气基还原HYL-Ⅲ工艺介绍
新一代Midrex钢铁生产工艺
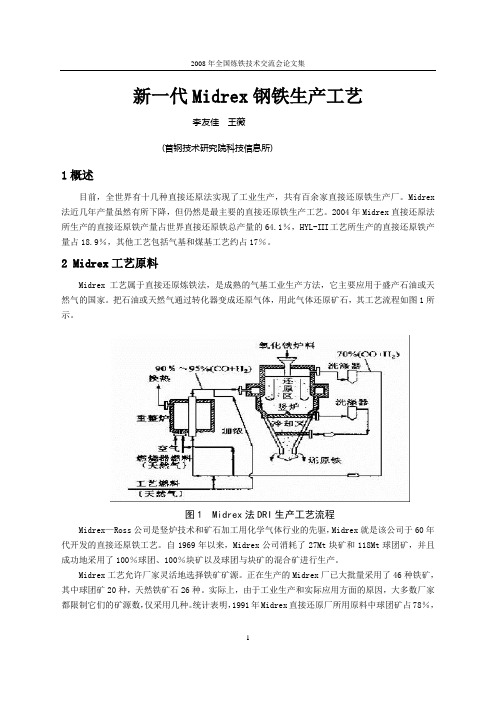
新一代Midrex钢铁生产工艺李友佳王薇(首钢技术研究院科技信息所)1概述目前,全世界有十几种直接还原法实现了工业生产,共有百余家直接还原铁生产厂。
Midrex 法近几年产量虽然有所下降,但仍然是最主要的直接还原铁生产工艺。
2004年Midrex直接还原法所生产的直接还原铁产量占世界直接还原铁总产量的64.1%,HYL-III工艺所生产的直接还原铁产量占18.9%,其他工艺包括气基和煤基工艺约占17%。
2 Midrex工艺原料Midrex工艺属于直接还原炼铁法,是成熟的气基工业生产方法,它主要应用于盛产石油或天然气的国家。
把石油或天然气通过转化器变成还原气体,用此气体还原矿石,其工艺流程如图1所示。
图1 Midrex法DRI生产工艺流程Midrex—Ross公司是竖炉技术和矿石加工用化学气体行业的先驱,Midrex就是该公司于60年代开发的直接还原铁工艺。
自1969年以来,Midrex公司消耗了27Mt块矿和118Mt球团矿,并且成功地采用了100%球团、100%块矿以及球团与块矿的混合矿进行生产。
Midrex工艺允许厂家灵活地选择铁矿矿源。
正在生产的Midrex厂已大批量采用了46种铁矿,其中球团矿20种,天然铁矿石26种。
实际上,由于工业生产和实际应用方面的原因,大多数厂家都限制它们的矿源数,仅采用几种。
统计表明,1991年Midrex直接还原厂所用原料中球团矿占78%,而块矿只占20%。
另外,对适合于Midrex直接还原工艺及其炼钢的铁氧化物原料的选择还应从化学和物理特性以及还原特性几方面加以考虑。
铁氧化物原料化学成分的重要性通常取决于最终使用者而非直接还原工艺。
随着三十多年来直接还原技术的进步,铁氧化物原料的化学成分对Midrex工艺来说已变得不太重要了。
然而化学成分对其后的DRI炼钢工艺却非常重要。
在直接还原工艺中,就原料而论,唯一的主要化学变化是从铁氧化物中脱氧,没有熔炼或精炼发生,基本上氧化铁原料中的所有杂质和脉石都存留在还原产品中。
如何构建低能耗的炼铁工艺流程

如何构建低能耗的炼铁工艺流程摘要:在介绍近年来国际上发展比较快的非高炉炼铁工艺以及一种低焦比高炉炼铁新工艺(全氧高炉)的基础上,综合考虑能源消耗、环境污染、资源利用、产品质量、生产效率等各方面因素,探讨如何构建低能耗的现代炼铁新工艺流程。
COREX、FINEX和HISMELT等熔融还原流程可以避免炼焦工艺引发的环境污染。
成熟的竖炉气基还原工艺是COREX流程工业化的重要保障, 粉体流化床由于粘结等问题尚未完全解决和铁浴炉二次燃烧与炉衬侵蚀之间的固有矛盾注定了FINEX和HISMELT实现的难度远高于COREX流程。
气基还原流程(MIDREX、HYL- III、FINMET) 目前都要使用天然气资源, 很难在我国得到发展。
转底炉可使用低强度的含碳球团,给煤基直接还原流程注入新的活力, 但其能耗高、生产效率低、产品质量差将会制约它的发展。
全氧高炉原理的是将以COREX的竖炉和熔融气化炉合为一体,降低高炉炼铁能耗,取消了COREX中部高温区的所有活动部件,将COREX工艺的优质块煤炉内造气改用廉价粉煤炉外气化来代替。
关键词:低能耗;熔融还原;直接还原;全氧高炉引言钢铁产品是人类社会最主要的结构材料,也是产量最大、覆盖面最广的功能材料。
2007年我国的粗钢产量约4. 9亿t/a,生铁产量4. 6亿t/a,遥遥领先于其它国家。
然而,钢铁工业又是资源、能源密集型产业,资源、能源消耗大,排放量大。
高炉炼铁主要包括原料造块(包括烧结、氧化球团)、焦化、高炉主体。
单原料造块一项,吨铁能耗就达到100kg标煤;炼焦工序的吨铁能耗需要65kg标煤;高炉主体吨铁燃料比在510kg左右,在考虑尾气能量回收利用情况下,能耗也在450 kg左右。
因此,每吨铁水的净能耗达到615kg左右,而一次能耗超过700kg标煤。
由于高炉炼铁系统的高能耗、高排放,长期以来,冶金界一直在开发无焦或少焦的非高炉炼铁流程。
1 熔融还原1.1 COREX流程1.1.1 COREX对煤种的要求较高COREX对煤种的要求较高,我国很多煤种不宜使用,另外COREX存在粉煤如何利用的问题。
达涅利ENERGIRON直接还原技术

世界金属导报/2010年/6月/22日/第014版设备制造达涅利ENERGIRON直接还原技术1简介本文根据CO2排放量分析,比较三种炼钢工艺对环境的影响:・传统联合炼钢厂,高炉-氧气顶吹转炉(BF-BOF)。
・现代联合炼钢厂,直接还原工艺(基于天然气)-电弧炉(DRP-EAF)。
・现代联合炼钢厂,直接还原工艺(基于可气化煤)-电弧炉(DRP-EAF)。
达涅利和HYL开发的ENERGIRON气基直接还原技术是先进的铁矿石冶炼工艺,此项技术的目标是:・通过减少温室气体排放降低对环境的影响。
・根据主要能量来源,利用各种工业气体,如天然气或煤气化产生的合成煤气或焦炉煤气。
