炼钢精炼连铸过程钢水74页PPT
合集下载
连续铸钢PPT课件

1.1钢包及其操作 一、钢包的作用及功能
钢包除具有盛装、
运载、精炼、浇
注钢水等功能外,
还具有倾翻、倒
渣和落地放置的
功能。
.
40
1.1钢包及其操作
二、钢包容量的确定
钢包的容量应与炼钢炉的最
大出钢量相匹配。
三、钢包形状的确定
1、钢包的直径和高度之比
2、锥度
3、钢包外形
.
41
.
42
四、钢包的结构
1、钢包本体
• 缺点:设备高,钢水静压力大,设备较笨 重,基建费用高
.
20
.
21
.
22
4、各种连铸机的特点
(2)立弯式连铸机(过渡机型)
• 特点:适用于浇注断面较小的铸坯
• 优点:具有立式连铸机垂直浇注和凝固的 特点,高度是立式的四分之三,水平出坯, 铸坯定尺长度不受限制,铸坯的运送也较 方便。
• 缺点:铸坯在顶弯和矫直点内部应力较大, 当铸坯变形率超过允许限度时容易产生内 部裂纹。
64.1%
铸坯质量设计和控制、不精整轧制、热送、直轧、 薄板坯(带)连铸
近终形连铸
高效连铸——高质量;高产量;.高效益;高可靠性;高机械化、自动12 化
连铸发展现状
⑴在世界范围内连铸比每年4%的速度增长
⑵生产高质量连铸坯的技术和体制已经确立
⑶逐步实现连铸坯热送和直接轧制(降低能耗、缩短生产周期)
⑷薄板坯(带)连铸正在兴起
在浇注过程中克服铸坯与结晶器及二冷区的阻力,顺利地将铸坯拉出, 并对弧形铸坯进行矫直。 ⑻引锭装置:“活底”,引锭头+引锭杆 ⑼切割装置:定尺长度 ⑽铸坯运出装置:辊道、推钢机、冷床
.
16
炼钢-精炼-连铸工艺简介(PPT 40页)
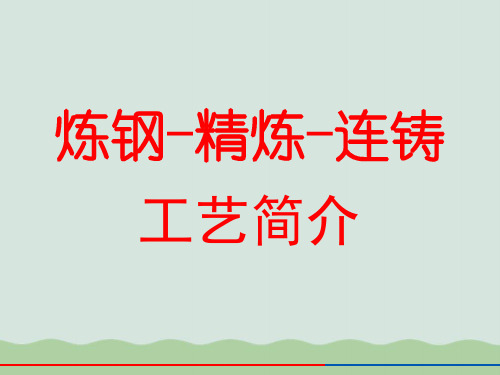
LF的基本功能
1、脱硫:利用造碱性还原渣和电弧的高温区进行脱硫 2、加热:采用电极放电加热钢水 3、合金化:成份微调 4、均匀钢液和去除夹杂:采用底吹Ar气搅拌钢液 5、生产组织中的缓冲:平衡转炉和铸机之间的供钢节奏。
喂线工艺
在RH-KTB工位和LF工位都设有 喂线装置,线的种类为Ca-Si 线和Ca-Al线。
•
1、有事业的峰峦上,有汗水的溪流飞 淌;在 智慧的 珍珠里 ,有勤 奋的心 血闪光 。
•
2、人们走过的每一个足迹,都是自己 生命的 留言; 留给今 天翻过 的日历 ,留给 未来永 久的历 史。
•
3、人生是一座可以采掘开拓的金矿, 但总是 因为人 们的勤 奋程度 不同, 给予人 们的回 报也不 相同。
出钢温度可由下式计算:
T出=T凝+△t1+△t2+△t3+△t4+△t5+α 式中:△t1—出钢过程温降,℃
△t2—出钢完毕至精炼开始的温降,℃ △t3—钢水精炼过程温降,℃ △t4—钢水精炼完毕至开浇前的温降,℃ △t5—钢水从钢包至中间包的温降,℃
α—连铸要求的钢水过热度,℃
终点控制
钢水达到钢种成分和温度要求的时刻,称之为“终点”。 1)钢中碳含量达到所炼钢种控制要求; 2)钢中P、S含量低于规格以下的一定范围; 3)出钢温度能保证进行精炼和浇铸; 4)对于沸腾钢,钢水应具有一定的氧化性。
连铸工艺示意图
连铸工艺的优点
• 简化工艺流程,提高生产效率
连铸省掉了脱模、整模、钢锭均热和开坯等工序。
• 提高金属收得率
连铸的切头、切尾损失为1%-2%,可提高金属收得率10%-14%。
• 降低能耗
