机加工表面质量标准
机加工表面质量标准

安徽铜陵松宝智能装备股份有限公司机加工零件外观检验标准1.范围本标准规定了无任何表面处理一般机加工件(机加工部位)在检验过程中外观可接收的标准。
2. 定义粗糙度:表面光洁程度。
撞伤:工件上的浅坑(人为原因碰撞导致的、非毛坯本身所具有的)。
划痕:浅的沟槽(其他锐利物导致表面划伤的痕迹)。
污渍:工件上的可见的油渍(加工、周转导致的油渍与污渍)。
毛刺:机加工后产生的尖锐突起、飞边等。
3. 外观等级分类3.1 产品分类:A. 一般结构件B. 轴类C. 其他类3.2 部件表面可见程度分类:Ⅰ.经常被注意到的(客户在使用时经常会看到的,正面的)。
Ⅱ.偶尔被注意到的(客户在使用时不经常看到的,侧面和底面的)。
Ⅲ.难以被注意的(只用在安装或维修时才能看到的,内部的)。
4. 职责品质检验负责对送检的零件按本标准进行检验,并判定合格或不合格。
5. 验收标准5.1 机加工件材料应符合图纸要求。
代用材料一律由设计技术员签字认可。
5.2 通用要求5.2.1 工件表面应没有污渍。
5.2.2 工件不得有锐边(以一般手指触摸没有扎手感),不得有毛刺。
5.2.3 表面粗糙度应符合图纸要求。
5.2.4 螺纹孔内不得有切削液,攻丝油等残留(防锈油除外)。
5.2.5 成品工件表面不允许有锈斑,锈迹。
5.3 表面撞伤,划伤判定标准注:表内缺陷数是在 60mmX100mm 范围内。
如物料还需要再进行表面处理,焊接等二次加工的,按不影响使用和二次加工判定。
如遇特殊异常(严重撞伤,明显有损观瞻的)由技术及品管协商处理。
6 包装和保护6.1 供方应采用合适的流转器具装运工件,避免跌落与磕碰。
6.2 如工件的表面要求比较高,应制作专用的流转器具或进行必要的包装。
拟制:审核:批准:。
五金机加工质量要求标准

五金机加工质量要求标准五金机加工质量要求标准五金机加工是制造业中非常重要的一个环节,它涉及到各种金属制品的加工和生产。
为了保证产品的质量,严格的质量要求标准是必不可少的。
下面将介绍五金机加工的质量要求标准,以便在实际操作中能够更好地进行控制和管理。
1. 尺寸精度要求在五金机加工过程中,尺寸精度是一个非常重要的指标。
产品的尺寸精度直接影响到产品的装配和使用。
因此,在加工过程中,必须严格控制产品的尺寸精度,确保其符合设计要求。
对于不同的产品,其尺寸精度要求也会有所不同。
在进行加工前,必须明确产品的尺寸精度要求,并在加工过程中进行相应的测量和调整。
2. 表面质量要求产品的表面质量直接影响到产品的外观和使用寿命。
在五金机加工过程中,必须严格控制产品的表面质量,确保其光洁度和平整度符合要求。
对于不同的产品,其表面质量要求也会有所不同。
在进行加工前,必须明确产品的表面质量要求,并在加工过程中进行相应的处理和检查。
3. 材料要求在五金机加工过程中,材料的选择对产品的质量有着重要的影响。
必须选择合适的材料,并对其进行相应的检验和测试,确保其符合产品的要求。
对于不同的产品,其材料要求也会有所不同。
在进行加工前,必须明确产品的材料要求,并采取相应的措施进行检验和测试。
4. 加工工艺要求在五金机加工过程中,加工工艺是一个非常重要的环节。
必须选择合适的加工工艺,并对其进行相应的调整和优化,确保产品能够达到设计要求。
对于不同的产品,其加工工艺要求也会有所不同。
在进行加工前,必须明确产品的加工工艺要求,并采取相应的措施进行调整和优化。
5. 检验标准要求在五金机加工过程中,检验是一个非常重要的环节。
必须建立完善的检验标准,并对产品进行相应的检验和测试,确保产品能够达到设计要求。
对于不同的产品,其检验标准要求也会有所不同。
在进行加工前,必须明确产品的检验标准要求,并采取相应的措施进行检验和测试。
综上所述,五金机加工质量要求标准是非常重要的,它直接关系到产品的质量和性能。
机械加工产品公差精度等级标准
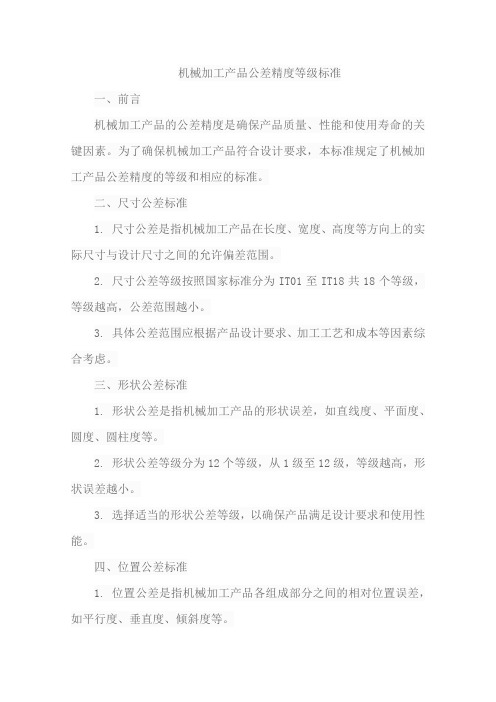
机械加工产品公差精度等级标准一、前言机械加工产品的公差精度是确保产品质量、性能和使用寿命的关键因素。
为了确保机械加工产品符合设计要求,本标准规定了机械加工产品公差精度的等级和相应的标准。
