产品质量分析与控制
质量分析与质量控制

质量分析与质量控制
质量分析与质量控制的主要内容是,通过管理程序和工具来维护、改善或保证一定质量标准的产品。
质量分析是识别和定义产品中的问题,并从可能的原因中建立新的质量标准,以便改善。
而质量控制则是在有目标、有计划地进行测试,以检查产品是否符合特定质量要求,以及分析错误原因及为产品改善质量提出建议。
质量分析与质量控制都包括多种方法,用于改进产品质量。
包括:
1. 检验:检验是指对产品在各个生产阶段的最终结果进行客观检查,以确保符合要求的质量标准。
2. 内部和外部审核:内部审核是为了确保组织内部实施质量标准,而外部审核是为了确保组织对外遵守质量标准。
3. 生产:生产是指根据规定进行生产,以确保产品质量。
4. 质量改进:质量改进涉及到找出问题,并发展解决方案,以改善产品质量。
5. 标准:标准包括组织内部的质量标准和技术标准,以及国际标准,这些标准旨在确保最终产品的质量。
6. 计量:计量是指运用精密仪器和设备,以验证产品和记录过程操作质量。
7. 质量保证:质量保证是指组织通过采取有效措施来完成产品质量标准的维护、改进和管理,以及确保客户满意。
通过质量分析和质量控制的方法可以提高产品的整体质量,从而满足客户的需求,提高企业的日益增长的市场竞争力。
为此,采用质量分析和质量控制的方法的企业必须付出一定的时间和金钱,因为它不仅涉及到监控,而且还涉及到制定和改进标准,实施审核和检查,以及培训员工。
此外,组织也必须对质量分析与质量控制进行持续监控,以确保和维护质量标准,并及时修正产品不符合要求的情况,以最大程度地满足客户需要。
产品质量管理与质量控制措施

产品质量管理与质量控制措施产品质量管理是指以满足客户需求为目标,通过对产品生命周期各个环节的监控和控制,确保产品质量的一系列管理活动。
而质量控制措施是指为了确保产品质量的各种方法和手段。
下面我将详细介绍产品质量管理和质量控制措施的内容。
首先,产品质量管理包括以下几个方面。
1.质量策划:制定质量目标、质量标准,确定产品质量的控制点和控制方法,确定质量管理的职责和权限。
2.质量组织:建立健全的质量管理组织体系,明确各级组织的职责、权限和责任。
3.质量设计:加强产品设计阶段的质量控制,通过完善的设计过程和评审机制,确保产品设计的科学性、合理性和可行性。
4.质量采购:建立合理的供应商审核和评价体系,对供应商进行选择、评价和管理,确保原材料和零部件的质量符合要求。
5.质量控制:建立适当的质量控制点和检验方法,对产品生产过程进行监控和控制,及时发现和解决质量问题,确保产品质量的稳定和可靠。
6.质量保证:建立完善的质量管理体系,包括质量手册、质量程序文件和记录等,确保质量管理的规范性和可执行性。
7.质量改进:通过对产品质量问题的分析和整理,不断改善和提升产品的质量水平,提高客户满意度。
其次,质量控制措施包括以下几个方面。
1.质量计划:根据产品质量目标和要求,制定全面的质量计划,包括质量检验计划、质量控制计划和质量改进计划等。
2.质量管理建立:建立健全的质量管理体系,包括质量手册、质量程序文件和记录等,确保质量管理的规范性和可执行性。
3.质量检验:通过对原材料、半成品和成品进行检验,把关产品质量,及时发现和纠正存在的问题。
4.质量控制:制定和执行严格的质量控制措施,包括质量控制点的设定、质量控制方法的建立和执行,保证产品质量的稳定和可靠。
5.质量改进:对产品质量问题进行深入的分析和研究,制定改进措施,不断提高产品质量水平。
6.质量培训:加强员工的质量意识培养,提高员工的质量管理能力,增强员工对产品质量的责任感和使命感。
产品质量成本的分析与控制

产品质量成本的分析与控制产品质量成本是指为了确保产品质量而支出的各种成本,包括内部和外部成本。
内部成本包括预防成本、评估成本和内部失误成本;外部成本则是由于产品质量问题给外部客户或社会带来的损失。
对产品质量成本进行有效的分析和控制,对企业提高竞争力和盈利能力具有重要意义。
首先,预防成本是为了预防产品质量问题而进行的活动所需要的成本。
这包括设立质量管理体系、进行员工培训、实施检测和检验控制等方面的费用。
通过加强预防措施,可以有效地减少产品质量问题的发生,提高产品质量,同时也能够降低后续的成本支出。
因此,企业应当注重提高产品质量意识,加强员工培训,建立健全的质量管理制度,从源头上控制产品质量问题的发生,降低预防成本的支出。
其次,评估成本是为了评估产品质量而进行的活动所需的成本。
这包括实施检测、检验、测量和试验等过程中所需要的费用。
评估成本是确保产品质量的重要一环,通过对产品进行质量评估可以及时发现问题并加以解决,确保产品符合规定的标准和要求。
企业应当建立科学的质量检测体系,加强对产品的评估工作,提高产品质量的可靠性和稳定性,从而降低评估成本的支出。
最后,内部失误成本是由于产品质量问题导致的内部损失所需要的费用。
这包括废品、报废、返修、重做和停工等方面的成本。
内部失误成本是因为产品质量问题而导致的经济损失,对企业的生产效率和盈利能力造成了严重的影响。
企业应当通过加强产品质量管理,完善生产过程控制,提高产品质量稳定性,降低内部失误成本的支出,提高企业经济效益。
另外,外部成本是由于产品质量问题给外部客户或社会带来的损失所需要的费用。
这包括客户投诉、产品退货、赔偿和产品召回等方面的成本。
外部成本是由于产品质量问题而给企业带来的社会责任和声誉损失,对企业形象和发展造成了不利影响。
企业应当重视产品质量问题,加强对外部客户的沟通和反馈,积极解决产品质量问题,降低外部成本的支出,提升企业品牌价值和市场竞争力。
综上所述,对产品质量成本进行有效的分析和控制对企业具有重要的意义。
质量控制部产品缺陷分析与质量控制策略
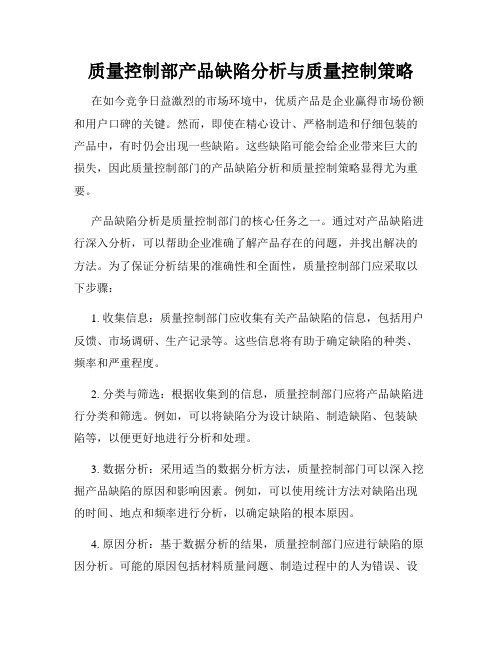
质量控制部产品缺陷分析与质量控制策略在如今竞争日益激烈的市场环境中,优质产品是企业赢得市场份额和用户口碑的关键。
然而,即使在精心设计、严格制造和仔细包装的产品中,有时仍会出现一些缺陷。
