(完整版)石墨电极
石墨电极

石墨电极石墨电极(graphite electrode)以石油焦、沥青焦为颗粒料,煤沥青为黏结剂,经过}昆捏、成型、焙烧、石墨化和机械加工而制成的一种耐高温的石墨质导电材料。
石墨电极是电炉炼钢的重要高温导电材料,通过石墨电极向电炉输入电能,利用电极端部和炉料之间引发电弧产生的高温为热源,使炉料熔化进行炼钢,其他一些电冶炼或电解设备也常使用石墨电极为导电材料。
2000年全世界消耗石墨电极100万t左右,中国2000年消耗石墨电极25万t左右。
利用石墨电极优良的物理化学性能,在其他工业部门中也有广泛的用途,以生产石墨电极为主要品种的炭素制品工业已经成为当代原材料工业的重要组成部门。
简史早在1810年汉佛莱•戴维(Humphry Davy)利用木炭制成通电后能产生电弧的炭质电极,开辟了使用炭素材料作为高温导电电极的广阔前景,1846年斯泰特(Stair)和爱德华(Edwards)用焦炭粉及蔗糖混合后加压成型,并在高温下焙烧从而制造出另一种炭质电极,再将这种炭质电极浸在浓糖水中以提高其体积密度,他们获得了生产这种电极的专利权。
1877年美国克利夫兰(Cleveland)的勃洛希(C.F.Brush)和劳伦斯(wrence)采用煅烧过的石油焦研制低灰分的炭质电极获得成功。
1899年普利查德(O.G.Pritchard)首先报道了用锡兰天然石墨为原料制造天然石墨电极的方法。
1896年卡斯特纳(H.Y.Gastner)获得了使用电力将炭质电极直接通电加热到高温,而生产出比天然石墨电极使用性能更好的人造石墨电极的专利权。
1897年美国金刚砂公司(Carborundum Co.)的艾奇逊(E.G.Acheson)在生产金刚砂的电阻炉中制造了第一批以石油焦为原料的人造石墨电极,产品规格为22mm×32m mX380mm,这种人造石墨电极当时用于电化学工业生产烧碱,在此基础上设计的“艾奇逊”石墨化炉将由石油焦生产的炭质电极及少量电阻料(冶金焦粒)构成“炉芯电阻”,通电后产生高温,使由石油焦制成的炭质电极在高温下“石墨化”而获得人造石墨电极。
石墨电极的生产工艺流程和质量指标的及消耗原理知识讲解

石墨电极的生产工艺流程和质量指标的及消耗原理目录一、石墨电极的原料及制造工艺二、石墨电极的质量指标三、电炉炼钢简介及石墨电极的消耗机理石墨电极的原料及制造工艺●石墨电极是采用石油焦、针状焦为骨料,煤沥青为粘结剂,经过混捏、成型、焙烧、浸渍、石墨化、机械加工等一系列工艺过程生产出来的一种耐高温石墨质导电材料。
石墨电极是电炉炼钢的重要高温导电材料,通过石墨电极向电炉输入电能,利用电极端部和炉料之间引发电弧产生的高温作为热源,使炉料熔化进行炼钢。
