生产双氧水用催化剂的制备
一、蒽醌法双氧水工艺技术简介

一、蒽醌法双氧水工艺技术简介定义:蒽醌法生产双氧水,即利用醌类物质可以被氢化还原再重新回复成醌的性质,以烷基蒽醌衍生物为载体,在催化剂催化下被氢化,而后氧化合成过氧化氢(俗称双氧水)。
蒽醌法生产双氧水是目前世界上该行业最为成熟的生产方法之一,国外大型的生产厂家都采用蒽醌法生产双氧水,在国内目前双氧水的制备也几乎都是蒽醌法。
目前,世界上双氧水的生产方法主要有电解法、蒽醌法、异丙醇法、氧阴极还原法和氢氧直接化合法5种,在全球范围内蒽醌法生产占有绝对优势。
蒽醌法又分为钯催化生产工艺和镍催化剂氢化生产工艺。
国内20世纪80年代中期以前,过氧化氢的生产主要以镍催化剂搅拌釜氢化蒽醌工艺为主,随着生产能力得不断扩大,与搅拌釜工艺相比,以钯为催化剂的固定床组件显示出氢化设备结构简单、装置生产能力大、生产过程中不需经常补加催化剂、安全性能好和操作方便等优点,借助于DCS集散控制技术,可大大提高装置得安全性能,该工艺已成为过氧化氢生产发展的方向。
目前国内工业上蒽醌法生产过氧化氢的方法有悬浮釜镍催化剂工艺、固定床钯催化剂工艺、流化床工艺等,其中蒽醌法固定床钯催化剂工艺因其投资少、产量高、操作简单以及其使用的钯催化剂具有用量少、活性高、易再生和使用安全等优点,而成为国内过氧化氢生产工艺的主流,蒽醌法固定床钯催化剂工艺:是以2-乙基蒽醌为载体,以芳烃和磷酸三辛酯为溶剂配制成混合液体工作液。
工作液在固定床内于一定的温度、压力和钯催化剂的催化作用下,与氢气进行氢化反应,氢化完成液再与空气中的氧气进行氧化反应,得到的氧化液经纯水萃取、净化得到双氧水。
工作液经处理后循环使用。
其中氢化工序为整个生产工艺的核心,而氢化工序运行的效果,直接取决于钯催化剂的性能。
钯催化剂作为蒽醌法过氧化氢生产中的一种昂贵的关键原料,在生产应用时必须结合其特点进行有效的控制,使钯催化剂安全平稳地使用,否则,会影响钯催化剂效能正常发挥,造成浪费,影响产品产量质量,甚至造成难以弥补的损失。
蒽醌法钯催化剂工艺生产双氧水安全管理技术要点

蒽醌法钯催化剂工艺生产双氧水安全管理技术要点蒽醌法生产双氧水的过程具有较强的危险性。
文章通过对于蒽醌法生产双氧水的过程存在的危险性以及易发事故的情况进行详细的分析,进一步总结并归纳事故发生的原因,从而提出具体的预防措施。
标签:蒽醌法;双氧水;生产安全;管理技术要点双氧水作为重要的化学原料在很多方面都有非常重要的作用,包括民用、军用、医用以及工业等方面。
双氧水具有氧化作用,常常用于生产硼酸钠、过碳酸钠、过氧乙酸、亚氯乙酸、过氧化硫脲等工业原料。
印染工业利用双氧水的漂白功能作为棉织物的漂白剂,也能够还原燃料染色。
而且用生产金属盐或者其他的化合物来出去铁以及其他重金属功能。
但是一直以来双氧水的制备具有非常高的危险性,所以制备效率不够。
文章通过对于蒽醌法制备双氧水的过程存在的安全隐患问题进行详细的分析,从而为双氧水生产过程的安全管理提出措施和建议。
