浅谈铸造缺陷对铸件的影响
浅析铸造缺陷成因加强铸件质量管理
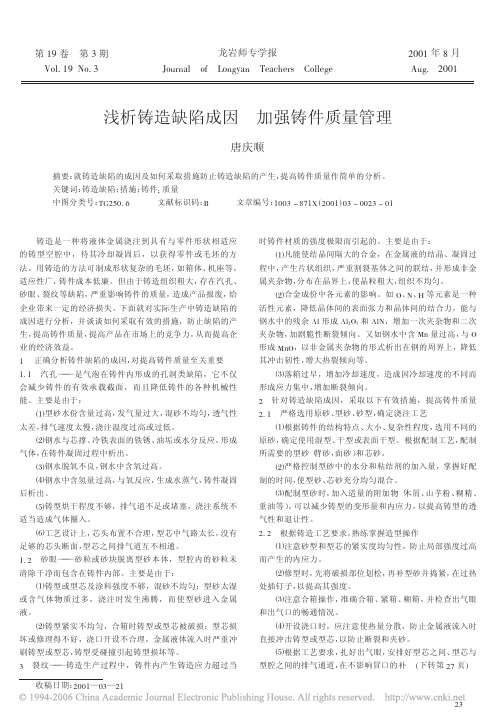
时铸件材质的强度极限而引起的。主要是由于: ! 凡能使结晶间隔大的合金,在金属液的结晶、凝固过 程中, 产生片状组织, 严重割裂基体之间的联结, 并形成非金 属夹杂物, 分布在晶界上, 使晶粒粗大, 组织不均匀。 " 合金成份中各元素的影响。如 F、 *、 G 等元素是一种 活性元素,降低晶体间的表面张力和晶体间的结合力,能与 钢水中的残余 ,( 形成 ,(! F" 和 ,(*,增加一次夹杂物和二次 夹杂物, 加剧脆性断裂倾向。又如钢水中含 H1 量过高, 与F 形成 H1F,以非金属夹杂物的形式析出在钢的周界上,降低 其冲击韧性, 增大热裂倾向等。 # 落箱过早,增加冷却速度,造成因冷却速度的不同而 形成应力集中, 增加断裂倾向。 ! !) $ 针对铸造缺陷成因,采取以下有效措施,提高铸件质量 严格选用原砂、 型砂、 砂型, 确定浇注工艺 大小、 复杂性程度, 选用不同的 ! 根据铸件的结构特点、 原砂, 确定使用湿型、 干型或表面干型。根据配制工艺, 配制 所需要的型砂 ( 背砂, 面砂 ) 和芯砂。 " 严格控制型砂中的水分和粘结剂的加入量,掌握好配 制的时间, 使型砂、 芯砂充分均匀混合。 加入适量的附加物 ( 木屑、 山芋粉、 糊精、 # 配制型砂时, 重油等 ) , 可以减少铸型的变形量和内应力, 以提高铸型的透 气性和退让性。 !) ! 根据铸造工艺要求, 熟练掌握造型操作 ! 注意砂型和型芯的紧实度均匀性,防止局部强度过高 而产生的内应力。 先将破损部位划松, 再补型砂并捣紧, 在过热 " 修型时, 处插钉子, 以提高其强度。 准确合箱、 紧箱、 糊箱, 并检查出气眼 # 注意合箱操作, 和出气口的畅通情况。 $ 开设浇口时,应注意使热量分散,防止金属液流入时 直接冲击铸型或型芯, 以防止断裂和夹砂。 扎好出气眼, 安排好型芯之间、 型芯与 % 根据工艺要求, 型腔之间的排气通道, 在不影响冒口的补 D 下转第 !B 页 E
铸造工艺流程中的铸件缺陷分析与改进策略

铸造工艺流程中的铸件缺陷分析与改进策略铸造工艺是一种重要的金属加工方法,用于制造各种形状的金属件。
然而,在铸造过程中,铸件缺陷是一个常见的问题,它会影响到铸件的质量和性能。
因此,对于铸造工艺流程中的铸件缺陷进行深入分析,并提出改进策略,对于提高铸件质量和工艺效率具有重要意义。
一、铸件缺陷的分类与原因分析在铸造工艺中,铸件缺陷可以分为表面缺陷和内部缺陷两类。
常见的表面缺陷包括气孔、砂眼、砂洞等;内部缺陷主要有夹杂物、孔洞、收缩系数不均匀等。
1.1 气孔气孔是铸造工艺中最常见的表面缺陷之一。
其形成的原因通常有两个方面,一是液态金属中溶解气体含量过高,二是在金属凝固过程中,气体生成而未能有效排除。
造成气孔的常见因素包括砂芯质量不佳、浇注温度过高、浇注速度过快等。
1.2 砂眼和砂洞砂眼是指铸件表面局部凹陷的缺陷,而砂洞是指铸件内部或边缘凹陷的缺陷。
主要原因包括模具缺陷、浇注系统设计不合理、浇注金属温度过低等。
1.3 夹杂物夹杂物是指铸件中存在的杂质,如炉渣、油污等。
其主要原因包括铁水净化不彻底、砂芯质量不佳等。
1.4 孔洞孔洞是指铸件内部存在的封闭空腔。
常见的孔洞形式包括气孔和收缩孔。
造成孔洞的原因主要有铁水中含气量高、铸型泥浆含水量高等。
1.5 收缩系数不均匀收缩系数不均匀是指铸件不同部位的收缩量不一致。
这可能会引起铸件的内部应力集中,从而导致开裂和变形。
收缩系数不均匀的原因包括铸造合金的特性、浇注温度的控制等。
二、改进策略为了减少铸件缺陷,提高铸件质量和工艺效率,以下是一些改进策略的具体措施:2.1 优化模具设计模具设计是影响铸件质量的关键因素之一。
通过优化模具结构、提高模具材料质量和表面光洁度,可以减少砂眼、砂洞等表面缺陷的产生。
2.2 控制浇注温度和速度浇注温度和速度对铸件质量有着直接的影响。
合理控制浇注温度和速度,可以降低气孔和夹杂物等缺陷的产生。
2.3 改进铸型材料和工艺选择合适的铸型材料,对铸件质量和工艺效率的提高至关重要。
球墨铸铁常见的铸造缺陷

球墨铸铁常见的铸造缺陷球墨铸铁是一种用途广泛的合金材料,广泛应用于汽车、机械、农业机械、建筑设备等工业领域。
虽然球墨铸铁有很多优点,如高强度、高韧性、耐腐蚀和低温性能等,但它也有一些常见的铸造缺陷需要注意。
第一,浇口缺陷。
浇口是铸造过程中的关键部位,它是铸件的入口,直接关系到铸件的质量。
球墨铸铁的浇口缺陷主要包括翘口、裂纹和气孔等。
这些缺陷会导致铸件的强度降低,表面质量差,甚至无法使用。
第二,气孔缺陷。
气孔是铸铁材料中最常见的缺陷之一,也是球墨铸铁的重要缺陷类型。
气孔是由于铸造过程中未能完全去除空气或其他气体引起的。
气孔会导致铸件的强度下降,同时对铸件的密封和耐腐蚀性能也有影响。
第三,缩孔缺陷。
缩孔是铸件内部的气孔,是由于铸造过程中液态金属流动受阻引起的。
缩孔也会影响铸件的强度和维修性能,过多的缩孔会导致铸件完全失效。
第四,热裂缺陷。
球墨铸铁具有很好的耐热性能,但在铸造过程中可能会出现热裂缺陷。
热裂是由于铸件随着温度升高而产生的热应力引起的。
这种缺陷可能会导致铸件断裂,影响使用寿命。
为了避免这些缺陷的发生,需要在整个铸造过程中加强质量控制和监测。
