薄壁零件车削加工方法探讨
浅谈薄壁零件数控车工加工工艺
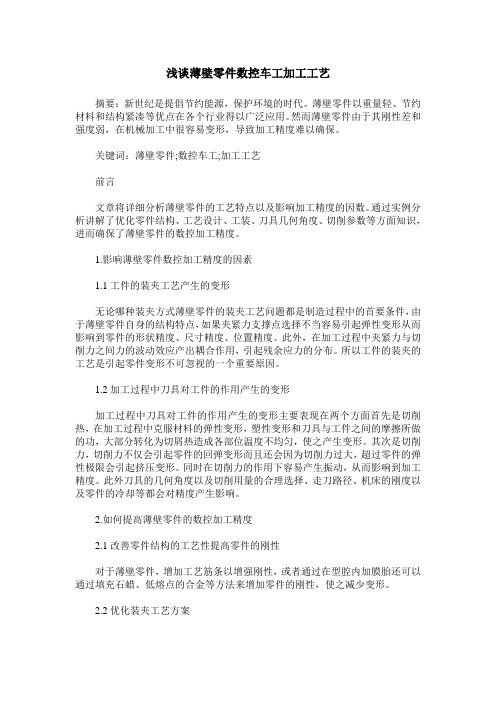
浅谈薄壁零件数控车工加工工艺摘要:新世纪是提倡节约能源,保护环境的时代。
薄壁零件以重量轻、节约材料和结构紧凑等优点在各个行业得以广泛应用。
然而薄壁零件由于其刚性差和强度弱,在机械加工中很容易变形,导致加工精度难以确保。
关键词:薄壁零件;数控车工;加工工艺前言文章将详细分析薄壁零件的工艺特点以及影响加工精度的因数。
通过实例分析讲解了优化零件结构、工艺设计、工装、刀具几何角度、切削参数等方面知识,进而确保了薄壁零件的数控加工精度。
1.影响薄壁零件数控加工精度的因素1.1工件的装夹工艺产生的变形无论哪种装夹方式薄壁零件的装夹工艺问题都是制造过程中的首要条件,由于薄壁零件自身的结构特点,如果夹紧力支撑点选择不当容易引起弹性变形从而影响到零件的形状精度、尺寸精度、位置精度。
此外,在加工过程中夹紧力与切削力之间力的波动效应产出耦合作用,引起残余应力的分布。
所以工件的装夹的工艺是引起零件变形不可忽视的一个重要原因。
1.2加工过程中刀具对工件的作用产生的变形加工过程中刀具对工件的作用产生的变形主要表现在两个方面首先是切削热,在加工过程中克服材料的弹性变形,塑性变形和刀具与工件之间的摩擦所做的功,大部分转化为切屑热造成各部位温度不均匀,使之产生变形。
其次是切削力,切削力不仅会引起零件的回弹变形而且还会因为切削力过大,超过零件的弹性极限会引起挤压变形。
同时在切削力的作用下容易产生振动,从而影响到加工精度。
此外刀具的几何角度以及切削用量的合理选择、走刀路径、机床的刚度以及零件的冷却等都会对精度产生影响。
2.如何提高薄壁零件的数控加工精度2.1改善零件结构的工艺性提高零件的刚性对于薄壁零件,增加工艺筋条以增强刚性,或者通过在型腔内加膜胎还可以通过填充石蜡、低熔点的合金等方法来增加零件的刚性,使之减少变形。
2.2优化装夹工艺方案不同的零件结构和加工方法对应不同的装夹工艺。
在已有的装夹工艺的基础上对其进行改进,优化设计是装夹工艺优化的基本方法。
薄壁筒类零件车削加工方法
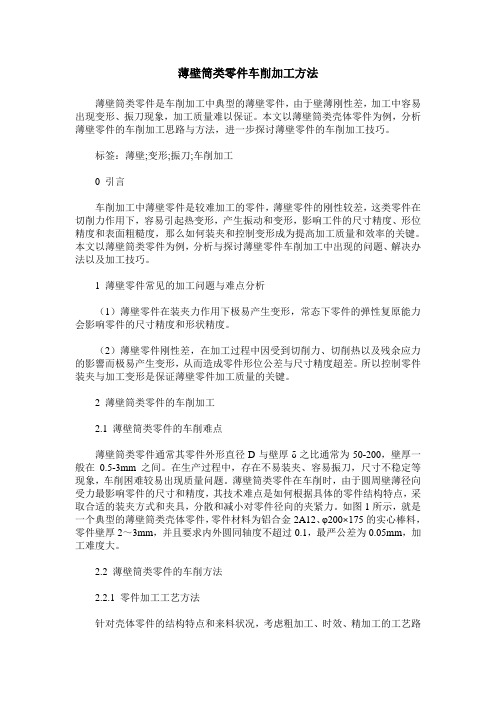
薄壁筒类零件车削加工方法薄壁筒类零件是车削加工中典型的薄壁零件,由于壁薄刚性差,加工中容易出现变形、振刀现象,加工质量难以保证。
本文以薄壁筒类壳体零件为例,分析薄壁零件的车削加工思路与方法,进一步探讨薄壁零件的车削加工技巧。
标签:薄壁;变形;振刀;车削加工0 引言车削加工中薄壁零件是较难加工的零件,薄壁零件的刚性较差,这类零件在切削力作用下,容易引起热变形,产生振动和变形,影响工件的尺寸精度、形位精度和表面粗糙度,那么如何装夹和控制变形成为提高加工质量和效率的关键。
本文以薄壁筒类零件为例,分析与探讨薄壁零件车削加工中出现的问题、解决办法以及加工技巧。
1 薄壁零件常见的加工问题与难点分析(1)薄壁零件在装夹力作用下极易产生变形,常态下零件的弹性复原能力会影响零件的尺寸精度和形状精度。
(2)薄壁零件刚性差,在加工过程中因受到切削力、切削热以及残余应力的影響而极易产生变形,从而造成零件形位公差与尺寸精度超差。
所以控制零件装夹与加工变形是保证薄壁零件加工质量的关键。
2 薄壁筒类零件的车削加工2.1 薄壁筒类零件的车削难点薄壁筒类零件通常其零件外形直径D与壁厚δ之比通常为50-200,壁厚一般在0.5-3mm之间。
在生产过程中,存在不易装夹、容易振刀,尺寸不稳定等现象,车削困难较易出现质量问题。
薄壁筒类零件在车削时,由于圆周壁薄径向受力最影响零件的尺寸和精度,其技术难点是如何根据具体的零件结构特点,采取合适的装夹方式和夹具,分散和减小对零件径向的夹紧力。
如图1所示,就是一个典型的薄壁筒类壳体零件,零件材料为铝合金2A12、φ200×175的实心棒料,零件壁厚2~3mm,并且要求内外圆同轴度不超过0.1,最严公差为0.05mm,加工难度大。
2.2 薄壁筒类零件的车削方法2.2.1 零件加工工艺方法针对壳体零件的结构特点和来料状况,考虑粗加工、时效、精加工的工艺路线,先粗车,时效后再精车外圆及右侧内孔尺寸。
薄壁零件加工装夹方法及车削加工技巧

薄壁零件加工装夹方法及车削加工技巧在薄壁零件加工过程中,由于零件容易发生变形,所以需要在精加工后进行光切加工,从而导致零件加工效率遭到了降低。
基于这种认识,本文结合薄壁零件加工问题,对薄壁零件加工装夹方法及车削加工技巧展开了分析,从而为关注这一话题的人们提供参考。
标签:薄壁零件;装夹方法;车削加工0 引言相较于普通零件,薄壁零件具有重量轻、结构简单等特点,拥有较高的结构精度。
但是这类零件的加工一直较为困难,在车削加工过程中容易发生变形,从而影响零件质量。
因此,还应加强对薄壁零件加工装夹方法及车削加工技巧的分析,减小零件变形量,进而更好的满足薄壁零件加工需要。
1 薄壁零件加工问题相较于普通零件,薄壁零件在加工的过程中较容易出现变形问题,如装夹不当、切削不合理、刀具不合适都将引发零件变形,从而影响零件加工质量。
1.1 装夹不当导致变形通常条件下,薄壁零件内外直径差距较小,强度较弱,在车床作业中直接利用三爪自定心卡盘进行固定,将导致各爪点局部不稳,引发零件整体变形。
在过去的薄壁零件加工中,需要使零件上各夹紧点达到稳定均衡,所以需要增大装夹接触面,从而使零件整体变形量得到减少。
但是采用该种加工方法,仍然无法杜绝零件变形问题的发生。
