7塔板结构设计
板式塔(筛板塔)设计教材
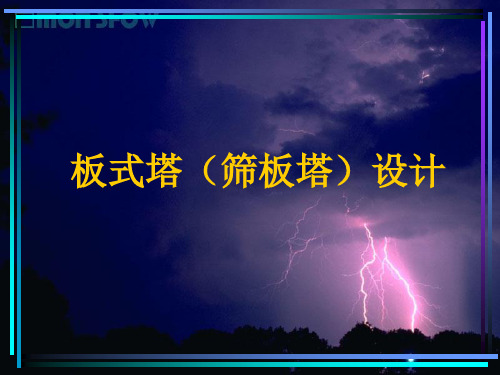
u
0.2
u f C f 20 20
式中
f
L V V
0.5
—— 气体负荷因子, m/s;可由 u
查取 图3
C f 20—— 液相表面张力,mN/m
V 、 L 是以塔内气体流通面积,即塔的横截面积减去降 注意: uAfT –Af )为依据计算的。 液管面积(
4. 塔和塔板主要尺寸的设计
4.1 塔和塔板设计的主要依据
进行塔和塔板设计时,所依据的主要参数是: 汽相 流量 VS ( m³ /s ), 密度 ρV ( kg/m³) 液相 流量 LS ( m³ /s ), 密度 ρL ( kg/m³) 表面张力 σ ( mN/m ) 注意:由于各块塔板的组成和温度不同,所以各块塔板 上的上述参数均不同,设计时应取平均值。具体方法如下: (1) 若V、L变化不大,可以精馏段或提馏段的平均值为 代表进行设计. (2) 若V、L变化较大,应分段处理,各段分别取平均值 进行设计。
4.2塔板的设计参数
筛板塔设计必须确定的主要结构参数有(参阅 图 2 ): (1)塔板直径D; (2)板间距HT; (3)溢流堰的型式,长度 lW 和高度 hw; (4)降液管型式、降液管底部与塔板间的距离ho; (5)液体进、出口安定区的宽度Ws’、Ws ,边缘 区宽度Wc; (6)筛孔直径do,孔间距t。
3.2 回流比的选定
选择原则:使塔的设备费用和操作费用的总和最低,
同时应考虑到操作时的调节弹性。
选择方法:
(1) 参考生产现场所提供的回流比数据; (2) 回流比取最小回流比Rmin的1.2~2倍; (3) 先求最少理论板数 Nmin , 以理论板数为Nmin 的两倍求取回流比R; (4) 作出回流比R和理论板数N的曲线图,在曲线 图上确定合适的回流比R。
板式塔塔盘设计
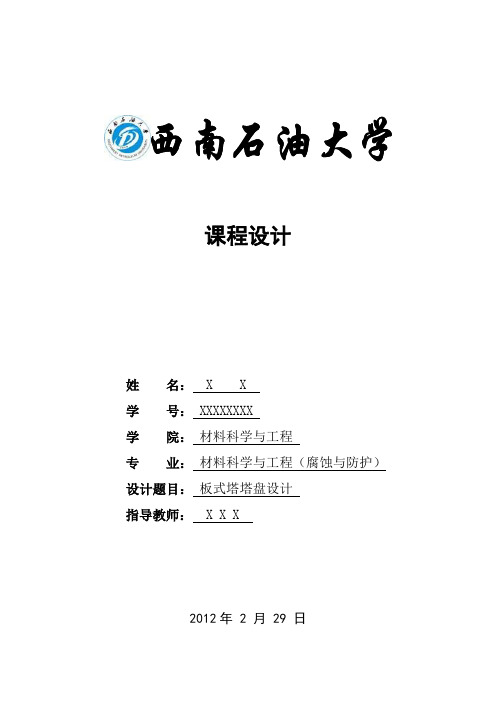
塔盘是气液两相接触传质的场所,为提高塔盘性能,采用各种形式塔盘。 1)泡罩塔 组成:升气管和泡罩 优点:塔盘操作弹性大,塔效率也比较高,不易堵 缺点:结构复杂,制造成本高,塔盘阻力大但生产能力不大 2)筛板塔盘 塔盘上开圆孔,孔径:3-8 mm,大孔径筛板:12-25 mm。 3)浮阀塔盘 优点:浮阀根据气体流量,自动调节开度,提高了塔盘的操作弹性、降低塔盘的压降,同时 具有较高塔盘效率,在生产中得到广泛的应用 缺点:浮阀易脱落或损坏 浮阀塔具有性能稳定、操作弹性大、塔盘效率高的优点,但是在处理粘稠度较大的物料方面 不及泡罩塔,在结构、生产能力、塔盘效率、压力降等方面不及筛板塔。 浮阀塔具有下列特点: 1、处理能力大,比同塔径的泡罩塔可增大 20~40%,接近于筛板塔 2、操作弹性大,一般约为 5~9,比筛板塔的操作弹性要大得多 3、塔盘效率高,比泡罩塔高 15%左右,与筛板塔接近 4、压降小,在常压塔中每块盘的压降一般为 400~660Pa 5、液面落差小 6、使用周期长。粘度稍大一些的液体也能正常操作
四、精馏塔的总体设计及结构设计 .................................... 17 1、确定塔设备的型式 ............................................ 17 2、确定塔板数目 ................................................ 17 3、拟定管口方位 ................................................ 17 4、结构设计 .................................................... 17 (1)零部件材料的选取....................................... 17 (2)塔盘结构............................................... 18 (3)工艺接管............................................... 18 (4)压力容器法兰和接管法兰................................. 18 (5)法兰密封垫片的选取..................................... 19 (6)裙座选取............................................... 19 (7)人孔设置............................................... 19 (8)手孔设置............................................... 19 (9)视镜和液位计的选取..................................... 19
化工原理板式塔设计
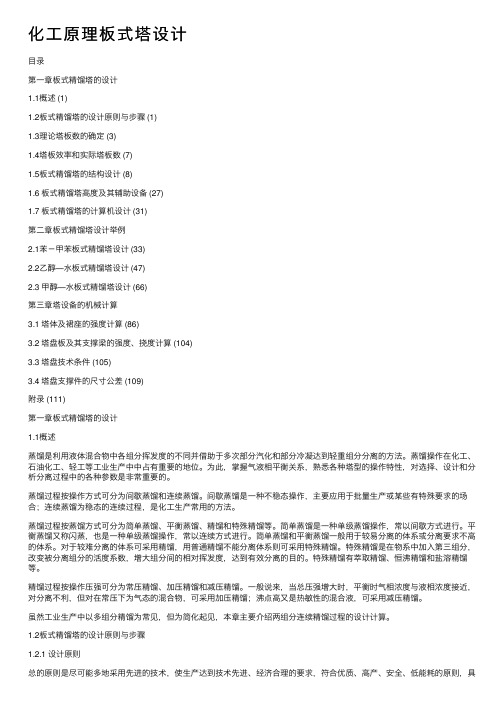
