线切割断丝原因及解决办法
电火花线切割产生断丝的原因有哪些

由于慢走丝是采取线电极连续供丝的方式,即线电极在运动过程中完成加工,因此即使线电极发生损耗,也能连续的予以补充,故能提高零件加工精度,但电火花线切割的断丝却成为这些优势的障碍,解决此问题十分必要。
下面我们就来具体介绍一下如何解决电火花线切割产生的断丝。
1、与工作液相关的断丝因素目前低速走丝电火花切割加工大多用纯净水和蒸馏水,廉价无污染。
使用工作液主要有两个作用:绝缘和冷却。
因此工作液应该有良好的吸热、传热和散热功能。
当工作液的性能变差,意味着工作液中存在的杂质离子大大增加,工作液的介电性能明显降低。
一方面会造成由介质粒子构成的导电桥导致的接触放电概率增加;另一方面,由于工作液的导电性能增加,使得加工间隙增大,此时的加工波形特征是一连串几乎没有开路和击穿延时的放电脉冲。
这时输入到加工间隙的能量密度非常大,极易造成断丝。
此时必须更换工作液。
放电过程中产生的加工屑也是造成断丝的因素之一。
有加工屑搭桥而成,或两极上相对突出的尖点偶尔相遇而形成的微短路状态具有较大的接触电阻。
由于电极丝运动,这种微短路很容易被拉开形成火花放电。
故此时脉冲电源输入到加工间隙的能量密度远大于正常加工时,使得电极丝的黏着部位产生脉冲能量集中释放,导致电极丝产生裂纹,从而可能造成断丝,因此加工过程中必须冲走这些微粒。
为了有效的冲走固体微粒,在没有工件几何形状的限制时,还应尽量选择密着加工,使水冲进割缝,更好的改善冲刷状况。
若喷水的方向不准确也易断丝。
因为喷水方向不准,工作液无法喷入切割逢,电极丝不能够冷却,使得电极丝局部温度突然升高,引起烧丝。
喷水位置应以水柱包住电极丝为好,并且上下喷水压力要相当。
2、与伺服控制相关的断丝因素伺服进给速度应与工件的蚀除速度保持一定关系,即保持加工间隙为一定值。
因为当伺服速度超过蚀除速度,就会出现频繁的短路现象,同时增大了断丝的可能性;反之,伺服速度过慢,两极见偏于开路,加工过程中也会因开路而短路,使切割速度降低,表面粗糙值增大。
慢走丝线切割加工问题解决方案

慢走丝线切割加工问题解决方案慢走丝线切割加工问题解决方案数控技术,即采用电脑程序控制机器的方法,按工作人员事先编好的程式对机械零件进行加工的过程。
下面是YJBYS店铺整理的慢走丝线切割加工问题解决方案,希望对你有帮助!1.断丝问题(1)放电状态不佳-----降低P值,如果此值降低幅度较大仍断丝,可考虑降低I值,直至不断丝。
此操作会降低加工效率,如果频繁断丝,请参考以下内容,找出真正导致断丝的原因。
(2)冲液状态不好,如上下喷嘴不能贴面加工,或者开放式加工时。
通常断丝位置在加工区域-----降低P值,并检查上下喷嘴帽是否损坏,如损坏请更换。
(3)导电块磨损严重或太脏,通常断丝位置在导电块附近---旋转或更换导电块,并进行清洗。
(4)导丝部太脏,造成刮丝,通常断丝位置在导丝部附近---清洗导丝部件。
(5)丝张力太大-----调低参数中的丝张力FW,尤其是锥度切割时。
(6)电极丝的类型、工件材料质量问题-----更换电极丝;降低P、I 值,直至不断丝。
(7)废丝桶中的丝溢出,造成短路,通常刚刚启动加工即会断丝-----将与地面接触的废丝放回废丝桶,排除短路。
(8)修切断丝,可能是偏移量不合适,造成修切修不动而断丝----减少偏移量之间的余量。
(9)后部收丝轮处断丝-----检查收丝轮压丝比,标准值为1:1.5 。
(10)导电块冷却水不充分,通常断丝位置在导电块附近-----检查冷却水回路。
(11)去离子水导电率过高,通常断丝位置在加工区域-----若超过标准值10μs,使去离子水循环至标准值或小于标准值后再加工;如仍不能达到标准值,请更换树脂。
(12)去离子水水质差,通常断丝位置在加工区域-----水箱中水出现浑浊或异味,请更换过滤纸芯、水。
(13)丝被拉断,下臂的下陶瓷导轮处有废丝嵌入或运转不灵活-----清理并重新调整安装陶瓷导轮,必要时检查导丝嘴磨损状况并更换。
(14)张力轮抖动过大(运丝不平稳)---用张力计校正丝张力。
线切割总断丝原因及解决办法
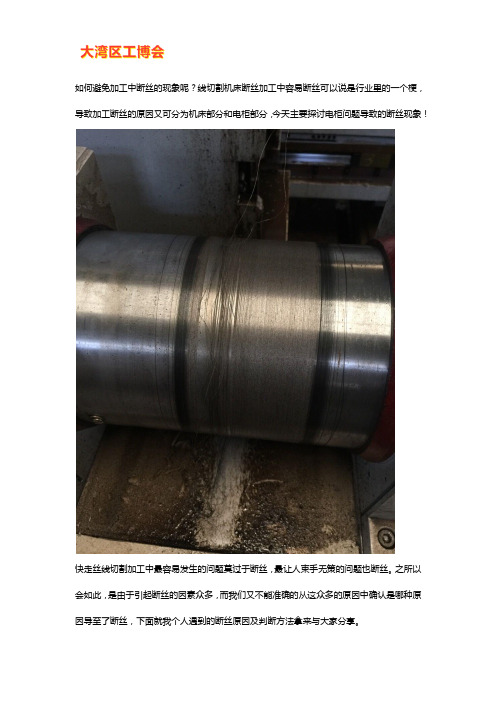
如何避免加工中断丝的现象呢?线切割机床断丝加工中容易断丝可以说是行业里的一个梗,导致加工断丝的原因又可分为机床部分和电柜部分,今天主要探讨电柜问题导致的断丝现象!
