光学外文文献及翻译
光学中英文 光学书籍_期刊介绍

序号关键词书名作者1成像C语言成像与光线追踪程序设计2成像成像跟踪技术导论杨宜禾,周维真著3成像成像光学王之江,伍树东著4成像成像过程的机理和应用雅各布森(K.I.Jacobeon),中国科学技术情报研究所编5成像出国参观考察报告 第六届光电成像器件会议6成像磁共振成像系统的原理及其应用赵喜平编著7成像共焦显微术的三维成像原理(澳)M.顾(Min Gu)著 王桂8成像光电成像原理邹异松等编著9成像光电子成像器件原理向世明,倪国强编著10成像脑磁共振波谱成像[巴西]LARA A.BRANDAO RO11成像热成像张维力,宋广礼编著12成像随机介质中光的传播与成像张逸新编著13成像微波成像术张直中著14成像微光与红外成像技术张敬贤等编著15成像现代成像系统徐之海,李奇16成像遥感成像原理及图像特征张 庸主编17成像医学成像技术杨国忠编著18成像医学成像技术霍纪文,王秀章主编19成像医学成像系统(美)A.马科夫斯基(Albert20成像医学数字成像技术胡军武主编21辐射电磁波与幅射系统Е.с.约敦22辐射光点幅射韩森林著23辐射光幅射测量原理与技术李振国, 魏 青主编24辐射核幅射测量歇普(J.Sharpe)著 钱景华25辐射红外幅射测量基础周书铨编26辐射研究幅射的电子学方法苏)萨宁(А.А.Санин)著 忻贤李旭主编27光电21世纪高职高专电子信息系列规划教材 光电28光电半导体光电化学(苏)古列维奇(Гуревнч,Ю.Я29光电半导体光电器件田等先编著30光电半导体光电器件及其应用上海无线电十七厂编辑31光电半导体光电器件及其应用上海无线电十七厂32光电半导体光电器件及其应用潘天明编著33光电场助半导体光电阴极理论与实验李晋闽著中国科学技术情报研究所编34光电出国参观考察报告 第六届光电成像器件会议35光电大气中之光电现象(日)国富信一著 沈懋德译36光电电子发射与光电阴极刘元震等编著37光电短程光电测距仪的应用毛能武编38光电短程光电测距仪和激光定位仪及其应用清华大学测量教研组编39光电多碱光电阴极 机理、特性与应用常本康著40光电分子材料 光电功能化合物游效曾著41光电钢中磷的光电比色测定法中国科学院化工冶金研究所42光电高等学校教材 光电材料黄书万编43光电光电、红外、比色温度计原理与检定李吉林等编44光电光电倍增管陈成杰,徐正卜著45光电光电倍增管( )W.哈特曼,( )F.伯恩哈46光电光电比色计和分光光度计方国铭,胡国成编著47光电光电比色计与分光光度计王 洁编著48光电光电测距张坤宜编著49光电光电测距仪(苏)康德拉什科夫(А.В.Кондр50光电光电测距仪实用检测新方法黄伟明著51光电光电测距应用技术毛能武等编著52光电光电测量何照才主编 中国人民解放53光电光电测试技术张广军主编54光电光电测试技术范志刚主编55光电光电测试仪器原理及应用[苏]Л.А.诺维茨基主编56光电光电成象器件及其应用张彤57光电光电成像原理邹异松等编著58光电光电传感器及其应用何勇59光电光电导物理及其应用应根裕编著60光电光电电路赵宏图61光电光电电子线路胡士凌,孔得入编著62光电光电对抗技术李世祥编著63光电光电对抗――信息武器徐起编著64光电光电发射材料 制备、特性与应用美)萨默(A.H.Sommer)著 侯65光电光电功能超薄膜黄春辉66光电光电管与光电倍增管史玖德编著67光电光电惯性技术杨培根等编著68光电光电化学太阳能转换(俄)波利斯科夫(Плесков,Ю69光电光电技术孙培懋,刘正飞编70光电光电技术刘振玉编71光电光电技术缪家鼎等编著72光电光电技术实验刘振玉主编73光电光电技术实用电路精选杨家德主编74光电光电技术与实验江月松75光电光电检测技术雷玉堂等编著76光电光电检测技术高稚允,高 岳编著77光电光电检测技术罗先和编著78光电光电检测技术钱浚霞79光电光电检测控制电路手册赵负图主编80光电光电检测原理及应用 上册秦积荣81光电光电检测原理及应用 下册秦积荣82光电光电检测原理及应用 中册秦积荣83光电光电接口器件手册庞振泰等译84光电光电接收器件及其应用张彤85光电光电精密仪器设计殷纯永86光电光电控制模型敏光编著曲维本,刘铁墉编87光电光电耦合器的原理及其在电子线路中的应用88光电光电器件方如章,刘玉凤编89光电光电器件沈塘和编90光电光电器件概论汤定元等编91光电光电器件和光学成像技术[英]D.A.罗斯92光电光电器件手册刘仁昌93光电光电世界刘建宇, 魏巍主编94光电光电探测技术 [修订版]王清正等编著95光电光电探测技术及应用卢春生编著96光电光电统计理论与技术周仁忠,阎吉祥编著97光电光电图像处理刘文耀等编著98光电光电图像处理竺子民[著]99光电光电微光摄影技术H.V.索尔著 王顺德译100光电光电位移精密测量技术叶盛祥编著101光电光电物理基础姜节俭编102光电光电系统与信号处理叶嘉雄等编著103光电光电显示器件手册(日)奥下博昭等著 庞振泰104光电光电线缆检测技术方建成等主编105光电光电线缆制造技术王家祥主编106光电光电信号检测吴 杰编107光电光电信号检测原理与技术赵远,张宇主编108光电光电信息处理系统 李志能,叶旭?妆嘀?109光电光电信息技术杨永才等编著110光电光电信息转换器苏)普列斯努欣111光电光电仪器质量问题文集中国科学院长春光机所情报112光电光电元器件速查代换大全庄跃辉113光电光电整纬装置何绍东,陈 梁编114光电光电直读光谱分析 (试用本)上海第五钢铁厂研究所115光电光电装置(理论与计算基础) A.B.巴甫洛夫国家科委高技术计划信息领116光电光电子器件与微电子光电子系统集成技术论117光电光电自动器及其应用(苏)克利敏契耶夫著 滕砥118光电光电自准直仪及其应用蔡淑璋, 景芳盛编著119光电国内外半导体光电器件实用手册中国光学、光电子行业协会120光电国内外半导体光电器件实用手册中国光学、光电子行业协会121光电汉英光电技术词汇杨培根122光电红外光电探测器及其材料万欣等编译123光电激光电源电路梁国忠,梁作亮编著124光电激光光电检测吕海宝等编著125光电激光光电仪器设计基础(苏)Ю.М.克利姆科夫著 王诚华译126光电集成光电器件和系统[英]D.A.罗斯127光电集成光电器件和系统(英)诺布尔(P.J.W.Noble)128光电金属陶瓷薄膜及其在光电技术中的应用孙大明,孙兆奇著129光电近代光电工程导论林宸生130光电军用光电系统高稚允等编著131光电实用光电技术李庆祥132光电实用光电控制电路精选陈尔绍等编(美)劳申巴赫(Rauschenba133光电太阳电池阵设计手册 光电能转换原理及其应闵乃本主编134光电探索新晶体 光电功能材料的结构、性能、分135光电微光电视蒋先进编136光电微机在光电技术中的应用辛德胜,申铉国编著137光电现代光电测试技术顾文郁138光电现代光电器件技术及应用宋丰华编著139光电现代空间光电系统及应用宋丰华编著140光电现代空间光电信息处理技术及应用宋丰华编著141光电象管与其它光电器件严增濯主编142光电真空光电器件(苏)别尔可夫斯基著 徐正143光电智能光电系统王永仲等编著144光电中国核科技报告 铀矿地勘测量中光电测距仪吴景勤陈朝晖145光电中国科学院博士学位研究生学位论文 新型无曹亚安146光电中国科学院感光化学研究所博士后研究工作147光谱x光光谱分析之原理与应用何文祥译148光谱X射线光谱分析谢忠信等编著149光谱X射线光谱分析的原理和应用(美)伯廷(E.P.Bertin)著150光谱X射线荧光光谱分析吉昂等编著151光谱玻璃的光学和光谱性质干福熹著辛仁轩编著152光谱等离子体发射光谱分析(原子光谱分析技术153光谱地球资源的多光谱摄影术(美)温德罗斯(S. Wendero154光谱分子光谱 [英文版][美]Jeanne L.McHale[著]155光谱分子光谱与激光钟立晨, 丁海曙著156光谱付里叶变换红外光谱的应用研究荆煦瑛主编157光谱傅里叶变换光谱(法)盖拉维利(Guelachvil尼高力FTIR中国用户协会编158光谱傅立叶变换红外光谱技术及应用研讨会论文159光谱高光谱遥感及其应用浦瑞良,宫鹏著160光谱光电直读光谱分析 (试用本)上海第五钢铁厂研究所161光谱光电子统计学及光谱与光通讯应用(美)塞勒(Saleh,B.)著 韩162光谱光谱导论唐纳德 L. 帕维亚 加里 M163光谱光谱分析(苏)罗蒙诺索娃,Л.С.,(苏)法尔科164光谱光谱分析常识高铮德 刘湘生等编著165光谱光谱分析法实验与习题郭德济主编166光谱光谱分析讲义冶金工业部钢铁研究院分析167光谱光谱光度测量与标准李在清著168光谱光谱仪器(苏)塔拉索夫(К.И.Тарасов169光谱光谱仪器 第二辑上海市仪表电讯工业局技术情报所,第170光谱光谱仪器 第一辑上海市仪表电讯工业局技术情报所,第171光谱光谱仪器设计吴国安著172光谱光谱仪器学林 中,范世福编173光谱光谱仪器原理李全臣,蒋月娟编著174光谱光声光谱法的原理和应用《光谱学与光谱分析》编辑175光谱光声光谱法及其应用(日)泽田嗣郎编 赵贵文等176光谱航天多光谱遥感韩心志编著177光谱红外光谱谢晶曦编著178光谱红外光谱法董庆年编179光谱红外光谱法入门钟海庆编180光谱红外光谱分析与新技术张叔良等编著181光谱红外光谱实用指南荆煦瑛等编著182光谱红外光谱在有机化学和药物化学中的应用谢晶曦, 常俊标, 王绪明编183光谱红外与拉曼光谱的计算原理与计算程序 (上胡皆汉 王国祯编著184光谱红外与拉曼光谱的计算原理与计算程序 (下胡皆汉 王国祯编著185光谱激光光谱分析法朱贵云,杨景和编著186光谱激光光谱分析法朱贵云,杨景和编著187光谱激光光谱技术概况北京光电技术研究所编辑188光谱近代傅里叶变换红外光谱技术及应用(上卷吴瑾光吴瑾光189光谱近代傅里叶变换红外光谱技术及应用(下卷190光谱近红外光谱分析基础与应用严衍禄主编191光谱近红外光谱及其在石油产品分析中的应用冯新泸,史永刚编著192光谱滤波差分法测量软X光谱江少恩,孙可煦[著]193光谱群论与光谱夏上达编著194光谱实用红外光谱解析卢?踩?,邓振华编195光谱无机和配位化合物的红外和拉曼光谱(日)中本一雄著 黄德如,汪196光谱稀土光谱理论张思远, 毕宪章著197光谱现代光谱分析手册万家亮编著198光谱现代近红外光谱分析技术陆婉珍等编著199光谱旋光谱和圆二色光谱(英)勒格朗(Legrand,M.),地质部情报研究所200光谱遥感专辑(第一辑) 矿物岩石的可见――中201光谱有机光谱分析张正行主编202光谱有色金属光谱分析方法《有色金属光谱分析方法》203光谱原子结构与原子光谱郑乐民,徐庚武编著204光谱中国污染水体光谱特征赵冬至,刘玉机主编205光谱紫外光谱在有机化学中的应用 上册黄 量,于德泉编著206光谱紫外光谱在有机化学中的应用 下册黄 量,于德泉编著207光纤存储区域网络设计:实现光纤通道和IP SAN[美]TOM CLARD208光纤单模光纤原理设计及应用[法]L.B.津霍姆著209光纤非线性光纤光学原理及应用(美)Govind P.Agrawal210光纤高速光纤计算机网络 FDDI窦文华211光纤光电子学与光纤传感器技术王玉田212光纤光纤测量与传感技术孙圣和213光纤光纤测量原理(美)马库塞214光纤光纤测试白崇思215光纤光纤传感技术张国顺216光纤光纤传感技术与应用王惠文217光纤光纤传感技术与应用郭凤珍218光纤光纤传感技术在大坝工程中的应用蔡德所219光纤光纤传感器(英)[B.卡尔肖]Brian220光纤光纤传感器及其应用刘瑞复221光纤光纤传感器技术手册徐予生222光纤光纤传感器入门(日)概本俊雄编223光纤光纤传感器译文集中国科学院安徽光机所224光纤光纤传感器译文集光纤传感技术情报协作网南225光纤光纤传感器原理张志鹏226光纤光纤传感与信号处理(英)卡尔肖227光纤光纤传感原理与应用技术崔三烈228光纤光纤传输系统杨祥林229光纤光纤传输系统(美)珀松尼克230光纤光纤传输系统设计张 煦231光纤光纤电视传输技术林如俭232光纤光纤干涉测量技术孟克生233光纤光纤孤子理论基础黄念宁234光纤光纤孤子通信理论基础杨祥林235光纤光纤光导分光光度计庄维新等236光纤光纤光缆的设计和制造陈炳炎237光纤光纤光缆工程测试胡先志238光纤光纤光学刘德明239光纤光纤光学廖延彪240光纤光纤和光器件的测量(意)坎切列里241光纤光纤激光器和放大器技术聂秋华242光纤光纤技术及其应用刘德明243光纤光纤技术及应用彭吉虎244光纤光纤技术在电工领域中的应用管喜康245光纤光纤接入网技术李勇246光纤光纤理论与测量周树同247光纤光纤理论与技术曾甫泉248光纤光纤区域网原理与设计屠世桢249光纤光纤视频传输技术白玉琨250光纤光纤数字通信技术解金山251光纤光纤数字通信技术解金山252光纤光纤数字通信接收机杨恩泽253光纤光纤数字通信实用基础纪越峰254光纤光纤数字通信系统及测试李学林255光纤光纤通信:通信用光纤、器件和系统(美)巴斯256光纤光纤通信用光电子器件和组件黄章勇257光纤光纤通信用光电子器件制作工艺基础黄章勇258光纤光纤通信用无源器件译丛 (3)四机部1423研究所情报室编259光纤光纤通信用无源器件译丛 (4) 四机部1423研究所情报室编260光纤光纤通信用新型光无源器件黄章勇261光纤光纤通信与光纤传感赵仲刚262光纤光纤通讯系统:原理与应用吴曜东263光纤光纤陀螺仪(法)Herve C. Lefevre 264光纤光纤系统―工艺、设计与应用(美)高锟著265光纤光纤用户传输网解金山266光纤光纤有线电视技术 (基础教材)韩伟267光纤光纤有线电视系统吕海涵268光纤光纤与光缆技术吴平269光纤光纤原理与技术姚建永270光纤光纤智能结构涂亚庆271光纤光纤智能结构涂亚庆272光纤激光与光纤李福利273光纤聚合物光纤江源274光纤宽带城域光纤网络技术周承刚275光纤摩托罗拉光电光纤器件手册美国摩托罗拉公司[美]摩托罗拉公司276光纤摩托罗拉光电光纤器件手册 第八章 槽型光[美]摩托罗拉公司277光纤摩托罗拉光电光纤器件手册 第二章 质理与[美]摩托罗拉公司278光纤摩托罗拉光电光纤器件手册 第九章 纤维光[美]摩托罗拉公司279光纤摩托罗拉光电光纤器件手册 第六章 功率光[美]摩托罗拉公司280光纤摩托罗拉光电光纤器件手册 第七章 分立发[美]摩托罗拉公司281光纤摩托罗拉光电光纤器件手册 第十二章 附录[美]摩托罗拉公司282光纤摩托罗拉光电光纤器件手册 第十一章 应用[美]摩托罗拉公司283光纤摩托罗拉光电光纤器件手册 第十章 发射器[美]摩托罗拉公司284光纤摩托罗拉光电光纤器件手册 第四章 光电隔[美]摩托罗拉公司285光纤摩托罗拉光电光纤器件手册 第五章 SOIC-8286光纤摩托罗拉光电光纤器件手册 第一章 概述[美]摩托罗拉公司(美) Chris Beauchamp287光纤使用Brocade光纤交换机建立SAN存储区域网288光纤通信光纤(日)大越孝敬等289光纤网络架设DIY 光纤、无线网络加强版谢志锋290光纤信息、通信、光纤方华飞291光纤英汉光通信光纤技术辞典龙赞易292光纤有线电视模拟―数字光纤与微波传输技术范寿嗣293光信息光信息存储的原理、工艺及系统设计戎霭伦等著294光信息光信息通信技术实用手册[日]光信息通信技术手册295光信息光信息网络日本映像信息媒体学会组编296光信息光信息综合实验郑光昭编著297光学《光学教程》学习指导宣桂鑫,王 尉298光学2000年的光学帕辛诺林诗彬299光学2000年青年光学学术讨论会暨院士报告会论300光学X光学手册苏达立 徐行敏301光学X射线光学在固体领域中的应用奎瑟302光学半导体导波光学器件理论及技术赵策洲303光学半导体导波光学器件理论及技术赵策洲304光学半导体光学性质沈学础305光学半导体光学性质莫斯,T.S.著 鲍友恭等译306光学半导体集成光学刘式墉307光学半导体纳米材料的非线性光学性质余保龙308光学半导体纳米材料的非线性光学性质余保龙309光学半导体纳米晶体的光学性质S. V. Gaponenko310光学变焦距光学系统设计陶纯堪311光学兵器工业科学技术辞典?光学工程《兵器工业科学技术辞典》312光学波动光学久保田广313光学波动光学赵达尊,张怀玉314光学波动过程、光学、核物理学(苏)齐楚林,А.А.著 万山,苏耀中315光学波动过程、光学、原子物理与核物理基础苏)齐楚林,А.А.著316光学波动过程光学核物理学[苏联]A?A?齐楚林著 万山 苏耀中译317光学波运过程、光学、原子物理与核物理基础[苏联]A.A.齐楚林318光学玻璃的光学和光谱性质干福熹319光学玻璃工艺学 光学零件之特殊加工А.Н.БАРДИН闫珂柱320光学玻色-爱因斯坦凝聚体形成的动力学和光学性闫珂柱321光学玻色-爱因斯坦凝聚体形成的动力学和光学性322光学薄膜光学 理论与实践尹树百323光学薄膜光学与技术唐晋发,顾培夫324光学不透明矿物晶体光学王曙325光学蔡司光学经纬仪的检修张凤利326光学蔡司型光学经纬仪的检修上海市城市建设局测量总队327光学测角光学仪器的调整与修理(苏)埃尔瓦伊斯(А.В.Эрвайс328光学测量仪器的光学设计与制造(苏)沃洛诺夫(Р.В.Воронов329光学常用的光学仪器薛桢330光学常用光学量仪顾励生331光学常用光学量仪顾励生332光学超快光学文集阮双琛333光学超快光学文集阮双琛334光学成像光学王之江335光学成像光学王之江兰茨别尔格,Г.С336光学初等物理学 第三卷 振动和波、光学和原子337光学传输光学(美)马库塞338光学传输光学(美)马库塞339光学磁光学刘公强340光学磁光学刘公强341光学大学物理 第三册 光学与量子物理周勇志342光学大学物理教程 光学蔡峰怡343光学大学物理教程 光学蔡峰怡344光学大学物理实验 光学部分亚沃尔斯基345光学大学物理手册 第四分册 声学、光学和电磁346光学大学物理学 第四册 波动与光学张三慧347光学大学物理学 第四册 光学、近代物理张三慧,史田兰348光学大学物理学 振动、波动与光学杨仲耆349光学大学用书 应用光学彭?淇?350光学带电粒子束光学吕建钦351光学单模纤维光学原理与应用热纳奥姆352光学导波光学范崇澄,彭吉虎353光学导波光学传感器:原理与技术靳伟 廖延彪 张志鹏354光学导波光学物理基础佘守宪355光学德英中光学和光学仪器词典356光学地球自转参数的重新归算 根据1962.0~1982.0光学天文学观测357光学第二届全国高速摄影与光学学会议论文集《第二届全国高速摄影与光358光学电磁场及电离子光学系统数值分析储璇雯359光学电磁场及电离子光学系统数值分析储璇雯360光学电光学手册美国无线电公司编 史斯,伍361光学电化学中的光学方法林仲华362光学电化学中的光学方法林仲华363光学电视中的电子光学楚喀尔曼364光学电学光学原子物理学问题介绍物理通报编委会365光学电影放映光学(苏)拉帕乌里(А.А.Лапаури366光学电影光学包学诚367光学电影摄影物镜光学设计电影镜头设计组368光学电子光学杜秉初369光学电子光学赵国骏370光学电子光学华中一,顾昌鑫371光学电子光学应根裕372光学电子光学卢斯特霍兹,A.A373光学电子光学成都电讯工程学院374光学电子光学(苏)喀尔曼(В.М.Кельман) 375光学电子光学苏联)范利白(Вайнриб,Е.А376光学电子光学基础陈文雄,西门纪业377光学电子光学计算机辅助设计童林夙378光学电子光学计算机辅助设计童林夙379光学电子光学教程任晴科380光学电子光学理论基础谢曼(О.И.Семан) 381光学电子光学应用肖士璋,冉启钧382光学电子光学正则理论与束流计算西门纪业383光学电子和离子光学原理及象差导论西门纪业384光学电子离子光学 《电子光学》第3版赵国骏385光学电子离子光学计算机辅助设计孙伯尧,汪健如386光学电子离子光学仪器原理邵健中387光学电子显微镜与电子光学黄兰友,刘绪平388光学动手动脑学物理 光学沈华,高立民389光学对称光学系统的象差W.T.韦尔福特390光学二元光学金国藩391光学二元光学金国藩392光学反射棱镜共轭理论 光学仪器的调整与稳象连铜淑393光学反射棱镜共轭理论 光学仪器的调整与稳象连铜淑394光学非成象聚光器光学 光和太阳能威尔福德395光学非成象聚光器光学光和太阳能W.T.威尔福德 R.维恩斯顿396光学非线性光纤光学原理及应用(美)Govind P.Agrawal397光学非线性光纤光学原理及应用(美)Govind P.Agrawal398光学非线性光学范琦康399光学非线性光学布洛姆伯根400光学非线性光学过巳吉401光学非线性光学王奎雄402光学非线性光学李荫远,杨顺华403光学非线性光学费浩生404光学非线性光学 原理与进展钱士雄405光学非线性光学 原理与进展钱士雄406光学非线性光学和材料阿雷克(Arecchi,F.T.)407光学非线性光学晶体材料科学张克从,王希敏408光学非线性光学频率变换及激光调谐技术姚建铨409光学非线性光学原理 上册沈元壤著 顾世杰译410光学非线性光学原理 下册沈元壤著 顾世杰411光学非线性与量子光学谭维翰412光学非线性与量子光学谭维翰413光学非线性与量子光学谭维翰杭州大学化学系分析化学教414光学分析化学手册 第三分册 电化学分析与光学杭州大学化学系分析化学教415光学分析化学手册 第三分册 电化学分析与光学416光学分子非线性光学的理论与实践叶 成417光学分子非线性光学的理论与实践叶 成418光学傅里叶光学卞松玲419光学傅里叶光学游明俊420光学傅里叶光学吕乃光421光学傅里叶光学 基本概念和习题422光学傅里叶光学导论J.W.顾德门。
光信息科学与技术专业中英文对照外文翻译文献

中英文对照外文翻译文献中英文资料对照外文翻译原文1.5 Experimental SetupDue to the many concepts and variations involved in performing the experiments in this project and also because of their introductory nature, Project 1 will very likely be the most time consuming project in this kit. This project may require as much as 9 hours to complete. We recommend that you perform the experiments in two or more laboratory sessions. For example, power and astigmatic distance characteristics may be examined in the first session and the last two experiments (frequency and amplitude characteristics) may be performed in the second session.A Note of CautionAll of the above comments refer to single-mode operation of the laser which is a very fragile device with respect to reflections and operating point. One must ensure that before performing measurements the laser is indeed operating single-mode. This can be realized if a single, broad fringe pattern is obtained or equivalently a good sinusoidal output is obtained from the Michelson interferometer as the path imbalance is scanned. If this is not the case, the laser is probably operating multimode and its current should be adjusted. If single-mode operation cannot be achieved by adjusting the current, then reflections may be driving the laser multimode, in which case the setup should be adjusted to minimize reflections. If still not operating single-mode, the laser diode may have been damaged and may need to be replaced.WarningThe lasers provided in this project kit emit invisible radiation that can damage the human eye. It is essential that you avoid direct eye exposure to the laser beam. We recommend the use of protective eyewear designed for use at the laser wavelength of 780 nm.Read the Safety sections in the Laser Diode Driver Operating Manual and in thelaser diode section of Component Handling and Assembly (Appendix A) before proceeding.1.5.1 Semiconductor Diode Laser Power Characteristics1.Assemble the laser mount assembly (LMA-I) and connect the laser to its power supply. We will first collimate the light beam. Connect the laser beam to a video monitor and image the laser beam on a white sheet of paper held about two to ten centimeters from the laser assembly. Slowly increase the drive current to the laser and observe the spot on the white card. The threshold drive current rating of the laser is supplied with each laser. Increase the current to about 10-20 mA over the threshold value.With the infrared imager or infrared sensor card, observe the spot on the card and adjust the collimator lens position in the laser assembly LMA-I to obtain a bright spot on the card. Move the card to about 30 to 60 centimeters from the lens and adjust the lens position relative to the laser to obtain a spot where size does not vary strongly with the position of the white card. When the spot size remains roughly constant as the card is moved closer or further from the laser, the output can be considered collimated. Alternatively, the laser beam may be collimated by focusing it at a distance as far away as possible. Protect fellow co-workers from accidental exposure to the laser beam.2.Place an 818-SL detector on a post mount (assembly M818) and adjust its position so that its active area is in the center of the beam. There should be adequate optical power falling on the detector to get a strong signal. Connect the photodetector to the power meter (815). Reduce the background lighting (room lights) so that the signal being detected is only from the laser. Reduce the drive current to a few milliamperes below threshold and, again, check to see that room light is not the dominant signal at the detector by blocking the laser light.3. Increase the current and record the output of the detector as a function of laser drive current. You should obtain a curve similar to Figure 1.2. If desired, the diode temperature may also be varied to observe the effects of temperature on threshold current. When examining laser diode temperature characteristics, the laser diode driver should be operated in the constant current mode as a safeguard against excessive currents that damage the diode laser. Note that as the diode temperature is reduced, the threshold decreases. Start all measurements with the diode current off to prevent damage to the laser by preventing drive currents too high above threshold. To prevent destruction of the laser, do not exceed the stated maximum drive current ofthe laser.1.5.2 Astigmatic Distance CharacteristicsThe laser diode astigmatic distance is determined as follows. A lens is used to focus the laser beam at a convenient distance. A razor blade is, then, incrementally moved across the beam to obtain data for total optical power passing the razor edge vs. the razor blade position. A plot of this data produces an integrated power profile of the laser beam (Figure 1.9a) which through differentiation exposes the actual power profile (Figure 1.9b) which, in turn, permits determination of the beam diameter (W).A beam diameter profile is obtained by measuring the beam diameter while varying the laser position. Figure 1.9c illustrates the two beam diameter profiles of interest: one for razor edge travel in the direction perpendicular to the laser diode junction plane and the other for travel in the direction parallel to the junction plane. The astigmatic distance for a laser diode is the displacement between the minima of these two profiles. This method is known as the knife edge technique.1. Assemble the components shown in Figure 1.8 with the collimator lens (LC), in the rotational stage assembly (RSA-I), placed roughly 1 centimeter away from the laser. The beam should travel along the optic axis of the lens. This is the same lens used in collimating the laser in the previous setup. The approximate placement of all thecomponents are shown in the figure. Make sure that the plane of the diode junction (xz plane in Figure 1.1) is parallel with the table surface.2. Due to the asymmetric divergence of the light, the cross-section of the beam leaving the laser and, further, past the spherical lens is elliptical. The beam, thus, has two distinct focal points, one in the plane parallel and the other in the plane perpendicular to the laser diode junction. There is a point between the two focal points where the beam cross-section is circular. With the infrared imager and a white card, roughly determine the position where the beam cross-section is circular.Figure 1.9 – Procedure