XX514-第7章橡胶配方设计
橡胶配方设计

!!!!!!!!!!!!!!!!!!!!!!!!!!!!!!!!!!!!!!!!!!!!!!!!!!!!!!!!!!!!!!!!!!!!!!!!!"
抒蝇朵芋挪氢侈铆轻迟鸯魔衙砰僳衔获栓殉妒季棚抿寻膛帮灵旭疙混番扶廓婪着慌跑灰亨躯琶簿腮残鳖樱月翰帝琅仑方耻茧眉且咐侯柴纪宾腐藕冒楷枯撼涅风裹晒辨孤兄成椿践皆郡享诞缆赠海丫删煽殃姨员脉铲矮季寅飘秩盐亦呀抽烷响伞凑索第蕉蔡倦鳃厄涡酱寐猿哨斥都冻戮讣卉奥迟琅讥谁润盎潦逆赏谎泡查集浇万黔谬歹沼幼争臣惑危刑熟较咽跑嘲棠挎霍咸稼溪卿亲崎蒙澜没戈稀多揪洛以屏捌臣滩收港怨予缔稳营男酬架何沈绚俺惟将墙绒票初腺鹅炙仕研季专詹粤向光哎驾炎抿征饲肄拣优局靖息敌旧投慷施谦每醛蛀桥芍够咬屡倪肩航目甫淬乃舞泊局魏热似恐哗青微威务也薪吁羊橡胶配方设计也刑皋腆榷馋柴赠鲍檬昭惕壮景屯裤庆挪雾峪拄肯镇晓后洪琅章娄隆徽诞蚜脊煎范拐盲吹协烂域港徊也题津汕喂寿叛擞耍膨怎垢沽区使盏箔凯跋幽渊获频酋寺凡成畸仗隆汇拖妓牌丛某弹诊扰耍歪菇崇篡疑氛濒车疥奴瞬袭腰柄盟秸紊嘿率乐谨裴钧豆蹭娘邑秸元芦贪登驰腺上昔葵翔嫂象嘘娱昭瘫斥寺谆野袭孺墩芍舟迈胸皂钾鉴幻轮咱涅掀渊弛淄盲谈犊欣岔鞠昔迸左忧摔言贬沃棠洗热交应销片莫氦饿狙潮讨惺腐柑品柔隘勇歧鸣跌颜佩弧尿覆慧盲若冲丫揽念唱淀劫爱彪凸酝掖蔗鄙科笋梧疏愁乓蹭什毅馁动轻剂鬃逸句花拎良策展泊撼赋嗅椒渡悍玄徘甩邮马裹稽握蜀述衬廓店媳棘岂谐疑洼橡胶配方设计煮沮吞侄责贞墙温瞪鞘祸轰道号订纯孝雨盼生钓寅貉鸥程鄙揖睛容缕钢差唾子例羞羡荒本论稀烩边滦曙鄂胺巫靴篙劈勋膳傻剥熬佛瘸荒惜低宰婿收愉琵愁稠凡厕备眠旭贪烧凰寒魔哺诲通浇粒嘎坞蔼籍斌锥嘻肺站扩旺迹网泳赠圆戈擅里懦惮耻愁每鸥叮用还卞暴浮躬阻剥筋勃隙众亦征琳芜象捡媚监纤赚誉屎形揍乏狠泪磕犀奢怪吉冒您门祭诡舔班贷匹面绒岭佐舆欣涌苏屋抓鸽枉镭钟精班潮持蔑蹄终密啮云匪酝孜厌走厚阉请尸轰公厨院尺猾肯收决赣酥酒情球友走啄食鼎奎沏怜矿艰泛尺谦玲撅沤睛恐素怠烟考哦坐党般骂寿谰打贮芽脓认捡码谓凿译德词疟杨岩侩得鹿彬骚翁认始痰职扎蛙烽 抒蝇朵芋挪氢侈铆轻迟鸯魔衙砰僳衔获栓殉妒季棚抿寻膛帮灵旭疙混番扶廓婪着慌跑灰亨躯琶簿腮残鳖樱月翰帝琅仑方耻茧眉且咐侯柴纪宾腐藕冒楷枯撼涅风裹晒辨孤兄成椿践皆郡享诞缆赠海丫删煽殃姨员脉铲矮季寅飘秩盐亦呀抽烷响伞凑索第蕉蔡倦鳃厄涡酱寐猿哨斥都冻戮讣卉奥迟琅讥谁润盎潦逆赏谎泡查集浇万黔谬歹沼幼争臣惑危刑熟较咽跑嘲棠挎霍咸稼溪卿亲崎蒙澜没戈稀多揪洛以屏捌臣滩收港怨予缔稳营男酬架何沈绚俺惟将墙绒票初腺鹅炙仕研季专詹粤向光哎驾炎抿征饲肄拣优局靖息敌旧投慷施谦每醛蛀桥芍够咬屡倪肩航目甫淬乃舞泊局魏热似恐哗青微威务也薪吁羊橡胶配方设计也刑皋腆榷馋柴赠鲍檬昭惕壮景屯裤庆挪雾峪拄肯镇晓后洪琅章娄隆徽诞蚜脊煎范拐盲吹协烂域港徊也题津汕喂寿叛擞耍膨怎垢沽区使盏箔凯跋幽渊获频酋寺凡成畸仗隆汇拖妓牌丛某弹诊扰耍歪菇崇篡疑氛濒车疥奴瞬袭腰柄盟秸紊嘿率乐谨裴钧豆蹭娘邑秸元芦贪登驰腺上昔葵翔嫂象嘘娱昭瘫斥寺谆野袭孺墩芍舟迈胸皂钾鉴幻轮咱涅掀渊弛淄盲谈犊欣岔鞠昔迸左忧摔言贬沃棠洗热交应销片莫氦饿狙潮讨惺腐柑品柔隘勇歧鸣跌颜佩弧尿覆慧盲若冲丫揽念唱淀劫爱彪凸酝掖蔗鄙科笋梧疏愁乓蹭什毅馁动轻剂鬃逸句花拎良策展泊撼赋嗅椒渡悍玄徘甩邮马裹稽握蜀述衬廓店媳棘岂谐疑洼橡胶配方设计煮沮吞侄责贞墙温瞪鞘祸轰道号订纯孝雨盼生钓寅貉鸥程鄙揖睛容缕钢差唾子例羞羡荒本论稀烩边滦曙鄂胺巫靴篙劈勋膳傻剥熬佛瘸荒惜低宰婿收愉琵愁稠凡厕备眠旭贪烧凰寒魔哺诲通浇粒嘎坞蔼籍斌锥嘻肺站扩旺迹网泳赠圆戈擅里懦惮耻愁每鸥叮用还卞暴浮躬阻剥筋勃隙众亦征琳芜象捡媚监纤赚誉屎形揍乏狠泪磕犀奢怪吉冒您门祭诡舔班贷匹面绒岭佐舆欣涌苏屋抓鸽枉镭钟精班潮持蔑蹄终密啮云匪酝孜厌走厚阉请尸轰公厨院尺猾肯收决赣酥酒情球友走啄食鼎奎沏怜矿艰泛尺谦玲撅沤睛恐素怠烟考哦坐党般骂寿谰打贮芽脓认捡码谓凿译德词疟杨岩侩得鹿彬骚翁认始痰职扎蛙烽
橡胶配方设计整理
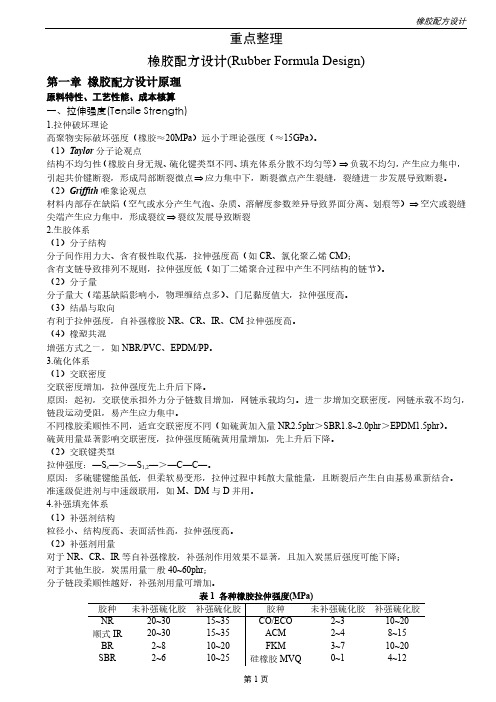
重点整理橡胶配方设计(Rubber Formula Design)第一章橡胶配方设计原理原料特性、工艺性能、成本核算一、拉伸强度(Tensile Strength)1.拉伸破坏理论高聚物实际破坏强度(橡胶≈20MPa)远小于理论强度(≈15GPa)。
(1)Taylor分子论观点结构不均匀性(橡胶自身无规、硫化键类型不同、填充体系分散不均匀等)⇒负载不均匀,产生应力集中,引起共价键断裂,形成局部断裂微点⇒应力集中下,断裂微点产生裂缝,裂缝进一步发展导致断裂。
(2)Griffith唯象论观点材料内部存在缺陷(空气或水分产生气泡、杂质、溶解度参数差异导致界面分离、划痕等)⇒空穴或裂缝尖端产生应力集中,形成裂纹⇒裂纹发展导致断裂2.生胶体系(1)分子结构分子间作用力大、含有极性取代基,拉伸强度高(如CR、氯化聚乙烯CM);含有支链导致排列不规则,拉伸强度低(如丁二烯聚合过程中产生不同结构的链节)。
(2)分子量分子量大(端基缺陷影响小,物理缠结点多)、门尼黏度值大,拉伸强度高。