快走丝线切割加工中最容易发生的问题莫过于断丝,最让人束手无策的问题也断丝。
之所以会如此,是由于引起断丝的因素众多,而我们又不能准确的从这众多的原因中确认是哪种原因导至了断丝,下面就我个人遇到的断丝原因及判断方法拿来与大家分享。
1.最容易忽视的原因:高频电源性能
电源能正常加工一般就认为电柜是好的,其实有两项性能对断丝影响很大,一是输出脉冲含有直流分量,二是有负向脉冲。
这两项性能简单的测量是无法发现的,只能用专业的测试仪才能检查出来;
2.输出的脉冲含有直流分量会使脉间时间内放电间隙不能有效的恢复绝缘状态,导致加工不稳定而断丝;
3.输出脉冲中有负向脉冲会使钼丝损耗加快而发生断丝;
在线切割加工电流不大、工件也不厚,又没有其它明显的断丝原因,断丝又频繁发生,基本就可以判断高频电源性能有问题了。
最全中走丝问题解决方案

史上最全的数控中走丝线切割加工问题解决方案1. 断丝1)钼丝质量差----选择质量好的钼丝。
2)加工参数选择不合理----针对不同的材料及工件厚度选择合适的加工参数,请注意,选用电流较大的条件时容易断丝。
3)导电块磨损出沟槽将丝夹断----调整导电块至一个新的位置,必要时更换导电块。
4)切割液浓度不合适----保持切割液浓度在11~12.5%。
5)工件变形夹断钼丝----避免材料切割变形:材料热处理工艺合理;预加工穿丝孔;预切割释放应力;优化切割路径。
6)工件材料内部有不导电的杂质或工件表面有不导电的氧化物----更换材料;去除不导电杂物质再切割。
7)冲液太小不能有效冲入切缝中, 放电条件恶劣化造成断丝----设定合理的冲液大小;定时检查切割液是否足够,循环通道是否畅通。
8)导轮(尤其是支撑导轮)精度问题----应该严格按照机床保养说明定期更换轴承,必要时更换导轮或轴承。
9)配重块提供的张力太大----0.2mm钼丝选用2个配重块;0.18mm钼丝选用1个配重块;0.15-0.12mm丝不用再配。
10)钼丝损耗较多后未及时更换----及时更换钼丝。
2. 表面粗糙度变差1)切割液使用时间过长,浓度不合适----保持冷却液浓度在11~12.5%,必要时更换切割液。
2)主导轮及轴承磨损----观察电极丝运行是否抖动,听各部位轴承有无异常响声,由此来判断是否要更换轴承或导轮,必要时请更换。
3)修切加工工艺有误----正确选用修切条件号及偏移量。
4)工件变形---避免材料切割变形:材料热处理工艺合理;预加工穿丝孔;预切割释放应力;优化切割路径。
5)钼丝损耗较多----更换新的钼丝。
6)材料的组织结构问题----不同的材料加工效果不一样。
7)机床状态欠佳----检查各导轮,丝筒部,导电块,各丝杠导轨的润滑是否在最佳状态。
3. 加工效率低1)加工参数选择不合理----针对不同的材料及工件厚度选择合适的加工参数,请注意,选用电流较小的条件加工效率低。
线切割加工中断丝后的处理方法
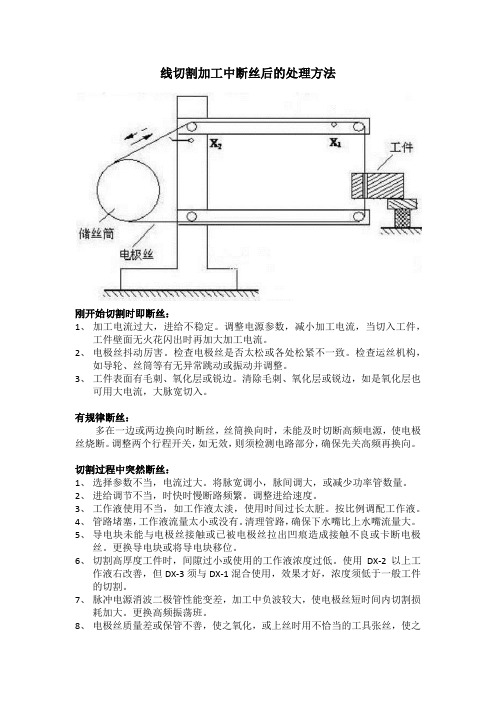
线切割加工中断丝后的处理方法刚开始切割时即断丝:1、加工电流过大,进给不稳定。
调整电源参数,减小加工电流,当切入工件,工件壁面无火花闪出时再加大加工电流。
2、电极丝抖动厉害。
检查电极丝是否太松或各处松紧不一致。
检查运丝机构,如导轮、丝筒等有无异常跳动或振动并调整。
3、工件表面有毛刺、氧化层或锐边。
清除毛刺、氧化层或锐边,如是氧化层也可用大电流,大脉宽切入。
有规律断丝:多在一边或两边换向时断丝,丝筒换向时,未能及时切断高频电源,使电极丝烧断。
调整两个行程开关,如无效,则须检测电路部分,确保先关高频再换向。
切割过程中突然断丝:1、选择参数不当,电流过大。
将脉宽调小,脉间调大,或减少功率管数量。
2、进给调节不当,时快时慢断路频繁。
调整进给速度。
3、工作液使用不当,如工作液太淡,使用时间过长太脏。
按比例调配工作液。
4、管路堵塞,工作液流量太小或没有。
清理管路,确保下水嘴比上水嘴流量大。
5、导电块未能与电极丝接触或已被电极丝拉出凹痕造成接触不良或卡断电极丝。
更换导电块或将导电块移位。
6、切割高厚度工件时,间隙过小或使用的工作液浓度过低。
使用DX-2以上工作液右改善,但DX-3须与DX-1混合使用,效果才好,浓度须低于一般工件的切割。
7、脉冲电源消波二极管性能变差,加工中负波较大,使电极丝短时间内切割损耗加大。
更换高频振荡班。
8、电极丝质量差或保管不善,使之氧化,或上丝时用不恰当的工具张丝,使之产生损伤。
注意电极丝的密封与上丝须用专业工具。