化⼯原理板式塔设计⽬录第⼀章板式精馏塔的设计1.1概述 (1)1.2板式精馏塔的设计原则与步骤 (1)1.3理论塔板数的确定 (3)1.4塔板效率和实际塔板数 (7)1.5板式精馏塔的结构设计 (8)1.6 板式精馏塔⾼度及其辅助设备 (27)1.7 板式精馏塔的计算机设计 (31)第⼆章板式精馏塔设计举例2.1苯-甲苯板式精馏塔设计 (33)2.2⼄醇—⽔板式精馏塔设计 (47)2.3 甲醇—⽔板式精馏塔设计 (66)第三章塔设备的机械计算3.1 塔体及裙座的强度计算 (86)3.2 塔盘板及其⽀撑梁的强度、挠度计算 (104)3.3 塔盘技术条件 (105)3.4 塔盘⽀撑件的尺⼨公差 (109)附录 (111)第⼀章板式精馏塔的设计1.1概述蒸馏是利⽤液体混合物中各组分挥发度的不同并借助于多次部分汽化和部分冷凝达到轻重组分分离的⽅法。
蒸馏操作在化⼯、⽯油化⼯、轻⼯等⼯业⽣产中中占有重要的地位。
为此,掌握⽓液相平衡关系,熟悉各种塔型的操作特性,对选择、设计和分析分离过程中的各种参数是⾮常重要的。
蒸馏过程按操作⽅式可分为间歇蒸馏和连续蒸馏。
间歇蒸馏是⼀种不稳态操作,主要应⽤于批量⽣产或某些有特殊要求的场合;连续蒸馏为稳态的连续过程,是化⼯⽣产常⽤的⽅法。
蒸馏过程按蒸馏⽅式可分为简单蒸馏、平衡蒸馏、精馏和特殊精馏等。
简单蒸馏是⼀种单级蒸馏操作,常以间歇⽅式进⾏。
平衡蒸馏⼜称闪蒸,也是⼀种单级蒸馏操作,常以连续⽅式进⾏。
简单蒸馏和平衡蒸馏⼀般⽤于较易分离的体系或分离要求不⾼的体系。
对于较难分离的体系可采⽤精馏,⽤普通精馏不能分离体系则可采⽤特殊精馏。
特殊精馏是在物系中加⼊第三组分,改变被分离组分的活度系数,增⼤组分间的相对挥发度,达到有效分离的⽬的。
特殊精馏有萃取精馏、恒沸精馏和盐溶精馏等。
精馏过程按操作压强可分为常压精馏、加压精馏和减压精馏。
⼀般说来,当总压强增⼤时,平衡时⽓相浓度与液相浓度接近,对分离不利,但对在常压下为⽓态的混合物,可采⽤加压精馏;沸点⾼⼜是热敏性的混合液,可采⽤减压精馏。
《立体传质塔板》课件

2023-2026
END
THANKS
感谢观看
KEEP VIEW
REPORTING
2023-2026
ONE
KEEP VIEW
立体传质塔板
REPORTING
CATALOGUE
目 录
• 立体传质塔板简介 • 立体传质塔板的设计与优化 • 立体传质塔板的操作与维护 • 立体传质塔板的发展趋势与展望 • 立体传质塔板的案例分析
PART 01
立体传质塔板简介
定义与特点
定义
立体传质塔板是一种新型塔板, 通过立体结构设计,实现高效传 质过程。
2
通过立体传质塔板,石油化工企业能够实现高效 、低能耗的分离过程,提高产品质量和收率。
3
立体传质塔板在石油化工行业中的应用还包括处 理重油、裂化气等复杂组分,降低环境污染。
应用案例二:制药行业
在制药行业中,立体传质塔板主 要用于分离和纯化药物中间体和
原料药。
通过立体传质塔板,制药企业能 够实现高纯度、高收率的分离过
生产的稳定性和连续性。
易维护
塔板设计应便于安装、拆卸和 维修,降低维护成本。
环保性
塔板设计应符合环保要求,减 少能耗和物耗,降低三废排放
。
塔板结构
01
02
03
折流式塔板
折流式塔板通过液体多次 折流流动,增加气液接触 时间,提高传质效率。
筛孔式塔板
筛孔式塔板通过液体通过 筛孔分散成细小液滴,增 加气液接触面积,提高传 质效率。
对设备运行和维护情况进行记 录,及时报告异常情况。
常见问题与解决方案
(完整word)板式塔设计原理
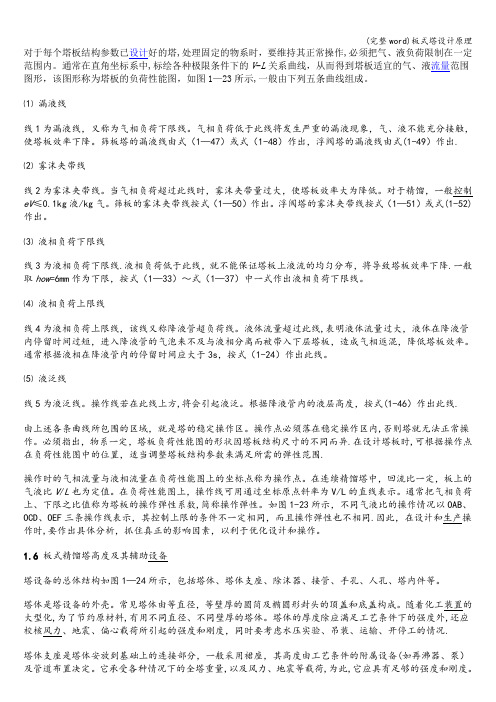
对于每个塔板结构参数已设计好的塔,处理固定的物系时,要维持其正常操作,必须把气、液负荷限制在一定范围内。
通常在直角坐标系中,标绘各种极限条件下的V-L关系曲线,从而得到塔板适宜的气、液流量范围图形,该图形称为塔板的负荷性能图,如图1—23所示,一般由下列五条曲线组成。
⑴ 漏液线线1为漏液线,又称为气相负荷下限线。
气相负荷低于此线将发生严重的漏液现象,气、液不能充分接触,使塔板效率下降。
筛板塔的漏液线由式(1—47)或式(1-48)作出,浮阀塔的漏液线由式(1-49)作出.⑵ 雾沫夹带线线2为雾沫夹带线。
当气相负荷超过此线时,雾沫夹带量过大,使塔板效率大为降低。
对于精馏,一般控制eV≤0.1kg液/kg气。
筛板的雾沫夹带线按式(1—50)作出。
浮阀塔的雾沫夹带线按式(1—51)或式(1-52)作出。
⑶ 液相负荷下限线线3为液相负荷下限线.液相负荷低于此线,就不能保证塔板上液流的均匀分布,将导致塔板效率下降.一般取how=6mm作为下限,按式(1—33)~式(1—37)中一式作出液相负荷下限线。
⑷ 液相负荷上限线线4为液相负荷上限线,该线又称降液管超负荷线。
液体流量超过此线,表明液体流量过大,液体在降液管内停留时间过短,进入降液管的气泡来不及与液相分离而被带入下层塔板,造成气相返混,降低塔板效率。
