总装车间现场技术管理与技术支持分析
技术支持工作总结汇报

技术支持工作总结汇报
尊敬的领导和同事们:
在过去的一段时间里,我有幸担任技术支持工作,为公司的发
展和客户的满意度做出了一些贡献。
现在我将对这段时间的工作进
行总结汇报,希望能够得到大家的认可和建议。
首先,我在技术支持工作中主要承担了以下几个方面的工作,
一是及时响应客户的技术问题,提供解决方案和支持;二是协助销
售团队进行产品演示和技术支持;三是参与产品的测试和改进工作;四是不断学习和提升自己的技术水平,以更好地服务客户和公司。
在这段时间里,我成功解决了许多客户的技术问题,得到了客
户的好评和信任。
我也积极参与了销售团队的产品演示和技术支持
工作,帮助他们更好地向客户展示产品的优势和特点。
同时,我也
在产品测试和改进方面发挥了一定的作用,为产品的质量和性能提
供了一些有益的建议和意见。
在工作中,我也不断学习和提升自己的技术水平,通过参加培
训和自学,我不断地充实自己的知识储备,以更好地适应公司的发
展和客户的需求。
在这个过程中,我也遇到了一些困难和挑战,但我始终坚持学习和努力,取得了一些进步和成就。
总的来说,我在技术支持工作中取得了一些成绩,但也存在一些不足和问题。
在今后的工作中,我将继续努力,不断提升自己的技术水平和服务能力,为公司的发展和客户的满意度做出更大的贡献。
谢谢大家的支持和关注!
技术支持人员,XXX。
日期,XXXX年XX月XX日。
技术支持部门技术支持与故障处理工作总结
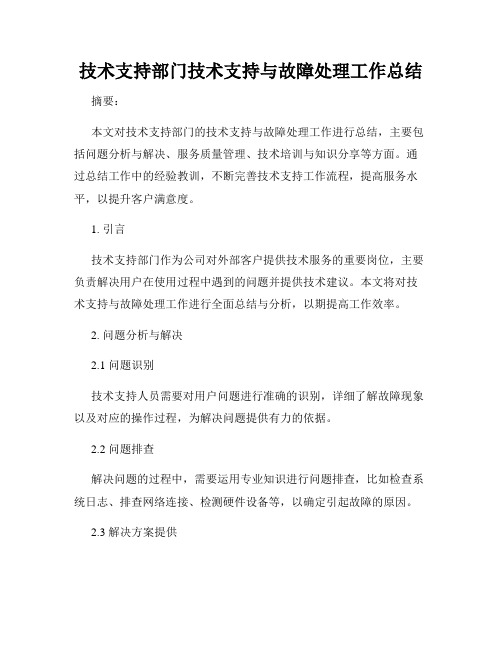
技术支持部门技术支持与故障处理工作总结摘要:本文对技术支持部门的技术支持与故障处理工作进行总结,主要包括问题分析与解决、服务质量管理、技术培训与知识分享等方面。
通过总结工作中的经验教训,不断完善技术支持工作流程,提高服务水平,以提升客户满意度。
1. 引言技术支持部门作为公司对外部客户提供技术服务的重要岗位,主要负责解决用户在使用过程中遇到的问题并提供技术建议。
本文将对技术支持与故障处理工作进行全面总结与分析,以期提高工作效率。
2. 问题分析与解决2.1 问题识别技术支持人员需要对用户问题进行准确的识别,详细了解故障现象以及对应的操作过程,为解决问题提供有力的依据。
2.2 问题排查解决问题的过程中,需要运用专业知识进行问题排查,比如检查系统日志、排查网络连接、检测硬件设备等,以确定引起故障的原因。
2.3 解决方案提供在问题排查的基础上,技术支持人员应提供有效的解决方案,可以是针对具体问题的操作指导,也可以是关键问题的修复程序。
2.4 效果验证提供解决方案后,技术支持人员应引导用户验证解决效果,并确保问题得到圆满解决。
3. 服务质量管理3.1 响应时间技术支持部门应设定合理的响应时间目标,及时响应用户提出的问题,在规定时间内给予答复或解决方案。
3.2 服务态度技术支持人员应积极、友好地与用户沟通,倾听用户需求,尽力满足用户的要求,展现专业素养。
3.3 问题跟进技术支持人员应积极主动地跟进用户的问题,关注问题解决进度,确保问题得到真正解决。
3.4 用户满意度调查定期对用户进行满意度调查,及时听取用户对技术支持工作的建议和意见,制定改进措施,提高服务质量。
4. 技术培训与知识分享4.1 技术培训技术支持部门应制定系统的技术培训计划,不断提升员工的专业技能与知识水平,以适应技术变革的发展。
4.2 知识库建设建立完善的知识库,收集整理常见问题的解决方法和经验,方便技术支持人员查询与使用,提高工作效率。
4.3 知识分享技术支持人员应定期组织知识分享会议,分享工作中的案例经验和解决方案,促进团队成员之间的学习与交流。
总装工厂现场管理制度范文

总装工厂现场管理制度范文总装工厂现场管理制度范一、概述总装工厂是汽车制造过程中的最后一道工序,负责完成车身与发动机、底盘等零部件组装工作。
为了确保总装工艺的质量和安全,有效管理总装工厂现场是非常重要的。
本文旨在制定一套完善的总装工厂现场管理制度,以确保生产过程的顺利进行。
二、组织架构1. 总装工厂现场管理小组总装工厂现场管理小组由总装工厂现场主管、生产线主管、质量控制主管、安全主管等组成。
负责制定总装工厂现场管理制度、监督现场管理的执行情况以及及时处理现场操作中出现的问题。
2. 生产线负责人每条生产线设立一名负责人,负责生产线的日常管理和生产任务的完成。
负责人需要具备丰富的生产管理经验和技能,并与现场管理小组保持密切的沟通和协作。
三、现场管理制度1. 现场安全管理(1)安全设施确保生产现场配备必要的安全设施和装备,包括消防器材、安全标识、紧急出口、安全栏杆等,以提供员工的安全保障。
(2)培训教育定期组织员工进行安全培训,包括安全操作规程、紧急处理措施、事故案例等方面的知识,提升员工的安全意识和应急能力。
(3)安全巡检定期开展安全巡检,检查生产现场的安全隐患并采取相应的措施进行处理,及时发现并排除安全隐患。
2. 现场5S管理(1)定期整理与清洁制定定期清洁计划,定期清理生产线的废料、垃圾和杂物。
保持生产现场的整洁和干净,为员工提供一个良好的工作环境。
(2)标准化管理制定标准化操作规程,明确每个岗位的具体工作内容和工作标准。
对员工进行培训,确保各操作流程按照标准进行。
(3)物品定位为设备、工具和材料设定定位位置,并使用标识牌进行标注,方便员工找到需要的物品,提高工作效率。
(4)安全与卫生建立安全与卫生制度,定期检查设备的安全隐患并及时处理。
组织员工进行定期体检,确保员工的身体健康。
3. 质量控制管理(1)质量检测建立质量检测制度,对产品进行必要的检测和测试。
确保产品的质量符合公司的质量标准。
(2)纠正措施对于因质量问题引发的异常情况,采取相应的纠正措施,及时处理异常产品,防止不良品进入市场。
总装线管理制度

