外文翻译---供应链管理ABC
供应链管理(中英对照)

Supply Chain Management供应链管理The so-called supply chain, in fact, from suppliers, manufacturers, warehouses, distribution centers and channels, and so constitute a logistics network. The same enterprise may constitute the different components of this network node, but the situation is different from a corporate network in different nodes. For example, in a supply chain, companies may not only in the same manufacturers, storage nodes, and in distribution centers, such as possession node location. In the more detailed division of labor, the higher the professional requirements of the supply chain, different nodes are basically composed by different enterprises. In the supply chain flows between the member units of raw materials, finished products, such as inventory and production constitutes the supply chain of goods flow.所谓供应链,其实就是由供应商、制造商、仓库、配送中心和渠道商等构成的物流网络。
外文文献翻译供应链管理与5s管理
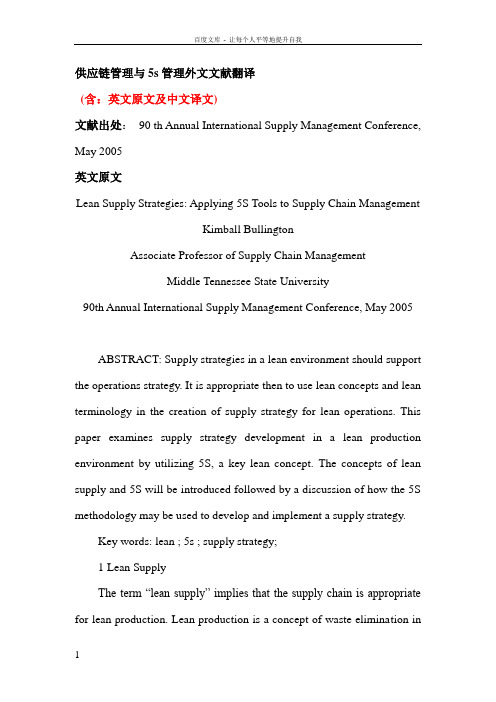
供应链管理与5s管理外文文献翻译(含:英文原文及中文译文)文献出处:90 th Annual International Supply Management Conference, May 2005英文原文Lean Supply Strategies: Applying 5S Tools to Supply Chain ManagementKimball BullingtonAssociate Professor of Supply Chain ManagementMiddle Tennessee State University90th Annual International Supply Management Conference, May 2005ABSTRACT: Supply strategies in a lean environment should support the operations strategy. It is appropriate then to use lean concepts and lean terminology in the creation of supply strategy for lean operations. This paper examines supply strategy development in a lean production environment by utilizing 5S, a key lean concept. The concepts of lean supply and 5S will be introduced followed by a discussion of how the 5S methodology may be used to develop and implement a supply strategy.Key words: lean ; 5s ; supply strategy;1 Lean SupplyThe term “lean supply” implies that the supply chain is appropriate for lean production. Lean production is a concept of waste elimination inprocesses, which has enjoyed popularity in manufacturing companies. The basic tenets of lean production as outlined by Womack and Jones (1996) include the following 、Specify value 、Identify the value stream、Organize the value stream to promote flow、Communicate demand through pull、Strive for perfection.It is appropriate for the supply management function in a lean environment to integrate lean concepts and terminology into the development of supply strategy. One of the foundational lean concepts that serves as a basis for all of the tenets given above is 5S.What is 5S?The 5S’s are lean concepts derived from the Japanese words: seiri (sort), seiton (set in order), seiso (shine or purity), seiketsu (standardize), and shitsuke (sustain) (Hirano,1996). Companies adopting the lean production philosophy often implement the 5S process to bring order to the workplace and thereby support lean production. 2 Why Use the 5S Concept as a Model for Lean Supply Strategy?5S is a proven model for organizing and maintaining a lean production environment. The relationship between purchasing or supply and the general management of operations may be improved through the use of a common vocabulary built around concepts familiar to the organizational head and the heads of other departments. For this reason, 5S is an appealing model for the development of supply strategy in a leanproduction environment. A model for using 5S to develop supply strategy follows.2 Sort:Remove All But the Necessary Materials, Equipment and Supplies.Typically, the first step in a producer’s implementation of 5S will be a tour of the target area marking with red tags those items that appear out of place or unnecessary. After reviewing each item, the item will either be put in its proper place or removed if it is unnecessary or redundant. The Sort process is essential to developing the organization of the workspace needed for lean production.Sorting the supply base includes selection of suppliers to add to the system and selecting suppliers to eliminate (supply base consolidation or rationalization). Implementing Sort in the supply base through supplier consolidation achieves the following benefits. It reduces the waste of inefficient work methods by reducing the number of suppliers that must be managed by the procurement staff. Sorting reduces the waste of selecting the wrong suppliers by focusing efforts of selection, evaluation, and improvement on a few select suppliers. This also improves the quality (conformance to specifications and delivery) of the products received from these suppliers by focusing quality assurance, control and improvement activities on a smaller number of suppliers. Sorting reduces processing waste as fewer purchase orders may be necessary and fewerselection audits are needed. Finally, Sorting increases the opportunity for supply chain partnering.So for the management of supply, the primary implementation of Sort is selection. There are several criteria that may be used to identify candidates for elimination in the sorting process.First, a performance review ., review of quality, delivery, and price performance) isolates some candidates for elimination. Next, a review of redundant suppliers is conducted. How many suppliers have identical or overlapping capabilities? Finally, a review of the number of part numbers purchased from each supplier will often result in identification of a large number of suppliers providing only one or a few parts.All of the sorting or consolidation is an effort to approach an optimum number of suppliers. Multiplying suppliers increases variation and overhead. The practice of utilizing multiple suppliers for a single part in order to reduce risk often increases risk, just as increasing the number of components in an assembly usually increases the probability of failure.Set in Order: Arrange Product and Equipment So It is Easy to Find and Easy to Use.Equipment and storage locations are labeled so equipment or tools will be easy to identify and put away when they are no longer in use ., tool cutouts or outlines on a peg board or in a tool chest). The labeling of storage locations with tape on the floor or the work station facilitatesvisual management. A glance is sufficient to identify missing tools or tools not properly stored.Arranging suppliers so they are easy to use brings to mind the concept of s egmentation. Segmentation provides a “place for everything” and allocates “everything in its place.” The supply base is sorted or segmented by value potential and risk, by strategic value and opportunity for cost improvement, by value potential and criticality, or other such criteria. The proper “place” for a supplier is a location in a segmentation matrix. The value of this exercise comes from clearly identifying how each supplier will be treated based on identifiable criteria. Table 1 is an example segmentation of the supply base by annual expenditures and risk yielding four segments of suppliers with different opportunities for value contribution.The key suppliers for lean production companies tend to be in the high risk –high value potential or “partnership” category of the supplier segmentation matrix.Partnership suppliers represent a higher risk to the company in terms of design complexity, startup communication, custom tooling, overall higher demand for buyer input, and schedule pressures ., just-intime support). Risk can also be thought of as the level of opportunity for adverse effects on value ., deterioration in delivery, lead time, price, or quality).The other supplier segments have different needs. The low risk –high value potential segment may include commodity items where price dominates other considerations. If the risk may be reduced for high risk –high value potential items, significant savings may be realized by some form of competitive bidding.The high risk –low value potential suppliers affect value by the nature of the factors that make them high risk. Risk factors could include demanding delivery requirements, advanced technology, etc. Temporary situations, such as cash flow problems or capacity limitations, could be the major risk factors. Segmentation helps prevent the supply manager from overlooking these potential problem suppliers. Finally, the low risk – low value potential suppliers typically have relatively high transaction costs as compared with the value of the product. The opportunity for adding value comes by consolidating these purchases and reducing transaction costs. Several different segmentations may be conducted in order to properly categorize the suppliers. The segmentation of suppliers may also include an evaluation of quality ., certified, conditional, approved status). Performance measures may be helpful in segmenting the remaining supply base. Hau Lee (2002) suggests the use of an uncertainty framework as a means of segmenting the supply base for demand and supply uncertainty.The location aspect of Set in Order may be addressed by identifyingthe location value of each supplier on a large map. This may identify further opportunities for consolidation by grouping suppliers locally or in targeted areas or along trucking routes so more than one supplier may be visited on a single trip. Other considerations for2.2.1 Keep Everything Swept and Clean.Cleaning implies system maintenance and inspection. As a work area is cleaned, problems such as oil leaks or other maintenance issues become more apparent before they have a chance to affect performance. The inspection of suppliers implies surveys or audits. The objective of auditing suppliers is to obtain objective evidence that supports the Sort and Segmentation decisions or evidence that supports action of a different sort, such as risk reduction and continuous improvement. These audits may include: site surveys, supplier self-assessments, remote surveys, third party certification type surveys ., ISO 9000 or QS 9000), or third party quality awards such as the Baldrige Award (or state award using the Baldrige criteria). Major changes in supplier personnel and the work place environment may not be detected by 3rd party audits such as ISO certification audits. First person audits should be structured in such a way as to detect performance or personnel changes.For key suppliers (identified in the Set in Order or Segmentation stage), on-site visits should be scheduled with a frequency appropriate to the relationship. For example, high risk-high value potential suppliersusually receive the highest frequency of visits followed by high risk – low value potential, and low risk - high value potential suppliers respectively. Low risk –low value potential suppliers are generally not surveyed except for mail surveys of regulatory compliance issues. 2.2.2 Integrating the First Three S.Standardize ensures that your implementation of the Sort, Set in Order, and Shine doesn’t deteriorate over time. It formaliz es the procedures, schedules and practices that sustain the system and drive future improvements. Problems avoided by Standardize include: Firstly , the number of suppliers grows unchecked,Secondly, the segmentation deteriorates and the classification of the suppliers becomes unknown,Thirdly, suppliers are not visited on a regular basis,Fourthly, surveys are conducted informally or with renegade processes.How can you standardize? Assign 3S duties. Ensure that the personal plans or objectives of the supply management personnel cover the sort (supplier consolidation), set in order (segmentation), and shine (audit) issues necessary.Strategic buyers, commodity managers, or the purchasing manager are charged with the resp onsibility of surveying the charts in each buyer’s area to ensure they are kept current. The results of these surveys may bedisplayed on checklist charts demonstrating the level of implementation.Often the motivation for adding suppliers comes from outside of the purchasing function. Do these functions understand why consolidation is valuable? One advantage of the 5S approach is that a common language will be used between purchasing and manufacturing. This should facilitate the communication between these groups, but what about interactions between design engineering and purchasing? This is a critical interface for two reasons. First, engineering is the source of many requests for new suppliers. Second, engineering, particularly design engineering, may have a creative environment that feels constrained by programs that promote rigid discipline. Engineers have complained that they see no reason to limit their supplier selections just so the buyers can play more solitaire on the computer. The 5S program provides reasoning behind the consolidation efforts. Survey schedules are maintained using software that reminds the process owner and the appropriate managers. In some organizations, the quality assurance department can serve a role as a third party to the process with supplier delivery performance being considered with quality performance for preferred supplier status. Supplier surveys or audits should be part of the personal evaluation process for the owners of this process ., buyers, supplier quality engineers, commodity managers).3 Discipline Starts With the Leadership.Do you care enough to be consistent with your message and vision? Are you communicating the strategy, including the reasons for your actions, outside of the procurement function? Are you training new employees properly? Does the proper structure exist to support this strategy? These are issues for leadership. No 5S process for supply management will be effective without vigilant leadership. Lean producers have used this process effectively, but consistent leadership over time is necessary to prevent system deterioration.4 Summary.Each element of the 5S technique corresponds to an element of supply strategy for a lean supply chain. 5S is a powerful tool in manufacturing, in part, because of its simplicity. Simplicity makes 5S a powerful supply management tool as well.中文译文精益供应策略:将5S工具应用于供应链管理作者:Kimball Bullington供应链管理副教授田纳西州立大学第90届国际供应管理年会,2005年5月摘要:精益环境中的供应战略应该支持运营战略。
