液压系统管路的循环冲洗
液压系统试压冲洗方案.(优选)
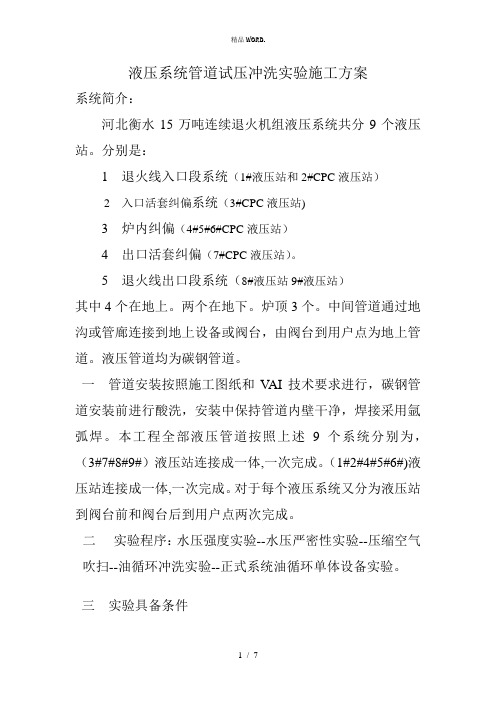
液压系统管道试压冲洗实验施工方案系统简介:河北衡水15万吨连续退火机组液压系统共分9个液压站。
分别是:1 退火线入口段系统(1#液压站和2#CPC液压站)2 入口活套纠偏系统(3#CPC液压站)3 炉内纠偏(4#5#6#CPC液压站)4 出口活套纠偏(7#CPC液压站)。
5 退火线出口段系统(8#液压站9#液压站)其中4个在地上。
两个在地下。
炉顶3个。
中间管道通过地沟或管廊连接到地上设备或阀台,由阀台到用户点为地上管道。
液压管道均为碳钢管道。
一管道安装按照施工图纸和V AI技术要求进行,碳钢管道安装前进行酸洗,安装中保持管道内壁干净,焊接采用氩弧焊。
本工程全部液压管道按照上述9个系统分别为,(3#7#8#9#)液压站连接成一体,一次完成。
(1#2#4#5#6#)液压站连接成一体,一次完成。
对于每个液压系统又分为液压站到阀台前和阀台后到用户点两次完成。
二实验程序:水压强度实验--水压严密性实验--压缩空气吹扫--油循环冲洗实验--正式系统油循环单体设备实验。
三实验具备条件1、检查实验设备是否齐全和设备状态是否良好。
2、检查实验介质和临时管道材料是否齐全。
3、按施工图和原理图检查待实验管道安装是否正确,排气阀和排污阀安装是否齐全和合理。
待实验系统管道按施工图纸全部安装检查完毕,并报业主、V AI和监理检查验收认可。
1、实验步骤:检查验收待实验管道—连接临时实验管道—水压强度实验—水压严密性实验—排水—压缩空气吹扫—油循环冲洗实验—排油—拆除临时实验管道、连接正式管道—正式系统油循环。
2、实验方法2.1检查验收实验管道根据本方案第三项“实验具备条件”检查验收管道。
2.2 连接临时实验管道2.2.1拆除油箱前回油法兰短管,拆除泵站出口供油法兰短管,拆除实验管道连接的所有用户点供、回油法兰短管。
2.2.2 按照水压实验管道连接示意图将用户点供回油管道用法兰短管连接,并在供回油管道中间安装阀门控制各支管道通断,在润滑站内将试压设备与回油管连接,在供油管首端安装法兰盲板和排水阀门,排水管道接到排放槽内,排放槽连接一台水泵用管道接至室外排污井内。
液压润滑管道循环冲洗要点
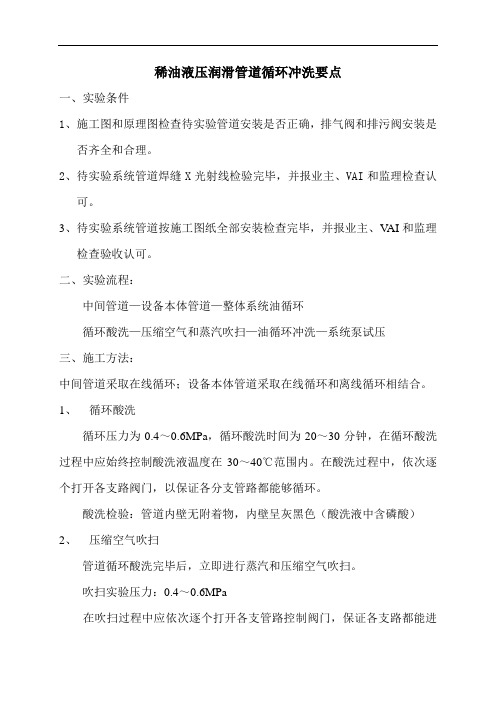
稀油液压润滑管道循环冲洗要点一、实验条件1、施工图和原理图检查待实验管道安装是否正确,排气阀和排污阀安装是否齐全和合理。
2、待实验系统管道焊缝X光射线检验完毕,并报业主、VAI和监理检查认可。
3、待实验系统管道按施工图纸全部安装检查完毕,并报业主、V AI和监理检查验收认可。
二、实验流程:中间管道—设备本体管道—整体系统油循环循环酸洗—压缩空气和蒸汽吹扫—油循环冲洗—系统泵试压三、施工方法:中间管道采取在线循环;设备本体管道采取在线循环和离线循环相结合。
1、循环酸洗循环压力为0.4~0.6MPa,循环酸洗时间为20~30分钟,在循环酸洗过程中应始终控制酸洗液温度在30~40℃范围内。
在酸洗过程中,依次逐个打开各支路阀门,以保证各分支管路都能够循环。
酸洗检验:管道内壁无附着物,内壁呈灰黑色(酸洗液中含磷酸)2、压缩空气吹扫管道循环酸洗完毕后,立即进行蒸汽和压缩空气吹扫。
吹扫实验压力:0.4~0.6MPa在吹扫过程中应依次逐个打开各支管路控制阀门,保证各支路都能进行吹扫。
直到将管道内的残留酸液全部吹出,管道内壁吹干,并在出口处用白布检查目测无可见的污物即可认为吹扫合格。
3、稀油系统油循环冲洗实验管道吹扫实验合格后,应立即进行油循环冲洗实验。
实验介质:N22#机械油(应无杂质和水分)冲洗实验压力:1.0~1.2MPa冲洗流量:400L/min冲洗油温度:40℃~60℃过滤方式:回油过滤检验标准:清洁度NAS7级,检验方法用颗粒计数器进行检查。
拆除实验管道连接的所有阀台阀块的接口法兰,将阀块移走后,开始循环时使用25μ和15μ的滤芯,当冲洗油清洁度达到NAS8级时更换为10μ和5μ滤芯进行循环,直到冲洗油清洁度达到NAS7级要求。
4、液压系统油循环冲洗实验每个液压系统分为液压站到阀台前和阀台后到用户点两部分完成实验。
实验介质:N22#机械油(应无杂质和水分)冲洗实验压力:1.0~1.2MPa冲洗流量:400L/min冲洗油温度:40℃~60℃过滤方式:回油过滤拆除实验管道连接的所有阀台阀块的接口法兰,将阀块移走后,开始循环时使用25μ和15μ的滤芯,当冲洗油清洁度达到NAS8级时更换为10μ和5μ滤芯进行循环,直到冲洗油清洁度达到NAS6级。
液压、润滑管道在线循环酸洗工法.