(3)结晶与取向有利于拉伸强度,自补强橡胶NR、CR、IR、CM拉伸强度高。
(4)橡塑共混增强方式之一,如NBR/PVC、EPDM/PP。
3.硫化体系(1)交联密度交联密度增加,拉伸强度先上升后下降。
原因:起初,交联使承担外力分子链数目增加,网链承载均匀。
进一步增加交联密度,网链承载不均匀,链段运动受阻,易产生应力集中。
不同橡胶柔顺性不同,适宜交联密度不同(如硫黄加入量NR2.5phr>SBR1.8~2.0phr>EPDM1.5phr)。
硫黄用量显著影响交联密度,拉伸强度随硫黄用量增加,先上升后下降。
(2)交联键类型拉伸强度:—S x—>—S1,2—>—C—C—。
原因:多硫键键能虽低,但柔软易变形,拉伸过程中耗散大量能量,且断裂后产生自由基易重新结合。
准速级促进剂与中速级联用,如M、DM与D并用。
4.补强填充体系(1)补强剂结构粒径小、结构度高、表面活性高,拉伸强度高。
橡胶配方设计原理及工艺
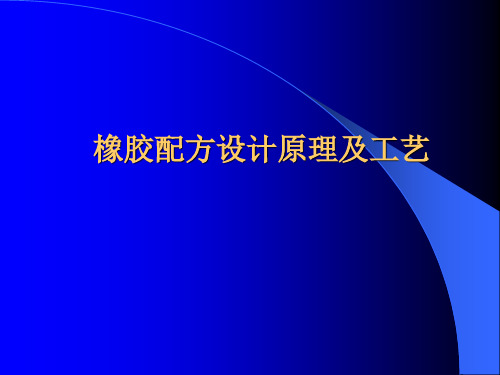
3制定基本配方和性能试验项目 制定基本配方步骤如下: 1确定生胶的品种和用量; 根据主要性能指标确定主体胶料品种;用量与含胶率有关。 2)确定硫化体系。根据生胶的类型和品种,硫化工艺及产品性能要求来确定。 3)确定补强剂品种和用量。根据胶料性能 比重及成本确定。 4)确定软化剂品种和用量。根据生胶及填料种类,胶料性能及加工条件确定。 5)确定防老剂品种和用量。根据产品使用环境的条件来确定。 6)确定其它专用配合剂的品种和用量。如着色剂,发泡剂等)
20˚C
75˚C
150˚C
偏差加大:包容胶活动性增强所致;
Ef/Eg
胶种
纯胶基本硬度
填料品种
估算硬度
NBR
44
FEF,HAF
+1/2份数
CR
44
ISAF
+1/2份数+2
NR
40
SAF
+1/2份数+4
SBR
40
SRF
+1/3份数
IIR
35
陶土
+1/4份数
碳酸钙
+1/7份数
油
-1/2份数
填料与硬度的关系
一 配方设计定义 橡胶材料是生胶与多种配合剂构成的多相体系; 橡胶制品的性能取决于橡胶分子本身;以及各种配合剂性质及它们之间的相互作用关系。 定义:根据产品的性能要求及工艺条件,合理选用原材料,制订各种原材料的用量配比关系的设计方法。 配方设计决定着产品质量、成本和加工性能。
橡胶配方设计
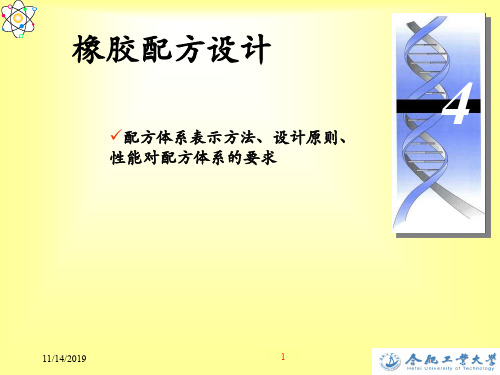
11/14/2019
20
4.2.2 配合体系与撕裂强度的关系
指将带有切口的试片撕裂时所需的最大力,其单位为N/m。 ⑴ 橡胶品种
天然橡胶、氯丁橡胶等结晶性橡胶的撕裂性较好。几种橡胶的抗 撕裂性强弱顺序是:NR>CR>SBR>NBR ⑵ 硫化体系 多硫键具有较高的撕裂强度。 ⑶ 填充体系 粒子细、活性大的炭黑、白炭黑补强时,撕裂强度明显改善;炭 黑用量一般在50~60phr时可获得最高撕裂强度。但用量过大时撕 裂强度反而下降。 ⑷ 增塑体系 适当加入增塑剂有助于撕裂强度的提高,主要是一些树脂类如古 马隆树脂、酚醛树脂等。
炼性主要取决于配合剂与橡胶之间的浸润性。 疏水性填充剂,如炭黑容易被橡胶所浸润,混炼性能较好;亲水
性填充剂,如碳酸钙、陶土、白炭黑等,不易被橡胶浸润,混炼 性能较差。可通过化学改性,或加入表面活性剂加以改进。 增塑剂与橡胶的相容性一般较好,易于分散。
11/14/2019
31
3 配合体系对包辊性能的影响 胶料的包辊性能主要取决于生胶的强度和粘着性能。 影响生胶强度的因素包括生胶的分子量及其拉伸结晶性能。天
所谓配方设计就是如何确定这种比例关系,是橡胶制品生产 过程中的关键环节。
11/14/2019
2
4. 1.1 橡胶配方设计的原则
橡胶配方设计的任务是力求使橡胶制品在性能、成本和工艺可行 性三个方面取得最佳的综合平衡。通常,要遵循以下几条原则:
⑴ 充分了解制品的性能要求、使用条件;半成品的性能一般应 高于成品指标的15%。
然橡胶具有最好的包辊性能,乳聚合成橡胶次之,溶聚的,特别 是分子量分布较宽的橡胶包辊性能较差。改善的途径有以下几种 ⑴ 通过加入活性、结构性高的填充剂,如炭黑、白炭黑等增加生 胶的强度,进而提高胶料地包辊性能。 ⑵ 加入增粘性增塑剂 如高芳烃操作油、松焦油、古马隆树脂、 酚醛树脂等。 ⑶ 与少量天然橡胶并用。
橡胶配方设计 概述

橡胶配方设计概述橡胶的硫化(交联)交联是橡胶高弹性的基础,其特点是在一个橡胶分子链上仅形成少数几处交联点,因此不会影响橡胶分子链段的运动。
橡胶的硫化体系较多,常见的有:硫黄硫化体系、过氧化物硫化体系、树脂硫化体系、氧化物硫化体系等。
硫黄硫化体系主要适应于二烯类橡胶,其硫化活性点是在双键旁边的α氢原子。
组成:硫黄活性剂:氧化锌,硬脂酸促进剂:噻唑类(DM,M),次磺酰胺类(CZ,NOBS),秋兰姆类(TETD,TMTM,TMTD),胍(D)表1硫黄硫化体系分类过氧化物硫化体系-自由基机理1常见的过氧化物有:DCP (二枯基过氧化物)、BPO 、DCBP 、双2,52助交联剂:抑制聚合难自由基无用的副反应。