总装线管理制度一、总装线作业管理(一)总装线作业管理的目的是通过科学的管理方式,确保总装线作业的合理组织、高效顺畅,使得产品顺利生产,质量可控可靠,安全可控可靠,节约成本并提高效率。
(二)总装线作业管理应遵守国家法律法规和公司管理政策,按照先进的管理制度进行组织,不断完善和提高总装线作业管理水平。
(三)总装线作业管理应依据生产计划,合理安排作业流程,确保各个工序有序衔接,减少生产中的等待和浪费,提高生产效率。
二、人员管理(一)总装线的人员应经过专业的培训,并且具备相关的证书和资质。
在工作过程中,要严格遵守操作规程,严格执行作业标准,保障生产质量和安全。
(二)生产部门负责总装线的人员配备和班组管理,要合理安排人员配置,根据生产需要灵活调配人员,保障总装线的正常运转。
(三)对于不符合作业标准的人员,应及时进行培训和引导,提高其工作能力和质量意识;对于违反操作规程的人员,应及时纠正和处理,确保生产作业的顺利进行。
三、设备管理(一)总装线设备是保障生产的关键因素,应按照规定定期进行维护和保养,确保设备的正常运转。
(二)对于设备的选型和更新,应根据生产需要和技术发展趋势进行合理选择和安排,在确保生产需求的前提下,控制设备投入成本。
(三)对于设备的故障和维修,应及时进行处理,减少生产中的停机时间,保障生产作业的连续进行。
四、质量管理(一)总装线质量管理应按照ISO9001等管理体系标准,建立和完善质量管理体系,确保产品质量达到国家标准和客户要求。
(二)对于生产过程中产生的废品和次品,应及时进行记录和分析,找出产生问题的原因,并采取有效措施,确保生产质量的稳定。
(三)质量管理应贯穿于整个生产过程,全员参与,全员质量意识,确保每一个岗位和每一项工作都符合质量要求。
五、安全管理(一)总装线安全管理应严格遵守国家相关法律法规,建立和完善安全管理体系,确保生产作业过程中的安全。
(二)对于生产过程中容易发生事故的环节,应加强安全监管和培训,提高员工安全意识和紧急反应能力。
浅谈汽车总装现场问题分析与改进

浅谈汽车总装现场问题分析与改进发表时间:2018-06-19T16:45:17.543Z 来源:《基层建设》2018年第12期作者:齐东亚[导读] 摘要:随着汽车工业和零部件工业的发展,汽车总装技术水平也有了较大的提高,国内对直接影响汽车产品质量及使用寿命和汽车产品生产最后环节的装配及出厂试验日趋重视,促进了汽车产品总装工艺水平的提高。
安徽江淮汽车集团股份有限公司安徽合肥 230000 摘要:随着汽车工业和零部件工业的发展,汽车总装技术水平也有了较大的提高,国内对直接影响汽车产品质量及使用寿命和汽车产品生产最后环节的装配及出厂试验日趋重视,促进了汽车产品总装工艺水平的提高。
本文主要介绍了总装现场问题的定义、分类,以及如何发现问题,如何进行问题的分析,并举例详细的说明了现场问题分析的步骤、方法及解决措施。
关键词:汽车总装;现场问题;问题分析 1、引言1.1 总装、汽车总装的定义、汽车总装现场问题的定义 1.1.1总装的定义:是指在一个基准零件上,装上若干部件、组件、套件和零件就成为整个机器,把零件和部件装配成最终产品的过程,称之为总装。
1.1.2汽车总装的定义:是将产品从研发阶段转化为实际生产的过程,也就是将研发部门设计的众多零件通过一系列操作,使其在数量和外观方面发生变化的生产过程。
数量的变化是指在装配过程中,总成、分总成和零部件的数量不断增加并相互有序地结合起来;外观的变化表现为各零部件之间有序结合并具有一定的相互位置关系,随着零件的增加,外形不断变化,最后形成整车。
1.1.3汽车总装现场问题的定义:是指由于设计问题、零件质量问题等原因,导致汽车的某零部件失去其功能,或存在质量隐患导致后期面临功能丧失故障的现象。
2、如何发现问题2.1 问题的排查车辆结构复杂,要尽量做到不遗漏问题需要循序渐进,按照一定的顺序排查问题;车辆按实现功能的不同可以分为很多的分组装置,如发动机总成、发动机悬置、供油系、进气系等,安装分组装置逐步排查可以避免遗漏问题。
总装工厂现场管理制度范本

第一章总则第一条为加强总装工厂现场管理,提高生产效率,确保产品质量,保障员工安全,特制定本制度。
第二条本制度适用于总装工厂所有生产区域、办公区域及辅助设施。
第三条总装工厂现场管理应遵循“安全第一、预防为主、持续改进”的原则。
第二章安全生产管理第四条员工进入生产区域必须正确佩戴安全帽、工作服、工作鞋,并按要求佩戴防护用品。
第五条生产区域严禁吸烟、使用明火,严禁存放易燃易爆物品。
第六条员工必须遵守操作规程,不得擅自更改生产工艺、操作流程。
第七条设备操作人员必须经过专业培训,取得相应资格证书后方可上岗。
第八条定期对生产设备进行维护保养,确保设备正常运行。
第九条发现安全隐患,应立即报告上级,并采取相应措施消除隐患。
第十条定期组织安全生产教育培训,提高员工安全意识。
第三章生产管理第十一条生产计划应合理制定,确保生产进度和质量。
第十二条员工必须按照生产计划进行生产,不得擅自调整生产任务。
第十三条生产过程中,员工应严格按照工艺规程进行操作,确保产品质量。
第十四条定期对生产过程进行监控,及时发现并解决生产中的问题。
第十五条建立质量追溯体系,确保产品质量可追溯。
第四章物料管理第十六条物料入库、出库必须按照规定程序进行,确保物料数量准确。
第十七条物料存放应分类摆放,标识清晰,便于查找。
第十八条物料领用需填写领料单,经相关部门批准后方可领用。
第十九条废旧物料应及时处理,防止浪费和污染。
第五章环境卫生管理第二十条生产区域、办公区域及辅助设施应保持整洁、卫生。
第二十一条员工应遵守环境卫生规定,不得随意丢弃垃圾。
第二十二条定期对生产区域进行清洁、消毒,确保环境卫生。
第六章奖惩制度第二十三条对严格遵守本制度,表现突出的员工给予奖励。
第二十四条对违反本制度,造成安全事故或质量问题的员工,给予相应处罚。
第七章附则第二十五条本制度由总装工厂负责解释。
第二十六条本制度自发布之日起实施。
(注:本制度范本仅供参考,具体内容可根据实际情况进行调整。
总装车间管理思路