由于提高了成坯率,省掉均热、开坯等能耗。
炼钢精炼连铸过程钢水PPT课件
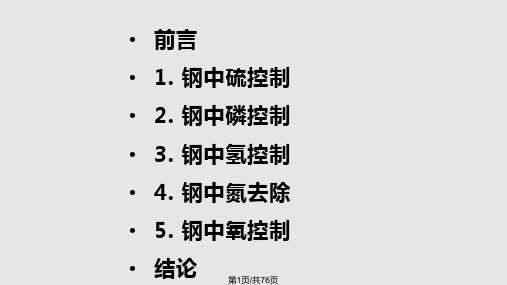
渣洗脱硫
43
18
58
46
钢包脱硫
54
21
61
44
喷吹脱硫
76
20
74
58
真空室脱硫 72
7
90
27
由于在真空条件下增加从底部向顶部气泡 膨 胀扩大了熔池的搅拌功,熔池的搅拌功(B)比大气 压下熔池搅拌大26~46倍,提高脱硫效率。
第16页/共76页
2. 钢中磷
高炉冶炼是不能脱磷的,矿石、焦碳、石 灰中磷几乎全部进入了生铁。铁水中磷含量一 般在0.1~0.2%,炼钢的任务就是通过造渣把[P] 去除到在规定范围内:
带入钢水的[S]为14ppm;石灰中S=0.065%,
带入钢水中的[S]为26ppm。出钢时钢水中[S]
来源是:
废钢+生铁/% 铁水/% 矿石+造渣剂/%
低S石灰(0.035%)
26
37
37
高S石灰(0.065%)
21
32
47
可见,对于转炉冶炼超低硫钢,使用高质量含 硫低的石灰、废钢和造渣剂,防止转炉回硫是非常 重要的。
第7页/共76页
d[%S ] dt
Ks
A V
([%S
]t
(%S ) t Ls
)
将上式积分可得到脱硫效率R:
R [%S]开 [%S]终 1 exp[B (1 1/ )]
[% S ]终
11/
第8页/共76页
1.4 脱硫操作
(1)铁水脱硫
脱硫方法有鱼雷罐喷吹、铁水罐喷吹和KR法等, 脱硫效果如表所示。由表可知,铁水罐喷吹脱硫可 使入转炉铁水[S]达到10ppm,而鱼雷罐则为 20ppm。可见,防止脱硫渣回硫是非常重要的。
钢铁冶炼过程.完整PPT资料

Carbon Steel
Carb✓on它Ste们el 各自的作用的是什么?
Carbon Steel
6 to✓n of炼ox铁yge是n a在re c什ons么um设ed备per里ton进of行co的al in?jected. 此 Ca外rb✓o,n炼轧Ste钢铁el每需吨要钢耗什氧么3~样6m的3、条钢材件加?工、连铸坯火焰切割,火焰清除、炉衬火焰每吨钢耗氧11. 怎样✓提焦高炼炭铁是过怎程中么的制能成源效的率??
(4)炼铁的主要反应过程:
空分✓设怎备主样要提是高为冶炼炼铁工过艺过程程中提的供工能业源气效体。率? ✓ 炼铁过程中的环保问题 ✓ 炼铁过程中的“休风”,“封炉”,“难行”,“悬料”,“崩料”?
炼铁原料:铁矿石,焦炭,石灰石:
高炉构造:
炼铁:
3CO+Fe2O3 =2Fe+3CO2
CO2+C=2CO C+O2=CO2
Some useful approximations are:
✓ 0.5 to 0.6 ton of oxygen are consumed per ton of coal injected. ✓ At high coal injection rates 100 Nm3 or 150kg of oxygen are consumed per ton of hot metal. ✓ A large 10,000 TPD blast furnace utilising max. coal injection rates will result in an oxygen demand of 1400 to 1500 TPD O2.
