热镀锌工艺学习资料
热镀锌工艺

什么是热镀锌?热镀锌又称为热浸镀锌,他是在高温下把锌锭融化,在放入一些辅助材料,然后把金属结构件浸入镀锌槽中,使金属构件上附着一层锌层。
热镀锌的优点在于他的防腐能力强,镀锌层的附着力和硬度较好。
缺点在于价格较高,需要大量的设备和场地,钢结构件过大不易放入镀锌槽中,钢结构件过于单薄,热镀又容易变形。
富锌涂料一般指的是含有锌粉的防腐涂料。
市场上的富锌涂料含锌量一。
备料—酸洗—水洗—助溶—热浸锌—冷却—钝化—清洗—分检—复检—包装—入库一、热镀锌工艺过程及有关说明工艺过程工件→脱脂→水洗→酸洗→水洗→浸助镀溶剂→烘干预热→热镀锌→整理→冷却→钝化→漂洗→干燥→检验有关工艺过程说明(1)脱脂可采用化学去油或水基金属脱脂清洗剂去油,达到工件完全被水浸润为止。
(2)酸洗可采用H2SO4 15%,硫脲0.1%,40~60℃或用HCl 20%,六次甲基四胺1~3g/L,20~40℃进行酸洗。
加入缓蚀剂可防止基体过腐蚀及减少铁基体吸氢量。
脱脂及酸洗处理不好会造成镀层附着力不好,镀不上锌或锌层脱落。
(3)浸助镀剂也称结合剂,可保持在浸镀前工件具有一定活性,以增强镀层与基体结合。
NH4Cl 15%~25%,ZnCl2 2.5%~3.5%,55~65℃,5~10min。
为减少NH4Cl挥发可适当加入甘油。
(4)烘干预热为了防止工件在浸镀时由于温度急剧升高而变形,并除去残余水分,防止产生爆锌,造成锌液爆溅,预热一般为120~180℃。
(5)热镀锌要控制好锌液温度、浸镀时间及工件从锌液中移出的速度。
温度过低,锌液流动性差,镀层厚且不均匀,易产生流挂,外观质量差;温度高,锌液流动性好,锌液易脱离工件,减少流挂及皱皮现象发生,附着力强,镀层薄,外观好,生产效率高;但温度过高,工件及锌锅铁损严重,产生大量锌渣,影响浸锌层质量,锌耗大,甚至无法施镀。
在同一温度下,浸镀时间长,镀层厚。
不同温度,要求同样的厚度时,高温浸镀所需时间长。
热镀锌钢管施工工艺(二)

热镀锌钢管施工工艺(二)引言:热镀锌钢管是一种常用于建筑和工程领域的防腐蚀材料,其施工工艺对于确保镀锌层质量和延长使用寿命至关重要。
本文将详细介绍热镀锌钢管施工工艺的相关内容,包括表面处理、预热处理、镀锌工艺、冷却处理和质量检验等五个大点。
正文:1. 表面处理1.1 清洗:在进行镀锌前,必须彻底清洗热镀锌钢管表面的油、污物和氧化层。
1.2 喷砂:采用高压喷砂器将表面喷砂,去除钢管表面的氧化层,增加其粗糙度,提高镀锌层的附着力。
1.3 酸洗:在喷砂后,采用酸洗工艺去除热镀锌钢管表面的氧化、锈蚀物和污垢,确保锌层质量。
2. 预热处理2.1 加热:将热镀锌钢管放入预热炉中,通过加热将其表面温度升至适宜的镀锌温度,通常为450℃左右。
2.2 温度控制:控制预热炉的温度及作业时间,确保热镀锌钢管的表面温度符合要求,避免过高或过低温度对镀锌层质量的影响。
3. 镀锌工艺3.1 浸镀:将预热处理后的热镀锌钢管浸入镀锌槽中,使其完全被锌溶液浸泡,进而形成锌层。
3.2 均匀性控制:采取合适的搅拌工艺,确保镀液的成分均匀,避免锌层出现厚度不均匀的问题。
3.3 时间控制:根据钢管的规格和要求的镀锌层厚度,控制钢管在镀锌槽中停留的时间,以保证锌层厚度符合标准。
4. 冷却处理4.1 空气冷却:将浸镀完成的热镀锌钢管从镀锌槽中取出,置于通风良好的区域进行自然冷却。
4.2 水冷却:对于某些特殊要求的热镀锌钢管,可采用水冷却的方式加快镀锌层的固化和降低钢管温度。
5. 质量检验5.1 外观检查:对热镀锌钢管进行外观质量的检查,包括表面是否平整、无气泡、无凹陷等。
5.2 厚度测量:使用厚度测量仪对镀锌层的厚度进行测量,确保其符合相关标准。
5.3 附着力测试:通过拉力试验等方法,测试锌层与钢管的附着力,判断镀锌层的质量。
5.4 锌层质量检查:检查锌层的颜色、光泽等指标,以评估其质量是否符合要求。
总结:热镀锌钢管施工工艺是保证镀锌层质量和延长使用寿命的关键。
热镀锌资料

39、正常的粘附中间层形成之后,由于恶劣的操作条件又使它遭到破坏,并因此生成了超厚的 Fe 一 Zn 合金层;
40、在生产操作中因温度、锌液中铝含量和浸锌时间控制不当,使中间粘附层没有来得及形成,从而造成镀层的粘附力下降。
29、中间层的形成需要一定的温度和时间,若提高锌液中铝含量也可加速此层的形成。
30、如果浸锌温度、时间和锌液中含铝量三个条件不能满足时,则 FeZA15 中间相层就不易形成,或者形成得不完整。
31、提高带钢人锌锅温度、延长浸锌时间(即降低带钢运行速度)或增加锌液中铝含量,便会促使中间层的形成,当形成了完整的粘附媒介层时,则镀层的附着力才有可能获得改善。
41、生产实践已经证实,把镀层粘附力不合格的产品成卷放人罩式炉中,采用下列回火工艺条件,即可使镀层的粘附性得到改善: 回火温度: 280 ℃; 回火时间: 24h ; 揭罩温度: 200 ℃ 。
42、回火后,锌层和铁一锌合金层中含铝的夹杂物就不再存在了,原来锌层凝固时凝结在钢表面上的铝发生了迁移,并且在钢基表面形成了均质的中间层。
43、铝的粘附作用是由于铝与铁有较大的亲和力,在热镀锌时,首先会迅速地在反应界面上形成起粘附作用的中间层。
44、锌液中各元素能以不同的形式对热‘镀锌发生影响:
提高或降低锌液的熔点;
增加或减小锌液的表面张力和黏度;
扩大或缩小表面的结晶锌花;
17、在固定温度的情况下,延长浸锌时间,一定会引起 Fe 一 Zn 合金层的增厚。
18、在热镀锌时应尽量缩短镀件的浸锌时间,减少其合金层厚度,以利于增加镀层的韧性。
镀锌系列知识点总结