9、切割高厚度工件时,电极丝直径选择不当或使用时间过长,以致电极丝直径太小。
超过150mm的工件必须使用0.18mm以上的电极丝,小于0.13mm的电极丝不宜切割高厚度工件。
10、丝筒转速太慢,造成电极丝在工作区域内停留时间过长。
检查丝筒电机是否达到额定转速,拖板是否转动灵活,丝筒夹缝中是否有异物。
工件接近切完时断丝:工件变形,夹断电极丝(断之前多会出现短路现象)或工件跌落卡断地电极丝,选择适当的切割线路与材料,快切割完时用磁铁吸住工件或用丝夹夹住。
高速走丝线切割机床断丝的解决方法(三篇)

高速走丝线切割机床断丝的解决方法高速走丝线切割机床适合加工各种复杂形状的冲模及单件齿轮、花键、尖角窄缝类零件,具有速度快、周期短等优点,应用非常普及。
高速走丝的线切割机床的电极丝主要是采用钼丝,电极丝运动速度快通常为8~12米/秒,而且是双向往返循环运行,在加工过程中很容易发生断丝。
如果在切割工件过程中多次断丝,不仅会造成一定的经济损失,而且会带来重新绕丝的麻烦;不仅耽误时间,而且会在工件上产生断丝痕迹,影响加工质量,严重的会造成工件报废。
本文详细的总结了高速走丝线切割机床在工作中经常出现的断丝原因及解决办法:一、钼丝钼丝的松紧程度。
如果钼丝安装太松,则钼丝抖动厉害,不仅会造成断丝,而且由于钼丝的抖动直接影响工件表面粗糙度。
但钼丝也不能安装得太紧,太紧内应力增大,也会造成断丝,因此钼丝在切割过程中,其松紧程度要适当,新安装的钼丝,要先紧丝再加工,紧丝时用力不要太大。
钼丝在加工一段时间后,由于自身的拉伸而变松。
当伸长量较大时,会加剧钼丝振动或出现钼丝在贮丝筒上重叠。
使走丝不稳而引起断丝。
应经常检查钼丝的松紧程度,如果存在松弛现象,要及时拉紧。
钼丝安装。
钼丝要按规定的走向绕在贮丝筒上,同时固定两端。
绕丝时,一般贮丝筒两端各留10mm,中间绕满不重叠,宽度不少于贮丝筒长度的一半,以免电机换向频繁而使机件加速损坏,也防止钼丝频繁参与切割而断丝。
机床上钼丝引出处有挡丝棒,挡丝棒是由两根红宝石制成的导向立柱,挡丝棒不像导轮那样作滚动运动,他们直接与钼丝接触,作滑动摩擦。
因此磨损很快,使用不久柱体与钼丝接触的地方就会形成深沟,必须及时检查并进行翻转和更换,否则会出现叠丝断丝。
二、运丝机构线切割机的运丝机构主要是由贮丝筒、线架和导轮组成。
当运丝机构的精度下降时(主要是传动轴承),会引起贮丝筒的径向跳动和轴向窜动。
贮丝筒的径向跳动会使电极丝的张力减小,造成丝松,严重时会使钼丝从导轮槽中脱出拉断。
贮丝筒的轴向窜动会使排丝不匀,产生叠丝现象。
快走丝线切割加工断丝的原因和解决方法

快走丝线切割加工断丝的原因和解决方法作者:谷平东来源:《职业·中旬》2013年第02期摘要:随着线切割技术的广泛应用,在加工中也经常遇到一些问题,诸如加工中断丝、短路等。
这些问题一直影响着线切割技术的发展,也给我们在加工时带来许多的麻烦。
为此,本人把在使用线切割机床中遇到的断丝问题及解决断丝的方法总结出来,以供有所需要的朋友参考。
关键词:电火花线切割电极丝断丝在操作线切割机床时,经常会遇到断丝的情况。
而断丝带来的麻烦是:①工件要重新加工,无法保证工件的加工完整性,影响工件的加工精度。
尤其是加工一些模具零件时,由于断丝引起的加工精度达不到要求而浪费材料。
②电极丝需重新安装,浪费大量时间,生产效率降低。
为解决断丝问题,笔者在操作线切割机床时反复试验,不断查找原因。
经过不懈努力,终于找出了线切割加工中出现断丝的原因并提出一些解决的方法,希望这些方法能对相关人员有所帮助。
一、电极丝安装不当引起的断丝1.电极丝安装时出现叠丝叠丝,是指电极丝没有按先后顺序盘绕在储丝筒上,而使电极丝层叠堆积在一起,如果出现叠丝,储丝筒在转动换向时会把电极丝拉断。
解决方法:正确安装电极丝,使电极丝有序地盘绕在储丝筒上,如图1所示。
图12.电极丝安装太松或太紧引起断丝电极丝安装时张紧力不够,机床在高速运行时,则钼丝抖动厉害,不仅会造成断丝,而且还会因钼丝的抖动直接影响工件表面粗糙度。
而电极丝安装时张紧力太大也容易断丝,因为电极丝材料主要为钼,钼金属比较脆,张紧力过大会使电极丝绷得太紧,机床运行时很容易拉断电极丝。
解决方法:当电极丝张紧力太小时,可以通过紧丝的方法进行调节,如图2所示;当电极丝张紧力太大时,适当调低丝架位置,如图3所示。
图2 紧丝操作图3 调低丝架2的位置二、线切割机床冷却系统出现问题引起的断丝线切割加工时用的冷却液主要是由线切割专用乳化液和自来水按一定比例进行勾兑而得。