通常根据液相在降液管内的停留时间应大于3s,按式(1-24)作出此线。
⑸ 液泛线线5为液泛线。
操作线若在此线上方,将会引起液泛。
根据降液管内的液层高度,按式(1-46)作出此线.由上述各条曲线所包围的区域,就是塔的稳定操作区。
操作点必须落在稳定操作区内,否则塔就无法正常操作。
必须指出,物系一定,塔板负荷性能图的形状因塔板结构尺寸的不同而异.在设计塔板时,可根据操作点在负荷性能图中的位置,适当调整塔板结构参数来满足所需的弹性范围.操作时的气相流量与液相流量在负荷性能图上的坐标点称为操作点。
在连续精馏塔中,回流比一定,板上的气液比V/L也为定值。
塔板结构及辅助设备设计

画出原则流程图(带控制点)
2.图例 图例是将物料流程图中画出的有关管线、阀门、设备附件、 计量一控制仪表等图形用文字予以说明。 3.图签 图签是写出图名、设计单位、设计人员、制图人员、审 核人员(签名)、图纸比例尺、图号等项内容的一份表格, 其位置在流程图有下角。 带控制点的工艺流程图一般是由工艺专业人员和自控 专业人员合作绘制出来的。作为化工原理课程设计只要 求能标绘出测量点位置即可。
易维持均匀。(how=6mm)。
3、最大液量线:液体流量过大则降液管内液体停
留时间过短(t=5s)
4、液泛线:降液管内的泡沫层高必须小于板间距与
溢流堰高之和(Hd/Φ =HT+hw)
5、雾沫夹带线:气体流量过大可使液沫夹带过量,
塔板效率即严重下降。(ev=0.1)
弹性的计算及调整
上弹性K上>1.5 下弹性K下>1.5
4.2.1
板面布置
5) 底隙h0:一般应低于外堰高6mm。
h0< hW-6mm,防止气体进入降液管;一般不宜小于 20-25mm ,以防堵塞。
6)筛孔布置: 孔径d0: 3-8mm 孔间距:t/d0取2.5-5,实际取3-4 板厚:碳钢3-4mm,不锈钢2-3mm 筛孔面积A0, 开孔区面积Aa 孔数n,开孔按正三角形排列
塔板校核需要输入的数据
表3 筛板塔预选参数 mm 秒
(1)清液层高度 (2)最少停留时间
塔板校核要求
精馏段第一块板和最后一块板的结构完
全相同;
提馏段第一块板和最后一块板的结构完
全相同;
精馏段和提馏段塔板结构可以不同
6、辅助设备计算
P101 E101 E102 C101 进料泵 进料预热器 再沸器 精馏塔
板式塔主要类型得结构与特点

板式塔主要类型得结构与特点工业上常用得板式塔有:泡罩塔、浮阀塔、筛板塔、穿流栅孔板塔浮阀塔具有得优点:生产能力大,塔板效率高,操作弹性大,结构简单,安装方便。
二、板式塔得流体力学特性1、塔内气、液两相得流动A 使气液两相在塔板上进行充分接触以增强传质效果B 使气液两相在塔内保持逆流,并在塔板上使气液量相保持均匀得错流接触,以获得较大得传质推动力。
2、气泡夹带:液体在下降过程中,有一部分该层板上面得气体被带到下层板上去,这种现象称为气泡夹带。
3、液(雾)沫夹带:气体离开液层时带上一些小液滴,其中一部分可能随气流进入上一层塔板,这种现象称为液(雾)沫夹带。
4、液面落差液体从降液管流出得横跨塔板流动时,必须克服阻力,故进口一侧得液面将比出口这一侧得高。
此高度差称为液面落差。
液面落差过大,可使气体向上流动不均,板效率下降。
5、气体通过塔板得压力降压力降得影响:A 气体通过塔板得压力降直接影响到塔低得操作压力,故此压力降数据就是决定蒸馏塔塔底温度得主要依据。
B 压力降过大,会使塔得操作压力改变很大。
C 压力降过大,对塔内气液两相得正常流动有影响。
压力降:ΔPP =ΔPC+ΔPL+ΔPδ塔板本身得干板阻力ΔPC板上充气液层得静压力ΔPL液体得表面张力ΔPδ折合成塔内液体得液柱高度M,则ΔPP /ρLg=ΔPC/ρLg +ΔPL/ρLg +ΔPδ/ρLg即hp =hc+hL+hδ浮阀塔得压力降一般比泡罩塔板得小,比筛板塔得大。
在正常操作情况,塔板得压力降以290—490 N/m2、在减压塔中为了减少塔得真空度损失,一般约为98—245Pa 通常应在保证较高塔板效率得前提下,力求减少塔板压力降,以降低能耗及改善塔得操作性能。
6、液泛(淹塔)汽液量相中之一得流量增大到某一数值,上、下两层板间得压力降便会增大到使降液管内得液体不能畅顺地下流。
当降液管内得液体满到上一层塔板溢流堰顶之后,便漫但上层塔板上去,这种现象,称为液泛(淹塔)如气速过大,便有大量液滴从泡沫层中喷出,被气体带到上一层塔板,或有大量泡沫生成。
(完整)板式塔
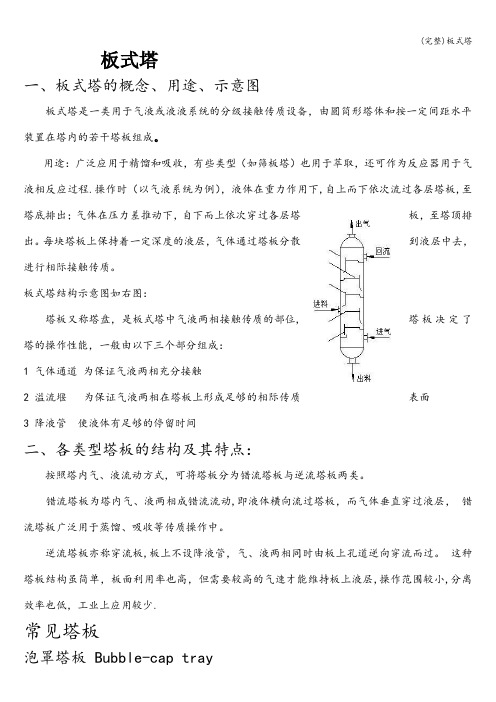
板式塔一、板式塔的概念、用途、示意图板式塔是一类用于气液或液液系统的分级接触传质设备,由圆筒形塔体和按一定间距水平装置在塔内的若干塔板组成。
用途:广泛应用于精馏和吸收,有些类型(如筛板塔)也用于萃取,还可作为反应器用于气液相反应过程.操作时(以气液系统为例),液体在重力作用下,自上而下依次流过各层塔板,至塔底排出;气体在压力差推动下,自下而上依次穿过各层塔板,至塔顶排出。
每块塔板上保持着一定深度的液层,气体通过塔板分散到液层中去,进行相际接触传质。
