28种炼钢方法
钢铁总结归纳
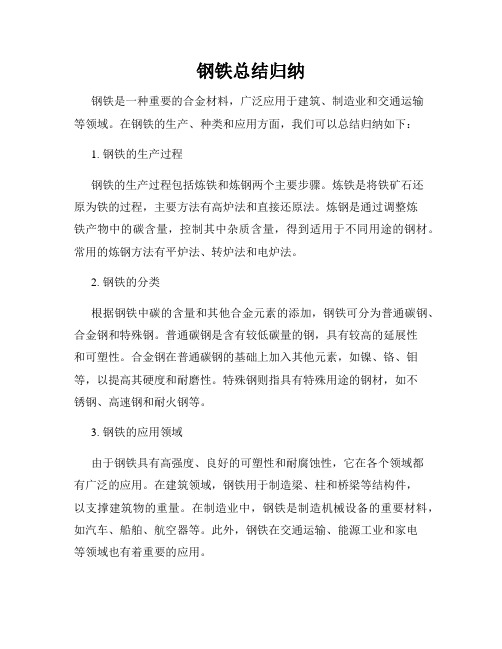
钢铁总结归纳钢铁是一种重要的合金材料,广泛应用于建筑、制造业和交通运输等领域。
在钢铁的生产、种类和应用方面,我们可以总结归纳如下:1. 钢铁的生产过程钢铁的生产过程包括炼铁和炼钢两个主要步骤。
炼铁是将铁矿石还原为铁的过程,主要方法有高炉法和直接还原法。
炼钢是通过调整炼铁产物中的碳含量,控制其中杂质含量,得到适用于不同用途的钢材。
常用的炼钢方法有平炉法、转炉法和电炉法。
2. 钢铁的分类根据钢铁中碳的含量和其他合金元素的添加,钢铁可分为普通碳钢、合金钢和特殊钢。
普通碳钢是含有较低碳量的钢,具有较高的延展性和可塑性。
合金钢在普通碳钢的基础上加入其他元素,如镍、铬、钼等,以提高其硬度和耐磨性。
特殊钢则指具有特殊用途的钢材,如不锈钢、高速钢和耐火钢等。
3. 钢铁的应用领域由于钢铁具有高强度、良好的可塑性和耐腐蚀性,它在各个领域都有广泛的应用。
在建筑领域,钢铁用于制造梁、柱和桥梁等结构件,以支撑建筑物的重量。
在制造业中,钢铁是制造机械设备的重要材料,如汽车、船舶、航空器等。
此外,钢铁在交通运输、能源工业和家电等领域也有着重要的应用。
4. 钢铁生产对环境的影响尽管钢铁在各个领域有着广泛的应用,但其生产对环境造成了一定的负面影响。
钢铁生产会产生大量的二氧化碳等温室气体,对全球气候变化产生贡献。
此外,钢铁产业还会排放大量的粉尘和废水,对环境造成污染。
因此,降低钢铁生产过程中的能耗和环境污染已成为钢铁企业和政府部门亟待解决的问题。
5. 钢铁行业的未来发展趋势随着经济的发展和技术的进步,钢铁行业也呈现出一些新的发展趋势。
首先,钢铁行业将更加注重绿色、低碳的发展方式,推动节能减排和循环利用。
其次,随着科技的进步,新材料的出现可能会对传统钢铁产业带来一定的冲击。
例如,复合材料和3D打印技术的应用可能会减少对钢铁的需求。
因此,钢铁行业需要不断创新和转型以适应未来的发展需求。
通过对钢铁生产、分类、应用、环境影响和未来发展趋势的归纳总结,我们对钢铁有了更全面的了解。
工业炼钢的原理初中化学

工业炼钢的原理初中化学一、炼钢基本原理炼钢的主要目的是降低生铁中含有的含碳量,同时去除磷、硫等有害元素,并调整钢中的合金元素含量。
生铁炼成钢的实质是降低生铁中的含碳量,而含碳量的降低则是通过加入氧化剂将生铁中过多的碳和其他杂质转化为气体或炉渣除去。
二、原料与辅料炼钢的主要原料是铁水,即转炉或电炉炼铁得到的含碳量较高的铁水。
辅料主要包括造渣材料(如石灰石、白云石等),用于形成炉渣去除杂质;氧化剂(如氧气、铁矿石等),用于氧化铁水中的碳和其他杂质;以及脱氧剂和合金剂,用于调整钢的成分。
三、炼钢炉种类1. 氧气转炉:主要利用氧气作为氧化剂,吹入熔化的铁水中,使碳和其他杂质氧化成气体排出。
2. 平炉:通过向炉内加入燃料进行燃烧,产生热量熔化铁水,并加入氧化剂进行脱碳和其他杂质。
3. 电炉:利用电能产生高温熔化铁水,并加入氧化剂进行脱碳和杂质去除。
四、氧气转炉炼钢氧气转炉炼钢是现代炼钢的主要方法。
在转炉中,通过吹入高压氧气与铁水中的碳和杂质发生氧化反应,生成CO等气体排出,从而达到降碳的目的。
五、平炉炼钢法平炉炼钢法是一种较为传统的炼钢方法。
在平炉中,通过加入燃料燃烧产生的高温熔化铁水,并加入氧化剂进行脱碳和杂质去除。
平炉炼钢法的特点是炉内温度均匀,适合生产优质钢。
六、电炉炼钢法电炉炼钢法是利用电能熔化铁水并进行脱碳和杂质去除的方法。
电炉炼钢法适用于生产特种钢和合金钢,因为它能够精确地控制炉温和加入合金元素的时间。
七、炉渣与脱磷在炼钢过程中,通过加入造渣材料形成炉渣,炉渣可以将磷等杂质带出炉外,从而实现脱磷的目的。
炉渣的成分和性质对于炼钢过程的稳定性和钢的质量有重要影响。
八、脱硫与脱氧脱硫主要是通过加入脱硫剂(如石灰石)与铁水中的硫发生反应,生成硫化物进入炉渣中从而去除。
脱氧则是为了防止钢在凝固过程中产生裂纹,通过加入脱氧剂(如硅铁、铝铁等)与钢中的氧发生反应,生成不溶于钢的氧化物或硫化物。
总结:工业炼钢是一个复杂的过程,需要精确控制各种工艺参数和操作条件,以确保生产出高质量的钢材。
中国人的一百项发明
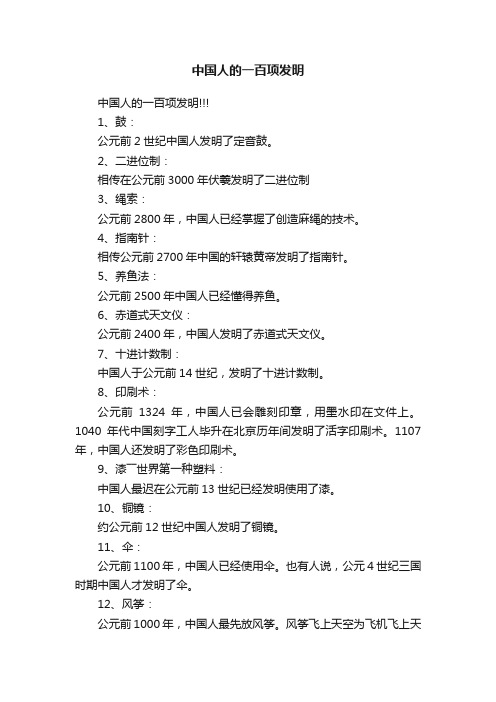
中国人的一百项发明中国人的一百项发明1、鼓:公元前2世纪中国人发明了定音鼓。
2、二进位制:相传在公元前3000年伏羲发明了二进位制3、绳索:公元前2800年,中国人已经掌握了创造麻绳的技术。
4、指南针:相传公元前2700年中国的轩辕黄帝发明了指南针。
5、养鱼法:公元前2500年中国人已经懂得养鱼。
6、赤道式天文仪:公元前2400年,中国人发明了赤道式天文仪。
7、十进计数制:中国人于公元前14世纪,发明了十进计数制。
8、印刷术:公元前1324年,中国人已会雕刻印章,用墨水印在文件上。
1040年代中国刻字工人毕升在北京历年间发明了活字印刷术。
1107年,中国人还发明了彩色印刷术。
9、漆――世界第一种塑料:中国人最迟在公元前13世纪已经发明使用了漆。
10、铜镜:约公元前12世纪中国人发明了铜镜。
11、伞:公元前1100年,中国人已经使用伞。
也有人说,公元4世纪三国时期中国人才发明了伞。