其他一些冶炼黄磷、工业硅、磨料等材料的矿热炉也用石墨电极作为导电材料。
利用石墨电极优良而特殊的物理化学性能,在其他工业部门也有广泛的用途。
生产石墨电极的原料有石油焦、针状焦和煤沥青●石油焦是石油渣油、石油沥青经焦化后得到的可燃固体产物。
色黑多孔,主要元素为碳,灰分含量很低,一般在0.5%以下。
石油焦属于易石墨化炭一类,石油焦在化工、冶金等行业中有广泛的用途,是生产人造石墨制品及电解铝用炭素制品的主要原料。
●石油焦按热处理温度区分可分为生焦和煅烧焦两种,前者由延迟焦化所得的石油焦,含有大量的挥发分,机械强度低,煅烧焦是生焦经煅烧而得。
中国多数炼油厂只生产生焦,煅烧作业多在炭素厂内进行。
●石油焦按硫分的高低区分,可分为高硫焦(含硫1.5%以上)、中硫焦(含硫0.5%-1.5%)、和低硫焦(含硫0.5%以下)三种,石墨电极及其它人造石墨制品生产一般使用低硫焦生产。
●针状焦是外观具有明显纤维状纹理、热膨胀系数特别低和很容易石墨化的一种优质焦炭,焦块破裂时能按纹理分裂成细长条状颗粒(长宽比一般在1.75以上),在偏光显微镜下可观察到各向异性的纤维状结构,因而称之为针状焦。
●针状焦物理机械性质的各向异性十分明显, 平行于颗粒长轴方向具有良好的导电导热性能,热膨胀系数较低,在挤压成型时,大部分颗粒的长轴按挤出方向排列。
因此,针状焦是制造高功率或超高功率石墨电极的关键原料,制成的石墨电极电阻率较低,热膨胀系数小,抗热震性能好。
石墨电极成分表

石墨电极成分表
石墨电极是用于电弧炉中熔炼金属的关键材料之一。
它通常由天然石墨和人工石墨组成,具有高温稳定性和导电性能。
以下是石墨电极的一般成分表,实际产品的成分可能有所不同,具体取决于生产工艺和应用领域:
1.碳素(Carbon):石墨电极的主要成分是碳,通常以石墨的形
式存在。
碳素是其导电性能的主要来源。
2.灰分(Ash):灰分是指石墨电极中不挥发的无机物残留部分。
它的含量会影响电极的纯度和导电性。
3.挥发分(Volatile Matter):电极中的挥发性成分,包括一些在
高温下挥发的有机物。
挥发分的含量会影响电极的稳定性。
4.硫含量(Sulfur):硫是一种杂质,其含量需要控制在较低水平,
以防止在高温下产生硫酸等有害气体。
5.氧含量(Oxygen):氧是另一个影响电极性能的杂质。
高氧含
量可能降低电极的导电性能。
6.密度(Density):电极的密度影响其机械性能和使用寿命。
7.导电系数(Electrical Conductivity):衡量电极导电性能的指
标,高导电系数通常表示较好的导电性能。
8.抗压强度(Compressive Strength):衡量电极在高温和高压
环境下的机械稳定性。