板式塔结构示意图如右图:塔板又称塔盘,是板式塔中气液两相接触传质的部位,塔板决定了塔的操作性能,一般由以下三个部分组成:1 气体通道为保证气液两相充分接触2 溢流堰为保证气液两相在塔板上形成足够的相际传质表面3 降液管使液体有足够的停留时间二、各类型塔板的结构及其特点:按照塔内气、液流动方式,可将塔板分为错流塔板与逆流塔板两类。
错流塔板为塔内气、液两相成错流流动,即液体横向流过塔板,而气体垂直穿过液层,错流塔板广泛用于蒸馏、吸收等传质操作中。
逆流塔板亦称穿流板,板上不设降液管,气、液两相同时由板上孔道逆向穿流而过。
这种塔板结构虽简单,板面利用率也高,但需要较高的气速才能维持板上液层,操作范围较小,分离效率也低,工业上应用较少.常见塔板泡罩塔板 Bubble-cap tray泡罩塔塔板上的主要部件是泡罩。
罩内覆盖着一段很短的升气管,升气管的上口高于罩下沿的小孔或齿缝。
塔下方的气体经升气管进入罩内之后,折向下到达罩与管之间的环形空隙,然后从罩下沿的小孔或齿 缝分散气泡而进入板上的液层。
优点:弹性大、操作稳定可靠。
缺点:结构复杂,成本高,压降大.对于大直径塔,塔板液面落差大,导致塔板操作不均匀。
现状:近二、三十年来已趋于淘汰三、板式塔的工艺设计筛板塔化工设计计算 (1)塔的有效高度 Z已知:实际塔板数 N P ; 塔板间距 H T ;有效塔高:塔体高度=有效高+顶部+底部+其他塔板间距和塔径的经验关系:(2)塔径确定原则: 防止过量液沫夹带液泛 步骤: 先确定液泛气速 uf (m/s ); 然后选设计气速 u ; 最后计算塔径 D.① 液泛气速pT N H Z ⋅=VVLf C u ρρρ-=2.02020⎪⎭⎫⎝⎛=σC CC :气体负荷因子,与 HT 、 液体表面张力和两相接触状况有关. 两相流动参数 FLV :② 选取设计气速 u 选取泛点率: u / u f一般液体, 0.6 ~0。
板式塔及其设计计算

筛孔气速:
u0
qVV S A0
筛孔数: n A0 Aa 2 2 0.785 d 0 d0 4
(6) 塔板的校核
对初步设计的结果进行调整和修正。
① 液沫夹带量校核 单位质量(或摩尔)气体所夹带的液体质量(或摩尔) ev : kg 液体 / kg气体,或 kmol液体 / kmol气体 单位时间夹带到上层塔板的液体质量(或摩尔) e:
《化工原理》电子教案
—— 板式塔及其设计计算
大连理工大学化工原理教研室 研制
6.10 板 式 塔 6.10.1 板式塔结构及性能
(1) 板式塔结构
功能:为混合物的气、液两相提供多级的充分、有效的接触
与及时、完全分离的条件。
塔顶气相
回流液 进料
塔底液相
汽、液两相接触方式
全塔:逆流接触
塔板上:错流接触
C20 uf
V L V
0.3
0.15
0.Байду номын сангаас1 0.01
0.02 0.03 0.04
FLV
0.07 0.1
qVL s qVV s
0.2
0.3 0.4
0.7 1.0
l v
筛板塔泛点关联图
② 选取设计气速 u
选取泛点率: u / uf
一般液体, 0.6 ~0.8 易起泡液体,0.5 ~ 0.6 设计气速 u = 泛点率 ×uf ③ 计算塔径 D 所需气体流通截面积 塔截面积: AT
6.10.3 常用塔板的类型
塔板是气液两相接触传质的场所,为提高塔板性能, 采用各种形式塔板。 (1)泡罩塔 组成:升气管和泡罩
优点:塔板操作弹性大,塔效率也比较高,不易堵。 缺点:结构复杂,制造成本高,塔板阻力大但生产能力不大。
设计实例(板式塔)

率控制。
漏液现象
控制阀孔动能因数在5~6之间。
浮阀塔的负荷性能图
• 雾沫夹带线:指控制ev=0.1kg液/kg气时的Vs—— Ls之间关系
浮阀的开度与阀孔处气相的动压有关,动压的大 小取决于气体的速度与密度。
即动能因数:由动能因数作为衡量气体流动时动压 大小的指标
F uo v
• F0——气体通过阀孔v时的动能因数 • uο————气体通过阀孔时的速度m/s • ρν————气体密度kg/m3
排孔要求
1、排孔图(鼓泡区):排完之后的总孔数与算得的N相近,并 按实排数目重算阀孔气速,核算阀孔动能因数F0。若F0在9~12 范围内,即可认为作图得出的阀数能够满足要求。否则应调整孔 矩、阀数,重新作图,反复计算。 2、也可根据已算出的阀数及溢流装置尺寸等,用作图法求出所 需的塔径,并与最初估算的塔径相比较,经反复调整有关参数, 直到作图所得出的塔径与最初估算的塔径相符为止。 3、最后核算开孔率是否合适,否则前述过程重算。 开孔率:对于常压塔或减压塔开孔率在10~14%之间,
常压和减压塔---如塔板压降不是很大,工艺计算时假定全塔各处压力相等-误差不大.
减压塔---压力分布与塔板的结构形式,气液负荷,气液物性等多种因素有关, 很难计算,一般先假设再较核.多次试差. .
精馏方案的选定
2.进料状态
原则讲,要使回流在全塔发挥作用,全部冷量应该加在 塔顶,全部热量加在塔底.但实际设计时应该考虑设备 费和操作费问题及操作平稳等多种因素.
