超高强度钢板的热冲压成形模具设计及优化方法
超高强度钢板热成形生产方案(一)

超高强度钢板热成形生产方案一、实施背景随着中国制造业的飞速发展,钢铁行业在国民经济中的地位愈加重要。
然而,国内超高强度钢的生产技术与国外先进水平还存在一定差距。
尤其在高品质、高强度、高可靠性方面,我们仍有大量的提升空间。
因此,进行超高强度钢的研发与生产,不仅是产业结构改革的需要,更是提升国家整体竞争力的必然要求。
二、工作原理超高强度钢的研发与生产,首先需要了解其工作原理。
一般来说,超高强度钢的强度高于500MPa,具有出色的抗冲击、抗疲劳性能。
其工作原理主要基于金属的强化机制,如固溶强化、细晶强化、析出强化等。
通过合理的成分设计和热处理工艺,可以显著提高钢材的强度和韧性。
三、实施计划步骤1.成分设计:根据需求和目标,设计合理的化学成分,如C、Si、Mn、Nb、V等元素的含量。
2.冶炼与连铸:通过高纯度冶炼技术,确保钢水中的杂质元素含量低于标准值。
连铸过程中,采用电磁搅拌技术,减小钢水温度梯度,降低裂纹倾向。
3.热处理:根据成分和性能要求,制定合适的热处理工艺。
如淬火、回火、冷却等步骤,以实现钢材的强化和韧化。
4.轧制与精整:通过多道次的轧制和精整,确保钢材的表面质量和尺寸精度。
5.性能检测与质量保证:对每一批次的钢材进行严格的性能检测,如拉伸试验、冲击试验、硬度检测等,确保产品质量达标。
四、适用范围超高强度钢因其出色的力学性能,适用于许多重要领域,如航空航天、汽车、建筑等。
特别是在对强度和可靠性要求极高的场合,如桥梁、高层建筑、高速列车等,其优势更加明显。
五、创新要点1.成分设计创新:通过引入新型合金元素,优化成分比例,达到提高强度和韧性的目的。
例如,添加一定量的Nb和V元素,可以显著提高钢材的抗拉强度和冲击韧性。
2.热处理技术创新:采用先进的热处理工艺,如两相区淬火、等温淬火等,以实现钢材的细晶强化和析出强化。
这些工艺不仅可以提高钢材的强度,还能保持良好的韧性。
3.生产流程优化:通过引入自动化和智能化设备,优化生产流程,提高生产效率。
超高强度钢板冲压件热成形工艺

超高强度钢板冲压件热成形工艺Company number:【0089WT-8898YT-W8CCB-BUUT-202108】.生产侵侵。
超高强度钢板冲压件热成形工艺热成形技术是近年来出现的一项专门用于生产汽车高强度钢板冲压件的先进制造技术。
本文介绍了该技术的原理,讨论了材料,工艺参数.模具等热成形工艺的主要影响因素,完成了汽车典型件热成形工艺试验试制。
获得了合格的成形件。
检测结果表明。
成形件的微观组织为理想的条状马氏体,其抗拉强度.硬度等性能指标满足生产要求。
1前言在降低油耗、减少排放的诸多措施中.减轻车重的效果最为明显.车重减轻10%.可节省燃油 3%一7%,因此塑料.铝合金.高强度钢板等替代材料在车辆制造中开始使用。
其中,高强度钢板可以通过减小板厚或者截面尺寸等方式减轻零件质量.在实现车辆轻量化和提高安全性方面比其他材料有明显优势,可以同时满足实现轻量化和提高安全性的要求,因此其在汽车领域内的应用越来越广泛。
热成形技术是近年来出现的一项专门用于成形高强度钢板冲压件的新技术,该项技术以板料在红热状态下冲压成形并同时在模具内被冷却淬火为特征.可以成形强度高达1500MPa的冲压件,广泛用于车门防撞梁.前后保险杠等保安件以及A柱,B柱.C柱.中通道等车体结构件的生产。
由于具有减轻质量和提高安全性的双重优势,目前.这一技术在德国.美国等工业发达国家发展迅速.并开发出商品化的高强钢热冲压件生产线.高强钢热冲压件在车辆生产中应用也很 .一吉林大学材料学院谷诤巍姜超●机械科学研究总院先进制造技术研究中心单忠德徐虹广泛。
国内汽车业对该项技术也十分认同,并有少数几个单位从国外耗巨资引入了相关技术与生产线, 为一汽-大众等汽车制造公司的部分车型配套热冲压件,关于该项技术的研究工作也已经开始。
本文阐述了热冲压成形工艺原理,对典型冲压件的热冲压成形工艺进行试验研究。
2热冲压成形工艺原理热成形工艺原理如图 1。
首先把常温下强度为500-600MPa的高强度硼合金钢板加热蛩J880-950℃.使之均匀奥氏体化. 然后送入内部带有冷却系统的模具内冲压成形.之后保压快速冷却淬火.使奥氏体转变成马氏体.成形件因而得到强化硬化.强度大幅度提高。
冲压模具设计制造的一些优化方法

冲压模具设计制造的一些优化方法冲压模具设计制造的一些优化方法模块化设计能有效减少产品设计时间并提高设计质量。
下面是店铺整理的冲压模具设计制造的一些优化方法介绍,欢迎参考。
一、模具的模块化方法缩短设计周期并提高设计质量是缩短整个模具开发周期的关键之一。
模块化设计就是利用产品零部件在结构及功能上的相似性,而实现产品的标准化与组合化。
大量实践表明,模块化设计能有效减少产品设计时间并提高设计质量。
因此本文探索在模具设计中运用模块化设计方法。