供应链管理系统双语英文翻译

供应链管理系统双语英文翻译1) A supply chain includes only the organizations directly involvedin supplying components needed for manufacturing.一个供应链仅包括直接参与提供所需的元件制造业的组织。
Answer: FALSE2) A supply chain consists of all parties involved, directly or indirectly, in fulfilling a customer request. Answer: TRUE 供应链由所有各方,直接或间接参与,满足客户要求。
3) A supply chain could be more accurately described as a supply network or supply web.Answer: TRUE供应链可以更准确地描述为供应网络。
4) The objective of every supply chain is to maximize the overall value generated. TRUE每一个供应链的目的是生成的整体价值最大化。
5) The objective of every supply chain is to maximize the value generated for the manufacturing component of the supply chain. Answer: FALSE每一个供应链的目标是最大化为供应链的制造组件生成价值。
6) Every supply chain must include all 5 stages. Answer: FALSE每个供应链必须包括所有 5 个阶段。
7) The cycle view of a supply chain holds that the processes in a supply chain are divided into a series of activities performed at the interface between successive stages. Answer: TRUE 供应链周期认为供应链流程分为一系列的活动上演在连续阶段之间的接口。
供应链管理外文翻译——Supplychain
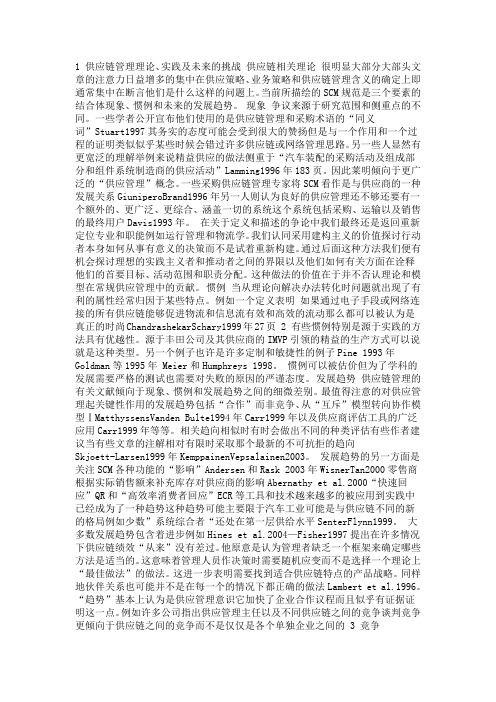
1 供应链管理理论、实践及未来的挑战供应链相关理论很明显大部分大部头文章的注意力日益增多的集中在供应策略、业务策略和供应链管理含义的确定上即通常集中在断言他们是什么这样的问题上。
当前所描绘的SCM规范是三个要素的结合体现象、惯例和未来的发展趋势。
现象争议来源于研究范围和侧重点的不同。
一些学者公开宣布他们使用的是供应链管理和采购术语的“同义词”Stuart1997其务实的态度可能会受到很大的赞扬但是与一个作用和一个过程的证明类似似乎某些时候会错过许多供应链或网络管理思路。
另一些人显然有更宽泛的理解举例来说精益供应的做法侧重于“汽车装配的采购活动及组成部分和组件系统制造商的供应活动”Lamming1996年183页。
因此莱明倾向于更广泛的“供应管理”概念。
一些采购供应链管理专家将SCM看作是与供应商的一种发展关系GiuniperoBrand1996年另一人则认为良好的供应管理还不够还要有一个额外的、更广泛、更综合、涵盖一切的系统这个系统包括采购、运输以及销售的最终用户Davis1993年。
在关于定义和描述的争论中我们最终还是返回重新定位专业和职能例如运行管理和物流学。
我们认同采用建构主义的价值探讨行动者本身如何从事有意义的决策而不是试着重新构建。
通过后面这种方法我们便有机会探讨理想的实践主义者和推动者之间的界限以及他们如何有关方面在诠释他们的首要目标、活动范围和职责分配。
这种做法的价值在于并不否认理论和模型在常规供应管理中的贡献。
惯例当从理论向解决办法转化时问题就出现了有利的属性经常归因于某些特点。
例如一个定义表明如果通过电子手段或网络连接的所有供应链能够促进物流和信息流有效和高效的流动那么都可以被认为是真正的时尚ChandrashekarSchary1999年27页 2 有些惯例特别是源于实践的方法具有优越性。
源于丰田公司及其供应商的IMVP引领的精益的生产方式可以说就是这种类型。
另一个例子也许是许多定制和敏捷性的例子Pine 1993年Goldman等1995年 Meier和Humphreys 1998。
供应链管理外文翻译

The Impact of Green Supply Chain Management on Transportation Cost ReductionABSTRACT: Supply chain management(SCM)has become an important competitive approach for organizations. The issue of green supply chain management is critical for the successful implementation of industrial ecosystems and industrial ecology. Organizations have a number of reasons for implementing these green supply chain policies, from reactive regulatory reasons, to proactive strategic and competitive advantage reasons. From an overall environmental and organizational perspective, it is important to understand the situation and what issues exist in this field. Many organizations worldwide have already experienced globalization and a shifting focus to competition among networks of companies in this environment. Multinational enterprises have established global networks of suppliers that take advantage of country-industry specific characteristics to build this competitive advantage. To success having this competitive advantage, logistics and supply chain managers have to balance efforts to reduce costs and innovate while maintaining good environmental performance. Therefore, today, competition is not between companies, between supply chains. This study brings us the effect of Green Supply Chain Management (GSCM) on the Transportation Cost Reduction (TCR). Keywords: Green Supply Chain; Transportation Cost; Cost Reduction1.IntroductionGlobal enterprises are permanently trying to develop new, flexible, applicable and innovative methods to enhance their success and competitiveness. Some of these organizations are enhancing their competitiveness through improvements in their environmental activities performance to comply with environmental law and regulations. The main point of complying with environmental law and regulations is customer environmental concerns and environmental impact of production and service activities. Besides, increasing of awareness of the propensity for environmental pollution within organizations’ supply network to c ost them in consumer complain, cleanup and punishment.To response the requirement of environmental law and regulations, minimum standards of environmental performance have become increasingly prevalent in the purchasing agreements of multinational corporations for their local and global suppliers. This requirement has become a new customer expectation from suppliers therefore suppliers have to reduce costs and improve quality and service to complete their responsibility for their customers.It is generally thought that green supply chain management has a great effect in increasing environmental performance, minimizing waste and achieving cost savings. Besides because of increasing synergy among business parties, green supply chain management enhances efficiency through partner and their supply networks. This synergy is expected to enhance the corporate image, competitive advantage andmarketing exposure.However, if green supply chain management practices are to be fully adopted by all organizations, a demonstrable link between such measures and cost saving, specifically transportation cost saving is very necessary. Bowen et al. state that organizations will adopt green supply chain management practices if they identify that this will result in specific financial and operational benefits.Thus, there is a clear research need to establish the potential link between structure of green supply chain and effective transportation cost saving, to provide an accelerator for enterprises to establish effective green their supply chains.Many enterprises have demonstrated significant efforts to establish green supply chain management initiatives. While there is not enough study which examine about cost reduction through Green Supply Chain Management and tested an empirical link between such efforts and Transportation Cost Reduction. Therefore, this paper presents the results of a survey of organizations to investigate the proposition that there is a significant relation between GSCM and TCR.2. Literature ReviewThis paper encompasses previous “functional” specific research on aspects of GSCM, to develop a conceptual model of GSCM and TCR. In this paper, the structure of green supply chain management encompasses environmental parameters as:(1) Purchasing and In-Bound Logistics,(2) Production or the Internal Supply Chain,(3) Distribution and Out-Bound Logistics,(4) Reverse Logistics.2.1 Purchasing and In-Bound LogisticsFrom the purchasing - the beginning point of supply chain - perspective of the supply network it is under discussion that GSCM has several benefits, ranging from cost reduction to integrating suppliers in a participative decision-making process that promotes environmental innovation). Green purchasing strategies which the largest part of inbound logistics side is adopted by the companies to response global concern of environmental stability.Green purchasing might enhance issues such as using environmental transportation, cost reduction, material substitution and waste minimization of hazardous materials. The involvement and support of suppliers is crucial to achieving such goals. Therefore, companies are increasingly managing their suppliers’ environmental performance to ensure that the materials and equipments supplied by them are environmentally-friendly in nature and are produced using environmentally friendly processes.Integration of suppliers into environmental management system could be completed in two steps. First step, Walton et al suggest that environmental issues become main part of strategic planning to response regulations and the demands of environmental accountability. In second step, organizations integrate their supplier to their supply chains to make reduction operational costs and improve customer service.2.2 Greening the Production Phase or the Internal Supply ChainThere are several notions that could be explained about green supply chain in production phase, such as cleaner production, design for environment, remanufacturing and lean production. Lean production has an importance to decrease the environmental impact of the internal supply chain. Lean production improves environmental performance by reducing general waste and minimizing hazardous wastes.Besides, production phase has an important role in keeping same quality level of organization that: having environmentally-friendly production; prevention of pollution at source; cleaner production practices are adopted; closed loop manufacturing (reverse logistics) is incorporated to the fullest extent possible, re-use and recycling of materials is maximized; material usage is reduced; the recyclable content of a product is increased; the production processes are optimized so that generation of waste, both hazardous or otherwise, is minimized; and products are redesigned (design for the environment). Also additionally design of the facility based on lean production is able to minimize vehicle movement.2.3 Greening the Outbound Function and Reverse LogisticsOn the outbound side of the green supply chain, reverse logistics, environment-friendly packaging, and environment-friendly distribution, are all initiatives that might improve the environmental performance of an organization and its supply chain. Management of wastes in the outbound function such as reverse logistics and waste exchange can lead to cost savings and enhanced competitiveness. Many of these initiatives involve compromises between various logistics functions as reverse logistics and environmental consideration in order to improve the environmental performance of an organization.In an eco-transportation system, required parameters of a transportation system such as type of transport, fuel sources, infrastructure, operational practices and organization, can be considered. These parameters and the dynamics that connect them, determine the environmental impact generated in the transportation logistics phase of the supply chain.3. Model and MethodologyAt this section, w investigate research question by using a questionnaire to collect data. After collecting, I use SPSS software to control relation between our variables by regression analysis.Model has three phases. In first phase, five dimensions are used of all GSCM dimensions which affect fuel consumption & maintenance, repairing expenditure. In second phase, the well known relation with fuel consumption & maintenance, repairing expenditure and transportation cost reduction is used to get result for this study. Transportation cost reduction side is third phase in our model. One point about methodology should be clarified in second phase.The reverse relation between fuel consumption & maintenance, repairing expenditure and transportation cost reduction. But the difficulties of finding fluctuation in transportation cost reduction in a direct way. To get result about transportation cost reduction, I use the second phase as a step phase. Through secondphase, I get effect of five dimensions into fuel consumption & maintenance, repairing expenditure, then using result and using reverse relation, I reach the point which explains the effect of five dimensions into transportation cost reduction.3.1 QuestionnaireTo validate the model given in the preceding section, regression analysis is used to determine the causal relationships between environmental transportation, suppliers by environmental criteria, helping suppliers to establish their own environmental management system, optimize internal process to minimize vehicle movement, reverse logistics and transportation cost reduction.An empirical survey-based research approach was adopted, comprising of 38 items. The questionnaire was distributed to the environmental management representative or the logistics representative of ISO 14001 certified organizations. The justification