水泥热工设备11水泥熟料形成过程及煅烧设备的分类
水泥煅烧技术及设备

蓖式冷却机水泥熟料冷却机是水泥回转窑中重要的设备,也是一种热交换装置,它通过高温物料向低温气体传热,使从回转窑内卸出的熟料(温度一般在1000—1400℃之间)经过冷却后温度阵至100一200℃,并将含有大量热量(相当于熟料热耗的20%一85%)的废气加以利用,提高窑的热效率;另外,熟料的冷却过程还可改善熟料质量和火焰燃烧条件,提高熟料易磨性,节约能源。
其主要功能是对水泥熟料进行冷却、输送;同时为回转窑及分解炉等提供热空气,是烧成系统热回收的主要设备。
随着现代新型干法水泥生产技术和装备的迅速发展,以及水泥熟料篦冷机的技术不断提高,高效能、运行可靠的熟料篦冷机成为确保系统生产能力的关键。
设计特点:●进料端采用了先进的KID系统及脉动供风,使出窑高温熟料快速冷却,提高了熟料的强度和易磨性,彻底消除堆“雪人”及“红河”现象对篦板的毁坏,提高设备运转率;●优化的篦床分区供风,精确控制各冷却区域的用风量,最终达到高效冷却,获得高的热回收效率,节能效果显著;●摆动补偿器能补偿篦床在三维空间的运动,使用寿命长;●所有轴承外臵,风室内无润滑点、运转可靠;●结构紧凑、占用空间少;●高效新型篦板结构,漏料量极少,减少篦板磨损、延长使用寿命。
拉链机间歇运行,减少故障率、降低电耗;●新结构的料封阀,减少空气泄漏。
结构简单、维护方便;●模块化设计,减少安装费用、加快安装进度;●完善的监测调控技术,确保篦冷机运行更加可靠、稳定窑的操作。
具有以上特点的HCFC型控制流篦冷机已广泛应用于水泥及氧化铝生产线的新建及老设备的改造,及电力行业中颗粒物料的冷却,生产实际使用已达到国际指标,保持国内领先水平。
技术指标:●产量600~10000 t/d ●热效率≥72%●入料温度1370℃●出料温度65℃+环境温度●出料熟料粒度≤25mm ●设备运转率≥98%●篦板使用>2年熟料冷却机性能是否满足要求,应考虑如下几方面的问题。
(1)冷却机的热效率回收熟料的热量与熟料带进冷却机的热量之比,叫冷却机的热效率。
水泥工艺学第五章水泥熟料的煅烧

带悬浮预热器和加热机的窑,分解反应有一部分在预 热器和加热机内进行,而带窑外分解炉的窑绝大部分的分 解反应是在分解炉内进行。
回转窑内物料温度和气体温度以及各带划分的大致情况图
第一节 生料在煅烧过程中的物理与 化学变化
一、干燥与脱水 1、干燥
自由水的蒸发; 各类窑生料的水分:立窑12-15%;湿法窑30-40%;立波 尔窑18-22%;预热器、预分解窑<1%
2、脱水
主要指粘土类矿物释放结合水,包括100℃释放吸附水、 400℃ -600℃释放结构水。脱水时,可以提高矿物的活性。
五、熟料的冷却
冷却目的: (1)回收热量,提高窑炉热效率。 (2)提高熟料易磨性和熟料质量。 (3)降低熟料温度,有利于熟料后续工序的进行。
熟料冷却速度对熟料质量以及性能的影响:
(1)防止或减少C3S的分解。 (2)避免β - C2S 转变成γ - C2S。 (3)改善水泥安定性。 (4)使熟料C3A晶体减少,提高水泥抗硫酸盐性能。 (5)改善熟料易磨性。 (6)可克服水泥瞬凝或快凝。
三、固相反应
1、反应过程 800℃ 生成CA、CF,开始形成C2S 800℃ -900℃ C12A7开始形成
900℃ -1100℃ C2AS形成后又分解, C3A C4AF开始形成。 所有CaCO3分解,f-CaO达到最大值。 1100℃ -1200℃ C3A C4AF大量形成,C2S达到最大值 1250℃ -1280℃ 出现液相。 2、特点 有固相参加、反应在表面进行、受扩散的影响,反应 速度慢。
水泥熟料烧成系统发展史
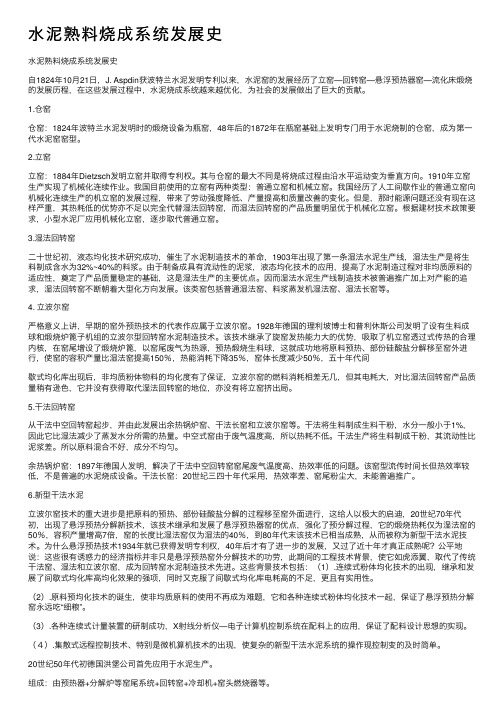