铁的合金 含碳的质量分数 杂质
机械加工 机械性能
生铁 2~4.3% 硅锰(较多) 硫磷(较多) 可铸不可锻 硬而脆
Carb✓on它Ste们el 各自的作用的是什么?
Carbon Steel
6 to✓n of炼ox铁yge是n a在re c什ons么um设ed备per里ton进of行co的al in?jected. 此 Ca外rb✓o,n炼轧Ste钢铁el每需吨要钢耗什氧么3~样6m的3、条钢材件加?工、连铸坯火焰切割,火焰清除、炉衬火焰每吨钢耗氧11. 怎样✓提焦高炼炭铁是过怎程中么的制能成源效的率??
(4)炼铁的主要反应过程:
空分✓设怎备主样要提是高为冶炼炼铁工过艺过程程中提的供工能业源气效体。率? ✓ 炼铁过程中的环保问题 ✓ 炼铁过程中的“休风”,“封炉”,“难行”,“悬料”,“崩料”?
炼铁原料:铁矿石,焦炭,石灰石:
高炉构造:
炼铁:
3CO+Fe2O3 =2Fe+3CO2
CO2+C=2CO C+O2=CO2
Some useful approximations are:
✓ 0.5 to 0.6 ton of oxygen are consumed per ton of coal injected. ✓ At high coal injection rates 100 Nm3 or 150kg of oxygen are consumed per ton of hot metal. ✓ A large 10,000 TPD blast furnace utilising max. coal injection rates will result in an oxygen demand of 1400 to 1500 TPD O2.
铁的合金 含碳的质量分数 杂质
机械加工 机械性能
生铁 2~4.3% 硅锰(较多) 硫磷(较多) 可铸不可锻 硬而脆
(四)连铸工艺与操作课件.ppt

精品
三、连铸生产工艺
上引锭杆 开浇 启车拉矫 脱引锭杆 切割 钢包更换 中间包更换
精品
停车
1.上引锭杆
油缸驱动→引 锭杆放到中间轨道→ 送入拉矫机引锭杆经 二冷段→入结晶器上 100-150mm→ 反 向 至结晶器下口 150mm 处 → 拉 矫 机 引锭杆夹紧定位→完 成安装操作.
精品
2.开 浇
连铸连轧新技术
第二讲 连铸工艺与操作
精品
主要内容
一、概 述 二、生产模拟 三、生产工艺 四、连铸设备 五、工艺参数
精品
一、概 述 1.连铸的发展概况 2.连铸机的特点 3.连铸机的机型
精品
1.连铸的发展概况
连续铸钢(连铸)是将钢水通过连铸机直接铸成钢坯 ,从而取代模铸和初轧开坯的一种钢铁生产先进 工艺。世界各国都以连铸比(连铸坯产量占钢总产 量比例)的高低来衡量钢铁工业生产结构优化的程 度和技术水平的高低。连铸的好处在于节能和提 高金属收得率。
精品
弧型连铸机:
设备高度明显下降,能够 适应提高拉速和加大断面的要 求
又分为:
直弧型连铸机:
采用直结晶器从结晶器下 保留2m直线段,然后为弧型段, 铸坯由直变弯,最后通过拉矫机 将弧形坯矫直; 优点:夹杂物易上浮,且比立弯式 高度低;
全弧型连铸机:
铸坯的运动轨迹是一条弧 线.结晶器,二冷段全为弧型,拉 矫机、切割机和出坯系统布置 在水平线上.
连轧为代 表,钢厂向紧凑化发展。
精品
2、 21世纪钢铁工业发展趋势
(1) 产品更加纯洁化 (2) 生产工艺更加高效低耗 (3) 生产过程对环境更加友好
精品
•
连铸液体金属是19世纪提出的。最初只能用
于浇铸低熔点的有色金属。1933年现代连铸之父
三、连铸生产工艺
上引锭杆 开浇 启车拉矫 脱引锭杆 切割 钢包更换 中间包更换
精品
停车
1.上引锭杆
油缸驱动→引 锭杆放到中间轨道→ 送入拉矫机引锭杆经 二冷段→入结晶器上 100-150mm→ 反 向 至结晶器下口 150mm 处 → 拉 矫 机 引锭杆夹紧定位→完 成安装操作.
