整体型螺旋翅片管省煤器对流传热系数的计算
省煤器结构比较

注:以基管32X4的管子,烟气横向冲涮受热面来计算:一、面积计算:1米的光管受热面积:F=3.14X0.032X1=0.1平米1米的膜式管受热面积:F=3.14X0.032X1+0.03X1X2-0.004X2=0.062平米(注:扁钢选择30X4)1米的扁钢缠绕翅片管受热面积:F=3.14X0.032X1+3.14X(0.044X0.044-0.032X0.032)÷4÷0.866X28=0.033平米(注:扁钢选择12X4,与管子轴线夹角60度)1米的整体型翅片管受热面积:F=0.0312平米分析:由以上计算可知,受热面积大小依次为:膜式>扁钢缠绕>整体型翅片管>光管比例为6.2:3.3:3.12:1,但综合传热效果依次为:整体型翅片管>扁钢缠绕>膜式>光管。
比例为3.8:2:1.5:1,原因是因为,传热是有温度梯度的,而整体型翅片管是的结构是与温度梯度相符合,不会造成温度集中。
这也正是整体型一次挤压成型专有技术特长所在。
温度集中会造成受热热应力集中,热应力集中点强度下降,膨胀不均,(扁钢容易开裂就是这样形成的)二、耐磨特性:耐磨特性依次为:整体型翅片管>扁钢缠绕>膜式>光管。
原因分析:烟气中含有灰分,灰分对管束进行冲刷,并在管子背面形成卡门涡流,而对光管而言,相对中心径向60度是冲刷最严重的点,这就是为什么第一排管子这个点最先爆管。
但不同的是,整体型翅片管及扁钢缠绕对烟气有个导流作用,灰份对受热面的冲涮就降低多了。
整体型翅片管又具有整体性能,不会开裂不会温度集中强度下降,因而抗冲涮性能是取强的。
三、寿命:寿命是与受热面的耐磨特性一致的。
四、性能持续性:在受热面积一定的呢况下,(扁钢开裂造成受热面积减少)积灰是造成性能下降的主要原因。
积灰是因为灰的流速在某一点降低甚至为零,灰就积聚,而卡门涡流就是积灰的主要原因。
卡门涡流发生在管子的背面径向60~120度区域,而积灰就在此区域,整体型的翅片是梯状结构,一方面对灰的导流,另一方面消除了卡门涡流,还符合温度梯度。
对流传热系数的计算公式
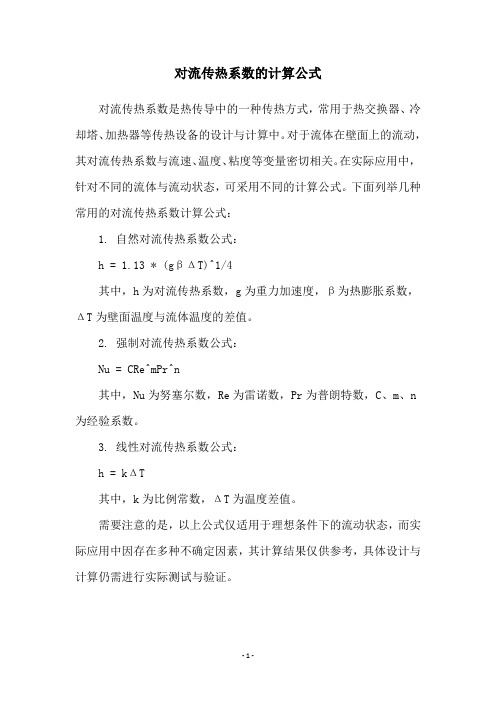
对流传热系数的计算公式
对流传热系数是热传导中的一种传热方式,常用于热交换器、冷却塔、加热器等传热设备的设计与计算中。
对于流体在壁面上的流动,其对流传热系数与流速、温度、粘度等变量密切相关。
在实际应用中,针对不同的流体与流动状态,可采用不同的计算公式。
下面列举几种常用的对流传热系数计算公式:
1. 自然对流传热系数公式:
h = 1.13 * (gβΔT)^1/4
其中,h为对流传热系数,g为重力加速度,β为热膨胀系数,ΔT为壁面温度与流体温度的差值。
2. 强制对流传热系数公式:
Nu = CRe^mPr^n
其中,Nu为努塞尔数,Re为雷诺数,Pr为普朗特数,C、m、n 为经验系数。
3. 线性对流传热系数公式:
h = kΔT
其中,k为比例常数,ΔT为温度差值。
需要注意的是,以上公式仅适用于理想条件下的流动状态,而实际应用中因存在多种不确定因素,其计算结果仅供参考,具体设计与计算仍需进行实际测试与验证。
- 1 -。
翅片管传热计算公式

翅片管传热计算公式翅片管传热是工程中常见的一种传热方式,它通过管道外表面上的翅片来增加传热面积,从而提高传热效率。
翅片管传热计算公式是用来计算翅片管传热效率的重要工具,它可以帮助工程师们准确地预测翅片管传热的性能,从而指导工程设计和优化。
翅片管传热计算公式的推导是基于传热学和流体力学的基本原理,它涉及到传热系数、翅片管的几何形状和流体性质等因素。
下面我们将从这些方面来详细介绍翅片管传热计算公式。
首先,翅片管传热计算公式中最重要的参数之一就是传热系数。
传热系数是描述传热效率的重要参数,它与流体的性质、流动状态、管壁材料等因素有关。
一般来说,传热系数可以通过实验测定或理论计算得到。
在翅片管传热计算中,传热系数的准确性对于预测传热效果至关重要。
其次,翅片管的几何形状也是影响传热效率的重要因素。
翅片管的翅片形状、尺寸和排列方式都会对传热性能产生影响。
一般来说,翅片管的传热面积越大,传热效果就越好。
因此,在翅片管传热计算中,需要考虑翅片的几何形状参数,并将其纳入计算公式中。
最后,流体的性质也是翅片管传热计算公式中需要考虑的因素之一。
流体的性质包括密度、粘度、导热系数等,它们会直接影响传热效率。
在翅片管传热计算中,需要根据流体的性质参数来确定传热系数和传热表面温度差,从而计算出传热效率。
在实际工程中,翅片管传热计算公式通常是基于一些简化假设和经验公式推导而来的。
例如,对于定常流体流动情况下的翅片管传热,可以采用Nusselt数和Reynolds数的关系来计算传热系数;对于不同形状和排列方式的翅片管,可以采用经验公式来估算传热面积增益系数。
这些简化的计算方法虽然可能会引入一定的误差,但在工程实践中已经得到了广泛的应用。
总之,翅片管传热计算公式是工程设计和优化中不可或缺的工具,它可以帮助工程师们准确地预测翅片管传热的性能,从而指导工程设计和优化。
在使用翅片管传热计算公式时,需要充分考虑传热系数、翅片管的几何形状和流体性质等因素,以确保计算结果的准确性和可靠性。
整体型螺旋翅片钢管式省煤器

单位长度受热面积>4F
大
单位长度受热面积>4F
单位重量表面积约2A
传热系数
低,K
在传热过程中烟气侧换热起主导作用。管内、外换热面积相等,导致烟气未将热量及时传递就流走。
高, >2K
存在接触热阻,传热不稳定。长期使用易产生焊缝开裂,不得不更换翅片管。假如裂缝间隙为0.1mm,空气的导热系数为0.021千卡每平方米小时度,则热阻达到0.0045平方米小时度每千卡,相当于180毫米厚钢板的热阻。
更高, >3K
1.无接触热阻。
2.翅片剖面呈梯形,更有利于换热性能。
3.单管换热系数是光管的6~7倍,管束的努谢尔数Nu大于光管的3倍。见附图2.