热敏性和高沸点的物料-----减压操作.P降低,相对挥
板式塔的设计

板式塔的设计板式塔的设计包括塔高的计算、塔径的确定、溢流装置的结构尺寸、板面布置、塔板校核及负荷性能图绘制等项内容。
一、板式塔的工艺计算(1)选定塔顶、塔底产品浓度(有时由设计任务书给出),进行全塔物料衡算,列出物料衡算总表。
(2)确定冷凝器、塔顶、塔底的操作压力。
(3)确定塔顶、塔底温度。
(4)选定进料状态,定出进料温度。
(5)在已定的操作压力下,作出x-y相平衡曲线。
(6)求出最小回流比。
(7)确定适宜的操作回流比。
(8)计算所需的理论板数及进料位置。
(9)确定全塔效率,算出精馏段、提馏段实际塔板数。
(11)计算塔顶冷凝器及塔底再沸器的热负荷,求出塔顶、塔底所需冷却剂量及加热蒸汽用量,列出全塔热量衡算总表。
二、筛孔塔板的设计参数液体在塔板上的流动型式确定之后,完整的筛板设计必须确定的主要结构参数有:①塔板直径D②板间距H T③溢流堰的型式,长度l和高度w hw④降液管型式及降液管底部与塔板间距的距离ho⑤液体进、出口安定区的宽度和边缘区宽度⑥筛孔直径d和孔间距0t三、筛孔塔板的设计程序1、板间距的选择和塔径D的初步确定初选板间距H T,取板上清液层高度h l=50-100mm之间,计算最大允许气速u max ,根据泛点百分率计算出设计气速u 和所需气体流通面积n A ,uV A S n =,按下表1选择塔板流型,并取堰长kD l w =,通常单流型可取k=0.6~0.8,双流型取k=0.5~0.7。
对容易发泡的物系k 可取得高一些,以保证液体在降液管内有更长的停留时间。
由教材图8-17查得溢流管面积f A 和塔板总面积T A 之比,即TnT Tf A A A A A -=,然后求得塔板总面积T A ,根据πTA D 4=求得D ,按塔设备系列化规格,将D 进行圆整。
当塔径小于1m 时,按100mm 递增,当塔径大于1m 时,按200mm 递增。
s V 为气体的体积流量m 3/s , s V 需要按精馏段和提馏段分开计算,最后根据塔径的大小确定均能满足要求的塔径。
(整理)板式塔设计指导书.pdf
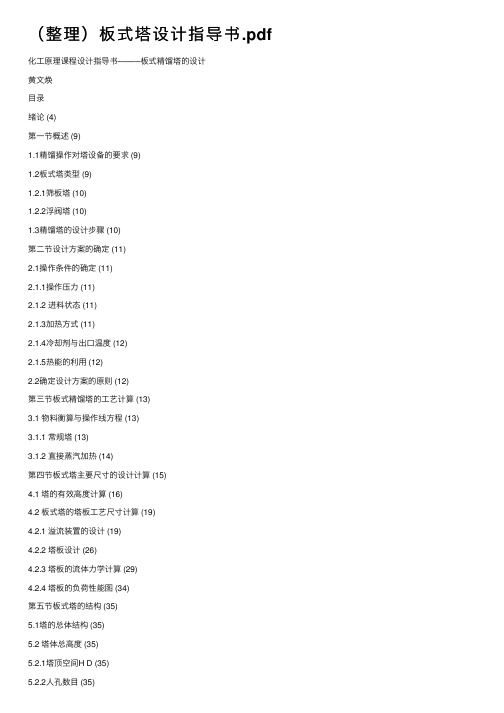
(整理)板式塔设计指导书.pdf 化⼯原理课程设计指导书–––––板式精馏塔的设计黄⽂焕⽬录绪论 (4)第⼀节概述 (9)1.1精馏操作对塔设备的要求 (9)1.2板式塔类型 (9)1.2.1筛板塔 (10)1.2.2浮阀塔 (10)1.3精馏塔的设计步骤 (10)第⼆节设计⽅案的确定 (11)2.1操作条件的确定 (11)2.1.1操作压⼒ (11)2.1.2 进料状态 (11)2.1.3加热⽅式 (11)2.1.4冷却剂与出⼝温度 (12)2.1.5热能的利⽤ (12)2.2确定设计⽅案的原则 (12)第三节板式精馏塔的⼯艺计算 (13)3.1 物料衡算与操作线⽅程 (13)3.1.1 常规塔 (13)3.1.2 直接蒸汽加热 (14)第四节板式塔主要尺⼨的设计计算 (15)4.1 塔的有效⾼度计算 (16)4.2 板式塔的塔板⼯艺尺⼨计算 (19)4.2.1 溢流装置的设计 (19)4.2.2 塔板设计 (26)4.2.3 塔板的流体⼒学计算 (29)4.2.4 塔板的负荷性能图 (34)第五节板式塔的结构 (35)5.1塔的总体结构 (35)5.2 塔体总⾼度 (35)5.2.1塔顶空间H D (35)5.2.2⼈孔数⽬ (35)5.2.3塔底空间H B (37)5.3塔板结构 (37)5.3.1整块式塔板结构 (37)第六节精馏装置的附属设备 (37)6.1 回流冷凝器 (38)6.2管壳式换热器的设计与选型 (38)6.2.1流体流动阻⼒(压强降)的计算 (39)6.2.2管壳式换热器的选型和设计计算步骤 (40)6.3 再沸器 (40)6.4接管直径 (41)6.4加热蒸⽓⿎泡管 (42)6.5离⼼泵的选择 (42)附:浮阀精馏塔设计实例 (43)附1 化⼯原理课程设计任务书 (43)附2 塔板的⼯艺设计 (43)附3 塔板的流体⼒学计算 (57)附4 塔附件设计 (64)附5 塔总体⾼度的设计 (67)附6 附属设备设计(略) (68)绪论⼀、化⼯原理课程设计的⽬的和要求课程设计是《化⼯原理》课程的⼀个总结性教学环节,是培养学⽣综合运⽤本门课程及有关选修课程的基本知识去解决某⼀设计任务的⼀次训练。
化工原理6.7 板式塔
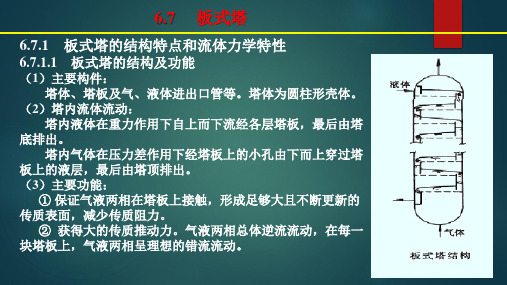
夹带较小,故塔板效率较高。
③ 操作弹性大。
④ 结构简单、造价低,安装检修方便。
⑤ 浮阀对材料的抗腐蚀性能要求较高。
脚钩
F-1型
6.7
板式塔
6.7.6.4 导向筛板(林德筛板)
(1)适用范围
适用于真空精馏操作的高效低压降塔板。
(2)评价指标
每块塔板的压降与板效率的比值。
6.7
6.7.1
板式塔