1.2 切削不合理导致变形在车削加工的过程中,会产生较强震动。
在切削工艺不合理的情况下,就会导致薄壁零件变形。
为减少切削时刀具所受的阻力,以免零件因阻力过大产生塑性变形或弹性变形,通常需要结合刀具类型进行前角调整。
比如在刀具为高速钢材质时,需要将前角设定为6°-30°。
在刀具为硬质合金刀时,前角在5°-20°范围内。
而未能进行车削用量的合理选择,将导致薄壁零件产生各种变形。
分析这一现象产生的原因可以发现,金属切削主要受两个因素的影响,即背吃刀量和进给量。
在同时增大这两个量的情况下,零件会因切削力增大而变形。
在背吃刀量减少、进给量增大的条件下,尽管切削力会减小,但是由于工作表面剩余面积较大,零件所受内应力也增大,最终导致零件变形。
薄壁类零件的车削工艺分析
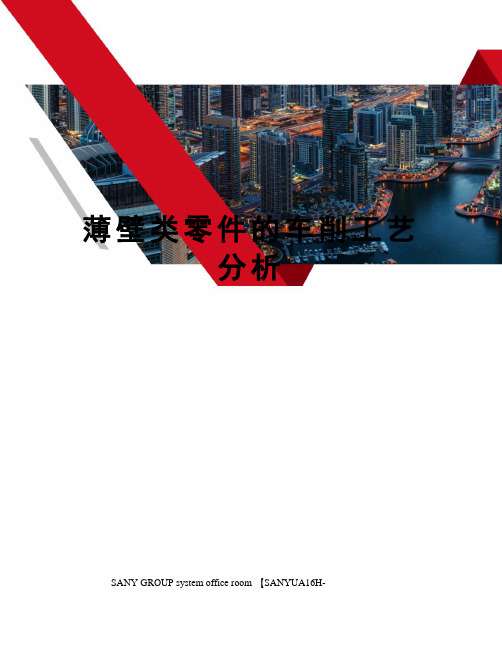
薄壁类零件的车削工艺分析SANY GROUP system office room 【SANYUA16H-薄壁类零件的车削工艺分析段立波一.引言薄壁类零件指的是零件壁厚与它的径向、轴向尺寸相比较,相差悬殊,一般为几十倍甚至上百倍的金属材料的零件,具有节省材料、结构简单等特点。
薄壁类零件已广泛地应用于各类石油机械部件。
但是薄壁类零件的车削加工是比较棘手的,具体的原因是因为薄壁类零件自身刚性差、强度弱,在车削加工中极容易变形,很难保证零件的加工质量。
如何提高薄壁类零件的加工精度是机械加工行业关心的话题。
二.薄壁类零件车削过程中常出现的问题、原因及解决办法我们在车削加工过程中,经常会碰到一些薄壁零件的加工。
如轴套薄壁件(图1),环类薄壁件(图2),盘类薄壁件(图3)。
本文详细分析了薄壁类零件的加工特点、防止变形的装夹方法、车刀材料、切削参数的选择及车刀几何角度。
进行了大量的实验,为以后更好地加工薄壁类零件,保证加工质量,提供了理论依据。
图1轴套薄壁件图2环类薄壁件图3盘类薄壁件1.薄壁类零件的加工特点1.1因零件壁薄,在使用通用夹具装夹时,在夹压力的作用下极易产生变形,而夹紧力不够零件又容易松动,从而影响零件的尺寸精度和形状精度。
如图4所示,当采用三爪卡盘夹紧零件时,在夹紧力的作用下,零件会微微变成三角形,车削后得到的是一个圆柱体。
但松开卡爪,取下零件后,由于零件弹性,又恢复成弧形三角形。
这时若用千分尺测量时,各个方向直径相同,但零件已变形不是圆柱体了,这种变形现象我们称之为等直径变形。
图4三爪卡盘装夹1.2因零件较薄,加工时的切削发热会引起零件变形,从而使零件尺寸难以控制。
对于膨胀系数较大的金属薄壁零件,如在一次安装中连续完成半精车和精车,由切削热引起零件的热变形,会对其尺寸精度产生极大影响,有时甚至会使零件卡死在芯轴类的夹具上。
1.3薄壁类零件加工内孔中,一般采用单刃镗刀加工,此时,当零件较长时,如果刀具参数及切削用量处理不当,将造成排屑困难,影响加工质量,损伤刀具。
某薄壁零件车削加工工艺研究
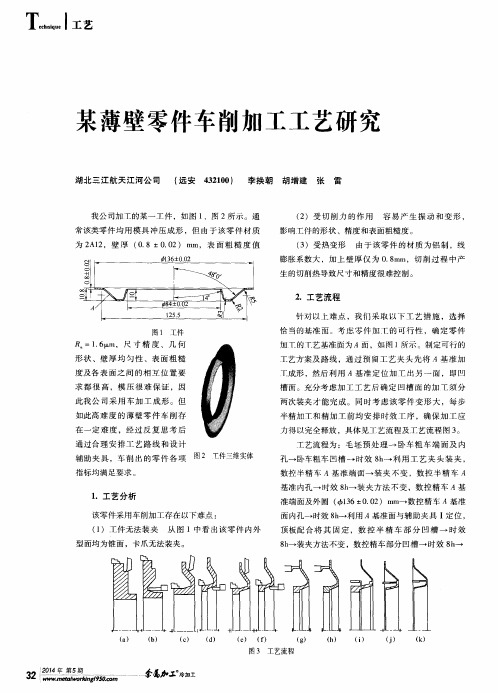
指标 均满 足要求 。
1 .工艺分析
该零 件采用 车 削加工 存在 以下难 点 :
( 1 )工 件无法 装 夹 从 图 1中看 出该 零 件 内外
准端 面及外 圆 ( 4 , 1 3 6. 4 - 0 . 0 2 )m m 一 数控 精 车 4基准
面 内孔一 时效 8 h 一利 用 A基 准面 与辅 助夹 具 I定 位 , 顶 板配 合 将 其 固 定 ,数 控 半 精 车 部 分 凹槽 一 时 效
l T件三维实体 辅助 夹 具 ,车 削 出 的 零 件 各 项 图2
半精加 T 和精 加 工 前 均 安 排 时 效 _ T序 ,确 保 加 工 应
力得 以完全 释放 ,具体 见 艺流程 及 _ 丁 艺流 程 图 3 。 工艺 流程 为 :毛 坯 预 处 理一 卧 车 粗 车 端 面 及 内 孔一 卧车粗 车 凹槽 一 时 效 8 h 一 利用工艺夹头装 夹, 数控 半精 车 A基 准 端 面 一 装 夹 不 变 ,数 控 半 精 车 A 基准 内孔 一 时 效 8 h 一 装 夹 方法 不 变 ,数控 精 车 A基
槽部分。
助夹具 I 拧 紧 ,通 过 辅 助 夹 具 Ⅱ上 的 端 面 和 锥 面 将
工件最 大 限度地 压 紧 固定 ( 见图 7 ) 。最 后 利用 普 通
3 .夹具设计
进 行 凹槽 半 精 加 工 和 精 加 工 工 序 时 ,工 件 的 刚 性 已经很 弱 ,无 法进 行装 夹 ,我们 通过 辅助 夹具 I和
Ⅱ解 决该难 题 。
自定 心卡 盘装 夹 即可 进 行 工 艺 夹 头 的去 除 及 剩 余 凹 槽 的半 精 和精加 T 。
( 1 )辅 助夹具 I 结构 如 图 4所 示 ,夹具 I 的内 型面 作为工 件 的定位 面 ,为此 内型 面形状 与 工件 的 A
薄壁套类零件车削加工方法

薄壁套类零件车削加工方法摘要:工业中广泛使用薄壁件,但是由于其加工工艺性差,在切削力、残余应力、切削热、夹紧力等因素影响下,薄壁件易发生加工变形,不易控制加工精度和提高加工效率。
本文对薄壁件加工过程中引起变形的因素进行了分析,通过改变工件的压紧方式和定位基准,设计制作工装并加工验证,得出加工薄壁件的合理工艺安排,顺利解决了工件变形问题,保证了加工质量,提高了加工效率。
关键词:薄壁套类零件车工夹具设计装夹方法一、前言航空工业中广泛使用薄壁结构零件。
薄壁零件由于其刚性好、强度高、相对重量较轻等优点,使得薄壁零件在社会中的运用越来越广泛。