for using a five-point scale served to understand that there might have been a tendency of having most negative responses loading heavily on the median level, the center point of the scale. The research instrument was distributed to corporations using an online survey website. Company representatives enter the website and response the questions through website.That website serves data as in SPSS file and SPSS estimates a series of separate but interdependent regression equations simultaneously. We have drawn upon the theory and the research objectives to determine which independent variable will predict which dependent variable. The proposed relationships are then translated into a series of structural equations for each dependent variable. The structural model expresses these relationships among independent and dependent variables.3.2 HypothesisAt this section, there are five different hypothesis e to examine the impact of GSCM on TCR. Five different hypothesis is coming from five different dimensions of GSCM. Of course, total dimensions are not only five but as representing in the preceding section, only five of all dimensions are used to create hypothesis. Hypothesis’ are in representing as below.3.3 ResultsBased on model and hypothesis, results have been gotten by using regression analysis method. In this analysis FCMRE and TCR is dependent variables and the other five dimensions of GSCM(Using more environmental transportation, Reverse logistics, Choice of suppliers by environmental criteria, Helping suppliers to establish their own EMS, Optimize internal process to minimize vehicle movement) are independent variables.4. ConclusionThis study concludes that green supply chain management encompasses potential to make cost saving in transportation. From production firm perspective, specially, main concerns of firms are continuously tracking, controlling and thinking how to manage their all kinds of cost, especially transportation cost.As mentioned in preceding sections, there is a relation as in formula mode between fuel consumption & maintenance, repairing expenditure (FCMRE) andtransportation cost. Because of the difficulties to collect and get the transportation cost data, model has fuel consumption & maintenance, repairing expenditure as a connection variable. This study proves the existing relation between GSCM and FCMRE. After proving this relation and using the relation between FCMRE and TCR, this study explains the impact of GSCM on transportation cost. Also, these research findings suggest that green their supply chains management affect not only fuel consumption, maintenance and repairing cost, but also through these variables affect transportation cost indirectly.绿色供应链管理对降低运输成本的影响摘要:供应链管理(SCM)已成为一种重要的竞争手段。
供应链简明相关专业英语词汇
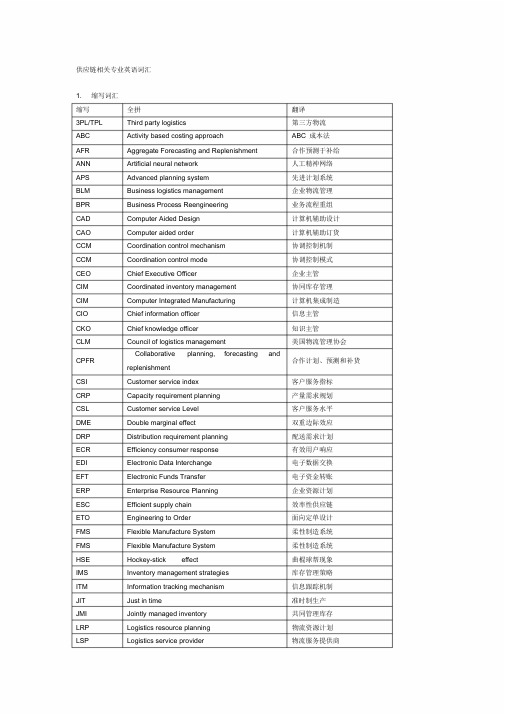
供应链相关专业英语词汇1. 缩写词汇缩写全拼翻译3PL/TPL Third party logistics 第三方物流ABC Activity based costing approach ABC 成本法AFR Aggregate Forecasting and Replenishment 合作预测于补给ANN Artificial neural network 人工精神网络APS Advanced planning system 先进计划系统BLM Business logistics management 企业物流管理BPR Business Process Reengineering 业务流程重组CAD Computer Aided Design 计算机辅助设计CAO Computer aided order 计算机辅助订货CCM Coordination control mechanism 协调控制机制CCM Coordination control mode 协调控制模式CEO Chief Executive Officer 企业主管CIM Coordinated inventory management 协同库存管理CIM Computer Integrated Manufacturing 计算机集成制造CIO Chief information officer 信息主管CKO Chief knowledge officer 知识主管CLM Council of logistics management 美国物流管理协会CPFRCollaborative planning, forecasting andreplenishment合作计划、预测和补货CSI Customer service index 客户服务指标CRP Capacity requirement planning 产量需求规划CSL Customer service Level 客户服务水平DME Double marginal effect 双重边际效应DRP Distribution requirement planning 配送需求计划ECR Efficiency consumer response 有效用户响应EDI Electronic Data Interchange 电子数据交换EFT Electronic Funds Transfer 电子资金转账ERP Enterprise Resource Planning 企业资源计划ESC Efficient supply chain 效率性供应链ETO Engineering to Order 面向定单设计FMS Flexible Manufacture System 柔性制造系统FMS Flexible Manufacture System 柔性制造系统HSE Hockey-stick effect 曲棍球帮现象IMS Inventory management strategies 库存管理策略ITM Information tracking mechanism 信息跟踪机制JIT Just in time 准时制生产JMI Jointly managed inventory 共同管理库存LRP Logistics resource planning 物流资源计划LSP Logistics service provider 物流服务提供商MIS Measuring index system 评价指标体系MPS master production scheduling 主生产排程MRP Material Requirement Planning 物料需求计划MRP ⅡManufacturing Resource Planning 制造资源计划MTO Make to order 按订单生产MTS Make to stock 备货生产NSM Negotiation selection method 协商选择法OEM Original equipment manufacturer 原始设备制造商POS Point of sale 销售终端QFD Quality function development 质量功能开发RSC Responsive supply chain 响应性供应链RSC Revenue sharing contracts 收益共享契约RCCP rough-cut capacity planning 粗能力计划SCC Supply chain coordination 供应链协调SCD Supply chain design 供应链设计SCM Supply chain management 供应链管理SCN Supply chain network 供应链网络SCP Supply chain planning 供应链计划SCP Supply chain partnership 供应链合作关系SFA Sales Forecast Accuracy 预测准确率SKU Stock Keeping Unit 库存进出计量的单位SI Sell in 销售进入渠道SO Sell out 销售给消费者SRM Supplier relationship management 供应商关系管理S&OP Sales and operation planning 销售运营计划TOC Theory of constraint 约束理论TPM Traditional purchase mode 传统采购模式TMS Transportation management system 运输管理系统VMI Vendor Managed Inventory 供应商管理库存WMAPE Weighted Mean Percentage Error 加权平均绝对百分比误差WMS Warehouse management system 仓储管理系统2. 非缩写核心词汇ABC classification ABC 分类Accessory 附件Action Report 行动报告Aggregate Planning .总体规划Agile Manufacturing 灵活制造Allocated Inventory 保留量Alternate BOM 替代物料表Anticipation Inventory 预期库存Assemble to Order 定单组装Automation 自动化Available Inventory 可用库存Available to Promise 可答应量Backlog 待交货Back Order 逾期订单Bill of Labor 人力表BOM Bill of Material 材料表bill of resources 资源表BOM Code 材料表码Bom Explosion 材料表展开Bom Implosion 材料表逆展Bom Structure 材科表结构Built-on-the-Iine parts 线上生产零件Bulk lssue 大批发料Bullwhip Effect 长鞭效应Business Plan 事业计划Capacity 产量Capacity Control 产量控制Capacity requirement planning 产量需求规划Check-in 结入Check-Out 结出Common part Bom 共享件材料表constraint management 限制因素管理continuous production 连续式生产critical capacity 关键产量critical part 关键零件customer order 客户定单customization 客制化customer service level 顾客服务水准cycle count interval 周期盘点区间cycle counting 周期盘点cycle time 周期时间Demand Management 需求管理demonstrated capacity 验证产量iscret manufacturing 装配式生产distribution center 配销中心distribution requirement planning 分销资源计划economic order quantity 经济订购量economic part period 经济量期emergency kanban 紧急看板finished goods 完成品firm planned order 固定计划定单first in first out 先进先出forecast 预测forecast horizon 预测期间fundamental data 基本资料gross requirement 总需求inbound queue control 输入端队列控制independent demand 独立需求input/output control 输入/输出控制intermittent production 问歇式生产inventory management 库存管理inventory status 库存状态inventory type 库存形态job 工件,工作job shop 工件生产工厂just in time 及时供补kanban 看板kanban ceiling 看板界限lead time 前置时间lead time offset 前置时问冲销least total cost 最低总成本批量法least unit cost 最低单位成本批量法level scheduling 平准化排程level production(linearity) 平准化生产linearity 定率生产load 负荷look ahead/look back 瞻前顾后法lot for lot 逐批批量法lot number 批号lot size 批量lot size inventory 批量库存lot sizing rule 批量法则maintenance, repair and operational supplies 间接物料make to order 定单生产make to stock 计划生产manufacturing bom 制造单元manufacturing cell 指令单manufacturing order 制造规划与控制manufacturing planning and control 制造资源规划master production scheduling 主生产排程material requirement planning 材料需求规划(计划)modular bom 模块材料表modular production 模块化生产mps item MPS 项目net requirement 净需求offset time 冲销时问on-hand inventory 在库量on-order inventory 在途量operations planning and control 作业规划与管制operations process chart 作业程序图order interval 订购区间order point 订购点parent/component 父件/子件pan number 件号past due 逾期量peg file 溯源文件pegging 溯源periodic order quantity 定期批量法periodic review system 定期评估法picking order 领料单plan-do-check-action cycle 计划一执行-检查-行动循环planned order receipts 计划定单收料planned order releases 计划定单发出planning bom 计划材料表planning horizon 计划期间planning time fence 计划时栅priority control 优先次序控制prioriry planning 优先次序规划preventive maintenance 预防性维护process manufacturing 流程式生产product family 产品族product line 产品线product structure 产品结构表product sub-line 产品副线production activity control 生产活动管制production rate 生产速率production plan 生产计划production planning 生产规划production run 生产连project-based production 项目式生产projected available balance 预计可用量pull system 拉式系统purchase order 订购单purchase reuisition 请购单quantity-per 单位用量quick response 快速反应rated capacity 评估产量raw material 原材料reasonableness test 合理测试receiving order 收料单refill kanban 补充看板re-order point 再订购点法repetitive manufacturing 重复性生产replacement part 替代件replenishment plan 补充计划replenishment time 补充时间resource requirement planning 资源需求规划rework kanban 重加工看板rolling kanban 滚动看板rolling schedule 滚动式排程rough-cut capacity planning 粗略产量规划safety stock 安全存量safety time 安全时间sales order 销售定单.scheduled receipts 在途量(已订未交货)scarp rate 报废率secondary stockroom 次级仓semi-finished goods 半成品serial number 序号shop calendar 厂历shop floor 制造现场shop floor control 制造现场控制stock keeping unit 材料库存单位subsontract order 外包单supply chain management 供应链管理synchronized control 同步控制synchronized production 同步生产theoretical capacity 理论产量Lime bucket 时段time phased order point 分期间订购点法transferring order 调拨单transportation inventory 运输库存total employee involvement 全员参与total preventive maintenance 全面预防型维护total productive maintenance 全面生产性维护total quality management 全面质量管理unit of measure 单位visual review system 目视评估法where-used report 用途表WIP inventory 在制品库存WIP tracking 在制品追踪work flow control system 工作流程控制系统work-in-process 在制品yield 良品率。
基于供应链的ABC分类管理

采购与供应管《u rc h a s e & S u p p ly基于供应链的A B C分类管理♦覃予摘要:以ABC分类法为基础,以产品模块化风险管理思想作参考,运用模糊集理论,建立 起充分考虑产品设计重要性、产品采购周期、产品价值因素等的物资ABC分类方法,对提升 库存管理水平,采购策略针对性以及加强现代物流结合性具有深刻的现实意义。
关键词:ABC分类法库存管理物料对于制造型企业而言,为满足客户需求,需对 产品进行细分,快速地对产品进行不断更迭。
产品 线的持续丰富虽然提高了企业的市场竞争能力,但是制造企业不得不增加采购原材料及外购件的宽 度,间接增加了库存压力,且大量库存资金的占用 增加了库存管理工作的难度。
如果缺乏科学的库存 物资管理手段,会降低库存周转率,浪费企业资 源,甚至会降低企业在所处环境的竞争力。
因此,提高制造企业的供应链库存管理水平对增强企业竞 争力具有重大的意义。
为适应现代化生产的需要,特别是迎合多品 种、小批量生产的环境,以ABC分类法为基础,参考产品模块化风险管理思想,运用模糊集理论,建立起充分考虑产品设计重要性、产品采购周期、产品价值因素等的物资ABC分类法。
该库存管理 方法利用模糊因子分析,将客观的数据参数化,建立一整套数据分析模型,制定相应的管理策略,从而使库存分类管理更加合理有效。
1传统A B C分类法U传统ABC分类法简介ABC分类法(Activity Based Classification,ABC)全称ABC分类库存控制法,是由意大利经 济学家维尔弗雷多•帕累托(VilfredoPareto)首创 的。
ABC分类法是储存管理中常用的分析方法,也是经济工作中的一种基本工作和认识方法。
1951年,管理学家戴克(H.F.Dickie)将其应 用于库存管理,命名为ABC法。
该分析方法的核 心思想是在影响一个事物的众多因素中分清主次,识别出少数的但对事物起决定性作用的关键因素 和多数的但对事物影响较少的次要因素。
供应链管理外文翻译文献
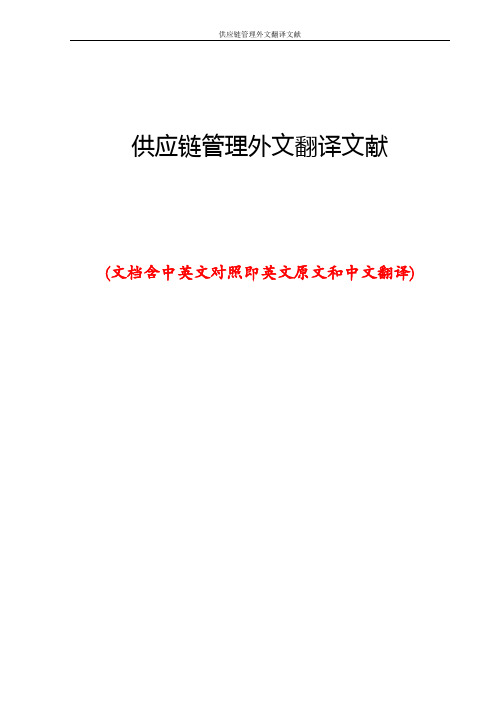
供应链管理外文翻译文献供应链管理外文翻译文献(文档含中英文对照即英文原文和中文翻译)Supply Chain ManagementThe so-called supply chain, in fact, from suppliers, manufacturers, warehouses, istribution centers and channels, and so constitute a logistics network. The same enterprise may constitute the different components of this network node, but the situation is different from a corporate network in different nodes. For example, in a supply chain, companies may not only in the same manufacturers, storage nodes, and in distribution centers, such as possession node location. In the more detailed division of labor, the higher the rofessional requirements of the supply chain, different nodes are basically composed by different enterprises. In the supply chain flows between the member units of raw materials, finished products, such as inventory and production constitutes the supply chain of goods flow.That is, to meet a certain level of customer service under the conditions, in order to make the whole supply chain to minimize costs and the suppliers, manufacturers, warehouses, distribution centers and channels, and so effectively organized together to carry out Product manufacturing, transport, distribution and sales management.From the above definition, we can be interpreted to include supply chain anagement of rich content.First of all, supply chain management products to meet customer demand in the process of the cost implications of various members of the unit are taken intoaccount, including from raw material suppliers, manufacturers to the warehouse distribution center to another channel. However, in practice in the supply chain analysis, it is necessary to consider the supplier's suppliers and customers of the customers, because their supply chain performance is also influential.Second, supply chain management is aimed at the pursuit of the whole supply chain's overall efficiency and cost effectiveness of the system as a whole, always trying to make the total system cost to a minimum. Therefore, the focus of supply chain management is not simply a supply chain so that members of the transportation costs to minimize or reduce inventory, but through the use of systems approach to coordinate the supply chain members so that the entire supply chain total cost of the minimum so that the whole supply chain System in the most fluent in the operation.Third, supply chain management is on the suppliers, manufacturers, warehouses, distribution centers and organically integrate the channel into one to start this problem, so many businesses, including its level of activities, including the strategic level, tactical and operational level Level, and so on.Although the actual