH3OCH3+H2O+QCO+3H2《--> CH4+H2O+Q4CO+8H2《--> C4H9OH+H2O8CO+17H2 --> C8H18+8H2 等甲醇合成催化剂经还原后才有活性,因此合成催化剂在使用前,需进行还原,还原方程式为:CuO+ H2 = Cu + H2O。
三、工艺流程简述来自合成气压缩岗位的压力5.5MPa,总硫含量小于0.1 ppm的合成气, 温度约为60C,经两个串联的气气换热器的壳程被来自合成塔反应后的出塔热气体加热到活性温度以上,进入甲醇合成塔顶部。
甲醇合成塔为立式绝热管壳型反应器。
合成操作规程

合成操作规程一、原始开车(大修后的开车)1、开车前的准备⑴确认以下准备工作已完成设备及管道的安装管道水压试验设备及管道吹扫和干燥(废热锅炉的煮炉)触媒的装填氮气气密试验⑵设备及管道上的所有阀门已正确就位,且处于适当的开关状态,管线盲板安装在合适位置,临时盲板和过滤器已拆除。
⑶仪表及联锁系统调试合格,功能正常。
⑷以下公用工程已按要求供应到位。
:冷却水、氮气、蒸汽、仪表空气、电。
⑸压缩机的油洗、单试、气密实验已完成,具备开车条件。
2、开车前的检查确认工作⑴检查确认各阀门均处于关闭状态⑵检查确认各调节阀处于受控状态,开关自由,中控与现场阀位一致。
⑶检查确认各联锁调试完毕。
3、氮气置换⑴氮气置换流程:从UV18007阀后氮气阀组引入→E1803壳程→R1801→E1801A管程→E1801管程↘F1801→E1802管程→E1803管程→E1804管程→E1805管程→E1806管程→E1807管程→→V1801→E1805壳程→HV18003↘V1802→PV18020排放↘PSV18010旁路⑵确认阀门的开关状态关闭UV18008、UV18007、从V1802返压缩机入口闸阀、LV18014及其旁路阀、前后切断阀。
手动微开LV18011A/B及其前后切断阀。
打开HV18001、TV18012、HV18002和F1801工艺气进出口蝶阀。
微开TV18007、TV18002、HV18003。
逐个打开各设备、管线的排放阀、导淋阀、分析取样阀。
⑶氮气置换的方法和步骤打开氮气阀组双道阀,关闭阀间导淋,将氮气引入合成回路。
关闭HV18003、PV18020和PSV18010旁路,将合成回路压力充至0.4-0.5MPa。
通过打开HV18003、PV18020和PSV18010旁路,将合成回路压力卸至0.05 MPa。
升压、卸压反复进行数次后,分别在取样点S-18005、S-18004取样分析,O2<0.2%为合格。
合成甲酸钠作业操作规程

合成甲酸钠作业操作规程1. 介绍甲酸钠是一种无机化合物,化学式为HCOONa。
它是甲酸和钠的盐,在工业和实验室中被广泛使用,是制备许多化学品的重要原料。
在本文中,我们将介绍合成甲酸钠的操作规程。
2. 实验材料•甲酸:99%纯度•碳酸钠:99%纯度•水:蒸馏水或去离子水•热板和玻璃棒•温度计•烧杯、烧瓶、滤纸和漏斗3. 实验步骤步骤一:准备试剂和设备1.取出所需试剂,甲酸和碳酸钠。
2.取出实验所需的设备,包括烧杯、烧瓶、漏斗和滤纸等。
步骤二:进行反应1.将烧瓶放在热板上,加入适量的蒸馏水或去离子水,大约为烧瓶容积的1/3。
2.用玻璃棒搅拌,加入碳酸钠,用温度计监测反应液温度,当温度升至80℃左右时停止加热。
3.慢慢加入甲酸,加完后继续搅拌,并将热板开到100℃进行加热。
步骤三:沉淀结晶分离1.将反应液加热到100℃,并继续搅拌,直到反应液中无未反应的碳酸钠。
2.将反应液进行过滤分离,将沉淀沉淀分离出来。
过滤过程中需用滤纸和漏斗过滤。
步骤四:结晶洗涤1.将过滤后的沉淀放在烧杯中,加入适量的蒸馏水或去离子水,用玻璃棒搅拌。
2.再次进行过滤分离,重复同样的步骤洗涤结晶。
步骤五:结晶干燥1.将过滤后的结晶放在玻璃器皿或其他干燥器皿中。
2.将结晶放在通风条件良好的地方干燥,直至干燥。
4. 实验注意事项1.实验中需保持安全,佩戴实验手套、防护眼镜等必要的防护用品。
2.需要小心操作,反应中不要让甲酸和钠碳酸反应过多。
3.在进行反应过程中,需温度控制良好,过热可能会导致反应失控。
4.合成后的甲酸钠应储存在干燥通风条件良好的地方,避免受潮。
5.通过本次实验,我们学习了甲酸钠的合成工艺和注意事项,并实际操作了甲酸钠的合成过程。
需要注意的是,在实验操作中需要谨慎,以免对人体和环境造成危害。
合成安全规程

合成岗位安全操作规程1、合成系统主要为高温、高压、易燃易爆工号,故进入装置区必须按规定穿戴劳保用品,尤其必须戴安全帽。