液压、润滑管道在线循环酸洗工法目录一.工法二.适用范围三.酸洗工艺四.酸洗注意事项五.施工组织六.循环酸洗装置七.工程质量八.经济效益分析九.工程实例介质管道酸洗是目前国内外普遍采用的管道除锈方法。
酸洗是以酸为主剂,配以若干种化学元素制成的添加剂,通过化学作用除去管道内壁上的油脂、铁锈、焊渣以及其它杂质,使管内壁露出金属本质,经钝化处理后,达到要求的清洁度,且不再锈蚀。
酸洗实际上是一个中间工艺,对于液压润滑管道安装,更是施工污染控制的关键。
使用什么酸洗方式,什么除锈剂,什么钝化液,才能使酸洗工艺适应性强,设备简单,占地小,环境不污染,操作人员安全,工艺简化,除锈效果好,残留酸小于规定值,成本低廉,这是介质管道酸洗追求的目标和探索的方向。
经反复论证和一段时间的筹备,我公司决定淘汰落后的槽式酸洗工艺,代之以先进的在线酸洗工艺。
(本工法正是在此基础上编制的。
)一、工法特点在线循环酸洗同传统的槽洗相比,尽管酸洗原理相同,都是利用酸的强还原性除去碳钢管壁上的锈蚀,但又有其不同之处,其优势更明显。
(一)除锈能力强,效果好。
酸洗时酸液循环往复地运动,酸液对管内壁始终带压冲刷,能在较短时间内达到除锈目的,且效果明显。
(二)环境污染小,操作人员安全,劳动强度小。
废液经中和并稀释后排放,对环境污染小;因酸洗整个过程仅是关停泵和操作阀门,相对槽洗强度小且极安全。
(三)管内壁残留液容易去除。
在线酸洗是带压冲洗,管内壁附着的杂质容易排净。
(四)在线酸洗质量更有保证。
槽式酸洗必然存在二次安装造成污染,而在线酸洗在密闭的空间里进行,与外界隔绝不存在二次污染问题,而槽洗有的从第一批管子酸洗到最后一批管子酸洗,再油循环时间长达一个月,在这期间极易二次回锈,而在线酸洗不存在二次回锈问题,因它酸洗后即油循环。
(五)在线酸洗对操作人员的素质要求较高,操作较复杂。
二.适用范围本工法仅适用于液压、润滑管道在线酸洗除锈。
三.酸洗工艺(一)工艺流程临时设施安装短接通水试压水冲洗脱脂水冲洗二次酸洗中和钝化水冲洗压缩空气吹干(涂油)(系统油冲洗)1. 酸洗回路连接(1)管中连接要求,管径相同或相近,每一回路总长不宜超过 300m(若超过300m,可分区或分段酸洗),主管上的支管可根据实际情况,形成通过主管多路进酸,再通过支管多路回酸;或通过主管多路进酸,支管汇流后多路回酸,与设备相连的细支管可在线外(地面)连成回路,进行线外循环酸洗。
液压管道在线快速化学清洗和油冲洗技术
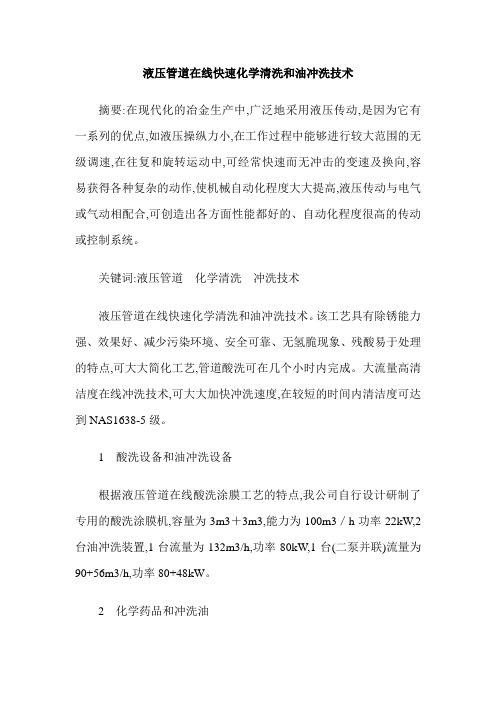
液压管道在线快速化学清洗和油冲洗技术摘要:在现代化的冶金生产中,广泛地采用液压传动,是因为它有一系列的优点,如液压操纵力小,在工作过程中能够进行较大范围的无级调速,在往复和旋转运动中,可经常快速而无冲击的变速及换向,容易获得各种复杂的动作,使机械自动化程度大大提高,液压传动与电气或气动相配合,可创造出各方面性能都好的、自动化程度很高的传动或控制系统。
关键词:液压管道化学清洗冲洗技术液压管道在线快速化学清洗和油冲洗技术。
该工艺具有除锈能力强、效果好、减少污染环境、安全可靠、无氢脆现象、残酸易于处理的特点,可大大简化工艺,管道酸洗可在几个小时内完成。
大流量高清洁度在线冲洗技术,可大大加快冲洗速度,在较短的时间内清洁度可达到NAS1638-5级。
1 酸洗设备和油冲洗设备根据液压管道在线酸洗涂膜工艺的特点,我公司自行设计研制了专用的酸洗涂膜机,容量为3m3+3m3,能力为100m3/h功率22kW,2台油冲洗装置,1台流量为132m3/h,功率80kW,1台(二泵并联)流量为90+56m3/h,功率80+48kW。
2 化学药品和冲洗油根据系统管径容积和管道内表面积准备足够的氢氧化钠,磷酸三钠、盐酸,氟化氢氨,防腐剂(六次甲基四氨)、柠檬酸和亚硝酸钠等化学药品。
油冲洗介质要与工作介质相容。
液压系统工作介质为46#抗磨液压油,润滑系统工作介质为220#中负荷齿轮油。
因此选用与两种工作介质均相容的10#机械油为冲洗油。
3 临时用水源、气源和电源在化学清洗过程中必须要有足够的水和气来保证清洗的连续性和质量。
在化学清洗的每道工序均要大量的水,所以干净且水量足够大的水源是必要的,否则可能严重影响清洗质量。
干燥的压缩空气或氮气是作为气源的要求,气源必须有足够的压力,以尽可能将残留的化学液体排除干净。