for finding astigmatic distance.3. Adjust the laser diode to lens distance such that the razor blades are located in the xy plane where the beam cross-section is circular.4. Move the laser diode away from the lens until minimum beam waist is reached at the plane of razor blades. Now, move the laser diode about 200 µm further away from the lens.5. Move razor blad e 1 in the x direction across the beam through the beam spread θx and record the x position and detected intensity at each increment (≤100 µm increments). The expected output is shown in Figure 1.9. The derivative of this curve yields the intensity profile of the beam in the x direction from which the beamdiameter is determined.6. Repeat with razor blade 2 for θy in the y direction.7. Move the laser closer to the lens in increments (≤50 µm) through a total of at least than 500µm. Repeat Steps 5 and 6 at each z increment, recording the z position.8. Using the collected data, determine the beam intensity profiles in the x and y directions as a function of the lens position z. This is done by differentiating each data set with respect to position. Then, calculate the beam diameter and plot as a function of z. The difference in z for the minimum in θx and θy is the astigmatic distance of the laser diode. Use of computer software, especially in differentiating the data, is highly recommended.If the laser junction is not parallel to the table surface, then for each measurement above, you will obtain an admixture of the two beam divergences and the measurement will become imprecise. If the laser is oriented at 45° to the surface of the table, the astigmatic distance will be zero.Different laser structures will have different angular beam divergences and, thus, different astigmatic distances. If you have access to several different laser types (gain guided, index guided), it may be instructive to characterize their astigmatic distances.1.5.3 Frequency Characteristics of Diode LasersIn order to study frequency characteristics of a diode laser, we will employ a Michelson interferometer to convert frequency variations into intensity variations. An experimental setup for examining frequency and, also, amplitude characteristics of a laser source is illustrated in Figure 1.10.1. In this experiment, it is very possible that light may be coupled back into the laser, thereby, destabilizing it. An optical isolator, therefore, will be required to minimize feedback into the laser. A simple isolator will be constructed using a polarizing beam splitter cube and a quarterwave plate. We orient the quarterwave plate such that the linearly polarized light from the polarizer is incident at 45° to the principal axes of the quarterwave plate so that light emerging from the quarterwave plate is circularly polarized. Reflections change left-circular polarized light into right-circular or vice versa so that reflected light returning through the quarterwave plate will be linearly polarized and 90° rotated with respect to the polarizer transmission axis. The polarizer, then, greatly attenuates the return beam.In assembling the isolator, make sure that the laser junction (xz plane in Figure 1.1) is parallel to the surface of the table (the notch on the laser diode case points upward) and the beam is collimated by the lens. The laser beam should be parallel tothe surface of the optical table. Set the polarizer and quarterwave (λ/4) plate in place. Place a mirror after the λ/4 plate and rotate the λ/4 plate so that maximum rejected signal is obtained from the rejection port of the polarizing beam splitter cube as shown in Figure 1.11. When this signal is maximized, the feedback to the laser should be at a minimum.2. Construct the Michelson interferometer as shown in Figure 1.12. Place the beam steering assembly (BSA-II) on the optical table and use the reflected beam from the mirror to adjust the quarterwave plate orientation. Set the cube mount (CM) on the optical breadboard, place a double sided piece of adhesive tape on the mount, and put the nonpolarizing beam splitter cube (05BC16NP.6) on the adhesive tape. Next, place the other beam steering assembly (BSA-I) and the detector mount (M818BB) in location and adjust the mirrors so that the beams reflected from the two mirrors overlap at the detector.When long path length measurements are made, the interferometer signal will decrease or disappear if the laser coherence length is less than the two way interferometer path imbalance. If this is the case, shorten the interferometer until the signal reappears. If this does not work, then check the laser for single-mode operation by looking for the fringe pattern on a card or by scanning the piezoelectric transducer block (PZB)in BSA-II and monitoring the detector output which should be sinusoidal with PZB scan distance. If the laser does not appear to be operating single-mode, realign the isolator and/or change the laser operating point by varying the bias current. Additionally, to ensure single-mode operation, the laser should be DC biased above threshold before applying AC modulation. Overdriving the laser can also force it into multimode operation.3. The Michelson interferometer has the property that depending on the position of the mirrors, light may strongly couple back toward the laser input port. In order to further reduce the feed-back, slightly tilt the mirrors as illustrated in Figure 1.13. If still unable to obtain single-mode operation, replace the laser diode.4. Place a white card in front of the detector and observe the fringe pattern with the infrared imager. Slightly adjust the mirrors to obtain the best fringe pattern. Try to obtain one broad fringe.5. Position the detector at the center of the fringe pattern so that it intercepts no more than a portion of the centered peak.6. By applying a voltage to the piezoelectric transducer block attached to the mirror (part PZB) in one arm of the interferometer (i.e. BSA-II), maximize the output intensity. The output should be stable over a time period of a minute or so. If it is not, verify that all components are rigidly mounted. If they are, then room air currents may be destabilizing the setup. In this case, place a box (cardboard will do) over the setup to prevent air currents from disturbing the interferometer setup.7.Place the interferometer in quadrature (point of maximum sensitivity between maximum and minimum outputs of the interferometer) by varying the voltage on the PZB.8. The output signal of the interferometer due to frequency shifting of the laser is given by ∆I∝∆φ = 2π/c ∆L ∆ν where ∆L is the difference in path length between the two arms of the interferometer and ∆ν is the frequency sweep of the laser that is induced by applying a current modulation. Remember that in a Michelson interferometer ∆L is twice the physical difference in length between the arms since light traverses this length difference in both directions. ∆L values of 3-20 cm represent convenient le ngth differences with the larger ∆L yielding higher output signals.Before we apply a current modulation to the laser, note that the interferometer output signal, ∆I, should be made larger than the detector or laser noise levels by proper choice of ∆L and current modulation amplitude di. Also recall from Section 1.3that when the diode current is modulated so is the laser intensity as well as its frequency. We can measure the laser intensity modulation by blocking one arm of the interferometer. This eliminates interference and enables measurement of the intensity modulation depth. We, then, subtract this value from the total interferometer output to determine the true dI/di due to frequency modulation. Apply a low frequency, small current modulation to the laser diode. Note that when the proper range is being observed15mA 10didv v 1--= and1mA 2.0didI I 1-= for the amplitude change only.Recallingi v L c 2di d di dI ∆∆∆=∆∝πφ)( ,15mA 10~didI Lv 2c --∆π, or15-mA 10L K 2~di dI -∆λπ where K is a detecto r response constant determined by varying ∆L.9. With the interferometer and detection system properly adjusted, vary the drive frequency of the laser and obtain the frequency response of the laser (Figure 1.4 or1.10a).You will need to record two sets of data: (i) the modulation depth of the interferometer output as a function of frequency, and (ii) the laser intensity modulation depth. The difference of the two sets of collected data will provide an estimate of the actual dI/di due to frequency modulation. Also note that if the current modulation is sufficiently small and the path mismatch sufficiently large, the laser intensity modulation may be negligible. You may need to actively keep theinterferometer in quadrature by adjusting the PZB voltage.Make any necessary function generator amplitude adjustments to keep the current modulation depth of the laser constant as you vary the frequency. This is because the function generator/driver combination may not have a flat frequency response. The effect of this is that the current modulation depth di is not constant and varies with frequency. So to avoid unnecessary calculations, monitor the current modulation depth by connecting the LASER MONITOR connector on the laser diode driver system to an oscilloscope and keep the modulation depth constant by adjusting the amplitude of the applied sinusoidal wave as a function of frequency. Record the frequency for your laser at which the thermal contribution to dν/di begins to become negligible and dν/di drops off (see Section 1.3).10. Keeping the above equations in mind, we will, now, measure the FM chirp characteristics of the laser. At a constant current modulation frequency (choose a modulation frequency where dν/di varies rapidly, i.e. where the slope of your grap h from Step 9, which should be similar to Figure 1.10a, is maximum), vary the current modulation depth di for different laser bias levels and derive a curve such as the one in Figure1.10b.The output dν should not vary significantly except around threshold and at high currents.CautionDo not exceed the specified drive currents/output power ratings of the diode or it may be damaged.11. The phase noise characteristic behavior (Section1.4) as a function of interferometer path length imbalance ∆L may be determ ined by inducing phase noise through application of laser current modulation. Make sure that the interferometer is in quadrature.Set the laser diode current above threshold, apply a small current modulation, and fix the modulation frequency at a desired value. Convenient frequencies may include 50 Hz, 2 kHz, and 50 kHz (see Reference 1.5). Monitor the detector output with a spectrum analyzer or an oscilloscope and record the peak-to-peak output intensity at interferometer quadrature. You may accomplish this by manually sweeping the PZB voltage to cause a minimum of π/2 phase shift, recording the maximum peak-to-peak intensity as a function of path length imbalance. It is important to ensure that instrument noise is below the signal levels expected and it is assumed that single-mode operation of the laser is maintained. Curves similar to Figure 1.10c should be obtained.1.5.4 Amplitude Characteristics of Diode LasersThe measurements of the intensity characteristics are taken by placing the detector before the interferometer as in Figure 1.10 or by blocking one mirror in the interferometer. Again, the laser must be operated single-moded with minimum feedback or the noise level and functionality will drastically change. The relative intensity noise (RIN) is defined as 20log(dI/I) where dI is the RMS intensity fluctuations so that for dI~10-4 , the RIN is -80 dB. Normally, these measurements are made with a spectrum analyzer and a 1 Hz bandwidth.When making RIN measurements, electronic and photodetector shot noise must be below the RIN levels. (OPTIONAL) You may determine the shot noise using an incoherent source (e.g. lamp) with an intensity level similar to that of the laser. The resultant frequency spectrum of noise with the light source excited gives a measure of the shot noise level which should be adjusted to be at least 10 dB greater than electronic noise levels. The measured shot noise should be checked with Equation0.47.1. Vary the laser drive current from below threshold through and above the threshold and record the laser output power and intensity noise at a desired frequency using a spectrum analyzer. When you calculate the RIN, assuming that shot and electronic noises are below the RIN level, a plot similar to that presented in Figure 1.10d should be obtained. In most cases, for single-mode operation, the noise peaks at threshold. The shape of the noise curve may vary if the laser is modulated, if it becomes multi-modal, or if the side-mode suppression on a nominally single-mode laser is not adequate (< 20 dB).2. It is instructive to operate the laser with modulation signals of varying depth and/or degrading the isolator performance by rotating the λ/4 plate to increase feedback to the laser. This will illustrate noise properties for various feedback conditions which are important to subsequent sensor and communication experiments. RINs of less than -150dB and -120dB are required for television broadcast signals and sensitive interferometric sensors, respectively.3. The intensity noise of diode lasers has a 1/f characteristic (performance is degraded as the frequency is lowered). With the laser above threshold and the photodetector connected to a spectrum analyzer, determine the RIN as a function of modulation frequency. The response shown in Figure 1.10e should be obtained where the noise becomes white (flat with frequency) starting somewhere between 100 kHz and 1 MHz for typical lasers.NOTE: The Michelson interferometer setup used in this project will again be used in Project3. It may, therefore, save time to proceed directly to Project3 before completing characterization of diode lasers in Project2.中文翻译1.5 实验装置由于在这个项目中执行这个实验时涉及到许多新的概念和变化,也因为它们是初始性的工作,项目1可能是这个实验单元中最耗时的项目。
光学传感器毕业论文中英文文献及翻译

英文文献及中文翻译一种精确测量倾斜角度的光学传感器摘要本文主要介绍了一种新型光学传感器,它可以同时准确地测量倾斜角或两轴倾斜角度。
这种传感器是基于激光干涉原理,因此具有很高的精度。
设计制作了一个传感器的模型来论证这个新的方法,这是一个光电传感器,传感器中没有移动的部分。
由正交于铅垂面的流动水平面提供参考面。
传感器和绝对水平面之间的角度随着被测量的物体倾斜而改变,这些变化反映在条纹图案的中心位置的转移方式。
不同的干涉条纹的中心位置随倾斜角的变化而改变。
干涉条纹图案进行记录和处理,转化为两轴、水平和垂直倾斜角度。
当使用1024*1024像素的传感器时,测量范围为700弧秒,其精度可高达+/ - 1弧秒。
关键词:倾斜角度传感器,倾斜仪,激光干涉I 介绍市场上目前有几种类型的商业倾斜角度测量传感器。
有些是角度传感器,有些是倾斜仪,它们的工作原理不同。
电解液体、电容和钟摆是现在大多数倾斜角度传感器和倾斜仪的三个主要工作原理。
在这里,我们提出了一种新的光学方法,建立了一个用激光、光学元件和图像传感器的光电传感器,它可以同时做精确的倾斜角度测量,不需要进行机械的移动,其工作原理是基于光学干涉,相干激光作为光源。
光线通过一个装满液态油的玻璃油盒。
由正交于铅垂面的流动水平面提供参考面。
当激光束穿过油箱有两束光线反射回来,一束是液体的表面产生的,另一束是容器玻璃产生的,干涉条纹就是由这两条光线形成的,条纹图案将随着倾斜角度的变化产生相应的变化,条纹图案采集和处理后将反映倾斜角度信息,光学工作原理使它不受磁场的影响。
该传感器可以同时测量两轴倾角。
流动的水平面确保了参考面是一个绝对的水平面。
高灵敏度光学干涉测量原理,保证了较高的精度。
II 原理图1说明了工作原理示意图,O点是光线扩大镜头的焦点,O点可以看作是点光源,它发出球面波。
由于地球重力的影响,液体油面始终保持水平,因此用油面作为参考平面。
该容器是玻璃材料的。
当传感器被放在目标表面时,其底部表面将连同目标对象一起倾斜。
光纤光学英文文献3

