薄壁零件车削加工方法探究
薄壁零件的数控车削加工探讨
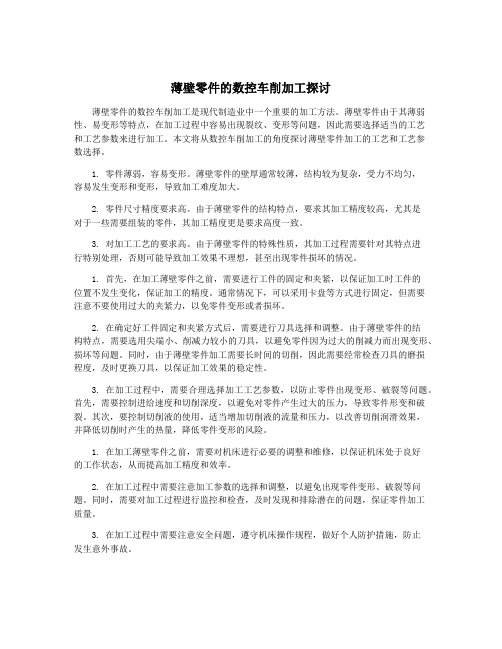
薄壁零件的数控车削加工探讨薄壁零件的数控车削加工是现代制造业中一个重要的加工方法。
薄壁零件由于其薄弱性、易变形等特点,在加工过程中容易出现裂纹、变形等问题,因此需要选择适当的工艺和工艺参数来进行加工。
本文将从数控车削加工的角度探讨薄壁零件加工的工艺和工艺参数选择。
1. 零件薄弱,容易变形。
薄壁零件的壁厚通常较薄,结构较为复杂,受力不均匀,容易发生变形和变形,导致加工难度加大。
2. 零件尺寸精度要求高。
由于薄壁零件的结构特点,要求其加工精度较高,尤其是对于一些需要组装的零件,其加工精度更是要求高度一致。
3. 对加工工艺的要求高。
由于薄壁零件的特殊性质,其加工过程需要针对其特点进行特别处理,否则可能导致加工效果不理想,甚至出现零件损坏的情况。
1. 首先,在加工薄壁零件之前,需要进行工件的固定和夹紧,以保证加工时工件的位置不发生变化,保证加工的精度。
通常情况下,可以采用卡盘等方式进行固定,但需要注意不要使用过大的夹紧力,以免零件变形或者损坏。
2. 在确定好工件固定和夹紧方式后,需要进行刀具选择和调整。
由于薄壁零件的结构特点,需要选用尖端小、削减力较小的刀具,以避免零件因为过大的削减力而出现变形、损坏等问题。
同时,由于薄壁零件加工需要长时间的切削,因此需要经常检查刀具的磨损程度,及时更换刀具,以保证加工效果的稳定性。
3. 在加工过程中,需要合理选择加工工艺参数,以防止零件出现变形、破裂等问题。
首先,需要控制进给速度和切削深度,以避免对零件产生过大的压力,导致零件形变和破裂。
其次,要控制切削液的使用,适当增加切削液的流量和压力,以改善切削润滑效果,并降低切削时产生的热量,降低零件变形的风险。
1. 在加工薄壁零件之前,需要对机床进行必要的调整和维修,以保证机床处于良好的工作状态,从而提高加工精度和效率。
2. 在加工过程中需要注意加工参数的选择和调整,以避免出现零件变形、破裂等问题。
同时,需要对加工过程进行监控和检查,及时发现和排除潜在的问题,保证零件加工质量。
薄壁零件车床加工方法的探讨

( 用专 用 夹具 加 工 薄壁 工 件 。 4)
2 防 止 和 减 少 薄 壁 工 件 变 形 的 方 法 ( ) 件 分 粗 、 加 工 , 加 工 后 进 行 时 效 处 理 , 除 1工 精 粗 消
( ) 圆对 内孔轴 线 的 径 向 圆跳 动量 00 ; 2外 .4 ( )右 端 面 与 左 端 面 轴 线 垂 直 度 为 o 0 3 .2、平 行 度 为
工 艺 与 装 备
4 9
薄壁 零 件 车 床加 工 方 法 的探 讨
田 宏 霞
( 州机 电职 业 技 术学 院 , 州 2 3 6 常 常 1 14)
摘 要 : 壁 零件 是 机 械加 工 中经 常 遇 到 的典 型 零 件 之 一 , 薄 一般 来说 , 车床 加 工 薄 壁零 件 时, 工件 的 安 用 在 装 、 具 的使 用、 工 方 法 等 方 面 , 刀 加 均有 较 多不 利 因素 , 而加 工 起 来 比 较 困难 . 不 注 意 , 因 稍 就会 导致 工件 精 度 达
起 热变 形 , 件 的尺 寸不 易 掌 握 。 工 1 一 般 薄 壁 零 件 的 加 工 装 夹 方 法
( ) 轴 向夹 紧力 , 薄 壁工 件 一 般 不 使 用 径 向夹 紧 4用 车
的 方 法 , 采 用 轴 向夹 紧 的 方 法 , 夹 紧 力 沿 刚 性较 好 的 应 使
轴线 方 向分 布 , 止 夹 紧变 形 。 防
( 工 件 壁 厚 2 r 长 度 2 0 m, 为 大 、 , 生 重 3) 0 m, a 5m 因 长 产
力 , 重 影 响 夹 紧 力 。 即 须 防 止夹 紧力 大 ( 转 第 6 严 下 O页 )
6 0
现 制 术 装 代 造技 与 备
薄壁类零件的车削工艺分析
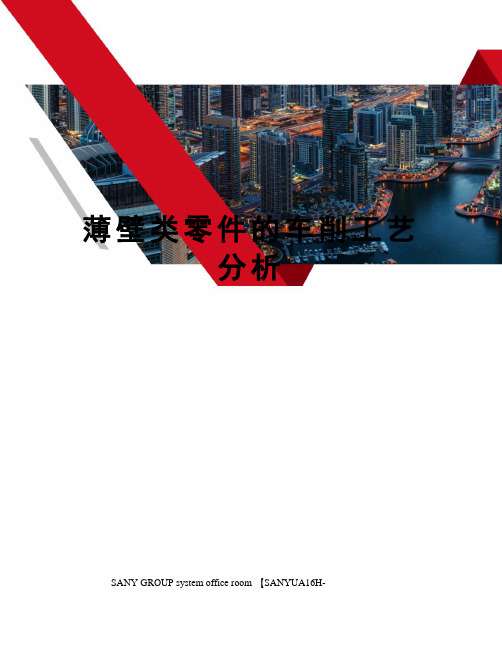
薄壁类零件的车削工艺分析SANY GROUP system office room 【SANYUA16H-薄壁类零件的车削工艺分析段立波一.引言薄壁类零件指的是零件壁厚与它的径向、轴向尺寸相比较,相差悬殊,一般为几十倍甚至上百倍的金属材料的零件,具有节省材料、结构简单等特点。
薄壁类零件已广泛地应用于各类石油机械部件。
但是薄壁类零件的车削加工是比较棘手的,具体的原因是因为薄壁类零件自身刚性差、强度弱,在车削加工中极容易变形,很难保证零件的加工质量。
如何提高薄壁类零件的加工精度是机械加工行业关心的话题。
二.薄壁类零件车削过程中常出现的问题、原因及解决办法我们在车削加工过程中,经常会碰到一些薄壁零件的加工。
如轴套薄壁件(图1),环类薄壁件(图2),盘类薄壁件(图3)。
本文详细分析了薄壁类零件的加工特点、防止变形的装夹方法、车刀材料、切削参数的选择及车刀几何角度。
进行了大量的实验,为以后更好地加工薄壁类零件,保证加工质量,提供了理论依据。
图1轴套薄壁件图2环类薄壁件图3盘类薄壁件1.薄壁类零件的加工特点1.1因零件壁薄,在使用通用夹具装夹时,在夹压力的作用下极易产生变形,而夹紧力不够零件又容易松动,从而影响零件的尺寸精度和形状精度。
如图4所示,当采用三爪卡盘夹紧零件时,在夹紧力的作用下,零件会微微变成三角形,车削后得到的是一个圆柱体。
但松开卡爪,取下零件后,由于零件弹性,又恢复成弧形三角形。
这时若用千分尺测量时,各个方向直径相同,但零件已变形不是圆柱体了,这种变形现象我们称之为等直径变形。
图4三爪卡盘装夹1.2因零件较薄,加工时的切削发热会引起零件变形,从而使零件尺寸难以控制。
对于膨胀系数较大的金属薄壁零件,如在一次安装中连续完成半精车和精车,由切削热引起零件的热变形,会对其尺寸精度产生极大影响,有时甚至会使零件卡死在芯轴类的夹具上。