12、风筝:公元前1000年,中国人最先放风筝。
风筝飞上天空为飞机飞上天空提供了原理和灵感。
13、米酒:公元前1000年,中国人发明了米酒。
14、弓箭:中国人于公元前8世纪发明了弓箭。
而欧洲的意大利在公元10世纪才使用弓,比我国晚了一千二百年。
15、古代机器人:公元前770年至公元前256年东周时期,中国人就已发明了古代机器人。
16、分行栽培与精细耕地法:公元前6世纪,中国人发明了分行栽培与精细耕地法;欧洲人到1731年才使用此项技术,比中国晚了二千四百年左右。
17、铁犁:公元前6世纪,中国人发明了铁犁。
欧洲人到17世纪才使用铁犁,比中国晚了二千三百年左右。
18、大定音钟:中国人于公元前6世纪发明了大定音钟;欧洲人到公元1000年才有定音钟,比中国晚了一千六百年左右。
19、长明灯:大约在公元前589年,中国人发明了长明灯。
灯蕊为石棉;灯油为海豹油或鲸油。
20、算盘:公元前550年中国人发明了算盘,用于计算。
21、地毯:公元前五百年地毯已在中国应用。
炼钢的种类

炼钢的种类
炼钢是指将生铁或其他含铁原料通过高温加热和冶炼等工艺过程,转化为具有一定成分和性能的钢铁材料。
根据不同的工艺方法和产品用途,炼钢可以分为以下几种类型:
1. 铸造钢:通过铸造方式生产的钢铁材料,具有良好的铸造性能和抗震性能,广泛应用于汽车、机床、建筑等领域。
2. 锻钢:经过锻造工艺生产的钢铁材料,具有较高的强度、韧性和耐磨性,主要用于制造重型机械、船舶、汽车发动机等。
3. 热轧钢:通过热轧工艺生产的钢铁材料,具有良好的延展性、韧性和耐磨性,广泛应用于建筑、桥梁、船舶等领域。
4. 冷轧钢:经过冷轧工艺处理的钢铁材料,具有较高的光洁度、厚度均匀度和精度,主要用于汽车、家电、电子等领域。
5. 镀锌钢:在钢铁表面镀上一层锌的钢材,具有良好的耐腐蚀性和延展性,广泛应用于建筑、桥梁、机械等领域。
6. 彩涂钢板:在钢板表面涂覆一层或多层有机涂层的钢板,具有良好的耐候性和美观性,主要用于建筑外墙、屋顶、装饰等领域。
7. 不锈钢:含有较高铬含量的钢铁材料,具有优良的耐腐蚀性、耐磨性和美观性,广泛应用于食品工业、化工设备、建筑装饰等领域。
8. 轻钢:采用轻质钢材生产的钢铁材料,具有轻质、高强度、良好的耐腐蚀性,主要用于汽车、飞机等交通工具以及建筑领域。
9. 钢铁合金:将钢铁与其他金属或非金属元素合金化,以提高钢铁的性能,如耐磨钢、耐热钢、合金结构钢等。
10. 复合钢:由两种或多种钢材组合而成的复合材料,具有良好的综合性能,如双相钢、复合钢板等。
这些炼钢种类根据不同的生产工艺和应用场景而有所区别,同时也可根据客户需求进行定制。
土法炼钢工艺
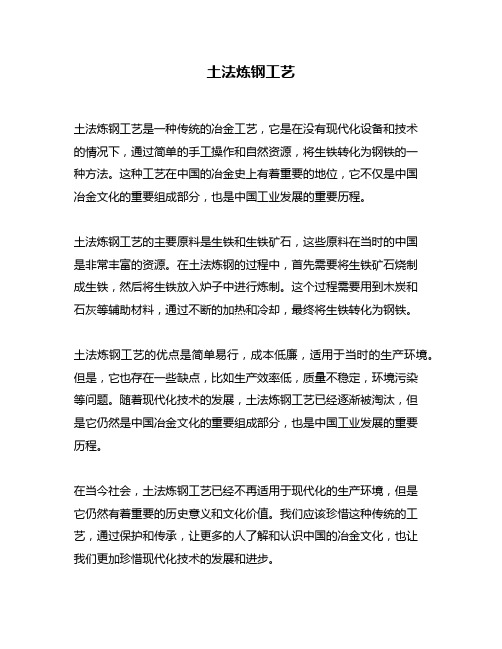
土法炼钢工艺
土法炼钢工艺是一种传统的冶金工艺,它是在没有现代化设备和技术
的情况下,通过简单的手工操作和自然资源,将生铁转化为钢铁的一
种方法。
这种工艺在中国的冶金史上有着重要的地位,它不仅是中国
冶金文化的重要组成部分,也是中国工业发展的重要历程。
土法炼钢工艺的主要原料是生铁和生铁矿石,这些原料在当时的中国
是非常丰富的资源。
在土法炼钢的过程中,首先需要将生铁矿石烧制
成生铁,然后将生铁放入炉子中进行炼制。
这个过程需要用到木炭和
石灰等辅助材料,通过不断的加热和冷却,最终将生铁转化为钢铁。
土法炼钢工艺的优点是简单易行,成本低廉,适用于当时的生产环境。
但是,它也存在一些缺点,比如生产效率低,质量不稳定,环境污染
等问题。
随着现代化技术的发展,土法炼钢工艺已经逐渐被淘汰,但
是它仍然是中国冶金文化的重要组成部分,也是中国工业发展的重要
历程。
在当今社会,土法炼钢工艺已经不再适用于现代化的生产环境,但是
它仍然有着重要的历史意义和文化价值。
我们应该珍惜这种传统的工艺,通过保护和传承,让更多的人了解和认识中国的冶金文化,也让
我们更加珍惜现代化技术的发展和进步。
总之,土法炼钢工艺是中国冶金文化的重要组成部分,它虽然已经被现代化技术所取代,但是它仍然有着重要的历史意义和文化价值。
我们应该珍惜这种传统的工艺,通过保护和传承,让更多的人了解和认识中国的冶金文化,也让我们更加珍惜现代化技术的发展和进步。
转炉炼钢工艺简介
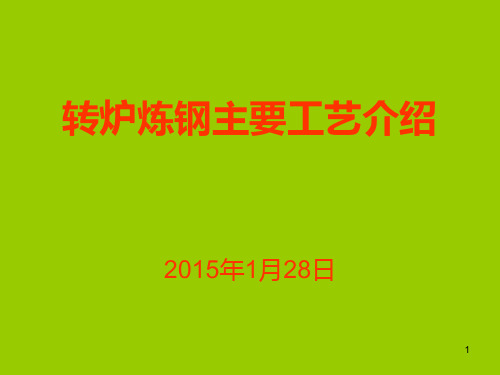
18
萤石作用及要求
• 作用
造渣加入萤石可以加速石 灰的溶解,萤石的助熔作 用是在很短的时间内能够 改善炉渣的流动性,但过 多的萤石用量,会加剧炉 衬的损坏,并污染环境。
• 质量要求 • CaF2≥75%, SiO2≤23%,S≤0.20%, P≤0.08%,H2O≤3.0% • 粒度:5-60mm
渣量=(石灰+镁球或熟白)×(2-3)
8
铁水成分及温度影响
• Mn的影响 • 锰是弱发热元素,铁水中Mn氧化后形成的(MnO)可促 进石灰溶解,加快成渣;减少氧枪粘钢,终点钢中余 锰高,能够减少合金用量,利于提高金属收得率;锰 在降低钢水硫含量和硫的危害方面起到有利作用。 Mn/Si的比值为0.8~1.00时对转炉的冶炼操作控制最 为有利。当前使用较多的为低锰铁水,一般铁水中 [Mn]=0.20%~0.40%。
6.设备少,投资节省。
4