2、设备管线上的压力表、温度计、安全阀等要定期校对,定期检查,发现损坏立即更换,汽包连锁系统、报警系统不得随意旁路和摘除,确有必要摘除时,要及时通知领导。
3、系统升降温、升降压一定要按有关规定进行,不得大幅度升降。
升降压速度一般可控制在柳.4MPa/min。
合成床层温度大于210C方可接气,合成塔触媒层温度严防超过工艺指标;4、甲醇分离器液位一定要稳,不得过高过低,以防带液或者窜气。
5、停车时要注意关现场所有高、中、低压截止阀,防止串压。
如系统停车时间较长,需要检修,必须全系统卸压充氮,使其保持微正压,使合成系统处于惰性环境中,且中控应注意床层温度是否有升高趋势,判断是否有空气漏入,应马上继续充氮置换,直至床层温度恢复正常。
6、甲醇属易燃易爆危险品,要防止超压、泄漏。
现场应加强巡检,发现问题及时处理。
当系统有甲醇“跑、冒、滴、漏''时,操作人员要戴甲醇防护眼睛。
当甲醵滴入眼睛时,要尽快用清水洗净,最好在就近的洗眼器上洗净。
如有泄露用沙土或者泡沫灭火,不得用水灭火。
若处理不了一定要用湿毛巾或衣服捂住口鼻往上风向和高处撤退。
7、本工号机电仪出现问题,危及人身安全时,立即汇报有关领导,必要时先处理后汇报,以防事故扩大化。
8、当停车检修塔器置换后,分析氧含量在19-21%时方可进入塔器,并且要有专人监护。
因故进入甲醇分离器时,必须有专人监护并佩带长管面具。
9、操作人员要定期进行救护和防火训练,强调防护设备的重要性,确保报警顺序,在特殊情况下必须通知消防队,确保事故在控制之下。
合成岗位安全操作规程
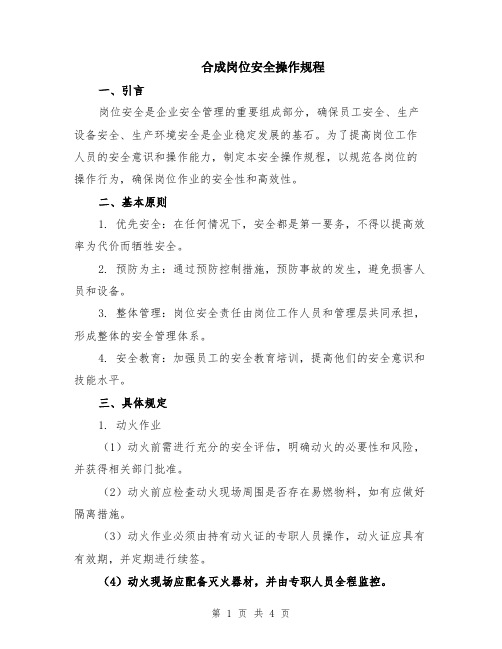
合成岗位安全操作规程一、引言岗位安全是企业安全管理的重要组成部分,确保员工安全、生产设备安全、生产环境安全是企业稳定发展的基石。
为了提高岗位工作人员的安全意识和操作能力,制定本安全操作规程,以规范各岗位的操作行为,确保岗位作业的安全性和高效性。
二、基本原则1. 优先安全:在任何情况下,安全都是第一要务,不得以提高效率为代价而牺牲安全。
2. 预防为主:通过预防控制措施,预防事故的发生,避免损害人员和设备。
3. 整体管理:岗位安全责任由岗位工作人员和管理层共同承担,形成整体的安全管理体系。
4. 安全教育:加强员工的安全教育培训,提高他们的安全意识和技能水平。
三、具体规定1. 动火作业(1)动火前需进行充分的安全评估,明确动火的必要性和风险,并获得相关部门批准。
(2)动火前应检查动火现场周围是否存在易燃物料,如有应做好隔离措施。
(3)动火作业必须由持有动火证的专职人员操作,动火证应具有有效期,并定期进行续签。
(4)动火现场应配备灭火器材,并由专职人员全程监控。
2. 高处作业(1)高处作业前应检查工作平台的稳固性和安全防护设施的完好性,如有异常应立即报告上级。
(2)高处作业必须穿戴符合标准的防护装备,包括安全带、安全帽等,并正确使用。
(3)高处作业需明确作业任务和作业流程,不得超出规定的范围和权限。
3. 机械设备操作(1)机械设备操作前应检查设备的工作状态和安全保护装置是否完好,如有异常应及时报修。
(2)操作人员必须接受相应培训和考核,持证上岗,并定期进行复审。
(3)操作人员在操作机械设备时,要严格按照操作规程进行操作,不得违章操作。
4. 危险品操作(1)危险品操作必须由持有相应操作证的专职人员操作,且必须定期进行培训和考核。
(2)危险品操作前应评估风险并采取相应的防护措施,如戴好防护手套、穿戴化学防护服等。
(3)危险品操作过程中,应遵循操作规范,不得超过规定的操作限度。
5. 电气设备操作(1)电气设备操作前应检查设备的绝缘情况和接地情况是否符合标准,如有异常应及时报修。
甲醇合成操作规程

主要副反应:2CO+4H2=CH3OCH3+H2O 4CO+8H2=C4H9OH+3H2O CO+3H2=CH4+H2O 2CO+2H2=CH4+CO2
2、2O2)
催化剂经过还原后才有活性。因此合成催化剂在使用前, 需要用 H2 进行还原,还原方程式为:CuO+H2=Cu+H2O
还原压力为 0.54MPa,最高还原温度为 230℃,还原气为 H2,稀释气体为 N2,要严格按照催化剂的升温还原程序进 行操作。
合成塔内催化剂的升温加热,用蒸汽喷射泵 M4001 来完 成。加入压力为 3.9MPa 的中压蒸汽,通过开工蒸汽喷射器 M4001 带动炉水循环,使催化剂床层温度逐渐上升。