1.3薄壁类零件加工内孔中,一般采用单刃镗刀加工,此时,当零件较长时,如果刀具参数及切削用量处理不当,将造成排屑困难,影响加工质量,损伤刀具。
某薄壁零件车削加工工艺研究
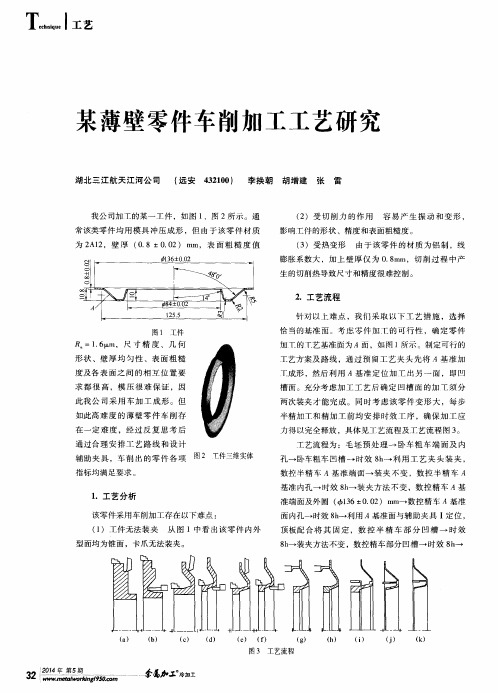
指标 均满 足要求 。
1 .工艺分析
该零 件采用 车 削加工 存在 以下难 点 :
( 1 )工 件无法 装 夹 从 图 1中看 出该 零 件 内外
准端 面及外 圆 ( 4 , 1 3 6. 4 - 0 . 0 2 )m m 一 数控 精 车 4基准
面 内孔一 时效 8 h 一利 用 A基 准面 与辅 助夹 具 I定 位 , 顶 板配 合 将 其 固 定 ,数 控 半 精 车 部 分 凹槽 一 时 效
l T件三维实体 辅助 夹 具 ,车 削 出 的 零 件 各 项 图2
半精加 T 和精 加 工 前 均 安 排 时 效 _ T序 ,确 保 加 工 应
力得 以完全 释放 ,具体 见 艺流程 及 _ 丁 艺流 程 图 3 。 工艺 流程 为 :毛 坯 预 处 理一 卧 车 粗 车 端 面 及 内 孔一 卧车粗 车 凹槽 一 时 效 8 h 一 利用工艺夹头装 夹, 数控 半精 车 A基 准 端 面 一 装 夹 不 变 ,数 控 半 精 车 A 基准 内孔 一 时 效 8 h 一 装 夹 方法 不 变 ,数控 精 车 A基
槽部分。
助夹具 I 拧 紧 ,通 过 辅 助 夹 具 Ⅱ上 的 端 面 和 锥 面 将
工件最 大 限度地 压 紧 固定 ( 见图 7 ) 。最 后 利用 普 通
3 .夹具设计
进 行 凹槽 半 精 加 工 和 精 加 工 工 序 时 ,工 件 的 刚 性 已经很 弱 ,无 法进 行装 夹 ,我们 通过 辅助 夹具 I和
Ⅱ解 决该难 题 。
自定 心卡 盘装 夹 即可 进 行 工 艺 夹 头 的去 除 及 剩 余 凹 槽 的半 精 和精加 T 。
( 1 )辅 助夹具 I 结构 如 图 4所 示 ,夹具 I 的内 型面 作为工 件 的定位 面 ,为此 内型 面形状 与 工件 的 A
(整理)薄壁零件车削加工方法探讨

薄壁零件车削加工方法探讨1. 薄壁零件的加工特点1.1 薄壁零件不能承受较大的径向力,用通用夹具安装困难。
1.2 薄壁零件的刚性差,在夹紧力的作用下,极易产生变形,常态下工件的弹性复原,会影响工件的尺寸精度和形状精度。
1.3 工件受切削热的影响,尺寸精度不易控制。
1.4 由于切削力的影响,工件易产生变形或振动,尺寸精度和表面粗糙度不易控制。
1.5 薄壁零件刚性差,不能采用较大的切削用量,生产效率低。
因此合理的选择装夹方法,加工方法,切削用量,减少振动及充分冷却和检测都是保证加工薄壁零件的关键。
2. 薄壁零件的装夹方法2.1 通用软爪定位装夹,选择正确的夹紧力作用点,使夹紧力作用在工件刚性较好的部位,适用于形状和尺寸公差要求不严的零件加工优点:装卸方便长度可定位,看承受较大切削力。
缺点:零件定位点较集中,零件加紧后变形较严重。
2.2 大面积扇形软爪装夹:采用扇形软爪的三爪卡盘,按与加工零件的装夹面动配合的要求,加工出卡爪的工作面,增大与零件的接触面积。
优点:增大夹紧力的作用面积,使工件支持面增大,夹紧力均匀分布在工作面上,可加大切削用量,不易产生变形。
缺点:扇形软爪不易加工。
2.3 芯棒装夹2.3.1 采用椎体芯轴装夹,将零件直接套在椎体芯轴加工。
2.3.2 采用圆柱芯轴装夹,将零件装在芯轴上采用轴线压紧。
减小零件径向变形。
优点:装卸零件方便,能保证较高的同心度,技术要求。
缺点:零件内孔被芯轴划伤。
2.4 磁力吸盘装夹:采用磁力吸盘将零件吸附在吸盘上,这时零件只受轴向力,而径向不受力。
优点:可一次较高零件内外圆。
缺点:零件找正比较麻烦,应用范围小。
3. 薄壁零件较高方法的选择3.1 先粗后精先粗加工出零件的外圆和内孔,外圆和内孔均匀留0.5 —0.8 毫米余量,端面单边留0.25 —0.3 毫米余量,然后选择适当的装夹方法,将零件精加工到图纸尺寸要求。
3.2 先内后外先加工内孔,以为孔较外圆难加工,易产生变形。
薄壁零件的车削技巧

薄壁零件的车削技巧薄壁零件是指壁厚相对较薄的零件,在车削加工中,由于其壁厚薄,容易产生变形和振动,所以需要特殊的车削技巧来保证加工质量。
本文将介绍薄壁零件的车削技巧。
首先,保持机床的稳定性。
薄壁零件在车削时容易产生振动,而振动会影响加工精度和表面质量。
为了保持机床的稳定性,首先要确保机床具备足够的刚性和抗震性,同时要确保机床的紧固件处于良好的状态,以免因紧固件松动而导致振动。
此外,还可以通过合理的刀具和夹具选择来减少振动,例如选择合适的刀具长度和刚度,使用刀柄的支撑力等。
其次,选择合适的切削参数。
在车削薄壁零件时,要选择合适的切削参数,以保证刀具的切削力不会过大。
一般来说,应尽可能采用小的进给量和切削深度,降低切削力。
另外,应注意保持刀具的尖角和刃磨状况良好,以减小刀具的切削力。
第三,选择合适的刀具和夹具。
在车削薄壁零件时,要选择合适的刀具和夹具,以提高加工的稳定性和精度。
刀具要选择具有较高刚度和切削性能的硬质合金刀具,以减小切削力和振动。
夹具要选择刚性好的夹具,以确保零件的稳定夹持,同时要避免夹持过紧而导致变形。
第四,采用适当的刀具路径。
在车削薄壁零件时,为了避免产生振动和变形,应采用适当的刀具路径。
一般来说,应优先选择切削路径中的外切削和镗削,避免内切削和过切削,这样可以减小刀具对零件的负荷,减少振动和变形。
第五,采用适当的刀具进给方式。
在车削薄壁零件时,应采用适当的刀具进给方式,以减小切削力和振动。
一般来说,可以采用铣削进给,即刀具的进给方向与工件的旋转方向相同,这样可以减小刀具对零件的冲击力和振动。
最后,进行切削加工时要进行监控和调整。
在车削薄壁零件时,要进行监控和调整,以确保加工质量。
