铝板带冷轧轧制油检测分析
铝带可逆冷轧机轧制油润滑控制系统研究
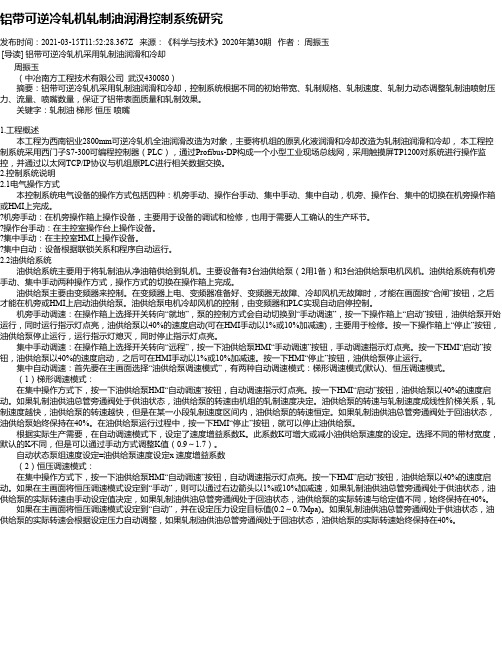
铝带可逆冷轧机轧制油润滑控制系统研究发布时间:2021-03-15T11:52:28.367Z 来源:《科学与技术》2020年第30期作者:周振玉[导读] 铝带可逆冷轧机采用轧制油润滑和冷却周振玉(中冶南方工程技术有限公司武汉430080)摘要:铝带可逆冷轧机采用轧制油润滑和冷却,控制系统根据不同的初始带宽、轧制规格、轧制速度、轧制力动态调整轧制油喷射压力、流量、喷嘴数量,保证了铝带表面质量和轧制效果。
关键字:轧制油梯形恒压喷嘴1.工程概述本工程为西南铝业2800mm可逆冷轧机全油润滑改造为对象,主要将机组的原乳化液润滑和冷却改造为轧制油润滑和冷却,本工程控制系统采用西门子S7-300可编程控制器(PLC),通过Profibus-DP构成一个小型工业现场总线网,采用触摸屏TP1200对系统进行操作监控,并通过以太网TCP/IP协议与机组原PLC进行相关数据交换。
2.控制系统说明2.1电气操作方式本控制系统电气设备的操作方式包括四种:机旁手动、操作台手动、集中手动、集中自动,机旁、操作台、集中的切换在机旁操作箱或HMI上完成。
机旁手动:在机旁操作箱上操作设备,主要用于设备的调试和检修,也用于需要人工确认的生产环节。
操作台手动:在主控室操作台上操作设备。
集中手动:在主控室HMI上操作设备。
集中自动:设备根据联锁关系和程序自动运行。
2.2油供给系统油供给系统主要用于将轧制油从净油箱供给到轧机。
主要设备有3台油供给泵(2用1备)和3台油供给泵电机风机。
油供给系统有机旁手动、集中手动两种操作方式,操作方式的切换在操作箱上完成。
油供给泵主要由变频器来控制。
在变频器上电、变频器准备好、变频器无故障、冷却风机无故障时,才能在画面按“合闸”按钮,之后才能在机旁或HMI上启动油供给泵。
油供给泵电机冷却风机的控制,由变频器和PLC实现自动启停控制。
机旁手动调速:在操作箱上选择开关转向“就地”,泵的控制方式会自动切换到“手动调速”,按一下操作箱上“启动”按钮,油供给泵开始运行,同时运行指示灯点亮,油供给泵以40%的速度启动(可在HMI手动以1%或10%加减速),主要用于检修。
铝板带冷轧轧制油检测分析

一、目的:检测冷轧轧制油性能二、范围:冷轧轧制油三、职责:四、内容:(一)运动粘度(参照GB/T265)1.1 仪器1.1.1 毛细管粘度计,定期检定并确定系数每次试验时,根据样品粘度范围选择不同毛细管内径的粘度计。
被测样品在选用的粘度计里流出时间不得少于200s1.1.2 恒温浴:附设自动搅拌装置和能够准确调节温度的热电装置(温控精度0.1℃)1.1.3 玻璃水银温度计,分度为0.1℃(定期检定)1.1.4 秒表,分度为0.1s,(定期检定)1.2试剂及溶液1.2.1石油醚,60~90℃,分析纯1.2.2无水乙醇,化学纯1.2.3铬酸洗液1.3试验准备1.3.1对油品来说,若试样含有水或机械杂质时。
在试验前必须经过脱水处理,并过滤机械杂质1.3.2对水基样品,若试样有杂质也需过滤1.3.3 粘度计必须清洁干燥。
若沾有污垢,则用石油醚(水基样品不用)、铬酸洗液、水、乙醇依次洗涤,烘干或倒置自然晾干1.3.4 开启恒温浴,将温度设定至测量所需的温度。
同时选择适宜量程并校准的温度计浸入恒温浴中,用夹子固定在支架上,试验的温度必须保持恒定到±0.1℃。
1.4试验步骤1.4.1 装样:在内径符合要求且清洁干燥的毛细管粘度计内装入试样,装样时,将橡皮管套在粗管的小玻璃支管上,并用食指堵住粗管口,将粘度计倒置,把毛细管的长玻璃管伸入样品内,用吸耳球通过橡皮管将样品吸到第二个刻度(注意不要使管身、扩张部分的液体发生气泡和裂隙)提起粘度计正放,擦干净外壁所附着的样品,并从支管上取下橡皮管套在有毛细管的长玻璃管口。