炼钢产业的特征就是大量使用化石燃料,而化石燃料排放导致全球变暖的温室气体(GHG),给环境造成极大的影响,这些气体主要是CO2。
CO2的排放量和特点由炼钢厂使用主要燃料的特性所决定。
在传统联合炼钢高炉工艺中,用来还原氧化铁的主要能源是煤。
在现代联合炼钢DRP直接还原工艺中,用来还原氧化铁的主要能源可以是天然气或煤或任何工业气体。
2联合炼钢厂的CO2排放2.1传统联合炼钢厂的CO2排放图1显示的是传统联合炼钢厂典型的能量平衡。
这个工厂设备包括:炼焦炉设备、烧结车间、生产铁水(HM)高炉、氧气顶吹转炉(BOF)、钢包炉/真空脱气设备、生产热轧带卷(HRC)的薄板坯连铸机和带钢热轧机。
能从传统联合炼钢厂中回收的主要气态燃料副产品包括:烧结车间气体(sPG)、炼焦炉设备气体(COG)、鼓风炉气体(BFG)和氧气顶吹转炉气体(BOFG)。
传统联合炼钢厂的能量平衡显示大多数气态燃料主要用于产生能量或燃烧发热。
传统联合钢厂烟道气排放CO2每吨钢水约为2.104t。
2.2现代联合炼钢厂的CO2排放图2显示的是现代联合炼钢厂典型的能量平衡,这些ENERGIRON直接还原炼钢厂的主要燃料是天然气。
这个工厂包括:球团车间、生产直接还原铁(DRI)的ENERGIRON直接还原炼钢车间(DRP)、电弧炉(EAF)、钢包炉/真空脱气设备、生产热轧带卷(HRC)的薄板坯连铸机和带钢热轧机。
焦炉煤气生产直接还原铁技术研究

焦炉煤气生产直接还原铁技术研究一、技术背景。
进展直接还原铁生产是电炉钢短流程进展的需要。
我国钢铁产量已持续连年居世界第一名,但钢铁工业结构不合理,主要体此刻低附加值产品多余,而高级钢材仍需入口。
随着我国钢铁工业结构的调整和对钢铁产品质量要求的提高,电炉钢短流程必然会取得较快进展。
传统的电炉冶炼以废钢作为主要原料,而我国废钢资源不足,每一年的废钢入口量都在1000万吨以上;另外,废钢中杂质元素的不断积累会对优质钢的生产造成不利影响。
直接还原铁作为废钢的重要替代品是电炉炼钢的理想原料,它具有纯净度高、成份稳固等长处,是进展钢铁生产短流程的基础。
利用焦炉煤气生产直接还原铁是钢铁行业实现节能减排的有效途径。
传统炼铁工艺受焦煤资源欠缺的影响,其进展受到制约。
进展直接还原铁生产不仅能够改变传统炼铁工艺长期以来对焦煤的依赖,同时能够减少二氧化碳排放量(与煤基直接还原相较,吨铁CO2排放量能够从2000kg降低到400kg以下),符合钢铁工业可持续进展的技术要求,是钢铁行业实现节能减排的有效途径。
多余焦炉煤气的存在为进展气基直接还原提供了根本动力。
我国焦化企业每一年产生大量多余的焦炉煤气,这为开展焦炉煤气竖炉法生产直接还原铁提供了可能。
另外,随着热风炉(和加热炉)技术的进步,利用单一的高炉煤气就可以够实现1300℃的风温,这使得利用低热值的煤制气加热焦炉(或用于加热炉),从而置换出部份焦炉煤气用于直接还原铁生产成为可能,这在必然程度上扩大了焦炉煤气的来源,为焦炉煤气规模化生产直接还原铁提供了保障。
焦炉煤气利用方式的选择。
两种途径:燃料化和资源化。
焦炉煤气中CH4:25%〜26%,H2 : 56%〜%,H2发烧值仅为2580kCal/m3约为曱烷的四分之一,因此,将焦炉煤气作发烧剂不尽合理。
由于氢气的还原潜能远远高于CO,因此将焦炉煤气用作还原剂更有利于其化学能的合理利用。
与天然气相较焦炉煤气中的甲烷含量更低,这使得其重整负荷减轻,耗氧量减少,能量消耗也降低。
直接还原炼铁

一 直接还原炼铁简介
7、世界直接还原铁生产概况 2012年,全球直接还原铁产量达到7402万吨,其中
印度位居第一,2005万吨。伊朗第二,1158万吨。
全球主要直接还原铁生产大国/MT
国家
印度
伊朗
墨西 哥 委内 瑞拉 中国
2004 9.37 6.41 6.54
7.83 0.43
2005 2006 2007 2008 2009 2010 2011 2012 12.04 14.74 19.06 21.20 22.03 23.42 21.97 20.05 6.85 6.85 7.44 7.46 8.20 9.53 10.37 11.58 5.98 6.17 6.26 6.01 4.15 5.37 5.85 5.59
2.4 Fastmet转底炉法工艺
2.5 CODIR煤基回转窑法工艺
➢该工艺原料可为球团矿、块矿,也可为粉矿,还原剂采用挥 发分较小的高活性煤 ,脱硫剂用石灰石或白云石。炉料、还 原煤和脱硫剂从回转窑尾部进入窑内后在与炉气逆向运动 过程中将矿石还原为海绵铁。
➢CODIR 回转窑工艺流程中约占总量 70 %的还原煤由窑头 用压缩空气喷入 ,因此较好地抑制了再氧化和结圈现象。冷 却筒采用间接和直接水冷相结合的方式 ,提高了设备的作业 率 ,有利于回转窑的连续、 稳定生产 ,在多种回转窑工艺中 具有较突出的优势。