logistics management, only through the organic supply chain integration, enterprises can significantly reduce costs and improve service levels, but in practice the supply chain integration is very difficult, it is because: First of all, in the supply chain There are different members of different and conflicting objectives. For example, providers generally want manufacturers to purchase large quantities of stable, and flexible delivery time can change; desire to the contrary with suppliers, although most manufacturers are willing toimplement long-term production operations, but they must take into account the needs of its customers and to make changes Positive response, which requires manufacturers choice and flexibility in procurement strategy. Therefore, suppliers and manufacturers to the goal of flexibility in the pursuit of the objectives inevitably exist between the contradictions.Secondly, the supply chain is a dynamic system, with time and constantly changing. In fact, customers not only demand and supply capacity to change over time, supply chain and the relationship between the members will change over time. For example, the increased purchasing power with customers, suppliers and manufacturers are facing greater pressure to produce more and more personalized varieties of high-quality products, then ultimately the production of customized products.Research shows that effective supply chain management can always make the supply chain of enterprises will be able to maintain stability and a lasting competitive advantage, thus increasing the overall supply chain competitiveness. Statistics show that, supply chain management will enable the effective implementation of enterprise total cost of about 20 per cent decline in the supply chain node on the enterprise-time delivery rate increased by 15 percent or more, orders to shorten the production cycle time 20 percent to 30 percent, supply chain Node on the enterprise value-added productivity increased by 15 percent or more. More and more enterprises have already recognized that the implementation of supply chain management of the great benefits, such as HP,IBM, DELL, such as supply chain management in the practice of the remarkable achievements made is proof.Supply chain management: it from a strategic level and grasp the overall perspective of the end-user demand, through effective cooperation between enterprises, access from the cost, time, efficiency, flexibility, and so the best results. From raw materials to end-users of all activities, the whole chain of process management.SCM (supply chain management) is to enable enterprises to better procurement of manufactured products and services required for raw materials, production of goods and services and their delivery to clients, the combination of art and science. Supply chain management, including the five basic elements.Plan: This is a strategic part of SCM. You need a strategy to manage all the resources to meet our customers for your products. Good plan is to build a series of methods to monitor the supply chain to enable it to effective, low-cost delivery of high quality for customers and high-value products or services.Procurement: you can choose the products and services to provide goods and services providers, and suppliers to establish a pricing, delivery and payment processes and create methods to monitor and improve the management, and the suppliers to provide goods and services Combined with management processes, including the delivery and verification of documentation, transfer of goods to your approval of the manufacturing sector and payments to suppliers and so on.Manufacturing: arrangements for the production, testing, packaged and ready for delivery, supply chain measurement is the largest part of the contents, including the level of quality, product yield and productivity of workers, such as the measurement.Delivery: a lot of "insider" as "logistics", is to adjust the user's orders receipts, the establishment of the storage network, sending and delivery service delivery personnel to the hands of customers, the establishment of commodity pricing system, receiving payments.Return: This is the supply chain problems in the handling part. Networking customers receive the refund of surplus and defective products, and customer applications to provide support for the problem.Source70 in the late 20th century, Keith Oliver adoption and Skf, Heineken, Hoechst, Cadbury-Schweppes, Philips, and other contact with customers in the process of gradually formed its own point of view. And in 1982, "Financial Times" magazine in an article on the supply chain management (SCM) of the significance, Keith Oliver was that the word will soon disappear, but "SCM" not only not disappeared, and quickly entered the public domain , The concept of the managers of procurement, logistics, operations, sales and marketing activities sense a great deal.EvolutionSupply chain has never been a universally accepted definition, supply chain management in the development process, many experts and scholars have putforth a lot of definition, reflecting the different historical backgrounds, in different stages of development of the product can be broadly defined by these For the three stages:1, the early view was that supply chain is manufacturing enterprises in an internal process2, but the supply chain concept of the attention of the links with other firms 3, the last of the supply chain concept of pay more attention around the core of the network links between enterprises, such as core business with suppliers, vendors and suppliers, and even before all the relations, and a user, after all the users and to the relationship.ApplySupply chain management involves four main areas: supply, production planning, logistics, demand. Functional areas including product engineering, product assurance, procurement, production control, inventory control, warehouse management, distribution management. Ancillary areas including customer service, manufacturing, design engineering, accounting, human resources, marketing.Supply Chain Management implementation steps: 1, analysis of market competition environment, identify market opportunities, 2, analysis of customer value, 3, identified competitive strategy, 4, the analysis of the core competitiveness of enterprises, 5, assessment, selection of partners For the supply chain partners of choice, can follow the following principles:1, partners must have available the core of their competitiveness.2, enterprises have the same values and strategic thinking3, partners must Fewer but Better.CaseAs China's largest IT distributor, Digital China in China's supply chain management fields in the first place. In the IT distribution model generally questioned the circumstances, still maintained a good momentum of development, and CISCO, SUN, AMD, NEC, IBM, and other famous international brands to maintain good relations of cooperation. e-Bridge trading system in September 2000 opening, as at the end of March 2003, and 6.4 billion yuan in transaction volume. In fact, this is the Digital China from the traditional distribution supply chain services to best reflect the changes. In the "distribution of services is a" concept, Digital China through the implementation of change channels, expansion of product and service operations, increasing its supply chain in the value of scale and specialized operations, to meet customer demand on the lower reaches of the In the course of the supply chain system can provide more value-added services, with more and more "IT services" color.供应链管理所谓供应链,其实就是由供应商、制造商、仓库、配送中心和渠道商等构成的物流网络。
供应链管理中库存管理ABC策略方法详解
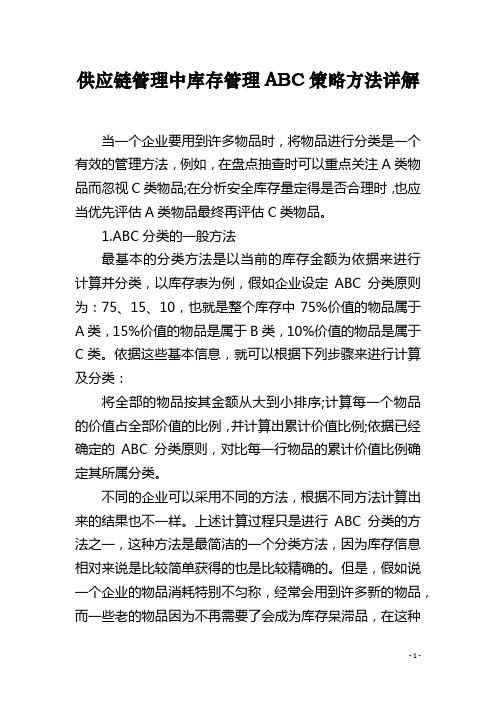
状况下,用库存结存额来作为 ABC 分类计算的依据就显得 不太合适,那么我们可以采另一种方式。下面我们对几个不 同的方法进行分析:
以前面一段时间内的消耗金额作为计算依据。 这种方法不是以库存物品的结余价值作为计算依据,而 是以前一段时间实际消耗的物品价值作为计算依据。假设这 里所说的“前面一段时间”是指“上一个月”,那么计算过 程如下:将全部物品按当月发出金额(当月发出量 X 当月结 存价格)从大到小排序;从头开头计算每一个物品的价值占全 部价值的比例,并计算出累计价值比例;依据已经确定的 ABC 分类原则,对比每一行物品的累计价值比例确定其所属分类。 上述二种计算方法所产生的结果差异很大,例如某物品 若以库存结存金额来计算,属于 C 类物品,而根据前一段时 间的实际消耗金额来计算,却变成了 A 类物品。 以今后一段时间内的需要消耗金额作为计算依据。 这种方法不是看现在库存状况怎样,也不是看过去消耗 的状况怎样,而是关注今后的需求如何。计算方法:以物品 今后一段时间需要消耗的金额(当月结余价格 X 今后一段时 间内需要消耗的数量)为计算依据,然后依据各项物品所占金 额比例来确定其 ABC 分类。 2.企业在做 ABC 分类时要留意什么? 以上列出了几个计算 ABC 分类的方法,不同方法会导 致不同的结果,这是正常的也是正确的。制造企业的状况各 不相同,管理的需求也不尽相同。有些企业关注根据过去的
ABC 分类是一个策略,其关键点就是用 ABC 来表示不
-4-
同物品的不同重要性,以便企业更有针对性地进行管理。
-5-
-2-
消耗信息来动,在不同的状况,企业可以确定最合适自己的 ABC 计算方法。同时,企业在做 ABC 分类时要留意以下几 点:
ABC 分类的各自比例如何划分? 有些企业把 ABC 的比例定为:80、15、5,也有企业定 为:70、20、10。我们说比例只是一个“标尺”,是要依据 需求和目标而定的。甚至也有企业不单单是划分了 ABC 三 类,而使用了 ABCD 四类,这些都是可以的。所谓 ABC 分 类,只是供应了一种方法,并不局限于只有 ABC 三类。 ABC 分类时的关键分类依据是什么? 计算依据是可以依据企业实际状况而设计的,不是单一 的,也不是一成不变的。假如一个企业既要把当前库存金额 考虑进去,也要把今后的需求状况考虑进去,那么还可以采 用“加权计算”的方法,最终目的是使 ABC 分类的结果真 正表达了企业的实际状况,满意企业管理的需求。 ABC 分类的有效期限如何确定? 企业在每天的运行过程中,会不断地产生各种信息并足 以影响到 ABC 的分类结果,如库存收发存的数据一直在发 生变化,计划需求信息也在不断发生变化,我们可以这么说: 在任何时候去重新运行 ABC 分类的计算过程,产生的分类 结果一定和上一次是不同的,在这种状况下,我们就需要使 ABC 分类保持适当的稳定,要确定重新计算的周期。 3.ABC 分类的作用
供应链管理外文翻译

供应链管理外文翻译Supply Chn ManagementIntroduction Supply chn management (SCM) is the strategic and operational management of the series of processes involved in moving a product or service from concept to final consumption. It includes the coordination and integration of supply, demand, raw materials, production, distribution, and最终 consumption. The goal of SCM is to create a seamless flow of information, materials, and finances from suppliers to customers, increasing efficiency, reducing costs, and improving service. Key Concepts1、Supply Chain: The series of businesses and organizations that are involved in the production and delivery of a product or service, including suppliers, manufacturers, warehouses, transportation companies, and retailers.2、Demand Management: The process of forecasting and managing customer demand to ensure that supply meets demand. This involves analyzing sales data, market research, and communication with customers to understand their needs.3、Logistics Management: The coordination and management of the transportation, storage, and inventory of goods from suppliers to customers. Logistics management aims to optimize transportation costs, reduce inventory, and ensure on-time delivery.4、Procurement Management: The process of purchasing the raw materials, components, and services required for production. It involves developing relationships with suppliers, negotiating prices, and ensuring quality and delivery.5、Information Management: The process of collecting, sharing, and using information throughout the supply chain. This includes the flow of orders, shipments, payments, and product information between businesses.6、Collaboration: The cooperation and communication between supply chain partners to achieve shared goals. This requires open communication, trust, and the sharing of data and resources.7、Continuous Improvement: The practice of constantly seeking to improve processes, reduce waste, and increase efficiency. It requires regular analysis of supply chain performance dataand the implementation of effective changes based on identified opportunities for improvement.Benefits SCM can provide significant benefits to businesses and their customers:1、Improved Efficiency: By optimizing supply chain processes and removing bottlenecks, SCM can increase operational efficiency and reduce costs.2、Enhanced Customer Satisfaction: SCM ensures that products are delivered promptly, accurately, and to the desired quality standards, resulting in satisfied customers.3、Increased Flexibility: SCM allows businesses to quickly adapt to changes in market conditions, customer demand, and supply.4、Reduced Risk: SCM improves the visibility and manageability of supply chain operations, which helps businesses identify and address potential risks before they become problems.5、Enhanced Competitiveness: Effective SCM can help businesses reduce costs, improve delivery times, and provide better quality products, which can provide a competitive advantage inthe market.Conclusion Supply chn management is critical for businesses today as it involves the entire process of moving products or services from concept to final consumption. By optimizing supply chn processes, improving collaboration, and continuously seeking improvement, businesses can achieve increased efficiency, customer satisfaction, flexibility, reduced risk, and enhanced competitiveness. Therefore, effective SCM is essential for businesses to remn competitive in today's rapidly changing global marketplace.。
供应链综合管理外文文献

