熔模铸造浇注系统计算
浇注系统的设计与计算
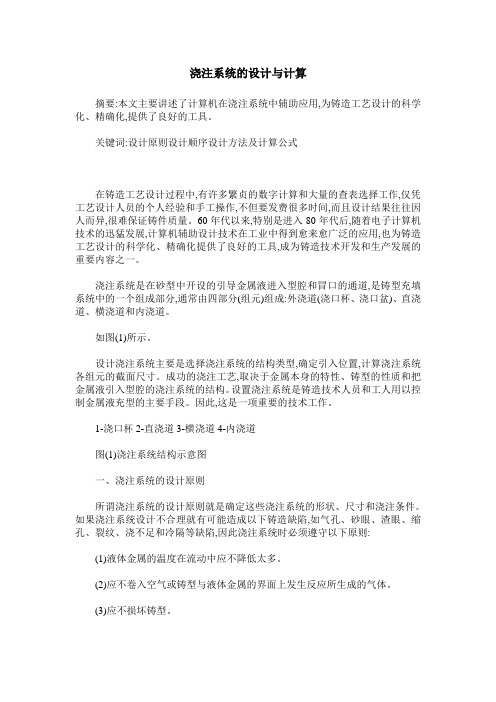
浇注系统的设计与计算摘要:本文主要讲述了计算机在浇注系统中辅助应用,为铸造工艺设计的科学化、精确化,提供了良好的工具。
关键词:设计原则设计顺序设计方法及计算公式在铸造工艺设计过程中,有许多繁贞的数字计算和大量的查表选择工作,仅凭工艺设计人员的个人经验和手工操作,不但要发费很多时间,而且设计结果往往因人而异,很难保证铸件质量。
60年代以来,特别是进入80年代后,随着电子计算机技术的迅猛发展,计算机辅助设计技术在工业中得到愈来愈广泛的应用,也为铸造工艺设计的科学化、精确化提供了良好的工具,成为铸造技术开发和生产发展的重要内容之一。
浇注系统是在砂型中开设的引导金属液进入型腔和冒口的通道,是铸型充填系统中的一个组成部分,通常由四部分(组元)组成:外浇道(浇口杯、浇口盆)、直浇道、横浇道和内浇道。
如图(1)所示。
设计浇注系统主要是选择浇注系统的结构类型,确定引入位置,计算浇注系统各组元的截面尺寸。
成功的浇注工艺,取决于金属本身的特性、铸型的性质和把金属液引入型腔的浇注系统的结构。
设置浇注系统是铸造技术人员和工人用以控制金属液充型的主要手段。
因此,这是一项重要的技术工作。
1-浇口杯2-直浇道3-横浇道4-内浇道图(1)浇注系统结构示意图一、浇注系统的设计原则所谓浇注系统的设计原则就是确定这些浇注系统的形状、尺寸和浇注条件。
如果浇注系统设计不合理就有可能造成以下铸造缺陷,如气孔、砂眼、渣眼、缩孔、裂纹、浇不足和冷隔等缺陷,因此浇注系统时必须遵守以下原则:(1)液体金属的温度在流动中应不降低太多。
(2)应不卷入空气或铸型与液体金属的界面上发生反应所生成的气体。
(3)应不损坏铸型。
(4)应防止掉砂和熔渣流入型腔。
(5)应防止液体金属过度加热铸型。
(6)应有助于方向性凝固。
(7)应不降低工艺出口率(型腔体积对包括浇注系统在内的整铸型型腔体积之比)。
(8)凝固以后应该容易去除。
二、浇注系统设计顺序不同的铸造方法、工厂、技术人员可能采用不同的浇注系统设计方法。
熔模铸造浇注系统计算
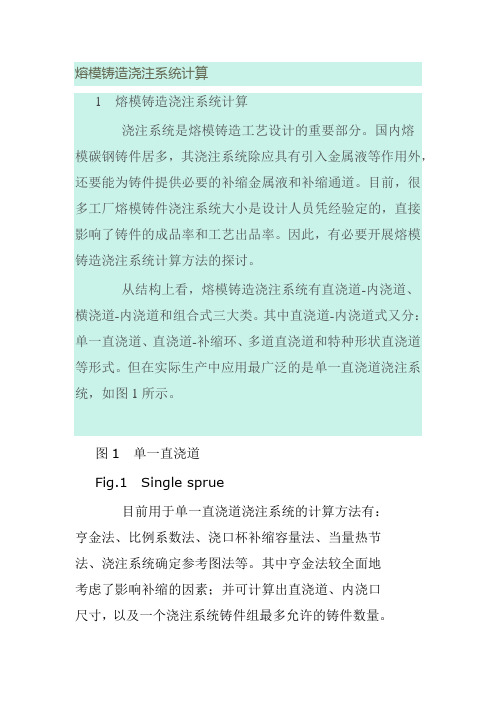
熔模铸造浇注系统计算1熔模铸造浇注系统计算浇注系统是熔模铸造工艺设计的重要部分。
国内熔模碳钢铸件居多,其浇注系统除应具有引入金属液等作用外,还要能为铸件提供必要的补缩金属液和补缩通道。
目前,很多工厂熔模铸件浇注系统大小是设计人员凭经验定的,直接影响了铸件的成品率和工艺出品率。
因此,有必要开展熔模铸造浇注系统计算方法的探讨。
从结构上看,熔模铸造浇注系统有直浇道-内浇道、横浇道-内浇道和组合式三大类。
其中直浇道-内浇道式又分:单一直浇道、直浇道-补缩环、多道直浇道和特种形状直浇道等形式。
但在实际生产中应用最广泛的是单一直浇道浇注系统,如图1所示。
图1单一直浇道Fig.1Single sprue目前用于单一直浇道浇注系统的计算方法有:亨金法、比例系数法、浇口杯补缩容量法、当量热节法、浇注系统确定参考图法等。
其中亨金法较全面地考虑了影响补缩的因素;并可计算出直浇道、内浇口尺寸,以及一个浇注系统铸件组最多允许的铸件数量。
据介绍亨金法更适用于该类浇注系统。
本文就单一直浇道浇注系统计算开展研究。
利用计算机对第一拖拉机股份有限公司(简称洛阳拖拉机厂)、东风汽车公司精密铸造厂(简称第二汽车制造厂)大量工艺已成熟零件的浇注系统与亨金法计算结果相比较,并对亨金法进行修正。
该修正公式可供各工厂技术人员在设计浇注系统时参考。
2亨金法简介为使铸件获得补缩,内浇口应设在铸件厚处(热节处),以保证在金属液凝固时,内浇口比铸件厚处晚凝固,而直浇道又比内浇口晚冷,从而利用直浇道中金属液补缩铸件。
因此,内浇口截面的热模数Mg(mm)是铸件热节处的热模数Mc(mm)、直浇道截面的热模数Ms(mm)、单个铸件质量Q(g)和内浇口长度Lg(mm)的函数,即Mg=f(Mc,Q,Lg,Ms)(1)前苏联学者亨金用不同铸件做试验,把公式(1)中各参数关系绘成曲线后发现,它们之间的关系为各种不同方次的抛物线关系,最后归纳得到下列公式:(2)式中Kh——比例系数,中碳钢Kh≈2。
熔模铸造余量计算公式