生产装配车间2012年工作管理思路公司新的一年开始,结合公司发展与去年工作中的不足之处,特拟定新一年管理思路,并逐步实施。
1、现场管理车间按照6S管理的要求,持续不断的对现场进行改善和提升。
对车间现场每天定时清理,对物料、工具、工装夹具及时撤离现场,保证现场通道、工作台面整洁、通畅;对所有工装按照产品型号进行刻字标识,并按规定存放,减少浪费,提高效率,并做及时检查,发现问题现场解决。
划分责任区,让现场每一块区域都有具体负责人,减轻现场管理压力;2、生产管理按时完成生产任务:对生产订单根据人员、交期等进行生产分析,合理安排生产。
根据年初生产计划,按照每月6万产量计算,我车间现有人员29人,已经可以完成生产任务。
严格按照生产计划完成生产订单,对缺料及技术、质量等异常及时上报、跟进,合理安排工作进度,对现场实行看板管理方式,每天将生产产量进行看板更新,对产品质量异常产品及时反馈;稳定产品质量,提高成品率:实现无大批量产品报废,降低产品次品率和报废率。
我车间去年全年叶轮泵合格率为:94.57%,齿轮泵合格率为:89.31%,今年拟定计划为:叶轮泵合格率提高到:96%,齿轮泵合格率提高到:95%,主要措施:1、严格按照生产作业指导书操作,2、加强员工对质量检查的培训,牢记产品检查的重点、要点; 4、增加产品生产前的试装工序,每批试装20只,减少批量问题,保障产品的质量。
5、对重要岗位进行技能、质量培训,提高技能与质量意识。
各部门间工作的配合:对新产品的试制工作积极配合,根据拟定的试制计划完成,将试制计划当做生产任务完成,并根据多年工作经验帮助其技术员分析问题,提高开发效率;质量问题配合品质部对投诉产品做质量分析,结合工序、人员、技术等环节,提出改善措施,对生产环节试装产品配合检验员完成首件确认;3、设备管理对生产现场所有设备进行定期检查,每天要求操作人员对设备点检表如实记录,对漏油、漏水、漏气设备及时申请上报维修,定时保养,对设备操作进行岗位培训,减少因误操作引起的设备损坏。
总装车间现场改善方法

隐患。
成本高昂
由于设备维护、人力成本等方 面的投入较大,总装车间的生
产成本可能较高。
02
现场改善方法
5S管理
整顿
对物品进行分类、标识和定位, 方便取用和归位。
清洁
维护和检查设备,确保其正常 运转。
整理
区分必需品和非必需品,清理 非必需品,保持工作区域整洁。
成品下线
总装车间完成汽车产品 组装后,进行最终的质 量检测和调试,合格后
下线。
总装车间存在的问题与挑战
01
02
03
04
生产效率低下
由于设备老化、工艺流程不合 理等原因,总装车间的生产效
率可能较低。
质量不稳定
由于零部件质量不均、操作人 员技能水平不高等原因,总装 车间的产品质量可能不稳定。
安全隐患多
案例一:生产线布局优化
实施步骤 1. 对现有生产线布局进行详细分析,找出存在的问题和瓶颈。
2. 根据产品特性和工艺流程,制定合理的生产线布局方案。
案例一:生产线布局优化
3. 对新方案进行模拟和验证,确保方案的可行性和有效性。
4. 实施新的生产线布局方案,并对实施效果进行跟踪和评估 。
案例二:作业流程改进
清扫
定期清扫设备和现场,保持干 净整洁。
素养
遵守规章制度,养成良好的工 作习惯。
目视化管理
标识明确
使用明显的标识和标签,方便员工快速识别。
图表展示
使用图表、看板等工具,实时展示生产进度、 质量等信息。
颜色管理
采用不同颜色进行时监控现场情况,提高管 理效率。
总结词
通过优化作业流程,减少生产中的浪 费和等待时间。
整车厂总装车间日常管理参数

