低氮分级燃烧技术介绍
低氮燃烧

低氮燃烧技术
低氮燃烧技术是一种有效的低NOx燃烧技术,运用空气分级燃烧原理对传统的煤粉炉燃烧系统进行综合改造不仅可以有效地降低NOx的排放量,还可以适当地保持其较好的经济性。
为了控制燃烧过程中NOx的生成量可采取的措施有:(1)降低过量空气系数和氧气浓度,使煤粉在缺氧条件下燃烧;(2)改善锅炉配风系统,降低燃烧过程中的NOx生成量;(3)增加一个或多个低NOx燃烧器,采用再燃技术。
燃烧区的氧浓度对各种类型的NOx生成都有很大影响。
将过量空气系数适当降低(不影响锅炉正常燃烧),燃烧区处于“微过氧燃烧”状态时,对抑制在该区中NOx的生成量有明显效果。
根据这一原理,在不影响锅炉正常燃烧的前提下,应用先进的自动化控制技术结合烟气再循环,适当降低燃烧区的空气量,可降低10-15%左右的NOx生成量。
锅炉的燃烧特性与锅炉结构、燃煤成分、操作要求等因素密切相关,并且存在炉膛出口温度与烟气中NOx含量正相变化的现象。
依据炉膛结构及煤粉燃烧特点,调整合理的配风系统,使燃烧区始终处于沸腾翻滚燃烧状态,加强烟气的搅动和补充足够的氧气,达到强化燃烧的目的,从而降低NOx生成量。
在降低燃烧区的氧浓度和改善锅炉配风系统基础上,增加一个或多个低NOx燃烧器。
通过燃料再燃技术,将燃烧过程分成主燃烧区、再燃区及燃尽区3个区域,把主燃烧区域中生成的NOx在再燃区还原成为分子氮气(N2)以降低NOx排放。
综合应用以上低氮燃烧措施后,可综合降低NOx生成量30%~40%。
低氮燃烧技术和燃烧烟气再循环工作原理
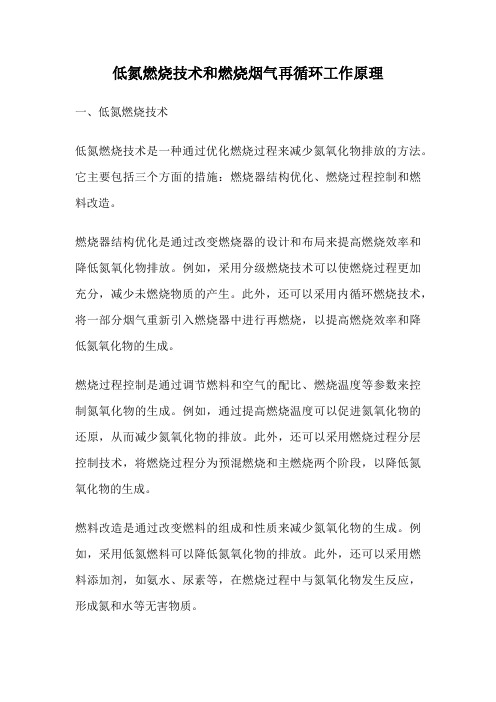
低氮燃烧技术和燃烧烟气再循环工作原理一、低氮燃烧技术低氮燃烧技术是一种通过优化燃烧过程来减少氮氧化物排放的方法。
它主要包括三个方面的措施:燃烧器结构优化、燃烧过程控制和燃料改造。
燃烧器结构优化是通过改变燃烧器的设计和布局来提高燃烧效率和降低氮氧化物排放。
例如,采用分级燃烧技术可以使燃烧过程更加充分,减少未燃烧物质的产生。
此外,还可以采用内循环燃烧技术,将一部分烟气重新引入燃烧器中进行再燃烧,以提高燃烧效率和降低氮氧化物的生成。
燃烧过程控制是通过调节燃料和空气的配比、燃烧温度等参数来控制氮氧化物的生成。
例如,通过提高燃烧温度可以促进氮氧化物的还原,从而减少氮氧化物的排放。
此外,还可以采用燃烧过程分层控制技术,将燃烧过程分为预混燃烧和主燃烧两个阶段,以降低氮氧化物的生成。
燃料改造是通过改变燃料的组成和性质来减少氮氧化物的生成。
例如,采用低氮燃料可以降低氮氧化物的排放。
此外,还可以采用燃料添加剂,如氨水、尿素等,在燃烧过程中与氮氧化物发生反应,形成氮和水等无害物质。
二、燃烧烟气再循环工作原理燃烧烟气再循环是一种通过将一部分燃烧产生的烟气重新引入燃烧器中进行再燃烧的技术。
它主要包括两个步骤:烟气收集和再循环。
烟气收集是将燃烧产生的烟气通过烟囱或其他烟气排放装置收集起来。
在收集过程中,需要对烟气进行净化处理,以去除其中的颗粒物、氮氧化物等污染物,以免对环境造成污染。
再循环是将收集到的烟气重新引入燃烧器中进行再燃烧。
通过再燃烧,可以使燃烧过程更加充分,提高燃烧效率。
此外,再燃烧还可以降低燃烧过程中的氮氧化物生成,从而减少氮氧化物的排放。
燃烧烟气再循环的工作原理是利用再循环系统将部分烟气从烟囱中抽取回燃烧器,与新鲜空气和燃料进行混合燃烧。
再循环系统一般包括烟气收集装置、再循环风机、再循环管道和再循环口等组成部分。
通过控制再循环烟气的比例和再循环位置,可以实现对燃烧过程的调节,提高燃烧效率和降低氮氧化物排放。
总结起来,低氮燃烧技术和燃烧烟气再循环技术是两种常用的减少氮氧化物排放和提高燃烧效率的方法。
低NOx燃烧技术原理及其技术性能分析

低 NOx 燃烧技术原理及其技术性能分析摘要:简要介绍了燃煤电厂NOx产生机理以及目前主流的低NOx燃烧技术原理。
关键词:低NOx燃烧技术;燃烧调整;锅炉燃烧效率;1低NOx燃烧技术原理及技术性能分析1.1空气分级燃烧空气分级燃烧技术(Air Staging)最早是在美国发展起来的,是目前国内外普遍应用,比较成熟的低NOx燃烧技术。
其基本原理是将燃烧所需空气分成两级送入,一级送入过量空气系数小于1,对于燃煤锅炉一般为理论空气量的70%~75%。
其余空气经由布置在燃烧器上游的专门空气喷口OFA(Over Fire Air)送入炉膛继续完成燃烧。
人为地形成准双区燃烧,即主燃烧区和燃烧完全区[6]。
主燃烧区内由于缺氧使燃烧处于“富燃料燃烧(贫氧燃烧)”状态,燃烧速度和温度降低,抑制了热力型NOx的生成。
此外,燃烧过程中生成的CO、NO、以及燃料中氮分解产生的CO、NO、HCN和NH等化合物相互复合作用同样也抑制了3燃料型NOx的生成。
燃烧完全区内燃烧所需其余空气以二次空气输入,调整过量空气系数(过量空气系数大于1)使未燃尽燃料燃烧完全。
此时虽然送入空气量较多,同样会使一些中间产物被氧化成NO,但由于空气分级技术此时反应区已由温度高的主燃烧区转移到温度低的燃烧完全区,抑制了燃料型NOx的生成。
采用空气分级燃烧技术后可使NOx排放量降低30%~60%。
尽管空气分级燃烧弥补了简单的降低过量空气系数燃烧所导致的燃料未完全燃烧损失和飞灰含碳量增加的缺点,但是,若主燃烧区,燃烧完全区两级空气比例分配不合理,或者燃烧混合条件不好,则会增加不完全燃烧带来的损失。
同时,主燃烧区的还原性气氛将导致灰熔点降低从而引起锅炉结渣和受热面腐蚀。
1.2燃料分级燃烧燃料分级燃烧通常采用的形式是燃料再燃烧技术,将燃烧过程设在三个区(主燃区、再燃区和燃尽区)进行,也称为三级燃烧技术,如图2-3所示。
其所依据原理为主燃区形成的NOx会在次燃烧区和烃根CHi、未完全燃烧产物(CO、C、。
低氮燃烧技术介绍