可以通过加工中的监测手段,例如振动传感器、力传感器等,对加工过程中的切削力、振动等进行监测,及时调整切削参数和刀具路径,以减小振动和变形,保证加工质量。
总之,薄壁零件的车削技巧包括保持机床稳定性、选择合适的切削参数、刀具和夹具、采用适当的刀具路径和进给方式,以及进行监控和调整等。
薄壁零件的车削方法

薄壁零件的车削方法1.用一次装夹车薄壁零件:车削短小薄壁工件时,为了保证内外圆轴线的同轴度,可用一次装夹车削。
例:薄壁衬套,材料为锡青铜,工件壁厚仅2mm,同轴度公差为0.025mm,精度要求较高。
车削方法见下图:夹持棒料,车出长度45mm,粗车内外圆均留0.5mm余量,钻,粗车内孔时,要求长度比图样长2mm即可。
以增加工件的刚性,加注切削液,使工件充分冷却后,精车内外圆至尺寸。
(油槽在半精车后拉出)切断工件,最后装夹在心轴上,车削另一端面和倒角。
2.用扇形卡爪及心轴装夹薄壁工件:例:薄壁套筒如图,车削方法:粗车留精车余量1~1.5mm,精车时,装夹在扇形软卡中,精车内孔及φ72H7,外圆φ980-0.1及端面A符合图样要求,然后以内孔和大端面为基准,夹在弹性胀力心轴上,即可精车外圆。
3.在花盘上车削薄壁工件:直径较大,尺寸精度和形位精度都较高的圆盘薄壁工件。
可装夹在花盘上加工。
车削方法:先装夹在三爪卡盘上粗车内孔及外圆,各留1~1.5mm余量,长度尺寸车至92+0.3+0.2,并精磨两端面至长度92。
然后装夹在花盘上精车内孔及外圆,精车内孔的装夹方法见图。
先在花盘端面上车出一凸台,凸台的直径和工件之间留0.5~1mm的间隙,(不用作定心)。
用螺栓,压板压紧工件端面,压紧力要均匀。
找正后,即可车削φ132H7, φ262H7内孔及内端平面。
精车外圆时的方法见下图:将三点接触压板(压板上有三条槽以让开压板)适当压紧,松开并取下压板及螺钉,即可车削外圆,使之符合图样要求.上面的压紧方法,因为压紧力在轴向,所以不容易引起变形。
4.在专用夹具上车削薄壁零件:如图,工件装上夹具后,当拧紧螺钉2时,压紧圈1便沿着斜面将工件压紧,即可车削工件的内孔,外圆及端面。
5.增加辅助支承车削薄壁零件:车削内孔精度要求高的薄壁零件时,可采用辅助支承来增加工件的刚性.6.增加工艺肋车削薄壁工件.在工件的装夹部位特制几根工艺支撑肋,使夹紧力作用在肋上,可减少变形.二.减少工件变形的方法:1.工件分粗精车,消除粗车时切削力过大而产生的变形,粗车后,使工件得到自然冷却,消除在精车时可能产生的热变形。
薄壁零件的数控车削加工探讨

薄壁零件的数控车削加工探讨随着工业的不断发展,薄壁零件在机械制造领域中的应用越来越广泛。
薄壁零件因其结构轻巧、重量小、强度高等特点,被广泛应用于汽车、航空航天、电子等领域。
薄壁零件的加工却是一项技术难题,尤其是数控车削加工对薄壁零件的加工要求更加严格。
本文将探讨薄壁零件的数控车削加工技术,并就其加工过程中的难点和解决方法进行深入探讨。
一、薄壁零件的特点薄壁零件在机械制造中具有独特的优势,主要表现在以下几个方面:1. 结构轻巧:薄壁零件由于壁厚较薄,因此重量相对较轻,适合在一些对重量要求较高的场合使用,比如汽车、航空航天等领域。
2. 外形复杂:薄壁零件的结构通常比较复杂,需要经过多道工序的加工才能完成,对加工工艺要求较高。
3. 强度高:尽管薄壁零件壁厚较薄,但是由于采用了特殊的材料和工艺,使得薄壁零件具有比较高的强度,能够满足工程应用的需要。
由于薄壁零件的特点,使得其在加工过程中存在一定的难度和挑战,尤其是在数控车削加工过程中更加明显。
二、数控车削加工对薄壁零件的要求数控车床是一种通过计算机程序控制刀具在数控车床上进行切削加工的设备,其具有高速度、高精度、高效率的特点,因此被广泛应用于薄壁零件的加工中。
由于薄壁零件的特殊性,数控车削加工对薄壁零件有着更高的要求。
1. 加工精度要求高:薄壁零件通常具有复杂的结构和精密的尺寸要求,因此数控车削加工需要保证加工精度,避免零件出现尺寸偏差和表面粗糙度。
2. 避免变形和残余应力:薄壁零件在加工过程中容易发生热变形和残余应力,因此在数控车削加工过程中需要采取有效的措施,避免零件变形和应力积累。
3. 提高加工效率:薄壁零件的加工通常需要多道工序,加工过程中需要保证高效率,提高生产效率。
在薄壁零件的数控车削加工过程中,存在一些难点需要克服:1. 大刚度:由于薄壁零件的壁厚较薄,零件的刚度相对较小,容易导致变形和振动,影响加工精度和表面质量。
2. 刀具选择:薄壁零件具有一定的脆性,因此刀具的选择对加工质量有着重要影响,需要选择合适的刀具以提高加工质量。
薄壁零件车削加工方法探究
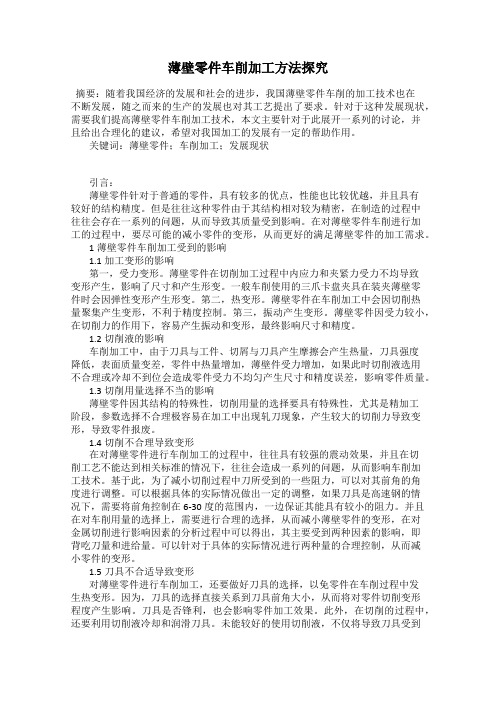
薄壁零件车削加工方法探究摘要:随着我国经济的发展和社会的进步,我国薄壁零件车削的加工技术也在不断发展,随之而来的生产的发展也对其工艺提出了要求。
针对于这种发展现状,需要我们提高薄壁零件车削加工技术,本文主要针对于此展开一系列的讨论,并且给出合理化的建议,希望对我国加工的发展有一定的帮助作用。
关键词:薄壁零件;车削加工;发展现状引言:薄壁零件针对于普通的零件,具有较多的优点,性能也比较优越,并且具有较好的结构精度。
但是往往这种零件由于其结构相对较为精密,在制造的过程中往往会存在一系列的问题,从而导致其质量受到影响。
在对薄壁零件车削进行加工的过程中,要尽可能的减小零件的变形,从而更好的满足薄壁零件的加工需求。
1薄壁零件车削加工受到的影响1.1加工变形的影响第一,受力变形。
薄壁零件在切削加工过程中内应力和夹紧力受力不均导致变形产生,影响了尺寸和产生形变。
一般车削使用的三爪卡盘夹具在装夹薄壁零件时会因弹性变形产生形变。
第二,热变形。
薄壁零件在车削加工中会因切削热量聚集产生变形,不利于精度控制。
第三,振动产生变形。
薄壁零件因受力较小,在切削力的作用下,容易产生振动和变形,最终影响尺寸和精度。