⽔泥熟料烧成系统发展史⽔泥熟料烧成系统发展史⾃1824年10⽉21⽇,J. Aspdin获波特兰⽔泥发明专利以来,⽔泥窑的发展经历了⽴窑—回转窑—悬浮预热器窑—流化床煅烧的发展历程,在这些发展过程中,⽔泥烧成系统越来越优化,为社会的发展做出了巨⼤的贡献。
1.仓窑仓窑:1824年波特兰⽔泥发明时的煅烧设备为瓶窑,48年后的1872年在瓶窑基础上发明专门⽤于⽔泥烧制的仓窑,成为第⼀代⽔泥窑窑型。
2.⽴窑⽴窑:1884年Dietzsch发明⽴窑并取得专利权。
其与仓窑的最⼤不同是将烧成过程由沿⽔平运动变为垂直⽅向。
1910年⽴窑⽣产实现了机械化连续作业。
我国⽬前使⽤的⽴窑有两种类型:普通⽴窑和机械⽴窑。
我国经历了⼈⼯间歇作业的普通⽴窑向机械化连续⽣产的机⽴窑的发展过程,带来了劳动强度降低、产量提⾼和质量改善的变化。
但是,那时能源问题还没有现在这样严重,其热耗低的优势亦不⾜以完全代替湿法回转窑,⽽湿法回转窑的产品质量明显优于机械化⽴窑。
根据建材技术政策要求,⼩型⽔泥⼚应⽤机械化⽴窑,逐步取代普通⽴窑。
3.湿法回转窑⼆⼗世纪初,液态均化技术研究成功,催⽣了⽔泥制造技术的⾰命,1903年出现了第⼀条湿法⽔泥⽣产线,湿法⽣产是将⽣料制成含⽔为32%~40%的料浆。
由于制备成具有流动性的泥浆,液态均化技术的应⽤,提⾼了⽔泥制造过程对⾮均质原料的适应性,奠定了产品质量稳定的基础,这是湿法⽣产的主要优点。
因⽽湿法⽔泥⽣产线制造技术被普遍推⼴加上对产能的追求,湿法回转窑不断朝着⼤型化⽅向发展。
该类窑包括普通湿法窑、料浆蒸发机湿法窑、湿法长窑等。
4. ⽴波尔窑严格意义上讲,早期的窑外预热技术的代表作应属于⽴波尔窑。
1928年德国的理利坡博⼠和普利休斯公司发明了设有⽣料成球和煅烧炉篦⼦机组的⽴波尔型回转窑⽔泥制造技术。
该技术继承了旋窑发热能⼒⼤的优势,吸取了机⽴窑透过式传热的合理内核,在窑尾增设了煅烧炉篦,以窑尾废⽓为热源,预热煅烧⽣料球,这就成功地将原料预热、部份硅酸盐分解移⾄窑外进⾏,使窑的容积产量⽐湿法窑提⾼150%,热能消耗下降35%,窑体长度减少50%,五⼗年代间歇式均化库出现后,⾮均质粉体物料的均化度有了保证,⽴波尔窑的燃料消耗相差⽆⼏,但其电耗⼤,对⽐湿法回转窑产品质量稍有逊⾊,它并没有获得取代湿法回转窑的地位,亦没有将⽴窑挤出局。
水泥熟料煅烧设备
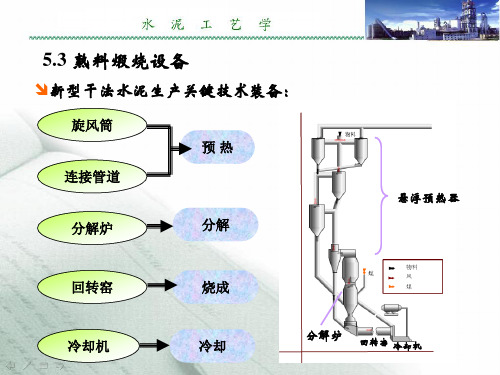
窑熟料携出热量回收。
• (4)作为熟料输送装备,输 送高温熟料。
热效率(%)
< 50 65~70 70~75
第四代推动棒 式篦冷机
45~55
1.5~2.0
72~76ຫໍສະໝຸດ 5.3.4 冷却机(Clinker Cooler)
• 熟料冷却机作业原理在于高效、快速地实现 熟料与冷却空气之间的气固换热。
5.3.4 冷却机(Clinker Cooler)
熟料冷却机的功能及其在预分解窑系统中的作用: • (1)作为工艺装备,对高温 熟料的骤冷。 • (2)作为热工装备,对二次 风、三次风的加热升温 • (3)作为热回收装备,对出
5.3 熟料煅烧设备
新型干法水泥生产关键技术装备:
旋风筒 预热 连接管道
悬浮预热器
分解炉
分解
回转窑
烧成
冷却机
冷却
分解炉
回转窑 冷却机
5.3.1 悬浮预热器(suspension preheater)
1、定义
是指低温粉状物料均
匀分散在高温气流之 中,在悬浮状态下进 行热交换,使物料得 到迅速加热升温的技 术。
2、优越性
物料悬浮在热气流中
,与气流的接触面积 大幅度增加,传热、 传质迅速可大幅度提 高了生产效率和热效 率。
5.3.1 悬浮预热器(suspension preheater)
水泥热工设备复习资料
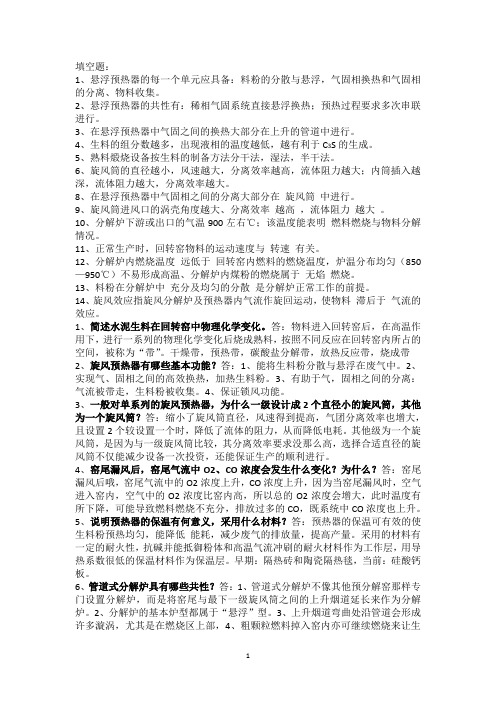
填空题:1、悬浮预热器的每一个单元应具备:料粉的分散与悬浮,气固相换热和气固相的分离、物料收集。