降低氮氧化物产生的方法
(3)采用全预混或部分预混加表面燃烧技术:20t以下NOx排放达到小 于30mg。全预混燃烧能够达到10mg。
降低氮氧化物产生的方法
(4)采用外烟气再循环(FGR)燃烧技术:可根据需要,按烟气循环量的 大小, 可以做到NOx排放低于60mg或30mg 。
降低氮氧化物产生的方法
贫燃预混
低氮燃烧器+ 烟气再循环
控制有效简单 催化燃烧可实现 零排放 效果好,成本适 中
>80%
<30-100
50-85%
低氮燃烧产品
价格信息: 迈夫特(MFT):北京节能技术监测中心 1T——12.8万; 2T——16.5万;(NTFB—25万) 4T——33.2万; 6T——44.5万;
北京市燃气(油)锅炉低氮改 造以奖代补资金管理办法
排放标准情况
2、欧洲标准:欧洲标准EN676 2000
等级 1 2 3
mg/m3 ≤170 ≤120 ≤80
ppm ≤91 ≤64.2 ≤42.8
排放标准情况
3、国家标准及部分地方标准
标准 GB13271-2014 生效日期 2014.7.1 燃油锅炉 在用:400; 新建: 250; 特别限值: 200 -400 在用:200; 新建:150; 400 400 250 燃气锅炉 在用:400; 新建: 200; 特别限值: 150 -400 在用:200; 新建:150; 300 200 250
谢谢各位的聆听!
欢迎交流!
NH3
HCN O2
NO HCO
[ NO ]
Ae
[ N 2 ] [O2 ]dt
局部当量比大于1.2时,上述反应将 不再快速
低氮燃烧技术
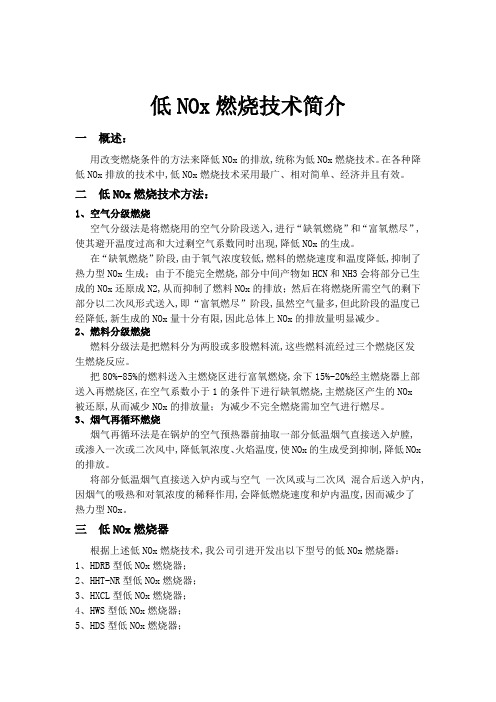
低NOx燃烧技术简介一概述:用改变燃烧条件的方法来降低NOx的排放,统称为低NOx燃烧技术。
在各种降低NOx排放的技术中,低NOx燃烧技术采用最广、相对简单、经济并且有效。
二低NOx燃烧技术方法:1、空气分级燃烧空气分级法是将燃烧用的空气分阶段送入,进行“缺氧燃烧”和“富氧燃尽”,使其避开温度过高和大过剩空气系数同时出现,降低NOx的生成。
在“缺氧燃烧”阶段,由于氧气浓度较低,燃料的燃烧速度和温度降低,抑制了热力型NOx生成;由于不能完全燃烧,部分中间产物如HCN和NH3会将部分已生成的NOx还原成N2,从而抑制了燃料NOx的排放;然后在将燃烧所需空气的剩下部分以二次风形式送入,即“富氧燃尽”阶段,虽然空气量多,但此阶段的温度已经降低,新生成的NOx量十分有限,因此总体上NOx的排放量明显减少。
2、燃料分级燃烧燃料分级法是把燃料分为两股或多股燃料流,这些燃料流经过三个燃烧区发生燃烧反应。
把80%-85%的燃料送入主燃烧区进行富氧燃烧,余下15%-20%经主燃烧器上部送入再燃烧区,在空气系数小于1的条件下进行缺氧燃烧,主燃烧区产生的NOx被还原,从而减少NOx的排放量;为减少不完全燃烧需加空气进行燃尽。
3、烟气再循环燃烧烟气再循环法是在锅炉的空气预热器前抽取一部分低温烟气直接送入炉膛,或渗入一次或二次风中,降低氧浓度、火焰温度,使NOx的生成受到抑制,降低NOx 的排放。
将部分低温烟气直接送入炉内或与空气一次风或与二次风混合后送入炉内,因烟气的吸热和对氧浓度的稀释作用,会降低燃烧速度和炉内温度,因而减少了热力型NOx。
三低NOx燃烧器根据上述低NOx燃烧技术,我公司引进开发出以下型号的低NOx燃烧器:1、HDRB型低NOx燃烧器;2、HHT-NR型低NOx燃烧器;3、HXCL型低NOx燃烧器;4、HWS型低NOx燃烧器;5、HDS型低NOx燃烧器;6、HSM型低NOx燃烧器;7、 HPM型低NOx燃烧器。
生物质锅炉低氮燃烧技术

生物质锅炉低氮燃烧技术
生物质锅炉是一种以生物质能源为燃料的热能装置,具有安全环保、可再生等优点。
为了减少生物质锅炉的氮氧化物排放,提高其燃烧效率,低氮燃烧技术被广泛应用于生物质锅炉中。
生物质锅炉低氮燃烧技术的核心是通过控制燃烧过程中的氧气和燃料的混合比例,使燃烧温度下降,减少氮氧化物的形成。
常用的低氮燃烧技术有分级燃烧、燃尽再燃、SNCR 和SCR 等。
分级燃烧是将燃料分为两部分,先在较低温度区燃烧一个部分燃料,产生一定的热量,再将部分燃烧产生的一氧化碳和未燃的燃料气体引入高温区燃烧,利用高温氧化还原反应继续燃烧燃料,并降低氮氧化物的产生。
燃尽再燃技术是在燃烧过程中注入少量燃料和空气,形成富油燃烧区,使未燃的烟气在富油燃烧区中燃烧,减少氮氧化物的产生。
SNCR 技术是在燃烧过程中向烟气中喷入氨水或尿素溶液,使氨水和尿素在高温下分解,产生氨和异氰酸酯,再和烟气中的氮氧化物发生反应,使其减少。
SCR 技术是在烟气中喷入选择性催化还原剂,使烟气中的氮氧化物发生选择性催化还原反应,将氮氧化物还原成氮气,减少氮氧化物的排放。
在采用低氮燃烧技术的同时,生物质锅炉还应注意燃料的选用和燃烧参数的调节。
燃料的质量、含氧量以及粒度都会影响到燃烧过程中氮氧化物的产生。
而燃烧参数如燃烧温度、燃料适宜比例等也需要根据实际情况进行调整和优化。
总之,生物质锅炉低氮燃烧技术的应用可以有效降低其氮氧化物排放量,减少对环境的污染。
随着技术的不断发展和应用的推广,相信生物质锅炉低氮燃烧技术会在未来得到更加广泛的应用。
工业锅炉常用低氮燃烧技术解决方案