冷却液在加工中主要起绝缘、冷却、清洗及润滑的作用。
线切割故障现象与排除方法
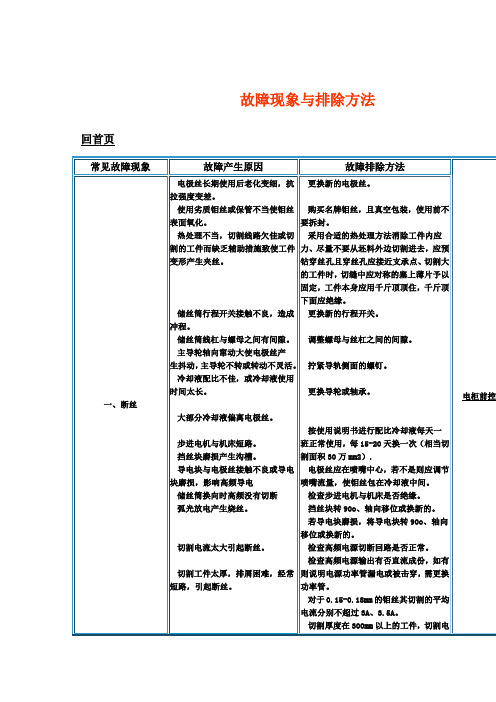
将电极丝重新张紧。
将电极线重新校垂直。
参看 NO.八
三、开机后机床面板上的红指示灯不亮
指示灯泡坏、无 6.3V 电源 保险丝烧坏。
更换6.3V/1.5V的灯泡。
更换保险丝。
四、开机后风扇不转
切割厚度在300mm以上的工件,切割电流应在2A-3A之间,功率管开4-6只即可、脉宽取3、4、5档,脉间取6-10倍率,可以开高压。
二、切割精度不符合要求或切割轨迹出异常
工作台丝杠付传动间隙大。
主导轮轴向有间隙,使电极丝产生抖动。
主导轮长期使用后 V 型槽底部磨损,底部圆角 R>钼丝半径。
材料没有经过相应的热处理,工件变形或切割线路不合理。
将主导轮前端的两个支架螺钉松开,拧紧主导轮两端的滚花螺钉,使主导轮既可灵活转动,轴向又无窜动,然后拧紧前端的支紧螺钉。若上述方法仍不能消除轴向间隙,则必须换新的轴承。
更换导轮。
选择切割线路时必须使切割程序的末端放在离夹持部分最近的地方。
将工件夹紧。
检查行程是否到了极限。
测量好并输入正确的距离数据 。
将开关放在高频位置上。
六、电极丝没断,但储丝筒电机和水泵电机突然停电
导电块与电极丝接触不良,产生虚假断丝。
将电极丝重新张紧,若导电块已磨出沟槽,可将导电块旋转一角度、轴向移动或更换新的导电块。
七、加工不稳定,电流表指 针明显示晃动
电极线松紧不均。
主导轮系统磨损。
喷液方向欠佳。
冷却液配比不佳。
电极丝导电不良。
对中心电路故障。
去除端面或中心孔表面的毛剌。
将开关拨到对中心位置。
线切割断丝原因和参数设置

线切割断丝原因分析:1.快走丝机床加工中断丝的主要原因若在刚开始加工阶段就断丝,则可能的原因有:(1) 加工电流过大(2) 钼丝抖动厉害。
(3) 工件表面有毛刺或氧化皮。
若在加工中间阶段断丝,则可能的原因有:(1) 电参数不当,电流过大。
(2) 进给调节不当,忽快忽慢,开路短路频繁。
(3) 工作液太脏。
(4) 导电块未与钼丝接触或被拉出凹痕。
(5) 切割厚件时,脉冲过小。
(6) 丝筒转速太慢。
(7)管道堵塞,工作液流量大减若在加工最后阶段出现断丝,则可能的原因有:(1) 工件材料变形,夹断钼丝。
(2) 工件跌落,撞落钼丝。
解决办法:1、加工参数:跟踪不要太紧,否则易出现短路,而短路会造成钼丝电流过大,局部产生高温,加速钼丝老化、脆化,易折。
短路电流应设在2a以下为好。
2、将脉宽挡调小,将间隙挡调大,或减少功率管个数3、贮丝筒换向时,未能及时切断高频电源,使钼丝烧断4、检测机床电路部分,要保证先关高频再换向5、工作液使用不当(如错误使用普通机床乳化液),乳化液太稀,使用时间长,太脏6、脉冲电源削波二极管性能变差,加工中负波加大,使钼丝短时间内损耗加大脉宽、脉间参数设置脉宽:线切割脉冲宽度越宽,单个脉冲的能量就月大。
切割得就越快,由于放电时间长,所以加工比较稳定。
但光洁度就越不好。
你要想光洁度好就要把脉宽调小。
脉间:说简单的就是给脏东西排出来的通道大小。
由于厚度大的工件排渣困难,所以就要加大脉间,给排渣有充裕的时间,另一方面减少生成腐蚀物。
使得加工稳定,少断丝脉冲:调整参数:脉宽越大,电流越大,加工越快,不过光洁度越差。
脉间越大,电流越小,加工速度慢,光洁度好。
一般加工厚度100以下的,可以用脉宽30us,脉间150us。
这个参数比较常用脉冲宽度操作方法:旋转“脉宽选择”旋钮,可选择8μs~80μs脉冲宽度,分五档,分别为1档为8μs,二档为20μs,三档为40μs,四档为60μs,五档为80μs选择原则说明:脉冲宽度宽时,放电时间长,单个脉冲的能量大,加工稳定,切割效率高,但表面粗糙度较差。
浅析线切割常见断丝原因及处理方法

网 络
( 未见 尚 实际应 用于汽 用) 车和航空 领域
表 1TCN lxa 和 TP TA 、FeRy T 三种协议在其它方面 的比较 三 、 结 束 语 未来若干年问C N A 总线将继续充当在汽车业 电子网 络架 构 的统治 角色 。汽 车工 业将 慢 慢 改变 它 的 电子 架 构 。最有 可能 的是 ,采用 一种 L N A I 、C N和 F e R y混 lx a 合的协议方 案 。 另一种 方式 是 , 多数汽 车工程 师认识 到 他们将需要 一个 比较大 的 “ 数据 管道 ” ,这 时 M tr l o oo a
传输 速率( p) Ms b