目前投入工业应用的直接还原工艺主要有Midrex工艺、HYLIII工艺、Finmet工艺、SL/RN工艺等。2012年全球DRI产量达 到7402万吨,Midrex工艺和HYL-III工艺生产的DRIDRI所占比 例达到76.3%。
2.1 Midrex(米德兰)法工艺
➢ Midrex 法具有工艺成熟、操作简单、生产率高、热耗低、 产品质量高等优点, 因此在直接还原工艺中占统治地位。
直接还原炼铁

炉内压力: 250KPa左右 天然气能耗:
10.2~11t/GJ 炉料在整个炉内停 留时间:10h左右
还原区温度: 850℃左右
金属化率:>92%
H 2 C O 1
C4 H 1/22 O催 化 剂 CO 2H 2
C4 H C2 O 催 化 剂 2CO 2H A2
12
2.2 HYL-III(Energiron)法工艺
A
13
2.2 HYL-III(Energiron)法工艺
C4 H H 2 O 催 化 3剂 2H CO
炉内压力:600KPa 天然气能耗:
10~11.3t/GJ 炉料在整个炉内停留
时间:大于10h 还原区温度:
900~960℃ 金属化率:>91%
H 2 C> O 2
A
14
2.3 HYL-ZR法工艺
直接还原炼铁
A
1
一 直接还原炼铁简介
1 、定义 直接还原炼铁(Direct Reduction Iron)是一种采用
天然气、煤气、非焦煤粉作燃料和还原剂, 使用球团矿、 块矿、粉矿在在软化温度以下直接还原生产固体直接还原 铁( DRI /HBI) 的炼铁工艺技术。
2 、优点 ① 使用非焦煤,取消了炼焦和烧结等高能耗高污染工序 ② DRI/HBI 中P、S和和有色杂质(Cu、Ni、Cr、Mo、Sn等)
➢ HYL-ZR是在原HYL工艺系列上发展起来的一种新型气基自 重整直接还原工艺,HYL-ZR技术可在其工艺和设备无任何改 动情况下使用焦炉煤气、Corex熔融还原炉产生的煤气或者 合成气 ,而其他技术大都需要对其基本配置进行重大改动 。目前开始在我国和印度等地区应用。
➢在竖炉内通过对还原气进行控制而产生合乎要求的还原气 体 ,其还原气体经过不完全燃烧 ,以及在还原反应器内经 过金属铁的催化作用在现场重整而生成 ,从而对铁矿石进 行还原;而传统HYL-Ⅲ 工艺是在添加蒸汽条件下使天然气 在催化重整装置中裂解。
我国煤基直接还原炼铁工艺发展
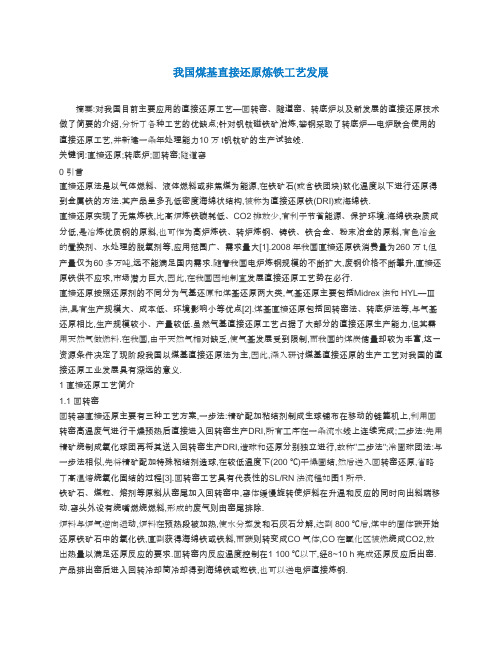
我国煤基直接还原炼铁工艺发展摘要:对我国目前主要应用的直接还原工艺—回转窑、隧道窑、转底炉以及新发展的直接还原技术做了简要的介绍,分析了各种工艺的优缺点;针对钒钛磁铁矿冶炼,攀钢采取了转底炉—电炉联合使用的直接还原工艺,并新建一条年处理能力10万t钒钛矿的生产试验线.关键词:直接还原;转底炉;回转窑;隧道窑0 引言直接还原法是以气体燃料、液体燃料或非焦煤为能源,在铁矿石(或含铁团块)软化温度以下进行还原得到金属铁的方法.其产品呈多孔低密度海绵状结构,被称为直接还原铁(DRI)或海绵铁.直接还原实现了无焦炼铁,比高炉炼铁碳耗低、CO2排放少,有利于节省能源、保护环境.海绵铁杂质成分低,是冶炼优质钢的原料,也可作为高炉炼铁、转炉炼钢、铸铁、铁合金、粉末冶金的原料,有色冶金的置换剂、水处理的脱氧剂等,应用范围广、需求量大[1].2008年我国直接还原铁消费量为260 万t,但产量仅为60多万吨,远不能满足国内需求.随着我国电炉炼钢规模的不断扩大,废钢价格不断攀升,直接还原铁供不应求,市场潜力巨大,因此,在我国因地制宜发展直接还原工艺势在必行.直接还原按照还原剂的不同分为气基还原和煤基还原两大类,气基还原主要包括Midrex法和HYL—Ⅲ法,具有生产规模大、成本低、环境影响小等优点[2].煤基直接还原包括回转窑法、转底炉法等,与气基还原相比,生产规模较小、产量较低.虽然气基直接还原工艺占据了大部分的直接还原生产能力,但其需用天然气做燃料.在我国,由于天然气相对缺乏,使气基发展受到限制,而我国的煤炭储量却较为丰富,这一资源条件决定了现阶段我国以煤基直接还原法为主,因此,深入研讨煤基直接还原的生产工艺对我国的直接还原工业发展具有深远的意义.1 直接还原工艺简介1.1 回转窑回转窑直接还原主要有三种工艺方案,一步法:精矿配加粘结剂制成生球铺布在移动的链篦机上,利用回转窑高温废气进行干燥预热后直接进入回转窑生产DRI,所有工序在一条流水线上连续完成;二步法:先用精矿烧制成氧化球团再将其送入回转窑生产DRI,造球和还原分别独立进行,故称"二步法";冷固球团法:与一步法相似,先将精矿配加特殊粘结剂造球,在较低温度下(200 ℃)干燥固结,然后送入回转窑还原,省略了高温焙烧氧化固结的过程[3].回转窑工艺具有代表性的SL/RN法流程如图1所示.铁矿石、煤粒、熔剂等原料从窑尾加入回转窑中,窑体缓慢旋转使炉料在升温和反应的同时向出料端移动.窑头外设有烧嘴燃烧燃料,形成的废气则由窑尾排除.炉料与炉气逆向运动,炉料在预热段被加热,使水分蒸发和石灰石分解,达到800 ℃后,煤中的固体碳开始还原铁矿石中的氧化铁,直到获得海绵铁或铁料,而碳则转变成CO气体,CO在氧化区被燃烧成CO2,放出热量以满足还原反应的要求.