催化联合装置工艺授课课件
合集下载
催化重整工艺与工程技术课件

催化重整的工业化应用
催化重整工艺在石油化工行业中有着广泛的应用,是生产高辛烷值汽油和芳烃等产 品的重要手段。
它能够提高汽油的燃烧性能,减少汽车尾气排放,同时能够生产出大量的化工原料 ,满足化工市场的需求。
目前,催化重整工艺已经成为现代石油化工行业中的重要组成部分,具有不可替代 的地位。
02
催化重整反应原理
评价指标
主要包括转化率、选择性 、稳定性等指标。
影响因素
催化剂的活性受到多种因 素的影响,如温度、压力 、原料性质等。
04
催化重整装置的操作 和维护
催化重整装置的操作规程
操作前检查
在启动催化重整装置前,应进行 全面检查,确保设备处于良好状
态。
严格遵守安全规定
操作过程中严格遵守安全规定, 防止产生意外事故。
它是在催化剂的作用下,通过加热、加氢、再蒸馏等步骤,将长链烃结构调整为 短链烃结构,提高汽油的辛烷值。
催化重整的工艺流程
原料油经过预处理后进入重整反 应器,在催化剂的作用下进行重
整反应。
反应产物经过加热、冷却、分离 等步骤,得到高辛烷值汽油和芳
烃等产品。
催化剂经过再生和循环使用,实 现催化重整过程的连续运行。
未来催化重整工艺还将继续探索和开发新的反应路径和反应条件,以实现更加高效、环保和 可持续的生产方式。
THANKS
感谢观看
制备方法。
随着环保要求的提高,如何降低 催化重整工艺中的污染物排放和 提高能源利用效率也成为当前面
临的重要挑战。
对未来催化重整工艺与工程技术发展的展望
随着人工智能、大数据等技术的发展,催化重整工艺将逐步实现智能化、自动化和精细化生 产,提高生产效率和产品质量。
催化重整工艺-PPT

24
某汽提塔实际标定结果
操作条件
塔底油品分析
进 料 量 (公 斤 /时 ) 塔 顶 压 力 (公 斤 /厘 米 )
17.300 7.2
比重 D420 初馏点
0.7233 83
进 料 温 度 (℃ )
130
10%
90
塔 顶 温 度 (℃ )
68
50%
104
塔 底 温 度 (℃ )
187
90%
127
重 沸 炉 出 口 温 度 (℃ )
6
我国的催化重整
50年代我国开始进行催化重整催化剂及工程技术 的研究和开发。
60年代初建成一套以生产芳烃为目的,规模2万 吨/年的半再生催化重整试验装置。
1965年我国自行研究、设计和建设的第一套工业 装置投产。
7
到2005年我国已有67套重整装置建成投产,装置 总加工能力 2289万吨/年。
半再生重整 47 套 990 万吨/年
连续重整
20 套 1299 万吨/年
合 计
67 套 2289 万吨/年
11
重整工艺
重整工艺包括重整反应、反应产物的处理和催化剂 的再生等过程。
根据催化剂再生方式的不同,催化重整工艺分为半 再生重整、 循环再生重整和连续(再生)重整三 种类型。
原料石脑油在进行重整反应之前,要先进行预处理, 除去硫、氮、水、砷、铅、铜及烯烃等杂质,并切 割出适当馏分,这是催化重整装置中不可缺少的一 部分。
12
二. 基本流程
13
原料预处理的三个主要环节
预分馏 – 切割馏分 预加氢 – 转化硫、氮、氧化合物,
饱和烯烃,脱金属 汽提塔 – 脱除 H2S,NH3,H2O
14
某汽提塔实际标定结果
操作条件
塔底油品分析
进 料 量 (公 斤 /时 ) 塔 顶 压 力 (公 斤 /厘 米 )
17.300 7.2
比重 D420 初馏点
0.7233 83
进 料 温 度 (℃ )
130
10%
90
塔 顶 温 度 (℃ )
68
50%
104
塔 底 温 度 (℃ )
187
90%
127
重 沸 炉 出 口 温 度 (℃ )
6
我国的催化重整
50年代我国开始进行催化重整催化剂及工程技术 的研究和开发。
60年代初建成一套以生产芳烃为目的,规模2万 吨/年的半再生催化重整试验装置。
1965年我国自行研究、设计和建设的第一套工业 装置投产。
7
到2005年我国已有67套重整装置建成投产,装置 总加工能力 2289万吨/年。
半再生重整 47 套 990 万吨/年
连续重整
20 套 1299 万吨/年
合 计
67 套 2289 万吨/年
11
重整工艺
重整工艺包括重整反应、反应产物的处理和催化剂 的再生等过程。
根据催化剂再生方式的不同,催化重整工艺分为半 再生重整、 循环再生重整和连续(再生)重整三 种类型。
原料石脑油在进行重整反应之前,要先进行预处理, 除去硫、氮、水、砷、铅、铜及烯烃等杂质,并切 割出适当馏分,这是催化重整装置中不可缺少的一 部分。
12
二. 基本流程
13
原料预处理的三个主要环节
预分馏 – 切割馏分 预加氢 – 转化硫、氮、氧化合物,
饱和烯烃,脱金属 汽提塔 – 脱除 H2S,NH3,H2O
14
苯乙烯联合装置讲课教程

影响脱氢反应的因素
反应级数 抚顺、大连、齐鲁
单级反应器的乙苯转化率 在40~50%之内。二级乙 苯的总转化率可达到6075%。
反应压力 稀释蒸汽
降低总压 、提供热量 、 消除积炭
二、 工艺原理
(二)苯乙烯单元
苯 乙 烯 的 自 聚 和 阻 聚 机 理
苯乙烯的自聚一般是在贮存过程中发生的,它的基本反应为:苯乙烯自由基 的生成、自由基的抑制和苯乙烯的氧化。 苯乙烯自由基的热激发生成机理为:首先生成苯乙烯的二聚物,然后二聚物 产品苯乙烯的自聚和 与另一苯乙烯分子反应而生成自由基。方程式如下: 阻聚机理 2C6H5C2H3→C10H11C6H5 C10H11C6H5+C6H5C2H3→C10H11C6H5+C6H5C’=CH3(苯乙烯自由基 R’) 氧同样可以从二聚物中脱氢生成过氧化自由基, C10H11C6H5+O2→ROO’ 自由基的存在和增长将导致苯乙烯高聚物的生成。 TBC与O2在苯乙烯阻聚中的作用: 苯乙烯中的氧也会导致苯甲醛等杂质的生成,因此苯乙烯中的氧含量一般控 制在10-20ppm为宜,苯乙烯液位以上的蒸汽空间中氧含量为5-7(V)%。
急性中毒的治疗原则: 吸入:迅速将患者移至空气新鲜处,保持呼吸道通畅。呼吸 心脏停止应立即进行人工呼吸和胸外心脏按摩术,马上就医。 眼睛接触:用流动清水或生理盐水冲洗,马上就医。 皮肤接触:立即脱去被苯污染的衣服,用肥皂水清洗被污染 的皮肤,注意保温。 慢性中毒的治疗原则: 可用有助于造血功能恢复的药物,并给预对症治疗。
谢谢大家!
