第三章 浇注系统的设计与计算[1]
浇注系统1
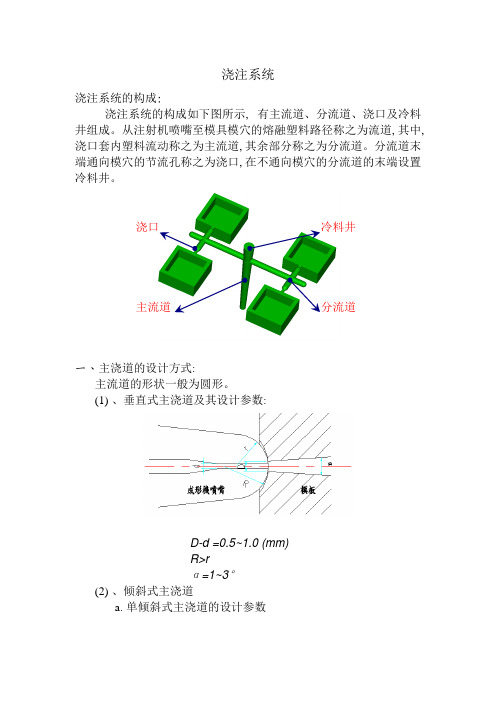
浇注系统浇注系统的构成: 浇注系统的构成如下图所示, 有主流道、分流道、浇口及冷料井组成。
从注射机喷嘴至模具模穴的熔融塑料路径称之为流道,其中,浇口套内塑料流动称之为主流道,其余部分称之为分流道。
分流道末端通向模穴的节流孔称之为浇口,在不通向模穴的分流道的末端设置冷料井。
一、 主浇道的设计方式:主流道的形状一般为圆形。
(1) 、垂直式主浇道及其设计参数:D-d =0.5~1.0 (mm) R>rα=1~3°(2) 、倾斜式主浇道a. 单倾斜式主浇道的设计参数主流道 分流道冷料井浇口a的取值主要与塑料性能有关a=30°(对于PE.PP.PA)a=20°(对于PS.SAN.ABS.PC.POM.PMMA)b.双倾斜式主浇道的设计参数R的值由所选射出成型机决定a最大可取15°注:表中的注塑量指注塑机一次的注射量,d为主流道入口直径, D为主流道出口直径。
二、分浇道的设计方式:确定分流道尺寸应考虑如下因素●制品的体积和壁厚●主流道至浇口的距离●流道的冷却方法●成型树脂的流动性●便于采用自动切除浇口装置●分流道的截面厚度要大于制品的壁厚●分流道的长度要尽量短, 不能短时, 其截面尺寸应相应长度增大●对于含有玻璃纤维等流动性较差的树脂, 流道截面要大一些●流道方向改变的拐角处, 应适当设置冷料井(1)、成品布置方式(按浇道的形状分)a、“H”形分布”b、“I”形分布:C、“X” 形分布:d、“O” 形分布:(3)B=1.25D Smax—制品最大壁厚常用塑料推荐的分流道直径:塑料名称分流道直径/mm 塑料名称分流道直径/mm 塑料名称分流道直径/mm PE 3~10 PMMA 8~10 PBT 3~8PP 4.8~10 硬PVC 6.4~16 PBT(含玻纤) 3~10 PS 3.2~10 PA (含玻纤) 4~12 PC 4.8~10 HIPS 3.2~10 PA 3~10 PC(含玻纤)5~13 ABS 3.2~10 PPS 6.4~10 PU 6.4~8 SAN 3.2~10 PPO 6.4~10POM 3.2~10 PES 6.4~10分流道直径还可以按以下公式计算:D =式中: D――分流道直径mm;W――制品塑料的质量,g;L――流道长度,mm;分流道直径还可以按图查取:分流道直径图表G –制品质量,g; S –制品肉厚,mm; D –分流道参考直径 ,mm;(4)各种截面形式的优缺点比较a、圆形截面流道:优点: 表面积与体积之比最小,压力损失及温度损失小,有利于塑料的流动及压力传递缺点: 必须在公母模上各分一半,给模具加工带来一定困难b、“U”形截面流道:优点: 其截面形式接近圆形截面,同时只需在模具的一面加工缺点: 与圆形截面相比,热损失较大,流道废料多c.梯形截面流道优点: 便于流道的加工及刀具选择缺点: 热量损失较大三、浇口的设计方式:(1)、各种浇口的优缺点比较(2)、各种浇口的设计参数值及其适用场合(3)、浇口位置的选择应注意的事项b.浇口应设在制品的最大壁厚处,使塑料从厚壁流向薄壁,并保持浇口至型腔处处的流程基本一致c.防止浇口产生喷射尔在充填过程中产生蛇形流d.浇口位置应设在制品的主要受力方向上,因为塑料的流动方向上所承受的拉应力和压应力最高.特别是带填料的增强塑料e.选择浇口位置时应考虑制品的尺寸要求,因为塑料经浇口充填型腔时在塑料的流动方向与垂直于流动方向上的收缩不尽相同,所以应考虑到变形和收缩的方向性对于窄长成品,浇口位置常设在其长度2/3的位置对于有肋的制品,浇口应与肋的方向一致,且不能正对肋,要错开四、排气槽的设计方式:(2)在公模仁中割出对插形式的排气入子(3)将深肋或圆柱割成入子,以便排气五、热流道系统设计:选择冷流道与热流道系统的原则在冷﹑热流道系统的选择上, 应根据成型制品的生产总量, 成型树脂的特性, 制品的形状, 模具制造与维护费用等各个方面综合考虑, 然后确定那种方式. 一般情况下, 首先考虑采用冷流道系统能否成型. 冷流道系统能否成型的条件如下:●成型制品是否在冷流道系统允许的成型树脂流动的距离范围之内●对成型后影响的程度如何●所产生的熔接痕影响制品的使用强度否,预定注塑面的开启行程和能否满足模具所需开启距离的要求若采用冷流道系统无法满足上述条件, 则考虑采用热流道系统, 对于冷﹑热流道系统都能满足成型要求时, 则需对比如下项目, 从经济角度确定采用那种方式●缩短成型周期产生的经济效益●节约树脂产生的经济效益●机械手取冷流道系统增加的模具制造与维护费用3.1.4 采用热流[道系统需考虑的事项●选择匹配成型目的系统●设计无树脂滞留, 流动通畅的集流腔歧系统●采取矫正;在热膨胀产生口错位的措施.