积灰
易积灰。
多在管子背面形成积灰。烟气侧的灰渣层导热系数很小,即使污垢层很薄,所产生的热阻也很大。每一毫米的灰渣层,相当于400毫米厚的钢壁。污垢热阻的存在,不但削弱了传热,还导致管壁温度显著升高,从而易使管壁过热而烧坏,以致引起事故。
相当于外装加强肋
因为翅片与母管有机一体,并形成螺旋带。比光管显著提高近3倍。见附图1.
耐磨损度
低
容易发生因烟气中的灰分颗粒的高速冲刷磨损,使得管壁减薄,引起爆管
提高
翅片对母体起到增加强度和阻挡直接冲刷的作用
显著提高。
采用热滚压轧制工艺生产,提高了金属组织致密度和硬度。硬度增加提高了整体型翅片管尤其是翅尖的耐磨性,对抵抗烟尘冲刷有利,解决了硫化床锅炉因受热面烟气流速高颗粒硬度大而磨损严重的问题。
整体型螺旋翅片钢管式省煤器(热交换器)
1.性能比较
传统类型省煤器是光管式省煤器(铸铁或钢管),比较新的有采用高频焊接技术实现的螺旋翅片管式省煤器。按换热管直径相同、壁厚相同,比较如下:
翅片管工艺计算公式

翅片管工艺计算公式翅片管的工艺计算公式主要包括传热面积计算、翅片参数计算、翅片管的传热系数计算等内容。
下面将详细介绍这些内容。
首先是传热面积计算。
传热面积是翅片管传热的基础参数,其大小直接影响着翅片管的传热效率。
传热面积的计算公式为:\[A = n \times \pi \times D \times L\]其中,A为传热面积,n为翅片管的数量,D为翅片管的外径,L为翅片管的长度。
通过这个公式,可以计算出翅片管的传热面积,为后续的工艺计算提供基础数据。
其次是翅片参数的计算。
翅片的设计参数包括翅片的宽度、高度、间距等,这些参数的选择对翅片管的传热性能有着重要影响。
翅片参数的计算公式为:\[P = \frac{1}{\sqrt{\frac{1}{h} \times \frac{2t}{k} \times \tanh{mL}}}\]其中,P为翅片的间距,h为流体的对流传热系数,t为翅片的厚度,k为翅片的导热系数,L为翅片的长度,m为翅片的形状系数。
通过这个公式,可以计算出翅片的间距,从而确定翅片的设计参数。
最后是翅片管的传热系数计算。
传热系数是衡量翅片管传热性能的重要参数,其大小取决于翅片管的结构和工艺参数。
传热系数的计算公式为:\[Nu = \frac{hD}{k}\]其中,Nu为翅片管的对流传热系数,h为流体的对流传热系数,D为翅片管的外径,k为流体的导热系数。
通过这个公式,可以计算出翅片管的传热系数,从而评估翅片管的传热性能。
通过以上的工艺计算公式,可以对翅片管的传热性能进行准确的计算和分析,为翅片管的设计和制造提供科学依据。
下面将结合一个实际案例,介绍如何应用这些工艺计算公式。
假设某工厂需要设计一台换热器,其传热介质为水,流体的对流传热系数为1000 W/m2·K,翅片管的外径为20mm,长度为2m,翅片的厚度为1mm,导热系数为200 W/m·K,形状系数为0.5。
现需要计算翅片管的传热面积、翅片参数和传热系数。
新型螺旋翅片管对流换热系数的研究

l 引言
素和变化规律。
2 物 理模 型
对流换热及其强化一直是人们研究的重要课 题…。流道截 面形状对传 热有很大影 响 ,在
物理模型如图 l 待预热空气 ( , 室温 )从管 温度为 管外加翅片是强化传热的最普遍 的方式之一 。 下部进入 ,高温烟气从管外横 向掠过 ( O 60C) 5 ̄ C,并 新型整体翅片管一次轧制成型 ,能够有效地避免 4 O一 0  ̄ 。为把 管内空 气加热 到 30 接触热阻的产 生,大大提高换热器的传热能力 , 避免管外烟气温降过大 ,造成水汽凝结 ,腐蚀翅 2 5o。 而且能够降低烟气对换热器管外表面的磨损和防 片管 ,烟气温 降应小于 30—30c 由于翅 片 止积灰¨ 。如果 能够利用这种换 热器 ,用高炉 】 煤气对进入热风炉的空气进行预热 ,则能够实现 能源的循环利用 。因此 十分有 必要对其进行研 究。本文主要研究换热器对流换热系数 的影响因
P n Ho g e C e gS ue a n w i h n h sn
( nvr t o c n ea dT c nlg e ig U ie i f i c e h o yB in ) sy S e n o j
Ab ta t B sn emeh d 0 u r a i lt n. ac mp trsf aei p l d t ac lt sr c y uigt to fn me cls h i muai o o ue ot r sa pi clua w e O e teh a —e c a e  ̄tmp rtr i l n ic s e h et x h n r e eauef da dt dsust g e o h lr yd c vei a e trn frc e ・ ai t n o e t l a a s n e h t e o伍