工业锅炉常用低氮燃烧技术解决方案
工业锅炉常用的低氮燃烧技术解决方案主要包括以下几种:
1. 空气分级燃烧:这种技术通过将空气分级为一次空气和二次空气,一次空气在预混区与燃料混合,二次空气在燃烧后期与燃料混合。
这种方式可降低炉膛温度,从而减少氮氧化物的生成。
2. 燃料分级燃烧:这种技术使用低氮氧化物产生能力的燃料,如生物质锅炉,或者使用催化剂促进氮氧化物的还原反应。
3. 低氧燃烧技术:这种方式可以减少氮氧化物的生成量,但需要注意氧浓度过低会导致碳不完全燃烧产生,可能导致有毒气体排放超标。
4. 烟气再循环技术:这种技术将一部分高温烟气回流到燃烧器,可以降低炉膛温度,从而减少氮氧化物的生成。
5. 燃料与空气预混合燃烧:采用这种技术可以减少燃烧过程中空气的总体需求量,同时燃料和空气的预先混合有助于控制火焰的传播,从而减少氮氧化物的生成。
6. 选择合适的锅炉类型:对于特定的工业应用,选择低氮锅炉或生物质锅炉等可以降低氮氧化物排放的设备,也是一种可行的低氮燃烧技术解决方案。
以上解决方案需要根据你的具体需求和锅炉的实际情况来选择和实施。
同时,低氮燃烧技术并不能完全消除氮氧化物的生成,还需要其他措施如改进燃烧设计、优化运行管理等来进一步降低氮氧化物的排放。
在实施这些技术时,应遵循相关环保法规,确保排放达标。
低氮燃烧烟气循环比率

低氮燃烧烟气循环比率一、低氮燃烧技术低氮燃烧技术是一种能够减少氮氧化物排放的燃烧技术。
在燃煤过程中,通过控制燃烧条件和反应温度等参数,可以减少氮氧化物的生成和排放。
低氮燃烧技术主要包括以下几种:1.空气分级燃烧技术:通过将燃料与空气的接触方式进行改变,降低燃烧区的氧含量,从而使燃烧温度降低,减少氮氧化物的生成和排放。
2.燃料分级燃烧技术:将燃料分为多段进行燃烧,减少初始燃烧区的燃料含量,从而降低燃烧温度和氮氧化物的生成。
3.烟气再循环技术:将部分烟气回流到燃烧区域,降低氧含量和燃烧温度,从而减少氮氧化物的生成和排放。
二、烟气循环比率的计算烟气循环比率是烟气再循环技术中的重要参数,它表示回流的烟气量与总烟气量的比值。
烟气循环比率的计算公式为:循环比率 = (回流烟气量 / 总烟气量) × 100%在实际操作中,需要根据不同的燃烧条件和设备参数来确定烟气循环比率的具体数值。
三、烟气循环对NOx排放的影响烟气循环对NOx排放的影响主要体现在以下几个方面:1.降低燃烧温度:回流的烟气会降低燃烧区的温度,从而减少高温条件下NOx的生成和排放。
2.改变燃料和空气的混合方式:回流的烟气会改变燃料和空气的混合方式,从而影响NOx的生成和排放。
3.增加燃料在燃烧区的停留时间:回流的烟气会增加燃料在燃烧区的停留时间,从而增加燃料与空气的接触机会,减少NOx的生成和排放。
四、低氮燃烧技术的发展趋势随着环保要求的不断提高,低氮燃烧技术的研究和应用也越来越受到关注。
未来低氮燃烧技术的发展趋势主要包括以下几个方面:1.多种低氮燃烧技术的联合应用:将不同的低氮燃烧技术进行组合应用,可以更好地降低NOx的排放。
2.增加烟气循环比率的控制精度:通过对烟气循环比率的精确控制,可以实现NOx排放的精确调控。
3.开发新型的低氮燃烧器:通过对燃烧器的优化设计,可以进一步降低NOx的排放。
五、结论低氮燃烧技术是减少氮氧化物排放的重要手段之一。
各种低氮燃烧技术的特点

各种低氮燃烧技术的特点技术01扩散式燃烧这是⼀种最简单的燃烧⽅式,该燃烧⽅式的优点是简单、容易点⽕、不会回⽕、燃烧稳定及燃具结构简单。
缺点是,对于空⽓需求量⼤的⾼热值燃⽓,靠层流扩散达不到完全燃烧,烟⽓中C0含量⽐较⾼,燃具体积⽐较⼤。
强制⿎风扩散燃烧⽅式多⽤于⼯业炉中的⼯业燃烧器。
采⽤这种燃烧⽅式需要合理地组织空⽓与燃⽓混合,避免产⽣⼤量的N0x与C0。
O2含量2%--12%;,相对点⽕容易。
但是,NOX含量⽆法控制。
技术02部分预混式燃烧部分预混式燃烧习惯上⼜称⼤⽓式燃烧。
与扩散式燃烧相⽐,部分预混式燃烧具有燃烧完全、⽕焰短、热强度⼤的优点,但是这种燃烧⽅式可能产⽣回⽕、离焰与脱⽕,在控制好⼀次空⽓的条件下,能具有⼀定范围的不离焰、不回⽕的稳定⽕焰区,在此区内可以调节热负荷。
部分预混式燃烧也有以下缺点:a.需要组织好⼆次空⽓,需要⾜够的⼆次空⽓进⼝⾯积及必要的炉膛⾼度,所以很难减⼩燃烧设备的体积。
b.燃烧产物中N0x含量较⾼,采取措施后,N0x含量降低,⽽C0含量升⾼,很难达到C0与N0x含量都降低的效果。
在有些较⼤功率燃烧器结构中,为了保证点⽕成功率,中⼼形成⽕焰⿊区,采⽤部分预混。
其他与扩散式燃烧相同。
技术03精准控制全预混式燃烧将燃烧所需空⽓精准混⼊燃⽓再进⾏燃烧的全预混式燃烧,其特点是⽕焰短,附着于燃烧表⾯,甚⾄看不到⽕焰,故也称作⽆焰式燃烧。
这种燃烧⽅式的稳定性较差,稳定燃烧的范围较⼩,必须采⽤防⽌离焰与回⽕的稳焰措施。
精准控制全预混式燃烧的优点:燃烧强度⼤,⽕焰短,可以降低炉膛⾼度;不需要⼆次空⽓,省去了⼆次空⽓的⼊⼝⾯积;具有较⼤的⾯积热强度与体积热强度,可缩⼩燃烧设备体积;⽕焰⾯可以靠近热交换器,增⼤传热系数;燃烧产物中C0及N0x含量都⽐较低。
精准控制全预混式燃烧的缺点及特殊的技术要求:当热负荷较⼤时,⽆法利⽤燃⽓⾃⾝压⼒通过引射器吸⼊空⽓,需要有保证燃⽓与空⽓混合⽐例的装置,并且维持此⽐例不受热负荷变化的影响;应有可靠的避免离焰、回⽕的稳焰措施,必要时需要冷却头部,防⽌回⽕。
分级燃烧-烟气外循环低氮燃烧原理