讲座习题:
1、乙苯单元采用中石油抚顺分公司开发的( 催化干气 )制乙苯技 术及大连化物所研制的催化干气制乙苯第( 三 )代催化剂 2、苯乙烯单元采用中石化上海石化所、华东理工大学和中石化上 海工程公司开发的乙苯负压( 绝热脱氢 )制苯乙烯工艺技术 3、苯烯比是反应进料中(苯 )与( 乙烯 )的分子比 4、乙苯脱氢反应中蒸汽的作用(降低总压) 、(提供热量) 、 (消除积炭) 5、干气精制包括:丙烯吸收、(脱丙烯 )、脱乙烯。 6、苯乙烯装置主要易燃易爆、有毒有害物质有:( 苯)、(乙 苯)、苯乙烯、DNBP、氢气等 7、苯乙烯装置罐区共有储罐( 14 )台,地下污油罐2台 8、苯乙烯食入中毒的急救措施:(饮足量温水),马上就医
催化重整装置(汽柴油生产技术课件)

循环氢 新氢
预
加
氢
反
应
器
含氢气体
预加氢反应压力影响因素
1、高分罐压力变化
高
分
罐
去蒸发塔
2、混合氢气压力变化
预分馏 塔底油
污水 预加氢加热炉
3、进料流量变化
预加氢反应空速
质量空速
预加氢进料流量(t/h) 预加氢催化剂总用量(t)
体积空速
预加氢进料流量(m3/h,20℃) 预加氢催化剂总用量(m3)
精制油
炉一
精制油
反一
六环脱氢 生成芳烃
重整反应床层温度
循环氢压缩机
炉二
炉三
炉四
氢气去预加氢
反二
反三
五环异构脱 氢生成芳烃
反四
高 分 罐
污水
烷烃异构脱 氢生产芳烃
去稳定塔
重整反应床层温度
炉一
循环氢压缩机
炉二
炉三
炉四
氢气去预加氢
精制油
反一
反二
反三
反四
四个反应器内,填装的催化剂量不同,发生的反应
类型不同,发生的反应量不同,四个反应器内的床层 温度各有不同。
预加氢加热炉
污水
精制油 1 2
1 2
1 2
1 2
1、原料中芳烃潜 含量变低
2、重整反应深度不够工艺要求:反应温 度、反应压力、空速、氢油比、催化剂活 性。
回流罐
裂化气 液化气
稳 定 塔
污水
稳定汽油
1、加氢反应脱硫,效果 与反应深度有关
3、第二次物理
方法脱硫
新氢
循环氢
排放氢
燃料气
预
回流罐
加
催化过程设备演示课件

4
——气态物料
进入催化反应器的气体为克服阻力,需先经压缩。压缩前需 先除去其中悬浮状的固态杂质,常采用气体过滤器,如苯酐生产 中作为净化空气用的滤布过滤器见图5-2。
5
压缩后的气体中会夹带少量的油质,需净化除去,用除油器 除去,见图5-3,油滴在铁皮上沉积下来,流至器底。
6
液体汽化和气体混合物的制备可按不同方法和在 各种不同构造的设备中进行,工业上常采用的两种 方法是:
15
一. 催化反应器分类
? 如果颗粒固定在位置上成为密相固定床,则为 固定
√ 床反应器。
? 如果颗粒堆积在缓慢移动的密相床中.排出结垢的 颗粒并加入新鲜的颗粒,则为 移动床反应器。
? 如果催化剂颗粒被向上流动的气体托住如流化床那 样,则为 流化床反应器。
? 如果催化剂颗粒悬浮在液体中,则为 悬浮床反应器 。
恒容过程
Vc
?
Vc ,n
?t
? 273 273
?1 ? p
10 5
m3
/
s
[教材错误! ]
Vc
?
Vc,n
t ?
? 273 273
1 ??
p
105
m3
/
s
变容过程
Vc
?
Vc , n
?t
? 273 273
??
p
? 105
m3
/
s
式中 φ体积换算系数
27
1.反应所需接触时间 τ的计算:
?
?
273 ? vVa p
? Vc,n t ? 273 ??
? 10 ? 5
14
? 气固相催化反应通常是在高温下进行(如 250 — 600℃),所以须采用能保证达到高温的热源、如 导热油、融盐、烟气等。压力可影响化学平衡进行 的方向、过程进行的速度和设备的生产能力。
——气态物料
进入催化反应器的气体为克服阻力,需先经压缩。压缩前需 先除去其中悬浮状的固态杂质,常采用气体过滤器,如苯酐生产 中作为净化空气用的滤布过滤器见图5-2。
5
压缩后的气体中会夹带少量的油质,需净化除去,用除油器 除去,见图5-3,油滴在铁皮上沉积下来,流至器底。
6
液体汽化和气体混合物的制备可按不同方法和在 各种不同构造的设备中进行,工业上常采用的两种 方法是:
15
一. 催化反应器分类
? 如果颗粒固定在位置上成为密相固定床,则为 固定
√ 床反应器。
? 如果颗粒堆积在缓慢移动的密相床中.排出结垢的 颗粒并加入新鲜的颗粒,则为 移动床反应器。
? 如果催化剂颗粒被向上流动的气体托住如流化床那 样,则为 流化床反应器。
? 如果催化剂颗粒悬浮在液体中,则为 悬浮床反应器 。
恒容过程
Vc
?