分离出粗甲醇后的气体,压力约为 4.9MPa,温度约为 40℃,返回 C3002 的循环段,经加压后循环使用。为了防 止合成系统中惰性气体的积累,要连续从系统中排放少量 的循环气体:一部分直接作驰放气送转化工段,另一部分 经水洗塔洗涤甲醇后作为驰放气送往转化工段,整个合成 系统的压力由驰放气排放调节阀 PV4005 来控制。
甲醇车间合成操作规程
度约为 60℃的循环气混合,混合后的入塔气以每小时 540000NM3 的流量进入入塔气预热器 E4001A.、B 的壳程, 被来自合成塔 R4001A.、B 反应后的出塔热气体加热到 225℃后,进入合成塔 R4001A.、B 顶部。
R4001A.、B 为立式绝热——管壳型反应器。管内装有低 压甲醇合成催化剂。当合成气进入催化剂床层后,在 5.30MPa,220~260℃下 CO、CO2 与 H2 反应生成甲醇和水, 同时还有微量的其他有机杂质生成。合成甲醇的两个反应 都是强放热反应,反应释放出的热大部分由合成塔 R4001A.、B 壳程的沸腾水带走。通过控制汽包压力来控制 催化剂床层温度及合成塔出口温度。从 R4001A.、B 出来的 热反应气进入入塔气预热器 E4001A.、B 的管程与入塔合成 气逆流换热,被冷却到 90℃左右,此时有一部分甲醇被冷 凝成液体。该气液混合物再经水冷器 E4002A、B 进一步冷 凝,冷却到≤40℃,再进入甲醇分离器 V4002 分离出粗甲 醇。
合成操作规程

合成岗位操作规程1、岗位职责1.1在甲醇班长的领导下,直属中控室指挥,完成本岗位的生产任务。
1.2严格执行本岗位操作技术规程和安全规程,不违章,不违纪,确保人身、设备安全和产品质量稳定。
1.3负责对各工艺数据如实记录,定时向生产调度室报告并服从调度室的指挥及安排。
1.4负责本岗位设备及所属管道阀门控制点、电气、仪表、安全防护设施等的管理。
1.5管好岗位所配工具、用具、防护器材、消防器材,通讯联络设施和照明。
1.6负责本岗位所管理设备的润滑、维护保养、环境卫生清洁,严防各种跑、冒、滴、漏事故的发生。
1.7发现生产异常或设备故障时应及时处理,并将发生的原因和处理经过及时向班长和生产调度室汇报,并如实记录。
1.8负责在《岗位操作记录报表》上填写各项工艺技术参数;在《生产作业交接班记录》中填写生产记录。
1.9按交接班制度认真做好交接班。
1.10服从班组和各部门分配工作,努力完成各项工作任务。
2、岗位工艺技术规定与操作指标2.1工艺说明甲醇合成原理经过合成气压缩机压缩后的合成气,一氧化碳和氢气在一定的压力、温度下,通过催化剂的催化作用,在合成塔内生成甲醇并放出一定的热量主要反应方程:CO+2H2←→CH3OH+ QCO2+3H2←→CH3OH+H2O+ Q这是放热的,体积缩小的反应,所以降低温度,提高压力有利于正反应的进行。
在合成甲醇的过程中,还有一些副反应发生。
2CO+4H2←→CH3OCH3+H2O+QCO+3H2←→CH4+H2O+Q4CO+8H2←→C4H9OH+3H2O8CO+17H2←→C8H18+8H2O2.2技术规定甲醇合成流程简述来自合成气压缩的新鲜合成气,分两股进入气气换热器(C40001AB)预热到200℃左右,分别进入甲醇合成塔(D40001AB),在催化剂的作用下进行甲醇合成反应CO+2H2=CH3OH+QCO2+3H2=CH3OH+H2O+Q及副反应 4CO+8H2=C4H9OH+3H2O8CO+17H2=C8H18+8H2O 等甲醇合成塔为管壳式反应器,两台并联操作,并分别与气气换热器相联,管内填装触媒,反应管外为沸腾热水,利用反应热副产中压饱和蒸汽。
合成岗位操作规程.doc

合成岗位操作规程一、岗位任务1、岗位主要任务本岗位是将合成气压缩岗位来的工艺气体,在一定温度、压力、催化剂作用下,在甲醇合成塔内合成粗甲醇,将生产的粗甲醇送至精馏岗位;并利用其反应热副产中压蒸汽,经减压减温送至低压蒸汽管网;合成弛放气送往能源利用公司做原料气或送往转化岗位做燃料气或送往焦化分厂做回炉煤气。
2、管辖范围甲醇合成塔、洗醇塔、稀醇水槽、闪蒸槽、甲醇分离器、汽包、磷酸盐槽、排污膨胀器、气气换热器、水冷器、取样冷却器、蒸汽喷射器、一级过滤器、二级过滤器、稀醇水泵、磷酸盐泵等设备及其相关的仪表、电气、管线、DCS。
二、基本原理入塔合成气中的一氧化碳、二氧化碳分别与氢气在一定的压力、温度下,通过铜基催化剂的催化作用,在甲醇合成塔内生成甲醇并放出一定的热量。
放出热量的多少与反应温度、压力、入塔气体成份、合成转化率有关,一般随系统压力的升高而增大。
主要反应方程:CO+2H2←→CH3OH+QCO2+3H2←→CH3OH+H2O+Q甲醇合成反应是放热的,体积缩小的反应,所以降低温度,提高压力有利于正反应的进行。
