船体典型结构节点抗疲劳设计研究
船体典型结构节点抗疲劳设计

船体典型结构节点抗疲劳设计摘要:随着我国经济在快速发展,社会在不断进步,利用抗疲劳设计优化方法对油船、散货船和集装箱船的典型结构节点进行分析,梳理若干典型节点的抗疲劳设计标准。
部分典型结构节点如舱口角隅等的抗疲劳设计标准可作为疲劳校核的等效方法。
在设计时,通过疲劳强度计算改进结构详细节点的设计,以保证船体构件的疲劳寿命能满足要求。
关键词:疲劳评估;典型节点;舱口角隅;等效设计引言近几年来,我国船舶建造领域发展迅速,相关检验标准不断完善。
在船舶船体建造检验过程中,由业主、船厂及专业检验机构共同完成船舶船体的检验工作。
具体检验内容较为复杂,需要在船舶船体建造的全过程中,及时开展相关检验工作,并做好分析和记录,及时纠正问题,确保船舶建造质量。
在实际操作过程中,由于检验内容多,容易出现疏漏,应通过采用检验节点控制方法,促进船舶船体检验的规范化和程序化发展。
1船舶船体建造科学设计合理布局作为大型工业产品,建造船舶的过程比较繁琐,对建造使用的工艺提出较高要求,在进行船舶设计的过程中,要对其进行合理的布局,因为在建造船舶的过程中,要确定出所建造的方向,然后开始进行船舶建造工作,每个阶段的生产工作已经做好分工,各个环节都明确了任务,船体建设成型后就不能进行调整和改变,假如在设计的过程时,没有按照要求进行设计,设计出的方案不合理,就会使得经济出现严重的损失,因此,要对设计的过程给予足够的重视。
首先,在建造船舶之前,要进行规范设计,对设计的方案要明确。
其次,设计师要确保设计出的方案和图纸有可行性,建造船舶的图纸在设计出来后,要将其交给船舶检验单位,进行图纸的审查和检验,图纸通过检验后才能开工,并且图纸还要由设计方、建造方和委托方进行检查,对其可行性进行讨论,这样建造出的船舶能够满足使用的要求。
此外,图纸符合实际的建造要求之后,造船厂要对规划和布局进行合理安排,将施工用到的人员和设备等进行有效配置,并且还要对施工的场地进行合理的勘察,要对建造使用的资金进行合理的预算,在建造过程中,要确保使用的材料符合质量的要求;在施工过程中,要对施工的各个阶段进行科学的规划,按照规定的工程进度进行施工,这样就可以使得船舶建造工作顺利地展开。
船舶结构力学与疲劳性能的研究
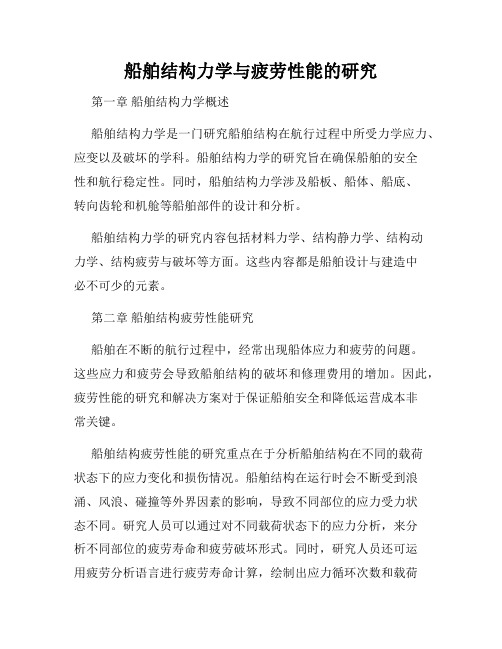
船舶结构力学与疲劳性能的研究第一章船舶结构力学概述船舶结构力学是一门研究船舶结构在航行过程中所受力学应力、应变以及破坏的学科。
船舶结构力学的研究旨在确保船舶的安全性和航行稳定性。
同时,船舶结构力学涉及船板、船体、船底、转向齿轮和机舱等船舶部件的设计和分析。
船舶结构力学的研究内容包括材料力学、结构静力学、结构动力学、结构疲劳与破坏等方面。
这些内容都是船舶设计与建造中必不可少的元素。
第二章船舶结构疲劳性能研究船舶在不断的航行过程中,经常出现船体应力和疲劳的问题。
这些应力和疲劳会导致船舶结构的破坏和修理费用的增加。
因此,疲劳性能的研究和解决方案对于保证船舶安全和降低运营成本非常关键。
船舶结构疲劳性能的研究重点在于分析船舶结构在不同的载荷状态下的应力变化和损伤情况。
船舶结构在运行时会不断受到浪涌、风浪、碰撞等外界因素的影响,导致不同部位的应力受力状态不同。
研究人员可以通过对不同载荷状态下的应力分析,来分析不同部位的疲劳寿命和疲劳破坏形式。
同时,研究人员还可运用疲劳分析语言进行疲劳寿命计算,绘制出应力循环次数和载荷幅值的疲劳曲线,从而掌握船舶结构疲劳的规律,制定相应的维护与保养计划。
第三章船舶结构力学在新材料应用方面的研究新材料的应用是船舶结构力学研究的重要方向之一。
从木质船到金属船,再到现代的玻璃钢船、碳纤维强化塑料船和铝合金船等,一直以来,新材料的更新换代明显提高了船舶的性能、可靠性和安全性。
对于新材料的应用,研究人员需要关注材料本身的力学性能,从而确定新材料的设计参数。
同时,还需要对新材料的实际使用情况进行分析和测试,研究其强度、疲劳性能等方面的特点,以确保新材料的应用具有可靠性和安全性。
第四章船舶结构力学在船型设计方面的研究船型与船舶结构紧密相连,船型的设计和选择会影响船舶结构的受力和运行状态。
因此,船型设计是船舶结构力学研究的重要方向之一。
船型设计需要综合考虑船舶的载重能力、航速、耐波性、稳性、操作性等因素。
船体典型结构节点抗疲劳设计
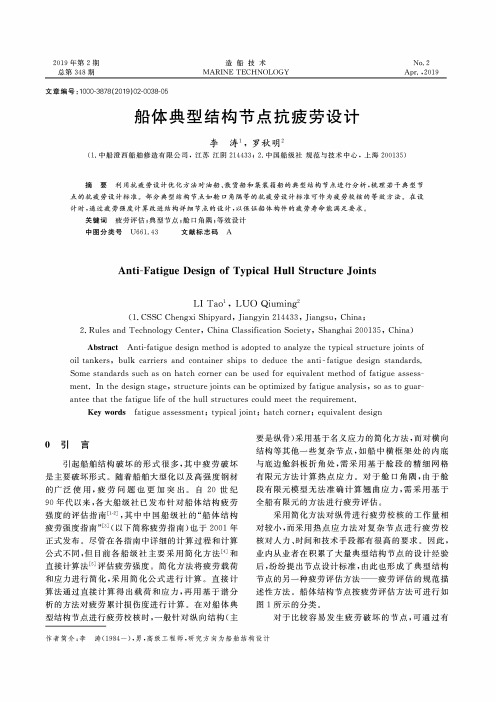
2019年第2期总第348期造船技术MARINE TECHNOLOGYNo. 2Apr.,2019文章编号:1〇〇〇-3878 (2〇19) 〇2-〇〇38-〇5船体典型结构节点抗疲劳设计李涛\罗秋明2(1.中船澄西船舶修造有限公司,江苏江阴214433; 2.中国船级社规范与技术中心,上海200135)摘要利用抗疲劳设计优化方法对油船、散货船和集装箱船的典型结构节点进行分析,梳理若干典型节点的抗疲劳设计标准。
部分典型结构节点如舱口角隅等的抗疲劳设计标准可作为疲劳校核的等效方法。
在设计时,通过疲劳强度计算改进结构详细节点的设计,以保证船体构件的疲劳寿命能满足要求。