1.4.2 恒温:将装有试样的粘度计浸入事先准备妥当的恒温浴中,并用夹子将粘度计固定在支架上,将粘度计调整成为垂直状态。
试验温度保持恒定在±0.1℃,恒温样品约15min。
1.4.3 测量:将样品吸至粘度计扩张球内,使试样液面稍高于刻度标线,注意不要让毛细管粘度计和扩张球内产生气泡或裂隙,计下试样从第一刻度标线到第二刻度标线间的流出时间。
用气相色谱法分析轧制油烷烃分布及添加剂含量

./.#’ ./.$’ ./.$’ ./.!( ./.12 ./.#0 ./.!2 ./.11 ./.!( ./.#2 ./.## ./.(( ./.#1 ./.1’ ./.-# ./.$./.0. ./.$2 ./.#./#’
%&’(#! 中
的百分比
!"#
定量分析讨论 (#)校正归一化法一般用于基础油和较理想的轧
./1’ ./’( #/1’ $/.$/-! ./12 #/.#/-1 #/’$ $/10 #/.( $/’0 1/’( 0/.’ 2/’( #/.( !/.( 1/’(/’0 2/’-
./10 #/.! #/-! #/’0 $/10 ./-$ ./’( #/-! #/’$ $/1’ #/.( !/#. 1/’1 0/.( 2/’’ #/.0 !/.1 1/’0 (/’0 2/’0
图% 系列色谱图
相近的 0() 醇, 配制成铝箔轧制油, 再加入与 0() 醇百
$..#,567/ $’8 9 ##
轻
合
金 加
工 技 术
表!
油品
$-
分 比 相 近 的 "#( 醇 。 冷 轧 油 内 标 样 品 : %&’(#- 或
)*&+,&#- 为基体,精确加入与实际轧制油中含量相
近的 "#( 醇, 配制成冷轧轧制油, 再加入与 "#( 醇百分 比相近的 "#- 醇。 (!) 实验操作同 $/#314。
./-$ ./’0 #/-$ #/’0 $/-./-. ./’2 #/1#/’’ $/10 #/.1 !/.( 1/’0 (/’2 ’/.( #/.’ !/.( -/.$ (/’’ ’/.0
./-$ #/.# #/-$ #/’’ $/-1 ./12 ./’2 #/1#/’# $/1( #/.( !/.0 1/’1 (/’2 2/’0 #/.$ !/.( 1/’( (/’2/’0
[2017年整理]关于铝加工轧制油性能指标比较和选择标准探讨
![[2017年整理]关于铝加工轧制油性能指标比较和选择标准探讨](https://img.taocdn.com/s3/m/15f3aa9603d276a20029bd64783e0912a2167c89.png)
关于铝加工轧制油性能指标比较和选择标准探讨刘壮怀,周东伟,许云杰,徐亮(道达尔石油(广州)有限公司,上海,200001)摘要:作为铝轧工艺中三大关键技术之一的工艺润滑技术,一直受到铝加工企业的关注。
其中,轧制油性能又对润滑效果起着关键作用。
因此,长期以来铝加工企业和油品供应商一直致力于对不同类型轧制油的性能和影响因素进行研究。
本文对国内外使用的铝轧轧制油的类型和性能作了比较和分析,探讨了影响轧制油性能的主要因素。
关键字:铝冷轧轧制油添加剂工艺润滑是铝材轧制过程中不可缺少的重要技术之一,直接影响铝材成品的质量和企业经济效益。
工艺润滑是一个非常复杂的技术领域,涉及物理、化学、摩擦学等学科。
目前铝轧工艺润滑主要通过使用轧制油来实现。
轧制油一般以基础油为主体,辅以少量的添加剂、抗氧剂等组成。
在铝材压延成型过程中,金属基体连续变形,不断产生新的金属表面,新表面的物理化学性能与原金属表面不同,具有很高的化学活性,极易和轧辊粘着。
轧制油要在加工界面上迅速铺展,形成一层均匀、不易破裂的润滑油膜,才能发挥较好的润滑和“压烫”效果。