2、悬浮预热器的共性有:稀相气固系统直接悬浮换热;预热过程要求多次串联进行。
3、在悬浮预热器中气固之间的换热大部分在上升的管道中进行。
4、生料的组分数越多,出现液相的温度越低,越有利于C3S的生成。
5、熟料煅烧设备按生料的制备方法分干法,湿法,半干法。
6、旋风筒的直径越小,风速越大,分离效率越高,流体阻力越大;内筒插入越深,流体阻力越大,分离效率越大。
8、在悬浮预热器中气固相之间的分离大部分在旋风筒中进行。
9、旋风筒进风口的涡壳角度越大、分离效率越高,流体阻力越大。
10、分解炉下游或出口的气温900左右℃;该温度能表明燃料燃烧与物料分解情况。
11、正常生产时,回转窑物料的运动速度与转速有关。
12、分解炉内燃烧温度远低于回转窑内燃料的燃烧温度,炉温分布均匀(850—950℃)不易形成高温、分解炉内煤粉的燃烧属于无焰燃烧。
13、料粉在分解炉中充分及均匀的分散是分解炉正常工作的前提。
14、旋风效应指旋风分解炉及预热器内气流作旋回运动,使物料滞后于气流的效应。
1、简述水泥生料在回转窑中物理化学变化。
答:物料进入回转窑后,在高温作用下,进行一系列的物理化学变化后烧成熟料,按照不同反应在回转窑内所占的空间,被称为“带”。
干燥带,预热带,碳酸盐分解带,放热反应带,烧成带2、旋风预热器有哪些基本功能?答:1、能将生料粉分散与悬浮在废气中。
2、实现气、固相之间的高效换热,加热生料粉。
3、有助于气,固相之间的分离:气流被带走,生料粉被收集。
4、保证锁风功能。
3、一般对单系列的旋风预热器,为什么一级设计成2个直径小的旋风筒,其他为一个旋风筒?答:缩小了旋风筒直径,风速得到提高,气团分离效率也增大,且设置2个较设置一个时,降低了流体的阻力,从而降低电耗。
其他级为一个旋风筒,是因为与一级旋风筒比较,其分离效率要求没那么高,选择合适直径的旋风筒不仅能减少设备一次投资,还能保证生产的顺利进行。
水泥热工设备

水泥的热工设备指水泥熟料的煅烧设备 及附属设备。
水泥熟料煅烧是水泥生产中的重要工序,是影 响和决定水泥质量的重要环节。 任何水泥熟料的煅烧都要经历干燥、预热、分 解、固相反应、烧成阶段。 水泥热工设备根据熟料煅烧的各个阶段所采用 的方法和设备不同,水泥的热工设备也各不相同。
一、分类 1. 按水泥煅烧熟料窑的结构分类
2、多筒冷却机 由环绕在回转窑出料端的若干个(4-16)冷却 筒构成。筒径一般为 0.8-1.4m, L/D 4.5-5.5, 长度4-7m,冷却筒与窑体连成一体,并随回转窑一 起回转。 特点: 结构简单,不需要另设传动装置,电耗较低, 无废气污染。但是冷却机与窑体连体,窑头胴体承 受的机械负荷很大,限制了多筒冷却机冷却能力的 进一步提高及在大型窑上的应用。 结构:
湿法中等长度回转窑:L/D 18-30,与料浆压滤机 组合
干法回转窑煅烧系统有:
干法中空长窑:L/D 20-38 干法短窑带余热锅炉:L/D 15-30 干法短窑与料球加热机组合(立波尔窑):L/D 10-15 干法短窑与悬浮预热器、预分解炉组合: L/D 14-17,通称新型干法分大约30-35%,,为 了强化传热,往往在窑内冷端加装链条和或窑炉外 加装料浆预热器。 湿法回转窑的热耗与干法相比,热耗较大,其热 量主要由燃料提供,支出的热量: 反应 :30-33% 蒸发料浆水分:25-30% 废气带走:20-24% 窑炉表面散热:10% 熟料和其他原因带走一部分热量
(二)冷却机类型
筒式冷却机 单筒 多筒式 推动篦式 振动篦式 回转篦式
蓖式冷却机
立筒式 其它冷却机 “g”型冷却机
(三)冷却机结构特点
1、单筒冷却机 是最早使用的冷却机,和回转窑相似。单筒冷却 机与回转窑的相对布置方法有逆流和顺流两种方式。 特点: 单筒冷却机结构简单,运转可靠,热效率高,无 废气收尘处理;但是冷却机内高温熟料不能骤冷, 熟料出冷却机温度较高,热散失较大,不适用大型 窑的配套使用。 结构:
第一节 水泥熟料的形成过程和煅烧设备的分类
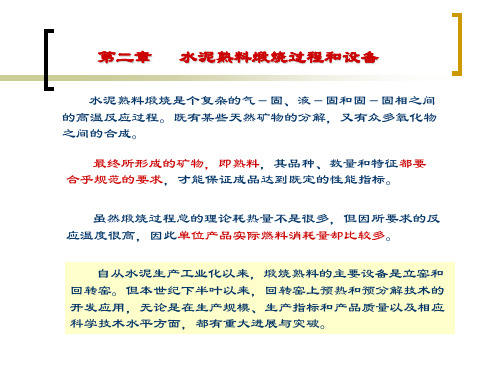
PCO2环境
—环境介质中CO2分压,包括分解产生的CO2和 燃气中CO2之和,Pa。
4、影响碳酸钙分解因素的讨论:
上式很明确表达了影响碳酸钙分解的诸因素及其 相互联系。 根据粗略估算:反应温度每升高10℃,反应时间可 缩短50%; 环境中CO2分压每降低2%,反应时间可缩短10%。 颗粒的粗细,愈细,分解愈快。 其他因素略。
3、碳酸钙分解反应的动力学关系 碳酸钙分解反应的动力学表达式,根据A · lle Mü 大量试验结果,将温度、粒度尺寸及环境条件考虑在 内,有如下实用关系:
1 1 e0 A e
1 3
E RT
1 1 1 PCO2 eq PCO2环境 d p / 2
(3)伊利石脱水 产物也是晶体结构,伴随体积膨胀
二、碳酸盐分解反应机制
1、碳酸盐分解反应 碳酸盐的分解主要为碳酸钙和碳酸镁的分解,其 化学反应式为:
碳酸盐(主要是碳酸钙、少量碳酸镁)的分解反 应是典型的缩核型强吸热的气固相反应。
CaCO3
2、石灰石颗粒的分解机制
分解过程分五步进行:
CaO
(1)气流向颗粒表面的传热过程; (2)热量由表面以热传导方式向分解面传递过程; (3)碳酸盐在一定温度下吸收热量,进行分解并放出 CO2的化学过程; (4)分解出的CO2,穿过CaO层面向表面扩散的传质 过程; (5)表面的CO2向周围介质气流扩散过程
900~1200℃
1250~1280℃ 1280~1450℃ 1450~1300℃
生料的干燥与脱水
干燥 自由水的蒸发。这一过程由于煅烧方式的不同而有 所差异。干法窑生料含水量一般不超过1.0%;半干法立 波尔窑和立窑为便于生料成球,通常含水12-15%,半湿 法立波尔窑过滤水分后的料块通常为18-22%;湿法为保 证料浆的可泵性则通常为30-40%。 自由水蒸发热耗: 100℃时,2257kJ/kgH2O(539kCal/kg)
水泥熟料的形成过程
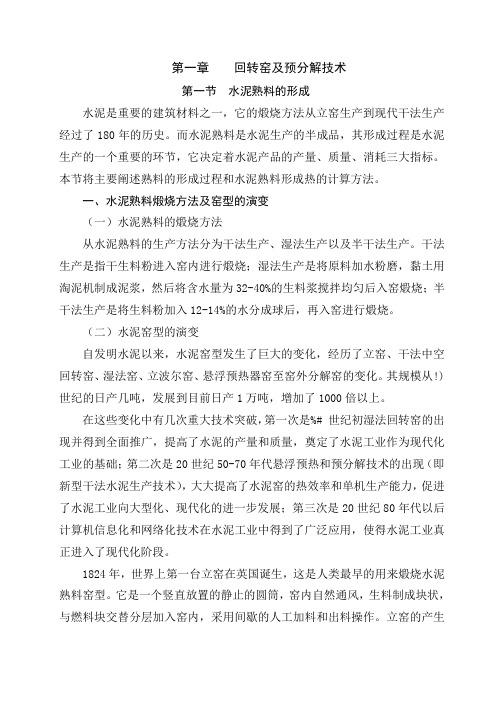
第一章回转窑及预分解技术第一节水泥熟料的形成水泥是重要的建筑材料之一,它的煅烧方法从立窑生产到现代干法生产经过了180年的历史。
而水泥熟料是水泥生产的半成品,其形成过程是水泥生产的一个重要的环节,它决定着水泥产品的产量、质量、消耗三大指标。
本节将主要阐述熟料的形成过程和水泥熟料形成热的计算方法。
一、水泥熟料煅烧方法及窑型的演变(一)水泥熟料的煅烧方法从水泥熟料的生产方法分为干法生产、湿法生产以及半干法生产。
干法生产是指干生料粉进入窑内进行煅烧;湿法生产是将原料加水粉磨,黏土用淘泥机制成泥浆,然后将含水量为32-40%的生料浆搅拌均匀后入窑煅烧;半干法生产是将生料粉加入12-14%的水分成球后,再入窑进行煅烧。
(二)水泥窑型的演变自发明水泥以来,水泥窑型发生了巨大的变化,经历了立窑、干法中空回转窑、湿法窑、立波尔窑、悬浮预热器窑至窑外分解窑的变化。
其规模从!) 世纪的日产几吨,发展到目前日产1万吨,增加了1000倍以上。
在这些变化中有几次重大技术突破,第一次是%# 世纪初湿法回转窑的出现并得到全面推广,提高了水泥的产量和质量,奠定了水泥工业作为现代化工业的基础;第二次是20世纪50-70年代悬浮预热和预分解技术的出现(即新型干法水泥生产技术),大大提高了水泥窑的热效率和单机生产能力,促进了水泥工业向大型化、现代化的进一步发展;第三次是20世纪80年代以后计算机信息化和网络化技术在水泥工业中得到了广泛应用,使得水泥工业真正进入了现代化阶段。
1824年,世界上第一台立窑在英国诞生,这是人类最早的用来煅烧水泥熟料窑型。