这些缺陷可能会给企业带来巨大的损失,因此质量控制部门的产品缺陷分析和质量控制策略显得尤为重要。
产品缺陷分析是质量控制部门的核心任务之一。
通过对产品缺陷进行深入分析,可以帮助企业准确了解产品存在的问题,并找出解决的方法。
为了保证分析结果的准确性和全面性,质量控制部门应采取以下步骤:1. 收集信息:质量控制部门应收集有关产品缺陷的信息,包括用户反馈、市场调研、生产记录等。
这些信息将有助于确定缺陷的种类、频率和严重程度。
2. 分类与筛选:根据收集到的信息,质量控制部门应将产品缺陷进行分类和筛选。
例如,可以将缺陷分为设计缺陷、制造缺陷、包装缺陷等,以便更好地进行分析和处理。
3. 数据分析:采用适当的数据分析方法,质量控制部门可以深入挖掘产品缺陷的原因和影响因素。
例如,可以使用统计方法对缺陷出现的时间、地点和频率进行分析,以确定缺陷的根本原因。
4. 原因分析:基于数据分析的结果,质量控制部门应进行缺陷的原因分析。
可能的原因包括材料质量问题、制造过程中的人为错误、设备故障等。
通过深入分析缺陷的原因,可以更好地制定对策和改进措施。
5. 结果报告:最后,质量控制部门应将缺陷分析结果汇总并形成报告。
报告应包括缺陷的种类、发生频率、原因分析及相应的解决措施。
这些报告能够为企业的决策提供依据,帮助提高产品质量和用户满意度。
除了缺陷分析,质量控制部门还需要制定相应的质量控制策略,以减少产品缺陷的出现。
以下是一些常用的质量控制策略:1. 优化设计:合理设计产品结构和工艺流程,降低产品出现缺陷的概率。
在产品设计阶段,应考虑到材料的可靠性、生产的可操作性和产品的耐用性等因素。
2. 强化制造过程控制:通过使用严格的制造标准和流程控制方法,确保每一个制造环节都符合产品质量要求。
质量控制的质量数据与分析

质量控制的质量数据与分析在现代生产与制造过程中,质量控制起着至关重要的作用。
通过采集、分析和应用质量数据,企业可以监测和改善产品或服务的质量水平。
本文将讨论质量控制中的质量数据和分析方法,并介绍如何利用这些数据来优化生产过程和提升产品质量。
一、质量数据的采集与分类质量数据是指通过实验、测试、观察等方式收集的与产品质量相关的信息。
根据数据来源和性质的不同,质量数据可以分为两类:主观数据和客观数据。
1. 主观数据主观数据是通过人的感觉、经验和判断获得的数据。
例如,产品的外观、手感、味道等。
在采集主观数据时,可以采用问卷调查、专家评判等方法,将数据量化并进行统计分析。
2. 客观数据客观数据是通过仪器、设备等客观手段获得的数据,具有客观性和准确性。
例如,产品的尺寸、重量、温度等。
在采集客观数据时,需要选择适当的测量方法和仪器,并确保数据的准确性和可靠性。
根据质量数据的性质和采集方式不同,可以将质量数据进一步分类为:离散数据和连续数据。
离散数据是指只能取有限值的数据,例如产品的合格与否、产品的次品率等。
连续数据是指可以在某一范围内取任意值的数据,例如温度、压力等。
二、质量数据的分析方法质量数据分析是指对采集到的质量数据进行统计和分析,以解释数据背后的规律和关系。
常用的质量数据分析方法包括描述性统计分析、控制图和假设检验等。
1. 描述性统计分析描述性统计分析是对质量数据的集中趋势和分散程度进行统计描述。
常用的统计指标包括平均值、中位数、标准差、极差等。
通过描述性统计分析,可以直观地了解质量数据的整体情况,并发现异常值或异常情况。
2. 控制图控制图是一种图形化的质量数据分析工具,用于监控和评估质量数据的稳定性和可控性。
常用的控制图包括平均图、范围图、标准差图等。
通过绘制控制图,可以判断质量过程是否处于控制状态,识别特殊因素的影响,并进行及时的校正和改善。
3. 假设检验假设检验是一种统计推断方法,用于比较质量数据与某个假设值或其他数据之间的差异是否显著。
产品检测与质量控制

产品检测与质量控制1. 简介产品检测与质量控制是制造企业在生产过程中的重要环节。
通过产品检测和质量控制,企业能够确保生产的产品符合规定的标准和质量要求,从而提高产品的可靠性和可持续性。
2. 产品检测的重要性产品检测是对产品进行实际测试和分析的过程。
它可以帮助企业发现产品中的问题和不合格项,并采取适当的纠正措施。
以下是产品检测的一些重要性:•确保产品符合标准:产品检测可以确保产品符合国家和行业的相关标准,如质量控制标准和安全标准。
这有助于保证产品的质量和安全性。
•避免产品召回:通过产品检测,企业可以在产品出厂前发现问题,并采取适当的措施,以避免产品召回。
产品召回不仅影响企业的声誉,还会导致巨大的财务损失。
•提高用户满意度:合格的产品可以满足客户的需求和期望,从而提高用户的满意度。
通过产品检测,企业可以确保用户收到高质量和可靠的产品。
3. 产品检测的方法产品检测涉及多种不同的方法和技术。
以下是一些常用的产品检测方法:•物理测试:物理测试是通过对产品的物理属性进行测量和分析,以确定其质量和性能。
例如,对材料的硬度、强度、耐磨性等进行测试。
•化学分析:化学分析可以确定产品中化学成分的含量和纯度。
通过化学分析,可以检测产品中有害物质的存在,并确保产品符合相应的安全标准。
•无损检测:无损检测使用各种技术和方法,如超声波、X射线和磁粉检测,对产品进行检测,而不会对产品造成任何损害。
无损检测可以用于检测产品内部的缺陷和问题,如裂纹和漏洞。
•运行测试:运行测试是通过对产品进行实际运行和使用的测试,以确定其性能和可靠性。
这可以包括对产品的耐久性、稳定性和寿命进行测试。
4. 质量控制的重要性质量控制是确保产品质量的过程。
它包括一系列的控制措施和步骤,旨在确保产品在生产过程中的各个环节都符合质量要求。
以下是质量控制的一些重要性:•提高生产效率:质量控制可以帮助企业识别和纠正生产过程中的问题和缺陷,以提高生产效率。
通过减少生产中的错误和废品,企业可以节省时间和成本。
产品质量问题分析及质量控制措施

产品质量问题分析及质量控制措施1.引言产品质量是企业发展和客户满意度的关键因素。