薄壁零件主要是指零件的壁厚小于2mm的零件。
它们在机械加工工业中占有较大比例,薄壁套类零件因其具有重量轻、节约材料和结构紧凑等特点,广泛应用于航空领域。
此类零件结构复杂,刚度较低,加工余量大,并有很多的形位公差要求,加工中极易发生变形和切削振动,让刀现象严重,装夹和定位较困难,一直以来都是加工难点。
二、结构分析此项套类零件是用来支承旋转轴及轴承,该类零件的主要表面是内孔和外圆,其主要技术要求是内孔及外圆的尺寸以及圆度要求;内外圆之间的同轴度要求;孔轴线与端面的垂直度要求。
薄壁套类零件壁厚很薄,径向刚度很弱,在加工过程中受切削力、切削热及夹紧力等因素的影响,极易变形,导致以上各项技术要求难以保证。
针对这些问题,本文对薄壁套类零件加工过程中装夹方法做了初步的探讨。
我厂生产某项车削加工薄壁套类后盖零件,首次投入400件,生产类型为大批量。
此项零件壁厚仅为0.7mm,最薄的地方为0.5mm。
三、初次加工存在的问题我们对首批加工情况进行调查、分析和研究,投入400件,超差品181件,报废19件,合格率仅为50%。
按照原来的加工方法,先镗右端内腔及环槽,再调头车削左端圆台,夹持零件右端外圆时零件已经变形,然后用和圆台同样大小的圆环将零件小端面压紧在芯轴上,接触面小,在加工过程中旋转,零件跳动量大,装夹不牢靠。
浅析薄壁零件的车削

浅析薄壁零件的车削摘要:薄壁零件由于刚性差,加工时容易引起变形,影响零件的加工精度。
本文通过分析薄壁零件在加工过程中可能出现的情况,探讨减小薄壁零件变形的方法。
关键词:薄壁变形目前,薄壁零件以其重量轻、结构紧凑等特点大量应用于各个行业,尤其在模具、航空航天和汽车工业等领域应用更为广泛。
但是由于薄壁零件的刚性较差,在车削过程中极易产生变形,不易保证零件的加工质量。
本文通过对薄壁零件在车削过程中可能出现的现象进行分析,探讨减小薄壁零件变形的方法。
一、薄壁零件加工时的现象分析影响薄壁零件加工精度的因素有很多,归纳起来主要有以下几个方面:1.受力变形薄壁零件在车削过程中由于工件内部可能存在的内应力及由于夹紧力不均匀而产生的夹紧外应力的共同作用下易使薄壁零件产生变形(见图1),从而影响零件的尺寸精度和形状精度。
例如,用三爪卡盘夹紧薄壁外圆,车削完成卸下后,被卡爪夹紧部分会因弹性变形而导致零件呈多角形。
为了减小变形,使用前车削扇形软卡爪内孔及内端面并符合零件定位外圆尺寸的0.05mm,且保持内孔与端面垂直,同时采用外加开口套筒或改用特殊软爪等措施来增大接触面积,使夹紧力均匀分布。
2.受热变形因工件较薄,车削过程中产生的切削热易引起工件热变形,使工件尺寸难以控制,对于薄壁零件,十分有害。
3.振动变形在切削力(特别是径向切削力)的作用下,车削时很容易产生振动和变形,从而影响工件的尺寸精度、形状、位置精度和表面粗糙度。
在切削过程中,径向切削力会使工件在径向产生弹性变形和振动。
图2所示为车削薄壁套筒零件的示意图,工件装在心轴上。
由于工件中间部分刚性较差,车削过程中弹性变形大,工件呈现中间厚两端逐渐变薄的曲面形状。
二、减小薄壁零件变形的方法根据薄壁零件的特点和要求选择合理的工艺方案,这是保证薄壁零件加工质量的关键,同时要从防止变形和保证精度出发去设计加工工艺。
1.通过热处理消除内应力薄壁零件的毛坯一般是锻造、铸造和钢板滚压焊接件,有较大的内应力,这种内应力的存在,将直接导致工件的变形。
(整理)薄壁零件车削加工方法探讨

薄壁零件车削加工方法探讨1. 薄壁零件的加工特点1.1 薄壁零件不能承受较大的径向力,用通用夹具安装困难。
1.2 薄壁零件的刚性差,在夹紧力的作用下,极易产生变形,常态下工件的弹性复原,会影响工件的尺寸精度和形状精度。
1.3 工件受切削热的影响,尺寸精度不易控制。
1.4 由于切削力的影响,工件易产生变形或振动,尺寸精度和表面粗糙度不易控制。
1.5 薄壁零件刚性差,不能采用较大的切削用量,生产效率低。
因此合理的选择装夹方法,加工方法,切削用量,减少振动及充分冷却和检测都是保证加工薄壁零件的关键。
2. 薄壁零件的装夹方法2.1 通用软爪定位装夹,选择正确的夹紧力作用点,使夹紧力作用在工件刚性较好的部位,适用于形状和尺寸公差要求不严的零件加工优点:装卸方便长度可定位,看承受较大切削力。
缺点:零件定位点较集中,零件加紧后变形较严重。
2.2 大面积扇形软爪装夹:采用扇形软爪的三爪卡盘,按与加工零件的装夹面动配合的要求,加工出卡爪的工作面,增大与零件的接触面积。
优点:增大夹紧力的作用面积,使工件支持面增大,夹紧力均匀分布在工作面上,可加大切削用量,不易产生变形。
缺点:扇形软爪不易加工。
2.3 芯棒装夹2.3.1 采用椎体芯轴装夹,将零件直接套在椎体芯轴加工。
2.3.2 采用圆柱芯轴装夹,将零件装在芯轴上采用轴线压紧。
减小零件径向变形。
优点:装卸零件方便,能保证较高的同心度,技术要求。
缺点:零件内孔被芯轴划伤。
2.4 磁力吸盘装夹:采用磁力吸盘将零件吸附在吸盘上,这时零件只受轴向力,而径向不受力。
优点:可一次较高零件内外圆。
缺点:零件找正比较麻烦,应用范围小。
3. 薄壁零件较高方法的选择3.1 先粗后精先粗加工出零件的外圆和内孔,外圆和内孔均匀留0.5 —0.8 毫米余量,端面单边留0.25 —0.3 毫米余量,然后选择适当的装夹方法,将零件精加工到图纸尺寸要求。
3.2 先内后外先加工内孔,以为孔较外圆难加工,易产生变形。
薄壁零件的车削技巧

薄壁零件的车削技巧薄壁零件是指壁厚相对较薄的零件,在车削加工中,由于其壁厚薄,容易产生变形和振动,所以需要特殊的车削技巧来保证加工质量。