1 蒽醌法双氧水生产过程中原料的危险性1.1 双氧水自身的危险性由于双氧水自身的稳定行与其中的浓度没有直接的关系,但是如果双氧水接触到重金属、碱性物质以及粗糙容器表面的过程中,或者是受到了光、热作用的影响之下就会产生快速的分解反应,同时还会释放出大量的热和氧气。
反应速度与温度、酸碱值之间的杂质含量也出现正相关。
所以一旦温度升高10℃,那么双氧水的分解速度就会加快1.3倍。
在这种情况下分解的过程也会促使温度不断升高,所以在这种相互促进的过程汇总也会对生产的过程造成极大的安全隐患。
1.2 氢气由于氢气自身具有易燃易爆的特点,所以一旦混入到混入了空气、氧气等具有可燃性的气体之后就会非常容易出现爆炸性的混合气体。
在氧气中,氢气的爆炸极限为4.7%-94%,而在空气中,氢气的爆炸极限则为4%-74%。
但是这一爆炸极限却并不是固定点,而会随着温度、压力、介质、材料等很多方面的情况所影响的。
2 蒽醌法双氧水生产工序的安全性2.1 氢化工序的安全性氧化塔中如果不慎进入了可能造成催化剂中毒的杂质或者由于人为操作不当的情况而造成空气、氧气以及双氧水之间含量比呈现出较高的工作液,在这种情况下就会引起氧化塔爆炸的情况,从而造成安全事故。
双氧水制备方法

双氧水制备方法
双氧水的制备主要有以下五种方法:
①2-乙基蒽醌法:这种方法是通过在一定的温度和压力下,使用催化剂如重芳烃,以及氢气与2-乙基蒽醌反应,生成2-乙基氢蒽醌。
随后,2-乙基氢蒽醌与氧发生氧化还原反应,生成过氧化氢和水。
这个过程中生成的过氧化氢通过萃取获得过氧化氢水溶液,并最终经过重芳烃净化处理,得到合格的产品。
②电解法:这是一种较早的生产双氧水的方法,主要利用铂作为阳极,铅或石墨作为阴极,将饱和硫酸氢铵溶液电解成过硫酸铵,然后用稀硫酸水解得到双氧水。
然而,由于能源消耗较大,这种方法目前仅限于小规模生产。
③氧阴极还原法:这种方法的原理是利用强碱性电解质在电解槽中进行电化学反应,使得空气中的氧在阴极处被还原成过羟基负离子,然后转化为双氧水。
这个过程中的关键步骤是用钙盐沉淀作用生成过氧化钙,并通过过滤和分解过程制得双氧水,同时产生了碳酸钙循环使用。
虽然这种方法生产双氧水简单且成本低廉,但由于产品中双氧水浓度较低,因此不是主流的生产方式。
④氢氧直接合成法:这种方法涉及将氢气和氧气直接合成为水蒸气,但在实际工业应用中并不常见。
⑤蒽醌法:这是在国内广泛使用的双氧水生产方法,它涉及到使用二乙基蒽醌、重芳烃和磷酸三辛酯配制成的工作液,在特定的温度和压力条件下,通入氢气进行氢化,然后再在特定温度下与空气或氧气进行逆流氧化,经过萃取、再生、精制和浓缩等一系列过程,最终得到质量分数为20至30%的过氧化氢水溶液。
光催化产双氧水

光催化产双氧水
双氧水是一种常见的氧化剂,广泛应用于医疗、卫生、环保等领域。
传统的双氧水制备方法是通过电解水来制备,但这种方法存在能耗高、设备复杂等问题。