本文旨在分析产品质量问题,找出原因,并提出相应的质量控制措施,以减少质量问题并提高产品质量。
2.产品质量问题分析首先,我们需要对产品质量问题进行充分的分析,以确定存在的问题类型和原因。
2.1 产品缺陷问题通过对用户反馈和售后服务记录的分析,我们发现产品存在以下缺陷问题:部分产品存在组装不良导致的松动、脱落等问题;部分产品存在外观缺陷,如划痕、气泡等;部分产品存在功能故障,如开关失灵、电池寿命短等。
2.2 生产工艺问题经过对生产线的观察和分析,我们发现生产工艺存在以下问题:原材料采购不严格,导致产品质量不稳定;生产设备维护不及时,影响了产品的生产质量;生产人员培训程度不够,导致操作不规范。
2.3 供应链管理问题我们发现供应链管理存在以下问题:供应商的产品质量监控不达标,给企业的产品质量带来了一定的不确定性;供应商交货周期不稳定,导致我们生产计划的不确定性;供应链信息传递不畅,导致企业对原材料信息的把握不足。
3.质量控制措施针对上述分析的产品质量问题及其原因,我们提出以下质量控制措施:3.1 强化原材料质量管理加强对供应商的审核和监督,建立严格的原材料质量控制标准,确保原材料的质量稳定。
加大进货检验力度,及时发现和拒收不合格原材料。
3.2 进一步完善生产工艺加强生产设备的维护和保养,确保生产线的正常运行。
提高生产人员的培训水平,制定操作规范,加强生产过程的监控和管理。
3.3 优化供应链管理与供应商建立更加紧密的合作关系,共同制定质量管理标准。
提供及时、准确的订单信息,并要求供应商按时交货。
建立有效的供应链信息反馈机制,及时了解原材料信息的变化。
3.4 强化售后服务加强售后服务团队的培训,提高售后服务人员的责任心和服务质量。
建立健全的售后服务体系,及时解决用户的问题,并对问题进行分析和总结。
4.结论产品质量问题分析是了解产品质量问题原因的关键步骤,而质量控制措施的实施可以有效减少产品质量问题的发生。
企业产品质量控制与效能分析
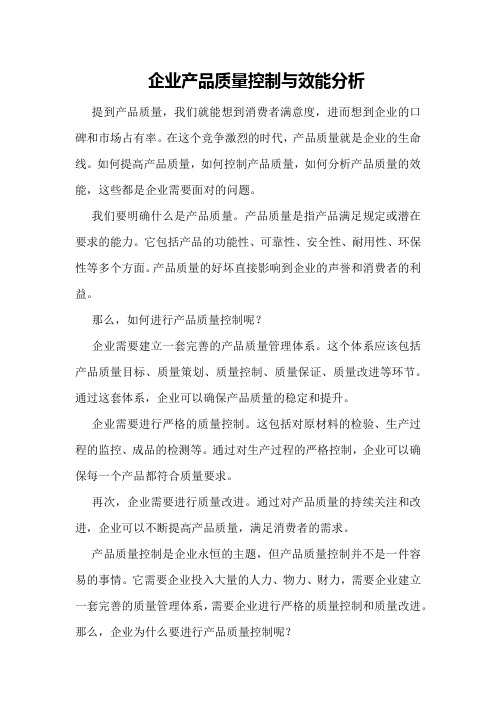
企业产品质量控制与效能分析提到产品质量,我们就能想到消费者满意度,进而想到企业的口碑和市场占有率。
在这个竞争激烈的时代,产品质量就是企业的生命线。
如何提高产品质量,如何控制产品质量,如何分析产品质量的效能,这些都是企业需要面对的问题。
我们要明确什么是产品质量。
产品质量是指产品满足规定或潜在要求的能力。
它包括产品的功能性、可靠性、安全性、耐用性、环保性等多个方面。
产品质量的好坏直接影响到企业的声誉和消费者的利益。
那么,如何进行产品质量控制呢?企业需要建立一套完善的产品质量管理体系。
这个体系应该包括产品质量目标、质量策划、质量控制、质量保证、质量改进等环节。
通过这套体系,企业可以确保产品质量的稳定和提升。
企业需要进行严格的质量控制。
这包括对原材料的检验、生产过程的监控、成品的检测等。
通过对生产过程的严格控制,企业可以确保每一个产品都符合质量要求。
再次,企业需要进行质量改进。
通过对产品质量的持续关注和改进,企业可以不断提高产品质量,满足消费者的需求。
产品质量控制是企业永恒的主题,但产品质量控制并不是一件容易的事情。
它需要企业投入大量的人力、物力、财力,需要企业建立一套完善的质量管理体系,需要企业进行严格的质量控制和质量改进。
那么,企业为什么要进行产品质量控制呢?产品质量控制可以提高消费者的满意度。
消费者购买产品的目的就是为了满足自己的需求,如果产品质量不好,消费者就不能得到满足,甚至会产生不满。
通过对产品质量的控制,企业可以提高消费者的满意度,从而提高企业的声誉。
总的来说,产品质量控制对企业发展具有重要作用。
那么,如何进行产品质量控制呢?企业需要建立一套完善的产品质量管理体系,包括质量目标、质量策划、质量控制、质量保证、质量改进等环节。
企业需要进行严格的质量控制,包括原材料检验、生产过程监控、成品检测等。
再次,企业需要进行质量改进,通过持续关注和改进产品质量,满足消费者需求。
企业需要建立一支专业的质量控制团队,保证产品质量稳定。
出现产品质量问题原因分析与控制措施(如何全方位控制产品质量?)

出现产品质量问题原因分析与控制措施(如何全方位控制产品质量?)01:总则:产品质量是生产出来的,不是检验出来的。
只有在生产过程中的每个环节,严格按照生产工艺和作业指导书要求进行,才能保证产品的质量。
如果忽略过程控制,只靠检验,是不可能保证产品质量的,因为质量检验,只能剔除次品和废品,并不能提高产品质量。
也就是说,质量控制的重点决不能放在事后把关,而必须放在制造阶段,即生产过程阶段。
然而很多的公司,一但有品质问题,就把责任往品质部门推,认为这就是品质部门的责任,因为很多公司都存在着这样的错误观点:•容许少数的不良,意外的瑕疵是无可避免的;•品质是品管部门的责任;•只重视产品的检验,检验人员需要负责解决瑕疵品;•出了问题,都觉得是品质部门的事情。
往往写报告时,品质部一个人完成,其他部门基本上不管;老板觉得品质不是很重要,研发很重要,赚钱才是最重要的。
所以,品质部门在公司并没有什么地位,往往说了几句真话,被该闪人了。
02:为什么会出现品质问题?•产品开发前问题不处理好,量产直通率太低,就希望靠着品质救火,想靠提高检测的频率,从中降低瑕疵品或不合格品;•加入返工料,不合格物料,却没有事先经过测试验证,没有准确的产品质量波动情况认知;•客户催着要货,上面施压,老大就根据自己的所谓的实际经验说话,对于不在标准范围的产品,实施特殊放行,导致产品问题;•行业提高了产品的质量标准,公司还依旧按照原来的标准生产;•生产过程中出现非人为的品质问题,却又不在检测频率范围内等。
品质的真实案例案例一:某汽车配件,使用某公司生产的ABS(750SQ),用了3.4吨后,发现用该原料制造的塑料件表面均有黑点,造成产品不合格,造成了巨大的损失。
案例二:某公司生产白色膜用于奶膜,所有的检测项目都合格,所以方法出厂,但是薄膜生产商在使用的时候,发现母粒味道比较难闻,后来就进行投诉。
最后导致,几百吨的订单,就因为这样的一个品质问题,黄了。