●防止树脂泄漏的措施●吸收集流腔加热板膨胀量与应力处理的措施●采用阀式结构浇口时应桷保阀杆运动灵活且无树脂泄漏外加热方式的优点●流道内树脂可均匀加热●容易更换树脂, 容易抱色外加热方式的缺点●热损失大●热流道板的温度高, 需采取针对膨胀的对策●热浇口套采用处热方式时, 需要有加热器安装空间, 并会造成浇口端部温度不足的情况内加热方式的优点●热损失小●热流道板的温度低, 一般不需要采取热膨胀对策●浇口附近的温度容易控制内加热方式的缺点是●树脂流道壁面和加热器外表面的温度差大●树脂流路截面积不易过大, 树脂流道阻力较大●流道壁面容易产生固化层, 更换树脂及换色较困难●成型树脂必须清洁无杂物●浇口套的内加热装置需经常更换热流道板采用管状加热,器进行外热时应考虑如下事项●管状加热器与热流道配合孔的配合暗隙应小于0.2mm●应使用多个功率加热器做到热流道板整体温均衡, 不能造成局部过热●结构上要便于加热器更换●热流道板的加热器安装孔内不能存留油●需设置加热器电压控制装置●热电偶要设在热,扣失小的部位, 量接近流道六、主浇道的拉料形式:F>A*P式中: F――注塑机的锁模力,KN;A――包括流道在内的塑料总投影面积,C㎡P ――模穴中塑料平均压力,Mpa;常用塑料模穴中的平均压力/Mpa:注射周期为每两次闭模之间的时间间隔,其中包括:充模时间: Ti升压及保压时间: Tn冷却时间: Tc开闭模及取件时间: TrT = Ti + Tn +Tc + Tr (S)(1)、充模时间依塑件大小、塑件种类、每次注射量而异。
浇注系统的设计与计算
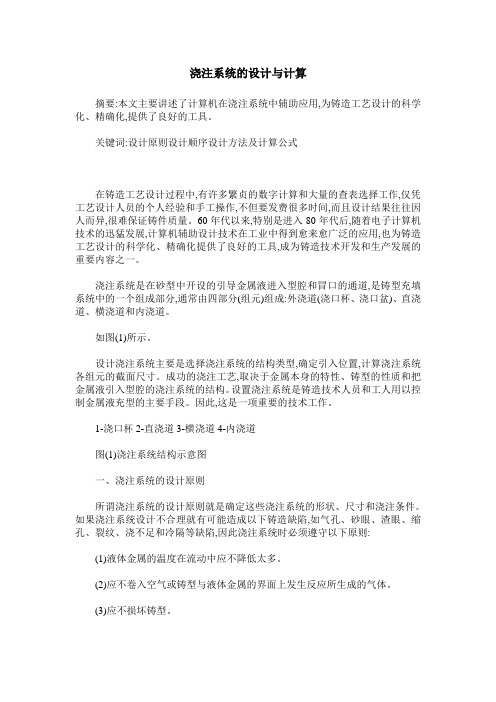
浇注系统的设计与计算摘要:本文主要讲述了计算机在浇注系统中辅助应用,为铸造工艺设计的科学化、精确化,提供了良好的工具。
关键词:设计原则设计顺序设计方法及计算公式在铸造工艺设计过程中,有许多繁贞的数字计算和大量的查表选择工作,仅凭工艺设计人员的个人经验和手工操作,不但要发费很多时间,而且设计结果往往因人而异,很难保证铸件质量。
60年代以来,特别是进入80年代后,随着电子计算机技术的迅猛发展,计算机辅助设计技术在工业中得到愈来愈广泛的应用,也为铸造工艺设计的科学化、精确化提供了良好的工具,成为铸造技术开发和生产发展的重要内容之一。
浇注系统是在砂型中开设的引导金属液进入型腔和冒口的通道,是铸型充填系统中的一个组成部分,通常由四部分(组元)组成:外浇道(浇口杯、浇口盆)、直浇道、横浇道和内浇道。
如图(1)所示。
设计浇注系统主要是选择浇注系统的结构类型,确定引入位置,计算浇注系统各组元的截面尺寸。
成功的浇注工艺,取决于金属本身的特性、铸型的性质和把金属液引入型腔的浇注系统的结构。
设置浇注系统是铸造技术人员和工人用以控制金属液充型的主要手段。
因此,这是一项重要的技术工作。
1-浇口杯2-直浇道3-横浇道4-内浇道图(1)浇注系统结构示意图一、浇注系统的设计原则所谓浇注系统的设计原则就是确定这些浇注系统的形状、尺寸和浇注条件。
如果浇注系统设计不合理就有可能造成以下铸造缺陷,如气孔、砂眼、渣眼、缩孔、裂纹、浇不足和冷隔等缺陷,因此浇注系统时必须遵守以下原则:(1)液体金属的温度在流动中应不降低太多。
(2)应不卷入空气或铸型与液体金属的界面上发生反应所生成的气体。
(3)应不损坏铸型。
(4)应防止掉砂和熔渣流入型腔。
(5)应防止液体金属过度加热铸型。
(6)应有助于方向性凝固。
(7)应不降低工艺出口率(型腔体积对包括浇注系统在内的整铸型型腔体积之比)。
(8)凝固以后应该容易去除。
二、浇注系统设计顺序不同的铸造方法、工厂、技术人员可能采用不同的浇注系统设计方法。
第三章 浇注系统的设计与计算(2)

2、冒口种类
冒口种类
普通冒口
顶冒口、暗冒口 侧冒口
特种冒口
大气压力冒口 发热冒口 保温冒口
铸铁件的 实用冒口
浇注系统当冒口 控制压力冒口
3、冒口形状
球形 圆柱形(带斜度) 球顶圆柱形 腰圆柱形 暗腰圆柱形
4、冒口形式 a)铸钢件 明边冒口 b)铸铁件 暗边冒口
5、冒口位置
1、铸件热节上方或侧旁; 2、铸件最高最厚部位; 3、一个冒口同时补缩几
Hp = Ho - C/ 2
间的确定
浇注快慢对铸件质量有重大影响。 浇注时间主要根据合金性质靠生产 经验选择。 球墨铸铁件的浇注时间参照图示曲线查 询。 一般采用快浇。 对于收缩大的合金件,采用慢浇有 利于补缩。
3)流量系数μ的确定
铸铁件流量系数
铸钢件流量系数
球墨铸铁件流量系数
计算步骤:
以内浇道为阻流(最小)截面,用奥赞(Osann)公式
S内
m
2gHp
计算每个内浇道截面积。
式中Hp可用浇口杯中液面到内浇道中心的距离Ho计算。
配套措施: 1)浇口杯应足够大; 2)严格控制浇注时间。
复习题
1.浇注系统由哪些部分组成?分别说明各个组元的 作用?