1
1 0
5
传输 效率
平均每 包数据 (b e ) 8y s t
有5y s 余数据 bt 冗 e
平均每包 数据
(5b e)有 24 ts y
平均每 包数据
( 0ye) b e 2 bts 有4y s 4 t
参考 文献 :
[] w . n e r p r . o . 1 w wha s n e o t c m
h a er C O e d R
cl+ a( H C f k /^ K O
其 议服务 他协
主 机时fN . 步 - J
分布时间 同步; 分布时 总线 问同步; 总 节点 监视器. 线冗余 线监 双 视器;网 络成员 检 查,双 线冗余
[ ] h r e .M r a ,S n o e h i a d — 4 C a l sJ u r y e ir T c n c l E i
CN A
小于lbtsc 动力传输、 M /e i 底盘、车载电子 现在
线切割机床常见故障及排除方法
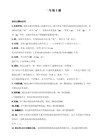
故障现象:4.丝筒不转(走丝电压有指示且较正常工作时高)。
可能原因:①碳刷磨损或转子污垢;
②电机M电源进线断。
排除方法:①更换碳刷、清洁电机转子;
②检查进线并排除。
故障现象:5.工作灯不亮。
排除方法:①紧电极丝;
②换断丝保护继电器。
故障现象:3.丝筒不转(按下走丝开按钮SB1无反应)。
可能原因:①外电源无电压;
②电阻R1烧断;
③桥式整流器VC损坏,造成保险丝FU1熔断。
排除方法:①检查外电源并排除;
②更换电阻R1;
(2) 线切割加工液
线切割加工液的作用是冷却、洗涤、排屑等,因此线切割加工液是否合格直接关系到加工后工件质量的好坏。检查线切割加工液是否太黑,是否有异味,如是,那么其综合性能就会变差,容易导致断丝。
(3) 电极丝(钼丝)
电极丝的质量、安装、保存等因素直接关系到加工后工件质量的好坏。检查电极丝是否选择得当,加工厚工件应选用粗一点的电极丝,这样有利于排屑,也可提高其张力;检查电极丝安装的松紧程度,太松时,电极丝抖动厉害,容易断丝,太紧了,内应力增大,也容易断丝;检查电极丝安装的位置是否偏离中心位置是否不在同一平面内,如是,电极丝极容易被卡断或夹断;检查电极丝的保存是否规范,如在存储时有受潮、氧化、暴晒情况,那么电极丝也会因此变脆而易断。
例2:一台线切割机换向不断高频。检查发现断丝保护挡丝体已被割成深凹槽,由于该断丝保护控制电路没有控制总电源的功能,只控制断高频电路。所以当挡丝体被割成深凹槽后,微动开关因铁块的下垂由常闭状态变成常开状态,从而不能关高频电路。更换该挡丝体,故障即消除。
3. 原理分析法
原理分析法是指在详细了解故障的情况下,根据电火花线切割机的工作原理,分析故障产生的原因,并尽可能找出解决问题的方案。这类方法多种多样,最常用的有以下几种:
线切割加工的断丝现象分析及处理ppt课件

电火花线切割加工特点
不需要制造形状复杂的工具电极 加工中并不把全部多余材料加工成为废屑,提 高了能量和材料的利用率 能够方便的加工各种复杂的的精密器件包括各 种微槽和窄缝 采用长金属丝做电极,单位长度的电极丝损耗 小,加工精度高。 电火花线切割一般采用精规准一次加工成形, 在加工过程中不需要转换加工规准
线切割加工的 断丝现象分析 及处理
电火花线切割加工原理 电火花线切割加工特点 电火花线切割的分类 电火花线切割断丝的现象及其危害 电火花线切割断丝的原因 电火花线切割断丝的防治方法
电火花线切割加工原理
线切割加工是电火花加工的一种。电火花线切割加工 是利用金属丝(钼丝﹑钨钼丝)与工件构成的两个电 极之间进行脉冲火花放电时产生的电腐蚀效应来对工 件进行加工,钼丝与工件之间有足够的具有一定绝缘 性的工作液。当钼丝与工件之间的距离小到一定程度 时,在脉冲电压的作用下,工作液被电离击穿,在钼 丝与工件之间形成瞬时的放电通道,产生瞬时高温, 使金属局部熔化甚至汽化而被蚀除下来,以达到成形 的目的。若工作台带动工件不断进给,就能切割出所 需的形状。
电火花线切割的分类
电火花线切割按切割速 度可分为快走丝和慢走丝。 快走丝加工的工件表面 粗糙度一般在Ra=1.25~2.5 微米范围内,而慢走丝可达 Ra=0.16微米,且慢走丝切割机的固定误差、 线误差和尺寸误差都较快走丝好,所以加工 高精度零件时慢走丝线切割机得到了广泛应用
电火花线切割断丝的现象及其危害