1.2切削液的影响车削加工中,由于刀具与工件、切屑与刀具产生摩擦会产生热量,刀具强度降低,表面质量变差,零件中热量增加,薄壁件受力增加,如果此时切削液选用不合理或冷却不到位会造成零件受力不均匀产生尺寸和精度误差,影响零件质量。
1.3切削用量选择不当的影响薄壁零件因其结构的特殊性,切削用量的选择要具有特殊性,尤其是精加工阶段,参数选择不合理极容易在加工中出现轧刀现象,产生较大的切削力导致变形,导致零件报废。
1.4切削不合理导致变形在对薄壁零件进行车削加工的过程中,往往具有较强的震动效果,并且在切削工艺不能达到相关标准的情况下,往往会造成一系列的问题,从而影响车削加工技术。
基于此,为了减小切削过程中刀所受到的一些阻力,可以对其前角的角度进行调整。
浅析薄壁套类工件的车削加工技术
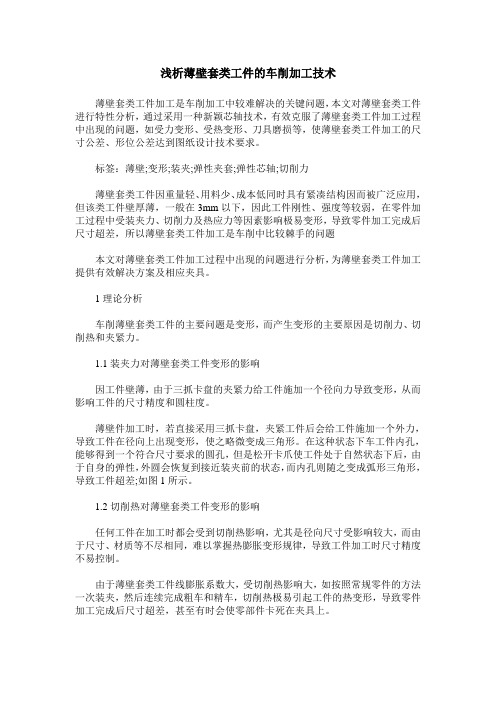
浅析薄壁套类工件的车削加工技术薄壁套类工件加工是车削加工中较难解决的关键问题,本文对薄壁套类工件进行特性分析,通过采用一种新颖芯轴技术,有效克服了薄壁套类工件加工过程中出现的问题,如受力变形、受热变形、刀具磨损等,使薄壁套类工件加工的尺寸公差、形位公差达到图纸设计技术要求。
标签:薄壁;变形;装夹;弹性夹套;弹性芯轴;切削力薄壁套类工件因重量轻、用料少、成本低同时具有紧凑结构因而被广泛应用,但该类工件壁厚薄,一般在3mm以下,因此工件刚性、强度等较弱,在零件加工过程中受装夹力、切削力及热应力等因素影响极易变形,导致零件加工完成后尺寸超差,所以薄壁套类工件加工是车削中比较棘手的问题本文对薄壁套类工件加工过程中出现的问题进行分析,为薄壁套类工件加工提供有效解决方案及相应夹具。
1理论分析车削薄壁套类工件的主要问题是变形,而产生变形的主要原因是切削力、切削热和夹紧力。
1.1装夹力对薄壁套类工件变形的影响因工件壁薄,由于三抓卡盘的夹紧力给工件施加一个径向力导致变形,从而影响工件的尺寸精度和圆柱度。
薄壁件加工时,若直接采用三抓卡盘,夹紧工件后会给工件施加一个外力,导致工件在径向上出现变形,使之略微变成三角形。
在这种状态下车工件内孔,能够得到一个符合尺寸要求的圆孔,但是松开卡爪使工件处于自然状态下后,由于自身的弹性,外圆会恢复到接近装夹前的状态,而内孔则随之变成弧形三角形,导致工件超差;如图1所示。
1.2切削热对薄壁套类工件变形的影响任何工件在加工时都会受到切削热影响,尤其是径向尺寸受影响较大,而由于尺寸、材质等不尽相同,难以掌握热膨胀变形规律,导致工件加工时尺寸精度不易控制。
由于薄壁套类工件线膨胀系数大,受切削热影响大,如按照常规零件的方法一次装夹,然后连续完成粗车和精车,切削热极易引起工件的热变形,导致零件加工完成后尺寸超差,甚至有时会使零部件卡死在夹具上。
1.3切削力对薄壁套类工件变形影响在切削力(特别是径向切削力)作用下,容易产生振动和变形,影响工件的尺寸精度,形状、位置精度和表面粗糙度[1]。
薄壁零件的数控车削加工探讨
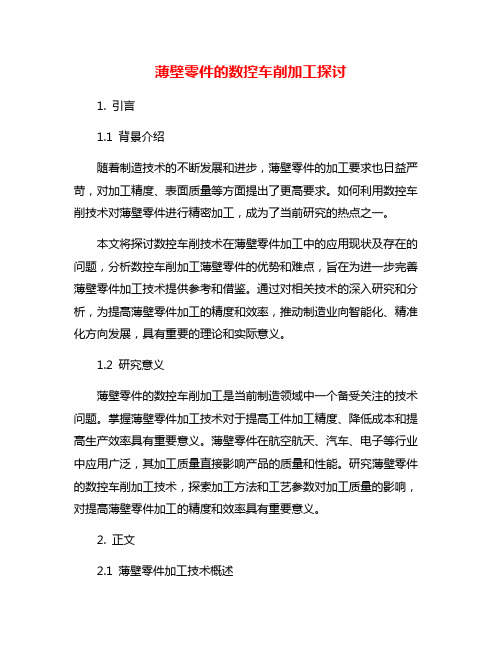
薄壁零件的数控车削加工探讨1. 引言1.1 背景介绍随着制造技术的不断发展和进步,薄壁零件的加工要求也日益严苛,对加工精度、表面质量等方面提出了更高要求。
如何利用数控车削技术对薄壁零件进行精密加工,成为了当前研究的热点之一。
本文将探讨数控车削技术在薄壁零件加工中的应用现状及存在的问题,分析数控车削加工薄壁零件的优势和难点,旨在为进一步完善薄壁零件加工技术提供参考和借鉴。
通过对相关技术的深入研究和分析,为提高薄壁零件加工的精度和效率,推动制造业向智能化、精准化方向发展,具有重要的理论和实际意义。
1.2 研究意义薄壁零件的数控车削加工是当前制造领域中一个备受关注的技术问题。
掌握薄壁零件加工技术对于提高工件加工精度、降低成本和提高生产效率具有重要意义。
薄壁零件在航空航天、汽车、电子等行业中应用广泛,其加工质量直接影响产品的质量和性能。
研究薄壁零件的数控车削加工技术,探索加工方法和工艺参数对加工质量的影响,对提高薄壁零件加工的精度和效率具有重要意义。
2. 正文2.1 薄壁零件加工技术概述薄壁零件是指壁厚较薄的零件,通常在汽车、航空航天等领域中广泛应用。
薄壁零件的加工技术在制造业中起着至关重要的作用。
在薄壁零件的加工中,最主要的挑战之一是加工过程中如何保持零件的形状和尺寸精度。
因为薄壁零件的壁厚较薄,加工过程中很容易产生变形,从而影响零件的质量和使用效果。
为了解决这一问题,可以通过调整加工参数、优化刀具选择和加工路径等方式来降低零件变形的可能性。
薄壁零件的加工还需要考虑到表面质量和加工效率的问题。
薄壁零件通常具有较高的表面要求,因此在加工过程中需要采用合适的刀具和加工策略来保证零件表面的光洁度和精度。
为了提高加工效率,可以通过提高切削速度、加工进给速度等方式来缩短加工周期。
薄壁零件的加工技术在现代制造业中具有重要意义,通过不断优化加工工艺和加工方法,可以更好地满足市场需求,提高产品质量和效率。
2.2 薄壁零件加工存在的问题1. 刀具选择困难:薄壁零件通常由软性材料制成,而软性材料容易产生振动和变形,因此在选择合适的刀具时需要考虑刀具的刚度和稳定性,以避免对薄壁零件造成损伤。
薄壁件加工
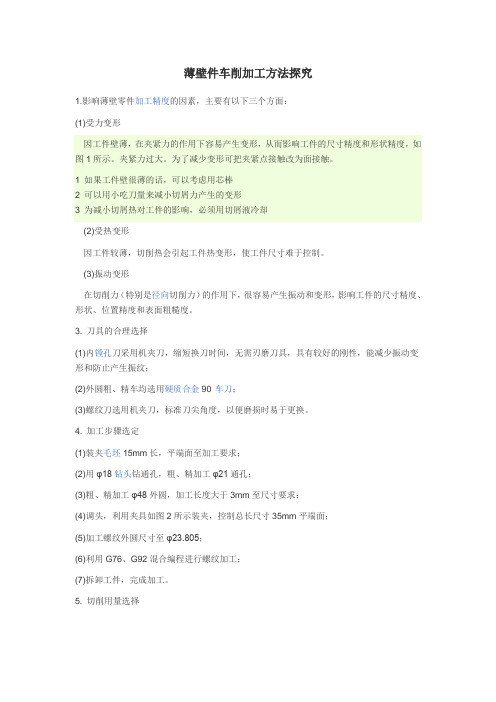
薄壁件车削加工方法探究1.影响薄壁零件加工精度的因素,主要有以下三个方面:(1)受力变形因工件壁薄,在夹紧力的作用下容易产生变形,从而影响工件的尺寸精度和形状精度,如图1所示。
夹紧力过大。
为了减少变形可把夹紧点接触改为面接触。
1 如果工件壁很薄的话,可以考虑用芯棒2 可以用小吃刀量来减小切屑力产生的变形3 为减小切屑热对工件的影响,必须用切屑液冷却(2)受热变形因工件较薄,切削热会引起工件热变形,使工件尺寸难于控制。