对于浇口和气孔缺陷,可以在设计过程中优化铸件结构和浇注系统,加强铸造参数的控制和优化。
对于缩孔和热裂缺陷,需要加强熔炼和浇注过程的管理,避免过度的冷却和应力积累。
总之,球墨铸铁作为一种重要的铸造材料,在铸造过程中容易出现一些常见的缺陷。
加强质量控制和监测,优化铸造结构和参数控制,可以有效地减少这些缺陷的出现,提高球墨铸铁的质量和使用寿命。
铸造工艺对铸件组织和性能的影响研究
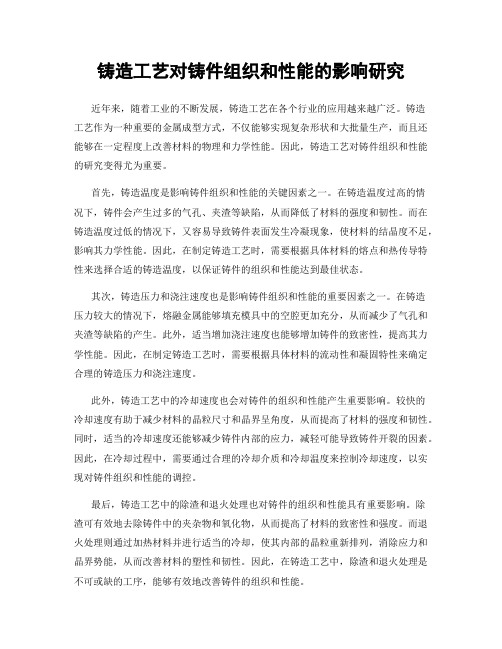
铸造工艺对铸件组织和性能的影响研究近年来,随着工业的不断发展,铸造工艺在各个行业的应用越来越广泛。
铸造工艺作为一种重要的金属成型方式,不仅能够实现复杂形状和大批量生产,而且还能够在一定程度上改善材料的物理和力学性能。
因此,铸造工艺对铸件组织和性能的研究变得尤为重要。
首先,铸造温度是影响铸件组织和性能的关键因素之一。
在铸造温度过高的情况下,铸件会产生过多的气孔、夹渣等缺陷,从而降低了材料的强度和韧性。
而在铸造温度过低的情况下,又容易导致铸件表面发生冷凝现象,使材料的结晶度不足,影响其力学性能。
因此,在制定铸造工艺时,需要根据具体材料的熔点和热传导特性来选择合适的铸造温度,以保证铸件的组织和性能达到最佳状态。
其次,铸造压力和浇注速度也是影响铸件组织和性能的重要因素之一。
在铸造压力较大的情况下,熔融金属能够填充模具中的空腔更加充分,从而减少了气孔和夹渣等缺陷的产生。
此外,适当增加浇注速度也能够增加铸件的致密性,提高其力学性能。
因此,在制定铸造工艺时,需要根据具体材料的流动性和凝固特性来确定合理的铸造压力和浇注速度。
此外,铸造工艺中的冷却速度也会对铸件的组织和性能产生重要影响。
较快的冷却速度有助于减少材料的晶粒尺寸和晶界呈角度,从而提高了材料的强度和韧性。
同时,适当的冷却速度还能够减少铸件内部的应力,减轻可能导致铸件开裂的因素。
因此,在冷却过程中,需要通过合理的冷却介质和冷却温度来控制冷却速度,以实现对铸件组织和性能的调控。
最后,铸造工艺中的除渣和退火处理也对铸件的组织和性能具有重要影响。
除渣可有效地去除铸件中的夹杂物和氧化物,从而提高了材料的致密性和强度。
而退火处理则通过加热材料并进行适当的冷却,使其内部的晶粒重新排列,消除应力和晶界势能,从而改善材料的塑性和韧性。
因此,在铸造工艺中,除渣和退火处理是不可或缺的工序,能够有效地改善铸件的组织和性能。
综上所述,铸造工艺对铸件组织和性能具有显著的影响。
适当选择铸造温度、铸造压力和浇注速度,合理控制冷却速度,以及进行除渣和退火处理,都能够改善铸件的组织和性能,使其更好地满足实际使用要求。
铸造合金中的晶格缺陷及其对性能的影响
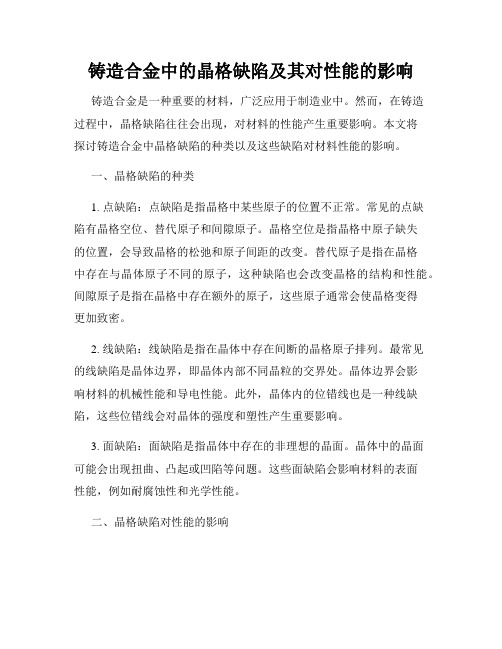
铸造合金中的晶格缺陷及其对性能的影响铸造合金是一种重要的材料,广泛应用于制造业中。
然而,在铸造过程中,晶格缺陷往往会出现,对材料的性能产生重要影响。
本文将探讨铸造合金中晶格缺陷的种类以及这些缺陷对材料性能的影响。
一、晶格缺陷的种类1. 点缺陷:点缺陷是指晶格中某些原子的位置不正常。
常见的点缺陷有晶格空位、替代原子和间隙原子。
晶格空位是指晶格中原子缺失的位置,会导致晶格的松弛和原子间距的改变。
替代原子是指在晶格中存在与晶体原子不同的原子,这种缺陷也会改变晶格的结构和性能。
间隙原子是指在晶格中存在额外的原子,这些原子通常会使晶格变得更加致密。
2. 线缺陷:线缺陷是指在晶体中存在间断的晶格原子排列。
最常见的线缺陷是晶体边界,即晶体内部不同晶粒的交界处。
晶体边界会影响材料的机械性能和导电性能。
此外,晶体内的位错线也是一种线缺陷,这些位错线会对晶体的强度和塑性产生重要影响。
3. 面缺陷:面缺陷是指晶体中存在的非理想的晶面。
晶体中的晶面可能会出现扭曲、凸起或凹陷等问题。
这些面缺陷会影响材料的表面性能,例如耐腐蚀性和光学性能。
二、晶格缺陷对性能的影响1. 机械性能:晶格缺陷会导致晶体内部的应力集中,从而影响材料的强度和塑性。
晶体边界和位错线是应力集中的主要来源,它们会削弱材料的结构。
此外,晶格缺陷还会影响材料的断裂韧性和疲劳寿命。
2. 导电性能:晶格缺陷会影响材料的导电性能。
晶格中存在的点缺陷可以改变电子的能带结构和电子迁移率。
例如,替代原子可以引入杂质能级,影响电子的导电行为。
晶格缺陷还会影响电子和离子的迁移速率,从而改变材料的电导率。
3. 光学性能:晶格缺陷对材料的光学性能也有显著影响。
晶格中的面缺陷可以散射光线,影响材料的透明度和折射率。
此外,晶格缺陷还可以影响材料的光吸收和发射特性,对光电器件的性能产生重要影响。
4. 热稳定性:晶格缺陷还会影响材料的热稳定性。
点缺陷和线缺陷在高温下容易发生变化,导致晶体结构的相变和晶格的失稳。
铸铁 缺陷 国标
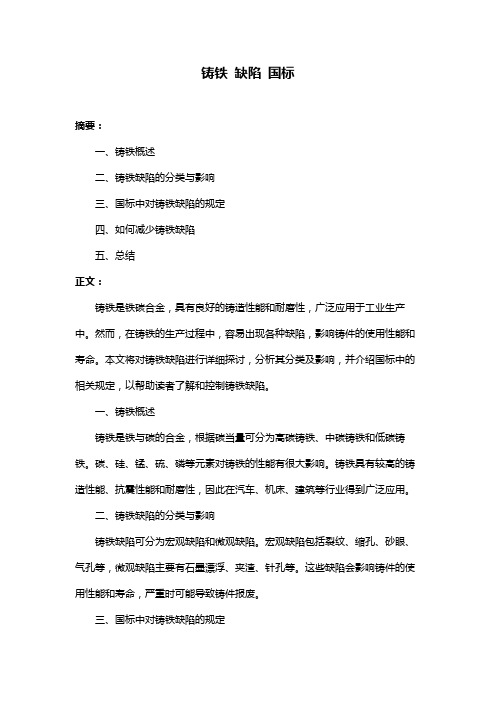
铸铁缺陷国标摘要:一、铸铁概述二、铸铁缺陷的分类与影响三、国标中对铸铁缺陷的规定四、如何减少铸铁缺陷五、总结正文:铸铁是铁碳合金,具有良好的铸造性能和耐磨性,广泛应用于工业生产中。
然而,在铸铁的生产过程中,容易出现各种缺陷,影响铸件的使用性能和寿命。
本文将对铸铁缺陷进行详细探讨,分析其分类及影响,并介绍国标中的相关规定,以帮助读者了解和控制铸铁缺陷。