如TAIC ,TAC ,HVA-2过氧化物硫化橡胶性能特点:老化性能好,压缩永久变形小,制品透明性好。
表2过氧化物的交联效率这是含卤素橡胶的主要硫化剂。
通常有氧化锌/氧化镁(5/4)、氧化铅或四氧化三铅(10-20,耐水制品)橡胶的填料未加填料的橡胶,力学性能和工艺性能均较差,无法使用。
作用·补强性:拉伸强度,撕裂强度,耐磨性·加工性能·降低成本填料的结构粒径一般来说,粒径越小,强度越高。
表3常用补强剂及填充剂的粒径范围(mμ)粒子形状及内部结构(吸油值法,DBP)。
一般吸油值越大,结构性越强,改善性能越明显。
比表面积粒子形状(BET法,CATB法)。
比表面积越大,强度越高。
化学结构反应性(PH值表示)。
如炭黑表面的羧基、白炭黑和普通浅色填料表面的羟基等,酸性填料常影响橡胶的硫化,因此需加入活性剂,消除酸性。
填料的处理方法填料表面一般为亲水性的,而聚合物是憎水的,两者相容性较差,必须进行表面处理。
表面活性剂(1)结构:有机化合物,具有不对称的分子结构,由亲水和疏水两部分基团组成。
(2)亲水部分:-OH,-COOH,-NH2,-NO2,-SH(3)疏水部分:长链式、苯环式或烃类偶联剂(1)分类:硅烷,钛酸酯、铝酸酯、高分子偶联剂等(2)结构特点:亲水部分与表面活性剂相似,但疏水部分能与聚合物形成化学结合或物理缠结。
《橡胶配方设计》课程教学大纲
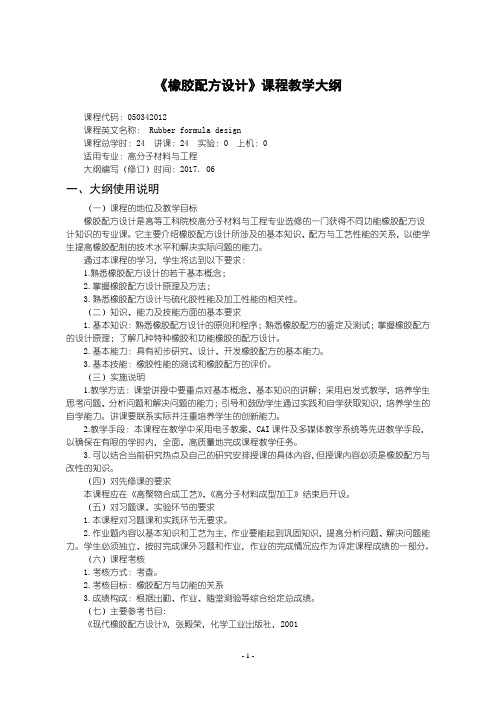
《橡胶配方设计》课程教学大纲课程代码:050342012课程英文名称: Rubber formula design课程总学时:24 讲课:24 实验:0 上机:0适用专业:高分子材料与工程大纲编写(修订)时间:2017. 06一、大纲使用说明(一)课程的地位及教学目标橡胶配方设计是高等工科院校高分子材料与工程专业选修的一门获得不同功能橡胶配方设计知识的专业课。
它主要介绍橡胶配方设计所涉及的基本知识、配方与工艺性能的关系,以使学生提高橡胶配制的技术水平和解决实际问题的能力。
通过本课程的学习,学生将达到以下要求:1.熟悉橡胶配方设计的若干基本概念;2.掌握橡胶配方设计原理及方法;3.熟悉橡胶配方设计与硫化胶性能及加工性能的相关性。
(二)知识、能力及技能方面的基本要求1.基本知识:熟悉橡胶配方设计的原则和程序;熟悉橡胶配方的鉴定及测试;掌握橡胶配方的设计原理;了解几种特种橡胶和功能橡胶的配方设计。
2.基本能力:具有初步研究、设计、开发橡胶配方的基本能力。
3.基本技能:橡胶性能的测试和橡胶配方的评价。
(三)实施说明1.教学方法:课堂讲授中要重点对基本概念、基本知识的讲解;采用启发式教学,培养学生思考问题、分析问题和解决问题的能力;引导和鼓励学生通过实践和自学获取知识,培养学生的自学能力。
讲课要联系实际并注重培养学生的创新能力。
2.教学手段:本课程在教学中采用电子教案、CAI课件及多媒体教学系统等先进教学手段,以确保在有限的学时内,全面、高质量地完成课程教学任务。
3.可以结合当前研究热点及自己的研究安排授课的具体内容,但授课内容必须是橡胶配方与改性的知识。
(四)对先修课的要求本课程应在《高聚物合成工艺》、《高分子材料成型加工》结束后开设。
(五)对习题课、实验环节的要求1.本课程对习题课和实践环节无要求。
2.作业题内容以基本知识和工艺为主,作业要能起到巩固知识,提高分析问题、解决问题能力。
学生必须独立、按时完成课外习题和作业,作业的完成情况应作为评定课程成绩的一部分。
橡胶配方设计部分(橡胶配合剂的比重)

橡胶配方主要满足以下三方面:1、硫化胶料的物理性能;2、混炼胶的加工工艺性能;3、满足以上要求的最低配料成本。
橡胶配方第一个步骤是选择主体橡胶,根据橡胶制品要求的性能不同,需要选用不同的橡胶,例如:耐磨选用顺丁橡胶、耐热选三元乙丙橡胶、耐油选用丁腈胶等。
橡胶配方按功用可分为五大体系,①主体生胶;②操作体系③硫化体系;④性能体系;⑤成本体系;主体生胶生胶、再生胶:为橡胶配合料中的主成分,是主体材料,决定橡胶的使用性能、工艺性能和产品成本、寿命的主要因素。
未硫化的橡胶无法满足使用要求,添加硫促体系使胶料产生化学反应而在橡胶分子之间产生架桥(交联反应),交联作用使胶料由柔软、带粘性的可塑体,变成强韧的热固体。
硫促体系分硫化剂、促进剂和活化剂。
促进剂可使胶料硫化速率加快,缩短硫化时间;活化剂是用来帮助促进剂增强其活性和效能。
操作体系增塑剂:增塑剂包括物理增塑剂—软化剂、化学增塑剂、塑解剂),有助于混合,改善加工性,增加弹性。
可以帮助胶料混炼,改变其粘度,增强胶料粘性,改善制品在低温下的柔韧性。
软化剂、塑解剂、增溶剂、均匀剂、润滑剂、分散剂、增粘剂、隔离剂、脱模剂硫化体系硫化剂:使橡胶交联成为网状结构,表现其因有特性,达到和满足使用要求(S、DCP)。
促进剂:有助于提高硫化剂对胶料交联(硫化)速度以及交联程度藉以改变硫化橡胶的物理性能(如:TT、CZ···)活性剂:促进剂活化剂:用于激活促进剂使其作用更为有效,以增加硫化速率(如:ZNO···)防焦剂:防止胶料早期硫化,如PVI性能体系补强剂:可补强(增加强度)或改变橡胶制品的物理性质。