9.抗折强度(Flexural Strength):衡量电极在弯曲应力下的抗
性。
需要注意的是,石墨电极的成分可以根据不同的生产工艺和应用领域进行调整。
在高温熔炼金属的过程中,电极会受到严重的热应力和化学腐蚀,因此其性能要求较高。
生产商通常会根据特定的工艺需求和用户要求定制电极产品。
石墨电极技术参数介绍
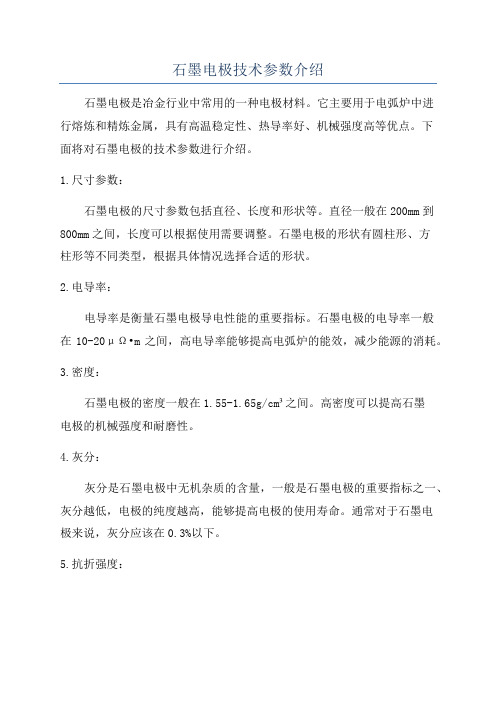
石墨电极技术参数介绍石墨电极是冶金行业中常用的一种电极材料。
它主要用于电弧炉中进行熔炼和精炼金属,具有高温稳定性、热导率好、机械强度高等优点。
下面将对石墨电极的技术参数进行介绍。
1.尺寸参数:石墨电极的尺寸参数包括直径、长度和形状等。
直径一般在200mm到800mm之间,长度可以根据使用需要调整。
石墨电极的形状有圆柱形、方柱形等不同类型,根据具体情况选择合适的形状。
2.电导率:电导率是衡量石墨电极导电性能的重要指标。
石墨电极的电导率一般在10-20μΩ•m之间,高电导率能够提高电弧炉的能效,减少能源的消耗。
3.密度:石墨电极的密度一般在1.55-1.65g/cm³之间。
高密度可以提高石墨电极的机械强度和耐磨性。
4.灰分:灰分是石墨电极中无机杂质的含量,一般是石墨电极的重要指标之一、灰分越低,电极的纯度越高,能够提高电极的使用寿命。
通常对于石墨电极来说,灰分应该在0.3%以下。
5.抗折强度:石墨电极的抗折强度是指在一定条件下电极抗折断的能力。
抗折强度一般在8-14MPa之间,抗折强度越高,电极越不容易断裂,使用寿命也更长。
6.膨胀系数:石墨电极的膨胀系数是指石墨电极在高温下热胀冷缩的程度。
膨胀系数较低的石墨电极能够减小因温度变化引起的氧化损坏和断裂风险。
7.抗渣性能:石墨电极的抗渣性能是指电极在高温下长时间与熔融金属接触不产生显著的变化,不易被渣蚀。
优秀的抗渣性能可以提高电极的使用寿命和稳定性。
8.精度要求:石墨电极的精度要求主要体现在加工精度和表面质量上。
加工精度包括直径精度、圆度精度和平行度精度等。
表面质量要求光滑,没有裂纹和明显的瑕疵。
9.石墨电极连接方式:石墨电极的连接方式有螺纹连接和插销连接两种。
螺纹连接方式简单可靠,适用于直径较大的电极。
插销连接方式则适用于直径较小的电极,可以提高电极的连接紧密度。
总结:石墨电极的技术参数主要包括尺寸参数、电导率、密度、灰分、抗折强度、膨胀系数、抗渣性能、精度要求以及连接方式等。
负极材料石墨电极
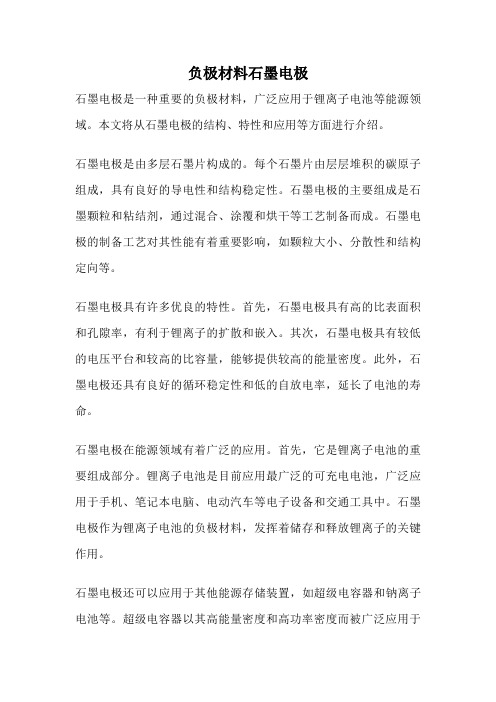
负极材料石墨电极石墨电极是一种重要的负极材料,广泛应用于锂离子电池等能源领域。
本文将从石墨电极的结构、特性和应用等方面进行介绍。
石墨电极是由多层石墨片构成的。