一、铸铁概述铸铁是铁与碳的合金,根据碳当量可分为高碳铸铁、中碳铸铁和低碳铸铁。
碳、硅、锰、硫、磷等元素对铸铁的性能有很大影响。
铸铁具有较高的铸造性能、抗震性能和耐磨性,因此在汽车、机床、建筑等行业得到广泛应用。
二、铸铁缺陷的分类与影响铸铁缺陷可分为宏观缺陷和微观缺陷。
宏观缺陷包括裂纹、缩孔、砂眼、气孔等,微观缺陷主要有石墨漂浮、夹渣、针孔等。
这些缺陷会影响铸件的使用性能和寿命,严重时可能导致铸件报废。
三、国标中对铸铁缺陷的规定我国国标GB/T 9441-2019《铸铁验收标准》对铸铁缺陷进行了详细规定。
标准中规定了各类缺陷的允许范围、检测方法和判定准则,为铸铁产品质量的验收提供了依据。
四、如何减少铸铁缺陷1.合理设计铸型和浇注系统,减小金属液的流动速度,降低产生缺陷的风险。
2.选用优质的铸造原材料,严格控制化学成分,提高铸铁的性能。
3.优化铸造工艺,提高熔炼、浇注、冷却等环节的控制水平。
4.加强铸造过程中的检测与检验,及时发现和消除缺陷。
五、总结铸铁缺陷是影响铸件质量的关键因素,了解其分类和影响,遵循国标的规定,采取有效的控制措施,对提高铸铁产品质量具有重要意义。
铸造缺陷及其对策

某铸件在浇注过程中,由于模具表面存在油污和杂质,导 致金属液中混入杂质,最终在铸件表面形成明显的夹渣。
解决方案
保持模具表面干净整洁,避免油污和杂质混入金属液;采 用过滤网或过滤器等措施,去除金属液中的杂质。
裂纹案例
裂纹
在铸造过程中,由于铸件结构不合理、模具温度不均匀或金属液冷 却过快等原因,导致铸件中产生裂纹。
夹渣
总结词
夹渣是由于铸造过程中熔渣混入金属液中,在铸件凝固时未能及时浮出而形成的 夹杂物。
详细描述
夹渣通常表现为不规则的块状或颗粒状,大小不一,对铸件的机械性能和使用寿 命有一定影响。夹渣的形成与金属液的净化程度、浇注系统和模具的设计等因素 有关。
裂纹
总结词
裂纹是铸造过程中由于金属液的冷却收缩而产生的缝隙,通 常表现为细长的线性缺陷。
加强生产过程监控
对生产过程进行实时监控,及时发现并处理异常 情况。
3
提高员工技能水平
加强员工技能培训,提高员工操作技能和安全意 识。
引入先进技术与管理方法
引进现代化铸造设备
采用自动化、智能化的铸造设备,提高生产效 率和产品质量。
推行精益生产管理
引入精益生产管理理念和方法,优化生产流程, 降低生产成本。
建立完善的质量管理体系
建立完善的质量管理体系,确保产品质量符合标准要求。
05
铸造缺陷的修复与处理
焊接修复
总结词
焊接修复是一种常见的铸造缺陷修复方法,适用于修复裂纹、断裂等缺陷。
详细描述
焊接修复通过将焊料熔化填充铸造缺陷,冷却后形成坚固的连接,实现对铸造缺陷的修复。焊接修复 具有操作简便、快速、成本低等优点,但需注意焊接过程中可能产生的热影响区和焊接应力,可能导 致新的缺陷或变形。
铸造过程中常见的几种缺陷
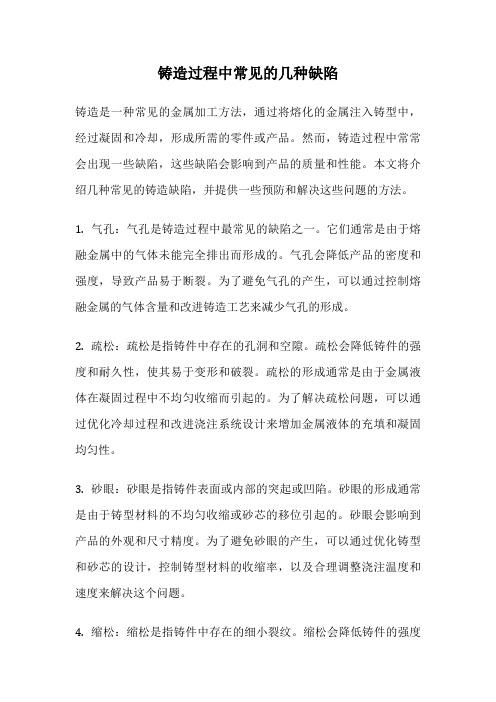
铸造过程中常见的几种缺陷铸造是一种常见的金属加工方法,通过将熔化的金属注入铸型中,经过凝固和冷却,形成所需的零件或产品。
然而,铸造过程中常常会出现一些缺陷,这些缺陷会影响到产品的质量和性能。
本文将介绍几种常见的铸造缺陷,并提供一些预防和解决这些问题的方法。
1. 气孔:气孔是铸造过程中最常见的缺陷之一。
它们通常是由于熔融金属中的气体未能完全排出而形成的。
气孔会降低产品的密度和强度,导致产品易于断裂。
为了避免气孔的产生,可以通过控制熔融金属的气体含量和改进铸造工艺来减少气孔的形成。
2. 疏松:疏松是指铸件中存在的孔洞和空隙。
疏松会降低铸件的强度和耐久性,使其易于变形和破裂。
疏松的形成通常是由于金属液体在凝固过程中不均匀收缩而引起的。
为了解决疏松问题,可以通过优化冷却过程和改进浇注系统设计来增加金属液体的充填和凝固均匀性。
3. 砂眼:砂眼是指铸件表面或内部的突起或凹陷。
砂眼的形成通常是由于铸型材料的不均匀收缩或砂芯的移位引起的。
砂眼会影响到产品的外观和尺寸精度。
为了避免砂眼的产生,可以通过优化铸型和砂芯的设计,控制铸型材料的收缩率,以及合理调整浇注温度和速度来解决这个问题。
4. 缩松:缩松是指铸件中存在的细小裂纹。
缩松会降低铸件的强度和韧性,使其易于断裂。
缩松的形成通常是由于金属液体在凝固过程中体积收缩而引起的。
为了避免缩松的产生,可以通过增加浇注温度和压力,以及优化铸型设计和浇注系统来减少金属液体的收缩。
5. 夹杂物:夹杂物是指铸件中存在的杂质和非金属物质。
夹杂物会降低铸件的强度和耐久性,导致其易于断裂。
夹杂物的形成通常是由于金属液体中的杂质和氧化物未能完全排除而引起的。
为了避免夹杂物的产生,可以通过改进金属液体的净化和过滤系统,以及优化浇注工艺和铸型设计来减少夹杂物的形成。
铸造过程中常见的缺陷包括气孔、疏松、砂眼、缩松和夹杂物。
这些缺陷会影响到铸件的质量和性能,因此在铸造过程中需要采取相应的措施来预防和解决这些问题。
铸造过程中常见的几种缺陷
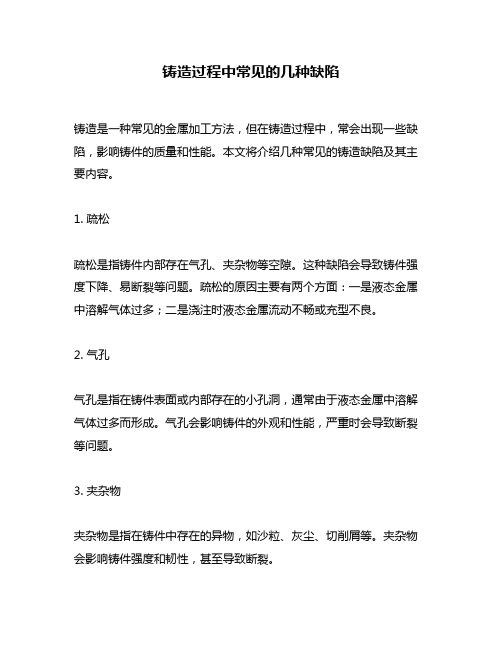
铸造过程中常见的几种缺陷
铸造是一种常见的金属加工方法,但在铸造过程中,常会出现一些缺陷,影响铸件的质量和性能。
本文将介绍几种常见的铸造缺陷及其主要内容。
1. 疏松
疏松是指铸件内部存在气孔、夹杂物等空隙。
这种缺陷会导致铸件强度下降、易断裂等问题。