回转窑内反应温度控制在1 100 ℃以下,经8~10 h完成还原反应后出窑.产品排出窑后进入回转冷却筒冷却得到海绵铁或粒铁,也可以送电炉直接炼钢.与高炉工艺相比较,回转窑工艺设备简单,投资少,适用于地方钢铁工业,弥补了高炉—转炉工艺的不足,此外,回转窑还适用于复合矿冶炼,冶金灰尘及各种工业废渣的回收利用,减少环境污染,降低了钢铁生产能耗.同时,回转窑工艺也存在一些缺点,包括窑内结圈、还原温度低(1 100 ℃以下)、流程长、对块矿或球团矿冷强度要求高、要求使用低硫煤等[4].我国山东鲁中矿山公司通过采取提高冷固烧结球团的冷热态强度、加强还原煤的选择和管理、优化回转窑的送风、抛煤、控温温度等措施,预防并降低回转窑结圈,取得了较好的收效.图1 SL/RN法工艺流程1.2 隧道窑隧道窑工艺即将精矿粉、煤粉、石灰石粉,按照一定的比例和装料方法,分别装入还原罐中,然后把罐放在罐车上,推入条形隧道窑中或把罐直接放到环形轮窑中,料罐经预热到1 150 ℃加热焙烧和冷却之后,得到直接还原铁.目前江苏永钢集团拥有两条260 m长煤气隧道窑,为亚洲最长隧道窑.隧道窑生产海绵铁工艺流程如图2所示.图2 隧道窑生产海绵铁工艺流程煤基隧道窑直接还原工艺具有技术成熟、作简单的特点,可因地制宜采用此工艺,利用当地小型分散的铁矿及煤矿资源优势,发展直接还原铁生产,为电炉提供优质原料.但是,总体上讲,我国隧道窑直接还原中存在生产规模较小、能耗高、污染严重、缺乏稳定的原料供应渠道等问题[5],所以,提高机械化程度、改变原料入炉方式、改进燃料及其燃烧、增设余热回收等成为各厂家不断努力改进工艺的方向.我国已建成或正在建设的隧道窑有100多座,约70多个单位规划建设产能5~30 万t/a的隧道窑直接还原铁厂,在不断总结实践经验的基础上,改进现行工艺,开发出诸如大型隧道窑直接还原、AMR—CBI隧道窑直接还原工艺、宽体球状海绵铁隧道窑、L-S快速还原工艺等多种新技术,掀开了隧道窑工艺规模扩大、产能提高、机械及自动化提升的序幕.1.3 转底炉转底炉煤基直接还原是最近几十年间发展起来的炼铁新技术,代表工艺为Fastmet,它由美国Midrex公司与日本神户制钢于20世纪60年发,是采用环形转底炉生产直接还原铁的一种方法.经过多年的半工业性试验和深入的可行性研究,现已完成工艺作参数和装置设计的优化.Fastmelt和ITmk3工艺是在此基础上增加对直接还原铁的处理.图3显示了这三种以转底炉为主体的直接还原工艺流程.图3 转底炉直接还原工艺流程煤粉与铁精粉按比例混匀制成球团,干燥后以1~3层球铺放在转底炉床面,随着炉底的旋转,炉料依次经过预热区、还原区和冷却区.还原区内球团被加热到1 250~1 350 ℃,由于煤粉与铁氧化物紧密接触,铁氧化铁被碳迅速还原成DRI,成品在800~1 000 ℃左右连续从转底炉卸出.球团矿在炉底停留8~30 min,这取决于原料特性、料层厚度及其他因素,成品可作电炉热装炉料或者转炉炉料,也可冷却或生产热压块(HBI).Fastmet工艺技术特点:①在高温敞焰下加热实现快速还原,反应时间只需10~20 min,生产效率高;②原料来源广泛,铁原料方面,除使用高品位粉矿、精矿外,还可用氧化铁皮、代油铁泥、炼钢粉尘、含En、Pb、As等有害杂质的铁矿等;还原剂方面,除煤以外焦末、沥青均可利用,不必担心出现结圈问题;③炉料相对炉底静止,对炉料强度要求不高;④废气中含有大量显热,可用作预热空气、干燥原料等[6]. Fastmelt工艺流程基本与Fastmet一致,只是在后续添加一个熔炉来生产高质量的液态铁水.Itmk3工艺是使金属化球团在转底炉中还原时熔化,生成铁块(Nuggets),同时脉石也熔化,形成渣铁分离.当然转底炉也存在着设备复杂、炉内气氛难控制、传热效率低以及对还原剂硫含量要求严格的缺点.就目前转底炉工艺开发的水平和规模而论,与高炉还有较大差距,但仍存在发展的广阔空间,天津荣程联合钢铁集团已兴建一条100万t级Fastmet生产线,建成目前世界最大的转底炉.另外,用转底炉可处理一些特殊铁矿,如含锌、铅、砷等有害杂质,或含镍、钒、钛等有用元素,均可利用转底炉的工艺优势,或高温挥发,或选择性还原,配合后续工艺,实现资源综合利用.马钢尘泥脱锌转底炉工程项目于2008年5月开工建设,2009年7月6日正式竣工投产,建成了整套转底炉(RHF)脱锌工艺技术装置,不仅解决了含锌尘泥循环利用的后顾之忧,而且将综合利用技术上升到高品质资源化水平.1.4 其他新工艺1.4.1 PF法煤基竖炉直接还原工艺中冶集团北京冶金设备研究设计总院,结合国内情况创新发明了PF法竖炉直接还原工艺.PF法是在吸收K-M法外热式竖炉煤基直接还原工艺的经验基础上,设计的以一种中国特色的罐式还原炉为主反应器的直接还原法.这种工艺技术可靠,技术经济指标在各种煤基直接还原工艺中属先进水平.PF法直接还原工艺流程如图4所示.