关键词疲劳评估;典型节点;舱口角隅;等效设计中图分类号U661.43 文献标志码 AAnti-Fatigue Design of Typical Hull Structure JointsLI Tao1,LUO Qiuming2(1. C S S C Chengxi Shipyard,Jiangyin 214433, Jiangsu,China;2.Rules and Technology Center,China Classification Society,Shanghai 200135, China)Abstract Anti-fatigue design method i s adopted to analyze the typical structure joints of o i l tankers,bulk carriers and container ships to deduce the anti-fatigue design standards.Some standards such as on hatch corner can be used for equivalent method of fatigue assessment.In the design stage,structure joints can be optimized by fatigue analysis,so as to guarantee that the fatigue l i f e of the hull structures could meet the requirement.Key words fatigue assessment;typical joint;hatch corner;equivalent design◎引言引起船舶结构破坏的形式很多,其中疲劳破坏 是主要破坏形式。
船舶结构的疲劳寿命分析与优化设计研究
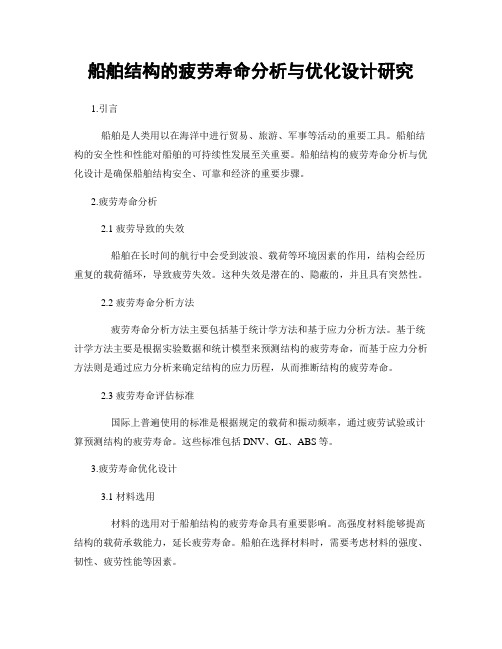
船舶结构的疲劳寿命分析与优化设计研究1.引言船舶是人类用以在海洋中进行贸易、旅游、军事等活动的重要工具。
船舶结构的安全性和性能对船舶的可持续性发展至关重要。
船舶结构的疲劳寿命分析与优化设计是确保船舶结构安全、可靠和经济的重要步骤。
2.疲劳寿命分析2.1 疲劳导致的失效船舶在长时间的航行中会受到波浪、载荷等环境因素的作用,结构会经历重复的载荷循环,导致疲劳失效。
这种失效是潜在的、隐蔽的,并且具有突然性。
2.2 疲劳寿命分析方法疲劳寿命分析方法主要包括基于统计学方法和基于应力分析方法。
基于统计学方法主要是根据实验数据和统计模型来预测结构的疲劳寿命,而基于应力分析方法则是通过应力分析来确定结构的应力历程,从而推断结构的疲劳寿命。
2.3 疲劳寿命评估标准国际上普遍使用的标准是根据规定的载荷和振动频率,通过疲劳试验或计算预测结构的疲劳寿命。
这些标准包括DNV、GL、ABS等。
3.疲劳寿命优化设计3.1 材料选用材料的选用对于船舶结构的疲劳寿命具有重要影响。
高强度材料能够提高结构的载荷承载能力,延长疲劳寿命。
船舶在选择材料时,需要考虑材料的强度、韧性、疲劳性能等因素。
3.2 结构布置结构的布置对于疲劳寿命具有重要影响。
合理的结构布置能够减小结构的应力集中,降低疲劳裂纹的发生,延长疲劳寿命。
3.3 疲劳损伤修复船舶在运营中可能会发生疲劳损伤,及时的修复和保养对于延长结构的疲劳寿命具有重要意义。
修复主要包括补焊、增强或更换受损部位等方式。
4.疲劳寿命研究进展4.1 数值仿真研究数值仿真是研究船舶结构疲劳寿命的重要手段。
通过建立结构的有限元模型,模拟结构在不同环境载荷下的应力响应,预测结构的疲劳寿命。
数值仿真技术的不断发展使得研究人员能够更加准确地分析船舶结构的疲劳寿命。
4.2 材料性能研究材料的性能对于疲劳寿命具有重要影响。
研究人员通过改善材料的强度、韧性、抗疲劳性等性能来延长结构的疲劳寿命。
材料的研究不断推动船舶结构疲劳寿命的提升。
船舶结构的疲劳寿命预测研究

船舶结构的疲劳寿命预测研究在船舶的设计和运营中,船舶结构的疲劳寿命是一个至关重要的问题。
疲劳失效可能导致船舶结构的损坏,甚至危及船舶的安全和正常运营。
因此,准确预测船舶结构的疲劳寿命对于船舶的设计、建造和维护具有重要意义。
船舶在航行过程中,会受到各种复杂的载荷作用,如波浪载荷、风载荷、货物载荷等。
这些载荷的长期作用会导致船舶结构材料内部产生微小的裂纹,并逐渐扩展,最终可能导致结构的疲劳破坏。
为了避免这种情况的发生,需要对船舶结构的疲劳寿命进行准确的预测。
目前,用于船舶结构疲劳寿命预测的方法主要有基于 SN 曲线的方法和基于断裂力学的方法。
基于 SN 曲线的方法是一种传统的疲劳寿命预测方法,它通过对大量试验数据的统计分析,得到材料或结构在不同应力水平下的疲劳寿命曲线(SN 曲线)。
然后,根据船舶结构所承受的应力历程和 SN 曲线,计算结构的疲劳损伤和寿命。
这种方法简单直观,但对于复杂的载荷情况和结构细节,其预测精度可能受到一定的限制。
基于断裂力学的方法则是从微观角度出发,考虑裂纹的萌生、扩展和断裂过程。
通过建立裂纹扩展模型,结合材料的断裂韧性等参数,预测裂纹扩展到临界尺寸所需的时间,从而得到结构的疲劳寿命。
这种方法对于含初始缺陷的结构和高应力集中区域的疲劳寿命预测具有较高的精度,但计算过程相对复杂,需要对断裂力学有深入的了解。
在实际的船舶结构疲劳寿命预测中,通常需要综合运用这两种方法。
对于一般的结构部位,可以采用基于 SN 曲线的方法进行初步预测;对于关键部位和存在初始缺陷的部位,则需要采用基于断裂力学的方法进行更精确的分析。
船舶结构的疲劳寿命预测还受到许多因素的影响。
首先是材料的性能,包括强度、韧性、疲劳性能等。
不同的材料在相同的载荷条件下,其疲劳寿命可能会有很大的差异。
因此,在进行疲劳寿命预测时,需要准确掌握材料的性能参数。
其次是结构的几何形状和尺寸。
结构的几何不连续、焊缝形状和尺寸等都会导致应力集中,从而影响疲劳寿命。
船舶结构的疲劳分析与优化

船舶结构的疲劳分析与优化在广阔无垠的海洋上,船舶作为重要的交通工具和运输工具,承担着各种重要的任务。
然而,在长期的使用过程中,船舶结构会面临疲劳问题,这可能会影响船舶的安全性和可靠性。
因此,对船舶结构的疲劳分析与优化显得尤为重要。