炉顶料仓 振动给料器 电子称 带式运输机 密封料仓 传动机构 实 心 轴
汽包 氧 枪 风 机 不 回 收 时 放 空 回收煤气 进入煤气柜
烟 道
文氏管 脱水器
溜 槽
洗 涤 塔
沉淀池
电动机 渣 罐 转 炉 吸 滤 池
水封逆止阀 送往高炉利用
支架Hale Waihona Puke 氧气顶吹转炉工艺流程示意图
5
二 、转炉炼钢用主要原材料
28
2.1装料制度:废钢量的确定
• 热量来源于:
• 转炉炼钢不需要外来热源;
铁水物理热及元素氧化化学热。 铁水及废钢的合理配比须根据炉子的热平衡计算确定。 • 硅的作用 优点:因发热量大,增大废钢加入量,一般铁水中Si增 加0.1%,废钢比增大1%。 缺点:增大渣量,侵蚀炉衬一般控制在0.3-0.5%。
炼钢工艺流程
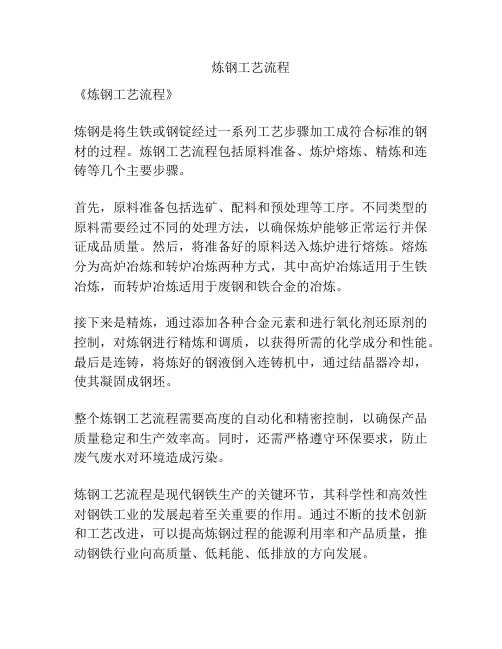
炼钢工艺流程
《炼钢工艺流程》
炼钢是将生铁或钢锭经过一系列工艺步骤加工成符合标准的钢材的过程。
炼钢工艺流程包括原料准备、炼炉熔炼、精炼和连铸等几个主要步骤。
首先,原料准备包括选矿、配料和预处理等工序。
不同类型的原料需要经过不同的处理方法,以确保炼炉能够正常运行并保证成品质量。
然后,将准备好的原料送入炼炉进行熔炼。
熔炼分为高炉冶炼和转炉冶炼两种方式,其中高炉冶炼适用于生铁冶炼,而转炉冶炼适用于废钢和铁合金的冶炼。
接下来是精炼,通过添加各种合金元素和进行氧化剂还原剂的控制,对炼钢进行精炼和调质,以获得所需的化学成分和性能。
最后是连铸,将炼好的钢液倒入连铸机中,通过结晶器冷却,使其凝固成钢坯。
整个炼钢工艺流程需要高度的自动化和精密控制,以确保产品质量稳定和生产效率高。
同时,还需严格遵守环保要求,防止废气废水对环境造成污染。
炼钢工艺流程是现代钢铁生产的关键环节,其科学性和高效性对钢铁工业的发展起着至关重要的作用。
通过不断的技术创新和工艺改进,可以提高炼钢过程的能源利用率和产品质量,推动钢铁行业向高质量、低耗能、低排放的方向发展。
铁合金冶炼几种方法

铁合金冶炼几种方法铁合金是一种重要的冶金材料,广泛应用于钢铁生产、电力工业、冶金工业等领域。
铁合金冶炼是指通过合金化的方式将铁与其他元素组成合金,以满足特定应用需求。
本文将介绍几种常见的铁合金冶炼方法。
一、高炉法高炉法是最主要、也是最常用的铁合金冶炼方法之一。
它是将铁矿石(如赤铁矿、磁铁矿)和焦炭作为主要原料,在高炉中进行冶炼。
高炉内,加入矿石和焦炭后,通过高温还原反应将矿石中的氧化铁还原为金属铁。
高炉法冶炼出的铁合金主要是生铁,其中含有一定的碳、硅等元素。
生铁可以作为制钢的原料,或者用于生产铸铁。
二、电炉法电炉法是另一种重要的铁合金冶炼方法。
它利用电力作为能源,在电弧炉中冶炼。
电弧炉是一种高温设备,通过电流经过两个电极之间的间隙,引发弧放电,产生高温。
在电炉法中,加入铁矿石和合金化剂,通过电弧的高温将铁矿石还原成金属铁。
电炉法冶炼出的铁合金品质高,可以根据需要控制合金中的各种元素含量。
三、转炉法转炉法是冶炼高品质铁合金的重要方法之一。
它是利用转炉设备将生铁与废钢等材料进行冶炼和合金化。
转炉是一种倾转式炼钢设备,通过吹氧将生铁中的杂质氧化,然后控制合金元素的加入,使铁合金中的各种合金元素达到需要的比例。
转炉法冶炼出的铁合金适用于高品质钢铁的生产。
四、氧化铝电解法氧化铝电解法是专门用于冶炼铝铁合金的方法。
它利用电流通过氧化铝溶液,通过电解反应将铁和铝分别沉积到阴阳极上,从而得到铝铁合金。
这种方法制备的铝铁合金品质稳定,可以广泛应用于汽车、航空航天等领域。
综上所述,铁合金冶炼的方法有高炉法、电炉法、转炉法和氧化铝电解法等。
不同的方法适用于不同的铁合金品种和冶炼要求。
随着工业的发展和技术的进步,铁合金冶炼方法也在不断更新和改进,以满足不断变化的市场需求。
转炉炼钢设备和工艺
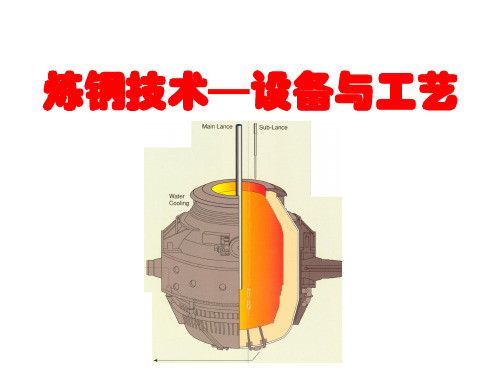
炉型主要尺寸的确定
b)筒球形熔池: 圆柱体和球缺两部分组成。 考虑炉底稳定性和熔池适当深度,一般球缺体的半径R为熔 池直径的1.1~1.25倍。国外大于200t转炉为0.8~1.0倍。 当R=1.1D时,金属熔池的体积为:
V熔 0.79H0D2 0.046D3
因此:熔池深度为:
V熔 0.046D3 H0 0.79D 2
炉型主要尺寸的确定
b)锥球形熔池: 由倒锥台和球缺体两部分组成。 据统计,球缺体曲率半径R=1.1D,球缺体高h2=0.09D, 倒锥台地面直径d1=(0.895~0.92)D。 熔池体积为:
V熔 0.70H0D2 0.0363 D3
熔池深度为:
V熔 0.0363D 3 H0 0.70D 2
炉底寿命短 炉容小 钢水含氮高 喷溅 污染 废钢比低
生产率高 N 、P 、 S 、 C 、 O 低 渣内FeO低 无喷溅 污染低 废钢比低 全 低 吹 O2+ 石 灰 粉
顶底复合吹氧+ 全量废钢 喷吹煤粉 大量高热值废 废钢预热 气 喷石灰粉 二次燃烧 很高废钢比 大量高热值废气
转炉炼钢车间设备组成
炉型主要尺寸的确定
h2 H0 H身 H帽 H内 H总 D D壳 d D出 一球缺高度; 一熔池深度; 一炉身高度; 一炉帽高度; 一转炉有效高度; 一转炉总高 一熔池直径; 一炉壳外径; 一炉口内径; 一出钢日直径; 一炉帽倾角