镀锌系列知识点总结一、镀锌的原理及特点1. 镀锌的原理镀锌的原理是利用锌对铁的亲和性,将锌涂覆在铁表面,形成一层锌层。
当这层锌遇到腐蚀物质时,会优先发生化学反应,保护下面的铁材料不受腐蚀。
这样可以有效延长铁材料的使用寿命。
2. 镀锌的特点镀锌的特点主要包括防腐蚀、美观、耐候性好等。
镀锌层具有良好的耐蚀性,不易受空气、水、酸、碱等腐蚀物质的侵蚀,从而延长了金属材料的使用寿命。
此外,镀锌的表面光滑均匀,具有一定的装饰效果,可以提高产品的美观度。
二、热镀锌的工艺及应用1. 热镀锌的工艺热镀锌是将金属材料浸入加热至适当温度的熔融锌中,使其表面形成锌层的工艺。
具体工艺步骤包括表面处理、熔融镀锌、冷却等。
熔融镀锌是一种对金属材料表面进行耐腐蚀处理的方法,适用于各种钢铁制品、汽车零部件、建筑材料等领域。
2. 热镀锌的应用热镀锌广泛应用于建筑工程、汽车制造、航空航天、冶金、农机制造等产业。
例如,建筑材料中常见的镀锌管、镀锌钢板等产品,都是通过热镀锌工艺制成的。
热镀锌的产品具有良好的防腐蚀性能,耐候性好,使用寿命长,因此备受青睐。
三、电镀锌的工艺及应用1. 电镀锌的工艺电镀锌是一种通过电化学方法,在金属表面镀上一层薄薄的锌层的工艺。
其主要步骤包括表面准备处理、活化、镀锌、清洗、烘干等。
电镀锌产品精密度高,表面光洁度好,适用于需要高精度、高表面质量的制品。
2. 电镀锌的应用电镀锌广泛应用于汽车零部件、电子产品、家电、建筑材料等领域。
例如,汽车零部件中的螺栓、螺母、零件等常采用电镀锌处理,以提高其表面的耐蚀性和美观度。
而在家电领域,电镀锌产品通常用于制作外壳、面板等部件,以防止其受到腐蚀,延长使用寿命。
四、镀锌产品的检测方法及标准1. 镀锌产品的检测方法镀锌产品的检测方法主要包括厚度测量、附着力测试、耐腐蚀性能测试等。
其中,厚度测量是常用的检测方法,通过测量镀锌产品表面的锌层厚度,来判断其防腐蚀性能。
而附着力测试可以检测锌层与金属基材的结合强度,从而评估镀锌产品的质量。
热镀锌复习资料

1.热镀锌:把带钢经过预处理后,浸入在锌液获得防护性镀层的一种工艺。
2.美钢联法突出特点:钢带加热之前采用电解脱脂和全辐射管加热工艺,因此钢带表面无需再经高温氧化、表面还原容易。
3.热镀锌分为:在线退火:氧化还原法。
线外退火:湿法和干法。
4.在线退火氢气还原法:1、森吉米尔法2、美钢联法3、改良森吉米尔法(无氧化加热法)5.镀层分类:大锌花D>3mm 小锌花 1<d<3mm 光整锌花d<1mm6.GI:纯锌热镀锌板 GA合金化镀锌板7.金属腐蚀:化学腐蚀:金属与周围介质直接发生化学反应引起的破坏,没有电流产生。
电化学腐蚀:在潮湿的坏境通过电极反应腐蚀,有电子得失并有电子产生。
通过原电池原理来进行。
8.锌作为阳极对钢铁基板起到牺牲阳极保护作用,防止钢板腐蚀反应。
9.合金化过程:钢带进入合金化炉,在45℃-75℃下短时间加热时,表面纯锌层与钢基体之间发生合金化反应(扩散反应)而形成由含铁量7%—15%的Fe-Zn化合物构成的合金化镀层10.镀层的附着能力主要不取决于Fe-Zn合金化层的薄厚,而大多数情况下是取决于刚基和Fe-Zn合金层之间由Fe2Al5形成的中间黏附层11.热镀锌层形成:A、镀层表面氧化膜。
B、纯锌层。
C、Fe-Zn合金层。
D、Fe2Al5中间层。
E、刚基。
F、温度变化曲线。
1-6镀锌层形成的步骤12.带钢热镀锌时,如果浸锌温度、时间和锌液中含铝量三个主要条件都不具备,则Fe2Al5中间相层就不易形成,或不完整13.合金层的吸铝量不仅取决于锌液中的铝含量,在更大程度上取决于浸入锌液中的带钢温度14.镀锌层附着力差的主要原因:①没有形成起黏附媒介作用的Fe2Al5中间层,这种产品镀层Fe-Zn合金层较薄可通过280℃回火加以改善②形成的Fe2Al5中间层又遭到破坏15.镀层中的铝含量是黏附强度的一个重要标准16.锌液450℃-460℃,温度↑铁损↑锌渣↑17.钢基中各种元素对热镀锌的影响:①含碳量↑铁损↑②硅:使镀层附着力↓③铜④锰、磷、硫⑤铝含量高于0.14%,则FeZn7会与锌液中外外加的铝反应形成Fe2Al5浮于锌液表面形成面渣,从而导致外加铝的损失。
镀锌管知识点总结

镀锌管知识点总结镀锌管是一种防腐蚀的钢管,通常用于输送水、气体和其他流体。
它的表面经过镀锌处理,可以在一定程度上防止钢管的腐蚀和氧化。
镀锌管的制作工艺、应用范围、优缺点等方面有很多知识点需要了解,下面将对镀锌管的知识点进行总结和介绍。
一、镀锌管的制作工艺1.热镀锌工艺:热镀锌是镀锌管制作的常见工艺,它通过将钢管浸入熔融的锌液中,使得表面形成一层锌铁合金。
这种工艺可以在钢管表面形成均匀、致密的镀层,具有较好的耐腐蚀性。
2.电镀锌工艺:电镀锌是将钢管放入含锌离子的电解液中,通过电流的作用使得锌离子在钢管表面沉积成锌层。
电镀锌工艺所制作的镀锌管,镀层较薄,但具有光亮、美观的特点。
二、镀锌管的种类1.热镀锌管:热镀锌管是指采用热镀锌工艺制作的镀锌管,它的镀锌层均匀致密,耐腐蚀性能良好,适用于输送水、气体等一般流体。
2.电镀锌管:电镀锌管是采用电镀锌工艺制作的镀锌管,其镀层相对较薄,适用于一些要求表面光洁度和美观度的场合。
此外,还有一些特殊材质的镀锌管,如钛锌管等。
三、镀锌管的优缺点1.优点:(1)较强的耐腐蚀性:镀锌管的镀层可以防止钢管表面的腐蚀和氧化,延长了钢管的使用寿命。
(2)美观性好:电镀锌管具有亮丽的表面,外观美观,适用于一些对外观要求较高的场合。
(3)维护成本低:由于镀锌管具有较强的耐腐蚀性,使用过程中的维护成本相对较低。
2.缺点:(1)镀锌管在高温和酸碱环境下容易发生腐蚀:当镀锌管在高温或酸碱环境下使用时,镀层容易受损,从而影响了耐腐蚀性能。
(2)电镀锌管的镀层较薄,抗腐蚀性能不如热镀锌管。
四、镀锌管的应用范围镀锌管由于具有较强的耐腐蚀性和美观性,被广泛应用于各种领域,如建筑、市政工程、电力、化工、航空航天等。
其中,常见的应用包括:1.给水工程:镀锌管常用于给水管道系统中,其耐腐蚀性能能够有效延长管道的寿命,保证给水系统的安全和可靠性。
2.燃气工程:镀锌管也常用于燃气管道系统,其耐腐蚀性能能够确保燃气管道不受腐蚀和氧化的影响,保证燃气系统的安全运行。
热镀锌专业技能培训(一)ppt课件