产品质量管理与质量控制措施
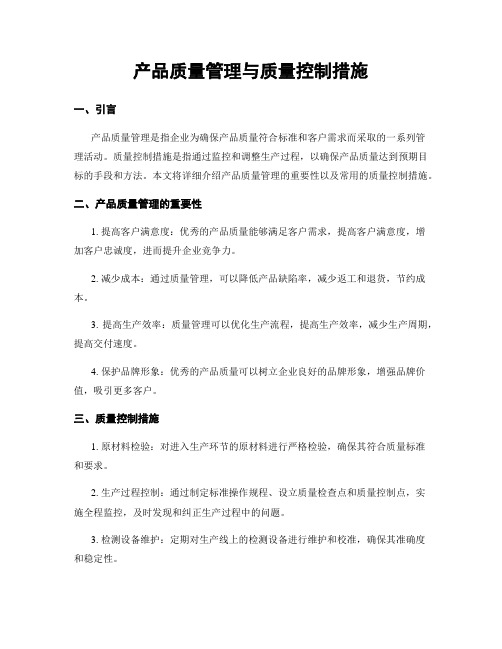
产品质量管理与质量控制措施一、引言产品质量管理是指企业为确保产品质量符合标准和客户需求而采取的一系列管理活动。
质量控制措施是指通过监控和调整生产过程,以确保产品质量达到预期目标的手段和方法。
本文将详细介绍产品质量管理的重要性以及常用的质量控制措施。
二、产品质量管理的重要性1. 提高客户满意度:优秀的产品质量能够满足客户需求,提高客户满意度,增加客户忠诚度,进而提升企业竞争力。
2. 减少成本:通过质量管理,可以降低产品缺陷率,减少返工和退货,节约成本。
3. 提高生产效率:质量管理可以优化生产流程,提高生产效率,减少生产周期,提高交付速度。
4. 保护品牌形象:优秀的产品质量可以树立企业良好的品牌形象,增强品牌价值,吸引更多客户。
三、质量控制措施1. 原材料检验:对进入生产环节的原材料进行严格检验,确保其符合质量标准和要求。
2. 生产过程控制:通过制定标准操作规程、设立质量检查点和质量控制点,实施全程监控,及时发现和纠正生产过程中的问题。
3. 检测设备维护:定期对生产线上的检测设备进行维护和校准,确保其准确度和稳定性。
4. 抽样检验:对生产线上的产品进行抽样检验,确保产品质量符合标准。
5. 不良品处理:对发现的不良品进行分类、记录和处理,分析不良品产生的原因,并采取措施避免类似问题再次发生。
6. 客户投诉处理:建立健全的客户投诉处理机制,及时响应客户投诉,调查问题原因,并采取措施解决问题,以提高客户满意度。
7. 持续改进:通过定期召开质量管理会议,采集员工和客户的意见和建议,不断改进产品质量和质量控制措施。
四、质量管理指标1. 产品合格率:指产品在生产过程中经过检验后,达到质量标准的比例。
2. 不良品率:指产品在生产过程中经过检验后,不符合质量标准的比例。
3. 客户满意度:通过客户调查和反馈,评估客户对产品质量的满意程度。
4. 返工率:指产品在生产过程中因质量问题而需要重新加工的比例。
5. 退货率:指客户因产品质量问题而退回的产品比例。
产品质量管理与质量控制措施
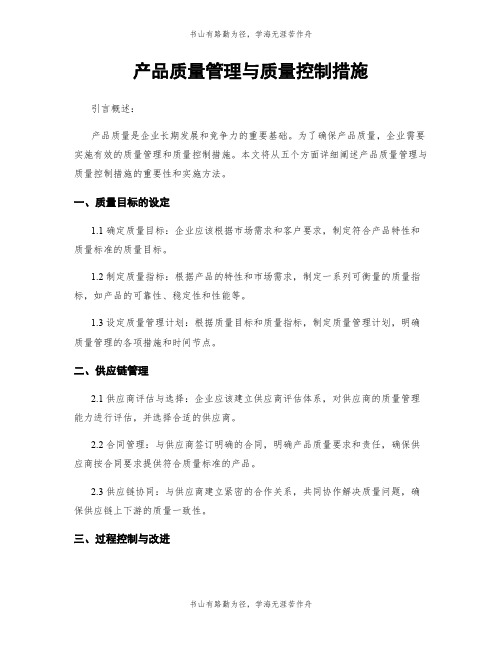
产品质量管理与质量控制措施引言概述:产品质量是企业长期发展和竞争力的重要基础。
为了确保产品质量,企业需要实施有效的质量管理和质量控制措施。
本文将从五个方面详细阐述产品质量管理与质量控制措施的重要性和实施方法。
一、质量目标的设定1.1 确定质量目标:企业应该根据市场需求和客户要求,制定符合产品特性和质量标准的质量目标。
1.2 制定质量指标:根据产品的特性和市场需求,制定一系列可衡量的质量指标,如产品的可靠性、稳定性和性能等。
1.3 设定质量管理计划:根据质量目标和质量指标,制定质量管理计划,明确质量管理的各项措施和时间节点。
二、供应链管理2.1 供应商评估与选择:企业应该建立供应商评估体系,对供应商的质量管理能力进行评估,并选择合适的供应商。
2.2 合同管理:与供应商签订明确的合同,明确产品质量要求和责任,确保供应商按合同要求提供符合质量标准的产品。
2.3 供应链协同:与供应商建立紧密的合作关系,共同协作解决质量问题,确保供应链上下游的质量一致性。
三、过程控制与改进3.1 过程流程管理:建立标准化的工艺流程和作业指导书,确保生产过程的稳定性和一致性。
3.2 过程监控与控制:通过实施过程监控和控制措施,及时发现和纠正生产过程中的异常,防止不良品的产生。
3.3 过程改进:通过持续的过程改进活动,提高生产过程的效率和质量,降低不良品率。
四、产品检验与测试4.1 原材料检验:对原材料进行严格的检验,确保原材料的质量符合要求。
4.2 在线检验:在生产过程中进行在线检验,及时发现和排除不良品,确保产品质量的稳定性。
4.3 最终产品检验和测试:对最终产品进行全面的检验和测试,确保产品的质量符合标准和客户要求。
五、质量反馈与持续改进5.1 客户反馈:建立健全的客户反馈机制,及时收集客户的意见和建议,为产品质量改进提供依据。
5.2 内部评审与审核:定期进行内部评审和审核,发现和解决质量管理中存在的问题,推动质量管理的持续改进。
如何正确进行产品质量控制和检测

如何正确进行产品质量控制和检测产品质量控制和检测是任何制造企业都不可或缺的一环。
只有通过正确的质量控制和检测方法,企业才能保证产品的质量,提高顾客满意度,并增强市场竞争力。
本文将从以下几个方面介绍如何正确进行产品质量控制和检测。
1. 确定质量标准在进行产品质量控制和检测前,企业首先需要明确产品的质量标准。
质量标准可以是国家标准、行业标准或企业自己制定的标准。
质量标准应该包括各项指标,例如外观、尺寸、材料、性能等。
通过明确质量标准,企业可以确保产品在生产过程中达到这些标准。
2. 建立合理的质量控制计划为了保证产品的质量,企业需要建立一套合理的质量控制计划。
该计划应包括从原材料采购到产品出厂的全过程。
质量控制计划应确定关键控制点,并采取相应的控制措施,如在关键控制点设置监测设备、培训员工等。
同时,企业还应制定不同阶段的抽样检测方案,确保产品质量的可控性和一致性。
3. 使用有效的检测方法企业在进行产品质量控制和检测时,应选择适合的方法和技术。
常用的检测方法包括物理检测、化学检测、无损检测等。
在选择检测方法时,企业可以考虑产品特性、成本、检测效果等因素,并与专业的检测机构进行合作,以确保检测结果的准确性和可靠性。
4. 做好数据分析和处理在产品质量检测过程中,企业需要对收集到的检测数据进行分析和处理。
通过统计分析,企业可以了解产品质量的整体状况,及时发现存在的问题,并采取相应的改进措施。
同时,企业还可以通过数据分析预测产品的质量趋势,为产品质量的持续改善提供参考。
5. 加强员工培训企业的员工是产品质量控制和检测的重要环节。
为了确保产品质量,企业应加强员工的培训和技能提升。
培训内容可以包括质量标准的理解和应用、质量控制方法和技术的掌握、仪器设备的操作等。