疏松的原因主要有两个方面:一是液态金属中溶解气体过多;二是浇注时液态金属流动不畅或充型不良。
2. 气孔
气孔是指在铸件表面或内部存在的小孔洞,通常由于液态金属中溶解气体过多而形成。
气孔会影响铸件的外观和性能,严重时会导致断裂等问题。
3. 夹杂物
夹杂物是指在铸件中存在的异物,如沙粒、灰尘、切削屑等。
夹杂物会影响铸件强度和韧性,甚至导致断裂。
4. 热裂纹
热裂纹是指在冷却过程中,由于金属内部应力过大而导致的裂纹。
热裂纹通常发生在厚度不均匀的铸件部位,如壁厚变化处、边缘等。
5. 缩孔
缩孔是指铸件内部存在的凹陷或空洞,通常由于液态金属在凝固过程中收缩而形成。
缩孔会影响铸件的强度和密封性能。
为避免上述铸造缺陷的出现,可以采取以下措施:
1. 控制液态金属中溶解气体含量,如采用真空熔炼等方法。
2. 优化浇注系统设计,确保液态金属流动畅通。
3. 严格控制充型质量,如采用振动充型、压力充型等方法。
4. 控制冷却速度和温度梯度,避免产生应力过大的情况。
5. 优化铸件结构设计,避免壁厚变化过大、边角过于尖锐等情况。
总之,在铸造过程中要注意各个环节的质量控制和优化设计,以确保铸件质量和性能。
铸件的常见缺陷及其检验

加强生产管理
总结词
强化生产过程中的质量控制和安全管理。
详细描述
建立完善的质量控制体系和安全管理制度,确保生产过程中的各个环节都得到有效的监 控和管理,防止缺陷的产生。
采用先进的铸造技术
总结词
积极引进和应用先进的铸造技术,提高铸件 质量。
详细描述
关注铸造技术的最新发展动态,积极引进和 应用先进的铸造技术,如3D打印技术、精 密铸造等,提高铸件的质量和性能。
外观影响
铸件表面缺陷影响产品美观,降低产品档次。
02
常见铸件缺陷类型
孔洞类缺陷
总结词
孔洞类缺陷是铸件中常见的缺陷之一,通常表现 为铸件内部或表面出现孔洞、气孔、缩孔等现象 。
检测方法
孔洞类缺陷可以通过X射线检测、超声波检测、磁 粉检测等方法进行检测。这些方法可以有效地检 测出铸件内部的孔洞和气孔,为后续的修复工作 提供依据。
产生原因
材料因素
原材料质量不佳、杂质含量高、金属材料的热膨胀系 数不匹配等。
工艺因素
铸造工艺不合理、浇注系统设计不当、冷却速度控制 不准确等。
环境因素
生产环境湿度过高、车间温度波动大、空气流通不畅 等。
对铸件质量的影响
功能影响
铸件缺陷可能导致铸件性能下降,如强度、耐磨 性、耐腐蚀性等。
安全影响
对于关键部件或承载件,铸件缺陷可能导致安全 事故,如断裂、失效等。
裂纹类缺陷的检测方法有多 种,如目视检测、渗透检测 、超声波检测等。这些方法 可以有效地检测出铸件中的 裂纹和热裂纹,为后续的修 复工作提供依据。
对于裂纹类缺陷,常用的修 复方法有焊接、打补丁、填 充等。根据铸件的具体情况 和缺陷程度,选择合适的修 复方法,确保铸件的结构强 度和使用寿命。
铸造常见的缺陷及解决办法

铸造常见的缺陷及解决办法铸造是一种常见的加工方法,用于制造大量金属和非金属产品。
然而,铸造过程中常常会出现一些缺陷,这些缺陷会影响铸件的质量和性能。
本文将介绍几种常见的铸造缺陷及解决办法。
气孔气孔是指在铸件内部或表面上出现的气泡。
这些气泡会影响铸件的强度和密封性能。
气孔的出现原因可能是铸造温度或压力不足,或是砂模中的水分蒸发不充分。
解决气孔的问题,需要改变铸造过程中的温度、压力或砂模中的水分含量。
另外,选择合适的金属合金也是避免气孔出现的重要因素,例如在铸造铝合金时,可以使用特殊的铝合金材料来降低气孔的出现。
毛刺毛刺是指在铸件表面上出现的细小凸起物。
这些毛刺会影响铸件的表面光滑度和密封性能。
毛刺的出现原因可能是砂模中的杂质、铸件表面的耗损或金属液体的流动不充分。
解决毛刺的问题,需要在铸造过程中施加足够的压力和控制金属液体的流动速度。
另外,使用高品质的砂模和特殊的涂料或添加剂也可以有效地减少毛刺的出现。
缩孔缩孔是指在铸件内部或表面上出现的缺陷。
这些缺陷会影响铸件的强度和密封性能。
缩孔的出现原因可能是铸造温度不足、金属合金不均匀、砂模中的气包或铸造中的氧化物等。
解决缩孔的问题需要改变铸造温度、金属合金中元素的成分、砂模的密度和金属液体中的氧化物含量。
此外,在铸造过程中添加特殊的合金和增量剂也可以有效地减少缩孔的出现。
内孔内孔是指在铸件内部出现的缺陷,这些缺陷会影响铸件的强度和密封性能。
内孔的出现原因可能是砂模泥中的气孔或金属液体中的气泡。
解决内孔的问题需要改变铸造过程中的气压和金属液体的流动速度。
此外,在铸造过程中添加特殊的漏铸剂和降泡剂也可以有效地减少内孔的出现。
总之,铸造过程中出现的缺陷会严重影响铸件的质量和性能。
通过改变铸造过程中的温度、压力和砂模的含水量,以及添加特殊的金属合金、涂料、合金和漏铸剂等,可以有效地减少这些缺陷的出现。
因此,在铸造过程中应该尽可能地避免出现这些问题,并采取合适的方法来解决这些问题。
铝合金针孔铸造缺陷及原因

铝合金针孔铸造缺陷及原因铝合金针孔铸造缺陷及原因针孔是精密铝合金铸件中常见的一种缺陷,也是最为严重的缺陷之一。
针孔会影响铝合金铸件的使用寿命,降低其安全性能,同时也会导致材料的能力值下降。
本文将分析铝合金针孔铸造缺陷及其原因。
一、铝合金针孔的基本特征针孔是铝合金铸造中常见的一种缺陷,其具有以下基本特征:1. 针孔通常呈球形或矩形,其大小从几微米到几毫米不等。
2. 针孔位置主要集中在表面、灰口、壳口以及热通道。