Vc ,n
?t
? 273 273
?1 ? p
10 5
m3
/
s
[教材错误! ]
Vc
?
Vc,n
t ?
? 273 273
1 ??
p
105
m3
/
s
变容过程
Vc
?
Vc , n
?t
? 273 273
??
p
? 105
m3
/
s
式中 φ体积换算系数
27
1.反应所需接触时间 τ的计算:
?
?
273 ? vVa p
? Vc,n t ? 273 ??
? 10 ? 5
14
? 气固相催化反应通常是在高温下进行(如 250 — 600℃),所以须采用能保证达到高温的热源、如 导热油、融盐、烟气等。压力可影响化学平衡进行 的方向、过程进行的速度和设备的生产能力。
双脱培训课件
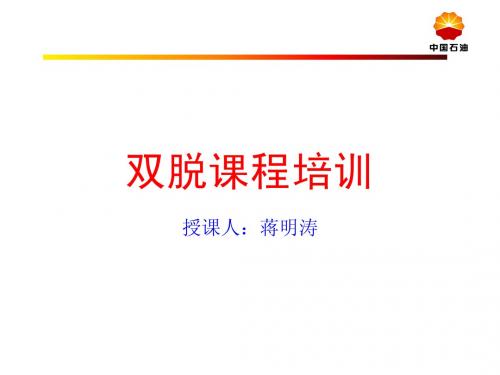
云南石化生产三部培训课件
碱液再生系统
为了脱出碱液中残留的可溶性DSO,除了DSO
分离器之外,还需要一个溶剂洗涤系统为了脱 出碱液中残留的可溶性DSO,除了DSO 分离 器之外,还需要一个溶剂洗涤系统。 由于DSO 本身也是烃,所以溶剂优先抽提碱液 相中的DSO。如果不采用溶剂洗涤步骤,那么 残留在再生碱液中的可溶性DSO 将在中被反抽 提至液态烃中。
云南石化生产三部培训课件
云南石化生产三部培训课件
碱液再生系统
由于这些反应较慢,因此,需要加入催化剂提
高反应速度。催化剂可促进氧化反应并保留在 碱相中,从而随之在整个系统中循环。
云南石化生产三部培训课件
碱液再生系统
氧化塔内产生的DSO大部分不溶于碱液,DSO
以微小的液滴悬浮在碱液中。由于这两种液体 之间的密度差别很小,必须保证在分离器内有 充分的停留时间,使得DSO 微滴可通过碱液上 升至分离器的顶部,它们在碱液相之上形成一 层液相,为了缩短两相充分分离的时间,在氧 化塔上游处加入一种溶剂,此溶剂起了两个作 用,一、它增加两相之间的密度差别以加速, 这使得从每一相夹带至另一相的夹带量减小了 许多。二、此溶剂可从碱液中抽提出一些可溶 性DSO,从而极大的降低了排出碱液中的总硫 含量。
云南石化生产三部培训课件
脱硫醇部分
包括催化液化石油气脱硫醇和轻烃回收液化石
油气脱硫醇 采用纤维膜接触脱硫醇工艺 空气氧化再生催化剂碱液及反抽提工艺
云南石化生产三部培训课件
纤维膜接触脱硫醇
从脱硫单元过来的液态烃中含有轻质硫醇(C1-
SH 至C4-SH)以及少量的酸性气体(硫化氢 和二氧化碳)。硫化氢和硫醇(RSH)属于液 态烃中普遍存在的酸性杂质。这些化合物在硫 醇抽提反应器中与碱溶液反应,从而生成硫化 钠(Na2S)、硫醇钠(NaSR)和水(H2O) 。由于这些硫化物的钠盐不能溶解于烃类相态 ,将进入碱液中,因此,可以有效地从烃类相 态中清除。相应的化学反应方程式如下:
碱液再生系统
为了脱出碱液中残留的可溶性DSO,除了DSO
分离器之外,还需要一个溶剂洗涤系统为了脱 出碱液中残留的可溶性DSO,除了DSO 分离 器之外,还需要一个溶剂洗涤系统。 由于DSO 本身也是烃,所以溶剂优先抽提碱液 相中的DSO。如果不采用溶剂洗涤步骤,那么 残留在再生碱液中的可溶性DSO 将在中被反抽 提至液态烃中。
云南石化生产三部培训课件
云南石化生产三部培训课件
碱液再生系统
由于这些反应较慢,因此,需要加入催化剂提
高反应速度。催化剂可促进氧化反应并保留在 碱相中,从而随之在整个系统中循环。
云南石化生产三部培训课件
碱液再生系统
氧化塔内产生的DSO大部分不溶于碱液,DSO
以微小的液滴悬浮在碱液中。由于这两种液体 之间的密度差别很小,必须保证在分离器内有 充分的停留时间,使得DSO 微滴可通过碱液上 升至分离器的顶部,它们在碱液相之上形成一 层液相,为了缩短两相充分分离的时间,在氧 化塔上游处加入一种溶剂,此溶剂起了两个作 用,一、它增加两相之间的密度差别以加速, 这使得从每一相夹带至另一相的夹带量减小了 许多。二、此溶剂可从碱液中抽提出一些可溶 性DSO,从而极大的降低了排出碱液中的总硫 含量。
云南石化生产三部培训课件
脱硫醇部分
包括催化液化石油气脱硫醇和轻烃回收液化石
油气脱硫醇 采用纤维膜接触脱硫醇工艺 空气氧化再生催化剂碱液及反抽提工艺
云南石化生产三部培训课件
纤维膜接触脱硫醇
从脱硫单元过来的液态烃中含有轻质硫醇(C1-
SH 至C4-SH)以及少量的酸性气体(硫化氢 和二氧化碳)。硫化氢和硫醇(RSH)属于液 态烃中普遍存在的酸性杂质。这些化合物在硫 醇抽提反应器中与碱溶液反应,从而生成硫化 钠(Na2S)、硫醇钠(NaSR)和水(H2O) 。由于这些硫化物的钠盐不能溶解于烃类相态 ,将进入碱液中,因此,可以有效地从烃类相 态中清除。相应的化学反应方程式如下:
苯乙烯联合装置讲课教程

机
制在10-20ppm为宜,苯乙烯液位以上的蒸汽空间中氧含量为5-7(V)%。
理
三、 工艺流程说明
(一)乙苯单元 (二)苯乙烯单元
(三) 辅助系统工程 (四) 罐 区
四、生产安全
苯的中ቤተ መጻሕፍቲ ባይዱ表现
急性中毒: 在短时内吸入大量的苯蒸汽可以引起急性中毒。轻症起初有粘膜