船舶在航行过程中,会受到多种复杂的载荷作用,如波浪力、风载荷、货物载荷等。
这些载荷的反复作用会导致船舶结构内部产生微小的裂纹,并逐渐扩展,最终可能导致结构的破坏。
船舶结构的疲劳破坏往往是在没有明显预兆的情况下发生的,一旦发生,后果不堪设想。
因此,为了确保船舶的安全运行,必须对船舶结构进行疲劳分析。
疲劳分析的第一步是对船舶所承受的载荷进行准确的评估。
这需要考虑船舶的航行环境、运营模式、货物装载情况等多种因素。
通过使用先进的数值模拟技术和实验方法,可以获取船舶在不同工况下所受到的载荷数据。
然后,根据这些数据,可以建立船舶结构的有限元模型。
有限元模型是一种有效的工具,可以将复杂的船舶结构离散为多个小的单元,并通过数学方程来描述每个单元的力学行为。
在建立有限元模型时,需要准确地定义材料的属性、边界条件和连接方式等。
通过对有限元模型进行计算,可以得到船舶结构在载荷作用下的应力分布和变形情况。
根据有限元分析的结果,可以确定船舶结构中的应力集中部位和潜在的疲劳危险区域。
这些区域往往是疲劳裂纹容易产生和扩展的地方。
为了评估这些区域的疲劳寿命,需要使用疲劳寿命预测方法。
目前,常用的疲劳寿命预测方法有基于应力的方法、基于应变的方法和基于损伤力学的方法等。
这些方法都有其优缺点和适用范围,需要根据具体情况选择合适的方法。
在进行疲劳寿命预测时,还需要考虑材料的疲劳性能参数,如疲劳极限、疲劳强度系数和疲劳指数等。
通过疲劳分析,可以了解船舶结构的疲劳性能,并发现潜在的问题。
然而,仅仅进行疲劳分析是不够的,还需要对船舶结构进行优化,以提高其疲劳性能。
船舶结构的优化可以从多个方面入手。
首先,可以通过改变结构的几何形状来降低应力集中。
船体结构典型节点疲劳模型试验

设计 、 试验数 据的处理 方式及试 验结果 进行研究 , 得 出 的 方 法 和 结 论 对 船 体 结 构 典 型 节 点 的疲 劳 模 型 试 验 具 有 参 考
Z H U Y i — f e n g , H U J i a - j u n , Z H A N G F a n , D I N G j u n , Q 1 E n ・ r o n g ( C h i n a S h i p S c i e n t i i f c R e s e a r c h C e n t e r , Wu x i 2 1 4 0 8 2 , C h i n a )
Ab s t r ac t : Th e u n c e r t a i n t y i s e x i s t e d i n t h e s h i p b ui l di ng p r o c e s s; me a n wh i l e, t he S — N c ur v e s a r e
型 节点 ; 疲 劳模 型 试 验 研 究 中图分 类号 : U 6 6 1 . 4 3 文献 标识 码 : A d o i : 1 0 . 3 4 0 4 / j . i s s n . 1 6 7 2— 7 6 4 9 . 2 0 1 3 . 0 9 . 0 0 4
第3 5卷 第 9期
2 0 1 3年 9月
舰
船
科
学
技
术
Vo 1 . 3 5 ,No . 9 S e p.,2 01 3
船舶结构的疲劳分析与可靠性评估研究

船舶结构的疲劳分析与可靠性评估研究第一章引言近年来,随着航海技术的不断发展,船舶结构的疲劳分析和可靠性评估越来越受到重视。
船舶作为运输工具,承受着恶劣海况、持续使用和负载变化等多种环境和工况的影响,会导致结构疲劳破坏和事故发生。
因此,对船舶结构的疲劳分析和可靠性评估进行研究,对提高船舶的安全性和可靠性具有重要意义。
第二章船舶结构疲劳分析2.1 疲劳理论基础在船舶结构的疲劳分析中,疲劳理论是基础,主要应用弹性力学和疲劳断裂力学原理。
通过应力集中因子、疲劳损伤累积和疲劳寿命预测等方法,分析船舶结构在多次循环荷载下的疲劳破坏机理。
2.2 船舶结构的疲劳载荷分析船舶在航行过程中受到波浪、风荷载和自身重力等多种荷载的作用。
疲劳载荷分析是对船舶结构在实际工况下受到的载荷进行测定、监测和计算的过程。
通过对载荷进行统计和频谱分析,确定船舶结构在设计寿命内的疲劳载荷谱。
2.3 船舶结构的疲劳强度评估船舶结构的疲劳强度评估是根据疲劳理论和载荷分析结果,确定船舶结构在设计寿命内的疲劳强度。
根据计算得到的应力和疲劳损伤累积,采用疲劳强度修正方法,对船舶结构疲劳强度进行评估。
第三章船舶结构可靠性评估3.1 可靠性理论基础船舶结构的可靠性评估是基于可靠性工程理论,主要包括失效模式与效应分析、可靠性评估方法和可靠性设计等内容。
通过概率论和数理统计等方法,对船舶结构的失效概率和可靠性参数进行评估和分析。
3.2 船舶结构的可靠性建模在进行船舶结构的可靠性评估时,需要对结构系统进行建模。
根据船舶结构的特点,采用可靠性分析中的可靠性网络、事件树和故障树等建模方法,对船舶结构的可靠性进行定量评估。
3.3 船舶结构的可靠性评估指标船舶结构的可靠性评估指标包括失效率、可靠度、安全系数等。
通过确定评估指标,对船舶结构的可靠性进行量化和比较,为决策和设计提供依据。
第四章研究方法和应用实例4.1 研究方法船舶结构的疲劳分析和可靠性评估研究中,应用了多种分析和评估方法,如有限元分析、疲劳寿命预测、可靠性分析等。
船舶结构的抗疲劳设计与分析研究与应用

船舶结构的抗疲劳设计与分析研究与应用在广袤的海洋中,船舶作为重要的交通工具和工程装备,承载着货物运输、人员往来以及各种海洋资源开发的重任。
然而,长期在复杂多变的海洋环境中运行,船舶结构面临着诸多挑战,其中疲劳损伤是一个不容忽视的问题。
为了确保船舶的安全性、可靠性和耐久性,船舶结构的抗疲劳设计与分析显得尤为重要。
船舶在航行过程中,会受到各种交变载荷的作用,如波浪载荷、风载荷、主机振动等。