3. 针孔的形态以及数量与铝合金铸件的造型、浇注方式、模具设计、铝合金成分以及熔炼过程中的气体、金属温度等因素有关。
二、铝合金针孔形成原因铝合金针孔是由多种原因导致的,主要包括以下几个方面:1. 铸件设计不当铸件设计不当是针孔等铝合金缺陷的主要原因之一。
如果铸件的几何形状不合理,壁厚过厚、凸角处太尖等,将会导致铝合金的成分难以很好地流向模具的各个部位,造成气泡和针孔。
2. 浇注参数失控铝合金的浇注形式和参数变化也是针孔形成的原因之一。
铸造过程中,如果铝水、模具温度及其它浇注参数受到不良因素的影响,可能会引发针孔缺陷的形成。
3. 模具设计不合理铸模的设计和制造质量是铸造质量的保证。
如果模具设计不合理、制造不良,如针部分设计不当、顶针多、模具表面粗糙、钢质等,都将造成铝合金浇注时产生气泡及针孔。
4. 铝合金成分不稳定铝合金成分的不稳定性也是针孔缺陷形成的原因之一。
如果铝合金中含有过多的水分、氧气或其他杂质,将会在熔融过程中挥发产生气泡。
5. 外部环境因素熔炼过程中的外部环境因素,如风速、压力、温度、湿度等,将会对铝合金的熔融过程产生影响,可能导致针孔的产生。
三、纠正铝合金针孔优点方法1. 优化铸造工艺,在浇注前充分除去铝合金表面氧化物及其它杂质。
2. 采用焊补方法消除函数。
3. 在铝合金中添加少量处理剂,如NaCl、TiH2等,将有助于消除铸造中产生的气泡。
4. 采用合适的温度控制,在铝合金熔炼的过程中保持温度的稳定性,并且避免熔池底部结渣。
铸造缺陷及其对策书

铸造缺陷及其对策书(实用版)目录一、铸造缺陷的概述二、铸造缺陷的种类三、铸造缺陷产生的原因四、铸造缺陷的对策五、结论正文一、铸造缺陷的概述铸造缺陷是指在铸造过程中,由于各种原因导致的铸件不符合设计要求的缺陷。
铸造缺陷不仅会影响铸件的性能和质量,还会增加生产成本,甚至可能导致设备损坏和安全事故。
因此,研究铸造缺陷及其对策对于提高铸件质量具有重要意义。
二、铸造缺陷的种类铸造缺陷种类繁多,根据缺陷的性质和形态,可以分为以下几类:1.表面缺陷:如砂眼、气孔、麻点、裂纹等。
2.内部缺陷:如缩孔、缩松、夹杂、偏析等。
3.形状缺陷:如变形、歪曲、尺寸偏差等。
4.成分缺陷:如碳、硅、锰等元素含量偏离设计要求。
5.组织缺陷:如晶粒粗大、组织不均匀、白口组织等。
三、铸造缺陷产生的原因1.原材料方面:如铸造砂质量差、石英砂含泥量过高、熔炼过程中元素烧损等。
2.工艺方面:如熔炼温度过高或过低、浇注速度过快或过慢、浇注过程中气泡产生等。
3.设备方面:如砂箱振动不均匀、浇注器设计不合理、炉子温度控制不准确等。
4.操作方面:如砂型制作不规范、合箱时压实不均匀、浇注高度不够等。
四、铸造缺陷的对策1.选择优质的原材料,提高铸型的质量。
2.优化熔炼工艺,控制熔炼温度、元素烧损和气体含量。
3.改进浇注工艺,合理控制浇注速度、压注压力和浇注高度。
4.完善设备设施,提高设备的精度和稳定性。
5.加强操作培训,提高工人的操作技能和质量意识。
五、结论通过对铸造缺陷及其对策的研究,可以降低铸件的缺陷率,提高铸件的质量和性能。
铸造质量缺陷知识点总结
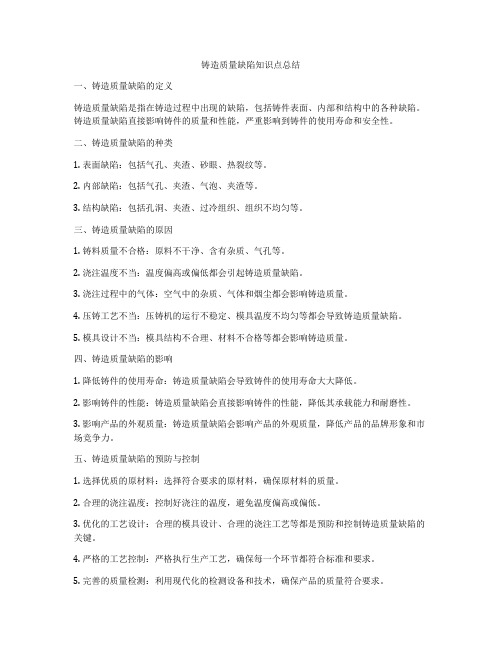
一、铸造质量缺陷的定义铸造质量缺陷是指在铸造过程中出现的缺陷,包括铸件表面、内部和结构中的各种缺陷。
铸造质量缺陷直接影响铸件的质量和性能,严重影响到铸件的使用寿命和安全性。
二、铸造质量缺陷的种类1. 表面缺陷:包括气孔、夹渣、砂眼、热裂纹等。
2. 内部缺陷:包括气孔、夹渣、气泡、夹渣等。
3. 结构缺陷:包括孔洞、夹渣、过冷组织、组织不均匀等。
三、铸造质量缺陷的原因1. 铸料质量不合格:原料不干净、含有杂质、气孔等。
2. 浇注温度不当:温度偏高或偏低都会引起铸造质量缺陷。
3. 浇注过程中的气体:空气中的杂质、气体和烟尘都会影响铸造质量。
4. 压铸工艺不当:压铸机的运行不稳定、模具温度不均匀等都会导致铸造质量缺陷。
5. 模具设计不当:模具结构不合理、材料不合格等都会影响铸造质量。
四、铸造质量缺陷的影响1. 降低铸件的使用寿命:铸造质量缺陷会导致铸件的使用寿命大大降低。
2. 影响铸件的性能:铸造质量缺陷会直接影响铸件的性能,降低其承载能力和耐磨性。
3. 影响产品的外观质量:铸造质量缺陷会影响产品的外观质量,降低产品的品牌形象和市场竞争力。
五、铸造质量缺陷的预防与控制1. 选择优质的原材料:选择符合要求的原材料,确保原材料的质量。
2. 合理的浇注温度:控制好浇注的温度,避免温度偏高或偏低。
3. 优化的工艺设计:合理的模具设计、合理的浇注工艺等都是预防和控制铸造质量缺陷的关键。
4. 严格的工艺控制:严格执行生产工艺,确保每一个环节都符合标准和要求。
5. 完善的质量检测:利用现代化的检测设备和技术,确保产品的质量符合要求。
1. 热处理修复:利用热处理技术对铸件进行修复,提高其结构和性能。
2. 焊接修复:对于一些大型铸件,可以使用焊接技术对其进行修复。
3. 精密加工:对于一些表面缺陷较大的铸件,可以利用精密加工技术进行修复。
4. 重新铸造:对于一些严重的缺陷,可以考虑重新铸造。
七、发展趋势随着科学技术的不断进步,铸造质量缺陷的预防和控制技术也在不断提高。
铸造缺陷总结汇报

铸造缺陷总结汇报铸造是一种常见的制造工艺,用于制造各种金属制品。