(3)振动变形在切削力(特别是径向切削力)的作用下,很容易产生振动和变形,影响工件的尺寸精度、形状、位置精度和表面粗糙度。
3. 刀具的合理选择(1)内镗孔刀采用机夹刀,缩短换刀时间,无需刃磨刀具,具有较好的刚性,能减少振动变形和防止产生振纹;(2)外圆粗、精车均选用硬质合金90°车刀;(3)螺纹刀选用机夹刀,标准刀尖角度,以便磨损时易于更换。
4. 加工步骤选定(1)装夹毛坯15mm长,平端面至加工要求;(2)用φ18钻头钻通孔,粗、精加工φ21通孔;(3)粗、精加工φ48外圆,加工长度大于3mm至尺寸要求;(4)调头,利用夹具如图2所示装夹,控制总长尺寸35mm平端面;(5)加工螺纹外圆尺寸至φ23.805;(6)利用G76、G92混合编程进行螺纹加工;(7)拆卸工件,完成加工。
5. 切削用量选择(1)内孔粗车时,主轴转速为500~600r/min,进给速度F100~F150,留精车余量0.2~0.3mm;(2)内孔精车时,主轴转速为1100~1200 r/min,为取得较好的表面粗糙度选用较低的进给速度F30~F45,采用一次走刀加工完成;(3)外圆粗车时,主轴转速为1100~1200 r/min,进给速度F100~F150,留精车余量0.3~0.5mm;(4)外圆精车时,主轴转速为1100~1200 r/min,进给速度F30~F45,采用一次走刀加工完成。
套类薄壁零件车削加工方法研究

套类薄壁零件车削加工方法研究套类薄壁零件在机械制造中应用非常广泛,其零件结构往往比较复杂,加工难度较大,但又因为其应用比较普遍,所以对于生产厂家来说,如何提高套类薄壁零件的生产效率和生产质量,成为一道热门问题。
车削加工作为数控加工中常见的一种加工方法,具有高效、精度高、加工质量好等优点,如何应用车削加工方法研究套类薄壁零件加工技术,这是一个非常有意义的问题。
本文主要介绍套类薄壁零件车削加工方法的研究,主要包括套类薄壁零件特点、车削加工方法的优点以及套类薄壁零件车削加工方法的具体研究。
一、套类薄壁零件的特点套类薄壁零件的特点主要体现在以下几个方面:1. 材质要求高:套类薄壁零件材质有很高的要求,它可以使用各种金属材料,如钢铁、铝合金、钛合金等。
材料质量好坏直接影响套类薄壁零件的质量。
2. 结构比较复杂:套类薄壁零件需要经过多次加工才能形成,其加工面也较多,需要进行多次车削加工才能完成。
3. 壁厚薄:套类薄壁零件通常需要保持薄壁的特性,同时也需要保证加工、装配、使用等环节的强度和稳定性。
这对车削加工的精准度和工艺控制要求非常高。
4. 表面质量要求高:套类薄壁零件需要保证光洁度、平整度、同心度等一系列表面质量指标的要求,这对车削加工的加工方式和加工工艺方案都有很高的要求。
二、车削加工方法的优点车削加工是工业制造中比较常见的加工方法,其优点包括以下几方面:1. 精度高:车削加工是通过钻法、扩棒法、插坐标法、槽切法等多种切削方法实现的,因此加工精度非常高,能满足高精度零件的加工要求。
2. 加工效率高:车削加工是数控加工中的一种常见方法,其加工效率高,可以实现批量加工,使产品成本降低。
3. 可加工的材料范围广:车削加工可加工的材料包括金属、非金属和各种复合材料,因此适用范围比较广。
4. 长期稳定:车削加工的设备精度高,同时数控技术的应用能够让加工过程实现长期稳定,成品的规格精度也能够得到有效保障。
三、套类薄壁零件车削加工方法的具体研究1. 切削参数的研究切削参数对车削加工的质量和效率影响比较大,因此,对套类薄壁零件车削加工时的切削参数进行研究和优化是非常必要的。
薄壁类零件的车削工艺分析

薄壁类零件的车削工艺分析段立波亠•引言薄壁类零件指的是零件壁厚与它的径向、轴向尺寸相比较,相差悬殊,一般为几十倍甚至上百倍的金属材料的零件,具有节省材料、结构简单等特点。
薄壁类零件已广泛地应用于各类石油机械部件。
但是薄壁类零件的车削加工是比较棘手的,具体的原因是因为薄壁类零件自身刚性差、强度弱,在车削加工中极容易变形,很难保证零件的加工质量。
如何提高薄壁类零件的加工精度是机械加工行业关心的话题。
•薄壁类零件车削过程中常出现的问题、原因及解决办法我们在车削加工过程中,经常会碰到一些薄壁零件的加工。
如轴套薄壁件(图1),环类薄壁件(图2),盘类薄壁件(图3)。
本文详细分析了薄壁类零件的加工特点、防止变形的装夹方法、车刀材料、切削参数的选择及车刀几何角度。
进行了大量的实验,为以后更好地加工薄壁类零件,保证加工质量,提供了理论依据。
图1轴套薄壁件图2环类薄壁件图3盘类溥壁件1. 薄壁类零件的加工特点1.1因零件壁薄,在使用通用夹具装夹时,在夹压力的作用下 极易产生变形,而夹紧力不够零件又容易松动,从而影响零件的尺 寸精度和形状精度。
如图4所示,当采用三爪卡盘夹紧零件时,在夹紧力的作用下, 零件会微微变成三角形,车削后得到的是一个圆柱体。
但松开卡爪, 取下零件后,由于零件弹性,又恢复成弧形三角形。
这时若用千分 尺测量时,各个方向直径相同,但零件已变形不是圆柱体了,这种 变形现象我们称之为等直径变形。
7 35Jr' 卜 A 討图4三爪卡盘装夹1.2因零件较薄,加工时的切削发热会引起零件变形,从而使零件尺寸难以控制。
对于膨胀系数较大的金属薄壁零件,如在一次安装中连续完成半精车和精车,由切削热引起零件的热变形,会对其尺寸精度产生极大影响,有时甚至会使零件卡死在芯轴类的夹具上。
1.3薄壁类零件加工内孔中,一般采用单刃镗刀加工,此时,当零件较长时,如果刀具参数及切削用量处理不当,将造成排屑困难,影响加工质量,损伤刀具。
薄壁零件数控车工加工工艺的探讨
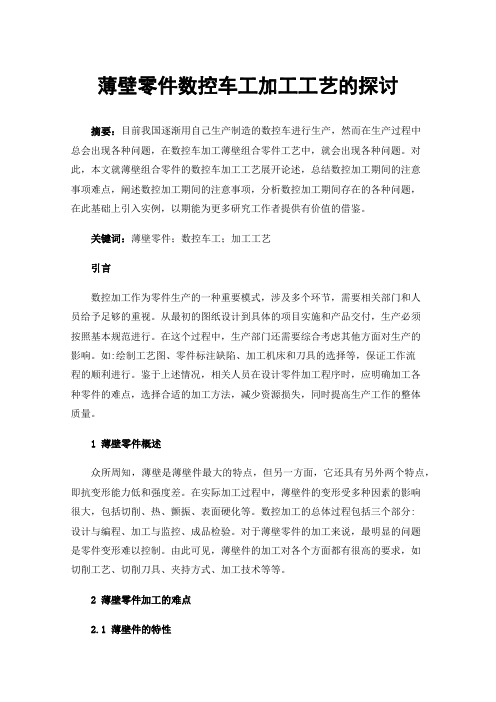
薄壁零件数控车工加工工艺的探讨摘要:目前我国逐渐用自己生产制造的数控车进行生产,然而在生产过程中总会出现各种问题,在数控车加工薄壁组合零件工艺中,就会出现各种问题。