超声波测厚法
03
利用超声波在金属中的传播速度与镀锌层厚度的关系进行测量。
附着力测试方法
划痕法
用划痕试验机在热镀锌件表面划出一定长度的划痕,观察锌层是 否剥落或翘起。
弯曲法
将热镀锌件弯曲至一定角度,检查锌层是否出现裂纹或剥落现象。
冲击法
用冲击试验机对热镀锌件进行冲击,观察锌层是否脱落或碎裂。
环保性能评估指标
合金层生长
合金层不断向钢材内部和 锌液方向生长,达到一定 厚度。
镀层结构
合金层与纯锌层、钢材基 体紧密结合,形成致密的 防护层。
影响因素分析
温度和时间
钢材成分和组织
锌液成分和纯度
操作工艺和设备
影响锌铁扩散速度和合 金层厚度。
影响合金层的形成和性 能。
影响镀层质量和耐腐蚀 性。
影响生产效率和产品质 量。
的听力损害和环境污染。
05 安全防护措施与 应急处理
个人防护装备选择和使用
头部防护
安全帽,防止高空坠 物伤害。
呼吸防护
防尘口罩或防毒面具, 避免吸入有害粉尘和 气体。
身体防护
穿戴防护服,耐酸碱、 耐高温,防止化学飞 溅和高温烫伤。
手部防护
耐酸碱手套,防止化 学腐蚀和高温伤害。
脚部防护
穿防砸、防滑鞋,防 止重物砸伤和滑倒。
建立应急组织
成立应急小组,明确各成员职责和联系方式。
定期演练和培训
定期组织应急演练和培训,提高员工应急处 置能力。
06 总结回顾与展望 未来发展趋势
本次培训重点内容回顾
01
02
03
04
热镀锌工艺原理及流程 介绍
热镀锌设备结构、功能 及使用注意事项
热镀锌工艺描述讲述讲解
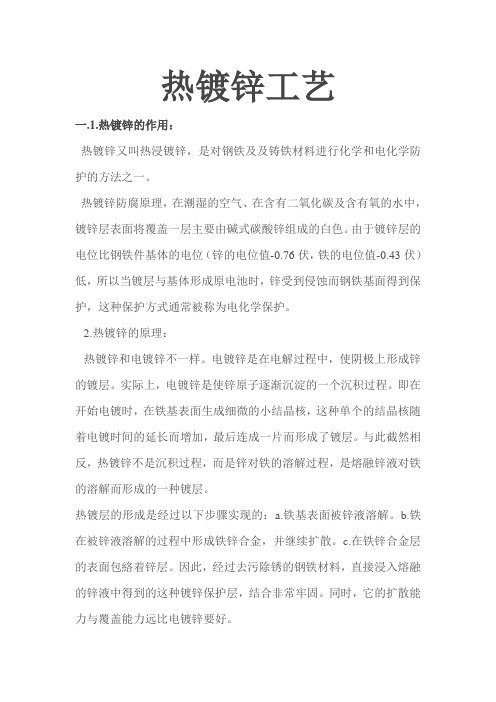
热镀锌工艺一.1.热镀锌的作用:热镀锌又叫热浸镀锌,是对钢铁及及铸铁材料进行化学和电化学防护的方法之一。
热镀锌防腐原理,在潮湿的空气、在含有二氧化碳及含有氧的水中,镀锌层表面将覆盖一层主要由碱式碳酸锌组成的白色。
由于镀锌层的电位比钢铁件基体的电位(锌的电位值-0.76伏,铁的电位值-0.43伏)低,所以当镀层与基体形成原电池时,锌受到侵蚀而钢铁基面得到保护,这种保护方式通常被称为电化学保护。
2.热镀锌的原理:热镀锌和电镀锌不一样。
电镀锌是在电解过程中,使阴极上形成锌的镀层。
实际上,电镀锌是使锌原子逐渐沉淀的一个沉积过程。
即在开始电镀时,在铁基表面生成细微的小结晶核,这种单个的结晶核随着电镀时间的延长而增加,最后连成一片而形成了镀层。
与此截然相反,热镀锌不是沉积过程,而是锌对铁的溶解过程,是熔融锌液对铁的溶解而形成的一种镀层。
热镀层的形成是经过以下步骤实现的:a.铁基表面被锌液溶解。
b.铁在被锌液溶解的过程中形成铁锌合金,并继续扩散。
c.在铁锌合金层的表面包絡着锌层。
因此,经过去污除锈的钢铁材料,直接浸入熔融的锌液中得到的这种镀锌保护层,结合非常牢固。
同时,它的扩散能力与覆盖能力远比电镀锌要好。
所谓扩散能力和覆盖能力,就是镀层在被镀材料表面上的均匀和完整性。
扩散能力又叫均镀能力,它是指镀层厚度的均匀分布能力;覆盖能力又叫深度能力或着落能力。
3.热镀锌的基本工艺过程:工件分类---酸洗---水洗----浸溶剂---烘干---浸镀----冷却----钝化------整修---打包二.镀前处理:1.工件分类:在工件进场后,首先要把有油漆、油污的工件挑选出来做脱脂处理(脱脂分机械法、火焰法、化学法)。
然后仔细观察工件有窝气或兜锌,如发现有要选择合理的穿挂方法以避免窝气、兜锌现象。
实在不行应联系厂家做合理的开孔处理。
二.酸洗:钢铁是容易氧化和腐蚀的金属,其表面一般都存在氧化皮和铁锈。
钢铁表面常见的氧化物有氧化亚铁(FeO,灰色)、三氧化二铁(Fe2O3,赤色)、含水三氧化二铁(Fe2O3.ȵH2O,橙红色)和四氧化三铁(Fe3O4,蓝黑色)等。
热镀锌生产加工基础知识

热镀锌(型钢)生产加工基础知识1、什么是热镀锌?目前我公司生产工艺过程有哪些处理工序?热镀锌又称为热浸镀锌,是在高温下把锌锭融化,在放入一些辅助材料,然后把型钢浸入镀锌槽中,使型钢附着一层锌层。
热镀锌的优点在于防腐能力强,镀锌层的附着力和硬度较好。
公司目前热浸(吹)镀生产工艺过程:黑材打栏→酸洗→水洗→助镀剂→烘干→热浸镀锌→风刀→冷却→钝化→检验包装2、热镀锌层形成过程热镀锌层形成过程是铁基体与最外面的纯锌层之间形成铁-锌合金的过程,镀件表面在热浸镀时形成铁-锌合金层,才使得铁与纯锌层之间很好结合,其过程可简单地叙述为:当铁工件浸入熔融的锌液时,首先在界面上形成锌与α铁(体心)固熔体。
这是基体金属铁在固体状态下溶有锌原子所形成一种晶体,两种金属原子之间是融合,原子之间引力比较小。
因此,当锌在固熔体中达到饱和后,锌铁两种元素原子相互扩散,扩散到(或叫渗入)铁基体中的锌原子在基体晶格中迁移,逐渐与铁形成合金,而扩散到熔融的锌液中的铁就与锌形成金属间化合物FeZn13,沉入热镀锌锅底,即为锌渣。
2、主要中控指标结合生产实际及两厂区近年来数据分析,需要对如下指标严格控制:①助镀液铵锌比:1.2---1.6②助镀液PH值:5---6 (以5左右为主)③助镀液Fe2+含量:目标1.5g/l以下④钝化液铬点:4--8(按实际情况夏季6以上)3、热镀锌过程中锌灰、锌渣的形成锌灰锌渣不仅严重影响到浸锌层质量,造成镀层粗糙,产生锌瘤,而且使热镀锌成本大大升高。
控制锌灰主要是控制好温度,减少锌液表面氧化而产生的浮渣;对于锌液中锌渣的形成主要是溶解在锌液中的铁含量超过该温度下的溶解度时所形成的流动性极差的锌铁合金,锌渣中锌含量可高达95%,这是热镀锌成本高的关键所在。
从铁在锌液中的溶解度曲线可以看出:不同的温度及不同的保温时间,其溶铁量即铁损量是不一样的。
在500℃附近时,铁损量随着加温及保温时间急剧增加,几乎成直线关系。
热镀锌工艺入门