模具模块化设计的实施:1、建立模块库模块库的建立有三个步骤:模块划分、构造特征模型和用户自定义特征的生成。
标准零件是模块的特例,存在于模块库中。
标准零件的定义只需进行后两步骤。
模块划分是模块化设计的第一步。
模块划分是否合理,直接影响模块化系统的功能、性能和成本。
每一类产品的模块划分都必须经过技术调研并反复论证才能得出划分结果。
对于模具而言,功能模块与结构模块是互相包容的。
结构模块的在局部范围内可有较大的结构变化,因而它可以包含功能模块;而功能模块的'局部结构可能较固定,因而它可以包含结构模块。
模块设计完成后,在Pro/E的零件/装配(Part/Assembly)空间中手工建构所需模块的特征模型,运用Pro/E的用户自定义特征功能,定义模块的两项可变参数:可变尺寸与装配关系,形成用户自定义特征(User-Defined Features,UDFs)。
生成用户自定义特征文件(以gph为后缀的文件)后按分组技术取名存储,即完成模块库的建立。
2、模块库管理系统开发系统通过两次推理,结构选择推理与模块的自动建模,实现模块的确定。
第一次推理得到模块的大致结构,第二次推理最终确定模块的所有参数。
通过这种途径实现模块"可塑性"目标。
在结构选择推理中,系统接受用户输入的模块名称、功能参数和结构参数,进行推理,在模块库中求得适用模块的名称。
如果不满意该结果,用户可指定模块名称.在这一步所得到的模块仍是不确定的,它缺少尺寸参数、精度、材料特征及装配关系的定义。
提升超高强钢构件热冲压技术的效率

提升超高强钢构件热冲压技术的效率提升超高强钢构件热冲压技术的效率随着工业技术的不断进步,越来越多的行业开始使用超高强钢构件。
然而,超高强钢的特殊性质使得其在加工过程中存在一些困难。
其中一种解决方案是热冲压技术,它可以提高超高强钢构件的可塑性和加工效率。
下面将为您介绍提升超高强钢构件热冲压技术效率的步骤。
第一步:确定热冲压过程的工艺参数。
超高强钢的成型温度是关键因素之一。
通过研究和试验,确定最适合该材料的热冲压温度范围。
此外,还需要确定合适的冷却速度和压力等工艺参数。
第二步:选择合适的热冲压设备和工具。
根据所要加工的构件尺寸和形状,选择适当的热冲压设备。
同时,确保所选设备具备高温加热和冷却功能,以实现热冲压过程的完整性。
选用合适的工具,如模具和模具配件,以确保构件的精度和质量。
第三步:优化超高强钢的加热方法。
超高强钢在加热过程中很容易形成氧化层,影响后续的冲压加工。
因此,需要采取适当的加热方法,如保护气氛下的加热或表面涂层等,以减少氧化层的形成。
第四步:控制冷却速度。
超高强钢的冷却速度对于构件的塑性和强度有着重要影响。
通过调整冷却系统的参数,如冷却介质的流量和温度,可以实现对冷却速度的有效控制。
合理的冷却速度可以提高构件的成形性,减少应力和变形。
第五步:优化模具设计。
模具的设计对于热冲压过程的效率和质量至关重要。
通过优化模具的结构和材料选择,可以减少摩擦力和热应力,提高构件的成形性和加工效率。
此外,还需要确保模具的耐热性和耐磨性,以增加模具的使用寿命。
第六步:进行实验和优化。
通过实验和测试,对上述步骤进行不断调整和优化,以达到最佳的热冲压效果和效率。
同时,根据实验结果,对工艺参数和设备进行调整和改进,以提高超高强钢构件热冲压技术的效率。
通过以上步骤,可以提升超高强钢构件热冲压技术的效率。
这将有助于提高超高强钢构件的加工质量和生产效率,推动相关行业的发展。
大型超高强钢热冲压成型装备关键技术及产业化应用
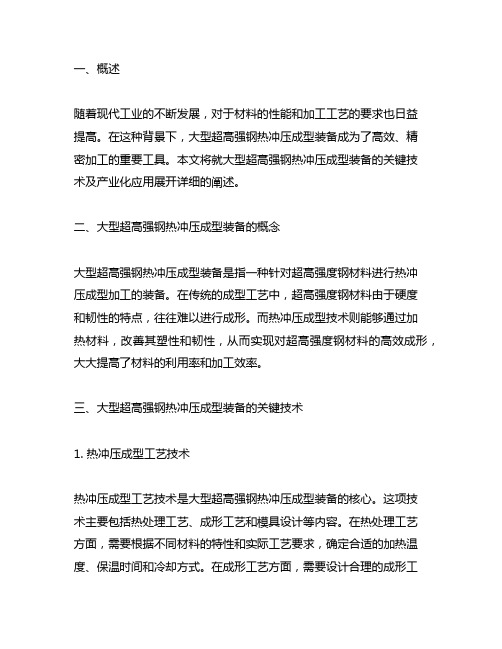
一、概述随着现代工业的不断发展,对于材料的性能和加工工艺的要求也日益提高。
在这种背景下,大型超高强钢热冲压成型装备成为了高效、精密加工的重要工具。
本文将就大型超高强钢热冲压成型装备的关键技术及产业化应用展开详细的阐述。
二、大型超高强钢热冲压成型装备的概念大型超高强钢热冲压成型装备是指一种针对超高强度钢材料进行热冲压成型加工的装备。
在传统的成型工艺中,超高强度钢材料由于硬度和韧性的特点,往往难以进行成形。
而热冲压成型技术则能够通过加热材料,改善其塑性和韧性,从而实现对超高强度钢材料的高效成形,大大提高了材料的利用率和加工效率。
三、大型超高强钢热冲压成型装备的关键技术1. 热冲压成型工艺技术热冲压成型工艺技术是大型超高强钢热冲压成型装备的核心。
这项技术主要包括热处理工艺、成形工艺和模具设计等内容。
在热处理工艺方面,需要根据不同材料的特性和实际工艺要求,确定合适的加热温度、保温时间和冷却方式。
在成形工艺方面,需要设计合理的成形工艺参数,包括压力、速度、温度等,从而确保成形过程的稳定性和高效性。
在模具设计方面,需要根据成形零件的形状和尺寸,设计合适的模具结构和加热方式,以实现对材料的精确成形。
2. 装备设计与制造技术大型超高强钢热冲压成型装备需要具备一定的加热、冷却和成形能力。
在装备设计方面,需要考虑材料的加热均匀性、成形的稳定性和模具的可靠性,从而确保整个成型过程的高效进行。