熔模铸造余量计算公式熔模铸造是一种常见的金属铸造方法,它采用熔融金属注入熔模中,通过冷却凝固形成所需的铸件。
在熔模铸造过程中,需要考虑余量的计算,以确保最终铸件的尺寸和形状符合设计要求。
余量计算是熔模铸造中非常重要的一环,它直接影响到最终产品的质量和精度。
余量是指在设计铸件模型时,为了弥补熔模收缩和加工后的尺寸偏差而预留的一定尺寸。
余量的计算需要考虑多个因素,包括熔模收缩率、材料特性、工艺参数等。
下面将介绍熔模铸造余量计算的公式及其相关内容。
1. 熔模收缩率。
熔模收缩率是指熔模在凝固冷却过程中所发生的线性收缩率。
不同的金属材料和熔模材料具有不同的收缩率,因此在计算余量时需要考虑具体的收缩率数值。
通常情况下,熔模收缩率可以通过实验测定或查阅相关资料获得。
2. 铸件尺寸。
铸件的尺寸是余量计算的基础,需要根据设计图纸或实际需求确定。
铸件的尺寸包括长度、宽度、厚度等多个方面,每个方面都需要考虑熔模收缩率和余量的影响。
3. 余量计算公式。
余量计算的基本公式为:余量 = 铸件尺寸×熔模收缩率。
在实际应用中,余量计算还需要考虑到熔模的形变、材料的变化等因素,因此公式可能会有所调整。
一般来说,余量计算公式可以根据具体情况进行调整和修正,以确保最终的余量能够满足实际需求。
4. 余量计算的影响因素。
余量计算的准确性直接影响到最终铸件的质量和精度。
在进行余量计算时,需要考虑以下几个影响因素:(1)熔模材料的特性,不同的熔模材料具有不同的热膨胀系数、导热系数等特性,这些特性会影响到熔模的收缩率和形变情况。
(2)铸件的设计要求,不同的铸件在尺寸和形状上有不同的要求,因此在余量计算时需要根据具体的设计要求进行调整。
(3)工艺参数,熔模铸造的工艺参数包括熔化温度、注射压力、冷却速度等,这些参数会直接影响到熔模的收缩和形变情况。
5. 余量计算的实际应用。
余量计算是熔模铸造中非常重要的一环,它直接影响到最终产品的质量和精度。
[精彩]第三章 浇注系统的设计与计算
![[精彩]第三章 浇注系统的设计与计算](https://img.taocdn.com/s3/m/2c43a13b10a6f524ccbf85c8.png)
Department of Materials Engineering
计算
1、 奥赞(Osann)公式 —阻流(最小)截面积的计算 。 阻流(最小)组元指浇注系统中最小截 面积的浇道,一般为内浇道,即
m A阻= 2 gHp
H P H0 P
2
2C
湖北汽车工业学院材料工程系 Department of Materials Engineering
轻合金浇注系统中安装过滤网
湖北汽车工业学院材料工程系 Department of Materials Engineering
4、内浇道的设计
1) 内浇道的作用: 控制液态金属充型速度和流动方向、温度分布和凝固顺序。 2) 形状:扁平梯形、月牙形和三角形。 3) 位置的选择: 依据铸件所需凝固方式和流动特性考虑。 同时凝固: 对于壁厚均匀的铸件,拟采用多个内浇道分散引入; 对于不均匀的铸件,则从薄壁处引入。 顺序凝固: 从厚壁处引入金属液。
湖北汽车工业学院材料工程系 Department of Materials Engineering
5、确定内浇道位置的几个具体问题
结构复杂的铸件,壁厚差别大的补缩区域则按顺 序凝固从厚处引入;整个铸件按同时凝固方式采 用多个内浇道充型。 要求各内浇道的流量分布合理。 液流顺壁流入,不冲刷 型壁、型芯和铸型凸出部分。 避开铸件重要部位, 防止晶粒粗大。 造型、清理操作方便, 不阻碍铸件收缩。 湖北汽车工业学院材料工程系
(二)按浇注系统各组元截面积的比例关系分
1、封闭式浇注系统
∑A内< ∑A横<A直
一般为 ∑A内:∑A横:A直=1:1.1:1.15
特点:
挡渣力强,金属消耗少,易清理;
浇注系统浇口尺寸计算参考文档

浇注系统相关尺寸计算
2.分流道的设计 分流道是主流道末端与浇口之间的通道。用于一模多腔或单型腔
多浇口(塑件尺寸大)的场合。
浇注系统相关尺寸计算
分流道的截面形状及尺寸 为便于机械加工及凝料脱模,分流道一般设置在分型面上。
浇注系统相关尺寸计算
3.浇口的设计 浇口亦称进料口,是连接分流道与型腔的最短通道。
料,常用于成型大而深的塑件。
浇注系统相关尺寸计算
②侧浇口 侧浇口又称边缘浇口,一般开设在分型面上,调整其截面的厚