板式塔的结构特点和流体力学特性
6.7.1.1 板式塔的结构及功能
(1)主要构件:
塔体、塔板及气、液体进出口管等。塔体为圆柱形壳体。
(2)塔内流体流动:
塔内液体在重力作用下自上而下流经各层塔板,最后由塔
底排出。
塔内气体在压力差作用下经塔板上的小孔由下而上穿过塔
板上的液层,最后由塔顶排出。
操作范围宽
缺点
适用范围
结构复杂
阻力大
生产能力低
某些要求弹性好的特殊
塔
浮阀板
效率高
操作范围宽
采用不锈钢
浮阀易脱落
分离要求高
负荷变化大
原油常压分馏塔
筛板
效率较高
成本低
安装要求水平易堵
操作范围窄
分离要求高
塔板较多
化工中丙烯塔
舌型塔板
结构简单
生产能力大
操作范围窄
效率较低
分离要求较低的
闪蒸塔
斜孔板
生产能力大
效率高
注意:气体和液体沿塔板的不均匀流动,传质量减少,
效率下降。
6.7
板式塔
6.7.2.3 板式塔的不正常操作
(1)液泛
板式塔塔板主要结构尺寸的新设计方法_负荷性能图法_吴兆亮
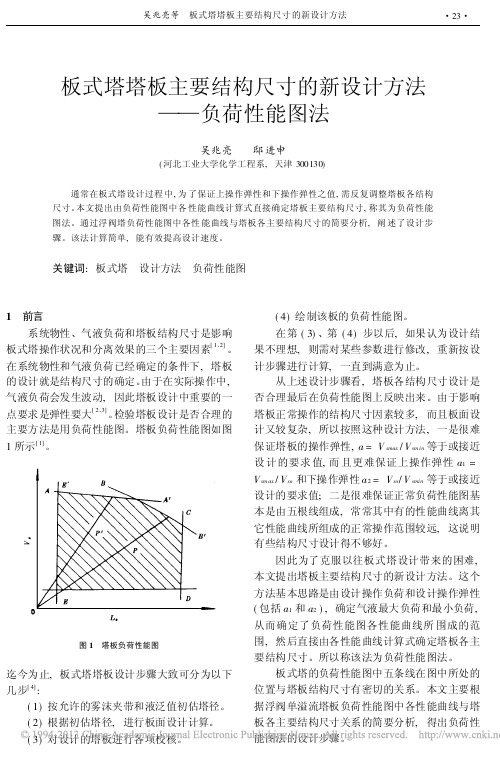
根据第 3. 2 步和第 3. 3 步得出的 D 中较大 值由式( 3) 按 L s = L smax 初步得出 X w , 得出的 X w 值若低于 0. 5, 以下按 0. 5 计算, 若高于 0. 8, 则适 当加大 D , 达到符合要求为止。 3. 5 校核 D , H T , 和 X w
· 24 · 化 学 工 程 1997 年第 25 卷第 1 期
2 负 荷 性能 图 中各 性 能 曲 线与 塔 板 主要 结 构 尺 寸的简要分析 2. 1 雾沫夹带上限线 AA ′
雾沫夹带上限线 AA′可根据式 ( 1) 作出。
泛点率 =
3 设计步骤 3. 1 确定最大与最小气液负荷
根据 V s0, Ls 0, a1 和 a2 得出 V smax , V , smin Lsmax 和 L smin 。 3. 2 初步确定 D 和 H T
由于在设计和实际操作中, 最大气液相负荷 常常由雾沫夹带所控制, 所以由式 ( 1) 按 V s = V smax 初步计算出 D 和 H T, D 作进一步圆整。 3. 3 校核 D 和初步确定
根据 D = 1. 6m, 由式 ( 3) 按 Ls = L smax 进
行计算, 则:
A f × 0. 45 0. 00896
=
5
Af =
× 1. 2× 2
62
sin
-1X
w
-
1. 62 4
X
w
苯-甲苯精馏塔一些计算计
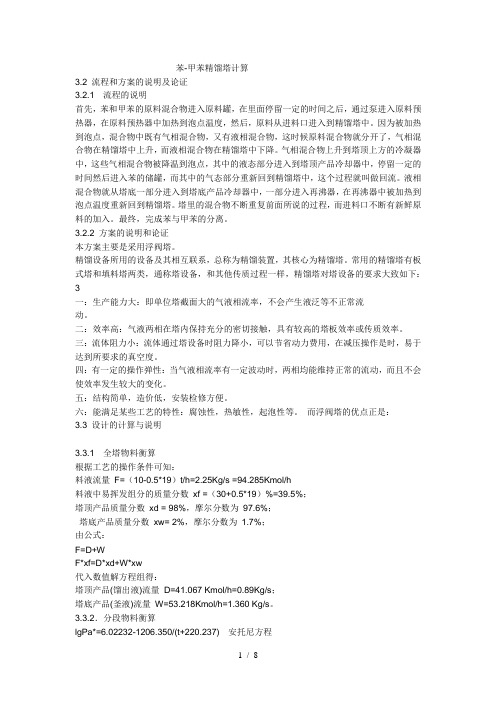
苯-甲苯精馏塔计算3.2 流程和方案的说明及论证3.2.1 流程的说明首先,苯和甲苯的原料混合物进入原料罐,在里面停留一定的时间之后,通过泵进入原料预热器,在原料预热器中加热到泡点温度,然后,原料从进料口进入到精馏塔中。
因为被加热到泡点,混合物中既有气相混合物,又有液相混合物,这时候原料混合物就分开了,气相混合物在精馏塔中上升,而液相混合物在精馏塔中下降。
气相混合物上升到塔顶上方的冷凝器中,这些气相混合物被降温到泡点,其中的液态部分进入到塔顶产品冷却器中,停留一定的时间然后进入苯的储罐,而其中的气态部分重新回到精馏塔中,这个过程就叫做回流。
液相混合物就从塔底一部分进入到塔底产品冷却器中,一部分进入再沸器,在再沸器中被加热到泡点温度重新回到精馏塔。
塔里的混合物不断重复前面所说的过程,而进料口不断有新鲜原料的加入。
最终,完成苯与甲苯的分离。
3.2.2 方案的说明和论证本方案主要是采用浮阀塔。
精馏设备所用的设备及其相互联系,总称为精馏装置,其核心为精馏塔。
常用的精馏塔有板式塔和填料塔两类,通称塔设备,和其他传质过程一样,精馏塔对塔设备的要求大致如下:3一:生产能力大:即单位塔截面大的气液相流率,不会产生液泛等不正常流动。
二:效率高:气液两相在塔内保持充分的密切接触,具有较高的塔板效率或传质效率。
三:流体阻力小:流体通过塔设备时阻力降小,可以节省动力费用,在减压操作是时,易于达到所要求的真空度。
四:有一定的操作弹性:当气液相流率有一定波动时,两相均能维持正常的流动,而且不会使效率发生较大的变化。
五:结构简单,造价低,安装检修方便。
六:能满足某些工艺的特性:腐蚀性,热敏性,起泡性等。
而浮阀塔的优点正是:3.3 设计的计算与说明3.3.1 全塔物料衡算根据工艺的操作条件可知:料液流量F=(10-0.5*19)t/h=2.25Kg/s =94.285Kmol/h料液中易挥发组分的质量分数xf =(30+0.5*19)%=39.5%;塔顶产品质量分数xd = 98%,摩尔分数为97.6%;塔底产品质量分数xw= 2%,摩尔分数为1.7%;由公式:F=D+WF*xf=D*xd+W*xw代入数值解方程组得:塔顶产品(馏出液)流量D=41.067 Kmol/h=0.89Kg/s;塔底产品(釜液)流量W=53.218Kmol/h=1.360 Kg/s。