图4 PF法直接还原工艺流程PF法直接还原工艺主要特点[1]:1)主体设备选用外热式竖炉,预热、还原、冷却三段根据不同的作用和温度选用不同材质和结构,便于传热和化学反应进行,提高热效率和设备寿命.2)原燃料适用性强,对精矿、还原剂和燃料没有特殊要求.3)采用外配碳工艺,还原剂适当过量,扩大了煤的选用范围,造球工艺也因不定量配入煤粉而简化,球团强度较高,DRI质量较好.4)多个反应罐可并列组成任意规模的还原设备,设计和组织生产灵活.1.4.2 低温快速还原新工艺2004年钢铁研究总院提出了低温快速冶金新工艺.新工艺利用纳米晶冶金技术的特点将铁矿的还原温度降低到700 ℃以下.新流程分为气基和煤基两种方法,工艺流程如图5、图6所示.图5 煤基低温快速还原新工艺图6 气基低温快速还原新工艺煤基法使用煤粉为还原剂,在700℃左右快速还原铁精矿粉;气基法使用还原性气体还原铁精矿粉,还原温度可低于600℃.新工艺具有能耗低、环境友好等特点,省去了烧结或造球工艺,缓解了钢铁行业对焦煤的依赖,符合我国国情[7].2 攀钢现状钒钛磁铁矿是攀西地区的特色资源,与普通矿相比,钒钛矿直接还原温度较高、还原时间较长,还原过程产生特有的膨胀粉化现象,因此,存在竖炉结瘤、流化床失流和黏结、回转窑结圈等技术难题.高炉流程冶炼钒钛矿,只回收了铁和钒,钛进入高炉渣没有回收,造成钛资源的大量流失.2005年以来,攀钢科研人员在充分吸收、借鉴新流程及相关研究成果的基础上,通过大量的试验研究,针对钒钛磁铁矿特点,提出并验证了钒钛磁铁矿"转底炉直接还原—电炉深还原—含钒铁水提钒—含钛炉渣提钛"工艺路线,彻底打通了钒钛矿资源综合利用新工艺流程,稳定获得了质量满足要求的低碳生铁、达到GB3283-87要求的片状V2O5和PTA121质量要求的钛白产品.依托该研究成果,攀钢集团攀枝花钢铁研究院于2008年5月4日正式启动了攀钢10 万t/a钒钛矿资源综合利用新工艺中试线工程项目,新建一条转底炉—熔分电炉联合使用,年处理能力10万t钒钛矿的试验生产线,为更深入地研究实践,实现转底炉处理钒钛矿的规模化生产提供了广阔的平台.中试线工艺流程如图7所示.本流程采用硫含量较低的白马铁精矿,还原剂采用无烟煤煤粉,粘结剂为有机粘结剂,原料混合后经高压压球机压球,生球烘干后进入转底炉系统.球团在转底炉内停留10~30 min后出料,金属化球团直接热装进入熔分电炉,在一定温度下还原后,产出含钒铁水及含钛炉渣.继续对铁水进行脱硫、提钒后,得到半钢、脱硫渣及钒渣,半钢进入铸铁机铸铁,生产出铸铁块.钛渣制取钛白,实验室条件下钛回收率达到80%以上;钒渣制取钒氧化物(V2O5),实验室条件下,钒回收率达到65%以上.与高炉流程相比,转底炉流程采用100%钒钛矿冶炼,克服了高炉流程必须配加普通矿的不足,在当前铁资源紧张的形势下,有助于充分发挥攀西地区资源优势,拉动区域经济发展.此外,转底炉流程的铁精矿不需烧结处理,不使用焦炭,从根本上避免了烧结烟气脱硫、焦煤资源采购困难以及环保压力大等问题.3 结语图7 资源综合利用中试线工艺流程煤炭资源总量丰富、焦煤短缺,铁矿资源储量大、富矿少、贫矿和共生矿多是中国钢铁工业面临的现实状况.这种能源、资源结构给煤基直接还原法生产海绵铁的发展提供了机遇.转底炉直接还原技术由于在生产率、规模化、投资费用、单位成本等方面都占有明显的优势,可作为发展直接还原技术的首选工艺.鉴于转底炉处理钒钛磁铁矿技术尚属世界首创,并无较多的经验借鉴,因此要大力开展针对钒钛磁铁矿直接还原的基础研究工作,在实践中借鉴各种直接还原方法已取得的成果,开拓创新,开创钒钛矿直接还原新纪元.参考文献[1] 陈守明,黄超,张金良.煤基竖炉直接还原工艺//2008年非高炉炼铁年会文集.中国金属学会,2008:132-135.[2] 杨婷,孙继青.世界直接还原铁发展现状及分析.世界金属导报,2006.[3] 刘国根,邱冠周,王淀佐.直接还原炼铁中的粘结剂.矿产综合利用,2001(4):27-30.[4] 韩跃新,高鹏,李艳军.白云鄂博氧化矿直接还原综合利用前景.金属矿山,2009 (5):1-6.[5] 魏国,赵庆杰,沈峰满,等.非高炉生产技术进步//2004年全国炼铁生产技术暨炼铁年会文集.2004:878-882.[6] 陶晋. 环形转底炉直接还原工艺现状及发展趋势. 冶金信息工作, 1997.6.[7] 郭培民,赵沛,张殿伟.低温快速还原炼铁新技术特点及理论研究.炼铁,2007,26(1): 57-60.来源:攀枝花钢铁研究院网站。
氢气还原三氯化砷制备高纯砷的工艺研究

【有的放矢】周国平说:“我们看见利益,却看不见真理;看见万物,却看不见美;看见世界,却看不见上帝。
我们的日子是满的,生命却是空的;头脑是满的,心却是空的。
”请以“满与空”为题写一篇不少于800字的文章。
要求:①角度自选;②立意自定;③除诗歌外,文体自选。
【思维导引】“满与空”这个题目属于关系型作文题,同时它还是一个哲理性的话题。
“满与空”可以是物理属性上的两种状态,如客人到家,给对方斟酒须要“满杯”;逛商场看到心仪的商品,但摸摸口袋却囊中羞涩,空空如也。