2.比较顶注式和底注式浇注系统的优缺点。
3.比较封闭式和开放式浇注系统的优缺点。
4 . 如何提高横浇道的撇渣效果?
铸钢冒口的理论依据及工作内容。 4. 何谓铸铁件的均衡凝固技术?有何重要意义? 5. 说明铸铁件实用冒口设计理念和设计计算内容。 6. 说明冷铁和铸肋的作用及应用。
u 防止旋涡,避免吸气或金属过度氧化; u 内浇道的位置和数量符合铸件所需凝固或补
缩原则; u 结构合理,造型简单; u 浇注系统本身消耗金属少。
[精彩]第三章 浇注系统的设计与计算
![[精彩]第三章 浇注系统的设计与计算](https://img.taocdn.com/s3/m/2c43a13b10a6f524ccbf85c8.png)
Department of Materials Engineering
计算
1、 奥赞(Osann)公式 —阻流(最小)截面积的计算 。 阻流(最小)组元指浇注系统中最小截 面积的浇道,一般为内浇道,即
m A阻= 2 gHp
H P H0 P
2
2C
湖北汽车工业学院材料工程系 Department of Materials Engineering
轻合金浇注系统中安装过滤网
湖北汽车工业学院材料工程系 Department of Materials Engineering
4、内浇道的设计
1) 内浇道的作用: 控制液态金属充型速度和流动方向、温度分布和凝固顺序。 2) 形状:扁平梯形、月牙形和三角形。 3) 位置的选择: 依据铸件所需凝固方式和流动特性考虑。 同时凝固: 对于壁厚均匀的铸件,拟采用多个内浇道分散引入; 对于不均匀的铸件,则从薄壁处引入。 顺序凝固: 从厚壁处引入金属液。
湖北汽车工业学院材料工程系 Department of Materials Engineering
5、确定内浇道位置的几个具体问题
结构复杂的铸件,壁厚差别大的补缩区域则按顺 序凝固从厚处引入;整个铸件按同时凝固方式采 用多个内浇道充型。 要求各内浇道的流量分布合理。 液流顺壁流入,不冲刷 型壁、型芯和铸型凸出部分。 避开铸件重要部位, 防止晶粒粗大。 造型、清理操作方便, 不阻碍铸件收缩。 湖北汽车工业学院材料工程系
(二)按浇注系统各组元截面积的比例关系分
1、封闭式浇注系统
∑A内< ∑A横<A直
一般为 ∑A内:∑A横:A直=1:1.1:1.15
特点:
挡渣力强,金属消耗少,易清理;
浇注系统浇口尺寸计算

浇注系统相关尺寸计算
浇口的平衡例题
解:由排列位置知2A2B4A4B相同,3A3B5A5B相同,1A1B相同, 因此只需求1A2A3A尺寸即可。先求2A尺寸,并以此为基准求2A3A 的尺寸。 2 2
d 5.08 1)分流道圆形截面积 AR :AR R mm 2 20.27 mm 2 2 2
2)基准浇口2A的截面尺寸: 由:AG 2 0.07 AR 1.42 mm2 得:t2 0.69mm, b2 3t2 2.07mm 3)求其他两组浇口的截面尺寸,由BGV相等得:
AG1 AG3 1.42 BGV 0.08 102 102 102 1.27 2 143 1.27 143 1.27 2 2 2
浇注系统相关尺寸计算
④点浇口 又称针点浇口或橄榄形浇口,是一种在塑件中央开设浇口时使 用的圆形限制性浇口,用于成型壳类、盒类的热塑性塑件。
优点: 浇口残留痕迹小,易取 得浇注系统的平衡,也利于 自动化操作。 缺点: 在模具结构上需增加一个 分型面,即双分型面,以便 浇口凝料取出。
浇注系统相关尺寸计算
浇注系统相关尺寸计算
浇口的平衡例题
由上式可得:
AG1 3t1 0.73mm2 , t1 0.49mm, b1 3t1 1.47 mm
2
AG3 3t3 1.87 mm2 , t 3 0.79mm, b3 3t3 2.37mm
2
计算结果:
1A/1B 型腔号、 尺寸
浇注系统相关尺寸计算
浇口的尺寸一般根据经验确定,截面积为分流道断面积的 3%~9%,截面形状常为矩形或圆形,浇口的长度为1~1.5mm。
注意: 在设计浇口时,往往先取较小的尺寸值,以便在试模时 逐步加以修正。
第三章锌合金压铸浇注系统设计

第三章锌合金压铸浇注系统设计* 浇注系统包括鹅颈、射咀、分流锥、浇道、浇口和排气系统;*常用有扇形浇道和锥形浇道兩種;*设计原则:浇注系统内的金属液能有效的、平稳的流动,并避免气体混入。
3.1澆注系统对填充条件的影响金属液在压铸过程中的充型状态是由压力、速度、时间、温度、排气等因素综合作用形成的,因而水口系统与压力传递、合金流速、填充时间、凝固时间、模具温度、排气条件有着密切的关系。
a.压力传递一方面要保证水口处金属液以高压、高速充填型腔,另一方面又要保证在流道和水口截面内的金属液先不凝固,以保证传递最终压力。
这样就需要最佳的流道和水口设计,最小的压力损失。
b.水口面积过大或过小都会影响填充过程,过大的水口充填速度低,金属过早凝固,甚至充填不足,过小的水口又会使喷射加剧,增加热量损失,产生涡流并卷入过多气体,减短模具寿命。
c.气体的排出主要取决于金属液的流动速度与流动方向,以及排溢系统的开设能否使气体顺畅排出,排气面积是否足够。
排气是否良好,将直接影响铸件的外形和强度。
d.模具温度的控制对铸件的质量产生很大的影响,同时影响生产的速度和效率,水口的合理设计可以对模具的温度分布起调节作用。
e.模具寿命除了取决于良好的钢材外,又与模具的工作状态有关,良好的水口系统设计也是为了使模具各部分热平衡处于最佳状态,而不是恶劣的状态下,这样才能得到压铸生产的最大经济效益。
3.2浇注系统位置的选择1.使金属液充型路径减少曲折,避免过多迂回,避免卷气,散失热量,压力损耗。