鐵離子滴定 從酸槽取樣並過濾 25ml 注入圓錐燒杯,加 30 滴濃度 10%硫酸滴足 0.1N 過錳酸鉀 KMnO4,直
對油漆殘存物去除效率遠不如加熱脫脂,因此並不被廣泛地使用。
1.2 酸脫脂
不論是磷酸或鹽酸基,都有許多酸中脫脂劑可以選擇,這些方式都不比加熱脫脂效果大。他們 有他們的用處。在某些案例,在酸脫脂後可以不需要水洗,即可進入下一個製程酸洗。不須單獨設 置脫脂槽,節省加熱能源。
1.3 噴砂
噴砂在熱浸鍍鋅工業中應用於以下三點: 1. 從工件上去除大片的油漆。 2. 增加鋅的附著量;浸鍍前使表面粗糙可使鍍層增加 50%的厚度。 3. 從高張力鋼移除鐵銹,避免因酸洗製成產生氫脆化。
抑制劑的兩項作用: 1. 防止侵蝕乾淨的金屬表面, 減少酸液中鐵的含量。 2. 為延長酸洗槽的壽命。
在酸液中加入少量的抑制劑,抑制作用將有效防止潔淨鋼件受侵蝕,且不會影響鐵锈的去除效 率。因此當大部份難去除的鐵锈移除之前,已除锈的部份也能免除酸液進一步的侵蝕。
由於在酸洗槽中加入抑制劑,而得到的光滑鋼件表面,同時也會有較好的鍍鋅表面;且鋅附著 量較少,此外也減低鐵在酸液的累積,使酸洗液能使用更久。雖然我們只提供鹽酸用的 AD11 抑制 劑,但硫酸抑制劑亦可在市場上取得。
永尚股份有限公司 / 石磊 編纂
-7-
第一章 脫脂和酸洗 ----------------------------------------------------------------------------------------------- 3 第二章 抑制劑 ----------------------------------------------------------------------------------------------------- 7 第三章 酸洗水洗 -------------------------------------------------------------------------------------------------- 8 第四章 助鍍液 ----------------------------------------------------------------------------------------------------- 9 第五章 助鍍液之處理 ------------------------------------------------------------------------------------------- 12 第六章 烘乾 ------------------------------------------------------------------------------------------------------- 17 第七章 鍍鋅爐 ---------------------------------------------------------------------------------------------------- 18 第八章 鋅槽 ------------------------------------------------------------------------------------------------------- 24 第九章 冷卻及鍍層表面處理 ---------------------------------------------------------------------------------- 26 第十章 鍍面修整 ------------------------------------------------------------------------------------------------- 27 第十一章 熱浸鍍鋅流程偵測 ---------------------------------------------------------------------------------- 28 第十二章 基本實驗室檢測方法 ------------------------------------------------------------------------------- 29 第十三章 鋅浴添加 鋁(Al)、鉛(Pb)、錫(Sn)、銻(Sb) 對熱浸鍍鋅鍍層之影響 -------------------- 32 第十四章 鋅鎳(Zn-Ni) 鍍鋅用合金 -------------------------------------------------------------------------- 36 第十五章 蒸發法鹽酸回收再生系統 ------------------------------------------------------------------------- 38 第十六章 冷凍法硫酸回收再生系統 -------------------------------------------------------------------------40
热镀锌工艺入门课程