近年来,光催化技术被广泛应用于双氧水的制备中,具有能耗低、环保等优点。
光催化产双氧水的原理是利用光催化剂吸收光能,产生电子和空穴,从而促进水分子的分解,生成氧气和氢离子。
氢离子与氧气反应生成双氧水。
光催化剂的选择对反应的效率和选择性有很大影响。
常用的光催化剂有二氧化钛、氧化锌、氧化铟等。
光催化产双氧水的优点在于能耗低、环保。
光催化反应不需要外部电源,只需要光源即可,因此能耗低。
同时,反应产物只有氧气和双氧水,不会产生有害物质,符合环保要求。
光催化产双氧水的应用也非常广泛。
在医疗领域,双氧水被用于消毒、杀菌等。
光催化产双氧水可以在医院、实验室等场所进行,不需要外部电源,方便快捷。
在环保领域,双氧水被用于废水处理、空气净化等。
光催化产双氧水可以在户外进行,不需要外部电源,适用于各种环境。
光催化产双氧水是一种能耗低、环保的制备方法,具有广泛的应用前景。
随着光催化技术的不断发展,相信光催化产双氧水的效率和选择性会得到进一步提高,为各个领域的应用提供更好的支持。
蒽醌法生产双氧水

一、蒽醌法双氧水工艺技术简介定义:蒽醌法生产双氧水,即利用醌类物质可以被氢化还原再重新回复成醌的性质,以烷基蒽醌衍生物为载体,在催化剂催化下被氢化,而后氧化合成过氧化氢(俗称双氧水)。
蒽醌法生产双氧水是目前世界上该行业最为成熟的生产方法之一,国外大型的生产厂家都采用蒽醌法生产双氧水,在国内目前双氧水的制备也几乎都是蒽醌法。
目前,世界上双氧水的生产方法主要有电解法、蒽醌法、异丙醇法、氧阴极还原法和氢氧直接化合法5种,在全球范围内蒽醌法生产占有绝对优势。
蒽醌法又分为钯催化生产工艺和镍催化剂氢化生产工艺。
国内20世纪80年代中期以前,过氧化氢的生产主要以镍催化剂搅拌釜氢化蒽醌工艺为主,随着生产能力得不断扩大,与搅拌釜工艺相比,以钯为催化剂的固定床组件显示出氢化设备结构简单、装置生产能力大、生产过程中不需经常补加催化剂、安全性能好和操作方便等优点,借助于DCS集散控制技术,可大大提高装置得安全性能,该工艺已成为过氧化氢生产发展的方向。
目前国内工业上蒽醌法生产过氧化氢的方法有悬浮釜镍催化剂工艺、固定床钯催化剂工艺、流化床工艺等,其中蒽醌法固定床钯催化剂工艺因其投资少、产量高、操作简单以及其使用的钯催化剂具有用量少、活性高、易再生和使用安全等优点,而成为国内过氧化氢生产工艺的主流,蒽醌法固定床钯催化剂工艺:是以2-乙基蒽醌为载体,以芳烃和磷酸三辛酯为溶剂配制成混合液体工作液。
工作液在固定床内于一定的温度、压力和钯催化剂的催化作用下,与氢气进行氢化反应,氢化完成液再与空气中的氧气进行氧化反应,得到的氧化液经纯水萃取、净化得到双氧水。
工作液经处理后循环使用。
其中氢化工序为整个生产工艺的核心,而氢化工序运行的效果,直接取决于钯催化剂的性能。
钯催化剂作为蒽醌法过氧化氢生产中的一种昂贵的关键原料,在生产应用时必须结合其特点进行有效的控制,使钯催化剂安全平稳地使用,否则,会影响钯催化剂效能正常发挥,造成浪费,影响产品产量质量,甚至造成难以弥补的损失。