二、尺寸公差标准1. 尺寸公差是指机械加工产品在长度、宽度、高度等方向上的实际尺寸与设计尺寸之间的允许偏差范围。
2. 尺寸公差等级按照国家标准分为IT01至IT18共18个等级,等级越高,公差范围越小。
3. 具体公差范围应根据产品设计要求、加工工艺和成本等因素综合考虑。
三、形状公差标准1. 形状公差是指机械加工产品的形状误差,如直线度、平面度、圆度、圆柱度等。
2. 形状公差等级分为12个等级,从1级至12级,等级越高,形状误差越小。
3. 选择适当的形状公差等级,以确保产品满足设计要求和使用性能。
四、位置公差标准1. 位置公差是指机械加工产品各组成部分之间的相对位置误差,如平行度、垂直度、倾斜度等。
2. 位置公差等级分为11个等级,从1级至11级,等级越高,位置误差越小。
3. 选择适当的位置公差等级,以确保产品装配精度和使用性能。
五、表面粗糙度标准1. 表面粗糙度是指机械加工产品表面微观几何形状的不平度。
2. 表面粗糙度等级分为Ra、Rz、Ry等多种评定参数,每个参数分为不同等级,等级越高,表面越光滑。
3. 选择适当的表面粗糙度等级,以确保产品表面质量和使用性能。
六、材料公差标准1. 材料公差是指机械加工产品所用材料的物理性能、化学成分等与设计要求之间的允许偏差范围。
2. 材料公差标准应根据产品使用环境和性能要求综合考虑,选择符合国家标准和行业标准的材料。
七、热处理公差标准1. 热处理公差是指机械加工产品在热处理过程中产生的尺寸、形状和性能变化与设计要求之间的允许偏差范围。
2. 选择适当的热处理工艺和参数,以确保产品热处理后的稳定性和性能。
八、装配公差标准1. 装配公差是指机械加工产品在装配过程中各零部件之间的相对位置误差和配合间隙。
机械加工工艺流程检验标准及规范
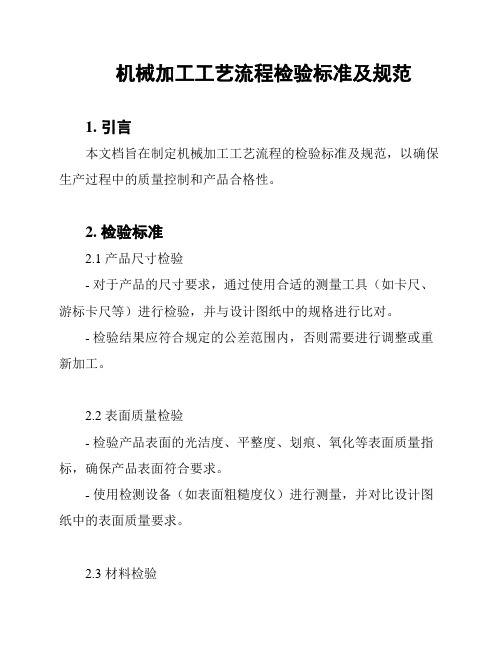
机械加工工艺流程检验标准及规范1. 引言本文档旨在制定机械加工工艺流程的检验标准及规范,以确保生产过程中的质量控制和产品合格性。
2. 检验标准2.1 产品尺寸检验- 对于产品的尺寸要求,通过使用合适的测量工具(如卡尺、游标卡尺等)进行检验,并与设计图纸中的规格进行比对。
- 检验结果应符合规定的公差范围内,否则需要进行调整或重新加工。
2.2 表面质量检验- 检验产品表面的光洁度、平整度、划痕、氧化等表面质量指标,确保产品表面符合要求。
- 使用检测设备(如表面粗糙度仪)进行测量,并对比设计图纸中的表面质量要求。
2.3 材料检验- 对使用的材料进行检验,确保其符合设计要求和相关标准。
- 检查材料的外观、密度、硬度等指标,并与相关标准进行对比。
2.4 装配与安装检验- 对于需装配和安装的零部件,进行装配和安装前的检验,确保其符合设计要求。
- 检验装配和安装的精度、间隙、螺纹连接等,并根据相应标准进行评估。
2.5 功能性检验- 对产品的功能进行检验,确保其符合设计要求。
- 进行实际操作或使用测试设备进行功能性测试,并进行性能指标评估。
3. 规范3.1 检验程序规范- 制定机械加工工艺流程的检验程序规范,定义各项检验的顺序和方法。
- 确保检验过程的可追溯性和一致性。
3.2 检验记录规范- 规定检验过程中产生的记录方法和要求。
- 记录检验结果、异常情况、处理措施等信息。
3.3 不合格品处理规范- 规定不合格产品的处理流程和责任分工,并制定相应的纠正和预防措施。
4. 结论制定机械加工工艺流程的检验标准及规范对于保证产品质量和生产效率具有重要意义。
本文档提出了产品尺寸、表面质量、材料、装配与安装、功能性等方面的检验标准,并规定了相应的检验程序和记录规范,以及不合格品的处理规范。
机械加工质量控制标准

机械加工质量控制标准在机械制造领域中,机械零部件的质量是至关重要的。
为了确保机械零部件的加工质量,我们需要遵守一定的标准和规范。
本文将介绍机械加工质量控制标准。
一、加工质量要求机械零部件的加工质量要求包括尺寸精度、形位公差、表面质量等方面的要求。
在进行加工之前,需要明确零部件的加工质量要求,并在加工过程中严格控制,以保证最终产品的质量。
1. 尺寸精度尺寸精度是衡量机械零部件加工质量的重要指标之一。
尺寸精度一般分为公差等级,根据零部件的实际要求选择适当的公差等级。