电源必须完全满足清洗、油冲洗装置以及临时照明灯具的使用,冲洗时不要断电。
4 组成循环管路在实际配管施工过程中就要考虑到化学清洗时的短接工作。
液压管道冲洗方案

首钢京唐工程液压管道冲洗方案编制:审核:批准:编制单位:编制日期:目录一、编制依据 (1)二、工程概况 (1)三、方案确定 (1)四、管道油冲洗方案 (2)五、安全措施 (6)六、应急预案 (6)一、编制依据1、《机械设备安装工程施工及验收通用规范》GB502312092、《冶金机械液压润滑和气动设备工程安装验收规范》GB50387-20063、目前收到的施工图纸及相关资料。
二、工程概况液压系统分为高压系统和低压系统2个部分,高压系统采用不锈钢管,最大工作压力为240bar,冲洗精度等级要求达到NAS3级,低压系统采用碳钢管,最大工作压力为140bar;冲洗精度等级要求达到NAS5级,润滑管路冲洗精度要求达到NAS5级,各类液压、润滑管道的直径规格从16mm~140mm共18种,管道总长约2800m液压系统的组件寿命和工作状况很大程度上取决于所传送工作介质的清洁程度,则必须对介质输送管路进行清洁。
三、方案确定液压、润滑系统冲洗主要有线外冲洗及在线冲洗两种方法。
线外冲洗是指采用专用的冲洗系统线外冲洗需很大的冲洗设备投资过大,而且一台冲洗设备不能同时冲洗两套系统,加上需要换油进行二次冲洗,这将使冲洗工期拖长在线冲洗是指利用液压系统主油泵、油箱及工作介质对管道进行冲洗,冲洗油泵、油箱用冲洗液进行冲洗,在线冲洗工期短能满足工程进度需要,不需要线外的专门冲洗设备,对大型的液压系统操作相对简单,但在线冲洗对各道工序要求严格对各个环节严格控制。
由于冲洗管道后的回油都必须经过回油过滤器,所有冲下来的杂物都被回油过滤拦截,所以回油过虑器是冲洗中最关键的环节。
其优点是投资少,且冲洗一次完成,工期相对较短。
该方案为了加快冲洗进度,采用在线冲洗的方法。
四、管道油冲洗方案油冲洗是为了除去管路系统中的异物,防止管道受污染和使用油变质,导致液压系统工作性能差;并保证液压系统的比例阀及油缸等在系统工作中不致出现机构异常磨损、卡阻现象,以及过滤器堵塞现象。
液压、润滑管道酸洗方案
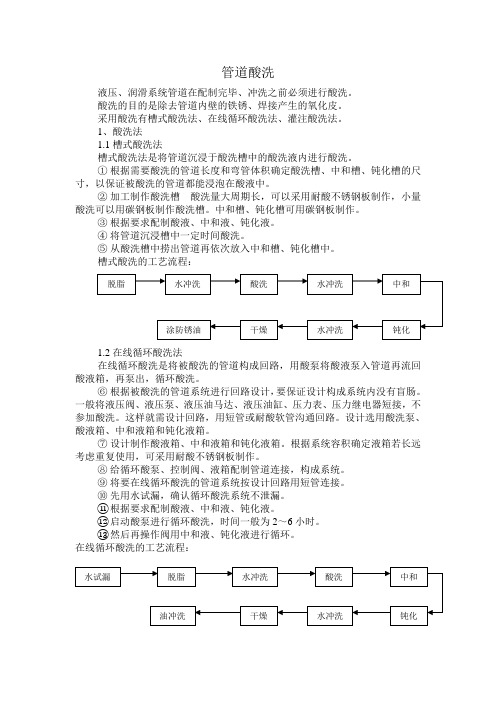
管道酸洗液压、润滑系统管道在配制完毕、冲洗之前必须进行酸洗。
酸洗的目的是除去管道内壁的铁锈、焊接产生的氧化皮。
采用酸洗有槽式酸洗法、在线循环酸洗法、灌注酸洗法。
1、酸洗法1.1槽式酸洗法槽式酸洗法是将管道沉浸于酸洗槽中的酸洗液内进行酸洗。
① 根据需要酸洗的管道长度和弯管体积确定酸洗槽、中和槽、钝化槽的尺寸,以保证被酸洗的管道都能浸泡在酸液中。
② 加工制作酸洗槽 酸洗量大周期长,可以采用耐酸不锈钢板制作,小量酸洗可以用碳钢板制作酸洗槽。
中和槽、钝化槽可用碳钢板制作。
③ 根据要求配制酸液、中和液、钝化液。
④ 将管道沉浸槽中一定时间酸洗。
⑤ 从酸洗槽中捞出管道再依次放入中和槽、钝化槽中。
槽式酸洗的工艺流程:1.2在线循环酸洗法在线循环酸洗是将被酸洗的管道构成回路,用酸泵将酸液泵入管道再流回酸液箱,再泵出,循环酸洗。
⑥ 根据被酸洗的管道系统进行回路设计,要保证设计构成系统内没有盲肠。
一般将液压阀、液压泵、液压油马达、液压油缸、压力表、压力继电器短接,不参加酸洗。
这样就需设计回路,用短管或耐酸软管沟通回路。
设计选用酸洗泵、酸液箱、中和液箱和钝化液箱。
⑦ 设计制作酸液箱、中和液箱和钝化液箱。
根据系统容积确定液箱若长远考虑重复使用,可采用耐酸不锈钢板制作。
⑧ 给循环酸泵、控制阀、液箱配制管道连接,构成系统。
⑨ 将要在线循环酸洗的管道系统按设计回路用短管连接。
⑩ 先用水试漏,确认循环酸洗系统不泄漏。
⑪ 根据要求配制酸液、中和液、钝化液。
⑫ 启动酸泵进行循环酸洗,时间一般为2~6小时。
⑬ 然后再操作阀用中和液、钝化液进行循环。
在线循环酸洗的工艺流程:1.3灌注酸洗法将酸液灌入管道内静置酸洗的方法。
对于零星的管道酸洗可采用此方法。
⑭将被酸洗的管道封堵,形成容腔,留出浇灌口和排泄口;⑮对被酸洗的管道容腔进行灌水试漏;⑯卸水,灌注酸液进行酸洗,一般静置4~8小时;⑰排泄酸液,进行水冲洗、中和、钝化。
液压系统长大管路的清洗
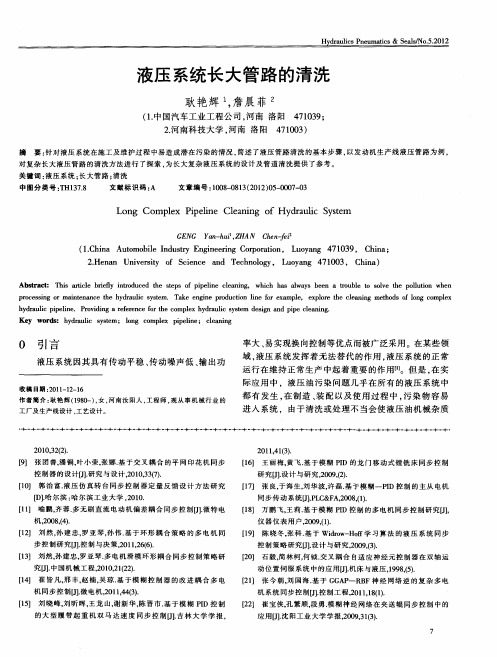
12 酸 洗 工 艺 流 程 .