精品
2.开 浇
连铸连轧新技术
第二讲 连铸工艺与操作
精品
主要内容
一、概 述 二、生产模拟 三、生产工艺 四、连铸设备 五、工艺参数
精品
一、概 述 1.连铸的发展概况 2.连铸机的特点 3.连铸机的机型
精品
1.连铸的发展概况
连续铸钢(连铸)是将钢水通过连铸机直接铸成钢坯 ,从而取代模铸和初轧开坯的一种钢铁生产先进 工艺。世界各国都以连铸比(连铸坯产量占钢总产 量比例)的高低来衡量钢铁工业生产结构优化的程 度和技术水平的高低。连铸的好处在于节能和提 高金属收得率。
精品
弧型连铸机:
设备高度明显下降,能够 适应提高拉速和加大断面的要 求
又分为:
直弧型连铸机:
采用直结晶器从结晶器下 保留2m直线段,然后为弧型段, 铸坯由直变弯,最后通过拉矫机 将弧形坯矫直; 优点:夹杂物易上浮,且比立弯式 高度低;
全弧型连铸机:
铸坯的运动轨迹是一条弧 线.结晶器,二冷段全为弧型,拉 矫机、切割机和出坯系统布置 在水平线上.
连轧为代 表,钢厂向紧凑化发展。
精品
2、 21世纪钢铁工业发展趋势
(1) 产品更加纯洁化 (2) 生产工艺更加高效低耗 (3) 生产过程对环境更加友好
精品
•
连铸液体金属是19世纪提出的。最初只能用
于浇铸低熔点的有色金属。1933年现代连铸之父
连铸工艺与设备74页

连铸工艺与设备 2. 连铸的工艺流程与设备
1/74
2.1 连铸机的工艺流程
由炼钢炉炼出的合格钢水经炉外精炼处理后,用钢 包运送到浇铸位置注入中间包,通过中间包注入强 制水冷的铜模—结晶器内。
结晶器是无底的,在注入钢水之前。必须先装上一 个“活底”,它同时也起到引出铸锭的作用,这个 “活底”就称为引锭杆。注入结晶器的钢水在迅速 冷却凝固成形的同时,其前部与伸入结晶器底部的 引锭杆头部凝结在一起。引锭杆的尾部则夹持在拉 坯机的拉辊中,当结晶器内钢水升到要求的高度后, 开动拉坯机,以一定的速度把引锭杆(牵着铸坯)从结 晶器中拉出。
15
2.2.1 钢包回转台
➢功能 钢包回转台将从精炼跨接受的钢包回转到浇注跨, 为连铸机提供钢水,实现多炉连浇,提高连铸机作 业率。 ➢ 位置 位于浇铸平台的混凝土基础上。
16
2.2.2 中间包
➢中间包是短流程炼钢中用到的一个耐火材料容器, 首先接受从钢包浇下来的钢水,然后再由中间包水 口分配到各个结晶器中去。 ➢中间包是连铸机钢水包和结晶器之间钢水过渡的 装置,用来稳定钢流,减小钢流对坯壳的冲刷,以 利于非金属夹杂物上浮,从而提高铸坯质量。通常 认为中间包起以下作用: 1) 分流作用。对于多流连铸机,由多水口中间包对 钢液进行分流。
9
钢包回转台
10
钢包回转台
11
2.2.1 钢包回转台
➢钢包升降有电机驱动和液压驱动两种形式,升降 行程0.6~lm,升降速度0.5~2m/min。 ➢回转固定装置的作用是保证钢包在浇注时有准确 定位,并不致在外力冲击下产生位移。 ➢由于偏载和回转造成巨大的倾翻力矩,通过地脚 螺栓传递到基础上,因此必须高度重视地脚螺栓的 设计。通常将地脚螺栓和锚固框架组成一个整体结 构,以抵抗强大的倾翻力矩。为使地脚螺栓在变载 荷下不致于松动,可使用预应力高强度螺栓。
1/74
2.1 连铸机的工艺流程
由炼钢炉炼出的合格钢水经炉外精炼处理后,用钢 包运送到浇铸位置注入中间包,通过中间包注入强 制水冷的铜模—结晶器内。