All-optical dynamic grating generation based on Brillouin scattering in polarization-maintainingfiberKwang Yong Song,1,*Weiwen Zou,2Zuyuan He,2and Kazuo Hotate21Department of Physics,Chung-Ang University,Seoul,Korea2Department of Electronic Engineering,The University of Tokyo,Tokyo,Japan*Corresponding author:songky@cau.ac.krReceived January30,2008;revised March20,2008;accepted March20,2008;posted March25,2008(Doc.ID92171);published April22,2008We report a novel kind of all-optical dynamic grating based on Brillouin scattering in a polarization main-tainingfiber(PMF).A moving acoustic grating is generated by stimulated Brillouin scattering between writ-ing beams in one polarization and used to reflect an orthogonally polarized reading beam at different wave-lengths.The center wavelength of the grating is controllable by detuning the writing beams,and the3dBbandwidth ofϳ80MHz is observed with the tunable reflectance of up to4%in a30m PMF.©2008OpticalSociety of AmericaOCIS codes:050.2770,060.2310,190.4370,290.5900.A high-speed and reconfigurable dynamic grating canbe used as a powerful tool in communication or sen-sor applications as a tunable opticalfilter,an opticalswitch,and a distributed sensor[1–4].The currentlyavailable scheme is to build up a gain or absorptiongrating in an Er-dopedfiber(EDF)by counterpropa-gating optical waves with the same optical frequency.However,such an EDF-based dynamic grating suf-fers a couple of significant problems,such as diffi-culty in separating the writing and reading beams[1,2]or an amplified spontaneous emission(ASE)noise due to optical pumping[3,4],which can givedisadvantages in practical applications.In this Letter,we demonstrate a novel kind of dy-namic grating based on stimulated Brillouin scatter-ing(SBS)in a polarization-maintainingfiber(PMF).An acoustic phonon generated by SBS between twocounterpropagating writing beams of one polariza-tion is used as a tunable and dynamic grating for theorthogonally polarized reading beam at differentwavelengths satisfying the phase-matching condi-tion.The reflected probe wave experiences an ordi-nary Brillouin shift by the Doppler effect,and the op-tical frequency difference between the writing andthe reading beams is determined by the birefringenceof the PMF.The basic theory,the operation principle,and the experimental configuration are described,and the results are explained using a simplifiedtheory of Brillouin scattering.SBS is generally modeled as a three-wave interac-tion between the pump͑1͒,Stokes͑2͒,and acousticwaves.When a phase-matching condition is satisfied(1−2=B,B being the Brillouin frequency),strongenergy transfer from the pump to the counterpropa-gating Stokes wave takes place generating acousticwaves,which stimulates the process.TheB is givenby following equation[5]:B=2nV a,͑1͒where n,V a,andare the refractive index,the veloc-ity of the acoustic wave,and the optical wavelength,respectively.In a PMF(or any medium with birefrin-gence),optical waves with two principal polarizations(i.e.,x and y polarization)experience differentB’sowing to their different refractive indexes.Consider-ing that the acoustic wave generated by SBS is a lon-gitudinal one that is free of the transversal polariza-tion[6],an interesting condition can be reached thatthe x-and the y-polarized optical waves in a PMFshow the sameB at different wavelengths.When thedispersion of the acoustic wave is ignored,the condi-tion is expressed by following equations:2n x V ax=2n y V ay,͑2͒n xx=n yy,͑3͒where n x,y andx,y(if n xϾn y,yϾx)are the refrac-tive indexes and the optical frequencies in x and y po-larizations,respectively.With⌬n=͑n x−n y͒ 1and⌬=y−x (x ory),Eq.(3)is simplified to⌬=⌬nn.͑4͒Since the SBS-induced acoustic waves can beviewed as moving gratings for the reflection of thepump wave without polarization dependence,it is ex-pected that acoustic waves generated by SBS be-tween the x-polarized pump and Stokes waves at theoptical frequencyx will show strong reflectance tothe y-polarized pump wave at the frequency ofx+⌬.Considering that the intensity and the wave-length of the acoustic waves are easily tuned by con-trolling the x-polarized“writing”beams,one may ex-pect the SBS in a PMF to play a role of a tunabledynamic grating.We composed an experimental setup,as shown inFig.1.For the writing of the dynamic grating,a926OPTICS LETTERS/Vol.33,No.9/May1,20080146-9592/08/090926-3/$15.00©2008Optical Society of America1550nm laser diode was used as a light source,and the output power was divided by a 50/50coupler.A single-sideband modulator (SSBM)and a microwave synthesizer were used to generate the Stokes wave (pump2)of the writing beams,and the output was amplified and polarized by an EDF amplifier (EDFA)and an x polarizer.The Brillouin pump wave (pump1)of the writing beams was prepared by amplifying the original wave with the same polarization as that of pump2.Pump1and the pump2were launched into a PMF in opposite direction to each other through po-larization beam combiners (PBC1,PBC2).The PMF was a PANDA fiber manufactured by Fujikura with a 30m length and a nominal ⌬n ϳ6.2ϫ10−4at the wavelength of 1300nm.For a reading beam (probe),a tunable laser with an operating wavelength near 1550nm was used as a light source after being polar-ized in the y axis.The output was launched into the PMF in the direction of the pump1through a polarization-maintaining circulator and PBC1.The transmitted power of the probe was measured using a power meter,and the backreflected spectrum was monitored using an optical spectrum analyzer (OSA)through a y polarizer.At first,we measured the Brillouin gain spectra of the PMF in the x and y axes.The B in the x axis was measured to be 10.502GHz,and the difference of the B ’s of two polarizations was ϳ3.6MHz,as depicted in the inset of Fig.1,which corresponds to ⌬n ϳ5.0ϫ10−4by Eq.(1).To induce the SBS in the x axis,we launched pump1and the pump2in the x axis with the output powers of 630and 10mW,respectively,setting their frequency offset ͑⌬f ͒to 10.502GHz.For the detection of the dynamic grating,the fre-quency of the probe was tuned at the higher fre-quency region while monitoring the spectrum with the OSA,and the result is shown in Fig.2.When ⌬(the frequency difference between pump1and the probe)was ϳ72.6GHz,a large reflection of the probe was observed (black curve)as a result of the dynamic grating at the frequency detuned from the probe by the same amount as that between pump1and pump2.When one of the pumps (pump1)was turned off,the dynamic grating disappeared as depicted by the gray curve although the probe was still propa-gated as confirmed by the Rayleigh scattering seen at the probe frequency.In both cases,the x -polarizedpumps were observed in spite of the use of the y po-larizer in front of the OSA,which originated from the finite extinction ratio ͑ϳ20dB ͒of the polarizing com-ponents.The small peaks near pump1correspond to the first-and second-order anti-Stokes waves that were suppressed in the SSBM used for the genera-tion of pump2.Figure 3(a)shows the reflectance of the dynamic grating with respect to ⌬,calculated from the ratio of the input and the reflected powers of the probe,while the pump powers were maintained to the same as the first measurement.The maximum reflectance was ϳ4%,and the 3dB width was ϳ80MHz.The overall shape looks asymmetric,which could be at-tributed to the irregularity of the local birefringence in the PMF.We fixed ⌬to 72.6GHz and swept ⌬f ,the fre-quency offset between pump1and pump2.The result is depicted in Fig.3(b),which fits well with a Lorent-zian curve with a 3dB width of 28MHz,similar to the ordinary Brillouin gain spectrum of the fiber.The dependence of the grating reflectance on the pump powers was measured by varying one of the pump powers with the other fixed,while ⌬was kept at 72.6GHz.Figures 4(a)and 4(b)show the reflec-tance of the grating as a function of the power of pump1and pump2,respectively.It is remarkable that the reflectance grows in an exponential form to some definite value with the power of pump1asFig. 1.Experimental setup:LD,laser diode;SSBM,single-sideband modulator;EDFA,Er-doped fiber ampli-fier;PBC,polarization beam combiner;OSA,optical spec-trum analyzer.The inset is the Brillouin gain spectra of the fiber under test in x and ypolarizations.Fig.2.Optical spectra monitored by an OSA in the gen-eration of dynamic grating.The gray curve corresponds to the case that one (pump1)of the writing beams is turned off,and the black curve with both writing beams turnedon.Fig.3.(Color online)(a)Reflectance of the dynamic grat-ing as a function of ⌬,the frequency difference between the pump1and the probe.(b)Reflectance of the dynamic grating at a fixed ⌬͑72.6GHz ͒as a function of the ⌬f ,the frequency offset between pump1and pump2.The curve shows the result of a Lorentzian fit.May 1,2008/Vol.33,No.9/OPTICS LETTERS 927shown in Fig.4(a),while it is linearly dependent on the power of pump2as depicted in Fig.4(b),where the result matches well with a linear fit with the slope of 3.8ϫ10−4͑/mW ͒.The slight inconsistency in the reflectance values of Figs.4(a)and 4(b)came from long-term drift of the optical frequencies of the pump and the probe lasers,whose effect was negli-gible in each measurement.The difference in dependence of the grating reflec-tance on the pump powers can be explained by the re-lation of the Brillouin gain and the reflectance.In the generation of the dynamic grating,the increased power of pump2through the gain of the SBS can be viewed as the reflection of pump1.Additionally,we may assume that pump1and the probe experience al-most the same reflectance,since they share the same acoustic grating.Therefore,if the pump depletion is ignored (i.e.,small reflection of pump1),the reflec-tance of the dynamic grating R can be estimated from the gain of the SBS [5]as follows:R =P probe out P probein Ϸ⌬P 2P 1=P 2͑e ͑g B P 1L eff /A eff ͒−1͒P 1,͑5͒where g B ,L eff ,A eff ,P 1,and P 2are the Brillouin gain coefficient,the effective length of the fiber,the mode effective area,the power of pump1,and the power of pump2,respectively.In Eq.(5),one can see that the reflectance of the grating linearly depends on P 2,and the reflectance will grow in an exponential form ac-cording to P 1if the gain is large enough.The final point in Fig.4(a)with pump1of 800mW looks devi-ated from the form of the exponential growth,which could be attributed to the gain saturation with the pump depletion due to too large amplification of pump2.The reflectance offset appearing in the lin-early fitted graph of Fig.4(b)can be attributed to the amplification of the SBS noise induced by the strong pump1.We think detailed properties of the grating can be explained by coupled wave equations (by five-wave mixing instead of the three-wave one in the ordinary case of the SBS),and there could be more factors that have an effect on the grating reflectance such as the probe power.Further research is needed on this point.The relation between the optical frequencies of pump1and the probe under the condition of the dy-namic grating generation is depicted in Fig.5,which shows good linearity as expected from Eq.(3).In the measurement,the powers of the pumps and the probe were kept constant,and the variation of B was negligible ͑Ͻ1MHz ͒.In conclusion,we have demonstrated a novel all-optical dynamic grating based on stimulated Bril-louin scattering in a polarization-maintaining fiber.The center frequency of the grating was ϳ72.6GHz detuned from the writing beam frequency,and the re-flectance as well as the peak frequency could be tuned by controlling the power and the frequency of the writing beam.Considering the high sensitivity of the dynamic grating to local birefringence [see Eq.(4)]as well as the high on–off extinction ratio ͑Ͼ60dB ͒,the spectral flexibility [7],and the short re-sponse time ͑ϳ10ns ͒[5]of the SBS,we believe the SBS-based dynamic grating has large potential for practical applications such as an all-optical switch and a highly sensitive fiber sensor.The authors are grateful to Luc Thévenaz from EPFL in Lausanne,Switzerland,for his contribution to the development of the idea.This work was sup-ported by the “Grant-in-Aid for Creative Scientific Research”and the “Global Center of Excellence Pro-gram”from the Ministry of Education,Culture,Sports,Science and Technology,Japan.K.Y.Song was supported by the Korea Research Foundation Grant funded by the Korean Government (MOE-HRD)(KRF-2007-331-C00116).References1.S.J.Frisken,Opt.Lett.17,1776(1992).2.B.Fischer,J.L.Zyskind,J.W.Sulhoff,and D.J.DiGiovanni,Opt.Lett.18,2108(1993).3.X.Fan,Z.He,Y.Mizuno,and K.Hotate,Opt.Express 13,5756(2005).4.X.Fan,Z.He,and K.Hotate,Opt.Express 14,556(2006).5.G.P .Agrawal,Nonlinear Fiber Optics ,2nd ed.(Academic,1995).6.W.Zou,Z.He,and K.Hotate,IEEE Photon.Technol.Lett.18,2487(2006).7.M.González Herráez,K.Y.Song,and L.Thávenaz,Opt.Express 14,1395(2006).Fig.5.(Color online)Optical frequency of the probe as a function of the frequency of pump1under the condition of the dynamic grating generation.The line is the result of a linearfit.Fig.4.(Color online)Reflectance of the dynamic grating as a function of pump power in the case of (a)pump1varied and pump2fixed to 10mW,and (b)pump2varied and pump1fixed to 200mW.The line is the result of a linear fit.928OPTICS LETTERS /Vol.33,No.9/May 1,2008。
(完整word版)光学外文文献及翻译

学号2013211033 昆明理工大学专业英语专业光学姓名辜苏导师李重光教授分数导师签字日期2015年5月6日研究生部专业英语考核In digital holography, the recording CCD is placed on the ξ-ηplane in order to register the hologramx ',y 'when the object lies inthe x-y plane. Forthe reconstruction ofthe information ofthe object wave,phase-shifting digital holography includes two steps:(1) getting objectwave on hologram plane, and (2) reconstructing original object wave.2.1 Getting information of object wave on hologram plateDoing phase shifting N-1 times and capturing N holograms. Supposing the interferogram after k- 1 times phase-shifting is]),(cos[),(),(),,(k k b a I δηξφηξηξδηξ-⋅+= (1) Phase detection can apply two kinds of algorithms:synchronous phase detection algorithms [9]and the least squares iterative algorithm [10]. The four-step algorithm in synchronous phase detection algorithm is in common use. The calculation equation is)2/3,,(),,()]2/,,()0,,([2/1),(πηξπηξπηξηξηξiI I iI I E --+=2.2 Reconstructing original object wave by reverse-transform algorithmObject wave from the original object spreads front.The processing has exact and clear description and expression in physics and mathematics. By phase-shifting technique, we have obtained information of the object wave spreading to a certain distance from the original object. Therefore, in order to get the information of the object wave at its initial spreading position, what we need to do is a reverse work.Fig.1 Geometric coordinate of digital holographyexact registering distance.The focusing functions normally applied can be divided into four types: gray and gradient function, frequency-domain function, informatics function and statistics function. Gray evaluation function is easy to calculate and also robust. It can satisfy the demand of common focusing precision. We apply the intensity sum of reconstruction image as the evaluation function:min ),(11==∑∑==M k Nl l k SThe calculation is described in Fig.2. The position occurring the turning point correspondes to the best registration distanced, also equals to the reconstructing distance d '.It should be indicated that if we only need to reconstruct the phase map of the object wave, the registration distance substituted into the calculation equation is permitted having a departure from its true value.4 Spatial resolution of digital holography4.1 Affecting factors of the spatial resolution of digital holographyIt should be considered in three respects: (1) sizes of the object and the registering material, and the direction of the reference beam, (2) resolution of the registering material, and (3) diffraction limitation.For pointx2on the object shown in Fig.3, the limits of spatial frequency are λξθλθθ⎥⎦⎤⎢⎣⎡⎪⎪⎭⎫ ⎝⎛-'-=-=-0211maxmax tan sin sin sin sin z x f R R Fig.2 Determining reconstructing distanceλξθλθθ⎥⎦⎤⎢⎣⎡⎪⎪⎭⎫⎝⎛-'-=-=-211minmintansinsinsinsin zxfRRFrequency range isλξξ⎥⎦⎤⎢⎣⎡⎪⎪⎭⎫⎝⎛-'-⎥⎦⎤⎢⎣⎡⎪⎪⎭⎫⎝⎛-=∆--211211tansintansinzxzxfso the range is unrelated to the reference beam.Considering the resolution of registering material in order to satisfy the sampling theory, phase difference between adjacent points on the