每个石墨片由层层堆积的碳原子组成,具有良好的导电性和结构稳定性。
石墨电极的主要组成是石墨颗粒和粘结剂,通过混合、涂覆和烘干等工艺制备而成。
石墨电极的制备工艺对其性能有着重要影响,如颗粒大小、分散性和结构定向等。
石墨电极具有许多优良的特性。
首先,石墨电极具有高的比表面积和孔隙率,有利于锂离子的扩散和嵌入。
其次,石墨电极具有较低的电压平台和较高的比容量,能够提供较高的能量密度。
此外,石墨电极还具有良好的循环稳定性和低的自放电率,延长了电池的寿命。
石墨电极在能源领域有着广泛的应用。
首先,它是锂离子电池的重要组成部分。
锂离子电池是目前应用最广泛的可充电电池,广泛应用于手机、笔记本电脑、电动汽车等电子设备和交通工具中。
石墨电极作为锂离子电池的负极材料,发挥着储存和释放锂离子的关键作用。
石墨电极还可以应用于其他能源存储装置,如超级电容器和钠离子电池等。
超级电容器以其高能量密度和高功率密度而被广泛应用于储能系统和电动车辆等领域。
石墨电极作为超级电容器的负极材料,能够提供较高的电导率和储存能量。
钠离子电池是一种新型的二次电池技术,与锂离子电池相比具有更高的丰富性和更低的成本。
石墨电极可以作为钠离子电池的负极材料,有望在大规模能源存储和电网调度等领域发挥重要作用。
石墨电极作为一种重要的负极材料,在能源领域有着广泛的应用前景。
通过优化其制备工艺和结构设计,可以进一步提高石墨电极的性能,满足不断增长的能源需求。
随着科学技术的不断进步,石墨电极将在能源存储和转换等领域发挥越来越重要的作用,推动能源技术的发展和进步。
石墨电极使用说明
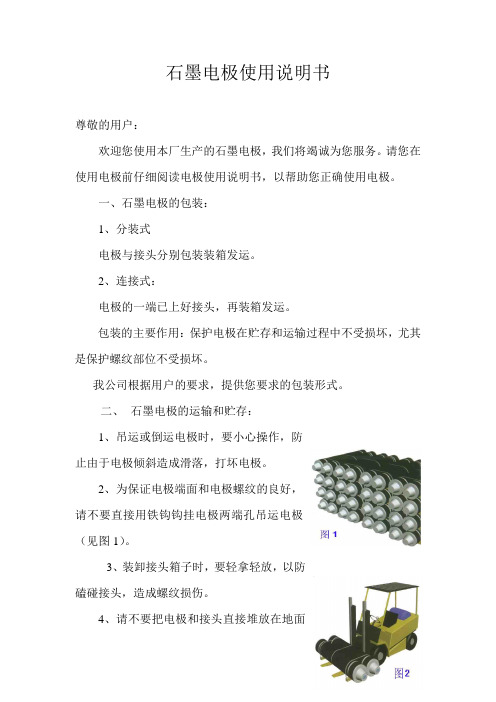
石墨电极使用说明书尊敬的用户:欢迎您使用本厂生产的石墨电极,我们将竭诚为您服务。
请您在使用电极前仔细阅读电极使用说明书,以帮助您正确使用电极。
一、石墨电极的包装:1、分装式电极与接头分别包装装箱发运。
2、连接式:电极的一端已上好接头,再装箱发运。
包装的主要作用:保护电极在贮存和运输过程中不受损坏,尤其是保护螺纹部位不受损坏。
我公司根据用户的要求,提供您要求的包装形式。
二、石墨电极的运输和贮存:1、吊运或倒运电极时,要小心操作,防止由于电极倾斜造成滑落,打坏电极。
2、为保证电极端面和电极螺纹的良好,请不要直接用铁钩钩挂电极两端孔吊运电极(见图1)。
3、装卸接头箱子时,要轻拿轻放,以防磕碰接头,造成螺纹损伤。
4、请不要把电极和接头直接堆放在地面上,要放在木方或铁架上,要防止电极碰损或粘上泥土,暂时不用的电极和接头,不要把包装物去掉,要防止灰尘、杂物落到螺纹上或电极孔内(见图2)。
5、电极在库房内贮存要摆放整齐,电极垛两侧要垫好,以防滑垛。