本文将介绍薄壁零件的车削技巧。
首先,保持机床的稳定性。
薄壁零件在车削时容易产生振动,而振动会影响加工精度和表面质量。
为了保持机床的稳定性,首先要确保机床具备足够的刚性和抗震性,同时要确保机床的紧固件处于良好的状态,以免因紧固件松动而导致振动。
此外,还可以通过合理的刀具和夹具选择来减少振动,例如选择合适的刀具长度和刚度,使用刀柄的支撑力等。
其次,选择合适的切削参数。
在车削薄壁零件时,要选择合适的切削参数,以保证刀具的切削力不会过大。
一般来说,应尽可能采用小的进给量和切削深度,降低切削力。
另外,应注意保持刀具的尖角和刃磨状况良好,以减小刀具的切削力。
第三,选择合适的刀具和夹具。
在车削薄壁零件时,要选择合适的刀具和夹具,以提高加工的稳定性和精度。
刀具要选择具有较高刚度和切削性能的硬质合金刀具,以减小切削力和振动。
夹具要选择刚性好的夹具,以确保零件的稳定夹持,同时要避免夹持过紧而导致变形。
第四,采用适当的刀具路径。
在车削薄壁零件时,为了避免产生振动和变形,应采用适当的刀具路径。
一般来说,应优先选择切削路径中的外切削和镗削,避免内切削和过切削,这样可以减小刀具对零件的负荷,减少振动和变形。
第五,采用适当的刀具进给方式。
在车削薄壁零件时,应采用适当的刀具进给方式,以减小切削力和振动。
一般来说,可以采用铣削进给,即刀具的进给方向与工件的旋转方向相同,这样可以减小刀具对零件的冲击力和振动。
最后,进行切削加工时要进行监控和调整。
在车削薄壁零件时,要进行监控和调整,以确保加工质量。
可以通过加工中的监测手段,例如振动传感器、力传感器等,对加工过程中的切削力、振动等进行监测,及时调整切削参数和刀具路径,以减小振动和变形,保证加工质量。
总之,薄壁零件的车削技巧包括保持机床稳定性、选择合适的切削参数、刀具和夹具、采用适当的刀具路径和进给方式,以及进行监控和调整等。
薄壁零件的车削
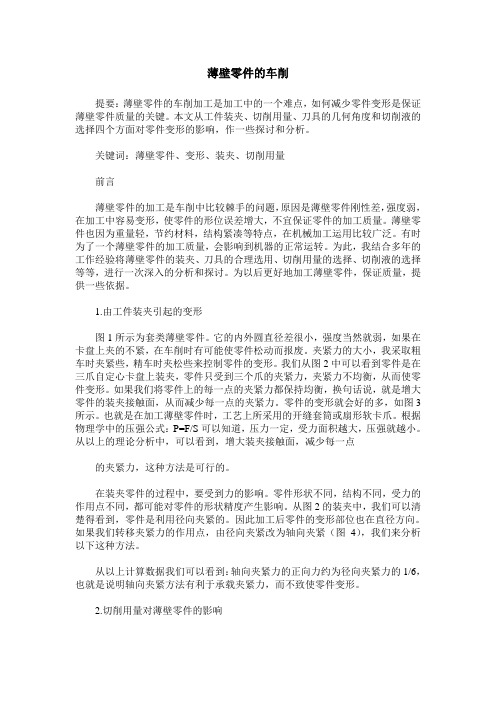
薄壁零件的车削提要:薄壁零件的车削加工是加工中的一个难点,如何减少零件变形是保证薄壁零件质量的关键。
本文从工件装夹、切削用量、刀具的几何角度和切削液的选择四个方面对零件变形的影响,作一些探讨和分析。
关键词:薄壁零件、变形、装夹、切削用量前言薄壁零件的加工是车削中比较棘手的问题,原因是薄壁零件刚性差,强度弱,在加工中容易变形,使零件的形位误差增大,不宜保证零件的加工质量。
薄壁零件也因为重量轻,节约材料,结构紧凑等特点,在机械加工运用比较广泛。
有时为了一个薄壁零件的加工质量,会影响到机器的正常运转。
为此,我结合多年的工作经验将薄壁零件的装夹、刀具的合理选用、切削用量的选择、切削液的选择等等,进行一次深入的分析和探讨。
为以后更好地加工薄壁零件,保证质量,提供一些依据。
1.由工件装夹引起的变形图1所示为套类薄壁零件。
它的内外圆直径差很小,强度当然就弱,如果在卡盘上夹的不紧,在车削时有可能使零件松动而报废。
夹紧力的大小,我采取粗车时夹紧些,精车时夹松些来控制零件的变形。
我们从图2中可以看到零件是在三爪自定心卡盘上装夹,零件只受到三个爪的夹紧力,夹紧力不均衡,从而使零件变形。
如果我们将零件上的每一点的夹紧力都保持均衡,换句话说,就是增大零件的装夹接触面,从而减少每一点的夹紧力。
零件的变形就会好的多,如图3所示。
也就是在加工薄壁零件时,工艺上所采用的开缝套筒或扇形软卡爪。
根据物理学中的压强公式:P=F/S可以知道,压力一定,受力面积越大,压强就越小。
从以上的理论分析中,可以看到,增大装夹接触面,减少每一点的夹紧力,这种方法是可行的。
在装夹零件的过程中,要受到力的影响。
零件形状不同,结构不同,受力的作用点不同,都可能对零件的形状精度产生影响。
从图2的装夹中,我们可以清楚得看到,零件是利用径向夹紧的。
因此加工后零件的变形部位也在直径方向。
如果我们转移夹紧力的作用点,由径向夹紧改为轴向夹紧(图4),我们来分析以下这种方法。
薄壁零件的车削方法

薄壁零件的车削方法1.用一次装夹车薄壁零件:车削短小薄壁工件时,为了保证内外圆轴线的同轴度,可用一次装夹车削。
例:薄壁衬套,材料为锡青铜,工件壁厚仅2mm,同轴度公差为0.025mm,精度要求较高。
车削方法见下图:夹持棒料,车出长度45mm,粗车内外圆均留0.5mm余量,钻,粗车内孔时,要求长度比图样长2mm即可。
以增加工件的刚性,加注切削液,使工件充分冷却后,精车内外圆至尺寸。
(油槽在半精车后拉出)切断工件,最后装夹在心轴上,车削另一端面和倒角。
2.用扇形卡爪及心轴装夹薄壁工件:例:薄壁套筒如图,车削方法:粗车留精车余量1~1.5mm,精车时,装夹在扇形软卡中,精车内孔及φ72H7,外圆φ980-0.1及端面A符合图样要求,然后以内孔和大端面为基准,夹在弹性胀力心轴上,即可精车外圆。
3.在花盘上车削薄壁工件:直径较大,尺寸精度和形位精度都较高的圆盘薄壁工件。
可装夹在花盘上加工。
车削方法:先装夹在三爪卡盘上粗车内孔及外圆,各留1~1.5mm余量,长度尺寸车至92+0.3+0.2,并精磨两端面至长度92。
然后装夹在花盘上精车内孔及外圆,精车内孔的装夹方法见图。
先在花盘端面上车出一凸台,凸台的直径和工件之间留0.5~1mm的间隙,(不用作定心)。
用螺栓,压板压紧工件端面,压紧力要均匀。
找正后,即可车削φ132H7, φ262H7内孔及内端平面。