通过培训,员工可以更好地理解产品质量的重要性,并能够熟练运用所学知识进行相应的操作和控制。
6. 与供应商建立合作关系在产品质量控制和检测过程中,与供应商的合作是非常重要的。
产品质量分析报告8篇

产品质量分析报告8篇第一篇:《产品质量分析报告:如何提高产品质量》随着市场竞争的加剧,产品质量已经成为企业竞争的重要因素之一。
本文将从产品质量的定义、影响因素、提高方法等方面进行分析,以期为企业提高产品质量提供参考。
一、产品质量的定义产品质量是指产品在使用过程中所表现出的性能、可靠性、安全性、耐久性、外观等方面的特征。
产品质量的好坏直接影响到产品的市场竞争力和企业的声誉。
二、影响产品质量的因素1.原材料的质量:原材料是产品的基础,原材料的质量直接影响到产品的质量。
2.生产工艺:生产工艺是影响产品质量的重要因素,生产工艺的不合理会导致产品质量的下降。
3.人员素质:生产人员的素质直接影响到产品的质量,人员素质的提高可以有效地提高产品的质量。
三、提高产品质量的方法1.加强原材料的质量控制:企业应该从源头上控制产品的质量,加强对原材料的质量控制,确保原材料的质量符合要求。
2.优化生产工艺:企业应该不断优化生产工艺,提高生产效率的同时,确保产品的质量。
3.加强人员培训:企业应该加强对生产人员的培训,提高生产人员的素质,确保生产人员能够熟练掌握生产工艺,提高产品的质量。
本文从产品质量的定义、影响因素、提高方法等方面进行了分析,希望能够为企业提高产品质量提供参考。
第二篇:《产品质量分析报告:如何解决产品质量问题》产品质量问题是企业在生产经营过程中经常遇到的问题,如何解决产品质量问题是企业必须面对的问题。
本文将从产品质量问题的原因、解决方法等方面进行分析,以期为企业解决产品质量问题提供参考。
一、产品质量问题的原因1.原材料的质量不过关:原材料是产品的基础,原材料的质量不过关会导致产品质量的下降。
2.生产工艺不合理:生产工艺的不合理会导致产品质量的下降。
3.人员素质不高:生产人员的素质不高会导致产品质量的下降。
二、解决产品质量问题的方法1.加强原材料的质量控制:企业应该从源头上控制产品的质量,加强对原材料的质量控制,确保原材料的质量符合要求。
如何正确进行产品质量控制和检测
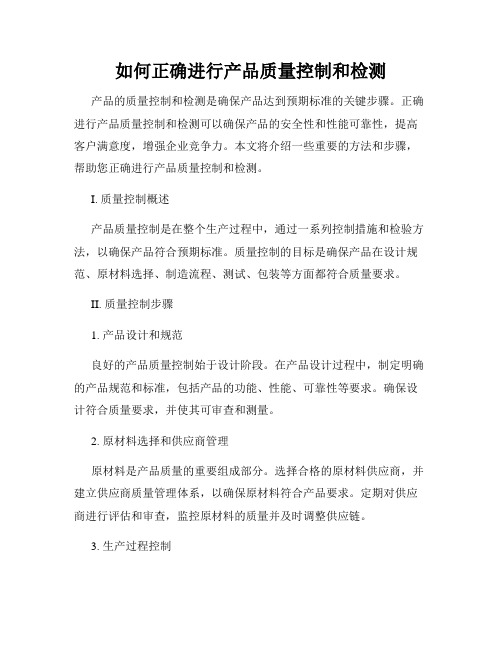
如何正确进行产品质量控制和检测产品的质量控制和检测是确保产品达到预期标准的关键步骤。
正确进行产品质量控制和检测可以确保产品的安全性和性能可靠性,提高客户满意度,增强企业竞争力。
本文将介绍一些重要的方法和步骤,帮助您正确进行产品质量控制和检测。
I. 质量控制概述产品质量控制是在整个生产过程中,通过一系列控制措施和检验方法,以确保产品符合预期标准。
质量控制的目标是确保产品在设计规范、原材料选择、制造流程、测试、包装等方面都符合质量要求。
II. 质量控制步骤1. 产品设计和规范良好的产品质量控制始于设计阶段。
在产品设计过程中,制定明确的产品规范和标准,包括产品的功能、性能、可靠性等要求。
确保设计符合质量要求,并使其可审查和测量。
2. 原材料选择和供应商管理原材料是产品质量的重要组成部分。
选择合格的原材料供应商,并建立供应商质量管理体系,以确保原材料符合产品要求。
定期对供应商进行评估和审查,监控原材料的质量并及时调整供应链。
3. 生产过程控制生产过程控制是质量控制的核心环节。
确保生产过程符合标准操作规程(SOP)和工艺流程,减少人为误差和机械故障对产品质量的影响。
建立严格的生产记录和追溯体系,对生产线进行监控和数据采集,及时发现并纠正潜在问题。
4. 检验和测试检验和测试是质量控制的重要手段。
通过对产品的关键参数、外观、尺寸等进行检验和测试,验证产品是否符合规范要求。
建立合适的检验方法和设备,制定检验标准,并进行合理的抽样检验和全面的产品测试。
5. 不合格品管理和改进在质量控制过程中,可能会发现不合格品。
立即对不合格品进行处理,包括分类、追溯原因、纠正和预防措施,以防止类似问题再次发生。
通过不合格品管理和改进措施,提高产品的质量稳定性和一致性。
III. 质量检测方法1. 抽样检验抽样检验是通过抽取少部分样本,对整个批次产品进行检验和判断。
在制定抽样计划时,应根据批次大小、产品的关键特性和检验级别等因素进行选择。
产品质检中的品质管理与控制

产品质检中的品质管理与控制在产品质检中的品质管理与控制产品质量一直以来都是企业发展的重要关键。
在现代竞争激烈的市场环境下,只有拥有优质的产品才能在激烈的竞争中立于不败之地。
为了保证产品的品质,质检部门在生产过程中起着至关重要的作用。
本文将探讨在产品质检中的品质管理与控制的重要性以及其相关的具体措施。
一、品质管理的重要性品质管理是指企业通过建立和实施一系列管理活动和控制措施,以确保产品的品质符合标准和要求。
品质管理的重要性表现在以下几个方面。
首先,品质管理可以提升产品的竞争力。
在市场竞争中,产品质量是消费者选择的重要因素。
如果产品质量无法得到保证,消费者将会转而选择其他品牌的产品,从而降低企业的市场份额。
通过品质管理,企业可以提高产品的品质,满足消费者的需求,提升产品的竞争力。
其次,品质管理可以减少生产过程中的错误和浪费。
通过建立合理的质量控制措施,及时发现和纠正生产过程中的问题,可以减少产品的次品率和废品率,降低资源的浪费,提高生产效率和经济效益。
再次,品质管理可以确保产品的安全性和可靠性。
特别是对于一些关键性产品,如食品、药品、机械设备等,安全性和可靠性是至关重要的。
品质管理可以保证产品符合相关的标准和法规要求,确保产品的使用安全和可靠性,维护消费者的权益。
最后,品质管理对企业品牌形象的建立和维护也具有重要作用。
优质的产品和可靠的品质管理可以树立企业的良好品牌形象,增强消费者的信任和忠诚度,提高企业的市场声誉。
二、品质管理与控制的具体措施品质管理与控制需要从产品研发、生产、销售等各个环节入手,采取一系列具体措施,确保产品的品质符合标准和要求。
首先,产品研发阶段需要重视品质管理。