1.脉冲电源脉冲电源是快走丝线切割机 床的关键装置之一,加工过程脉冲电源 电信号的不稳定会直接影响断丝问题。 (1)加工电流很大,火花放电异常,导致 断丝。 (2)输出电流超过限值断丝。在加工过程 中电流超过限值,将钼丝烧断。
快走丝线切割加工断丝的原因和解决方法

煎 _
( b 】 1 一 电极丝 2 - 一 导轮
图4
( C ) 导轮截 面
解决方法: ( 1 )导轮 磨 损 严 重 或 被割 坏 时要 及 时更 换 导轮。 ( 2 )当 电 极丝 运 行 时 , 导 轮不 旋 转 ,导 轮 可 能被 金
图2 紧 丝 操 作 图3 调低丝架 2 的位置
断 丝 的 原 因 并 提 出一 些 解 决 的方 法 , 希 望 这 些 方 法 能对 相 及 时 的 冷 却 而 导 致 电极 丝 烧 断 。 另外 , 当 喷 嘴 被 电极 丝 长 关 人 员 有所 帮助 。
一
、
电极 丝 安 装 不 当 引起 的 断丝
而 引起 电极 丝烧 断 。 解 决方 法 :一 是 定期 更换 工 作液 ,清洗 工 作液 箱 和工 作
属 泥 和 污 垢 或 其 他 金 属 废 料 卡住 无 法 转 动 。此 时 要 用 煤 油 清 洗 导 轮 , 清 除干 净 ,保 证 导 轮 随 电极 丝 一起 转 动 。
② 电 极 丝 需 重 新 安 装 ,浪 费 大量 时 间 ,生 产 效 率 降低 。 为 解 决 断 丝 问题 ,笔 者 在 操 作 线切 割 机 床 时 反 复 试 验 ,不 断 查 找 原 因 。 经 过 不 懈 努 力 , 终 于 找 出 了线 切 割 加 工 中 出现
系 统 主 要 由工 作 液 箱 、工 作 液 泵 、输 液 管 和 喷 嘴 所 组 成 。 冷 却 液 是 循 环 使 用 的 , 随着 工 作 液使 用 时 间 增 长 , 工 作 液
关 键词 : 电 火花 线切 割 电极 丝 断 丝
在 操 作 线 切 割 机 床 时 , 经 常 会 遇 到 断 丝 的情 况 。而 断 和 自来 水 按 一 定 比例 进 行 勾 兑而 得 。 冷 却 液 在 加 工 中主 要 丝 带来 的 麻 烦 是 :① 工 件 要 重 新 加 工 ,无 法 保 证 工 件 的 加 起 绝 缘 、 冷 却 、清 洗 及 润 滑 的作 用 。 因此 ,冷 却 液 的 供 给 工 完整 性 , 影 响 工 件 的加 工 精 度 。 尤 其 是 加 工 一 些 模 具 零 正 常 与 否 会 对 加 工 造 成 很 大 的影 响 。 线切 割机 床 上 的 冷 却 件 时 , 由于 断 丝 引 起 的加 工 精 度 达 不 到 要 求 而 浪 费材 料 。
线切割频繁断丝的原因

线切割频繁断丝的原因1. 引言线切割是一种常见的金属加工方法,通过电火花放电的方式将导电线切割工件。
然而,在实际应用中,我们可能会遇到线切割频繁断丝的问题。
本文将探讨线切割频繁断丝的原因,并提供相应的解决方案。
2. 原因分析2.1 导电线质量问题导电线是线切割中重要的零部件之一,其质量直接影响到线切割的效果。
导电线若质量不合格,容易出现断丝现象。
以下是导电线质量不合格可能导致断丝的原因:•材料问题:导电线材料应具有良好的导电性和耐磨性。
若使用劣质材料制作导电线,容易出现断丝现象。
•直径不均匀:导电线直径不均匀会导致放电时产生的热量不均匀分布,进而造成局部过热和断丝。
•表面光洁度差:表面粗糙度大、存在氧化物或沉积物的导电线容易产生放电不稳定,从而引起断丝。
2.2 放电参数设置问题放电参数的合理设置对于线切割效果至关重要。
以下是放电参数设置不当可能导致断丝的原因:•脉冲电流过高:脉冲电流过高会导致放电时的能量过大,容易引发过热和断丝。
•脉冲宽度过长:脉冲宽度过长会造成能量持续输入,导致局部过热和断丝。
•放电间隙不合适:放电间隙过大或过小都会影响到放电效果,进而引起断丝。
2.3 工件材料问题工件材料的选择和质量也会对线切割产生影响。
以下是工件材料问题可能导致断丝的原因:•硬度过高:硬度过高的材料难以被切割,容易导致导电线受力增大而断丝。
•含有硬质颗粒:工件表面存在硬质颗粒会增加切割阻力,使得导电线容易受力集中并断丝。
2.4 刀具磨损问题刀具的磨损情况也会影响到线切割的效果。
以下是刀具磨损问题可能导致断丝的原因:•导电线固定不当:若导电线与刀具之间的接触不紧密,容易造成放电不稳定和断丝。
•刀具绝缘层破损:刀具绝缘层破损会导致放电过程中的能量散失,进而引起放电不稳定和断丝。