2.尽量使金属液流至各部位距离相等,如开中心水口。
3.使温度分布符合工艺要求(模温、铸件温度)、尽量选择最短流程。
4.尽量采用单个水口,避免各水口的射流产生对撞,当需多处水口时,考虑射流相互促进,避免卷气,能量损耗。
5.尽量避免正面冲击型芯或型壁,减少动能损耗、卷气、流向混乱、粘模。
6.减少铸件收缩变形的倾向,使易收缩部位得到补缩、增压。
7.有利于排气。
浇注系统设计方案

流道设计的优化与改进
减少流道阻力
采用大截面、短流程的流道
防止金属液氧化
采用密封式或保护气氛浇注系 统
提高充型能力
采用多浇口、分流道设计
降低能耗
采用热平衡设计,减少热量损 失
04 模具设计
模具材料的选用
01
02
03
耐热性
选择耐热性好的材料,如 钢材、铝合金等,以确保 模具在高温下件结构、生产批量、合金种类、浇注条件
适用场合
直浇道适用于中小型铸件的大批量生产;横浇道适用于大型铸件的 单件、小批量生产;内浇道适用于各种铸件
流道尺寸与形状的确定
流道截面积
满足金属液的流量要求,保证充 型能力
流道长度与宽度
根据铸件大小、浇注温度和速度确 定
流道高度
根据金属液的静压力头和浮力确定
调整工艺参数
调整浇注温度、注射压力和注射速度等工艺 参数,提高浇注质量和效率。
改进模具结构
优化模具冷却、排气和顶出机构,提高模具 使用寿命。
采用先进的浇注技术
如应用热流道技术、顺序阀控制等,提高生 产效率和浇注质量。
浇注系统方案的经济性分析
模具成本
生产成本
评估不同浇注系统方案对模具材料、加工 和装配成本的影响。
排溢系统设计
设计有效的排溢系统,以 排除模具内的气体和溢出 的金属液,防止产品产生 气孔和浇不足等缺陷。
模具冷却系统的设计
冷却水道设计
合理布置冷却水道,以提高模具的冷 却效果,减少冷却时间,提高生产效 率。
冷却介质选择
冷却水道密封
确保冷却水道的密封性,防止冷却液 泄漏,以保证生产安全和产品质量。
根据模具材料和使用条件,选择合适 的冷却介质,如水、油等。
第三章浇注系统设计
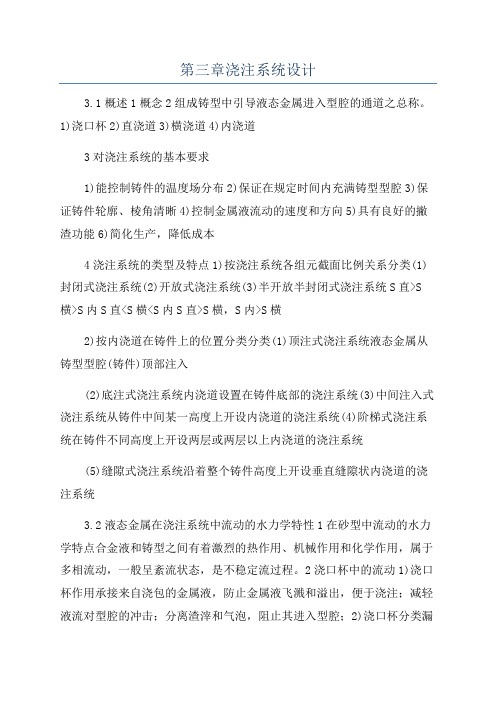
第三章浇注系统设计3.1概述1概念2组成铸型中引导液态金属进入型腔的通道之总称。
1)浇口杯2)直浇道3)横浇道4)内浇道3对浇注系统的基本要求1)能控制铸件的温度场分布2)保证在规定时间内充满铸型型腔3)保证铸件轮廓、棱角清晰4)控制金属液流动的速度和方向5)具有良好的撇渣功能6)简化生产,降低成本4浇注系统的类型及特点1)按浇注系统各组元截面比例关系分类(1)封闭式浇注系统(2)开放式浇注系统(3)半开放半封闭式浇注系统S直>S 横>S内S直<S横<S内S直>S横,S内>S横2)按内浇道在铸件上的位置分类分类(1)顶注式浇注系统液态金属从铸型型腔(铸件)顶部注入(2)底注式浇注系统内浇道设置在铸件底部的浇注系统(3)中间注入式浇注系统从铸件中间某一高度上开设内浇道的浇注系统(4)阶梯式浇注系统在铸件不同高度上开设两层或两层以上内浇道的浇注系统(5)缝隙式浇注系统沿着整个铸件高度上开设垂直缝隙状内浇道的浇注系统3.2液态金属在浇注系统中流动的水力学特性1在砂型中流动的水力学特点合金液和铸型之间有着激烈的热作用、机械作用和化学作用,属于多相流动,一般呈紊流状态,是不稳定流过程。
2浇口杯中的流动1)浇口杯作用承接来自浇包的金属液,防止金属液飞溅和溢出,便于浇注;减轻液流对型腔的冲击;分离渣滓和气泡,阻止其进入型腔;2)浇口杯分类漏斗形浇口杯(用于中、小型铸件)和盆(池)形浇口杯(用于中、大型铸件3)影响浇口杯内水平漩涡的主要因素是浇口杯内液面的深度,其次是浇注高度、浇注方向和浇口杯的结构等3直浇道中的流动1)直浇道的作用将来自浇口杯的金属液引入横浇道、内浇道或直接导入型腔,并提供充型过程所必需的压力2)直浇道形状通常是上大下小的圆锥形,有时为等截面圆柱形、上小下大的倒圆锥形、蛇形和片状形等形状3)液态金属在直浇道中存在充满式流动或非充满式流动两种流态4直浇道窝1)直浇道窝作用缓冲,缩短直浇道—横浇道拐弯处的高度紊流区;改善内浇道流量分布,减少横浇道—内浇道拐弯处的局部阻力系数和水头损失;浮出金属液中的气体。
铸造工艺学第3章 浇注系统设计

适用于各类灰铸铁件及球铁件。
封
A杯>A直<A横<A内
阻流截面设在直浇道下端,或在横浇道中, 或在集渣包出口处,或在内浇道之前设置
闭 A杯>A直>A集渣包出 的阻流挡渣装置处。
开口
阻流截面之前封闭,其后开放,故既有利 于挡渣,又使充型平稳,兼有封闭式与开
放 A直>A阻<A横后<A 放式的优点。
式内
适用于各类铸铁件,在中小件上应用较多, 特别是在一箱多件时应用广泛。目前铸造
金属液进入横浇道后,起初以较大的速度沿着它 的长度方向往前流动,直到横浇道的末端处,并 冲击该处的型壁,使液流的动能变为位能,在横 浇道末端处附近的金属液面就升高,形成金属浪 并开始返回移动,直到退回的金属浪与从直浇道 流出的液流相遇后,横浇道中的液面将同时上升 到充满为止。
3.1.4 液态金属在横浇道中的流动情况
横浇道起挡 渣作用应 具备的条 件
横浇道必须呈充满状态
液流的流动速度宜低于渣 粒的悬浮速度 液流的紊流搅拌作用要尽 量小
应使夹杂物有足够的时间上浮到金属 液顶面,横浇道的顶面应高出内浇道 吸动区一定距离,末端应加长;
内浇道和横浇道应有正确 的相对位置。
3.1.4 液态金属在横浇道中的流动情况
提向横浇道挡渣能力的主 要途径是改变横浇道的结 构以增加流程中的阻力, 减慢金属液的流速,减少 紊流搅拌作用。常见的方 法有以下几种: 1) 缓流式浇注系统
图3-14 上台面铸件的倾斜浇注
3.3.2 浇注系统的计算