企业在产品研发过程中应该根据市场需求和消费者需求确定产品的品质要求和标准。
同时,还需要建立科学的研发流程和规范,确保产品的设计符合要求,避免出现设计缺陷。
其次,生产过程中的品质管理也非常重要。
企业应该建立健全的质量管理体系,包括制定详细的生产工艺和标准操作规程,建立质量检测和监控系统,保证生产过程中的质量可控。
工业产品质量控制与改进分析

工业产品质量控制与改进分析工业产品的质量控制和改进是制造业生产过程中至关重要的环节。
优质的产品质量不仅能够赢得市场的认可和消费者的满意,还能够提高企业的竞争力和盈利能力。
因此,如何有效地进行质量控制和改进,成为了制造业企业必须重视和解决的问题。
一、质量控制的重要性优质的工业产品不仅具备稳定的性能和可靠的使用寿命,还能够提高用户的工作效率,并为用户创造经济效益。
然而,如果工业产品的质量无法得到有效的控制和保证,将给用户带来巨大的损失和风险。
因此,质量控制对于工业产品具有重要的意义。
首先,质量控制能够保障产品的稳定性和可靠性。
通过制定严格的产品检验标准和质量管控流程,可以确保产品在制造过程中的各个环节严格按照标准操作,减少产品出现质量问题的概率。
例如,在汽车制造过程中,通过对零部件的质量检测和产品的组装工艺控制,可以降低汽车在使用过程中的故障率,提高产品的可靠性和使用寿命。
其次,质量控制能够提高产品的交付性能和满足度。
通过优化生产工艺和提升生产设备的精度和性能,可以提高产品的加工精度和一致性,从而满足用户对于产品性能和精度要求的需求。
例如,在电子产品制造行业中,通过调整和优化生产工艺,可以提高产品的响应速度和稳定性,提升用户对于产品的满意度。
最后,质量控制能够降低制造成本和提高企业绩效。
通过降低产品的缺陷率和退货率,可以减少企业的资源浪费和成本支出。
同时,通过提高产品的质量和用户满意度,可以增加企业的市场份额和获取更多的订单,进一步提高企业的收入和利润。
因此,质量控制不仅能够保障产品质量,还可以为企业带来经济效益和竞争优势。
二、质量控制的方法和手段在进行工业产品质量控制的过程中,可以采用多种方法和手段,以确保产品的质量稳定和可靠。
首先,可采用统计质量控制方法。
通过采集产品制造过程中的关键数据,并进行统计分析,可以发现生产过程中的潜在问题和变异因素,及时调整生产参数,减少产品的变异和缺陷率。
例如,在食品加工过程中,通过对原料的检测和加工环节的监控,可以控制产品的含糖量、含油量等关键指标,确保产品的质量符合标准要求。
产品质量问题分析及质量控制措施

产品质量问题分析及质量控制措施1. 引言产品质量对于企业的长期发展至关重要。
质量问题不仅会给企业带来损失,还会影响客户满意度和品牌声誉。
因此,及时分析产品质量问题,并制定合理的质量控制措施,是确保产品质量的关键。
2. 问题分析2.1. 核心问题首先,我们需要分析产品质量问题的根本原因。
通过对相关数据和客户反馈进行分析,我们发现以下核心问题:- 设计问题:产品设计不合理导致质量问题。
- 生产过程问题:生产过程中存在工艺不合理或操作失误。
- 材料问题:使用了质量不稳定的原材料。
2.2. 影响问题产品质量问题带来的影响多方面,包括但不限于:- 客户投诉和退货增加,影响客户满意度。
- 产品质量问题的频繁出现损害企业声誉和品牌形象。
- 重复生产和拒收率增加导致成本增加,影响企业盈利能力。
2.3. 原因分析针对核心问题,我们需要深入分析其原因,以找到合适的解决方案。
- 设计问题:加强与设计部门的合作,建立设计评审机制,提前发现和纠正设计问题。
- 生产过程问题:加强员工培训和操作规范,制定详细的工艺流程和操作指南。
- 材料问题:加强供应商管理,建立高品质原材料供应链,进行严格的入库检验。
3. 质量控制措施为了解决产品质量问题,我们需要采取以下质量控制措施:- 设计控制:建立设计评审机制,规范设计过程,确保产品设计的合理性和可行性。
- 生产控制:加强员工培训,持续改进生产工艺,建立严格的质量检查制度。
- 材料控制:加强供应商管理,与稳定的供应商建立长期合作关系,进行严格的原材料入库检验。
- 测试控制:建立完善的测试流程,对产品进行全面的检测和验证。
- 反馈控制:及时收集和分析客户反馈,对产品质量问题进行追踪和改进。
4. 结论产品质量问题分析及质量控制措施的制定对于确保产品质量至关重要。
我们应该加强团队合作,解决核心问题,并搭建完善的质量控制体系,以提升客户满意度和保护企业品牌形象。
只有通过持续改进和精益求精,我们才能在激烈的市场竞争中脱颖而出,并取得长期成功。
质量控制报告:产品质量分析与提升建议
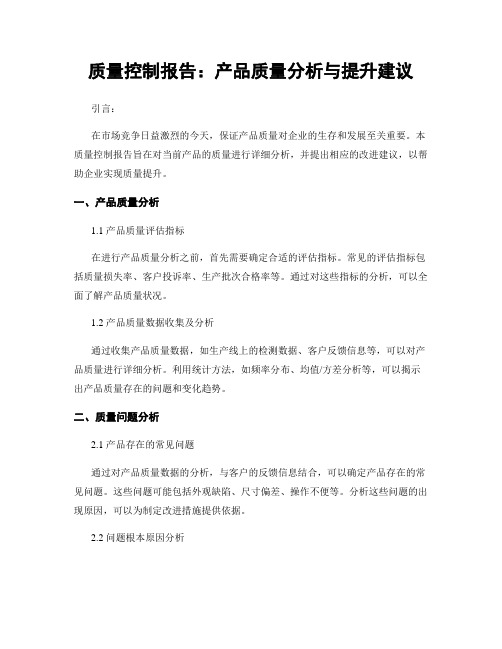
质量控制报告:产品质量分析与提升建议引言:在市场竞争日益激烈的今天,保证产品质量对企业的生存和发展至关重要。
本质量控制报告旨在对当前产品的质量进行详细分析,并提出相应的改进建议,以帮助企业实现质量提升。
一、产品质量分析1.1 产品质量评估指标在进行产品质量分析之前,首先需要确定合适的评估指标。
常见的评估指标包括质量损失率、客户投诉率、生产批次合格率等。
通过对这些指标的分析,可以全面了解产品质量状况。
1.2 产品质量数据收集及分析通过收集产品质量数据,如生产线上的检测数据、客户反馈信息等,可以对产品质量进行详细分析。
利用统计方法,如频率分布、均值/方差分析等,可以揭示出产品质量存在的问题和变化趋势。
二、质量问题分析2.1 产品存在的常见问题通过对产品质量数据的分析,与客户的反馈信息结合,可以确定产品存在的常见问题。
这些问题可能包括外观缺陷、尺寸偏差、操作不便等。
分析这些问题的出现原因,可以为制定改进措施提供依据。
2.2 问题根本原因分析对于产品质量问题的分析,除了直接的表面原因外,还需要进行根本原因的分析。
通过使用质量工具,如因果关系图、故障模式与效果分析(FMEA)等,可以找到问题背后的深层次原因,以避免问题再次出现。
三、质量改进建议3.1 工艺改进在质量问题分析的基础上,可以针对产品存在的问题,提出针对性的工艺改进建议。