筒球型氧气顶吹转炉主要尺寸
炉型主要尺寸的确定
熔池直径(D): 转炉熔池在平静状态时金属液面的直径。 计算方法: G D K t 推荐经验公式:
氧气顶吹转炉总图
转炉系统设备
炉型 炉壳 炉体支撑 转炉倾动机构
中国古代的钢铁冶炼技术简史
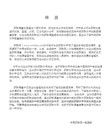
中国古代钢铁发展的特点与其他各国不同。世界上长期采用固态还原的块炼铁和固体渗碳钢,而中国铸铁和生铁炼钢一直是主要方法。由于铸铁和生铁炼钢法的发明与发展,中国的冶金技术在明代中叶以前一直居世界先进水平。
我国古代炼钢技术至迟发明于春秋晚期。由先秦到西汉中晚期,主要制钢工艺是块铁渗碳法;由汉代到明清,主要又是炒钢法和灌钢法,其次还有百炼钢法和炒铁渗碳法,汉魏南北朝时还有“铸铁脱碳钢”,汉代还有坩埚炼钢法。炒钢工艺主要生产一般的可锻铁(包括钢和熟铁),灌钢工艺主要生产含碳较高的刃钢,百炼钢是对普通炒钢的再加工。
到了晋朝又发明了 “灌钢法”,这是中国古代炼钢技术的又一重大成就,采用这种炼铁法为原料制造出来的刀,就是著名的优质兵器――“宿铁刀”。
把加热的铁急剧冷却,提高硬度的淬火技术,早在中国的古代就为人们所掌握,并普遍采用这种处理方法来提高兵刃的硬度。中国人发明了用不同的液体来淬火,从而提高兵刃质量的方式。其中包括用不同河流,不同月份的水。而且还把野兽的尿液和脂肪作为冷却剂,用于淬火处理上,起到了惊人的效果。
此外,在中国很早的古代就掌握了把加热的铁漫漫冷却处理的回火技术,并广泛用于不同用途的兵器的制造中。
据〈中华百科要览〉记载:中国是最早用煤炼铁的国家,汉代时已经试用,宋、元时期已普及。到明代(公元1368~1644年)已能用焦炭冶炼生铁。
中国的生铁炼钢 生铁和韧性铸铁的大规模生产导致了生铁制钢的发明。在汉代先后发明了以下几种生铁制钢的方法。
灌钢 中国生铁制钢技术自战国初期到汉代经过几百年的历程,从块炼铁、渗碳炼钢发展到生铁固体脱碳炼钢、炒钢、炼制熟铁,以及重新渗碳硬化或淬火硬化。在这个基础上,发明了利用液态生铁对熟铁进行扩散渗碳炼钢的方法。这一方法的最早记载见于《北齐书·綦母怀文传》,称为“宿铁”,后世称为灌钢,又称团钢。这是中国古代炼钢技术的又一重大成就。
钢铁冶金学(炼铁部分)
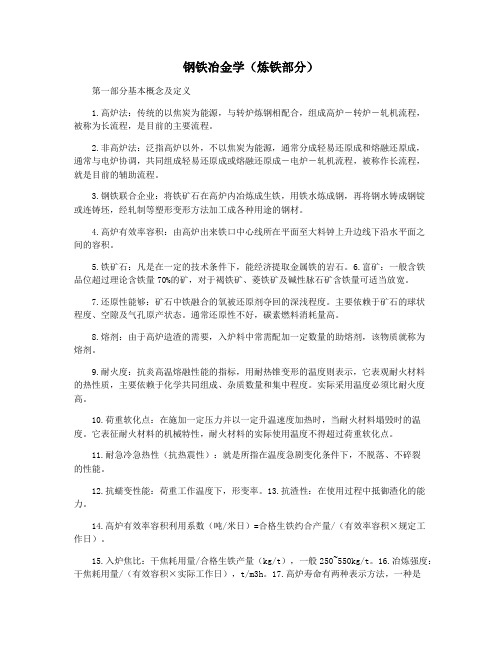
钢铁冶金学(炼铁部分)第一部分基本概念及定义1.高炉法:传统的以焦炭为能源,与转炉炼钢相配合,组成高炉―转炉―轧机流程,被称为长流程,是目前的主要流程。
2.非高炉法:泛指高炉以外,不以焦炭为能源,通常分成轻易还原成和熔融还原成,通常与电炉协调,共同组成轻易还原成或熔融还原成―电炉―轧机流程,被称作长流程,就是目前的辅助流程。
3.钢铁联合企业:将铁矿石在高炉内冶炼成生铁,用铁水炼成钢,再将钢水铸成钢锭或连铸坯,经轧制等塑形变形方法加工成各种用途的钢材。
4.高炉有效率容积:由高炉出来铁口中心线所在平面至大料钟上升边线下沿水平面之间的容积。
5.铁矿石:凡是在一定的技术条件下,能经济提取金属铁的岩石。
6.富矿:一般含铁品位超过理论含铁量70%的矿,对于褐铁矿、菱铁矿及碱性脉石矿含铁量可适当放宽。
7.还原性能够:矿石中铁融合的氧被还原剂夺回的深浅程度。
主要依赖于矿石的球状程度、空隙及气孔原产状态。
通常还原性不好,碳素燃料消耗量高。
8.熔剂:由于高炉造渣的需要,入炉料中常需配加一定数量的助熔剂,该物质就称为熔剂。
9.耐火度:抗炎高温熔融性能的指标,用耐热锥变形的温度则表示,它表观耐火材料的热性质,主要依赖于化学共同组成、杂质数量和集中程度。
实际采用温度必须比耐火度高。
10.荷重软化点:在施加一定压力并以一定升温速度加热时,当耐火材料塌毁时的温度。
它表征耐火材料的机械特性,耐火材料的实际使用温度不得超过荷重软化点。
11.耐急冷急热性(抗热震性):就是所指在温度急剧变化条件下,不脱落、不碎裂的性能。
12.抗蠕变性能:荷重工作温度下,形变率。
13.抗渣性:在使用过程中抵御渣化的能力。
14.高炉有效率容积利用系数(吨/米日)=合格生铁约合产量/(有效率容积×规定工作日)。
15.入炉焦比:干焦耗用量/合格生铁产量(kg/t),一般250~550kg/t。
16.冶炼强度:干焦耗用量/(有效容积×实际工作日),t/m3h。
阳春新钢铁炼钢工艺介绍(11.06.21)
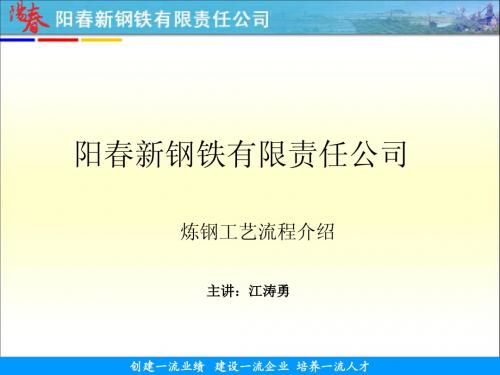
4 5 6
25 25 13
创建一流业绩 建设一流企业 培养一流人才
二、转炉工艺及设备 1、 转炉炉型主要参数 、
名 称 转炉公称容量 转炉平均炉产钢水量 炉壳全高 炉壳外径 转炉炉壳高径比 炉膛内高 炉膛内径 炉膛内高/内膛内径 炉膛内高 内膛内径 炉膛内容积(新衬) 炉膛内容积(新衬) 容积比 炉口直径 溶池直径 溶池深度 出钢口直径 炉底总厚度 炉衬总厚度 符号 T T1 H D H/D h d h/d V V/T d0 d1 h1 d2 h1 d3 mm mm mm mm mm mm m3 mm mm 单位 T T mm mm 数 据 120 100 8820 6050 1.458 7552 4380 1.70 96.49 0.877 2475 4305 1371 140/120 910 600其中大面处 其中大面处700 其中大面处
