PCB常见缺陷及可接受标准
PCB常见缺陷及可接受实用标准

PCB常见缺陷及可接受实用标准PCB(Printed Circuit Board,印刷电路板)是现代电子产品中最常见的一种组件,它通过电路的印刷、组装和焊接,将电子元件连接在一起,实现电子设备的功能。
然而,在PCB的制造过程中,常会出现一些缺陷,这些缺陷可能影响电子设备的性能和可靠性。
因此,制造PCB时必须要遵循一些可接受的实用标准,以确保PCB的质量。
1.焊接质量不良:焊接是将电子元件连接到PCB上的重要步骤。
当焊接质量不良时,会导致焊点不牢固,甚至存在焊接虚焊的情况。
这些问题会导致电子元件的连接不可靠,对PCB的性能和可靠性产生负面影响。
2.电路导通不畅:PCB上的导线和线路是电子元件之间传递信号的重要媒介。
如果导线和线路不通畅,就会导致信号传输受阻,影响电子设备的正常工作。
常见的导通不畅问题包括导线断开、导线短路和导线粘连等。
3.隔离不良:在PCB上,不同的电路往往需要隔离开来,以防止相互干扰。
当隔离不良时,就会出现电路互相干扰的情况,影响电子设备的信号稳定性和抗干扰能力。
隔离不良的表现包括隔离距离不足、隔离层不牢固和隔离层污染等。
4.电器仿真效果不佳:在PCB设计阶段,常常需要进行电气仿真,以验证电路设计的正确性和性能。
如果电气仿真效果不佳,就会导致电路设计存在缺陷,无法满足性能要求。
电器仿真效果不佳的原因可以是元件模型不准确、电路参数设置错误和仿真软件问题等。
为了确保PCB的质量,制造业界制定了一些可接受的实用标准,使制造商和消费者能够统一对PCB的质量进行评估。
其中最重要的标准之一是IPC-A-600,它是IPC(Institute of Printed Circuits,印制电路协会)颁布的标准,用来评估PCB的外观和可接受的缺陷等级。
IPC-A-600将PCB的缺陷分为多个等级,从IPC-A-600A到IPC-A-610F,每个等级都对缺陷的种类、数量和位置进行详细的规定,以便制造商和消费者能够根据需求选择合适的等级。
pcb常见缺陷原因与措施

加强操作人员的安全意识教育, 确保生产过程中的安全和稳定。
04
PCB常见缺陷的检测方法与技 巧
目视检测法
直接观察PCB表面
通过肉眼或放大镜观察PCB表面是否存在裂纹、变形、气泡、污 渍等缺陷。
检查焊接质量
目视检测法可以用于检查焊接质量,如焊点大小、形状、光泽度等 是否符合要求。
识别元器件
目视检测法可以用于识别元器件的型号、规格、极性等是否正确。
焊盘腐蚀
使用合适的清洗剂清洗腐蚀的焊盘,然后用烘干机烘干。
阻焊层缺陷修复方法与技巧
阻焊层脱落
使用合适的涂料重新涂刷脱落的阻焊层,然后用烘干机烘 干。
阻焊层变色
使用合适的清洗剂清洗变色的阻焊层,然后用烘干机烘干 。
阻焊层起泡
检查阻焊层起泡原因,如果是由于涂层过厚导致,可以使 用砂纸打磨起泡区域,然后重新涂刷阻焊层,最后用烘干 机烘干。
生产设备问题
总结词
设备故障或误差
详细描述
PCB生产过程中使用的设备,如钻孔机、曝光机、蚀刻机等,如果出现故障或误 差,可能导致PCB出现孔径不准确、线路不清晰、蚀刻过度等缺陷。
生产工艺问题
总结词
工艺参数不当
详细描述
PCB生产过程中的各项工艺参数,如温度、压力、时间等,如果设置不当,可能导致PCB出现翘曲、起泡、氧化 等缺陷。
优化生产工艺和流程
对生产工艺和流程进行持续改 进,提高生产效率和产品质量 。
引入先进的生产技术和设备, 提高生产自动化程度。
优化生产布局和物流管理,减 少生产过程中的浪费和损失。
提高操作人员技能和素质
加强操作人员技能培训,提高操 作人员的技能水平和操作规范意
识。
建立激励机制,鼓励操作人员积 极参与技术革新和改进活动。
pcb板检验及接收标准
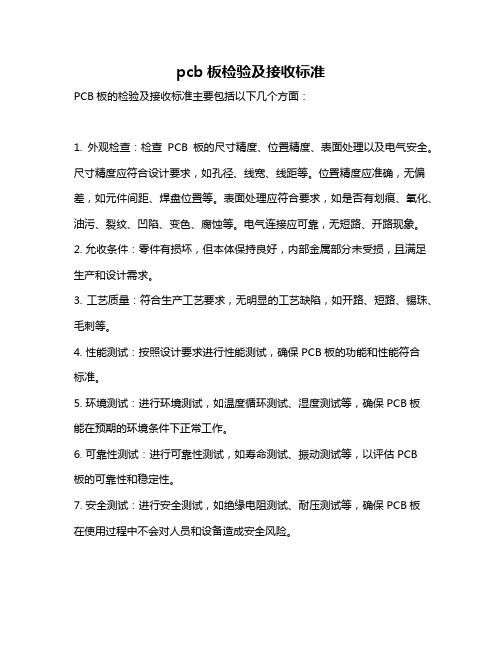
pcb板检验及接收标准
PCB板的检验及接收标准主要包括以下几个方面:
1. 外观检查:检查PCB板的尺寸精度、位置精度、表面处理以及电气安全。
尺寸精度应符合设计要求,如孔径、线宽、线距等。
位置精度应准确,无偏差,如元件间距、焊盘位置等。
表面处理应符合要求,如是否有划痕、氧化、油污、裂纹、凹陷、变色、腐蚀等。
电气连接应可靠,无短路、开路现象。
2. 允收条件:零件有损坏,但本体保持良好,内部金属部分未受损,且满足生产和设计需求。
3. 工艺质量:符合生产工艺要求,无明显的工艺缺陷,如开路、短路、锡珠、毛刺等。
4. 性能测试:按照设计要求进行性能测试,确保PCB板的功能和性能符合
标准。
5. 环境测试:进行环境测试,如温度循环测试、湿度测试等,确保PCB板
能在预期的环境条件下正常工作。
6. 可靠性测试:进行可靠性测试,如寿命测试、振动测试等,以评估PCB
板的可靠性和稳定性。
7. 安全测试:进行安全测试,如绝缘电阻测试、耐压测试等,确保PCB板
在使用过程中不会对人员和设备造成安全风险。
8. 文件资料:提供完整的生产记录、检验报告等文件资料,以便后续的质量追溯和问题解决。
在检验及接收PCB板时,需综合考虑以上各个方面,确保所采购或生产的PCB板符合质量要求和设计标准。
PCB常见缺陷及可接受实用标准

常见缺陷图片以及接受标准1、孔偏2、异形槽孔毛刺 3..铅锡堵孔接受标准:环宽不小于 0.05mm,且应小于90度。
偏孔数量不超过总数量的5% 。
接受标准:孔内毛刺不能影响客户装配,达到最小孔径要求;接受标准:对于插件孔不影响孔径的孔内聚锡可以接受,不允许孔内堵孔。
4、孔内毛刺 5..偏孔,变形 6. 孔壁空洞文档大全接受标准:1、孔壁质量满足最低要求。
2、未违反孔径要求的下限。
接受标准:孔径大小在公差范围内;不能有明显变形,通常变形的量不超过0.05mm.接受标准(IPC标准):1、任何孔不可超过3个破洞,发生破洞的孔不超过总孔数的5%;2、任何破洞不超过孔长的5%和孔周的1/4。
7、焊盘破损(缺损)8、孔(边)内毛刺9、过孔锡珠接受标准:导体连接处永不可低于0.05mm之宽度,或不可低于起码线宽,两者以数字较小者为允许准则。
接受标准:对于孔(内)边毛刺要求不能影响最小孔径。
接受标准:对于过孔内目视不能有成颗粒的锡珠,焊接时锡珠不能流出孔内。
10、内层偏移11、红孔/黑孔12、焊盘破损接受标准:1、最小环宽不能低于客户要求或0.05mm。
2.图形的偏移不影响任何间距(含内层焊盘与铜区之间,接受标准:(元件孔)化金及铅锡厚度均匀并涵盖到孔内无露铜之现象;(过孔)每块接收3-5个。