然而,在铸造过程中,常常会出现一些缺陷,这些缺陷会对产品的质量和性能产生不良影响。
因此,及时总结和汇报铸造缺陷是非常重要的,下面我们来详细讨论一下。
首先,铸造缺陷的种类非常多样。
常见的铸造缺陷主要包括气孔、夹杂物、缩孔、疏松、铸钢、铸锻件表面缺陷等。
这些缺陷的产生原因可以是多方面的,比如金属液内含的气体未能完全排出,金属液流动不畅导致夹杂物的进入,铸型砂中水分过多导致疏松缩敛等等。
其次,针对不同种类的铸造缺陷,需要采取相应的解决方法。
对于气孔和夹杂物来说,需要通过提高浇注温度和浇注速度来减少气体的溶解度和夹杂物的进入;对于缩孔和疏松来说,主要应采用合适的浇注系统和优化固化过程,以提高金属液的流动性和减少气体和夹杂物的进入。
至于铸钢和铸锻件表面的缺陷,则需要采用相应的表面处理方法,提高表面的光洁度和平整度。
此外,铸造缺陷的发生与操作人员的技术水平和操作规范密切相关。
因此,在铸造过程中,必须加强操作人员的培训和管理,提高他们的技能水平和操作规范,从而减少铸造缺陷的发生。
同时,还需要加强对原材料的检验和质量控制,以确保原材料的质量符合要求,减少缺陷的发生。
最后,为了及时发现和解决铸造缺陷,必须建立起完善的缺陷检测和处理体系。
在铸造过程中,需要定期对铸造产品进行检测,及时发现并处理缺陷。
对于已经发生的缺陷,需要采取相应的补救措施,以保证产品的质量和性能。
此外,还需要建立起缺陷统计和分析的机制,对不同缺陷的发生频率和原因进行统计和分析,以便进一步改进铸造工艺和提高产品质量。
综上所述,铸造缺陷的总结和汇报对于保证产品质量和提高铸造工艺至关重要。
只有及时总结和汇报铸造缺陷,才能不断改进铸造工艺,提高产品质量,推动企业的发展。
因此,我们应该重视铸造缺陷的问题,加强对其的研究和解决,为企业的可持续发展做出贡献。
铸造缺陷及防止方法

铸造缺陷及防止方法铸造是一种常用的金属加工工艺,可以将熔化的金属倒入铸型中,通过冷却凝固形成所需形状的金属制品。
然而,在铸造过程中,由于多种因素的影响,往往会导致一些缺陷出现在铸件上。
这些缺陷可能会降低铸件的质量和性能,因此有必要研究和防止铸造缺陷的发生。
一、常见的铸造缺陷类型1.气孔:气孔是铸造缺陷中最常见的一种,它是由金属液中残留的气体在凝固过程中形成的小空洞。
气孔会降低铸件的强度和密封性能,并且可能导致泄漏的发生。
2.夹杂物:夹杂物是指固体杂质或其他金属液滴等不溶于基体金属的颗粒物质。
夹杂物会引起局部应力集中和腐蚀等问题,从而降低铸件的耐蚀性和机械性能。
3.砂眼:砂眼是指铸件表面上的凹陷或孔洞,主要由于铸型中的砂粒脱落或重叠造成。
砂眼会影响铸件的外观和尺寸精度,降低其使用价值。
4.缩孔:缩孔是铸件内部或表面上的凹陷,它是由于金属凝固过程中产生的体积收缩引起的。
缩孔会降低铸件的强度和韧性,增加冲击和断裂的风险。
二、铸造缺陷的防止方法1.优化铸造工艺:通过合理设计铸造工艺参数,如浇注温度、浇注速度、浇注方式等,可以减少金属液中的气体吸收,并降低气孔和夹杂物的形成。
2.提高模具质量:优质的模具能够提供良好的液态金属充填条件,并且减少金属液和砂模接触引起的气体和杂质污染。
因此,选择高质量的模具材料和加工工艺非常重要。
3.合理选择铸造材料:根据铸件的要求选择适合的铸造材料,如选用低气性和低杂质含量的金属,可以减少铸造缺陷的发生。
4.加强铸造设备维护:定期检查和维护铸造设备,特别是容易产生污染和损坏的部件,可以减少外来杂质和缺陷的产生。
5.实施严格的质量控制和检验:建立科学的质量控制体系,制定详细的工艺规范和操作规程,严格按照要求进行检验和记录,及时发现和解决潜在的缺陷问题。
总结:铸造缺陷是铸件制造过程中经常面临的问题,但通过合理的措施和方法,可以有效地预防和减少铸造缺陷的发生。
优化铸造工艺、提高模具质量、合理选择铸造材料、加强设备维护以及实施严格的质量控制和检验,是有效预防铸造缺陷的关键。
铸造缺陷及其对策书

铸造缺陷及其对策书一、铸造缺陷的类型与影响1.缺陷类型概述铸造过程中,铸件可能出现的缺陷种类繁多,主要包括裂纹、气孔、夹渣、变形、缩孔等。
这些缺陷不仅影响铸件的外观质量,还会对其性能产生不良影响。
2.缺陷对铸件性能的影响铸造缺陷会对铸件的强度、韧性、耐磨性等性能造成负面影响。
例如,裂纹会导致铸件在使用过程中出现断裂;气孔会使铸件的强度降低;夹渣会使铸件的内部性能不均匀。
二、铸造缺陷的成因与分析1.原材料问题原材料的质量对铸件的缺陷产生具有重要影响。
金属原材料中的有害物质、非金属杂质、气体含量等都会导致铸件出现缺陷。
2.铸造工艺问题铸造工艺参数设置不合理、充型速度过快或过慢、冷却速度不适等都会导致铸件产生缺陷。
3.模具与设备问题模具质量不佳、磨损严重、设备精度不足等都会对铸件的质量产生不良影响。
4.操作问题操作过程中,工人技术水平低、操作不当、责任心不强等也是导致铸件缺陷的重要原因。
三、对策与改进措施1.选用优质原材料为确保铸件质量,应选用优质金属原材料,并对原材料进行严格检测,控制有害物质和杂质的含量。
2.优化铸造工艺根据铸件的结构和性能要求,合理设置铸造工艺参数,提高充型速度和冷却速度,以减少缺陷产生。
3.提高模具与设备质量定期检查和维修模具与设备,确保其精度和可靠性。
同时,加强工人的技术培训,提高操作水平。
4.加强操作培训与管理加强操作人员的培训与管理,提高其技术水平和责任心,降低人为因素导致的缺陷。