板式塔的15种塔板介绍

在低气量时,开度小;气量大时,阀片自 动上升,开度增大。因此,气量变化时, 通过阀片周边流道进入液体层的气速较稳 定。同时,气体水平进入液层也强化了气 液接触传质。
优点:结构简单,生产能力和操作弹性大,
板效率高。综合性能较优异。
缺点:采用不锈钢,浮阀易脱落
JCV浮阀塔板
结构:阀笼与塔板固定,阀片在阀笼内上 下浮动。
网孔塔板
网孔塔板由冲有倾斜开孔的薄板制成,具 有舌形塔板的特点。这种塔板上装有倾斜 的挡沫板,其作用是避免液体被直接吹过 塔板,并提供气液分离和气液接触的表面。
网孔塔板具有生产能力大,压降低,加工 制造容易的特点。
垂直筛板
在塔板上开按一定排列的若干大孔(直径 100~200mm),孔上设置侧壁开有许多筛孔 的泡罩,泡罩底边留有间隙供液体进入罩 内。
缺点:板效率及操作弹性不及溢流塔板。
与溢流式塔板相比,逆流式塔板应用范围 小得多,常见的板型有筛孔式、栅板式、 波纹板式等。
泡罩塔板
在工业上最早(1813年)应用的一种塔板, 其主要元件由升气管和泡罩构成,泡罩安 装在升气管顶部,泡罩底缘开有若干齿缝 浸入在板上液层中,升气管顶部应高于泡
罩齿缝的上沿,以防止液体从中漏下。
浮舌塔板
为使舌形塔板适应低负荷生产,提高操作 弹性,研制出了可变气道截面(类似于浮 阀塔板)的浮舌塔板。
斜孔塔板
在舌形塔板上发展的斜孔塔板,斜孔的开 口方向与液流垂直且相邻两排开孔方向相 反,既保留了气体水平喷出、气液高度湍 动的优点,又避免了液体连续加速,可维 持板上均匀的低液面,从而既能获得大的 生产能力,又能达到好的传质效果。
优点:气流由舌片喷出并带动液体沿同方 向流动。气液并流避免了返混和液面落差, 塔板上液层较低,塔板压降较小。
塔设备规范——精选推荐
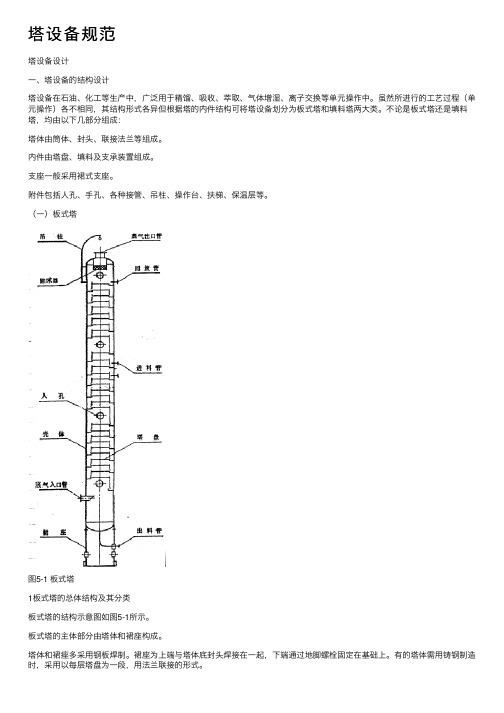
塔设备规范塔设备设计⼀、塔设备的结构设计塔设备在⽯油、化⼯等⽣产中,⼴泛⽤于精馏、吸收、萃取、⽓体增湿、离⼦交换等单元操作中。
虽然所进⾏的⼯艺过程(单元操作)各不相同,其结构形式各异但根据塔的内件结构可将塔设备划分为板式塔和填料塔两⼤类。
不论是板式塔还是填料塔,均由以下⼏部分组成:塔体由筒体、封头、联接法兰等组成。
内件由塔盘、填料及⽀承装置组成。
⽀座⼀般采⽤裙式⽀座。
附件包括⼈孔、⼿孔、各种接管、吊柱、操作台、扶梯、保温层等。
(⼀)板式塔图5-1 板式塔1板式塔的总体结构及其分类板式塔的结构⽰意图如图5-1所⽰。
板式塔的主体部分由塔体和裙座构成。
塔体和裙痤多采⽤钢板焊制。
裙座为上端与塔体底封头焊接在⼀起,下端通过地脚螺栓固定在基础上。
有的塔体需⽤铸钢制造时,采⽤以每层塔盘为⼀段,⽤法兰联接的形式。
板式塔的内件主要由多层塔盘组成。
各层塔盘的结构相同,由⽓液接触元件(如浮阀、筛孔、泡罩等)、塔盘板、溢流装置、降液管受液盘以及⽀承件、紧固件等元件组成。
⼀般塔盘间距相同。
开有⼈孔的塔盘间距较⼤,通常为700mm。
最底⼀层塔盘到塔底的距离也⽐塔盘间距⾼,因为塔底空间起着贮槽的作⽤,保证料液有⾜够的储存,使塔底液体不致流空。
最⾼⼀层塔盘和塔项距离也⾼于塔盘间距,在这⼀段上往往装有除沫器。
塔盘结构有整块式和分块式两种。
采⽤形式与塔径⼤⼩有关,当直径⼩于700mm的板式塔采⽤整块式塔盘,由于塔体分段,所以塔盘的安装可在塔外进⾏,塔体不需开设⼈孔。
当塔的直径⼤于700mm时,应采⽤分块式塔盘,塔体上开设⼈孔,塔盘的装、拆可以在塔内进⾏。
按塔盘上⽓、液两相接触元件结构的不同,板式塔⼜可分为:泡罩塔、筛板塔、浮阀塔、⾆形塔以及各种复合型塔。
⽬前,国内⽯油化⼯⽣产中使⽤较多的板式塔为筛板塔和浮阀塔。
1.整块式塔盘结构采⽤整块式塔盘的塔体是由若⼲塔节组成,各塔节之间⽤法兰联接,每个塔节安装⼀⾄数块塔盘。
根据塔盘的⽀承⽅式,整块式塔盘分为定距管式和重叠式两类。
- 1、下载文档前请自行甄别文档内容的完整性,平台不提供额外的编辑、内容补充、找答案等附加服务。
- 2、"仅部分预览"的文档,不可在线预览部分如存在完整性等问题,可反馈申请退款(可完整预览的文档不适用该条件!)。
- 3、如文档侵犯您的权益,请联系客服反馈,我们会尽快为您处理(人工客服工作时间:9:00-18:30)。
7.塔板结构设计
(1)溢流装置(教材168页)
板式塔的溢流装置包括溢流堰、降液管和受液盘。
降液管有圆形和弓形之分,除了某些小塔为了制造方便,采用圆形降液管外,一般均采用弓形降液管。
分析比对各种溢流装置的特点
①确定溢流管类型和溢流形式
分析讨论各种溢流形式的优缺点(本设计选用弓形溢流管、单溢流)
②选堰长l w单溢流取l w=(0.6~0.8)D
③计算堰上液层高度h ow
堰上液层高度
h对塔板的操作性能有很大影响。
堰上液层
OW