加工过程中需采用合适的加工工艺和设备,保证尺寸精度的达到要求。
2. 形位公差形位公差是衡量机械零部件几何形状和位置精度的指标。
对于要求较高的零部件,需要在制定工艺方案和选择设备时考虑形位公差的控制。
在加工过程中,应严格按照设计要求进行加工,保证形位公差的控制。
3. 表面质量零部件的表面质量对于产品的整体外观和性能有较大的影响。
在机械加工过程中,应注重工艺操作的细节,控制好加工参数和刀具状况,保证零部件的表面光洁度和无明显缺陷。
二、加工工艺要求机械加工工艺是保证零部件加工质量的重要环节。
在加工过程中,应根据零部件的具体要求和材料特性,合理选择加工工艺和设备,并制定相应的操作规程。
1. 工艺路线在制定加工工艺时,需要明确每道工序的加工内容和顺序。
合理的工艺路线可以最大程度地减少加工扭曲和变形,提高零部件的加工精度。
2. 加工方法不同的零部件可能采用不同的加工方法,如车削、铣削、钻削、磨削等。
选择合适的加工方法需要考虑加工效率和加工质量的平衡,确保加工过程中的稳定性和准确性。
3. 刀具选择刀具是机械加工中不可或缺的工具,合适的刀具选择能够有效地提高加工质量。
在选择刀具时,需要考虑加工材料的硬度、表面光洁度等因素,并结合具体的加工操作进行选用。
三、设备要求机械加工设备对于加工质量的控制至关重要。
高精度、稳定性好的设备能够提供良好的加工基础,保证零部件加工质量的稳定性和可靠性。
机械加工生产标准

机加工生产标准1.目的对机加工产品质量控制,以确保满足公司的标准和客户的要求。
2.范围适用所有机加工产品,和对供应商机加工产品的要求及产品的检验。
3.定义3.1A级表面:产品非常重要的装饰表面,即产品使用时始终可以看到的表面。
3.2 B级表面:产品的内表面或产品不翻动时客户偶尔能看到的表面。
3.3 C级表面:仅在产品翻动时才可见的表面,或产品的内部零件。
4.机加工的要求43p&K~7u0m4.1机加工件材料要符合图纸,选用的材料的符合国家标准。
4.2机加工件图纸未注尺寸公差参考国家标准线性尺寸的未注公差GB/T1804-f要求进行检验。
4.3机加工件图纸未注角度公差参考国家标准角度的未注公差GB/T11335-m要求进行检验。
4.4机加工件图纸未注形位公差参考国家标准形位的未注公差GB/T1184-H 要求进行检验。
4.5图纸中尺寸标注为配合形式加工的,采用间隙配合,具体要求为:外配合为配合为配作对象最大尺寸+0.01~+0.10mm:内配合为配作对象最小尺寸-0.10~-0.01。
5.机加工质量的控制5.1零件加工按照图纸加工,对图纸有标示不清、模糊、错误和对图纸产1生疑问的与上级领导联系。
5.2零件加工按照工艺流程去做。
5.3零件加工过程中遇到加工错误或尺寸超出公差范围要与上级领导联系,公司工艺人员将会确认零件可以采用或不可采用。
5.4需要划线加工的零件,加工后不允许有划线的痕迹。
5.5所有机加工的零件要去毛刺、钻孔后要倒角、棱角要倒钝(特殊要求除外)。
5.6碰到零件加工错误不应该善做主张对零件进行修改,应与上级领导联系获得技术支持。
6.机加工外观的控制*wm6.1机加工中由于控制不力和操作不当造成机械碰伤、表面划伤的不允许存在A级表面,允许存在B,C级表面.。
6.2变形、裂纹不允许存在A,B,C级表面。
6.3需要表面处理的零件表面不允许有氧化层、铁锈、凹凸不平的缺陷。
7.机加工质量检验7.1外观检验:不允许有翘曲、变形、裂纹、划伤、碰伤、凹凸不平及表面粗糙度符合要求。
机加工件检验标准
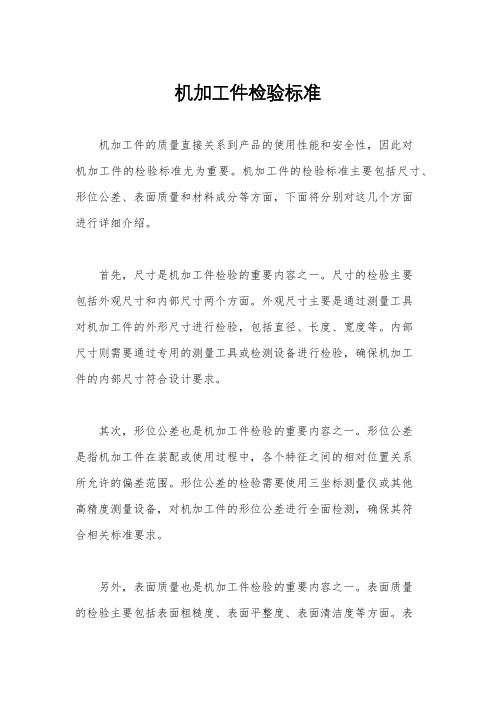
机加工件检验标准机加工件的质量直接关系到产品的使用性能和安全性,因此对机加工件的检验标准尤为重要。
机加工件的检验标准主要包括尺寸、形位公差、表面质量和材料成分等方面,下面将分别对这几个方面进行详细介绍。
首先,尺寸是机加工件检验的重要内容之一。
尺寸的检验主要包括外观尺寸和内部尺寸两个方面。
外观尺寸主要是通过测量工具对机加工件的外形尺寸进行检验,包括直径、长度、宽度等。
内部尺寸则需要通过专用的测量工具或检测设备进行检验,确保机加工件的内部尺寸符合设计要求。
其次,形位公差也是机加工件检验的重要内容之一。