接受标准:1、对于SMT焊盘破损不能小于长和宽的20%,破损面积小于焊盘面积的10%;文档大全文档大全焊盘相互之间),通常要求所影响距离不可以多于设计的+/-20%;2、对于插件孔焊盘最小环宽需保持0.05mm ,起破损不能超过环长度的25%或2.5mm 。
13、DR2偏孔14、DR2 孔偏15、偏孔接受标准:二次孔不允许与板边相切,且最小剩余位置不得出现分层(白边)情况、油墨脱落情况。
接受标准:孔径必须在公差范围内;位置偏移小于0.05mm.接受标准:要求孔环至少在0.05mm 以上(上图为可接受缺陷)。
16、油墨入孔17、散热孔边聚锡18.过孔油墨高出板面接受标准:1.对于过孔,如果客户无特殊要求则允许油墨入孔;2.对于插件孔,原则上不允许油墨入孔;接受标准:整体平整,聚锡不能高出SMT 焊盘。
pcb常见缺陷原因与措施

焊点氧化
长时间存储可能导致焊点氧化,引起接触不良 或开路。
结构变化
长时间存储可能导致PCB结构变化,如弯曲或变形。
04
检测与修复过程中的常见缺陷 原因
检测设备故障或精度不足
设备老化
设备长时间使用可能导致 部件磨损,影响检测精度 。
设备维护不当
定期维护和保养不到位, 可能导致设备故障。
设备校准问题
制定操作规范
制定详细的操作规范和作业指导书,确保员工严格按照规范进行操 作。
建立激励机制
建立员工激励机制,鼓励员工积极学习和提高自己的技能水平。
加强运输和存储环节的管理和监控
确保运输安全
选择具有良好信誉和稳定运输能力的物流公司,确保 产品在运输过程中不受损坏或丢失。
加强存储管理
制定存储管理规定和操作规范,确保产品存储环境良 好,避免产品在存储过程中受损或变质。
进行定期检查
对存储和运输环节进行定期检查,及时发现和处理可 能出现的问题。
06
针对不同类型缺陷的具体应对 措施建议
针对原材料问题的应对措施建议
严格控制原材料质量
对供应商进行评估和选择,确保原材料的质 量稳定可靠。
加强原材料检验
对进料进行严格检验,确保符合设计要求和 相关标准。
建立原材料追溯体系
对原材料进行标识和追溯,以便及时发现和 解决问题。
设备校准不准确,导致检 测结果偏差。
修复技术不当或材料问题
修复方法选择不当
针对不同缺陷应采用不同的修复方法 ,选择不当可能导致修复效果不佳。
材料质量问题
修复工艺问题
修复过程中工艺控制不当,如温度、 压力、时间等参数控制不准确,可能 导致修复失败。
pcb板检验及接收标准
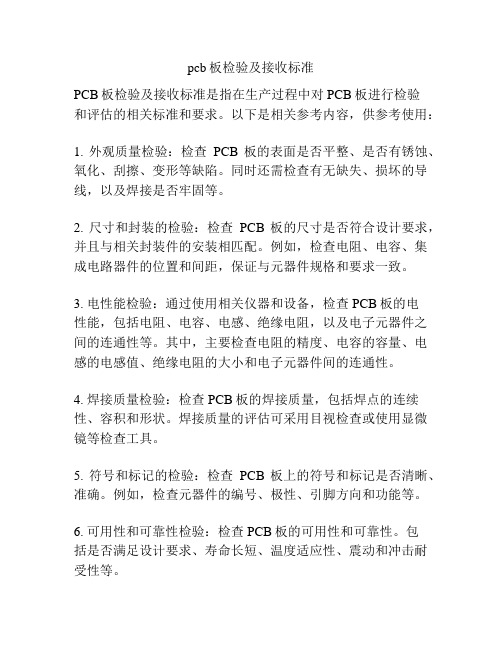
pcb板检验及接收标准PCB板检验及接收标准是指在生产过程中对PCB板进行检验和评估的相关标准和要求。
以下是相关参考内容,供参考使用:1. 外观质量检验:检查PCB板的表面是否平整、是否有锈蚀、氧化、刮擦、变形等缺陷。
同时还需检查有无缺失、损坏的导线,以及焊接是否牢固等。
2. 尺寸和封装的检验:检查PCB板的尺寸是否符合设计要求,并且与相关封装件的安装相匹配。
例如,检查电阻、电容、集成电路器件的位置和间距,保证与元器件规格和要求一致。
3. 电性能检验:通过使用相关仪器和设备,检查PCB板的电性能,包括电阻、电容、电感、绝缘电阻,以及电子元器件之间的连通性等。
其中,主要检查电阻的精度、电容的容量、电感的电感值、绝缘电阻的大小和电子元器件间的连通性。
4. 焊接质量检验:检查PCB板的焊接质量,包括焊点的连续性、容积和形状。
焊接质量的评估可采用目视检查或使用显微镜等检查工具。
5. 符号和标记的检验:检查PCB板上的符号和标记是否清晰、准确。
例如,检查元器件的编号、极性、引脚方向和功能等。
6. 可用性和可靠性检验:检查PCB板的可用性和可靠性。
包括是否满足设计要求、寿命长短、温度适应性、震动和冲击耐受性等。
7. 环保和安全性检验:检查PCB板的环境友好性和安全性。
包括检查是否符合相关环保标准,如RoHS要求,并确保PCB板的使用不会对人体和环境造成损害。
PCB板的接收标准可根据不同的需求和行业标准来制定,以确保PCB板的质量和性能。
标准的制定需要考虑到PCB板的用途、工作条件和相关要求。
一般来说,接收标准应包括上述的外观质量、尺寸和封装、电性能、焊接质量、符号和标记、可用性和可靠性、环保和安全性等检验内容,并制定了相应的合格标准和接受标准。
综上所述,PCB板检验及接收标准是保证PCB板质量的重要环节。
通过对PCB板各项指标的检查和评估,可以确保PCB板的性能和可靠性,提高产品的质量,并满足相关要求和标准。
PCB缺陷判定与接收标准对照

浙江柳市线路板有限公司PCB 缺陷判定与接收标准对照页数 第1页共21页A线路铜箔凹坑,如右图“A ”处的剖面图,浙江柳市线路板有限公司PCB缺陷判定与接收标准对照页数第2页共21页理想标准线路无缺陷。
s ≤0.1mm ²h 表示沙孔大小制作:潘安超 2008-9-15沙孔超过标准要求第1条,不接收。
浙江柳市线路板有限公司PCB 缺陷判定与接收标准对照页数 第5页共21页制作:潘安超 2008-9-15浙江柳市线路板有限公司PCB 缺陷判定与接收标准对照页数 第6页共21页氧化点 S <1χ1mm ²S >3χ5mm²超过标准要求第1条,不接收。
制作:潘安超2008-9-15浙江柳市线路板有限公司PCB缺陷判定与接收标准对照页数第7页共21页浙江柳市线路板有限公司PCB 缺陷判定与接收标准对照页数 第8页共21页锡高H >0.3mm制作:潘安超 2008-9-15超出标准要求,不接收。
L <0.05mm超出2、3级标准要求,不接收。
浙江柳市线路板有限公司PCB 缺陷判定与接收标准对照页数 第11页共21页H<0.075mm表示油墨在孔壁的四周浙江柳市线路板有限公司PCB 缺陷判定与接收标准对照页数 第12页共21页W >0.3mmW <0.075mm在2级标准要求范围内,可接受。
客户特别要求除外。
超出标准要求2、3级,不接收。
浙江柳市线路板有限公司PCB 缺陷判定与接收标准对照页数 第13页共21页标准要求:(气泡)1 线与焊盘间的阻焊油墨气泡宽度h 不超过间距的20%,2级标准都可接收。
3级标准不接收,2 线路到焊盘间的气泡S ≤0.1mm ²,且不超过三个点,3级标准可接收。
3 线路到焊盘间的气泡S ≤0.2mm ²,且不容许超过三个点,2级标准可接收。
4 以上是指在用3M 胶带拉不掉油下可接收的范围。
浙江柳市线路板有限公司PCB缺陷判定与接收标准对照页数第14页共21页PCB缺陷判定与接收标准对照页数第15页共21页PCB缺陷判定与接收标准对照页数第16页共21页h >0.15mm锡面粗糙超出2、3级接收标准,不接收。
PCB可靠性缺陷分析及相关标准

二、层压
4)固化度不足: 现象:
1)板件容易变形; 2)易爆板; 3)钻孔时钻污很多,易造成孔壁粗糙度超标; 4)因钻污多,凹蚀时不容易去除,易造成孔壁与内
层连接不良。
原因:料温异常或层压曲线与B片不匹配; 标准:ΔTg≤3℃
9
三、机械钻孔
1)孔内纤维丝:
原因:钻咀侧刃不锋利; 标准:不影响孔径及不影响孔铜厚度及质量
2
内容:
一、 棕(黑)化
二、 层压
三、 机械钻孔
四、 激光钻孔
五、 PTH
六
电镀
七、 蚀刻
八、 填孔
九、 感光
十、 沉金
十一、 沉锡
十二、 沉银
十三、 其他
3
一、棕(黑)化
1)爆板:
原因:棕(黑)化不良 热冲击后大铜面处出现分层 标准:不允许
4
一、棕(黑)化
2)离子污染超标:
10
三、机械钻孔
2)钻偏:
成因:钻孔时零位漂移、钻机压脚没有压紧或钻孔补偿不匹配等;
标准:最小内层焊盘≥1mil或满足客户要求
11
三、机械钻孔
3)内层环宽:
原因:钻偏或内层涨缩与钻孔补偿不匹配; 标准:最小的环宽≥0.025mm 或满足客户要求
12
三、机械钻孔
4)内层隔离环宽
原因:钻偏或内层涨缩与钻孔补偿不匹配; 标准:最小的隔离环宽≥0.1mm
32
六、电镀
4)叠镀
原因: 1)孔壁粗糙度太大. 2)沉铜效果不好,没有将 孔壁覆盖完全. 3)电镀缸光剂/整平剂比例 失调. 4)电镀缸氯离子浓度过高. 5)电镀参数设定不当
定的最小值 ,芯吸作用(A)没有超过80mm[3.150min]
PCB品质控制常见缺点及标准

•3.0綠油缺點
缺點名稱﹕綠油擦花
•擦花不得露 出底材或線 路﹐在 100×150㎜范 圍內只允許 1×30㎜條狀刮 痕兩條﹐點 狀擦花在1×1 ㎜內三點可 接收
PPT文档演模板
PCB品质控制常见缺点及标准
•綠油缺點
缺點名稱﹕綠油气泡
•直徑不超過 0.25mm﹐每 面只允許2個 ﹐不橋接線 路可接收
PPT文档演模板
PCB品质控制常见缺点及标准
•綠油缺點
缺點名稱﹕綠油下有雜物
•不可接收
PPT文档演模板
PCB品质控制常见缺点及标准
•綠油缺點
缺點名稱﹕Undercut
•小于 2mil可 接收
PPT文档演模板
PCB品质控制常见缺点及标准
•綠油缺點
缺點名稱﹕對位偏
•BGA區域不允許 綠油上墊﹐其余 上墊不超過2mil 可接收
PPT文档演模板
PCB品质控制常见缺点及标准
•綠油缺點
缺點名稱﹕顯影不淨(滲油)
•上墊不超過 2mil可接收
PPT文档演模板
PCB品质控制常见缺点及标准
•綠油缺點
缺點名稱﹕綠油橋脱落
•不允許
PPT文档演模板
PCB品质控制常见缺点及标准
•綠油缺點
缺點名稱﹕綠油起皺
•不露出 線路﹐能 滿足附著 力要求可 接收
•SMD/BGA/PAD缺點
缺點名稱﹕SMD、BGA、光学点有綠油
•綠油上墊 邊不可超过 2mil﹐BGA 光学点不允 許有綠油
PPT文档演模板
PCB品质控制常见缺点及标准
•SMD/BGA/PAD缺點
缺點名稱﹕金面變色
•不可接收
PPT文档演模板
PCB品质控制常见缺点及标准
PCBA缺点判定标准Rev-C

E104 锡膏厚度不良Solder pastethicknessover spec锡膏厚度大于或小于规格值锡膏厚度不符合工程规格值不接受.E201零件偏位ComponentMisalignment零件突出焊垫位置1.引脚突出板子焊点宽度(W或P)的50%以上不接受(Chip零件);2.引脚突出板子焊点宽度(W或P)的50%或0.5mm以上不接受(SMT IC); 选择较小值.* W & P: 取宽度之较小者.E202零件错误WrongComponent所安装之零件和工程数据规格不一致1.零件料号与BOM要求不相符不接受;2.零件厂商及版本与BOM要求不符或非AVL厂商不接受.1003 1002標準值錯誤值WAE203零件侧立(SMT)ComponentMountingon Side芯片组件侧向(水平90度翻转)焊接在PAD上1.侧立零件最大尺寸不超过:(L)3 mm *(W)1.5mm可接受2.侧立零件被高零件挡住可接受.注: 若可接受之侧立零件每板每面超过5个则该板不可接受.E204少件MissingComponent依据工程数据之规定应安装的零件漏安装少件不接受.E205零件损伤DamagedComponent零件本体破损、龟裂、裂纹(缝)1.SMT零件破损露出本体或伤及零件功能部分不可接受.2.PTH零件破损露出本体或伤及零件功能部分不可接受.3.连接器破损至Pin脚部份或影响装备及功能不可接受(RJ45不允许有裂纹/缝).虛線部份為無零件(缺件)E206零件不良DefectiveComponent零件功能丧失或不符合其使用规格1.零件参数超出规格不接受.E207 零件印刷不良ComponentPrintingfail零件漏印刷、印错或印刷模糊1.零件油墨印刷或激光或标签贴纸,无法清楚辨识规格不接受;2.零件有印刷内容漏印或错误不接受.E208反白(SMT)Mountingupside down有标示的组件,标示一面朝向PCB,以致看不见其规格标示1.反白零件经确认功能与焊接良好后可接受,否则不接受.注: 若可接受之反白零件每板每面超过5个则该板不可接受.1003印刷不良1003絲印面E209多件ExtraComponentPCB上不应安装零件之位置安装有零件PCB上多件不接受.E210零件翘脚Co-planarity 贴片IC或零件脚高翘,未平贴板面IC或零件脚翘脚不允许E211零件反向ReversedComponent晶体管, 二极管,IC, 极性电容, 排阻或其它有方向性零件,其方向与PCB上记号相反极性零件不允许极性/方向反.電容“-”極PCB“-”極二極管“-”極PCB“+”極零件極性與PCB不一致E212碑立Tombstoning芯片组件竖立,焊接在一个PAD焊垫上不可有碑立现象.E301多锡ExcessSolder零件脚吃锡过量1.零件两端之锡量多达伤及零件本体;2.焊锡突出焊垫边缘.*. 凡符以上2点任意一点均不可接受.E302少锡InsufficientSolder零件任何一侧吃锡低于PCB厚度25%或零件焊锡端高度之25%(SMT)1.IC脚爬锡高度< 50%,或吃锡长度<50%;2.Chip零件焊锡带爬锡端高度<25%或0.5mm,取校小值;3.PTH零件吃锡<270o,或爬锡高度<75%;4.BGA 焊点吃锡面积<50%锡球面积 .*. 凡符以上任意一点均不可接受.(非功能支撑Pin除外).E303包焊Enclosedsoldering零件脚末端埋入焊点内看不到焊脚端部的轮廓不允许.E304空焊Open Solder 零件脚与PAD焊垫间完全无锡空焊不允许空焊.E305锡桥SolderBridge由于焊锡使不同电位两点之间电阻值为零或不应导通的两点导通锡桥不允许.E306锡尖SolderprojectionsPAD, 零件脚,螺丝孔焊锡凸出部份1.