A supply chain consists of all parties involved, directly or indirectly, in fulfilling a customer request. The supply chain includes not only the manufacturer and suppliers, but also transporters, warehouses, retailers, and even customers themselves. Within each organization, such as a manufacturer, the supply chain includes all functions involved in receiving and filling a customer request. These functions include, but are not limited to, new product, development, marketing, operations, distribution, finance, and customer service.Consider a customer walking into a Wal-Mart store to purchase detergent. The supply chain begins with the customer and his or her need for detergent. The next stage of this supply chain is the Wal-Mart retail store that the customer visits. Wal-Mart stocks its shelves using inventory that may have been supplied from a finished-goodswarehouse or a distributor using trucks supplied by a third party. The distributor in turn is stocked by the manufacturer (say, Procter &Gamble [P&G] in this case). The P&G manufacturing plant receives raw material from a variety of suppliers, who may themselves have been supplied by lower-tier suppliers. For example, packaging material may come from Pactiv Corporation (formerly Tenneco Packaging) while Pactiv receives raw materials to manufacture the packaging from other suppliers. This supply chain is illustrated in Figure 1—1, with the arrows corresponding to the direction of physical product flow.A supply chain is dynamic and involves the constant flow of information, product, and funds between different stages. In our example, Wal-Mart provides the product, as well as pricing and availability information, to the customer. The customer transfers funds to Wal-Mart. Wal-Mart conveys point-of-sales data as well as replenishment orders to the warehouse or distributor, who transfers the replenishmentorder via trucks back to the store. Wal-Mart transfers funds to the distributor after the replenishment. The distributor also provides pricing information and sends delivery schedules to Wal-Mart. Wal-Mart may send back packaging material to be recycled. Similar information, material, and fund flows take place across the entire supply chain.In another example, when a customer makes a purchase online from Dell Computer, the supply chain includes, among others, the customer, Dell's Web site, the Dell assembly plant, and all of Dell's suppliers and their suppliers. The Web site provides the customer with information regarding pricing, product variety, and product availability. Having made a product choice, the customer enters the order information and pays for the product. The customer may later return to the Web site to check the status of the order. Stages further up the supply chain use customer order information to fill the request. That process involves an additional flow of information, product, and funds among various stages of the supply chain.These examples illustrate that the customer is an integral part of the supply chain. In fact, the primary purpose of any supply chain is to satisfy customer needs and, in the process, generate profit for itself. The term supply chain conjures up images of product or supply moving from suppliers to manufacturers to distributors to retailers to customers along a chain. This is certainly part of the supply chain, but it is also important to visualize information, funds, and product flows along both directions of this chain. The term supply chain may also imply that only one player is involved at each stage. In reality, a manufacturer may receive material from several suppliers and then supply several distributors. Thus, most supply chains are actually networks. It may be more accurate to use the term supply network or supply web to describe the structure of most supply chains, as shown in Figure 1-2.A typical supply chain may involve a variety of stages, including the following: Customers, Retailers, Wholesalers/distributors, Manufacturers, Component/raw material suppliersEach stage in a supply chain is connected through the flow of products, information, and funds. These flows often occur in both directions and may be managed by one of the stages or an intermediary.Each stage in Figure 1-2 need not be present in a supply chain. As discussed in Chapter 4, the appropriate design of the supply chain depends on both the customer's needs and the roles played by the stages involved. For example, Dell has two supply chain structures that it uses to serve its customers.For its corporate clients and also some individuals who want a customized personal computer (PC), Dell builds to order; that is, a customer order initiates manufacturing at Dell. For these customers, Dell does not have a separate retailer, distributor, or wholesaler in the supply chain. Since , Dell has also sold its PCs through Wal-Mart in the United States and the GOME Group, China's largest electronics retailer. Both Wal-Mart and the GOME Group carry Dell machines in inventory. This supply chain thus contains an extra stage (the retailer) compared to the direct sales model also used by Dell.In the case of other retail stores, the supply chain may also contain a wholesaler or distributor between the store and the manufacturer.The objective of every supply chain should be to maximize the overall value generated. The value (also known as supply chain surplus) a supply chain generates is the difference between what the value of the final product is to the customer and the costs the supply chain incurs in filling the customer's request.Supply Chain Surplus=Customer Value-Supply Chain CostThe value of the final product may vary for each customer and can be estimated by the maximum amount the customer is willing to pay for it. The difference between the value of the product and its price remains with the customer as consumer surplus. The rest of the supply chain surplus becomes supply chain profitability, the difference between the revenue generated from the customer and the overall cost across the supply chain. For example, a customer purchasing a wireless muter from Best Buy pays $60, which represents the revenue the supply chain receives. Customers who purchase the muter clearly value it at or above $60. Thus, part of the supply chain surplus is left with the customer as consumer surplus. The rest stays with the supply chain as profit. Best Buy and other stages of the supply chain incur costs to convey information, produce components, store them, transport them, transfer funds, and so on. The difference between the $60 that the customer paid and the sum of all costs incurred by the supply chain to produce and distribute the muter represents the supply chain profitability.Supply chain profitability is the total profit to be shared across all supply chain stages and intermediaries. The higher the supply chain profitability, the more successful is the supply chain.For most profit-making supply chains, the supply chain surplus will be strongly correlated with profits. Supply chain success should be measured in terms of supply chain profitability and not in terms of the profits at an individual stage. (In subsequent chapters, we see that a focus on profitability at individual stages may lead to a reduction in overall supply chain profits.)A focus on growing the supply chain surplus pushes all members of the supply chain toward growing the size of the overall pie.Having defined the success of a supply chain in terms of supply chainprofitability, the next logical step is to look for sources of value, revenue, and cost. For any supply chain, there is only one source of revenue: the customer. The value obtained by a customer purchasing detergent at Wal-Mart depends upon several factors, including the functionality of the detergent, how far the customer has to travel to Wal-Mart, and the likelihood of finding the detergent in stock. The customer is the only one providing positive cash flow for the Wal-Mart supply chain. All other cash flows are simply fund exchanges that occur within the supply chain, given that different stages have different owners. When Wal-Mart pays its supplier, it is taking a portion of the funds the customer provides and passing that money on to the supplier. All flows of information, product, or funds generate costs within the supply chain. Thus, the appropriate management of these flows is a key to supply chain success. Effective supply chain management involves the management of supply chain assets and product, information, and fund flows to maximize total supply chain surplus. A growth in supply chain surplus increases the size of the total pie, allowing contributing members of the supply chain to benefit.In this book, we have a strong focus on analyzing all supply chain decisions in terms of their impact on the supply chain surplus. These decisions and their impact can vary for a wide variety of reasons. For instance, consider the difference in the supply chain structure for fast-moving consumer goods observed in the United States and India. U.S. distributors play a much smaller role in this supply chain compared to their Indian counterparts. We argue that the difference in supply chain structure can be explained by the impact a distributor has on the supply chain surplus in the two countries.Retailing in the United States is largely consolidated, with large chains buying consumer goods from most manufacturers. This consolidation gives retailerssufficient scale that the introduction of an intermediary such as a distributor does little to reduce costs and may actually increase costs because of an additional transaction. In contrast, India has millions of small retail outlets. The small size of Indian retail outlets limits the amount of inventory they can hold, thus requiring frequent replenishment-an order can be compared with the weekly grocery shopping for a family in the United States. The only way for a manufacturer to keep transportation costs low is to bring full truckloads of product close to the market and then distribute locally using "milk runs" with smaller vehicles. The presence of an intermediary who can receive a full truckload shipment, break bulk, and then make smaller deliveries to the retailers is crucial if transportation costs are to be kept low. Most Indian distributors are one-stop shops, stocking everything from cooking oil to soaps and detergents made by a variety of manufacturers. Besides the convenience provided by one-stop shopping, distributors in India are also able to reduce transportation costs for outbound delivery to the retailer by aggregating products across multiple manufacturers during the delivery runs. Distributors in India also handle collections, because their cost of collection is significantly lower than that of each manufacturer collecting from retailers on its own would be. Thus, the important role of distributors in India can be explained by the growth in supply chain surplus that results from their presence. The supply chain surplus argument implies that as retailing in India begins to consolidate, the role of distributors will diminish.There is a close connection between the design and management of supply chain flows (product, information, and funds) and the success of a supply chain. Wal-Mart, Amazon, and Seven-Eleven Japan are examples of companies that have built their success on superior design, planning, and operation of their supply chain. In contrast, the failure of many online businesses such as Webvan can be attributed to weaknessesin their supply chain design and planning. The rise and subsequent fall of the bookstore chain Borders illustrates how a failure to adapt its supply chain to a changing environment and customer expectations hurt its performance. Dell Computer is another example of a company that had to revise its supply chain design in response to changing technology and customer needs. We discuss these examples later in this section.Wal-Mart has been a leader at using supply chain design, planning, and operation to achieve success. From its beginning, the company invested heavily in transportation and information infrastructure to facilitate the effective flow of goods and information. Wal-Mart designed its supply chain with clusters of stores around distribution centers to facilitate frequent replenishment at its retail stores in a cost-effective manner. Frequent replenishment allows stores to match supply and demand more effectively than the competition. Wal-Mart has been a leader in sharing information and collaborating with suppliers to bring down costs and improve product availability. The results are impressive. In its annual report, the company reported a net income of more than $14.3 billion on revenues of about $408 billion. These are dramatic results for a company that reached annual sales of only $1 billion in 1980. The growth in sales represents an annual compounded growth rate of more than 20 percent.。
供应链相关专业英语词汇
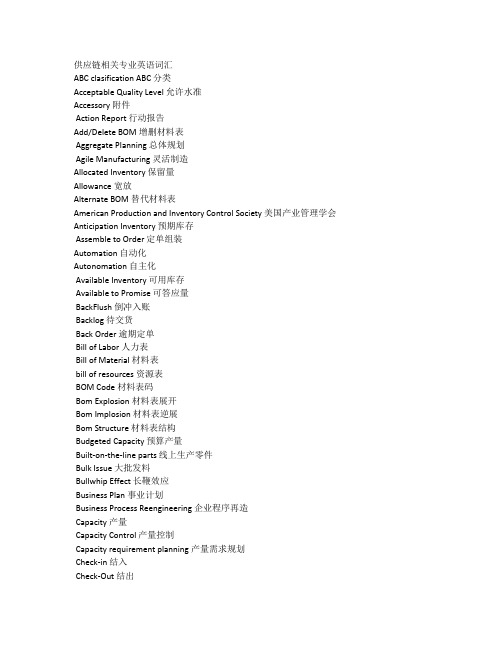