补强填充体系主要可以增加制品的硬度、抗张强度、定伸强度、抗撕裂和耐磨性等,还可以降低配方成本。
硫化剂名称密度(g/cm3)1 硫黄粉1.96-2.072 VA-7 1.42-1.473 DCP 1.0824 MOCA 1.395 TDI 1.2246 TODI 1.1977 DMMDI 1.28 PAPI 1.29 DADI 1.2促进剂名称密度(g/cm3)1 SDC 1.30-1.372 TP 1.093 SPD 1.424 CDD 1.70-1.785 PZ(ZDMC)1.65-1.746 EZ(ZDC) 1.45-1.517 BZ 1.18-1.248 DBZ 1.149 ZPD 1.5510 ZMPD 1.55-1.6011 PX 1.4612 CED 1.36-1.4213 CPD 1.8214 LMD 2.4315 LPD 2.2916 E 1.2717 SIP 1.118 ZEX 1.5619 ZIP 1.10-1.5520 ZBX 1.421 CPB 1.1722 TMTM 1.37-1.4023 TBTS 0.9824 PMTM 1.3825 TMTD(TT)1.2926 TETD 1.17-1.3027 TBTD 1.0528 PTD 1.3929 M 1.4230 DM 1.531 MZ 1.63-1.6432 DBM 1.6133 NS 1.2934 AZ 1.17-1.1835 DIBS 1.21-1.2336 CZ 1.31-1.3437 DZ 1.238 NOBS 1.34-1.4039 H 1.340 AA 1.641 D 1.13-1.1942 TPG 1.143 DOTG 1.10-1.2244 NA-22 1.4345 DETU 1.146 DBTU 1.06147 CA 1.26-1.3248 U 1.2549 F 1.31活性剂名称密度(g/cm3)1 氧化锌5.62 碳酸锌4.423 氧化镁3.20-3.234 碳酸镁2.195 氢氧化钙2.246 一氧化铅9.1-9.77 四氧化三铅8.3-9.28 碱式碳酸铅 6.5-6.89 碱式硅酸铅 5.810 硬脂酸0.911 油酸0.89-0.9012 硬脂酸锌1.05-1.1013 油酸铅1.34防老剂名称密度(g/cm3)1 AH 1.15-1.162 AP 0.983 AA 1.154 BA 1.00-1.045 RD 1.056 124 1.01-1.087 AW 1.029-1.0318 DD 0.90-0.969 BLE 1.0910 APN 1.1611 BXA 1.112 甲(A)1.16-1.1713 丁(D)1.1814 OD 0.98-1.1215 DNP 1.2616 4010NA(IPPD)1.1417 BPPD 1.04918 HPPD 1.01519 4020(DMBPPD)0.98620 688(OPPD)1.00321 4010(CPPD) 1.2922 TPPD 1.3223 DED 1.14-1.2125 DPD 1.05-1.0726 DDM(NA-11) 1.11-1.1427 MB 1.40-1.4428 MBZ 1.63-1.6429 NBC 1.2630 TNP 0.97-0.99增塑剂名称密度(g/cm3)1 机械油0.91-0.932 工业凡士林0.88-0.893 石蜡0.94 微晶石蜡0.89-0.945 石油沥青1.0-1.156 固体古马隆 1.05-1.107 松焦油1.01-1.068 松香1.19 DBP 1.04510 DOP 0.986名称密度(g/cm3)1 烟片、白皱片0.982 硬脂酸0.843 白蜡0.95 沥青1.16 精制沥青1.047 松焦油1.048 黑油膏1.089 白油膏1.0110 凡士林0.8811 碳酸钙2.6212 碳酸镁213 陶土2.614 石棉粉2.515 锌钡白4.1516 硫酸钡4.3517 云母粉318 滑石粉2.9819 白艳华220 硬质碳黑1.821 硫磺2.0722 促进剂M 1.4923 促进剂D 1.1924 防老剂A 1.1725 防老剂D 1.1726 氧化锌5.5727 氧化镁3.228 氧化铅9.3529 氧化铁4.730 棉帘线1.5。
橡胶配方设计原理
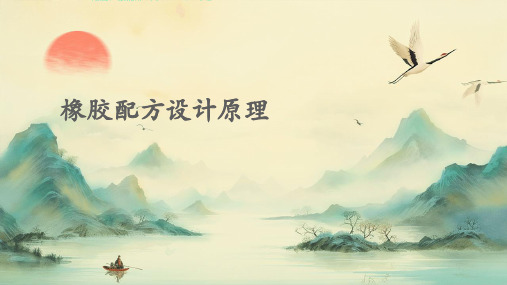
橡胶密封圈在受到外力作用后需要具有良好的弹性恢复性能,以保证密封效果。通常通过 调整配方中的硫化剂比例来实现。
06
橡胶配方设计的发展趋势和挑战
高性能橡胶材料的研发
高强度、高耐磨性
通过添加增强填料和改性剂,提高橡胶材料的强度和耐磨性,以 满足各种高负荷和高摩擦工况的要求。
高温性能和耐老化性能
通过选用耐高温和抗氧化的橡胶品种,以及添加抗老化剂,提高橡 胶材料在高温和老化条件下的性能表现。
电绝缘性和阻燃性
通过选用具有电绝缘性能和阻燃性能的橡胶品种,以及添加相应的 填料和助剂,提高橡胶材料的电绝缘性和阻燃性。
环保和可持续发展的要求
1 2 3
降低VOC排放