热镀锌工艺入门课程热镀锌是一种常用的防腐蚀方法,具有广泛的应用领域,包括建筑、电力、交通等行业。
本文将介绍热镀锌工艺的入门课程,帮助读者了解其基本原理、工艺流程和操作要点。
一、基本原理热镀锌是指将铁制品(一般为钢材)在加热至一定温度后蘸入熔化的锌中,通过物理和化学反应在钢材表面形成一层锌铁合金镀层的工艺。
通过锌的阴极保护作用,为钢材提供了优异的防腐蚀性能。
二、工艺流程1. 原料准备:选择优质的钢材作为基材,并对其表面进行清洗、除油和除锈等预处理工作,确保镀层的附着力。
2. 酸洗:将钢材浸入酸性溶液中,去除表面的氧化物、锈蚀物和杂质,以提高镀层附着力。
3. 热镀锌:将经过酸洗的钢材通过起吊装置悬挂在镀锌槽中,控制锌槽内的液体温度保持在适当范围,使锌快速融化形成熔融锌液。
将钢材蘸入熔融锌液中,保持一定时间,使钢材表面和锌液中的铁发生反应,形成锌铁合金镀层。
4. 冷却:将锌化后的钢材从锌槽中提取出来,经过自然冷却或水冷却,使得镀层变硬并固定在钢材表面。
5. 检验:对热镀锌后的钢材进行外观检查和物理性能测试,确保镀层质量符合要求。
三、操作要点1. 控制镀液温度:热镀锌中的锌槽内的液体温度对于镀层质量至关重要,需要根据具体情况控制在合适范围。
2. 控制蘸锌时间:蘸锌时间的长短会影响镀层的厚度以及镀层结构,需要根据要求进行控制。
3. 避免过度晃动:在蘸锌过程中,要保持钢材稳定,避免过度晃动或与其他钢材相互碰撞,以保证镀层的均匀性和平整度。
4. 保护钢材的锌镀层:热镀锌后的钢材需要合理包装,避免与空气、水分或其他腐蚀性物质接触,以延长锌镀层的使用寿命。
通过本文的介绍,读者可以初步了解热镀锌工艺的基本原理、工艺流程和操作要点。
当然,热镀锌是一个较为复杂的工艺,对于实际操作还需要进一步的专业培训和实践经验。
四、镀层性能和应用热镀锌工艺可以提供均匀、致密、耐腐蚀的锌铁合金镀层,具有良好的防腐蚀性能和装饰性能。
镀锌钢材在户外环境下具有较长的使用寿命,能够有效延缓钢材的腐蚀速度,减少修补和更换的频率,降低使用成本。
镀锌工艺培训
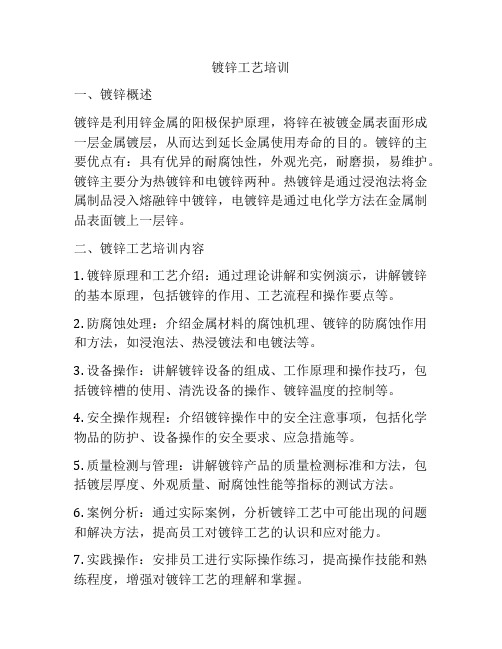
镀锌工艺培训一、镀锌概述镀锌是利用锌金属的阳极保护原理,将锌在被镀金属表面形成一层金属镀层,从而达到延长金属使用寿命的目的。
镀锌的主要优点有:具有优异的耐腐蚀性,外观光亮,耐磨损,易维护。
镀锌主要分为热镀锌和电镀锌两种。
热镀锌是通过浸泡法将金属制品浸入熔融锌中镀锌,电镀锌是通过电化学方法在金属制品表面镀上一层锌。
二、镀锌工艺培训内容1. 镀锌原理和工艺介绍:通过理论讲解和实例演示,讲解镀锌的基本原理,包括镀锌的作用、工艺流程和操作要点等。
2. 防腐蚀处理:介绍金属材料的腐蚀机理、镀锌的防腐蚀作用和方法,如浸泡法、热浸镀法和电镀法等。
3. 设备操作:讲解镀锌设备的组成、工作原理和操作技巧,包括镀锌槽的使用、清洗设备的操作、镀锌温度的控制等。
4. 安全操作规程:介绍镀锌操作中的安全注意事项,包括化学物品的防护、设备操作的安全要求、应急措施等。
5. 质量检测与管理:讲解镀锌产品的质量检测标准和方法,包括镀层厚度、外观质量、耐腐蚀性能等指标的测试方法。
6. 案例分析:通过实际案例,分析镀锌工艺中可能出现的问题和解决方法,提高员工对镀锌工艺的认识和应对能力。
7. 实践操作:安排员工进行实际操作练习,提高操作技能和熟练程度,增强对镀锌工艺的理解和掌握。
三、镀锌工艺培训的意义1. 提高操作技能:通过培训,可以使操作人员学习到镀锌工艺的理论知识和实际操作技能,提高生产工艺水平和操作效率。
2. 保障产品质量:加强员工对镀锌工艺的了解和掌握,可以提高产品的质量稳定性和一致性,降低次品率和质量事故发生的风险。
3. 提高安全意识:培训中加强安全操作规程的宣讲,让员工充分认识到操作中的安全风险,提高安全意识和应急处置能力。
4. 促进团队合作:员工通过培训可以增进对镀锌工艺的理解和认同,增强团队协作能力,实现员工内部协作和沟通的优化。
5. 增加员工技能:培训可以提高员工的职业技能水平,增加就业竞争力,为公司和员工共赢创造更大的价值。
镀锌工艺培训(第二章)--19页-BD
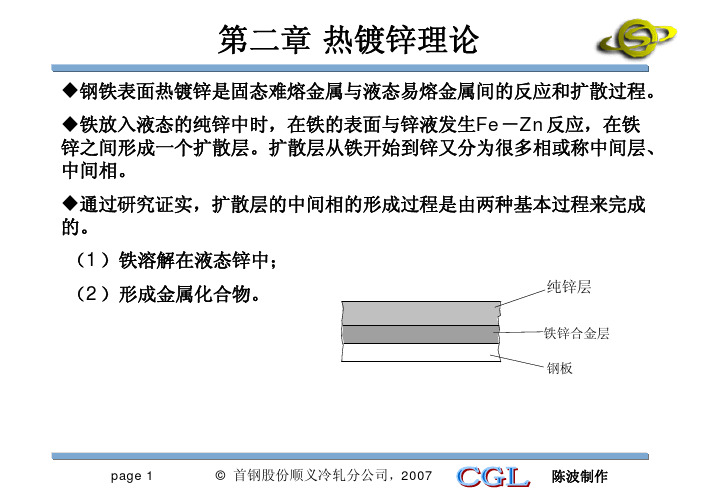
第二章热镀锌理论钢铁表面热镀锌是固态难熔金属与液态易熔金属间的反应和扩散过程。
铁放入液态的纯锌中时,在铁的表面与锌液发生Fe -Zn 反应,在铁锌之间形成一个扩散层。
扩散层从铁开始到锌又分为很多相或称中间层、中间相。
通过研究证实,扩散层的中间相的形成过程是由两种基本过程来完成的。
(1)铁溶解在液态锌中;(2)形成金属化合物。
钢板铁锌合金层纯锌层第一节中间相形成的两个基本过程铁溶解在液态锌中的过程:热镀锌时,铁原子跑到液态锌中形成了一定浓度的溶液(Fe%)。
设某温度下的饱和浓度为Fe’%,则:(1)Fe%< Fe’%(镀锌时间短),则在该反应过程中就不产生固相。
镀锌完后其表面上的结晶或者是一种共晶(FeZn7+Zn),或者是共晶中夹杂着多余的均匀分布的FeZn7晶体。
(2)Fe%>Fe’%(镀锌时间长),则在反应过程中FeZn7晶体就应形成并长大。
形成底碴,或造成锌粒缺陷。
第一节中间相形成的两个基本过程形成金属化合物Fe5Zn21的过程:z金属化合物Fe5Zn21的形成是一个反应过程,它的形成存在一个滞后现象,这段推迟时间一般称为孕育期t,它的倒数1/t称为化合物的形成速度。
z在确定的热镀锌条件下,镀锌层的合金层厚度及结构主要取决于铁的溶解速度(单位时间内被溶解掉的铁量dQ/dt)和金属化合物形成速度的对比关系。
铁的溶解及化合物的形成(1)当铁的溶解速度≈Fe5Zn21形成速度,早期形成共晶与FeZn7,后形成Fe5Zn21(能有力阻止铁的进一步溶解)。
(2)当铁的溶解速度远>Fe5Zn21形成速度,带钢表面上形成Fe5Zn21的这一反应便大大减慢,化合物Fe5Zn21就完全不会形成。
(3)当铁的溶解速度<Fe5Zn21形成速度,则镀锌一开始Fe5Zn21便首先形成,并阻止了铁的进一步溶解。
在此情况下,镀锌层的合金层可能只由一种Fe5Zn21晶体组成。
实践证明,就是镀锌时间较短,也有可能形成这样的结构。
热镀锌实用工艺描述
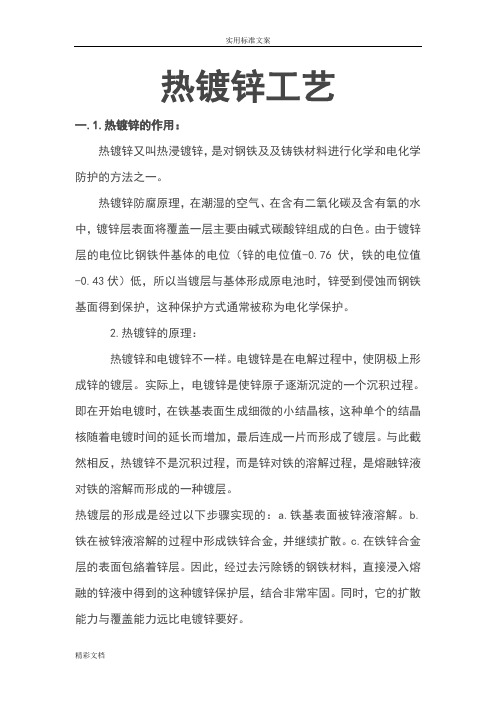
热镀锌工艺一.1.热镀锌的作用:热镀锌又叫热浸镀锌,是对钢铁及及铸铁材料进行化学和电化学防护的方法之一。
热镀锌防腐原理,在潮湿的空气、在含有二氧化碳及含有氧的水中,镀锌层表面将覆盖一层主要由碱式碳酸锌组成的白色。
由于镀锌层的电位比钢铁件基体的电位(锌的电位值-0.76伏,铁的电位值-0.43伏)低,所以当镀层与基体形成原电池时,锌受到侵蚀而钢铁基面得到保护,这种保护方式通常被称为电化学保护。
2.热镀锌的原理:热镀锌和电镀锌不一样。
电镀锌是在电解过程中,使阴极上形成锌的镀层。
实际上,电镀锌是使锌原子逐渐沉淀的一个沉积过程。
即在开始电镀时,在铁基表面生成细微的小结晶核,这种单个的结晶核随着电镀时间的延长而增加,最后连成一片而形成了镀层。
与此截然相反,热镀锌不是沉积过程,而是锌对铁的溶解过程,是熔融锌液对铁的溶解而形成的一种镀层。
热镀层的形成是经过以下步骤实现的:a.铁基表面被锌液溶解。
b.铁在被锌液溶解的过程中形成铁锌合金,并继续扩散。
c.在铁锌合金层的表面包絡着锌层。
因此,经过去污除锈的钢铁材料,直接浸入熔融的锌液中得到的这种镀锌保护层,结合非常牢固。
同时,它的扩散能力与覆盖能力远比电镀锌要好。
所谓扩散能力和覆盖能力,就是镀层在被镀材料表面上的均匀和完整性。
扩散能力又叫均镀能力,它是指镀层厚度的均匀分布能力;覆盖能力又叫深度能力或着落能力。
3.热镀锌的基本工艺过程:工件分类---酸洗---水洗----浸溶剂---烘干---浸镀----冷却----钝化------整修---打包二.镀前处理:1.工件分类:在工件进场后,首先要把有油漆、油污的工件挑选出来做脱脂处理(脱脂分机械法、火焰法、化学法)。
然后仔细观察工件有窝气或兜锌,如发现有要选择合理的穿挂方法以避免窝气、兜锌现象。
实在不行应联系厂家做合理的开孔处理。
二.酸洗:钢铁是容易氧化和腐蚀的金属,其表面一般都存在氧化皮和铁锈。
钢铁表面常见的氧化物有氧化亚铁(FeO,灰色)、三氧化二铁(Fe2O3,赤色)、含水三氧化二铁(Fe2O3.ȵH2O,橙红色)和四氧化三铁(Fe3O4,蓝黑色)等。
镀锌工艺资料