便、 方便 检查 、 效果 可靠 ; 缺点 是 回路 长度 较长 ; ( ) 合 回路 : 于 管路 口径 变 化 较 大 , 3混 对 回路 连 接 繁琐 且 管路 较长 的系 统 可采 用 此 回路 方 式 进 行 冲 洗 , 但各 回路 的管径 应基 本 一致 ,以确 保各 管 路 的流 速 达
O 引 言
液压 系统 因其具 有传 动 平稳 、 动 噪声 低 、 出功 传 输
收 稿 日期 :0 1 1— 6 2 1- 2 1
率大 、 易实 现换 向控 制等优 点而被 广泛 采用 。在某 些领 域 , 压 系统 发挥 着无 法 替代 的作 用 , 压 系统 的正 常 液 液 运 行在 维 持正 常生 产 中起 着 重要 的作 用[ 1 1 。但是 , 实 在
控 制 策 略 研究 [. 计 与研 究 ,09() J设 ] 20, . 3 f0 石 毅 , 林 柯 , 钺 . 叉 耦 合 自适 应 神 经 元 控 制 器 在 双 轴 运 21 简 何 交
动 位 置 伺 服 系统 中 的应 用 [. 床 与 液 压,9 8( . J机 ] 19 , ) 5 【1 张 今 朝 , 国海 . 于 G A - R F神 经 网 络 逆 的复 杂 多 电 2】 刘 基 GP B
中管 道 内的 流体 流速 达 到 冲洗要 求 进行 确 定 ,也 可根 据实 际情况 , 在现 有能力 下对 回路进 行分 段 冲洗 。冲洗 回路一 般有 以下几 种形 式 : ( ) 联 回路 : 用此 回路 的优点 是 循 环 冲洗 回路 1并 采
液压管道循环酸洗、油冲洗操作规程
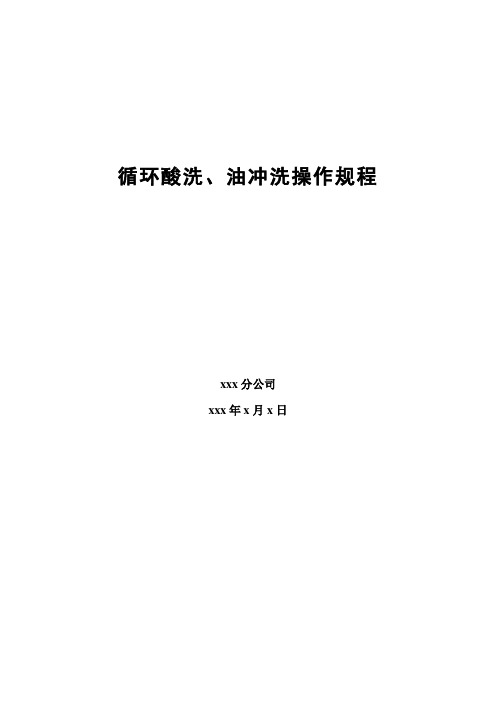
E、钝化合格后用压缩空气进行吹扫方法同酸液吹扫。
4、脱脂液循环
A、脱脂液浓度配比:氢氧化钠10%
B、1吨脱脂液质量配比:
清洁水:氢氧化钠=900㎏:100㎏
C、循环压力为0.4~0.6MPa,每个支路循环脱脂时间为60分钟,在循环脱脂过程中应始终控制脱脂液温度在50~60℃左右。在循环脱脂过程中,依次逐个打开各阀台支路阀门,以保证各分支管路都能够循环。
2、压缩空气吹扫
A、管道循环酸洗检查合格后,用压缩空气将酸液吹回酸箱,多余酸液用小水泵抽回酸箱或盛放在塑料桶中。
B、吹扫压力:0.4~0.6Mpa
C、吹扫过程中应依次逐个打开各支管路控制阀门,保证每个支路都能进行吹扫。直到将管道内的残留酸液全部吹出,管道内壁吹干,并在出口处用白布检查目测无可见的污物和酸液即可认为吹扫合格。
油冲洗合格后,用压缩空气进行吹扫,并用小油泵和透明塑料管将清洁油抽回干净的油箱和油桶中,注意保持油清洁。
6、液压系统油循环冲洗
每个液压系统分为液压站到阀台前和阀台后到用户点两部分完成实验。
实验介质:N22#机械油
冲洗实验压力:1.0~1.2MPa
冲洗流量:中间管道400L/min以上
阀台到用户100L/min
时间
工作内容
检查处理结果
记录人8:003、油轴承系统:NAS74、齿轮润滑系统:NAS9
5、工作辊弯辊系统:NAS8
6、加热炉液压系统:NAS8
四、人员安排
1、白班:8:00--22:00
班长:xxx
组员:
力工:
2、夜班:20:00--9:00
班长:
液压管道冲洗方案

1、工程概况:1.1我公司承担天津薄板厂重卷机组液压设备安装工程。
重卷机组液压系统主要由一个油站和21组阀台组成,其中2组阀台分别控制开卷机、外轴承钢卷支架、CPC带钢对中装置、钢卷打开台、入口夹送辊、切头剪、带尾部夹送辊、废钢卷取机、毡压力机、扳直辊、定径剪进料夹送辊、下压力辊、皮带助卷机、卷取机、出口钢卷小车等。
1.2液压油站通过油泵给主控制阀提供压力后(压力为16Mpa)经过主管线分别进入21组液压阀台,进入阀台后通过换向阀把压力油分别送到执行机构,主执行机构的压力为12Mpa。
2、冲洗方案:液压系统管路冲洗采用线外循环冲洗,冲洗工具为冲洗油站(Q=90L/min P=2Mpa),冲洗介质为32#冲洗油,油样清洁度要求为NAS7级。
2.1 管道冲洗管道冲洗分主管线管道冲洗和支管线管道冲洗,主管线管道为连接油站至各阀台的进油、回油及泄油管路;支管线的管道为21组阀台后进入执行机构的A管和B管。
2.2主管线管道冲洗脱开与油站及阀台之间连接的进油、回油及泄油管道,把与油站连接的管道与冲洗油站连接,连接方式为进油管道接油站的进油口,回油与泄油管利用连接接头串联后与油站的回油口连接形成回路,启动油站进行循环冲洗,冲洗时打开加热器使油温保持40~55℃2.3支管线管道冲洗脱开与阀台及各执行机构油缸连接的管道(A管B管),将其与冲洗油站进油及回油口连接形成回路,启动油站进行循环冲洗,冲洗时打开加热器使油温保持40~55℃2.4冲洗要求2.4.1冲洗时油温保持在40~55℃2.4.2冲洗完毕后油样清洁度为NAS7级合格3、冲洗注意事项:3.1冲洗前用面团清洁油箱,确认干净后用滤油机加入冲洗油3.2开机循环冲洗时应将回路中阀门开至最大3.3采集油样时应在靠近油箱的回油管最低部位采集3.4采集的油样应密封好后送检,三次检验合格后方确认冲洗干净3.5冲洗时所用的管件管道在接入冲洗回路前应酸洗合格4、安全措施:4.1非指定冲洗人员不得随意出入现场以防误动操作系统4.2循环冲洗时要有专人看护以防以外情况发生4.3现场必须配备防火器材以防火情不能及时处理4.4发现漏油现象时必须停机处理不可带压工作4.5现场配备锯屑以清理油污防止人员滑倒5、冲洗用料计划:无缝钢管Φ60 40m 无缝钢管Φ50 40m无缝钢管Φ25 10m 无缝钢管Φ20 10m无缝钢管Φ16 10m 无缝钢管Φ10 10m滤芯1μ2个滤芯5μ4个滤芯10μ6个四氯化碳60kg 铁丝16# 5kg 冲洗接头Φ25 35个冲洗接头Φ20 45个冲洗接头Φ16 45个冲洗接头Φ10 20个法兰DN60 4对法兰DN50 4对32#冲洗油2吨螺栓M16X55 32条螺栓M12X50 32条胶皮垫DN60 2个胶皮垫DN50 2个草袋20个锯屑3立方米黄沙3立方米干粉灭火器6个弯头DN60 8个弯头DN50 8个。