双氧水是怎样制成的原理
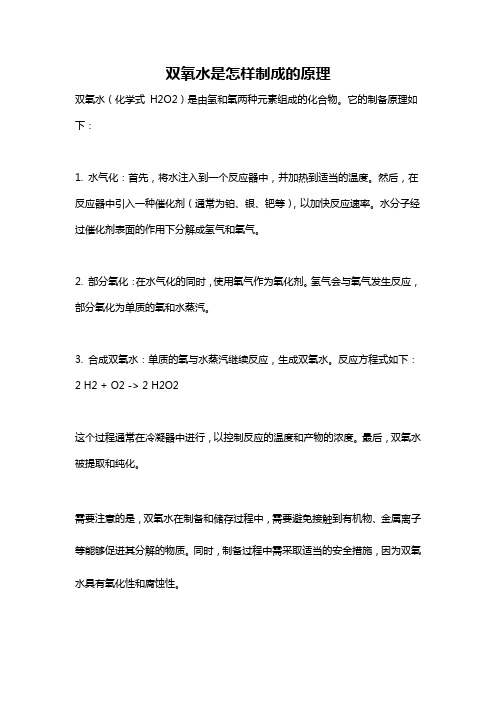
双氧水是怎样制成的原理
双氧水(化学式H2O2)是由氢和氧两种元素组成的化合物。
它的制备原理如下:
1. 水气化:首先,将水注入到一个反应器中,并加热到适当的温度。
然后,在反应器中引入一种催化剂(通常为铂、银、钯等),以加快反应速率。
水分子经过催化剂表面的作用下分解成氢气和氧气。
2. 部分氧化:在水气化的同时,使用氧气作为氧化剂。
氢气会与氧气发生反应,部分氧化为单质的氧和水蒸汽。
3. 合成双氧水:单质的氧与水蒸汽继续反应,生成双氧水。
反应方程式如下:2 H2 + O2 -> 2 H2O2
这个过程通常在冷凝器中进行,以控制反应的温度和产物的浓度。
最后,双氧水被提取和纯化。
需要注意的是,双氧水在制备和储存过程中,需要避免接触到有机物、金属离子等能够促进其分解的物质。
同时,制备过程中需采取适当的安全措施,因为双氧水具有氧化性和腐蚀性。
戊基蒽醌法双氧水产能

戊基蒽醌法双氧水产能介绍戊基蒽醌法双氧水产能是指通过戊基蒽醌法制造双氧水的能力。
双氧水是一种常见的化学物质,具有氧化性和消毒能力,广泛应用于医疗、美容、清洁等领域。
戊基蒽醌法是一种生产双氧水的方法,本文将对戊基蒽醌法双氧水产能进行全面、详细、完整且深入地探讨。
戊基蒽醌法原理戊基蒽醌法是一种以戊基蒽醌为催化剂制备双氧水的方法。
其原理如下: 1. 将氢氧化钠和过氧化氢溶液混合,生成过氧化钠。
2. 将过氧化钠与戊基蒽醌反应,生成双氧水和戊基蒽醌酚。
3. 通过蒸馏等方法分离纯净的双氧水。
戊基蒽醌法双氧水产能的影响因素戊基蒽醌法双氧水产能受多种因素的影响,包括但不限于以下几个方面: 1. 催化剂浓度:戊基蒽醌浓度越高,反应速率越快,产能越高。
2. 反应温度:适宜的反应温度可以提高反应速率,提高产能。
3. 反应时间:反应时间过短可能导致反应不完全,产能下降。
4. 原料质量:原料质量的优劣直接影响产能和产品质量。
5. 设备性能:设备的先进程度和运行稳定性会对产能产生影响。
戊基蒽醌法双氧水产能的优化策略为了提高戊基蒽醌法双氧水的产能,可以采取以下优化策略: ### 优化催化剂浓度通过合理控制戊基蒽醌的浓度,可以提高反应速率和产能。
但过高的浓度可能导致成本增加和催化剂的浪费,因此需要在经济效益和产能之间进行权衡。
控制反应温度适宜的反应温度可以提高反应速率和产能。
通过调节反应温度,可以找到最佳的反应条件,提高产能和产品质量。
延长反应时间适当延长反应时间可以提高反应的完全性,增加产能。
但过长的反应时间可能导致成本增加和生产周期延长,需要综合考虑。
优化原料质量选用高质量的原料可以提高产能和产品质量。
通过严格的原料选择和采购管理,可以降低废品率,提高产能。
更新设备引进先进的设备可以提高生产效率和产能。
先进的设备具有更高的自动化程度和稳定性,可以减少人工操作,提高产能和产品质量。