刺激症状,随后出现兴奋或酒醉状态,并伴有头痛、头晕、恶心、 呕吐等现象。重症还可能出现震颤、昏迷、阵发性或强直性抽搐、 血压下降,严重时可因呼吸和循环衰竭而死。
通过乙苯精馏塔操作是能够控 制的。
二、 工艺原理
(二)苯乙烯单元
主要是脱烷基反应,反 应式为:
C6H5C2H5=C6H6+C2 H4
C6H5C2H5+H2=C6H5 CH3+CH4
副反应
脱氢反应
乙苯脱氢 反应机理
C6H5C2H5=C6H5C2H3+H2
乙苯通过强吸热脱氢反应生成 苯乙烯,所以高温有利于乙苯
四、生产安全
乙苯的中毒表现
急性中毒: 引起咽、喉和气管的刺激症状,并有胸闷。醒后可有脑病和中
毒性肝炎的发生。直接吸入液体可致肺出血和化学性肺炎。 慢性影响:
眼及上呼吸道刺激症状、神经衰弱综合症。皮肤出现脱皮、龟 裂、粗糙。
急救措施: 同苯的急救的措施。
四、生产安全
苯乙烯的中毒表现
急性中毒: 高浓度时,对眼及上呼吸道粘膜产生刺激,出现眼痛、流泪、
反应温度
增加 脱氢反应是产 物体积增加的
气相反应,低
催化剂种类
压有利于乙苯
催化剂用脱量氢,且不存
在选择性降低
影响脱氢反应的因素
的问题。
催化装置简介课件

原料的预处理
在进入催化装置之前,原料需要经过一系列的预处理步骤,以确保其满足反应 要求。预处理包括原料的混合、加热、过滤、干燥等环节,以去除杂质、水分 和其他不利于反应的物质。
预处理的必要性
预处理能够提高原料的纯度和反应活性,减少催化剂的损耗和副产物的生成, 从而提高产品的质量和产率。
催化剂的装填与活化
催化剂的选择与制备
催化剂的活化
根据反应类型和原料性质,选择合适 的催化剂并进行制备。制备过程包括 催化剂的合成、改性、成型等环节。
在一定温度和压力下,对装填好的催 化剂进行活化处理,使其具备催化活 性。活化过程中需要注意控制温度、 压力和蔼氛等参数。
催化剂的装填
将制备好的催化剂装入催化装置中, 确保其散布均匀、填充紧密。装填方 式对催化效果和反应效率有重要影响 。
反应工艺的改进
通过改进反应工艺,降低能耗和减少副产物生成,提高产品 的质量和收率。例如,采用新型反应器、优化反应条件等手 段,实现高效、绿色的催化反应。
环保要求对催化装置的影响
环保法规的制约
随着环保法规的日益严格,催化装置的环保要求也越来越高。企业需要采取有效 措施,降低催化装置对环境的影响,如采用绿色合成路线、减少废物排放等。
温度
温度对化学反应速率和催化剂活 性有重要影响,过高或过低的温 度可能导致催化剂失活或产生副
反应。
压力
压力对化学反应的影响主要体现在 气体反应中,压力的变化可能会影 响反应速率和产物组成。
浓度与配料比
原料和催化剂的浓度以及配料比对 化学反应的进行和产置的工艺流程
原料的预处理
石油化工
精细化工
环境治理
能源工业
催化裂化、加氢裂化、 加氢精制等。
在进入催化装置之前,原料需要经过一系列的预处理步骤,以确保其满足反应 要求。预处理包括原料的混合、加热、过滤、干燥等环节,以去除杂质、水分 和其他不利于反应的物质。
预处理的必要性
预处理能够提高原料的纯度和反应活性,减少催化剂的损耗和副产物的生成, 从而提高产品的质量和产率。
催化剂的装填与活化
催化剂的选择与制备
催化剂的活化
根据反应类型和原料性质,选择合适 的催化剂并进行制备。制备过程包括 催化剂的合成、改性、成型等环节。
在一定温度和压力下,对装填好的催 化剂进行活化处理,使其具备催化活 性。活化过程中需要注意控制温度、 压力和蔼氛等参数。
催化剂的装填
将制备好的催化剂装入催化装置中, 确保其散布均匀、填充紧密。装填方 式对催化效果和反应效率有重要影响 。
反应工艺的改进
通过改进反应工艺,降低能耗和减少副产物生成,提高产品 的质量和收率。例如,采用新型反应器、优化反应条件等手 段,实现高效、绿色的催化反应。
环保要求对催化装置的影响
环保法规的制约
随着环保法规的日益严格,催化装置的环保要求也越来越高。企业需要采取有效 措施,降低催化装置对环境的影响,如采用绿色合成路线、减少废物排放等。
温度
温度对化学反应速率和催化剂活 性有重要影响,过高或过低的温 度可能导致催化剂失活或产生副
反应。
压力
压力对化学反应的影响主要体现在 气体反应中,压力的变化可能会影 响反应速率和产物组成。
浓度与配料比
原料和催化剂的浓度以及配料比对 化学反应的进行和产置的工艺流程
原料的预处理
石油化工
精细化工
环境治理
能源工业
催化裂化、加氢裂化、 加氢精制等。
催化重整装置生产原理及工艺流程[专家学习]
![催化重整装置生产原理及工艺流程[专家学习]](https://img.taocdn.com/s3/m/61f178176529647d26285292.png)
3
一、催化重整装置工艺流程简述
催化重整装置可分为五个大的部分:预处理部分、重整部分、抽 提部分、精馏部分、辅助生产部分。以下我们要详细介绍本装置各部 分的工艺流程
一类特制
4
瓦斯 轻烃
预
分 常顶料
馏
重整装置总体框图
预
重整
抽提
加
重 整
抽 提
氢
二加氢来料
辅助系统
一类特制
汽油 余油 苯
精馏
精 馏
汽油
5
(一)、预处理部分