1. 衡量轧制油性能的主要指标和不同组分类型轧制油的性能特点差异1.1衡量轧制油性能的主要指标和它们对轧制过程的影响随着铝加工企业对最终产品质量的要求不断提高,对轧制油的各项技术指标的要求也越来越严格。
一般来说,运动粘度、密度、赛波特色度、馏程(初馏点和干点)、闭口闪点、苯胺点、芳烃含量、硫含量、水分、酸值、氧化稳定性、退火清洁性和食品、环保认证是衡量轧制油质量高低的主要指标。
1.1.1运动粘度、粘度指数、闭口闪点和馏程粘度反应了液体的内摩擦,当油受外力作用发生相对移动时,油分子产生的阻力使油品无法继续顺利移动,其阻力的大小就称为粘度。
因此,它是油品流动性能的主要指标,比如很多润滑油就是以其粘度来分牌号的。
粘度指数(Viscosity Index)是表示油品的粘度随着温度变化而变化的速率大小。
铝冷轧大量使用回收油润滑性能变化测试

铝冷轧大量使用回收油润滑性能变化测试发表时间:2020-08-19T15:41:48.877Z 来源:《基层建设》2020年第12期作者:曹永国1 李学兵2 张慧财3 杨杰4 [导读] 摘要:本文采用实验的方法,测试了回收油对轧制油工艺油润滑性能的影响,并通过补充特定添加剂的方式,保证了工艺油理化指标及轧制过程的稳定性。
1身份证号码:34292119790113XXXX;2身份证号码:13010219800508XXXX;3身份证号码:13072819840203XXXX;4身份证号码:13010219821122XXXX;1. 河南中孚高精铝材有限公司河南郑州 450000;2,3,4. 河北省金属加工润滑材料工程技术研究中心河北石家庄050800摘要:本文采用实验的方法,测试了回收油对轧制油工艺油润滑性能的影响,并通过补充特定添加剂的方式,保证了工艺油理化指标及轧制过程的稳定性。
关键词:回收油;轧制;工艺润滑;摩擦系数0 引言近年来,铝加工行业响应国家“绿色环保”、“节能减排”的政策号召,加之行业竞争惨烈形势下的成本压力,轧制工艺油的“回收油”再利用越来越普遍。
而由于“回收油”与原生“基础油”的组分及性能上的差异性,给轧制过程中的质量控制带来种种困扰,本文即描述:从传统工艺油构成与加“回收油”工艺油的两个维度进行研究测试过程,从结构的角度找性能的差异性,力求找到使用“回收油”出现诸如“润滑性下降”等问题的原因,并为得到有效解决提供数据基础。
1 实验1.1 实验方法将铝加工行业冷轧过程中普遍使用D100基础油、回收油、醇酯-12添加剂、回收油补充添加剂作为原料,按不同比例配制成工艺油,并对工艺油进行PB及摩擦系数测试。
1.2原料指标为方便描述,对以下基础油和添加剂进行编号。
其中,A——行业普遍用铝板带冷轧添加剂;B——行业普遍用D100基础油;B-1——行业普遍回收油;A-1——针对回收油补充添加剂。
铝板带箔轧制过程中轧制油的使用和管理

铝板带箔轧制过程中轧制油的使用和管理"##$%&’(%)* ’*+ ,’*’-./.*( )0 1)$$%*- 2%$ +34%*- "$3/%*3/ 5(4%#1)$$%*- 6)347.李亚红, 刘桂云B C D E AF=GH ? B C I 2J K AL J G( 东北轻合金有限责任公司,黑龙江 哈尔滨 !899:9;摘要:阐述了铝板、带、箔材在冷轧过程中轧制油的日常管理及监测,并提出了轧制不同产品所用不同轧制油及添加剂 的类型。
关键词:基础油;添加剂M 铝板带箔轧制 中图分类号:N 200)文献标识码:3文章编号:&$$’9’*0() *$$0)$79$$&79$*铝板、带、箔材轧制过程中,轧制油的管理极为重要。
轧制油不仅起到润滑、冷却作用,也起到洗涤作用。
轧制过程中产生的氧化物、铝屑以及空气中落入的尘 土等,都会被轧制油带走。