整车厂总装车间日常管理参数1. 引言整车厂总装车间是汽车制造过程中的关键环节之一,负责将各个部件进行组装和安装,完成整车的制造。
为了保证生产顺利进行,并达到高质量、高效率的要求,必须建立日常管理参数体系,对车间进行全面的管理。
本文将从以下几个方面详细介绍整车厂总装车间日常管理参数的制定与实施。
2. 重要参数2.1 产能指标产能指标是衡量整车厂总装车间生产能力的重要参数之一。
它包括每日生产车辆的数量、车间的产能利用率、生产周期等关键指标。
车间管理者需要根据厂商要求和市场需求,制定合理的产能指标,并进行动态监控和调整,以确保生产能够按时、按量完成。
2.2 质量指标质量是整车厂总装车间工作的核心。
质量指标包括产品出厂合格率、返工率、质量事故率等。
车间管理者需要制定严格的质量标准,并确保车间生产过程的每个环节都符合这些标准。
同时,还需要建立完善的质量管理体系,包括质量监控、质量检测、质量问题处理等,以提高产品质量,降低质量风险。
2.3 成本指标成本是企业经营的核心之一,也是整车厂总装车间日常管理的重要内容。
成本指标包括直接人工成本、能源消耗成本、物料成本等。
车间管理者需要通过优化生产工艺、降低生产成本、提高生产效率等手段,控制好成本指标,以提高企业的盈利能力。
2.4 安全指标安全是整车厂总装车间工作的首要考虑因素。
安全指标包括安全事故率、员工消防安全培训合格率、车间安全设施运行状态等。
车间管理者需要建立安全管理体系,制定安全操作规程和应急预案,加强安全培训和宣传,提高员工的安全意识,确保车间工作环境的安全性。
3. 参数制定与实施3.1 参数制定车间管理者需要根据企业的实际情况,结合行业标准和政府法规,制定适合整车厂总装车间的管理参数。
参数的制定需要考虑车间的规模、设备水平、人员组织结构等因素,确保参数的科学性和可操作性。
此外,还需要与各个相关部门进行充分的沟通与协调,确保参数制定的合理性与一致性。
3.2 参数实施参数的实施需要全员参与,形成全员共识和合力。
一汽大众奥迪总装车间质量管理问题与对策
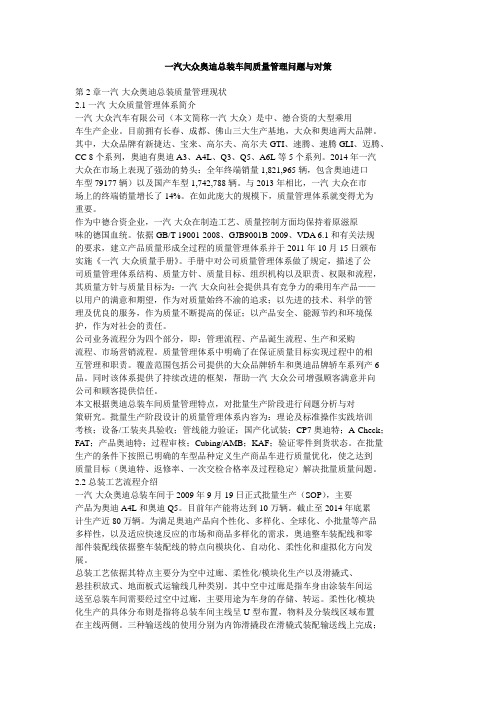
一汽大众奥迪总装车间质量管理问题与对策第2章一汽-大众奥迪总装质量管理现状2.1一汽-大众质量管理体系简介一汽-大众汽车有限公司(本文简称一汽-大众)是中、德合资的大型乘用车生产企业。
目前拥有长春、成都、佛山三大生产基地,大众和奥迪两大品牌。
其中,大众品牌有新捷达、宝来、高尔夫、高尔夫GTI、速腾、速腾GLI、迈腾、CC 8个系列,奥迪有奥迪A3、A4L、Q3、Q5、A6L等5个系列。
2014年一汽- 大众在市场上表现了强劲的势头:全年终端销量1,821,965辆,包含奥迪进口车型79177辆)以及国产车型1,742,788辆。
与2013年相比,一汽-大众在市场上的终端销量增长了14%。
在如此庞大的规模下,质量管理体系就变得尤为重要。
作为中德合资企业,一汽-大众在制造工艺、质量控制方面均保持着原滋原味的德国血统。
依据GB/T 19001-2008、GJB9001B-2009、VDA 6.1和有关法规的要求,建立产品质量形成全过程的质量管理体系并于2011年10月15日颁布实施《一汽-大众质量手册》。
手册中对公司质量管理体系做了规定,描述了公司质量管理体系结构、质量方针、质量目标、组织机构以及职责、权限和流程,其质量方针与质量目标为:一汽-大众向社会提供具有竞争力的乘用车产品——以用户的满意和期望,作为对质量始终不渝的追求;以先进的技术、科学的管理及优良的服务,作为质量不断提高的保证;以产品安全、能源节约和环境保护,作为对社会的责任。
公司业务流程分为四个部分,即:管理流程、产品诞生流程、生产和采购流程、市场营销流程。
质量管理体系中明确了在保证质量目标实现过程中的相互管理和职责。
覆盖范围包括公司提供的大众品牌轿车和奥迪品牌轿车系列产6 品。
同时该体系提供了持续改进的框架,帮助一汽-大众公司增强顾客满意并向公司和顾客提供信任。
本文根据奥迪总装车间质量管理特点,对批量生产阶段进行问题分析与对策研究。
批量生产阶段设计的质量管理体系内容为:理论及标准操作实践培训考核;设备/工装夹具验收;管线能力验证;国产化试装;CP7奥迪特;A-Check;FAT;产品奥迪特;过程审核;Cubing/AMB;KAF;验证零件到货状态。
浅谈生产现场管理Shopfloor Management在总装车间的推广

浅谈生产现场管理Shopfloor Management在总装车间的推广摘要:优化生产车间现场管理是企业的重要任务之一,也是企业经营管理取得成功的基础保证。
本文以一汽-大众长春基地整车制造二部总装二车间为例,对该车间生产现场管理做了详细的调查,引入SFM管理模块,开展人员培训、试点运行、推广车间,总结了生产现场管理的相关经验。
关键词:生产现场管理,Shopfloor Management,SFM引言:汽车制造行业是国民经济中重要的组成部分,它与人们的生产、生活密切相关,是经济和社会发展水平的重要体现。
2019年,我国汽车产量达到了2572.1万辆,销量达2576.9万辆,产销量蝉联全球第一,汽车保有量已达2.6亿辆,可以说是名副其实的汽车大国。
虽然我国的汽车业有如此辉煌的成就,但是与欧、美、日发达国家的先进生产管理模式相比,我国的汽车制造业的生产现场管理方式还是相对落后,主要表现为生产技术积累不足、现场管理混乱、品质稳定性差、能源效率不高、环境污染严重等。
这些问题已经严重制约了我国汽车制造企业的管理水平的提高,阻碍了汽车行业的进一步发展。
一汽-大众公司是德国大众集团世界工厂的重要组成部分,是我国汽车制造业的龙头企业。
其中长春基地整车制造二部建厂17年,生产过开迪、新宝来、速腾、迈腾、高尔夫、高尔夫GTI、CC和奥迪Q3等多种车型,有非常丰富的生产管理经验,但是在生产现场管理方面仍然存在一些欠缺。
全球所有的大众集团生产工厂都在积极推行康采恩生产体系(KPS),其中SFM现场管理是其中一个重要的组成模块。
一、Shopfloor Management理念SFM是一种较为先进的生产现场管理方法,它使生产过程遇到的问题都暴露出来,不仅让生产第一线的员工积极加入到解决问题的团队中,同时也促使其它职能部门围绕生产提供及时和准确的支持,从而形成一种解决问题的文化和氛围。
1.2.1.1激发班长主观能动性在汽车生产车间内,班长、工长和主管是生产管理中三个重要的管理层级,如果他们不能很好的沟通合作,而只是期望着的班长解决所有的现场问题,只会让班长疲于应对而问题不会得到解决。
工厂日常管理的技术支持和技术手段