这些载荷的反复作用会导致船舶结构内部产生微小的裂纹,并逐渐扩展,最终可能导致结构的失效。
因此,抗疲劳设计的目标就是要通过合理的结构设计和材料选择,尽可能地减少疲劳裂纹的产生和扩展,延长船舶的使用寿命。
在船舶结构的抗疲劳设计中,首先要对船舶所承受的载荷进行准确的分析和预测。
这需要考虑到船舶的航行区域、航行速度、载货量等多种因素。
通过先进的数值模拟技术和实验方法,可以获取船舶在不同工况下的载荷分布情况,为后续的设计提供依据。
材料的选择也是抗疲劳设计的关键环节之一。
高强度、高韧性的材料能够更好地抵抗疲劳损伤。
例如,一些新型的合金材料和复合材料在船舶结构中的应用越来越广泛。
然而,材料的性能不仅仅取决于其化学成分,还与制造工艺、热处理等因素密切相关。
因此,在选择材料时,需要综合考虑各种因素,以确保材料在实际使用中的性能能够满足抗疲劳要求。
船舶结构的几何形状和连接方式对疲劳性能也有着重要的影响。
合理的结构设计可以减少应力集中,降低疲劳裂纹产生的风险。
例如,采用平滑的过渡曲线、避免尖锐的棱角和突变的截面,可以有效地降低应力集中系数。
在连接部位,如焊接节点,焊接工艺和质量的控制至关重要。
不良的焊接工艺可能会导致焊接缺陷,从而成为疲劳裂纹的起始点。
除了设计阶段,在船舶的建造和运营过程中,也需要采取一系列的措施来保障结构的抗疲劳性能。
在建造过程中,严格控制施工质量,确保结构的制造精度和焊接质量符合设计要求。
在运营过程中,定期对船舶进行检测和维护,及时发现并处理潜在的疲劳损伤。
船舶与海洋工程结构物疲劳断裂分析研究现状及展望
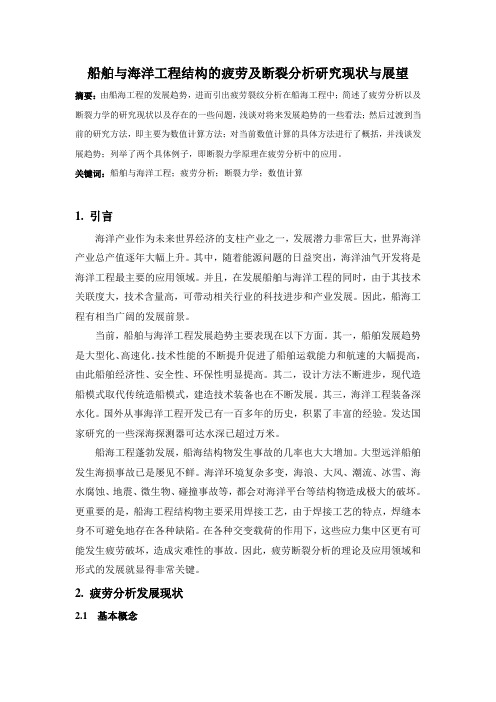
船舶与海洋工程结构的疲劳及断裂分析研究现状与展望摘要:由船海工程的发展趋势,进而引出疲劳裂纹分析在船海工程中;简述了疲劳分析以及断裂力学的研究现状以及存在的一些问题,浅谈对将来发展趋势的一些看法;然后过渡到当前的研究方法,即主要为数值计算方法;对当前数值计算的具体方法进行了概括,并浅谈发展趋势;列举了两个具体例子,即断裂力学原理在疲劳分析中的应用。
关键词:船舶与海洋工程;疲劳分析;断裂力学;数值计算1. 引言海洋产业作为未来世界经济的支柱产业之一,发展潜力非常巨大,世界海洋产业总产值逐年大幅上升。
其中,随着能源问题的日益突出,海洋油气开发将是海洋工程最主要的应用领域。
并且,在发展船舶与海洋工程的同时,由于其技术关联度大,技术含量高,可带动相关行业的科技进步和产业发展。
因此,船海工程有相当广阔的发展前景。
当前,船舶与海洋工程发展趋势主要表现在以下方面。
其一,船舶发展趋势是大型化、高速化。
技术性能的不断提升促进了船舶运载能力和航速的大幅提高,由此船舶经济性、安全性、环保性明显提高。
其二,设计方法不断进步,现代造船模式取代传统造船模式,建造技术装备也在不断发展。
其三,海洋工程装备深水化。
国外从事海洋工程开发已有一百多年的历史,积累了丰富的经验。
发达国家研究的一些深海探测器可达水深已超过万米。
船海工程蓬勃发展,船海结构物发生事故的几率也大大增加。
大型远洋船舶发生海损事故已是屡见不鲜。
海洋环境复杂多变,海浪、大风、潮流、冰雪、海水腐蚀、地震、微生物、碰撞事故等,都会对海洋平台等结构物造成极大的破坏。
更重要的是,船海工程结构物主要采用焊接工艺,由于焊接工艺的特点,焊缝本身不可避免地存在各种缺陷。
在各种交变载荷的作用下,这些应力集中区更有可能发生疲劳破坏,造成灾难性的事故。
因此,疲劳断裂分析的理论及应用领域和形式的发展就显得非常关键。
2. 疲劳分析发展现状2.1 基本概念载荷值随时间作周期性或非周期性变化的载荷成为交变载荷,由于载荷的变化使试件或构件的材料内产生随时间变化的交变应力与交变应变。
船舶结构强度与疲劳强度的计算技术研究
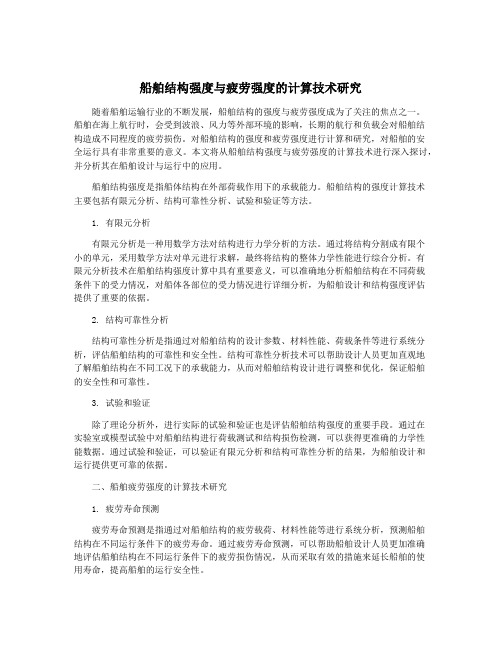
船舶结构强度与疲劳强度的计算技术研究随着船舶运输行业的不断发展,船舶结构的强度与疲劳强度成为了关注的焦点之一。
船舶在海上航行时,会受到波浪、风力等外部环境的影响,长期的航行和负载会对船舶结构造成不同程度的疲劳损伤。
对船舶结构的强度和疲劳强度进行计算和研究,对船舶的安全运行具有非常重要的意义。
本文将从船舶结构强度与疲劳强度的计算技术进行深入探讨,并分析其在船舶设计与运行中的应用。
船舶结构强度是指船体结构在外部荷载作用下的承载能力。
船舶结构的强度计算技术主要包括有限元分析、结构可靠性分析、试验和验证等方法。
1. 有限元分析有限元分析是一种用数学方法对结构进行力学分析的方法。
通过将结构分割成有限个小的单元,采用数学方法对单元进行求解,最终将结构的整体力学性能进行综合分析。
有限元分析技术在船舶结构强度计算中具有重要意义,可以准确地分析船舶结构在不同荷载条件下的受力情况,对船体各部位的受力情况进行详细分析,为船舶设计和结构强度评估提供了重要的依据。
2. 结构可靠性分析结构可靠性分析是指通过对船舶结构的设计参数、材料性能、荷载条件等进行系统分析,评估船舶结构的可靠性和安全性。
结构可靠性分析技术可以帮助设计人员更加直观地了解船舶结构在不同工况下的承载能力,从而对船舶结构设计进行调整和优化,保证船舶的安全性和可靠性。
3. 试验和验证除了理论分析外,进行实际的试验和验证也是评估船舶结构强度的重要手段。
通过在实验室或模型试验中对船舶结构进行荷载测试和结构损伤检测,可以获得更准确的力学性能数据。
通过试验和验证,可以验证有限元分析和结构可靠性分析的结果,为船舶设计和运行提供更可靠的依据。
二、船舶疲劳强度的计算技术研究1. 疲劳寿命预测疲劳寿命预测是指通过对船舶结构的疲劳载荷、材料性能等进行系统分析,预测船舶结构在不同运行条件下的疲劳寿命。