结晶器是无底的,在注入钢水之前。必须先装上一 个“活底”,它同时也起到引出铸锭的作用,这个 “活底”就称为引锭杆。注入结晶器的钢水在迅速 冷却凝固成形的同时,其前部与伸入结晶器底部的 引锭杆头部凝结在一起。引锭杆的尾部则夹持在拉 坯机的拉辊中,当结晶器内钢水升到要求的高度后, 开动拉坯机,以一定的速度把引锭杆(牵着铸坯)从结 晶器中拉出。
15
2.2.1 钢包回转台
➢功能 钢包回转台将从精炼跨接受的钢包回转到浇注跨, 为连铸机提供钢水,实现多炉连浇,提高连铸机作 业率。 ➢ 位置 位于浇铸平台的混凝土基础上。
16
2.2.2 中间包
➢中间包是短流程炼钢中用到的一个耐火材料容器, 首先接受从钢包浇下来的钢水,然后再由中间包水 口分配到各个结晶器中去。 ➢中间包是连铸机钢水包和结晶器之间钢水过渡的 装置,用来稳定钢流,减小钢流对坯壳的冲刷,以 利于非金属夹杂物上浮,从而提高铸坯质量。通常 认为中间包起以下作用: 1) 分流作用。对于多流连铸机,由多水口中间包对 钢液进行分流。
9
钢包回转台
10
钢包回转台
11
2.2.1 钢包回转台
➢钢包升降有电机驱动和液压驱动两种形式,升降 行程0.6~lm,升降速度0.5~2m/min。 ➢回转固定装置的作用是保证钢包在浇注时有准确 定位,并不致在外力冲击下产生位移。 ➢由于偏载和回转造成巨大的倾翻力矩,通过地脚 螺栓传递到基础上,因此必须高度重视地脚螺栓的 设计。通常将地脚螺栓和锚固框架组成一个整体结 构,以抵抗强大的倾翻力矩。为使地脚螺栓在变载 荷下不致于松动,可使用预应力高强度螺栓。
炼钢连铸工艺知识讲座(PPT 149页)

5
炼钢、方坯连铸工艺断面图
6
目前二期工程已全面启动,预计2006年四季度竣工投产。 二期建设完成后,炼钢主要装备有:
• 三座210t转炉,全部采用副枪及计算机炼钢、顶底复合吹炼、挡渣出钢。 • 三套铁水脱硫扒渣设施,铁水实现100%脱硫处理。 • 炉外精炼:
(1) 一座吹氩站 (2) 一座CAS-OB钢水精炼站 (3) 一座双工位电极旋转式LF钢包精炼炉(带钢包喷粉) (4) 一座带顶吹氧RH真空精炼设施(预留一座) • 两台不同断面的双流板坯连铸机,一台断面900—1600mm、另一台1100— 2150mm。厚度230、250mm(以230mm为主),长度8000—10500mm,最大单重 38.5t • 两台方坯连铸机 • 两座500立方米活性石灰套筒窑
工业用气
氧气、氩气,制氧厂提供。
30
铁合金供应
铁合金贮料间 铁合金高位料仓供应方式
(适用于大型转炉车间)
31
散状料供应
散状原料间的地下料仓贮料量一般按3-10天考虑,白 灰定存量应控制在1-2天内。地下料仓深处应考虑设有 排水设施,散状料输送和加入系统应设置除尘设施。
散状料高位料仓布置。
[Mn]+[O]=(MnO)
[Si]+2(FeO)=(SiO2)+2[Fe] [Mn]+(FeO)=(MnO)+[Fe]
脱磷反应
脱硫反应
19
2[P]+ 5(FeO)+4(CaO)=(4 CaO.P2O5)+5[Fe]
(CaO)+[ FeS]= (CaS)+(FeO)
2、铁水脱硫处理
• 铁水脱硫的必要性
32
散状料上料系统
炼钢、方坯连铸工艺断面图
6
目前二期工程已全面启动,预计2006年四季度竣工投产。 二期建设完成后,炼钢主要装备有:
• 三座210t转炉,全部采用副枪及计算机炼钢、顶底复合吹炼、挡渣出钢。 • 三套铁水脱硫扒渣设施,铁水实现100%脱硫处理。 • 炉外精炼:
(1) 一座吹氩站 (2) 一座CAS-OB钢水精炼站 (3) 一座双工位电极旋转式LF钢包精炼炉(带钢包喷粉) (4) 一座带顶吹氧RH真空精炼设施(预留一座) • 两台不同断面的双流板坯连铸机,一台断面900—1600mm、另一台1100— 2150mm。厚度230、250mm(以230mm为主),长度8000—10500mm,最大单重 38.5t • 两台方坯连铸机 • 两座500立方米活性石灰套筒窑
工业用气
氧气、氩气,制氧厂提供。
30
铁合金供应
铁合金贮料间 铁合金高位料仓供应方式
(适用于大型转炉车间)
31
散状料供应
散状原料间的地下料仓贮料量一般按3-10天考虑,白 灰定存量应控制在1-2天内。地下料仓深处应考虑设有 排水设施,散状料输送和加入系统应设置除尘设施。
散状料高位料仓布置。
[Mn]+[O]=(MnO)
[Si]+2(FeO)=(SiO2)+2[Fe] [Mn]+(FeO)=(MnO)+[Fe]
脱磷反应
脱硫反应
19
2[P]+ 5(FeO)+4(CaO)=(4 CaO.P2O5)+5[Fe]
(CaO)+[ FeS]= (CaS)+(FeO)
2、铁水脱硫处理
• 铁水脱硫的必要性
32
散状料上料系统
炼钢及连铸工艺课件

氧气是转炉炼钢的主要氧化剂,其纯度达到或超过99.5%,氧 气压力要稳定,并脱除水分。 铁矿石中铁的氧化物存在形式是Fe2O3、Fe3O4和FeO其氧含量分 别是30.06%,27.64%和22.28%。在炼钢温度下,Fe2O3不稳 定,在转炉中较少使用。铁矿石作为氧化剂使用要求高 (全铁>56%),杂质量少,块度合适。 氧化铁亦称铁磷,是钢坯加热,轧制和连铸过程中产生的氧 化壳层,铁量约占70%-75%。氧化铁皮还有助于化渣和冷却 作用,使用时应加热烘烤,保持干燥。
高碱度烧结矿或球团矿也可做合成造渣剂 使用,其化学成分和物理性能稳定,造渣效果 良好。
在冶炼过程中,由于配料或装料不当以及脱碳过 量等原因,有时造成钢中碳含量没有达到预期的要求, 这时要向钢液中增碳。常用的增碳剂有增碳生铁、电极 粉、石油焦粉、木炭粉和焦炭粉。
转炉冶炼中,高碳钢种时,使用含杂质很少的石油 焦作为增碳剂。对顶吹转炉炼钢用增碳剂的要求是固定 碳要高,灰分,挥发分和硫,磷,氮等杂质含量要低, 且干燥,干净,粒度适中。其固定碳C≥96%,挥发分 ≤1.0%,S≤0.5%,水分≤0.5%,粒度在1-5mm。
国内一些企业顶吹转炉的炉容比
厂名 宝钢 首钢 鞍钢 本钢 攀钢 首钢 太钢
吨位/t
300
210
180
120
120
80
50
炉熔比/m3·-1 1.05 0.97 0.86 0.91 0.90 0.84 0.97 t
供氧制度的主要内容包括确定合理的喷头 结构、供氧强度、氧压和枪位控制。供氧是保 证杂质去除速度、熔池升温速度、造渣制度、
控制喷溅去除钢中气体与夹杂物的关键操作,
关系到终点的控制和炉衬的寿命,对一炉钢冶 炼的技术经济指标产生重要影响。
连铸工艺与操作

•结 •晶 •器 •及 •振 •动 •台
•电 •磁 •搅 •拌 •设 •备
•二 •冷 •段
•拉 •引 •锭
•矫 •装
•机 •置