它是一个竖直放置的静止的圆筒,窑内自然通风,生料制成块状,与燃料块交替分层加入窑内,采用间歇的人工加料和出料操作。
立窑的产生揭开了水泥工业窑的历史。
1877年出现了回转窑,它是一个倾斜卧着的回转圆筒,生料粉由高端加入,低端有燃料燃烧,物料一方面运动一方面被煅烧。
这便是最早的干法回转窑生产(见图1-1)图1-1 回转窑的最初形式在干法回转窑的生产中,由于初期的回转窑窑体较短,出窑废气的温度较高,热耗较高,随后出现了干法长窑,即干法中空窑,以及带预热锅炉的回转窑。
精品课件--水泥熟料煅烧及设备
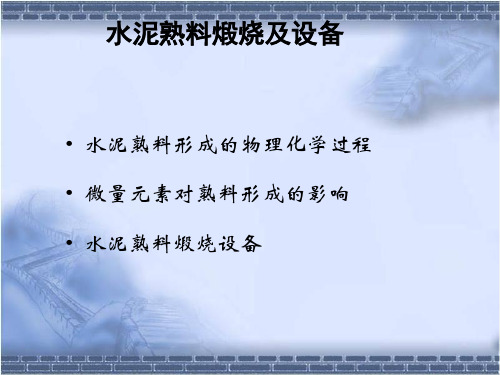
2)化学反应
最易和硫反应形成硫酸盐:
K2O+SO3
K2SO4
Na2O+SO3
Na2SO4 钾钠芒硝
3K2O+Na2O+4SO3
3K2SO4 Na2SO4
(氧化气氛)
K2O+CaO+SO3
2CaSO4 K2SO4
(还原气氛)
钙明矾石
剩余的碱置换熟料矿物
30-40%。
• 对于湿法生产,降低水分是节能关键
(2)预热----粘土脱水分解
• 脱水反应: Al2O3·2SiO2·2H2O → Al2O3·2SiO2(偏高岭石) + 2H2O Al2O3·2SiO2→ Al2O3 + 2SiO2 • 粘土矿物的化合水: ①晶体配位水:以OH-离子状态存在晶体结构中,400-600℃
大小; • 5)生料分散程度:分解炉中完成90%分解仅需 2秒,回
转窑内分解15分钟; • 6)矿化剂的影响。
(4)固相反应
反应历程: • 800℃: CA、CF、C2S 开始形成 • 800~900℃:C12A7 开始形成 • 900~1100℃:C3A、C4AF开始形成; • 1100~1200℃:大量形成C3A、C4AF,C2S达到最
3)钡、锶、钒、硼等元素的存在,有利于熟料煅烧和矿物 形成,不同程度的起到矿化、助熔、稳定β-C2S和活化矿 物的作用。
3.3 水泥熟料煅烧设备
回转窑系统流程 (1)窑中系统:回转窑筒体 (2)窑尾系统:喂料系统、烟室、预热器、分解炉、
增湿塔、排风机、收尘器、余热发电系统、烟囱. (3)窑头系统:窑罩、喷煤管、鼓风机、喂煤系统、
C3A·3CS·H32+2C4AH13=3(C3A·CS·H12)+2CH+20H C3A·CS·H12称单硫型硫铝酸钙,以AFm表示。 d)AFt全部转变为AFm后,若还有C3A,则形成C4AH13和AFm的固溶体: C3A·CS·H12+C3A+CH+12H=2 C3A(CS,CH)H12
11水泥熟料形成过程及煅烧设备的分类
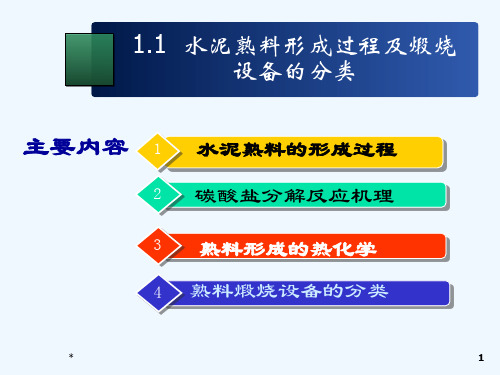
➢ 2 生料的脱水(预热带)
(1)高岭石脱水
CaCO3 CaOCO2165kJkg1(890C)
(2)蒙脱石脱水
MgCO MgOCO1420124kJkg(560~650C) Al2O3.4SiO2.m H2O→Al2O3.4SiO2+m H2O (晶体结构—活性低)
1
(3)伊利石脱水
32
晶体结构,伴随体积膨胀
➢ 机体散热多 ➢不完全燃烧热损失高 ➢系统漏风严重 ➢废气带走的热较多
*
返回 115
国内外不同窑型的热耗、热效率
项目
理论热耗
湿法长窑
干法长窑
热耗 热效 热耗 热效率 (kj/kg) 率(%) (kj/kg) (%)
1756 28.99 1756 44.07
半干法 热耗 (kj/kg)
1756
预热器窑 热效 热耗 热效 率 (%) (kj/kg) 率(%)
形成液相 硅酸三钙形成
吸热 105kJ/kg 熟料 微吸热 8.6kJ/kg-C3S
*
114
1.1.3 熟料矿物形成的热化学
2、熟料的形成热仅与矿物的组成有关。
熟料矿物的形成热(理论热耗)1675--1755 Kj/kg ;
实际热耗:目前 > 2900Kj/kg
思考:为什么实际热耗>理论热耗?