电极的堆放高度一般不超过2米。
6、存放的电极要注意防雨、防潮。
受潮湿的电极,使用前要烘干,以免炼钢时电极产生裂纹和增加氧化。
7、存放电极接头不要靠近高温处,以防温度过高使接头栓熔化。
三、电极连接前的准备:1、去掉新电极孔的保护罩,检查电极孔内螺纹是否完整,螺纹不完整的与售后服务技术人员联系,由售后服务技术人员确定电极是否可以使用;检查孔内是否清洁,如不清洁要清理干净后方可使用(见图3)。
2、将电极吊具拧入一端电极孔内,在电极的另一端下面放好软垫(见图4),避免损坏电极接头。
3、用压缩空气先吹净待接电极表面和孔内的灰尘、杂物等,然后吹净新电极的表面和接头上的灰尘、杂物等;如压缩空气不能将电极表面吹干净,要用毛刷清理干净(见图5、图6)。
四、加接电极的操作步骤:1、将新电极吊到待接电极上方对准电极孔,慢慢落下。
2、把隔离器放于两电极之间,新电极慢慢落下,避免损坏电极孔和接头螺纹(见图7)。
石墨电极标准

石墨电极标准石墨电极是一种重要的炼钢工艺材料,广泛应用于钢铁冶炼行业。
石墨电极标准的制定对于提高产品质量、促进行业健康发展具有重要意义。
本文将从石墨电极的材料、规格、性能等方面进行介绍,为相关行业人士提供参考。
一、石墨电极的材料。
石墨电极主要由石墨和配套的材料组成。
石墨是石墨电极的主要材料,其质量直接影响着电极的使用效果。
优质的石墨应具有高纯度、低灰分、良好的导电性能和热稳定性。
配套材料包括结构胶、填料等,其选择应根据电极的具体使用条件和要求进行合理搭配。
二、石墨电极的规格。
石墨电极的规格通常包括直径、长度、孔径等参数。
不同规格的电极适用于不同规模和工艺要求的炉子。
在制定石墨电极标准时,应充分考虑不同规格电极的生产工艺、使用性能和市场需求,制定合理的规格范围和允许偏差,以满足不同用户的需求。
三、石墨电极的性能。
石墨电极的性能直接关系到其在冶炼过程中的稳定性和耐用性。
主要性能包括导电性能、热稳定性、机械强度和耐火性等。
导电性能是石墨电极的重要指标,直接影响着冶炼过程中的能耗和生产效率。
热稳定性和耐火性则关系到电极在高温条件下的使用寿命和安全性。
机械强度则决定了电极在使用过程中的稳定性和可靠性。
四、石墨电极的标准制定。
制定石墨电极标准应充分考虑国内外行业标准和相关法规法规的要求,结合实际生产和使用情况,制定具有可操作性和指导性的标准内容。
标准的制定应包括石墨电极的材料、规格、性能要求、试验方法、检验规则、标志、包装、运输和贮存等内容,确保产品质量和使用安全。
五、石墨电极标准的应用。
石墨电极标准的制定不仅有利于规范产品质量,提高行业整体水平,还能促进技术创新和产品升级。
标准的实施可以引导企业加强自主研发和技术创新,推动行业向高端化、智能化方向发展。