供应链相关专业英语词汇ABC clasification ABC 分类Acceptable Quality Level 允许水准Accessory 附件Action Report 行动报告Add/Delete BOM 增删材料表Aggregate Planning 总体规划Agile Manufacturing 灵活制造Allocated Inventory 保留量Allowance 宽放Alternate BOM 替代材料表American Production and Inventory Control Society 美国产业管理学会Anticipation Inventory 预期库存Assemble to Order 定单组装Automation 自动化Autonomation 自主化Available Inventory 可用库存Available to Promise 可答应量BackFlush 倒冲入账Backlog 待交货Back Order 逾期定单Bill of Labor 人力表Bill of Material 材料表bill of resources 资源表BOM Code 材料表码Bom Explosion 材料表展开Bom Implosion 材料表逆展Bom Structure 材料表结构Budgeted Capacity 预算产量Built-on-the-line parts 线上生产零件Bulk Issue 大批发料Bullwhip Effect 长鞭效应Business Plan 事业计划Business Process Reengineering 企业程序再造Capacity 产量Capacity Control 产量控制Capacity requirement planning 产量需求规划Check-in 结入Check-Out 结出Client/ Server Architecture 主从式架构Common part Bom 共享件材料表Computer aided design system 计算机辅助设计系统connected flow 相连材料流consolidated freight 合并货运constraint management 限制因素管理continuous improvement 连续改善continuous production 连续式生产critical capacity 关键产量critical part 关键零件customer order 客户定单customization 客制化customer service level 顾客服务水准cycle count interval 周期盘点区间cycle counting 周期盘点cycle time 周期时间customer relationship management 客户关系管理data flow diagram 数据流程图de-coupling stock 反耦合库存Demand Management 需求管理Demand Rate 需求速率Demand time fence 需求时栅demonstrated capacity 验证产量dependent demand 依赖需求diagnostic test 诊断测试disconnected flow 分离材料流iscret manufacturing 装配式生产distribution center 配销中心distribution requirement planning 配销需求规划drum-buffer-rope control DBR 管制法earliest start date 最早开工日economic order quantity 经济订购量economic part period 经济量期elimination,combination,rearrangement,simplification ECRS 改善法 emergency kanban 紧急看板employee empowerment 员工授权employee involvement 员工参与end user computing 使用者自建系统engineering to order 定单设计engineering change 设计变更engineering product structure 工程用产品结构表 exception report 企业资料规划enterprise resource planning 例外报告executive information system 主管信息系统existence test 存在测试expeditor 催料人员final assembly schedule 最终组装排程finished goods 完成品firm planned order 固定计划定单first in first out 先进先出fixed order quantity 定量批量法flow shop 流程生产工厂forecast 预测forecast horizon 预测期间fundamental data 基本资料gateway workstation 投料工作站graphic user interface 图形接口gross requirement 总需求group technology 群组技术hedge inventory 避险库存inbound queue control 输入端队列控制independent demand 独立需求input/output control 输入/输出控制intermittent production 间歇式生产inventory management 库存管理inventory status 库存状态inventory sub-type 库存副型态inventory type 库存型态item 材料(项目)item master 材料主档job 工件,工作job shop 工件生产工厂joint operation 联合作业just in time 及时供补kanban 看板kanban ceiling 看板界限latest start date 最晚开工日lead time 前置时间lead time offset 前置时间冲销least total cost 最低总成本批量法least unit cost 最低单位成本批量法level scheduling 平准化排程level production(linearity) 平准化生产linearity 定率生产load 负荷look ahead/look back 瞻前顾后法lot for lot 逐批批量法lot number 批号lot size 批量lot size inventory 批量库存lot sizing rule 批量法则low-level code 最低阶码maintenance, repair and operational supplies 间接物料make to order 定单生产make to stock 计划生产managerial product structure 管理用产品结构表manufacturing bom 制造单元manufacturing cell 制令单manufacturing order 制造规划与控制manufacturing planning and control 制造资源规划master production scheduling 主生产排程master scheduler 主生产排程员material service sheduling 主服务排程material handling 材料搬运material requirement planning 材料需求规划(计划) mean absolute deviation 平均绝对差modular bom 模块材料表modular production 模块化生产mps item MPS 项目mrp crusades MRP 改革运动mrp nervousness MRP 不安定性multilevel mps 多阶主生产排程net change 净变法net requirement 净需求offset time 冲销时间one less at a time 一次减一点on-hand inventory 在库量on-order inventory 在途量open system platform 开放系统平台operations planning and control 作业规划与管制operations process chart 作业程序图option 选用件optional bom 选用材料件order interval 订购区间order point 订购点original equipment manuafacturer 原设备制造商outbound queue control 输出端队列控制overflow stockroom 溢量仓parent/component 父件/子件part number 件号part periodic balancing 量期平衡批量法past due 逾期量peg file 溯源文件pegging 溯源period length 期长periodic order quantity 定期批量法periodic review system 定期评估法phantom 幽灵材料phantom bom 幽灵材料表phantom component 幽灵子件picking order 领料单pipeline stock 管路库存plan-do-check-action cycle 计划-执行-检查-行动循环planned order receipts 计划定单收料planned order releases 计划定单发出planning bom 计划材料表planning horizon 计划期间planning time fence 计划时栅point of use 使用点primary stockroom 基本仓priority control 优先次序控制priority planning 优先次序规划preventive maintenance 预防性维护process flow chart 制程流程图process manufacturing 流程式生产product configuration system 产品构造系统product family 产品族product line 产品线product load profile 产品负荷表product structure 产品结构表product sub-line 产品副线production activity control 生产活动管制production rate 生产速率production plan 生产计划production planning 生产规划production run 生产连project-based production 项目式生产projected available balance 预计可用量projected on-hand 预计在库量pseuo bom 假材料表pull signal 拉式讯号pull system 拉式系统purchase order 订购单purchase reuisition 请购单quantity-per 单位用量quick response 快速反应rated capacity 评估产量raw material 原材料reasonableness test 合理测试receiving order 收料单refill kanban 补充看板regeneration 再生法re-order point 再订购点法repetitive manufacturing 重复性生产replacement part 替代件replenishment plan 补充计划replenishment time 补充时间resource profile 资源负荷表resource requirement planning 资源需求规划rework kanban 重加工看板rolling kanban 滚动看板rolling schedule 滚动式排程rough-cut capacity planning 粗略产量规划route 途程routing 途程表safety stock 安全存量safety time 安全时间safety order 销售定单scheduled receipts 在途量(已订未交量)scarp rate 报废率secondary stockroom 次级仓semi-finished goods 半成品serial number 序号setup 准备作业shop calendar 厂历shop floor 制造现场shop floor control 制造现场控制shop order 制令单significant numbering 显义编号standard coefficient 标准系数stock keeping unit 材料库存单位subsontract order 外包单super bom 超材料单supply chain management 供应链管理synchronized control 同步控制synchronized production 同步生产theoretical capacity 理论产量theory of constraints 限制理论three tier architecture 三层式架构throughtput 产出率time bucket 时段time phased order point 分期间订购点法transferring order 调拨单transportation inventory 运输库存total employee involvement 全员参与total preventive maintenance 全面预防性维护total productive maintenance 全面生产性维护total quality management 全面质量管理two bin system 双箱法two level mps 双阶主生产排程unit of measure 单位visual review system 目视评估法where-used report 用途表 WIP inventory 在制品库存 WIP tracking 在制品追踪work flow control system 工作流程控制系统 work-in-process 在制品 yield 良品率。
供应链管理ABC_外文原文
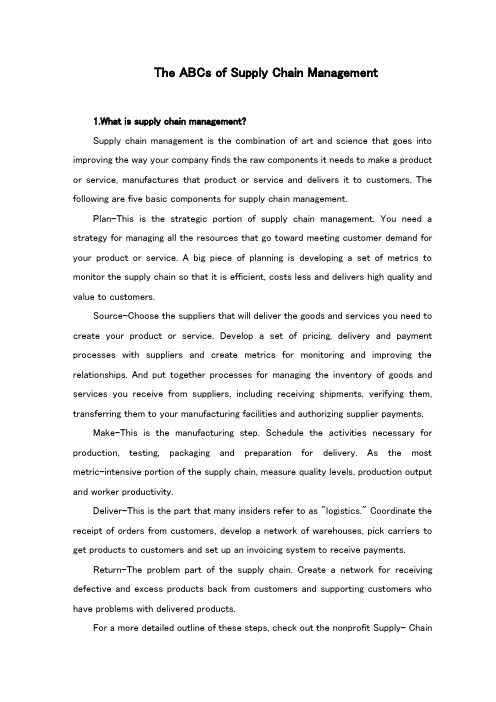
The ABCs of Supply Chain Management1.What is supply chain management?Supply chain management is the combination of art and science that goes into improving the way your company finds the raw components it needs to make a product or service, manufactures that product or service and delivers it to customers. The following are five basic components for supply chain management.Plan-This is the strategic portion of supply chain management. You need a strategy for managing all the resources that go toward meeting customer demand for your product or service. A big piece of planning is developing a set of metrics to monitor the supply chain so that it is efficient, costs less and delivers high quality and value to customers.Source-Choose the suppliers that will deliver the goods and services you need to create your product or service. Develop a set of pricing, delivery and payment processes with suppliers and create metrics for monitoring and improving the relationships. And put together processes for managing the inventory of goods and services you receive from suppliers, including receiving shipments, verifying them, transferring them to your manufacturing facilities and authorizing supplier payments.Make-This is the manufacturing step. Schedule the activities necessary for production, testing, packaging and preparation for delivery. As the most metric-intensive portion of the supply chain, measure quality levels, production output and worker productivity.Deliver-This is the part that many insiders refer to as "logistics." Coordinate the receipt of orders from customers, develop a network of warehouses, pick carriers to get products to customers and set up an invoicing system to receive payments.Return-The problem part of the supply chain. Create a network for receiving defective and excess products back from customers and supporting customers who have problems with delivered products.For a more detailed outline of these steps, check out the nonprofit Supply- ChainCouncil's website at.2.What does supply chain management software do?Supply chain management software is possibly the most fractured group of software applications on the planet. Each of the five major supply chain steps previously outlined composes dozens of specific tasks, many of which have their own specific software. There are some large vendors that have attempted to assemble many of these different chunks of software together under a single roof, but no one has a complete package. Integrating the different software pieces together can be a nightmare. Perhaps the best way to think about supply chain software is to separate it into software that helps you plan the supply chain and software that helps you execute the supply chain steps themselves.Supply chain planning (SCP) software uses fancy math algorithms to help you improve the flow and efficiency of the supply chain and reduce inventory. SCP is entirely dependent upon information for its accuracy. If you're a manufacturer of consumer packaged goods for example, don't expect your planning applications to be very accurate if you can't feed them accurate, up-to-date information about customer orders from your retail customers, sales data from your retailer customers' stores, manufacturing capacity and delivery capability. There are planning applications available for all five of the major supply chain steps previously listed. Arguably the most valuable (and complex and prone to error) is demand planning, which determines how much product you will make to satisfy your different customers' demands.Supply chain execution (SCE) software is intended to automate the different steps of the supply chain. This could be as simple as electronically routing orders from your manufacturing plants to your suppliers for the stuff you need to make your products.For an expanded overview of this topic, read the Supply Chain Executive Summary.3.Do I need to have ERP software before I install supply chain software?This is a very controversial subject. You may need ERP if you plan to install SCP applications because they are reliant upon the kind of information that is stored in themost quantity inside ERP software. Theoretically you could assemble the information you need to feed the SCP applications from legacy systems (for most companies this means Excel spreadsheets spread out all over the place), but it can be nightmarish to try to get that information flowing on a fast, reliable basis from all the areas of the company. ERP is the battering ram that integrates all that information together in a single application, and SCP applications benefit from having a single major source to go to for up-to-date information. Most CIOs who have tried to install SCP applications say they are glad they did ERP first. They call the ERP projects "putting your information house in order." Of course, ERP is expensive and difficult, so you may want to explore ways to feed your SCP applications the information they need without doing ERP first.SCE applications are less dependent upon gathering information from around the company, so they tend to be independent of the ERP decision. But chances are, you'll need to have the SCE applications communicate with ERP in some fashion. It's important to pay attention to SCE software's ability to integrate with the Internet and with ERP or SCP applications because the Internet will drive demand for integrated information. For example, if you want to build a private website for communicating with your customers and suppliers, you will want to pull information from SCE, SCP and ERP applications together to present updated information about orders, payments, manufacturing status and delivery.4.What is the goal of installing supply chain management software?Before the Internet came along, the aspirations of supply chain software devotees were limited to improving their ability to predict demand from customers and make their own supply chains run more smoothly. But the cheap, ubiquitous nature of the Internet, along with its simple, universally accepted communication standards have thrown things wide open. Now, theoretically anyway, you can connect your supply chain with the supply chains of your suppliers and customers together in a single vast network that optimizes costs and opportunities for everyone involved. This was the reason for the B2B explosion; the idea that everyone you do business with could be connected together into one big happy, cooperative family.Of course, the reality behind this vision is that it will take years to come to fruition. But considering that B2B has only been around for a few years, some industries have already made great progress, most notably consumer-packaged goods (the companies that make products that go to supermarkets and drug stores), high technology and autos.When you ask the people on the front lines in these industries what they hope to gain from their supply chain efforts in the near term, they will all respond with a single word: visibility. The supply chain in most industries is like a big card game. The players don't want to show their cards because