造成热耗高的原因:
C3A、C4AF,f-CaO最大。
1100--1200℃,大量形成C3A和C4AF,C2S达到最大值。
特 点:多级反应;放热反应。
反应产物:C2S、C3A、C4AF
*
7
1.1.1 水泥熟料的形成过程
5、1250 ~1280℃,有液相形成
主要由C3A、C4AF、少量的mgo、Na2O、K2O组 成。
水泥熟料的形成过程原料
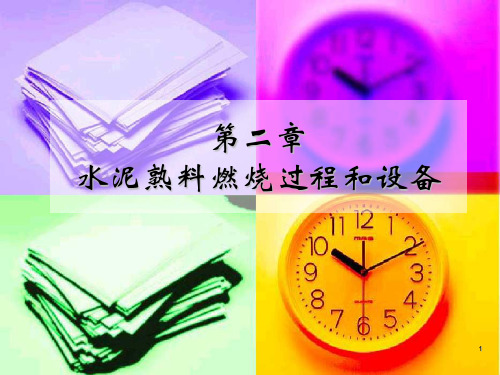
29
回转窑
生产能力高(10000吨/日) 操作较稳定,熟料质量好,劳动生产率高 投资大,钢材消耗多,建设周期较长
30
水泥技术的发展
立窑 湿法生产 60年代初期,预均化技术,流态化 1951,1971出现悬浮预热器和分解炉 沸腾床(不成熟)
31
水泥窑类型特征及主要工业指标
C2S+L(CaO) →C3S
熟料的理论热耗(1675~1755 kJ/kgsh )
固相反应矿物形成总放热量估算
1 (C3 S 465 C2 S 610 C3 A 88 C4 AF 105)KJ / Kg熟料 100 熟料中各成分百分含量
Q矿物放热
生产1kg熟料所需理论热耗经验公式: - 21.40SiO2sh -2.47Fe2O3sh(kJ/kgsh)
窑型 分类 所带附属设备 长径 单位熟料热耗q 比L/D kJ/kg熟料 单机生产能力 (大型)t/日
回 转 窑
湿法长窑:带内 30-38 部热交换装置如 链条,格子式热 交换器 湿法回转窑 湿法窑:带外部 热交换装置,如 18-30 料浆蒸发机、压 滤机、料浆干燥 机
干法回转窑 半干法窑
5300-6800
(lg(2x ))
CaC03分解反应的动力学表达式
考察温度、粒径、环境1 (来自 eo ) A1 3
EK RT
[
1 PCO2 eq
1 ] PCO2 环境 d p / 2
工业上:eo≧95%或1min: △eo<0.2%视为分解完全
1
eo CaCO3分解率 % A 反应的频率因子 3.05106 Pa m / s E 反应活化能 171.850J / m ol K R 气体常数 8.314J / m ol K T 反应温度℃ d p 颗粒直径 m
水泥沸腾煅烧 窑炉

水泥沸腾煅烧窑炉1. 简介水泥沸腾煅烧窑炉是水泥生产过程中的重要设备,用于将原料中的石灰石和粘土等成分在高温下进行煅烧反应,产生水泥熟料。
本文将详细介绍水泥沸腾煅烧窑炉的工作原理、结构和运行过程。
2. 工作原理水泥沸腾煅烧窑炉采用干法生产水泥,其工作原理主要包括以下几个步骤:2.1 原料进料与预热原料(石灰石、粘土等)通过输送系统进入窑炉的上部,同时在窑炉中预热。
预热过程主要是利用窑炉底部高温燃烧的煤粉热量,使原料中的水分和有机物挥发出来,提高煅烧效率。
2.2 煅烧反应经过预热的原料从窑炉上部进入煅烧区域,此时窑炉内的温度可达到1400℃以上。
在高温下,原料中的石灰石和粘土发生化学反应,生成水泥熟料。
这个过程被称为煅烧反应,是水泥生产的关键步骤。
2.3 冷却与熟料处理煅烧后的水泥熟料从窑炉下部排出,进入冷却器进行快速冷却。
在冷却器中,水泥熟料与冷却风进行热交换,降低温度。
冷却后的水泥熟料被送入熟料磨进行细磨,最终成为水泥产品。
3. 结构水泥沸腾煅烧窑炉主要由以下几个部分组成:3.1 窑筒窑筒是窑炉的主体部分,呈长圆筒形。
窑筒内部分为多个不同温度区域,包括预热区、煅烧区和冷却区等。
窑筒由高温耐火材料构成,能够承受高温和化学侵蚀。