例如,通过优化生产工艺流程,改进设备维护制度等,可有效提升产品的质量水平。
3.2 设备升级产品质量与生产设备密切相关,在面对制约产品质量的问题时,可以考虑进行设备升级。
这可能包括购买更先进的生产设备、使用更高精度的检测仪器等,以提高生产效率和产品质量。
四、质量控制与监测措施4.1 质量控制体系建设建立完善的质量控制体系是确保产品质量稳定和持续提升的基础。
通过制定标准操作规程、加强内部质量培训等措施,可以提高质量控制的稳定性和准确性。
4.2 质量监测与反馈研究市场动态与用户需求,及时进行质量监测并收集客户反馈信息,有助于企业及时发现产品质量问题,并采取相应改进措施。
产品质量控制中的关键环节分析
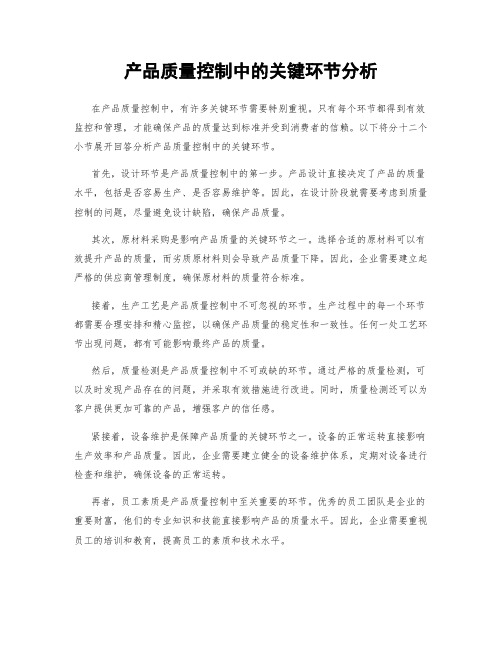
产品质量控制中的关键环节分析在产品质量控制中,有许多关键环节需要特别重视。
只有每个环节都得到有效监控和管理,才能确保产品的质量达到标准并受到消费者的信赖。
以下将分十二个小节展开回答分析产品质量控制中的关键环节。
首先,设计环节是产品质量控制中的第一步。
产品设计直接决定了产品的质量水平,包括是否容易生产、是否容易维护等。
因此,在设计阶段就需要考虑到质量控制的问题,尽量避免设计缺陷,确保产品质量。
其次,原材料采购是影响产品质量的关键环节之一。
选择合适的原材料可以有效提升产品的质量,而劣质原材料则会导致产品质量下降。
因此,企业需要建立起严格的供应商管理制度,确保原材料的质量符合标准。
接着,生产工艺是产品质量控制中不可忽视的环节。
生产过程中的每一个环节都需要合理安排和精心监控,以确保产品质量的稳定性和一致性。
任何一处工艺环节出现问题,都有可能影响最终产品的质量。
然后,质量检测是产品质量控制中不可或缺的环节。
通过严格的质量检测,可以及时发现产品存在的问题,并采取有效措施进行改进。
同时,质量检测还可以为客户提供更加可靠的产品,增强客户的信任感。
紧接着,设备维护是保障产品质量的关键环节之一。
设备的正常运转直接影响生产效率和产品质量。
因此,企业需要建立健全的设备维护体系,定期对设备进行检查和维护,确保设备的正常运转。
再者,员工素质是产品质量控制中至关重要的环节。
优秀的员工团队是企业的重要财富,他们的专业知识和技能直接影响产品的质量水平。
因此,企业需要重视员工的培训和教育,提高员工的素质和技术水平。
此外,管理体系是产品质量控制中的重要环节之一。
建立科学合理的管理体系可以有效监控并规范生产过程,确保产品质量的稳定性和可靠性。
而一旦出现问题,也能够及时发现并解决,保证产品质量达标。
接下来,售后服务是产品质量控制中不可忽视的关键环节。
客户的满意度直接关系到产品的口碑和市场形象。
因此,企业需要提供优质的售后服务,及时解决客户遇到的问题,留住客户、提升口碑。
产品质量与质量控制
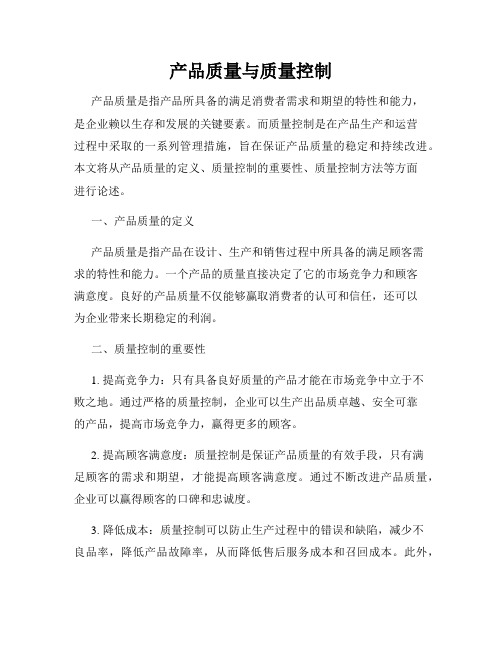
产品质量与质量控制产品质量是指产品所具备的满足消费者需求和期望的特性和能力,是企业赖以生存和发展的关键要素。
而质量控制是在产品生产和运营过程中采取的一系列管理措施,旨在保证产品质量的稳定和持续改进。
本文将从产品质量的定义、质量控制的重要性、质量控制方法等方面进行论述。
一、产品质量的定义产品质量是指产品在设计、生产和销售过程中所具备的满足顾客需求的特性和能力。
一个产品的质量直接决定了它的市场竞争力和顾客满意度。
良好的产品质量不仅能够赢取消费者的认可和信任,还可以为企业带来长期稳定的利润。
二、质量控制的重要性1. 提高竞争力:只有具备良好质量的产品才能在市场竞争中立于不败之地。
通过严格的质量控制,企业可以生产出品质卓越、安全可靠的产品,提高市场竞争力,赢得更多的顾客。
2. 提高顾客满意度:质量控制是保证产品质量的有效手段,只有满足顾客的需求和期望,才能提高顾客满意度。
通过不断改进产品质量,企业可以赢得顾客的口碑和忠诚度。
3. 降低成本:质量控制可以防止生产过程中的错误和缺陷,减少不良品率,降低产品故障率,从而降低售后服务成本和召回成本。
此外,高质量的产品使用寿命更长,可以增加用户的再购买率,促进企业的利润增长。
三、质量控制方法1. 严格的原材料采购:原材料是产品质量的基础,采购部门应按照一定的标准和程序,选择优质的原材料供应商,确保原材料的质量符合产品要求。
2. 设立质量控制体系:企业应根据国家和行业的标准要求,建立一套完整的质量控制体系。
包括产品设计阶段的质量控制、生产过程中的质量控制、产品检验和测试的质量控制以及售后服务的质量控制等。
3. 建立质量检测与监控机制:引入先进的质量检测设备和技术,对产品进行全面的质量检测,实施全过程的质量监控。
发现问题及时整改,确保产品符合质量标准。
4. 培训员工:员工是质量控制的关键,企业应加强员工的质量意识培养和技能培训,确保员工具备足够的技能和知识来生产高质量的产品。
- 1、下载文档前请自行甄别文档内容的完整性,平台不提供额外的编辑、内容补充、找答案等附加服务。
- 2、"仅部分预览"的文档,不可在线预览部分如存在完整性等问题,可反馈申请退款(可完整预览的文档不适用该条件!)。
- 3、如文档侵犯您的权益,请联系客服反馈,我们会尽快为您处理(人工客服工作时间:9:00-18:30)。
产品质量分析与控制
14年度公司三条生产线产品场内平均合格率88.09%,其中精铸生产线平均合格率为95.04%同比13年为92.84%上升2.2%,树脂砂
生产线平均合格率85.22%同比13年为75.25%上升9.97%,红砂生产
线平均合格率为84.03%同比13年为83.42%上升2.3%,14年度平均
合格率同比13年度平均合格率(83.83)%同比上升4.26%(表一)
1.2014年度出运产品退废率4.05%,13年度退废率7.83%,同比13年上升3.78%
2.2014年度总退废率按照总退废金额÷总销售额=885110÷21854569=4.05%
上述质量目标未完成或完成不好根本原因主要有:
一、精铸生产线产品主要缺陷统计表;