戊基蒽醌法双氧水产能的应用前景戊基蒽醌法双氧水产能的提高将推动双氧水在各个领域的应用。
工业制备双氧水的方法

工业制备双氧水的方法
工业制备双氧水的方法
双氧水,化学式为H2O2,是一种常见的氧化剂,具有强烈的漂白能力,广泛应用于化学、制药、印染等领域。
本文将介绍工业制备双氧水的
常用方法。
一、直接合成法
直接合成法是最常用的双氧水制备方法。
该方法利用氢氧化物和过氧
酸盐的反应,以氧气为氧化剂,在催化剂的作用下将氧气和水加入过
氧化氢水溶液的反应釜中,即可得到高浓度的双氧水。
二、电解法
电解法又称为返流法,是利用电解水溶液得到氧气和氢氧根离子,在
两者作用下生成双氧水。
电解法可以产生高纯度的双氧水,但需要高
能消费和设备成本较高的电力装置。
三、过氧化氢乙酸法
过氧化氢乙酸法是在乙酸的作用下,通过氧化剂过氧化氢将醇类氧化
成醛酸,并进一步逐步脱除金属离子,形成高浓度的双氧水。
虽然该
方法制备成本较高,但产生的双氧水浓度高、纯度高。
四、超声波法
超声波法是利用超声波的波动力对过氧化氢水溶液进行处理,即将过氧化氢水溶液放入超声波反应器中,通过超声波的震荡使其氧化度降低,从而产生高浓度的双氧水。
五、永磁室温离子液体法
永磁室温离子液体法是一种新型的双氧水制备方法,它可以在室温和气压条件下产生高浓度的双氧水。
该方法主要是通过将离子液体与过氧化氢水溶液混合,然后在氧化剂作用下使其反应生成高浓度的双氧水。
总之,以上这些方法都是制备双氧水的常用方法,不同的制备方法具有不同的优缺点。
在实际生产过程中,根据需要选择不同的制备方法将有助于提高生产效率和质量。
双氧水的生产方法

双氧水的生产方法1.1 蒽醌法蒽醌法生产双氧水是目前世界上该行业最为成熟的生产方法之一,国外大型的生产厂家都采用蒽醌法生产双氧水,在国内目前双氧水的制备也几乎都是蒽醌法。
20世纪初,人们发明以2-烷基蒽醌作为氢的载体循环使用生产双氧水的方法,后经多次改进,使该技术日趋成熟。
其工艺为2-烷基蒽醌与有机溶剂配制成工作溶液,在压力为0.30MPa、温度55℃~65℃、有催化剂存在的条件下,通入H2进行氢化,再在40℃~44℃下与空气进行逆流氧化,经萃取、再生、精制与浓缩制得到H2O2水溶液成品,目前我国市场上有质量分数分别为27.5%、35.0%和50.0%三种规格的产品。
国内20世纪80年代中期以前,过氧化氢的生产主要以镍催化剂搅拌釜氢化蒽醌法工艺为主,随着生产能力的不断扩大,与搅拌釜工艺相比,以钯为催化剂的固定床工艺逐渐显示出其优越性:氢化设备结构简单、装置生产能力大、生产过程中不需经常补加催化剂、安全性能好和操作方便等优点,借助于计算机集散控制技术,可大大提高装置的安全性能,该工艺已成为过氧化氢生产发展的方向;近期新建装置及老厂的工艺改造几乎都采用蒽醌法,多采用钯催化固定床,镍-钯混合床。
目前在国内还没有出现氢化流化床的文献报道,只有上海阿托菲纳双氧水公司和福建第一化工厂引进国外技术采用钯催化氢化流化床的专利工艺。