精车外圆时的方法见下图:将三点接触压板(压板上有三条槽以让开压板)适当压紧,松开并取下压板及螺钉,即可车削外圆,使之符合图样要求.上面的压紧方法,因为压紧力在轴向,所以不容易引起变形。
4.在专用夹具上车削薄壁零件:如图,工件装上夹具后,当拧紧螺钉2时,压紧圈1便沿着斜面将工件压紧,即可车削工件的内孔,外圆及端面。
5.增加辅助支承车削薄壁零件:车削内孔精度要求高的薄壁零件时,可采用辅助支承来增加工件的刚性.6.增加工艺肋车削薄壁工件.在工件的装夹部位特制几根工艺支撑肋,使夹紧力作用在肋上,可减少变形.二.减少工件变形的方法:1.工件分粗精车,消除粗车时切削力过大而产生的变形,粗车后,使工件得到自然冷却,消除在精车时可能产生的热变形。
薄壁零件车削加工方法探究
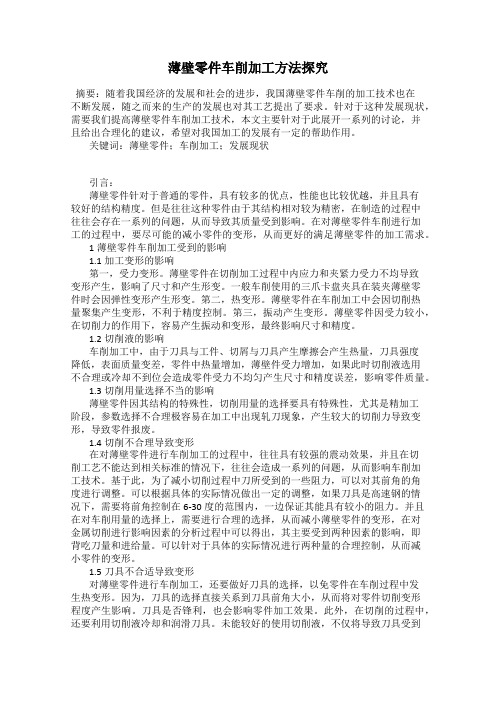
薄壁零件车削加工方法探究摘要:随着我国经济的发展和社会的进步,我国薄壁零件车削的加工技术也在不断发展,随之而来的生产的发展也对其工艺提出了要求。
针对于这种发展现状,需要我们提高薄壁零件车削加工技术,本文主要针对于此展开一系列的讨论,并且给出合理化的建议,希望对我国加工的发展有一定的帮助作用。
关键词:薄壁零件;车削加工;发展现状引言:薄壁零件针对于普通的零件,具有较多的优点,性能也比较优越,并且具有较好的结构精度。
但是往往这种零件由于其结构相对较为精密,在制造的过程中往往会存在一系列的问题,从而导致其质量受到影响。
在对薄壁零件车削进行加工的过程中,要尽可能的减小零件的变形,从而更好的满足薄壁零件的加工需求。
1薄壁零件车削加工受到的影响1.1加工变形的影响第一,受力变形。
薄壁零件在切削加工过程中内应力和夹紧力受力不均导致变形产生,影响了尺寸和产生形变。
一般车削使用的三爪卡盘夹具在装夹薄壁零件时会因弹性变形产生形变。
第二,热变形。
薄壁零件在车削加工中会因切削热量聚集产生变形,不利于精度控制。
第三,振动产生变形。
薄壁零件因受力较小,在切削力的作用下,容易产生振动和变形,最终影响尺寸和精度。
1.2切削液的影响车削加工中,由于刀具与工件、切屑与刀具产生摩擦会产生热量,刀具强度降低,表面质量变差,零件中热量增加,薄壁件受力增加,如果此时切削液选用不合理或冷却不到位会造成零件受力不均匀产生尺寸和精度误差,影响零件质量。
1.3切削用量选择不当的影响薄壁零件因其结构的特殊性,切削用量的选择要具有特殊性,尤其是精加工阶段,参数选择不合理极容易在加工中出现轧刀现象,产生较大的切削力导致变形,导致零件报废。
1.4切削不合理导致变形在对薄壁零件进行车削加工的过程中,往往具有较强的震动效果,并且在切削工艺不能达到相关标准的情况下,往往会造成一系列的问题,从而影响车削加工技术。
基于此,为了减小切削过程中刀所受到的一些阻力,可以对其前角的角度进行调整。
薄壁类零件的车削工艺分析

薄壁类零件的车削工艺分析段立波亠•引言薄壁类零件指的是零件壁厚与它的径向、轴向尺寸相比较,相差悬殊,一般为几十倍甚至上百倍的金属材料的零件,具有节省材料、结构简单等特点。
薄壁类零件已广泛地应用于各类石油机械部件。
但是薄壁类零件的车削加工是比较棘手的,具体的原因是因为薄壁类零件自身刚性差、强度弱,在车削加工中极容易变形,很难保证零件的加工质量。
如何提高薄壁类零件的加工精度是机械加工行业关心的话题。
•薄壁类零件车削过程中常出现的问题、原因及解决办法我们在车削加工过程中,经常会碰到一些薄壁零件的加工。
如轴套薄壁件(图1),环类薄壁件(图2),盘类薄壁件(图3)。
本文详细分析了薄壁类零件的加工特点、防止变形的装夹方法、车刀材料、切削参数的选择及车刀几何角度。
进行了大量的实验,为以后更好地加工薄壁类零件,保证加工质量,提供了理论依据。
图1轴套薄壁件图2环类薄壁件图3盘类溥壁件1. 薄壁类零件的加工特点1.1因零件壁薄,在使用通用夹具装夹时,在夹压力的作用下 极易产生变形,而夹紧力不够零件又容易松动,从而影响零件的尺 寸精度和形状精度。
如图4所示,当采用三爪卡盘夹紧零件时,在夹紧力的作用下, 零件会微微变成三角形,车削后得到的是一个圆柱体。
但松开卡爪, 取下零件后,由于零件弹性,又恢复成弧形三角形。
这时若用千分 尺测量时,各个方向直径相同,但零件已变形不是圆柱体了,这种 变形现象我们称之为等直径变形。
7 35Jr' 卜 A 討图4三爪卡盘装夹1.2因零件较薄,加工时的切削发热会引起零件变形,从而使零件尺寸难以控制。
对于膨胀系数较大的金属薄壁零件,如在一次安装中连续完成半精车和精车,由切削热引起零件的热变形,会对其尺寸精度产生极大影响,有时甚至会使零件卡死在芯轴类的夹具上。
1.3薄壁类零件加工内孔中,一般采用单刃镗刀加工,此时,当零件较长时,如果刀具参数及切削用量处理不当,将造成排屑困难,影响加工质量,损伤刀具。
数控车削加工薄壁零件的技巧
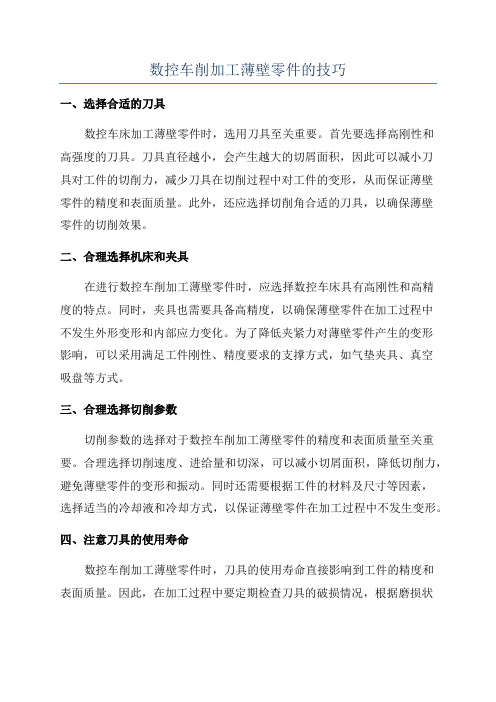
数控车削加工薄壁零件的技巧一、选择合适的刀具数控车床加工薄壁零件时,选用刀具至关重要。
首先要选择高刚性和高强度的刀具。
刀具直径越小,会产生越大的切屑面积,因此可以减小刀具对工件的切削力,减少刀具在切削过程中对工件的变形,从而保证薄壁零件的精度和表面质量。
此外,还应选择切削角合适的刀具,以确保薄壁零件的切削效果。
二、合理选择机床和夹具在进行数控车削加工薄壁零件时,应选择数控车床具有高刚性和高精度的特点。
同时,夹具也需要具备高精度,以确保薄壁零件在加工过程中不发生外形变形和内部应力变化。