3.2 燃烧系统燃烧系统包括煤粉燃烧器、燃烧风机和煤粉输送系统等。
煤粉燃烧器将煤粉与空气混合后喷入窑炉底部,通过燃烧产生高温热量。
燃烧风机提供燃烧所需的氧气,并将烟气排出窑炉。
3.3 冷却系统冷却系统包括冷却器和冷却风机等。
冷却器是窑炉下部的一个装置,通过冷却风和水泥熟料之间的热交换,将熟料快速冷却至适宜的温度。
3.4 输送系统输送系统用于将原料和水泥熟料从窑炉的上部和下部输送到相应的位置。
输送系统通常由皮带输送机、斗式提升机和螺旋输送机等组成。
4. 运行过程水泥沸腾煅烧窑炉的运行过程主要包括以下几个步骤:4.1 点火与预热在窑炉启动前,需要进行点火工作。
点火后,燃烧器喷入煤粉并点燃,产生高温热量。
煅烧基本原理和工艺设备
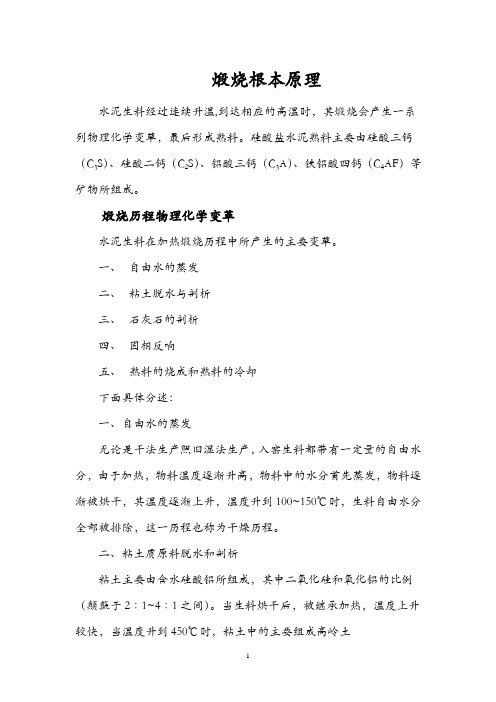
煅烧根本原理水泥生料经过连续升温,到达相应的高温时,其煅烧会产生一系列物理化学变革,最后形成熟料。
硅酸盐水泥熟料主要由硅酸三钙(C3S)、硅酸二钙(C2S)、铝酸三钙(C3A)、铁铝酸四钙(C4AF)等矿物所组成。
煅烧历程物理化学变革水泥生料在加热煅烧历程中所产生的主要变革。
一、自由水的蒸发二、粘土脱水与剖析三、石灰石的剖析四、固相反响五、熟料的烧成和熟料的冷却下面具体分述:一、自由水的蒸发无论是干法生产照旧湿法生产,入窑生料都带有一定量的自由水分,由于加热,物料温度逐渐升高,物料中的水分首先蒸发,物料逐渐被烘干,其温度逐渐上升,温度升到100~150℃时,生料自由水分全部被排除,这一历程也称为干燥历程。
二、粘土质原料脱水和剖析粘土主要由含水硅酸铝所组成,其中二氧化硅和氧化铝的比例(颠簸于2∶1~4∶1之间)。
当生料烘干后,被继承加热,温度上升较快,当温度升到450℃时,粘土中的主要组成高岭土(Al2O3·2SiO2·2H2O)失去结构水,变为偏高岭石(2SiO2·Al2O3)。
Al2O3·2SiO2·2H2O →Al2O3+2SiO2+2H2O↑(无定形) (无定形)高岭土进行脱水剖析反响时,在失去化学结合水的同时,自己结构也受到破坏,酿成游离的无定形的三氧化二铝和二氧化硅。
其具有较高的化学活性,为下一步与氧化钙反响创造了有利条件。
在900℃~950℃,由无定形物质转变为晶体,同时放出热量。
三、石灰石的剖析脱水后的物料,温度继承升至600℃以上时,生料中的碳酸盐开始剖析,主要是石灰石中的碳酸钙和原料中混合的碳酸镁进行剖析,并放出二氧化碳,其反响式如下:600℃MgCO3 → MgO+CO2↑900℃CaCO3→ CaO+CO2↑实验表明:碳酸钙和碳酸镁的剖析速度随着温度升高而加快,在600℃~700℃时碳酸镁已开始剖析,加热到750℃剖析剧烈进行。
- 1、下载文档前请自行甄别文档内容的完整性,平台不提供额外的编辑、内容补充、找答案等附加服务。
- 2、"仅部分预览"的文档,不可在线预览部分如存在完整性等问题,可反馈申请退款(可完整预览的文档不适用该条件!)。
- 3、如文档侵犯您的权益,请联系客服反馈,我们会尽快为您处理(人工客服工作时间:9:00-18:30)。
缩核型强吸热气固反应; 烧失量大.
问题二:影响碳酸盐分解速度的因素?
7
影响碳酸盐分解速度的因素?
石灰质原料的活性和物理性质;结构致密,结晶粗大的 石灰石,分解速率慢;
生料中粘土质组分的性质:粘土质中的矿物组分的活 性依次按高岭土、蒙脱石、伊利石、石英降低.粘土质 原料活性越大,可加速碳酸盐的分解过程.