• 锌层应均匀、连续, 无缺陷、裂纹等 • 检查锌层外观质量 是否符合标准
• 锌层与金属基体结 合紧密,无脱落现象 • 检查锌层结合力是 否符合标准
• 通过盐雾试验、浸 液腐蚀试验等方法评 估锌层的耐腐蚀性能 • 检查锌层耐腐蚀性 能是否符合标准
镀锌层的维护与修复
镀锌层的维护
• 定期检查镀锌层的外观质量 • 避免镀锌层受到划伤、撞击等损伤 • 定期进行镀锌层的表面处理,如抛光、清洁等
环保法规对镀锌工艺的影响
• 镀锌企业需要投入较多的资金进行环保改造 • 镀锌企业的生产成本提高 • 镀锌工艺的发展受到一定的限制
镀锌工艺的环保解决方案
• 镀锌工艺的环保解决方案 • 采用环保型镀锌添加剂 • 优化镀锌工艺,降低污染物排放 • 对镀锌废水、废气、固体废弃物等进行处理
• 环保型镀锌添加剂 • 降低镀锌过程中产生的污染物 • 提高镀锌层的性能 • 降低镀锌企业的环保成本
05
磁粉检测
• 检查锌层是否有裂 纹、缺陷等 • 评估锌层的完整性
镀锌层的质量控制标准
镀锌层的质量控制标准
锌层厚度 的控制标
准
锌层外观 质量的控 制标准
锌层结合 力的控制
标准
锌层耐腐 蚀性能的 控制标准
• 锌层厚度 • 锌层外观质量 • 锌层结合力 • 锌层耐腐蚀性能
• 根据产品要求和工 艺条件设定锌层厚度 范围 • 检查锌层厚度是否 符合标准
镀锌工艺的分类及特点
镀锌工艺的分类
• 热镀锌工艺 • 冷镀锌工艺 • 电镀锌工艺
冷镀锌工艺特点
• 锌层厚度薄,耐腐蚀性能较差 • 适用于薄板、线材等金属基体 • 生产成本低,生产效率较高
热镀锌工艺特点
• 锌层厚度大,耐腐蚀性能好 • 适用于各种金属基体 • 生产成本高
镀锌工艺培训(第一章)BD

13
问题2:金属的大气腐蚀
三、铝的大气腐蚀 (先讲牺牲阳极保护法) 铝在大气中也会发生腐蚀,表面会生成氧化层,而Al2O3是非常稳 定和难于溶解的物质,它使钢板表面处于一种钝态,极不活跃,即 使刮伤后也能很快再生成Al2O3,保护了Al的进一步氧化,所以具 有良好的耐氧化性,但因此对钢板的阴极保护作用不如镀锌层。
© 首钢股份公司顺义冷轧分公司,2007
陈波制作
为什么钢铁会腐蚀? 其根本原因还是钢铁自身的原因,任何金属最稳定的状态
就是它原来在自然界中所处的状况,所以一旦条件适合, 它们便恢复到原先的矿物状态,生成氧化物、硫化物、碳 酸盐等,这就是金属的腐蚀现象。
9
影响金属腐蚀的外因(外界介质)
腐蚀除决定于金属本身的化学性质和组织结构外,还与周 围的介质有很大关系。
3、Patience is bitter, but its fruit is sweet. (Jean Jacques Rousseau , French thinker)忍耐是痛苦的,但它的果实是甜蜜的。10:516.17.202110:516.17.202110:5110:51:196.17.202110:516.17.2021
16
强制外加电流保护法
强制外加电流阴极保护是通过外加直流电源以及辅助阳极,迫使电 流从土壤中流向被保护金属,使被保护金属结构电位低于周围环境。
被保护金属、辅助阳极在腐蚀介质中形成的电解池中,分别是负极、 正极。
辅助阳极本身不消耗。 强制外加电流保护方法需要一个持续不断的电流,所以在这套保护
试验地点北京青岛广州武汉江津地理位置东经1161612025113191140310617北纬39543606230830382919海拔高度734180662332086气候类型特征温和城市气候温和海洋溅射亚热带城市气候亚热带城市气候亚热带乡村气候年平均温度119123210168179年平均相对湿度5772777681大气中so0108101309003360101202316降水中cl痕量3448857331169517119空气中cl0038901381001960014800084ph6375566142水中so痕量29938936014192编号种类镀层厚度基板厚度mm处理方式基材电镀锌2020060钝化al镇静热镀锌140140050钝化al镇静热镀锌100100060钝化al镇静高强热镀锌140140150未钝化al镇静深冲电镀锌2020100钝化深冲热镀锌140140150未钝化al镇静080钝化深冲热镀锌7070090钝化根据iso9226中关于评定大气腐蚀性的规定采用的试样尺寸为150mm100mm试样固定在曝晒架上与水平呈45角面向南面
镀锌工艺培训(第二章)

硅:含硅量较高的镇静钢对镀锌影响非常大,若采用一般生产工艺镀 锌层的附着性是得不到保证的。在生产实践中已证实采用一般生产工 艺带钢表面经常出现不规则的脱锌区域,若提高带钢加热温度延长还 原时间,是可以得到改善的。其主要原因是带钢在加热过程中可引起 硅的表面富集,引起锌-铁合金层的剧烈增厚,造成附着性下降。由于 采用含硅较高的原料生产热镀锌产品不能采用一般生产工艺,故造成 生产成本增加,设备损耗增大等一系列后果,为此热镀锌的原料均采 用低硅的沸腾钢或铝镇静钢。
460℃ 419℃ 1 2 3 4 5 6
F E D C B A
锌锅
A—带钢,B—Fe2Al5中间层,C—Fe-Zn合金层,D—纯锌层,E—镀层外表氧 化膜,F—带钢温度变化曲线
page 9
加铝热镀锌镀层的粘附性机理
在加铝法带钢热镀锌过程中,由于铝对铁比锌对铁有较大的 热力学亲合力,Fe-Al的自由焓为40卡/克· 原子,大于 Fe-Zn的自由焓,因此带钢在镀锌过程中能够超比例地从锌 液中吸取大量的铝,且Fe-Al化合物优先于Fe-Zn化合物在 钢基表面形成并直接富集于钢基表面上。只要铝存在,富集 过程就进行,而且不仅在熔融状态,就是在凝固之后,这个 过程一直进行到低于扩散和反应所需的温度为止。由此可知, 在镀锌的过程中,在温度、镀锌时间的影响下,Fe-Al化合 物优先在钢基表面形成。一个薄而均质的中间层,它牢固的 附着在钢基表面,起到粘附镀层的媒介作用。
page 11
第四节 加铝热镀锌镀层粘附性的结构判别
在镀锌的温度范围内,Fe2Al5能够溶解大约13%的锌, 当溶锌量超过13%时,Fe2Al5将处于过饱和状态,生 成高锌固溶体。此时的中间层中铝的绝对含量虽然没有 减少,但铝的百分含量却显著降低,由于锌的过饱和可 能呈细粒分散析出,破坏了Fe2Al5中间层的均质性, 使中间层丧失了阻止Fe、Zn扩散的作用,并形成较厚 的Fe-Zn合金层。镀层的附着性也随之变坏。
热镀锌工艺学习资料

热镀锌工艺学习资料镀锌工艺学习资料1、工艺流程2、钢铁对热镀锌的影响因素钢材成分、表面状态、表面粗糙度、金属的内应力、镀件几何尺寸3、钢材中影响热镀锌的主要元素:碳(C)、硅(Si)、锰(Mn)、磷(P) 4、钢材中含碳量越高,铁锌反应越剧烈,锌层也越厚。
镀材质硅含量锌层表面容易形成锌瘤,并产生大量漏镀。
Q235 ≤0.35 硅可使铁在锌液中的溶解速度加快,镀锌层变灰,粘附性变差,增加锌灰、锌渣等。
镀锌层变灰,会随着钢中硅含量Q345 ≤0.5 的增高存在着一个波浪式的变化,该现象称为“圣德林效应”。
Q420 ≤0.5 5、酸洗原理:酸与工件表面氧化铁皮、铁锈及杂物进行反应,将工件表面洗净。
欠酸洗即为钢管酸洗时间过短表面氧化铁皮、铁锈及杂物未洗尽。
当工件欠酸洗时,钢管表面仍然有铁锈或其它杂物存在。
过酸洗即为酸洗时间过长,使钢管基体受到过分的腐蚀。
过酸洗时,钢管表面将会出现粗糙麻面或表面发黑或表面有粗糙的黑色麻面。
6、配制盐酸酸液浓度及温度要求是什么?酸洗液配制浓度为18%―20% 酸洗液温度为室温酸洗操作:采用预酸洗工艺,梯度酸洗,上下反复提动3次。
如何配酸?1、槽液高度不允许超过酸槽高度的2/3;2、根据槽液高度添加2/5的清水;3、加入含量≥30%左右的盐酸,补足槽中余下容积;4、按原酸1%比例,添加抑雾剂及除锈剂,防止盐酸挥发及过酸洗现象的产生7、酸洗回收标准为,酸含量小于15克/升同时亚铁含量大于350克/升8、助镀剂的作用(1)、清除工件表面,去除酸洗后残留在工件表面的铁盐或氧化物,使钢铁件在进入锌液时具有最大的表面活性;(2)、在工件表面沉积一层盐膜,防止工件从助镀池到锌锅的一段时间内在空气中锈蚀;(3)、净化工件浸入锌液处的液相锌,使工件与锌液快速浸润并反应。
助镀剂:PH值助镀剂适宜的PH值范围为4-5,这个PH值范围的助镀剂可以给酸洗后的镀件表面进一步清洁,弥补酸洗时可能存在的不足。
热镀锌资料