分级燃烧-烟气外循环低氮燃烧原理引言:随着环境保护意识的提高以及对空气污染控制要求的不断增加,燃烧技术的改进和创新已成为重要的研究方向。
分级燃烧-烟气外循环低氮燃烧技术作为一种有效降低燃烧过程中氮氧化物(NOx)排放的方法,被广泛应用于工业燃烧过程中。
本文将介绍分级燃烧-烟气外循环低氮燃烧的原理及其优势。
一、分级燃烧原理分级燃烧是指将燃料在两个或多个燃烧器中进行连续燃烧,通过逐级供氧、燃料分级等方式,使燃烧过程更加充分,同时降低燃烧温度,减少NOx的生成。
其基本原理是通过分离燃料的不同部分,在不同的燃烧区域进行燃烧,从而减少燃烧温度和燃料在燃烧过程中的接触时间,降低NOx的生成。
二、烟气外循环低氮燃烧原理烟气外循环是指将部分燃烧产生的烟气从燃烧器中抽取出来,再经过处理后重新注入燃烧器进行再燃烧。
通过烟气外循环,可以降低燃烧温度,延长燃烧时间,减少燃料在高温下与空气中的氮气反应生成NOx的机会。
同时,烟气外循环还可以提高燃烧器的稳定性和可调性,使燃烧效果更加理想。
三、分级燃烧-烟气外循环低氮燃烧原理分级燃烧和烟气外循环两种技术的结合,可以进一步提高低氮燃烧效果。
在分级燃烧-烟气外循环低氮燃烧系统中,燃料首先在预混燃烧器中进行初级燃烧,产生一部分烟气。
然后,这部分烟气经过处理后,通过外循环系统注入到主燃烧器中进行再燃烧。
这样,燃烧过程中的燃料分级和烟气外循环相结合,使燃烧过程更加充分,燃烧温度更低,从而有效降低NOx的生成。
四、分级燃烧-烟气外循环低氮燃烧的优势1. 有效降低NOx排放:通过分级燃烧-烟气外循环低氮燃烧技术,可以将NOx排放降低到较低水平,符合严格的环境排放标准。
2. 提高燃烧效率:分级燃烧和烟气外循环的组合利用了燃料的多次燃烧,使燃料充分燃烧,提高燃烧效率,降低能源消耗。
3. 稳定可靠的燃烧过程:分级燃烧-烟气外循环低氮燃烧技术能够提高燃烧器的稳定性和可调性,使燃烧过程更加可控,减少了燃烧过程中的不稳定现象。
低氮分级燃烧技术介绍

低氮分级燃烧技术一.低NO x优化燃烧技术的分类及比较为了实现清洁燃烧,目前降低燃烧中NO、排放污染的技术措施可分为两大类:一类是炉内脱氮,另一类是尾部脱氮。
1.1炉内脱氮炉内脱氮就是采用各种燃烧技术手段来控制燃烧过程中NO x的生成,又称低NO x燃烧技术,下表给出了现有几种典型炉内脱氮技术的比较。
表2技术名称效果优点缺点低氧燃烧根据原来运行条件,最多降低20%投资最少导致飞灰含碳量增加降低投入运行的燃烧器数目15%—30% 投资低,易于锅炉改装有引起炉内腐蚀和结渣的可能,并导致飞灰含碳量增加空气分级燃烧(OFA)最多30% 投资低并不是对所有炉膛都适用,有可能引起炉内腐蚀和结渣,并降低燃烧效率低NO x燃烧器与空气分级燃烧相结合时可达60% 用于新的和改装的锅炉,中等投资,有运行经验结构比常规燃烧器复杂.烟气再循环(FGR)最多20% 能改善混合燃烧,中等投资增加再循环风机,使用不广泛燃料分级(再燃) 达到50% 适用于新的和改造现有锅炉,可减少已形成的NO X,中等投资可能需要增加第二种燃料,可能导致飞灰含碳量增加,运行经验较少1.2尾部脱氮尾部脱氮又称烟气净化技术,即把尾部烟气中已经生成的氮氧化物还原或吸附,从而降低NO x排放。
烟气脱氮的处理方法可分为:催化还原法、液体吸收法和吸附法三大类。
催化还原法是在催化剂作用下,利用还原剂将NO x还原为无害的N2。
这种方法虽然投资和运转费用高,且需消耗氨和燃料,但由于对NO x效率很高,设备紧凑,故在国外得到了广泛应用,催化还原法可分为选择性非催化还原法和选择性催化还原法相比,设备简单、运转资金少,是一种有吸引力的技术。
液体吸收法是用水或者其他溶液吸收烟气中的NO x。
该法工艺简单,能够以硝酸盐等形式回收N进行综合利用,但是吸收效率不高。
吸附法是用吸附剂对烟气中的NO x进行吸附,然后在一定条件下使被吸附的NO x脱附回收,同时吸附剂再生。
此法的NO x脱除率非常高,并且能回收利用。
低氮燃烧器改造技术方案

低氮燃烧器改造技术方案中国作为全球最大的燃煤国家之一,在能源利用和环境保护方面面临着巨大的挑战。
煤炭燃烧产生的氮氧化物是空气污染的主要原因之一,因此低氮燃烧技术应运而生。
本文将介绍低氮燃烧器改造技术方案,以应对当前煤炭燃烧所带来的环境压力。
一、低氮燃烧技术简介低氮燃烧技术是通过优化燃烧过程,降低燃料中的氮氧化物排放。
目前主流的低氮燃烧技术包括分级燃烧、空燃比调节和燃烧温度控制等。
1. 分级燃烧技术分级燃烧技术采用多级供气方式,通过分区燃烧降低燃料的燃烧温度,减少氮氧化物的生成。
通过合理控制气流的分配,不仅可以提高燃烧效率,还能有效降低氮氧化物的排放量。
2. 空燃比调节技术空燃比调节技术是通过控制燃烧过程中的空气和燃料的比例,降低氮氧化物的生成。
通过优化燃烧器结构和控制系统,使燃烧器在不同负荷下都能保持适宜的空燃比,从而实现低氮燃烧。
3. 燃烧温度控制技术燃烧温度是影响氮氧化物生成的重要因素之一。
采用燃烧温度控制技术,可以通过调节燃烧器的出口温度,使其保持在适宜的范围内,从而降低氮氧化物的生成。
二、低氮燃烧器改造方案为了实现低氮燃烧,需要对现有的燃烧器进行改造。
下面介绍一个典型的低氮燃烧器改造方案。
1. 燃烧器结构优化通过对燃烧器的结构进行优化,可以提高燃烧效率和低氮燃烧能力。
例如,采用多孔板状燃料供给器,可以实现燃料的均匀分布,增强燃烧稳定性;增加燃烧器内部的混合器,可以提高燃烧效率。
2. 回转流化床技术回转流化床技术是一种燃烧方式,能够有效降低氮氧化物的生成。
通过引入适量的再循环废气和控制空气的分布,可以使燃料在燃烧过程中充分混合,减少氮氧化物的生成。
3. 进一步减少氮氧化物排放除了燃烧器的改造,还可以采取其他降低氮氧化物排放的措施。
例如,增加烟气再循环率,使部分烟气重新进入炉膛进行二次燃烧;采用SNCR(选择性非催化还原)技术,在燃烧过程中喷射还原剂,降低氮氧化物的浓度。
三、低氮燃烧器改造的经济效益与环境效益低氮燃烧器改造不仅能够降低氮氧化物的排放,减少空气污染,还能带来一系列的经济效益。
推荐:低氮分级燃烧技术