创建一流业绩 建设一流企业 培养一流人才
5.3造渣制度
造渣制度包括以下内容: 1)炉渣碱度和石灰加入量: 碱度指渣中碱性氧化物/酸性 氧化物( R =CaO/SiO2 ),一 般 为 2.8-4.0, 石 灰 消 耗 5080kg/吨钢。 2)炉渣氧化性:用∑(%FeO) 表示,FeO高利于成渣,脱P,但 降 低 金 属 回 收 率 。一 般 终 渣 FeO:12-16%。 3)渣中(MgO):为防止炉渣侵 蚀炉衬,造渣时加入含镁材料 ,采用溅渣护炉渣中MgO:812%。
创建一流业绩 建设一流企业 培养一流人才
3.2 主厂房主要参数及吊车配备
序号 1 2 跨间名称 炉渣跨 加料跨 长×宽 (m) ) 142×18 × 363×24 × 一期306×15) (一期 × ) 轨面标 高 (m) ) 17.04 23 起重机配置 数量×吨位) (数量×吨位) 2×75/20t × 2×180/63t、1×30+30t、 × 、 × 、 2 ×16t磁盘吊 磁盘吊 1×10t单梁桥式吊车 × 单梁桥式吊车 2×200/63t × 2×80/20t × 3 ×(16+16t)磁盘吊 )
火法冶金
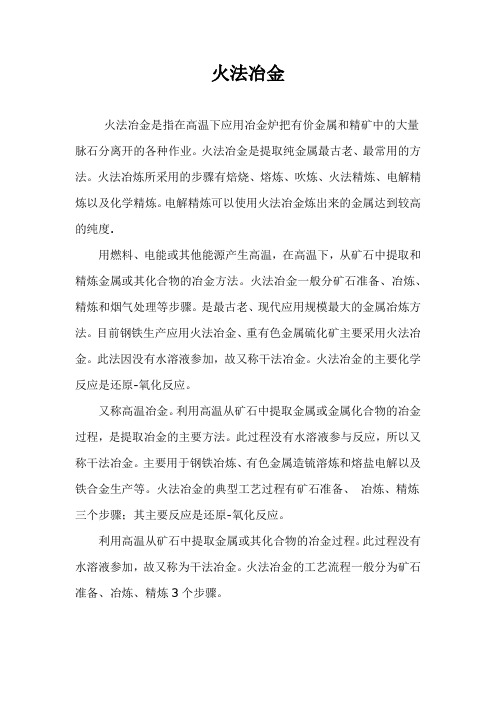
火法冶金火法冶金是指在高温下应用冶金炉把有价金属和精矿中的大量脉石分离开的各种作业。
火法冶金是提取纯金属最古老、最常用的方法。
火法冶炼所采用的步骤有焙烧、熔炼、吹炼、火法精炼、电解精炼以及化学精炼。
电解精炼可以使用火法冶金炼出来的金属达到较高的纯度.用燃料、电能或其他能源产生高温,在高温下,从矿石中提取和精炼金属或其化合物的冶金方法。
火法冶金一般分矿石准备、冶炼、精炼和烟气处理等步骤。
是最古老、现代应用规模最大的金属冶炼方法。
目前钢铁生产应用火法冶金、重有色金属硫化矿主要采用火法冶金。
此法因没有水溶液参加,故又称干法冶金。
火法冶金的主要化学反应是还原-氧化反应。
又称高温冶金。
利用高温从矿石中提取金属或金属化合物的冶金过程,是提取冶金的主要方法。
此过程没有水溶液参与反应,所以又称干法冶金。
主要用于钢铁冶炼、有色金属造锍溶炼和熔盐电解以及铁合金生产等。
火法冶金的典型工艺过程有矿石准备、冶炼、精炼三个步骤;其主要反应是还原-氧化反应。
利用高温从矿石中提取金属或其化合物的冶金过程。
此过程没有水溶液参加,故又称为干法冶金。
火法冶金的工艺流程一般分为矿石准备、冶炼、精炼3个步骤。
①矿石准备。
选矿得到的细粒精矿不易直接加入鼓风炉(或炼铁高炉),须先加入冶金熔剂(能与矿石中所含的脉石氧化物、有害杂质氧化物作用的物质),加热至低于炉料的熔点烧结成块;或添加粘合剂压制成型;或滚成小球再烧结成球团;或加水混捏;然后装入鼓风炉内冶炼。
硫化物精矿在空气中焙烧的主要目的是:除去硫和易挥发的杂质,并使之转变成金属氧化物,以便进行还原冶炼;使硫化物成为硫酸盐,随后用湿法浸取;局部除硫,使其在造锍熔炼中成为由几种硫化物组成的熔锍。
②冶炼。
此过程形成由脉石、熔剂及燃料灰分融合而成的炉渣和熔锍(有色重金属硫化物与铁的硫化物的共熔体)或含有少量杂质的金属液。
有还原冶炼、氧化吹炼和造锍熔炼3种冶炼方式:还原冶炼:是在还原气氛下的鼓风炉内进行。
28种炼钢方法
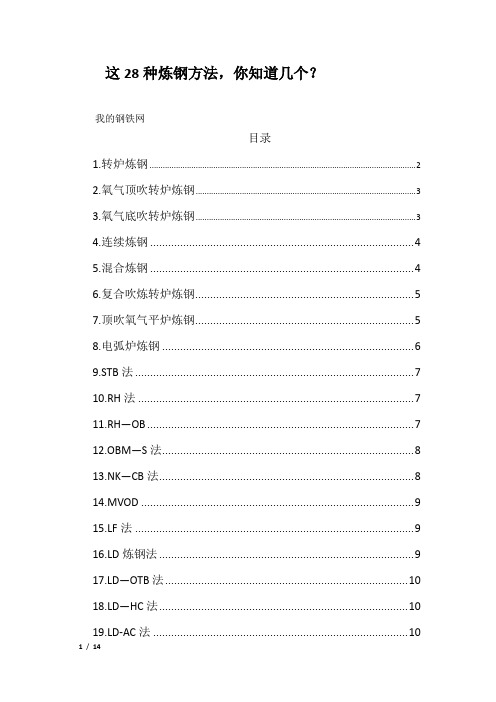
这28种炼钢方法,你知道几个?我的钢铁网目录1.转炉炼钢 (2)2.氧气顶吹转炉炼钢 (3)3.氧气底吹转炉炼钢 (3)4.连续炼钢 (4)5.混合炼钢 (4)6.复合吹炼转炉炼钢 (5)7.顶吹氧气平炉炼钢 (5)8.电弧炉炼钢 (6)9.STB法 (7)10.RH法 (7)11.RH—OB (7)12.OBM—S法 (8)13.NK—CB法 (8)14.MVOD (9)15.LF法 (9)16.LD炼钢法 (9)17.LD—OTB法 (10)18.LD—HC法 (10)19.LD-AC法 (10)20.KS法 (11)21.K—ES法 (11)22.FINKL—VAD法 (11)23.DH法 (12)24.CLU法 (12)25.CAS法 (12)26.CAS—OB法 (13)27.ASEA-SKF法 (13)28.AOD法 (13)1.转炉炼钢一种不需外加热源、主要以液态生铁为原料的炼钢方法。
其主要特点是靠转炉内液态生铁的物理热和生铁内各组分,如碳、锰、硅、磷等与送入炉内的氧气进行化学反应所产生的热量作冶炼热源来炼钢。
炉料除铁水外,还有造渣料(石灰、石英、萤石等);为了调整温度,还可加入废钢以及少量的冷生铁和矿石等。
转炉按炉衬耐火材料性质分为碱性(用镁砂或白云为内衬)和酸性(用硅质材料为内衬);按气体吹入炉内的部分分为底吹顶吹和侧吹;按所采用的气体分为空气转炉和氧气转炉。
酸性转炉不能去除生铁中的硫和磷,须用优质生铁,因而应用范围受到限制。
碱性转炉适于用高磷生铁炼钢,曾在西欧获得较大发展。
空气吹炼的转炉钢,因其含氮量高,且所用的原料有局限性,又不能多配废钢,未在世界范围内得到推广。
2.氧气顶吹转炉炼钢用纯氧从转炉顶部吹炼铁水成钢的转炉炼钢方法,或称LD法;在美国通常称BOF法,也称BOP法。