通过疲劳寿命预测,可以帮助船舶设计人员更加准确地评估船舶结构在不同运行条件下的疲劳损伤情况,从而采取有效的措施来延长船舶的使用寿命,提高船舶的运行安全性。
船体结构典型节点疲劳模型试验
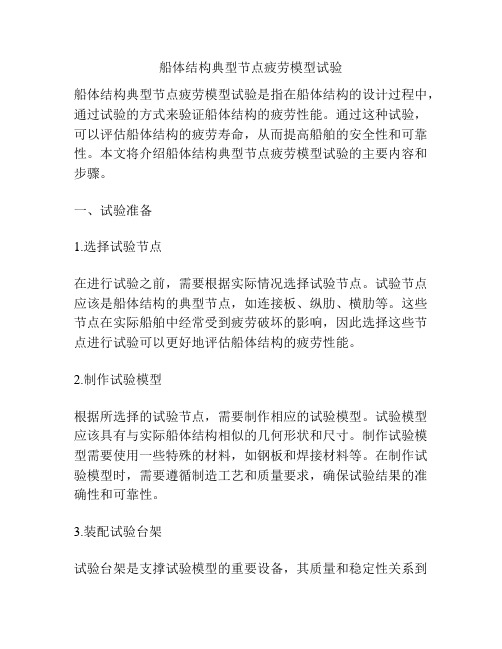
船体结构典型节点疲劳模型试验船体结构典型节点疲劳模型试验是指在船体结构的设计过程中,通过试验的方式来验证船体结构的疲劳性能。
通过这种试验,可以评估船体结构的疲劳寿命,从而提高船舶的安全性和可靠性。
本文将介绍船体结构典型节点疲劳模型试验的主要内容和步骤。
一、试验准备1.选择试验节点在进行试验之前,需要根据实际情况选择试验节点。
试验节点应该是船体结构的典型节点,如连接板、纵肋、横肋等。
这些节点在实际船舶中经常受到疲劳破坏的影响,因此选择这些节点进行试验可以更好地评估船体结构的疲劳性能。
2.制作试验模型根据所选择的试验节点,需要制作相应的试验模型。
试验模型应该具有与实际船体结构相似的几何形状和尺寸。
制作试验模型需要使用一些特殊的材料,如钢板和焊接材料等。
在制作试验模型时,需要遵循制造工艺和质量要求,确保试验结果的准确性和可靠性。
3.装配试验台架试验台架是支撑试验模型的重要设备,其质量和稳定性关系到试验结果的准确性和可靠性。
在装配试验台架之前,需要根据试验模型的尺寸和重量设计合适的支撑结构。
试验台架应该具有足够的刚性和稳定性,以保证试验模型的受力状态和变形情况与实际船舶相似。
二、试验步骤1.加载试验模型在进行试验之前,需要进行预加载。
预加载的目的是消除模型自身的应力,使模型达到稳定的状态。
加载试验模型时需要确保试验模型的受力状态和变形情况与实际船舶相似。
按照设计要求和试验方案逐步增加荷载,直至试验模型发生疲劳破坏。
2.记录试验数据试验过程中需要记录试验数据,并及时采取必要的措施进行数据处理。
试验数据包括受力情况、变形情况、振动情况等,这些数据是评估试验结果的重要依据。
3.分析试验结果试验结束后,需要对试验结果进行分析。
通过分析试验数据,可以得出试验模型的疲劳寿命以及其它相关参数。
如果试验结果不符合设计要求,需要进行相应的技术改进或设计调整。
三、试验结论通过船体结构典型节点疲劳模型试验,可以评估船体结构的疲劳性能,提高船舶的安全性和可靠性。
船舶结构强度与疲劳强度的计算技术研究
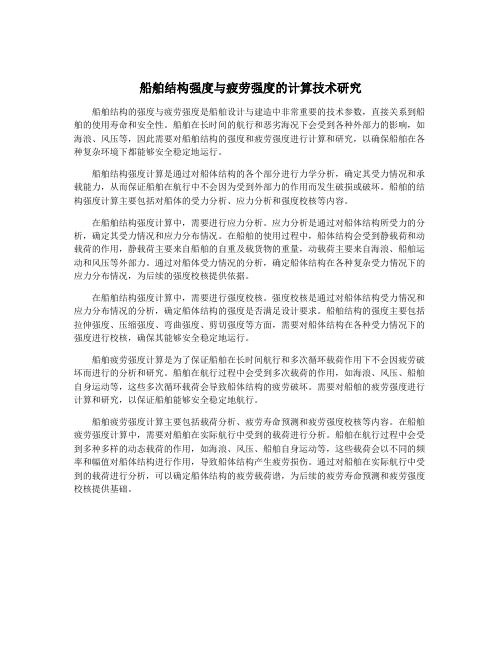
船舶结构强度与疲劳强度的计算技术研究船舶结构的强度与疲劳强度是船舶设计与建造中非常重要的技术参数,直接关系到船舶的使用寿命和安全性。
船舶在长时间的航行和恶劣海况下会受到各种外部力的影响,如海浪、风压等,因此需要对船舶结构的强度和疲劳强度进行计算和研究,以确保船舶在各种复杂环境下都能够安全稳定地运行。
船舶结构强度计算是通过对船体结构的各个部分进行力学分析,确定其受力情况和承载能力,从而保证船舶在航行中不会因为受到外部力的作用而发生破损或破坏。
船舶的结构强度计算主要包括对船体的受力分析、应力分析和强度校核等内容。
在船舶结构强度计算中,需要进行应力分析。
应力分析是通过对船体结构所受力的分析,确定其受力情况和应力分布情况。
在船舶的使用过程中,船体结构会受到静载荷和动载荷的作用,静载荷主要来自船舶的自重及载货物的重量,动载荷主要来自海浪、船舶运动和风压等外部力。
通过对船体受力情况的分析,确定船体结构在各种复杂受力情况下的应力分布情况,为后续的强度校核提供依据。
在船舶结构强度计算中,需要进行强度校核。
强度校核是通过对船体结构受力情况和应力分布情况的分析,确定船体结构的强度是否满足设计要求。
船舶结构的强度主要包括拉伸强度、压缩强度、弯曲强度、剪切强度等方面,需要对船体结构在各种受力情况下的强度进行校核,确保其能够安全稳定地运行。
船舶疲劳强度计算是为了保证船舶在长时间航行和多次循环载荷作用下不会因疲劳破坏而进行的分析和研究。
船舶在航行过程中会受到多次载荷的作用,如海浪、风压、船舶自身运动等,这些多次循环载荷会导致船体结构的疲劳破坏。
需要对船舶的疲劳强度进行计算和研究,以保证船舶能够安全稳定地航行。
船舶疲劳强度计算主要包括载荷分析、疲劳寿命预测和疲劳强度校核等内容。
在船舶疲劳强度计算中,需要对船舶在实际航行中受到的载荷进行分析。
船舶在航行过程中会受到多种多样的动态载荷的作用,如海浪、风压、船舶自身运动等,这些载荷会以不同的频率和幅值对船体结构进行作用,导致船体结构产生疲劳损伤。
船舶结构的抗疲劳设计与分析

船舶结构的抗疲劳设计与分析在广阔的海洋中,船舶作为重要的交通工具和运输工具,承载着大量的人员和货物。
为了确保船舶在复杂多变的海洋环境中安全可靠地运行,船舶结构的设计至关重要。
其中,抗疲劳设计是船舶结构设计中一个关键的环节,直接关系到船舶的使用寿命和航行安全。
船舶在航行过程中,会受到各种载荷的作用,如风、浪、流、货物装卸等。
这些载荷的长期作用会导致船舶结构产生疲劳损伤,进而影响船舶的结构强度和安全性。
因此,进行船舶结构的抗疲劳设计和分析是非常必要的。
船舶结构的疲劳问题是一个复杂的多因素问题。
首先,载荷的不确定性是一个重要因素。
海洋环境中的风浪等自然条件变化无常,导致作用在船舶上的载荷难以精确预测。
其次,船舶结构的复杂性也增加了疲劳分析的难度。
船舶由众多的构件组成,它们之间的连接方式和相互作用关系复杂,使得应力分布不均匀。
此外,材料的性能也会对疲劳寿命产生影响,不同的材料具有不同的疲劳特性。
为了有效地进行船舶结构的抗疲劳设计,需要对疲劳载荷进行准确的评估。
这包括对风、浪、流等环境载荷的分析,以及对船舶运动响应的计算。
通过先进的数值模拟技术和实验研究,可以获取较为准确的载荷数据,为后续的疲劳分析提供基础。