在装备制造技术方面,需要采用先进的加工工艺和材料技术,确保装备具备高强度、高稳定性和高耐用性,能够满足超高强度钢材料的加工需求。
3. 自动化控制技术自动化控制技术是大型超高强钢热冲压成型装备的重要保障。
通过自动化控制系统,可以实现对热处理、成形和模具等环节的精准控制,确保成型过程的稳定性和可靠性。
自动化控制系统还可以实现对装备运行状态的实时监测和故障诊断,提高了装备的运行效率和安全性。
四、大型超高强钢热冲压成型装备的产业化应用大型超高强钢热冲压成型装备的产业化应用已经在汽车、航空航天、轨道交通等领域得到广泛应用。
冲压磨具结构设计中的优化方法提高冲压效果的有效途径

冲压磨具结构设计中的优化方法提高冲压效果的有效途径在冲压磨具结构设计中,优化方法可以有效提高冲压效果的效率。
通过设计和改进冲压磨具的结构,可以降低冲压过程中的摩擦力和应力集中,提高产品质量和生产效率。
本文将介绍几种优化冲压磨具结构的方法。
1. 合理选择磨具材料磨具的材料选择关系到冲压加工的效果和寿命。
常用的磨具材料有高速钢、硬质合金等。
根据不同的冲压工件要求,选择合适的材料可以提高冲压磨具的硬度和耐磨性,减少磨具损耗和加工成本。
2. 设计合理的结构形式磨具的设计结构形式应根据冲压工件的形状和加工要求进行合理选择。
合理的结构设计可以减少冲击载荷和振动,降低冲压过程中的噪音和能量消耗。
例如,在冲压过程中,为了减少应力集中,可以采用圆角设计,增加局部强度,提高磨具的抗变形能力等。
3. 优化磨具的表面处理磨具的表面处理可以提高冲压效果和寿命。
通过表面处理可以增加磨具的硬度、抗磨性和降低摩擦系数。
常用的表面处理方法有热处理、镀膜和涂层等。
合适的表面处理方法可以延长磨具的使用寿命,提高冲压效果。
4. 运用CAD/CAE技术进行优化设计利用计算机辅助设计软件(CAD)和计算机辅助工程分析软件(CAE)对磨具结构进行仿真和优化分析,可以快速获取磨具结构的各种参数和性能指标。
通过CAD/CAE技术的应用,可以避免设计方案中的缺陷和问题,提高设计效率和精度。
5. 加强磨具的检测和维护对于已经使用的冲压磨具,定期进行检测和维护是保持冲压效果的有效途径。
通过检查和维护可以及时发现和解决磨具的磨损、变形和缺陷等问题,保持磨具的准确性和稳定性,延长使用寿命。
通过优化冲压磨具的结构设计,可以有效提高冲压效果的效率,降低加工成本和改善产品质量。
合理选择磨具材料、设计合理的结构形式、优化磨具的表面处理、运用CAD/CAE技术进行优化设计和加强磨具的检测和维护都是提高冲压效果的有效途径。
高强度钢板热冲压成形模具设计规范

材料选取参考 。为建立热冲压模具 的标 准化 和模 块化设 计规 范奠定基础 , 促进 国产热 冲
压装备 生产线的构建和产业化 实现。 关键词 : 高强度钢板; 热冲压成形; 模具设计 ; 设计规范
中 图分 类号 : T G3 8 5 . 2 文 献标 识 码 : B
De s i g n Spe c i ic f a t i o n o f Ho t S t a mp i ng Fo r mi ng
a n d i t s i nd u s t r i a l i z a t i o n .
Ke y wo r d s : h i g h s t r e n g t h s t e e l p l a t e ; h o t s t a mp i n g or f mi n g ; d i e d e s i g n ; d e s i g n s p e c i i f c a t i o n
对高强度钢板热成的效果越好在考虑导热效果的同时还要兼顾材料形模具基本结构工作部件的模具圆角凸凹模间隙的强度及抗冲击性能图7为不同材料强度与温度的压边圈及拉伸筋等的确定不同于冷成形的结构设计关系图8为不同材料冲击性能与温度的关系
・Hale Waihona Puke 冲模技术
・
高强度钢板热 冲压成 形模具设计规范
谭 海林 , 赖春 明 , 李文元 1 . 湖 南化 工职业技术 学院机 械 工程 系( 湖 南株 洲 4 1 2 0 0 4 ) 2 . 湖 南工业 大学机械 工程 学院 ( 湖 南株洲 4 1 2 0 0 7 )
Di e f o r t h e Hi g h S t r e n g t h S t e e l Pl a t e
基于Kriging模型的超高强度钢板热冲压工艺参数优化

基于Kriging模型的超高强度钢板热冲压工艺参数优化I. 引言(1)研究背景及意义(2)当前研究现状(3)研究内容和目的(4)研究方法和步骤II. 超高强度钢板材料特性及热冲压工艺特点(1)超高强度钢板的优势和应用领域(2)热冲压工艺的工艺流程和参数对零件性能的影响(3)超高强度钢板在热冲压工艺中的问题和优化方向III. Kriging模型理论及其在工艺参数优化中的应用(1)Kriging模型的基本理论和特点(2)Kriging模型在工艺参数优化中的应用原理(3)Kriging模型构建过程和优化算法IV. 超高强度钢板热冲压工艺参数优化实验研究(1)实验设计和数据采集(2)Kriging模型构建和优化过程(3)优化结果分析和验证V. 结论与展望(1)研究成果总结和评价(2)存在的问题和改进方向(3)未来研究展望和发展趋势注:具体内容需根据实际研究情况和要求进行修改。