形位公差是指机加工件在装配或使用过程中,各个特征之间的相对位置关系所允许的偏差范围。
形位公差的检验需要使用三坐标测量仪或其他高精度测量设备,对机加工件的形位公差进行全面检测,确保其符合相关标准要求。
另外,表面质量也是机加工件检验的重要内容之一。
表面质量的检验主要包括表面粗糙度、表面平整度、表面清洁度等方面。
表面质量的检验需要使用表面粗糙度仪、平整度测量仪等专用设备,对机加工件的表面质量进行全面检测,确保其符合产品要求。
最后,材料成分也是机加工件检验的重要内容之一。
材料成分的检验需要使用化学分析仪器对机加工件的材料成分进行检测,确保其符合设计要求,以保证产品的使用性能和安全性。
总之,机加工件的检验标准涉及到尺寸、形位公差、表面质量和材料成分等多个方面,需要使用不同的测量工具和检测设备进行全面检验。
只有严格按照相关标准要求进行检验,才能确保机加工件的质量符合产品要求,提高产品的使用性能和安全性。
机加件通用检验标准
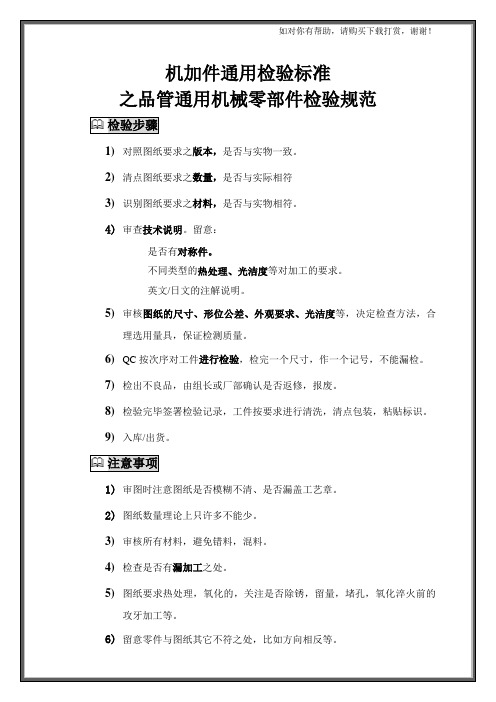
2) 术语和定义 A 级表面:在使用过程中总能被客户看见的部分(如:面壳的正面和顶面,后壳
的顶面,手柄,透镜,按键及键盘正面,探头整个表面等) 。
B 级表面:在使用过程中常常被客户看见的部分(如:面壳的左右侧面,底壳
或后壳的左右侧面及背面等) 。这些表面允许有轻微不良,但是不致引起挑剔客 户不购买产品。
可热处理不锈钢:SUS440C 铁 弗 龙 : PT
黑 赛 钢 : 黑 POM
铁(冷轧板):SPCC 45#钢:SS400、SGD400-D
铬钢:SKD、NAK55、NAK80
外观检视 1) 外观检视条件
——视力:校正视力 1.0 以上 ——目视距离:检查物距眼睛 A 级面 40 ㎝,B、C 距眼睛一臂远。 ——目视角度:45 度~90 度(检查时产品应转动) ——目视时间:A级面 15 秒/面,B、C面 10 秒/面 ——灯光:大于 500LUX 的照明度
钝化膜现象,呈现为区别于周围彩色的白色。
雾状:镀铬、镀镍表面上的模糊、不清晰、不光亮的现象。 颗粒:因材料夹杂物或外来物(如焊渣)的影响而在表面形成的,颜色与正常
表面一致的凸起现象。
挂具印:指电镀、氧化、喷涂等表面处理生产过程中,因装挂用辅助工具的遮
挡而使其与零件相接触的部位产生局部无膜层的现象。
2) 未注公差角度的极限偏差
长度 0~10 10~50
如对你有帮助,请购买下载打赏,谢谢!
公差
±1°
±30′
±20′
±10′
±5′
3) 直线度和平面度的未注公差儿
长度 公差 ≦10 0.02 ﹥10~30 0.05 ﹥30~100 0.1
单位:mm GB 1184-96 ﹥ 100 ~ ﹥ 300 ~ ﹥ 1000 ~ 300 1000 3000 0.2 0.3 0.4 单位:mm GB/T 1184-96
机加工零件油漆质检标准

机加工零件油漆质检标准
本标准适用于对机加工零件表面涂装油漆的质量检验。
1.表面处理
1.1表面处理质量应符合设计要求,表面应无油渍、污垢、锈蚀、旧漆等杂质。
1.2表面处理后的粗糙度应符合设计要求,一般应控制在Ra3.2~6.3μm之间。
1.3表面处理后的清洁度应符合设计要求,一般应达到GB/T8923-88标准中的St2级或Sa2级。
2.涂装质量
2.1涂装材料应符合设计要求,选用时应考虑涂料的性能、用途、施工条件和环境等因素。
2.2涂装施工时应严格遵守工艺规程,涂层应均匀、平整、光滑,色泽一致,无气泡、桔皮、裂纹、流挂、脱落等缺陷。
2.3涂层厚度应符合设计要求,一般应控制在规定范围之内。
2.4涂装完成的零件表面应无漏涂、虚涂、脱漆等现象。
3.附着力和耐磨性
3.1涂层的附着力应符合设计要求,一般应达到GB/T9286-88标准中的1级或2级。
3.2涂层的耐磨性应符合设计要求,一般应达到GB/T1768-93标准中的1级或2级。
4.漆膜性能
4.1漆膜的硬度应符合设计要求,一般应达到GB/T6739-96标准中的1级或
2级。
4.2漆膜的耐冲击性应符合设计要求,一般应达到GB/T6749-97标准中的1级或2级。
4.3漆膜的耐候性应符合设计要求,一般应达到GB/T1775-95标准中的2级或3级。
5.外观质量