一类特制
15
一类特制
16
一类特制
17
工艺原理 在各种烃类中,如果碳原子数相同,正构烷烃的辛烷值比异构烷
烃低得多,环烷烃的辛烷值又比芳香烃低。直馏汽油中主要成份是正 构烷烃和环烷烃,催化重整之目的就是在一定温度、压力、氢油比条 件下通过催化剂的作用,将正构烷烃和环烷烃分子中的原子重新调整 排列转化生成分子量相近或相等的芳香烃和异构烷烃,从而获得高辛
以下我们要详细介绍本装置各部分的工艺流程4一类特制常顶料预分馏预加氢辅助系统重整抽提精馏汽油二加氢来料重整抽提精馏瓦斯轻烃苯余油汽油重整装置总体框图5一类特制预处理部分预分馏塔系统预加氢系统蒸发脱水塔系统一预处理部分6一类特制初顶直馏石脑油自罐区输转87单元47罐区545556罐来经预分馏进料泵泵101102升压后进入预分馏进料换热器换102加热然后进入预分馏塔塔101塔顶分出不适宜重整进料的轻馏分塔底馏出物去预加氢
C
C
+ H2
一类特制
21
C
C
+ 4H2
-H2
nC6H14
+ 4H2
在我国多数原油中,直馏分含烷烃50~60%,其中正构烷烃又占近 半数,促进这类反应对提高汽油辛烷值和增产芳烃有很重要的意义。
催化重整装置课件
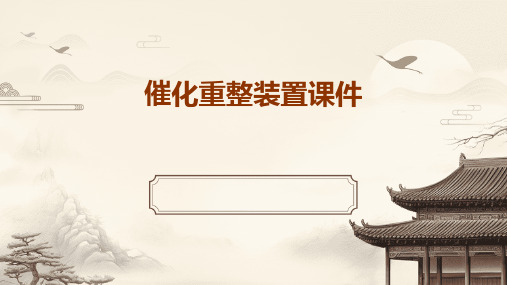
2
研究方向包括开发新型催化剂材料、优化催化剂 制备工艺以及改善催化剂活性与选择性的方法。
3
未来发展方向将更加注重催化剂的环保性能和可 持续性,以适应日益严格的环保法规和市场需求 。
降低能耗与物耗
能耗与物耗是催化重整装置运 行成本的重要组成部分,降低 能耗与物耗对于提高经济效益
具有重要意义。
研究方向包括优化重整工艺 流程、改进换热器设计、提 高热能利用效率以及开发新
常见故障及排除方法
故障三
产品收率下降
原因
原料中杂质过多、反应深度不够或催化剂中毒 。
排除方法
加强原料预处理、调整反应条件或更换催化剂。
05
CATALOGUE
催化重整装置的发展趋势与展 望
提高催化剂的活性与选择性
1
催化剂是催化重整装置的核心,提高其活性与选 择性对于提高重整油的辛烷值和氢气产量具有重 要意义。
未来发展方向将更加注重环保与 安全性能的协同提升,以实现经 济效益、社会效益和环境效益的
统一。
THANKS
感谢观看
催化重整装置课件
CATALOGUE
目 录
• 催化重整装置概述 • 催化重整装置的工艺流程 • 催化重整装置的操作与控制 • 催化重整装置的维护与保养 • 催化重整装置的发展趋势与展望
01
CATALOGUE
催化重整装置概述
催化重整装置的定义
催化重整装置是一种将石油烃类化合 物进行重整的装置,通过催化剂的作 用,将直馏汽油转化为高辛烷值的汽 油或苯、甲苯等芳烃类化学品。
程。
02 03
反应条件
催化重整反应需要高温、高压和催化剂的条件,温度通常在500-700℃ ,压力在1-5大气压,使用不同类型的催化剂可以调节反应的选择性和 产物分布。
催化重整设备课件

• 连续重整工艺的主要特征是装置内设有 单独的催化剂连续再生循环回路,使积 炭催化剂连续不断地进行再生,催化剂 始终保持有较高的活性。
• 目前此类型工艺有美国UOP公司的CCR铂 重整工艺和法国IFP的连续重整工艺。
1、UOP公司的CCR Platforming工艺
催化剂依靠重力下移,输送磨损低, 产生粉尘少,占地少,但检修较费时。
1、壳体
又称反应器筒体,壁厚不超过40毫 米,用单层厚钢板卷焊而成。
2、中心管
由管、定距圆钢和外包丝网组成。 内管布满φ6-φ8mm的小孔,外层用不 锈钢丝包扎。国内将外包冲孔板代替外 包丝网,因为外包不锈钢丝网使催化剂 破碎较严重。
3、扇形筒
• 目的:使油 气在反应器 内形成径向 流动;
• 要求:均布 于反应器内 壁圆周为限。
施。
(4)麦格纳重整装置简介
• 采用多个反应器, 催化剂装量按反应 器顺序递增;
• 各反应器入口温度 不同,逐级递升;
• 循环气分两路,一 路从一反进入,另 一路三反或四反进 入。
2、连续再生式重整装置简介
第一、二、 三反应器叠在一 起,催化剂由上 而下通过,然后 至再生器再生, 油气经加热进入 第四反应器。
(4)流化床反应器的内部构件
• 为了提高气-固流化的单程转化率,一般 选用湍动床流化系统;
• 当固体物料的颗粒性质难以改变或一定 时,内部构件的结构十分重要;
• 内部构件分两类:横向构件,纵向构件。
1)横向构件
• 多孔板 最常见;开孔率为10-40%,每隔一
米左右安装一块挡板,床层建立在挡板 上,防止气泡成长,改善停留时间分布; 挡板的夹带量和泄漏量决定床层之间的 固体交换量,有助于建立全床合适的温 度梯度和浓度梯度。其流动特性表现在 气-固相在挡板床层内激烈混合,层间进 行有限交换。
• 目前此类型工艺有美国UOP公司的CCR铂 重整工艺和法国IFP的连续重整工艺。
1、UOP公司的CCR Platforming工艺
催化剂依靠重力下移,输送磨损低, 产生粉尘少,占地少,但检修较费时。
1、壳体
又称反应器筒体,壁厚不超过40毫 米,用单层厚钢板卷焊而成。
2、中心管