它是现代炼钢的主要方法。
炉子是一个直立的坩埚状容器,用直立的水冷氧枪从顶部插入炉内供氧。
炉身可倾动。
炉料通常为铁水、废钢和造渣材料;也可加入少量冷生铁和铁矿石。
炼钢厂工艺流程

炼钢厂工艺流程
《炼钢厂工艺流程》
炼钢是一项复杂的工艺,通过各种操作和工序将生铁转化为高质量的钢铁。
炼钢厂工艺流程包括了多个步骤,每一个步骤都非常重要,需要严格控制和操作。
首先,生铁将会被装载到高炉中进行初步冶炼。
在这个阶段,矿石和焦炭会被加入到高炉中,经过高温的燃烧和还原,将生铁的矿石中的杂质转化为炼铁。
随后,炼铁会被送入转炉或电炉中进行精炼,其中杂质将被进一步去除,从而得到高品质的炼钢。
在转炉或电炉中,炼钢师会加入适量的废钢、锰、铬等合金元素,以调整钢铁的化学成分,以满足特定的用途和要求。
随后,炼钢师会通过吹氧和搅拌钢液的方式,控制炉温和杂质的去除,从而得到所需品质的炼钢。
最后,炼钢会被倒入浇注包或连铸机中,进行成形和冷却,得到半成品或成品钢材。
在整个流程中,需要精密的控制和操作,以确保炼钢的质量和性能。
总的来说,《炼钢厂工艺流程》是一个对工艺和操作要求非常严格的工艺,需要炼钢师有着丰富的经验和技术,才能确保生产出高质量的钢材。
炼钢的原理化学方程式

炼钢的原理化学方程式炼钢是一种重要的冶金工艺,通过炼钢可以将生铁中的杂质去除,从而得到高质量的钢材。
炼钢的原理主要是利用化学反应来去除杂质,下面我们就来详细了解一下炼钢的原理和化学方程式。
首先,炼钢的原理是利用氧气与生铁中的杂质发生氧化还原反应。
在炼钢过程中,首先需要将生铁加热至熔化状态,然后通过吹氧等方法向熔融的生铁中通入氧气。
氧气与生铁中的杂质发生化学反应,将杂质氧化成氧化物,从而使其脱离熔融的金属,最终形成渣浆。
这样就可以将杂质从生铁中去除,得到高质量的钢材。
其次,炼钢的化学方程式主要包括氧化反应和还原反应两种类型。
在氧化反应中,氧气与生铁中的碳、硅、锰等杂质发生氧化反应,生成相应的氧化物。
以碳为例,其氧化反应方程式为:Fe + C + O2 → FeO + CO2。
在这个方程式中,生铁中的碳与氧气发生反应,生成氧化铁和二氧化碳。
通过这样的氧化反应,可以将生铁中的碳氧化成氧化物,从而去除碳的杂质。
另外,还原反应也是炼钢过程中的重要化学反应。
在炼钢过程中,还原剂通常是氧化铁,它可以与生铁中的氧化物反应,将氧化物还原成金属。
以氧化铁为例,其还原反应方程式为:FeO + C → Fe + CO。
在这个方程式中,氧化铁与碳发生反应,生成铁和一氧化碳。
通过这样的还原反应,可以将生铁中的氧化物还原成金属,从而得到高质量的钢材。
总的来说,炼钢的原理化学方程式是通过氧化还原反应去除生铁中的杂质,从而得到高质量的钢材。
通过合理控制炼钢过程中的氧化还原反应,可以有效去除生铁中的杂质,提高钢材的质量。
希望通过本文的介绍,能够对炼钢的原理和化学方程式有更深入的了解。
4、转炉炼钢工艺制度(下)
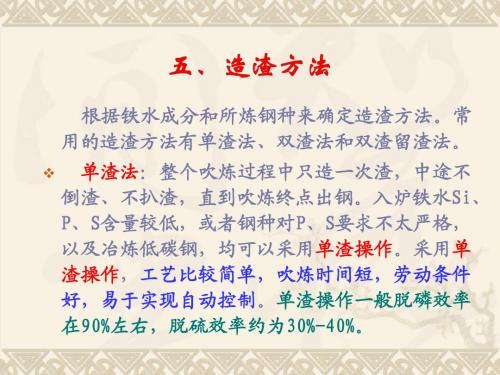
六、温度制度
在吹炼一炉钢的过程中,需要正确控制温度。
温度制度主要是指炼钢过程温度控制和终点温
度控制。
转炉吹炼过程的温度控制相对比较复杂,如 何通过加冷却剂和调整枪位,使钢水的升温和 成分变化协调起来,同时达到吹炼终点的要求, 是温度控制的关键。
热量来源:铁水的物理热和化学热,它 们约各点热量来源的一半。 热量消耗:习惯上转炉的热量消耗可分 为两部分,一部分直接用于炼钢的热量, 即用于加热钢水和炉渣的热量;一部分未 直接用于炼钢的热量,即废气、烟尘带走 的热量,炉口炉壳的散热损失和冷却剂的 吸热等。
双渣留渣法:将双渣法操作的高碱度、高氧 化铁、高温、流动性好的终渣留一部分在炉内, 然后在吹炼第一期结束时倒出,重新造渣。此 法的优点是可加速下炉吹炼前期初期渣的形成, 提高前期的去磷、去硫率和炉子热效率,有利 于保护炉衬,节省石灰用量。采用留渣操作时, 在兑铁水前首先要加废钢稠化冷凝熔渣,当炉 内无液体渣时才可兑入铁水,以避免引发喷溅。
加速渣料的熔化
加速石灰溶解的措施 1)适宜的炉渣成分 渣中的(FeO)是石灰溶解的基本熔剂,原因在于: (1)(FeO)可与CaO及2CaO· SiO2作用生成低熔点的盐,能有效 地降低炉渣的粘度,改善石灰溶解的外部传质条件; (2)(FeO)是碱性氧化渣的表面活性物质,可以改善炉渣对石 灰的润湿性,有利于熔渣向石灰表面的孔中渗透,增大二者之间的 接触面积; (3)Fe2+及O2-的半径是同类中最小的,扩散能力最强; (4)有足够的(FeO)存在时,可以避免石灰表面生成C2S而有 利于石灰的溶解。 因此,吹炼操作中应合理地控制枪位,始终保持较高的 (FeO)含量。(MnO)对石灰溶解的影响与(FeO)类似,生产中可 在渣料中配加适量锰矿。
- 1、下载文档前请自行甄别文档内容的完整性,平台不提供额外的编辑、内容补充、找答案等附加服务。
- 2、"仅部分预览"的文档,不可在线预览部分如存在完整性等问题,可反馈申请退款(可完整预览的文档不适用该条件!)。
- 3、如文档侵犯您的权益,请联系客服反馈,我们会尽快为您处理(人工客服工作时间:9:00-18:30)。