•切 •割 •机
PPT文档演模板
连铸工艺与操作
1.钢包及回转台
钢包又称盛钢桶、 钢水包、大包等; 它是用于盛装、运 载钢液并进行浇注 的设备,也是钢液 炉外精炼的容器。
PPT文档演模板
高度比立式下降, 但由于增加了一次弯 曲和矫直,易造成裂 纹。
PPT:
设备高度明显下降,能够 适应提高拉速和加大断面的要 求 又分为:
直弧型连铸机:
采用直结晶器从结晶器下 保留2m直线段,然后为弧型段, 铸坯由直变弯,最后通过拉矫机 将弧形坯矫直; 优点:夹杂物易上浮,且比立弯式 高度低;
实际生产中需采取在钢包内调整钢水温度的措施: 1)钢包吹氩调温 2)加废钢调温 3)在钢包中加热钢水技术 4)钢水包的保温
PPT文档演模板
连铸工艺与操作
3.连铸机的机型
立式连铸机: 钢水从结晶器内开始
凝固到铸坯完全凝固后切 成定尺,铸坯始终沿直线 运动,中间包、结晶器、 导辊、拉坯辊和切割机都 沿直线布置。 优 点:
PPT文档演模板
连铸工艺与操作
2、 21世纪钢铁工业发展趋势
(1) 产品更加纯洁化 (2) 生产工艺更加高效低耗 (3) 生产过程对环境更加友好
PPT文档演模板
连铸工艺与操作
•
连铸液体金属是19世纪提出的。最初只能用
于浇铸低熔点的有色金属。1933年现代连铸之父
容汉斯提出连铸振动系统,1943年建成第一台实
连铸工艺与操作
二、生产模拟
PPT文档演模板
•连铸工位全景
炼钢-连铸工艺介绍 ppt课件
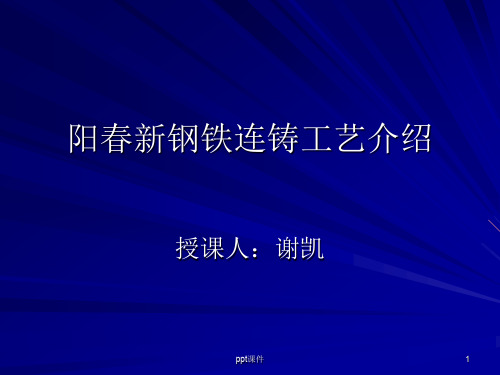
7.拉矫机:它的作用是拉坯、矫直、送引锭。
8.引锭存放装置:它的作用是存放引锭杆。
ppt课件
4
9.火焰切割装置:它的作用是把铸坯安照要 求切割成规定的尺寸。
10.辊道:它的作用是支撑、输送钢坯。
11.冷床:它的作用是冷却、贮存钢坯。
12.推钢机:它的作用是负责把钢坯集的主要工艺参数
ppt课件
8
连铸工艺过程主要控制系统的简要 说明
1.结晶器液面控制系统
结晶器液面控制通过放射性同位素传感 器测得液面信号,控制中间罐的塞棒移动, 必要时也调节拉坯速度,以稳定钢水液面。 在自动开浇过程中,结晶器液面控制将按 照一个储存的时间斜率进行控制,在正常 浇铸过程中,按PI控制规律实现闭环自动控 制,可以有效的提高铸坯质量。
2.2.2:浸入式水口 钢水与熔融石英水口会发生反应,生成MnO.Sio2, 熔点为1200℃左右,水口被侵蚀,生成物成为外来 夹杂物。因此,浇注高「 Mn 」和含「Al」的钢时, 必须使用铝锆碳质水口。
2.2.3:浇注过程中下渣、卷渣 2.3:铸坯中的夹杂物:外来夹杂物(钢包下渣+卷 渣)41%;二次氧化39%;脱氧产物20%。 2.4:从来源上说,钢中夹杂物可分为三类: 2.4.1:没有上浮的脱氧产物。 2.4.2:浇注过程中生成的二次氧化产物。 2.4.3:凝固过程中形成的夹杂物。
ppt课件
13
C类:(硅酸盐)延性好,形态比较大 (大于3),呈黑色或灰色,一般端角呈锐 角;
D类:(球状氧化物)不变形,带菱角或圆 形,形态比较小(小于3),无规则分布, 呈黑色或蓝色;
Ds类:(单颗粒球状)夹杂物呈圆形或近 似球形,是直径大于13µm的单颗粒夹杂物。
⑵金相显微镜观察法
8.引锭存放装置:它的作用是存放引锭杆。
ppt课件
4
9.火焰切割装置:它的作用是把铸坯安照要 求切割成规定的尺寸。