液压油系统酸洗方案

前言齐鲁石化72万吨/年乙烯改造工程中之一离子膜烧碱扩建装置,有部分油管线需进行开工前的化学清洗。
以除去管线在制造、存放、运输、安装过程中所产生的腐蚀产物、焊渣、尘埃、油脂和机械杂质等污染物,缩短油运时间,保证开工后管线内油的洁净度,从而确保设备的安全运行。
1、化学清洗系统流程说明:循环箱一清洗泵一管线一循环箱将管线与设备的连接处拆开,将拆下的管线连接起来形成回路。
2、化学清洗前的准备工作:2、l清洗时所用水源、电源、蒸汽、氮气等公用工程应充足,并安全可靠,由甲方提供,确保清洗工作顺利进行。
2、2临时系统安装完毕,应通过1.5倍的工作压力的水压试验,清洗泵试运转无异常,方可进行化学清洗。
2、3排放系统应畅通,废液处理的临时或正常设施安装完毕,并能有效处理废液。
2、4化学清洗的药品经检验确证无误,并按技术安全措施的要求备足各种药品及化验仪器。
2、5参加化学清洗的人员应培训完毕。
2、6应按DL/T794.200l《火力发电厂锅炉化学清洗导则》中第十一篇的安全条例做好安全工作。
2、7腐蚀指示片,清洗系统测量装置应安装完毕,仪表校正无误。
2、8不参加化学清洗的设备及系统应与化学清洗系统可靠的隔离。
3、清洗工艺程序及步骤工艺程序:水冲洗一碱洗脱脂一水冲洗一酸洗一水冲洗一漂洗一防锈处理一最后水冲洗一检查验收3、1水冲洗:先用工业水冲洗临时系统,在用水冲洗系统至出水澄清。
在冲洗的同时进行系统水压和升温试验。
3.2碱洗脱脂:碱洗的目的除去管内油污,为下一步酸洗打好基础。
碱洗时,加Na3P04、Na2C03和JX-1洗涤剂循环清洗8小时,温度控制在80-90℃。
并每小时分析一次PH值、P碱度、M碱度。
同时,每半小时记录一次系统压力、温度。
当P碱度、M碱度平衡后,脱脂工作结束。
3、3碱洗后的水冲洗:先将碱液排净后,用水冲洗至出水PH<8.4,水质透明。
3、4酸洗:通过循环箱内的加热器将系统升温至80℃,先在循环箱内加入Lan-826缓蚀剂、联氨还原剂循环均匀后再加入柠檬酸,用氨水调PH 值3-3.5,维持温度在85-90℃循环清洗6-8小时。
液压、润滑管道循环油冲洗方案

液压、润滑管道循环油冲洗液压、润滑系统的管道经过酸洗后,还必须进行循环冲洗才能投入工作。
循环冲洗就是采用工作油液或另外选定的低粘度冲洗油,用泵打入接成回路的管道内进行高速冲洗,以清除管内壁上各种固体污染物的施工工艺。
它也是液压、润滑系统施工的关键工序之一。
1、循环冲洗方法1.1线外冲洗法线外冲洗法是将管道拆离安装位置,在地面上连接成循环冲洗回路进行冲洗的方法。
管道冲洗采用线外循环冲洗法,这种方法具有以下优缺点:可较方便地将管径相同或相近的管子连接成一个回路:较少需要临时连接管;需要较大的场地;冲洗后还需要二次安装,易被再次污染;需自备冲洗用油泵、油箱等冲洗设备。
1.2线内冲洗法线内冲洗法是将管道在安装位置上连接成回路,利用液压、润滑系统回路充冲洗油液进行油冲洗。
这种冲洗方法可利用原回路及泵进行冲洗,不需另外添置冲洗设备和联结回路。
冲洗结束后,不用拆解回路,避免了污染。
2、冲洗回路设计2.1线外冲洗需要设计回路,可以根据管径设计,将管路联结成串联或并联。
注意管径大小的排列,依流向从大至小排列。
2.2线内冲洗只需局部设计回路。
系统中不参加冲洗的伺服阀、比例阀等要短接。
冲洗时,先冲洗主干管。
将出、回油主干管连接成回路,将支管断开或加盲板。
冲洗后,将出、回油干管恢复系统原样,再冲洗支管。
将不参加冲洗的阀短接。
若系统中的支管回路较多,可分批打开冲洗。
可采取通断阀的方式打开或关闭回路。
冲洗完毕,放尽冲洗油,更换成工作油。
3、冲洗油液和冲洗参数选定3.1冲洗油液液压、润滑系统用油,除采用石油基油为工作介质外,还出于降低工作介质的成本以及在高温、明火环境下消除工作介质着火引起火灾的隐患,日渐增多地采用了以下几种工作介质:水包油和油包水乳化液水—乙二醇液压液磷酸脂基液压液。
对于以上这些不同的工作介质以及对工作介质要求严格程度不同的系统,应选择不同的冲洗油液。
3.2对于采用石油基油为工作介质的液压伺服系统宜采用工作油来冲洗。
液压管路循环冲洗中流量的选择
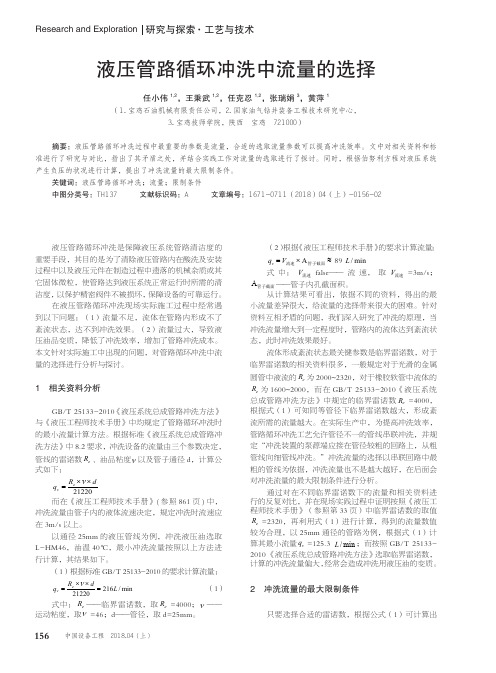
与《液压工程师技术手册》中均规定了管路循环冲洗时
的最小流量计算方法。根据标准《液压系统总成管路冲
洗方法》中 8.2 要求,冲洗设备的流量由三个参数决定,
管线的雷诺数 Re 、油品粘度ν 以及管子通径 d,计算公 × d 21220
而在《液压工程师技术手册》( 参照 861 页 ) 中,
(1)
式 中: Re —— 临 界 雷 诺 数, 取 Re =4000; ν —— 运动粘度,取ν =46;d——管径,取 d=25mm。
156 中国设备工程 2018.04 ( 上 )
(2)根据《液压工程师技术手册》的要求计算流量: qvqv==VV流流 速速××AA管管 子子 截截 面面≈≈898899LL/ m/ minin 式 中: V流速 false—— 流 速, 取 V流速 =3m/s; A管子截面 ——管子内孔截面积。 从计算结果可看出,依据不同的资料,得出的最 小流量差异很大,给流量的选择带来很大的困难。针对 资料互相矛盾的问题,我们深入研究了冲洗的原理,当 冲洗流量增大到一定程度时,管路内的流体达到紊流状 态,此时冲洗效果最好。 流体形成紊流状态最关键参数是临界雷诺数,对于 临界雷诺数的相关资料很多,一般规定对于光滑的金属 圆管中液流的 Re 为 2000~2320,对于橡胶软管中流体的 Re 为 1600~2000, 而 在 GB/T 25133-2010《 液 压 系 统 总成管路冲洗方法》中规定的临界雷诺数 Re =4000, 根据式(1)可知同等管径下临界雷诺数越大,形成紊 流所需的流量越大。在实际生产中,为提高冲洗效率, 管路循环冲洗工艺允许管径不一的管线串联冲洗,并规 定“冲洗装置的泵源端应接在管径较粗的回路上,从粗 管线向细管线冲洗。”冲洗流量的选择以串联回路中最 粗的管线为依据,冲洗流量也不是越大越好,在后面会 对冲洗流量的最大限制条件进行分析。 通过对在不同临界雷诺数下的流量和相关资料进 行的反复对比,并在现场实践过程中证明按照《液压工 程师技术手册》(参照第 33 页)中临界雷诺数的取值 Re =2320,再利用式(1)进行计算,得到的流量数值 较为合理,以 25mm 通径的管路为例,根据式(1)计 算其最小流量 qv =125.3 L / min ;而按照 GB/T 251332010 《液压系统总成管路冲洗方法》选取临界雷诺数, 计算的冲洗流量偏大,经常会造成冲洗用液压油的变质。