离分淡浓用以可, 中用应程工在。性特烧燃的同相油燃化雾与有粉煤 的度尺个这,究研关有据根,粉煤的mμ34于小径粒指是粉煤细超 。料燃燃再为 作粉煤化细超的%02�%01入喷区燃再,粉煤浓的%09�%08烧燃区燃主 ,料燃为煤用燃际实炉锅以均区燃再、主炉锅。761.1=α口出区尽燃 ,9.0 � 8.0= α 口 出 区 燃 再 ,0.1 � 9.0= α 口 出 区 燃 主 � 为 值 标 目 数 系 气空量过口出域区各。区尽燃和区燃再、区燃主为分划区烧燃膛炉个 整将,果结究研的期前和理原术技烧燃xON低燃再粉煤细超据根 。尽燃 物产烧燃全完未的来出区燃再从证保,)风尽燃为称(气空的量定一给 供区尽燃在�成生xON的新了制抑还且而,xON的成生经已原还够能仅 不区燃再 �原还被xON的成生区燃主在,氛气性原还的强很有具,)0.1< α (0.1 于 小 数 系 气 空 量 过 区燃 再 , 区 燃 再 入 送 料 燃 的 %02 � %51, xON 成 生 烧 燃 区 燃 主 在 料 燃 , 区 燃 主 入 送 料 燃 的 %58 � %08 将
烧燃的氧低、温高、度浓粉煤高个一织组域区器烧燃主膛炉在于利有 。利有当相尽燃及燃稳对�烧燃火着域区此在粉煤使�气烟温高的来 游上进冲向逆流气粉煤风次一使切反风次一淡、浓。布分间空烧燃区 壁近与区心中的同不然截性特了成形上面截平水膛炉在 �计设该 。变不度角流射圆切原持维风次二器 烧燃主余其�流射风次二置偏性刚层一置布�间之风次一层两在时同 �置布切反用采流射风次一淡、浓有所将术技本�域区烧燃主在 布分区两的面截平水域区烧燃、 �二� 。果效的显明其极有具成形 xON 型力热 和成形 xON 型料燃的烧燃粉煤低降于对�性特烧燃级分气空、烧燃级 分 淡浓 下 上 料 燃 的度 尺 间 空 大 了成 构 上 间 空向 纵 膛 炉 在 术技 该 。平水度温的高够足区烧燃主膛炉炉锅证保�右左 0.1 在数系气空量 过域区此时行运�xON 的成生已原还�部上区烧燃主入进�出析量大 物原还 xON�下态状的氧缺在�平水高较到达温炉域区此�数系气空 量过的域区此低降当适以可整调过通时行运�利有尽燃火着对�置布 中集体整部下的粉煤的右左%08 炉锅占证保�区烧燃主的性特燃稳火 着高有具成组器烧燃粉煤浓层四部下的成构 �域区烧燃主在样这 。右左 aP002 约力阻 � �比度浓量质� 2 �8 为比淡浓后离分 �器离分风旋力阻低 效高型道管的发开司公用采部全粉煤风次一 。节调立独层分以可都嘴 喷粉煤淡、浓的层八室四下上�器烧燃形齿 xON 低粉煤风次一淡的层 四室两为部上 �器烧燃粉煤形齿 xON 低离分下上淡浓的室三第为间中 �器烧燃形齿 xON 低粉煤风次一浓的层四室两置布部下�器烧燃粉煤 层五的炉锅 WM003 于对 �间空烧燃淡浓个两下上成分区烧燃主将 。差偏温烟口出炉锅整调 及风送向靶需按现实 �口喷动摆右左下上可为计设均口喷风尽燃有所 �时同�段手要主的 xON 型力热及型料燃低降是�度高原还的够足有 间之风尽燃位高与区器烧燃主了证保先首它�右左%52 的量风总占约 �风尽燃 AFOS 层三了置布布�上以米 3 约部顶区器烧燃主距在 布分区三的间空向纵、 �一�
低NOx燃烧技术介绍
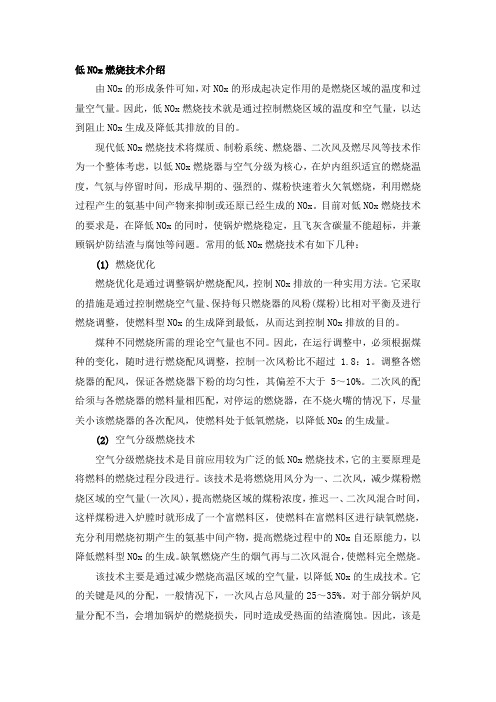
低NOx燃烧技术介绍由NOx的形成条件可知,对NOx的形成起决定作用的是燃烧区域的温度和过量空气量。
因此,低NOx燃烧技术就是通过控制燃烧区域的温度和空气量,以达到阻止NOx生成及降低其排放的目的。
现代低NOx燃烧技术将煤质、制粉系统、燃烧器、二次风及燃尽风等技术作为一个整体考虑,以低NOx燃烧器与空气分级为核心,在炉内组织适宜的燃烧温度,气氛与停留时间,形成早期的、强烈的、煤粉快速着火欠氧燃烧,利用燃烧过程产生的氨基中间产物来抑制或还原已经生成的NOx。
目前对低NOx燃烧技术的要求是,在降低NOx的同时,使锅炉燃烧稳定,且飞灰含碳量不能超标,并兼顾锅炉防结渣与腐蚀等问题。
常用的低NOx燃烧技术有如下几种:(1)燃烧优化燃烧优化是通过调整锅炉燃烧配风,控制NOx排放的一种实用方法。
它采取的措施是通过控制燃烧空气量、保持每只燃烧器的风粉(煤粉)比相对平衡及进行燃烧调整,使燃料型NOx的生成降到最低,从而达到控制NOx排放的目的。
煤种不同燃烧所需的理论空气量也不同。
因此,在运行调整中,必须根据煤种的变化,随时进行燃烧配风调整,控制一次风粉比不超过 1.8:1。
调整各燃烧器的配风,保证各燃烧器下粉的均匀性,其偏差不大于5~10%。
二次风的配给须与各燃烧器的燃料量相匹配,对停运的燃烧器,在不烧火嘴的情况下,尽量关小该燃烧器的各次配风,使燃料处于低氧燃烧,以降低NOx的生成量。
(2)空气分级燃烧技术空气分级燃烧技术是目前应用较为广泛的低NOx燃烧技术,它的主要原理是将燃料的燃烧过程分段进行。
该技术是将燃烧用风分为一、二次风,减少煤粉燃烧区域的空气量(一次风),提高燃烧区域的煤粉浓度,推迟一、二次风混合时间,这样煤粉进入炉膛时就形成了一个富燃料区,使燃料在富燃料区进行缺氧燃烧,充分利用燃烧初期产生的氨基中间产物,提高燃烧过程中的NOx自还原能力,以降低燃料型NOx的生成。
缺氧燃烧产生的烟气再与二次风混合,使燃料完全燃烧。
分级燃烧-烟气外循环低氮燃烧原理