在材料选择方面,应优先选用具有良好抗疲劳性能的材料。
例如,高强度钢在船舶结构中的应用越来越广泛,但需要注意其在焊接等加工过程中可能产生的疲劳裂纹。
同时,对材料的质量控制也非常重要,避免材料中存在缺陷影响疲劳寿命。
船舶结构的细节设计对于抗疲劳性能有着重要的影响。
例如,在构件的连接处,应尽量减少应力集中现象。
通过采用合理的过渡圆角、优化焊接工艺等方法,可以降低连接处的应力水平,提高抗疲劳能力。
此外,对于容易产生疲劳损伤的部位,如甲板开口、舱口角隅等,应进行特殊的加强处理。
在船舶结构的抗疲劳分析中,常用的方法有基于应力的方法和基于损伤的方法。
基于应力的方法通过计算结构的应力范围和循环次数,结合材料的疲劳性能曲线来评估疲劳寿命。
基于参数化子模型的 SWATH 船典型节点抗疲劳设计
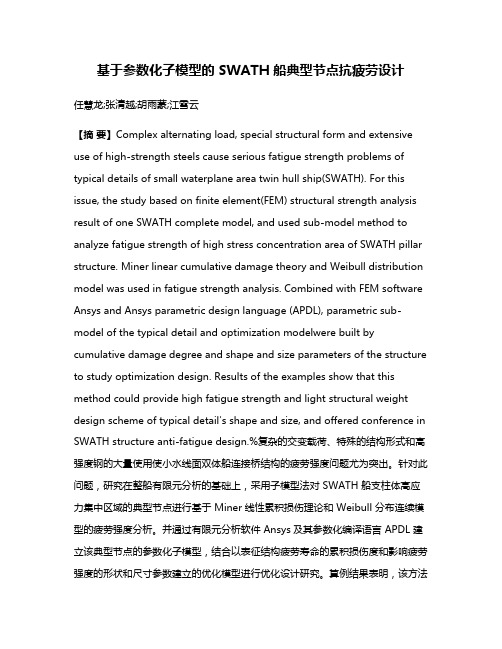
基于参数化子模型的 SWATH 船典型节点抗疲劳设计任慧龙;张清越;胡雨蒙;江雪云【摘要】Complex alternating load, special structural form and extensive use of high-strength steels cause serious fatigue strength problems of typical details of small waterplane area twin hull ship(SWATH). For this issue, the study based on finite element(FEM) structural strength analysis result of one SWATH complete model, and used sub-model method to analyze fatigue strength of high stress concentration area of SWATH pillar structure. Miner linear cumulative damage theory and Weibull distribution model was used in fatigue strength analysis. Combined with FEM software Ansys and Ansys parametric design language (APDL), parametric sub-model of the typical detail and optimization modelwere built by cumulative damage degree and shape and size parameters of the structure to study optimization design. Results of the examples show that this method could provide high fatigue strength and light structural weight design scheme of typical detail′s shape and size, and offered co nference in SWATH structure anti-fatigue design.%复杂的交变载荷、特殊的结构形式和高强度钢的大量使用使小水线面双体船连接桥结构的疲劳强度问题尤为突出。
基于谱分析法的穿浪双体船典型节点疲劳强度评估
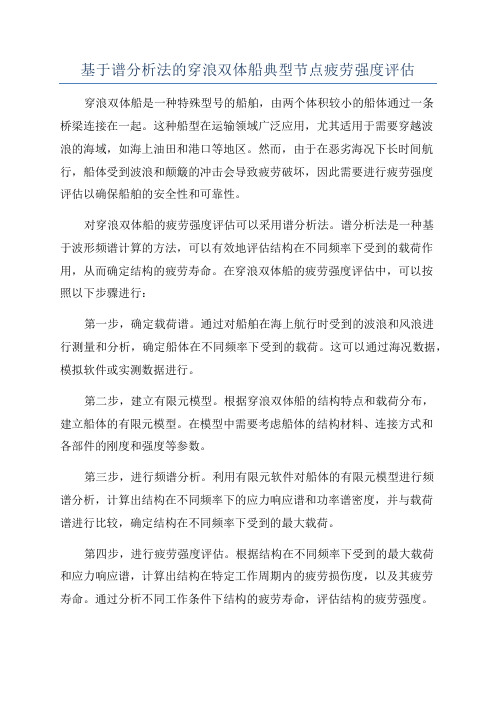
基于谱分析法的穿浪双体船典型节点疲劳强度评估穿浪双体船是一种特殊型号的船舶,由两个体积较小的船体通过一条桥梁连接在一起。
这种船型在运输领域广泛应用,尤其适用于需要穿越波浪的海域,如海上油田和港口等地区。
然而,由于在恶劣海况下长时间航行,船体受到波浪和颠簸的冲击会导致疲劳破坏,因此需要进行疲劳强度评估以确保船舶的安全性和可靠性。
对穿浪双体船的疲劳强度评估可以采用谱分析法。
谱分析法是一种基于波形频谱计算的方法,可以有效地评估结构在不同频率下受到的载荷作用,从而确定结构的疲劳寿命。
在穿浪双体船的疲劳强度评估中,可以按照以下步骤进行:第一步,确定载荷谱。
通过对船舶在海上航行时受到的波浪和风浪进行测量和分析,确定船体在不同频率下受到的载荷。
这可以通过海况数据,模拟软件或实测数据进行。
第二步,建立有限元模型。
根据穿浪双体船的结构特点和载荷分布,建立船体的有限元模型。
在模型中需要考虑船体的结构材料、连接方式和各部件的刚度和强度等参数。
第三步,进行频谱分析。
利用有限元软件对船体的有限元模型进行频谱分析,计算出结构在不同频率下的应力响应谱和功率谱密度,并与载荷谱进行比较,确定结构在不同频率下受到的最大载荷。
第四步,进行疲劳强度评估。
根据结构在不同频率下受到的最大载荷和应力响应谱,计算出结构在特定工作周期内的疲劳损伤度,以及其疲劳寿命。
通过分析不同工作条件下结构的疲劳寿命,评估结构的疲劳强度。
通过以上步骤,可以对穿浪双体船的典型节点进行疲劳强度评估,为船舶的结构设计和使用提供参考依据。
同时,谱分析法具有计算精度高、数据处理简便等优点,适用于船舶结构的疲劳分析和评估工作。
在今后的工作中,可以进一步优化疲劳分析方法,提高结构的疲劳强度,确保船舶在恶劣海况下的安全运行。
舰船结构疲劳容限设计优化研究
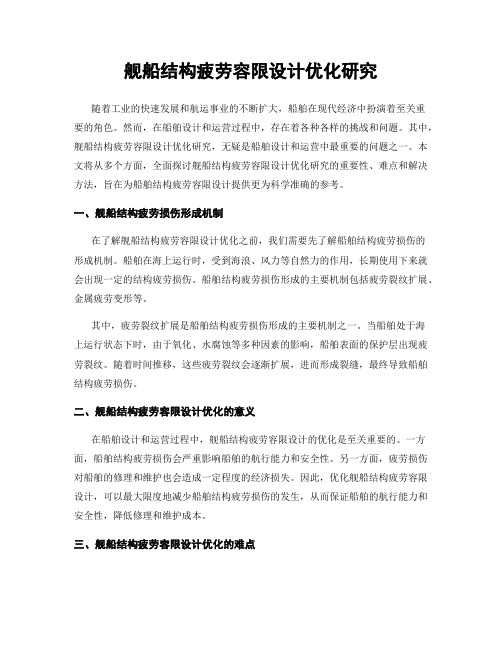
舰船结构疲劳容限设计优化研究随着工业的快速发展和航运事业的不断扩大,船舶在现代经济中扮演着至关重要的角色。
然而,在船舶设计和运营过程中,存在着各种各样的挑战和问题。