同时,标准的应用还能提高产品的国际竞争力,促进出口贸易和国际合作。
六、总结。
石墨电极标准的制定是一个系统工程,需要各方共同参与和努力。
只有通过标准化的生产和使用,才能保证产品质量、提高效率,推动行业健康发展。
石墨电极简介介绍

中国作为全球最大的石墨电极生产国和消费国,其市场需求持续旺盛。然而,随着国内产能的过剩和竞争的加剧 ,石墨电极行业的利润空间逐渐缩小。未来,企业需要加大技术研发和产品创新力度,提高产品质量和附加值。
石墨电极的未来发展前景
总结词
环保、高效、节能方向发展
详细描述
未来,石墨电极行业将朝着环保、高效、节能方向发展。随着国家对环保要求的提高和能源结构的调 整,高效、环保的石墨电极产品将成为市场主流。同时,随着新能源、电动汽车等新兴产业的快速发 展,石墨电极在动力电池等领域的应用也将不断扩大。
05
石墨电极的未来技术发展
提高石墨电极的性能
提高石墨电极的导电性能
通过优化石墨电极的微观结构,提高其电子导电性能。
增强石墨电极的抗折强度
研究石墨电极的断裂机制,优化其抗折强度。
延长石墨电极的使用寿命
通过改进石墨电极的生产工艺和使用环境,提高其使用寿命。
开发新型石墨电极材料
探索新型石墨材料
研究新型石墨材料的合成方法,提高其性能。
石墨电极简介介绍
汇报人:文小库 2023-11-25
目 录
• 石墨电极概述 • 石墨电极的生产工艺 • 石墨电极的应用领域 • 石墨电极的市场现状及前景 • 石墨电极的未来技术发展
01
石墨电极概述
石墨电极的定义
• 石墨电极是一种由石墨材料制成的电导体,通常用于高温电弧炉中作为电极材料。它具有高导电性、高热稳定 性和高机械强度等优点,是钢铁、有色金属冶炼及电化学行业的重要材料。
石墨电极的结构
• 石墨电极通常由石墨材料、粘结剂和浸渍物组成。其中,石墨材料是主要成分,其结构包括骨料和填料。骨料是构成电极 主体的大块石墨,而填料则用于填充骨料之间的空隙。粘结剂和浸渍物则用于提高电极的机械强度和导电性。
石墨电极参数介绍
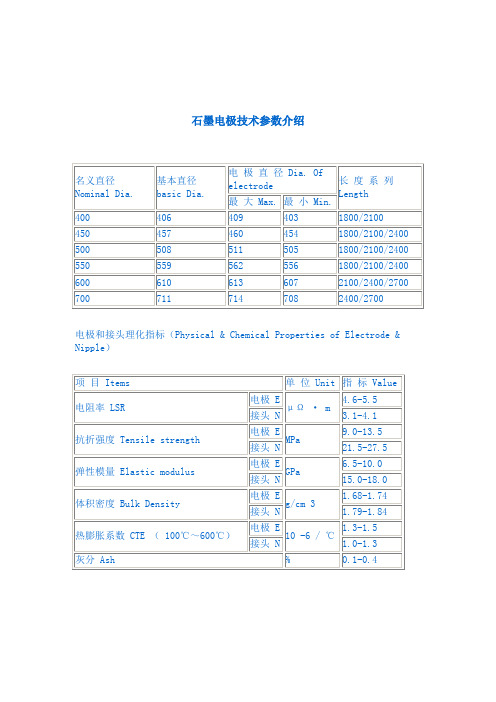
电极E
μΩ·m
4.6-5.5
接头N
3.1-4.1
抗折强度Tensile strength
电极E
MPa
9.0-13.5
接头N
21.5-27.5
弹性模量Elastic modulus
电极E
GPa
6.5-10.0
接头N
15.0-18.0
体积密度Bulk Density
电极E
g/cm 3
1.68-1.74
石墨电极技术参数介绍
名义直径Nominal Dia.
基本直径basic Dia.
电极直径Dia. Of electrode
长度系列Length
最大Max.
最小Min.