锡尖高度超出焊点之高度(2.3mm)2.锡尖与周围零件(焊点)之距离小于2.5mm.3.锡尖影响组装作业.*. 以上任意一点均不可接受.E307锡珠Solder Ball PCBA残留颗粒/珠状的焊锡1.P CBA上残留锡珠引起短路;2.P CBA表面残留锡珠直径>0.13mm且未贴附在金属表面;3.通孔内之锡珠直径ф>0.5.4.锡珠使PAD/铜箔之间距<0.13mm*. 凡符合以上任意1点均不可接受.反之,若不属于以上4点则可接受E308锡渣SolderSplashPCBA残留渣/丝状的焊锡残留锡渣不允许.注: 允收原则同锡珠.E309锡裂FractureSolder锡点出现裂纹或分离1.SMT零件焊点不允许有锡裂;2.零件脚与焊点间出现裂纹不允许.E310冷焊Cold Solder 锡焊锡熔合不完全或冷却不当使锡点表面颗粒状,灰暗无光泽冷焊不允许.E311 焊点腐蚀Soldercorrode焊点被化学物腐蚀,以致焊点不光滑或缺口1.焊点清洗未干,凈造成焊点腐蚀成灰暗色;2.焊点氧化或在铜上产生青绿色及发霉.*. 凡符以上2点任意一点均不可接受.E312 焊点针孔/气泡Pin hole焊点上出现细小空洞1.针孔之孔径超过吃锡面的1/4;2.针孔孔径未超过吃锡面的1/4,但针孔贯穿整个通孔焊点(PTH).3.BGA 焊点气泡直径>1/4锡球直径.*. 凡符以上3点任意一点均不可接受.E313 焊盘/Pad翘起Liftedlands/pads焊盘/Pad部分或全部与pcb基板分离翘起1.焊盘/Pad外缘翘起高度<1pad之高度,可以接受,若此现像连续发生或发生率大于1%时,需找到真正原因以改善制程.2.焊盘/Pad翘起高度>/=1pad之厚度不允许.E401脚长&脚短Lead toolong/short零件脚长歪斜足以引起与周围焊点或零件短路或超出规格值或引脚很短被焊锡包封1.Cable/Wire 引脚突出PCB (Lmax)大于5mm,其它零件脚突出PCB (Lmax)大于2.3mm不可接受.2.所有零件脚轮廓不清晰或突出PCB(Lmin)小于0.5mm不可接受.注: PCB厚度大于2.3mm时不适应此标准E402 Pin针沾锡SolderedpinsPin针上沾有多余的锡1.连接器Pin针沾锡影响Pin针尺寸;2.RJ45 内Pin针沾锡.3.镀金Pin或金手指沾锡.*. 凡符以上3点任意一点均不可接受.E403高低针Uneven pin Pin针高于或低于其它Pin针的高度连接器之Pin针高于或低于其它Pin针高度0.2mm以上不可接受.E404Pin针歪Bent pins Pin针歪斜或扭曲1.连接器Pin针歪斜尺寸大于Pin针宽度之1/2不可接受,2.Pin针歪影响插件作业困难者不可接受.3.Pin针出现一般目视可见之扭曲者不可接受.PCB基板CONNECTORPIN>0.2mmPCB基板CONNECTORPIN>1/2 D DE405绝缘入锡Insulatorsoldering零件引脚绝缘部份埋入焊锡中导线或其它零件之绝缘部份埋入焊锡均不接受.E406零件浮高Liftedcomponent零件本体离PCBPad的高度超过规定值1.插头连接器浮高 >0.5mm,2.立式组件浮高 > 1.5mm;3.卧式零件浮高 >1.5mm.*.凡符以上3点任意一点均不可接受.但大功率零件不在此限(耗散功率>1W的零件浮高必须> 1.5mm,否则不可接受).E408剪脚不良Pin cut fail焊点被剪或剪锡裂1.剪脚剪至焊点处引起焊点锡裂;2.剪脚剪至焊点处,且未进行补焊.*.凡符以上2点任意一点均不可接受.E501PCB 脏污PCB Dirty PCBA表面有脏污,影响外观1.PCBA板上油污或油墨面积超过2*2mm2不可接受.2.水溶性(油性)助焊剂未清洗干凈或残留有明显可见水纹不可接受.E502PCB烧焦PCB Burns PCB板线路或基板有烤焦发黄发黑PCB不可有焦黄(黑)现象.E503 PCB弯曲或扭曲PCB bow ortwistPCB 4个角不在同一平面上或与板中间不在同一平面上1.PCBA SMT回焊后弯曲/扭曲度>0.75%.2.PCBA PTH波峰焊后弯曲/扭曲度>1.5%.*.凡符以上2点任意一点均不可接受*弯曲度=弯曲高度/长度*扭曲度=扭曲高度/对角长度E504防焊膜损伤Solder MaskDamaged防焊漆脱落或有刮痕至露铜或可见基板1.防焊膜松动颗粒物没能完全移除或影响组装作业2.防焊膜泡疤/刮伤/脱漆有跨越相邻线路;3.胶带测试后关键点出现泡疤/脱漆4.有助焊剂/油剂或清洁剂留在防焊膜下5.防焊膜泡疤/刮伤/脱漆有可能造成锡桥.*.凡符以上5点任意一点均不可接受E505PCB孔塞PCB holeblock零件孔及螺丝固定孔/预留孔及零件孔内有锡或其它异物1.有锡膏或锡塞住零件孔螺丝孔且影响其后制程作业;2.零件孔有零件脚或非金属异物塞住.*.凡符以上2点任意一点均不可接受E506基板损伤PCB DamagedPCB部分断裂或分离1.板边分层造成向内渗透深度>1.5mm,2.基板部份线路部分出现破裂或光晕现象3.基板部份出现脱落影响板边间距.4.板边缩小宽度>2.5mm.*.凡符以上4点任意一点均不可接受PCB基板零件孔異物堵塞E507 PCB内层剥离PCBDelaminationPCB基板出现板层分离(或气泡)1.内层剥离面积(或气泡面积)超过两PTH间距离之25%;2.PCB内层剥离面积(或气泡面积)延伸(横跨)至表面导线或PAD之下方导线.*.凡符以上2点任意一点均不可接受E508间距过小Distance tooshort相邻组件导脚或焊点间间距过小两相邻焊点或引脚之间距离小于0.13mm不可接受.E509开路Open circuitPCB 线路有断开/裂缝, 使铜线应导通而未导通不允许开路.PCB基板銅箔PAD 銅箔開路<0.13mm<0.13mmE510短路ShortcircuitPCB 两点(或以上)铜线间有短路, 使铜线间不应导通而有导通不允许短路.E511 残留异物ForeignmaterialPCBA表面或零件间残留异物1.残留有导电性异物(如:铁脚等);2.残留非导电性异物,并粘着于接触点上;3.残留前头标签或非正常标签或印章;4.通风处残留有非导电性异物.*.凡符以上4点任意一点均不可接受E601 Label贴附位置不正确LabellocationfailLABEL未贴到规定位置或倒贴bel贴附位置与图面指定位置不符;bel倒贴或贴歪角度大于15度.*.