对此,本文就薄壁组合零件的数控车加工工艺展开论述,总结数控加工期间的注意事项难点,阐述数控加工期间的注意事项,分析数控加工期间存在的各种问题,在此基础上引入实例,以期能为更多研究工作者提供有价值的借鉴。
关键词:薄壁零件;数控车工;加工工艺引言数控加工作为零件生产的一种重要模式,涉及多个环节,需要相关部门和人员给予足够的重视。
从最初的图纸设计到具体的项目实施和产品交付,生产必须按照基本规范进行。
在这个过程中,生产部门还需要综合考虑其他方面对生产的影响。
如:绘制工艺图、零件标注缺陷、加工机床和刀具的选择等,保证工作流程的顺利进行。
鉴于上述情况,相关人员在设计零件加工程序时,应明确加工各种零件的难点,选择合适的加工方法,减少资源损失,同时提高生产工作的整体质量。
1薄壁零件概述众所周知,薄壁是薄壁件最大的特点,但另一方面,它还具有另外两个特点,即抗变形能力低和强度差。
在实际加工过程中,薄壁件的变形受多种因素的影响很大,包括切削、热、颤振、表面硬化等。
数控加工的总体过程包括三个部分:设计与编程、加工与监控、成品检验。
对于薄壁零件的加工来说,最明显的问题是零件变形难以控制。
由此可见,薄壁件的加工对各个方面都有很高的要求,如切削工艺、切削刀具、夹持方式、加工技术等等。
2薄壁零件加工的难点2.1薄壁件的特性与一般零件相比,薄壁组合零件具有零件轻、省资源等特点,在各个领域均有体现。
但在实际加工时,薄壁组合零件具有不稳定、易变性等特性,而这也是加工过程应注重的问题。
从其结构来看,薄壁组合零件硬度低,易受压力、温度等因素影响而产生形变,既会影响零件整体尺寸,也会降低其在机械设备中的具体运行情况,进而造成不必要的损失。
2.2刀具的选择薄壁组合零件加工的另一个难点在于刀具的选择。
薄壁工件的车削加工工艺详细介绍
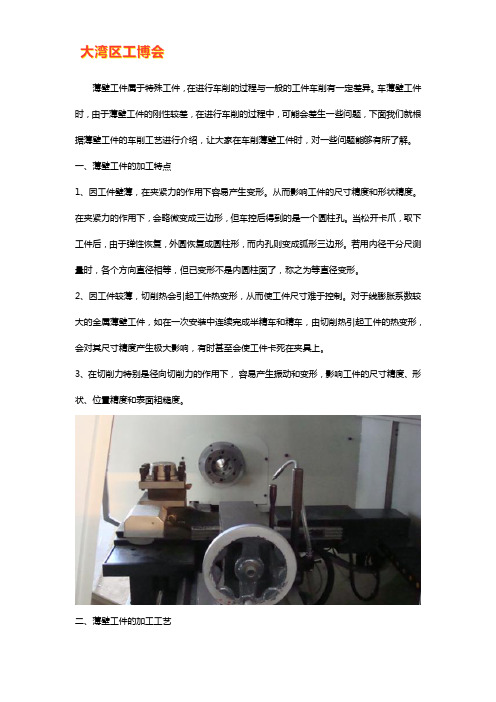
薄壁工件属于特殊工件,在进行车削的过程与一般的工件车削有一定差异。
车薄壁工件时,由于薄壁工件的刚性较差,在进行车削的过程中,可能会差生一些问题,下面我们就根据薄壁工件的车削工艺进行介绍,让大家在车削薄壁工件时,对一些问题能够有所了解。
一、薄壁工件的加工特点1、因工件壁薄,在夹紧力的作用下容易产生变形。
从而影响工件的尺寸精度和形状精度。
在夹紧力的作用下,会略微变成三边形,但车控后得到的是一个圆柱孔。
当松开卡爪,取下工件后,由于弹性恢复,外圆恢复成圆柱形,而内孔则变成弧形三边形。
若用内径千分尺测量时,各个方向直径相等,但已变形不是内圆柱面了,称之为等直径变形。
2、因工件较薄,切削热会引起工件热变形,从而使工件尺寸难于控制。
对于线膨胀系数较大的金属薄壁工件,如在一次安装中连续完成半精车和精车,由切削热引起工件的热变形,会对其尺寸精度产生极大影响,有时甚至会使工件卡死在夹具上。
3、在切削力特别是径向切削力的作用下,容易产生振动和变形,影响工件的尺寸精度、形状、位置精度和表面粗糙度。
二、薄壁工件的加工工艺1、工件分粗、精车阶段精车时,由于切削余量较大,夹紧力稍大些,变形也相应大些;精车时,夹紧力可稍小些,一方面夹紧变形小,另一方面精车时还可以消除粗车时因切削力过大而产生的变形。
2、合理选用道具的集合参数精车薄壁工件时,刀柄的刚度要求高,车刀的修光刃不易过长,一般取0.2—0.3mm,刃口要锋利。
3、增加装夹接触面采用开缝套筒或一些特制的软卡爪。
使接触面增大,让夹紧力均匀分布在工件上,从而使工件夹紧时不易产生变形。
4、应采用轴向夹紧夹具车薄壁工件时,工件靠轴向夹紧套(螺纹套)的端面实现轴向夹紧,由于夹紧力沿工件轴向分布,而工件轴向刚度大,不易产生夹紧变形。
5、增加工艺肋有些薄壁工件在其装夹部位特制几根工艺肋,以增强此处刚性,使夹紧力作用在工艺肋上,以减少工件的变形,加工完毕后,再去掉工艺肋。
6、充分浇注切削液通过充分浇注切削液,降低切削温度,减少工件热变形。
数控车床车削大直径薄壁零件方法探析
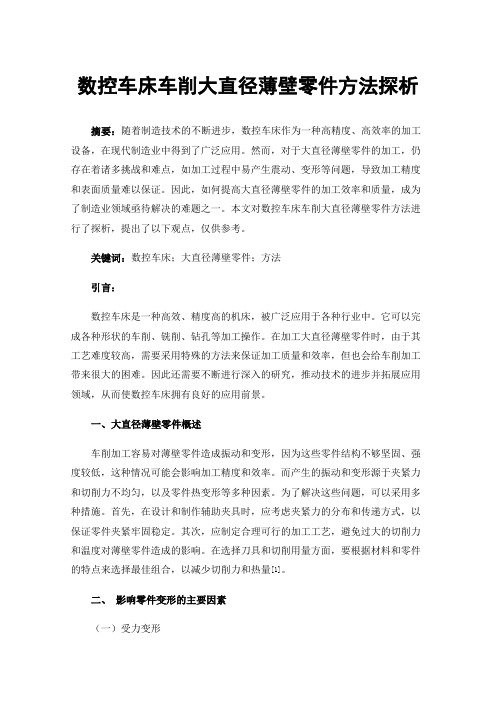
数控车床车削大直径薄壁零件方法探析摘要:随着制造技术的不断进步,数控车床作为一种高精度、高效率的加工设备,在现代制造业中得到了广泛应用。
然而,对于大直径薄壁零件的加工,仍存在着诸多挑战和难点,如加工过程中易产生震动、变形等问题,导致加工精度和表面质量难以保证。
因此,如何提高大直径薄壁零件的加工效率和质量,成为了制造业领域亟待解决的难题之一。
本文对数控车床车削大直径薄壁零件方法进行了探析,提出了以下观点,仅供参考。
关键词:数控车床;大直径薄壁零件;方法引言:数控车床是一种高效、精度高的机床,被广泛应用于各种行业中。
它可以完成各种形状的车削、铣削、钻孔等加工操作。
在加工大直径薄壁零件时,由于其工艺难度较高,需要采用特殊的方法来保证加工质量和效率,但也会给车削加工带来很大的困难。
因此还需要不断进行深入的研究,推动技术的进步并拓展应用领域,从而使数控车床拥有良好的应用前景。
一、大直径薄壁零件概述车削加工容易对薄壁零件造成振动和变形,因为这些零件结构不够坚固、强度较低,这种情况可能会影响加工精度和效率。
而产生的振动和变形源于夹紧力和切削力不均匀,以及零件热变形等多种因素。
为了解决这些问题,可以采用多种措施。
首先,在设计和制作辅助夹具时,应考虑夹紧力的分布和传递方式,以保证零件夹紧牢固稳定。
其次,应制定合理可行的加工工艺,避免过大的切削力和温度对薄壁零件造成的影响。
在选择刀具和切削用量方面,要根据材料和零件的特点来选择最佳组合,以减少切削力和热量[1]。
二、影响零件变形的主要因素(一)受力变形当工件壁薄时,夹紧力会引起变形,从而影响尺寸和形状的准确度。
为了避免这种情况,需要采用合适的夹紧方法进行加工,以确保工件的精度和质量。
(二)受热变形在切削加工过程中,由于工件材料特性和壁薄结构,产生大量热量,导致工件热变形使尺寸难以控制。
这需要采取降温措施或者改进加工方式以减少热源。