recording plate should be less than π, namely resolution of the registration material.cfff=∆η21)(minmaxπ4.2 Expanding the spatial resolution of reconstruction imageExpanding the spatial resolution can be realized at least in three ways: (1) Reducing the registration distance z0 can improve the reconstruction resolution, but it goes with reduction of the reconstruction area at the same ratio.Therefore, this method has its limitation. (2) Increasing the resolution and the imaging size of CCD with expensive price. (3) Applying image-synthesizing technique[11]CCD captures a few of images between which there is small displacement (usually a fraction of the pixel size) vertical to the CCD plane, shown in Fig.4(Schematic of vertical moving is the same).This method has two disadvantages. First, it is unsuitable for dynamic testing and can only be applied in the static image reconstruction. Second, because the pixel size is small (usually 5μm to 10μm) and the displacement should a fraction of this size (for example 2μm), it needs a moving table with high resolution and precision. Also it needs high stability in whole testing.In general, improvement of the spatial resolution of digital reconstruction is Fig.3 Relationship between object and CCDstill a big problem for the application of digital holography.5 Testing resultsFig.5 is the photo of the testing system. The paper does testing on two coins. The pixel size of the CCD is 4.65μm and there are 1 392×1 040 pixels. The firstis one Yuan coin of RMB (525 mm) used for image reconstruction by phase-shifting digital holography. The second is one Jiao coin of RMB (520 mm) for the testing of deformation measurement also by phase-shifting digital holography.5.1 Result of image reconstructionThe dimension of the one Yuancoin is 25 mm. The registrationdistance measured by ruler isabout 385mm. We capture ourphase-shifting holograms andreconstruct the image byphase-shifting digital holography.Fig.6 is the reconstructed image.Fig.7 is the curve of the auto-focusFig.4 Image capturing by moving CCD along horizontal directionFig.5 Photo of the testing systemfunction, from which we determine the real registration distance 370 mm. We can also change the controlling precision, for example 5mm, 0.1 mm,etc., to get more course or precision reconstruction position.5.2 Deformation measurementIn digital holography, the method of measuring deformation measurement differs from the traditional holography. It gets object wave before and after deformation and then subtract their phases to obtain the deformation. The study tested effect of heating deformation on the coin of one Jiao. The results are shown in Fig.8, Where (a) is the interferential signal of the object waves before and after deformation, and (b) is the wrapped phase difference.5.3 Improving the spatial resolutionFor the tested coin, we applied four sub-low-resolution holograms to reconstruct the high-resolution by the image-synthesizing technique. Fig.9 (a) is the reconstructed image by one low-resolution hologram, and (b) is the high-resolution image reconstructed from four low-resolution holograms.Fig.6 Reconstructed image Fig.7 Auto-focus functionFig.8 Heating deformation resultsFig.9 Comparing between the low and high resolution reconstructed image6 SummaryDigital holography can obtain phase and amplitude of the object wave at the same time. Compared to other techniques is a big advantage. Phase-shifting digital holography can realize image reconstruction and deformation with less noise. But it is unsuitable for dynamic testing. Applying the intensity sum of the reconstruction image as the auto-focusing function to evaluate the registering distance is easy, and computation is fast. Its precision is also sufficient. The image-synthesizing technique can improve spatial resolution of digital holography, but its static characteristic reduces its practicability. The limited dimension and too big pixel size are still the main obstacles for widely application of digital holography.外文文献译文:标题:图像重建中的相移数字全息摘要:相移数字全息术被用来研究研究艺术品的内部缺陷。
光学外文文献及翻译

学号********** 昆明理工大学专业英语专业光学姓名辜苏导师李重光教授分数导师签字日期2015年5月6日研究生部专业英语考核In digital holography, the recording CCD is placed on the ξ-ηplane in order to register the hologramx ',y 'when the object lies inthe x-y plane. Forthe reconstruction ofthe information ofthe object wave,phase-shifting digital holography includes two steps:(1) getting objectwave on hologram plane, and (2) reconstructing original object wave.2.1 Getting information of object wave on hologram plateDoing phase shifting N-1 times and capturing N holograms. Supposing the interferogram after k- 1 times phase-shifting is]),(cos[),(),(),,(k k b a I δηξφηξηξδηξ-⋅+= (1) Phase detection can apply two kinds of algorithms:synchronous phase detection algorithms [9]and the least squares iterative algorithm [10]. The four-step algorithm in synchronous phase detection algorithm is in common use. The calculation equation is)2/3,,(),,()]2/,,()0,,([2/1),(πηξπηξπηξηξηξiI I iI I E --+=2.2 Reconstructing original object wave by reverse-transform algorithmObject wave from the original object spreads front.The processing has exact and clear description and expression in physics and mathematics. By phase-shifting technique, we have obtained information of the object wave spreading to a certain distance from the original object. Therefore, in order to get the information of the object wave at its initial spreading position, what we need to do is a reverse work.Fig.1 Geometric coordinate of digital holographyexact registering distance.The focusing functions normally applied can be divided into four types: gray and gradient function, frequency-domain function, informatics function and statistics function. Gray evaluation function is easy to calculate and also robust. It can satisfy the demand of common focusing precision. We apply the intensity sum of reconstruction image as the evaluation function:min ),(11==∑∑==M k Nl l k SThe calculation is described in Fig.2. The position occurring the turning point correspondes to the best registration distanced, also equals to the reconstructing distance d '.It should be indicated that if we only need to reconstruct the phase map of the object wave, the registration distance substituted into the calculation equation is permitted having a departure from its true value.4 Spatial resolution of digital holography4.1 Affecting factors of the spatial resolution of digital holographyIt should be considered in three respects: (1) sizes of the object and the registering material, and the direction of the reference beam, (2) resolution of the registering material, and (3) diffraction limitation.For pointx2on the object shown in Fig.3, the limits of spatial frequency are λξθλθθ⎥⎦⎤⎢⎣⎡⎪⎪⎭⎫ ⎝⎛-'-=-=-0211maxmax tan sin sin sin sin z x f R R Fig.2 Determining reconstructing distanceλξθλθθ⎥⎦⎤⎢⎣⎡⎪⎪⎭⎫ ⎝⎛-'-=-=-0211minmin tan sin sin sin sin z x f R R Frequency range isλξξ⎥⎦⎤⎢⎣⎡⎪⎪⎭⎫ ⎝⎛-'-⎥⎦⎤⎢⎣⎡⎪⎪⎭⎫ ⎝⎛-=∆--02110211tan sin tan sin z x z x f so the range is unrelated to the reference beam.Considering the resolution of registering material in order to satisfy the sampling theory, phase difference between adjacent points on the recording plate should be less than π, namely resolution of the registration material.c f f f =∆η21)(min max 4.2 Expanding the spatial resolution of reconstruction imageExpanding the spatial resolution can be realized at least in three ways: (1) Reducing the registration distance z 0 can improve the reconstruction resolution, but it goes with reduction of the reconstruction area at the same ratio.Therefore, this method has its limitation. (2) Increasing the resolution and the imaging size of CCD with expensive price. (3) Applying image-synthesizing technique [11]CCD captures a few of images between which there is small displacement (usually a fraction of the pixel size) vertical to the CCD plane, shown in Fig.4(Schematic of vertical moving is the same).This method has two disadvantages. First, it is unsuitable for dynamic testing and can only be applied in the static image reconstruction. Second, because the pixel size is small (usually 5μm to 10μm) and the displacement should a fraction of this size (for example 2μm), it needs a moving table with high resolution and precision. Also it needs high stability in whole testing.In general, improvement of the spatial resolution of digital reconstruction isFig.3 Relationship between object and CCDstill a big problem for the application of digital holography.Fig.4 Image capturing by moving CCD along horizontal direction5 Testing resultsFig.5 is the photo of the testing system. The paper does testing on two coins. The pixel size of the CCD is 4.65μm and there are 1 392×1 040 pixels. The firstis one Yuan coin of RMB (525 mm) used for image reconstruction by phase-shifting digital holography. The second is one Jiao coin of RMB (520 mm) for the testing of deformation measurement also by phase-shifting digital holography.Fig.5 Photo of the testing system5.1 Result of image reconstructionThe dimension of the one Yuancoin is 25 mm. The registrationdistance measured by ruler isabout 385mm. We capture ourphase-shifting holograms andreconstruct the image byphase-shifting digital holography.Fig.6 is the reconstructed image.Fig.7 is the curve of the auto-focusfunction, from which we determine the real registration distance 370 mm. We can also change the controlling precision, for example 5mm, 0.1 mm,etc., to get more course or precision reconstruction position.Fig.6 Reconstructed image Fig.7 Auto-focus function5.2 Deformation measurementIn digital holography, the method of measuring deformation measurement differs from the traditional holography. It gets object wave before and after deformation and then subtract their phases to obtain the deformation. The study tested effect of heating deformation on the coin of one Jiao. The results are shown in Fig.8, Where (a) is the interferential signal of the object waves before and after deformation, and (b) is the wrapped phase difference.Fig.8 Heating deformation results5.3 Improving the spatial resolutionFor the tested coin, we applied four sub-low-resolution holograms to reconstruct the high-resolution by the image-synthesizing technique. Fig.9 (a) is the reconstructed image by one low-resolution hologram, and (b) is the high-resolution image reconstructed from four low-resolution holograms.Fig.9 Comparing between the low and high resolution reconstructed image6 SummaryDigital holography can obtain phase and amplitude of the object wave at the same time. Compared to other techniques is a big advantage. Phase-shifting digital holography can realize image reconstruction and deformation with less noise. But it is unsuitable for dynamic testing. Applying the intensity sum of the reconstruction image as the auto-focusing function to evaluate the registering distance is easy, and computation is fast. Its precision is also sufficient. The image-synthesizing technique can improve spatial resolution of digital holography, but its static characteristic reduces its practicability. The limited dimension and too big pixel size are still the main obstacles for widely application of digital holography.外文文献译文:标题:图像重建中的相移数字全息摘要:相移数字全息术被用来研究研究艺术品的内部缺陷。
光纤光学英文文献5

Amplification and ASE suppression in a polarization-maintaining ytterbium-doped all-solid photonic bandgap fibreC. B. Olausson1,2*, C. I. Falk3, J. K. Lyngsø1,2, B. B. Jensen3, K. T. Therkildsen3, J. W.Thomsen3, K. P. Hansen1, A. Bjarklev2 and J. Broeng11Crystal Fibre A/S, Blokken 84, DK-3460 Birkerød, Denmark2DTU Fotonik, Ørsteds Plads, building 343, 2800 Kgs. Lyngby, Denmark3Niels Bohr Institute, Universitetsparken 5, 2100 København, Denmark*Corresponding author: cbo@Abstract: We demonstrate suppression of amplified spontaneous emissionat the conventional ytterbium gain wavelengths around 1030 nm in acladding-pumped polarization-maintaining ytterbium-doped all-solidphotonic crystal fibre. The fibre works through combined index andbandgap guiding. Furthermore, we show that the peak of the amplifiedspontaneous emission can be shifted towards longer wavelengths byrescaling the fibre dimensions. Thereby one can obtain lasing oramplification at longer wavelengths (1100 nm – 1200 nm) as the amount ofamplification in the fibre is shown to scale with the power of the amplifiedspontaneous emission.©2008 Optical Society of AmericaOCIS codes: (060.2280) Fiber design and fabrication; (060.2270) Fiber characterization;(060.2400) Fiber properties; (060.2420) Fibers, polarization-maintaining; (060.5295) Photoniccrystal fibers; (060.3510) Lasers, Fiber.References and links1.G. Bouwmans, L. Bigot, Y. Quiquempois, F. Lopez, L. Provino, and M. Douay, "Fabrication andcharacterization of an all-solid 2D photonic bandgap fiber with a low-loss region (< 20 dB/km) around1550 nm," Opt. Express 13, 8452-8459 (2005).2.G. Canat, J. C. Mollier, J. P. Bouzinac, G. L. M. Williams, B. Cole, L. Goldberg, G. Kulcsar, Y. Jaouen,“Power limitations of fiber lasers at 1.5 µm by parasitic lasing effects,” in Conference on Lasers andElectro-Optics/Quantum Electronics and Laser Science and Photonic Applications Systems Technologies,Technical Digest (CD) (Optical Society of America, 2004), paper CMK6.3. A. Shirakawa, J. Ota, H. Maruyama, and K. -I. Ueda, "Linearly-Polarized Yb-Doped Fiber Laser DirectlyOperating at 1178 nm for 589-nm Generation," in Advanced Solid-State Photonics, OSA Technical Digest Series (CD) (Optical Society of America, 2007), paper MD1.4.S. Sinha, C. Langrock, M. Digonnet, M. Fejer, and R. Byer, "Efficient yellow-light generation by frequencydoubling a narrow-linewidth 1150 nm ytterbium fiber oscillator," Opt. Lett. 31, 347-349 (2006).5.N. Malossi, S. Damkjaer, P. L. Hansen, L. B. Jacobsen, L. Kindt, S. Sauge, J. W. Thomsen, F. C. Cruz, M.Allegrini, and E. Arimondo, "Two-photon cooling of magnesium atoms," Phys. Rev. A 72, 051403 (2005).6. A. Wang, A. K. George, and J. C. Knight, "Three-level neodymium fiber laser incorporating photonicbandgap fiber," Opt. Lett. 31, 1388-1390 (2006).7.V. Pureur, L. Bigot, G. Bouwmans, Y. Quiquempois, M. Douay, and Y. Jaouen, "Ytterbium-doped solidcore photonic bandgap fiber for laser operation around 980 nm," Appl. Phys. Lett. 92, 061113 (2008).8.R. Goto, K. Takenaga, K. Okada, M. Kashiwagi, T. Kitabayashi, S. Tanigawa, K. Shima, S. Matsuo, and K.Himeno, "Cladding-Pumped Yb-Doped Solid Photonic Bandgap Fiber for ASE Suppression in ShorterWavelength Region," in Optical Fiber Communication Conference and Exposition and The National Fiber Optic Engineers Conference, OSA Technical Digest (CD) (Optical Society of America, 2008), paperOTuJ5.9.T. Birks, F. Luan, G. Pearce, A. Wang, J. Knight, and D. Bird, "Bend loss in all-solid bandgap fibres," Opt.Express 14, 5688-5698 (2006).10.K. P. Hansen, C. B. Olausson, J. Broeng, K. Mattsson, M. D. Nielsen, T. Nikolajsen, P. M. W. Skovgaard,M. H. Sørensen, M. Denniger, C. Jakobsen, and H. R. Simonsen, “Airclad fiber laser technology,” Proc.SPIE 6873, 687307 (2008).