这28种炼钢方法,你知道几个?我的钢铁网目录1.转炉炼钢 (2)2.氧气顶吹转炉炼钢 (3)3.氧气底吹转炉炼钢 (3)4.连续炼钢 (4)5.混合炼钢 (4)6.复合吹炼转炉炼钢 (5)7.顶吹氧气平炉炼钢 (5)8.电弧炉炼钢 (6)9.STB法 (7)10.RH法 (7)11.RH—OB (7)12.OBM—S法 (8)13.NK—CB法 (8)14.MVOD (9)15.LF法 (9)16.LD炼钢法 (9)17.LD—OTB法 (10)18.LD—HC法 (10)19.LD-AC法 (10)20.KS法 (11)21.K—ES法 (11)22.FINKL—VAD法 (11)23.DH法 (12)24.CLU法 (12)25.CAS法 (12)26.CAS—OB法 (13)27.ASEA-SKF法 (13)28.AOD法 (13)1.转炉炼钢一种不需外加热源、主要以液态生铁为原料的炼钢方法。
其主要特点是靠转炉内液态生铁的物理热和生铁内各组分,如碳、锰、硅、磷等与送入炉内的氧气进行化学反应所产生的热量作冶炼热源来炼钢。
炉料除铁水外,还有造渣料(石灰、石英、萤石等);为了调整温度,还可加入废钢以及少量的冷生铁和矿石等。
转炉按炉衬耐火材料性质分为碱性(用镁砂或白云为内衬)和酸性(用硅质材料为内衬);按气体吹入炉内的部分分为底吹顶吹和侧吹;按所采用的气体分为空气转炉和氧气转炉。
酸性转炉不能去除生铁中的硫和磷,须用优质生铁,因而应用范围受到限制。
碱性转炉适于用高磷生铁炼钢,曾在西欧获得较大发展。
空气吹炼的转炉钢,因其含氮量高,且所用的原料有局限性,又不能多配废钢,未在世界范围内得到推广。
2.氧气顶吹转炉炼钢用纯氧从转炉顶部吹炼铁水成钢的转炉炼钢方法,或称LD法;在美国通常称BOF法,也称BOP法。
它是现代炼钢的主要方法。
炉子是一个直立的坩埚状容器,用直立的水冷氧枪从顶部插入炉内供氧。
炉身可倾动。
炉料通常为铁水、废钢和造渣材料;也可加入少量冷生铁和铁矿石。
通过氧枪从熔池上面向下吹入高压的纯氧(含O299.5%以上),氧化去除铁水中的硅、锰、碳和磷等元素,并通过造渣进行脱磷和脱硫。
各种元素氧化所产生的热量,加热了熔池的液态金属,使钢水达到现定的化学成分和温度。
它主要用于冶炼非合金钢和低合金钢;但通过精炼手段,也可用于冶炼不锈钢等合金钢。
3.氧气底吹转炉炼钢通过转炉底部的氧气喷嘴把氧气吹入炉内熔池,使铁水冶炼成钢的转炉炼钢方法。
其特点是;炉子的高度与直径比较小;炉底较平并能快速拆卸和更换;用风嘴、分配器系统和炉身上的供氧系统代替氧气顶吹转炉的氧枪系统。
由于吹炼平稳、喷溅少、烟尘量少、渣中氧化铁含量低,因此氧气底吹转炉的金属收得率比氧气顶吹转炉的高1%~2%;采用粉状造渣料,由于颗粒细、比表面大,增大了反应界面,因此成渣快,有利于脱硫和脱磷。
此法特别适用于吹炼中磷生铁,因此在西欧用得最广。
4.连续炼钢不分炉次地将原料(铁水、废钢)从炉子一端不断地加入,将成品(钢水)从炉子的另一端不断地流出的炼钢方法。
连续炼钢工艺的设想早在19世纪就已出现。
由于这种工艺具有设备小、工艺过程简单而且稳定等潜在优越性,几十年来许多国家都作了各种各样方法的大量试验,其中主要有槽式法、喷雾法和泡沫法三类,但迄今为止都尚未投入工业化生产。
5.混合炼钢用一个炉子炼钢、另一个电炉炼还原渣或还原渣与合金,然后在一定的高度下进行冲混的炼钢方法。
用此法处理平炉、转炉及电炉所炼钢水,可提高钢的质量。
冲混可增加渣、钢间的接触面积,加速化学反应以及脱氧、脱硫,并有吸附和聚合气体及夹杂物的作用,从而提高钢的纯结度和质量。
6.复合吹炼转炉炼钢在顶吹和底吹氧气转炉炼钢法的基础上,综合两者的优点并克服两者的缺点而发展起来的新炼钢方法,即在原有顶吹转炉底部吹入不同气体,以改善熔池搅拌。
目前,世界上大多数国家用这种炼钢法,并发展了多种类型的复吹转炉炼钢技术,常见的如英国钢公司开发的以空气N2或Ar2作底吹气体、以N2作冷却气体的熔池搅拌复吹转炉炼钢法—BSC—BAP 法,德国克勒克纳—马克斯冶金厂开发的用天然保护底枪、从底部向熔池分别喷入煤和氧的KMS法、日本川崎钢铁公司开发的将占总氧量30%的氧气混合石灰粉一道从炉底吹入熔池的K—BOP法以及新日本钢铁公司开发的将占总氧量10%~20%的氧气从底部吹入,并用丙烷或天然气冷却炉底喷嘴的LD—OB法等。
7.顶吹氧气平炉炼钢从50年代中期开始,在平炉生产中采用1~5支水冷氧枪由炉顶插入熔炼室,直接向熔池吹氧的炼钢方法。
该法改善了熔池反应的动力学条件,使碳氧反应的热效应由原来的吸热变为放热,并改善了热工条件;生产率大幅度地得到提高。
8.电弧炉炼钢利用电弧热效应熔炼金属和其他物料的一种炼钢方法。
炼钢用三相交流电弧炉是最常见的直接加热电弧炉。
炼钢过程中,由于炉内无可燃气体,可根据工艺要求,形成氧化性或还原性气氛和条件,故可以用于冶炼优质非合金钢和合金钢。
按电炉每吨炉容量的大小,可将电弧炉分为普通功率电弧炉、高功率电弧炉和超高功率电弧炉。
电弧炉炼钢向高功率、超高功率发展的目的是为了缩短冶炼时间、降低电耗、提高生产率、降低成本。
随着高功率和超高功率电炉的出现,电弧炉已成为熔化器,一切精炼工艺都在精炼装置内进行。
近十年来直流电弧炉由于电极消耗低、电压波动小和噪音小而得到迅速发展,可用于冶炼优质钢和铁合金。