(二)阻流组元(或内浇道)截面积的计算及各组元 之间的比例关系的确定 阻流组元截面(简称阻流截面)的大小实际上反映了浇 注时间的长短。在一定的压头下阻流截面大,浇注时 间就短,所以阻流截面的大小对铸件质量的影响与浇 注时间长短的影响基本一致。生产中有各种确定阻流 截面尺寸的方法和实用的图、表,大多都是以水力学 原理为基础的,此处着重介绍水力学计算法。
第三章 浇注系统的设计与计算
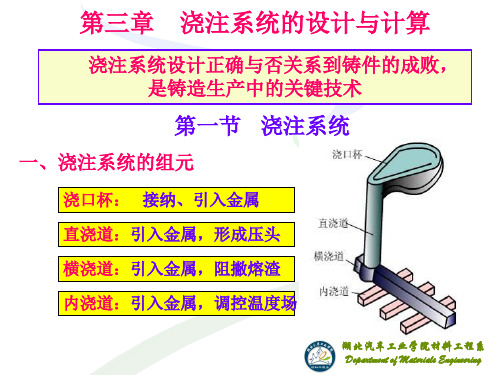
应用:
主要用于结构复杂的各 种黑色金属铸件和易氧化 的有色合金铸件。
汽缸头
湖北汽车工业学院材料工程系 Department of Materials Engineering
中间浇注应用广泛
中间浇注综 合有顶注式和 底注式的优缺 点; 内浇道、横 浇道设在分型 面上,造型方 便。
湖北汽车工业学院材料工程系 Department of Materials Engineering
第三章
浇注系统的设计与计算
浇注系统设计正确与否关系到铸件的成败, 是铸造生产中的关键技术
第一节 浇注系统
一、浇注系统的组元
浇口杯: 接纳、引入金属
直浇道:引入金属,形成压头
横浇道:引入金属,阻撇熔渣 内浇道:引入金属,调控温度场
湖北汽车工业学院材料工程系 Department of Materials Engineering
球墨铸铁呈 “糊状凝固” , 冒口的有效补缩距离较灰铸铁小 , 其不同条件下的湿型试验数据参见下表。
铸件壁厚 δ/mm 6.35 12.70 水 平 补 缩
湿 型 —— 101.6-114.3 湿 型 31.75 101.6 湿 型 —— 88.9
垂直补缩
壳型 —— 88.9
15.86
25.4 38.1
复习题
1.浇注系统由哪些部分组成?分别说明各个组元的 作用? 2.比较顶注式和底注式浇注系统的优缺点。 3.比较封闭式和开放式浇注系统的优缺点。
4 . 如何提高横浇道的撇渣效果?
5. 内浇道在铸件浇铸中能够起到哪些重要作用? 6.确定内浇道位置要注意哪些具体问题? 湖北汽车工业学院材料工程系
Department of Materials Engineering
浇注系统的设计和计算实例

油杯铸件的流量系数μ按文献[3]表 3-4 取值见表 10-4。
第7页
浇注系统设计和计算实例
铸铁及铸钢的流量系数μ值 种类 湿型 铸铁 铸钢 大 0.35 0.25
铸型阻力 中 0.42 0.32
小 0.5 0.42
流量系数μ值查得μ = 0.5, 按文献[3]表 3-5 进行修正: ① 油杯铸件浇注温度为 1330℃,浇注温度提高 50℃,μ值+0.05;
= 1.07������������2 0.31 × 0.5 × 2.18 × √7.38 油杯铸件采用的是封闭式浇注系统,阻流截面在内浇道上,所以内浇道的 总结面积为 1.07cm2。
1.1 选择浇注系统类型
油杯铸件为铸铁的湿型小件,查文献[2]表 3-1 浇注系统按各单元面积比例 分类,如表 9-1 所示。 表 9-1 浇注系统按各单元面积比例分类 截面比例关系 特点及应用 ������杯 > ������直 > ������横 > ������内 阻流截面在内浇道上。浇注开始后,金属液容易 充满浇注系统; 挡渣能力较强,但充型液流的速度较快,冲刷力 大,易产生喷溅; 一般的说金属液消耗少,且清理方便,应用于铸 铁的湿型小件及干型中、大件
I
浇注系统设计和计算实例
1
浇注系统位置的选择
浇注系统是铸型中液态金属流入型腔的通道,主要由浇口杯、直浇道、横 浇道、和内浇道四个部分组成。浇注系统设计的合理与否对铸件质量影响很 大,容易引起各种类型的铸造缺陷,如:浇不足、冷隔、冲砂、夹渣、夹杂、 夹砂等铸造缺陷。设计时应根据铸件的结构特点、合金种类、技术要求合理地 设计浇注系统。设计浇注系统应遵守以下原则: (1)引导金属液平稳、连续地充型,避免卷气、金属氧化物夹杂和冲刷型 芯; (2)充型过程中流动的方向和速度可以控制,保证铸件轮廓清晰、完整; (3)在合适的时间内充满型腔,避免形成夹砂铸件补缩、防止铸件变形、裂纹等 缺陷; (5)具有挡渣、溢渣能力,净化金属液; (6)浇注系统应当简单、可靠,减少金属液消耗,便于清理。
第三章 浇注系统设计
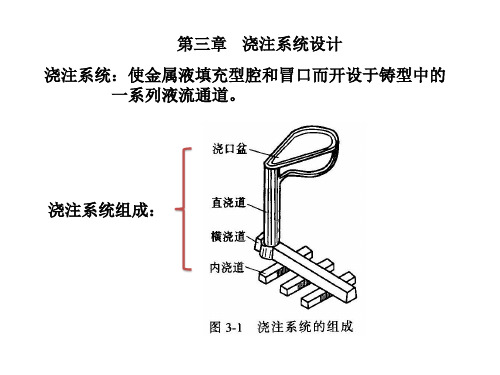
m Nnq
m —— 浇注金属质量(kg);N —— 同时浇注的浇包数; n —— 单个浇包的包孔数。
四、铸造非铁合金的浇注系统
特点:密度小、熔点低、热容量小而热导率大,且极 易氧化和液态吸气性强。 常见铸造缺陷:非金属夹杂、浇不到、冷隔、气孔、 缩孔、缩松及裂纹、变形等。
设计非铁合金浇注系统应注意: 非铁合金降温快,应快浇。 1)浇注温度不高,对 型砂的热作用较轻。
二、计算举例(浇注系统设计方法和步骤) 图3-19为灰铸铁件的垂直分型浇注系统的结构形 式,即模板布置简图。
1.绘制模板布置简图 模板布置来自于工艺设计方案和参照造型机标准模 板尺寸及合理吃砂量(图中A、B、C三个尺寸)等。据此 确定出各层铸件内浇道的金属压力头为: h1 =100mm; h2 =250mm; h3 =350mm。 2.计算型内金属质量m 每个铸件质量 2kg,共布置12件。铸件工艺出品率 (灰铁件)按70%估计,则型内金属质量(即铁液质量 数)为2×12 kg / 0.7 = 34.3 kg。
3.确定浇注时间和浇注速度q 造型机产率为300箱/h,节拍12s/型。据表3-8查出 浇注时间为8s。约用2s充满浇注系统,则充填单个型腔的 净浇注时间为6s。每个型腔的浇注速度应为2kg/6s≈0.33 kg/s。