如果轧制油得不到有效过 滤,那么随着轧制的进行,油的污染将会越来越严重。
导致铝带卷表面出现划痕和油污,铝箔出现针孔。
轧制 油中存在 /! 4 以上的颗粒是使轧制油发生黑化的原 因5&6,颗粒数量越多,黑化越严重。
轧制油的组成是在基 础油中加入添加剂,以增加其油膜强度,有利于轧制的 顺利进行,而且,轧制不同的产品应采用不同种类的添 加剂。
目前,国内常用的轧制油过滤系统为板式过滤 器,用硅藻土作为助滤剂,无纺布作介质。
免铝箔表面产生油斑的要求。
( +)粗、精轧时共用一种低粘度的基础油,调整添 加剂的含量来满足粗、精轧不同的工艺要求。
这样做, 从轧制油的管理上比较方便,也是可行的9!,+:。
表 ! 为铝板、带轧机所使用的 ;!** 轧制油和箔材 轧机使用的 ;/* 轧制油的基础油的理化性能指标。
表 ! 不同轧制油的基础油的性能指标检验项目 "&$$ 检验方法"#$ 密度( !"!)#$%·&’(馏程 #! 闪点 #! 运动粘度( )*!)#&&+·,’!硫 # &%·$%’!灰分 # - 外观 杂质和水%*$(/ *0)+*/) ,&$* *(&-*(1) .$() .$($$)无色、无味、透明 无23#.!//)’+*** 01#.2"(2’34 01#.+2!’/(( 3!) 01#.+2"’// 56#.*+"(’3+ 01#."*/’/(" 3!)目测 目测%&’() *$$+*)) ,%$ &())-&(’) .$() .$($$)无色、无味、透明 无轧制油和添加剂的组分我公司的铝板、带、箔材轧机所使用的轧制油的基础油均为低硫、低芳烃类。
铝材冷轧过程工艺控制及产品表面质量的实验研究

铝材冷轧过程工艺控制及产品表面质量的实验研究铝材冷轧过程工艺控制及产品表面质量的实验研究王录1,孙建林1,马艳丽1,高雅1( 1北京科技大学材料科学与工程学院,北京100083)摘要:铝板冷轧过程中,对轧制油中添加剂的含量及种类加以控制,可以改善铝板表面质量。
本次实验中初选出几种复合添加剂用来轧制相同厚度的铝板,并对轧后铝材表面质量进行分析。
结果显示轧制润滑可以减小摩擦,提高生产效率;同时又使得轧后铝板表面粗糙度降低,表面质量明显改善。
当润滑状态处于边界润滑时,添加剂会发挥其作用;添加剂不同,其在铝材轧制过程中发挥的作用也不同。
综合比较可以看出,复合添加剂比单独加入一种添加剂的油膜强度高,混合醇型与醇酯型添加剂的油膜强度相当,但醇酯型添加剂无论在减摩降压效果,还是成品表面质量改善上都能产生更好的效果。
关键词:铝材;轧制;表面质量;添加剂Experimental study on cold-rolling process control and Surface Quality of aluminumWang Lu1, Sun Jian-lin1, Ma Yan-li1, Gao Ya1(1 School of Materials Science and Engineering, University of Science and Technology Beijing, Beijing 100083)Abstract:In the processing of cold rolling aluminum, the content and species of rolling oil within different additives can be controlled to improve the quality of aluminum. It was used in this experiment for rolling the same thickness aluminum by adopting combination additives selected primarily. A