四、缺陷预防与控制方法1.完善质量管理体系建立健全质量管理体系,确保铸件生产过程中的质量控制。
2.强化过程控制加强对生产过程的监控,及时发现和处理问题。
3.检测与评估技术采用先进的检测与评估技术,对铸件进行全面的质量检测,确保铸件质量达到要求。
4.故障排查与处理针对出现的铸件缺陷,进行故障排查,找出原因并采取相应措施进行处理。
五、案例分析与总结1.案例一:铸件裂纹缺陷分析与改进通过对裂纹缺陷的成因分析,发现原材料中有害物质含量过高、铸造工艺参数设置不合理等问题。
浅谈铸造缺陷对铸件的影响
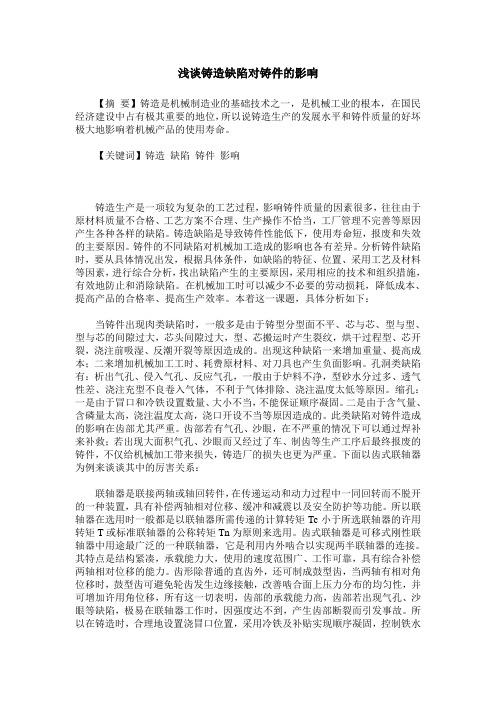
浅谈铸造缺陷对铸件的影响【摘要】铸造是机械制造业的基础技术之一,是机械工业的根本,在国民经济建设中占有极其重要的地位,所以说铸造生产的发展水平和铸件质量的好坏极大地影响着机械产品的使用寿命。
【关键词】铸造缺陷铸件影响铸造生产是一项较为复杂的工艺过程,影响铸件质量的因素很多,往往由于原材料质量不合格、工艺方案不合理、生产操作不恰当,工厂管理不完善等原因产生各种各样的缺陷。
铸造缺陷是导致铸件性能低下,使用寿命短,报废和失效的主要原因。
铸件的不同缺陷对机械加工造成的影响也各有差异。
分析铸件缺陷时,要从具体情况出发,根据具体条件,如缺陷的特征、位置、采用工艺及材料等因素,进行综合分析,找出缺陷产生的主要原因,采用相应的技术和组织措施,有效地防止和消除缺陷。
在机械加工时可以减少不必要的劳动损耗,降低成本、提高产品的合格率、提高生产效率。
本着这一课题,具体分析如下:当铸件出现肉类缺陷时,一般多是由于铸型分型面不平、芯与芯、型与型、型与芯的间隙过大,芯头间隙过大,型、芯搬运时产生裂纹,烘干过程型、芯开裂,浇注前吸湿、反潮开裂等原因造成的。
出现这种缺陷一来增加重量、提高成本;二来增加机械加工工时、耗费原材料、对刀具也产生负面影响。
孔洞类缺陷有:析出气孔、侵入气孔、反应气孔,一般由于炉料不净,型砂水分过多、透气性差、浇注充型不良卷入气体,不利于气体排除、浇注温度太低等原因。
缩孔:一是由于冒口和冷铁设置数量、大小不当,不能保证顺序凝固。
二是由于含气量、含磷量太高,浇注温度太高,浇口开设不当等原因造成的。
此类缺陷对铸件造成的影响在齿部尤其严重。
齿部若有气孔、沙眼,在不严重的情况下可以通过焊补来补救;若出现大面积气孔、沙眼而又经过了车、制齿等生产工序后最终报废的铸件,不仅给机械加工带来损失,铸造厂的损失也更为严重。
下面以齿式联轴器为例来谈谈其中的厉害关系:联轴器是联接两轴或轴回转件,在传递运动和动力过程中一同回转而不脱开的一种装置,具有补偿两轴相对位移、缓冲和减震以及安全防护等功能。
铸造缺陷对镁合金压铸件性能的影响
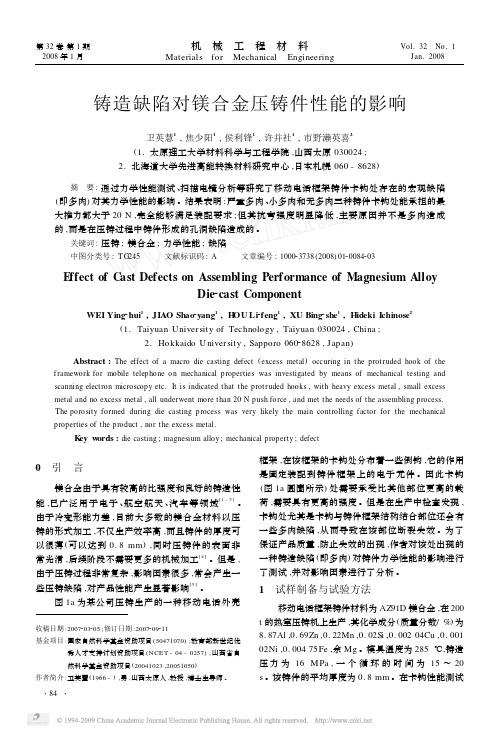
铸造缺陷对镁合金压铸件性能的影响卫英慧1,焦少阳1,侯利锋1,许并社1,市野濑英喜2(1.太原理工大学材料科学与工程学院,山西太原030024;2.北海道大学先进高能转换材料研究中心,日本札幌060-8628)摘 要:通过力学性能测试、扫描电镜分析等研究了移动电话框架铸件卡钩处存在的宏观缺陷(即多肉)对其力学性能的影响。
结果表明:严重多肉、小多肉和无多肉三种铸件卡钩处能承担的最大推力都大于20N ,完全能够满足装配要求;但其抗弯强度明显降低,主要原因并不是多肉造成的,而是在压铸过程中铸件形成的孔洞缺陷造成的。
关键词:压铸;镁合金;力学性能;缺陷中图分类号:T G 245 文献标识码:A 文章编号:100023738(2008)0120084203E ffect of C ast Defects on Assembling Performance of Magnesium AlloyDie 2cast ComponentWEI Ying 2hui 1,JIAO Shao 2yang 1,H OU Li 2feng 1,XU Bing 2she 1,Hideki Ichinose 2(1.Taiyuan University of Technology ,Taiyuan 030024,China ;2.Hokkaido U niversity ,Sapporo 06028628,J apan )Abstract :The effect of a macro die casting defect (excess metal )occuring in the protruded hook of theframework for mobile telephone on mechanical properties was investigated by means of mechanical testing and scanning electron microscopy etc.It is indicated that the protruded hooks ,with heavy excess metal ,small excess metal and no excess metal ,all underwent more than 20N push force ,and met the needs of the assembling process.The porosity formed during die casting process was very likely the main controlling factor for the mechanical properties of the product ,nor the excess metal.K ey w ords :die casting ;magnesium alloy ;mechanical property ;defect0 引 言镁合金由于具有较高的比强度和良好的铸造性能,已广泛用于电子、航空航天、汽车等领域[1-3]。