三、零件变形的控制措施(一)装夹方式在加工工件时,夹紧方式是确保精度和质量的关键因素之一。
薄壁零件的数控车削加工探讨

薄壁零件的数控车削加工探讨一、薄壁零件在数控车削加工中的问题1. 变形问题:薄壁零件在数控车削加工中容易受到刀具切削力的影响,从而产生变形。
尤其是在加工过程中,由于热变形效应的存在,薄壁零件更容易出现变形现象。
变形不仅会影响零件的尺寸精度和几何形状,还会降低零件的使用寿命和性能。
2. 振动问题:由于薄壁零件的结构特点,容易受到切削力的作用而产生振动现象。
振动不仅会影响加工质量,还会加剧刀具磨损、降低加工精度、影响加工表面质量等问题。
3. 切屑问题:薄壁零件在数控车削加工中,由于切削力的作用,容易产生大量的切屑,而这些切屑往往会对加工表面造成损坏,同时也会对工件和刀具造成损伤。
以上问题对薄壁零件的加工质量和加工效率都会产生较大的影响。
如何解决这些问题,提高薄壁零件的加工质量和效率,是当前数控车削加工中的一个重要课题。
二、解决问题的方法和技术1. 刀具选择和切削参数的优化:在数控车削加工中,合理选择刀具和优化切削参数对薄壁零件的加工具有重要意义。
选择合适的刀具材料和刀具几何形状对降低切削力、延长刀具使用寿命非常重要。
通过优化切削速度、进给量、切削深度等切削参数,可以有效地减少切削力、降低振动,从而保证薄壁零件的加工质量。
2. 支撑技术:薄壁零件在数控车削加工中,可以采用支撑技术来减少变形和振动。
支撑技术可以通过在零件上设置支撑点、改变切削路线等方式,有效地提高零件的刚度和稳定性,减少变形和振动。
可以在薄壁零件的内部设置支撑件,以增加结构的刚性,减少振动和变形。
3. 刀轴倾角补偿技术:在数控车削加工中,刀轴倾角对薄壁零件的加工具有重要影响。
合理地设置刀轴倾角可以有效地减少切削力和振动,避免因为切削力对零件产生的变形。
通过刀轴倾角补偿技术,可以实现对零件的精密加工,提高加工质量。
4. 加工路径优化技术:在数控车削加工中,通过优化加工路径,可以减少切屑对加工表面的损害,同时也可以减少切削力和振动。
在薄壁零件的加工中,通过合理设置加工路径和切削方向,可以减少切屑的产生,提高加工表面的光洁度和平整度。
薄壁零件的数控车削加工探讨
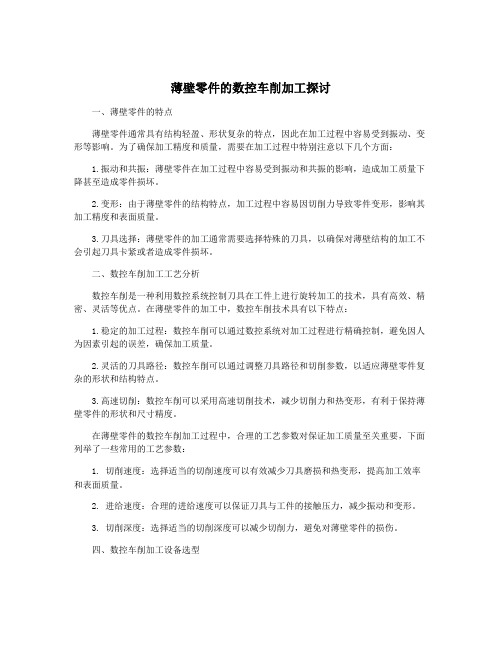
薄壁零件的数控车削加工探讨一、薄壁零件的特点薄壁零件通常具有结构轻盈、形状复杂的特点,因此在加工过程中容易受到振动、变形等影响。
为了确保加工精度和质量,需要在加工过程中特别注意以下几个方面:1.振动和共振:薄壁零件在加工过程中容易受到振动和共振的影响,造成加工质量下降甚至造成零件损坏。
2.变形:由于薄壁零件的结构特点,加工过程中容易因切削力导致零件变形,影响其加工精度和表面质量。
3.刀具选择:薄壁零件的加工通常需要选择特殊的刀具,以确保对薄壁结构的加工不会引起刀具卡紧或者造成零件损坏。
二、数控车削加工工艺分析数控车削是一种利用数控系统控制刀具在工件上进行旋转加工的技术,具有高效、精密、灵活等优点。
在薄壁零件的加工中,数控车削技术具有以下特点:1.稳定的加工过程:数控车削可以通过数控系统对加工过程进行精确控制,避免因人为因素引起的误差,确保加工质量。
2.灵活的刀具路径:数控车削可以通过调整刀具路径和切削参数,以适应薄壁零件复杂的形状和结构特点。
3.高速切削:数控车削可以采用高速切削技术,减少切削力和热变形,有利于保持薄壁零件的形状和尺寸精度。
在薄壁零件的数控车削加工过程中,合理的工艺参数对保证加工质量至关重要,下面列举了一些常用的工艺参数:1. 切削速度:选择适当的切削速度可以有效减少刀具磨损和热变形,提高加工效率和表面质量。
2. 进给速度:合理的进给速度可以保证刀具与工件的接触压力,减少振动和变形。
3. 切削深度:选择适当的切削深度可以减少切削力,避免对薄壁零件的损伤。
四、数控车削加工设备选型1. 设备精度:选择精度高、稳定性好的数控车床,以确保对薄壁零件的加工能够满足工程要求。
2. 加工范围:选择加工范围适中的数控车床,以适应不同尺寸和形状的薄壁零件加工需求。
3. 加工性能:选择具有高速切削、高刚性和稳定性的数控车床,有利于提高加工效率和加工质量。
薄壁零件的数控车削加工是一个复杂而又重要的加工过程。
- 1、下载文档前请自行甄别文档内容的完整性,平台不提供额外的编辑、内容补充、找答案等附加服务。
- 2、"仅部分预览"的文档,不可在线预览部分如存在完整性等问题,可反馈申请退款(可完整预览的文档不适用该条件!)。
- 3、如文档侵犯您的权益,请联系客服反馈,我们会尽快为您处理(人工客服工作时间:9:00-18:30)。
薄壁零件车削加工方法探究
发表时间:2019-07-08T14:56:53.290Z 来源:《防护工程》2019年第7期作者:洪玉亭王保强
[导读] 在对薄壁零件车削进行加工的过程中,要尽可能的减小零件的变形,从而更好的满足薄壁零件的加工需求。
南京理工大学工程训练中心江苏南京 210094
摘要:随着我国经济的发展和社会的进步,我国薄壁零件车削的加工技术也在不断发展,随之而来的生产的发展也对其工艺提出了要求。
针对于这种发展现状,需要我们提高薄壁零件车削加工技术,本文主要针对于此展开一系列的讨论,并且给出合理化的建议,希望对我国加工的发展有一定的帮助作用。
关键词:薄壁零件;车削加工;发展现状
引言:
薄壁零件针对于普通的零件,具有较多的优点,性能也比较优越,并且具有较好的结构精度。
但是往往这种零件由于其结构相对较为精密,在制造的过程中往往会存在一系列的问题,从而导致其质量受到影响。
在对薄壁零件车削进行加工的过程中,要尽可能的减小零件的变形,从而更好的满足薄壁零件的加工需求。
1薄壁零件车削加工受到的影响
1.1加工变形的影响
第一,受力变形。
薄壁零件在切削加工过程中内应力和夹紧力受力不均导致变形产生,影响了尺寸和产生形变。