也可以是人心灵深处的两种状况。
结合提示语我们至少可以这样理解:“满”可以指物质欲望太甚、日程安排太满等等,“空”可以指心中没有真善美的滋养,生命很空洞、苦涩,过分追逐外界而忘记自我的存在,完全投入到物欲谋求中,忘记心中忽视对道德律的敬畏等等。
【存在问题】1、“满”和“空”在作文中可以指代实的东西,也可以指代虚的东西。
但不少学生在本次作文没有将“满”和“空”具体指代的内容说出、说清,整篇文字看起来空洞无物,套话连篇。
注意:几乎所有高考作文题都存在一个切入口化大为小的问题,将作文题中的相关概念缩小范围,有所明确、有所具体指代是做好作文最基本的前奏。
)2、点题、扣题意识仍非常单薄。
(这一点非常重要,做不好让人觉得你在偏题、甚至是跑题)建议:每位同学用红笔在自己的试卷上圈画出自己的点题、扣题的字句。
3、入题太慢不少同学行文至三分之一处,仍然不见题目中的关键字、关键词。
原则上必须在文章的第一节末尾处就该出现题目中的关键字、关键词。
4、题目为关系型作文题,但不少学生在行文中丝毫不理会两者之间的关系,各自为政。
有些同学即使提及两者关系,但是由于缺乏较高的思辨能力,二者关系处理起来也是有失偏颇。
建议:学生平时多训练自己对某些具体问题的思辨能力。
5、部分记叙文没有从自己生活中选材,缺乏相应的观察和思考,却在虚构一个虚假故事,严重脱离生活实际。
如故事的主题发生在小山村中、某个大都市中、某个公司里等等。
复杂难选铁矿石直接还原技术的应用

复杂难选铁矿石直接还原技术的应用张进(武汉科技大学资源与环境工程学院,湖北武汉,430081)摘要本文阐述了我国复杂难选铁矿开发利用现状,对近年来处理复杂难选铁矿的新工艺—直接还原技术进行了介绍和分析,指出了该工艺的特色和优点。
重点介绍了直接还原技术在我国复杂难选铁矿中的应用实践,同时指出煤基转底炉直接还原工艺较适合处理我国复杂难选铁矿,并针对目前存在的问题,提出了下一步的研究方向。
关键词难选铁矿现状直接还原应用世界铁矿资源丰富,据美国地质调查局报告,截止2005年底,世界铁矿石储量为1600亿t,储量基础为3700亿t,铁金属储量为800亿t,储量基础为1800亿t。
世界铁矿资源分布的特点是南半球国家富铁矿床多,如巴西、澳大利亚、南非等国;北半球国家贫铁矿床多,如前苏联地区、美国、加拿大、中国等国。
我国铁矿石富矿少、贫矿多,97%的铁矿石为30%以下的低品位铁矿,国内尚存大量未被开发利用的难选铁矿。
另外,铁矿石资源开发利用自进入21世纪以来,呈逐渐上升态势,2006年世界铁矿石价格比上一年上涨19%,使我国钢铁行业面临着巨大的压力[1]。
总结国内难选铁矿选矿技术进展、推进选矿技术进步,更好地利用这部分资源,对支持我国钢铁行业的发展,具有一定的现实意义。
1复杂难选铁矿石研发利用现状我国探明的铁矿资源量380~410亿t,主要特点是贫、细、杂,平均铁品位32%,比世界平均品位低11个百分点。
其中97%的铁矿石需要选矿处理,并且复杂难的红铁矿占的比例大(约占铁矿石储量的20.8%)[2]。
铁矿床成因类型多样,矿石类型复杂。
表1.1 我国铁矿石主要分布特点[2]Table 1.1 The main distribution characteristics of iron ore in our country进展,即先通过强磁一反浮选获得低杂质含量的铁精矿,然后通过普通焙烧或者与磁铁精矿混合生产球团矿可大幅度提高产品的铁品位,仍不失为优质炼铁原料。
气基竖炉工艺
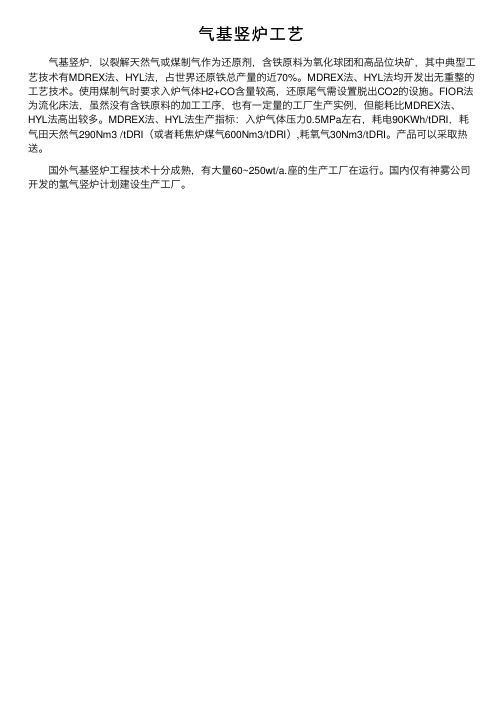
⽓基竖炉⼯艺
⽓基竖炉,以裂解天然⽓或煤制⽓作为还原剂,含铁原料为氧化球团和⾼品位块矿,其中典型⼯艺技术有MDREX法、HYL法,占世界还原铁总产量的近70%。
MDREX法、HYL法均开发出⽆重整的⼯艺技术。
使⽤煤制⽓时要求⼊炉⽓体H2+CO含量较⾼,还原尾⽓需设置脱出CO2的设施。
FIOR法为流化床法,虽然没有含铁原料的加⼯⼯序,也有⼀定量的⼯⼚⽣产实例,但能耗⽐MDREX法、HYL法⾼出较多。
MDREX法、HYL法⽣产指标:⼊炉⽓体压⼒0.5MPa左右,耗电90KWh/tDRI,耗⽓⽥天然⽓290Nm3 /tDRI(或者耗焦炉煤⽓600Nm3/tDRI),耗氧⽓30Nm3/tDRI。
产品可以采取热送。
国外⽓基竖炉⼯程技术⼗分成熟,有⼤量60~250wt/a.座的⽣产⼯⼚在运⾏。
国内仅有神雾公司开发的氢⽓竖炉计划建设⽣产⼯⼚。
直接还原法

5、世界煤基直接还原铁生产概况 ★据统计 ,1980 年全球直接还原铁(海绵铁)的产 量仅为728 万 t ,2006 年约为 5980 万 t。平均 年增长率在 8 % 以上。印度连续四年为最大 的直接还原铁生产国 ,2006 年产量接近1500 万t , t ,同比增长35 % , 35 ,占世界总产量的 25 % , ,委 内瑞拉以产量 860 万 t 位居第二 ,伊朗以产量 690 万 t 位居第三 ,墨西哥以产量620 万 t 位 居第四。 2008 年底还有一些新增产能将投