案例三:设备预防性维护系统
要点一
总结词
要点二
详细描述
设备预防性维护系统可以实时监控设备运行状态,预测设 备故障,及时进行维修,提高设备利用率。
设备预防性维护系统基于物联网和大数据技术,可以实时 监控设备的运行状态、温度、压力等参数,通过数据分析 预测设备故障发生的可能性,及时进行维修,从而提高设 备利用率,减少设备故障对生产的影响。
工业互联网
工业互联网是将物理世界与数 字世界相连接,实现生产过程 的智能化和互联互通。
物联网(IoT)
物联网是指通过互联网对物品 进行远程信息传输和智能化管 理的网络,应用于工厂日常管 理中可以实现生产过程的可视 化、远程监控等。
IIoT应用场景
工业互联网与物联网的结合应 用可以实现工厂的智能化生产 和管理,包括设备监测与维护 、生产计划与调度、质量控制 等。
80%
传感器技术
传感器用于监测和测量生产过程 中的各种参数,如温度、压力、 位置、速度等。
100%
数据采集与监控
通过传感器采集数据,并实时监 控生产过程,有助于及时发现和 解决问题,提高生产效率。
80%
数据处理与分析
采集到的数据可以通过数据处理 和分析技术,提取有价值的信息 ,为决策提供支持。
工业互联网与物联网(IIoT)
工厂日常管理的技术支持和技 术手段
汇报人:
2023-12-05
目
CONTENCT
录
• 工厂日常管理概述 • 工厂日常管理的技术支持 • 工厂日常管理的技术手段 • 工厂日常管理技术手段的应用案例 • 工厂日常管理技术的挑战与解决方
案 • 未来工厂日常管理技术的发展趋势
01
工厂日常管理概述
装配式建筑施工过程中的设备与技术支持

装配式建筑施工过程中的设备与技术支持随着现代科技的不断发展,装配式建筑在建筑行业中得到了广泛应用。
由于其快速、高效、环保等优势,越来越多的人开始关注和选择使用装配式建筑作为解决方案。
在装配式建筑施工过程中,设备与技术支持扮演着重要角色,本文将通过分析,介绍装配式建筑施工过程中设备与技术支持的具体内容和重要性。
一. 设备支持1. 施工机械设备在装配式建筑施工中,各种先进的机械设备起到了关键作用。
例如:吊车、行走架等用于运输和安装梁柱、墙板等构件;拆模机用于拆除模板,在提高施工效率和质量上发挥了积极作用。
机械设备凭借其高效率和降低人力成本的特点,大大提升了装配式建筑的整体制造水平。
2. 智能化设备随着智能科技的迅猛发展,在装配式建筑领域也广泛应用了智能化设备。
比如,在施工过程中,通过使用无人机进行实时监测和勘察可以大幅提高施工效率,保证施工的准确性;利用激光测量仪等精确测量设备能够提供更加准确的数据,使施工过程更加精细化。
这些智能化设备不仅提高了装配式建筑的质量水平,还为项目的管理和维护带来便利。
二. 技术支持1. BIM技术BIM(Building Information Modeling)技术在装配式建筑中起到了至关重要的作用。
BIM技术通过数字模型对各个构件进行三维建模,并结合其他设计参数,分析其受力情况、交通运输、吊装路径等问题。
利用BIM技术可以实现对整个装配式建筑项目的全过程管理,包括设计、构造、运营和拆除。
这种综合信息管理系统有助于解决装配式建筑在设计与施工阶段需要协同配合完成的各项任务。
2. 工艺与操作技术支持装配式建筑施工需要熟练的操作技术和丰富经验的工艺支持。
因为装配式建筑的构件大部分在工厂制造,现场施工时需要准确、精细地进行安装。
操作技术的熟练程度直接影响到施工质量和效率。
此外,工艺支持能够针对不同建筑结构,提供合理的拼装方案和各种应急措施。
三. 重要性1. 提高施工效率装配式建筑采用模块化设计和制造,通过设备与技术支持将每个模块进行专业加工和组合,大大节约了时间。
车间管理技术总结范文

随着社会经济的不断发展,企业对生产效率和质量的要求越来越高,车间管理技术作为企业生产的核心环节,其重要性不言而喻。
以下是对我司车间管理技术的总结,旨在梳理过去一年的工作成果,并为今后的工作提供借鉴。
一、生产管理1. 生产计划:根据公司年度生产目标,制定详细的生产计划,包括生产任务、进度安排、物料需求等,确保生产任务的顺利完成。
2. 生产调度:合理安排生产任务,优化生产流程,提高生产效率。
针对生产过程中出现的突发状况,及时调整生产计划,确保生产进度不受影响。
3. 质量控制:严格执行ISO9001质量管理体系,加强原材料、生产过程、成品的质量检验,确保产品质量稳定可靠。
二、设备管理1. 设备维护:建立健全设备维护保养制度,定期对设备进行保养,确保设备处于良好运行状态。
2. 设备更新:根据生产需求,及时更新设备,提高生产效率,降低生产成本。
3. 设备管理信息化:利用信息化手段,对设备运行状态、维修记录、备件消耗等进行实时监控,提高设备管理效率。
三、安全管理1. 安全教育:定期开展安全教育培训,提高员工安全意识,确保生产过程中的安全。
2. 安全检查:加强对生产现场的巡查,及时发现安全隐患,并采取措施予以整改。
3. 应急预案:制定完善的应急预案,提高应对突发事件的能力。
四、人员管理1. 人员培训:针对不同岗位,开展有针对性的培训,提高员工技能水平。
2. 人员激励:建立健全激励机制,激发员工工作积极性,提高工作效率。
3. 人员考核:定期对员工进行考核,了解员工工作表现,为人员调整和优化提供依据。
五、成本控制1. 原材料管理:优化采购流程,降低采购成本,确保原材料质量。
2. 能源管理:加强能源消耗监测,提高能源利用效率,降低生产成本。
3. 成本核算:定期进行成本核算,分析成本构成,找出成本控制点,提高企业盈利能力。
总结:过去一年,我司车间管理技术在生产管理、设备管理、安全管理、人员管理和成本控制等方面取得了显著成果。
装配式建筑施工的施工设备管理与技术支持