由管、定距圆钢和外包丝网组成。 内管布满φ6-φ8mm的小孔,外层用不 锈钢丝包扎。国内将外包冲孔板代替外 包丝网,因为外包不锈钢丝网使催化剂 破碎较严重。
3、扇形筒
• 目的:使油 气在反应器 内形成径向 流动;
• 要求:均布 于反应器内 壁圆周为限。
施。
(4)麦格纳重整装置简介
• 采用多个反应器, 催化剂装量按反应 器顺序递增;
• 各反应器入口温度 不同,逐级递升;
• 循环气分两路,一 路从一反进入,另 一路三反或四反进 入。
2、连续再生式重整装置简介
第一、二、 三反应器叠在一 起,催化剂由上 而下通过,然后 至再生器再生, 油气经加热进入 第四反应器。
(4)流化床反应器的内部构件
• 为了提高气-固流化的单程转化率,一般 选用湍动床流化系统;
• 当固体物料的颗粒性质难以改变或一定 时,内部构件的结构十分重要;
• 内部构件分两类:横向构件,纵向构件。
1)横向构件
• 多孔板 最常见;开孔率为10-40%,每隔一
米左右安装一块挡板,床层建立在挡板 上,防止气泡成长,改善停留时间分布; 挡板的夹带量和泄漏量决定床层之间的 固体交换量,有助于建立全床合适的温 度梯度和浓度梯度。其流动特性表现在 气-固相在挡板床层内激烈混合,层间进 行有限交换。
催化联合装置培训2
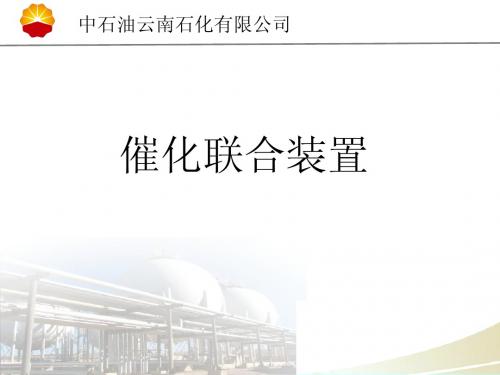
中石油云南石化有限公司
• 重油催化裂化装置工艺原理: 渣油等大分子烃类,在高温低压操作条件下,通过 催化裂化催化剂表面强酸中心的催化作用,使烃类分子 发生以裂化、异构化、氢转移反应为主的多种复杂反应 ,使大分子烃类转化为各种小分子烃类的混合物,并通 过后续分馏稳定系统分离出干气、液化气、汽油、柴油 及油浆等产品,反应过程形成的焦炭被用于工艺过程消 耗并提供热量。 催化裂化生产在非临氢条件下进行,属于脱碳反应 ,原料中的碳向油浆、焦炭等大分子产品富集,而氢则 向干气、液化气、汽油等小分子产品富集,原料的氢含 量(或烃族组成)对产品分布与装置操作有重要影响。
• • • •
中石油云南石化有限公司
异构化/芳构化 —烷基化功能
—补偿加氢过程损失的辛烷值
23
催化裂化反应现有的一些认识 现代催化裂化过程:
抑制与正碳离子裂化竞争的自由基反应
—— 以获取重油转化良好选择性
提高双分子反应的选择性
—— 以提高汽油产率和质量
提高正碳离子裂化选择性
—— 以增产丙烯
24
第一部分 催化联合装置概述
中石油云南石化有限公司 • 催化联合装置由四套装置构成 1、催化裂化装置 2、双脱联合装置 3、气分装置 4、MTBE装置 催化联合装置与常减压联合装置(包括常减压 装置和轻烃回收装置)组成生产一部联合装置
中石油云南石化有限公司
• 催化联合装置的生产过程: 1、催化裂化装置: 加氢渣油来自渣油加氢装置作为催化裂化装置的原料。 ⑴催化裂化装置组成: ①反应--再生部分(常规提升管+UOPVSS成套技术-LPEC快速床+湍流床 再生技术) ②主风机及烟气能量回收部分 ③分馏、吸收稳定部分(含气压机部分) ④产汽及余热回收部分 ⑤ 烟气脱硫脱硝部分 ⑵经过催化裂化装置后的产品: ①干气:进入双脱联合装置脱硫,进厂瓦斯管网。 ②液化气:进入双脱联合装置脱硫脱硫醇,合格的液化气产品到气分 装置 ③汽油:进入催化汽油加氢装置 ④柴油:进入催化柴油加氢装置 ⑤焦炭:催化裂化装置再生系统消耗 ⑥油浆:经油浆过滤器后,作为焦化装置的一部分原料。
催化重整装置生产原理及工艺流程课件

催化重整装置生产原理 及工艺流程课件
目录 CONTENT
• 催化重整装置概述 • 催化重整装置生产原理 • 催化重整装置工艺流程 • 催化重整装置操作与维护 • 催化重整装置安全与环保 • 催化重整装置发展与展望
01
催化重整装置概述
催化重整装置的定义
催化重整装置是一种将石油烃类原料 进行重整的装置,通过催化剂的作用 ,将原料转化为芳烃和氢气的过程。
产品分离部分
能量回收部分
包括分馏塔、稳定塔等设备,用于将重整 产物分离成各种组分,如汽油、苯、甲苯 等。
包括热回收系统、发电系统等,用于回收 重整反应中产生的热量和压力能。
02
催化重整装置生产原理
原料预处理原理
原料预处理
预处理是催化重整装置生产中的 重要环节,主要目的是去除原料 中的杂质,如水分、盐类、重金 属等,以提高原料的质量和稳定 性。
未来催化重整装置将更加注重能效提升、污染物排放减少和资源循环利用,通过技术创新和产业升级,实现绿色 可持续发展。
感谢您的观看
THANKS
氢气和副产品分别收集起来。
产品精制
02
重整油经过精制处理,通过吸附、萃取等方法脱除杂质和不稳
定组分,提高产品的质量和稳定性。源自产品储存和运输03
处理后的重整油和其他产品储存于储罐中,根据市场需求进行
运输和销售。
04
催化重整装置操作与维 护
装置启动与运行
启动准备
检查装置的各项准备工作,包 括原料、催化剂、仪表、阀门
产品种类及性质
产品的种类和性质取决于 原料的组成、反应条件和 催化剂的种类。
产品分离与提纯
产品经过分离与提纯,去 除杂质和未反应的原料, 得到符合质量要求的最终 产品。