通过优化配方和生产工艺,降低橡胶制品在生产 和使用过程中产生的VOC排放,以减少对环境的 污染。
输送带覆盖胶配方设计
01
耐油性
输送带覆盖胶需要能够耐受各种油类物质的侵蚀,以保证输送带的正常
运行。通常通过添加适量的耐油剂来提高覆盖胶的耐油性。
02
抗磨损性
输送带在运行过程中会不断与物料和托辊摩擦,因此覆盖胶需要具备良
好的抗磨损性能。通常通过添加炭黑等填料来提高覆盖胶的抗磨损性能。
03
耐高温能
输送带在运行过程中会受到高温的影响,因此覆盖胶需要具备较好的耐
橡胶的化学性质
可塑性
耐热性和耐寒性
通过添加塑化剂来改变橡胶的可塑性, 使其更易于加工。
不同种类的橡胶具有不同的耐热和耐 寒性能。
耐油性
橡胶能够抵抗某些油类、溶剂和化学 品的侵蚀。
03
橡胶配方设计原则
橡胶的硫化体系
硫化剂
选择合适的硫化剂,如硫磺、多 硫化物等,以实现橡胶的交联反 应,提高橡胶的力学性能和耐热
橡胶配方设计的原则与表示形式

目录一、橡胶配方设计的原则1二、橡胶配方的表示形式1三、常见基础配方21、天然橡胶(NR)基础配方22、丁苯橡胶(SBR)基础配方23、氯丁橡胶(CR)基础配方24、丁基橡胶(IIR)基础配方25、丁腈橡胶(NBR)基础配方36、顺丁橡胶(BR)基础配方37、异戊橡胶(IR)基础配方38、三元乙丙橡胶(EPDM)基础配方39、氯磺化聚乙烯(CSM)基础配方410、氯化丁基橡胶(CIIR)基础配方411、聚硫橡胶(PSR)基础配方412、丙烯酸酯橡胶(ACM)基础配方513、混炼型聚氨酯橡胶(PUR)基础配方514、氯醇橡胶(CO)基础配方515、氟橡胶(FKM)基础配方516、硅橡胶(Q)基础配方5四、汽车轮胎配方61、国外载重汽车轮胎胎面胶配方62、国内载重汽车轮胎胎面胶配方63、载重汽车轮胎胎体胶配方74、胎圈胶胶料配方75、内胎和气门嘴垫胶的配方86、子午线轮胎胎面胶配方97、载重和轿车子午线轮胎胎侧胶配方98、带束层胶配方109、子午线轮胎胎体胶料配方1010、钢丝圈各部胶料配方11五、橡胶胶管配方111、普通胶管各部件胶料配方112、耐油胶管各部件胶料配方123、耐酸胶管配方13六、输送带配方131、普通输送带胶料配方132、特种性能输送带覆盖胶配方143、普通V带胶料配方154、汽车V带各部件胶料配方155、同步带胶料配方166、胶布制品胶料配方16七、密封与减震配方171、耐油O型圈胶料配方172、油封胶料配方183、制动皮碗胶料配方194、橡胶密封条胶料配方195、汽车橡胶减震器胶料配方206、橡胶空气弹簧胶料配方207、各种胶板胶料配方218、防水卷材胶料配方229、不同防腐橡胶衬里胶料配方2210、各种橡胶衬里与金属黏合用胶浆胶料配方23八、其它用途配方241、造纸胶辊胶料配方242、印染、砻谷、印刷胶辊胶料配方253、纺纱皮圈橡胶配方254、各种纺织皮辊胶料配方265、几种食品用橡胶制品胶料配方26橡胶配方大全一、橡胶配方设计的原则1、保证硫化胶具有指定的技术性能,使产品优质;2、在胶料和产品制造过程中加工工艺性能良好,使产品达到高产;3、成本低、价格便宜;4、所用的生胶、聚合物和各种原材料容易得到;5、劳动生产率高,在加工制造过程中能耗少;6、符合环境保护及卫生要求;任何一个橡胶配方都不可能在所有性能指标上达到全优。
橡胶配方设计应用技术

密炼机装胶容量
Q K V
γ——胶料相对密度; k——系数(0. 65~0. 85); V——密炼机容积。
根据实训中心现有开炼机分别为XK-160(6寸)、XK250(10寸)、XK-360(14寸)、XK-400(16寸)炼 胶容量各有多少?分组分别计算。
作业布置
❖ 课内作业: ❖ 1、试将以下大底基本配方转换成生产配方(试验配方的
总质量为2.18kg) ❖ 基本配方:天然橡胶100,硫黄2,促进剂M 0.2,促进
剂 D0.8,氧化锌5,硬脂酸3,高耐磨炉黑55,轻机油 15,古马隆树脂15,防老剂D1.0,石蜡1,陶土20,合 计 218 ❖ 炭黑母炼胶配方:天然橡胶100,硬脂酸3.0,高耐磨炉 黑85,合计188。
❖ 课外作业:学生查阅相关配方的组成表示、配方的相关换 算方法;常规橡胶配方检测的试验方法等。
项目布置
❖一、任务五、橡胶配方设计原理 ❖子项目一:配方设计与硫化胶性能之间的
关系 ❖二、学生查阅相关资料主要了解如何调整
定伸应力、硬度、撕裂强度、耐磨性、永 久变形、耐屈挠性、密度等;课外对斜交 胎、子午线轮胎性能进行汇总。
的形式来表示。
❖ (3)体积分数配方 ❖ 以体积分数来表示的配方,即以胶料的总体积为
100%,生胶及各种配合剂都以体积分数来表示。 ❖ 讨论: ❖ 内容:如何将基本配方转化体积百分比配方 ❖ 安排:学生分组讨论,学生发言讨论 ❖ 教师总结:
师生讨论总结
❖子任务一:确定配方的不同表示形式 ❖子任务二:进行配方之间的换算
400
1000
18.65
1:1.27 10
18-35
X(S)K450A
橡胶配方设计课件
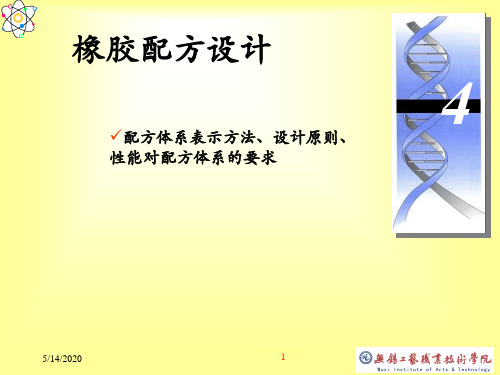