deep analysis and evaluation of surface quality has been done on investigation data of this experiment. The results indicate that, rolling with lubrication can reduce friction and improve production efficiency. The surface roughness and quality of aluminum after rolling are also decreased at same time. Lubrication additives will have donetheir work when the lubrication states are mainly in boundary lubrication. Different lubricants exert their own function in the rolling process. The comparison results show that the oil-film strength of compound additives is superior to that of single additives, and the oil-film strength of additives with alcohol-ester is equivalent to that of mixed alcohol. Nevertheless, the additive containing alcohol-ester can produce better effect, both in the aspects of antifriction and the improvement of surface quality. Key words:aluminum, cold rolling, surface quality, lubrication additive自国务院节能减排方案的提出,人们愈加意识到“十一五”期间降低能源消耗和减少污染排放的重要性,迫切需要一种“节能减排型”润滑剂,因而需要润滑剂不仅具有合适的粘度、良好的退火清洁度等性能,还要能够有效地减小轧后产品表面粗糙度、降低能源和减少环境污染等。
冷轧铝板轧制油中基础油对轧制效果的影响
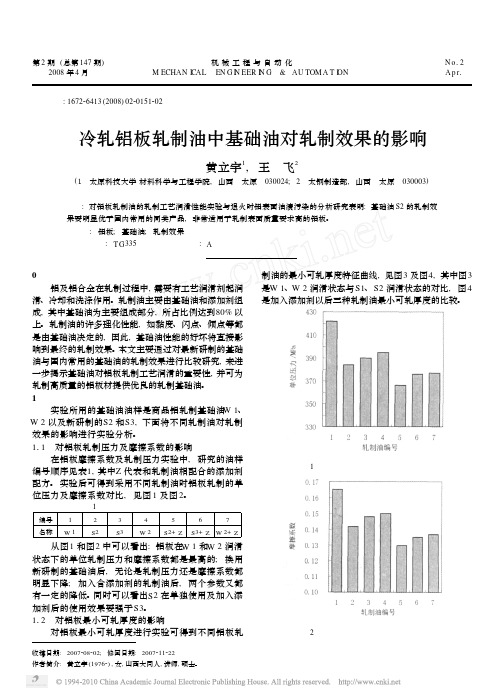
位压力及摩擦系数对比, 见图 1 及图 2。
表 1 实验中轧制油编号及名称
编号 1
2
3
45Leabharlann 67名称 W 1
S2
S3
W 2 S2+ Z S3+ Z W 2+ Z
从图1 和图2 中可以看出: 铝板在W 1 和W 2 润滑 状态下的单位轧制压力和摩擦系数都是最高的; 换用 新研制的基础油后, 无论是轧制压力还是摩擦系数都 明显下降; 加入含添加剂的轧制油后, 两个参数又都 有一定的降低。同时可以看出S2 在单独使用及加入添 加剂后的使用效果要强于 S 3。 112 对铝板最小可轧厚度的影响
油与国内常用的基础油的轧制效果进行比较研究, 来进 一步揭示基础油对铝板轧制工艺润滑的重要性, 并可为 轧制高质量的铝板材提供优良的轧制基础油。
1 实验过程 实验所用的基础油油样是商品铝轧制基础油W 1、
W 2 以及新研制的S2 和S3, 下面将不同轧制油对轧制 效果的影响进行实验分析。
111 对铝板轧制压力及摩擦系数的影响 在铝板摩擦系数及轧制压力实验中, 研究的油样
(1. 太原科技大学 材料科学与工程学院, 山西 太原 030024; 2. 太钢制造部, 山西 太原 030003)