装配式建筑施工的施工设备管理与技术支持随着城市化进程的加速和人们对于建筑质量、环境友好性以及施工效率的要求不断提高,装配式建筑作为一种新兴的建造方式受到了广泛关注。
然而,在进行装配式建筑施工过程中,合理且有效地管理和支持施工设备显得尤为重要。
本文将从施工设备管理和技术支持两个方面进行讨论,以探究如何优化装配式建筑施工。
一、施工设备管理1. 设备调度与利用装配式建筑施工过程中涉及大量机械设备,如吊车、塔吊等。
合理调度并充分利用这些设备是提高效率的关键。
首先,根据项目计划编制详细的设备使用计划,并确保各项任务前后衔接紧密。
其次,定期检查维护设备,确保其正常运行状态,避免因故障导致停工延期。
最后,在低峰时段合理安排设备检修、保养等操作,以提高整体利用率。
2. 施工现场布局在装配式建筑施工现场,设备的布局合理与否直接影响到施工效率。
首先,需要根据具体项目规模和要求进行科学布置,并确保设备之间的协调运作。
其次,为提高安全性,要对设备进行固定和防护,避免意外事故。
最后,在施工场地内部设置明确的标识和通道,方便设备进出以及人员疏散。
3. 设备信息化管理通过建立设备信息化管理系统,实时掌握设备使用情况、维护记录等能够提高施工效果。
可以结合物联网技术对各类设备进行监测与远程管理,及时了解设备状况并预防潜在问题。
同时,在系统中设置报警机制,一旦发现异常情况能够迅速响应并采取相应措施。
二、技术支持1. 建立专业化团队装配式建筑的施工涉及多个专业领域,因此建立一个高效、专业的技术支持团队十分关键。
该团队应包括设计师、工程师和技术人员等,并且需要持续进行培训以保持技术更新与创新。
2. 施工方案优化技术支持团队应该根据项目需求与特点,制定出最佳的施工方案。
这其中包括构件的拆装顺序、协作流程等细节,在保证质量和效率的前提下,选择最合适的方法进行操作。
3. 技术指导与解决方案在实际装配式建筑施工过程中,遇到问题是不可避免的。
技术支持团队应及时提供施工指导并给出解决方案,帮助项目顺利进行。
工装设备技术支持与售后服务方案范文

工装设备技术支持与售后服务方案范文工装设备技术支持与售后服务方案
一、技术支持
1. 技术支持服务目标
提供全面的技术支持服务,确保客户在设备使用过程中遇到的问题能够及时得到解决,提高设备使用效率,降低客户维护成本。
2. 技术支持服务内容
(1)设备安装调试:根据客户需求,提供设备安装、调试及试运行服务,确保设备正常运行。
(2)设备维护:定期对设备进行检查、维护和保养,确保设备正常运行,延长设备使用寿命。
(3)故障诊断与排除:对客户在使用过程中遇到的问题进行诊断和排除,提供解决方案。
(4)技术培训:根据客户需求,提供设备操作技能培训,提高客户操作技能。
(5)技术咨询:为客户提供技术咨询,解答客户技术难题。
二、售后服务方案
1. 售后服务目标
提供全面的售后服务,确保客户在使用过程中遇到的问题能够及
时得到解决,提高客户满意度。
2. 售后服务内容
(1)设备安装调试:根据客户需求,提供设备安装、调试及试运行服务,确保设备正常运行。
(2)设备维护:定期对设备进行检查、维护和保养,确保设备正常运行,延长设备使用寿命。
(3)故障诊断与排除:对客户在使用过程中遇到的问题进行诊断和排除,提供解决方案。
(4)定期巡检:定期对设备进行巡检,发现潜在问题,提前解决,避免故障发生。
(5)技术培训:根据客户需求,提供设备操作技能培训,提高客户操作技能。
装配式建筑施工中的设备管理与技术支持策略

装配式建筑施工中的设备管理与技术支持策略一、引言装配式建筑是当前建筑行业的发展趋势,它具有快速、环保和经济等优势,受到了广泛关注和应用。
在装配式建筑施工过程中,设备管理和技术支持是确保项目顺利进行和高质量完成的重要因素。
本文将探讨装配式建筑施工中的设备管理与技术支持的策略。
二、设备管理策略1. 设备选购与租赁在装配式建筑施工过程中,需要合适的设备来进行构件制作、安装和调试等工作。
首先,对于常用设备应及时更新,并考虑到其适用性和效能,选择符合项目需求的优质设备。
此外,在短期需求或特殊项目中,可以考虑租赁设备以降低成本,并确保所租赁设备良好运行。
2. 设备维护与保养定期维护和保养设备是确保其长期可靠性和正常使用的关键措施。
为了实现施工过程中的连续生产,应制定详细计划来进行检修和保养,减少设备故障的发生。
此外,培训设备操作人员,确保其熟悉设备运行原理和日常维护技巧,并建立设备使用记录以及故障处理流程。
3. 设备库存管理合理的设备库存管理有助于提高施工效率并减少成本浪费。
通过分析项目需求和施工进度,预先规划所需设备类型、数量和时间,定期核对库存,并采取补充或调整措施以满足实际需要。
同时,在退场前进行设备检查,做好报废或维修处理。
三、技术支持策略1. 优质技术供应商选择装配式建筑施工中需要与多个技术供应商合作,包括构件制造商、安装服务商等。
为了确保技术支持的可靠性和高效性,应选择具有良好信誉和丰富经验的供应商进行合作。
与供应商建立长期合作关系,并在施工前明确双方责任与权益。
2. 技术培训与人员配备良好的技术支持需要具备熟练的人员和全面的培训计划。
在施工过程中,应针对不同工序或设备进行培训,确保施工人员能够熟练操作和维护设备。
同时,指定专人负责技术支持,并与供应商保持密切的沟通合作。
3. 技术创新与问题解决装配式建筑领域的技术不断发展,为了提高施工效率和质量, 需要关注新的技术趋势和解决方案。
定期评估并引入先进技术,如BIM技术等。
装配式建筑施工的设备与技术支持分析