凡符以上2点任意一点均不可接受E602Label 错误Label Error 使用LABEL之内容与规格不符bel印刷内容与规格要求不符;bel颜色与规格要求不同;bel呎寸与规格要求不同;4.Barcode无法扫描.* 以上所称规格包括SOP及客户样品E603 Label浮起LabelpeelingLABEL粘贴不紧、翘起或部份脱离PCBLabel浮起大于Label面积之10%不允许(仅限于C级面,A/B级面另行规定).E604Label不良Label Defect LABEL印刷不良或破损,无法识别bel印刷不完整以致无法识别;bel破损影响外观;3.Barcode扫瞄内容错误或读不出;4.字迹重迭.*.凡符以上4点任意一点均不可接受CARTON ID CT-090000188 OKCARTON ID CS-90000188NGE 901Stand off 裂痕,外观不平且出现锯齿状压合后Stand off出现开裂现象及外圆桶出现凹凸不平之现象不可接受﹕裂痕多于三条﹐或两裂痕相互间隔少于90度﹐或有任一裂痕到圆桶内﹐或压合后外观不平且出现锯齿状现象E902可接受﹕裂痕不多于三条﹐且相互间隔至少相差90度﹐且裂痕不能到圆桶内E903 目标﹕平整﹐牢固与PCB板连接﹐没有松动现象﹐Standoff外径与PCB孔沿至少有180度紧贴标准判定原则说明:检视条件: 除进行焊点及零件装配之检查需采用放大装置外,其余(如脏污,变形损伤等)项目之检验与判定,均需在光照度为80~100蜡烛光源及距离30CM条件下进行检查.1). 除了仲裁目的外,不需对本标准检查项目进行具体的量测 (例如: 不需要给出‘’‘装配与焊点之具体尺寸和百分比)..2). 进行直观检查时,要求使用放大装置辅助检查.放大装置之公差可以是放大倍数之±15%.放大装置及其光源应与被检查项目的要求匹配,检查焊点连接之放大倍数应依被检件之最小焊盘宽度来选择.原则上检验用时放大倍数>/= 10, 仲裁使用时放大倍数>/= 20.( 仲裁用之放大倍数仅用于产品拒收条件之确认与仲裁)3). 若本判定标准之内容客户有另行规定或违反IPC-A-610 C ClassII之规定,则以客户规定或IPC-A-610 C ClassII之规定执行.。
pcb常见缺陷原因与措施

pcb常见缺陷原因与措施以pcb常见缺陷原因与措施为题,对pcb常见缺陷进行分析,并提出相应的解决措施。
一、常见pcb缺陷及其原因1. 焊盘剥落:焊盘剥落是pcb制造中常见的缺陷,主要原因包括焊接温度不合适、焊盘表面处理不当以及焊接压力不均等。
这些问题会导致焊盘与基板之间的粘附力不足,造成焊盘剥落。
2. 焊接短路:焊接短路是pcb制造中的另一个常见问题,主要原因是焊接过程中,焊料过多或焊接位置不准确,导致电路之间产生短路。
此外,焊接过程中的静电也是引起焊接短路的重要原因之一。
3. 焊接开路:焊接开路是pcb制造中的常见问题,主要原因是焊接温度不够高或焊接时间不足,导致焊料未完全熔化,无法与基板形成牢固的连接。
此外,焊盘与焊盘之间的距离也会影响焊接质量,距离过大会导致焊接开路。
4. 焊盘错位:焊盘错位是pcb制造中常见的缺陷,主要原因是焊盘布局设计不合理或制造过程中的误操作。
焊盘错位会导致焊接位置不准确,影响电路的连接性能。
5. 焊盘过度露铜:焊盘过度露铜是pcb制造中的常见缺陷,主要原因包括蚀刻不当、工艺参数设置错误以及材料选择不当等。
过度露铜会导致焊盘的机械强度下降,容易引起焊盘剥落或焊接开路。
二、常见pcb缺陷的解决措施1. 控制焊接温度和时间:合理控制焊接温度和时间是防止焊盘剥落、焊接短路和焊接开路的关键。
通过调整焊接参数,确保焊料能够充分熔化并与基板形成牢固的连接。
2. 加强焊盘表面处理:焊盘表面处理对焊盘的粘附性有很大影响。
通过选择合适的表面处理方法,如喷锡、化学镀金等,可以提高焊盘的附着力,减少焊盘剥落的风险。
3. 控制焊接压力和位置:合理控制焊接压力和位置是防止焊盘错位的关键。
通过调整焊接设备的参数,确保焊接位置准确,避免焊盘错位。
4. 优化焊接工艺:通过优化焊接工艺,如优化焊接温度曲线、调整焊接速度等,可以减少焊接短路和焊接开路的发生。
此外,加强对焊接操作人员的培训,提高他们的技术水平和操作规范性,也是防止焊接缺陷的重要手段。
PCB缺陷分类及允收标准

次要不良
主要不良
须为半透明可辨认,且不可影响电气性能 基材内异物 微粒距最近导电图形的距离>5mil,且使相邻导体间距≥规定的 最小间距.如果没有规定,则≥0.8mm其影响面积<5%。
主要不良
内容
检验项目
板面 板边
允收标准
不允许起泡、分层 平滑、无毛刺、无粗糙边缘及板边缺口 板面不允许露纤维 擦花长≤100mm,但不露纤维(后工序能被磨刷掉) 表面杂物为不导电物体,长≤2mm
不良属性
严重不良 次要不良
外观
主要不良
ห้องสมุดไป่ตู้基材
尺寸≤50*50mm内单面不超过5点,位于非线路区者允收, 白点,白斑 不允许桥接线路/pad 不可超过 织纹显露 ≤板子面积的5% 不得渗入最近导体间距之50%以内
PCB的主要缺陷
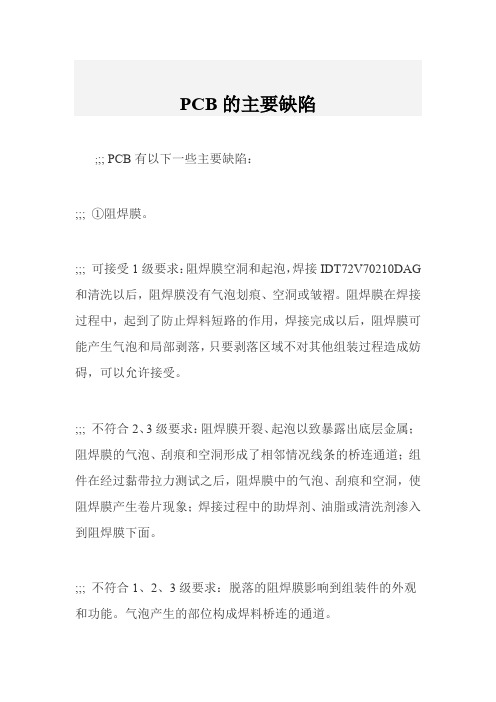
PCB的主要缺陷;;; PCB有以下一些主要缺陷:;;; ①阻焊膜。
;;; 可接受1级要求:阻焊膜空洞和起泡,焊接IDT72V70210DAG 和清洗以后,阻焊膜没有气泡划痕、空洞或皱褶。
阻焊膜在焊接过程中,起到了防止焊料短路的作用,焊接完成以后,阻焊膜可能产生气泡和局部剥落,只要剥落区域不对其他组装过程造成妨碍,可以允许接受。
;;; 不符合2、3级要求:阻焊膜开裂、起泡以致暴露出底层金属;阻焊膜的气泡、刮痕和空洞形成了相邻情况线条的桥连通道;组件在经过黏带拉力测试之后,阻焊膜中的气泡、刮痕和空洞,使阻焊膜产生卷片现象;焊接过程中的助焊剂、油脂或清洗剂渗入到阻焊膜下面。
;;; 不符合1、2、3级要求:脱落的阻焊膜影响到组装件的外观和功能。
气泡产生的部位构成焊料桥连的通道。
;;; 可接受1、2、3级要求:阻焊膜起泡、划痕和空洞,没有构成相邻线路和导体表面的桥连通道,阻焊膜局部脱落的部位,也不形成具有潜在危害的情况,可判为合格(1、2、3级)。
;;; ②,层压板。
在一般情况下,分层和起泡缺陷是材料和工艺方面的原因造成的。
对于发生在功能性区域和非功能性区域之间的起泡和分层,只要是非导电性的,若其他性能都符合要求,则可以接受。
;;; 发生起泡和分层的部位局限在通孔或导分层——基材的层间或基材与导电箔间电线条中间地带50%以内,可接受1、2级(降级);发生起泡和分层的部位局限在通孔或导电线条中间地带的25%以内,可接受3级要求;发生起泡和分层的部位扩大到能把金属化孔或者板下面的导条连通起来,1、2、3级均为不合格。