度和宽度可以调节熔体充模时的剪切速率及浇口固化时间,主要用 于中小型塑件的多型腔模具。
浇注系统相关尺寸计算
③扇形浇口 成型大平面板状及薄壁塑件时,宜采用扇形浇口。在扇形浇口的
整个长度上,沿进料方向截面宽度逐渐变大,为保持断面积处处相 等,浇口的截面厚度逐渐减小。
浇注系统相关尺寸计算
浇口的平衡
相同塑件多型腔的BGV值
BGV AG LR LG
AG ----浇口的截面积( mm2) LR ----从主流道中心到浇口的流动通道的长度( mm2) LG ----浇口的长度( mm)
浇注系统相关尺寸计算
浇口的平衡
2)不同塑件多型腔的BGV值
Wa BGVa AGa LRb LGb Wb BGVb AGb LRa LGa
浇注系统相关尺寸计算
浇口的尺寸一般根据经验确定,截面积为分流道断面积的 3%~9%,截面形状常为矩形或圆形,浇口的长度为1~1.5mm。
注意: 在设计浇口时,往往先取较小的尺寸值,以便在试模时
逐步加以修正。
浇注系统相关尺寸计算
(2)浇口的类型
①直接浇口 直接浇口又称中心浇口、主流道浇口,这种浇口由主流道直接进
熔模铸造浇注系统计算
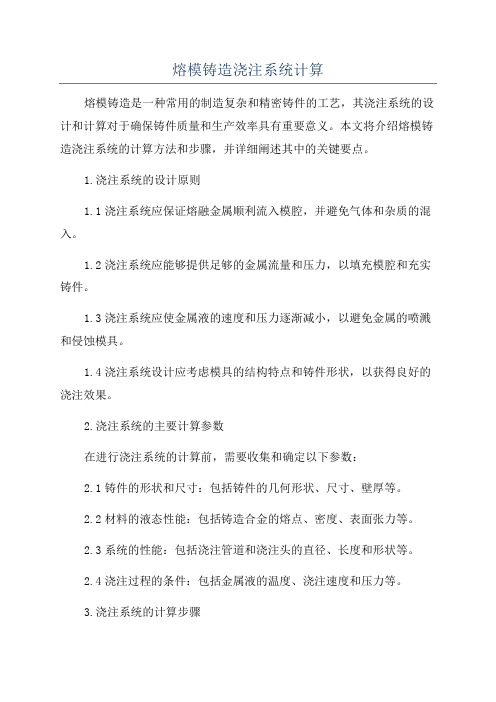
熔模铸造浇注系统计算熔模铸造是一种常用的制造复杂和精密铸件的工艺,其浇注系统的设计和计算对于确保铸件质量和生产效率具有重要意义。
本文将介绍熔模铸造浇注系统的计算方法和步骤,并详细阐述其中的关键要点。
1.浇注系统的设计原则1.1浇注系统应保证熔融金属顺利流入模腔,并避免气体和杂质的混入。
1.2浇注系统应能够提供足够的金属流量和压力,以填充模腔和充实铸件。
1.3浇注系统应使金属液的速度和压力逐渐减小,以避免金属的喷溅和侵蚀模具。
1.4浇注系统设计应考虑模具的结构特点和铸件形状,以获得良好的浇注效果。
2.浇注系统的主要计算参数在进行浇注系统的计算前,需要收集和确定以下参数:2.1铸件的形状和尺寸:包括铸件的几何形状、尺寸、壁厚等。
2.2材料的液态性能:包括铸造合金的熔点、密度、表面张力等。
2.3系统的性能:包括浇注管道和浇注头的直径、长度和形状等。
2.4浇注过程的条件:包括金属液的温度、浇注速度和压力等。
3.浇注系统的计算步骤根据以上参数和原则,进行浇注系统的计算,一般可分为以下几个步骤:3.1确定浇注管道和浇注头的几何参数:根据铸件的形状和尺寸,确定浇注管道和浇注头的直径、长度和形状。
通常,浇注管道和浇注头的直径会逐渐减小,以保证金属液的速度和压力逐渐降低。
3.2计算浇注头的流速和压力:根据材料的液态性能和浇注过程的条件,计算金属液在浇注头中的流速和压力。
这一步需要考虑金属液的粘度、密度以及浇注头的形状、长度等参数。
3.3计算浇注管道和浇注头的阻力:根据浇注管道和浇注头的形状和尺寸,计算流动的阻力。
这一步需要考虑流动的雷诺数、曼宁系数和摩擦因数等参数。
3.4确定浇注时间和浇注压力:根据铸件的尺寸和形状,计算金属液的流速和浇注时间,进而确定浇注压力。
通常,浇注时间应保证金属液充分填充模腔,并保持一定的冲刷效果。
4.浇注系统的优化完成上述计算后,可以进行浇注系统的优化,包括以下几个方面:4.1浇注管道的优化:可以通过改变浇注管道的形状和尺寸,减小阻力和压力损失,提高浇注效率。
熔模铸造浇注补缩系统讲解
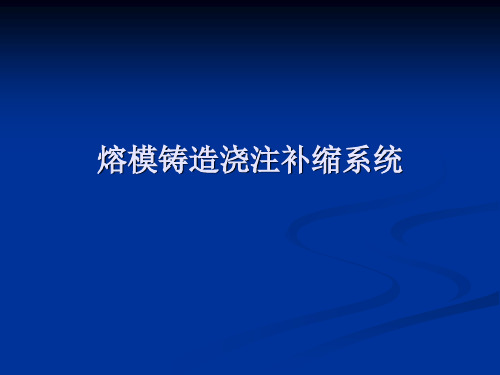
σ=1.5N/m
②浇注温度
过热度=130~160℃
型壳焙烧后的炉外冷却特性
出炉过程和浇注过程 的金属液温度降低
③薄壁部位缓慢冷却
小型静翼叶片
辅助浇道
④不能憋气
⑤浇注中途不能停顿
(2)充填的平稳性
①底注
②流动状态
③倾斜浇注
④夹杂分布 ⑤小直浇道
⑥过滤网
2.保证补缩
产生原因 体收缩率:
(%) 1.9943 7.459WC - 4.73WC2 KiWi KT (Tp TL)
W Ni Mn Cr Si Al Ki -0.53 -0.0354 +0.0585 +0.12 +1.03 +1.07
体收缩率→凝固收缩流动(冷却 慢处流向冷却快处)→冷却慢处流 下孔 洞(缩孔)
②冒口大小计算
Ⅰ热节圆法
Ⅱ模数法 M铸:M颈:M冒=1:(1.05~1.3):(1.2~1.5) V冒(k-β)=βV铸 V冒=V铸×β/(k-β)