一般车削使用的三爪卡盘夹具在装夹薄壁零件时会因弹性变形产生形变。
第二,热变形。
薄壁零件在车削加工中会因切削热量聚集产生变形,不利于精度控制。
第三,振动产生变形。
薄壁零件因受力较小,在切削力的作用下,容易产生振动和变形,最终影响尺寸和精度。
1.2切削液的影响
车削加工中,由于刀具与工件、切屑与刀具产生摩擦会产生热量,刀具强度降低,表面质量变差,零件中热量增加,薄壁件受力增加,如果此时切削液选用不合理或冷却不到位会造成零件受力不均匀产生尺寸和精度误差,影响零件质量。
1.3切削用量选择不当的影响
薄壁零件因其结构的特殊性,切削用量的选择要具有特殊性,尤其是精加工阶段,参数选择不合理极容易在加工中出现轧刀现象,产生较大的切削力导致变形,导致零件报废。
1.4切削不合理导致变形
在对薄壁零件进行车削加工的过程中,往往具有较强的震动效果,并且在切削工艺不能达到相关标准的情况下,往往会造成一系列的问题,从而影响车削加工技术。
基于此,为了减小切削过程中刀所受到的一些阻力,可以对其前角的角度进行调整。
可以根据具体的实际情况做出一定的调整,如果刀具是高速钢的情况下,需要将前角控制在6-30度的范围内,一边保证其能具有较小的阻力。
并且在对车削用量的选择上,需要进行合理的选择,从而减小薄壁零件的变形,在对金属切削进行影响因素的分析过程中可以得出,其主要受到两种因素的影响,即背吃刀量和进给量。
可以针对于具体的实际情况进行两种量的合理控制,从而减小零件的变形。
1.5刀具不合适导致变形
对薄壁零件进行车削加工,还要做好刀具的选择,以免零件在车削过程中发生热变形。
因为,刀具的选择直接关系到刀具前角大小,从而将对零件切削变形程度产生影响。
刀具是否锋利,也会影响零件加工效果。
此外,在切削的过程中,还要利用切削液冷却和润滑刀具。
未能较好的使用切削液,不仅将导致刀具受到磨损,还将导致零件出现变形。
2薄壁零件车削加工措施
2.1合理选择装夹方案,控制受力变形
车削薄壁零件可选择开缝套筒,开缝套筒可改变三爪卡盘三点夹紧、工件不能均匀受力的问题,它可以增大接触面积,切削力也会被均匀分布在工件上,该装夹方式可用于薄壁零件内孔车削。
还可采用特制弧形软爪进行装夹,弧形软爪装夹也可增加夹持面积,分散切削力,进而达到减少夹紧力和车削变形,可用于薄壁零件的外圆部分加工。
2.2合理选择切削液
根据机械加工基础的相关知识可知切削液在车削加工过程中的作用明显。
合理选择切削液能让零件切削温度降低150℃左右,提升零件表面质量,减少切削力且能提高刀具寿命。
根据多年经验,选择卤化液或切削油作为加工薄壁零件的冷却液能达到较好的效果,因此合理选择薄壁零件加工中的切削液,能降低切削过程中的热量和切削力,减少薄壁零件产生的热变形和受力不均匀产生的变形,也能提高加工效率。
2.3合理选择切削用量
合理选择切削用量在薄壁零件加工中的重要性不言而喻。
切削用量包含背吃刀量、进给量、切削速度三个要素。
合理利用切削三要素,可减少切削力,减少变形。
薄壁零件车削过程中,背吃刀量增加切削力增加,会让薄壁受力增加产生变形,根据多年经验,车削45钢薄壁零件精加工阶段背吃刀量在0.4mm为最佳。
在背吃刀量一定的情况下,进给力增大,会增大表面粗糙度,导致薄壁零件内应力增加,产生变形,一般精加工进给量为0.1mm/r。
切削速度对切削力的影响较小,在刀具、工件材料允许的情况下,甚至可以选择较高的切削速度,但速度提高后,要防止薄壁零件车削中出现振动现象,不利于表面质量,因此,在刀具允许的切削速度内,速度一般选择100m/min。
虽然切削用量的合理选择对薄壁零件切削比较重要,但薄壁零件变形跟很多因素有关。
切削过程中还要根据刀具材料、零件材料、机床性能合理选择切削用量。
2.4合理选择车削刀具
在车削薄壁零件时,刀具材料最好选择硬质合金或陶瓷刀片,日常使用的高速钢和白钢刀会因材料硬度达不到要求产生较大的切削力。
此外刀具几何角度对切削力的影响较大,刀具前角决定刀具的锋利程度,增大刀具前角能缩小摩擦,降低切削力,但热量不易散失,
刀具寿命不高。
后角决定摩擦力和切削力的大小,后角越大,摩擦力和切削力越小,但刀具强度会降低。
刀具主偏角决定轴向力和径向力的分布,主偏角越大,径向力越小,反之轴向力越小。
因此,精车薄壁零件时,应选择较大的前角和后角,主偏角角度控制在90°左右,镗削薄壁内孔时,可选取较大的主偏角。
2.5优化切削参数
在对薄壁零件进行车削加工技术的过程中,想要尽可能减小零件的变形,还要进行车削参数的控制,不断优化车削加工技术。
并且在粗加工的过程中,如果刀具以及机床不能够符合相关的标准,可能会影响整体的加工技术。
在精加工的过程中,也要针对于实际的情况,对每齿的进给量进行控制,采用较小的切深和小直径的刀具来进行切削加工,确保零件可以保持较为稳定的状态,从而降低加工过程中零件所收到的摩擦力和切削热。
还可以降低零件变形的情况,提高机床的综合性能,合理的对主轴的转速进行控制,并且根据实际的生产情况对机床的参数进行控制。
针对于普通的铣削,高速铣削速度更快,径向切深较大,切削速度更大。
因此,要想不断提高生产的性能,在进行切削的过程中,需要根据切削的速度进行一定的改善,从而不断减小刀具磨损的情况,采用较大的主偏角以及前角。
3小结
综上所述,车削薄壁类零件,首先要充分分析零件,制定合理的加工工艺,其次要选取合理的装夹方式、切削用量和切削液及刀具等,以保证薄壁零件加工质量。
参考文献:
[1]丁金晔.薄壁零件车削加工方法探究[J].南方农机,2019,50(05):49.
[2]陈方国.薄壁筒类零件车削加工方法[J].山东工业技术,2019(06):35+13.
[3]李卫清.薄壁零件加工装夹方法及车削加工技巧[J].山东工业技术,2018(08):56-57.
[4]任健强.薄壁零件加工装夹方法及车削加工技巧[J].中国设备工程,2017(13):124-125.。