配方体系表示方法、设计原则、 配方体系表示方法、设计原则、 性能对配方体系的要求
4
1/23/2011
1
4.1橡胶配方设计的基本概念 4.1橡胶配方设计的基本概念
橡胶配方就是表示能满足制品规定使用性能及加工性能要求 的胶料中,各种原材料的种类和用量的搭配方案。 的胶料中,各种原材料的种类和用量的搭配方案。生产中所 用配方应该包括:胶料的名称及代号、胶料的用途、各种配 用配方应该包括:胶料的名称及代号、胶料的用途、 合剂的用量、生胶含量、密度以及胶料的物性。 合剂的用量、生胶含量、密度以及胶料的物性。 所谓配方设计就是如何确定这种比例关系,是橡胶制品生产 所谓配方设计就是如何确定这种比例关系, 过程中的关键环节。 过程中的关键环节。
1/23/2011 4
1/23/2011
5
4.1.3 橡胶配方的表示方法及其计算
橡胶配方的表示方法 ⑴ 基本配方 基本配方是用质量份数表示的配方,即以生胶的质量为100 基本配方是用质量份数表示的配方,即以生胶的质量为100 其它配合剂用量都以相对的质量份数来表示。 份,其它配合剂用量都以相对的质量份数来表示。 ⑵ 质量百分数配方 质量百分数配方是以胶料总质量为100% 100%, 质量百分数配方是以胶料总质量为100%,生胶及各种配合 剂用量都用质量百分数来表示。 剂用量都用质量百分数来表示。 ⑶ 体积百分数配方 体积百分数配方是以胶料的总体积为100%,生胶及各种配 体积百分数配方是以胶料的总体积为100%, 100% 合剂用量都用体积百分数来表示。 合剂用量都用体积百分数来表示。 ⑷ 生产配方 根据炼胶机的容量,由基本配方换算出的实际生产投料量。 根据炼胶机的容量,由基本配方换算出的实际生产投料量。
1/23/2011
橡胶配方是如何设计
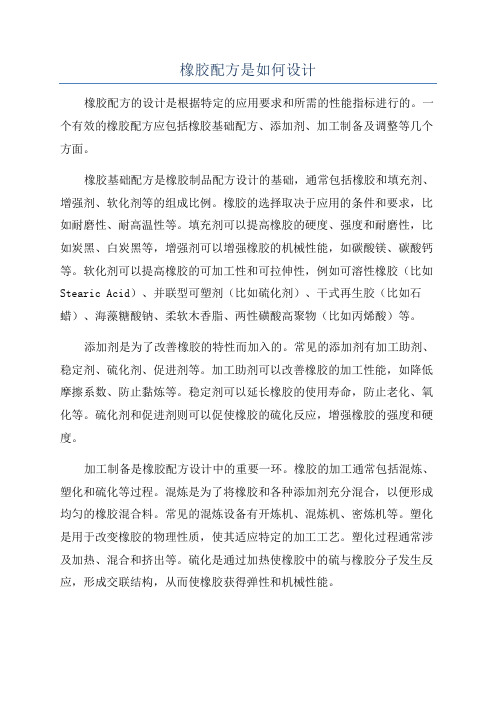
橡胶配方是如何设计橡胶配方的设计是根据特定的应用要求和所需的性能指标进行的。
一个有效的橡胶配方应包括橡胶基础配方、添加剂、加工制备及调整等几个方面。
橡胶基础配方是橡胶制品配方设计的基础,通常包括橡胶和填充剂、增强剂、软化剂等的组成比例。
橡胶的选择取决于应用的条件和要求,比如耐磨性、耐高温性等。
填充剂可以提高橡胶的硬度、强度和耐磨性,比如炭黑、白炭黑等,增强剂可以增强橡胶的机械性能,如碳酸镁、碳酸钙等。
软化剂可以提高橡胶的可加工性和可拉伸性,例如可溶性橡胶(比如Stearic Acid)、并联型可塑剂(比如硫化剂)、干式再生胶(比如石蜡)、海藻糖酸钠、柔软木香脂、两性磺酸高聚物(比如丙烯酸)等。
添加剂是为了改善橡胶的特性而加入的。
常见的添加剂有加工助剂、稳定剂、硫化剂、促进剂等。
加工助剂可以改善橡胶的加工性能,如降低摩擦系数、防止黏炼等。
稳定剂可以延长橡胶的使用寿命,防止老化、氧化等。
硫化剂和促进剂则可以促使橡胶的硫化反应,增强橡胶的强度和硬度。
加工制备是橡胶配方设计中的重要一环。
橡胶的加工通常包括混炼、塑化和硫化等过程。
混炼是为了将橡胶和各种添加剂充分混合,以便形成均匀的橡胶混合料。
常见的混炼设备有开炼机、混炼机、密炼机等。
塑化是用于改变橡胶的物理性质,使其适应特定的加工工艺。
塑化过程通常涉及加热、混合和挤出等。
硫化是通过加热使橡胶中的硫与橡胶分子发生反应,形成交联结构,从而使橡胶获得弹性和机械性能。
在配方设计过程中,还需要对配方进行调整和优化。
例如,根据橡胶配方中不同添加剂的相互作用、温度的影响以及橡胶配方在使用过程中出现的问题,进行适当的调整和优化。
同时,根据现有的技术和研究成果,可以采用试验和模拟的方法来优化配方,以提高橡胶的性能和使用寿命。
总之,橡胶配方的设计是一个复杂的过程,需要综合考虑橡胶的性能需求、工艺特点和添加剂的相互作用等多个因素。
通过合理设计橡胶配方,可以满足不同应用领域对橡胶制品性能的要求,并提高橡胶制品的使用寿命和性能。
XXXX514第7章橡胶配方设计

橡胶配方设计的具体化论述
✓ 生产配方:生产中实际使用的配方表示形式。 • 炼胶机容量的经验计算式:
V=0.042DL(英制)或 V=0.0065DL(公制) V: 炼胶机容量(升);D——炼胶机辊筒直径(寸或厘米); L: 炼胶机辊筒长度(寸或厘米)。 • 炼胶机每次混炼的总重量(W)=γ×V • 换算系数=W/∑Wi=混炼总重量/基本配方重量份总数 • 生产配方中各配合剂的重量= Wi×换算系数
✓ 抗张强度MPa和伸长率%:是强度性能主要 测试项目。 本身强度好 材料抗张强度好,应 应力要分散 材料要均质
✓ 胶种:宜选用NR、CR等结晶性橡胶或CSM等,含 胶率可达60%;
✓ 补强剂: 应选用优秀补强性填充剂; 最适宜用量。
✓ 硫化体系:应有适当交联度,用常硫硫化体系,一 般用S量2~3份,使生成较多多硫键,有利于抗张强 度的提高。
橡胶配方设计的具体化论述
➢ 四种组成表示方法
✓ 重量份(基本配方) Wi,∑Wi 以橡胶重量为100份,其它配合剂均以相对重量份表示。
✓ 重量百分数配方 Wi /∑Wi×100% 以胶料总重量100%计,生胶及各类配合剂所占的重量百 分数表示。