they don't trust anyone else with the information. But if they showed their hands they could all benefit. Suppliers wouldn't have to guess how much raw materials to order, and manufacturers wouldn't have to order more than they need from suppliers to make sure they have enough on hand if demand for their products unexpectedly goes up. And retailers would have fewer empty shelves if they shared the information they had about sales of a manufacturer's product in all their stores with the manufacturer. The Internet makes showing your hand to others possible, but centuries of distrust and lack of coordination within industries make it difficult.5.What is supply chain collaboration?Let's look at consumer packaged goods as an example of collaboration. If there are two companies that have made supply chain a household word, they are Wal-Mart and Procter & Gamble. Before these two companies started collaborating back in the '80s, retailers shared very little information with manufacturers. But then the two giants built a software system that hooked P&G up to Wal-Mart's distribution centers. When P&G's products run low at the distribution centers, the system sends an automatic alert to P&G to ship more products. In some cases, the system goes all the way to the individual Wal-Mart store. It lets P&G monitor the shelves through real-time satellite link-ups that send messages to the factory whenever a P&G item swoops past a scanner at the register.With this kind of minute-to-minute information, P&G knows when to make, ship and display more products at the Wal-Mart stores. No need to keep products piled up inwarehouses awaiting Wal-Mart's call. Invoicing and payments happen automatically too. The system saves P&G so much in time, reduced inventory and lower order-processing costs that it can afford to give Wal-Mart "low, everyday prices" without putting itself out of business.Cisco Systems, which makes equipment to hook up to the Internet, is also famous for its supply chain collaboration. Cisco has a network of component suppliers, distributors and contract manufacturers that are linked through Cisco's extranet to form a virtual, just-in-time supply chain. When a customer orders a typical Cisco product-for example, a router that directs Internet traffic over a company network-through Cisco's website, the order triggers a flurry of messages to contract manufacturers of printed circuit board assemblies. Distributors, meanwhile, are alerted to supply the generic components of the router, such as a power supply. Cisco's contract manufacturers, some of whom make subassemblies like the router chassis and others who assemble the finished product, already know what's coming down the order pipe because they've logged on to Cisco's extranet and linked in to Cisco's own manufacturing execution systems.Soon after the contract manufacturers reach into Cisco's extranet, the extranet starts poking around the contractor's assembly line to make sure everything is kosher. Factory assemblers slap a bar code on the router, scan it and plug in cables that simulate those of a typical corporate network. One of those cables is a fire hose for Cisco's automated testing software. It looks up the bar code, matches it to a customer's order and then probes the nascent router to see if it has all the ports and memory that the customer wanted. If everything checks out-and only then-Cisco's software releases the customer name and shipping information so that the subcontractor can get it off the shop floor.And there you have it. No warehouses, no inventory, no paper invoices, just a very nosy software program that monitors Cisco's supply chain automatically, in real-time, everywhere, simultaneously. The chain runs itself until there's a problem, in which case the system alerts some poor human to get off his duff and fix something. Supply chain software junkies call this "management by exception." You don't need to do anythingunless there is something wrong..If there's a weakness to these collaborative systems, it's that they haven't been tested in tough times-until recently. Cisco's network was designed to handle the company's huge growth. Distributed decision making is great if the decisions have mostly to do with making and selling more things. But Cisco and its network were caught completely off guard by the recent tumble in the economy. It took awhile to turn all the spigots off in its complex network when demand for its products plummeted and Cisco and its supply chain partners got stuck with a lot of excess inventory-as did most other big manufacturers in high technology. Cisco was forced to take a hard look at its supply chain planning capability. SCP software is much better at managing growth than it is at monitoring a decline and correcting it.6.What are the roadblocks to installing supply chain software?Gaining trust from your suppliers and partners. Supply chain automation is uniquely difficult because its complexity extends beyond your company's walls. Your people will need to change the way they work and so will the people from each supplier that you add to your network. Only the largest and most powerful manufacturers can force such radical changes down suppliers' throats. Most companies have to sell outsiders on the system. Moreover, your goals in installing the system may be threatening to those suppliers, to say the least. For example, Wal-Mart's collaboration with P&G meant that P&G would assume more responsibility for inventory management, something retailers have traditionally done on their own. Wal-Mart had the clout to demand this from P&G, but it also gave P&G something in return-better information about Wal-Mart's product demand, which helped P&G manufacture its products more efficiently. To get your supply chain partners to agree to collaborate with you, you have to be willing to compromise and help them achieve their own goals.Internal resistance to change. If selling supply chain systems is difficult on the outside, it isn't much easier inside. Operations people are accustomed to dealing with phone calls, faxes and hunches scrawled on paper, and will most likely want to keep it that way. If you can't convince people that using the software will be worth their time, they will easily find ways to work around it. You cannot disconnect the telephones andfax machines just because you have supply chain software in place.Many mistakes at first. There is a diabolical twist to the quest for supply chain software acceptance among your employees. New supply chain systems process data as they are programmed to do, but the technology cannot absorb a company's history and processes in the first few months after an implementation. Forecasters and planners need to understand that the first bits of information they get from a system might need some twea king. If they are not warned about the system's initial naiveté, they will think it is useless. In one case, just before a large automotive industry supplier installed a new supply chain forecasting application to predict demand for a product, an automaker put in an order for an unusually large number of units. The system responded by predicting huge demand for the product based largely on one unusual order. Blindly following the system's numbers could have led to inaccurate orders for materials being sent to suppliers within the chain. The company caught the problem but only after a demand forecaster threw out the system's numbers and used his own.That created another problem: Forecasters stopped trusting the system and worked strictly with their own data. The supplier had to fine-tune the system itself, then work on reestablishing employees' confidence. Once employees understood that they would be merging their expertise with the system's increasing accuracy, they began to accept and use the new technology.7.Many B2B exchanges say they offer supply chain software. Should I use their software or install my own?Public (many-to-many) B2B exchanges and private (you to everyone else in your supply chain) exchanges began with grand promises of auctions and procurement savings for members, but few suppliers were tempted. Since then, most of these websites have morphed into becoming online hosts for supply chain software. For small companies that can't afford to buy the software on their own, the public exchanges will probably be their source. But for now many of the offerings are immature and aren't getting much use. Companies that can afford to are building their own private connections with their trading partners online rather than going through public exchanges. But even these companies will eventually use the public exchanges whenthey can. Building and maintaining software just isn't a great deal if there's someone out there willing to do it for you.The ambitious public exchanges, with their independence and neutrality, hold out the hope of attracting more buyers and suppliers together in one place, but the level of specificity of a public exchange's supply chain software will probably never reach the depth that a company could build with a select few suppliers in a private exchange. So most decision makers are saying they will use public exchanges for the generic supply chain connections they make, and build their own for the really strategic deep, supply chain relationships they have.。
供应链管理外文翻译
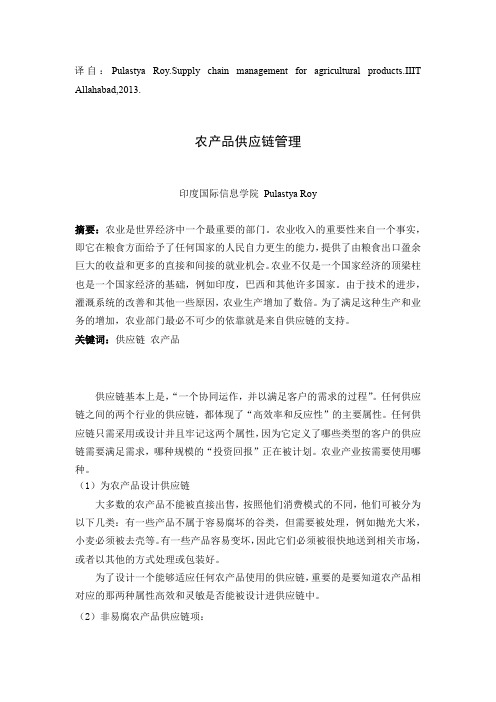
译自:Pulastya Roy.Supply chain management for agricultural products.IIIT Allahabad,2013.农产品供应链管理印度国际信息学院Pulastya Roy摘要:农业是世界经济中一个最重要的部门。
农业收入的重要性来自一个事实,即它在粮食方面给予了任何国家的人民自力更生的能力,提供了由粮食出口盈余巨大的收益和更多的直接和间接的就业机会。
农业不仅是一个国家经济的顶梁柱也是一个国家经济的基础,例如印度,巴西和其他许多国家。
由于技术的进步,灌溉系统的改善和其他一些原因,农业生产增加了数倍。
为了满足这种生产和业务的增加,农业部门最必不可少的依靠就是来自供应链的支持。
关键词:供应链农产品供应链基本上是,“一个协同运作,并以满足客户的需求的过程”。
任何供应链之间的两个行业的供应链,都体现了“高效率和反应性”的主要属性。
任何供应链只需采用或设计并且牢记这两个属性,因为它定义了哪些类型的客户的供应链需要满足需求,哪种规模的“投资回报”正在被计划。
农业产业按需要使用哪种。
(1)为农产品设计供应链大多数的农产品不能被直接出售,按照他们消费模式的不同,他们可被分为以下几类:有一些产品不属于容易腐坏的谷类,但需要被处理,例如抛光大米,小麦必须被去壳等。
有一些产品容易变坏,因此它们必须被很快地送到相关市场,或者以其他的方式处理或包装好。
为了设计一个能够适应任何农产品使用的供应链,重要的是要知道农产品相对应的那两种属性高效和灵敏是否能被设计进供应链中。
(2)非易腐农产品供应链项:几乎所有的洋葱,谷物如小麦,水稻,玉米等,和一些蔬菜如马铃薯,大葱等是高度无差别的需求,而且它们不易变坏,所以对这类农产品供应链相比响应性更应注重效率和成本效益。
这些农产品的供应与市场需求联系起来就显得尤为重要。
谷物在它们从地里收获后需要一些加工和抛光的过程,供应链就从这里开始发挥作用。
供应链管理外文翻译文献
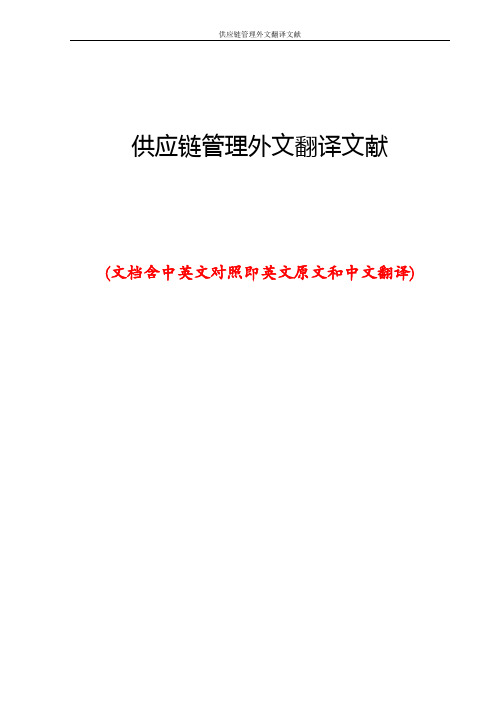
供应链管理外文翻译文献供应链管理外文翻译文献(文档含中英文对照即英文原文和中文翻译)Supply Chain ManagementThe so-called supply chain, in fact, from suppliers, manufacturers, warehouses, istribution centers and channels, and so constitute a logistics network. The same enterprise may constitute the different components of this network node, but the situation is different from a corporate network in different nodes. For example, in a supply chain, companies may not only in the same manufacturers, storage nodes, and in distribution centers, such as possession node location. In the more detailed division of labor, the higher the rofessional requirements of the supply chain, different nodes are basically composed by different enterprises. In the supply chain flows between the member units of raw materials, finished products, such as inventory and production constitutes the supply chain of goods flow.That is, to meet a certain level of customer service under the conditions, in order to make the whole supply chain to minimize costs and the suppliers, manufacturers, warehouses, distribution centers and channels, and so effectively organized together to carry out Product manufacturing, transport, distribution and sales management.From the above definition, we can be interpreted to include supply chain anagement of rich content.First of all, supply chain management products to meet customer demand in the process of the cost implications of various members of the unit are taken intoaccount, including from raw material suppliers, manufacturers to the warehouse distribution center to another channel. However, in practice in the supply chain analysis, it is necessary to consider the supplier's suppliers and customers of the customers, because their supply chain performance is also influential.Second, supply chain management is aimed at the pursuit of the whole supply chain's overall efficiency and cost effectiveness of the system as a whole, always trying to make the total system cost to a minimum. Therefore, the focus of supply chain management is not simply a supply chain so that members of the transportation costs to minimize or reduce inventory, but through the use of systems approach to coordinate the supply chain members so that the entire supply chain total cost of the minimum so that the whole supply chain System in the most fluent in the operation.Third, supply chain management is on the suppliers, manufacturers, warehouses, distribution centers and organically integrate the channel into one to start this problem, so many businesses, including its level of activities, including the strategic level, tactical and operational level Level, and so on.Although the actual logistics