吸热 1420kJ/kg-MgCO3 放热 260 ~ 285kJ/kg 脱水 高岭土 吸热 1655kJ/kg-CaCO3 放热 420~500kJ/kg 熟料
吸热 105kJ/kg 熟料 微吸热 8.6kJ/kg-C3S 13
2、碳酸盐分解反应机理
按B .福斯滕观点分五步:
(1)气流向颗粒表面的传热过程; (2)热量由表面以热传导方式向分 解面传递过程; (3)碳酸盐在一定温度下吸收热量, 进行分解并放出CO2的化学过程; (4)分解出的CO2,穿过CaO层面 向表面扩散的传质过程; (5)表面的CO2向周围介质气流扩 散过程
新型干法水泥回转窑系统
1.1、系统概述
• 1.1.1 水泥熟料形成过程及煅烧设备分类 • 1.1.2 回转窑煅烧系统 • 1.1.3 新型干法水泥回转窑系统的几个重要
性能指标
1.1.1 水泥熟料形成过程及煅烧 设备分类
要求:
• 理解水泥熟料的形成过程,重点掌握影响 碳酸盐分解反应的因素。
• 理解熟料矿物形成的热化学。 重点:
熟料矿物的形成热(理论热耗)1675--1755 Kj/kg
14:25:09
4、水泥熟料煅烧设备的分类(了解)
1、按生料的制备方法分:
干法-制备料粉; 湿法-制备成料浆(含水30-40%); 半干法-制备成料球(含水12-14%). • 2、按窑型分:
回转窑(干法窑、半干法窑、湿法窑) 立窑(煅烧料球)
②反应式:C2S(液)+CaO(液)
C3S(固)
③哪些因素影响水泥熟料的烧成?
最低共熔温度
液相量和液相粘度
煅烧温度和烧成时间。
14:25:09
11
(7)水泥熟料冷却阶段:(T<1300℃)(冷却带)
C3S的形成终止。
水泥熟料的矿物组成: C3S 、 C2S、 C3A、C4A
水泥熟料烧成每个阶段需要的温度 和热效应不同,如下表:
(2)蒙脱石脱水 Al2O3.4SiO2.m H2O→Al2O3.4SiO2+m H2O (晶体结构—活性低)
(3)伊利石脱水 晶体结构,伴随体积膨胀
6
(3)碳酸盐分解阶段(600℃-900 ℃)
CaCO3 CaO CO2 1655kJ .kg1(890C ) MgCO3 MgO CO2 1420 ~ 1214kJ .kg1(560 ~ 650C )
14:25:09
9
(5)1250 ~1280℃,有液相形成
主要由C3A、C4AF、少量的mgo、Na2O、 K2O组成。
900~1300℃主要承担固相反应任务,为放热 反应,称为固相反应带。
14:25:09
10
(6)水泥熟料烧成阶段(烧成带)
①条件:温度:1300℃~1450℃~1300℃
液相量: 20% ~ 30%
14:25:09
12
温度和热效应
温度(℃)
100 450 600 900
900 900 ~ 1200 1250 ~ 1280
130014~:251:049 50~1300
反应
游离水蒸发 粘土结合水逸出
碳酸镁分解 粘土中无定形物
结晶 碳酸钙分解 固相反应
形成液相 硅酸三钙形成
相应温度下1吨物料的热变 化 吸热 2250kJ/kg 水 吸热 932kJ/kg 高岭土
14:25:09
16
思考题:
1、熟料在回转窑内经历了哪些物理化学变化? 2、以湿法窑为例说明窑内各反应带的划分? 3、窑外分解窑的工艺流程?有何优点? 4、回转窑内为何要加强通风? 5、影响碳酸盐反应的因素有哪些? 6、窑外分解水泥回转窑与普通回转窑相比有哪些不
• --800℃,开始形成CA,C2F,C2S • 800 ℃--900℃,开始形成C12A7 • 900 ℃--1000℃时形成C2AS并接着分解,开始形成
C3A、C4AF,f-CaO最大。 • 1100--1200℃,大量形成C3A和C4AF,C2S达到最大值。
特 点:多级反应;放热反应。 反应产物:C2S、C3A、C4AF
掌握水泥熟料煅烧过程; 掌握碳酸盐分解机理及影响因素。
14:25:09
1、水泥熟料的形成过程
回顾水泥熟料生产的工艺流程?
石灰质原料、 粘士质原料 少量的铁质原料
按一定要求的 比例配合
1450℃
生料
熟料
经均化、 粉磨、调 配而成。
发生了什么变化?
14:25:09
1、水泥熟料的形成过程
(1) 生料的干燥(干燥带) (2 )生料的脱水(预热带) (3)碳酸盐分解阶段(600℃-900 ℃) (4)固相反应过程 (5)1250 ~1280℃,有液相形成 (6)水泥熟料烧成阶段(烧成带) (7)水泥熟料冷却阶段:(T<1300℃)
4
(1) 生料的干燥(干燥带)
➢ 干燥阶段(水分的蒸发~100~150℃)
自由水的蒸发。耗热:100℃时,2250kJ/kgH2O
这一过程由于煅烧方式的不同而有所差异。 干法窑生料含水量一般不超过1.0%;
14:25:09
5
(2)生料的脱水(预热带)
(1)高岭石脱水
Al2O3 2SiO2 2H2O Al2O3 2SiO2 2H2O
14:25:09
热量
CaCO3 CaO
CO2
3、熟料矿物形成的热化学
(1)、什么是熟料矿物的形成热? 指生料在加热过程中发生了一系列物理 化学变化,将全过程的总吸热量减去总 放热量,由0℃的干生料在没有任何热 量损失和物料损失的情况下,烧成1Kg 熟料所需的净热量。
(2)、熟料的形成热仅与矿物的组成有关。
生料细度和颗粒级配:生料细度细,颗粒均匀,粗粒少, 分解速率快;
生料悬浮分散程度:生料悬浮分散良好, 增大了传热面 积,提高了碳酸盐分解速率;
窑系统的CO2分压:通风良好, CO2分压较低,有利于碳 酸盐分解。
温度14:2随5:09温度升高,分解时间缩短;分解率提高。 8
(4)、固相反应过程