1.精铸产品缺陷类型主要集中在缩孔/缩松和漏壳/破壳两大项;1.1缩孔:废品总数量为2109件主要集中65C箱体,S20轴板,S30阀板以及4X阀板,冒口根部产生缩孔。
主要集中的原因有浇注温度过高以及工艺操作不规范及过程控制不严谨导致。
1.2破壳/漏壳: 废品总数量为3881件,产生废品主要原因一有以下几点:
1.2.1主要人为操作因数,挂砂时候操作不当导致壳层偏薄,模壳在焙烧过程中摆放不当导致破壳/漏壳等。
1.2.2产品干燥时间过长导致模壳开裂和鼓包,制壳工艺执行的力度不够,操作没有按照工艺执行,操作粗糙。
1.2.3有些大件产品操作时比较困难导致型壳的厚度不均匀,型壳强度无法承受压力导致漏壳。
二、红砂生产线产品主要缺陷统计表;
铜生产线产品缺陷类型主要集中在缩孔/气孔砂眼2大类型:
1.30-14”以上铜阀板冒口处缩孔,主要问题为炉胆及浇包未烘透,浇注时铜水除气不够,砂片未烘干透导致铸件冒口端气缩孔。
2.31U铜阀体及铜阀板表面砂眼气孔,主要为工艺出气浮渣不当导致。
3.现场生产管理的缺失是产品报废的主要原因。
三、树脂砂产品生产线主要缺陷统计表;
1.缩孔产品主要集中为31U 4寸5寸/31 10寸12寸阀体工艺不稳
定导致缩孔。
2.其中气孔的质量问题有以下大方面失效产生,第一点;造型设备
陈旧造成砂和树脂固化比例不均匀浇注后型腔内含气量高形成气孔,第二点:主要集中在合箱前砂片未烘干及合箱时部分封箱膏流入铸型内,导致铸件气孔。
2014年主要质量问题的产品以及现场解决问题产品如下,主要在以下几方面:
一、质量管理体系的建立维护和有效运行
1.完成公司TUV质量体系年审工作。
2.完成TUV材料认证的年审工作。
3.准备DNV船级社续证计划在201
4.12月前完成。
4.IS0 9001-2008版本将升级至2015版,后续计划2015年对
体内审员进行培训。
二、有效推进铸造工艺和模具质量的改进
模具改进方面:
1.模具是产品质量重要环节,精铸14年共提交,125副模具维修,未
修完成模具还有15副,砂铸14年共提35副模具维修全部合格,未修完成模具还有4副,剩下未完成的计划在2014年12月份完成并且在原先工艺的基础上对砂铸模具进行改进砂铁比,节约制造成本。
工艺改进方面:
1.通过改进4X阀板的浇注工艺,由原先的正方形模头更改为三角型
产品出品率较之前提高6%左右,试样结果良好,已经投入使用。
2.586新产品通过熔炼工艺的改进,对铸件浇注后进行加罩保温处
理,解决了586材质产品浇注后裂纹缺陷问题。
3.为满足顾客对精密铸造铜合金铸件的需求,对CC499K铜合金水泵
进行中温蜡硅溶胶试样,增加精密铸造铜合金方面的生产能力。
4.为满足生产需求,通过对65C箱体打磨工装的改进加快的65C箱
体的生产进度,由原先日生产量10件增加至20件满足了生产需求。
三、过程监视和测量的加强
2014年在2013年的基础上对以下过程监视和测量区域均配置予以保持。
如手提式硬度计和超声波测厚仪器、手提式 MT磁粉探伤设备,有效控制大件产品的硬度和壁厚尺寸以及焊补位置探伤,蜡模车间通过测温仪对蜡液静置桶除水桶等进行监视测量确保蜡液质量,挂砂车间重新采购了一套黏度测量杯确保制壳浆液浓度,人员上我们对特殊过程的生产人员及检验人员进行定期培训,确保过程数据的准确性及有效性。
总结2014的质量不稳定的原因并结合2013年生产发展趋势的基础上,扩大对质量管理与控制的范畴、制定多层次机制,规划实施如下措施:
1.具体检验员岗位与职责
根据公司2015年总体计划,需要增加1名技术人员协助生产线工程师对质量隐患进行信息汇总以及推进质量问题的解决。
2.建立检验员培训机制
1.2015年部门人员将作调整,第一,负责实验室测试人员加强对产品性能测试和质量分析以及标准理解并对相关试验人员能力进行培训,提高工作效率。
第二,结合生产实际调整现场检验员能灵活处理不同产品的检验方式方法以及检验标准理解在2014年的基础上进一步深入,第三、安排外出等方面学习,来提升我们检验队伍人员的业务能力的不断提高,更好地服务于生产,更好地建立检验队伍梯队建设。
3. 产品质量管理以及原材料控制;
针对2014年三条生产出现重大的质量缺陷如;1.精铸生产线的破壳/漏壳2.砂铸生产线缩孔,气孔。
3.红砂生产线缩孔将作为2015年的重点整改内容,针对该质量问题对现场各个环节的工艺参数以及模具保养计划,操作要领进行监控,将检验落实到具体负责人并协助铸造工程师质量改进推动计划。
原材料方面加强进货检验能力,尤其对一些关键材料的控制如砂子,蜡,不锈钢,树脂等材料的检测力度确保产品质量稳定。
5.加大过程监视和测量
质量问题频发甚至群发有九成以上都属过程操中工艺执行力失控与操作控制不当引起的,有的甚至酿成质量事故,必须引起高度重视,2015将采取以下控制措施:
1)由现场工程师及质量管理员牵头对操作人员进行定期培训,严格要求三条生产线如实按照工艺执行,建立现场监督机制时时通报。
2)加强炉前化验质量控制降低投料成本。
3)增加各材内部控制标准,确保材质性能的稳定性。
4)加大对现场检验力度,更准、更快完成当天产品检验。
5)加大炉前测温结果与实际记录进行比对。
6)对现场实行日检查机制,将产品质量做到预防在先,竭力遏止不良品交到客户手中。
7)掌握品质变异的4MIE要素的预防工作与分析。
6. 形成质量例会机制
通过开展每周一下午的定期质量例会,汇总“不合格会签单”和现场质量问题以及客户NCR/CAR等质量问题进行跟踪过程或结果与及时封闭、客户质量问题投诉的分解与讨论及时落实退废品,统计每周厂内报废品进行原因分析落实相应工程师解决,厂内合格率进行分析、模具运行状态等,建立了质量问题讨论小组协商对策,在短时间内有效解决产品质量问题。
7. 提高产品质量水平
通过总结这些年的经验和教训,针对2014年发生质量事故的教训、加深对产品质量的重视程度、开展预防工作,配合好工程师将3条铸造生产线(精铸,树脂砂,红砂)以及新增机加工生产线的质量隐患逐一消除,努力上述措施的落实,新的一年里有信心也有决心完成以下质量目标:。