Ⅲ冒口计算图
D冒=max[dr,dR]
dr__保证冒口比铸件冷却慢所需的冒口直径 d End
横浇道式:单一横浇道、多道横浇道、 圆板、圆环、多层、多层多道
冒口式 组合式
单一直浇道
带补缩节的直浇道
多道直浇道 过渡直浇道
空心直浇道
单一横浇道
多道横浇道
圆板
圆环
多层多道
多层
冒口式
组合式
3、按补缩组元分
Ⅰ.中心直浇道 Ⅱ.横浇道
Ⅲ.竖浇道
Ⅳ.底注竖浇道+侧冒口
Ⅴ.侧冒口
Ⅵ.顶冒口
铸件刚度小,直(横)浇道刚度大 铸件变形大 铸件刚度大,直(横)浇道刚度小 铸件变形小
铸钢件浇注时间计算
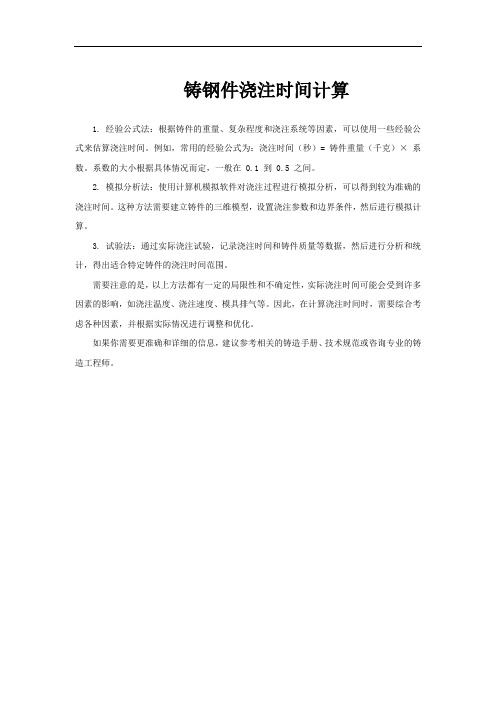
铸钢件浇注时间计算
1. 经验公式法:根据铸件的重量、复杂程度和浇注系统等因素,可以使用一些经验公式来估算浇注时间。
例如,常用的经验公式为:浇注时间(秒)= 铸件重量(千克)×系数。
系数的大小根据具体情况而定,一般在 0.1 到 0.5 之间。
2. 模拟分析法:使用计算机模拟软件对浇注过程进行模拟分析,可以得到较为准确的浇注时间。
这种方法需要建立铸件的三维模型,设置浇注参数和边界条件,然后进行模拟计算。
3. 试验法:通过实际浇注试验,记录浇注时间和铸件质量等数据,然后进行分析和统计,得出适合特定铸件的浇注时间范围。
需要注意的是,以上方法都有一定的局限性和不确定性,实际浇注时间可能会受到许多因素的影响,如浇注温度、浇注速度、模具排气等。
因此,在计算浇注时间时,需要综合考虑各种因素,并根据实际情况进行调整和优化。
如果你需要更准确和详细的信息,建议参考相关的铸造手册、技术规范或咨询专业的铸造工程师。
模铸有关计算公式

模铸有关计算公式
模铸是一种常见的金属铸造工艺,通过将金属熔化后倒入模具中,然后冷却凝固成型,最终得到所需的零件或产品。
在模铸过程中,需要进行各种参数的计算,以确保最终产品的质量和精度。
本文将介绍模铸过程中常见的计算公式,帮助读者更好地理解和应用模铸技术。
1. 铸件重量计算公式。
在模铸过程中,首先需要计算铸件的重量,以确定所需的原材料数量和生产成本。
铸件重量的计算公式如下:
铸件重量(kg)= 铸件体积(cm³)×铸件密度(g/cm³)× 0.001。
其中,铸件体积可以根据模具的设计参数和产品图纸进行计算,铸件密度则根据具体的金属材料来确定。
通过这个公式,可以快速准确地计算出铸件的重量,为生产计划和原材料采购提供参考依据。
2. 浇注系统计算公式。
在模铸过程中,浇注系统的设计对最终产品的质量和成型效果有着重要影响。
浇注系统的计算公式如下:
浇注压力(MPa)= (液态金属重力头压力 + 液态金属浇注冲击压力)/ 浇注面积。
液态金属重力头压力可以根据液态金属的密度和浇注高度来计算,液态金属浇注冲击压力则需要根据具体的浇注工艺和设备参数来确定。
通过计算浇注压力,可以合理设计浇注系统,确保金属能够充分填充模具,并避免产生气孔和缺陷。
3. 固化时间计算公式。
在模铸过程中,金属液态态态态态态态态态态态态态态态态态态态态态态态态态态态态态态态态态态态态态态态态态态态态态态态态态态态态态态态态态态态态态态态态态态态态态态态态态态态态态态态态态态态态态态态态态态态态态态态态态态态态。
铸造业浇注系统的计算
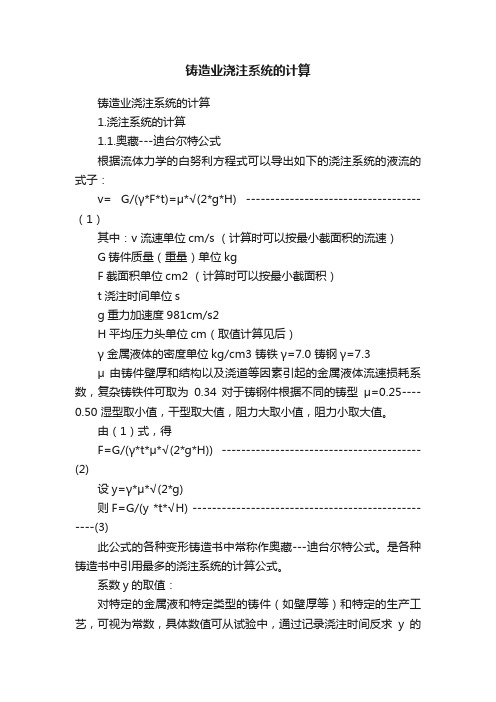
铸造业浇注系统的计算铸造业浇注系统的计算1.浇注系统的计算1.1.奥藏---迪台尔特公式根据流体力学的白努利方程式可以导出如下的浇注系统的液流的式子:v= G/(γ*F*t)=μ*√(2*g*H) ------------------------------------(1)其中:v 流速单位cm/s (计算时可以按最小截面积的流速)G铸件质量(重量)单位kgF截面积单位cm2 (计算时可以按最小截面积)t浇注时间单位sg重力加速度981cm/s2H平均压力头单位cm(取值计算见后)γ 金属液体的密度单位kg/cm3 铸铁γ=7.0 铸钢γ=7.3μ 由铸件壁厚和结构以及浇道等因素引起的金属液体流速损耗系数,复杂铸铁件可取为0.34 对于铸钢件根据不同的铸型μ=0.25----0.50 湿型取小值,干型取大值,阻力大取小值,阻力小取大值。