9.STB法原文为SumitomoTopandBottomblowingprocess,由日本住友金属公司开发的顶底复吹转炉炼钢法。
该法综合了氧气顶吹转炉炼钢法和氧气底吹转炉炼钢法两者的优点。
用于吹炼低碳钢,脱磷效果好且成本下降显著。
所用的底吹气体为O2、CO2、N2等。
在STB法基础上又开发了从顶部喷吹粉末的STB—P法,进一步改善了高碳钢的脱磷条件,并用于精炼不锈钢。
10.RH法又称循环法真空处理。
由德国Ruhrstahl/Heraeus二公司共同开发。
真空室下方装有两个导管,插入钢水,抽真空后钢水上升至一定高度,再在上升管吹入惰性气体Ar、Ar上升带动钢液进入真空室接受真空处理,随后经另一导管流回钢包。
真空室上装有加合金的加料系统。
此法已成为大容量钢包(>80t)的钢水主要真空处理方法。
11.RH—OBRH吹氧法是在真空循环脱气(RH)法中加上吹氧操作(OxygenBlowing)来升温。
用于精炼不锈钢,是利用减压下可优先进行脱碳反应;用于精炼普通钢则可减轻转炉负荷。
也可采用加铝升温。
12.OBM—S法原文为OxygenBottomMaxhutte—Scarp,由德国Maxhutte-Klockner厂发明的以天然气或丙烷作底吹氧枪冷却介质的氧气底吹转炉炼钢法。
OBM—S是在OBM氧气底吹转炉的炉帽上安装侧吹氧枪,底部氧枪吹煤气、天然气预热废钢,从而达到增加废钢比的目的。
13.NK—CB法原文为NKKCombinedBlowingSystem,由日本钢管公司于1973年建立的顶底复吹转炉炼钢法,即在顶吹的同时,从炉底吹入少量气体(Ar,CO2,N2),以加强钢渣的搅拌,并控制钢水中的CO分压。
该法采用多孔砖喷嘴,用于炼低碳钢可降低成本;用于炼高碳钢则有利于脱磷。
该法应与铁水预处理工艺结合起来。
14.MVOD在VAD法的设备上增设水冷氧枪,使之在真空下可吹氧脱碳的方法,由于真空下脱碳为放热反应,可省去VAD法的真空加热措施。
操作过程与VOD法相同。
15.LF法原文为LadleFurnace,是1971年日本特殊钢公司(大同钢特殊钢公司)开发的钢包炉精炼法。
其设备和工艺由氩气搅拌、埋弧加热和合金加料系统组合而成。
这种工艺的优点是:能精确地控制钢水化学成分和温度;降低夹杂物含量;合金元素收得率高。
LF炉已成为炼钢炉与连铸机之间不可缺少的一种炉外精炼设备。
16.LD炼钢法1952年奥钢联林茨(Linz)厂与奥地利阿尔卑斯矿冶公司多纳维茨(Donawitz)厂最早在工业上开发成功的氧气顶吹转炉炼钢法,并以该两厂的第一个字母而命名。
该法问世后在全世界范围迅速得到推广。
美国称此法为BOF或BOP法,即BasicOxygenFurnace或Process的简称。
详见氧气顶吹,转炉。
17.LD—OTB法原文为LD—OxgyenTopanBottomProcess,由日本神户制钢公司加古川厂开发的顶底复合吹炼转炉炼钢工艺。
其特点是使用了专门的底吹单环缝形喷嘴(SA喷嘴),因而底吹气体能控制在很宽的范围内。
底部吹入惰性气体。
18.LD—HC法原文为LD—HainautSaubreCRM,系比利时开发的用于吹炼高磷铁水的顶底复合吹炼转炉炼钢法,即LD底吹氧,用碳氢化合物保护喷嘴。
19.LD-AC法原文为LD-Arbed-CentreNational,法国钢铁研究所开发的顶吹氧气喷石灰粉炼钢法,用于吹炼高磷铁水。
原文KlocknerSteelmaking,系采用100%固体料操作的底部喷煤粉氧气转炉炼钢工艺。
底吹氧比率为60%~100%。
21.K—ES法将底吹气体技术、二次燃烧技术和喷煤粉技术结合起来的电弧炉炼钢法,它是由日本东京炼钢公司和德国Kiokner公司共同开发的技术,可以以煤代电。
22.FINKL—VAD法电弧加热钢包脱气法或称真空电弧脱气法。
其特点是在真空室的盖上增设有电弧加热装置,并在真空下用氩气搅拌。
该法的脱气效果稳定,而且能脱硫、脱碳和加入大量合金。
设备主要由真空室、电弧加热系统、合金加料装置、抽真空系统及液压系统组成。
德国DortmundHorder联合冶金公司开发的一种真空处理装置。
内衬耐火材料的真空室,下部装上有耐火衬的导管插入钢包,真空室或钢包周期性地放下与提升,使一部分钢水进入真空室,处理后返回钢包。
上部有加合金料装置和真空加热保温装置。
目前已不再建造这种设备。
24.CLU法一种不锈钢的精炼方法。
其原理与AOD法相同,物点是采用水蒸气代替氩气。
该方法是法国Creusot-Loire公司和瑞典Uddeholm公司共同研制成功的,并于1973年正式投入生产。
水蒸气与钢液接触后分解为H2和O2;H2使CO分压降低。
同时,该分解反应为吸热反应,因而可抑制钢液温度上升。
但铬的氧化烧损比AOD法的严重。
25.CAS法原文为Compositionadjustmentbysealedargonbubbling,是在氩气密封下进行合金成分微调的炉外精炼方法。
该法由钢包底部吹氩,将渣排开后,下降浸渍罩,继续吹氩,然后加合金微调成分。
其优点是可精确控制成分,且合金收得率高。
26.CAS—OB法原文为Compositonadjustmentbysealedargonbubblingwithoxygenblowing,是在CAS设备上增设吹氧枪的炉外精炼方法。