5.1涂装完成的零件外观应无明显的色差、光差、流挂、橘皮、针孔等缺陷。
5.2涂装完成的零件外观应平整光滑,无明显颗粒、划痕、凹凸等缺陷。
机加工表面光洁度标准

机加工表面光洁度标准机加工表面光洁度是制造业中一项十分重要的技术指标,它反映了产品表面的光洁度和精度水平,直接影响到产品的外观和质量。
因此,对于机加工表面光洁度的标准化要求非常严格。
下面是常见的几种机加工表面光洁度标准:一、Ra标准Ra是指表面平均粗糙值,用于表示表面的光洁度和粗糙度。
在机加工中,通常使用Ra作为表面光洁度的量化指标来衡量工件表面的质量。
一般来说,Ra值越低,表明表面越光滑,精度越高。
常见的Ra标准如下:1. Ra0.8:要求表面极为光滑,具有镜面效果。
2. Ra1.6:表面光洁度较高,不能有任何毛刺或其他瑕疵。
3. Ra3.2:表面较光滑,但仍可容忍细小的毛刺或者凹凸不平。
4. Ra6.3:表面较为光滑,但仍可容忍细小的毛刺,凸起和凹陷。
二、Rz标准Rz是指表面糙度值,用于表示机加工后的表面粗糙度,它是一种全面的表面粗糙度指标。
在机加工技术中,Rz值通常用于表面质量控制和工艺参数的调整。
常见的Rz标准如下:1. Rz10:表面非常光滑,具有较高的表面品质。
2. Rz20:表面光滑度较高,表面可容忍少量细小的毛刺或凹凸。
3. Rz40:表面粗糙度较高,仅能容忍较细小的凹凸或毛刺。
4. Rz80:表面极度粗糙,仅能容忍少量细小的凸起。
三、其他常见标准除了Ra和Rz标准外,机加工表面光洁度的标准还有以下几种:1. Rmax:表面极值高度,其值越低表明表面越平整。
2. RMS:均方根粗糙度,其中越小表明表面越光滑。
3. Rt:峰谷高度,是表面粗糙度指标中的一种,其值越小表示表面越光滑。
总之,机加工表面光洁度标准非常重要,不同的标准适用于不同的机加工工艺和产品类型。
为了保证产品的品质和质量,需要根据实际情况选择合适的标准,进行严格的表面光洁度检测和控制。
加工表面粗糙度标准
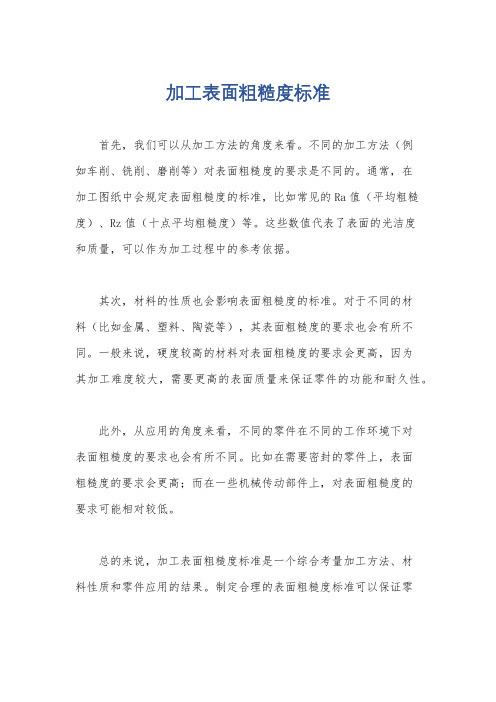
加工表面粗糙度标准
首先,我们可以从加工方法的角度来看。
不同的加工方法(例
如车削、铣削、磨削等)对表面粗糙度的要求是不同的。
通常,在
加工图纸中会规定表面粗糙度的标准,比如常见的Ra值(平均粗糙度)、Rz值(十点平均粗糙度)等。
这些数值代表了表面的光洁度
和质量,可以作为加工过程中的参考依据。
其次,材料的性质也会影响表面粗糙度的标准。
对于不同的材
料(比如金属、塑料、陶瓷等),其表面粗糙度的要求也会有所不同。
一般来说,硬度较高的材料对表面粗糙度的要求会更高,因为
其加工难度较大,需要更高的表面质量来保证零件的功能和耐久性。
此外,从应用的角度来看,不同的零件在不同的工作环境下对
表面粗糙度的要求也会有所不同。
比如在需要密封的零件上,表面
粗糙度的要求会更高;而在一些机械传动部件上,对表面粗糙度的
要求可能相对较低。
总的来说,加工表面粗糙度标准是一个综合考量加工方法、材
料性质和零件应用的结果。
制定合理的表面粗糙度标准可以保证零
件的质量和性能,提高加工效率和降低成本。
因此,在实际加工过程中,需要根据具体情况制定和执行相应的表面粗糙度标准。
机械加工表面质量名词解释

机械加工表面质量名词解释
机械加工表面质量是指通过机械加工(如铣削、车削、磨削等)所制造出来的工件表面的质量特征。
机械加工表面质量有着重要的意义,它直接影响到工件的性能和使用寿命。
因此,人们对机械加工表面质量提出了严格的要求,并制定出一系列的标准来进行评估。
常见的机械加工表面质量名词包括:
1. 粗糙度:是表面波动的一种度量,是表面轮廓中高低峰与表面基准面的平均距离。
它通常用Ra、Rz等参数来表示。
2. 平整度:是表面局部平坦程度的指标,是表面局部平坦面与平坦基准面间的距离差。
它通常用Waviness来表示。
3. 光洁度:是表面的反射能力,是表面镜面反射光线的亮度和光线散射的能力。
它通常用Rt来表示。
4. 凸度:是表面的突出程度的指标,是表面上的突起的最大高度与表面基准面的距离。
它通常用Rp、Rv来表示。
5. 波度:是表面上连续波动的指标,是表面波动的周期和振幅的综
合量。
它通常用Waviness来表示。