翅片管换热器传热计算

翅片管换热器传热计算摘要:换热器传热壁两侧流体的传热膜系数相差较大时,换热器的总传热系数将主要取决于较小的流体的传热系数,为了提高换热器的传热能力,可在传热膜系数小的一侧加翅片管。
影响翅片管表面强化传热的主要因素是翅片高度、翅片节距以及翅片材料的导热系数等,而翅片管翅根直径、管束的纵向节距和横向节距对翅片侧流体的流动阻力的影响很大。
翅片侧流体通过管排的压力降与翅片管纵向管排数成正比,而当纵向管排数大于4排时,管排数量对传热系数没有明显影响。
关键词:翅片效率;努塞尔数;传热系数;压力降换热器传热壁两侧流体的传热膜系数相差较大时,换热器的总传热系数将主要取决于较小的流体的传热系数。
为了提高换热器的传热能力,可在传热膜系数小的一侧加翅片。
如一侧流体是传热膜系数较小的气体,另一侧是传热膜系数较大的液体,这时就可以在传热膜系数较小的气体一侧加装翅片。
1计算条件一台翅片管换热器,管程走导热油,设计温度278℃。
壳程走空气,温度从20℃升到180℃,空气的流量为60kg/s,壳程的压降控制在600Pa以下。
2计算方法2.1计算翅片管的传热面积和流动通道翅片的表面积翅片之间的管表面积翅片管总表面积A=AF+AW=5242.8589+359.68682=5602.5457 m2由于P<x,则穿过nt根管的最小流动面积为:Smin=2ntL(x-P3)=2×26×6.8×(0.1369356-0.0917878)=15.964262m22.2计算翅片管的传热系数Vmax=M/(Sminρ)=60/(15.964262×0.9)=4.1759944m/sRe=VmaxDrρ/μ=4.1759944×0.038×0.9/0.000022=6491.7731Pr=cpμ/λ=1021.6×0.000022/0.031=0.7250065由于l/Dr=0.018/0.038=0.47,翅片管为高翅管,则努塞尔数:管排平均传热系数2.3翅片管传热方程管壁温度与流体温度的温差:换热器需要的换热量:Q=MCp(T2-T1)=60×1021.6×(180-20)=9807360 J/sQ计>Q,换热器满足要求。
翅片管换热系数
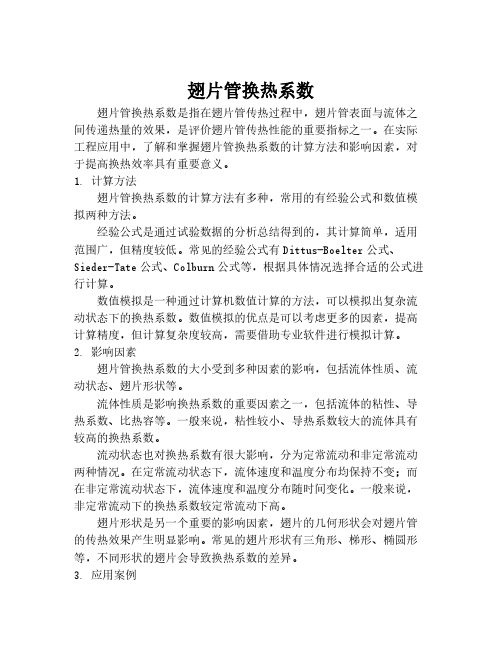
翅片管换热系数翅片管换热系数是指在翅片管传热过程中,翅片管表面与流体之间传递热量的效果,是评价翅片管传热性能的重要指标之一。
在实际工程应用中,了解和掌握翅片管换热系数的计算方法和影响因素,对于提高换热效率具有重要意义。
1. 计算方法翅片管换热系数的计算方法有多种,常用的有经验公式和数值模拟两种方法。
经验公式是通过试验数据的分析总结得到的,其计算简单,适用范围广,但精度较低。
常见的经验公式有Dittus-Boelter公式、Sieder-Tate公式、Colburn公式等,根据具体情况选择合适的公式进行计算。
数值模拟是一种通过计算机数值计算的方法,可以模拟出复杂流动状态下的换热系数。
数值模拟的优点是可以考虑更多的因素,提高计算精度,但计算复杂度较高,需要借助专业软件进行模拟计算。
2. 影响因素翅片管换热系数的大小受到多种因素的影响,包括流体性质、流动状态、翅片形状等。
流体性质是影响换热系数的重要因素之一,包括流体的粘性、导热系数、比热容等。
一般来说,粘性较小、导热系数较大的流体具有较高的换热系数。
流动状态也对换热系数有很大影响,分为定常流动和非定常流动两种情况。
在定常流动状态下,流体速度和温度分布均保持不变;而在非定常流动状态下,流体速度和温度分布随时间变化。
一般来说,非定常流动下的换热系数较定常流动下高。
翅片形状是另一个重要的影响因素,翅片的几何形状会对翅片管的传热效果产生明显影响。
常见的翅片形状有三角形、梯形、椭圆形等,不同形状的翅片会导致换热系数的差异。
3. 应用案例翅片管换热系数在实际工程中有着广泛的应用。
例如,翅片管传热器是一种常见的换热设备,广泛应用于化工、冶金、制药等领域。
通过翅片管传热器,可以有效地将高温流体的热量传递给低温流体,达到能量利用和节能的目的。
在设计和选择翅片管传热器时,需要根据具体工况条件确定合适的翅片管换热系数。
根据流体的性质、流动状态和翅片的形状等因素,结合经验公式和数值模拟等方法,计算得到合理的换热系数,以确保传热效果的高效和可靠性。
空调翅片换热器的传热系数该如何计算?如何最优化?