由(1)式,得F=G/(γ*t*μ*√(2*g*H)) -----------------------------------------(2)设y=γ*μ*√(2*g)则F=G/(y *t*√H) ---------------------------------------------------(3)此公式的各种变形铸造书中常称作奥藏---迪台尔特公式。
是各种铸造书中引用最多的浇注系统的计算公式。
系数y的取值:对特定的金属液和特定类型的铸件(如壁厚等)和特定的生产工艺,可视为常数,具体数值可从试验中,通过记录浇注时间反求y的平均值作为今后计算的常数。
如,一拖一铁厂的原二线为0.18—0.22 原三四线为0.13 原一线为0.15—0.16现在的KW线,由于砂型的紧实度特高,y=0.04左右平均压头H的取值:顶注为H=h底注为H=h-c/2从铸件中间浇注为H=h-c/4其中h为浇口杯平面到内浇口的高度,c为铸件的高度。
公式推导从略,见有关的书籍。
以上计算出的是浇注系统的最小截面积。
熔模铸造浇注系统横浇道计算方法适用性分析

熔模铸造浇注系统横浇道计算方法适用性分析清华大学兰宏志‘吕志同回双景姜不居摘要对工艺成熟的熔模铸件浇注系统横浇道数据进行数理统计分析,检验了亨金法及其修正公式在实际横浇道设计中的适用性,并表明修正公式更符合生产实际情况。
关键词:熔模铸造横浇道数理统计AnalysisontheApplicabilityoftheCalculationMethodofInvestmentCastingGatingSystemwithaHorizontalRunnerLanHongzhi,LvZhigang,YahShuangjing,JiangBuju(TsingHuaUniversity)ABSTRACTBasedonmathcmatlcalstatisticstheory,allanalysisismadeonthebasisofdatacollectedfromiTlaturegatingsystemswithahorizontalrunner,andapplicabilityofHengJenmethodandit'smodificationformulaaretcstedFurthermore,itshowsthemodificationformulafordesigninggatingsystemagreeswellwiththepracti∞productionsituation.KeyWords:InvestmentCasting,HorizontalRunner,MathematicalStatistics1熔模铸造浇注系统计算浇注系统的计算是熔模铸造工艺设计的核心部分,其设计是否合理直接影响着铸件的质量。
浇注系统除应具有引入金属液等作用外,还要能为铸件提供必要的补缩金属液和补缩通道。
现在国内多数工厂熔模铸件浇注系统的尺寸是凭借设计人员的经验确定的.对一般的小铸件都不进行详细计算,而对热节较明显或较大的铸件,也只是根据热节圆的尺寸按照一个粗略的比例来估计内浇道、直浇道及横浇道的截面尺寸,并没有根据模数的概念来分析浇注系统,直接影响了铸件的成品率和工艺出品率。
浇注系统的计算
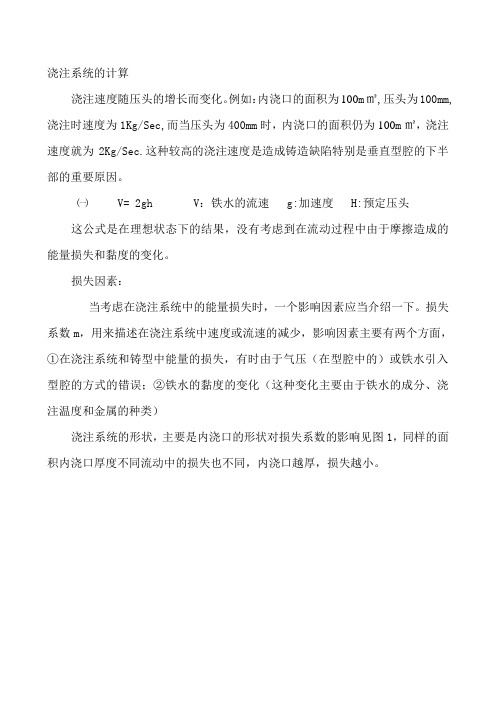
浇注系统的计算浇注速度随压头的增长而变化。
例如:内浇口的面积为100m㎡,压头为100mm,浇注时速度为1Kg/Sec,而当压头为400mm时,内浇口的面积仍为100m㎡,浇注速度就为2Kg/Sec.这种较高的浇注速度是造成铸造缺陷特别是垂直型腔的下半部的重要原因。
㈠ V= 2gh V:铁水的流速 g:加速度 H:预定压头这公式是在理想状态下的结果,没有考虑到在流动过程中由于摩擦造成的能量损失和黏度的变化。
损失因素:当考虑在浇注系统中的能量损失时,一个影响因素应当介绍一下。
损失系数m,用来描述在浇注系统中速度或流速的减少,影响因素主要有两个方面,①在浇注系统和铸型中能量的损失,有时由于气压(在型腔中的)或铁水引入型腔的方式的错误;②铁水的黏度的变化(这种变化主要由于铁水的成分、浇注温度和金属的种类)浇注系统的形状,主要是内浇口的形状对损失系数的影响见图1,同样的面积内浇口厚度不同流动中的损失也不同,内浇口越厚,损失越小。