分级燃烧-烟气外循环低氮燃烧原理分级燃烧-烟气外循环低氮燃烧是一种先进的燃烧技术,广泛应用于工业锅炉和电厂燃烧设备中。
它通过优化燃烧过程,减少氮氧化物(NOx)的生成,达到降低污染物排放的目的。
该技术的原理是将燃烧过程分为多个阶段进行,通过分级燃烧的方式实现燃烧效率的提高和燃烧产物的优化。
在燃烧过程中,燃料和空气经过预处理后分别进入不同的燃烧区域,实现燃料的充分燃烧和烟气的低氮燃烧。
燃料经过预处理后进入底层燃烧区域,与一部分空气进行初次燃烧。
在这个阶段,燃料的一部分燃烧产物会被还原成一氧化碳(CO)和水蒸气(H2O),而另一部分燃烧产物则会被部分氧化生成一氧化氮(NO)。
然后,燃料和燃烧产物进入上层燃烧区域,与剩余的空气进行二次燃烧。
在这个阶段,底层燃烧区域产生的一氧化碳和一氧化氮会继续与剩余氧气反应生成二氧化碳(CO2)和氮氧化物(NOx)。
为了减少氮氧化物的生成,烟气外循环被引入燃烧过程中。
烟气外循环是指将一部分烟气从锅炉的燃烧区域中抽离出来,经过处理后再重新进入燃烧区域。
通过循环烟气的方式,可以有效降低燃烧温度和氧浓度,减少氮氧化物的生成。
同时,循环烟气中的水蒸气还可以吸收燃烧过程中产生的热量,提高锅炉的热效率。
分级燃烧-烟气外循环低氮燃烧技术的应用可以显著降低氮氧化物的排放。
通过优化燃烧过程,减少一氧化氮的生成,可以降低大气污染物对环境的影响,保护大气环境的质量。
同时,该技术还可以提高燃烧设备的热效率,降低燃料的消耗和运行成本。
总结起来,分级燃烧-烟气外循环低氮燃烧是一种先进的燃烧技术,通过燃烧过程的分级和烟气外循环的方式,实现燃烧效率的提高和氮氧化物排放的降低。
该技术的应用可以有效改善大气环境质量,提高燃烧设备的能源利用效率,具有广阔的应用前景。
低氮燃烧工作原理及技术

低氮燃烧工作原理及技术低氮燃烧是一种重要的环保技术,通过对燃烧过程进行优化,减少氮氧化物(NOx)的排放量。
本文将从低氮燃烧的原理和技术两个方面进行探讨。
一、低氮燃烧的原理低氮燃烧的核心原理是在燃烧过程中控制燃料和空气的混合比例,以降低燃烧温度和燃料中的氮氧化物生成量。
具体来说,低氮燃烧可以通过以下几种方式实现:1. 燃料优化:通过调整燃料的成分和供应方式,降低燃料中的氮含量。
例如,在煤炭燃烧过程中,可以采用低氮煤或混合燃烧的方式,减少氮氧化物的生成。
2. 空气优化:通过调整燃烧过程中的空气供应方式,使燃料和空气的混合更加均匀充分,提高燃料的燃烧效率,减少氮氧化物的生成。
例如,可以采用预混合燃烧技术,将燃料和空气提前混合,并在燃烧室中均匀分布,以降低燃烧温度和氮氧化物的生成。
3. 燃烧控制:通过调整燃烧过程中的温度、压力和时间等参数,控制燃烧的速率和程度,以降低氮氧化物的生成。
例如,可以采用分级燃烧技术,将燃烧过程分为多个阶段,逐步降低燃烧温度和氮氧化物的生成。
二、低氮燃烧的技术低氮燃烧技术主要包括燃烧器设计和燃烧过程控制两个方面。
1. 燃烧器设计:燃烧器是燃烧过程中的关键设备,其设计合理与否直接影响到燃烧效率和氮氧化物的生成。
在低氮燃烧器的设计中,通常采用以下几种技术手段:(1)风分级技术:通过在燃烧器中设置多个风道,分别控制燃料和空气的供应量,使其达到最佳的混合比例,降低氮氧化物的生成。
(2)预混合技术:将燃料和空气提前混合,并在燃烧室中均匀分布,以实现燃烧的均匀和充分,降低燃烧温度和氮氧化物的生成。
(3)燃烧室设计:通过优化燃烧室的结构和形状,使燃料和空气的混合更加均匀,燃烧过程更加稳定,减少氮氧化物的生成。
2. 燃烧过程控制:在低氮燃烧过程中,燃烧过程的控制至关重要。
通过控制燃烧过程中的温度、压力、空气和燃料供应量等参数,可以有效地降低氮氧化物的生成。
常用的燃烧过程控制技术包括:(1)燃烧温度控制:通过控制燃烧过程中的空气供应量和燃料供应量,控制燃烧温度在适当范围内,以降低氮氧化物的生成。
低氮燃烧知识点总结

低氮燃烧知识点总结一、低氮燃烧技术原理1. 燃烧过程中氮氧化物的产生燃烧过程中,空气中的氮气和氧气在高温下会发生化学反应,生成氮氧化物。
其中最主要的产物是一氧化氮(NO)和二氧化氮(NO2),它们统称为氮氧化物(NOx)。
NOx的生成主要有两种途径,一是热力生成,即在燃烧温度高的情况下,氮气和氧气直接发生氧化反应生成NOx;二是燃料中的有机氮在燃烧过程中进入气相后再和氧气发生反应生成NOx。
2. 低氮燃烧技术原理低氮燃烧技术主要通过改变燃烧工艺和调整燃料供给,降低燃烧温度和燃烧产物中氧含量,从而减少NOx的生成。
具体包括以下几种技术:(1)提高燃烧温度通过提高燃烧温度,使氨和氧气在高温下尽量充分混合,可以提高NOx的生成速率,减少氨的耗损。
(2)燃烧空气预热采用热回收技术,将烟气中的热量回收并用于预热燃烧用空气,降低燃烧温度,减少NOx的生成。
(3)燃烧过程控制采用先进的燃烧控制系统,调整燃烧过程中的氧气供给和燃料供给,保持燃烧温度在适宜范围内,减少NOx的生成。
(4)利用催化剂在燃烧过程中引入催化剂,使NOx在催化剂的作用下还原成氮气和水蒸气,从而减少NOx的排放。
(5)选择低氮燃料选择低氮燃料,降低燃料中有机氮的含量,减少NOx的生成。
二、低氮燃烧技术应用1. 工业领域低氮燃烧技术在工业锅炉、热风炉、干燥设备等燃烧设备中得到了广泛的应用。
这些设备通常是大型的燃烧设备,燃烧过程中产生的NOx排放较大,采用低氮燃烧技术可以显著降低NOx排放,符合环保要求。
2. 能源领域在发电厂、燃气轮机、燃气锅炉等燃烧设备中,低氮燃烧技术也得到了广泛的应用。
能源领域的燃烧设备通常是大功率的设备,燃烧过程中产生的NOx排放对环境影响较大,采用低氮燃烧技术可以降低NOx排放,保护环境。
3. 其他领域低氮燃烧技术也逐渐应用于民用燃气壁挂炉、燃气热水器等小型家用燃烧设备中。
这些设备通常是近距离使用的设备,排放的NOx会直接对空气质量产生影响,采用低氮燃烧技术可以减少NOx排放,保护人们的健康。
低氮燃烧器改造技术方案