液压站(液压系统)的安装与调试

液压站(液压系统)的安装与调试液压站(液压系统)的安装与调试1 安装:必须对管路进⾏循环冲洗。
⽤循环冲洗过滤装置使液压系统的管路反复冲洗过滤, 采⽤变换冲洗⽅向和振动管路的办法加强冲洗效果,并经常检查过滤器滤芯情况.循环24-72⼩时后,将装置中的滤芯更换成过滤精度10微⽶的滤芯,继续循环冲洗过滤,直到化验油品的清洁度不低于NSA1638标准9级,或不低于ISO4406标准18/15级后结束循环冲洗过滤装置.各电磁换向阀接线时,应严格按规格中规定的电压和电流值进⾏配接,并通过操作台上的相应开关反复操作⼏次,检查动作的灵活性,正确性,可靠性。
2 调试前的准备⼯作:2.1 清洗油箱,盘形制动器,以及各个液压元件,清洗⼲净是液压站能否正常⼯作的关键。
2.2 由于新油的清洁度不能满⾜液压系统要求,向油箱加⼊新油时,必须⽤过滤精度为10um的滤油车,通过空⽓滤清器(序号4)加油。
向油箱灌注规定的液压油到合适的液位。
2.3 检查蓄能器充⽓情况。
蓄能器充⽓介质为氮⽓,将充⽓⼯具C处连到氮⽓瓶,从蓄能器上卸下保护帽和⽓阀帽,放松充⽓⼯具的锁紧螺母D,将螺母E与蓄能器上充⽓阀相连,然后拧紧D和B,把⼿柄A逆时针旋到底。
关闭充⽓⼯具,打开氮⽓瓶上的截⽌阀,调节氮⽓减压器,把氮⽓瓶的压⼒由减压器减到较低压⼒,顺时针慢慢转动⼿柄A,顶杆顶开充⽓阀,然后让氮⽓缓缓充⼊⽓囊,看压⼒表压⼒到要求为⽌,充⽓压⼒为1.2倍P⼀级值。
充⽓完毕应将⼿柄A逆时针旋到头,关闭充⽓⼯具。
在关闭截⽌阀和减压器后,应打开充⽓⼯具上的放⽓塞B,放掉管路上的残余⽓体,然后卸下充⽓⼯具,检查有⽆漏⽓,最后装上⽓阀帽和保护帽。
蓄能器充⽓时,应打开截⽌阀15,在蓄能器内油压压⼒达到零后进⾏。
2.4按液压站的电控原理图检查配接电线是否正确。
2.5油箱加满油后,点动开关检查电机转向,从泵的轴端看,顺时针⽅向为正确,如果电机反转,重新对电机进⾏接线,防⽌损坏油泵3 调试后的技术性能达到以下的要求:3.1 油压稳定:⼯作油压在1MPa~0.8Pmax之间变化时不允许有⼤于±0.6MPa压⼒振摆现象, 不允许有振幅⼤于0.2 MPa的⾼频振荡。
高线液压、润滑系统在线循环酸洗、冲洗施工方案
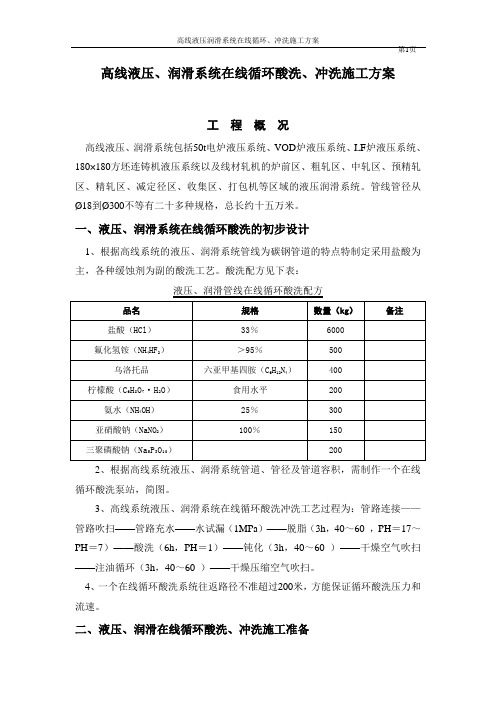
高线液压、润滑系统在线循环酸洗、冲洗施工方案工程概况高线液压、润滑系统包括 电炉液压系统、 炉液压系统、 炉液压系统、 方坯连铸机液压系统以及线材轧机的炉前区、粗轧区、中轧区、预精轧区、精轧区、减定径区、收集区、打包机等区域的液压润滑系统。
管线管径从 到 不等有二十多种规格,总长约十五万米。
一、液压、润滑系统在线循环酸洗的初步设计、根据高线系统的液压、润滑系统管线为碳钢管道的特点特制定采用盐酸为主,各种缓蚀剂为副的酸洗工艺。
酸洗配方见下表:液压、润滑管线在线循环酸洗配方2、根据高线系统液压、润滑系统管道、管径及管道容积,需制作一个在线循环酸洗泵站,简图。
3、高线系统液压、润滑系统在线循环酸洗冲洗工艺过程为:管路连接——管路吹扫 管路充水 水试漏( ) 脱脂( , ~ , = ~ = ) 酸洗( , = ) 钝化( , ~ ) 干燥空气吹扫 注油循环( , ~ ) 干燥压缩空气吹扫。
、一个在线循环酸洗系统往返路径不准超过 米,方能保证循环酸洗压力和流速。
二、液压、润滑在线循环酸洗、冲洗施工准备1、人员准备:液压、润滑系统管线在线循环酸洗工作是技术性复杂、工艺麻烦、责任心很强的工作,施工单位必须选派专职技术人员负责,组织专业酸洗队伍,并要在施工前进行技术培训,搞好技术交底工作。
2、材料、设备的准备:高线系统液压、润滑管线在线循环酸洗、冲洗材料、设备3、外部环境条件准备①循环酸洗需用自来水(PH6~7)必须保证。
需上一条从50t电炉到轧线5.3米平台临时供水管线。
②压缩空气是循环酸洗工作必备条件,必须保证压力和流量。
③蒸汽也是循环酸洗工作的必备条件,也必须保证。
④废酸液要能及时排放,还保证不污染环境。
三、液压、润滑系统管线在线循环酸洗、冲洗回路的联接1、液压润滑管线在线循环酸洗冲洗回路联接前的要求:①液压、润滑系统在线循环酸洗前,站内、站外轧线上的所有的管材、管件都要安装,焊接完毕形成工作状态。
②所有法兰、活接头联接处都要拆下检查,发现问题(即管线内壁焊缝处有结瘤、残渣)要打磨干净,用压缩空气将管线内部吹扫干净,由业主方代表检查合格方可二次安装,二次安装前需把法兰、活接头接口端面清理干净,涂上干油加装密封垫后紧固到位。
液压管路油循环冲洗操作流程
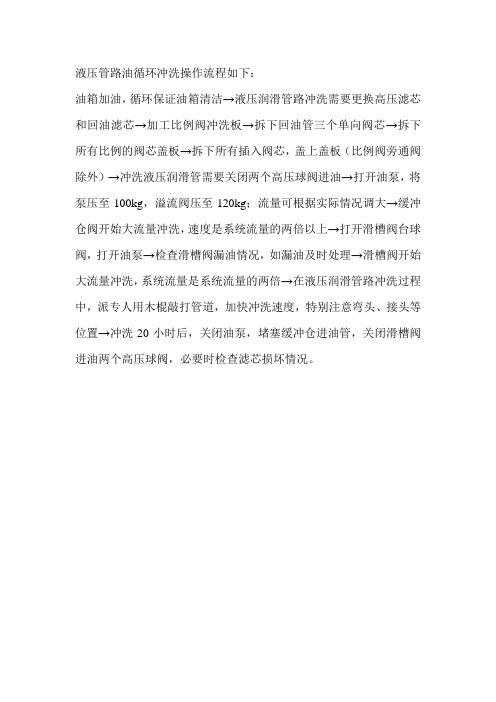
液压管路油循环冲洗操作流程如下:
油箱加油,循环保证油箱清洁→液压润滑管路冲洗需要更换高压滤芯和回油滤芯→加工比例阀冲洗板→拆下回油管三个单向阀芯→拆下所有比例的阀芯盖板→拆下所有插入阀芯,盖上盖板(比例阀旁通阀除外)→冲洗液压润滑管需要关闭两个高压球阀进油→打开油泵,将泵压至100kg,溢流阀压至120kg;流量可根据实际情况调大→缓冲仓阀开始大流量冲洗,速度是系统流量的两倍以上→打开滑槽阀台球阀,打开油泵→检查滑槽阀漏油情况,如漏油及时处理→滑槽阀开始大流量冲洗,系统流量是系统流量的两倍→在液压润滑管路冲洗过程中,派专人用木棍敲打管道,加快冲洗速度,特别注意弯头、接头等位置→冲洗20小时后,关闭油泵,堵塞缓冲仓进油管,关闭滑槽阀进油两个高压球阀,必要时检查滤芯损坏情况。
液压管路冲洗要求

液压管路冲洗要求管道处理1在管路安装施工前需对管道进行酸洗处理,清除氧化物和杂质。
2施工完成后,再对整个管路进行酸洗、脱脂、钝化、中和处理,可根据现场条件采用离线和在线方式进行,一般情况都采用新设泵源、在线循环方式,利用四合一清洗液进行管路清洗处理。
3利用在线循环方式进行管道冲洗处理应连续作业,一般在24h后开始检查管口冲洗质量,冲洗流体的流速应≥1.5m/s。
管路循环冲洗管道处理完毕后,再对管路进行循环冲洗,以彻底清除管内杂物。
1 循环冲洗的方式站内循环冲洗:指对液压泵站内的管路进行的循环冲洗,此项工作一般在制造厂进行,不用在施工现场进行。
站外循环冲洗:指对液压泵站到执行机构之间的管线进行的循环冲洗。
线外循环冲洗:指对液压系统的某些管路或集成块,拿到另一处组成回路,进行循环冲洗,冲洗合格后再装回系统中。
为了便于施工,通常采用站外循环冲洗方式,也可根据实际情况后将两种冲洗方式混合使用,达到提高冲洗效果,缩短冲洗周期的目的。
对于工作压力在9~15Mpa、采用叶片泵的辅助低压系统,在流量允许情况下可直接利用本系统采用站外循环冲洗方式进行管路循环冲洗;对于工作压力≥21Mpa、采用轴塞泵(或变量泵)的高压系统或伺服系统,应先另设泵源进行管路的冲洗,在油液清洁度≥8级(NAS)时,再利用本系统进行管路循环冲洗。
2冲洗回路的选定对于冲洗回路的选择,必须根据系统功率、排量确认每条冲洗回路中管道内的流体流速达到冲洗要求(见“循环冲洗注意事项”)进行确定,也可根据实际情况,在现有能力下对回路进行分段冲洗。
冲洗回路一般有以下几种形式:1)并联回路:采用此回路的优点是循环冲洗回路较短,管路口径相近,容易掌握、效果较好;缺点是回路连接繁琐,不易检查确定每一条管路的冲洗效果,冲洗泵源较大。
2)串联回路:采用此回路的优点是回路连接简便、方便检查、效果可靠;缺点是回路长度较长。
3)混合回路:对于管路口径变化较大,回路连接繁琐且管路较长的系统可采用此回路方式进行冲洗,但各回路的管径应基本一致(压力损失基本相同),以确保各管路的流速达到冲洗要求;此方式兼有并、串联回路的优点。
- 1、下载文档前请自行甄别文档内容的完整性,平台不提供额外的编辑、内容补充、找答案等附加服务。
- 2、"仅部分预览"的文档,不可在线预览部分如存在完整性等问题,可反馈申请退款(可完整预览的文档不适用该条件!)。
- 3、如文档侵犯您的权益,请联系客服反馈,我们会尽快为您处理(人工客服工作时间:9:00-18:30)。
液压系统管路的循环冲洗
摘要:介绍了液压系统管路循环冲洗的方法和步骤,并在实际生产维护中得到应用。
经过严格的冲洗,可以减少和避免系统调试和早期运行中的故障,缩短系统的调试周期,减少损失,有效的提高了生产率。
关键词:管路循环冲洗;清洗工艺;可靠性;使用寿命;液压循环管路
作为自动化程度较高的铜板带材加工企业,液压系统的应用十分广泛。
液压传动技术有其不可比拟的优点,但是,其抗污染能力低是比较突出的弱点。
据有关资料,液压故障有70%~80%是由油液污染导致的。
污染物混入液压系统后会加速液压元件的磨损、烧伤,甚至破坏,堵塞严重时会因阻力过大而将滤芯(网)击穿,完全丧失过滤作用,造成液压系统的恶性循环。
即使专业的安装维护人员处理不当也可能埋下故障隐患。
管路冲洗的主要步骤为:循环酸洗、油冲洗和管路复原,下面主要对油冲洗进行说明。
一、管路的循环冲洗
管路油冲洗是管路施工的重要环节。
管路循环冲洗必须在管路酸洗和二次安装完毕后的较短时间内进行。
目的是为了清除管路内在酸洗或安装过程中以及液压元件制造过程中遗落的机械杂质或其他微粒,达到液压系统正常运行时所需要的清洁度。
根据控制元件的不同,液压系统可分为伺服系统、比例系统和普
通系统等。
通常,伺服系统油液清洁度需达到nas1638的5级要求;比例系统油液清洁度需达到nas1638的7级要求;普通系统油液清洁度需达到nas1638的9级要求。
冲洗油一般采用专用洗油或与工作介质相同的液压油,冲洗时油液流速需为紊流状态(雷诺数
re>3000)
1.1 油冲洗的方式
油冲洗方式较常见的有站内循环冲洗、站外循环冲洗、管线外循环冲洗等。
1.2 循环冲洗主要工艺流程及参数
(1)冲洗流量:视管径大小、回路形式进行计算,保证管路中油流成紊流状态,管内油流的流速应在3m/s以上。
(2)冲洗压力:冲洗时,压力为0.3-0.5mpa,每间隔2小时升压一次,压力为1.5-2mpa,运行15-30分钟,再恢复低压冲洗状态,从而加强冲洗效果。
(3)冲洗温度:用加热器将油箱内油温加热到40-60℃,冬季施工油温可提高到80℃,通过提高冲洗温度能够缩短循环冲洗时间。
(4)振动:为彻底清除粘附在管壁上的氧化铁皮等杂质,在冲洗过程中每间隔3-4小时用木锤、铜锤、橡胶锤或使用震动器沿管线从头至尾进行敲打震动。
重点敲打焊缝、法兰、变径、弯头及三通等部位。
敲打时要环绕管壁四周均匀进行,不得伤害管子外表面。
一般的,震动器的频率为50-60hz,振幅为1.5-3mm为宜。
[3]
(5)充气:为了进一步加强冲洗效果,可向管内充入
0.4-0.5mpa的压缩空气,造成管内冲洗油的紊流状态涡流,充分搅起杂质,增强冲洗效果。
每班可充气两次,每次8-10min。
空气压缩机出口处要装有精度较高的过滤器。
某单位在某进口轧机液压系统管路冲洗中,安装人员用外接总排量为1400l/min的cb齿轮泵对管路进行冲洗,额定压力为2.5mpa,溢流阀设定为3mpa,油液温度约40℃,在线式冲洗,用冲洗板将各种控制阀短接,将执行元件用胶管接成短路,用vg46液压油冲洗480小时,并不断更换滤芯,油液最终颗粒度达到nas 5级满足设备要求,但是依然存在冲洗不彻底的问题。