#98542 - $15.00 USD Received 8 Jul 2008; revised 15 Aug 2008; accepted 17 Aug 2008; published 20 Aug 2008 (C) 2008 OSA 1 September 2008 / Vol. 16, No. 18 / OPTICS EXPRESS 1365711.W. J. Wadsworth, R. M. Percival, G. Bouwmans, J. C. Knight, T. A. Birks, T. D. Hedley, and P. S. J.Russell, "Very High Numerical Aperture Fibers," IEEE Photonics Tech. Lett. 16, 843-845 (2004).12. A. Cerqueira S. Jr., F. Luan, C. Cordeiro, A. George, and J. Knight, "Hybrid photonic crystal fiber," Opt.Express 14, 926-931 (2006).13.J. K. Lyngsø, B. J. Mangan, and P. J. Roberts, "Polarization Maintaining Hybrid TIR/Bandgap All-SolidPhotonic Crystal Fiber," in Conference on Lasers and Electro-Optics/Quantum Electronics and LaserScience Conference and Photonic Applications Systems Technologies, OSA Technical Digest (CD) (Optical Society of America, 2008), paper CThV1.14.N. M. Litchinitser, S. C. Dunn, B. Usner, B. J. Eggleton, T. P. White, R. C. McPhedran, and C. Martijn deSterke, "Resonances in microstructured optical waveguides," Opt. Express 11, 1243-1251 (2006).1. IntroductionIn photonic bandgap (PBG) fibres light is confined within a low-index core by a microstructured cladding typically formed by silica and air. In this work an all-solid PBG fibre is used in which the PBG cladding is made by a triangular lattice of germanium-doped high-index micro-rods in a silica background, which raise the overall cladding index as in [1], while the core consists of a single ytterbium-doped micro-rod as gain medium. Combining the wavelength filtering effect of PBG confinement with an ytterbium-doped core results in efficient suppression of amplified spontaneous emission (ASE) at the conventional ytterbium gain wavelengths around 1030 nm and thus a reduction in parasitic lasing outside the bandgap, which typicially limits the operation of long wavelength fibre lasers and amplifiers [2]. Frequency doubled fibre lasers and amplifiers around 1180 nm [3,4] are of interest for yellow light generation in medical and astronomical application, while frequency quadrupling of fibre lasers can generate narrow linewidth UV light in the range 255 nm – 295 nm for applications in atomic physics [5]. Previous work on the use of the photonic bandgap filtering effect for shorter wavelength laser operation at 907 nm and 980 nm is reported in [6,7].In this paper, we demonstrate suppression of ASE for two different all-solid PBG fibres with different bandgap positions. We show that the ASE peak can be shifted towards longer wavelengths by rescaling the dimensions of the fibre and thereby moving the bandgap. It has been shown that the ASE peak of an all-solid PBG fibre can be shifted towards longer wavelengths by reducing the coiling diameter [8], however, this method works by and suffers from significant bend losses [9]. With the present approach, we show that tight coiling of the fibre is not necessary in order to shift towards longer wavelengths. Furthermore, we demonstrate that the amplification in the fibres scales with the ASE power for a given wavelength.a b cFig. 1. (a) Microscope image of the fibre structure. The lighter regions are the germanium-doped rods constituting the pump-cladding, while the two darker regions are the boron rods. (b)Microscope image of the core region. (c) Microscope image of the airclad surrounding thepump-cladding structure.2. Fibre propertiesTwo all-solid photonic PBG fibres were fabricated with a cladding pitch of 9.45 μm and 9.80 μm, respectively. The signal core consists of an ytterbium-doped rod, which is index matched to the silica background. The core is surrounded by the PBG pump-cladding structure made#98542 - $15.00 USD Received 8 Jul 2008; revised 15 Aug 2008; accepted 17 Aug 2008; published 20 Aug 2008 (C) 2008 OSA 1 September 2008 / Vol. 16, No. 18 / OPTICS EXPRESS 13658by an eight period triangular lattice structure of high-index germanium-doped rods. For the two fibres we measured the diameter of the cladding to 214 μm and 220 μm, respectively. Both fibres have pump absorption of 1.1 dB/m at 976 nm. Furthermore, the PBG pump cladding is surrounded by an airclad structure providing the pump guide with a large numerical aperture of 0.57, allowing for efficient high-power cladding-pumping [10,11].The polarization-maintaining properties of the fibre are obtained by incorporating two low index boron-doped rods on either side of the core. The boron-doped rods act as stress applying parts, inducing high birefringence in the fibre while the lower index results in confinement by total internal reflection (TIR) in one direction and bandgap guiding in other directions [12]. The birefringence is on the order of 10-4.Microscope images of the fibre structure, the core and the airclad structure surrounding the pump cladding are shown in Fig. 1. The lighter regions are the germanium-doped rods, while the two darker regions near the core are the boron rods.Core properties of the fibre have been determined by performing measurements on a fibre which is identical to the fibre in question in terms of pump cladding and core properties, but without the surrounding airclad. Near-field measurements at 1150 nm yield a 1/e2 mode field diameter of 10.0 µm in the axis parallel to the stress rods, a mode field diameter of 10.8 µm in the axis perpendicular to the stress rods and an average numerical aperture of 0.1. A near field image taken in the third order bandgap using 1150nm light is shown in Fig. 2. The lack of an anti-resonant tail of light in the boron-doped stress rods on either side of the core is evidence of index guiding in the direction of the stress rods and bandgap guiding in the other direction.A passive version of this type of hybrid TIR / bandgap fibre has been reported in [13].Fig. 2. Near field CCD image taken in the third order bandgap using 1150 nm light, where thestress rods are in the horizontal direction. An anti-resonant tail of light is visible in thesurrounding high-index germanium-doped rods, but not in the boron-doped stress rods.Recently, ASE suppression in an ytterbium-doped all-solid photonic PBG fibre for long wavelength applications has been demonstrated [8]. The present fibre design is polarization-maintaining and holds potential for higher power due to the airclad surrounding the pump cladding.3. Suppression of amplified spontaneous emissionThe transmission spectrum of the fibres is measured using the setup in Fig. 3(a). In order to only transmit light in the core, light from a white light source is launched into 1 m of single-mode large mode area (LMA) fibre with a core size of 10 um, which is then butt-coupled to the 10 µm core of 30 m of the ytterbium-doped all-solid PBG fibre. The light from the core of the PBG fibre is subsequently collected by a high NA 10 µm core fibre in order to limit light collected by the optical spectrum analyzer (OSA) to the core region.#98542 - $15.00 USD Received 8 Jul 2008; revised 15 Aug 2008; accepted 17 Aug 2008; published 20 Aug 2008 (C) 2008 OSA 1 September 2008 / Vol. 16, No. 18 / OPTICS EXPRESS 13659Fig. 3. (a) Experimental setup for measuring the bandgap transmission spectrum and (b) setupfor measuring the ASE spectrum.The ASE spectrum in the core is measured using the setup shown in Fig. 3(b). The 976 nm pump light is launched into the pump cladding of the PBG fibre using a multi-mode fibre with a core size of 100 µm and the output core light is collected by the same high NA fibreFigure 5 shows the ASE spectra of the two different ytterbium-doped all-solid PBG fibres, one designed with a bandgap centered at 1140 nm (red) and another designed with a bandgap centered at 1180 nm (black). Results show that the peak of the ASE spectrum can be shifted towards longer wavelengths by moving the bandgap position in the fibre. This is done by rescaling the fibre dimensions in the drawing process.#98542 - $15.00 USD Received 8 Jul 2008; revised 15 Aug 2008; accepted 17 Aug 2008; published 20 Aug 2008 (C) 2008 OSA 1 September 2008 / Vol. 16, No. 18 / OPTICS EXPRESS 136604. Amplification and laser propertiesThe amplification properties of the fibres are measured using the forward seeded amplification setup depicted in Fig. 6. The PBG fibre is pumped with up to 3 W of 980 nm light and seeded with 2 mW of 1080 nm – 1145 nm light from a laser cavity created from 30 m of the same PBG fibre and a laser dispersing prism. The seed laser cavity is tuned using a mirror. Furthermore, the pump light is launched at an angle in order to reduce guidance in the high-index rods and obtain maximum pump absorption.Fig. 6. Amplification setup using forward seeding with a seed setup tunable in the range 1080nm – 1145 nm.The amplification results for the two PBG fibres are presented in Fig. 7. For both fibres results show that the amplification for a given wavelength scales with the ASE power. For the specified pump power an amplification of up to 15dB is obtained in both fibres. Peak amplification occurs at the wavelengths that experience the least loss due to the bandgap combined with the highest gain due to their emission cross section. Increasing the pump power will shift the ASE peak, and hence also the peak amplification, towards the left bandgap edge.#98542 - $15.00 USD Received 8 Jul 2008; revised 15 Aug 2008; accepted 17 Aug 2008; published 20 Aug 2008 (C) 2008 OSA 1 September 2008 / Vol. 16, No. 18 / OPTICS EXPRESS 136618(b) the ASE suppression is apparent in the output power spectrum outside the bandgap, when the fibre with a bandgap centered at 1180 nm is lasing at exactly the edge of the bandgap.can open new possibilities for high-power ytterbium-doped fibre lasers and amplifiers lasing at longer wavelengths above the conventional ytterbium gain wavelengths.#98542 - $15.00 USD Received 8 Jul 2008; revised 15 Aug 2008; accepted 17 Aug 2008; published 20 Aug 2008 (C) 2008 OSA 1 September 2008 / Vol. 16, No. 18 / OPTICS EXPRESS 13662。
光学工程的英语文献

光学工程的英语文献English:For English literature on optical engineering, one can delve into various aspects of the field ranging from fundamental principles to advanced applications. A good starting point might be textbooks like "Optical Engineering Fundamentals" by Bruce H. Walker, which covers the basic principles of optics, including geometrical optics, wave optics, and optical system design. For those interested in more specialized topics, journals like the "Journal of the Optical Society of America A" and "Optics Express" offer a plethora of research papers on cutting-edge advancements in optical science and engineering. Topics covered in these journals include but are not limited to optical imaging, photonics, laser technology, optical materials, and computational optics. Additionally, conference proceedings from events like the "SPIE Optical Engineering + Applications" conference provide insights into the latest developments and innovations in the field. These resources collectively offer a comprehensive overview of the current state and future directions of optical engineering, catering to both beginners and seasoned professionals.中文翻译:对于光学工程的英文文献,人们可以深入研究该领域的各个方面,从基本原理到先进应用。
高分辨率手机镜头的光学设计与性能仿真外文翻译原文

Open Access Library JournalDesign of a 16.5 Megapixel Camera Lens fora Mobile PhoneYuke Ma, V. N. BorovytskyDepartment of Optical and Optoelectronic Devices, National Technical University of Ukraine, Kyiv, UkraineEmail: sherry_rain@Received 15 February 2015; accepted 2 March 2015; published 6 March 2015Copyright © 2015 by authors and OALib.This work is licensed under the Creative Commons Attribution International License (CC BY)./licenses/by/4.0/AbstractA 16.5 megapixel camera lens for a mobile phone is designed. The lens consists of 3 plastic as-pheric lenses, one glass spheric lens and an infrared glass filter. CMOS OV16850 with a pixel size of1.12 micrometers from Omni Vision is used as an image sensor. The lens has an effective focal lengthof 4.483 mm, a F-number of 2.50, a field-of-view (FOV) of 76.2 degree, and a total length of 5.873 mm.The maximum distortion of the lens is less than 2.0%. The minimum value of all field relative il-lumination is over 39.8%.KeywordsMobile Phone Camera Lens, 16.5 Megapixel Sensor, ZemaxSubject Areas: Mobile Computing Systems, Optical Communications1. IntroductionOn 7 October 2014, Omni Vision Technologies Inc. (NASDAQ:OVTI) announced a 16.5 megapixel digital im-age sensor OV16850 [1]. To design a 16-megapixel camera lens in a compact size is not a trivial task [2]. In the published papers, Song et al. (2010) [3] studied a 5 megapixel camera lens for mobile phone by a structure of 4 pieces of plastic aspheric lens. Recently, Peng (2013) [4] investigated a 8 megapixel camera lens for cell phone by using 1 glass and 3 pieces of plastic aspheric lens (1G3P) to complete the optical system. Yin et al. (2014) [5] investigated a 13 megapixel camera lens for mobile phone by choosing a 5 pieces of plastic aspheric lens (5P) structure configuration.This paper presents a detailed design of a 16.5 megapixel camera lens by a 1P1G2P lens configuration for the first time to our knowledge.Sensor OV16850 has the following specifications: pixel size of 1.12 micrometers, resolution of 5408 pixel × 3044 pixel, diagonal length of 6.95 mm or the image height, and the chief ray angle (CRA) of 33.4 degree. Ny-quist sampling frequency of the sensor can be calculated via 1000/(2 × 1.12) = 446 lp/mm. So the limited reso-Y. K. Ma, V. N. Borovytsky lution of the camera lens should be better than 446 lp/mm. An image height of 6.95 mm and a FOV of 76.2 de-gree of lens determine a focal length of 4.432 mm. We set the effective focal length (EFFL) of the lens to be less than 4.5 mm, so the total optical length (TOL) of a camera lens for a mobile phone can be confined to 5.90 mm. The specification parameters for a 16.5 M pixel mobile phone camera lens are summarized in Table 1.2. Design Method2.1. Optical MaterialsOptical resin E48R from Zeonex [6] is used in this design. The optical resin offers high transparency, low fluo-rescence, low birefringence, low water absorption, low cost, high heat resistance, and easy molding for massive production. Since the lens has a large FOV, and its high order optical aberrations such as high order spherical aberration, astigmatism, coma, high order chromatic aberrations, etc., is rather large, in order to have a more steady and clear picture, one element of the lens is set to be an aspheric glass lens, the material of the 2nd ele-ment is SF56A with a optical refractive index of 1.785 and a dispersion coefficient of 26.08, the first, the third and the fourth element of the lens are chosen to be E48R, whose optical refractive index is 1.531 and the cor-respondent dispersion coefficient is 56.0, the fifth element is an infrared filter (IR), and the last is a cover glass BK9.2.2. Design ProceduresZemax [7] is used to simulate the lens optical system. Considering low price and massive production, an initial configuration 1P1G2P of the lens is chosen for the design by trial and error process. There are 6 elements in this lens, the first to the fourth element is the aspheric lens respectively, the fifth element is an IR filter and the sixth is a glass cover of the sensor. All the surfaces of the element 1 to 4 are set to even aspheric profiles, the fifth and the sixth elements are plane. Radius, thickness of each surface from 1 to 8 is set to be variable, all surface conic constants as well as aspheric coefficients are set to be variable either.2.3. Optimization ProceduresThe optimization procedure includes three steps.Step 1 1) Using operand EFFL to define the effective focal length of the lens, using operand TOTR to confine the total optical length of the lens system, using operand RAID to confine the CRA, using operand REAY to de-fine the image height; 2) The merit function also consisted of operands MNCA, MXCA and MNEA to define the air thickness and air boundary constrains, meanwhile operands MNCG, MXCG and MNEG are used to glass case either; 3) Initially, operand LONA is used to control the spherical aberration, LACL is used to control the lateral color for this focal system. TRAY and SUMM are used to control the coma, and operand DIMX is used to control the distortion of each field of view; 4) Using operand TRAY, DIFF, RAGC, ACOS and TANG to control tangential curvature; 