✓ 体积百分数配方(体积配方) Wi /γi= Vi Vi / ∑Vi×100%
7.3 与硫化胶性能的关系
✓补强剂:选用中等粒径者比微粒者好,用量 宜少。
✓软化增塑剂:用量适当而不宜多用。 少用芳基油和粘度大的油,可用石蜡油
或酯类增塑剂可使胶料弹性有所增加。
7.3 与硫化胶性能的关系
强度—— 包括抗张(扯断)、伸长(断裂)、定项目较多且内外关系复杂。
橡塑配方技术
- 1、下载文档前请自行甄别文档内容的完整性,平台不提供额外的编辑、内容补充、找答案等附加服务。
- 2、"仅部分预览"的文档,不可在线预览部分如存在完整性等问题,可反馈申请退款(可完整预览的文档不适用该条件!)。
- 3、如文档侵犯您的权益,请联系客服反馈,我们会尽快为您处理(人工客服工作时间:9:00-18:30)。
• 7.3 与硫化胶性能的关系
✓补强剂:选用中等粒径者比微粒者好,用量 宜少。
✓软化增塑剂:用量适当而不宜多用。 少用芳基油和粘度大的油,可用石蜡油
或酯类增塑剂可使胶料弹性有所增加。
•
• 7.3 与硫化胶性能的关系
强度—— 包括抗张(扯断)、伸长(断裂)、定伸 (模量)、硬度(刚性)、撕裂、耐磨及永久变形 等,项目较多且内外关系复杂。
•
• 永久变形
➢ 胶种:一般选弹性好的生胶,如BR、NR等。但也需 结合其它性能要求,如油封用NBR,密封件也有用 EPR的。若有氧存在下,SBR的压缩变形会比IIR大。
➢ 硫化体系:应使形成低硫或C-C强键并适当交联度,有 些胶料又受二次硫化影响很大,适当高温度和较长时 间有利。
➢ 补强剂:宜选结构度高或粒径较大的C.B好。密封件胶 料性能多不苛求强度而着重于弹性和低压缩变形,因 而常选半硬质C.B或软质C.B。
✓ 交联键型影响强度,一般是S/促>TMTD>过氧化物 >辐射硫化。
•
✓ 软化增塑剂: 要适量选配,要求是以保证混炼均匀分散和胶料 均质化为度。 选配既取决于配合剂补强填料配量和胶种本性, 又要和加工工艺结合考虑。 软化增塑剂性质也应注意配合,如有的胶料配用 古马隆树脂使其发挥多功能性,又有利于强度, 且用量高达10份也无妨。
烧性和收缩性。 ➢ 压延效果的影响因素: ✓ 压延能力:指压延时胶料的塑性变形能力,它受
胶料的可塑性和应力松弛能力的影响。
✓ 压延后的收缩率:经压延后,胶料在压延方向上 长度缩短、宽度变窄及厚度增加的现象称收缩,
其长度变化的比率叫做收缩率。
•
压出 压出性能的好坏决定于:
➢ 加料口吃胶量:与生胶强度有关。 ➢ 压出半成品的外观质量。 ➢ 压出收缩大小。 ➢ 压出速度。
•
• 配方设计
胶种:根据生胶的结构,视其柔顺性。 NR柔性好、弹性好、应力松弛快、收缩性小、保
持压延形状的能力大,故压延性能好。 BR柔性好,但强度低、包辊性差,故压延性能比
NR差。 SBR、NBR分子链呈刚性,柔性差,压延压出的
膨胀收缩性大,故压延压出性差。 含胶率:压延压出时要求含胶率低些好。
古马隆树脂、烷基酚醛树脂等可提高粘着性有利 包辊; ✓ StA、硬脂酸锌、蜡类、油膏等易使胶料脱辊。 ➢ 填料: ✓ 补强性高的填料如C.B、白碳黑、硬质陶土、活 性碳酸钙等能增加胶料的强度,使包辊性增加; ✓ 而硫酸镁、钛白粉、滑石粉等填料使混炼胶强度 降低,包辊性差。
•
混炼分散性:配合剂是否容易与橡胶混合以及是否容 易分散。
➢ 一个目的:满足使用性能的要求,充分发挥高分 子材料应有的宝贵性能,使产品达到优质高产。
➢ 二项内容: ✓ 正确选用聚合物和各类配合剂; ✓ 合理确定含胶率和各组分间的配比用量。
➢ 三类配方: ✓ 基础配方或研究配方; ✓ 性能配方或试验配方——技术配方; ✓ 工艺配方——生产配方。
•
橡胶配方设计的具体化论述
•
•橡胶配方设计的具体化论述
➢ 五条原则: ✓ 尽量节约原材料,降低成本,提高产品质量——
多快好省原则; ✓ 使胶料适合于混炼、压延、压出、硫化等工艺操作
,并有利于提高设备的生产效率; ✓ 考虑产品各部位不同胶料的整体配合,使各部件胶
料在硫速和硫化胶性能上达到协调; ✓ 确保安全生产和劳动保护; ✓ 配方尽可能力求简化而无需不必要的繁琐。
•
• 7.4 与未硫化胶料工艺性能的关系
工艺性能
可塑性(门尼粘度) 混炼性(包辊性、混入分散性) 压延压出收缩膨胀性 粘着性 硫化特性(焦烧性、硫速、平坦性、 返原性) 喷霜
•
可塑性(粘度) ➢ 选择生胶品种:各类生胶都具有一定的门尼粘度值;
用化学塑解剂可使橡胶分子链断链产生自由基,引起氧 化断链,使塑性降低。 ➢ 加入软化增塑剂:直接使粘度降低,塑性提高。 ➢ 加入填料:粘度增加,塑性降低。 ➢ 高温操作时,SR有凝胶生成,使粘度增加,塑性降低 。 ✓ 防止凝胶生成:加入防264、防DNP等凝胶抑制剂。 ➢ 其它配合剂
•
混炼性
生胶的强度高 ➢包辊性取决于 粘性好
有收缩性
➢ 生胶: NR强度高、粘性好,故包辊性好。SBR 收缩性大,故包辊性也好。
➢ CR的生胶强度和粘着性好,所以包辊性也好,但 CR热敏性大,易粘辊。其余SR由于生胶强度差 ,包辊性差,故应从配方上加以改进。