• 2.2对于结构复杂的钢制件,客户应提供了解产品的相关资 料,如制件的图纸或结构示意图,产品结构的必要交流。 • 2.3产品热镀锌前处理、浸锌后处理有无特殊要求:比如对 热镀锌工艺的要求,具体到前处理、热浸锌、后处理方面 包括:酸洗有无特殊要求,镀锌操作是采取挂镀还是吹镀, 镀锌后是否需要再喷塑、喷漆等处理等; • 2.4结构、焊接件应确保焊接质量,以防止镀锌后因焊接质 量问题影响镀锌产品的整体质量。 包括焊接区域的焊剂、 焊渣的清理等。 15
• 待镀件确认
为确保镀锌质量,必须对来料(以下统称待镀件)进 行全面确认。主要确认项目如下: 1、待镀件表面情况:待镀件的表面锈蚀、粘附物及平 整度。 ⑴表面锈蚀非常严重的,确认除锈后是否造成镀件基 体损坏;
24
• ⑵粘附物: 包括标签、胶水、油漆、油脂等异物附着在镀件 表面,使被覆盖的镀件表面不能有效实施酸洗、浸助 剂等工艺,造成镀锌漏镀,且在锌锅中产生锌灰,增 加成本,所以发现后需及时清除。如发现油漆等不能 有效清除的情况,及时与客户沟通,商议解决方案。
徐州大黄山热镀锌厂 生产部制
1
目
录
contents
• 1、热镀锌概述 1.1热浸镀锌定义 1.2热浸镀锌优点 1.3热浸镀锌产品类别 1.4热浸镀锌相关要求 • 2、镀锌工艺流程 • 3、热镀锌产品质量缺陷
2
第一章 热镀锌概述
Hot Dip Galvanizing
•
热镀锌是由较古老的热镀方法发展而来的,自从1836 年法国把热镀锌应用于工业以来,已经有一百七十多年的 历史了。然而,热镀锌工业是近六十年来伴随冷轧带钢的 飞速发展而得到了大规模发展。随着工业的发现,热镀锌 产品已经运用到很多领域,被广泛运用于电力铁塔、通信 铁塔、铁路、公路防护、路灯杆、船用构件、建筑钢结构 构件、变电站附属设施、轻工业等。
热镀锌的工艺过程
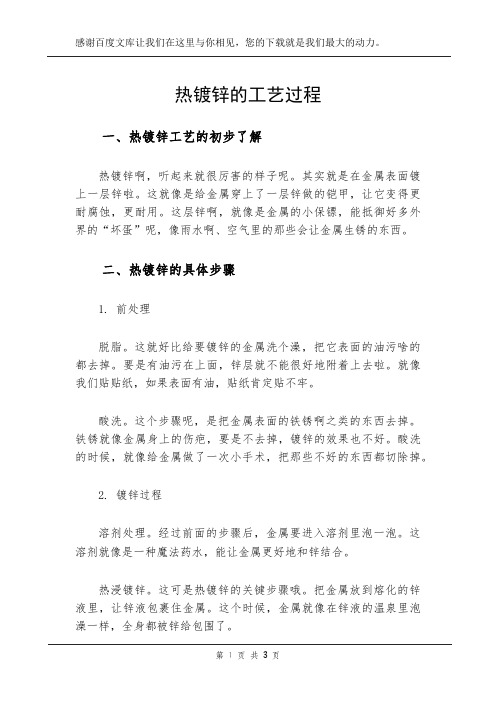
热镀锌的工艺过程一、热镀锌工艺的初步了解热镀锌啊,听起来就很厉害的样子呢。
其实就是在金属表面镀上一层锌啦。
这就像是给金属穿上了一层锌做的铠甲,让它变得更耐腐蚀,更耐用。
这层锌啊,就像是金属的小保镖,能抵御好多外界的“坏蛋”呢,像雨水啊、空气里的那些会让金属生锈的东西。
二、热镀锌的具体步骤1. 前处理脱脂。
这就好比给要镀锌的金属洗个澡,把它表面的油污啥的都去掉。
要是有油污在上面,锌层就不能很好地附着上去啦。
就像我们贴贴纸,如果表面有油,贴纸肯定贴不牢。
酸洗。
这个步骤呢,是把金属表面的铁锈啊之类的东西去掉。
铁锈就像金属身上的伤疤,要是不去掉,镀锌的效果也不好。
酸洗的时候,就像给金属做了一次小手术,把那些不好的东西都切除掉。
2. 镀锌过程溶剂处理。
经过前面的步骤后,金属要进入溶剂里泡一泡。
这溶剂就像是一种魔法药水,能让金属更好地和锌结合。
热浸镀锌。
这可是热镀锌的关键步骤哦。
把金属放到熔化的锌液里,让锌液包裹住金属。
这个时候,金属就像在锌液的温泉里泡澡一样,全身都被锌给包围了。
3. 后处理冷却。
从锌液里出来的金属还很热呢,要让它冷却下来。
就像我们刚从热水里出来,要慢慢适应外面的温度。
钝化处理。
这一步是给镀了锌的金属再上一层保护膜。
就像给穿了铠甲的金属又加了一件披风,让它的防护能力更强。
三、热镀锌工艺中的注意事项1. 温度控制在热浸镀锌的时候,锌液的温度可重要啦。
温度太高或者太低都不行。
如果温度太高,锌液可能会太稀,镀上去的锌层可能就不均匀;要是温度太低呢,锌液太稠,金属在里面可能就不能很好地被镀上锌。
2. 金属表面的质量前面的脱脂和酸洗一定要做好。
如果金属表面还有残留的油污或者铁锈,那镀锌的质量肯定好不了。
就像盖房子,如果地基没打好,房子肯定不牢固。
3. 镀锌的时间在热浸镀锌的时候,金属在锌液里泡的时间也得合适。
泡的时间短了,锌层可能太薄,达不到很好的防护效果;泡的时间太长呢,锌层可能太厚,浪费锌不说,还可能影响金属的一些性能。
- 1、下载文档前请自行甄别文档内容的完整性,平台不提供额外的编辑、内容补充、找答案等附加服务。
- 2、"仅部分预览"的文档,不可在线预览部分如存在完整性等问题,可反馈申请退款(可完整预览的文档不适用该条件!)。
- 3、如文档侵犯您的权益,请联系客服反馈,我们会尽快为您处理(人工客服工作时间:9:00-18:30)。
镀锌工艺学习资料
1、工艺流程
2、钢铁对热镀锌的影响因素
钢材成分、表面状态、表面粗糙度、金属的内应力、镀件几何尺寸
应,将工件表面洗净。
欠酸洗即为钢管酸洗时间过短表面氧化铁皮、铁锈及杂物未洗尽。
当工件欠酸洗时,钢管表面仍然有铁锈或其它杂物存在。
过酸洗即为酸洗时间过长,使钢管基体受到过分的腐蚀。
过酸洗时,钢管表面将会出现粗糙麻面或表面发黑或表面有粗糙的黑色麻面。
6、配制盐酸酸液浓度及温度要求是什么?
酸洗液配制浓度为18%—20% 酸洗液温度为室温
酸洗操作:采用预酸洗工艺,梯度酸洗,上下反复提动3次。
如何配酸?
1、槽液高度不允许超过酸槽高度的2/3;
2、根据槽液高度添加2/5的清水;
3、加入含量≥30%左右的盐酸,补足槽中余下容积;
4、按原酸1%比例,添加抑雾剂及除锈剂,防止盐酸挥发及过酸洗现象的产生
7、酸洗回收标准为,酸含量小于15克/升同时亚铁含量大于350克/升
8、助镀剂的作用
(1)、清除工件表面,去除酸洗后残留在工件表面的铁盐或氧化物,使钢铁件在进入锌液时具有最大的表面活性;
(2)、在工件表面沉积一层盐膜,防止工件从助镀池到锌锅的一段时间内在空气中锈蚀;
(3)、净化工件浸入锌液处的液相锌,使工件与锌液快速浸润并反应。
助镀剂:PH值助镀剂适宜的PH值范围为4-5,这个PH值范围的助镀剂可以给酸洗后的镀件表面进一步清洁,弥补酸洗时可能存在的不足。
溶剂中亚铁的控制