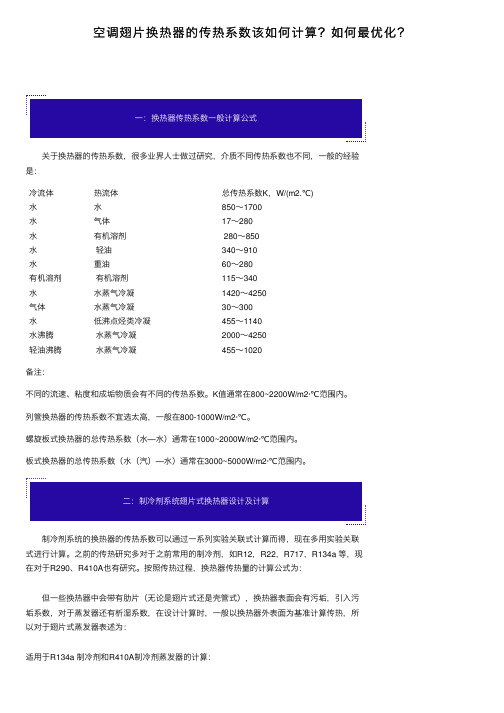
空调翅⽚换热器的传热系数该如何计算?如何最优化?⼀:换热器传热系数⼀般计算公式关于换热器的传热系数,很多业界⼈⼠做过研究,介质不同传热系数也不同,⼀般的经验是:冷流体热流体总传热系数K,W/(m2.℃)⽔⽔850~1700⽔⽓体17~280⽔有机溶剂 280~850⽔轻油340~910⽔重油60~280有机溶剂有机溶剂115~340⽔⽔蒸⽓冷凝1420~4250⽓体⽔蒸⽓冷凝30~300⽔低沸点烃类冷凝455~1140⽔沸腾⽔蒸⽓冷凝2000~4250轻油沸腾⽔蒸⽓冷凝455~1020备注:不同的流速、粘度和成垢物质会有不同的传热系数。
K值通常在800~2200W/m2·℃范围内。
列管换热器的传热系数不宜选太⾼,⼀般在800-1000W/m2·℃。
螺旋板式换热器的总传热系数(⽔—⽔)通常在1000~2000W/m2·℃范围内。
板式换热器的总传热系数(⽔(汽)—⽔)通常在3000~5000W/m2·℃范围内。
⼆:制冷剂系统翅⽚式换热器设计及计算制冷剂系统的换热器的传热系数可以通过⼀系列实验关联式计算⽽得,现在多⽤实验关联式进⾏计算。
之前的传热研究多对于之前常⽤的制冷剂,如R12,R22,R717,R134a 等,现在对于R290、R410A也有研究。
按照传热过程,换热器传热量的计算公式为:但⼀些换热器中会带有肋⽚(⽆论是翅⽚式还是壳管式),换热器表⾯会有污垢,引⼊污垢系数,对于蒸发器还有析湿系数,在设计计算时,⼀般以换热器外表⾯为基准计算传热,所以对于翅⽚式蒸发器表述为:适⽤于R134a 制冷剂和R410A制冷剂蒸发器的计算:这个公式⽐较复杂,所需参数⽐较多,⽽且计算时需要假设热流q 来进⾏迭代计算,但经过计算对⽐发现,可以在上⼀个公式的基础上再乘以⼀个系数,经推算为1.05,就可以将上⼀个公式⽤于R134a。
冷柜⼯况的管内侧换热系数不到1000 W/(m2.C)(R22),这和制冷剂质量流速有关,有研究⼈员⽤Kandlikar 关联式通过计算机模拟得出了R134a 不同质量流速下的换热特征(空调⼯况),见下图:下⾯,⼩编再分享⼀些教科书进⾏计算的参数:三:标准中翅⽚换热器传热系数如何得出?最后,我们来看下现⾏标准JB/T7659.4中翅⽚换热器的传热系数是怎么得出的?1、传热系数的计算⽅法换热器热⼯计算的基本公式是:式中,Φ是换热量,单位:Wk是传热系数,单位:W/(㎡·K)A是换热表⾯积,单位:㎡t1、t2分别是两种换热流体的温度,单位:K(开⽒温度)Δt 是换热温差,单位:K根据公式(1),那么传热系数k的公式如下:要算出翅⽚式换热器的传热系数k,就要先算出换热量Φ、换热⾯积A、换热温差Δt。
翅片管传热计算公式

翅片管传热计算公式翅片管传热是工程中常见的一种传热方式,通过翅片管的表面积增大,从而增加传热面积,提高传热效率。
翅片管传热计算公式是用来计算翅片管传热效率的重要工具,下面我们将详细介绍翅片管传热计算公式的推导和应用。
1. 翅片管传热原理。
翅片管传热是利用翅片管的翅片增加传热面积,从而提高传热效率的一种传热方式。
翅片管通常用于换热器、冷凝器等设备中,通过增加翅片的数量和面积,可以有效提高传热效率,降低设备的体积和成本。
2. 翅片管传热计算公式的推导。
翅片管传热计算公式的推导是基于传热学的基本原理和热传导方程。
在翅片管传热过程中,热量从管壁传递到翅片上,再由翅片传递到周围的介质中,因此翅片管传热可以看作是一维热传导问题。
根据传热学的基本原理和热传导方程,可以推导出翅片管传热计算公式。
翅片管传热计算公式的推导涉及到热传导方程、热传导系数、翅片管的几何形状等多个因素,具体推导过程比较复杂,这里就不展开讨论了。
感兴趣的读者可以参考相关的传热学教材和论文进行深入学习。
3. 翅片管传热计算公式的应用。
翅片管传热计算公式的应用是工程实际中的重要问题。
在工程设计和优化过程中,需要准确地计算翅片管的传热效率,从而选择合适的翅片管参数和优化设备结构。
翅片管传热计算公式的应用涉及到多个因素,包括翅片管的材料、几何形状、传热系数等。
在实际应用中,通常需要根据具体的工程条件和要求来选择合适的翅片管传热计算公式,进行计算和分析。
4. 翅片管传热计算公式的改进。
目前,翅片管传热计算公式的研究仍在不断深入。
随着传热学理论的发展和工程实践的需求,翅片管传热计算公式的改进是一个重要的研究方向。
翅片管传热计算公式的改进可以从多个方面进行,包括考虑非定常传热、多相传热、传热界面的影响等。
通过改进翅片管传热计算公式,可以更准确地预测翅片管的传热效率,为工程设计和优化提供更可靠的依据。
5. 结语。
翅片管传热计算公式是工程中重要的传热计算工具,它的准确性和可靠性直接影响到工程设备的传热效率和性能。
翅片换热器传热系数

翅片换热器传热系数翅片换热器是一种常见的传热设备,用于增加传热表面积,提高传热效率。
传热系数是评价传热性能的重要参数之一,在翅片换热器设计和优化中起着关键的作用。
本文将详细介绍翅片换热器传热系数的定义、影响因素以及传热系数的计算方法。