;;; ③显布纹。
显布纹是其材表面的一种现象,即其板表面显出玻璃布的编织花纹,此时玻璃布的纤维应没有断裂,并完全被树脂覆盖。
显布纹现象对于1、2、3级要求都可接受。
;;;;;;;;;;;;;; ;;;; ;④露织物,即基材表面露出未被树脂完全覆盖的没有断裂的玻璃布纤维。
优选1、2、3级要求:没有露织物。
PCB常见缺陷及可接受规范标准

常见缺陷图片以及接受标准1、孔偏2、异形槽孔毛刺 3..铅锡堵孔接受标准:环宽不小于0.05mm,且应小于90度。
偏孔数量不超过总数量的5% 。
接受标准:孔内毛刺不能影响客户装配,达到最小孔径要求;接受标准:对于插件孔不影响孔径的孔内聚锡可以接受,不允许孔内堵孔。
4、孔内毛刺 5..偏孔,变形 6. 孔壁空洞接受标准:1、孔壁质量满足最低要求。
2、未违反孔径要求的下限。
接受标准:孔径大小在公差范围内;不能有明显变形,通常变形的量不超过0.05mm.接受标准(IPC 标准):1、 任何孔不可超过3个破洞,发生破洞的孔不超过总孔数的5%;2、 任何破洞不超过孔长的5%和孔周的1/4。
7、焊盘破损(缺损)8、孔(边)内毛刺9、过孔锡珠接受标准:接受标准:接受标准:导体连接处永不可低于0.05mm之宽度,或不可低于起码线宽,两者以数字较小者为允许准则。
对于孔(内)边毛刺要求不能影响最小孔径。
对于过孔内目视不能有成颗粒的锡珠,焊接时锡珠不能流出孔内。
10、内层偏移11、红孔/黑孔12、焊盘破损接受标准:1、最小环宽不能低于客户要求或0.05mm。
2.图形的偏移不影响任何间距(含内层焊盘与铜区之间,焊盘相互之间),通常要求所影响距离不可以多于设计的+/-20%;接受标准:(元件孔)化金及铅锡厚度均匀并涵盖到孔内无露铜之现象;(过孔)每块接收3-5个。
接受标准:1、对于SMT焊盘破损不能小于长和宽的20%,破损面积小于焊盘面积的10%;2、对于插件孔焊盘最小环宽需保持0.05mm,起破损不能超过环长度的25%或2.5mm。
13、DR2偏孔14、DR2 孔偏15、偏孔接受标准:二次孔不允许与板边相切,且最小剩余位置不得出现分层(白边)情况、油墨脱落情况。
接受标准:孔径必须在公差范围内;位置偏移小于0.05mm.接受标准:要求孔环至少在0.05mm以上(上图为可接受缺陷)。
16、油墨入孔17、散热孔边聚锡18.过孔油墨高出板面接受标准:接受标准:接受标准:1.对于过孔,如果客户无特殊要求则允许油墨入孔;2.对于插件孔,原则上不允许油墨入孔;3.对于NPTH孔,要求油墨入孔后不能影响其孔径。
PCB常见缺陷及可接受实用标准

常见缺陷图片以及接受标准1、孔偏2、异形槽孔毛刺 3..铅锡堵孔接受标准:环宽不小于 0.05mm,且应小于90度。
偏孔数量不超过总数量的5% 。
接受标准:孔内毛刺不能影响客户装配,达到最小孔径要求;接受标准:对于插件孔不影响孔径的孔内聚锡可以接受,不允许孔内堵孔。
4、孔内毛刺 5..偏孔,变形 6. 孔壁空洞文档大全接受标准:1、孔壁质量满足最低要求。
2、未违反孔径要求的下限。
接受标准:孔径大小在公差范围内;不能有明显变形,通常变形的量不超过0.05mm.接受标准(IPC标准):1、任何孔不可超过3个破洞,发生破洞的孔不超过总孔数的5%;2、任何破洞不超过孔长的5%和孔周的1/4。
7、焊盘破损(缺损)8、孔(边)内毛刺9、过孔锡珠接受标准:导体连接处永不可低于0.05mm之宽度,或不可低于起码线宽,两者以数字较小者为允许准则。
接受标准:对于孔(内)边毛刺要求不能影响最小孔径。
接受标准:对于过孔内目视不能有成颗粒的锡珠,焊接时锡珠不能流出孔内。
10、内层偏移11、红孔/黑孔12、焊盘破损接受标准:1、最小环宽不能低于客户要求或0.05mm。
2.图形的偏移不影响任何间距(含内层焊盘与铜区之间,接受标准:(元件孔)化金及铅锡厚度均匀并涵盖到孔内无露铜之现象;(过孔)每块接收3-5个。
接受标准:1、对于SMT焊盘破损不能小于长和宽的20%,破损面积小于焊盘面积的10%;文档大全文档大全焊盘相互之间),通常要求所影响距离不可以多于设计的+/-20%;2、对于插件孔焊盘最小环宽需保持0.05mm ,起破损不能超过环长度的25%或2.5mm 。
13、DR2偏孔14、DR2 孔偏15、偏孔接受标准:二次孔不允许与板边相切,且最小剩余位置不得出现分层(白边)情况、油墨脱落情况。
接受标准:孔径必须在公差范围内;位置偏移小于0.05mm.接受标准:要求孔环至少在0.05mm 以上(上图为可接受缺陷)。
16、油墨入孔17、散热孔边聚锡18.过孔油墨高出板面接受标准:1.对于过孔,如果客户无特殊要求则允许油墨入孔;2.对于插件孔,原则上不允许油墨入孔;接受标准:整体平整,聚锡不能高出SMT 焊盘。
PCB常见问题验收标准
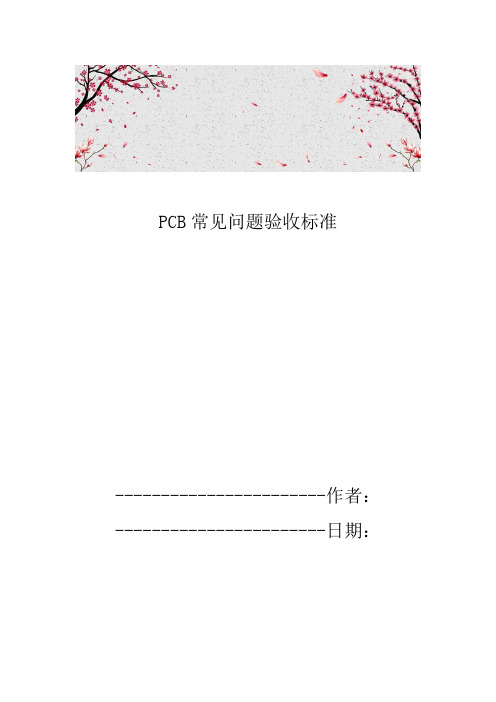
PCB常见问题验收标准-----------------------作者:-----------------------日期:常见问题验收标准目录一、板面品质1.板边损伤 (2)2.板面污渍 (2)3.板面余铜 (2)4.锡渣残留 (2)5.异物(非导体) (2)6.划伤/擦花 (3)7.基材压痕 (3)8.凹坑 (3)9.外来夹杂物 (4)10.缺口/空洞/针孔 (4)11.导线压痕 (5)12.导线露铜 (5)13.补线 (5)14.导线粗糙 (5)15.短路修理 (5)16.焊盘露铜 (6)二、孔外观品质1.表层PTH孔环 (6)2.表层NPTH孔环 (6)三、字符品质1.字符错印、漏印 (6)2.字符模糊 (6)3.标记错位 (7)4.标记油墨上焊盘 (7)5.其它形式的标记 (7)四、阻焊品质1.阻焊膜厚度 (7)2.阻焊膜脱落 (7)3.阻焊膜起泡/分层 (8)4.阻焊膜波浪/起皱/纹路 (8)5.阻焊膜的套准 (8)6.阻焊桥漏印 (9)7.阻焊桥断裂 (9)8.阻焊膜附着力 (9)9.阻焊膜修补 (10)10.阻焊膜色差 (10)五、其它要求1.打叉板 (10)2.包装 (10)3.电测 (10)一、板面标准1.板边损伤合格:无损伤;板边、板角损伤尚未出现分层;不合格:板边、板角损伤出现分层;不合格品报废:板边、板角损伤后出现严重分层;不合格返工、返修、特采:板角损伤尚出现分层,但深度小于5.0mm,返修修理后与客户沟通,客户不接受报废处理。
2.板面污渍合格:板面整洁,无明显污渍;不合格:板面有油污、粘胶等脏污;不合格品的特采:板面有油污、粘胶等脏污不能通过清洗、擦洗的,申请特采;不合格品的返修、返工:板面有油污、粘胶等脏污能通过清洗、擦洗的。