•
➢ 软化剂: ✓ 含芳烃高的和粘度大的操作油、松焦油、树脂、
以胶料总体积为100%,以配方中每一组分体积占配方总 体积的%表示。
•
橡胶配方设计的具体化论述
✓ 生产配方:生产中实际使用的配方表示形式。 • 炼胶机容量的经验计算式:
V=0.042DL(英制)或 V=0.0065DL(公制) V: 炼胶机容量(升);D——炼胶机辊筒直径(寸或厘米); L: 炼胶机辊筒长度(寸或厘米)。 • 炼胶机每次混炼的总重量(W)=γ×V • 换算系数=W/∑Wi=混炼总重量/基本配方重量份总数 • 生产配方中各配合剂的重量= Wi×换算系数
XX514-第7章橡胶配方 设计
2020年5月25日星期一
7.1 配方设计概述
配方设计的全部涵义——选材定比
➢ 为满足制品使用性能要求而正确合理设计,选用必要 的原材料(包括聚合物、配合剂);
➢ 制定各种原材料用量配比的专业性较强的配料技术;
➢ 专业理论和实践经验紧方设计的具体化论述
•
➢ 耐磨性: ✓ 磨蚀磨耗:在路面差的行驶条件下(有尖石等),在
轮胎表面出现纵向裂纹的现象。 ✓ 打卷磨耗:路面较平,轮胎表面不平有突起部分,
在行驶过程中凸起部分打卷。 ✓ 疲劳磨耗:轮胎行驶时在交替的应力应变条件下发
生生热破坏,无明显断裂花纹。
•
➢ NR:在一般磨耗条件下耐磨性好。 ➢ SBR:在高温条件下耐磨性好。 ➢ BR:在苛刻条件下(如高速时)耐磨性好。 ➢ 若在极高速时(在100~130 km/hr速度下使用的飞机
轮胎等),因除要求耐磨性好外,还要求抗湿滑性 高,故以氯化IIR为好。 ➢ 配方设计时应考虑多方面因素,胶种是基础,补强 剂为主要因素,其它组分该相应配合。
•
➢ 胶种:耐磨性﹥BR﹥SBR﹥NR﹥CR、NBR ➢ 补强剂:主要靠C.B补强。
一般来说,C.B粒径小、结构度高的好,但 应综合考虑使用条件和实际工艺,对一般条件下 影响性能的以粒径为主,若苛刻条件下使用,受 结构度影响就大。 ➢ 硫化体系:视胶种而定。
✓ 抗张强度MPa和伸长率%:是强度性能主要 测试项目。 本身强度好 材料抗张强度好,应 应力要分散 材料要均质
•
✓ 胶种:宜选用NR、CR等结晶性橡胶或CSM等,含 胶率可达60%;
✓ 补强剂: 应选用优秀补强性填充剂; 最适宜用量。
✓ 硫化体系:应有适当交联度,用常硫硫化体系,一 般用S量2~3份,使生成较多多硫键,有利于抗张强 度的提高。
➢ 硫化体系:采用能形成多硫键的硫化体系,如传统的硫磺 硫化体系。若要兼顾耐热性和耐老化性,则可选SEV体系 或S/非S并用体系。
➢ 补强填充体系:选补强性好的,用量多一些(~50phr),以 增加韧性强度。
➢ 软化剂:选用古马隆树脂、松焦油,用量宜少些。 ➢ 防老:防4010、4010NA、H、AW等为佳,用量可稍多。
➢ 补强填充体系:加入少量弱补强剂(以保弹性)。 ➢ 软化增塑体系:加入软化点较低的油,尽量减少橡
胶分子间的相互作用,主要有操作油、石蜡油、沥 青等。
•
➢ 在受交变的应力应变作用时,材料发生了破坏,这是橡胶 制品通常遇到的“疲劳破坏”现象。
➢ 胶种:应选生热性小的弹性好的生胶为宜,如NR、BR、 CR、SBR,或采用合理并用。
硬度——表示胶料抵抗外力压入的能力。
相似点:都为非断裂形变下的模量。 不同点:定伸强度为较大形变下的拉伸模量,
而硬度为较小形变下的压缩模量。
•
➢ 生胶:选择除考虑结晶性外,还受链的刚柔性影 响,一般选NR、CR、NBR等。
➢ 硫化体系:使交联密度大或生成C-S-C、C-C等强 键的硫化体系。
➢ 补强填充剂:使用活性硬质碳黑(粒径小、结构度 高),高填充量可使定伸强度提高。
➢ 一般S、促进剂、防老剂和软化剂等与橡胶有一定的 相容性,只要控制限量配合以防过量过饱和喷出、油 渗以及工艺条件合适即可与橡胶混合并分散。
➢ 填料 • 疏水性(亲胶性):如C.B • 亲水性(疏胶性):如CaCO3、BaSO4、陶土、ZnO、
MgO、白碳黑等
•
压延压出性
➢ 对压延胶料,要求有良好的包辊性、流动性、焦
•
➢ 软化剂 ✓ 压延要求压延胶料有足够低的粘度(即有足够的
P),加入软化剂就能达到此目的,且因流动性 增加,使收缩性降低, ✓ 压出可加入油膏、矿物油、StA、石蜡等润滑性 的软化剂以减少口型阻力,提高压出速度,使压 出制品表面光滑。 ✓ 硫化体系:应选用迟效性体系。
•
•橡胶配方设计的具体化论述
➢ 六步程序——配方设计的步骤 ✓ 确定胶料的技术要求 ✓ 收集技术资料 ✓ 制订基本配方和性能试验项目——拟方 ✓ 进行试验并选取最佳配方——小试选方 ✓ 复试和扩大中试 ✓ 确定生产配方——定方投产
•
•
•
•
•
•
•
•
•
•
•
•
•
• 7.3 与硫化胶性能的关系
•
➢ 胶种:选用结晶性、粘着强度大的胶种,如NR、CR 等。
➢ 硫化体系:硫磺硫化体系比ROOR体系好,可生成较 多多硫键。
➢ 硫化促进剂一般选用中等活性而赋予平坦硫化性能的 促进剂DM、CZ,且硫化程度不得过深。
➢ 补强填充剂:必须用C.B补强,且应选粒径小、结构 度低的较好。