翅片换热器传热系数受到多种因素的影响,包括流体性质、流体流速、翅片形状和尺寸等。
首先,流体性质对传热系数有很大的影响。
传热介质的热导率和动力粘度决定了能量传递的速率,因此直接影响传热系数的大小。
其次,流体流速也是影响传热系数的重要因素。
当流体流速增加时,流体与翅片之间的对流传热增强,导致传热系数的增加。
此外,翅片的形状和尺寸也影响传热系数。
翅片的形状决定了翅片与流体之间的传热面积和流动阻力,而翅片的尺寸则决定了翅片之间的间隙大小,直接影响传热效果。
计算翅片换热器传热系数的方法有很多,常用的方法包括经验公式法、数值模拟法和试验测量法。
经验公式法是一种简单而实用的方法,可以用于初步估算传热系数。
常用公式包括Dittus-Boelter公式、Sieder-Tate公式和Gnielinski公式等。
这些公式根据研究者对流动形式和传热机制的理解,通过分析实验数据得到的经验公式,适用于不同的工况和翅片形状。
数值模拟法是一种计算机辅助的方法,可以通过数学模型对流动和传热进行模拟,得到传热系数的数值结果。
这种方法能够更准确地预测传热性能,但需要进行复杂的计算和模拟。
试验测量法是一种直接测量传热系数的方法,通过在实验设备中进行传热实验,测量流体的温度差和传热功率来计算传热系数。
这种方法最为准确,但成本较高且需要一定的实验设备和技术支持。
综上所述,翅片换热器传热系数是衡量传热性能的重要参数,其大小受到多种因素的影响。
通过合理选择流体、优化翅片形状和尺寸等措施,可以提高传热系数,进而提高翅片换热器的传热效率。
在实际应用中,需要综合考虑传热效率、成本和设备运行要求等因素,进行合理的设计和选择。
翅片管换热系数

翅片管换热系数摘要:1.翅片管换热系数的基本概念2.翅片管换热系数的计算方法3.影响翅片管换热系数的因素4.提高翅片管换热系数的方法5.翅片管换热系数在实际应用中的重要性正文:翅片管换热系数是热力学领域中一个重要的参数,它反映了换热器中热量传递的效率。
在工业生产、空调制冷等领域中,翅片管换热器得到了广泛的应用。
本文将从翅片管换热系数的基本概念、计算方法、影响因素、提高方法以及在实际应用中的重要性等方面进行详细阐述。
一、翅片管换热系数的基本概念翅片管换热系数是指在单位时间内,单位面积上交换的热量。
它受到许多因素的影响,如换热器的设计、流体的性质、流动状态等。
在实际工程中,准确估算翅片管换热系数对于优化系统设计、提高能源利用率具有重要意义。
二、翅片管换热系数的计算方法翅片管换热系数的计算方法有多种,其中较为常见的是采用努塞尔数(Nusselt Number)和雷诺数(Reynolds Number)两个无量纲数进行计算。
计算公式如下:u = h / kRe = μ × v / √(ρ × k)其中,Nu为努塞尔数,h为翅片管换热系数,k为热传导系数;Re为雷诺数,μ为流体动力粘度,v为流体流速,ρ为流体密度。
三、影响翅片管换热系数的因素1.翅片类型:不同类型的翅片(如螺旋翅片、波纹翅片等)对换热系数产生不同的影响。
2.翅片间距:翅片间距越大,换热系数越小,但流体的压降也会相应降低。
3.流体性质:流体的性质(如粘度、比热容等)对换热系数有显著影响。
4.流动状态:层流与紊流两种流动状态对换热系数的影响截然不同,紊流换热系数通常更高。
四、提高翅片管换热系数的方法1.选择合适的翅片类型和间距:根据实际工况,选用适合的翅片类型和调整翅片间距,以实现较高的换热系数。
2.优化流体流动:通过改变流体的流动状态,如采用湍流促进剂等,以提高换热系数。
3.改进换热器设计:例如增加换热面积、提高热传导性能等,从而提高换热系数。
螺旋鳍片管传热计算的数值分析

入一 烟气 的热 导率 ,W/(m·K1;
h 一开齿鳍片齿根高度,m ;
入厂 管 子 的热 导 率 ,W/(m·K);
I 传 热 系数 ,W/(m2.K1;
九 _ 管 内介质 的热 导率 ,W/(m·K);
m一 鳍 片材 料和 结构特 性 系数 ,1/m ;
1lr一 修正 系数 。团股份有限公司作为国 内 最 大 的 余 热 锅 炉 制 造 基 地 ,具 有 丰 富 的 燃 机 余热 锅 炉 设 计 、制 造 经 验 。为 了提 升大 型 燃 气 一 蒸 汽 联 合 循 环 余 热 锅 炉 设 计 、制 造 能力 ,杭 州 锅 炉集 团 于 2002年 引进 美 国 N/ E全 套 余 热锅 炉 技 术 ,之 后 为 了加 强 余 热 锅 炉 性 能 设 计 水 平 ,又 从 德 国 KED 公 司 引进 PPSD 用 于燃 机余 热 锅炉 的动态 模拟 和 启 动 曲线 的绘制 。
3
热介质,由于二者 黑度相 差不大,因此也不 算公 式如 下 :
(罟)。· ( ]。· ,r·, c8 必考虑管 内辐射 。传热系数 Q。和 d:分别
按公式 (3)和 (4)进 行 :
ct ==c。c c e
0t,1
kc
(3)
雷诺准 则 数 Re按 下式计 算 :
伐 2 CLl【i
2
余 热 锅 炉 2016.1
C广 相 对长 度修 正系 数 ; C 一 受热情 况修 正 系数 ;