3. 解决方案为了解决线切割频繁断丝的问题,我们可以采取以下措施:•选择优质导电线材料:选择具有良好导电性和耐磨性的导电线材料,确保材料质量符合要求。
浅谈线切割机床断丝原因及预防

浅谈线切割机床断丝原因及预防作者:张伟来源:《职业·中旬》2009年第09期高速走丝线切割机床具有高质量、高效率等优点,在模具制造、成形刀具加工、难加工材料和精密复杂零件的加工方面有不可替代的作用。
但是线切割加工中常常断丝,造成了电极丝的大量浪费和成本增加,重新人工上丝会影响机床的加工效率,使加工零件的精度和表面质量下降甚至工件报废。
因此,笔者介绍几种断丝现象及相应的解决方法和预防措施。
一、断丝现象及解决办法1、空转时断丝主要原因是钼丝排列时叠丝、丝筒转动不灵活、电极丝卡在导电块槽中等。
可通过检查钼丝是否在导轮槽中、排丝机构的螺杆是否间隙过大、丝筒轴线是否与线架相垂直、丝筒夹缝中是否进入杂物以及更换或调整导电块位置方法排除。
2、开始切割时即断丝初始切割时,钼丝在工件之外,上下导丝轮开距大,钼丝和工件之间的间隙处于不佳状态,钼丝没有阻尼而抖动剧烈,或加工电流过大,进给不稳、工件表面有毛刺,或有不导电氧化皮或锐边造成断丝。
解决方法是刚切入时用过调整参数使电流适当减小,切入后,工件侧壁面无火花时再增大电流。
检查走丝系统部分,如导轮、轴承、丝筒是否有异常跳动、振动并清除氧化皮、毛刺。
3、切割过程中突然断丝原因主要有:选择电参数不当,电流过大;进给调节不当,开路短路频繁;工作液太稀、太脏,管道堵塞,工作液流量大减;导电块未能与钼丝接触或已被钼丝拉出凹痕;切割厚件时,钼丝直径太小,间歇过小;脉)中电源削波二极管性能变差,加工中负波较大,钼丝短时间内损耗加大:钼丝被氧化或上丝不当,使丝损伤:丝筒转速太慢,使钼丝在工作区停留时间过长等。
可通过将间歇档调大,或减少功率管个数;使用线切割专用工作液;清洗管道;更换或将导电块移一个位置;更换削波二极管;更换钼丝,使用上丝轮紧丝:合理选择丝速档;选择直径合适的钼丝等方法排除。
4、工件接近切完时断丝原因可能是工件材料的内应力导致变形,夹断钼丝:或工件跌落时,撞断钼丝。
线切割钼丝断丝原因汇总及解决方法

以下是有关线切割机械部分造成的断丝的原因及解决办法:1、导电块造成的断丝:线切割钼丝长时间运行加工接触导电块,造成导电块会有沟痕,长时间不处理造成沟痕过大而导致的夹断钼丝。
解决办法:定期将导电块旋转一定角度或横移位置,或更换新的导电块。
2、导轮造成的断丝:钼丝是通过导轮来进行导向的,所以导轮的精度会影响钼丝的运行,导轮中的轴承的轴向和径向跳动会影响钼丝放电加工的稳定。
解决办法:需要定期喷注润滑脂保养导轮,到了使用期限就需要更换轴承,或更换导轮组件。
3、上丝紧丝造成的断丝:在上丝的时候如果张丝用力过大,可能也会造成断丝;紧丝时如果用力过小则造成钼丝张力不够,用力过大则会造成钼丝拉伤从而导致断丝。
解决办法:需要拿捏合适的力度来上丝紧丝。
4、运丝筒造成的断丝。
加工过程中,运丝筒不断的进行移动,从而引发的径向跳动会造成钼丝切割过程中张力变化,会引起叠丝,从而造成断丝。
解决办法:需要定期检测运丝筒精度并做调正。
5、钼丝在运丝筒上缠绕不合理造成的断丝:钼丝在运丝筒的两段需要预留5-10MM的钼丝,不然钼丝会在换向时张紧力度不均挣断钼丝,钼丝的叠丝也会造成断丝。
解决办法:应该在上丝的时候合理的调正钼丝。
6、换向传感器失灵造成的断丝:开关压板没有固定好,或没有压下行程开关,或行程开关失灵。
解决办法:线切割加工前保证换向开关及开关压板的可工作性。
7、钼丝没有挂好造成的断丝:上丝时如果钼丝没有挂在正确的走丝路径上,如导轮外,开机就会拉断钼丝。
解决办法:上丝完成后,检查一遍钼丝路劲,查看是否都挂好在正确的走丝路径上。
8、钼丝热胀冷缩造成的断丝:如果加工完成后,钼丝未停靠在运丝筒两边,钼丝张力过紧会在冷却后挣断钼丝。
解决办法:停机后,钼丝停靠在运丝筒的一端,如不继续加工,还应松开钼丝的一端。
- 1、下载文档前请自行甄别文档内容的完整性,平台不提供额外的编辑、内容补充、找答案等附加服务。
- 2、"仅部分预览"的文档,不可在线预览部分如存在完整性等问题,可反馈申请退款(可完整预览的文档不适用该条件!)。
- 3、如文档侵犯您的权益,请联系客服反馈,我们会尽快为您处理(人工客服工作时间:9:00-18:30)。