5) Using operand TRAY, DIFF, RAGC, ACOS, TANG, CONS and PROD to con-trol sagittal curvature; 6) Operand TRAC is used to control the spot size of each field of view for the whole wa-velength.Step 2 After the initial optimization, high order controlling operands are added in the merit function, i.e., 1) Using operand TRAY, RAGC, ACOS, TANG, DIVI and DIFF to control the axial and longitudinal chromatic aberrations; 2) Using operand TRAY, RAGC, ACOS, TANG, DIVI, CONS, PROD and DIFF to control the high order spherical aberration; 3) Using TRAY, DIVI and DIFF to control the high order chromatic spherical aber-ration; 4) Using FCGT, FCGS, DIFF and SUMM to control the astigmatism.Step 3 Siedel coefficients are observed after each optimization completed, the layout is watched to show a reasonable configuration. At last, 1) Both MTFS, MTFT is added to the merit function to improve the lens reso-lution; 2) Meanwhile TRAC is replaced by operand OPDX; 3) Weight in merit function is always ready to change to optimize some heavy contribution items in order to get a reasonable lens configuration.Table 1.The specification parameters for a mobile phone camera lens of 16.5 megapixels.EFFL TOL FOV F-number Image height CRA Relativeillumination distortionBack focal length<4.5 mm <5.9 mm 76.2 degree 2.50 >6.95 mm <33.4 degree >35% <2% >0.2 mmY. K. Ma, V. N. Borovytsky3. ResultsThe optimized lens configuration is shown in Figure 1, the correspondent lens data are listed in Table 2 and Table 3. The lens has a total track of 5.873 mm, with an effective focal length of 4.483 mm, and of a back focal length 0.207 mm. The lens has a FOV of 76.2 degree, the image height is 6.97 mm which is a little larger than the CMOS sensor size and implies an easy installation of the CMOS sensor to the lens module. The CRA is less than 33.4 degree; a good coupling between the optics and the COMS is expected.The Spot Diagram, MTF, curvature and distortion, lateral color, chromatic focal shift, and relative illumina-tion can be used to evaluate the lens design. The RMS radius of spot size shall be less than three times of the pixel size (Yu [8]), to this design, it is 3.36 micrometer. The RMS spots of all fields are shown in Figure 2. The RMS spot radius of fields 1 - 6 (FOV 0.000 to FOV 0.787) is 2.545 μm, 2.761μm, 2.662μm, 2.856 μm, 2.337 μm, and 2.091μm respectively, much less than the imaging needs of the CMOS sensor, meanwhile the radius of spot size of field 7 (FOV 0.92) is 5.641 μm and that of field 8 (FOV 1.0) is 4.985μm, very close to this need, that is to say that the whole FOV can image very clearly.Table 2. Lens configuration data.Surf: type Radius Thickness Glass Semi-diameter Conic OBJ Standard Infinity Infinity Infinity 0.000STO Even asphere 3.134 1.413 E48R 1.077 4.1312 Even asphere −3.115 0.021 1.233 1.6043 Spheric −2.252 0.445 SF56A 1.219 0.0004 Spheric −9.057 0.512 1.346 0.0005 Even asphere −4.306 1.378 E48R 1.409 4.8686 Even asphere −2.443 0.938 1.823 −1.2047 Even asphere −2.310 0.354 E48R 2.167 −8.7898 Even asphere −5.332 0.300 3.174 1.6419 Standard Infinity 0.313 BK7 3.222 0.00010 Standard Infinity 0.200 3.344 0.000IMA Standard Infinity 3.485 0.000 Table 3. Aspheric coefficients of each correspondent surface. Aspheric coefs A B C D E F G HSTO Evenasphere 0.050 −0.015 −5.30E-003 −3.136E-003 −3.048E-003 0.000 0.000 0.0002 Evenasphere −0.043 −0.015 −0.012 3.559E-003 −2.045E-003 0.000 0.000 0.0003 Evenasphere 0.000 0.000 0.000 0.000 0.000 0.000 0.000 0.0004 Evenasphere 0.000 0.000 0.000 0.000 0.000 0.000 0.000 0.0005 Evenasphere 0.093 −0.033 −1.072E-003 −3.462E-003 −4.413E-004 0.000 0.000 0.0006 Evenasphere −0.060 9.480E-003 −2.006E-003 −9.711E-004 −1.576E-004 1.665E-003 0.000 0.0007 Evenasphere −0.101 −6.280E-003 1.653E-003 −1.796E-003 3.519E-004 4.051E-005 −9.441E-006 0.0008 Evenasphere 0.196 −0.012 1.030E-003 3.686E-007 −1.956E-006 −4.296E-007 5.719E-008 −3.874E-010Y. K. Ma, V. N. BorovytskyFigure 1. 16.5 M pixels mobile phone camera lens layout.Figure 2. 16.5 M pixels mobile phone camera lens spot diagram.Y. K. Ma, V. N. Borovytsky MTF is a comprehensive standard to evaluate the imaging nature of a lens. In this design, the MTF value of central field at 223 lp/mm is 53.4% and 21.4% at 446 lp/mm. For FOV 0.8 zone, MTF value at 223 lp/mm is more than 37.6% in sagittal plane and more than 32.6% in tangential plane, at 446 lp/mm, MTF value is more than 14% in sagittal plane and more than 2% in tangential plane. The MTF curve is shown in Figure 3.The curvature and distortion of the lens is shown in Figure 4; it is shown in Figure 4 that the lens has a low field curvature; it is within 0.05, much less than the imaging need 0.1, and the distortion is less than 2%. It meets the design need.Figure 3.16.5 M pixels mobile phone camera lens MTF curve.Figure 4. Field curvature and distortion of a 16.5 M pixels mobile phone camera lens.Y. K. Ma, V. N. Borovytsky Both the lateral color and chromatic focal shift of the lens revealed a nearly diffraction limited design of this 16.5 M pixels mobile phone camera lens. They are shown in Figure 5 and Figure 6 respectively. In Figure 5, the lateral color of the maximum field is within the Airy disk which implies a diffraction limited design.It is also indicated in Figure 6that the chromatic focal shift of the lens is within diffraction limited. Relative illumination of the lens should be checked; it is shown Figure 7. It can be found in Figure 7that the minimum of the relative illumination value is 40%. Both an auto gain controlling circuit and an auto balance controlling circuit can keep a uniform brightness of the image. It is concluded that this design of a 16.5 M pixels mobile phone camera lens can meet the design needs.Figure 5.The lateral color of a 16.5 M pixels mobile phone camera lens.Figure 6.Chromatic focal shift of a 16.5 M pixels mobile phone camera lens.Y. K. Ma, V. N. BorovytskyFigure 7.Relative illumination of a 16.5 M pixels mobile phone camera lens.At last, a tolerance analysis was made and the results show that a 5 μm deviation in radius, thickness, a 10μm deviation in decenter, and a 0.2 degree in tilt are permitted. It is also shown in Table 2 that the smallest thick-ness of the plastic piece is 0.354 mm which means that a precision injection molding for massive production of the plastic lens elements can be expected. The glass element for this design is set to be a standard spheric surface for an easy production consideration.In conclusion, this 16.5 M pixels mobile phone camera lens is a practical design.4. ConclusionBy using Zemax, a 16.5 M pixels mobile phone camera lens is designed. The lens consists of 3 plastic aspheric lenses, one glass spheric lens and an infrared glass filter. OV16850 whose pixel size of 1.12 micrometer from Omnivision is used as a image sensor. The lens has an effective focal length of 4.483 mm, a F-number of 2.50, a field-of-view (FOV) of 76.2 degree, and a total length of 5.873 mm. This is a practical design for a 16.5 M pix-els mobile phone camera lens.References[1]Geary, J.M. (2002) Introduction to Lens Design with Practical Zemax Example. Willmann-Bell Inc., Richmond.[2]Zhang, P., et al. (2009) Design of a 5 Megapixel Mobile Phone Camera Lens. Journal of Applied Optics, 30, 934-938.[3]Song, D.F., et al. (2010) Design of Lens for 5 Mega-Pixel Mobile Phone Cameras. Journal of Applied Optics, 31, 34-38.[4]Peng, X.F. Design of High Pixel Mobile Phone Camera Lens. Research Journal of Applied Sciences, Engineering andTechnology, 6, 1160-1165.[5]Yin, Z.D., et al. (2014) Optical Design of a 13 Megapixel Mobile Phone Camera Lens. Laser & Optoelectronics Progress,51, 163-168.Y. K. Ma, V. N. Borovytsky[6]World’s Foremost Optical Polymer for Precision-Molded Optics. /optics.aspx[7][8]Yu, D.Y. (1999) Engineering Optics. China Mechanical Press, Beijing.。
光学外文书籍
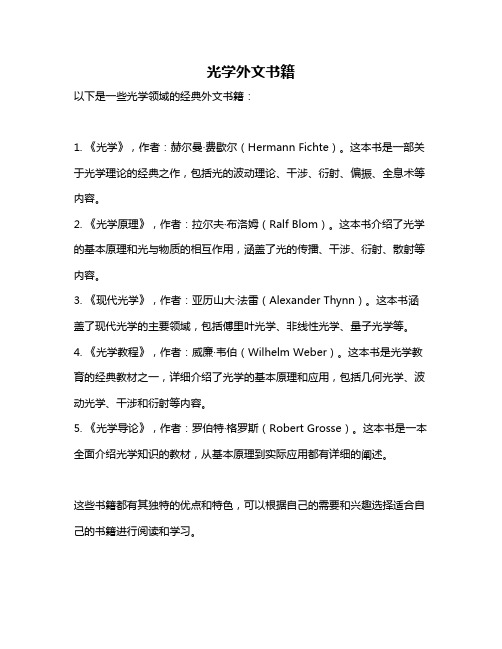
光学外文书籍
以下是一些光学领域的经典外文书籍:
1. 《光学》,作者:赫尔曼·费歇尔(Hermann Fichte)。
这本书是一部关于光学理论的经典之作,包括光的波动理论、干涉、衍射、偏振、全息术等内容。
2. 《光学原理》,作者:拉尔夫·布洛姆(Ralf Blom)。
这本书介绍了光学的基本原理和光与物质的相互作用,涵盖了光的传播、干涉、衍射、散射等内容。
3. 《现代光学》,作者:亚历山大·法雷(Alexander Thynn)。
这本书涵盖了现代光学的主要领域,包括傅里叶光学、非线性光学、量子光学等。
4. 《光学教程》,作者:威廉·韦伯(Wilhelm Weber)。
这本书是光学教育的经典教材之一,详细介绍了光学的基本原理和应用,包括几何光学、波动光学、干涉和衍射等内容。
5. 《光学导论》,作者:罗伯特·格罗斯(Robert Grosse)。
这本书是一本全面介绍光学知识的教材,从基本原理到实际应用都有详细的阐述。
这些书籍都有其独特的优点和特色,可以根据自己的需要和兴趣选择适合自己的书籍进行阅读和学习。
光电信息工程外文翻译文献
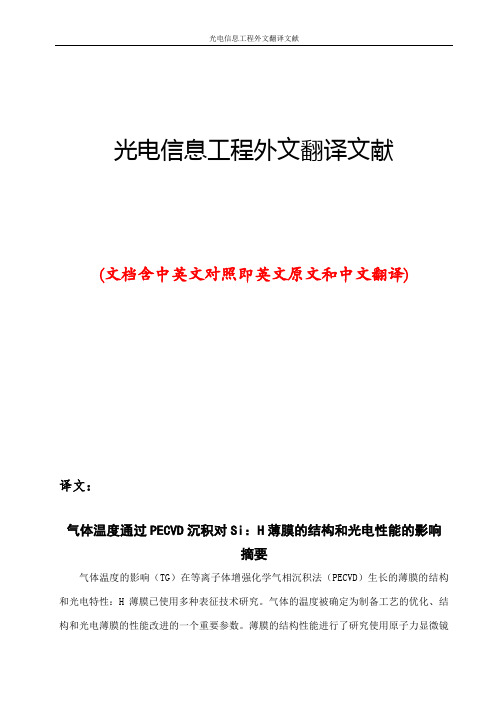
光电信息工程外文翻译文献(文档含中英文对照即英文原文和中文翻译)译文:气体温度通过PECVD沉积对Si:H薄膜的结构和光电性能的影响摘要气体温度的影响(TG)在等离子体增强化学气相沉积法(PECVD)生长的薄膜的结构和光电特性:H薄膜已使用多种表征技术研究。
气体的温度被确定为制备工艺的优化、结构和光电薄膜的性能改进的一个重要参数。
薄膜的结构性能进行了研究使用原子力显微镜(AFM),傅立叶变换红外光谱(FTIR),拉曼光谱,和电子自旋共振(ESR)。
此外,光谱椭偏仪(SE),在紫外线–可见光区域的光传输的测量和电气测量被用来研究的薄膜的光学和电学性能。
它被发现在Tg的变化可以修改的表面粗糙度,非晶网络秩序,氢键模式和薄膜的密度,并最终提高光学和电学性能。
1.介绍等离子体增强化学气相沉积法(PECVD)是氢化非晶硅薄膜制备一种技术,具有广泛的实际应用的重要材料。
它是用于太阳能电池生产,在夜视系统红外探测器,和薄膜晶体管的平板显示装置。
所有这些应用都是基于其良好的电气和光学特性以及与半导体技术兼容。
然而,根据a-Si的性质,PECVD制备H薄膜需要敏感的沉积条件,如衬底温度,功率密度,气体流量和压力。
许多努力已经花在制备高品质的薄膜具有较低的缺陷密度和较高的结构稳定性的H薄膜。
众所周知,衬底温度的强烈影响的自由基扩散的生长表面上,从而导致这些自由基更容易定位在最佳生长区。
因此,衬底温度一直是研究最多的沉积参数。
至于温度参数在PECVD工艺而言,除了衬底温度,气体温度(Tg)美联储在PECVD反应室在辉光放电是定制的a-Si的性能参数:H薄膜的新工艺。
事实上,TG PECVD系统的变化可以影响等离子体的能量在辉光放电,并最终改变了薄膜的性能。
根据马丁吕,当薄膜制作接近前后颗粒的形成机制在a-Si∶H薄膜,薄膜性能对TG的相关性比衬底温度更为显著。
然而,大多数的研究到目前为止只集中在衬底温度的影响。
在我们以前的研究中,我们报道的气体温度对磷的结构演化的影响掺杂的a-Si∶H薄膜的拉曼光谱。
光学设计常用术语解释及英汉对照翻译汇总
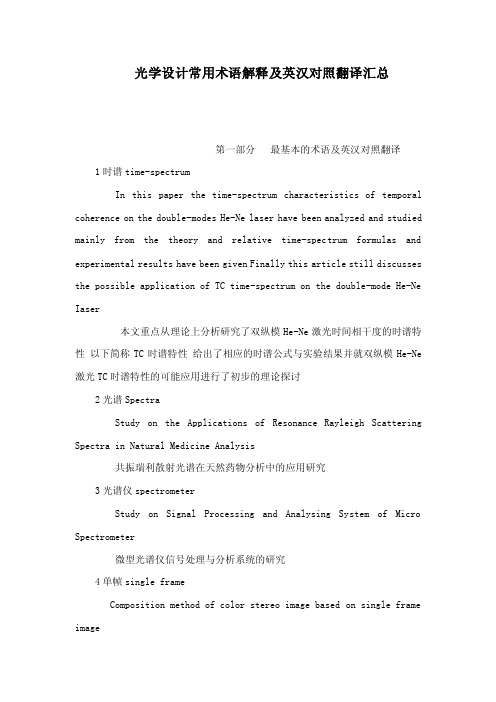
光学设计常用术语解释及英汉对照翻译汇总第一部分最基本的术语及英汉对照翻译1时谱time-spectrumIn this paper the time-spectrum characteristics of temporal coherence on the double-modes He-Ne laser have been analyzed and studied mainly from the theory and relative time-spectrum formulas and experimental results have been given Finally this article still discusses the possible application of TC time-spectrum on the double-mode He-Ne Iaser本文重点从理论上分析研究了双纵模He-Ne激光时间相干度的时谱特性以下简称TC时谱特性给出了相应的时谱公式与实验结果并就双纵模He-Ne 激光TC时谱特性的可能应用进行了初步的理论探讨2光谱SpectraStudy on the Applications of Resonance Rayleigh Scattering Spectra in Natural Medicine Analysis共振瑞利散射光谱在天然药物分析中的应用研究3光谱仪spectrometerStudy on Signal Processing and Analysing System of Micro Spectrometer微型光谱仪信号处理与分析系统的研究4单帧single frameComposition method of color stereo image based on single frame image基于单帧图像的彩色立体图像的生成5探测系统Detection SystemResearch on Image Restoration Algorithms in Imaging Detection System成像探测系统图像复原算法研究6超光谱Hyper-SpectralResearch on Key Technology of Hyper-Spectral Remote Sensing Image Processing超光谱遥感图像处理关键技术研究7多光谱multispectral multi-spectral multi-spectrumSimple Method to Compose Multi spectral Remote Sensing Data Using BMP Image File用 BMP 图像文件合成多光谱遥感图像的简单方法8色散dispersionResearches on Adaptive Technology of Compensation for Polarization Mode Dispersion偏振模色散动态补偿技术研究9球差spherical aberrationThe influence of thermal effects in a beam control system and spherical aberration on the laser beam quality 光束控制系统热效应与球差对激光光束质量的影响10慧差comaThe imum sensitivity of coma aberration evaluation is about λ25 估值波面慧差的极限灵敏度为λ25 11焦距focal distanceAbsolute errors of the measured output focal distance range from –120 to 120μm 利用轴向扫描法确定透镜出口焦距时的绝对误差在–120120μm之间12物距object distanceOn the basis of computer calculations for a series of image tubes we proposed an approximation for structure characteristic parameter K characterizing the internal connection between magnification Mobject distance P and image distance Q of an electron-optical system 本文在对象管的一系列计算基础上进一步提出表征电子光学系统放大率M物距P与象距Q之间内在联系的结构特征参数K的近似值第二部分常用的光学设计术语的英汉对照翻译及基本解释光学系统的名词解释aperture stop孔径光阑 4U dB限制进入光学系统之光束大小所使用的光阑 \hH-[Wastigmatism像散 RlbD一个离轴点光源所发出之光线过透镜系统后子午焦点与弧矢焦点不在同一个位置上 0"H0marginal ray边缘光束 QUkl4由轴上物点发出且通过入射瞳孔边缘的光线 zQ ]_chief ray主光束 8 LQy0u[由离轴物点斜向入射至系统且通过孔径阑中心的光线 SFa_4fchromatic aberration色像差8ZW4g _不同波长的光在相同介质中有不的折射率所以轴上焦点位置不同因而造成色像差 LQrhBqcoma慧差 uO4 r当一离轴光束斜向入射至透镜系统经过孔径边缘所成之像高与经过孔径中心所成之像高不同而形成的像差 AJX Zddistortion畸变 2gYrq像在离轴及轴上的放大率不同而造成分为筒状畸变及枕状畸变两种形式 39YJD entrance pupil入射瞳孔 UaleW由轴上物点发出的光线经过孔径阑前的组件而形成的孔径阑之像亦即由轴上物点的位置去看孔径阑所成的像 yVskexit pupil出射瞳孔 T4 P 2T由轴上像点发出的光线经过孔径阑后面的组件而形成的孔径阑之像亦即由像平面轴上的位置看孔径阑所成的的像 d pc3G rfield curvature场曲 NQDf所有在物平面上的点经过光学系统后会在像空间形成像点这些像点所形成的像面若为曲面则此系统有场曲 T Iqfield of view视场视角物空间中在某一距离光学系统所能接受的最大物体尺寸此量值以角度为单位 edom2-Pf-number焦数 5Q G有效焦距除以入射瞳孔直径的比值其定义式如下有时候f-number也称为透镜的速度 4 f 的速度是2 f 速度的两倍 yqs"WJ7qmeridional plane子午平面 r 0dFypF在一个轴对称系统中包含主光线与光轴的平面BH"pmqnumerical aperture数值孔径 ExQ1折射率乘以孔径边缘至物面像面中心的半夹角之正弦值其值为两倍的焦数之倒数数值孔径有物面数值孔径与像面数值孔径两种 nGI 9tsagittal plan弧矢平面纬平面 VIqztL]包含主光线且与子午平面正交的平面 I mS 4nsagittal ray弧矢光束纬光束 Mlr\U所有由物点出发而且在弧矢平面上的斜光线 2r4BK3ray-intercept curve光线交切曲线]G_ N_\子午光线截在像平面上的高度相对于经过透镜系统后发出之光线的斜率之关系图或是定义为经过透镜系统后的光线位移相对于孔径坐标的图此两种定义法可依使用者需要选择在OSLO 中采用后者 Buh jDGspherical aberration球差 RDkfg近轴光束与离轴光束在轴上的焦点位置不同而产生 Lx mvignetting渐晕光晕 tn2]n离轴越远越接近最大视场的光线经过光学系统的有效孔径阑越小所以越离轴的光线在离轴的像面上的光强度就越弱而形成影像由中心轴向离轴晕开 BQHvl jP 角放大率 ZA-q_bk近轴像空间主光线角与近轴物空间主光线角的比率叫做角放大率角的测量与近轴入瞳和出瞳的位置有关 lIaqUd切迹法 LK ErUtJm切迹法指的是系统入瞳的连续均匀的光线选择默认瞳处的光线总是连续均匀的然而有时也会有非连续均匀的光线在这种情况下ZE支持光瞳切迹法也就是改变光瞳处的光波振幅有三种类型的切迹均匀型高斯型矩阵型对每一种类型除连续均匀以外切迹因素取决于光瞳处振幅的变化率 mJpvU7n后焦长度ZE定义的后焦长度是沿着Z轴的方向最后一个玻璃面到像面的距离如果没有玻璃面后焦的长度是Surface1到近轴像面的距离 7 jEKc主像面主像面有时又叫主点指的是物和像空间共轭位置有特定的放大率主像面包括放大率为+1的平面角放大率为+1的节平面放大率为-1反节面和放大率为0的像方焦平面和物方焦平面除了焦平面之外其他主像面之间也相互构成共轭面也就是说像空间的主像面与物空间的主像面是共轭面等等如果透镜的物空间和像空间有相同的折射率那么节面与主像面重合 AR8 59主光线 UgN如果没有护真光阑和像差则把从一特定场点穿过入瞳中央到达像面的光线称作主光线注意到没有护真光阑和像差则任何穿过入瞳中央的光线将穿过光阑和出瞳 U0PQ\o当考虑到护真光阑则主光线的定义为只穿过光阑中央不一定穿过光阑中央的光线如果有光瞳像差这是客观存在的那么主光线可以穿过近轴入光瞳如果不用准直或光阑中央用准直但一般说来不会二者同时存在 a -IJMZE从不用主光线来计算主要的计算是参考主要的或中央光线注意质心参数优于主光线因为他在像面上受到的干扰小 n0 qf坐标轴系 Z afgw光学轴是Z轴光线开始传播的方向是Z轴的正方向在传播方向上加一块平面镜会使传播反向坐标系尊从右手定则传播方向是从左向右沿着Z轴正方向经过奇数平面镜之后光线指向Z轴负方向因此经过奇数平面镜之后所有的厚度是负的 su ] v衍射极限衍射极限指的是一个光学系统的性能受到衍射的物理机制的限制而不是设计或者制作的不完整性普遍的约定是系统的衍射极限是根据光程差来计算或度亮的如果波峰到波谷的OPD光程差小于波长的四分之一那么就说系统处于衍射极限 38E这里还有许多方式决定系统的衍射极限例如施特雷尔比在同一系统里形成的有象差点像的衍射图峰值与无象差的峰值亮度之比用于像质的评价RMS OPD标准背离最大斜差对一个系统来说用这种方法是衍射极限而另一种不是衍射极限这是可能的 Q8n关于一些ZE的图例如MTF或Diffraction Encircled energy衍射能量圈图等衍射极限的光学表示衍射极限的响应是显而易见的这些数据通常根据视场域的某一参考点的追踪光线计算出来的光瞳迹变护真光阑F表面孔径等等都和传输有关但不管实际的光路怎样光程差都定为0对于系统来说如果场角在00点处则参考点的位置在坐标轴场点如果不定义00点那么场点通常有11代替边缘厚度YUqdqg]边缘厚度的求解可以改变中心厚度也就是边缘厚度的求解可改变接下来的一个表面的入射光线意思是下一表面的半径会改变如果下一表面的半径用边缘厚度来计算就会出现infinite loop或者circular definition因为这个原因边缘厚度求解计算的边缘厚度严格的针对第一和第四表面尽管第二表面的曲率和形状被用到但从来未涉及到它的半径[R6OZ]y有效焦距 b_jL3w _后主像面到近轴像面的距离他的计算是不断变化的主像面的计算总是根据近轴光线数据既使像空间的折射率不是1有效焦距也总是以10的折光线为参考 R-nJ 2dt入光瞳直经 E93入光瞳直径等于物空间中用透镜单位表示的近轴像光阐的大小 O KS1rG8入光瞳位置 hE_2近轴入光瞳的位置与系统的第一表面相联系第一表面不是物面surface 0而是surface1 K puI[0出光瞳直径 G F\ vNX[出光瞳直径等于近轴像空间用透镜单位表示的近轴像光阐的大小 Z1WzQR近轴出光瞳的位置相联系于像表面_4 up场角和高度 46CEo场点可被定义为角物高对系统来说是有限别性的共轭面近轴像高和真实像高z9eA"pL场角通常是用度数表示的度数是根据物空间的近轴入瞳的位置来度量的 Yb 94 浮动光阐大小 oLG] 8AvZE支持系统的浮动光阐的定义指的是入瞳位置物空间的数值孔径像空间的F及表面光阐的曲率半径因此设半径相应的其他表面的值也随之而定这种是定义孔径的最有效的方法尤其在设置虚拟的光学校正面时很方便玻璃 THZh9Za玻璃的输入是根据LDE的Glass列空缺代表空气折射率为1还可以通过输入MIRROR来定义平面镜通过glass catalog tool得到所有的玻璃目录 ND Hexapolar rings [N[P66\m]ZE通常选择一定光线模式来作为通用的计算例如点图光线模式指的是进入初瞳的一系列模式The hexapolar模式是旋转轴对称用环绕中央光线的环数来表示第一个环包括6束光线第二个环12束第三个环18束如此类推 ca4像空间工作数F jW81 q J像空间工作数F是近轴有效焦距比上近轴入瞳的直径 EdHUSB像空间数值孔径NA szDCG_fY像空间数值孔径用主波长来计算 bjs\c\47透镜单位 32\3PXkw透镜单位主要用来度量透镜系统包括毫米厘米英寸米 rcdaBIN边缘光线n边缘光线指的是从物中心到入瞳边缘在像平面成像的光线sl非近轴系统 Te 3AA非近轴系统指的是不能用近轴光线充分描述的系统 "9xvhbU归一化场域和光瞳坐标 k5 Zj bZE程序和文件中经常用到归一化场域和光瞳坐标四个归一化坐标HxHyPxand PyHx和Hy值是归一化场域坐标Px Py是归一化光瞳坐标 MKvZ[j归一化场域和光瞳坐标用一个单位圆来表征视场半径的大小或者物高是归一化场域坐标的范围入瞳的半经用来限制归一化光瞳坐标例如假如最大物高是10mm 如果定义了3个场域分别在0710mm坐标Hx 0Hy 1指的是物空间 YmjF]光线的开始位置是x 0mmy 10mm坐标 Hx -1Hy 0 指物体 x 10mmy 0mm 光瞳的坐标也是同样的方式表式假如入瞳的半径不是直径是8mm那么Px 0Py 1指的是入瞳顶端边缘的光线则在入瞳表面光线的坐标是x 0y 8 QRSPSK注意归一化坐标总是位于-1到1之间采用归一化坐标的优点是某一条光线总是有同样的坐标例如边缘光线的坐标总是Hx 0Hy 0Px 0Py 1主光线的坐标总是Hx 0Hy 1 Px 0Py 1系统应用归一化坐标的另一个优点是当光瞳的大小和位置变化时仍然有意义假如要优化一个透镜设计您定义了计算系统绩效函数的光线通过应用归一化坐标当光瞳的大小和位置或物的大小和位置改变了或者正在优化之中同样的光线仍然适用 \Kt h0k归一化视场坐标的角位置用度数定义例如假定您选择y-field的角度是0710度就表示您的最大场角是10度则归一化场角的坐标Hx 0Hy 1表示x-field是0度y-field是10度归一化场角的坐标Hx -05Hy 04表示x-field是-5度y-field 是4度注意到如果没有x-field您可以用一个非0的Hx来描光Hx和 Hy的值总是指被物方最大角空间限定的圆形区域如果您限定x-field是10度y-field是6度则最大圆形区域是1166度接着Hx和 