a广 烟 气侧 对流 传 热系数 ,W/(m2.K); n k一 烟 气侧 折算传 热 系数 ,W/(m2·K);
C 一温度 修正 系数 ;
Q __管 内对 流传 热 系数 ,W/(m2·K);
翅片式换热器的设计及计算
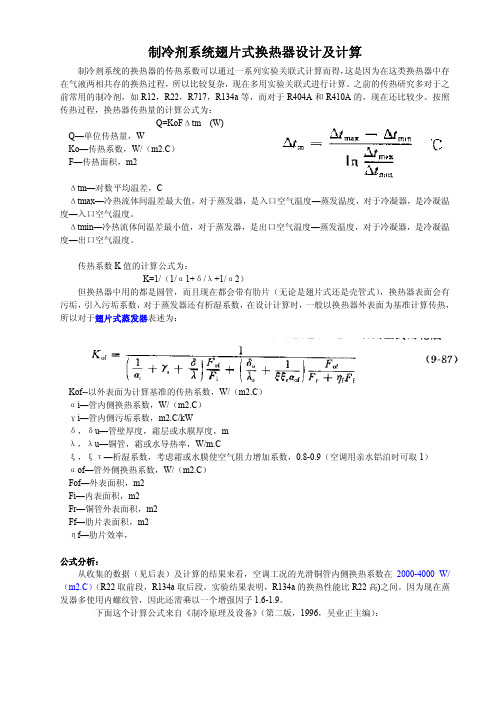
制冷剂系统翅片式换热器设计及计算制冷剂系统的换热器的传热系数可以通过一系列实验关联式计算而得,这是因为在这类换热器中存在气液两相共存的换热过程,所以比较复杂,现在多用实验关联式进行计算。
之前的传热研究多对于之前常用的制冷剂,如R12,R22,R717,R134a等,而对于R404A和R410A的,现在还比较少。
按照传热过程,换热器传热量的计算公式为:Q=KoFΔtm (W)Q—单位传热量,WKo—传热系数,W/(m2.C)F—传热面积,m2Δtm—对数平均温差,CΔtmax—冷热流体间温差最大值,对于蒸发器,是入口空气温度—蒸发温度,对于冷凝器,是冷凝温度—入口空气温度。
Δtmin—冷热流体间温差最小值,对于蒸发器,是出口空气温度—蒸发温度,对于冷凝器,是冷凝温度—出口空气温度。
传热系数K值的计算公式为:K=1/(1/α1+δ/λ+1/α2)但换热器中用的都是圆管,而且现在都会带有肋片(无论是翅片式还是壳管式),换热器表面会有污垢,引入污垢系数,对于蒸发器还有析湿系数,在设计计算时,一般以换热器外表面为基准计算传热,所以对于翅片式蒸发器表述为:Kof--以外表面为计算基准的传热系数,W/(m2.C)αi—管内侧换热系数,W/(m2.C)γi—管内侧污垢系数,m2.C/kWδ,δu—管壁厚度,霜层或水膜厚度,mλ,λu—铜管,霜或水导热率,W/m.Cξ,ξτ—析湿系数,考虑霜或水膜使空气阻力增加系数,0.8-0.9(空调用亲水铝泊时可取1)αof—管外侧换热系数,W/(m2.C)Fof—外表面积,m2Fi—内表面积,m2Fr—铜管外表面积,m2Ff—肋片表面积,m2ηf—肋片效率,公式分析:从收集的数据(见后表)及计算的结果来看,空调工况的光滑铜管内侧换热系数在2000-4000 W/(m2.C)(R22取前段,R134a取后段,实验结果表明,R134a的换热性能比R22高)之间。
因为现在蒸发器多使用内螺纹管,因此还需乘以一个增强因子1.6-1.9。
螺旋管式换热器设计参数计算

介质名称柴油进口温度t1 ℃粘度μ kg/m·h 91.375比热C kcal/kg·℃进口压力P1 MPa 75允许压降△P Kpa 污垢热阻ri kcal/m2·h·℃0.0006141管道绝对粗糙度ε mm介质名称水蒸汽进口蒸汽温度T1 ℃冷凝水粘度μf kg/m·h 0.80129冷凝水密度ρf kg/m3重力加速度g m/h2127000000所需冷凝液量Wf kg/h 材质CT90蛇管外径D0 m 蛇管螺旋间距Pt(1.5-2*D0) m 0.04蛇管根数 N 每根蛇管高度 m 2.8每根蛇管换热面积A m2导热系数Kw kcal/m·h·℃4321505954.590.015333333670.3127174计算所需传热面积A计四、总传热系数(外径基准)总传热系数U五、计算所需传热面积A计传热温差△T2.1德雷为德方程(层流)三、壳程对流传热系数ho(冷凝传热)(Di·Gi/μ)·(Di/DH)1/2=1.3蛇管结构一、工艺参数1.1管程介质1.2壳程介质二、管程对流传热系数hi管内质量流速Gi=4Wt/(πDi 2)=Di/DH=2.2西班方程(湍流)冷凝负荷Γ20出口温度t2 ℃125质量流量Wt kg/h 0.4811446导热系数k kcal/m·h·℃0.106554密度ρ kg/m36000预测的出口压力P2 MPa 69所需传热量Q kcal/h0.4175进口蒸汽压力P3 MPa 0.8出口冷凝水温度T2 ℃940.027冷凝水导热系数kf kcal/m·h·℃0.59048冷凝潜热q kcal/kg 902.8158783污垢热阻r0 kcal/m2·h·℃0.00020470.0318蛇管内径Di m 0.023蛇管螺旋径D H m 1每根蛇管圈数 N070每根蛇管长度L m 32.9546091壳侧容器内径D m 1.7壳侧容器筒体长度H m kg/m2·h 5413.263537412.60382365253.318115kcal/m2·h·℃34.62387087m20.00711834m2·h·℃/kcal 140.482186992.80520067233.7735832251.156885kcal/m2·h·℃2.736906852kg/m·h 雷诺数Re=Di·Gi/μ=Pr=Cμ/k=(Re)crit 20853.24704kcal/m2·h·℃kcal/m2·h·℃λ-1/2)=。
翅片管换热系数

翅片管换热系数1. 什么是翅片管换热系数?翅片管换热系数是描述翅片管换热性能的一个重要参数。
换热系数是指在单位时间内,单位面积的热量传递量与温度差之间的比值。
对于翅片管换热器而言,翅片管换热系数是指翅片管内部与外部之间的热传导和对流换热效果的综合指标。