工件应充分水洗,确保清洗干净,以免过多亚铁带入溶剂中;工件浸泡溶剂以形成足够
助镀剂的配制
举例:喷镀线一般氯化锌180g/L,氯化铵280g/L;此锌铵比为1.55总量460g/L。
计算:先确定助镀池的容积,假设为10个立方,
则理论上需投入氯化锌量:10*180=1800公斤,氯化铵量:10*280=2800公斤。
助镀液的温度宜控制在60-80°,喷镀线在不烘焦的前提下进行调节。
锌锅加热方式简介:端烧加热、平焰加热、高速脉冲加热锌锅材质:XG08F
锌熔点: 419.5℃铅熔点: 327℃铝熔点: 660℃
化锌周期的保温段为:炉膛温度的150℃、250℃、400℃
9、锌灰是怎样产生的?
1、锌液接触空气被氧化后形成氧化锌。
2、工件表面的溶剂在浸锌过程中形成氯化物和残渣。
10、锌渣是怎么产生的?
溶解在锌液中的铁含量超过该温度下铁的溶解度时,发生锌-铁合金反应,形成流动性极差的锌铁合金。
11、锌灰的控制:
●在锌锅内加适量的铝。
●降低锌液温度,保持在工艺温度的下限。
●避免或减少锌液搅动,尽可能保持工件干燥。
●在不影响生产的情况下,锌灰尽量少打。
●减少锌液面与空气的接触面积,部分区域可采用湿法(撒氯化氨)。
12、锌渣的控制:
1、严格遵守酸洗和溶剂处理工艺操作规程,减少因操作不当将大量铁盐带入锌液中
2、定期挖渣及时打捞锌锅内的掉件
13、增加锌层厚度的因素
(1)、铁—锌合金层表面不平滑,(2)、锌液中含有较多锌渣时,锌液粘度增高。
(3)、锌液温度偏低。
(4)、锌液中氧化锌积聚过多,会严重影响锌液流动。
(6)、大量使用再熔锌和低品位的锌时。
7)、工件从锌液中引出的速度愈快,表面上的张力对锌液的作用力就越小。
(8)、外吹风压过小。
(9)、浸锌时间不稳定。
(10)、工件材质带来的影响。
14、怎样设法降低锌耗
(1)、降低镀在工件表面上的锌:合理掌握锌液温度、锌液的粘度、浸锌时间、引出速度、内外吹风压、空冷时间等。
(2)、减少氧化掉的锌:在锌液中加入适量的铝;减少锌液表面与空气接触的面积,控制锌液温度在下限,保证溶剂中的各项含量在规定的范围,待镀工件溶剂一定要烘干。
(3)、减少变成锌渣的锌:避免锌锅过热;采用低碳、低硅的钢材作锌锅;前处理严格控铁;减少锌液震荡,控制锌液温度并且加热要均匀。
(4)、减少操作过程中损失的锌:防止锌锅漏锌;加适量的铝,减少锌的氧化;采用适量的压力将余锌收回;尽量将锌灰中的锌粒分离回收;低温生产;经常清理碎锌、碎片,清扫现场使其全部回收;
15、白锈、黑斑形成因素
●镀件水冷后没有完全干燥
●直接暴露在雨水或具有腐蚀性环境中
●紧密堆放的镀件由于空气流通不好而干燥缓慢
●自喷漆修复大面积漏镀
●钝化膜形成欠缺
16、镀锌锅渗漏的原因:
(1)锌液温度过高。
(2)加热炉膛温度高于750 ℃。
(3)锌渣太厚,镀锌锅壁上获得的热量不能很快传送到锌液当中,锅壁上造成了局部过热现象,时间长导致穿孔。
(4)温差过大:会使锅壁上形成铁-锌合金层脱落,而失去保护作用,加速锌锅的腐蚀。
(5)机械冲刷:工件在锌液中的移动,及工件出锅时大量锌液流向锌锅内,有力地冲刷了镀锌锅的壁面,使铁—锌合金层脱落而失去保护作用。
(7)溶剂:从工件上脱落的溶剂,未完全失去性能时与锌锅壁接触后会强烈地腐蚀锅壁。
(8)锅壁上粘附的锌灰造成热量的聚集,以及锌液面上铝含量的富集造成锅壁的腐蚀。
(9)因炉灶设计不合理,造成锌锅壁局部温度过高,腐蚀锌锅。
(10)镀锌锅板材:在钢板材料中,含有较高的碳和硅都会加速锌液对锌锅的腐蚀。
17、铝(Al)在锌液中的作用
1、提高镀锌层的光亮性
2、减少锌液表面锌的氧化,减少锌灰的产生
3、锌液中适量的铝含量能降低锌铁的反应速度,起到降低锌层的作用
危害:当锌锅内铝含量严重超标时,需要更多的铁来进行反应,这些铁不仅仅
来自工件,还来自锌锅的内壁。
从而加剧了锌锅的侵蚀,影响锌锅的使用寿命。
18、铅(Pb)在锌液中的作用
1、可提高锌液流动性,减少流痕,降低锌耗
2、可降低操作温度,降低能耗
3、提高工件表面在锌液中的浸润性,避免漏镀现象的发生
4、适当的铅含量可保护锌锅底部,减少锌对锅底的腐蚀
5、沉积的铅有助于锌渣的打捞
危害:锌液中加铅对吊镀件的表面会产生锌花,镀层灰暗,影响外观质量。
铅块的添加必须在锌铁合金层形成之后,否则锌锅底部积聚了含有未饱和锌
的铅层会与锌锅钢板接触,破坏钢板的组织结构,腐蚀锌锅。
含铅量过高时,锌液的流动性反而会变差。
20、镍(Ni)在锌液中的作用
1、可抑制硅含量小于0.25的钢材在锌液中的异常铁锌反应,减小这类钢
材出现灰暗、超厚、粘附性差的镀层(抑制圣德林效应)
2、提高镀层的光亮性、硬度、耐磨度;
3、可减少锌灰的生成量;
危害:锌液中的镍含量过高时,铁在锌液中的溶解度下降,铁的析出与锌反应形成锌渣,所以过高的镍含量会增加锌渣的生成。
镍的过量添加,可能会在锌液中出现颗粒增加及浮渣现象。
19、锡(Sn)在锌液中的作用
1、可提高工件表面浸润性,可使锌液中铝的应用含量提高,减少漏镀现象
2、提高工件表面光亮度
危害:锡的过量加入,会导致Fe-Al层中的铝含量下降,锌层增厚;
可导致镀层的抗氧化性能降低;会降低锌锅的使用寿命;锌液中的锡含量不能超过0.07% 20、锌液中铁的来源
1、工件表面带入的铁
2、工件本体材料的铁基溶入锌液中的铁
3、锌锅内壁溶入锌液中的铁
4、锌锭及合金中附带的铁
21、锌液中铁的危害
1、锌液中的铁与锌结合生成密度较大的锌铁金属间化合物——锌渣
2、锌液中铁含量的增加时锌液粘稠度增加,锌液的流动性变差,增加锌层厚度
3、过多的铁含量导致工件的外观质量变坏产生灰色和粘附性的颗粒
22、热镀锌中影响镀层的主要因素有:锌液成分、锌液温度、浸锌时间、引出速度、工件表面平滑度、喷吹压力、工件材质以及溶剂浓度。