损失系数m是一个典型的经验数据,可以预定一用于浇注系统的计算,预定的m在以后的流动实验中将被修正。
当考虑到m时公式㈠将被修正为:V=m 2gH ㈡流速 W 的概念是指在一段时间内经过浇道的铁水的公斤重量。
ω= G/T ㈢ω也可以表达为 W= ρ * F * V V 流过浇道的速度F 浇道的截面积G/T= ρ * F* VF=------------------------ 对于铁水:ρ=6.89*10 Kg/mm g =9810 mm/SecF= 1036*G/T*m* H ㈣只有对于理想运动状态才没有损失,在任何真实运动中都存在损失系数是0---1之间的分数,损失系数越大损失越小。
在水力系统中,如浇注系统中存在损失,由损失系数来表示,表 1 给出了不同损失系数的流动损失(在浇注系统中):m 0.9 0.8 0.7 0.6 0.5 0.4 0.3 0.2% 11 25 43 67 100 150 233 400 占无摩擦流动的百分比1/9 2/8 3/7 4/6 5/5 6/4 7/3 8/22.金属液在浇注系统中的流动:静态的流层、平稳的流动只能在以下条件下实现。
铸件浇注系统 最精准 适用于垂直线 水平线 树脂砂线计算
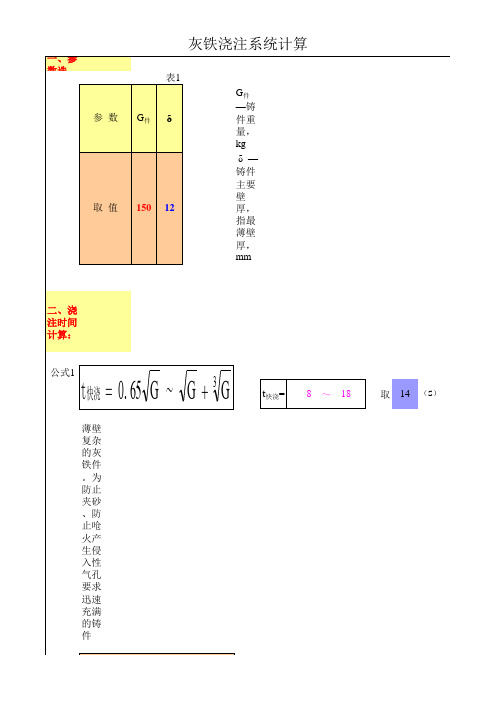
m)
G件 —铸 件重 量 (不 含浇 冒 口) ,
(Kg
)
参数 G件
δ
s G件 3
s=1/5 δG件
数值 150 12 12.2 7.11 360
t = 19.4 (s)
四、最 小阻力 截面积 计算:
公式4
F阻
G件
2g • t •
G— 铸件 重 量, kg
ρ— 铸件 密 度, kg/c m3;
ω— 材质 指 数,
g— 重力 加速 度, 980c m/s2
δ— 铸件 主要 壁 厚, 常指 最薄 壁 厚, mm
灰铸 铁: 0.00 71, 球 铁: 0.00 73, 铸 钢: 0.00
78
灰铸 铁: 0.24 ,球 铁: 0.23 ,铸 钢: 0.22
t— 铸件 有效 浇注 时 间, s
表4 参数 G件 /Kg ρ /kg/cm3 2g0.5 浇注t /s
尺寸 a b c 单位
数据 40 50.7 20 mm
直浇 道的 直径 为:
Φ=
44.2 mm
方案2 浇道 比 值 取值 实际面积
F直
1
1
11.6
F横 1.3~1.5 1.3
15.1
∑F内 1.1~1.2 1.2
14.0
方案3 浇道 比 值 取值 实际面积
F直
1
1
17.5
F横 1.3~1.5 1.2
一、参 数选
参数
取值
灰铁浇注系统计算
表1 G件 δ
150 12
G件 —铸 件重 量, kg
δ— 铸件 主要 壁 厚, 指最 薄壁 厚, mm
二、浇 注时间 计算:
第三章 浇注系统的设计与计算
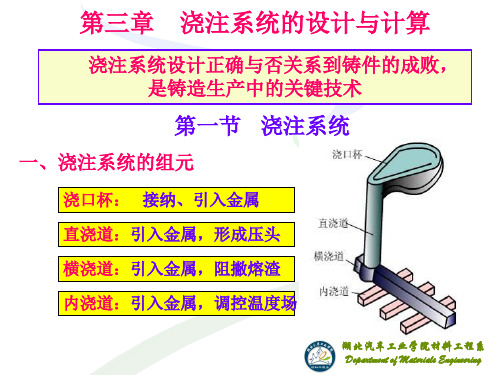
应用:
主要用于结构复杂的各 种黑色金属铸件和易氧化 的有色合金铸件。
汽缸头
湖北汽车工业学院材料工程系 Department of Materials Engineering
中间浇注应用广泛
中间浇注综 合有顶注式和 底注式的优缺 点; 内浇道、横 浇道设在分型 面上,造型方 便。
湖北汽车工业学院材料工程系 Department of Materials Engineering
第三章
浇注系统的设计与计算
浇注系统设计正确与否关系到铸件的成败, 是铸造生产中的关键技术
第一节 浇注系统
一、浇注系统的组元
浇口杯: 接纳、引入金属
直浇道:引入金属,形成压头
横浇道:引入金属,阻撇熔渣 内浇道:引入金属,调控温度场
湖北汽车工业学院材料工程系 Department of Materials Engineering
球墨铸铁呈 “糊状凝固” , 冒口的有效补缩距离较灰铸铁小 , 其不同条件下的湿型试验数据参见下表。
铸件壁厚 δ/mm 6.35 12.70 水 平 补 缩
湿 型 —— 101.6-114.3 湿 型 31.75 101.6 湿 型 —— 88.9
垂直补缩
壳型 —— 88.9
15.86
25.4 38.1
复习题
1.浇注系统由哪些部分组成?分别说明各个组元的 作用? 2.比较顶注式和底注式浇注系统的优缺点。 3.比较封闭式和开放式浇注系统的优缺点。
4 . 如何提高横浇道的撇渣效果?