为了降低夹紧力对薄壁零件产生的变形影响,可以采用满足工件刚性、精度要求的支撑方式,如气垫夹具、真空吸盘等方式。
三、合理选择切削参数切削参数的选择对于数控车削加工薄壁零件的精度和表面质量至关重要。
合理选择切削速度、进给量和切深,可以减小切屑面积,降低切削力,避免薄壁零件的变形和振动。
同时还需要根据工件的材料及尺寸等因素,选择适当的冷却液和冷却方式,以保证薄壁零件在加工过程中不发生变形。
四、注意刀具的使用寿命数控车削加工薄壁零件时,刀具的使用寿命直接影响到工件的精度和表面质量。
因此,在加工过程中要定期检查刀具的破损情况,根据磨损状况及时更换刀具。
另外,要合理安排刀具的刀具卸刀和出刀次数,避免刀具的过度磨损。
五、加工顺序的确定在数控车削加工薄壁零件时,工艺的合理规划是非常重要的。
应该根据零件的形状和要求,合理确定加工顺序,优先进行刚性要求高的部位的加工,再进行壁厚较薄的部位的加工,以避免由于前期加工引起的零件形变对后续加工的影响。
综上所述,数控车削加工薄壁零件的技巧包括选择合适的刀具、合理选择机床和夹具、合理选择切削参数、注意刀具的使用寿命以及确定合理的加工顺序。
只有掌握了这些技巧,才能够有效地提高薄壁零件的加工质量和生产效率。
薄壁工件的车削加工工艺详细介绍
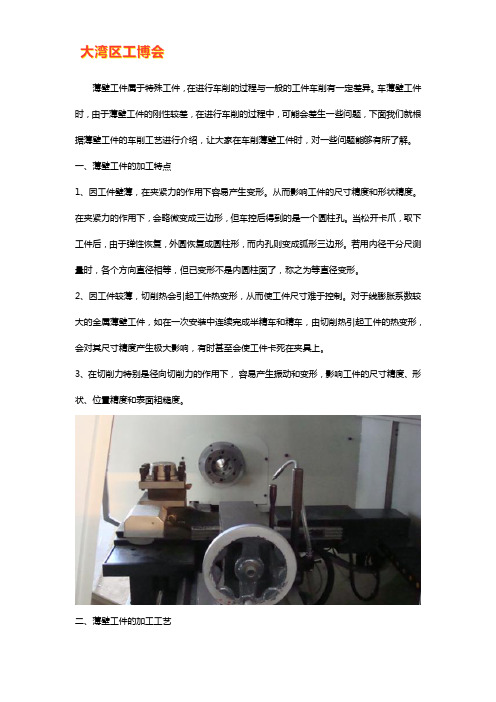
薄壁工件属于特殊工件,在进行车削的过程与一般的工件车削有一定差异。
车薄壁工件时,由于薄壁工件的刚性较差,在进行车削的过程中,可能会差生一些问题,下面我们就根据薄壁工件的车削工艺进行介绍,让大家在车削薄壁工件时,对一些问题能够有所了解。
一、薄壁工件的加工特点1、因工件壁薄,在夹紧力的作用下容易产生变形。
从而影响工件的尺寸精度和形状精度。
在夹紧力的作用下,会略微变成三边形,但车控后得到的是一个圆柱孔。
当松开卡爪,取下工件后,由于弹性恢复,外圆恢复成圆柱形,而内孔则变成弧形三边形。
若用内径千分尺测量时,各个方向直径相等,但已变形不是内圆柱面了,称之为等直径变形。
2、因工件较薄,切削热会引起工件热变形,从而使工件尺寸难于控制。
对于线膨胀系数较大的金属薄壁工件,如在一次安装中连续完成半精车和精车,由切削热引起工件的热变形,会对其尺寸精度产生极大影响,有时甚至会使工件卡死在夹具上。
3、在切削力特别是径向切削力的作用下,容易产生振动和变形,影响工件的尺寸精度、形状、位置精度和表面粗糙度。
二、薄壁工件的加工工艺1、工件分粗、精车阶段精车时,由于切削余量较大,夹紧力稍大些,变形也相应大些;精车时,夹紧力可稍小些,一方面夹紧变形小,另一方面精车时还可以消除粗车时因切削力过大而产生的变形。
2、合理选用道具的集合参数精车薄壁工件时,刀柄的刚度要求高,车刀的修光刃不易过长,一般取0.2—0.3mm,刃口要锋利。
3、增加装夹接触面采用开缝套筒或一些特制的软卡爪。
使接触面增大,让夹紧力均匀分布在工件上,从而使工件夹紧时不易产生变形。
4、应采用轴向夹紧夹具车薄壁工件时,工件靠轴向夹紧套(螺纹套)的端面实现轴向夹紧,由于夹紧力沿工件轴向分布,而工件轴向刚度大,不易产生夹紧变形。
5、增加工艺肋有些薄壁工件在其装夹部位特制几根工艺肋,以增强此处刚性,使夹紧力作用在工艺肋上,以减少工件的变形,加工完毕后,再去掉工艺肋。
6、充分浇注切削液通过充分浇注切削液,降低切削温度,减少工件热变形。
薄壁零件的数控车削加工探讨

薄壁零件的数控车削加工探讨一、薄壁零件在数控车削加工中的问题1. 变形问题:薄壁零件在数控车削加工中容易受到刀具切削力的影响,从而产生变形。
尤其是在加工过程中,由于热变形效应的存在,薄壁零件更容易出现变形现象。
变形不仅会影响零件的尺寸精度和几何形状,还会降低零件的使用寿命和性能。
2. 振动问题:由于薄壁零件的结构特点,容易受到切削力的作用而产生振动现象。
振动不仅会影响加工质量,还会加剧刀具磨损、降低加工精度、影响加工表面质量等问题。
3. 切屑问题:薄壁零件在数控车削加工中,由于切削力的作用,容易产生大量的切屑,而这些切屑往往会对加工表面造成损坏,同时也会对工件和刀具造成损伤。
以上问题对薄壁零件的加工质量和加工效率都会产生较大的影响。
如何解决这些问题,提高薄壁零件的加工质量和效率,是当前数控车削加工中的一个重要课题。
二、解决问题的方法和技术1. 刀具选择和切削参数的优化:在数控车削加工中,合理选择刀具和优化切削参数对薄壁零件的加工具有重要意义。
选择合适的刀具材料和刀具几何形状对降低切削力、延长刀具使用寿命非常重要。
通过优化切削速度、进给量、切削深度等切削参数,可以有效地减少切削力、降低振动,从而保证薄壁零件的加工质量。
2. 支撑技术:薄壁零件在数控车削加工中,可以采用支撑技术来减少变形和振动。
支撑技术可以通过在零件上设置支撑点、改变切削路线等方式,有效地提高零件的刚度和稳定性,减少变形和振动。
可以在薄壁零件的内部设置支撑件,以增加结构的刚性,减少振动和变形。
3. 刀轴倾角补偿技术:在数控车削加工中,刀轴倾角对薄壁零件的加工具有重要影响。
合理地设置刀轴倾角可以有效地减少切削力和振动,避免因为切削力对零件产生的变形。
通过刀轴倾角补偿技术,可以实现对零件的精密加工,提高加工质量。
4. 加工路径优化技术:在数控车削加工中,通过优化加工路径,可以减少切屑对加工表面的损害,同时也可以减少切削力和振动。
在薄壁零件的加工中,通过合理设置加工路径和切削方向,可以减少切屑的产生,提高加工表面的光洁度和平整度。
数控车削加工薄壁零件如何克服变形?