在合成甲醇的过程中,由于触媒原因及二氧化碳和其它气体的存在,还有一些副反应发生,生成二甲醚、高级烷烃、醇、酸等杂质,如:2CH3OH←→CH3OCH3+H2O+QCO+3H2←→CH4+H2O+Q4CO+8H2←→C4H9OH+H2O8CO+17H2←→C8H18+8H2等甲醇合成催化剂经还原后才有活性,因此合成催化剂在使用前,需进行还原,还原方程式为:CuO+ H2 = Cu + H2O。
三、工艺流程简述来自合成气压缩岗位的压力5.5MPa,总硫含量小于0.1 ppm的合成气,温度约为60℃,经两个串联的气气换热器的壳程被来自合成塔反应后的出塔热气体加热到活性温度以上,进入甲醇合成塔顶部。
甲醇合成塔为立式绝热管壳型反应器。
管内装有低压甲醇合成催化剂,当合成气进入催化剂床层后,在5.5MPa、220~260℃下,CO、CO2与H2反应生成甲醇和水,同时还有微量的其它有机杂质生成。
合成作业安全操作规程(通用版)

( 操作规程 )单位:_________________________姓名:_________________________日期:_________________________精品文档 / Word文档 / 文字可改合成作业安全操作规程(通用版)Safety operating procedures refer to documents describing all aspects of work steps and operating procedures that comply with production safety laws and regulations.合成作业安全操作规程(通用版)一、岗位任务1、在高温、高压和有触媒的条件下,将合格的H2、N2混合气合成氨。
2、合成氨经分离、冷凝得液氨,贮存于氨罐。
3、液氨在氨冷器中气化送往吸收,制取NH4HCO3。
3H2+N22NH3+Q二、工艺流程图(另附)三、岗位工艺指标1、压力:合成塔进口:≤31.4MPa合成塔进出口压差:≤0.8MPa液氨贮罐:≤1.6MPa循环机压差:≤2。
8MPa•循环机油压:≥0。
15~0.25MPa气氨总管压力:≤0.2MPa系统升降压速率:每分钟0.4-0.6MPa2、温度:合成塔出口温度<300℃触媒层温度波动:≤±5℃热点温度:一二段:480±5℃:三段:480±5℃:四段:460±5℃水冷器出口:<35℃氨冷出口一5℃~一20℃合成塔热点升降温速率:每小时45℃气体成份微量CO+CO2≤25PPM,正常生产:30-50PPM,半量生产:﹥50PPM,停止送气。
氢氮比2.0~2.8,合成塔进口氨含量<3.0%。
冰机:(1)压力:进口气氨压力:0.18~0.3MPa出口气氨压力:≤1.6MPa油泵油压≥0.15~0.25MPa(2)温度:冰机出口温度<150℃循环油位:1/2~2/3四、岗位开停车步骤:l、正常开车:(1)接通知后,检查阀门(补充气、塔进出口、付线、循环机及各段冷、热激各阀门开关位置是否正确及排放阀位置)。
合成岗位安全操作规程(三篇)
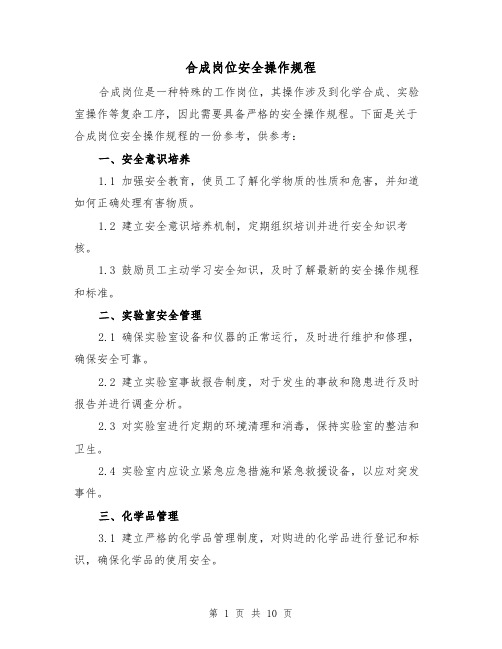
合成岗位安全操作规程合成岗位是一种特殊的工作岗位,其操作涉及到化学合成、实验室操作等复杂工序,因此需要具备严格的安全操作规程。
下面是关于合成岗位安全操作规程的一份参考,供参考:一、安全意识培养1.1 加强安全教育,使员工了解化学物质的性质和危害,并知道如何正确处理有害物质。
1.2 建立安全意识培养机制,定期组织培训并进行安全知识考核。
1.3 鼓励员工主动学习安全知识,及时了解最新的安全操作规程和标准。
二、实验室安全管理2.1 确保实验室设备和仪器的正常运行,及时进行维护和修理,确保安全可靠。
2.2 建立实验室事故报告制度,对于发生的事故和隐患进行及时报告并进行调查分析。
2.3 对实验室进行定期的环境清理和消毒,保持实验室的整洁和卫生。
2.4 实验室内应设立紧急应急措施和紧急救援设备,以应对突发事件。
三、化学品管理3.1 建立严格的化学品管理制度,对购进的化学品进行登记和标识,确保化学品的使用安全。
3.2 根据化学品的性质和危险等级,制定相应的存放和处置规范,确保化学品的密闭、稳定和分区存放。
3.3 对化学品进行分类,明确危险品和非危险品的处理方式,并建立相应的记录和报告制度。
3.4 对于过期、变质或不合格的化学品,应及时予以淘汰和处理,并进行相应的记录和报告。
四、实验操作规程4.1 在进行实验前,应仔细阅读实验操作手册,并熟悉实验的流程和步骤。