Hy将受到这个半径的归一化 olB mj 注意如果用角定义那么坐标就是归一化视场坐标如果用物高定义那么坐标就是归一化物高坐标物空间数值孔径 VCZB G物空间数值孔径是度量从物方进入光线的散度数值孔径被定义作近轴边缘光线角的折射指数WA[R R近轴和parabasal光线 dUjG 1l近轴光线是指可以用斯涅尔定理来描述的光线斯涅尔定理是对于小角度可改写为公式可以参看手册在光学中的大量定义是遵循这种线性关系失常指的是偏离这种性质因此近轴光学系统经常忽略这种失常即认为它是线性的 b尽管这个数字化的公式用来计算近轴模型很简便例如焦距F放大率等等但ZE通常不用这些公式而是用parabasal光线通常是坐标或者主光线来计算 bOgu8kj ZE用parabasal光线的原因是很多系统包括非近轴成分 z[Gqub近轴像高 JTv2rn5在近轴像平面上近轴像的半径大小叫近轴像高 t qSph近轴放大率 jl DDt a近轴像高和物高的比率叫近轴放大率它在近轴像平面测量无限大共轭系统的近轴放大率是0 c rXa近轴工作数F fy28Htd有效的忽略失常的工作数F叫近轴工作数F 3xT]BS4Yt主波长 Xe 1jPJ主波长用微米表示用来计算系统的其他值 qm2曲率半径G用透镜单位度量的每一表面的弯曲程度 8z\ Wk-mz表面光圈 v Mke表面光圈包括圆形矩形椭圆形和网孔形用户还可以自己定义光圈和光阑浮动光圈是基于半径值而定义的表面光圈对系统光圈没有影响 oXbRG6ma系统光圈 Xo7dVX系统光圈是系统F入瞳直径数值孔径或光闸四个中的任何一个足以定义其他三个系统光圈用来定义物空间的入瞳直径反过来发射所有的光线系统光圈只是圆形的而且只有一个系统光圈厚度 YgKkN用透镜单位表示的这一表面到下一表面的相对距离厚度不是累计的每一个值都是独一无二的且沿着Z轴的方向 SxJqPXpn总迹 XBgYB\F8总迹指的是光学系统最左面到最右面的长度从第一表面开始计算任何一个位于表面1和像平面间的厚度都考虑了忽略坐标旋转 78 T Z渐晕因子 WR97 5渐晕因子是描述入瞳大小和不同场角位置的系数ZE有五个渐晕因子VDXVDYVCXVCYVAY这些因素表征偏轴量选择默认代表把他们设为0表示没有渐晕Mi Lr9光学系统的视场角和入瞳可以看坐是一个单位圆而前面所说的归一化场域和光瞳坐标是两个单位圆如果没有渐晕ZE在大部分计算中将会描绘所有的光线Dysn"很多光学系统都要精选光阑这就是意味着一部分光线将被挡去放置光谰的原因是第一在广角透镜中降低了透镜的大小第二可以除去一部分过分偏轴的光线放置光谰通常使场角函数的F值增加这样会使像变暗但是大部分偏轴光线被除去后可以提高像的质量 g 4h工作数F O8Xey G工作数F比像空间工作数F更有用因为它是基于真实光线数据计算的 E7M入射瞳孔 hHVdA1u由轴上物点发出的光线经过孔径光阑前的元件而形成的孔径光阑的像亦即由轴上物点的位置去看孔径光阑所成的像孔径光阑在物空间的共轭像入瞳和出瞳对整个系统来说显然是物和像的关系 "-07[X出射瞳孔 fY G由轴上物点发出的光线经过孔径光阑后面的元件而形成的孔径光阑的像亦即由像平面轴上的位置去看孔径光阑所成的像出瞳距离最小为6㎜在军用光学仪器中由于考虑倒加眼罩和在戴防毒面具的情况下仍能观察出瞳距离一般为20㎜左右焦数x0l有效焦距除以入射瞳孔直径的值有时也称透镜的速度 u5G_YK[子午平面 GMEFeH [O1在一个轴对称系统中包含主光线与光轴的平面 z[弧矢平面 zfQXwer包含主光线且与子午平面正交的平面 -d "Q eU弧矢光束 wuoORZgP所有由物点出发而且在弧矢平面上的斜光线 O PGjA光线交切曲线 VV子午光线截在像平面上的高度相对于经过透镜系统后发出的光线的斜率的关系图或者定义为经过透镜系统后的光线位移相对于孔径坐标的图 eCAN渐晕 pZ K"Z-离轴越远越接近最大视场的光线经过光学系统的有效孔径越小所以越离轴的光线在离轴的像面上的光强度就越弱而形成影像由中心向离轴晕开Mwc体视 -q UTC当观察外界物体时除了能够知道物体的大小形状亮度以及表面颜色以为还能够产生远近的感觉这种远近的感觉的感觉称为空间深度感觉无论是用单眼或者双眼观察时都能产生但是双眼的深度感觉比单眼的强得多也在正确得多我们把这种双眼的深度感觉称为双眼立体视觉简称为体视 ew 8om为了使人眼能够形成良好的体视感双眼仪器左右两个光学系统必须满足以下的要求 lw2 9zV1双眼仪器左右两个光学系统的光轴要平行 a i2两个光学系统的视放大率要一致 qb kpum3两个光学系统之间不应该有相对的像倾斜景深 qI"rKehjA0空间物体成像的清晰度景深能在像面上获得晰度像的物空间深度就是系统的景深在几何光学中将像平面上允许的最大光斑直径作为景深标准 x N2rC3光线追迹 XXDw依次按照在每个面入射高和会聚角的数值求出光线光路的过程 2s vqf物方顶焦距 NRy]dqKT自光学系统第一面顶点到系统物方焦点的距离 iKFcqp物方截距 o5aNVFU自顶点到入射光线与光轴交点的距离 scwi像方顶焦距CXMQs像方焦点离开最后一面顶点的距离称为像方顶焦距\9H像方截距 Gh- 6ltC自顶点到出射光线与光轴交点的距离 jI1" z主平面 49I N垂轴放大率等于1的一对共轭面 oO q2e焦物距 r pCEr自光学系统物方焦点到轴上物点的距离焦像距 HF qAq自光学系统像方焦点到轴上像点的距离Wg节平面 4CN fGMe"角放大率等于1的一对共轭面 nntfp光焦度 pCQyq Cn像方折合焦距的倒数 0daDHr视度 D"7-D与网膜共轭的物面到眼睛距离的倒数 a 0o A8视见函数 9Uldz光度学中为了表示人眼对不同波长辐射的敏感度差别定义了一个函数Vλ称为视见函数在可见光范围内人眼对黄绿光最敏感V555 1 tz0Dht主观光亮度 1R noI外界物体通过眼睛成像在视网膜上刺激视神经细胞引起视觉的强度称为主观光亮度1对于发光点来说当望远镜的出瞳直径大于瞳孔直径时如果忽略系统的光能损失通过望远镜观察时的主观光亮度等于人眼直接观察时主观光亮度的Г2倍2对于发光面来说使用望远镜观察时的主观光亮度永远小于眼睛直接观察时主观光亮度这与发光点的情况完全不同 [FNOk消色差物镜 ipWg"两条谱线之间的轴向色差经过校正的物镜 L9T-Hk复消色差物镜 wVj ymLN三条谱线之间的轴向色差经过校正的物镜变形系统 i s8gm9A使物体在长宽两个方向上按不同的比例成像的光学系统 CmLFt"Pl变焦距系统77M e焦距在一定范围内改变而保持像面不动的光学系统 jSQU HC调焦镜 xn4"W光学系统的一部分通过其移动能配合系统物面位置改变保持光学系统成像在原位置上cjx光圈数 CEMYy gZ被检光学表面与其参考光学表面曲率半径有偏差时所产生的干涉圈数 FBwy[x 光圈局部误差 "P\vh被检光学表面与其参考光学表面产生的干涉条纹的不规则程度r PmN"O标准样板精度 Ur\U\y标准样板的曲率半径名义值与其曲率半径实际值的偏差 zBJQ光学零件气泡度1ab R光学零件在一定范围内含有的气泡的大小和个数4 镜头总长和光学总长 TTL 光学总长是指从系统第一个镜片表面到像面的距离而镜头总长是指最前端表面一般指Barrel表面到像面例如Sensor 表面的距离一般来说镜头太长或太短其设计都会变得困难制造时对工艺要求较高示意图如下页 UNION的镜头规格书中图面所标注的E即为机械总长5 机械后焦 MBF 和光学后焦机械后焦是指从镜头机械后端面到像面的距离而光学后焦是指从镜头最后一个镜片的最后一面到像面的距离它们两者的差别随不同光学系统的不同而不同同时在光学行业内对光学后焦也有两种表达联合光电目前采用光学后焦1的描述6最佳对焦距离和景深景深反映一个光学系统对空间物体成像清晰程度而最佳对焦距离是指一个光学系统景深最佳时的调焦距离这里讲的最佳在实际应用时其实是相对而言的对焦距离取决于使用者客户或消费者希望光学系统所能拍摄的距离范围7 光学畸变 Opt distortion 和TV畸变 TV distortion 畸变是指光学系统对物体所成的像相对于物体本身而言的失真程度光学畸变是指光学理论上计算所得到的变形度 TV畸变则是指实际拍摄图像时的变形程度 DC相机的标准是测量芯片 Sensor 短边处的变形一般来说光学畸变不等于TV畸变特别是对具有校正能力的芯片来说畸变通常分两种桶形畸变和枕形畸变比较形象的反映畸变的是哈哈镜使人变得又高又瘦的是枕型畸变使人变得矮胖的是桶型畸变8 相对照度 Relative illumination又简写为RI 它是指一个光学系统所成像在边缘处的亮度相对于中心区域亮度的比值无单位在实际测量的结果中它不仅同光学系统本身有关也同所使用的感光片 SENSOR 有关同样的镜头用于不同的芯片可能会有不同的测量结果9 最大出射角 chief angle 它是指光学系统镜头所能拍摄范围内的光主光线在通过光学系统镜头后到达像面如SENSOR 时同像面所成的最大夹角出射角越小设计越困难镜头的总长也会相对变长10 IR Filter 滤光片它主要用于调整整个系统的色彩还原性它往往随着芯片的不同而使用不同的波长范围因为芯片对不同波长范围的光线其感应灵敏度不一样对于目前应用较广的CMOS和CCD感光片它非常重要早期的CCD系统中采用简单的IRF往往还不能达到较好的色彩还原性效果11 MTF 它从一定程度上反映了一个光学系统对物体成像的分辨能力一般来说 MTF越高其分辨力越强 MTF越低其分辨力越低由于MTF也只是从一个角度来评价镜头的分辨率也存在一些不足故在目前的生产中大多数还是以逆投影检查分辨率为主12镜头样品生产周期1塑胶镜头塑胶镜片成形时间一般为6-8个小时镀膜5-6个小时组立4-8个小时检测及数据准备4-5个小时所以在没有库存而模具又能够及时切换的情况下从接到PO或联络到样品完成需要2-3天的时间2玻璃镜头周期比塑胶镜头周期长很多最简单的定焦镜头发出图纸时如果供应商已备好材料马上日夜加班加工零件我司接到零件后加班组装检测在一切顺利没有出现任何差错的情况下7天左右可提供样品一般只有最重要客户最重要机种不计代价时才会采用这种时间一般重要样品的要20天以上同供应商联系后确定时间为好。
外文翻译 光学
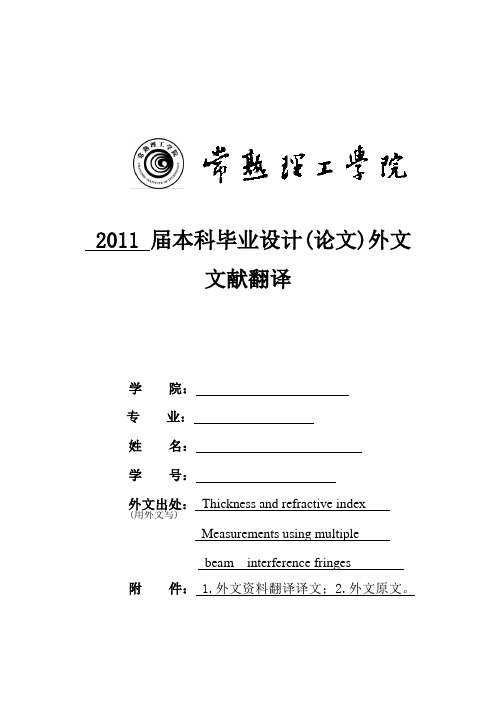
2011 届本科毕业设计(论文)外文文献翻译学院:专业:姓名:学号:外文出处:Thickness and refractive index(用外文写)Measurements using multiplebeam interference fringes附件: 1.外文资料翻译译文;2.外文原文。
使用多波束,干涉条纹测量厚度和折光率摘要我们报告中采用的光干涉仪利用在表面平等的彩色条纹确定了分离薄膜厚度和折射率在一个比较广的范围内。
特别是,在二边缘位置的未测量的基础上我们将展示如何计算两个表面分离距离(膜厚度)。
我们讨论了测量精度,尽管所有的距离理论精度是1Å,在实践中我们表明,在距离比较大的情况下很难达到这样的精度。
在表面力装置试验中,通常使用3或5层的干扰仪。
尽管虽然三层干涉仪分析适用于任何数量的层次,但是在这里我们使用3层干涉仪。
当透明的基质层(通常是云目表)接触时,pth-order 的边缘位置0p λ通常在可见光的波长范围内。
基板表面后,相隔的距离为d 的位置形成三层干涉。
边缘转移到更长的波长,他们的新位置D P λ根据所给公式2242sin()2tan()4(1)(1)cos()D P med D P D P Y D Y πμμλπμλπμμμλ=--+ (1),假设没有分散(我们在后面讨论这点),对上面的公式转化变成000102200112sin()12tan()1(1)cos()(1)1p D P p p med D P p D P p p D λλμπλλπμλλλμπμλλ----=-+±-- (1a ),其中Y 是每个基板光学厚度(我们将谈论光学与物理厚度之间的差别)μ =μ/ μ med,其中,μ(μγ或μβ)和μmed 分别是云母和中间介质的折射率,在式中。
(1a ),+和 - 分别指到p 奇数偶数阶边缘,也可用其他方法计算厚度(例如,参考[4]);然而简单的方程(1a )使其成为最常用的方法。
光学专业英语50句翻译
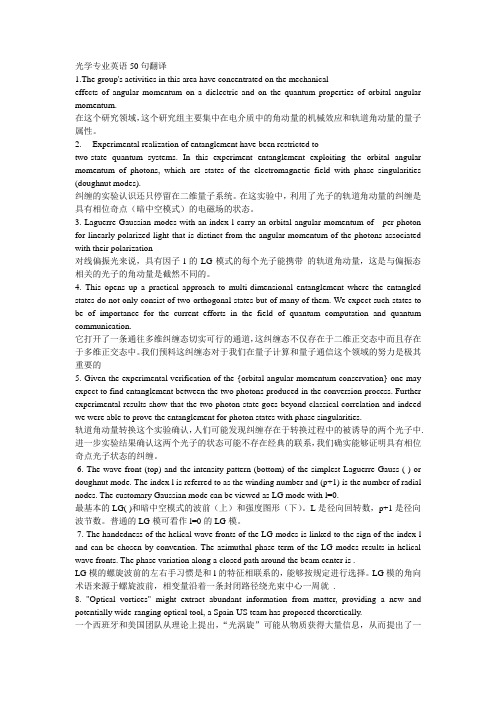
光学专业英语50句翻译1.The group's activities in this area have concentrated on the mechanicaleffects of angular momentum on a dielectric and on the quantum properties of orbital angular momentum.在这个研究领域,这个研究组主要集中在电介质中的角动量的机械效应和轨道角动量的量子属性。
2. Experimental realization of entanglement have been restricted totwo-state quantum systems. In this experiment entanglement exploiting the orbital angular momentum of photons, which are states of the electromagnetic field with phase singularities (doughnut modes).纠缠的实验认识还只停留在二维量子系统。
在这实验中,利用了光子的轨道角动量的纠缠是具有相位奇点(暗中空模式)的电磁场的状态。
3. Laguerre Gaussian modes with an index l carry an orbital angular momentum of per photon for linearly polarized light that is distinct from the angular momentum of the photons associated with their polarization对线偏振光来说,具有因子l的LG模式的每个光子能携带的轨道角动量,这是与偏振态相关的光子的角动量是截然不同的。
光学光刻中英文外文文献翻译
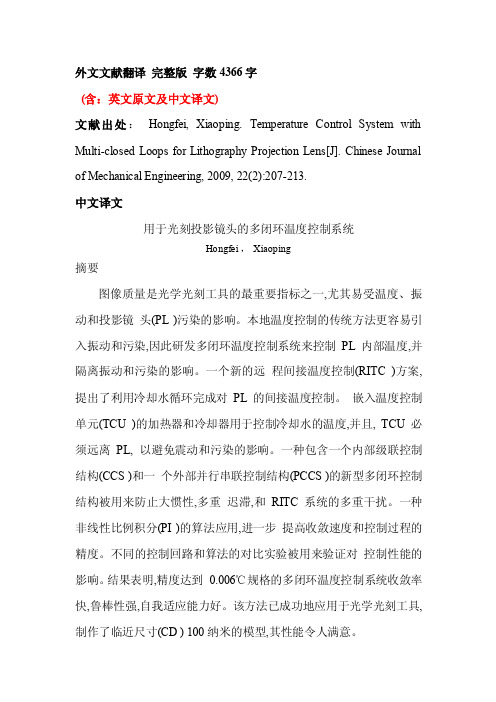
外文文献翻译完整版字数4366字(含:英文原文及中文译文)文献出处:Hongfei, Xiaoping. Temperature Control System with Multi-closed Loops for Lithography Projection Lens[J]. Chinese Journal of Mechanical Engineering, 2009, 22(2):207-213.中文译文用于光刻投影镜头的多闭环温度控制系统Hongfei , Xiaoping摘要图像质量是光学光刻工具的最重要指标之一,尤其易受温度、振动和投影镜头(PL )污染的影响。
本地温度控制的传统方法更容易引入振动和污染,因此研发多闭环温度控制系统来控制PL 内部温度,并隔离振动和污染的影响。
一个新的远程间接温度控制(RITC )方案,提出了利用冷却水循环完成对PL 的间接温度控制。
嵌入温度控制单元(TCU )的加热器和冷却器用于控制冷却水的温度,并且, TCU 必须远离PL, 以避免震动和污染的影响。
一种包含一个内部级联控制结构(CCS )和一个外部并行串联控制结构(PCCS )的新型多闭环控制结构被用来防止大惯性,多重迟滞,和RITC 系统的多重干扰。
一种非线性比例积分(PI )的算法应用,进一步提高收敛速度和控制过程的精度。
不同的控制回路和算法的对比实验被用来验证对控制性能的影响。
结果表明,精度达到0.006℃规格的多闭环温度控制系统收敛率快,鲁棒性强,自我适应能力好。
该方法已成功地应用于光学光刻工具,制作了临近尺寸(CD ) 100纳米的模型,其性能令人满意。
关键词:投影镜头,远程间接温度串级控制结构,并行串连控制结构,非线性比例积分(PI )的算法1引言由于集成电路缩小, 更小的临界尺寸(CD ) 要求, 生产过程的控制越来越严格。
作为最重要的制造工艺设备,先进的光学光刻工具需要更严格的微控制环境[1],如严格控制其温度、洁净度、气压、湿度等。
英文文献翻译

Preparation and characterization of Ag-TiO2 hybrid clusters powders[1](Ag-TiO2混合团簇粉末的制备和表征)Abstract:液相电弧放电法被用于制备纳米Ag-TiO2复合超细粉末。
XRD和TEM图表明颗粒呈葫芦状形态,分布狭窄。
我们讨论了实验条件对产品的影响,比较了这种方法制备的粉末和其他γ射线辐照法制备的粉末。
Introduction:材料合成技术,提高了研究特定电子和光学特性的能力。
这也导致了设备和不同效应的快速发展,如集成光学型偏振器[1]和量子霍耳效应。
所需的长度尺度对于这些结构的控制是在纳米级别的[ 2 ]。
科学家面临的一个新的挑战是半导体量子点的生长,它具有新的光学响应,引起了对其基础物理方面和三阶非线性光致发光的应用等的研究兴趣。
这方面的一个例子是Ag-TiO2复合材料通过胶体方法合成[ 3 ]或由γ射线辐照法合成[ 4 ]。
对比其他制备超细金属颗粒的方法,γ射线辐照法能在室温的环境压力下产生粉末。
在这封信中,我们开发了一种新的方法,即液相电弧放电法,用以制备纳米复合材料,当它经水热处理可以得到纳米级别的超细粉。
Preparation and photocatalytic activity of immobilized composite photocatalyst (titania nanoparticle/activated carbon)[2]固定化复合光催化剂(TiO2纳米颗粒/活性炭)的制备和光催化活性研究Abstract:制备了一种固定化复合光催化剂——TiO2纳米颗粒/活性炭(AC),并研究了它在降解纺织染料的光催化活性。
AC通过油菜籽壳制备。
碱性红18(BR18)和碱性红46(BR46)被用来作为模型染料。
并采用了傅里叶变换红外(FTIR),波长色散X射线光谱(WDX),扫描电子显微镜(SEM),紫外可见分光光度法,化学需氧量(COD)和离子色谱(IC)分析。
外文翻译中文

Research Journal of Applied Sciences, Engineering and Technology 6(1): 89-94, 2013ISSN: 2040-7459; e-ISSN: 2040-7467© Maxwell Scientific Organization, 2013Submitted: October 22, 2012 Accepted: December 14, 2012 Published: June 05, 2013LED照明系统的研究和设计摘要:在这项研究中,光学特性、热特性、电特性的LED装置进行了研究。
分析光学模型的重要性后,我们建立的模型LED光源使用光学仿真软件分析建模四个因素和法律的影响,基于射线跟踪模型的强度分布与制造商。
在此基础上,我们扩大了二次光学设计,即增加LDE 的方法光水平。
在比较不同形式的non-imaging光学组件,与实际情况相结合,最后的选择是与LDE旋转抛物面反射器组成的系统。
此外,反映LDE改变身体的相对位置和空间导致整个系统的正常光强度出现两个峰值,但他们的原因是不同的。
此外,理论分析和计算机模拟相结合的方法来研究LDE阵列照明是利用的分布。
LDB数组公式的照明分布推导出平面平行的另外,由计算机模拟验证和同意。
影响因素的定量研究路面照度分布是由以前的研究的基础上,结合实际的道路照明工程。
这些因素是:LDE数组形式,领导的数量,LDE LDE间距,路灯之间的时间间隔。
派生的整个道路照明分布公式和相应的曲线给出了基本方法分析实际问题的相关结果LDE照明光学系统设计和研究基础。
这些因素是:LDE数组形式,领导的数量,LDE LDE间距,路灯之间的时间间隔。
派生的整个道路照明分布公式和相应的曲线给出了基本方法分析实际问题的相关结果LDE照明光学系统设计和研究基础。
关键词:计算机模拟、LDE阵列、光学仿真软件,理论分析介绍:他半导体是一个21世纪的焦点和最引人注目的新技术相关领域的多元技术材料、设备结构、光学设计、包装技术、电源电路、灯、灯光效果和视觉匹配(Tsunemasa et al .,2004;Murakmai et al .,2000;Uehida et al .,2000;爱德华et al .,1997)。
外文翻译---复杂光学曲面慢刀伺服超精密车削技术研究

Study on the Technology of Slow Tool Servo Ultra-Precision Diamond Turning for Complex Optical SurfaceJournal of Manufacturing Systems V ol. 16/No. 1 1997 The inclusion of freeform elements in an optical system provides opportunities for numerous improvements in performance. However, designers are reluctant to utilize freeform surfaces due to the complexity and uncertainty of their fabrication. Single diamond turning is a novel machining process capable of generating freeform optical surfaces or rotational non-symmetric surfaces at high levels of accuracy. In order to achieve good results with this technology some key parameters need to be satisfied. These parameters include tool geometry, tool path generation, tool radius correction,and servo system performance. The servo capacity of slow-tool-servo machine is analysed, and a method to determine tool geometry parameter based on surface analysis is developed. The methods of tool radius compensation and tool path generation to ensure the stability of X-axis are researched. Experiment results show that slow-tool-servo machining technology can be used in preparation of optical free form surfaces elementSlow Tool Servo and Fast Tool Servo are the develop faster ultra-precision processing technology in the rencent , the two kind of technology can significantly improve the microstructure are arrays and free surface optical device processing efficiency.Slow Tool Servo is on the lathe spindle and turning the Z axis are control, make the spindle into position controllable C axis, machine Tool of the X and Z, C three axis in the space form the cylindrical coordinate system, at the same time, high performance and high programming of CNC system will resolution complex face form components of the three-dimensional cartesian coordinate into polar coordinates, and all moving axis to send interpolation into to instructions, precise coordination shaft and the relative motion of the cutting Tool, and to realize the complex face form of turning machining parts. Slow knife servo turning the Z axis X axis and often also make sine reciprocating motion, requires multi-axis interpolation linkage. Therefore, in the process of parts required before more face form the analysis of the coordination between the shaft, then determines the tool path and cutting tools compensation. In addition, slow sword by machine tool servo slide inertia and response speed and motor to influence is bigger, machine tool dynamic response speed is low, suitable for processing face form and larger complex for optical device.Fast Tool Servo turning and slow knife Servo differ in that will be processing complex shape face turning into shape face and form the microstructure of the surface, and then will both stack. The X axis and Z axis to realize the turn into shape trajectory, lathe spindle of only position detection do not track control. With installed in the Zaxis but independent of CNC outside the system of redundancy axes to drive the cutting tools, complete turning the surface microstructure form the Z axis movement. The processing method has high frequency, high stiffness, the characteristics of high precision.Diamond tools in piezoelectric actuators can be under the reciprocating movement of the Z axis. Control system in real-time acquisition spindle Angle signal, and on the basis of real-time sends out of control, real-time control tool to micro into, so as to realize the cutting tool tracking face form the rise and fall of the change. A sharp sword servo in processing only for parts before face form for accurate calculation, generation of the components of the form that can characterize data files. In addition, a sharp sword servo system frequency response high, the movement of the trip with only a few mm, more suitable for processing face form mutation or discontinuous, limited schedule tiny structures within.Freeform surfaces can be used in optical systems to achieve novel functions, improve performances, reduce size, and decrease the cost of various products. Therefore, optical freeform surfaces find applications in the fields of optics, medicine, fiber communication, life science, aerospace etc. Freeform optics has become the key element of quantitative light technology, which is becoming increasingly important in various fields. However, designers are reluctant to utilize freeform surfaces due to the complexity and uncertainty of their fabrication. Slow Slide Servo is a novel machining process capable of generating freeform optical surfaces or rotationally non-symmetric surfaces at high levels of accuracy. In order to achieve high accuracy optical complex surface by using Slow Tool Servo turning, the major research efforts include the following points.1. The theory of Slow Tool Servo turning and key technologies. A systematic introduction of the theory of Slow Tool Servo turning is first given by analyzing machine architecture and movements. By comparing with some other conventional technologies, the key technologies are high dynamic feed drive system, advanced interpolation technology and position control spindle technology. Then, the research emphasis on the performance of feed drive system and curve interpolation algorithm. Several aspects are discussed to improve the motion accuracy and control performance of feed drive system. PVT interpolation algorithm is introduced to Slow Tool Servo turning to overcome inherit drawback of conventional interpolation algorithm. In order to estimate the machining scope and accuracy, study on the machining capacity of Slow Tool Servo turning.2. The design theory of tool geometry parameters in ultra-precision Slow Tool Servo turning complex optical surface. Based on the requirements of slow tool servo, two types of tool are designed and analytic geometry models of cutting edge are built.A geometrical approach is introduced to formulate the relationship between tool tip and complex surface. By virtue of surface analytic method, the problem is solved efficiently, combined with the NURBS representation of complex surface. Experiments are carried out to validate solving algorithm. In addition, the relation models between tool shape and roughness, optical property and materials are built.3. The programming theory of tool path in ultra-precision Slow Tool Servoturning complex optical surface. In the basic design algorithm of complex optical surface slow tool servo turning, firstly study on the tool contact path design method and accuracy control skills of discrete process. Then, cutting edge compensation problem is considered. Two algorithms (normal direction compensation method and keeping X steady method) are proposed to avoid interfaces between surface and tool tip of zero rake angle. A tool path correct algorithm is developed to overcome over cutting and lack cutting due to non-zero rake angel. With regard to the calculate problem of tool path outer of surface region, space curve interpolation algorithm and surface continuation methods are proposed. In order to improve the manchining accuracy, error compensation algorithm is studied base on the tool path correction.4. The error model and simulation algorithm of Slow Tool Servo turning. Base on the discrete vector intersection, geometry simulation algorithm of slow tool servo turning is constructed. Then, major error sources and its transformations in complex surface turning are analyzed. An error model of slow tool servo turning is built base on multi-body theory. Experiments are carried out to validate simulation algorithm and error model.5. Finally, plentiful experiments are performed on a variety of complex optical surfaces including off-axis parabolic, array lenses, wave front correcting glass, spiral phase plate, continuous phase plate and so on. The successful machining results prove the validity and advantages of the proposed algorithms and the proposed process improvements.Slow knife servo turning the typical machine tool layout forms as shown in figure 1 shows, and common single point diamond turning and a sharp sword servo turning processing layout is similar. Two straight line into a "T" to shaft font layout. The main shaft is installed on the X axis. X axis direction of the movement and workpiece axis of vertical direction of the axis. Cutting tools installed in the Z axis, movement direction perpendicular to the X axis and the spindle and workpiece axis parallel. The installation in the spindle and then turn together, diamond tools according to the different Angle ϕ and radial position relative to the surface movement x, namely tool by cylindrical coordinate system should be movement.Fig.1 Configuration of slow-tool-servo turning latheThis in ultra-precision turning ordinary machine developed on the basis, the spindle movement speed control to the position control, use C, X, Z axis in polar coordinates or cylindrical coordinate system linkage realized in the rotary symmetrical surface processing method, because the Z axis motion drive tools can only achieve the highest dozens of Hertz, compared with a sharp sword hundreds, even thousands of Hertz sports slower so called slow knife servo technology.