目录 CONTENT
• 催化重整装置概述 • 催化重整装置生产原理 • 催化重整装置工艺流程 • 催化重整装置操作与维护 • 催化重整装置安全与环保 • 催化重整装置发展与展望
01
催化重整装置概述
催化重整装置的定义
催化重整装置是一种将石油烃类原料 进行重整的装置,通过催化剂的作用 ,将原料转化为芳烃和氢气的过程。
产品分离部分
能量回收部分
包括分馏塔、稳定塔等设备,用于将重整 产物分离成各种组分,如汽油、苯、甲苯 等。
包括热回收系统、发电系统等,用于回收 重整反应中产生的热量和压力能。
02
催化重整装置生产原理
原料预处理原理
原料预处理
预处理是催化重整装置生产中的 重要环节,主要目的是去除原料 中的杂质,如水分、盐类、重金 属等,以提高原料的质量和稳定 性。
未来催化重整装置将更加注重能效提升、污染物排放减少和资源循环利用,通过技术创新和产业升级,实现绿色 可持续发展。
感谢您的观看
THANKS
氢气和副产品分别收集起来。
产品精制
02
重整油经过精制处理,通过吸附、萃取等方法脱除杂质和不稳
定组分,提高产品的质量和稳定性。源自产品储存和运输03
处理后的重整油和其他产品储存于储罐中,根据市场需求进行
运输和销售。
04
催化重整装置操作与维 护
装置启动与运行
启动准备
检查装置的各项准备工作,包 括原料、催化剂、仪表、阀门
产品种类及性质
产品的种类和性质取决于 原料的组成、反应条件和 催化剂的种类。
产品分离与提纯
产品经过分离与提纯,去 除杂质和未反应的原料, 得到符合质量要求的最终 产品。
- 1、下载文档前请自行甄别文档内容的完整性,平台不提供额外的编辑、内容补充、找答案等附加服务。
- 2、"仅部分预览"的文档,不可在线预览部分如存在完整性等问题,可反馈申请退款(可完整预览的文档不适用该条件!)。
- 3、如文档侵犯您的权益,请联系客服反馈,我们会尽快为您处理(人工客服工作时间:9:00-18:30)。
6)新世纪初,两段提升管催化裂化技术工业 化,是提升管催化裂化技术的又一新里程碑 7)多种汽油降烯烃技术与催化剂的开发,提 高了产品质量,满足环保法规要求。 8)山东地炼企业的催化裂化装置的发展非常 快,从80年代最早的3.5万吨/年的小催化到 现在的大装置140万吨/年的单套装置已有多 套,有的企业建有多套催化装置,当前国内 最大的单套催化能力为广西石化350万吨/年, 在中石油中石化还有多套300万吨/年的。
催化裂化反应
1、催化原料在催化剂的作用下发生一系列的化学反应, 同时反应的产物还会在催化剂的作用下发生二次反应, 因为反应的最终产物为焦炭和气体,因此要控制原料 油和催化剂的接触时间,控制二次反应,使想要的产 品的收率最大化。 2、主要反应类型 1)分解(裂化)反应:主要是大分子断链成为小分子, 一般在直链烷烃、烯烃、环烷烃开环等为主。 2)氢转移反应:氢从一个分子上脱下来加到另一个烯 烃分子上使之饱和,二烯烃最容易接受氢成为单烯烃, 是催化裂化特有的反应。 3)异构化反应:不改变分子量,但改变分子结构。 4)芳构化反应:在完成芳构化的同时脱氢。 5)聚合反应:多个小分子合成大分子,最终结果生成 焦炭。
气分装置加工能力:15万吨/年,18吨/小时 原料:为催化装置所产的液化气、焦化装 置液化气 产品:丙烷、丙烯、混合碳四,其中混合 碳四作为MTBE装置的原料。 工艺原理:气分部分是典型的精馏单元,主 要靠各介质的沸点不同进行切割分离。 (结合DCS画面简单介绍气分工艺流程)
MTBE装置加工能力:原料8万吨/年,产出 MTBE 2.2万吨/年,加工量10吨/小时,其中原 料中异丁烯含量约占17% 反应原理:混合碳四中的异丁烯与甲醇在树脂 催化剂的作用下发生醚化反应生成甲基叔丁基 醚,可以作为化工原料、调对高辛烷值汽油的 组分,因其辛烷值较高在117,装置上出的纯 度在95%左右,辛烷值会少低一些,在作为汽 油调和组分时需要注意氧含量的控制。 剩余产品:醚后碳四,因其含有正丁烯,还可 继续深加工。(结合DCS画面简单介绍工艺)
催化主要产品
1、干气:约占2.5-4%,主要用途送至公司燃料气管网做燃料。 2、液化气:约占10-15%,主要送至气分装置进行分离为丙烷、 丙烯、碳四;碳四中的异丁烯组分再与甲醇反应生成MTBE。 3、汽油:约占35-45%,辛烷值在90左右,送至汽油加氢装置 脱硫后作为产品外销。 4、催化柴油:约占25-35%,因其十六烷值低、安定性差,主 要送至加氢装置做原料。 5、油浆:约占3-7%,主要受原料性质影响,原料越重因其裂 解性能越差,油浆收率就会随之升高,如原料为石蜡基蜡油, 装置基本不会外送油浆,如原料为环烷基,因其裂解性能差, 外甩油浆量就会较大。主要用途:作燃料、进焦化作原料,因 其中含有一定量的催化剂粉末会影响焦炭的灰分,掺炼比例要 控制。 6、焦炭:约占7-12%,主要用于催化剂再生时燃烧提供所需热 量,不会在产品中体现工能力80万吨/年 2、两器形式:同高并列,前置烧焦罐,石 油大学开发的两段提升管TMP工艺,但有 些变动。 3、装置组成部分:反再系统、主风机组、 分馏系统、富气压缩机组、吸收稳定系统、 双脱系统、开工锅炉系统。(根据DCS画面 讲解主要流程工艺)