第一章:引言1.1 研究背景及意义随着汽车、航空航天等领域对材料性能和零部件质量要求的不断提高,超高强度钢材料逐渐成为了这些领域的研究热点。
作为一种高强度、耐磨、耐腐蚀的材料,超高强度钢在提高零件性能和轻量化方面具有重要作用。
其中,超高强度钢板在汽车制造中的应用也越来越广泛,例如车身骨架、车门板、支撑件等。
同时,在零件制造过程中,其性能与质量往往受到许多因素的影响,如材料的力学性能、冲压工艺参数等。
其中,热冲压作为一种相对先进的板材成形工艺,因其具有成形精度高、能适用于不同形状或尺寸的模具等优点,被广泛应用于超高强度钢板成形中。
通过适当的热冲压温度和压力控制,可以实现材料变形的均匀分布,从而达到零件外形和内部性能的优化。
因此,在超高强度钢板热冲压过程中,合理的工艺参数选择对于零件性能和质量具有重要影响,如何寻求适当的工艺参数来优化超高强度钢板热冲压成形过程,已经成为了一个重要的问题。
1.2 当前研究现状在超高强度钢板热冲压方面,已有许多研究进行了探讨。
高强钢热冲压成型工艺流程 预热处理 冲压成形 淬火
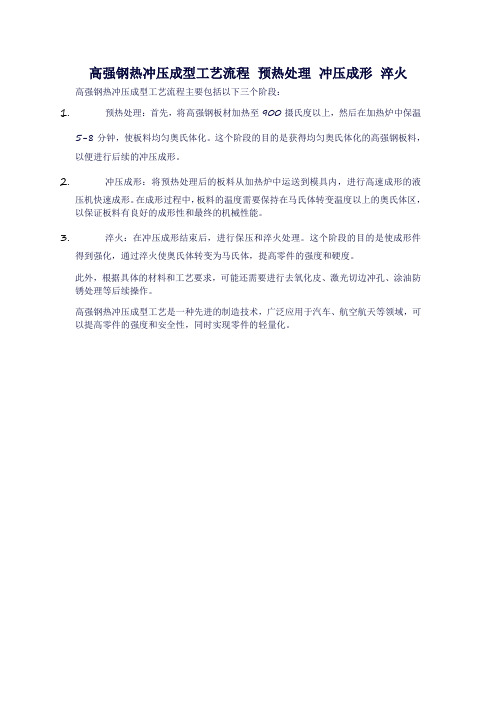
高强钢热冲压成型工艺流程预热处理冲压成形淬火高强钢热冲压成型工艺流程主要包括以下三个阶段:
1.预热处理:首先,将高强钢板材加热至900摄氏度以上,然后在加热炉中保温
5-8分钟,使板料均匀奥氏体化。
这个阶段的目的是获得均匀奥氏体化的高强钢板料,以便进行后续的冲压成形。
2.冲压成形:将预热处理后的板料从加热炉中运送到模具内,进行高速成形的液
压机快速成形。
在成形过程中,板料的温度需要保持在马氏体转变温度以上的奥氏体区,以保证板料有良好的成形性和最终的机械性能。
3.淬火:在冲压成形结束后,进行保压和淬火处理。
这个阶段的目的是使成形件
得到强化,通过淬火使奥氏体转变为马氏体,提高零件的强度和硬度。
此外,根据具体的材料和工艺要求,可能还需要进行去氧化皮、激光切边冲孔、涂油防锈处理等后续操作。
高强钢热冲压成型工艺是一种先进的制造技术,广泛应用于汽车、航空航天等领域,可以提高零件的强度和安全性,同时实现零件的轻量化。
高强钢热冲压成型工艺流程 预热处理 冲压成形
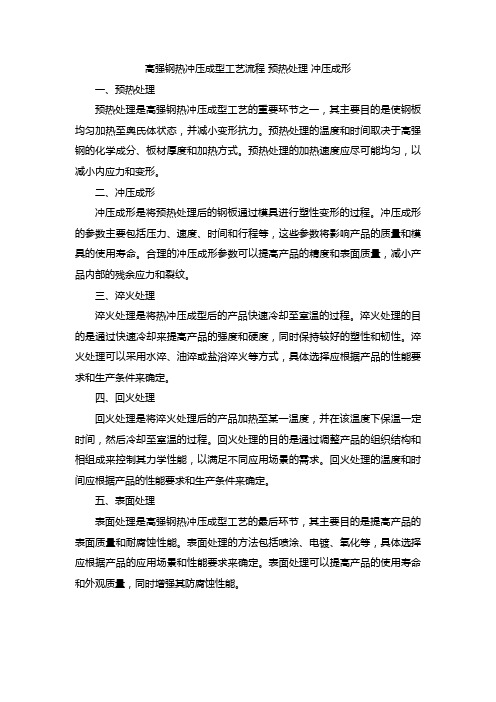
高强钢热冲压成型工艺流程预热处理冲压成形一、预热处理预热处理是高强钢热冲压成型工艺的重要环节之一,其主要目的是使钢板均匀加热至奥氏体状态,并减小变形抗力。
预热处理的温度和时间取决于高强钢的化学成分、板材厚度和加热方式。
预热处理的加热速度应尽可能均匀,以减小内应力和变形。
二、冲压成形冲压成形是将预热处理后的钢板通过模具进行塑性变形的过程。
冲压成形的参数主要包括压力、速度、时间和行程等,这些参数将影响产品的质量和模具的使用寿命。
合理的冲压成形参数可以提高产品的精度和表面质量,减小产品内部的残余应力和裂纹。
三、淬火处理淬火处理是将热冲压成型后的产品快速冷却至室温的过程。
淬火处理的目的是通过快速冷却来提高产品的强度和硬度,同时保持较好的塑性和韧性。
淬火处理可以采用水淬、油淬或盐浴淬火等方式,具体选择应根据产品的性能要求和生产条件来确定。
四、回火处理回火处理是将淬火处理后的产品加热至某一温度,并在该温度下保温一定时间,然后冷却至室温的过程。
回火处理的目的是通过调整产品的组织结构和相组成来控制其力学性能,以满足不同应用场景的需求。
回火处理的温度和时间应根据产品的性能要求和生产条件来确定。
五、表面处理表面处理是高强钢热冲压成型工艺的最后环节,其主要目的是提高产品的表面质量和耐腐蚀性能。
表面处理的方法包括喷涂、电镀、氧化等,具体选择应根据产品的应用场景和性能要求来确定。
表面处理可以提高产品的使用寿命和外观质量,同时增强其防腐蚀性能。
通过以上五个方面的介绍,可以看出高强钢热冲压成型工艺的流程涉及多个环节。
在生产过程中,要保证每个环节的质量和稳定性,以获得高性能的高强钢制品。
超高强度钢材的合金设计与热处理工艺优化
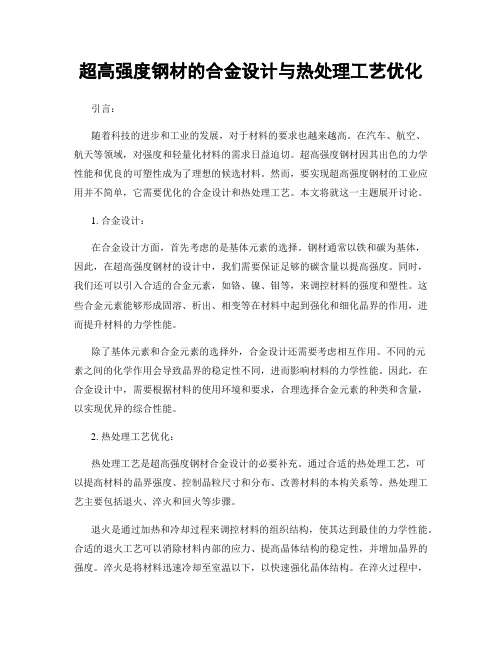
超高强度钢材的合金设计与热处理工艺优化引言:随着科技的进步和工业的发展,对于材料的要求也越来越高。
在汽车、航空、航天等领域,对强度和轻量化材料的需求日益迫切。
超高强度钢材因其出色的力学性能和优良的可塑性成为了理想的候选材料。
然而,要实现超高强度钢材的工业应用并不简单,它需要优化的合金设计和热处理工艺。
本文将就这一主题展开讨论。