3.板面余铜合格:无余铜或余铜满足下列条件a) 板面余铜距最近导体间距≥0.2mm;b) 每面不多于1处;c) 每处最大尺寸≤0.5mm;不合格:不满足上述任一条件;不合格品的返工、返修:把余铜修理掉。
PCB常见缺陷及可接受标准

.常见缺陷图片以及接受标准3.. 铅锡堵孔、异形槽孔毛刺1、孔偏2接受标准:接受标准:接受标准:对于插件孔不影响孔径的孔内聚锡可以接受,不允孔内毛刺不能影响客户装配,达到最小孔径要求;环宽不小于度。
,且应小于90 0.05mm许孔内堵孔。
偏孔数量不超过总数量的5%6. 孔壁空洞4、孔内毛刺5..偏孔,变形..接受标准:接受标准:接受标准(IPC标准):1、孔径大小在公差范围内;不能有明显变形,通常变形任何孔不可超过3个破洞,发生破洞的孔不超过、孔壁质量满足最低要求。
1总孔数的5%;、未违反孔径要求的下限。
0.05mm.的量不超过22、任何破洞不超过孔长的5%和孔周的1/4。
9、过孔锡珠、孔(边)内毛刺7、焊盘破损(缺损)8接受标准:接受标准:接受标准:对于过孔内目视不能有成颗粒的锡珠,焊接时锡珠不能对于孔(内)边毛刺要求不能影响最小孔径。
或不可低于起码0.05mm导体连接处永不可低于之宽度,线宽,两者以数字较小者为允许准则。
流出孔内。
..10、内层偏移11、红孔/黑孔12、焊盘破损接受标准:接受标准:接受标准:1、最小环宽不能低于客户要求或0.05mm。
(元件孔)化金及铅锡厚度均匀并涵盖到孔内无露铜之SMT1、对于焊盘破损不能小于长和宽的20%,破2.图形的偏移不影响任何间距(含内层焊盘与铜区之间,现象;(过孔)每块接收10%;3-5个。
损面积小于焊盘面积的焊盘相互之间),通常要求所影响距离不可以多于设计的2、对于插件孔焊盘最小环宽需保持0.05mm,起破+/-20%;。
损不能超过环长度的25%或2.5mm13、DR2偏孔14、DR2 孔偏15、偏孔接受标准:接受标准:接受标准:以上(上图为可接受缺0.05mm要求孔环至少在二次孔不允许与板边相切,且最小剩余位置不得出0.05mm.孔径必须在公差范围内;位置偏移小于..现分层(白边)情况、油墨脱落情况。
陷)。
18.、散热孔边聚锡过孔油墨高出板面1716、油墨入孔接受标准:接受标准:接受标准:整体平整,聚锡不能高出SMT焊盘。
- 1、下载文档前请自行甄别文档内容的完整性,平台不提供额外的编辑、内容补充、找答案等附加服务。
- 2、"仅部分预览"的文档,不可在线预览部分如存在完整性等问题,可反馈申请退款(可完整预览的文档不适用该条件!)。
- 3、如文档侵犯您的权益,请联系客服反馈,我们会尽快为您处理(人工客服工作时间:9:00-18:30)。
常见缺陷图片以及接受标准1、孔偏2、异形槽孔毛刺 3..铅锡堵孔接受标准:环宽不小于0.05mm,且应小于90度。
偏孔数量不超过总数量的5% 。
接受标准:孔内毛刺不能影响客户装配,达到最小孔径要求;接受标准:对于插件孔不影响孔径的孔内聚锡可以接受,不允许孔内堵孔。
4、孔内毛刺 5..偏孔,变形 6. 孔壁空洞接受标准:1、孔壁质量满足最低要求。
2、未违反孔径要求的下限。
接受标准:孔径大小在公差范围内;不能有明显变形,通常变形的量不超过0.05mm.接受标准(IPC标准):1、任何孔不可超过3个破洞,发生破洞的孔不超过总孔数的5%;2、任何破洞不超过孔长的5%和孔周的1/4。
7、焊盘破损(缺损)8、孔(边)内毛刺9、过孔锡珠接受标准:导体连接处永不可低于0.05mm之宽度,或不可低于起码线宽,两者以数字较小者为允许准则。
接受标准:对于孔(内)边毛刺要求不能影响最小孔径。
接受标准:对于过孔内目视不能有成颗粒的锡珠,焊接时锡珠不能流出孔内。
10、内层偏移11、红孔/黑孔12、焊盘破损接受标准:1、最小环宽不能低于客户要求或0.05mm。
2.图形的偏移不影响任何间距(含内层焊盘与铜区之间,焊盘相互之间),通常要求所影响距离不可以多于设计的+/-20%;接受标准:(元件孔)化金及铅锡厚度均匀并涵盖到孔内无露铜之现象;(过孔)每块接收3-5个。
接受标准:1、对于SMT焊盘破损不能小于长和宽的20%,破损面积小于焊盘面积的10%;2、对于插件孔焊盘最小环宽需保持0.05mm,起破损不能超过环长度的25%或2.5mm。
13、DR2偏孔14、DR2 孔偏15、偏孔接受标准:二次孔不允许与板边相切,且最小剩余位置不得出现分层(白边)情况、油墨脱落情况。
接受标准:孔径必须在公差范围内;位置偏移小于0.05mm.接受标准:要求孔环至少在0.05mm以上(上图为可接受缺陷)。
16、油墨入孔17、散热孔边聚锡18.过孔油墨高出板面接受标准:1.对于过孔,如果客户无特殊要求则允许油墨入孔;2.对于插件孔,原则上不允许油墨入孔;3.对于NPTH孔,要求油墨入孔后不能影响其孔径。
接受标准:整体平整,聚锡不能高出SMT焊盘。
接受标准:如客户无特殊要求,任何情况下,油墨不得高于焊盘25.4um且不能高于SMT焊盘。
19、非孔(槽)孔化,除钯不净20、油墨上焊盘(原件孔)21、过孔堵孔接受标准:不接收任何非孔内有孔化或除钯不净2.孔化的程度是该孔经过波峰焊时孔内不能占有Pb/Sn或占有Pb/Sn而不影响孔径。
接受标准:1、绿漆阻剂已对孔环失准,但此歪掉的绿漆尚未违反起码环宽的品质要求(至少要在3/4周边即270度上拥有.05mm宽的佘环,且尚未沾有绿漆)2、尢其对于做为焊接的通孔而言,绿漆并未入孔壁。
3、尚未曝露邻近的孤立焊垫或导线。
接受标准:过孔油墨堵孔不能透光;堵孔深度必须要保证孔内饱满三分之二。
22.磨孔上板面23、光标聚锡24、光标变形接受标准:有效板面不允许出现板面有磨冲孔问题。
接受标准:与正常生产出来的其他SMT焊盘的整体或平均平整度及亮度一致。
不能有氧化、压痕、发黑、麻点,也不能有明显划痕(擦伤),铅锡堆积,或其他异物覆盖。
接受标准:1、不能有明显变形,通常要求变形的量不超过0.1mm。
2、。
3、光标不能被油墨覆盖、不能明显变色等。
25、.焊盘破损26、.过孔油墨高于焊盘27、.光标脱落接受标准:要求孔环保持0.05mm外,还要求焊接面积至少在原设计的80%以上。
接收标准;所有过孔堵孔油墨不能高于SMT焊盘。
接受标准;结合力:不能起层、移位,更不能掉落28、蓝胶高于焊盘29、金手指划痕30、板面多铜接收标准:允许高出焊盘,但不能超出0.5mm,不能出现突然高企的起泡。
接收标准:凹点,凹陷及下陷区其等最大尺寸尚未超过0.15mm,此等缺陷每片缺点每片手指上不可超过3个,有此缺点的手指数不可超过总数的30%。
接收标准:板面不接收肉眼可见多余的明显残铜。