4.2 严格遵守实验室操作规范,如佩戴个人防护装备、正确使用实验器材等。
4.3 在进行合成实验时,一定要掌握好操作温度、压强以及化学品的用量等参数,并合理安排实验步骤。
4.4 在进行有毒、易爆、易燃等特殊实验时,应加强风险评估,并采取相应的安全措施,如设置消防器材、安全防护罩等。
4.5 实验过程中应避免使用齐齐哈尔,如开火、吸烟等行为,确保实验室的安全。
五、事故处理与应急预案5.1 定期组织员工参加事故处理和应急预案培训,提高应急处理能力。
5.2 建立事故报告制度,对于发生的事故要及时报告,并进行事故调查和分析,总结教训,并采取相应的纠正和改进措施。
甲醇合成操作规程

合成部分第一节岗位的任务和管辖范围合成岗位的主要任务而言之有两个:一、是合成粗甲醇。
二、是回收反应热副产蒸汽。
净化工序送来的新鲜气,经联合压缩机压缩段压缩后和合成回路来的循环气混合,经循环段压缩后导入合成系统,在适当的压力、温度条件下,通过甲醇催化剂的作用使一定量的一氧化碳、二氧化碳和氢合成粗甲醇,分离后的气再循环使用,反应器管间的锅炉给水被反应热加热产生蒸汽送入汽包,通过压力(用于控制合成塔炉温)调节后送入蒸汽管网。
合成岗位的管辖范围包括:甲醇合成塔、塔前预热器、甲醇分离器,冷却器、合成汽包、洗醇塔、汽包上水泵、洗醇泵、软水槽,及以上设备所附属的设备管道、阀门、仪表、液位计等。
主要设备一览表第三节生产原理及工艺流程一、生产原理主反应:CO+2H2=CH3OH+QCO2+3H2=CH3OH+H2O+Q副反应:2CO+4H2=CH3OCH3+H2O+QCO+3H2=CH4+H2O+Q4CO+8H2=C4H9OH+3H2O+QCO2+H2=CO+H2O-QnCO+2nH2=(CH2)n+NH2O+Q甲醇主反应是可逆放热反应,反应时体积缩小,并且只有在催化剂存在的条件下,才能较快进行,所以反应在较高压力和适当的反应温度下进行,一氧化碳、二氧化碳才能获得较高转化率。
二、工艺流程说明来自净化温度为40度,压力为3—3.3MPa的新鲜气进入合成塔联合压缩机压缩段升压至 6.48MPa,经冷却分离水后与合成回来的循环气混合,进入循环段压缩至6.8MPa(温度48度)后送入合成系统.出循环段的合成气先经中间换热器管间.被管内反应气加热至220~225度由合成塔顶部斜向45度进入合成塔反应管顶端,沿轴向进入反应管.反应管内装有铜基催化剂,在催化剂的作用下合成甲醇.并伴有微量的副反应.反应后反应器底部出来的含甲醇7.0%温度为225度气体,进入中间换热器管内,与管间的气体换热后被降至97度;在此,有少量的甲醇气体冷凝;然后进入甲醇分离器分离甲醇,从分离器顶部出来的气体从洗醇塔中部进入,和从洗醇塔上部来的稀醇水在填料层逆流接触,气体中少量的甲醇被吸收.吸收少量甲醇的稀醇水减压后进入稀醇水槽,由洗醇水泵打入洗醇塔内,循环吸收.当甲醇浓度达到8~10%后,由洗醇塔后调节阀直接排入精馏工段.从洗醇塔顶部出来的气体,绝大部分是未反应的合成气及惰性气体.为防止惰性气体在系统中的累积,必须将一部分气体排出.排出后的循环气,进入联合压缩机的循环段,继续进行循环.驰放气送到总厂压缩三段出口回收利用.从甲醇分离器底部排出的甲醇,送入闪蒸槽.在此减压至0.3~0.4MPa并闪蒸出大部分溶解气体.闪蒸气送入总厂.闪蒸槽出来的粗甲醇送往粗甲醇计量槽或精馏生产.甲醇合成塔管间环隙通过汽包给水泵不断的打入锅炉给水.反应器与汽包通过上升管及下降管相连接,形成一个独立的蒸汽发生系统.汽包蒸汽出口管线压力控制阀,通过保持蒸汽压力来控制催化剂床层温度的恒定.合成塔还装有一个开车用的蒸汽加热系统,由一个蒸汽喷射器及循环水管组成.开工用饱和蒸汽通过针形阀冷凝.产生动力以推动反应器管间的锅炉水不断地循环,加热管内催化剂以达到活性温度.第四节工艺指标一、压力及压差(MPa)1.补气压力3~3.32.合成系统入口压力6.83.系统压差小于0.34.合成塔压差小于0.15.升降压速率小于0.4MPa6.放醇压力小于0.5MPa7.闪蒸槽压力小于0.4MPa8.汽包给水压力~5.69.汽包蒸汽压力2.4~4.010.开工蒸汽压力1.3(低压),4.0~4.5(中压)11.洗醇泵出口压力6.612.洗醇泵油压0.25~0.3二、温度1.合成塔热点温度初期230正负5度,中期235~260度,末期265正负5度.2.水冷器温度小于40度3.水冷前温度~90度,汽包给水温度~120度4.汽包蒸汽出口温度220~260度5.合成塔催化剂升降温速率:210度前小于40℃/H6.合成塔出口温度200~220度7.