10.辊道:它的作用是支撑、输送钢坯。
11.冷床:它的作用是冷却、贮存钢坯。
12.推钢机:它的作用是负责把钢坯集的主要工艺参数
ppt课件
8
连铸工艺过程主要控制系统的简要 说明
1.结晶器液面控制系统
结晶器液面控制通过放射性同位素传感 器测得液面信号,控制中间罐的塞棒移动, 必要时也调节拉坯速度,以稳定钢水液面。 在自动开浇过程中,结晶器液面控制将按 照一个储存的时间斜率进行控制,在正常 浇铸过程中,按PI控制规律实现闭环自动控 制,可以有效的提高铸坯质量。
2.2.2:浸入式水口 钢水与熔融石英水口会发生反应,生成MnO.Sio2, 熔点为1200℃左右,水口被侵蚀,生成物成为外来 夹杂物。因此,浇注高「 Mn 」和含「Al」的钢时, 必须使用铝锆碳质水口。
2.2.3:浇注过程中下渣、卷渣 2.3:铸坯中的夹杂物:外来夹杂物(钢包下渣+卷 渣)41%;二次氧化39%;脱氧产物20%。 2.4:从来源上说,钢中夹杂物可分为三类: 2.4.1:没有上浮的脱氧产物。 2.4.2:浇注过程中生成的二次氧化产物。 2.4.3:凝固过程中形成的夹杂物。
ppt课件
13
C类:(硅酸盐)延性好,形态比较大 (大于3),呈黑色或灰色,一般端角呈锐 角;
D类:(球状氧化物)不变形,带菱角或圆 形,形态比较小(小于3),无规则分布, 呈黑色或蓝色;
Ds类:(单颗粒球状)夹杂物呈圆形或近 似球形,是直径大于13µm的单颗粒夹杂物。
⑵金相显微镜观察法
连铸连轧工艺精品PPT课件
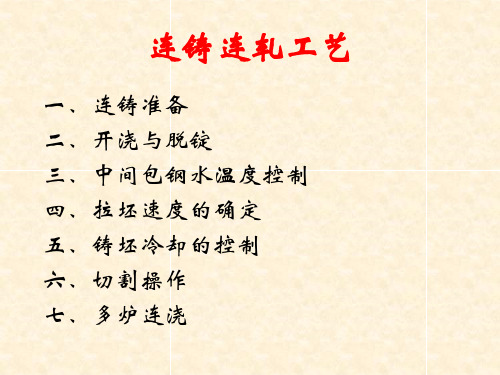
• 上引锭杆:通过引锭杆小车将其运输到浇注位 置,完全装入结晶器内。
• 中间包烘烤:中间包温度太低会导致钢水降温 过大,易造成中间包不能正常开浇,应预热到 1100℃左右。 三种预热时间—180min,120min, 90min。
2.1 开 浇 2.2 脱 锭
3 中间包钢水温度的控制
3.1 浇铸温度的确定 (浇铸温度也称目标浇铸温度): T浇=TL+△T
延伸率与Mn/S比的关系
1.1.2 浇铸温度
• 定义:指中间包内的钢水温度,也可指钢水进入 结晶器时的温度。
通常一炉钢水需在中间包内测温3次,即开浇 后5min、浇铸中期和浇铸结束前5min,而这3次 温度的平均值被视为平均浇铸温度。
• 要求: 在尽可能高的拉速下,保证铸坯出结晶器时形成
足够厚度的坯壳,从而保证连铸过程安全进行; 在结晶器内,钢水将热量平稳的传导给铜板,使
• △T4:钢包精炼结束钢水在静置和运往连铸 平台的温降
分析: 热量损失形式:钢水上表面通过渣层的热损失、
钢包包衬吸热。 热量损失大小:钢包内衬吸热降低,加了保温
剂,温降减小低。
• △T5:钢水从钢包注入中间包过程中产生的温降
分析: 热量损失形式:辐射热损失、对流热损失、钢包吸热。 影响因素:钢流保护状况;中间包的容量、材质、
1.1.1 钢水的成分 • 钢水中元素的分类:
合金元素—有意加入钢中,使其达到规定 的成分范围,保证钢的机械性能。
杂质元素—非有意加入钢中,不被希望存在于钢 中,对钢的性能有害。
残余元素—砷As、锑Sb、铜Cu等,对钢的热脆性 和腐蚀性有不良影响。由原材料或耐 火材料带入。
微量元素—硼B、钛Ti等,含量小于0.1%,为改变 某种性能而有意加入。