、双氧水用途及概况1.1.1.1物理性质:双氧水(学名过氧化氢),分子式:H2O2,分子量:34,无色、无味透明无毒,但对皮肤有漂白及烧灼作用。
皮肤受其侵蚀可引起皮炎、起泡或针刺般疼痛,重者长期不痊愈。
它能强烈刺激眼睛,危害眼粘膜,长期接触,可使毛发变黄。
双氧水蒸汽可引起眼睛流泪,刺激眼、鼻、喉的粘膜。
双氧水蒸气在空气中的最大浓度不应高于0.03mg/L1.1.2化学性质:双氧水是一种强氧化性物质,但遇到比它更强的氧化剂,比如高锰酸钾、氯气等,则呈还原性质。
它的化学性质比较活泼,可以参加分解、分子加成、取代、氧化还原等反应。
双氧水 生产工艺
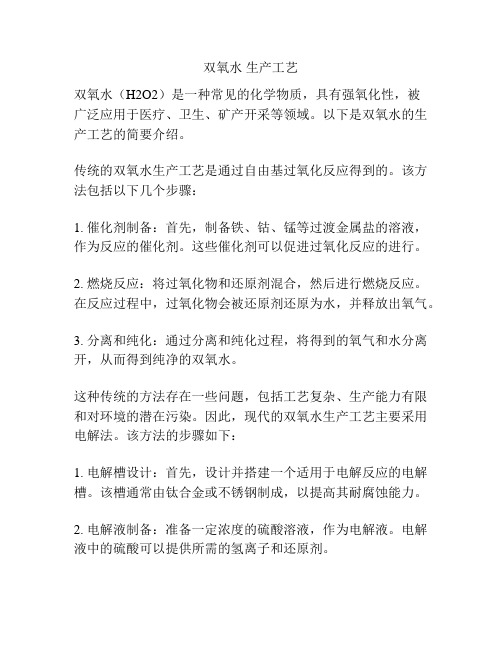
双氧水生产工艺双氧水(H2O2)是一种常见的化学物质,具有强氧化性,被广泛应用于医疗、卫生、矿产开采等领域。
以下是双氧水的生产工艺的简要介绍。
传统的双氧水生产工艺是通过自由基过氧化反应得到的。
该方法包括以下几个步骤:1. 催化剂制备:首先,制备铁、钴、锰等过渡金属盐的溶液,作为反应的催化剂。
这些催化剂可以促进过氧化反应的进行。
2. 燃烧反应:将过氧化物和还原剂混合,然后进行燃烧反应。
在反应过程中,过氧化物会被还原剂还原为水,并释放出氧气。
3. 分离和纯化:通过分离和纯化过程,将得到的氧气和水分离开,从而得到纯净的双氧水。
这种传统的方法存在一些问题,包括工艺复杂、生产能力有限和对环境的潜在污染。
因此,现代的双氧水生产工艺主要采用电解法。
该方法的步骤如下:1. 电解槽设计:首先,设计并搭建一个适用于电解反应的电解槽。
该槽通常由钛合金或不锈钢制成,以提高其耐腐蚀能力。
2. 电解液制备:准备一定浓度的硫酸溶液,作为电解液。
电解液中的硫酸可以提供所需的氢离子和还原剂。
3. 电解反应:将电解槽中的阳极和阴极分别连接到电源,并将电解槽中的电解液加热至一定温度。
在电解过程中,水分子将被电解成氧气和氢离子。
氢离子进一步与氧气结合,形成双氧水。
4. 分离和纯化:通过分离和纯化过程,将得到的双氧水从电解液中分离出来,并提高其纯度。
电解法相较于传统的自由基过氧化反应法,具有生产效率高、工艺简单和环境友好的优点。
然而,电解法也存在一些挑战,如电解槽的设计和维护、催化剂的共腐蚀等问题,需要通过技术创新和优化来解决。
总之,双氧水的生产工艺可以通过传统的自由基过氧化反应法或现代的电解法来实现。
随着技术的进步和创新,双氧水的生产工艺将不断改进和优化,以满足不同应用领域的需求。
双氧水生产方法

双氧水生产方法
双氧水即过氧化氢,其生产方法主要有以下几种:
1. 碱性过氧化氢制法:生产碱性过氧化氢用含醌空气电极,其特征在于每对电极由阳极板、塑料网、阳离子隔膜和含醌空气阴极组成,在电极工作区的上、下端设有进入流体的分配室和排出流体的收集室,在流体进口处设有节流孔。
2. 2-乙基蒽醌法:工业规模化生产主要方法是2-乙基蒽醌(EAQ)法。