装配式建筑施工的设备与技术支持分析装配式建筑是一种快速、高效的建筑方式,近年来受到了越来越多的关注。
在装配式建筑施工过程中,设备与技术支持起着至关重要的作用。
本文将对装配式建筑施工中所涉及到的设备与技术支持进行分析,并探讨其优势和发展前景。
一、设备支持1. 装配式建筑机械设备装配式建筑需要使用各种机械设备来实现构件制造、运输和安装等工序。
例如,在构件制造环节,需要使用自动化生产线和数控机床等设备,以提高构件精度和生产效率;在运输环节,常用的机械设备有塔吊、升降机等,它们能够快速而安全地将构件从生产厂区运送到施工现场;在安装环节,则可以利用龙门架、吊车等大型机械设备来完成。
2. 智能化仪器设备智能化仪器设备是装配式建筑领域不可或缺的一部分。
例如,在钢结构构件制造过程中,利用先进的3D扫描仪可以实时获取构件尺寸信息,以便进行实际制造和加工;在构件安装过程中,可以利用全站仪进行精确的定位和测量,保证施工的准确性。
3. 自动化生产线自动化生产线是装配式建筑的重要设备之一。
通过将装配式施工过程中的各个环节进行智能化、自动化处理,可以大幅度提高生产效率和质量稳定性。
例如,在钢结构构件制造过程中,使用自动化生产线可以实现高精度切割、焊接等作业,有效减少人为因素对产品质量造成的影响;而在混凝土预制构件制造方面,则可以借助模具技术和自动送料系统来提高生产效率。
二、技术支持1. BIM技术BIM(Building Information Modeling)技术是当前装配式建筑领域应用最广泛的技术之一。
通过将建筑设计与施工过程中的各项参数整合到一个三维模型中,BIM技术能够更好地协调设计与施工之间的关系,并提前发现潜在问题。
在装配式建筑施工中,BIM技术能够帮助实现零误差、高效率的施工过程,并且为后期运营和维护提供了可靠的数据基础。
2. 智能化监控系统智能化监控系统可以应用于装配式建筑施工的各个环节,包括构件制造、运输和安装等。
总装科年终工作总结