5. 内浇道在铸件浇铸中能够起到哪些重要作用? 6.确定内浇道位置要注意哪些具体问题? 湖北汽车工业学院材料工程系
Department of Materials Engineering
模具浇注系统体积的估算
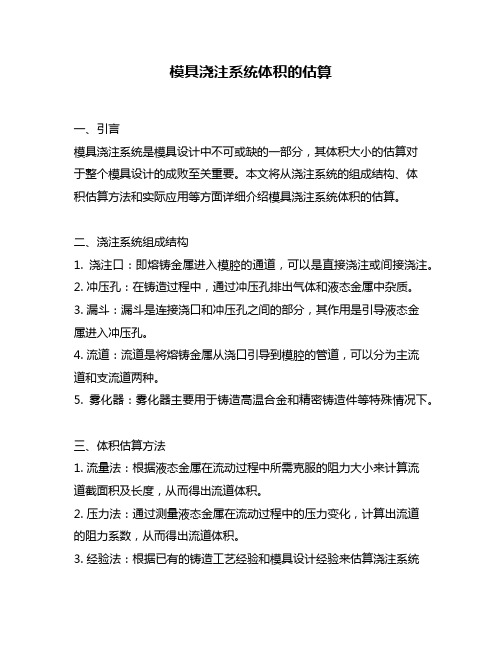
模具浇注系统体积的估算一、引言模具浇注系统是模具设计中不可或缺的一部分,其体积大小的估算对于整个模具设计的成败至关重要。
本文将从浇注系统的组成结构、体积估算方法和实际应用等方面详细介绍模具浇注系统体积的估算。
二、浇注系统组成结构1. 浇注口:即熔铸金属进入模腔的通道,可以是直接浇注或间接浇注。
2. 冲压孔:在铸造过程中,通过冲压孔排出气体和液态金属中杂质。
3. 漏斗:漏斗是连接浇口和冲压孔之间的部分,其作用是引导液态金属进入冲压孔。
4. 流道:流道是将熔铸金属从浇口引导到模腔的管道,可以分为主流道和支流道两种。
5. 雾化器:雾化器主要用于铸造高温合金和精密铸造件等特殊情况下。
三、体积估算方法1. 流量法:根据液态金属在流动过程中所需克服的阻力大小来计算流道截面积及长度,从而得出流道体积。
2. 压力法:通过测量液态金属在流动过程中的压力变化,计算出流道的阻力系数,从而得出流道体积。
3. 经验法:根据已有的铸造工艺经验和模具设计经验来估算浇注系统体积。
四、实际应用1. 流量法和压力法是目前比较常用的浇注系统体积估算方法,在实际应用中需要根据具体情况选择合适的方法。
2. 在模具设计中,要充分考虑浇注系统的复杂性和成本因素,尽可能地减少不必要的流道和漏斗等部件。
3. 在模具制造过程中,要严格按照设计要求进行加工和装配,确保浇注系统能够正常运行。
五、结论模具浇注系统体积的估算是模具设计中非常重要的一环,需要根据具体情况选择合适的估算方法,并在实际应用中加以考虑和改进。
只有通过科学合理地设计和制造浇注系统,才能够获得高质量、高效率的铸件。
3.3.3 浇注系统设计与计算
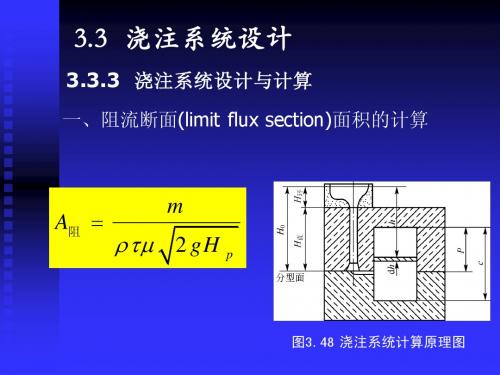
3.3.3 浇注系统设计与计算 一、阻流断面(limit flux section)面积的计算
m A阻 = ρτµ 2 gH p
图3.48 浇注系统计算原理图
3.3.3 浇注系统设计与计算 一、阻流断面(limit flux section)面积的计算
1) 平均静压头 的计算 平均静压头Hp的计算
H p = H 0 − p / 2c
2
图3.48 浇注系统计算原理图
一、阻流断面(limit flux section)面积的计算
H0的确定: 的确定
表3-3 压力角的最小值α
铸件壁厚δ/mm L/mm 3~5 5~8 8~15 15~2 0 20~2 5 25~3 5 35~4 5 00 3000 2800 根 据 具 体 情 况 确 定 6~7 6~7 6~7 7~8 7~8 8~9 8~9 8~9 5~6 5~6 6~7 6~7 6~7 6~7 7~8 7~8 5~6 5~6 5~6 6~7 6~7 6~7 6~7 6~7 5~6 5~6 5~6 6~7 6~7 6~7 6~7 6~7 4~5 4~5 4~5 5~6 5~6 5~6 5~6 5~6 4~5 4~5 4~5 4~5 4~5 5~6 5~6 6~7 用两个或更多 的直浇道浇注
V型min/mm·s-1 8~10 20~30 10~20 20~30 30~100
V上升=C/τ
4~10 1.5~4~
3.3.3 浇注系统设计与计算 一、阻流断面(limit flux section)面积的计算 二、各组元断面比例的选择 三、确定浇注系统断面尺寸的图表
吃砂量
2600 2400 2200 2000
3.3.3 浇注系统设计与计算 一、阻流断面(limit flux section)面积的计算
浇注系统计算

模具浇注系统设计方案1、金属液充型的静压力头:经测量h1=230mm,h2=420mm;2、铸件重量:G=23.7N,铸型中铸件总重量为23.7*6=142.2N;3、每型需要的铁水重量:现有模具的工艺出品率为69%,设改造后的工艺出品率为73%142.2/73%=194.8N≈19.5kg4、浇注重量速度:设定每型浇注时间为8s,每个型腔充型时间为6s每个铸件的浇注重量速度:23.7/6≈3.95N/S整型的浇注重量速度:194.8/8=24.35N/S5、选择浇口杯:查表得浇口杯重量为16N=1.6kg6、确定内浇道面积:h1=230mm,面积f1=26mm2;h2=420mm,面积f2=19.5mm2;灰铸铁的流量系数取μ=0.5,实际内浇道面积为:F1=26/0.5=52mm2 选30*2mm=60mm2F2=19.5/0.5=39mm2 选25*2mm=50mm27、横浇道面积:上排60*1.3=78mm2 选11*7*9mm=81mm2下排50*1.3=65mm2 选10*7*8mm=68mm28、直浇道面积:上段1(81*2+68)*1.2=276mm2选16*13*20mm=290mm2上段2(81 +68*2)*1.2=260.4mm2选16*13*18mm=261mm2下段1 68 *1.2=81.6mm2选12*9*12mm=126mm2下段2 68*2*1.2=163.2mm2选14*10*14mm=168mm2 9、分水横浇道面积290*1.1=319mm2 选16*13*22mm=319mm210、浇注系统总重量:内浇道:(60*20*3+50*20*3)*7.2/1000=47.52g横浇道:〔81*3+38*3〕*140*7.2/1000= 450.58g直浇道:上段(290+261)*220 *7.2/1000=872.78g下段(126+168)*160 *7.2/1000=338.69g 横分水道:319*180*2*7.2/1000=826.85g总重:47.52+450.58+872.78+338.69+826.85+1600=4.14 kg理论工艺出品率:12.84/(12.84+4.14 )*100%≈75.62% 10、工艺简图如下:。
浇注系统的计算和设计

浇注系统的计算和设计Fra bibliotek1、浇注系统计算的水力学公式
在浇注系统的类型和引入位置确定以 后、就可进一步确定浇注系统各基本单元的尺 寸和结构。