2-乙基蒽醌在一定温度压力在催化剂作用下和氢气反应生成2-乙基氢蒽醌,2-乙基氢蒽醌在一定温度压力下与氧发生氧化还原反应,2-乙基氢蒽醌还原生成2-乙基蒽醌同时生成过氧化氢,再经过萃取获得过氧化氢水溶液。
3. 电解法:电解法是20世纪前半期生产双氧水的主要方法,该法是以Pt 为阳极,铅或石墨为阴极,将饱和硫酸氢铵溶液电解成过硫酸铵,再用稀硫酸水解得到双氧水。
该法能源消耗大,仅限于小规模生产。
4. 氧阴极还原法:用此法生产双氧水是将强碱性电解质于电解槽中,使空气中的氧在阴极还原成过羟基负离子,然后在回收装置中转变为双氧水,其过程是借助钙盐沉淀作用,生成过氧化钙,过滤分解,用CO2分解制得双氧水,同时产生碳酸钙循环使用。
该法生产双氧水简单,成本低,无污染,但产品中双氧水浓度低。
以上是双氧水的生产方法,希望对解决您的问题有所帮助。
蒽醌法生产双氧水反应方程式

蒽醌法生产双氧水反应方程式
蒽醌法是一种生产双氧水的方法,其反应方程式为:
2C6H4O2 + O2 → 2H2O2 + 2CO2
在这个反应中,蒽醌作为催化剂,促进了过氧化氢的合成。
蒽醌是一
种有机化合物,它能够与氧气反应生成过氧化物,而过氧化物则能够
分解成双氧水和二氧化碳。
具体来说,在蒽醌法中,苯酚和过量的丙酮在催化剂存在下进行缩合
反应,生成二(α-苯基甲基)环己酮。
然后,在空气存在下,二(α-苯基
甲基)环己酮与蒽醌发生复杂的氧化反应,生成双氧水和二氧化碳。
需要注意的是,在蒽醌法中,催化剂的选择非常重要。
如果催化剂含
有铜、铁等金属离子,则会导致产量低下、质量不稳定等问题。
因此,在实际生产中,通常采用纯净的蒽醌作为催化剂。
总之,蒽醌法是一种可靠的生产双氧水的方法,其反应方程式为
2C6H4O2 + O2 → 2H2O2 + 2CO2。
在实际生产中,需要注意催化
剂的选择和质量控制等问题,以确保产品的质量和产量。
- 1、下载文档前请自行甄别文档内容的完整性,平台不提供额外的编辑、内容补充、找答案等附加服务。
- 2、"仅部分预览"的文档,不可在线预览部分如存在完整性等问题,可反馈申请退款(可完整预览的文档不适用该条件!)。
- 3、如文档侵犯您的权益,请联系客服反馈,我们会尽快为您处理(人工客服工作时间:9:00-18:30)。
生产双氧水用催化剂的制备
2016-11-04 12:10来源:内江洛伯尔材料科技有限公司作者:研发部
生产双氧
水用催化剂的制备
双氧水是一种重要的无机化工产品,在造纸、化工、食品、环保等领域应用广泛。
双氧水使用过程中分解的最终产物主要是水,不会产生二次污染物,是一种环境友好的氧化剂,而且以双氧水为氧化剂的氧化过程具有反应条件温和、选择性高的优点。
随着绿色化工过程的不断发展,双氧水作为绿色氧化剂的应用将会日益广泛,如环己酮,己内酰胺,对苯二酚,环氧丙烷等新兴清洁生产过程均以双氧水作为氧化剂。
近年来,随着双氧水的一些新应用以及从环保角度出发,双氧水的需求量将会日益增加,进而促使双氧水产量保持持续增长态势。