低氮燃烧器改造技术方案引言随着环保意识的提高和我国大气污染治理的加强,低氮燃烧技术作为一种有效的降低燃烧产生的氮氧化物(NOx)排放的方法已经得到广泛应用。
本文将介绍低氮燃烧器改造技术方案,包括低氮燃烧器的原理、改造的具体方法以及改造后的效果。
低氮燃烧器原理低氮燃烧器是一种通过优化燃烧过程来减少氮氧化物产生的燃烧设备。
其主要原理是通过改变燃料和空气的混合方式和燃烧温度来降低燃烧时氮气和氧气的反应速率,从而减少氮氧化物的生成。
低氮燃烧器通常采用以下几种技术来实现低氮燃烧:1.燃烧空气分级:通过将燃烧空气分为多个级别,分别与燃料混合并燃烧,可以降低燃烧的温度,减少氮氧化物的生成。
2.吹风预混燃烧:将燃烧气体和空气预先混合,并通过喷嘴将混合气体喷入燃烧室,可以使燃烧更加均匀稳定,减少氮氧化物的生成。
3.氧化剂还原剂分级燃烧:通过将氧化剂和还原剂分为多个级别,分别与燃料混合并燃烧,可以调节燃烧过程中氧化还原反应的位置和速率,降低氮氧化物的生成。
低氮燃烧器改造方法低氮燃烧器改造是在现有燃烧器基础上进行的改进和优化。
对于不同类型的燃烧设备,改造方法有所不同。
以下是常用的低氮燃烧器改造方法:1.燃烧室结构优化:通过对燃烧室结构进行优化设计,包括增加混合区长度、改善燃料和空气的混合程度等,可以提高燃烧效率,减少氮氧化物的生成。
2.燃料预处理:对燃料进行预处理,包括脱硫、脱氮等,可以减少燃料中氮氧化物的含量,从而降低燃烧过程中氮氧化物的生成。
3.燃料分级燃烧:通过将燃料分为多个级别,分别与空气混合并燃烧,可以减少燃烧过程中氮氧化物的生成。
4.燃烧风机优化:通过优化燃烧风机的设计和调节,可以使燃烧过程更加均匀稳定,减少氮氧化物的生成。
5.添加燃烧辅助装置:如添加SNCR(Selective Non-CatalyticReduction)装置,通过加入适量的还原剂来减少氮氧化物的生成。
低氮燃烧器改造效果通过采用低氮燃烧器改造技术,可以显著降低燃烧设备的氮氧化物排放。
- 1、下载文档前请自行甄别文档内容的完整性,平台不提供额外的编辑、内容补充、找答案等附加服务。
- 2、"仅部分预览"的文档,不可在线预览部分如存在完整性等问题,可反馈申请退款(可完整预览的文档不适用该条件!)。
- 3、如文档侵犯您的权益,请联系客服反馈,我们会尽快为您处理(人工客服工作时间:9:00-18:30)。
低氮分级燃烧技术介绍 Prepared on 22 November 2020低氮分级燃烧技术一.低NO x优化燃烧技术的分类及比较为了实现清洁燃烧,目前降低燃烧中NO、排放污染的技术措施可分为两大类:一类是炉内脱氮,另一类是尾部脱氮。
炉内脱氮炉内脱氮就是采用各种燃烧技术手段来控制燃烧过程中NO x的生成,又称低NO x燃烧技术,下表给出了现有几种典型炉内脱氮技术的比较。
表2尾部脱氮尾部脱氮又称烟气净化技术,即把尾部烟气中已经生成的氮氧化物还原或吸附,从而降低NO x排放。
烟气脱氮的处理方法可分为:催化还原法、液体吸收法和吸附法三大类。
催化还原法是在催化剂作用下,利用还原剂将NO x还原为无害的N2。
这种方法虽然投资和运转费用高,且需消耗氨和燃料,但由于对NO x效率很高,设备紧凑,故在国外得到了广泛应用,催化还原法可分为选择性非催化还原法和选择性催化还原法相比,设备简单、运转资金少,是一种有吸引力的技术。
液体吸收法是用水或者其他溶液吸收烟气中的NO x。
该法工艺简单,能够以硝酸盐等形式回收N进行综合利用,但是吸收效率不高。
吸附法是用吸附剂对烟气中的NO x进行吸附,然后在一定条件下使被吸附的NO x脱附回收,同时吸附剂再生。
此法的NO x脱除率非常高,并且能回收利用。
但一次性投资很高。
炉内脱氮与尾部脱氮相比,具有应用广泛、结构简单、经济有效等优点。
表2中各种低NO x燃烧技术是降低燃煤锅炉NO x排放最主要也是比较成熟的技术措施。
一般情况下,这些措施最多能达到50%的脱除率。
当要进一步提高脱除率时,就要考虑采用尾部烟气脱氮的技术措施,SCR和SNCR法能大幅度地把NO x排放量降低到200mg/m3,但它的设备昂贵、运行费用很高。
根据我国发展现状和当前经济实力还不雄厚的国情,以及相对宽松的国家标准CB13223一2003,在今后相当长一段时间内,我国更适合发展投资少、效果也比较显着的炉内脱氮技术。
即使采用烟气净化技术,同时采用低NO x燃煤技术来控制燃烧过程NO x的产生,以尽可能降低化设备的运行和维护费用。
表2中各炉内脱氮技术又以燃料分级效率较高。
燃料再燃技术是有效的降低NO x排放的措施,早在1980年日本的三菱公司就将天然气再燃技术应用于实际锅炉,NO x排放减少50%以上。
美国能源部的“洁净煤技术”计划也包括再燃技术,其示范项目分别采用煤或天然气作为再燃燃料,NO x排放减少30%到70%。
在日本、美国、欧洲再燃技术大量应用于新建电站锅炉和已有电站锅炉的改造,在商业运行中取得良好的环境效益和经济效益。
在我国燃料再燃烧技术研究和应用起步较晚,主要是因为我国过去对环保的要求较低,另一方面则是出于技术经济上的考虑。
进入90年代,我国严重缺电局面开始缓和,大气污染日益严重,1994年全国85个大中城市中NO x超标的城市就有30个,占35%。
1998年对全国322个省控城市量监测结果分析,NO x年日平均值范围在一m3,全国平均为m3,治理大气污染成为十分迫切的任务。
随着环保要求的不断提高,研究适应我国国情的低成本的再燃低NO x燃烧技术具有良好的前景。
二.分级燃烧原理抑制NOx的生成可采取的措施有:1.降低锅炉峰值温度,将燃烧区的煤粉量降低。
2.降低氧浓度(即降低过量空气系数),将部分二次风管堵住。
3.由于要保证锅炉的出力,可将部分煤粉和空气从锅炉上部投入,这样就控制了燃烧火焰中心区域助燃空气的数量,缩短燃烧产物在高温火焰区的停留时间,避免了高温和高氧浓度的同时存在。
4.在炉膛中设立再燃区,利用在主燃区中燃烧生成的烃根CHi和未完全燃烧产物CO、H2、C和CnHm等,将NO的还原成N2。
如示意图1所示。
图1分级燃烧原理图将80%~85%的燃料送入主燃区,燃料在主燃区燃烧生成NOx,15%~20%的燃料送入再燃区,再燃区过量空气系数小于(α<,具有很强的还原性气氛,在主燃区生成的NOx被还原;再燃区不仅能够还原已经生成的NOx,而且还抑制了新的NOx生成;在燃尽区供给一定量的空气(称为燃尽风),保证从再燃区出来的未完全燃烧产物燃尽。