安装人员认为流量决定了流速,只要有流量流速就能保证,和泵的压力无关,这就是理解误区。
液体从一个表面冲走颗粒并携带至下游的能力正比于液体在元
件表面的能量的大小。
在层流流动中,元件的表面有一个液体的稳态层,作用于元件表面的作用力很小,从液流研究中得到的实验数据表明,液体中流速各不相同,液体中心的速度最高,管壁出液体流速为零。
如果一个颗粒太小而潜入层流边层(速度为零、靠近液体表面的静止层),则通过冲洗就不能将其除去。
要除去一个颗粒,该颗粒直径就应该是层流边层厚度的两倍
综上所述要提高冲洗效率,采用紊流冲洗是最有效的,剧烈的紊流能够减小层流层的厚度并冲刷管壁,将颗粒卷走。
紊流程度的大小由雷偌数决定:
雷诺数(re)的公式:re=1000vd/ν
式中:v—流速(m/s);
d—管内径(mm);
ν—液压油的运动黏度(mm2/s);如vg46号液压油在40oc下黏度为46 mm2/s。
摩擦系数(λ)的公式:λ=0.3164*re-0.25,
式中:re介于2300~10000(光滑金属圆管)之间。
压差(pa)的公式:△p=v2*λ*l*ρ/(2*d),
式中:△p —压差(mpa);
l—管路长度(m);
ρ—液压油密度(870~900kg/m3);
v—平均流速;
对于光滑金属管,紊流需要re﹥2300
对于前述的液压系统,参数如下:
泵理论流量q:1400l/min;
管径d:最大ф90mm
长度l—10m(直管,不考虑分管和弯头压力损失);
油粘度υ—46mm2/s(40℃时vg46机械油);
油密度ρ—900kg/m3。
由公式:雷诺系数 re=1000vd/υ=21.22q/1000dυ(1)
摩擦系数λ=0.3164/re0.25 (2)
式中 v——液压油在管道中的流速m/s;
v= q10-3 /60 = 21.22q/d2 = 3.67m/s
3.1416d2 10 -6/4
代入数据,得re为7180,λ为0.0344。
管路的沿程压力损失:
δp =ρgλlv2/(d2g)(3)
得理论δp =23.2 mpa﹥3mpa
变换(3)式,计算该系统要达到紊流冲洗所必须具备的冲洗压力,选取雷诺数re为2300,代入(2)式,得λ为 0.0457。
根据(1)式,得速度v=1.2m/s,则依(3)式δp=3.29mpa,这就是紊流冲洗的最低冲洗压力,低于该压力管路冲洗达不到紊流条件。
达到紊流的最小流量为q=vd 2/21.22=458 l/min就够了,当冲洗ф90管路,冲洗压力超过3mpa时,部分流量要通过溢流阀流回油箱。
实际冲洗ф90管路时泵压只有1mpa左右,没能达到紊流条件,所以说虽然油液最终颗粒度达到nas 5级满足了设备要求,但是冲洗管路不彻底,只是把油液清洁度提高了。
下来再看小管径的冲洗:
取小管径d=ф20mm,l=100m,re=2300其余不变,计算得
得λ= 0.0457,v=5.29m/s,
最小压差δp=ρ(0.3164/re0.25)l(reυ/1000d)2/2d =2877.5 mpa
这显然无法达到,所以有
由δp=ρ(0.3164/re0.25)l(reυ/1000d)2/2d 化简得
δp=1.58×10-7×ρre+1.75lυ2/d3
当re=2300,ρ为定值时,由上可见减小管路长度l,和运动粘度υ可以减小最低冲洗压力δp,尤其是υ的降低可以更显著地降低δp,降低υ可以通过加温实现。
提高系统的油温,雷诺数可提高几倍甚至十几倍。
升温可通过电加热器进行,也可采用系统调压阀循环加热。
当油温达60℃以后停止加热,向系统供压油进行冲洗。
降至常温后再升温,整个冲洗过程油温与时间关系见图1。
图1 高温冲洗曲线
由以上计算可知,对小管径而言,要保证冲洗在紊流状态下进行就必须提高系统的冲洗压力和介质的温度。
加温和高压是大流量(紊流)的必要条件。
同时在冲洗过程中,还要周期性的反复升降力,以产生冲击,冲掉附着在管道内壁的杂物。
为了提高冲洗效果,在冲洗过程中的液压泵以间歇运动为佳,其间歇时间一般为10~30分钟,可在这一间歇时间内检测冲洗效果。
在冲洗过程中,为了有利于管内壁上的附着物脱落,可以用木棒或橡皮锤等非金属锤轻轻敲击管道,可连续或间歇地敲击。
冲洗过程中还应该注意以下事项:
(1)油箱使用前用半干面团清洁,油箱要封闭,减少现场空气中颗粒进入油箱的机会;
(2)向油箱中加入冲洗油时应使用带过滤器的加油小车,以滤除桶装油中的污染物;
(3)更换滤芯时暂停冲洗泵,注意不要带入杂质;
(4)对排空和排污要定期进行,以确保系统充满,并及时排出气体和污染物;
(5)在冲洗的前期,油中水分蒸发很重要,在冲洗油箱上应有蒸汽逸出的窗口;
(6)冲洗合格后在抽出冲洗油、管线使用前要注意保护,以免污染物进入系统。
系统冲洗后即可将所有元件、管道按要求连成工作回路。
此过程要特别注意管接头的清洁,连接完毕后尽量避免拆卸,必要时要注意用干净的布包扎好,确保管接头、管口不受污染。
三、总结
液压系统的污染控制贯穿于整个加工及组装过程,要求操作者每一步都要采取保洁措施,最大限度地降低液压系统污染,确保液压系统能够安全、可靠地运行。
任何抱有侥幸心理而放弃清洗和不当的方法都会对设备带来致命的损害。
经过严格的冲洗后,可以减少和避免系统调试和早期运行中的故障,缩短系统的调试周期,减少不必要的损失。
但是,系统的污染控制是一个不断进行的过程,不可能一劳永逸,在系统的运行期间还要定期检测油液状态,并控制污染物使其保证在系统允许的清洁度范围内。
参考文献
[1] 成大先.机械设计手册(第4版)[m].北京:化学工业出版社,2002.
[2] 路甬祥.液压气动手册[m].北京:机械工业出版社,2005.
[3] 何席兵.液压系统管路酸洗处理工艺[j].人民长江,2008,39(10):37-38.。