4.选用浇口杯 根据铸型的浇注速度,参照表3-7,可查出浇口杯 尺寸。 如用手工浇注,使用4号浇口杯,铁液积存5.5kg; 如用自动浇注,使用2号浇口杯,铁液积存4kg。
A直: A横: A内=1:2:4
第二节
浇注系统组元中金属液的流动特性及组元设计
一、浇口杯(盆)
1.漏斗形浇口杯
特点:漏斗形浇口杯结构简 单,制作方便,其本身消耗 金属液少。 适用:小型铸件,在机器造 型中广泛使用。 杯底安放滤孔芯,可挡 渣并对金属液起缓冲作用。
注塑模具设计之浇注系统的设计

浇注系统的设计1主流道的设计主流道是指浇注系统中从注射机喷嘴与模具浇口套接触处开始到分流道为止的塑料熔体的流经通道。
它的形状与尺寸对塑料熔体的流动速度和充模时间有较大的影响。
主流道通常设计在模具的浇口套中,为了让主流道凝料能顺利从浇口套中拔出,主流道设计成圆锥形,锥角a 取3度,流道的表面粗糙度Ra(1)主流道尺寸1)主流道长度:小型模具的L 主应小于等于60mm ,本次设计中取50mm.2)主流道小端直径:d=注射机喷嘴尺寸+(0.5~1)mm=(2+1)mm=3mm.(查课本P81表5.1)3)主流道大端直径:D=d+2L 主tana ≈8.24mm4)主流道球面半径:SR=注射机喷嘴球头半径+(1~2)mm=(12+2)=14mm.5)球面配合高度:h=3mm.(2)主流道的凝料体积222233=) 3.14/350 4.12+1.5+4.12 1.5=1329.5 1.333V L R r R r mm cm π++=⨯⨯⨯=主主主主主主(()(3)主流道当量半径4.12 1.5 2.8122R r Rn mm ++===(4)主流道浇口套形式由于注射机与高温塑料熔体及注射机喷嘴反复接触,易磨损。
因此,设计中常设计成可拆卸更换的浇口套。
主流道衬套为标准件可选购。
对材料的要求较严格,因而,尽管小型注射模可以将主流道浇口套与定位圈设计成一个整体,但考虑到上述因素,仍将其分开设计,以便于拆卸更换。
同时也便于选用优质钢材进行单独加工和热处理。
材料一般采用碳素工具钢(T8A 或T10A),热处理淬火表面硬度为50~55HRC.2分流道的设计分流道是指主流道末端与浇口之间的一段塑料熔体的流动通道。
分流道的作用是改变熔体流向,使其以平稳的流态均衡地分配到各个型腔。
(1)分流道的布置形式在设计时应考虑尽量减少在流道内的压力损失和避免熔体温度降低,同时还要考虑减小分流道的容积和压力平衡,因此,采用平衡式分流道。
《浇注系统设计》课件

与增材制造技术结合
优化浇注系统结构,提高生产效率和产品质量。
与物联网技术结合
实现浇注系统的远程监控和数据采集。
与人工智能技术结合
利用人工智能技术对浇注过程进行智能分析和优化。
THANKS
感谢观看
充型。
经济性原则
在满足使用要求的前提下,尽 量减少浇注系统的材料消耗和 加工成本。
可靠性原则
浇注系统应具有足够的强度和 刚度,能够承受金属液的冲刷 和压力。
易维护性原则
浇注系统应便于安装、调试和 维修,降低使用过程中的维护
成本。
设计流程
方案设计
根据需求分析,设计浇注系统 的结构形式和尺寸参数。
加工制造
开放式浇注系统
开放式浇注系统是指塑料或金属从进 料口直接流入模具型腔,没有溢流槽 的浇注系统。
封闭式浇注系统
封闭式浇注系统是指塑料或金属从进 料口流入模具型腔后,通过溢流槽将 多余的塑料或金属收集起来,并从溢 流槽中排出。
02
浇注系统的设计原则与 流程
设计原则
高效性原则
浇注系统应高效地完成浇注任 务,确保金属液快速、均匀地
溢流槽的设计
溢流槽位置
合理设置溢流槽的位置,以引导金属 液流向正确的方向,避免金属液溢出 模具。
溢流槽尺寸
根据金属液的流量和流动特性,设计 合适的溢流槽尺寸,以确保金属液能 够顺畅地流入溢流槽并排出模具。
排气槽的设计
排气槽位置
在模具的关键部位设置排气槽,以排除 气体,避免形成气孔和疏松等缺陷。
VS
01
新材料应用
探索和应用新型材料,提高浇注系 统的耐磨、耐高温等性能。
仿真பைடு நூலகம்拟技术
第三章 浇注系统的设计与计算[1]
![第三章 浇注系统的设计与计算[1]](https://img.taocdn.com/s3/m/0675f3f14693daef5ef73de4.png)
1)浇口杯应足够大; 2)严格控制浇注时间。
湖北汽车工业学院材料工程系 Department of Materials Engineering
3
计算实例:
1、绘制模板布置简图
各层铸件内浇道的金属压力头: h1=100mm; h2=250mm; h3=350mm。
2、计算型内金属质量 m /kg
普通冒口
顶冒口、暗冒口 侧冒口
特种冒口
大气压力冒口 发热冒口 保温冒口
铸铁件的 实用冒口
浇注系统当冒口 控制压力冒口
湖北汽车工业学院材料工程系 Department of Materials Engineering
4
3、冒口形状
球形
圆柱形(带斜度)
球顶圆柱形
腰圆柱形
暗腰圆柱形
4、冒口形式 a)铸钢件
湖北汽车工业学院材料工程系 Department of Materials Engineering
(二)按浇注系统各组元截面积的比例关系分
1、封闭式浇注系统
∑A内< ∑A横<A直 一般为 ∑A内:∑A横:A直=1:1.1:1.15
特点:
挡渣力强,金属消耗少,易清理;
充型流速高,易喷射冲砂;
用于不易氧化的金属。
第三章 浇注系统的设计与计算
浇注系统设计正确与否关系到铸件的成败, 是铸造生产中的关键技术
第一节 浇注系统 一、浇注系统的组元
浇口杯: 接纳、引入金属