management, only through the organic supply chain integration, enterprises can significantly reduce costs and improve service levels, but in practice the supply chain integration is very difficult, it is because: First of all, in the supply chain There are different members of different and conflicting objectives. For example, providers generally want manufacturers to purchase large quantities of stable, and flexible delivery time can change; desire to the contrary with suppliers, although most manufacturers are willing toimplement long-term production operations, but they must take into account the needs of its customers and to make changes Positive response, which requires manufacturers choice and flexibility in procurement strategy. Therefore, suppliers and manufacturers to the goal of flexibility in the pursuit of the objectives inevitably exist between the contradictions.Secondly, the supply chain is a dynamic system, with time and constantly changing. In fact, customers not only demand and supply capacity to change over time, supply chain and the relationship between the members will change over time. For example, the increased purchasing power with customers, suppliers and manufacturers are facing greater pressure to produce more and more personalized varieties of high-quality products, then ultimately the production of customized products.Research shows that effective supply chain management can always make the supply chain of enterprises will be able to maintain stability and a lasting competitive advantage, thus increasing the overall supply chain competitiveness. Statistics show that, supply chain management will enable the effective implementation of enterprise total cost of about 20 per cent decline in the supply chain node on the enterprise-time delivery rate increased by 15 percent or more, orders to shorten the production cycle time 20 percent to 30 percent, supply chain Node on the enterprise value-added productivity increased by 15 percent or more. More and more enterprises have already recognized that the implementation of supply chain management of the great benefits, such as HP,IBM, DELL, such as supply chain management in the practice of the remarkable achievements made is proof.Supply chain management: it from a strategic level and grasp the overall perspective of the end-user demand, through effective cooperation between enterprises, access from the cost, time, efficiency, flexibility, and so the best results. From raw materials to end-users of all activities, the whole chain of process management.SCM (supply chain management) is to enable enterprises to better procurement of manufactured products and services required for raw materials, production of goods and services and their delivery to clients, the combination of art and science. Supply chain management, including the five basic elements.Plan: This is a strategic part of SCM. You need a strategy to manage all the resources to meet our customers for your products. Good plan is to build a series of methods to monitor the supply chain to enable it to effective, low-cost delivery of high quality for customers and high-value products or services.Procurement: you can choose the products and services to provide goods and services providers, and suppliers to establish a pricing, delivery and payment processes and create methods to monitor and improve the management, and the suppliers to provide goods and services Combined with management processes, including the delivery and verification of documentation, transfer of goods to your approval of the manufacturing sector and payments to suppliers and so on.Manufacturing: arrangements for the production, testing, packaged and ready for delivery, supply chain measurement is the largest part of the contents, including the level of quality, product yield and productivity of workers, such as the measurement.Delivery: a lot of "insider" as "logistics", is to adjust the user's orders receipts, the establishment of the storage network, sending and delivery service delivery personnel to the hands of customers, the establishment of commodity pricing system, receiving payments.Return: This is the supply chain problems in the handling part. Networking customers receive the refund of surplus and defective products, and customer applications to provide support for the problem.Source70 in the late 20th century, Keith Oliver adoption and Skf, Heineken, Hoechst, Cadbury-Schweppes, Philips, and other contact with customers in the process of gradually formed its own point of view. And in 1982, "Financial Times" magazine in an article on the supply chain management (SCM) of the significance, Keith Oliver was that the word will soon disappear, but "SCM" not only not disappeared, and quickly entered the public domain , The concept of the managers of procurement, logistics, operations, sales and marketing activities sense a great deal.EvolutionSupply chain has never been a universally accepted definition, supply chain management in the development process, many experts and scholars have putforth a lot of definition, reflecting the different historical backgrounds, in different stages of development of the product can be broadly defined by these For the three stages:1, the early view was that supply chain is manufacturing enterprises in an internal process2, but the supply chain concept of the attention of the links with other firms 3, the last of the supply chain concept of pay more attention around the core of the network links between enterprises, such as core business with suppliers, vendors and suppliers, and even before all the relations, and a user, after all the users and to the relationship.ApplySupply chain management involves four main areas: supply, production planning, logistics, demand. Functional areas including product engineering, product assurance, procurement, production control, inventory control, warehouse management, distribution management. Ancillary areas including customer service, manufacturing, design engineering, accounting, human resources, marketing.Supply Chain Management implementation steps: 1, analysis of market competition environment, identify market opportunities, 2, analysis of customer value, 3, identified competitive strategy, 4, the analysis of the core competitiveness of enterprises, 5, assessment, selection of partners For the supply chain partners of choice, can follow the following principles:1, partners must have available the core of their competitiveness.2, enterprises have the same values and strategic thinking3, partners must Fewer but Better.CaseAs China's largest IT distributor, Digital China in China's supply chain management fields in the first place. In the IT distribution model generally questioned the circumstances, still maintained a good momentum of development, and CISCO, SUN, AMD, NEC, IBM, and other famous international brands to maintain good relations of cooperation. e-Bridge trading system in September 2000 opening, as at the end of March 2003, and 6.4 billion yuan in transaction volume. In fact, this is the Digital China from the traditional distribution supply chain services to best reflect the changes. In the "distribution of services is a" concept, Digital China through the implementation of change channels, expansion of product and service operations, increasing its supply chain in the value of scale and specialized operations, to meet customer demand on the lower reaches of the In the course of the supply chain system can provide more value-added services, with more and more "IT services" color.供应链管理所谓供应链,其实就是由供应商、制造商、仓库、配送中心和渠道商等构成的物流网络。
供应链管理方法外文文献翻译2023年译文3565字

供应链管理方法外文文献翻译2023年译文3565字供应链管理方法外文文献翻译(2023年译文,3565字)引言供应链管理在现代商业环境中起着至关重要的作用。
通过优化物流、协调供应商和客户之间的合作关系,供应链管理可以提高企业的效率和竞争力。
本文翻译来自外文文献,介绍了一些供应链管理方法的应用和实践。
主要方法1. 跨功能协调:供应链管理强调不同职能部门之间的协同合作。
通过加强内部沟通和协作,企业可以更好地满足客户需求,并提高整体供应链的效率。
2. 供应商管理:合理管理供应商关系对于供应链管理至关重要。
通过建立长期合作关系、进行供应商绩效评估以及共享信息,企业可以更好地掌控供应链的可靠性和稳定性。
3. 库存管理:有效的库存管理能够保持供应链的平衡,避免过量库存或库存短缺的问题。
通过采用合理的预测方法和库存控制技术,企业可以最大程度地降低库存成本,并确保及时供应。
4. 运输优化:优化物流网络和运输计划是供应链管理的关键步骤。
通过分析运输成本、提高货物追踪能力以及优化配送路线,企业可以降低物流成本并提高交付效率。
5. 技术应用:现代技术的应用为供应链管理提供了许多机会。
例如,物联网技术可以实现供应链的实时监控和数据分析,以便更好地进行决策和优化。
结论供应链管理方法的应用对于企业的成功至关重要。
本文介绍了一些常见的供应链管理方法,包括跨功能协调、供应商管理、库存管理、运输优化和技术应用。
通过综合运用这些方法,企业可以提高自身效率和竞争力,并实现可持续的业务增长。
- 1、下载文档前请自行甄别文档内容的完整性,平台不提供额外的编辑、内容补充、找答案等附加服务。
- 2、"仅部分预览"的文档,不可在线预览部分如存在完整性等问题,可反馈申请退款(可完整预览的文档不适用该条件!)。
- 3、如文档侵犯您的权益,请联系客服反馈,我们会尽快为您处理(人工客服工作时间:9:00-18:30)。
毕业设计(论文)外文资料翻译外文出处:The ABCs of Supply Chain (用外文写)Management附件:1.外文资料翻译译文;2.外文原文。
附件1:外文资料翻译译文供应链管理ABC1.什么是供应链管理供应链是一种关于整合的科学和艺术,它主要探究提高企业采购生产商品所需的原材料、生产商品,并把它供应给最终顾客的效率的途径。
以下是供应链管理的五个基本组成模块:计划--它是供应链的战略层面。
企业需要有一个控制所有资源的战略以满足客户对产品或服务的需求。
计划的核心是建立一套机制去监控整条供应链以便使它能有效运作:低成本、高品质配送和增值客户服务。
该模块连结着供应链的作业与营运目标,主要包括需求/供给规划(Demand/Supply Planning)与规划基础建设(infrastructure)两项活动,对所有采购运筹流程、制造运筹流程与配送运筹流程进行规划与控制。
需求/供给规划活动包含了评估企业整体产能与资源、总体需求规划以及针对产品与配销管道,进行存货规划、配送规划、制造规划、物料及产能的规划。
规划基础建设管理包含了自制或外包决策的制定、供应链的架构设计、长期产能与资源规划、企业规划、产品生命周期的决定、新旧产品线规划与产品线的管理等。
采购—选择供给你提供用来生产产品或服务的原材料或服务的供应商。
和供应商建立一套价格、供应、支付过程的体系,创造一种机制以监控此过程、改善供应商关系。
理顺此过程以管理供应商交付的原材料库存或服务,其中包括收货、出货、检验、中转和批准支付。
此模块有采购作业与采购基础建设两项管理活动,其目的是描述一般的采购作业与采购管理流程。
采购作业包含了寻找供货商、收料、进料品检、拒收与发料作业。
采购基础建设的管理包含了供货商评估、采购、运输管理、采购品质管理、采购合约管理、付款条件管理、采购零组件的规格制定。
制造—这是制造步骤。
计划这些必需的活动:生产、测试、包装、预出货。
作为供应链的核心机制,它意味着质量水平、产品输出和工厂产能的有效控制。
此模块具有制造执行作业与制造基础建设两项管理活动,其目的是描述制造生产作业与生产的管理流程。
制造执行作业包含了领料、产品制造、产品测试与包装出货等。
制造基础建设的管理包含了工程变更、生产状况掌握、生产品质管理、现场排程制定、短期产能规划与现场设备管理等。
配送—许多权威人士都把它归咎为物流的一部分。
它包括客户下达的订单,建立仓库网络,选择承运商,分发货物给客户,建立收款制度等。
本模块包含订单管理、仓储管理、运输管理与配送基础建设等四项管理活动,其目的是描述销售(sales)与配送(distribution)的一般作业与管理流程。
订单管理作业包含了接单、报价、顾客资料维护、订单分配、产品价格资料维护、应收账款维护、授信与开立发票等流程。
仓储管理作业包含了拣料、按包装明细将产品包装入柜、确认交货地点与运送货物等流程。
运输管理作业包含产品运输方式安排、进出口管理、货品安装适宜规划、进行安装与产品试行(例如,销售大型机器给顾客,须先帮忙安装完毕,然后进行试车)。
配送基础建设的管理包括配送管道的决策制定、配送存货管理、配送品质的掌握与销售管理法的制定。
回收—供应链的难题之一。
这需要创建一个网络以接收那些客户返回的缺陷产品或过剩产品,支持对接收到的货物产生质疑的客户。
以退回的货物的属性分,包括:不良品、间接物料(MRO)、过剩成品。
以退货作业的对象分,包括:顾客对供货商、供货商对顾客。
以对于退货响应方式包括:核准作业、退货排程、退换作业、销毁作业。
2.供应链管理软件功能供应链管理软件可能是这个星球上最分散的应用软件。
以前五个主要的供应链模块中的每一个都是涵盖了至少一打不同的作业,这些作业又都有他们各自独特的软件来支持。
因此有一些大的软件供应商尝试将这些不同的软件模块整合在一个平台之上,但是由于种种因素没有一家供应商能有一个完整的软件包,整合这些不同的软件模块已成为他们的噩梦。
或许建置供应链软件最好的途径是把他们拆分开:帮助企业计划供应链的软件和帮助企业执行供应链的软件。
供应链计划(SCP)软件使用独特的数学算法来帮助企业减少存货,提高供应链运作效率。
供应链计划软件完全依靠精确的数据来运行。
例如,一个制造厂商,如果不能提供最新的客户订单信息、分销商的库存信息、工厂制造能力信息、配送能力给供应链计划软件,就不要期望供应链计划软件能跑出精确的你所期望的结果。
供应链计划软件适用于先前提到的供应链的五个主要模块,他的核心在于需求计划--企业能生产多少产品来满足不同的客户需求。
供应链执行(SCE)软件的功能是使供应链的不同步骤自动化。
它通过信息排程的方式将订单从生产工厂传递给原材料供应商。
3.在安装供应链管理软件之前是否需要有企业资源计划软件这是一个非常有争议的问题。
一般的,如果企业计划安装供应链计划软件,那么企业可能首先要有企业资源计划软件,因为供应链计划软件依赖各种信息才能良好的运转,而这些信息大部分在企业资源计划软件中都已经存在。
理论上你可以从企业历史遗留下来的系统(对于大多数企业来说,EXCEL表在各种不同的地方都有使用)中收集供应链计划软件所需的各种数据,但是要快速、可靠的从企业的各个部门搜集其所有所需的信息简直就是一场恶梦。
然而企业资源计划软件就是一个整合所有信息的有效工具。
如果企业已经建置了企业资源计划软件,供应链计划软件就有了一个单一稳定的数据源。
许多准备安装供应链计划软件的CIO声称他们会首先安装企业资源计划软件,他们称企业资源计划项目为“建立舒适的信息储藏室”。
当然,建立企业资源计划系统花费昂贵并且非常困难,因此如果没有首先安装企业资源计划软件那就需要一条为供应链计划软件提供所需数据的方法。
供应链执行软件较少的依靠来自企业的各种集成信息,因此受企业资源计划软件的约束较少。
但是在另一方面,供应链执行软件必须能通过不同的方式与企业资源计划软件进行数据交换。
现在供应链执行软件与互联网、企业资源计划软件、供应链计划软件的数据交互能力显得尤为重要。
举个例子,企业想建立一个联接客户和供应商的WEB站点,就必须从SCE,SCP和ERP中提取最新的有关订单、结算、制造状况、配送等数据。
4.安装供应链管理软件的目标在互联网时代到来之前,人们对供应链软件的期望被局限在提高企业预测客户需求的能力和保证供应链更平稳的运行上。
但是随着互联网的普及,它事实上已成为公认的网际时代数据交换的标准方式。
现在,理论上企业可以将自己的供应链与客户和供应商的供应链连结在一起,形成一个单一的、巨大的供应网络,进而优化成本、发现机会:这在以前对每个企业来说都是非常棘手的。
这也是B2B兴起的重要原因:每一个与你发生商业行为的团体都能被连结在一起,形成一个合作互赢的大团体。
当然,这些技术能够带来效益还需要一段时间。
但是鉴于B2B只是经过了短短几年,在一些行业的应用已经取得了显著的进步,像快速消费品行业、高科技制造业、汽车制造业。
当你问及那些行业的领先者,他们期望在未来从供应链中得到什么,他们所有的回答只有一个词:可见性。
多数行业的供应链就像一场大的扑克牌游戏:玩家不会展示他的牌因为他不相信其他的任何游戏参与者,尽管如果他展示他手中的牌他肯定会受益。
所以供应商得去猜测有多少原材料会被订购。
制造商得去从供应商那里订购超过需求的原材料以确保如果有不确定的客户需求的到来。
零售商几乎没有缺货,如果他肯让制造商分享相关产品的销售信息。
互联网使企业展示手中的信息给其他企业成为可能,但是千百年来的不信任和缺乏平等机制使他变得非常困难。
5.什么是供应链协同让我们看一个快速消费品行业的协同案例:沃尔马(Wal-Mart)和宝洁(Procter & Gamble)的供应链协同。
在上世纪八十年代两家公司开始建立供应链协同机制之前,零售商很少与制造商分享信息。
但是两个巨人开发了一套软件系统用以联接宝洁和沃尔马的配送中心,当在沃尔马配送中心的宝洁产品库存下降到一定水平时,这个系统会发出一个自动的警报给宝洁,从而执行一个补货的动作。
这个信息系统至始至终联接着沃尔马的所有商店,它让宝洁可以监控沃尔马货架上宝洁产品存量的变化。
当宝洁的某个品项存货发生突然下降时,可以通过实时的卫星链路将信息发送回工厂。
依靠这些实时的信息,宝洁知道应该什么时候生产、出货,在沃尔马的商店里陈列多少产品,不需要位置堆积如山的库存来保证对沃尔马的供货,并且结算和发票处理业实现了自动化。
这个系统帮助宝洁实现了时间的节约、库存的降低和低的订单处理成本,从而也实现了沃尔马“天天低价”的目标。
思科系统(Cisco Systems),一家互联网设备供应商,也因为它的供应链协同而出名。
思科通过连接供应商、集成商、契约制造商的增值网构筑了一个虚拟的JIT(just-in-time)供应链。
当一个客户订购了思科的产品时,比如说客户直接通过思科的WEB站点订购了一台路由器,这个订单将会触发一大堆信息给集成电路板的契约制造商。
同时,集成商也得到路由器的加工信息:比如说为路由器安装一个供电电源。
思科的契约制造商有一些是从事路由器基座之类的零部件生产,还有一些是组装成品,他们已经知道都应该为这台路由器安装哪些零件,安装工序是什么,因为他们已经通过思科的增值网连接着思科的制造执行系统。
契约制造商进入思科的增值网后,增值网会开始检查契约制造商的生产线,确认哪条是合适于生产路由器的。
生产厂会粘贴一个条码给路由器,插进电线以模拟检测它对各种不同网络化境的适应。
完成之后对比它是否与客户订单符合。
如果这些都检查没有问题,然后就要写入思科的软件系统,最后就可以出货给客户。
思科依靠这个强大的软件程序来无论何时何地都可以监控整个供应链,并且不再有仓库、存货、纸质发票。
供应链可以自动运行,如果有问题出现,软件会发出警报给管理人员来解决问题,修补错误。
供应链软件管理员称之为“例外管理”,如果没有错误发生就不需要做什么事情。
如果说这个供应链协同软件有什么弱点,就是说他们没有得到充分的检验,特别是在现在。
思科的网络被设计成用来支持企业的快速增长。
分布式的制造决策是非常好用的,如果决策能处理制造和销售过程中的大部分事情。
但是思科的网络对于近来的经济波动几乎完全没有办法适应。
当客户对思科产品的需求飞速下降时,它要花费大量的时间来调整所有的流程以适应复杂的供应链,思科和它的供应链伙伴也会受到大量过程库存的欺骗,这也是大型高科技制造企业的通病。
思科被迫更加关注它的供应链计划能力。
6.安装供应链软件的障碍得到你的供应商和合作伙伴的信任。
自动化供应链之所以难以实现是因为它的复杂性已经超出了单个企业所能控制的范围。
企业员工需要改变工作方式,并且也需要把供应商的员工纳入自己的网络。