摘要: 对铝板轧制油的轧制工艺润滑性能实验与退火时铝表面油渍污染的分析研究表明: 基础油 S2 的轧制效 果要明显优于国内常用的同类产品, 非常适用于轧制表面质量要求高的铝板。 关键词: 铝板; 基础油; 轧制效果 中图分类号: T G335 文献标识码: A
第 2 期 (总第 147 期) 2008 年 4 月
- 1、下载文档前请自行甄别文档内容的完整性,平台不提供额外的编辑、内容补充、找答案等附加服务。
- 2、"仅部分预览"的文档,不可在线预览部分如存在完整性等问题,可反馈申请退款(可完整预览的文档不适用该条件!)。
- 3、如文档侵犯您的权益,请联系客服反馈,我们会尽快为您处理(人工客服工作时间:9:00-18:30)。
一、目的:检测冷轧轧制油性能二、围:冷轧轧制油三、职责:四、容:(一)运动粘度(参照GB/T265)1.1 仪器1.1.1 毛细管粘度计,定期检定并确定系数每次试验时,根据样品粘度围选择不同毛细管径的粘度计。
被测样品在选用的粘度计里流出时间不得少于200s1.1.2 恒温浴:附设自动搅拌装置和能够准确调节温度的热电装置(温控精度0.1℃)1.1.3 玻璃水银温度计,分度为0.1℃(定期检定)1.1.4 秒表,分度为0.1s,(定期检定)1.2试剂及溶液1.2.1石油醚,60~90℃,分析纯1.2.2无水乙醇,化学纯1.2.3铬酸洗液1.3试验准备1.3.1对油品来说,若试样含有水或机械杂质时。
在试验前必须经过脱水处理,并过滤机械杂质1.3.2对水基样品,若试样有杂质也需过滤1.3.3 粘度计必须清洁干燥。
若沾有污垢,则用石油醚(水基样品不用)、铬酸洗液、水、乙醇依次洗涤,烘干或倒置自然晾干1.3.4 开启恒温浴,将温度设定至测量所需的温度。
同时选择适宜量程并校准的温度计浸入恒温浴中,用夹子固定在支架上,试验的温度必须保持恒定到±0.1℃。
1.4试验步骤1.4.1 装样:在径符合要求且清洁干燥的毛细管粘度计装入试样,装样时,将橡皮管套在粗管的小玻璃支管上,并用食指堵住粗管口,将粘度计倒置,把毛细管的长玻璃管伸入样品,用吸耳球通过橡皮管将样品吸到第二个刻度(注意不要使管身、扩部分的液体发生气泡和裂隙)提起粘度计正放,擦干净外壁所附着的样品,并从支管上取下橡皮管套在有毛细管的长玻璃管口。
1.4.2 恒温:将装有试样的粘度计浸入事先准备妥当的恒温浴中,并用夹子将粘度计固定在支架上,将粘度计调整成为垂直状态。
试验温度保持恒定在±0.1℃,恒温样品约15min。
1.4.3 测量:将样品吸至粘度计扩球,使试样液面稍高于刻度标线,注意不要让毛细管粘度计和扩球产生气泡或裂隙,计下试样从第一刻度标线到第二刻度标线间的流出时间。
重复进行,计算各次流动时间与算术平均值差数不超过算术平均值的±0.5%,取两次的平均值。
1.5计算在温度T时,试样的运动粘度V(mm2/s)按下式计算。
V=C×T式中:C——粘度计常数,(mm2/s2)T——试样流动时间,s(二)微量水分(参照体积法GB/T7600)。
2.1试剂及仪器100ml烧杯、微量进样器0.5微升1毫升、微量水分测定仪、蒸馏水、待测样品。
2.2仪器的标定打开仪器电源开关,按确定键,仪器开始搅拌电解,抽取0.1微升蒸馏水,点击启动键,待蜂鸣声响之后观察显示器读数,直到将显示值标到100±8微克即为标定完毕。
2.3试验步骤2.3.1根据被测样品的含水情况选择合适的进样器。
2.3.2将进样器用被测样品冲洗2~3次(来回抽取样品),然后吸入一定量的样品,为注样作好准备。
2.3.3把样品通过进样口注入到电解液中,电解自动开始。
2.3.4测定结束,蜂鸣器响,仪器显示数值便为实际所测定的水分,单位为微克。