在切削过程中,薄壁受切削力的作用,容易产生变形,从而导致出现椭圆或中间小,两头大的“腰形”现象。
另外薄壁套管由于加工时散热性差,极易产生热变形,不易保证零件的加工质量。
下图零件不仅装夹不方便,而且加工部位也难以加工,需要设计一专用薄壁套管、护轴。
▌工艺分析根据图纸提供的技术要求,工件采用无缝钢管进行加工,内孔和外壁的表面粗糙度为Ra1.6μm,用车削可达到,但内孔的圆柱度为0.03mm,对于薄壁零件来讲要求较高。
在批量生产中,工艺路线大致为:下料—热处理—车端面—车外圆—车内孔—质检。
“内孔加工”工序是质量控制的关键。
我们抛开外圆、薄壁套管就内孔切削就难保证0.03mm的圆柱。
▌车孔的关键技术车孔的关键技术是解决内孔车刀的刚性和排屑问题。
增加内孔车刀的刚性,采取以下措施:(1)尽量增加刀柄的截面积,通常内孔车刀的刀尖位于刀柄的上面,这样刀柄的截面积较少,还不到孔截面积的1/4,如下左图所示。
若使内孔车刀的刀尖位于刀柄的中心线上,那么刀柄在孔中的截面积可大大地增加,如下右图所示。
(2)刀柄伸出长度尽能做到同加工工件长度长5-8mm,以增加车刀刀柄刚性,减小切削过程中的振动。
▌解决排屑问题主要控制切削流出方向,粗车刀要求切屑流向待加工表面(前排屑),为此采用正刃倾角的内孔车刀,如下图所示。
精车时,要求切屑流向向心倾前排屑(孔心排屑),因此磨刀时要注意切削刃的磨削方向,要向前沿倾圆弧的排屑方法,如下图所示精车刀合金用YA6,目前的M类型,它的抗弯强度、耐磨、冲击韧度以及与钢的抗粘和温度都较好。
刃磨时前角磨以圆以圆弧状角度10°-15°,后角根据加工圆弧离壁0.5-0.8mm(刀具底线顺弧度),c切削刃角k向为§0.5-1为沿切屑刃B点修光刃为R1-1.5,副后角磨成7°-8°为适,E内刃的A-A点磨成圆向外排屑。
▌加工方法(1)加工前必须要做一件护轴。
薄壁零件的数控车削加工探讨
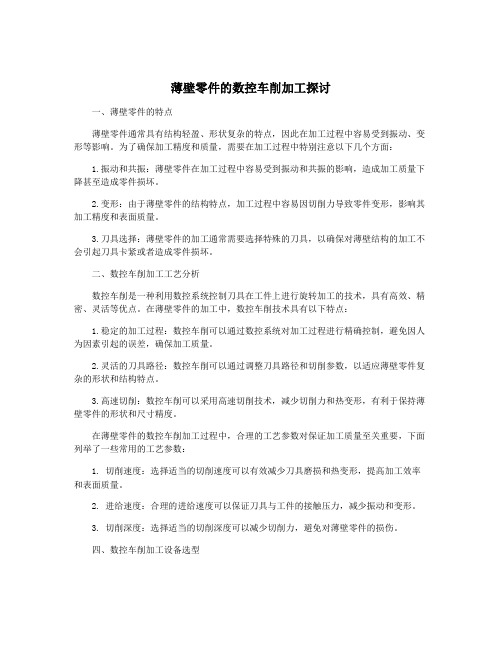
薄壁零件的数控车削加工探讨一、薄壁零件的特点薄壁零件通常具有结构轻盈、形状复杂的特点,因此在加工过程中容易受到振动、变形等影响。
为了确保加工精度和质量,需要在加工过程中特别注意以下几个方面:1.振动和共振:薄壁零件在加工过程中容易受到振动和共振的影响,造成加工质量下降甚至造成零件损坏。
2.变形:由于薄壁零件的结构特点,加工过程中容易因切削力导致零件变形,影响其加工精度和表面质量。
3.刀具选择:薄壁零件的加工通常需要选择特殊的刀具,以确保对薄壁结构的加工不会引起刀具卡紧或者造成零件损坏。
二、数控车削加工工艺分析数控车削是一种利用数控系统控制刀具在工件上进行旋转加工的技术,具有高效、精密、灵活等优点。
在薄壁零件的加工中,数控车削技术具有以下特点:1.稳定的加工过程:数控车削可以通过数控系统对加工过程进行精确控制,避免因人为因素引起的误差,确保加工质量。
2.灵活的刀具路径:数控车削可以通过调整刀具路径和切削参数,以适应薄壁零件复杂的形状和结构特点。
3.高速切削:数控车削可以采用高速切削技术,减少切削力和热变形,有利于保持薄壁零件的形状和尺寸精度。
在薄壁零件的数控车削加工过程中,合理的工艺参数对保证加工质量至关重要,下面列举了一些常用的工艺参数:1. 切削速度:选择适当的切削速度可以有效减少刀具磨损和热变形,提高加工效率和表面质量。
2. 进给速度:合理的进给速度可以保证刀具与工件的接触压力,减少振动和变形。
3. 切削深度:选择适当的切削深度可以减少切削力,避免对薄壁零件的损伤。
四、数控车削加工设备选型1. 设备精度:选择精度高、稳定性好的数控车床,以确保对薄壁零件的加工能够满足工程要求。
2. 加工范围:选择加工范围适中的数控车床,以适应不同尺寸和形状的薄壁零件加工需求。
3. 加工性能:选择具有高速切削、高刚性和稳定性的数控车床,有利于提高加工效率和加工质量。
薄壁零件的数控车削加工是一个复杂而又重要的加工过程。
铝合金薄壁零件的车削工艺要点分析
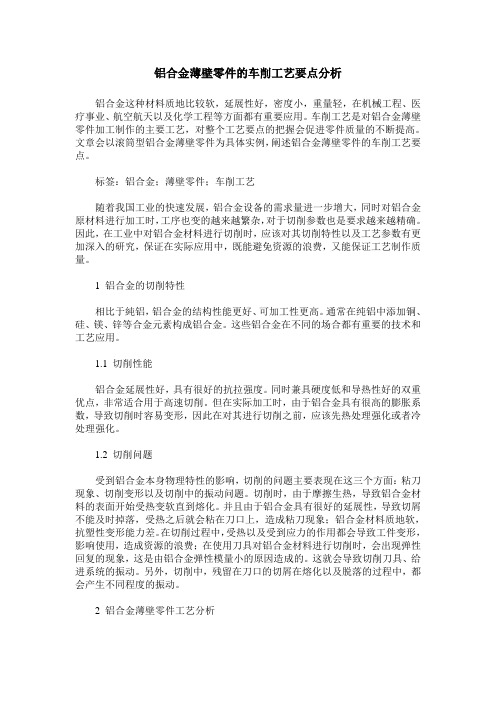
铝合金薄壁零件的车削工艺要点分析铝合金这种材料质地比较软,延展性好,密度小,重量轻,在机械工程、医疗事业、航空航天以及化学工程等方面都有重要应用。
车削工艺是对铝合金薄壁零件加工制作的主要工艺,对整个工艺要点的把握会促进零件质量的不断提高。
文章会以滚筒型铝合金薄壁零件为具体实例,阐述铝合金薄壁零件的车削工艺要点。
标签:铝合金;薄壁零件;车削工艺随着我国工业的快速发展,铝合金设备的需求量进一步增大,同时对铝合金原材料进行加工时,工序也变的越来越繁杂,对于切削参数也是要求越来越精确。
因此,在工业中对铝合金材料进行切削时,应该对其切削特性以及工艺参数有更加深入的研究,保证在实际应用中,既能避免资源的浪费,又能保证工艺制作质量。
1 铝合金的切削特性相比于純铝,铝合金的结构性能更好、可加工性更高。
通常在纯铝中添加铜、硅、镁、锌等合金元素构成铝合金。
这些铝合金在不同的场合都有重要的技术和工艺应用。
1.1 切削性能铝合金延展性好,具有很好的抗拉强度。
同时兼具硬度低和导热性好的双重优点,非常适合用于高速切削。
但在实际加工时,由于铝合金具有很高的膨胀系数,导致切削时容易变形,因此在对其进行切削之前,应该先热处理强化或者冷处理强化。