根据超细煤粉再燃低NOx燃烧技术原理和前期的研究结果,将整个炉膛燃烧区划分为主燃区、再燃区和燃尽区。
各区域出口过量空气系数目标值为:主燃区出口α=~,再燃区出口α=~,燃尽区出口α=。
锅炉主、再燃区均以锅炉实际燃用煤为燃料,主燃区燃烧80%~90%的浓煤粉,再燃区喷入10%~20%的超细化煤粉作为再燃燃料。
超细煤粉是指粒径小于43μm的煤粉,根据有关研究,这个尺度的煤粉有与雾化燃油相同的燃烧特性。
在工程应用中,可以用浓淡分离器从常规煤粉中分离。
三.分级燃烧的技术特点1.优异的低负荷不投油稳燃能力。
该设计的理念之一是建立煤粉早期浓缩着火,为此公司开发了高效浓淡分离装置、两层浓浓、淡淡一次风合用一层一次风室,中间完全分隔的一次风煤粉燃烧器、周界齿形的煤粉燃烧喷嘴,同时一次风煤粉反切射流技术,极大地提高锅炉的不投油低负荷稳燃能力。
根据设计和校核煤种的着火特性,选用合适的煤粉浓缩比、煤粉喷嘴、和浓一次风反切角度,在煤种允许的变化范围内确保煤粉及时着火稳燃,并且燃烧器状态良好。
2.优异的煤粉高效燃尽、防结渣及高温腐蚀的特性首先,高浓度煤粉的早期着火提高了燃烧效率;同时通过在炉膛的不同高度布置底部二次风、偏置二次风、上部OFA和空间分离的S-OFA,将炉膛分成三个相对独立的部分:燃烧区,NOx还原区和燃尽区。
在每个区域合理的控制各自的过量空气系数,这种改进的空气分级方法通过优化每个区域的过量空气系数,在有效降低NOx排放的同时能最大限度地提高燃烧效率;第三,通过燃烧器区域的刚性偏置二次风,在炉膛壁面附近形成低煤粉浓度的氧化区,避免了炉膛结渣和高温腐蚀的发生。
第四,本技术将煤粉浓淡分离,所有浓一次风煤粉都布置在了燃烧区域下部,相当于提高了煤粉燃尽高度及NOx还原高度,有利于提高锅炉燃烧效率及降低NOx的排放水平。
3.超低的NOx燃烧排放特性分级燃烧技术的最突出特点是超低NOx燃烧特性,在保证稳燃高效的前提下,通过采用高效浓淡分离技术、空间燃烧分级技术、一次风逆向射流等手段不仅保证煤粉早着火,稳定燃烧,通过采用上下、左右可调燃尽风喷口技术,实现炉内按需供风和降低炉膛出口烟温偏差,更重要的是实现了锅炉超低NOx 的燃烧排放。
4.优异的小油点火稳燃能力。
该设计采用公司经过了大量工业应用的煤粉气化小油燃烧点火技术,在第一层的浓、淡一次风的煤粉燃烧器中布置了小油点火装置,可以在锅炉冷态以及热态启动时完全不投入大油枪,极大地降低了锅炉的启动和在更低负荷下的稳燃油耗。
5.分离燃尽风SOAF还具有较好的降低炉膛出口烟温偏差特性采用空间空气的分级燃烧技术不仅是降低NOx排放、提高煤粉燃尽率的重要手段,同时采用对SOFA的水平摆动调整,更有助于降低炉膛出口两侧烟温偏差而导致的过热器及再热器壁温偏差的作用。
6.五大技术特点保证锅炉改造后大幅提高锅炉运行经济性CEE超低NOx燃烧技术无任何运行成本,它不仅实现锅炉的超低NOx排放,同时实现了锅炉高效稳燃、防结渣、防高温腐蚀、低负荷不投油稳燃、锅炉小油点火稳燃的特性,扩大了锅炉的煤种适应性等功能,在工业化应用中取得了优异的效果。
四、改造方案(烟煤)下面以典型的300MW四角切圆燃烧锅炉为例介绍基于分级燃烧技术的CEE低氮燃烧技术:整个燃烧系统的各喷嘴布置示意见图1所示。
图2CEE 燃烧技术的炉膛纵向空间燃烧组织示意图 图1.锅炉燃烧系统各喷嘴布置示意图3CEE燃烧技术的一室两层浓一次风煤粉燃烧器示意图图4CEE主燃烧器区域炉膛水平截面燃烧组织示意图首先,采用在各煤粉管道中布置的的旋风分离器对一次风煤粉进行浓淡分离,两个浓浓、淡淡的一次风煤粉进入一个一次风室,构成一个一室两层的煤粉燃烧器。
从下往上,一次风煤粉喷嘴依次为:两室四层浓浓一次风、一层浓淡一次风、两层淡淡一次风,见图1所示。
第二,将燃烧区域分成上下三个区域,下部为由两层四室浓一次风构成的主燃烧稳燃区,中部为两层四室的淡一次风构成的NOx还原区,顶部为由在主燃烧区上部布置的两层分离SOFA构成的燃尽区,见图2所示。
第三,在炉膛燃烧区域的水平截面,一次风喷嘴射流反切,在每层浓一次风喷嘴上部布置一层刚性的偏置二次风,这样构成了在炉膛中央的高浓度煤粉、高温、低氧的主燃烧区,在炉膛壁面附近构成了低煤粉浓度、低温、高过量空气系数的氧化区;同时SOFA燃尽风喷嘴反切,并可水平、上下摆动,调节炉膛出口火焰温度和避免炉膛出口两侧烟温偏差,见图2、图4、图5所示。
第四,一次风煤粉燃烧器采用齿形低NOx煤粉喷嘴,见图6所示。
该结构类似于WR宽调节比燃烧器,但采用了本公司的摆动配合结构,减少了煤粉喷嘴的周界风设计,而在煤粉喷嘴上下两侧各增加了一层二次风,见图2所示。
第五,在最下层的浓一次风和淡一次风燃烧器布置小油点火装置,以保证冷热态锅炉启动的少油点火启动,以及实现锅炉非正常的超低负荷(低于的30%MCR)的节油稳燃。
五、CEE超低NOx燃烧系统技术特点CEE技术的最突出特点是超低NOx燃烧特性,在保证稳燃高效的前提下,通过采用高效浓淡分离技术、空间燃烧分级技术、一次风逆向射流等手段不仅保证煤粉早着火,稳定燃烧,通过采用上下、左右可调燃尽风喷口技术,实现炉内按需供风和降低炉膛出口烟温偏差,更重要的是实现了锅炉超低NOx的燃烧排放。
它包含了两大核心技术特点:(一)、纵向空间的三区分布在距主燃烧器区顶部约3米以上,布布置了三层SOFA燃尽风,约占总风量的25%左右,它首先保证了主燃烧器区与高位燃尽风之间有足够的还原高度,是降低燃料型及热力型NOx的主要手段;同时,所有燃尽风喷口均设计为可上下左右摆动喷口,实现按需靶向送风及调整锅炉出口烟温偏差。
将主燃烧区分成上下两个浓淡燃烧空间,对于300MW锅炉的五层煤粉燃烧器,下部布置两室四层的浓一次风煤粉低NOx齿形燃烧器,中间为第三室的浓淡上下分离低NOx齿形煤粉燃烧器,上部为两室四层的淡一次风煤粉低NOx 齿形燃烧器,上下四室八层的浓、淡煤粉喷嘴都可以分层独立调节。
一次风煤粉全部采用公司开发的管道型高效低阻力旋风分离器,分离后浓淡比为8:2(质量浓度比),阻力约200Pa左右。
这样在主燃烧区域,构成的下部四层浓煤粉燃烧器组成具有高着火稳燃特性的主燃烧区,保证占锅炉80%左右的煤粉的下部整体集中布置,对着火燃尽有利,运行时通过调整可以适当降低此区域的过量空气系数,此区域炉温达到较高水平,在缺氧的状态下,NOx还原物大量析出,进入主燃烧区上部,还原已生成的NOx,运行时此区域过量空气系数在左右,保证锅炉炉膛主燃烧区足够高的温度水平。