进中间换热器前温度~48度三、液位1.醇分液位1/3~1/22.汽包液位40%~70%3.闪蒸槽液位1/2~2/34.洗醇塔液位1/3~1/25.稀醇槽液位1/2~2/3四、成分1.补气:(H2-CO2)/(CO+CO2)=2.12.入塔气: (H2-CO2)/(CO+CO2)=4.323.循环气中惰性气含量:开车初期10~15%末期15~20%4.新鲜气CO=25%正负3 CO2=5正负2%5.合成塔入口气CO=9正负2%,CO2=7正负2%6.合成汽包脱盐水电导率小于150第五节正常开、停车步骤一、原始开车1.开车前的准备1)消防器材、防护用品、仪器、工具、备品备件以及开车人员配备落实。
飞源化工合成反应的操作规程

飞源化工合成反应的操作规程为了加强企业的安全生产,确保合成岗位安全生产有序正常操作运转,特制订合成岗位安全生产操作规程,希望合成岗位各位员工认真执行。
一、投料前的准备1、检查反应釜、配料釜、高位槽、包装桶是否干净、完好;更换合成产品生产前,反应釜、配料釜、高位槽、包装桶进行清洗。
2、检查反应釜、配料釜、高位槽各阀门是否处于应处于的状态。
3、检查反应釜、配料釜中是否按工艺要求放好纯水。
4、上岗前要穿好工作服、戴好安全帽、戴好橡胶耐腐手套,戴好橡胶饭单、橡胶袖套、戴好活性炭防毒口罩及眼罩,工作完毕要更衣,保持良好的工作习惯。
5、合成装置现场不允许长期堆放原料,当天生产用的原料,当天从仓库内领取。
二、严格按工艺要求进行操作1、严格按工艺要求按投料比投料,按温度和流量的要求操作。
2、在生产中,突然遇到停电时,操作工应立即停止进料或配料,反应釜夹套内桶冷却水。
3、在配料中要进行记录并检查余料,发现投错料时及时向上汇报,由生产部主任工程师拿出处理办法后,再进行配料。
4、在反应过程中发生超温,及时反应釜夹套内通冷却水。
5、在反应过程中发生氧化剂先加完,应关闭单体和还原剂进料,及时向上汇报,由生产部主任工程师拿出处理办法后,再进行投料。
6、在反应过程中发生单体先加完,应关闭氧化剂和还原剂进料,及时向上汇报,由生产部主任工程师拿出处理办法后,再进行投料。
7、在反应过程中发生还原剂先加完,应关闭单体和氧化剂进料,及时向上汇报,由生产部主任工程师拿出处理办法后,再进行投料。
8、流程示意图和生产流程简述见附件“合成生产流程示意图和生产流程简述”。
三、设备操作的安全要求和注意事项1、准备必要的开车工具,如扳手、管钳等;2、生产前检查各有关阀门的开闭状态,如关闭底阀,开启冷却水阀门等。
3、检查加注各部润滑油脂。
4、确认传动部分完好后,点动电机,检查搅拌轴是否按顺时针方向旋转,严禁反转。
5、听减速机和电机声音是否正常,摸减速机、电机、机座轴承等各部位的开车温度情况:一般温度≤40°C、最高温度≤60°C(手背在上可停留8秒以上为正常)。
- 1、下载文档前请自行甄别文档内容的完整性,平台不提供额外的编辑、内容补充、找答案等附加服务。
- 2、"仅部分预览"的文档,不可在线预览部分如存在完整性等问题,可反馈申请退款(可完整预览的文档不适用该条件!)。
- 3、如文档侵犯您的权益,请联系客服反馈,我们会尽快为您处理(人工客服工作时间:9:00-18:30)。
Q/NMWH 内蒙古乌拉山化肥有限责任公司企业标准Q/NMWH·JS04 04-2010合成岗位操作规程2010-04-25发布2010-04-25实施本标准由湖北宜化集团有限责任公司标准化委员会提出。
本标准2010年4月25日首次发布。
本标准起草单位:合成氨事业部本标准主要起草人:郝建成本标准修订单位:事业部、生产部、电控部、安监部、设备动力部本标准修订人员:魏建参与本标准审核单位:生产部、设备动力部、安环部、电控部、集团技术开发部、安全生产管理部参与本标准审核人:张胜元、郑永和、本标准审批人:目录第一章、新合成岗位操作规程 (5)1、主题内容与适用范围2、基本原理与工艺流程3、岗位管辖范围及外部联系4 、本岗位工艺指标5 、三轴一径氨合成塔的操作要点6 、正常操作注意事项7、系统开车8、系统停车9、主要设备一览表10、不正常现象的处理第二章、旧合成岗位操作规程 (15)1、岗位任务2、反应方程式与工艺流程3、岗位管辖范围及外部联系4、本岗位工艺指标5、二轴二径氨塔操作要点6、正常操作注意事项7、系统开车8、系统停车9、不正常现象的处理10、旧合成设备一览表第三章、醇烃化岗位操作规程 (27)1 主要任务与管辖范围2 工作原理与工艺流程3醇烃化系统工艺指标4醇烃化系统设备一览表5醇化系统正常生产中的操作要点6 醇-烃化系统的开停车7 不正常现象判断及处理第四章、循环机岗位操作规程 (36)1、醇烃化循环机岗位操作规程2、合成循环机岗位操作规程第五章、合成工段紧急预案 (50)1、合成紧急停车核心内容2、合成塔电炉丝烧坏的主要原因及防范措施3、合成塔顶着火与爆炸的原因及处理方法4、合成工段应急预案(应急准备和响应)5、系统危害因素见表第六章、合成工段生产异情演练培训 (60)1、新合成后锅出口法兰着火演练第七章、中空纤维膜分离装置一一氢回收装置操作说明及操作规程 (62)第一章新合成系统操作规程1 、主题内容与适用范围本规程规定了合成氨反应的基本原理,合成塔系统的工艺流程,工艺条件,正常操作,事故处理及主要设备简介等内容。