1. 合金设计:在合金设计方面,首先考虑的是基体元素的选择。
钢材通常以铁和碳为基体,因此,在超高强度钢材的设计中,我们需要保证足够的碳含量以提高强度。
同时,我们还可以引入合适的合金元素,如铬、镍、钼等,来调控材料的强度和塑性。
这些合金元素能够形成固溶、析出、相变等在材料中起到强化和细化晶界的作用,进而提升材料的力学性能。
除了基体元素和合金元素的选择外,合金设计还需要考虑相互作用。
不同的元素之间的化学作用会导致晶界的稳定性不同,进而影响材料的力学性能。
因此,在合金设计中,需要根据材料的使用环境和要求,合理选择合金元素的种类和含量,以实现优异的综合性能。
2. 热处理工艺优化:热处理工艺是超高强度钢材合金设计的必要补充。
通过合适的热处理工艺,可以提高材料的晶界强度、控制晶粒尺寸和分布、改善材料的本构关系等。
热处理工艺主要包括退火、淬火和回火等步骤。
退火是通过加热和冷却过程来调控材料的组织结构,使其达到最佳的力学性能。
合适的退火工艺可以消除材料内部的应力、提高晶体结构的稳定性,并增加晶界的强度。
淬火是将材料迅速冷却至室温以下,以快速强化晶体结构。
在淬火过程中,通过在材料中形成马氏体相,可以提高其硬度和强度。
回火是在淬火后对材料进行再加热处理,以调整材料的硬度和脆性,使其既有足够的强度又能具备一定的塑性。
在热处理工艺优化中,除了上述基本步骤外,还需要考虑加热速率、保温时间、冷却速率等参数的合理控制。
这些参数的选择与钢材的成分有关,需要通过实验和模拟方法来确定最佳的工艺条件。
结论:超高强度钢材的合金设计与热处理工艺优化是实现材料力学性能提升的关键。
高强度钢板冲压成形仿真与优化
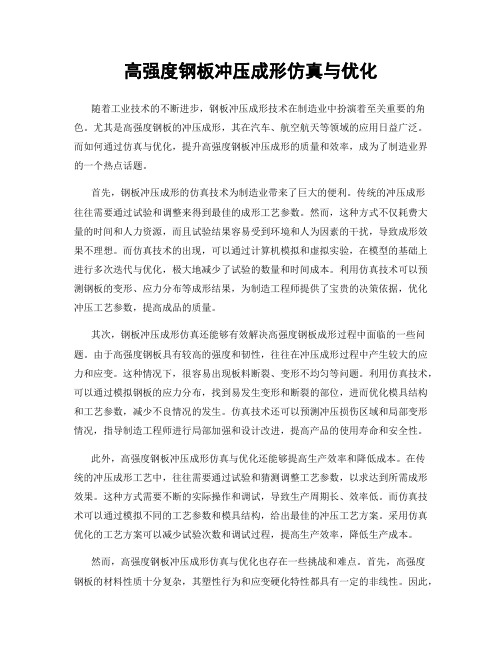
高强度钢板冲压成形仿真与优化随着工业技术的不断进步,钢板冲压成形技术在制造业中扮演着至关重要的角色。
尤其是高强度钢板的冲压成形,其在汽车、航空航天等领域的应用日益广泛。
而如何通过仿真与优化,提升高强度钢板冲压成形的质量和效率,成为了制造业界的一个热点话题。
首先,钢板冲压成形的仿真技术为制造业带来了巨大的便利。
传统的冲压成形往往需要通过试验和调整来得到最佳的成形工艺参数。
然而,这种方式不仅耗费大量的时间和人力资源,而且试验结果容易受到环境和人为因素的干扰,导致成形效果不理想。
而仿真技术的出现,可以通过计算机模拟和虚拟实验,在模型的基础上进行多次迭代与优化,极大地减少了试验的数量和时间成本。
利用仿真技术可以预测钢板的变形、应力分布等成形结果,为制造工程师提供了宝贵的决策依据,优化冲压工艺参数,提高成品的质量。
其次,钢板冲压成形仿真还能够有效解决高强度钢板成形过程中面临的一些问题。
由于高强度钢板具有较高的强度和韧性,往往在冲压成形过程中产生较大的应力和应变。
这种情况下,很容易出现板料断裂、变形不均匀等问题。
利用仿真技术,可以通过模拟钢板的应力分布,找到易发生变形和断裂的部位,进而优化模具结构和工艺参数,减少不良情况的发生。
仿真技术还可以预测冲压损伤区域和局部变形情况,指导制造工程师进行局部加强和设计改进,提高产品的使用寿命和安全性。
此外,高强度钢板冲压成形仿真与优化还能够提高生产效率和降低成本。
在传统的冲压成形工艺中,往往需要通过试验和猜测调整工艺参数,以求达到所需成形效果。
这种方式需要不断的实际操作和调试,导致生产周期长、效率低。
而仿真技术可以通过模拟不同的工艺参数和模具结构,给出最佳的冲压工艺方案。
采用仿真优化的工艺方案可以减少试验次数和调试过程,提高生产效率,降低生产成本。
然而,高强度钢板冲压成形仿真与优化也存在一些挑战和难点。
首先,高强度钢板的材料性质十分复杂,其塑性行为和应变硬化特性都具有一定的非线性。
高强度钢板热冲压水冷模具设计研究
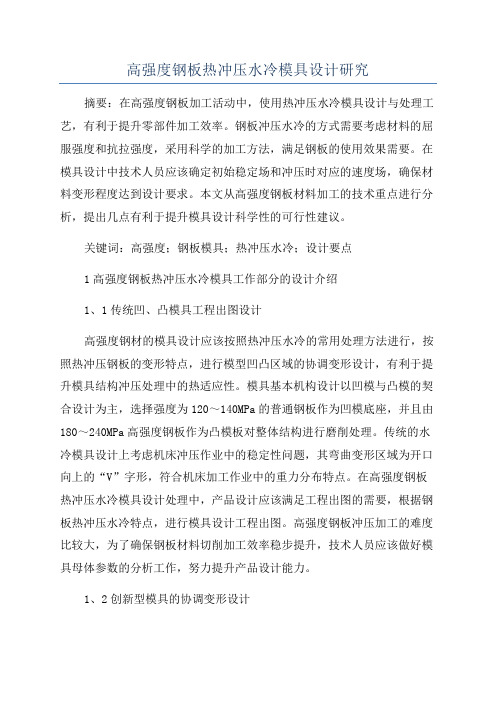
高强度钢板热冲压水冷模具设计研究摘要:在高强度钢板加工活动中,使用热冲压水冷模具设计与处理工艺,有利于提升零部件加工效率。
钢板冲压水冷的方式需要考虑材料的屈服强度和抗拉强度,采用科学的加工方法,满足钢板的使用效果需要。
在模具设计中技术人员应该确定初始稳定场和冲压时对应的速度场,确保材料变形程度达到设计要求。
本文从高强度钢板材料加工的技术重点进行分析,提出几点有利于提升模具设计科学性的可行性建议。
关键词:高强度;钢板模具;热冲压水冷;设计要点1高强度钢板热冲压水冷模具工作部分的设计介绍1、1传统凹、凸模具工程出图设计高强度钢材的模具设计应该按照热冲压水冷的常用处理方法进行,按照热冲压钢板的变形特点,进行模型凹凸区域的协调变形设计,有利于提升模具结构冲压处理中的热适应性。
模具基本机构设计以凹模与凸模的契合设计为主,选择强度为120~140MPa的普通钢板作为凹模底座,并且由180~240MPa高强度钢板作为凸模板对整体结构进行磨削处理。
传统的水冷模具设计上考虑机床冲压作业中的稳定性问题,其弯曲变形区域为开口向上的“V”字形,符合机床加工作业中的重力分布特点。