(三)闪点(参照闭口GB/T261)3.1试剂及仪器闪点试验杯、点火枪、全自动闭口闪点试验器、待测样品。
3.2试验步骤3.2.1打开电源开关,进入【参数设置】界面,对预置温度、滞后温度、打印状态等选项进行设置。
3.2.2将干燥试样杯加入试样放入加热浴。
3.2.3按功能键进入【样品测试】界面,按开始键,升降臂自动落下,气源接通,试验开始计时。
3.2.4用点火枪或按住仪器左侧的电子点火器按钮,将引火头引燃,火焰应控制在3~4毫米。
仪器在低于预置温度23±5℃时开始点火划扫。
3.2.5闪火被测出时,仪器停止数据采集,显示闪火温度打印记录结果,停止加热,关闭火焰,升降臂自动抬起,实验结束。
3.2.6待试样杯油样温度降到常温时,将试样杯拿出,倒掉废样,用石油醚清洗干净。
(四)颗粒度(NAS1638)4.1试剂及仪器石油醚(沸程90~120℃),250ml试剂瓶,超声波清洗器,油液颗粒度分析仪。
4.2实验步骤4.2.1打开仪器电源开关,仪器自检完成后进入主界面。
4.2.2将检测杯或专用检测瓶清洗干净后,烘干,加入过滤过的石油醚溶液(等级在6级一下),并将其置于气压舱,密封气压藏。
点击【清洗操作】,执行清洗操作,清洗完毕后点击【返回】,回到主界面。
4.2..3根据检测要求进行通道设置,我们需要设置的检测标准为NAS1638。
4.2.4将待测样品加入样品瓶中,旋紧瓶盖,并用手使劲摇晃5分钟。
再将样品瓶瓶盖稍松,放入超声波清洗槽中,除去样品中的气泡,直至气泡上升至液面为止,时间尽量短,然后静置2~3秒,以待余气上升至液面。
4.2.5根据样品的粘度情况选择常压检测或加压检测。
4.2.6检测结束后进行数据查询,在数据查询界面可查询到样品的等级。
点击【打印当前页】或【打印全部页】将所需项目逐一打印出来。
4.2.7检测完毕后必须用过滤过的石油醚溶液(沸程90~120℃)执行数次清洗操作,清洗完毕后,方可进行下一个样品的检测或关机。
(五)馏程5.1试剂及仪器100ml量筒、125ml支型蒸馏烧瓶、温度计最小分度1℃或小于1℃(400℃)、橡胶塞、秒表、人造沸石、待测样品。
5.2试验步骤5.2.1打开仪器,点击【参数设置】,对试验参数进行设定。
打开电源,设置冷浴温度,打开冷浴和制冷开关,当实际温度降到所设的冷浴温度时,关掉制冷。
5.2.2用量筒量取100ml试样加到容量为125ml的支形蒸馏烧瓶中。
5.2.3将温度计用胶塞安装在支形蒸馏烧瓶上,使得温度计探头与蒸馏烧瓶支管侧下部对齐。
5.2.4将安装了温度计的烧瓶安装到放置了支板的加热台上,用胶塞将蒸馏烧瓶支管紧紧的与冷凝管相连,调节蒸馏烧瓶使其处于直立的位置。
5.2.5调节升降台按钮,使蒸馏烧瓶支板紧紧的接触蒸馏烧瓶的底部。
将容量为100ml的接收量筒放置在冷凝液溢流口。
5.2.6打开电炉开关,调节加热电压,开始蒸馏,并在同一时间开启秒表计时。
5.2.7测初馏点:记录从冷凝管的末端滴下第一滴冷凝液时所观察到的温度计读数,且秒表所示的时间。
5.2.8分别记录接收量筒接收到的的溶液体积为总容量的5%、50%、90%、95%时,温度计的读数及秒表所示的时间。
5.2.9测终馏点:记录试验中温度计所示的最高温度(即温度升高到一定值时,突然下降前的温度),并记录秒表所示的时间。
(六)铜片腐蚀6.1仪器与材料试验弹、试管(长150mm,外径25mm,壁厚1~2mm。
在试管30ml处刻一环线)、水浴或其他液体浴(或铝块浴)、磨片夹钳或磨具、观察试管(扁平形)、温度计(全浸,最小分度1℃或小于1℃)、异辛烷和石油醚、铜片(纯度大于99.9%的电解铜。
宽为12.5mm,厚为1.5~3.0mm,长为75mm)、65微米(240粒度)的碳化硅或氧化铝(刚玉),砂纸(或纱布),105微米(150目)的碳化硅或氧化铝(刚玉)砂粒,以及药用脱脂棉。