总装科年终工作总结总装科是我所在公司的一个重要部门, 负责产品的总装和调试工作。
在过去的一年里, 总装科团队克服了各种困难和挑战, 在工作中取得了一系列的成绩。
现将我们的工作总结如下:一、工作内容1.产品总装: 我们按照生产计划, 完成了大量产品的总装任务。
总装过程中, 我们高度重视品质控制, 严格按照质量标准进行操作, 确保产品的质量和性能达到要求。
2.调试工作: 我们承担了产品调试的工作, 确保产品能够正常运行。
我们遵循严谨的调试流程, 全面测试产品的各个功能, 同时进行问题排查和修复, 保证产品的稳定性和可靠性。
3.技术支持:我们为其他部门提供技术支持,解答他们在使用产品过程中的问题。
我们通过及时沟通和技术培训,提高了其他部门对产品的使用效率,同时增强了团队的凝聚力和合作能力。
二、成绩回顾1.完成了年度总装任务: 我们按照计划, 顺利完成了年度总装任务, 没有出现严重延误或质量问题。
这表明我们具备良好的执行能力和组织协调能力。
2.有效提升了调试效率: 通过优化调试流程和增加自动化设备的使用, 我们提高了调试效率, 减少了调试时间和人力成本。
同时, 我们建立了一套完善的故障排查和修复机制, 最大程度地减少了产品在使用过程中出现的问题。
3.全面提升了技术能力:我们积极学习新技术和新知识,不断提升自己的专业水平。
我们参加了各类培训和学习活动,掌握了一些新的调试技能和工具,为团队的综合实力提升做出了积极贡献。
4.获得了客户的赞誉:我们始终将客户需求放在首位,不断优化产品和服务。
在过去的一年里,我们获得了多个客户的赞誉和好评,获得了客户满意度的极高评分。
三、存在的问题在工作中, 我们也面临一些问题和不足之处, 需要进一步改进和提升。
1.人员短缺: 由于工作量的增加, 我们人手相对不足, 导致工作压力较大。
未来需要针对这一问题加大招聘力度, 增加人员配置, 保证工作质量和效率。
2.设备更新:部分设备已经使用了较长时间,存在一定的性能下降和易损坏的风险。
- 1、下载文档前请自行甄别文档内容的完整性,平台不提供额外的编辑、内容补充、找答案等附加服务。
- 2、"仅部分预览"的文档,不可在线预览部分如存在完整性等问题,可反馈申请退款(可完整预览的文档不适用该条件!)。
- 3、如文档侵犯您的权益,请联系客服反馈,我们会尽快为您处理(人工客服工作时间:9:00-18:30)。
总装车间现场技术管理与技术支持分析
张庆庚
关键词:现场优势;质量管理。
摘要:本文主要通过总装车间的现场技术管理、技术支持工作的特点的分析,着重阐述总装生产现场技术管理、技术支持工作对于整车质量问题的解决、整车质量问题的提升的必要性、独特性,以及总装一线的工程技术人员的素质对质量问题的可靠及高效解决的重要性。
现在大多数企业所采用的都是全员质量管理方式,此种方式强调质量管理的普遍性与全员性,在这过程中,企业的各部门、各环节都被看作关系到产品质量的控制点,此种质量管理方式如果不实现对关键点的控制,就容易将各部门对质量工作的相关性和重要程度模糊起来,往往会造成企业在质量管理过程中失去重点,使企业丧失竞争力,所以企业在那些关系到自身生存和发展的关键环节上,必须具有独有的、比竞争对手更强的、持久的某种优势、能力或知识体系,而质量管理则是基本的能力要求。
从质量管理环节上讲,研发、工艺、生产、检验等各个部门都对质量有重要影响。
我们今天主要谈谈的是总装生产环节中的现场技术管理、技术支持工作对质量的影响,即总装现场的技术管理、技术支持工作有哪些特点及对整车质量的控制与提升有哪些影响。
现场技术管理、技术支持工作的目的
首先我们谈谈总装车间现场技术管理与技术支持工作的目的,总装车间现场技术管理与技术支持工作的主要目的是使整个的生产过程得到有效的监控,在出现波动时,能够快速的消除质量波动,将整个产品的质量问题完全控制在生产环节,不使之传递到销售及用户手中,而对整个产品的声誉造成不良影响。
具统计:整车正式生产后的所有问题,90%是在生产过程中被发现与解决的,而生产过程中的问题的解决,也可以有效的减少在销售、售后过程中的质量问题。
现场技术管理与技术支持工作的主要目的是通过对整个生产过程的有效的监控与管理,达到消除生产波动,提升生产产品的整体水平的作用。
现场技术管理、技术支持工作的内容
上面我们讲了车间现场技术管理、技术支持工作的目的,现在我们在讲车间现场技术管理与技术支持工作所包含的内容,概况的讲,主要包括工艺管理、工艺优化、现生产技术支持三部分。
现场工艺管理主要是对生产过程进行全过程监控,保证整个生产过程的一致性。
总装生产相对于其它生产环节而言具体“依赖人”的特征,比如冲压更依赖于的模具的控制,车身更依赖于对夹具的控制,涂装更依赖于对设备的控制,而总装生产大部分工作都是人工进行装配,所以所有的操作过程更依赖于人。
那么总装生产过程的监控就要注重于对人的监控,保证所有操作者都是严格按工艺要求进行标准化操作,严格按照设备要求进行规范化操作,这是总装现场技术支持的第一要务。
工艺优化,所有的工艺过程只有更好,没有最好。
无论是生产节拍、操作顺序、工具工装、生产材料等都可以不断的进行优化以提高质量、降低成本。
所有总装车间现场技术支持的第二大要务就是不断的进行工艺优化以提高工艺过程水平。
现场技术支持部分主要是对现场出现的各种技术性问题给予及时的及有效的支持,保证现场生产过程的平稳运行,不致于受各种技术性问题的影响而导致生产不顺畅。
比如物料配置问题,现场质量问题等。
我们都知道,一般的生产现场在技术管理上都存在着不规范的情况,所有有效的全过程监控和管理,实质是一个艰巨的具有基础性、技术性、开创性、细致性特征的工作。
因此此项工作必须得到全公司所有部门的重视与支持。
现场技术支持工作独特的和重要的内容
上面我们对车间现场技术管理与技术支持工作内容进行了大体的分析,下面我们着重分析一下现场技术支持工作在整个质量环中的独特的和重要的作用。
要分析车间现场技术支持工作的对于质量问题解决有利的独特性,必须认清现场技术支持工作相对于其它技术支持工作的重要区别,车间现场技术支持工作的与其它技术支持工作的区别主要在于“现场性”。
现场发现问题、现场分析问题、现场进行试验、现场解决问题。
具有及时性、高效性,对于在现场的问题能及时发现并能及时解决,不至于将问题带到销售或售后带来不良影响。
首先,车间现场能及时发现问题,整个生产过程中,通过操作者的工位点检、检查员的专项检查、整机工况试验、工艺员的工艺过程检查,几乎所有的问题都能在生产车间现场被发现,我们曾经统计过,在产品进行试生产阶段后,几乎90%以上的问题都是生产现场发现的。
其次,在车间现场发现的质量缺陷或质量问题,能第一时间进行现场保持、缺陷保持,构成质量问题的第一现场。
而质量问题在第一现场的保持,便于对问题的相关方面进行分析,并可以尽可能快速的找到“问题点”,而对于质量问题而言,“问题点”的找到,对质量问题的解决会起到关键性和决定性的作用。
找到问题点后,就可以针对问题点展开解决方案,从而使质量问题得到有效的和快速的解决。
在寻找问题点的过程中,车间有大量的人力、工装、设备,能对问题的分析给以很大的支持,对各种的试验能快速的进行。
在此试验的保证下,能及时高效的提出解决方案并进行试验最终解决问题。
一般生产线上问题如果经车间反馈后相关部门调查研究就需一定时日、改进方案论证与实施又需一定时日,而在车间现场进行针对性的调查研究则可大大缩短研究时间、大大缩短方案论证时间、大大缩短解决时间。
如带天窗车在安装后扶手后在顶棚处出现褶皱,原车间工艺员反馈到相关部门后,车身部门的回复是查车身相应的安装点检测结果都合格,配套件经检具检查后也合格,使问题的调查陷入了僵局,此种质量缺陷迟迟得不到解决,后来车间工艺人员在有质量缺陷的问题车上进行顶棚剖解,剖解后可直观的看到干涉的部位,即找到了“问题点”然后针对此“问题点”进行分析与调查,立即查出了问题的原因,并有针对性的提出具体的解决方案,使问题得到及时的解决。
现场技术支持工作经常存在的问题与解决
现在我们再谈谈现场技术支持工作的问题:现在生产现场技术支持工作所存在的主要问题在两方面,一方面是文件变更的维护管理;一方面是现场质量问题的分析解决力度上不够。
对于现场质量问题的分析与处理方面,现在生产现场的技术支持工作的问题主要是自主性不强,当生产现场出现质量问题时,现场的技术支持人员大都充当一个信息员的角色,将问题传递到相关部门,没有进行有效的前期的初步分析和判断,没有制定实之有效的临时解决措施;相关的部门到现场进行分析时解决时,又由于没有一个初步的评判使调查分析与解决时间延长,或由于本位主义而导致可能否定自己问题而产生互相推诿情况的产生。
使现场的质量问题不能解决或不能及时快速解决。
甚至使质量问题有可能由于没有及时解决而流到
生产之外,进入销售和售后而影响用户的满意度,产生用户抱怨而损害企业形象。
比如在总装生产现场出现一个零部件与车身不匹配的情况,那么配套件与车身都可能有问题,而车身与配套件的相关人员到现场后,有可能出现相互推诿的情况,而如果车间工艺人员在此前有一个初步的判断,比如判断出车身的问题,则可直接将车身相关人员找来协调解决。
那么生产现场的技术支持人员能否具有作高效分析与判断的可能性呢? 这完全有可能,一方面这与车间现场技术人员的素质有很大关系。
另一方面,车间现场的技术支持工作具有其它部门的技术人员所不具有的独特性与优势,即现场优势,而这些优势恰恰能够为车间技术支持的人员提供有利的外部条件,使质量问题能够得到高效的解决。
现场技术支持工作的素质要求
下面我们讨论生产现场的技术支持人员的素质要求,从事生产现场的技术支持的人员需有较高的素质,此素质不仅是业务素质、而且包括身体素质。
现在我们讨论一下车间现场技术支持人员的素质要求,车间现场的技术支持工作,表现为各种车间现场出现的技术问题要及时快速的解决,保证生产的平稳运行,在这过程中,可能遭遇各种各样的复杂情况,而且生产的压力很大,所以要求车间现场的技术支持工作首先要有超强的业务专长,能够对于质量问题进行高效的分析与判断,并快速的解决。
除此之外,为了能适应高强度的生产,生产现场的技术支持人员不仅要有超强的业务专长,而且要年富力强。
这样才能适应车间现场的技术支持工作。
在现场发现质量问题时,能够第一时间进行分析、试验、判断、提出临时性或永久性的解决方案。
如果需要与其它部门进行协调,则能够有效的进行沟通,使问题的原因能有效的进行传递与解决。
作者简介
张庆庚男出生于1975年9月25日 1999年毕业于沈阳工业大学机制专业, 学士学位, 现在沈阳华晨金杯汽车有限公司总装工艺处任装配工艺工程师, 主要研究汽车的整车装配工艺, 通讯地址:沈阳市大东区东山嘴子14号, 邮编110044. 电子邮箱:zhongguoalibaba@.。