1、Fastmet法 ★Fastmet 法是采用环形回转炉生产直接还原铁的一种 方法。该方法用煤粉和铁矿粉作原料 ,制成的冷固结含 炭球团矿在炉中不依靠焦炭和天然气而实现高温还原。 ★特点: (1)用转底炉运载炉料 ,并在高温敞焰下加热实现快速还 原。 (2)还原过程时间很短 ,仅仅 6~12 min ,设备的起动与 停止、 产量的调整都可比较简单地进行。
2、直接还原法的优点 ①不用焦炭,取消了焦炉、烧结等工序 ②DRI中硫、磷、有色金属杂质含量低,利于炼优 质钢 3、直接还原法的缺点 ①对原料要求高,要优质的高品家地区严重缺乏焦煤, 不能发展高炉— —转炉工艺, 但他们有丰富的天然气和普通烟 煤, 有价廉质优的铁矿石。 ②科学技术进步,对钢材质量和品种提出了更 高的要求。 ③废钢-电炉-连铸连轧钢铁生产短流程的兴起。
1、Midrex和 Hy L - Ⅲ 气基竖炉技术 目前 ,全世界共有百余家直接还原铁生产厂。 Midrex和 Hy L - Ⅲ 气基竖炉法是最主要的直接还 原铁生产工艺 , 2006年这两种方法所生产的直接 还原铁产量占世界直接还原铁总产量的 78 . 1% ( Midrex 法 占 59 . 7 %, Hy L - Ⅲ法 占18 . 4 % )。 近年 ,这两种工艺技术得到不断发展。
直接还原铁技术

直接还原铁技术直接还原铁是铁矿在固态条件下直接还原为铁,可以用来作为冶炼优质钢、特殊钢的纯净原料,也可作为铸造、铁合金、粉末冶金等工艺的含铁原料。
这种工艺是不用焦碳炼铁,原料也是使用冷压球团不用烧结矿,所以是一种优质、低耗、低污染的炼铁新工艺,也是全世界钢铁冶金的前沿技术之一。
直接还原炼铁工艺有气基法和煤基法两种,按主体设备可分为竖炉法、回转窑法、转底炉法、反应罐法、罐式炉法和流化床法等。
目前,世界上90%以上的直接还原铁产量是用气基法生产出来的。
但是天然气资源有限、价高,使生产量增长不快。
用煤作还原剂在技术上也已过关,可以用块矿,球团矿或粉矿作铁原料(如竖炉、流化床、转底炉和回转窑等)。
但是,因为要求原燃料条件高(矿石品位要大于66%,含SiO2+Al2O3杂质要小于3%,煤中灰分要低等),规模小,设备寿命低,生产成本高和某些技术问题等原因,致使直接还原铁生产在全世界没有得到迅速发展。
因此,高炉炼铁生产工艺将在较长时间内仍将占有主导地位。
1.直接还原铁的质量要求直接还原铁是电炉冶炼优质钢种的好原料,所以要求的质量要高(包括化学成份和物理性能),且希望其产品质量要均匀、稳定。
1.1 化学成份直接还原铁的含铁量应大于90%,金属化率要>90%。
含SiO2每升高1%,要多加2%的石灰,渣量增加30Kg/t,电炉多耗电18.5kwh。
所以,要求直接还原铁所用原料含铁品位要高:赤铁矿应>66.5%,磁铁矿>67.5%,脉石(SiO2+Al2O3)量<3%~5%。
直接还原铁的金属化率每提高1%,可以节约能耗8~10度电/t。
直接还原铁含C<0.3%,P<0. 03%,S<0.03%,Pb、Sn、As、Sb、Bi等有害元素是微量。
1.2 物理性能回转窑、竖炉、旋转床等工艺生产的直接还原铁是以球团矿为原料,要求粒度在5~30mm。
隧道窑工艺生产的还原铁大多数是瓦片状或棒状,长度为250~380mm,堆密度在1.7~2. 0t/m³。
第四章 直接还原流程(上)
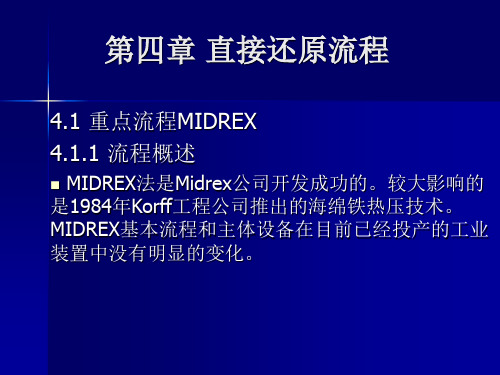
4.2.4 尾气清洗系统
还原尾气和冷却尾气进入尾气清洗系统 后分别通过一个洗涤塔,将粉尘洗净。然后 再分别通过一个脱水器,将机械水分离出来。 净冷却尾气和净还原尾气应当根据具体成分 统一或分别予以回收。
4.2.5原燃料性质
工业试验共使用了四种铁矿:巴西CVRD球团 (巴西球),瑞典球团(瑞典球),澳大利亚纽曼 山块矿(澳洲块),巴西MBR直接还原块矿(巴西 块)。
基本还原气中CO和H2约占总量的95%。此 外还有0.8%左右的CH4和微量的含硫气体, 其余基本是CO2。冷还原气在加热过程中会 发生水煤气反应,使成分稍有变化。
其他还原气是在基本还原气的基础上配加 纯氢形成的。工业试验共使用了10种成分 的还原气,热还原气性质见下表。
4Байду номын сангаас2.6 主要工艺参数
4.2 BL流程
BL流程直接还原梳程是宝山钢铁(集团)公司 (B)和鲁南化肥厂(L)联合开发的。 流程的最大特点是使用非焦煤制取还原气, 使竖炉海绵铁生产脱离了天然气资源的限制。 对于缺乏廉价天然气资源的地区具有极大的 吸引力。 流程由造气、还原气加热、还原和尾气清洗 四大系统组成。
4.2.1 造气系统
4.1.7 MIDREX装置与能耗
MIDREX是目前最完善的直接还原工艺。自20世纪 50年代末实现工业化以来,已形成不同规模的标 准化设计: 100型: 年产海绵铁16.5万t 400型: 年产海绵铁45万t 600型: 年产海绵铁67.5万t 1000型: 年产海绵铁100万t 其中使用最广泛的是400型的设计方案。