6.2腐蚀标准色板腐蚀标准色板的分级分级名称说明(注①)新磨光的铜片—(注②)1 轻度变色a.淡橙色,几乎与新磨光的铜片一样b.深橙色2 中度变色a.紫红色b.淡紫色c.带有淡紫蓝色,或银色,或两种都有,并分别覆盖在紫红色上的多色彩d.银色e.黄铜色或金黄色3 深度变色a.洋红色覆盖在黄铜色上的多色彩b.有红和绿显示的多色彩(孔雀绿),但不带灰色4 腐蚀a.透明的黑色、深灰色或仅带有孔雀绿的棕色b.石墨黑色或无光泽的黑色c.有光泽的黑色或乌黑发亮的黑色6.3试片的制备6.3.1表面准备表面准备的操作步骤:把一砂纸放在表面平坦的表面上,用煤油或洗涤溶剂湿润砂纸,以旋转动作将铜片对着砂纸摩擦,用无灰滤纸或夹钳夹持,以防止铜片与手指接触。
6.3.2最后磨光从溶剂中取出铜片,用无灰滤纸保护手指来夹拿铜片。
取一些105微米(150目)的碳化硅或氧化铝(刚玉)砂粒法国在玻璃板上,用1滴洗涤溶剂湿润,并用一块脱脂棉,蘸取砂粒。
用不锈钢镊子夹持铜片,千万不能接触手指。
先摩擦铜片各端边,然后将铜片夹在夹钳上,用沾在脱脂棉上的碳化硅或氧化铝(刚玉)砂粒磨光主要表面。
磨时要沿铜片的长轴方向,再返回来磨以前,使动程越出铜片末端。
用一块干净的脱脂棉使劲摩擦铜片,以除去所有的金属屑,直到用一块新的脱脂棉擦拭时不再留下污斑为止。
当铜片擦净后,马上浸入以准备好的试样中。
6.4试验步骤5.1打开电源开关,按试验要求在温控显示器上对试验温度进行设置。
5.2将油样倒入清洁、干燥的试管中30ml刻线处,并将经过处理的干净的铜片在一分钟浸入该试管的试样中。
5.3 把试管小心的移入试管架,并把试管架移入符合该试样实验要求的恒温水浴中,按要求的时间进行水浴加热。
5.4在恒温浴中放置的时间达到要求时间后,取出试管并关掉电源开关。
5.5把试管中的油样倒入烧杯中,倒时要让铜片轻轻的滑入,以免碰破烧杯。
5.6用不锈钢镊子立即将铜片取出,浸入洗涤剂中,洗去试样。
5.7立即取出铜片,用定量滤纸吸干铜片上的洗涤溶剂。
5.8把铜片放在扁平试管中,与腐蚀标准色板比较来检查变色或腐蚀迹象。
(七)灰分(参照GB508——85)7.1试剂及仪器瓷坩埚或瓷蒸发皿50ml和90~120ml、电热板或电炉、马弗炉、干燥器、定量滤纸直径90mm、盐酸(化学纯)。
7.2准备工作将稀盐酸(1:4)注入所用的坩埚煮沸几分钟,用蒸馏水洗涤,烘干后,放入马弗炉中775±25℃下至少煅烧十分钟,取出在空气中冷却三分钟,移入干燥器,冷却至室温进行称量。
准确至0.0001克。
7.3试验步骤7.3.1称取25克试样装入称量好的干燥的50ml坩埚中。
7.3.2取出一滤纸叠成两折,卷成圆锥形,把尖端的5~10毫米之顶端部分剪去,放入坩埚。
把剪成圆锥形的滤纸(引火芯)安稳的插在坩埚的油中,将大部分试样表面盖住。
7.3.3测定含水的试样时将装有试样和引火芯的坩埚置于电热板上,缓慢加热使其不溅出,让水分慢慢蒸发,直到浸透试样的滤纸可以燃着为止。
7.3.4试样燃烧后,将盛有残渣的坩埚移入加热到775±25℃的马弗炉中,在此温度下保持 1.5~2小时,直到残渣完全成为灰烬。
7.3.5残渣成灰烬后,将坩埚方在空气中冷却3分钟,然后在干燥器中冷却至室温后进行称量,准确至0.0001克。
再移入马弗炉中煅烧20~30分钟。
重复煅烧,冷却及称量,直至两次称量间的差数不大于0.005克。
7.3.6计算:灰分含量(%)=灰分重量/试样重量×100%(八)酸值(参照GB508——85)8.1试剂及仪器多孔电热水浴锅、三角烧瓶(250ml、300ml)、空气冷凝管、量筒(50ml)、移液管(25ml、10ml)、碱式滴定管(25ml)、微量滴定管(2ml、5ml)、氢氧化钾—乙醇溶液(0.05mol/L)、95%乙醇(分析纯)、甲酚红指示剂或碱性蓝6B。