高度太小,会造成液体在堰上分布不均,影响传质效果,设计时应使堰上液层高度大于6mm,若小于此值须采用齿形堰;堰上液层高度太大,会增大塔板压降及液沫夹带量。
一般不宜大于60~70mm,超过此值时可改用双溢流型式。
先选平直堰,按平直堰公式教材169页式(7-55)计算h ow,若算得h ow<6mm应改用齿形堰,再用齿形堰公式计算h ow,齿形堰计算h ow的公式参考有关资料。
齿形堰:5/22)/(1042.4w n h ow l h L h -⨯= m
④确定出口堰高h w
h w =h L ﹣h ow 教材169页式(7-54)
⑤求降液管底隙高度h o
教材170页式(7-57)或式(7-58)
降液管底隙高度o h 不宜小于20~25mm,否则易于堵塞。
塔径较
小时可取o h 为25~30mm,塔径较大时可取40mm 左右。
⑥受液盘及进口堰(教材170页)
平受液盘一般需在塔板上设置进口堰,以保证降液管的液
封,并使液体在板上分布均匀。
进口堰的高度`w h ,可按下述原
则考虑。
当出口堰的高度W h 大于降液管底隙高度o h 时,则取`w
h 和W h 相等。
在个别情况W h <o h 时,则应取`w h >o h ,以保证液封。
进口堰与降液管的水平距离1h 不应小于o h ,以保证液流畅通。
对于φ800mm 以上的塔,多采用凹形受液盘。
这种结构便于液体的侧线采出,在液量较低时仍可形成良好的液封,且有改变液体流向的缓冲作用。
其深度一般在50mm 以上,但不能超过板间距的三分之一。
(2)浮阀数目的计算 ( 教材171页)
24O O S
d u V n π=
S V —上升蒸汽量,m 3
/s ;O d —阀孔直径,O d =39 mm 。
O u —气体通过阀孔时的气速,m/s 浮阀塔的操作性能以板上所有浮阀处于刚刚全开时的情况为最好。
浮阀的开度与阀孔处气相的动压有关,而动压的大小取决于气相的速度与密度。
“动能因数”作为衡量气体流动时动压大小的指标。
气体通过阀孔时的动能因数为:
V O O u F ρ=
①浮阀型式的选定 教材165页
本设计采用F -1型重阀,阀孔直径d 0=39mm ,阀片外径
48m m ,最小开度2.5mm ,阀重约33g
②选动能因数F O
根据工业生产装置的数据,对于F 1型重阀,当板上所有浮阀
刚刚全开时,浮阀塔的操作性能最高,此时O F 的数值常在8~12之间。
③计算阀孔气速u O 教材171页式(7-60) ④浮阀数目的计算 教材171页式(7-61)
(3)塔板布置
①确定塔板形式
塔板可分整块式和分块式两种,D<900mm的塔采用整块塔板,D>800mm的塔采用分块塔板,D=800~900mm时,根据制造和安装的具体情况两种均可采用。
②确定安定区(破沫区)宽度W s、无效区宽度W c
教材171页
安定区的宽度以W s表示,可按下述范围选取,即:
当D<1.5m, W s=60~75mm(出堰前);W s=50~75mm(进堰前)当D≥1.5m, W s=80~110mm
无效区W c : D<2500mm小塔在30~50mm;
D>2500mm大塔一般为50~70mm。
③确定浮阀排列方式教材171页
本设计采用三角形叉排
④画塔板布置图,确定实际浮阀数
(4)验算
①验算动能因数F0
要求在F0 在8~12之间教材172页
②验算开孔率Ф
要求Ф在10%~14%之间 教材172页
③验算液体在降液管中的停留时间θ
要求θ≥3~5s 教材170页式(7-56)
8.计算塔高Z
Z=H 顶+(N 实﹣2)H T +H f +H 底
H 顶—塔顶空间(不包括顶盖),取经验值,一般为1.3~1.5m ;
N 实—实际塔板数;
H f —进料段高度,m ;通常比其他板间距略大一些
H T —板间距,m ;在决定板间距时还应考虑安装检修的需要,
例如在塔体的人孔手孔处应留有足够的工作空间。
H T >600mm 时,4~6层开设一个人孔。
H 底—塔低空间(不包括底盖),取经验值,一般为1.3~2m 。
H 底也可根据塔釜液体停留时间进行计算。
教材166页
根据 min 15~10H D 42='L 底
π
求H 底
9.计算塔的进出口管直径,并选取进出口管规格
管径尺寸由管内流体的体积流量和流速决定,管径按下式计算并选取。
u
q d V π4=
式中 q V——管内流体的体积流量,m3/s;
u——管内流体的流速,m/s,取经验值。
各管内流速的经验值可按如下选取:
(1)蒸气管流速
常压时 u=12~20m/s (2)回流液管流速
借助位差重力回流 u=0.2~0.5m/s
用泵强制回流 u=1.0~2.5m/s (3)加料管流速
由高位槽进料 u=0.4~0.8m/s
用泵直接加料 u=1.5~2.5m/s (4)料液排出管流速
塔釜溶液出塔流速 u=0.5~1.0m/s (5)饱和水蒸气管流速
表压为295kPa以下 u=20~40m/s
表压为785kPa以下 u=40~60m/s。