直浇道:引入金属,形成压头 横浇道:引入金属,阻撇熔渣 内浇道:引入金属,调控温度场
湖北汽车工业学院材料工程系 Department of Materials Engineering
铸铁件流量系数
3.3.3 浇注系统设计与计算
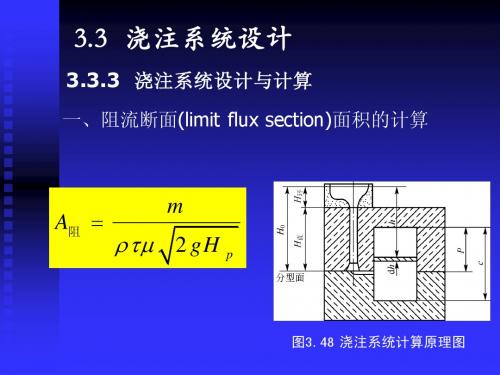
3.3.3 浇注系统设计与计算 一、阻流断面(limit flux section)面积的计算
m A阻 = ρτµ 2 gH p
图3.48 浇注系统计算原理图
3.3.3 浇注系统设计与计算 一、阻流断面(limit flux section)面积的计算
1) 平均静压头 的计算 平均静压头Hp的计算
H p = H 0 − p / 2c
2
图3.48 浇注系统计算原理图
一、阻流断面(limit flux section)面积的计算
H0的确定: 的确定
表3-3 压力角的最小值α
铸件壁厚δ/mm L/mm 3~5 5~8 8~15 15~2 0 20~2 5 25~3 5 35~4 5 00 3000 2800 根 据 具 体 情 况 确 定 6~7 6~7 6~7 7~8 7~8 8~9 8~9 8~9 5~6 5~6 6~7 6~7 6~7 6~7 7~8 7~8 5~6 5~6 5~6 6~7 6~7 6~7 6~7 6~7 5~6 5~6 5~6 6~7 6~7 6~7 6~7 6~7 4~5 4~5 4~5 5~6 5~6 5~6 5~6 5~6 4~5 4~5 4~5 4~5 4~5 5~6 5~6 6~7 用两个或更多 的直浇道浇注
V型min/mm·s-1 8~10 20~30 10~20 20~30 30~100
V上升=C/τ
4~10 1.5~4~
3.3.3 浇注系统设计与计算 一、阻流断面(limit flux section)面积的计算 二、各组元断面比例的选择 三、确定浇注系统断面尺寸的图表
吃砂量
2600 2400 2200 2000
3.3.3 浇注系统设计与计算 一、阻流断面(limit flux section)面积的计算
- 1、下载文档前请自行甄别文档内容的完整性,平台不提供额外的编辑、内容补充、找答案等附加服务。
- 2、"仅部分预览"的文档,不可在线预览部分如存在完整性等问题,可反馈申请退款(可完整预览的文档不适用该条件!)。
- 3、如文档侵犯您的权益,请联系客服反馈,我们会尽快为您处理(人工客服工作时间:9:00-18:30)。
∴
Mr = f Mc
f —冒口安全系数,
一般取f =1.2 。
湖北汽车工业学院材料工程系 Department of Materials Engineering
5
对于碳钢、低合金钢铸件
侧冒口 :Mc : Mn : Mr = 1 : 1.1 : 1.2 内浇道通过冒口:
湖北汽车工业学院材料工程系 Department of Materials Engineering
(二)按浇注系统各组元截面积的比例关系分
1、封闭式浇注系统
∑A内< ∑A横<A直 一般为 ∑A内:∑A横:A直=1:1.1:1.15
特点:
挡渣力强,金属消耗少,易清理;
充型流速高,易喷射冲砂;
用于不易氧化的金属。
Kc
r
c
;
τ = Mr 2 r Kr
∴
( ) ( ) Mr 2 ≥ Mc 2
Kr
Kc
湖北汽车工业学院材料工程系 Department of Materials Engineering
式中
Mr 、 Mc —冒口与被补缩铸件部位
的模数;
Kr、 Kc —冒口与被补缩铸件的
凝
固系数。
对于普通冒口, Kr =Kc,
依据铸件所需凝固方式和流动特性考虑。 同时凝固:
对于壁厚均匀的铸件,拟采用多个内浇道分散引入; 对于不均匀的铸件,则从薄壁处引入。
顺序凝固:
从厚壁处引入金属液。
湖北汽车工业学院材料工程系 Department of Materials Engineering
2
5、确定内浇道位置的几个具体问题
结构复杂的铸件,壁厚差别大的补缩区域则按顺 序凝固从厚处引入;整个铸件按同时凝固方式采 用多个内浇道充型。
二、对浇注系统的要求
足够的浇注速度,流动平稳,满足一定时间 内充满型腔; 防止冲砂,避免铸件出现夹砂 、冷隔等缺陷;
防止旋涡,避免吸气或金属过度氧化; 内浇道的位置和数量符合铸件所需凝固或补
缩原则; 结构合理,造型简单; 浇注系统本身消耗金属少。
湖北汽车工业学院材料工程系 Department of Materials Engineering
明边冒口 b)铸铁件
暗边冒口
湖北汽车工业学院材料工程系 Department of Materials Engineering
5、冒口位置
1、铸件热节上方或侧旁; 2、铸件最高最厚部位; 3、一个冒口同时补缩几
个铸件; 4、不选应力集中部位,
希望放在加工面上; 5、 用冷铁隔开冒口的
补缩范围。
湖北汽车工业学院材料工程系 Department of Materials Engineering
二 铸钢件冒口的设计与计算
冒口必须提供足够的金属 液,补偿铸件凝固的体收缩, 条件应有:
即 Vr =Vcε/(η-ε)
ε (Vc + Vr ) + Ve ≤ Vrη
式中: Vr —冒口体积; Vc—铸件体积; Ve—型壁移动所扩大 的体积;
ε—体收缩率;
η—冒口补缩效率。
湖北汽车工业学院材料工程系 Department of Materials Engineering
—阻流(最小)截面积 的计算 。
阻流(最小)组元指浇
注系统中最小截面积的浇
道,一般为内浇道,即
m A阻= ρτμ 2gHp
2
H =H −P
P
0
2C