以上这些指标是机械加工表面质量中比较重要的一部分,每一个指标都有着自己的标准和要求。
为了确保机械加工表面质量的标准化和规范化,人们制定了一系列的标准,如ISO/DIS 4287、ISO 4288、GB/T 11683等。
这些标准可以帮助人们更加准确地评估和控制机械加工表面质量。
机加工表面粗糙度标准等级
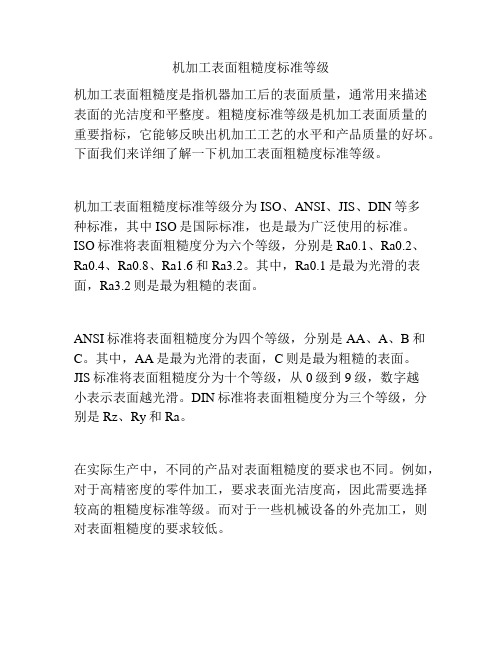
机加工表面粗糙度标准等级
机加工表面粗糙度是指机器加工后的表面质量,通常用来描述表面的光洁度和平整度。
粗糙度标准等级是机加工表面质量的重要指标,它能够反映出机加工工艺的水平和产品质量的好坏。
下面我们来详细了解一下机加工表面粗糙度标准等级。
机加工表面粗糙度标准等级分为ISO、ANSI、JIS、DIN等多
种标准,其中ISO是国际标准,也是最为广泛使用的标准。
ISO标准将表面粗糙度分为六个等级,分别是Ra0.1、Ra0.2、Ra0.4、Ra0.8、Ra1.6和Ra3.2。
其中,Ra0.1是最为光滑的表面,Ra3.2则是最为粗糙的表面。
ANSI标准将表面粗糙度分为四个等级,分别是AA、A、B和C。
其中,AA是最为光滑的表面,C则是最为粗糙的表面。
JIS标准将表面粗糙度分为十个等级,从0级到9级,数字越
小表示表面越光滑。
DIN标准将表面粗糙度分为三个等级,分别是Rz、Ry和Ra。
在实际生产中,不同的产品对表面粗糙度的要求也不同。
例如,对于高精密度的零件加工,要求表面光洁度高,因此需要选择较高的粗糙度标准等级。
而对于一些机械设备的外壳加工,则对表面粗糙度的要求较低。
在进行机加工时,要根据产品的要求选择合适的粗糙度标准等级,并控制好加工参数,以保证加工出来的产品符合要求。
同时,在进行检测时也需要使用相应的检测仪器,例如表面粗糙度仪、光学显微镜等。
总之,机加工表面粗糙度标准等级是机器加工后的表面质量的重要指标,不同的产品对表面粗糙度有不同的要求,因此在进行机加工时需要选择合适的粗糙度标准等级,并控制好加工参数,以保证加工出来的产品符合要求。
外观质量要求

一、下料通用要求♦:♦表面应平整无弯曲变形,否则应矫正。
焊接坡口应平整,无裂纹等缺陷。
♦:♦下料后应清除翻浆、飞溅,缺肉应焊补打磨。
手工气割下料件应将割口打磨平整。
♦有超声波检验要求的,下料后应按要求进行探伤检查。
♦同时满足多种下料方式的,优先选用精度高的下料方法。
平整处理要求1♦平整处理主要依据GB/T19804-2005.未注直线度、平面度和平行度公差取公差等级F级。
♦超过以上公差要求的应进行平整处理,使工件的直线度、平面度和平行度误差在标准范围内。
♦平整处理一般以火焰整平为主,机械矫正为辅。
平整处理要求2♦下料前应复检板材,不符合表面平整度要求的,应校平后再下料。
♦下料后板材不符合表面平整度要求的,应再次进行校平处理。
♦校平时不应直接锤击板材表面。
♦校平后板材表面应无凹凸痕迹。
平整处理要求3♦钢板卷制时,应检查卷板机辊子表面是否有明显的凹凸痕迹,若有,应修补、打磨处理。
♦筒体焊接时,应检查转胎表面是否有明显的凹凸痕迹,若有应修补打磨处理。
表面质量要求1♦板边应边缘整齐,表面光滑,外形规则。
钢板和钢带表面不应有扭翘、脱膜、锈蚀、气泡、裂纹、结疤和夹杂物等缺陷。
♦:♦板材表面不应有肉眼可见的裂纹、折叠、结疤和夹杂物等缺陷。
♦:♦板材下料后割口应平整,不应有翻浆、毛刺、凹坑、飞溅物、飞边等缺陷。
表面质量要求2♦焊接结构件的外缘非焊接部位,割口不平度应不大于1mm。
不能满足以上要求时,应用砂轮打磨至平整光滑。
♦毛刺、飞边应打磨干净,局部过大的毛刺、飞边可用气割去除后再用角磨机打磨光滑。
二、铸锻件外观质量♦执行标准《铸锻件外观质量》SINOMA-TEC-TS-003-2012♦相关标准GB/T6414铸件尺寸公差与机械加工余量JB/T5000.4重型机械通用技术条件第四部分:铸铁件JC/T401.3建材机械用铸钢件缺陷处理规定JC/T691 高铭铸铁衬板技术条件铸件表面质量1♦:♦铸件上的型砂、芯砂、芯骨、粘砂、夹砂、飞边及内腔残余物应清理干净,并铲磨光滑平整,且不高于母材表面。
机械加工表面质量第三章
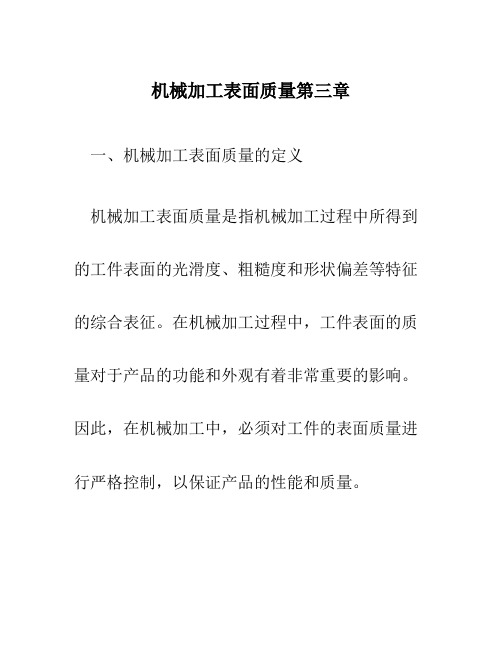