在高强度钢板热冲压水冷模具设计处理中,产品设计应该满足工程出图的需要,根据钢板热冲压水冷特点,进行模具设计工程出图。
高强度钢板冲压加工的难度比较大,为了确保钢板材料切削加工效率稳步提升,技术人员应该做好模具母体参数的分析工作,努力提升产品设计能力。
1、2创新型模具的协调变形设计新型的冷成型改进模具设计在模型上方增加了压边圈,确保热冲压水冷模具在弯曲变形中不出现无规则变形问题。
用它来处理260~300MPa的超高强度钢板与320~420MPa特高强度钢板的冲压作业,能够收获良好的冲击性能。
新型的冷改进模具设计方法中凹模与凸模的弯曲变形区呈“Z”形,其变形量更加均匀。
新型的冲压水冷模具设计强化了对于压边圈的使用和设计,确保高强度钢板在冲压处理时不出现滚动和不协调变形现象。
高强度钢板热冲压成形模具设计规范

高强度钢板热冲压成形模具设计规范王东生(凌源钢铁集团有限责任公司,辽宁 凌源 122500) 摘 要:伴随着科学技术的不断进步,传统冷冲压处理的方式在实践中遭遇瓶颈,为了有效提升相应工作的时效性,相关人员研究依据热冲压成形技术,能有效进行高强度钢板处理,其中,要着重挂住高强度钢板热冲压成形模具设计的规范化程度,从而维护技术应用的实际价值,实现经济效益和管理效益的共赢。
关键词:高强度;钢板;热冲压;模具设计 中图分类号:TU391 文献标识码:A 文章编号:11-5004(2019)04-0105-2收稿日期:2019-04作者简介:王东生,男,生于1986年,蒙古族,辽宁人,大专,助理工程师,研究方向:模具设计与制造。
热冲压成形技术是一项专门用于成形高强度钢板的新技术。
通过热冲压成形技术可以完成超高强度钢板冲压件的制作,而这项制作技术就是把提前加热至奥氏体化温度以上的板料放置到需要制成的模具之中,并在其放置且逐渐成形的时候进行淬火,这样最终获得的零件能够拥有极高的强度。
同时尺寸也能够更为精准,应用到汽车上后能够起到降低车身重量和为汽车安全性能提供保障的作用。
本文针对超高强度钢板热冲压成形模具设计进行研究,以期在对其了解的基础上进行优化,希望能够起到使得这项技术得到进一步提高的目的。
1 热冲压成形模具设计基本要求在热冲压成形模具设计工作开展的过程中,要结合实际情况建立健全完整的基础管理框架,并且按照标准化要求履行相应工作。
热成形模具的应用不仅仅在于能实现模具的成形处理,也在于对制件结构进行集中的冷却,从而实现淬火处理的目标,基于此,在实际应用中,热冲压成形模具设计的过程相较于传统冷冲压处理过程要更加复杂。
值得一提的是,在热冲压成形模具处理的过程中,本身就要处于冷热交替的环境中,因此,技术人员要对模具的实际应用材料予以集中管理,挑选更加适宜的材料完成相应处理工序。
第一,选取的材料要具备较好的成形能力,能结合相应的操作过程有效完成批量生产,并且确保生产处的样件外形的尺寸精度以及表面的质量都能满足实际需求,整体质量合格。
冲压模具设计与优化的关键技术分析
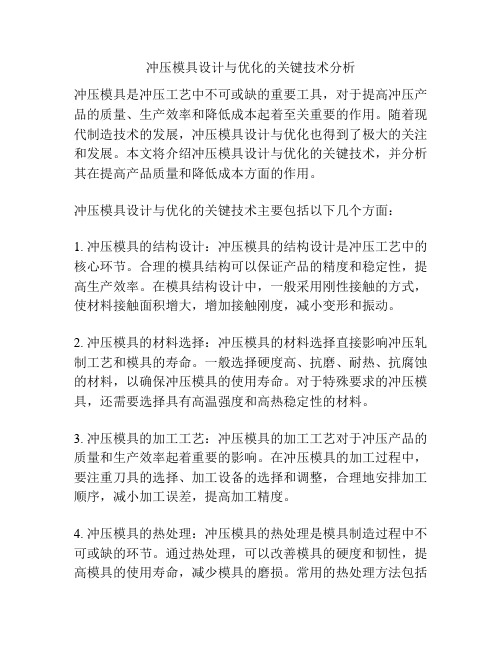
冲压模具设计与优化的关键技术分析冲压模具是冲压工艺中不可或缺的重要工具,对于提高冲压产品的质量、生产效率和降低成本起着至关重要的作用。
随着现代制造技术的发展,冲压模具设计与优化也得到了极大的关注和发展。
本文将介绍冲压模具设计与优化的关键技术,并分析其在提高产品质量和降低成本方面的作用。
冲压模具设计与优化的关键技术主要包括以下几个方面:1. 冲压模具的结构设计:冲压模具的结构设计是冲压工艺中的核心环节。
合理的模具结构可以保证产品的精度和稳定性,提高生产效率。
在模具结构设计中,一般采用刚性接触的方式,使材料接触面积增大,增加接触刚度,减小变形和振动。
2. 冲压模具的材料选择:冲压模具的材料选择直接影响冲压轧制工艺和模具的寿命。
一般选择硬度高、抗磨、耐热、抗腐蚀的材料,以确保冲压模具的使用寿命。
对于特殊要求的冲压模具,还需要选择具有高温强度和高热稳定性的材料。
3. 冲压模具的加工工艺:冲压模具的加工工艺对于冲压产品的质量和生产效率起着重要的影响。
在冲压模具的加工过程中,要注重刀具的选择、加工设备的选择和调整,合理地安排加工顺序,减小加工误差,提高加工精度。
4. 冲压模具的热处理:冲压模具的热处理是模具制造过程中不可或缺的环节。
通过热处理,可以改善模具的硬度和韧性,提高模具的使用寿命,减少模具的磨损。
常用的热处理方法包括淬火、回火、渗碳等。
冲压模具设计与优化的关键技术在提高产品质量和降低成本方面起着重要作用。
首先,通过合理的模具结构设计可以减小变形和振动,提高产品的形状精度和尺寸精度。
其次,通过合理的材料选择和加工工艺可以提高模具的耐磨性和使用寿命,减少模具的更换次数和生产停机时间,提高生产效率。
此外,通过合理的热处理可以提高模具的硬度和韧性,减少模具的磨损,降低成本。
总之,冲压模具设计与优化的关键技术对于提高产品质量和降低成本具有重要的作用。