湖北汽车工业学院材料工程系 Department of Materials Engineering
1)金属充填型腔时平均静压头 Hp 的计算
根据水力学相关公式推导得知 ,
上底宽11mm;下底宽22mm;高22mm 。
实际:S分直=363mm2。 7、 水平横浇道尺寸 S横=1.3×363 mm2=472 mm2。
选上底宽12.5mm;下底宽25mm;高25mm;
实际截面积469mm2。
湖北汽车工业学院材料工程系 Department of Materials Engineering
三 、浇注系统的类型
(一)按内浇道在铸件上的位置分
1. 顶注式
图中:
a) 普通式
b) 楔形式
c) 压边式
d) 雨淋式
e) 搭边式
湖北汽车工业学院材料工程系 Department of Materials Engineering
顶注式的优缺点
优点
压头大,流动阻力小,能 够减少浇不足、冷隔缺陷;温度 分布上高下低,铸件补缩效果好
湖北汽车工业学院材料工程系 Department of Materials Engineering
(一)应用 模数法计算冒口尺寸
1、模数概念
冷凝物体的模数是它的体积V 和散热面积A 之比。
即
M=V/A
计算原理是基于冒口 的凝固时间τr 大于铸件补缩部
位的凝固时间τc ,
即 而
( ) ( ) τc=
τ ≥ τ Mc 2
缺点
对型腔底部冲击力大,易 激溅、氧化、卷入空气,可造成 砂眼、铁豆、气孔、氧化夹渣等 缺陷。
湖北汽车工业学院材料工程系 Department of Materials Engineering
优点:
底注式的优缺点
充型平稳。横浇道、内 浇道充满时利于挡渣;能 够减少金属氧化。
缺点:
温度分布下高上低,铸 件补缩效果不好;
配套措施:
1)浇口杯应足够大; 2)严格控制浇注时间。
湖北汽车工业学院材料工程系 Department of Materials Engineering
3
计算实例:
1、绘制模板布置简图
各层铸件内浇道的金属压力头: h1=100mm; h2=250mm; h3=350mm。
2、计算型内金属质量 m /kg
7.如何应用奥赞(Osann)公式计算阻流截面积? 如何确定或计算式中各个工艺参数?
8.一铸铁件重 5 吨,平均壁厚为30毫米,试求浇注 时间?若为铸钢件,其浇注时间 应为多少?
第三节 冒口、冷铁与铸肋
一 概述 1、冒口的作用:补缩 、排气、集渣
2、冒口种类
冒口种类
湖北汽车工业学院材料工程系 Department of Materials Engineering
内浇道附近易于过热, 易发生缩松和晶粒粗大等 缺陷;
铸件顶部、边远处容易 形成浇不到,冷隔等缺陷。
应用:
主要用于结构复杂的各 种黑色金属铸件和易氧化 的有色合金铸件。
汽缸头
湖北汽车工业学院材料工程系 Department of Materials Engineering
中间浇注应用广泛
中间浇注综 合有顶注式和 底注式的优缺 点;
小结—浇注系统设计步骤
选择浇注系统类型; 确定内浇道在铸件上的位置、数目和金属引入方
向; 决定直浇道高度(一般取决于砂箱高度); 计算浇注时间并核算金属在型内的上升速度; 计算阻流(最小)截面积; 确定组元截面积比; 于铸造工艺上绘制浇注系统结构及组元截面图。
湖北汽车工业学院材料工程系 Department of Materials Engineering
普通冒口
顶冒口、暗冒口 侧冒口
特种冒口
大气压力冒口 发热冒口 保温冒口
铸铁件的 实用冒口
浇注系统当冒口 控制压力冒口
湖北汽车工业学院材料工程系 Department of Materials Engineering
4
3、冒口形状
球形
圆柱形(带斜度)
球顶圆柱形
腰圆柱形
暗腰圆柱形
4、冒口形式 a)铸钢件
2)浇注时间的确定
浇注快慢对铸件质量有
重大影响。 浇注时间主要根据合
金性质靠生产经验选择。 球墨铸铁件的浇注时间参 照图示曲线查询。 一般
采用快浇。 对于收缩大的合金
件,采用慢浇有利于补缩。
湖北汽车工业学院材料工程系 Department of Materials Engineering
3)流量系数μ的确定
铸铁件流量系数
铸钢件流量系数
球墨铸铁件流量系数
湖北汽车工业学院材料工程系 Department of Materials Engineering
计算步骤:
以内浇道为阻流(最小)截面,用奥赞(Osann)公式
S内
=
ρτμ
m 2gH p
计算每个内浇道截面积。
式中Hp可用浇口杯中液面到内浇道中心的距 离Ho计算。
对于从分型面注入:
式中
Hp = Ho – P 2 / 2C
Ho —阻流面以上的金属液静压头,mm ;
P —阻流面以上的型腔高度,mm ;
C—铸件高度, mm ; 对于
顶注式 : 底注式 :
P=O , Hp = Ho
Hp = Ho - C/ 2
湖北汽车工业学院材料工程系 Department of Materials Engineering
4、 选用浇口杯
根据铸型的浇注速度,使用4号浇口杯,铁液积存5.5 kg; 5、分别计算或由内浇道计算诺谟图查各层内浇道截面积:
(流量系数取 μ=0.5)
S1=70mm2 ; S2=45mm; S3=38mm2。 6、分直浇道截面积
∑S内 =2×(70+45+38)=306mm2, S分直=1.2×S内=306×1.2=367mm2 分直浇道的截面尺寸:
湖北汽车工业学院材料工程系 Department of Materials Engineering
2、开放式浇注系统
∑A内> ∑A横>A直
开放式浇注系统初期各组元不可能全充满, 撇渣能力较差,充形流速不高;