机械加工表面质量第三章一、机械加工表面质量的定义机械加工表面质量是指机械加工过程中所得到的工件表面的光滑度、粗糙度和形状偏差等特征的综合表征。
在机械加工过程中,工件表面的质量对于产品的功能和外观有着非常重要的影响。
因此,在机械加工中,必须对工件的表面质量进行严格控制,以保证产品的性能和质量。
机械加工表面质量的评定主要包括以下几个方面:1.光滑度:表面的光滑度是指表面平整度和光泽度的综合评价。
优良的光滑度可以提高工件的表面美观度,并减少与介质之间的摩擦和粘附。
2.粗糙度:表面的粗糙度是指表面上微小凹凸的高度和间距。
粗糙度对于工件的摩擦、磨损和密封性能有着重要的影响。
粗糙度越小,表面越光滑,摩擦系数越小。
3.形状偏差:形状偏差主要包括平面度、直线度、圆度和轮廓度等。
形状偏差反映了工件表面轮廓与理想轮廓之间的偏离程度。
形状偏差对于工件的密封性能、装配性能和运动精度有着重要的影响。
二、机械加工表面质量的评定方法机械加工表面质量的评定方法主要包括两种:检验法和测量法。
2.1 检验法检验法是通过肉眼或放大镜观察工件表面的外观和质量特征进行评定。
这种方法简单直观,适用于工件表面质量要求不高的情况。
常见的检验法包括目视检查、放大镜检查和样品比对检验等。
2.2 测量法测量法是利用各种测量仪器对工件表面的光滑度、粗糙度和形状偏差等进行定量测量和评定。
测量法具有高精度、高灵敏度的特点,适用于对工件表面质量要求较高的情况。
常见的测量方法包括光学测量、机械测量和电子测量等。
2.2.1 光学测量光学测量是利用光学仪器进行工件表面质量的测量和评定。
常见的光学测量方法有:•白光干涉法:利用白光的干涉原理测量工件表面的形状偏差。
•投影仪测量法:利用投影仪进行工件表面形状偏差的测量。
•激光扫描法:利用激光扫描仪对工件表面进行扫描,获取工件表面形状的三维信息。
2.2.2 机械测量机械测量是利用机械仪器对工件表面质量进行测量和评定。
常见的机械测量方法有:•宏观测量法:利用尺子、卡尺等测量工具对工件表面的尺寸、平面度等进行测量。
机械加工成品质量技术指标或者标准

机械加工成品质量技术指标或者标准机械加工成品的质量技术指标或标准是指用于评估和衡量机械加工成品质量的各种要素和要求。
这些指标或标准可以帮助制造商和用户确定成品是否符合预期的要求,并确保其质量以满足用户需求。
以下是一些常见的机械加工成品质量技术指标或标准。
1.尺寸精度:尺寸精度是机械加工成品中最重要的指标之一。
它指的是成品与设计尺寸之间的差异。
常见的尺寸精度标准包括公差和尺寸偏差。
对于某些关键零部件,如发动机配件或航空航天部件,尺寸精度可能非常高,因为它们的功能和性能可能受到微小尺寸差异的影响。
2.表面粗糙度:表面粗糙度是指机械加工成品表面的纹理和光洁度。
高品质的机械加工成品应具有平滑、均匀的表面,以确保其与其他部件的贴合和运动的顺畅。
表面粗糙度可以通过测量平均粗糙度、峰值高度等参数来评估。
3.功能性能:机械加工成品的功能性能指其在特定工作条件下执行所需功能的能力。
这取决于成品的材料、设计和加工质量等因素。
功能性能测试可能包括强度测试、疲劳寿命测试、耐腐蚀性测试等,以确保成品能够在预期的使用环境下可靠地工作。
4.材料性能:材料性能是机械加工成品质量的关键要素之一。
它指的是成品所使用材料的物理、化学和力学性能。
常见的材料性能指标包括强度、硬度、韧性、耐磨性、耐腐蚀性等。
制造商必须选择具有适当材料性能的材料以满足成品的需求,并确保最终产品的质量。
5.安全性能:对于某些机械加工成品,如汽车零部件或医疗设备,安全性能是至关重要的。
安全性能指成品在使用时对人、设备或环境造成的潜在危险程度。
制造商必须遵守相关的安全标准和法规,以确保成品的安全性能达到要求。
6.可靠性:可靠性是指机械加工成品在一定时间内保持稳定和无故障运行的能力。
可靠性工程是通过使用可靠性分析和测试方法来评估和改进成品的可靠性。
对于一些关键应用领域,如航空航天、医疗和能源等,可靠性要求非常高,因为成品的故障可能导致严重的后果。
综上所述,机械加工成品的质量技术指标或标准涉及尺寸精度、表面粗糙度、功能性能、材料性能、安全性能和可靠性等多个方面。
机械加工质量控制标准及规范