2 、基本原理与工艺流程2.1 氨合成反应的基本原理2.1.1 反应的平衡:氨合成反应的化学方程式为3H2+N2≒ 2NH3+Q由反应式可以看出以下特点:a、氨合成反应是一个可逆反应b、这是一个放热反应c、由三个分子的氢和一个分子的氮(共四个分子)合成得到二个分子的氨。
因此氨合成反应是分子数减少的过程,也就是体积缩小的过程。
从反应式可以看出这个反应就是可逆反应,反应开始时,混合气体中氢和氮化合成氨的速度比氨分解成氢和氮的速度大,因而这时气体混合物中氨浓度逐渐增大,随着反应的进行,合成与分解的反应速度渐趋相等,如果不改变外界条件,则混合气中氨的含量不增不减,也就是说合成与分解反应的速度相等;这种状态称为平衡状态,但一切平衡都是相对的和暂时的,平衡状态只能在一定的条件下才能保持。
合成反应的化学平衡,和其它化学平衡一样,是随着反应条件(温度、压力、气体组成)的改变而改变的,反应条件改变以后,原来的平衡关系也改变了,并在新的反应条件下建立新的平衡;由于反应条件的改变破坏了反应平衡,使反应物或生成物的浓度发生改变的过程,称为平衡的转移过程,在实际生产过程中,就是根据平衡转移原理,选择适宜的反应条件,以促使氨的合成。
从平衡的观点出发,温度愈低,压力越高则反应越趋向合成氨的方向移动,达到平衡时混合气体中的氨含量达到最大值。
2.2.2 反应的速度氨合成的反应速度,是指单位时间内,氢和氮合成为氨的数量多少。
在工业生产中,不仅要求获得较高的氨含量,同时还要求有较快的反应速度,以便在单位时间内有较多的氢和氮合成为氨。
氨合成的反应与温度、压力、气体的组成和触媒有关。
a、温度:通常提高温度可以使反应速度加快。
温度升高,能使反应物气体分子的运动速度加快,分子与分子碰撞次数增加,分子运动的能量增大,从而增大了反应物分子有效相结合的机会。
b、压力:在较高压力下,可使一定体积内气体的密度增加,气体分子间的距离减小,从而增加了反应物分子间的碰撞机会而使反应加速。
c、气体的组成:在氨的浓度较低时,可以适当提高混合气中氮的浓度,一般氢氮比维持在2.7─2.8左右,当氨浓度接近于平衡时,氢、氮比接近于3:1。
d、触媒:从上述可知,低温对平衡有利而对于反应速度不利。
为了解决这个矛盾,就采用一种加速反应而本身又不起化学变化的物质─触媒。
事实证明:在氨合成反应中,如果不用触媒,即使温度提高到700─800℃,压力达到98MPa以上,反应速度仍然很慢。
当压力和温度更高时,则不需要触媒,反应就能以相当快的速度进行。
2 、工艺流程由压缩机六段来的新鲜气和冷交二出(热出)出来的气体汇合一起进入卧式氨冷器管内被壳程液氨冷却降温,进入氨分,分离下的液氨去中间槽,分离后的气体进入冷交,由下沿冷交中心管上行至冷交上部换热器管内,与管外冷交热进气换热提高温度后,由上管口导出,去循环机提压,经循环油分分离油水后,分为三路;一路为系统近路去热交二次出口,另一路约30%循环气由合成塔上部进入塔内件与外筒环隙下行,升高温度,并降塔壁温度,由塔底出来,温度~90℃。
塔底出来的气一部分为f3冷激气进入径向混合器调节径向段温度,另一部分塔底出来的气与第三路70%的循环气汇合,与热交管内的热气进行热交换,提高温度~178℃从热交下部导出并分为四路:一路做f1冷激气调节二轴床层温度;二路做f2冷激气调节三轴床层温度;三路做f0冷激气由塔底经中心管进入塔上部,调节一轴床层零米温度;四路为塔二入主进气由塔下部进入下换热器管间再次提温后和f0冷激气混合,经中心管进入塔上部一床层反应。
气体经三轴反应后到径向段反应,再被管间的塔二入主进气降温~350℃出塔,进入废锅回收热量并副产蒸汽,出废锅~220℃的气体进热交管内加热入塔气体,自身温度降到约90℃从热交顶部导出(与系统近路气汇合)去2台并联的水冷器降温到约35~40℃,再进入冷交上部换热器管间降温,到下部分离,分离下的液氨去中间槽;分离后的气体出冷交,少部分气体去H2回收装置,大部分进入氨冷形成循环。