400
406
409
403
1800/2100
450
457
460
454
1800/2100/2400
500
508
511
505
1800/2100/2400
550
559
562
556
1800/2100/2400
600
610
613
607
2100/2400/2700
700
711
714
708
2400/2700
电极和接头理化指标(Physical & Chemical Properties of Electrode & Nipple)
项目Items
单位Unit
指标Value
接头nipple
中径d 2、D 2 Medium Dia.
电极孔
螺距P Pitch
石墨电极

石墨电极石墨是冶金工业中的一种重要材料,除前面所讲的用于坩埚、耐火材料等以外,还在炼钢电炉,电弧炉中作电极。
1955年开始使用人造石墨电极,近几年开始使用天然石墨电极,而且发展很快。
一、石墨电极1.石墨电极的制造工艺人造石墨电极的原料主要是石油焦和沥青焦。
它们是由石油沥青和煤沥青经焦化处理得到的,是一种低灰份、低硫份,易于石墨化的理想炭素材料。
生产人造石墨电极的工艺流程图原料经破碎加工,达到适宜的粒度后,送入1000~1300℃煅烧炉中进行热处理,以除去原料中的水份和挥发份,以提高其密度、机械强度、导热和导电性能。
石墨化工序是人造石墨电极关键的一环,它是在常压和2000℃以上的温度下,使石油焦和沥青焦的碳原子由二维空间的乱层结构,转化为三维有序排列的石墨晶粒。
石墨化的好坏对产品质量影响很大。
结晶化程度与电极的导电性能有关,石墨化工序采用大型石墨化炉进行,耗电量极高,每吨电极耗电约5000~6000kwh。
天然石墨电极生产工艺天然石墨电极的原料由高碳鳞片状石墨,中温煤沥青经破碎混合组成。
根据电极产品的规格不同,各种原料的颗粒级配有所不同。
生产时原料先进行干混。
干料混均后进行适当的加热。
再加入一定数量的沥青进行湿混,使粘结剂与原料混均,成为可塑性好的糊料。
将糊料送入电极挤压机的料缸中,经预压排除空气,再压制成型。
成型后的生坯送入焙烧炉中焙烧,使粘结剂煤沥青在一定温度下裂解,并产生聚合反应,使碳原子之间形成焦碳网络,把石墨粉紧密连接起来,形成一个具有一定机械强度和理化性能的整体。
焙烧俺一定升温曲线升至1300℃,需要时间为219~240h。
采用冶金焦和石英砂混合作填充及覆盖料。
浸渍后二次焙烧条件基本相同,时间稍短一些。
浸渍过程是将以此焙烧产品送入预热炉中,温度达260~320℃,预热3~5h后入浸渍罐。
浸渍时,液态沥青在一定的真空压力、温度条件下浸入制品的微孔中。
然后用水冷却后出罐。
一个周期要6h。
浸渍后的电极经二次焙烧后再进行加工,出厂。
石墨电极 国标

石墨电极国标石墨电极是电化学工业中常用的一种电极材料,也是国际上公认的高效电极材料之一。
它由石墨粉末和粘结剂经过浸渍、成型、烘干等工艺制成。
石墨电极具有导电性好、热稳定性高、耐腐蚀性强等特点,被广泛应用于冶金、化工、电力等领域。