机械加工质量控制标准及规范
一、引言
机械加工质量控制是确保制造过程中产品达到预期质量的关键要素。
本文档旨在介绍机械加工质量控制的标准及规范,并提供相关指导。
二、质量控制标准
1. 尺寸控制:确保零件尺寸与设计要求相符合,并符合国家相关标准。
2. 几何形状控制:确保零件的几何形状达到设计要求,如平面度、圆度、直线度等。
3. 表面质量控制:确保零件表面光洁度、粗糙度等符合要求,采用适当的表面处理方法。
4. 材料控制:确保使用的材料符合产品要求,包括材料的物理性能、化学成分等。
5. 装配控制:确保零件的装配质量达到要求,包括零件之间的间隙、配合、误差等。
三、质量控制规范
1. 加工工艺规范:明确机械加工过程中的具体工艺要求,包括
机床的选用、切削参数的设定、工件固定方式等。
2. 检测方法规范:规定机械零部件在加工过程中的检测方法,
包括使用的检测工具、检测标准等。
3. 质量记录规范:要求对机械加工过程中的关键节点进行记录,包括尺寸、几何形状、表面质量、材料等的检测结果。
4. 不合格品处理规范:明确不合格品的处理流程,包括原因分析、责任追究、修整或重新加工的方式等。
四、总结
机械加工质量控制的标准及规范对于保障产品质量至关重要。
本文档提供了一个基本的指导框架,但具体的标准和规范应根据实
际情况制定,并在实践中不断改进。
以上为《机械加工质量控制标准及规范》的文档内容。
---
注:本文档中的内容仅供参考,不做任何法律解释和依据。
机械加工检验标准及方法
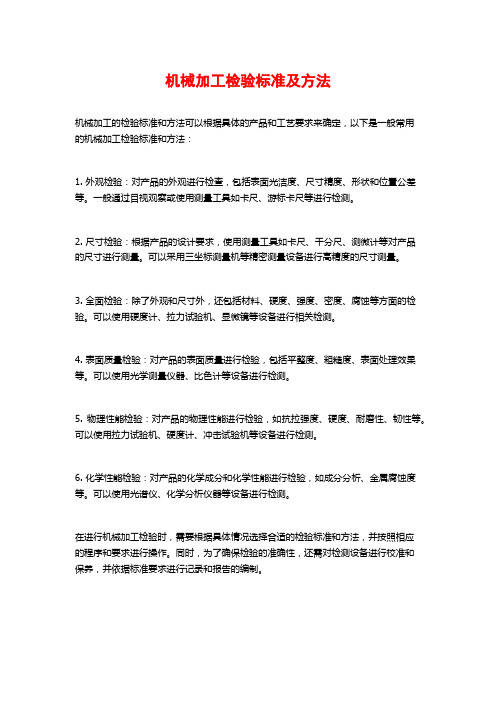
机械加工检验标准及方法
机械加工的检验标准和方法可以根据具体的产品和工艺要求来确定,以下是一般常用
的机械加工检验标准和方法:
1. 外观检验:对产品的外观进行检查,包括表面光洁度、尺寸精度、形状和位置公差等。
一般通过目视观察或使用测量工具如卡尺、游标卡尺等进行检测。
2. 尺寸检验:根据产品的设计要求,使用测量工具如卡尺、千分尺、测微计等对产品
的尺寸进行测量。
可以采用三坐标测量机等精密测量设备进行高精度的尺寸测量。
3. 全面检验:除了外观和尺寸外,还包括材料、硬度、强度、密度、腐蚀等方面的检验。
可以使用硬度计、拉力试验机、显微镜等设备进行相关检测。
4. 表面质量检验:对产品的表面质量进行检验,包括平整度、粗糙度、表面处理效果等。
可以使用光学测量仪器、比色计等设备进行检测。
5. 物理性能检验:对产品的物理性能进行检验,如抗拉强度、硬度、耐磨性、韧性等。
可以使用拉力试验机、硬度计、冲击试验机等设备进行检测。
6. 化学性能检验:对产品的化学成分和化学性能进行检验,如成分分析、金属腐蚀度等。
可以使用光谱仪、化学分析仪器等设备进行检测。
在进行机械加工检验时,需要根据具体情况选择合适的检验标准和方法,并按照相应
的程序和要求进行操作。
同时,为了确保检验的准确性,还需对检测设备进行校准和
保养,并依据标准要求进行记录和报告的编制。
- 1、下载文档前请自行甄别文档内容的完整性,平台不提供额外的编辑、内容补充、找答案等附加服务。
- 2、"仅部分预览"的文档,不可在线预览部分如存在完整性等问题,可反馈申请退款(可完整预览的文档不适用该条件!)。
- 3、如文档侵犯您的权益,请联系客服反馈,我们会尽快为您处理(人工客服工作时间:9:00-18:30)。
精心整理
安徽铜陵松宝智能装备股份有限公司
机加工零件外观检验标准
1.范围
本标准规定了无任何表面处理一般机加工件(机加工部位)在检验过程中外观可接收的标准。
2. 3.1A.B.C.3.2Ⅰ.Ⅱ.偶尔被注意到的(客户在使用时不经常看到的,侧面和底面的)。
Ⅲ.难以被注意的(只用在安装或维修时才能看到的,内部的)。
4. 职责
品质检验负责对送检的零件按本标准进行检验,并判定合格或不合格。
5. 验收标准
5.1机加工件材料应符合图纸要求。
代用材料一律由设计技术员签字认可。
精心整理
5.2通用要求
5.2.1工件表面应没有污渍。
5.2.2工件不得有锐边(以一般手指触摸没有扎手感),不得有毛刺。
5.2.3表面粗糙度应符合图纸要求。
5.2.4螺纹孔内不得有切削液,攻丝油等残留(防锈油除外)。
5.2.5成品工件表面不允许有锈斑,锈迹。