目前大都采用水力学近似公式或经验 公式计算出浇注系统的最小截面积,再根据铸 件的结构特点、几何形状等确定浇道比,确定 各单元的尺寸和结构。
计算阻流截面的水力学公式
一、平均静压头HP的计算
传统的解法中假定: 1) 金属液从浇口杯顶液面至流出阻流所作的功,可用 总质量m、 重力加速度g和平均计算压力头Hp的连乘积来表示,即等于mgHp 2) 假定铸件(型腔)的横截面积S沿高度方向不变
快浇的缺点: 对型壁有较大的冲击作用,容易造成涨砂、冲 砂、抬箱等缺陷。浇注系统的重量稍大,工艺出品率略低
快浇适用于:
薄壁的复杂铸件、铸型上半部分有薄 壁的铸件,具有大平面的铸件,铸件 表皮易生成氧化膜的合金铸件,采用 底注式浇注系统而铸件顶部又有冒口 的条件下和各种中大型灰铸铁件、球 墨铸铁件
慢浇的优点 金属对型壁的冲刷作用轻;可防止涨砂、抬箱、冲砂等缺陷。 有利型内、芯内气体的排除。对体收缩大的合金,当采用顶 注法或内浇道通过冒口时,慢浇可减小冒口。浇注系统消耗 金属少。
5、计算阻流截面积S阻
如果铸件质量很大,则计算铸件质量m时,应包括型 腔扩大量——由于各种原因引起的增重。增重原因有: 木模壁厚偏差 起模时扩砂量 铸型及砂芯干燥过程中的尺寸变化 合箱偏差及浇注时的涨砂等
- 1、下载文档前请自行甄别文档内容的完整性,平台不提供额外的编辑、内容补充、找答案等附加服务。
- 2、"仅部分预览"的文档,不可在线预览部分如存在完整性等问题,可反馈申请退款(可完整预览的文档不适用该条件!)。
- 3、如文档侵犯您的权益,请联系客服反馈,我们会尽快为您处理(人工客服工作时间:9:00-18:30)。
熔模铸造浇注系统计算
1 熔模铸造浇注系统计算
浇注系统是熔模铸造工艺设计的重要部分。
国熔模碳钢铸件居多,其浇注系统除应具有引入金属液等作用外,还要能为铸件提供必要的补缩金属液和补缩通道。
目前,很多工厂熔模铸件浇注系统大小是设计人员凭经验定的,直接影响了铸件的成品率和工艺出品率。
因此,有必要开展熔模铸造浇注系统计算方法的探讨。
从结构上看,熔模铸造浇注系统有直浇道-浇道、横浇道-浇道和组合式三大类。
其中直浇道-浇道式又分:单一直浇道、直浇道-补缩环、多道直浇道和特种形状直浇道等形式。
但在实际生产中应用最广泛的是单一直浇道浇注系统,如图1所示。
图1 单一直浇道
Fig.1 Single sprue
目前用于单一直浇道浇注系统的计算方法有:
亨金法、比例系数法、浇口杯补缩容量法、当量热节
法、浇注系统确定参考图法等。
其中亨金法较全面地
考虑了影响补缩的因素;并可计算出直浇道、浇口尺
寸,以及一个浇注系统铸件组最多允许的铸件数量。
据介绍亨金法更适用于该类浇注系统。
本文就单一直浇道浇注系统计算开展研究。
利用计算机对第一拖拉机股份(简称拖拉机厂)、东风汽车公司精密铸造厂(简称第二汽车制造厂)大量工艺已成熟零件的浇注系统与亨金法计算结果相比较,并对亨金法进行修正。
该修正公式可供各工厂技术人员在设计浇注系统时参考。
2 亨金法简介
为使铸件获得补缩,浇口应设在铸件厚处(热节处),以保证在金属液凝固时,浇口比铸件厚处晚凝固,而直浇道又比浇口晚冷,从而利用直浇道中金属液补缩铸件。
因此,浇口截面的热模数Mg(mm)是铸件热节处的热模数Mc(mm)、直浇道截面的热模数Ms(mm)、单个铸件质量Q(g)和浇口长度Lg(mm)的函数,即Mg=f(Mc,Q,Lg,Ms) (1)
前联学者亨金用不同铸件做试验,把公式(1)中各参数关系绘成曲线后发现,它们之间的关系为各种不同方次的抛物线关系,最后归纳得到下列公式:
(2)
式中Kh——比例系数,中碳钢Kh≈2。
一般工厂直浇道尺寸已标准化。
利用式(2)可
计算出铸件浇口截面热模数,从而得到浇口具体尺寸。
采用这种单一直浇道形式浇注系统组成的铸
件组,其最大允许铸件的数量nmax为:
(3)
式中γ——合金的密度,g/cm3
Fs——直浇道截面积,cm2
H——直浇道高度,cm
β——合金的体收缩系数,中碳钢β≈4%。
式(2)、(3)就是常称的亨金公式。
亨金在发表该公式的文章中提到,公式还必须考虑生产实际情况,如直浇道最佳直径在20~55 mm之间,浇口长度最好8 mm,用不同切断浇口方法可稍有加长等等。
3 亨金法实用性分析
3.1 熔模铸件选择
在拖拉机厂和第二汽车制造厂共收集210个熔模铸件及其浇注系统系统。
其中拖拉机厂75型、150型和180型拖拉机的130个零件,第二汽车制造厂80个汽车零件。
这些铸件废品率均小于5%,无缩孔、缩松等缺陷,其浇注工艺已成熟。
熔模铸件多为小件,所选210个零件的质量从0.01 kg到3.6 kg,铸件热节处模数从1.2 mm到5.9 mm,这对于熔模铸件来说是具
有代表性的。
钢种多数是ZG45,ZG35,少量是ZG15。
两厂生产工艺相似,均为单一直浇道系统,直浇道直径为38~55 mm,直浇道长度300 mm或350 mm;90%左右采用易割浇口,均不设单独冒口。
使用水玻璃型壳,型壳层数多为六层半。
铸件浇注时钢液浇温1 540~1 580 ℃,型壳温度大于400 ℃。
3.2 亨金公式(2)实用性分析
利用计算机将以上210个熔模铸件实际使用的浇注系统和用亨金公式(2)计算的数据进行比较。
表1和表2为部分铸件浇口截面模数有关数据。
将拖拉机厂和第二汽车制造厂全部零件热节处的模数和浇口截面模数关系、铸件质量和浇口截面模数关系分别拟合成图2、图3曲线,其中曲线1为实际值、曲线2为计算值。
如前所述,所统计铸件质量从0.01 kg到3.6 kg,图3铸件质量只统计到0.6 kg,大于0.6 kg铸件其件重和浇口截面处模数关系趋势是一致的。
表1 拖拉机厂部分铸件有关数据
Table 1 Related data of some castings selected from
The Precise Foundry Flant of the China First Tractor
& Construction Machinery Corporation
表2 第二汽车制造厂部分铸件有关数据
Table 2 Related data of some castings selected from
Precise Foundry Works of DFM。