每处尺寸最大小于等于0.5mm;板面余铜造成导体间距的减小小于20%。
31、线条砸伤32、板面划痕33、板面划伤露铜接受标准:1、孤立的线边缺口、针孔、刮伤之各式综合虽造成基材的曝露,只要未缩减起码线宽到达成低于20%者;2、情况下此等缩减(线边粗糙、缺口)在线长方面面均不可超过13MM,或线长的10%。
两者中以数字面较小者做为取决的对象。
接受标准:划痕、压痕及加工痕迹如果不跨接导线或未使纤维暴露/破坏超过最小要求,并且缺陷的穿透深度不应使介质间距低于最小值。
接受标准:1、绿漆表面已出现破裂或已有划伤,但尚未穿透而露出导体线路。
2、绿漆表面有破裂及划伤且已穿透至包有锡铅的导线上,但尚未透过锡层而造成露铜。
34、内层划痕35、镀层不良36、层压凹痕接受标准:不影响外观,不影响层间结合力。
接受标准:1、不影响外观和使用性能。
2、任何情况下长度不能超过板的1/2或10mm,两者取较小值;3、可结合参考划痕。
接受标准:1、凹痕的深度不能影响介质层的厚度;2、凹痕不能发生在焊盘位置或金手指位置;3、目视不明显,触摸无明显感觉。
4、可结合参考划痕问题。
37、线条剥离38、开路/针孔/缺口39、层压分层(白斑)接受标准:线条不能偏离其本身所在位置,用胶带做撕起试验时证明镀层附着力很好,其表面镀层不可出现被拉移或浮起的现象。
故任何情况下不能接受线条剥离。
接受标准:1.线边缺口、针孔、刮伤之各式综合虽造成基材的曝露,只要未缩减起码线宽到达成低于20%者2、任何情况下此等缩减(线边粗糙、缺口)在线长方面面均不可超过13MM,或线长的10%。
两者中以数字面较小者做为取决的对象。
接受标准:1、所造成的瑕疵使得导体之间的间距缩减,尚未低于其起码间距。
2、白斑所涵盖的领域,落于不同电位之相邻导线间尚未超出其间距之50%者。
3、经制程中多次高热试验后均无扩大的现象。
4、板边出现白斑区域时,对板边至最近导线之边宽,尚未逼小到其下限宽度者,对未明指边宽者则该距离应大于2.5mm40、镀层结瘤41、金手指凹点42、镀层凹点接受标准:1、表面贴装焊盘出现结瘤时,不能在各个垫宽与垫长的80%区域内。
2、结瘤的大小不能超过0.8mm且不能影响元件装配。
接受标准:凹点最大尺寸尚未超过0.15mm,此等缺点每片手指上不可超过3个,有此缺点的手指数不可超过总数的30%接受标准:1、凹点不能影响到SMT以及以后工序的装配功能;2、导线上的接受标准可视同“针孔/缺口”。
43、残铜(蚀刻不净)44..铅锡不匀(修复不良)45、OSP不良(基铜上有异物)接受标准:1、任何有关线边粗糙、铜刺等合并效应对孤立区规定起码间距之缩减尚未超过30% 接受标准:要求对铅锡不平整的情况进行修复,修复后的焊盘要求平整,可焊性良好。
接受标准:OSP膜上不能有异物,不能影响其可焊性能。
46..化金色差47、OSP铜面氧化48、漏镀(化金板)接受标准:肉眼看不是很明显,不影响可焊。
接受标准:1、不能影响其边表观,要求颜色均匀;2、不能影响其可焊性能。
接受标准:焊接区域不接收没有镀上镍和金,露出铜的颜色。
49、板面铅锡渣50、化锡不良51、金手指划痕接受标准:1、板面杂质不能为导体;2、其所在位置不能减少相邻导体的最小间距;3、杂质完全被油墨固定,任何情况下非机械用力不会脱落。
接受标准:化锡面无水迹印,锡面无发黑、无发黄、露铜、擦花等不良,要求外观颜色均匀一致;锡厚需符合客户要求,沉锡板的锡厚一般控制在0.7~1.2UM之间,测试PADSIZE在1mmX1mm。
可焊性良好。
接受标准:金手指关键区域内无明显划痕,其它区域的划痕不露镍和露铜。
且每面金手指划痕不多于2处。
52. 化银板检验53、化金色差,氧化54、..OSP氧化接受标准:板面颜色均匀一致,不掉绿油,不掉银;可焊性良好。
接受标准:板面氧化不接受;色差肉眼可见不明显;且必须可焊性测试OK。
接受标准:要求OSP表层颜色均匀,没有明显色差;可焊性良好。
55、.铅锡发白/黑(铅锡偏薄)56、OSP膜面划伤(露铜)57、板面金渣接受标准:1、铅锡达到客户最薄厚度要求;2、可焊性能良好;3、目视检验无明显发黑,发白。
接受标准:要求OSP膜面不能露铜。
接受标准:板面不允许有金渣。
58、门阵焊盘铅锡不平整59、.油墨起泡60、.修补、(返工)不良接收标准:肉眼可见门阵焊盘比较平整。
接受标准:1、缺陷未超过0.25mm,每板不超过2处;2、未影响最小绝缘间距;3、未漏出基铜。
接受标准:1、对于露铜或ET修复后的露铜进行补油修复;2、所补的油墨与板本身油墨型号相同;3、不得出现油墨上焊盘情况;4、其它相关要求将FI操作指导书补油注意事项。
61、蓝胶可剥性不好62、蓝胶不好63、漏印接受标准:蓝胶板必须经过热冲击,可焊性,回流焊实验后可以剥离。
接受标准:蓝胶厚度顾客有要求的按顾客要求,没有厚度要求的必须大于0.3mm;顾客有要求盖蓝胶的区域不允许漏印。
接受标准:板面颜色必须一致,线条拐角处油墨达到顾客最小要求。
64、.油墨不匀(焊盘边油墨发黄)65、油墨上焊盘(SMT):66、.油墨异物(线圈板)接受标准:1、满足最小油墨厚度要求;2、经过热冲击后无起泡现象。
接受标准:1、未造成相邻导体暴露,未侵犯到金手指和测试点;2、一面受到侵犯,焊盘大于1.25mm时,允许0.05mm上焊盘,焊盘小于1.25mm时,允许0.025mm上焊盘。
接受标准:对于线圈板,板面异物为:1、异物非导体;2、异物没有影响磁芯位置的板厚;3、参考板面异物接受标准。
67、显影不净68、.阻焊桥脱落69、油墨开裂接受标准:表面贴装焊盘1、垫距在1.25mm或较大者,其被侵犯的垫面宽度不可超过0.05mm.2、凡垫距小于1.25mm其被侵犯之垫面的宽度不可超过0.025mm 接受标准:如非客户本身设计,要求门阵之间阻焊桥完整无无缺损。
接受标准:油墨开裂容易造成导体乔接,且一般热冲击后缺陷有扩散,故油墨开裂不能接受。
70、.印蓝胶不良(覆盖不完整)71、阻焊桥脱落72、.字符不清接受标准:1、根据客户的设计的蓝胶位置图,所有金属孔和金属焊盘、线条必须被蓝胶覆盖完整;2、蓝胶厚度需达到MI要求。
接受标准:如非客户本身设计,要求门阵之间阻焊桥完整无无缺损。
接受标准:1、字符能够辨认。
2、一面受到侵犯,焊盘大于1.25mm时,允许0.05mm上焊盘,焊盘小于1.25mm时,允许0.025mm上焊盘。
73、.字符油墨不匀74.显影不净(无金属导体区)75、漏印接受标准:对于客户用于绝缘的油墨,凹点(最薄处)必须达到客户要求的油墨厚度要求。
接受标准:凡客户设计为没有油墨的区域,不论是导体区域还是非导体区域,一律不接受显影不净的问题。