气分、MTBE装置介绍
催化剂
1、我国催化裂化催化剂主要生产基地 中石化齐鲁催化剂公司(山东淄博周村) 中石化长岭催化剂公司(湖南岳阳长岭) 中石油兰州石化催化剂厂(甘肃兰州) 现已有多家民企开始生产催化剂,淄博正轩、青岛惠 城、山西腾茂等 2、催化剂的主要性能指标 微反活性、比表面积、孔体积、密度、粒度分布、抗 磨指数、抗重金属能力等(见表2) 催化剂的基质主要是Al2O3,为提高活性,增加了分子筛, 通过粘结剂成为一体,主要是为提高活性、对原料裂 解的选择性、抗重金属能力等多方面考虑。 新鲜剂的活性在78左右,比表面积在250-300㎡/g
原料组成及性质
1、主要有直馏蜡油、焦化蜡油、加氢蜡油、常压渣油、减 压渣油等 比重:0.86-0.93 残碳:0.3-10 Ni+V:310PPm H含量:11.8-13% 氢平衡是制约催化裂化产品分布的关键。催裂化反应也 可理解为是氢的再分配,因此原料中的氢含量越多,就会 越容易裂解,轻组分收率就越高。我装置在设计时提出的 氢含量要求不小于11.8% 2、评价催化裂化原料的指标: 1)馏分组成:馏程程范围300-500℃ , 密度小于 0.92g/cm3,随着原料变重当前的密度已到0.94左右。 2)烃类族组成: 石蜡基原料裂解性能最好,其次是中间基,环烷基原料 (主要指芳烃类)裂解性能差。
5)金属含量:钠、铁、镍、钒、铜 要严格限制重金属含量,对催化剂产生毒素作 用,活性下降,选择性差,生焦大。 通过电脱盐控制钠盐含量小于3ug/g。 镍小于10 ug/g ,钒小于1 ug/g 。 镍具有脱氢作用,会造成干气中氢含量上升、 焦炭收率上升、目的产物下降,通过分析干气 中的H/C就能判断镍的含量变化。 钒会破坏分子筛的晶体结构,降低催化剂活性。 6)我公司催化装置原料油设计指标(见表1)
催化裂化联合装置 基础知识培训
2014.07.22
主要内容
催化裂化装置发展历程 原料和产品 催化剂 反应原理 我公司催化装置工艺介绍
催化裂化装置发展历程
1、概述
1)催化裂化是目前我国最重要的二次加工工艺,是最重要 的重质油轻质化过程之一。
2)肩负着我国80%以上汽油与30%以上柴油的生产任务。 3)这是由我国原油重质馏分多的特点决定的。 4)大于350℃馏分占60%-70%以上
汽油加氢装置介绍
装置加工能力:32万吨/年,40吨/小时 工艺原理:采用法国Axens公司工艺包,在全馏分 选择性加氢后,使汽油中的二烯烃饱和,再把轻 重汽油切割后,重汽油进行加氢脱硫,降至< 100ppm,根据国四汽油标准,现在要降至50ppm 以下。通过调整反应温度能够实现。 轻汽油送至醚化单元,其中的异戊稀与甲醇反应 生成甲基叔戊基醚,醚后轻汽油与脱臭后的重汽 油汇合后送至罐区。 重汽油在加氢装置经脱硫后送至无碱脱臭单元, 在催化剂的作用下使其博士试验通过、硫醇硫< 10ppm后与轻汽油汇合出装置。 (结合工艺流程图讲解工艺要点)
5)必须有强大的二次加工工艺,满足国民经济对轻质油品 的需求。
6)催化裂化工艺在我国做到了最大能力的衍生,反再系统
有多种工艺。
2、发展历程
1)五十年代引进前苏联移动床催化裂化(小球催化 剂) 1965年我国第一套流化催化裂化在抚顺石油二厂 建成投产设计能力为60万吨/年,75年改造为90万 吨/年。 2)七十年代分子筛催化剂的出现,带动了提升管催 化裂化技术的发展。 3)1984年石家庄炼油厂大庆全常渣催化裂化的工业 运行,翻开了我国重油催化裂化的新篇章。 4)九十年代初,前郭炼油厂实现了吉林原油全减压 渣油催化裂化;1998年大庆全减渣在燕化炼油厂 实行了工业化。 5)九十年代,催化裂化家族技术生产低烯烃成为催 化裂化技术的又一新领域。
平衡剂
经过使用的催化剂为平衡剂,因为平衡剂是连续 使用的,因此对平衡剂的各项指标进行检测分析 是非常重要的。 主要参考指标: 重金属含量,直接影响催化剂的活性中心,造成 活性下降及比表面积降低(主要分析镍、钒、钠、 铁、钙、锑等)。 比表面积,直接影响原料油与催化剂的接触效果。 活性,主要反映中毒情况。 粒度分布,能够反映催化剂的流动性。 (平衡剂分析报告单见表3)
烷烃多的原料,易裂化轻收高,催化理想原料。 芳烃多,难裂化,轻收少,生焦量多。 烃类的生焦能力排序:芳烃>烯烃>环烷烃>烷烃 通过分析原料的四组分可以较直观的判断原料性质,饱 和烃、芳香烃、胶质、沥青质
3)残碳:反映了原料中生焦物质的多少。 馏分油0.4%, 渣油4-10%,生焦大,一般作为掺炼,具体掺炼量只要依据 反再系统的热量平衡。 4)含硫、含氮 硫含量多,转化率下降、汽油产率下降、气体产率上升,产品 选择性差,增加设备管线腐蚀,烟气中的硫化物增加很多,我 装置提出的设计参数是最大不能超过1.5% 氮含量多,碱性氮化物能强烈吸附在催化剂表面,中和酸性中 心,造成活性降低,一般要求原料中的碱性氮小于700ppm,中 性氮化物对使油品安定性下降。焦化蜡油因其碱性氮含量高、 含烯烃和芳烃多转化率低一般作为掺炼原料,经验值为不超7%。