- 1、下载文档前请自行甄别文档内容的完整性,平台不提供额外的编辑、内容补充、找答案等附加服务。
- 2、"仅部分预览"的文档,不可在线预览部分如存在完整性等问题,可反馈申请退款(可完整预览的文档不适用该条件!)。
- 3、如文档侵犯您的权益,请联系客服反馈,我们会尽快为您处理(人工客服工作时间:9:00-18:30)。
浅谈铸造缺陷对铸件的影响
【摘要】铸造是机械制造业的基础技术之一,是机械工业的根本,在国民经济建设中占有极其重要的地位,所以说铸造生产的发展水平和铸件质量的好坏极大地影响着机械产品的使用寿命。
【关键词】铸造缺陷铸件影响
铸造生产是一项较为复杂的工艺过程,影响铸件质量的因素很多,往往由于原材料质量不合格、工艺方案不合理、生产操作不恰当,工厂管理不完善等原因产生各种各样的缺陷。
铸造缺陷是导致铸件性能低下,使用寿命短,报废和失效的主要原因。
铸件的不同缺陷对机械加工造成的影响也各有差异。
分析铸件缺陷时,要从具体情况出发,根据具体条件,如缺陷的特征、位置、采用工艺及材料等因素,进行综合分析,找出缺陷产生的主要原因,采用相应的技术和组织措施,有效地防止和消除缺陷。
在机械加工时可以减少不必要的劳动损耗,降低成本、提高产品的合格率、提高生产效率。
本着这一课题,具体分析如下:
当铸件出现肉类缺陷时,一般多是由于铸型分型面不平、芯与芯、型与型、型与芯的间隙过大,芯头间隙过大,型、芯搬运时产生裂纹,烘干过程型、芯开裂,浇注前吸湿、反潮开裂等原因造成的。
出现这种缺陷一来增加重量、提高成本;二来增加机械加工工时、耗费原材料、对刀具也产生负面影响。
孔洞类缺陷有:析出气孔、侵入气孔、反应气孔,一般由于炉料不净,型砂水分过多、透气性差、浇注充型不良卷入气体,不利于气体排除、浇注温度太低等原因。
缩孔:一是由于冒口和冷铁设置数量、大小不当,不能保证顺序凝固。
二是由于含气量、含磷量太高,浇注温度太高,浇口开设不当等原因造成的。
此类缺陷对铸件造成的影响在齿部尤其严重。
齿部若有气孔、沙眼,在不严重的情况下可以通过焊补来补救;若出现大面积气孔、沙眼而又经过了车、制齿等生产工序后最终报废的铸件,不仅给机械加工带来损失,铸造厂的损失也更为严重。
下面以齿式联轴器为例来谈谈其中的厉害关系:
联轴器是联接两轴或轴回转件,在传递运动和动力过程中一同回转而不脱开的一种装置,具有补偿两轴相对位移、缓冲和减震以及安全防护等功能。
所以联轴器在选用时一般都是以联轴器所需传递的计算转矩Tc小于所选联轴器的许用转矩T或标准联轴器的公称转矩Tn为原则来选用。
齿式联轴器是可移式刚性联轴器中用途最广泛的一种联轴器,它是利用内外啮合以实现两半联轴器的连接。
其特点是结构紧凑,承载能力大,使用的速度范围广、工作可靠,具有综合补偿两轴相对位移的能力。
齿形除普通的直齿外,还可制成鼓型齿,当两轴有相对角位移时,鼓型齿可避免轮齿发生边缘接触,改善啮合面上压力分布的均匀性,并可增加许用角位移,所有这一切表明,齿部的承载能力高,齿部若出现气孔、沙眼等缺陷,极易在联轴器工作时,因强度达不到,产生齿部断裂而引发事故。
所以在铸造时,合理地设置浇冒口位置,采用冷铁及补贴实现顺序凝固,控制铁水
碳当量、含磷量、降低含气量等方法有效地预防缩孔;控制充型速度不易过高,充型要平稳,型、芯排气畅通、设出气冒口、炉料干净,熔炼不要过分氧化,提高出炉温度等预防气孔的发生。
经过一系列的前期工作,浇注出的铸件经过调质处理、机械加工、齿部淬火等热处理工艺,最终才能达到使用要求。
另外,铸造缺陷的种类还有很多,造成铸造缺陷的原因也各有差异,缺陷对铸件造成的影响也各有不同。
作为一个专业技术人员一定要认清自己所处的位置,知道自己应该做什么、怎样做。
要了解客户需求并进行新产品的技术开发工艺工作,现场技术服务和质量分析,协助质量部解决相关质量问题。
我国铸件产量已连续七年稳坐世界头把交椅,成为铸造大国。
据2005年第12期《Moder Casting》杂志公布的统计资料,2004年我国逐渐产量为2242万吨,比美国和日本的总和还要多,比2003年增长23.6%,可是总体来说,我们所生产的铸件还属于低附加值产品。
中国要从一个铸造大国转变成铸造强国,必须首先设法提升铸件质量和技术附加值。
解决这个问题,就需要有:(1)铸造相关的专业学历,丰富的工作经验;(2)精通铸造工艺、模具、工装设计;(3)会使用铸造工艺协助设计软件;(4)熟悉铸造相关的质量体系和质量方法;(5)积极向上,有强烈的责任心,有创新能力。
我们要想做大、做强,必须从一点一滴的小事做起,从产生铸件缺陷的细微小处做起,严把质量关,提升所在企业的知名度,我们才能立足市场,成为时代的骄傲。
《铸造缺陷的产生对铸件造成的影响》这一课题的研究,还有待我们专业技术人员去做进一步的探讨。
(作者单位:河北省邯郸市轧钢备件制造厂)。