随着现代制造技术的不断发展,冲压模具设计与优化也将越来越重要。
高强度板冲压工艺及模具制造

高强度板冲压工艺及模具制造在汽车高强度板的冲压工艺设计过程中,科学地进行工艺补充造型以及变参数的拉延筋设计,削减了模具调试次数,缩短了模具制造周期和制造成本,保证了产品质量。
高强度板应用在车身结构中能够使车身减重达到25%左右,节约约15%的燃油。
因此,提高高强度板在车身结构件中的利用率,对于实现汽车质量轻量化、节省能源、爱护环境和平安性能等方面具有重要意义。
本文结合实际重点介绍了汽车掩盖件中高强度板材的冲压工艺设计与模具制造留意事项。
冲压工艺所示为我公司担当开发某模具项目的一个冲压件前防撞梁外板。
其材料为D340LA,料厚为1.2mm,形状尺寸:长为1290mm,宽为220mm,高为67mm。
前防撞梁外板依据产品的尺寸,我们可以看出,该产品外部外形并不简单,但却属于高强度钢板。
通常,对于高强度板材零件的冲压过程,会产生零件扭曲、回弹和翘曲等问题,必需加以解决。
因此,要在冲压工艺制定过程中留意以下事项:1. 拉延成形要充分高强度板材零件在冲压时,其外形要尽量全部拉延出来,不要靠后序的翻边、整形工序来实现,也就是说,要通过拉延成形,让板料产生充分的塑性变形,削减自身的回弹应力。
但如何才能让高强度板材产生充分的塑性变形,需要通过设计合理的工艺补充来实现,以往此类零件的拉延筋通常设计成圆形的,但对于此件,我们采纳了方筋.前防撞梁外板拉延数模前防撞梁外板拉延方筋尺寸2.进行CAE分析通过拉延成形工序做好数模后,必需要进行CAE分析,并依据分析的结果,判定零件回弹趋势大小,然后在数据上加以补偿,并用补偿后的数模作为加工依据。
零件的拉延工序回弹补偿。
3.冲孔模具型面加工数据的确定拉延工序后、翻边修整工序前的修边冲孔模具型面加工数据,肯定要以调试好的最终拉延件为准,而不能以经过CAE分析后作过回弹补偿的拉延数模数据为准。
这就需要对最终拉延件进行逆向建模,然后以逆向建模的数据作为加工修边冲孔模具的加工工艺数模依据。
- 1、下载文档前请自行甄别文档内容的完整性,平台不提供额外的编辑、内容补充、找答案等附加服务。
- 2、"仅部分预览"的文档,不可在线预览部分如存在完整性等问题,可反馈申请退款(可完整预览的文档不适用该条件!)。
- 3、如文档侵犯您的权益,请联系客服反馈,我们会尽快为您处理(人工客服工作时间:9:00-18:30)。
超高强度钢板的热冲压成形模具设计及
优化方法
摘要:热冲压成形技术,属于高强度的冲压技术一种制作方式,被广泛应用
至超过强度类型钢板生产制造当中。
为能够更好地满足此类钢板的生产制造需求,注重对热冲压成形模具合理设计及其优化较为重要。
故本文主要探讨超高强度钢
板热冲压成形模具相关设计和优化方法,仅供业内相关人士参考。
关键词:钢板;超高强度;热冲压;冲压成形;模具设计;优化方法
前言
现阶段,针对高强度类型钢板产品实际生产制造当中,往往需用到热冲压成
形技术,可确保钢板生产制造更具精准性,为产品质量提供保证。
因而,对超高
强度钢板热冲压成形模具相关设计和优化方法开展综合分析较为必要。
1、关于热冲压成形工艺概述
热冲压成形工艺,属于零件的一种加工方式,坯料加热到特定温度后,借助
冲压装置处于成形模具当中实施冲压与淬火同步处理,获取所需外形、金属类型
材料相变的材料成型一种技术工艺或者方法。
2、模具设计和优化方法
2.1设计分析
针对超高强度钢板实际生产制造当中热冲压成形模具总体设计,其所涉及的
内容相对较多,对凹凸模型实施角设计往往比较重要,受拉伸件将决定着部件实
际大小,且该拉伸件显著影响着热冲压的整个拉裂过程。
现场实施锻造期间,对
凹凸模板当中可预留好间隙,可促使板料与模具的关系得以增强,确保二者实现
紧密连接,模具间隙如果有问题出现,则必然影响到模具冷却及其形成;设计者
还需结合各项参数要求,对拉伸筋及延边圈等零件实施合理设计,确保各零件更
具匹配度[1]。
同时,热冲压模具成形,其对于超高强度钢板方面有着高要求。
热
冲压方面工艺制造实施过程,板料均需得到高强度的相应加热处理,确保其能够
结晶。
再落实冲压成形方面的设计操作,维持一定静置时间,则零件尺寸、形状
基本稳定。
而这一过程,往往对板料要求会相对较高,为避免材料自身强度下降,则加热过程需注重淬火处理,以此获取超过强度相应钢构件。
工艺成形整个过程,因热冲压、淬火应当同步落实,所以,该钢板务必经由热冲压整个热循环过程。
钢板在现场被加热至最终结晶,考虑到现场有一定的流动空气,则钢板表面部位
会因氧化而逐渐脱落,自身强度必然受到影响。
故热冲压模具成形整个过程,超
高强度类型钢板自身的抗高温性、耐腐蚀性均应当相对较强;此外,成形模具均
应提高对于各材料选用、冷却系统相关设置要求。
模具材料具体选用方面,不但
要确保超高强度钢板自身有良好的耐腐蚀性及抗高温性,还应当能够将较强摩擦
均抵抗住,以促使模具表面总体磨损效应得以降低。