一、与钼丝相关的断丝 1、张力及走丝速度 1)提高钼丝的张力可减少丝振的影响,从而提高精度和切割速度,并且明显减少断丝,一般认为张力在12-15N较合适。 2)走丝速度的提高有利于钼丝把工作液带入较大厚度工件的放电间隙中,确保电蚀产物的排除和放电加工的稳定。但走丝速度过高,钼丝抖动严重,将会破坏加工的稳定性,加工精度和表面粗糙度都会变差,并易造成断丝。走丝速度过低时由于损耗大,也易断丝,一般经验以小于10m/s为宜。 二、与导丝结构相关的断丝 1、与运丝筒相关断丝 1)运丝筒内外圆不同轴,会产生不平衡惯量,运转时容易产生叠丝而导致断丝。 2)运丝筒的轴和轴承等零件常因磨损而产生间隙,易引起丝抖动而断丝。 3)运丝筒换向时如没有切断高频电源,会导致钼丝在短时间内因温度过高而产生烧丝,因此需检查运丝筒后端的行程开关是否失灵(控制高频的继电器是否损坏)。 4)要保持运丝筒、导轮转动灵活,否则在往返运转时会引起导丝系统的振动而发生断丝。 5)需调整好运丝筒后端的限位挡块,避免运丝筒冲出限位行程而断丝。 6)应在换向后不久停机,防止运丝筒因惯性超程冲坏传动件及拉断钼丝。 2、与导轮、导电块相关的断丝 1)若导轮和导电块因磨损而产生沟槽,或导轮轴承磨损后产生间隙,都容易造成钼丝抖动而断丝。 2)应保证钼丝与导电块、加工工件与工作台面接触良好,否则高频电源负极无法丝
钼丝圈
厚工件一般指厚度大于100mm的工件。断丝的主要原因是: 1、切割开始的断丝 这是因初始切割时,钼丝在工件之外,上下导轮开距大,便引起钼丝拉动抖动,使钼丝和工件之间的间隙不稳定,易形成弧放电,使电弧集中于某一段,就会引起断丝。在电火花加工中,电弧放电是造成负极腐蚀损坏的主要因素。 2、切割过程中的断丝 当钼丝切入工件后,由于切缝窄,乳化液渗透困难,切缝中的电蚀物(碳黑与金属物)不易排除,使加工条件变坏,在切缝中产生二次、三次的放电加工,致使切缝变宽,间隙入于不佳状态,使脉冲形成电弧放电,引起断丝。 3、切割快结束时的断丝 在快切割完而尚差几毫米,甚至几十微米时的断丝除上述原因外,还有工件的自重或工件材料内应力导致的变形造成的夹丝拉断,解决的方法是:可自制简易的工装夹具、材料厂在加工前作必要的热处理。 四、与工作液相关的断丝 1、工作液变黑后的综合性能就会变差,极易造成断丝。因此要经常观其色,嗅其味,发现异常及时更换,使工作液保持一定的介电能力。尤其是加工硬质合金时,电蚀物较多,易使工作液的渗透性和流动性差,造成排屑不良。 2、如何鉴别皂化液 1)绕一点新钼丝,在工件上试割约1小时,观察钼丝的颜色,若呈灰白色,冷却液可切割较薄工件,如灰白色中夹杂黑色斑或黑条,黑条处直径明显变细,需要更换新的工作液。 2)看起弧和通路电流。启动运丝筒,人工强迫高频电流接通,使钼丝慢慢向工件靠拢,不要接触工件,大约间距1-1.5mm,此时应没有火花。然后给工件冷却,使钼丝与工件间距构成液体通路,若有火花产生或电流表读数值在原空载基础上增加10mA以上,(空载30mA左右),此时工作液不可再用。 五、与电参数相关的断丝 1、根据工件厚度选择合理的电参数,将脉冲间隔打开一些,这样有利于熔化金属微粒的排出。同时峰值电流的空载电压不宜过高,否则使单个脉冲能量变大,切割速度加快,容易产生集中放电和拉弧,引起断丝。一般空载电压为100V左右。 2、根据工件厚度选择合适的放电间隙,放电间隙过小,容易产生短路,也不利于冷却和电蚀物的排除;放电间隙过大将影响表面粗糙度及加工速度.当切割厚度较大的工件时应尽量选用大脉宽电流同时放电间隙也要相应大一点(一般应大于0.02mm)从而增强排屑效果提高切割的稳定性. 六、与高频电源相关的断丝 1、短路电流峰值过大,即功放管投入的数量太多,超过了钼丝所能承受的电流,将会使钼丝过热,因过度疲劳而脆断。 2、高频脉冲负波过大,脉冲的负波直接腐蚀钼丝,使丝损耗增大,降低丝的使用寿命,造成短时间内断丝。 3、脉冲宽度及脉冲间隔选择不当,在加工厚度较大的工件时,脉冲宽度过大,会使放电间隙中出现放电点集中的现象,烧伤钼丝;脉冲间隔过小,使间隙中的电蚀物不能充分排出,消电离不充分,也容易断丝。此时在钼丝上可以明显看出烧伤痕迹(即黑色斑点)。 七、与工作台移动相关的断丝 1、工件的切割精度靠丝杆来保证,丝杆和螺母的间隙是靠弹簧来消除的。如果丝杆润滑不良或弹簧力不足,会引起工作台不匀速移动,在这种情况下切割,高频电流会出现频繁的短路,如不及时排除故障,势必造成断丝。 2、在调节变频跟踪速度时,应尽量使进给速度约等于工作蚀除速度,这样脉冲利用率高,加工速度快,加工状态稳定。进给速度过高,短路频繁,丝老化快,在电流表上可看出加工电流较大;加工速度过低,进给速度调节过慢,易使放电间隙不稳定,产生过渡电弧放电,极易烧断钼丝。