2005年国外双氧水装置的生产能力已约达300万t/a(100% H2O2计)。
国
内双氧水生产同样发展迅速,生产能力和产量以每年15%〜20%左右的速度递增,2006年底国内双氧水生产装置已近百套,生产能力接近100万吨(100% H2O2计)。
在双氧水制备工艺中,蒽醌自氧化法占有绝对优势,其核心过程就是蒽醌催化加氢,而加氢催化剂是影响加氢过程的关键。
加氢催化剂经历了 Raney镍催化剂、钯黑催化剂到非均布载体钯催化剂的发展过程,目前仍然存在催化剂效率低,失活快等诸多问题。
整体蜂窝催化剂是由许多狭窄的整齐排列的平行通道组成的一体化催化剂,具有毫米级的反应通道,特征尺寸小,同时还具有低压降、低能耗、无需进行产物与催化剂分离和易于集成放大等诸多优点。
对于多相反应,当保持适当的气、液两相流速时,流体在整体催化剂通道内将形成活塞流,此时气泡和通道壁之间只存在一层很薄的液膜,同时液柱内还存在液相循环流动,这将大大增加气-液和液-固间的传质速率,提高催化剂的利用效率。
目前双氧水的生产存在制备工艺复杂,其中存在的影响因素较多,针对上述问题,本文提出了一种新型双氧水生产用催化剂的制备方法。
其使用整体蜂窝作为基体,采用分步担载高比表涂层和活性组分的方法制备催化剂,通过调整涂层量有效控制活性组分浸渍厚度,从而降低催化剂内部传质阻力,提高催化剂的活性
及选择性。
制备的整体式催化剂用于蒽醌加氢过程,活性高、选择性好。
其技术方案为:
1)堇青石整体蜂窝基体的预处理:用体积浓度为3-15%稀HNO3浸泡2_12小时,去离子水洗至中性,120°C干燥2-6小时,1000°C焙烧2_10小时;
2)选取Cr金属的硝酸盐、氢氧化物和/或氧化物中的一种或两种物质,加入质量浓度为1-10%硝酸,每克物质加入3-5ml稀硝酸,经6-18 小时球磨成浆料;3)将上述步骤2~)所获得的浆料或溶胶浸渍在经过步骤1)处理的整体蜂窝基体上,干燥、350-120(TC焙烧后形成带涂层的载体;
4)将幻所述的整体蜂窝载体浸渍于含Pd的前驱物溶液,可进行单次或多次浸渍,每次都经过干燥、200-80(TC焙烧,形成催化剂。
相较于传统蒽醌法制备双氧水所用的催化剂,本方法的有点在于:
1.本发明的整体催化剂活性组分浸渍深度可以通过调整涂层量进行控制,活性组分负载量与活性组分浸渍层深度匹配好,提高了反应物料在气液、液固和气固之间的传质效率,降低内部传质阻力。
2.本发明提出一种整体催化剂的制备方法,并用于蒽醌催化加氢制双氧水过程。
在反应温度50°C,压力0. 3MPa,液体空速l^T1,气体空速UOtT1条件下,时空收率20. 93〜 82. 21kg. H2O2 (100% )/m
3. cat. h,是商用颗粒催化剂的3倍以上。
3.本发明的整体催化剂与传统的蒽醌加氢颗粒催化剂相比,克服了活性组分流失、磨损等问题,且无需进行反应液和催化剂的分离,装填和更换催化剂方便快捷。