复杂光学曲面慢刀伺服超精密车削技术研究自由曲面光学元件具有许多优异的光学性能,越来越多地应用到现代光学系统设计中。
光学信息工程外文翻译
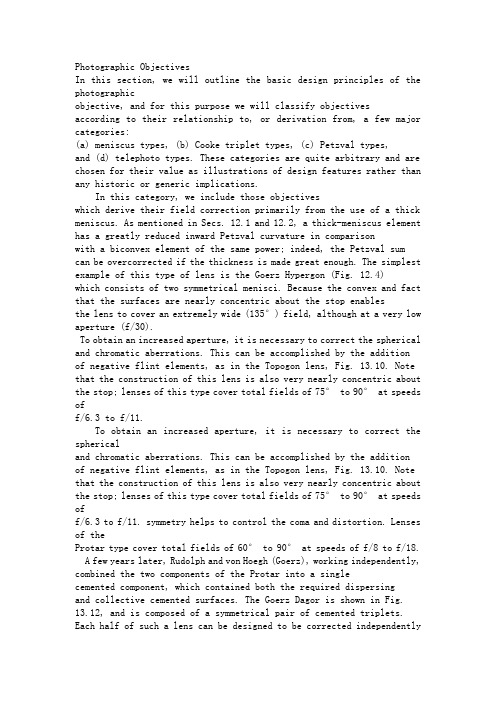
Photographic ObjectivesIn this section, we will outline the basic design principles of the photographicobjective, and for this purpose we will classify objectivesaccording to their relationship to, or derivation from, a few major categories:(a) meniscus types, (b) Cooke triplet types, (c) Petzval types,and (d) telephoto types. These categories are quite arbitrary and are chosen for their value as illustrations of design features rather than any historic or generic implications.In this category, we include those objectiveswhich derive their field correction primarily from the use of a thick meniscus. As mentioned in Secs. 12.1 and 12.2, a thick-meniscus element has a greatly reduced inward Petzval curvature in comparisonwith a biconvex element of the same power; indeed, the Petzval sum can be overcorrected if the thickness is made great enough. The simplest example of this type of lens is the Goerz Hypergon (Fig. 12.4)which consists of two symmetrical menisci. Because the convex and fact that the surfaces are nearly concentric about the stop enablesthe lens to cover an extremely wide (135°) field, although at a very low aperture (f/30).To obtain an increased aperture, it is necessary to correct the spherical and chromatic aberrations. This can be accomplished by the additionof negative flint elements, as in the Topogon lens, Fig. 13.10. Note that the construction of this lens is also very nearly concentric about the stop; lenses of this type cover total fields of 75° to 90° at speeds off/6.3 to f/11.To obtain an increased aperture, it is necessary to correct the sphericaland chromatic aberrations. This can be accomplished by the additionof negative flint elements, as in the Topogon lens, Fig. 13.10. Note that the construction of this lens is also very nearly concentric about the stop; lenses of this type cover total fields of 75° to 90° at speeds off/6.3 to f/11. symmetry helps to control the coma and distortion. Lenses of theProtar type cover total fields of 60° to 90° at speeds of f/8 to f/18.A few years later, Rudolph and von Hoegh (Goerz), working independently, combined the two components of the Protar into a singlecemented component, which contained both the required dispersingand collective cemented surfaces. The Goerz Dagor is shown in Fig. 13.12, and is composed of a symmetrical pair of cemented triplets. Each half of such a lens can be designed to be corrected independentlyso that photographers were able to remove the front component toget two different focal lengths. A great variety of designs based on this principle were produced around the turn of the century, using three, four, and even five cemented elements in each component, although very little was gained from the added elements. Protars and Dagors are still used for wide-angle photography because of the fine definition obtained over a wide field, especially when used at a reduced aperture. See Fig. 14.14 for an example of a Dagor design.The additional degree of freedom gained by breaking the contact of the inside crowns of the Dagor construction proved to be of more value than additional elements. Lenses of this type (Fig. 13.13) are probably the best of the wide-angle meniscus systems and cover fields upto 70° total at speeds of f/5.6 (or faster for smaller fields). The Meyer Plasmat, the Ross W. A. Express, and the Zeiss Orthometar are of this construction, and recently excellent 1:1 copy lenses (symmetrical) have been designed for photocopy machines. Note that the broken contact allows the inner crown to be made of a higher-index glass.The design of the thick-meniscus anastigmats is a complex undertaking because of the close interrelationship of all the variables. In general the exterior shape and thickness are chosen to control the Petzval sum and power, and the distance from the stop can be used to adjust the astigmatism. However, the adjustment of element powersto correct chromatic inevitably upsets the balance, as does the bending of the entire meniscus to correct spherical. What is necessary is one simultaneous solution for the relative powers, thicknesses, bendings, and spacings; an approach of the type described in Secs. 12.7 and 12.8 for the simultaneous solution of the third-order aberrations is ideally suited to this problem, and the automatic computer design programs make easy work of it.suited to this problem, and the automatic computer design programs make easy work of it.The double-Gauss (Biotar) (Fig. 13.14) and the Sonnar types (Fig.13.15) of objectives both make use of the thick-meniscus principle, although they differ from the preceding meniscus types in that they are used at larger apertures and smaller fields. The Biotar objective in its basic form consists of two thick negative-meniscus inner doublets and two single positive outer elements as shown in Fig. 13.14. This is an exceedingly powerful design form, and many high-performancelenses are modifications or elaborations of this type. If the vertex length is made short and the elements are strongly curved about the central stop, fairly wide fields may be covered. Conversely, a long system with flatter curves will cover a narrow field at high aperture.Common elaborations of the Biotar format include compounding the outer elements into doublets or triplets or converting the meniscusdoublets into triplets. Frequently the outer elements are split (after shifting some power from the inner crowns) in order to increase the speed. Some recent designs have advantageously broken the contact at the cemented surface, especially in the front meniscus.As indicated above, the double-Gauss (Biotar) is an extremely powerful and versatile design form. It is the basis of most normal focal length 35-mm camera lenses and is found in many applications where extremely high performance is required of a lens. It can be made into a wide-angle lens or can be modified to work at speeds in excess of f/1.0 with equal facility.。
- 1、下载文档前请自行甄别文档内容的完整性,平台不提供额外的编辑、内容补充、找答案等附加服务。
- 2、"仅部分预览"的文档,不可在线预览部分如存在完整性等问题,可反馈申请退款(可完整预览的文档不适用该条件!)。
- 3、如文档侵犯您的权益,请联系客服反馈,我们会尽快为您处理(人工客服工作时间:9:00-18:30)。
学号2013211033 昆明理工大学专业英语专业光学姓名辜苏导师李重光教授分数导师签字日期2015年5月6日研究生部专业英语考核In digital holography, the recording CCD is placed on the ξ-ηplane in order to register the hologramx ',y 'when the object lies inthe x-y plane. Forthe reconstruction ofthe information ofthe object wave,phase-shifting digital holography includes two steps:(1) getting objectwave on hologram plane, and (2) reconstructing original object wave.2.1 Getting information of object wave on hologram plateDoing phase shifting N-1 times and capturing N holograms. Supposing the interferogram after k- 1 times phase-shifting is]),(cos[),(),(),,(k k b a I δηξφηξηξδηξ-⋅+= (1) Phase detection can apply two kinds of algorithms:synchronous phase detection algorithms [9]and the least squares iterative algorithm [10]. The four-step algorithm in synchronous phase detection algorithm is in common use. The calculation equation is)2/3,,(),,()]2/,,()0,,([2/1),(πηξπηξπηξηξηξiI I iI I E --+=2.2 Reconstructing original object wave by reverse-transform algorithmObject wave from the original object spreads front.The processing has exact and clear description and expression in physics and mathematics. By phase-shifting technique, we have obtained information of the object wave spreading to a certain distance from the original object. Therefore, in order to get the information of the object wave at its initial spreading position, what we need to do is a reverse work.Fig.1 Geometric coordinate of digital holographyexact registering distance.The focusing functions normally applied can be divided into four types: gray and gradient function, frequency-domain function, informatics function and statistics function. Gray evaluation function is easy to calculate and also robust. It can satisfy the demand of common focusing precision. We apply the intensity sum of reconstruction image as the evaluation function:min ),(11==∑∑==M k Nl l k SThe calculation is described in Fig.2. The position occurring the turning point correspondes to the best registration distanced, also equals to the reconstructing distance d '.It should be indicated that if we only need to reconstruct the phase map of the object wave, the registration distance substituted into the calculation equation is permitted having a departure from its true value.4 Spatial resolution of digital holography4.1 Affecting factors of the spatial resolution of digital holographyIt should be considered in three respects: (1) sizes of the object and the registering material, and the direction of the reference beam, (2) resolution of the registering material, and (3) diffraction limitation.For pointx2on the object shown in Fig.3, the limits of spatial frequency are λξθλθθ⎥⎦⎤⎢⎣⎡⎪⎪⎭⎫ ⎝⎛-'-=-=-0211maxmax tan sin sin sin sin z x f R R Fig.2 Determining reconstructing distanceλξθλθθ⎥⎦⎤⎢⎣⎡⎪⎪⎭⎫⎝⎛-'-=-=-211minmintansinsinsinsin zxfRRFrequency range isλξξ⎥⎦⎤⎢⎣⎡⎪⎪⎭⎫⎝⎛-'-⎥⎦⎤⎢⎣⎡⎪⎪⎭⎫⎝⎛-=∆--211211tansintansinzxzxfso the range is unrelated to the reference beam.Considering the resolution of registering material in order to satisfy the sampling theory, phase difference between adjacent points on the recording plate should be less than π, namely resolution of the registration material.cfff=∆η21)(minmax4.2 Expanding the spatial resolution of reconstruction imageExpanding the spatial resolution can be realized at least in three ways: (1) Reducing the registration distance z0 can improve the reconstruction resolution, but it goes with reduction of the reconstruction area at the same ratio.Therefore, this method has its limitation. (2) Increasing the resolution and the imaging size of CCD with expensive price. (3) Applying image-synthesizing technique[11]CCD captures a few of images between which there is small displacement (usually a fraction of the pixel size) vertical to the CCD plane, shown in Fig.4(Schematic of vertical moving is the same).This method has two disadvantages. First, it is unsuitable for dynamic testing and can only be applied in the static image reconstruction. Second, because the pixel size is small (usually 5μm to 10μm) and the displacement should a fraction of this size (for example 2μm), it needs a moving table with high resolution and precision. Also it needs high stability in whole testing.In general, improvement of the spatial resolution of digital reconstruction is Fig.3 Relationship between object and CCDstill a big problem for the application of digital holography.5 Testing resultsFig.5 is the photo of the testing system. The paper does testing on two coins. The pixel size of the CCD is 4.65μm and there are 1 392×1 040 pixels. The firstis one Yuan coin of RMB (525 mm) used for image reconstruction by phase-shifting digital holography. The second is one Jiao coin of RMB (520 mm) for the testing of deformation measurement also by phase-shifting digital holography.5.1 Result of image reconstructionThe dimension of the one Yuancoin is 25 mm. The registrationdistance measured by ruler isabout 385mm. We capture ourphase-shifting holograms andreconstruct the image byphase-shifting digital holography.Fig.6 is the reconstructed image.Fig.7 is the curve of the auto-focusFig.4 Image capturing by moving CCD along horizontal directionFig.5 Photo of the testing systemfunction, from which we determine the real registration distance 370 mm. We can also change the controlling precision, for example 5mm, 0.1 mm,etc., to get more course or precision reconstruction position.5.2 Deformation measurementIn digital holography, the method of measuring deformation measurement differs from the traditional holography. It gets object wave before and after deformation and then subtract their phases to obtain the deformation. The study tested effect of heating deformation on the coin of one Jiao. The results are shown in Fig.8, Where (a) is the interferential signal of the object waves before and after deformation, and (b) is the wrapped phase difference.5.3 Improving the spatial resolutionFor the tested coin, we applied four sub-low-resolution holograms to reconstruct the high-resolution by the image-synthesizing technique. Fig.9 (a) is the reconstructed image by one low-resolution hologram, and (b) is the high-resolution image reconstructed from four low-resolution holograms.Fig.6 Reconstructed image Fig.7 Auto-focus functionFig.8 Heating deformation resultsFig.9 Comparing between the low and high resolution reconstructed image6 SummaryDigital holography can obtain phase and amplitude of the object wave at the same time. Compared to other techniques is a big advantage. Phase-shifting digital holography can realize image reconstruction and deformation with less noise. But it is unsuitable for dynamic testing. Applying the intensity sum of the reconstruction image as the auto-focusing function to evaluate the registering distance is easy, and computation is fast. Its precision is also sufficient. The image-synthesizing technique can improve spatial resolution of digital holography, but its static characteristic reduces its practicability. The limited dimension and too big pixel size are still the main obstacles for widely application of digital holography.外文文献译文:标题:图像重建中的相移数字全息摘要:相移数字全息术被用来研究研究艺术品的内部缺陷。