其中,舰船结构疲劳容限设计优化研究,无疑是船舶设计和运营中最重要的问题之一。
本文将从多个方面,全面探讨舰船结构疲劳容限设计优化研究的重要性、难点和解决方法,旨在为船舶结构疲劳容限设计提供更为科学准确的参考。
一、舰船结构疲劳损伤形成机制在了解舰船结构疲劳容限设计优化之前,我们需要先了解船舶结构疲劳损伤的形成机制。
船舶在海上运行时,受到海浪、风力等自然力的作用,长期使用下来就会出现一定的结构疲劳损伤。
船舶结构疲劳损伤形成的主要机制包括疲劳裂纹扩展、金属疲劳变形等。
其中,疲劳裂纹扩展是船舶结构疲劳损伤形成的主要机制之一。
当船舶处于海上运行状态下时,由于氧化、水腐蚀等多种因素的影响,船舶表面的保护层出现疲劳裂纹。
随着时间推移,这些疲劳裂纹会逐渐扩展,进而形成裂缝,最终导致船舶结构疲劳损伤。
二、舰船结构疲劳容限设计优化的意义在船舶设计和运营过程中,舰船结构疲劳容限设计的优化是至关重要的。
一方面,船舶结构疲劳损伤会严重影响船舶的航行能力和安全性。
另一方面,疲劳损伤对船舶的修理和维护也会造成一定程度的经济损失。
因此,优化舰船结构疲劳容限设计,可以最大限度地减少船舶结构疲劳损伤的发生,从而保证船舶的航行能力和安全性,降低修理和维护成本。
三、舰船结构疲劳容限设计优化的难点在舰船结构疲劳容限设计优化过程中,存在着多种难点和挑战。
其中,最主要的难点包括疲劳寿命预测、载荷谱选择、损伤积累分析等。
首先,疲劳寿命预测是舰船结构疲劳容限设计优化过程中最关键的难点。
疲劳寿命预测需要考虑多种因素,如船舶的结构材料、力学性能、海况、运行速度等等。
同时,船舶的工作环境和工作负荷也会对疲劳寿命预测造成一定的影响。
其次,载荷谱选择也是舰船结构疲劳容限设计优化的难点之一。
在选择载荷谱时,需要考虑多种因素,如船舶的运行状态、海况、航线等等。
船舶结构的疲劳与强度分析

船舶结构的疲劳与强度分析在广阔的海洋上,船舶作为重要的交通工具和运输工具,承载着无数的货物和人员。
然而,在长期的航行和复杂的海洋环境中,船舶结构面临着诸多挑战,其中疲劳与强度问题尤为关键。
理解和解决这些问题对于保障船舶的安全、可靠性以及使用寿命具有至关重要的意义。
船舶结构的疲劳是指在循环载荷作用下,材料或结构出现裂纹萌生、扩展,直至最终失效的现象。
这就好比我们反复弯折一根铁丝,经过多次弯折后,铁丝会在某个薄弱点断裂。
对于船舶来说,海浪的起伏、机器的振动、货物的装卸等都会产生循环载荷。
这些载荷虽然在单次作用下可能不会对船舶结构造成明显破坏,但长期积累下来,就可能导致结构疲劳损伤。
船舶在航行中会经历各种复杂的海况,如风浪、流等。
海浪的冲击会使船舶产生周期性的弯曲和扭转,这种反复的变形会在船舶结构内部产生应力。
当应力超过一定限度时,材料就会出现微观的缺陷,如位错、滑移带等。
随着循环次数的增加,这些微观缺陷逐渐聚集、扩展,形成微小的裂纹。
一旦裂纹达到一定长度,就会快速扩展,导致结构的失效。
船舶结构的强度则是指结构抵抗外力作用而不发生破坏或过大变形的能力。
这就像一座桥梁需要足够的强度来承受车辆和行人的重量一样,船舶结构也必须具备足够的强度来应对各种载荷。
船舶结构的强度分析包括静强度分析和动强度分析。
静强度分析主要考虑船舶在静止或匀速航行时所受到的恒定载荷,如重力、浮力、货物重量等。
通过计算这些载荷作用下结构的应力和变形,来评估结构是否满足强度要求。
而动强度分析则考虑船舶在动态环境下,如遭遇风浪、碰撞等情况下的响应。
这需要考虑惯性力、冲击力等动态载荷的影响,通常需要借助更复杂的数值分析方法和实验手段。
在实际的船舶设计和运营中,疲劳和强度问题是相互关联的。
如果船舶结构的强度不足,那么在正常使用过程中就更容易出现疲劳损伤。
反之,如果没有充分考虑疲劳问题,即使结构在初始阶段具有足够的强度,也可能在长期使用后由于疲劳裂纹的扩展而失效。
- 1、下载文档前请自行甄别文档内容的完整性,平台不提供额外的编辑、内容补充、找答案等附加服务。
- 2、"仅部分预览"的文档,不可在线预览部分如存在完整性等问题,可反馈申请退款(可完整预览的文档不适用该条件!)。
- 3、如文档侵犯您的权益,请联系客服反馈,我们会尽快为您处理(人工客服工作时间:9:00-18:30)。
船体典型结构节点抗疲劳设计研究
摘要:长期以来,船体结构的疲劳问题一直是船舶设计工作者十分关注的问题,特别是由于高强度钢在船体结构中的广泛使用,疲劳问题变得更加突出。
本文简
要分析了影响焊接接头疲劳强度的几种因素,并提出了提高结构抗疲劳性能的工
艺方法,可供有关方面参考。
关键词:疲劳设计;工艺方法;因素;船体结构
1前言
随着船舶大型化的发展,船舶结构的疲劳强度已成为确保船体结构安全的重
要问题,越来越受到国际航运及造船界的普遍重视。
由于船体结构疲劳所产生的
裂纹,破坏到一定程度对整个船舶将产生灾难性的后果,对船员人命安全及物质
财产产生重大损失,但疲劳裂纹的产生又具有很强的突发性和隐蔽性,极难发现。
因此在船舶设计阶段就应认真考虑船体结构的疲劳强度,船舶结构疲劳强度评估
的重要性不言而喻。
另外,船舶节点的抗疲劳设计是当代船舶设计核心技术之一,是从设计源头
提高船舶使用寿命的重要手段。
本文从影响焊接接头疲劳强度的因素、提高抗疲
劳性能的节点设计方法和工艺方法等方面,对船舶节点的抗疲劳设计展开讨论。
若把分析结论运用于设计实践,可为今后更好的进行结构抗疲劳设计提供理论基础,对提高新船的结构设计水平具有一定参考意义。
2影响焊接接头疲劳强度的因素
船舶结构节点多为焊接接头,焊接接头的疲劳强度主要决定于焊缝型式和焊
接工艺。
在相同的焊接工艺下,焊缝型式(如:对接接头、搭接接头、丁字接头、十字接头等)不同,焊接接头的疲劳强度不相同;同样,焊缝型式相同时,采用