设计模具当中冷却系统,务
必以系统结构方面设计为实施模具设计的一部分重点内容,让热冲压全过程当中
同步实施淬火处理和批量生产方面需求。
还应当满足对零件实施冷却处理方面的
速度需求,确保以更快速度带走所产生的热量,使得整个模具温度达到良好的平
衡性。
2.2技术问题
为能够更好地对热冲压成形模具实施设计优化,且就必须要考虑到设计技术
方面现存一些重点问题。
一是,针对材料成形实际温度及其降温速度相互间的关
系方面。
针对于热冲压相应成形技术,材料成形及其降温速度,均是模具力学性
重要影响因素范畴,对超高强度类型钢板当中热冲压成形模具总体设计效果有影
响产生。
钢板材料整体经由热冲压相应处理过程,往往涉及力学、传热各个方面,与应力、应变实际情况相结合后,二者相互间合理的关系即可获取到,但超高强
度这种钢板成形期间,钢板材料实际降温速度往往有差异性存在,应力及其应变
曲线均存在差异性,这就需改变基础条件,便于获取到更具合理性的一个本构关
系[2];二是,针对材料成形具体温度和降温速率相互间的极限方面。
钢板材料倘
若处于弯曲条件,则热冲压实际占据地位往往有利,则弹性变形整体减少明显。
但对复杂性的一些部位加工,会选取多种加工操作程序,还应当全面细致地掌握
材料处于高温条件之下的成形极限。
在一定程度上,变形和温度之间关联性较大,且对于冲头下降、钢板氧化方面会有复合影响产生,模具总体设计优化期间需设
计者予以考虑在内;三是,热冲压各零件质控方面。
热冲压各个零件质控,往往
受宏观层面的工艺条件所影响,且与材料整个微观层面的组织变化存在关联性。
冲压过程当中欠缺均匀性情况下,零件性能必然不均匀;对冲压实操节拍把控及
其零件性能为一种对立关系。
冲压零件,其若是冷却还不够充分情况下便取出,
则制品硬度及其精度无法得到保证。
故对于不同零件开展冷却设计及其质控工作
当中,应当注重冷却沟槽整体合理的优化布设,提高模具总体的冷却速度,确保
零件能够实现均匀性地降温,则热冲压所有零件达到良好质控效果。
2.3优化方法
一是,热冲压成形模具总体设计优化期间,材料选取从属重要节点,应当充
分考虑材料自身的热力学性。
在一定程度上,热冲压成形模具通常是借助模具作
业面和零件之间接触传热,将零件热量带走,对零件予以淬火处理。
故模具材料
自身应当有优良的导热能力,保证钢板和模具之间可实现快速传热,以此赋予材
料优良冷却功能。
同时,因模具处于冷热交替条件之下服役,故模具材料自身应
当有着优良的热机械性及耐磨性等,确保模具尺寸实际精度稳定,且表面部位硬
度较好,可以承受着比较强烈的热摩擦及氧化皮等所致磨损。
还需对模具当中设
冷却水专属流道,确保模具材料自身有优良耐锈蚀特性,冷却管道实际使用过程
不会受冷却介质所产生锈蚀及堵塞情况;二是,注意充分把握好超强钢板的物理
特性,如屈服强度范围为500-1180,用途范围包含着A,B柱防撞梁等,以此为基础,更好地落实超高强度钢板热冲压成形模具相关设计和优化工作;三是,注意
板材在具体热成型前期,它的热处理实际温度范围往往会对成型之后产生影响,
且对于成型设备方面也有着较高要求,所以,务必要严格把控好板材在具体热成
型前期的热处理总体温度,确保其处于合理范围,以免影响到成形之后,还应当
对成形设备予以合理选用,确保其能够满足实际要求。
模具内保压具体时间、冲
压后期的产品冷却处理后的温度,均需结合具体需求予以合理调节,还需对有间
歇性的热成型技术工艺流程予以合理设计及把控;四是,注重对模具间隙与凹凸
模的圆角半径予以优化。
对热冲压整个成形模具予以设计优化,考虑到板料成形、淬火操作通常受模具间隙所产生影响,所以,可确保模具间隙能够适当减小,便
于对模具和板料相互间更好地传热,但板料实际所需承担应力还有应变压力均相
对较大,更会逐渐变薄。
故热冲压成形整个模具设计实践中,模具间隙务必提前
留好,对模具成形、淬火提供便利条件。
热冲压实际成形过程,凹凸模整个圆角
半径比较利于实施模具冷却,板料当中的应力会有所下降。
故应当考虑具体情况,对圆角半径方面予以优化;五是,冷却管道总体直径相对较小情况下,冷却管道
的总数和制造成本会增加。
故设计者应当与水流速度结合,对小直径的冷却管道
予以优化,合理调整冷却管道的直径,确保冷却效果得以提升。
3、结语
综上所述,为确保高精度、高质量地完成超高强度钢板实际生产制造,则需
广大设计者能够充分了解热冲压成形模具总体设计技术方面关键问题,从模具材
料的合理选用、注重对模具间隙与凹凸模的圆角半径合理优化、冷却管道合理优
化设计方面入手,实现对热冲压成形模具总体良好的设计优化,为超高强度钢板
总体生产制造的高效开展奠定基础。
参考文献:
[1]刘鹏,尤宝卿,聂飞,等.热冲压成形零件生产工艺与控制[J].锻造与冲
压,2021(10):18-18,20-23.
[2]杨桂娟赵红美.超高强度硼钢板的热冲压成型技术研究[J].有色金属工
程,2022,12(9):I0005-I0006.。