炉顶煤气冷却流程的气路大致形成一个单环,标准 流程的气路则形成双环。因此,有人将炉顶煤气冷 却流程称为单循环操作方式,标准流程称为双循环 操作方式。
气基还原HYL-Ⅲ工艺介绍

HYL-Ⅲ流程是HojalatayLamiaS.A.(Hylsa)公司在墨西哥的蒙特利尔开发成功的。
这一工艺的前身是该公司早期开发的间歇式固定床罐式法(HYL-I、HYL-Ⅱ)。
1975年一座日产25t的中间试验装置投入运转。
1980年,将一套1960年建成的固定床装置改造成能力为年产25万t的HYL-Ⅲ装置并投入生产。
1983年,又将一套1974年投产的固定床改造成年产50万t的竖炉。
用HYL-Ⅲ代替HYI-I、HYL-Ⅱ体现了由间歇运行到连续运行的讲步趋势。
还原气以水蒸气为裂化剂,以天然气为原料通过催化裂化反应制取。
还原气转化炉以天然气和部分炉顶煤气为燃料。
燃气余热在烟道换热器中回收,用以预热原料气和水蒸气。
从转化炉排出的粗还原气首先通过一个热量回收装置,用于水蒸气的生产。
然后通过一个还原气洗涤器清洗冷却,冷凝出过剩水蒸气,使氧化度降低。
净还原气与一部分经过清洗。
加压的炉顶煤气混合,通入一个以炉顶煤气为燃料的加热炉,预热至900~960°C。
从加热炉排出的高温还原气从竖炉的中间部位进入还原段。
在与矿石的对流运动中,还原气完成对矿石的还原和预热,然后作为炉顶煤气从炉顶排出竖炉。
炉顶煤气首先经过清洗,将还原过程产生的水蒸气冷凝脱除,提高还原势。
并除去灰尘,以便加压。
清洗后的炉顶煤气分为两路。
一路作为燃料气供应还原气加热炉和转化炉。
另一路加压后与净还原气混合,预热后作为还原气使用。
可使用球团矿和天然块矿为原料。
加料和卸料都有密封装置。
料速通过卸料装置中的蜂窝轮排料机进行控制。
在还原段完成还原过程的海绵铁继续下降进入冷却段。
冷却段的工作原理与MIDREX类似。
可将冷还原气或天然气等作为冷却气补充进循环系统。
海绵铁在冷却段中温度降低到50℃左右,然后排出竖炉。
HYI-Ⅲ的气耗约为10~11.3GJ·t-1。
,电耗90kw·h·t。
海绵铁金属化率约为91%。
与MIDREX流程相比HYL-Ⅲ具有下列特点:(1)采用高压操作。
- 1、下载文档前请自行甄别文档内容的完整性,平台不提供额外的编辑、内容补充、找答案等附加服务。
- 2、"仅部分预览"的文档,不可在线预览部分如存在完整性等问题,可反馈申请退款(可完整预览的文档不适用该条件!)。
- 3、如文档侵犯您的权益,请联系客服反馈,我们会尽快为您处理(人工客服工作时间:9:00-18:30)。
HYL-Ⅲ流程是HojalatayLamiaS.A.(Hylsa)公司在墨西哥的蒙特利尔开发成功的。
这一工艺的前身是该公司早期开发的间歇式固定床罐式法(HYL-I、HYL-Ⅱ)。
1975年一座日产25t的中间试验装置投入运转。
1980年,将一套1960年建成的固定床装置改造成能力为年产25万t的HYL-Ⅲ装置并投入生产。
1983年,又将一套1974年投产的固定床改造成年产50万t的竖炉。
用HYL-Ⅲ代替HYI-I、HYL-Ⅱ体现了由间歇运行到连续运行的讲步趋势。
还原气以水蒸气为裂化剂,以天然气为原料通过催化裂化反应制取。
还原气转化炉以天然气和部分炉顶煤气为燃料。
燃气余热在烟道换热器中回收,用以预热原料气和水蒸气。
从转化炉排出的粗还原气首先通过一个热量回收装置,用于水蒸气的生产。
然后通过一个还原气洗涤器清洗冷却,冷凝出过剩水蒸气,使氧化度降低。
净还原气与一部分经过清洗。
加压的炉顶煤气混合,通入一个以炉顶煤气为燃料的加热炉,预热至900~960°C。
从加热炉排出的高温还原气从竖炉的中间部位进入还原段。
在与矿石的对流运动中,还原气完成对矿石的还原和预热,然后作为炉顶煤气从炉顶排出竖炉。
炉顶煤气首先经过清洗,将还原过程产生的水蒸气冷凝脱除,提高还原势。
并除去灰尘,以便加压。
清洗后的炉顶煤气分为两路。
一路作为燃料气供应还原气加热炉和转化炉。
另一路加压后与净还原气混合,预热后作为还原气使用。
可使用球团矿和天然块矿为原料。
加料和卸料都有密封装置。
料速通过卸料装置中的蜂窝轮排料机进行控制。
在还原段完成还原过程的海绵铁继续下降进入冷却段。
冷却段的工作原理与MIDREX类似。
可将冷还原气或天然气等作为冷却气补充进循环系统。
海绵铁在冷却段中温度降低到50℃左右,然后排出竖炉。
HYI-Ⅲ的气耗约为10~11.3GJ·t-1。
,电耗90kw·h·t。
海绵铁金属化率约为91%。
与MIDREX流程相比HYL-Ⅲ具有下列特点:
(1)采用高压操作。
炉内最高压力达600kPa。
(2)以水蒸气为裂化剂,不存在裂化剂引起催化剂硫中毒的问题。
因此对矿石含硫没有特殊限制。
(3)竖炉运转失常时不影响还原气转化炉的工作。
(4)在对设备不做大改动的前提下可改换转化炉工作方式。