3 岗位管辖范围及外部联系3.1合成管辖范围:包括合成塔、热交、冷交、废锅、两台水冷器、卧式氨冷器、氨中间槽以及以上设备所附属的设备、管道、阀门、仪表、液位计等。
3.2 本岗位与外部联系:a、本岗位与造气控制室联系氢氮比。
b、本岗位与中和、冰机、氨库联系气氨压力。
c、本岗位与循环机联系循环量。
d、本岗位与醇烃化系统联系气量和气体成分。
e、本岗位压缩机联系精炼气压力。
f、本岗位与氢回收联系氢回收量的大小。
g、本岗位与分析化验室联系各类分析。
h、本岗位与电气联系电炉的开停、使用情况以及其它电气设备的使用。
i、本岗位与调度室联系全部生产事宜。
5 、轴-径向氨合成塔的操作要点5.1 采用绝热、层间冷激操作上层触媒层(一轴)温度由塔副线f0调节第二层触媒层(二轴)温度由f1冷激气调节第三层触媒层(三轴)温度由f2冷激气调节第四层触媒层(径向层)温度由f3冷激气调节5.2 系统近路及循环机副线对全塔触媒温度能起到全面的控制作用,对触媒整体温度调节是比较均匀的。
所以在操作系统稳定的情况下,通过近路的调节起到事半功倍的效果。
5.3 在系统近路全部关死的情况下,如系统运行稳定,可单独用塔副线调节,它不但对第一层触媒起到直接控制作用,同时对第二、三、四层触媒温度起到间接调节作用。
6 、正常操作注意事项6.1 经常检查调节合成塔温度、压力、各液位。
6.2 经常检查系统各压差的变化情况。
6.3 经常注视入塔气体成份变化。
6.4 根据负荷及触媒层温度调节循环量。
6.5 触媒温度控制6.5.1 负荷一定时,温度变化慢,趋势幅度小,可用塔副线调节第一层温度。
如某一层出口温度高可用开冷激阀作单一调整。
6.5.2 负荷变动大,温度变化趋势大,采用循环量来调节,并以冷激阀作配合调节。
6.5.3 必要时请电工开电炉来控制温度。
6.5.4 严密注意各反应条件的变化对温度的影响,并作预见性的处理。
6.6塔压力的控制6.6.1 压力高可加大空速,必要时开驰放气及塔后放空。
6.6.2 压力上涨幅度快,可采取同时开大塔前、塔后放空,并视情况开补充气放空阀。
6.6.3 联系压缩工段减负荷。
6.6.4严密注意各操作条件的变化对压力的影响,并作相应的预见性的处理。
7、正常开车7.1开车前的准备7.1.1检查各设备、管道、阀门、分析取样点、电器、仪表等,必须正常完好。
7.1.2检查系统内所有阀门的开、关位置,应符合开车要求。
7.1.2与供水、供电部门及相关工段联系,作好开车准备。
7.2系统未经检修处于保压、保温状况下的开车7.2.1、系统停车时间很短,催化剂层温度都在活性范围内,启动循环机,缓慢补充新鲜气,将温度调节到正常范围。
7.2.2、系统充压可以根据情况从旧系统六段充精制气4.0~6.0Mpa。
如系统保压的压力仍有4.0~6.0Mpa(低于此压力则应缓慢充压至4.0~6.0Mpa)。
A、关闭各冷激阀;B、开环隙2~3扣,使环隙冷气正常流动,保证塔壁温度正常;C、开循环机使气体循环;D、开启电加热器;E、热点150℃时开水冷,300℃开氨冷;F、热点350℃时,催化剂已有活性,开始缓慢补气,逐步增加压力,当下部温度升至450℃,依情况开启各冷激阀,逐渐减少电加热器的电流,直至切断,恢复正常分流。
并联系调度调节好氢气,联系净化调整好指标。
7.3系统检修或热洗后的开车(可以根据情况从旧系统六段充精制气)7.3.1、先将系统吹净,吹净时要与合成塔隔绝。
7.3.2、系统置换。
按升压速率,导精制气至0.5Mpa、1.0 Mpa、1.5Mpa三次置≤0.2%,置换合格。
换,O27.3.3、气密试验。
用精制气按5.0Mpa、10.0Mpa、20.0Mpa、30.0Mpa查漏四次。
发现漏点,作好记号,卸压后处理,严禁带压紧螺栓。
7.3.4、按照1.2.2步骤开车。
8、系统停车8.1 停车前的准备8.1.1 准备好仪表、工具、联系调度室。
8.1.2 氨蒸发器停止加液氨,关加氨自调阀。
8.1.3 视情况各自调阀改为手动操作。
8.1.4 通知压缩工序按规定停车。
停供新鲜气。
8.2 降温停车8.2.1 联系电工开用电炉(操作熟练可不启动电炉)。
8.2.2 按40~45℃/h的速率进行降温,并视情况调节循环量和电炉功率,视情况降压。
8.2.3 系统压力为5.0~10.0MPa、触媒层温度≤300℃时进行压氨,将各设备内余氨压净,并防止低压管道压力憋高。
8.2.4 触媒层温度降到200℃以下时,停止废热锅炉的“水~汽”系统。
8.2.5 触媒层温度降到100℃以下时,停电炉。