1.2 切削问题受到铝合金本身物理特性的影响,切削的问题主要表现在这三个方面:粘刀现象、切削变形以及切削中的振动问题。
切削时,由于摩擦生热,导致铝合金材料的表面开始受热变软直到熔化。
并且由于铝合金具有很好的延展性,导致切屑不能及时掉落,受热之后就会粘在刀口上,造成粘刀现象;铝合金材料质地软,抗塑性变形能力差。
在切削过程中,受热以及受到应力的作用都会导致工件变形,影响使用,造成资源的浪费;在使用刀具对铝合金材料进行切削时,会出现弹性回复的现象,这是由铝合金弹性模量小的原因造成的。
这就会导致切削刀具、给进系统的振动。
另外,切削中,残留在刀口的切屑在熔化以及脱落的过程中,都会产生不同程度的振动。
- 1、下载文档前请自行甄别文档内容的完整性,平台不提供额外的编辑、内容补充、找答案等附加服务。
- 2、"仅部分预览"的文档,不可在线预览部分如存在完整性等问题,可反馈申请退款(可完整预览的文档不适用该条件!)。
- 3、如文档侵犯您的权益,请联系客服反馈,我们会尽快为您处理(人工客服工作时间:9:00-18:30)。
薄壁零件车削加工方法探讨
1.薄壁零件的加工特点
1.1薄壁零件不能承受较大的径向力,用通用夹具安装困难。
1.2薄壁零件的刚性差,在夹紧力的作用下,极易产生变形,常态下工件的弹性复原,会影响工件的尺寸精度和形状精度。
1.3工件受切削热的影响,尺寸精度不易控制。
1.4由于切削力的影响,工件易产生变形或振动,尺寸精度和表面粗糙度不易控制。
1.5薄壁零件刚性差,不能采用较大的切削用量,生产效率低。
因此合理的选择装夹方法,加工方法,切削用量,减少振动及充分冷却和检测都是保证加工薄壁零件的关键。
2.薄壁零件的装夹方法
2.1通用软爪定位装夹,选择正确的夹紧力作用点,使夹紧力作用在工件刚性较好的部位,适用于形状和尺寸公差要求不严的零件加工。
优点:装卸方便长度可定位,看承受较大切削力。
缺点:零件定位点较集中,零件加紧后变形较严重。
2.2大面积扇形软爪装夹:采用扇形软爪的三爪卡盘,按与加工零件的装夹面动配合的要求,加工出卡爪的工作面,增大与零件的接触面积。
优点:增大夹紧力的作用面积,使工件支持面增大,夹紧力均匀分布在工作面上,可加大切削用量,不易产生变形。
缺点:扇形软爪不易加工。
2.3芯棒装夹
2.3.1采用椎体芯轴装夹,将零件直接套在椎体芯轴加工。
2.3.2采用圆柱芯轴装夹,将零件装在芯轴上采用轴线压紧。
减小零件径向变形。
优点:装卸零件方便,能保证较高的同心度,技术要求。
缺点:零件内孔被芯轴划伤。
2.4磁力吸盘装夹:采用磁力吸盘将零件吸附在吸盘上,这时零件只受轴向力,而径向不受力。
优点:可一次较高零件内外圆。
缺点:零件找正比较麻烦,应用范围小。
3.薄壁零件较高方法的选择
3.1 先粗后精
先粗加工出零件的外圆和内孔,外圆和内孔均匀留0.5—0.8毫米余量,端面单边留0.25—0.3毫米余量,然后选择适当的装夹方法,将零件精加工到图纸尺寸要求。
3.2先内后外
先加工内孔,以为孔较外圆难加工,易产生变形。
然后加工外圆,可采用芯轴装夹,以内孔定位轴向夹紧,防止零件加工中产生影响加工精度。
3.3一次完成
在一次装夹中完成所需要的加工的所以尺寸,主要应用于毛坯料是
棒料或带有工艺台的薄壁零件加工。
.
4.薄壁零件加工切削用量的选择
在精加工时,应采用大的切削速度,小的进给量(根据车间现有的情况选出以下参数)当机床精度降低时,应适当降低切削速度。
薄壁零件切削用量参数(精车)
5.减小薄壁零件车削时产生振动措施
5.1调整机床主轴和拖板各部间隙,使转动和滑动部分处于最佳状态。
5.2使用吸振材料,用软塑料,橡胶带,棉纱等材料填充或包裹工件。
车削时减小振动和消除噪音的作用。
5.3填充低熔点的物质(如石蜡)就低熔点的物质,填入薄壁零件与芯轴内孔只觉得缝隙,两端用堵头封上,不但减小振动,还可以减小变形。
5.4楔形芯轴填充法,应用铝制楔形芯轴,使楔形芯轴与工件内孔紧密配合达到减振的目的。
6.充分冷却
在加工薄壁零件时,应使薄壁零件得到冷却,降低切削温度,减小零件受热而产生变形,提高了加工精度。
.
7.薄壁零件的检测
薄壁零件在加工完毕好,采用不同的检测方法,往往会出现不同的检测结果,适用检测尺寸的测量力不能过大,应尽量选择小的测量力或无测量力的测量方式,可检测准确。
检测外圆尺寸用打表的方式较好:内孔尺寸用铝板测具测量。
以为用打表方式检测外圆,几乎不受测量力的影响,检测结果准确,采用铝板测量内孔尺寸比内径表撑力想的多,零件不易发生变形。
但也要注意测具橡皮筋不能太久,否则会出现和内径表撑力一样的零件变形尺寸结果。
8.图例说明如图一:
由于该零件属于薄壁环类零件,刚性差,毛坯为棒料,材料牌号为GH3030,采用一次装夹完成图样所示全部尺寸要求,加工步骤如下:1.现车出基准面A和外圆尺寸①,尺寸②留余量
2.车外圆槽保证尺寸④,③,⑧,⑦,⑥,⑤
3.车台阶圆保证尺寸⑩,⑥,⑨
4.车端面槽保证尺寸②,⑾,⑿,⒀,⒁,⒂,⒃,⒄
5.车内孔保证尺寸⒅并切断
此零件加工难点:
1.加工槽时刀具宽度小,刚性差,易扎刀。
2.零件壁薄易变形,加工时需要刀具锋利,切削用量要合适。
3.加工过程中要冷却充分,以便降低切削热,减少零件热变形和刀具磨
损。
.。