2. 翅片管换热系数的影响因素翅片管换热系数受到多种因素的影响,下面将对一些主要因素进行介绍。
2.1 翅片形状和尺寸翅片的形状和尺寸对换热系数有较大的影响。
通常情况下,翅片的面积越大,换热系数越高。
此外,翅片形状的选择也会对换热系数产生影响。
常见的翅片形状有矩形、梯形等,不同形状的翅片在不同工况下的换热效果也有所差异。
2.2 流体流速流体流速是影响翅片管换热系数的重要因素之一。
当流体流速增加时,流体与翅片管之间的对流换热效果增强,换热系数也会相应增加。
因此,在设计翅片管换热器时,需要根据流体流速的要求来确定翅片的尺寸和形状。
2.3 翅片材料和表面处理翅片的材料选择和表面处理也会对换热系数产生影响。
一般来说,热导率较高的材料可以提高翅片管的换热系数。
此外,通过对翅片表面进行特殊处理,如增加表面粗糙度或涂覆特殊涂层,也可以提高换热系数。
2.4 温度差温度差是影响翅片管换热系数的另一个重要因素。
温度差越大,换热系数越高。
因此,在实际应用中,需要根据具体的工况来选择合适的翅片管,以获得较高的换热系数。
3. 计算翅片管换热系数的方法计算翅片管换热系数是翅片管换热器设计的重要一环。
下面介绍两种常用的计算方法。
3.1 理论计算方法理论计算方法是通过数学模型和理论公式来计算翅片管换热系数。
这种方法需要根据具体的翅片管结构和工况条件,建立相应的数学模型,并利用热传导和流体力学的基本原理进行计算。
理论计算方法通常精度较高,但需要较多的计算和理论基础。
3.2 实验测定方法实验测定方法是通过实际试验来测定翅片管换热系数。
这种方法通常需要搭建实验装置,在实验室或现场进行试验。
管式加热炉的对流传热之翅片管和钉头管的外膜传热系数(1)
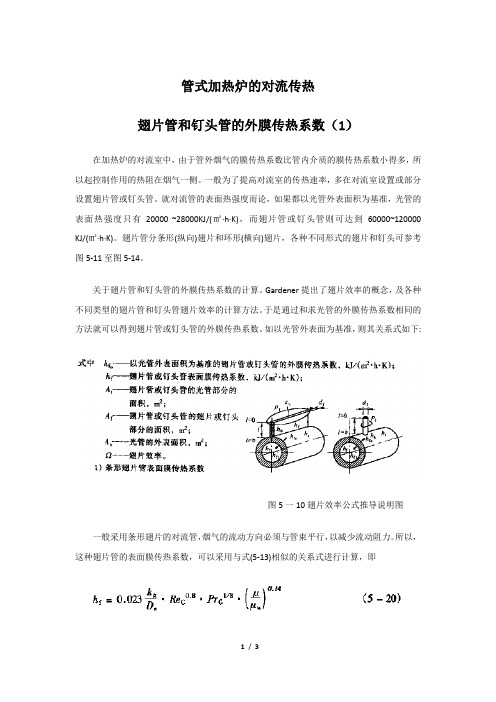
管式加热炉的对流传热翅片管和钉头管的外膜传热系数(1)在加热炉的对流室中,由于管外烟气的膜传热系数比管内介质的膜传热系数小得多,所以起控制作用的热阻在烟气一侧。
一般为了提高对流室的传热速率,多在对流室设置或部分设置翅片管或钉头管。
就对流管的表面热强度而论,如果都以光管外表面积为基准,光管的表面热强度只有20000 ~28000KJ/(㎡·h·K),而翅片管或钉头管则可达到60000~120000KJ/(㎡·h·K)。
翅片管分条形(纵向)翅片和环形(横向)翅片,各种不同形式的翅片和钉头可参考图5-11至图5-14。
关于翅片管和钉头管的外膜传热系数的计算。
Gardener提出了翅片效率的概念,及各种不同类型的翅片管和钉头管翅片效率的计算方法。
于是通过和求光管的外膜传热系数相同的方法就可以得到翅片管或钉头管的外膜传热系数。
如以光管外表面为基准,则其关系式如下:图5一10翅片效率公式推导说明图一般采用条形翅片的对流管,烟气的流动方向必须与管束平行,以减少流动阻力。
所以,这种翅片管的表面膜传热系数,可以采用与式(5-13)相似的关系式进行计算,即式中当量直径D e和式(5 - 13)的定义是相同的,只不过在计算自由截面积和传热周边时,必须考虑翅片的具体情况。
2)环形翅片管表面膜传热系数环形翅片管一般多采用圆管和圆形翅片,且烟气流动的方向与管束垂直。
对正三角形排列的管束,Briggs通过实验提出了如下准数方程式:3)钉头管表面膜传热系数钉头管一般采用烟气流动方向与管束垂直的方式,因此钉头管表面膜传热系数,可以使用与式(5-17)或(518)相同的关系式进行计算.只不过将式中的D o改换为D e,即其中当量直径D e和式(5-13)的定义相同。
4)翅片效率Gardner定义翅片效率为翅片单位表面积通过的平均热量与光管单位表面积通过的平均热量之比值,即首先,Gardner作了下述假定:(1)翅片或钉头的传热过程是稳定传热,即传热量和温度分布与时间无关;(2)翅片的材质是均匀的,各向同性,形状对称;(3)翅片本身不存在热源;(4}翅片表面任一点处的热通量与流体和翅片的温度差成正比;(5)翅片的导热系数为常数;(6)整个翅片的表面膜传热系数相等;(7)围绕翅片的流体温度是一样的;(8)翅片根部的温度是一样的;(9)翅片的厚度比高度小得多,因此横过翅片的温度梯度可以忽略不计;(10)通过翅片顶端外缘的热量比通过翅片侧面的热量小得多,可以忽略不计;(11)翅片和管子的联结不存在结合阻力。
翅片换热器计算范文

翅片换热器计算范文
首先,翅片换热器的计算需要确定其传热面积。
传热面积是翅片换热器设计的关键参数,直接影响着传热效果。
传热面积的计算需要根据被换热流体的热负荷、温度差、翅片的几何尺寸等因素进行综合计算。
一般而言,传热面积可以通过以下公式计算:
A=Q/(UxΔTm)
其中,A代表传热面积,Q代表热负荷,U代表传热系数,ΔTm代表热负荷平均温差。
传热面积的选择要根据应用情况进行合理的调整,以满足热负荷需求。
其次,翅片换热器的传热系数需要进行估算。
传热系数是翅片换热器设计中的另一个重要参考参数,它反映了翅片换热器传热效果的好坏。
传热系数的计算需要考虑多个因素,包括流体的物性、流速、壁面特性等。
一般而言,传热系数可以通过以下公式进行估算:
1/U = 1/hi + Δx / λ + 1/ho
其中,U代表传热系数,hi代表内部传热系数,ho代表外部传热系数,Δx代表翅片厚度,λ代表翅片材料的导热系数。
最后,翅片换热器的传热效率需要进行评估。
传热效率是翅片换热器传热性能的重要指标,它可以通过以下公式进行计算:
ε=(Tc-Th)/(Tm-Th)
其中,ε代表传热效率,Tc代表被换流体的出口温度,Th代表被换流体的入口温度,Tm代表热媒的平均温度。
传热效率的计算结果应该大于0.8,以保证换热效果的良好。
综上所述,翅片换热器的计算涉及到传热面积、传热系数和传热效率的确定。
通过合理的计算,可以为翅片换热器的设计与选择提供有效的依据,保证其换热效果的高效与稳定。
螺旋翅片管的换热计算

研究对象 ,其导热微分方程为 :
55r′(
′
r
55rt′)
+
55<′(
1 r′
55<t′)
+
r′λq
=
0
(1)
ne
∫∫Rm2 Td <d R = sw
0. 5 m2p TP ( Rn + Rs ) ΔRΔ<
(6)
式中 , q 为肋片上 、下表面换热量的折算内热源 。
整理得 :
2h(t -
q=
δ
tf )
en
∫∫5 5R
(
R
5 5
T) R
d
Rd
<
=
[
Rn ( TN (δR)
n
TP )
-
ws
Rs ( TP (δR)
s
TS )
]Δ<
(4)
ne
∫∫5 5<
(
1 R
5 5
<T)
d
<d
R
=
[
TE Re
- TP (δ<) e
-
sw
TP - TW Rw (δ<) W
]ΔR
(5)
图 1 hk 区域平均表面传热系数分布图
=
r′2 ,
T=
T2 ( <′)
<′
=
0
,55
T
<′
=
0
<′=
π,
5T 5 <′
=
0
(3)
式中各系数的计算式如下 :
aE
=
ΔR Re (δ<) e
- 1、下载文档前请自行甄别文档内容的完整性,平台不提供额外的编辑、内容补充、找答案等附加服务。
- 2、"仅部分预览"的文档,不可在线预览部分如存在完整性等问题,可反馈申请退款(可完整预览的文档不适用该条件!)。
- 3、如文档侵犯您的权益,请联系客服反馈,我们会尽快为您处理(人工客服工作时间:9:00-18:30)。
整体型螺旋翅片管省煤器对流传热系数的计算
介绍了整体型螺旋翅片管的优势,阐述了适用于整体型螺旋翅片管对流传热系数计算的相关公式并根据实际运行参数反推此数据,可直接应用于工程实际。
标签:整体型螺旋翅片管;对流传热系数;计算公式
引言
整体型螺旋翅片管作为锅炉承压元件,因其具有比光管、高频焊接翅片管、H型翅片管更高的耐磨性能,更好的抗积灰性能和更高的传热效率,而越来越多地应用于磨损积灰较严重的锅炉省煤器、余热锅炉蒸发器,以及要求更高传热效率及受热面布置更为紧凑的场合。
然而,在锅炉热力计算时,对整体型螺旋翅片管的对流传热系数,尚没有一个准确、公认的计算方法。
文章按照我国通用的原苏联锅炉机组热力计算标准方法,结合最新实验成果,以省煤器工程应用实例为引,给出整体型螺旋翅片管对流传热系数的计算公式和方法。
1 整体型螺旋翅片管省煤器对流传热系数的计算方法
2 工程实例
一般省煤器设计计算的大体步骤可按以下步骤进行:
(2)按工质侧热平衡式求出工质出口焓及温度。
(3)根据烟气和工质的进出口温度和烟道尺寸情况大致布置受热面,可得出工质及烟气的平均温度?驻T、温压、烟气及工质的流速及受热面积H等。
(4)确定省煤器受热面的传热系数K。
我公司改造的某75t/h循环流化床锅炉省煤器改造,拟选用图2所示规格的整体型翅片管,按上述步骤计算所得的省煤器布置型式为:采用错列管束布置,横向17排,节距122mm,纵向12排,节距75mm,管子受烟气横向冲刷面积1619.9m2,烟气流速ω约7.79m/s。
3 结束语
整体轧制成型的螺旋翅片管是一项先进的制管工艺技术,目前国家尚未制定统一的生产制造标准,河南省赛福尔科技有限公司生产的整体型翅片管和制定的相应企业标准(Q/HSF001-2007《高压锅炉用整体型螺旋翅片钢管》,Q/HSF002-2007《低中压锅炉用整体型螺旋翅片钢管》),已经通过国家多个相关机构的全面技术测试和评定,达到或超过国家锅炉行业用钢管标准的相关规定,随着这种管子陆续在一些循环流化床锅炉及余热锅炉的省煤器上的应用,正逐渐被众多用户所认可,其具备的“高效、节能、经济、不易积灰、耐磨损、使用寿命长、环境适应能力强”等优点,使其尤其能广泛应用于燃用劣质燃料的循环流
化床锅炉和磨损积灰严重的余热锅炉,并且经济效益显著,可以作为作为光管及焊接式螺旋翅片管省煤器的更新换代产品。
参考文献
[1]史月涛,等.螺旋翅片管防磨和防積灰特性的试验研究[J].动力工程,2006(1).
[2]林宗虎,徐通模.实用锅炉手册(第二版)[M].北京:化学工业出版社,2009.
[3]卓宁,等.整体型螺旋翅片管束灰污系数的试验研究[J].动力工程,1997(4).
[4]锅炉机组热力计算标准方法[M].北京:机械工业出版社,1976.
作者简介:马慧敏(1986-),男,工学学士,从事锅炉压力容器及结构件的开发和设计。