不同的焊接工艺(如:手工电弧焊、CO2气体保护焊、埋弧自动焊等),疲劳强
度也会不相同。
在实际的船舶设计和施工过程中,影响焊接接头疲劳强度的因素
众多,主要有:应力集中、表面加工、焊接残余应力、焊接缺陷、尺寸因素等。
2.1应力集中和表面加工的影响
应力集中和焊接残余应力是影响焊接接头疲劳强度的两大主要因素。
试验表明,焊缝的凸出部是应力集中源,如果焊后不经机械加工,将使其疲劳强度大大
降低。
降低凸出部高度h,增大凸出部与轴线交角θ和过渡圆角半径r,将使疲劳强度增加。
使用机械加工方法将凸出部切除,应力集中可大大减小,对接接头的
疲劳极限可提高30%-70%。
对接头的整个表面进行打磨,可使母体金属和接头的
疲劳极限再提高30%左右。
但当焊缝有严重缺陷或未焊透时,其缺陷或未焊透处
的应力集中要比焊缝表面的应力集中严重得多,这时对焊缝表面进行机械加工是
毫无意义的。
另外,不同的焊缝型式,应力集中的程度不同:搭接接头的应力集中比对接
接头严重,疲劳强度也有所降低;对于丁字接头和十字接头,由于焊缝向基体金
属过渡处有明显的截面变化,其应力集中系数远比对接接头高,因此疲劳强度也
远比对接接头低。
提高丁字接头和十字接头疲劳强度的根本措施是:开破口焊接
使完全焊透和使焊缝向基体金属光滑过渡。
2.2焊接残余应力
焊接过程中常常产生拉伸残余应力,其值往往能达到材料的屈服点。
拉伸残
余应力相当于增加一个拉伸平均应力,从而使其疲劳极限降低。
为了消除焊接残
余应力,有时将焊接件进行退火或回火,这对焊接件的疲劳极限有双重影响。
消
除残余应力能使疲劳极限提高,但同时又使焊缝附近区域的金属软化,从而使疲
劳极限降低。
退火的最终的效果取决于两种因素的综合作用。
另外,喷丸处理和
锤击是提高焊接接头疲劳强度的有效手段。
2.3焊接缺陷
当母材或焊材质量差或焊接质量不高时,在焊接接头中可能产生各种缺陷,
如冷裂缝、热裂缝、未焊透、气孔和夹渣等,这些缺陷能造成严重的应力集中,
而大大降低其疲劳强度。
一般来说,焊接缺陷对疲劳强度的影响,与缺陷的种类、尺寸、方向和位置等很多因素有关。
2.4尺寸因素:
对于同一应力范围,随着构件厚度增加,接头的抗疲劳强度可能会降低。
这
种效应的产生是因为与邻近板厚度有关的焊趾的局部几何形状和厚度上的应力梯
度变化。
因此,基本设计S-N曲线适用于不超过基准厚度22mm的厚度。
对净厚
度大于22mm的构件,接头构件的S-N曲线应进行修正。
3提高结构抗疲劳性能的工艺方法
下面以双壳油轮的甲板横向强框架的大肘板趾部、内底板与底边舱斜板相交处、横舱壁与内壳相交处、底边舱斜板与内壳相交处、纵舱壁的垂直桁与内底连
接处、横舱壁的水平桁与内壳连接处等6个部位为例,说明提升结构抗疲劳性能
的工艺方法。
3.1规定的工艺方法
设计阶段,确定节点规范要求的疲劳寿命时,不考虑趾部打磨的优点。
但是
在采用所有设计方法后,如:增加局部厚度、延伸焊脚长度、修改局部几何形状等,结构的疲劳寿命仍然不能满足要求,可以考虑采用此方法。
计算出的疲劳寿
命应大于17年,且不考虑打磨效果。
采用打磨方式时,结构细节的打磨标准应
该包含打磨范围、光洁度、最终的焊缝形状、打磨工艺和采用的质量标准等。
打
磨最好采用旋转式砂轮,将打磨范围扩展到板面以下,以便消除焊趾缺陷的影响,并对打磨区域进行有效的腐蚀保护。
这种处理方法是在焊趾处形成一个光滑的凹面,并将任何可见的切口打磨至其底部以下至少0.5mm。
通常,产生凹面的深度
应尽可能小,其深度最大为1mm。
如能遵循以上的打磨建议,则可认为寿命最大提高至2倍。
3.2提高疲劳性能的工艺措施
(1)改善焊缝形状:如:打磨焊缝表面、打磨焊缝在焊趾处的圆角、采用TIG技术和等离子覆盖技术等;(2)减少焊接残余应力:如敲击(含锤击、针状
敲击等)、热处理以减轻应力、改变应力性质等;(3)改善焊接接头的环境条件:涂油漆和树脂涂料等。
3.3焊后特殊处理:TIG重熔和超声冲击技术
(1)焊趾处因焊缝向母材的过渡不圆顺、不光滑造成了应力集中,TIG重熔
能使焊趾处凸出部与轴线交角θ和过渡圆角半径r增大,使疲劳性能提高,而且TIG重熔对焊接接头焊趾外形的改变优于超声冲击处理。
(2)通过增大焊趾区硬度来改善疲劳性能:TIG和超声冲击处理可通过硬化
焊趾区材料而获得更好的疲劳性能改善量,前者的影响大于后者。
(3)对焊趾残余应力的影响:超声冲击处理后,在焊趾区形成了垂直于焊缝方向的残余压应力;原始焊态,残余应力较小,基本为0;TIG重熔后形成了残余
拉应力。
残余压应力对疲劳有利,残余拉应力对疲劳有害,因此,超声冲击处理
比TIG重熔对疲劳强度更有利。
(4)对提高焊接接头疲劳强度和寿命效果的对比:在高应力水平、短寿命区,TIG重熔比超声冲击处理对疲劳强度更有利;而在低应力水平、中长寿命区,超
声冲击处理比TIG重熔对疲劳强度有利。
综合以上4点,TIG重熔和超声冲击技术两方法有着很强的互补性。
如果将
焊接接头先进行一遍TIG重熔处理,获得高硬度,没有焊接缺陷且为平滑过渡;
再进行一次超声冲击处理,以获得高数值的残余拉应力,则焊接接头的疲劳强度
必有大幅度提高。
4结语
船舶结构节点的抗疲劳设计是船舶精益设计的一个重要方面,是决定船舶使
用寿命的主要因素。
通过对船体典型结构节点抗疲劳设计进行研究,得出若干典
型节点的抗疲劳设计标准,在具体设计时可参照这些设计标准。
通过对船舶节点
的抗疲劳设计进行了深入研究和讨论,旨在为今后全面按共同规范进行新船设计时,针对船舶节点的抗疲劳设计,提供一些参考性建议。
参考文献:
[1]李涛,罗秋明.船体典型结构节点抗疲劳设计[J].造船技术,2019(02):
38-42.
[2]陈超核.船体结构疲劳强度分析直接计算法[J].暨南大学学报(自然科学与医学版),2005(01):141-144.。