石墨电极具有良好的导电性能。
石墨电极是由石墨粉末制成的,石墨具有良好的导电性能,能够有效地传导电流。
在电化学反应中,电流通过石墨电极,使反应物发生氧化还原反应。
石墨电极的导电性能直接影响着反应的效率和速度。
石墨电极具有较高的热稳定性。
在高温条件下,石墨电极能够保持较高的稳定性,不易熔化或变形。
这使得石墨电极可以在高温环境下进行电化学反应,如电解、电镀等。
石墨电极的热稳定性是其被广泛应用于冶金领域的重要原因之一。
石墨电极还具有良好的耐腐蚀性。
石墨电极在酸、碱、盐等腐蚀性介质中具有较高的稳定性,能够长时间地使用而不发生腐蚀。
这使得石墨电极可以在化工领域中广泛应用,如电解制氯碱、电解铝等工艺中。
石墨电极的耐腐蚀性能决定了其在化工领域的应用范围和效果。
除了上述特点,石墨电极还具有其他一些优点。
首先,石墨电极具有良好的机械强度和韧性,能够承受较大的压力和振动。
其次,石墨电极的制造工艺相对简单,成本较低,易于大规模生产。
此外,石墨电极还可以根据需要进行定制,以满足不同领域的需求。
然而,石墨电极也存在一些局限性。
首先,由于石墨电极的导电性能较好,在某些特殊情况下可能会发生电流过大的情况,导致石墨电极烧损或损坏。
其次,石墨电极在高温条件下可能会发生氧化反应,导致其导电性能下降。
此外,石墨电极的制造工艺和原材料的选择也对其性能产生一定影响。
石墨电极作为一种重要的电极材料,具有导电性好、热稳定性高、耐腐蚀性强等特点,被广泛应用于冶金、化工、电力等领域。
石墨电极的优点在于其良好的导电性能、高热稳定性和耐腐蚀性,同时具有较强的机械强度和韧性,制造工艺简单且成本较低。
然而,石墨电极也存在一些局限性,如容易受到电流过大和高温氧化等因素的影响。
(完整版)石墨电极
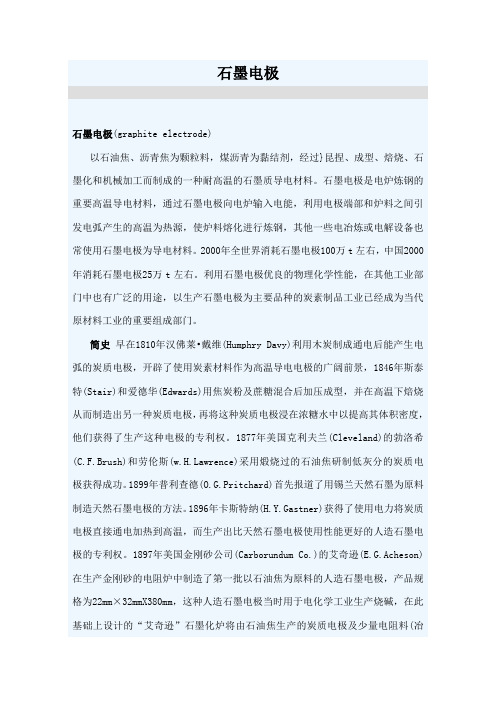
石墨电极石墨电极(graphite electrode)以石油焦、沥青焦为颗粒料,煤沥青为黏结剂,经过}昆捏、成型、焙烧、石墨化和机械加工而制成的一种耐高温的石墨质导电材料。
石墨电极是电炉炼钢的重要高温导电材料,通过石墨电极向电炉输入电能,利用电极端部和炉料之间引发电弧产生的高温为热源,使炉料熔化进行炼钢,其他一些电冶炼或电解设备也常使用石墨电极为导电材料。
2000年全世界消耗石墨电极100万t左右,中国2000年消耗石墨电极25万t左右。
利用石墨电极优良的物理化学性能,在其他工业部门中也有广泛的用途,以生产石墨电极为主要品种的炭素制品工业已经成为当代原材料工业的重要组成部门。
简史早在1810年汉佛莱•戴维(Humphry Davy)利用木炭制成通电后能产生电弧的炭质电极,开辟了使用炭素材料作为高温导电电极的广阔前景,1846年斯泰特(Stair)和爱德华(Edwards)用焦炭粉及蔗糖混合后加压成型,并在高温下焙烧从而制造出另一种炭质电极,再将这种炭质电极浸在浓糖水中以提高其体积密度,他们获得了生产这种电极的专利权。
1877年美国克利夫兰(Cleveland)的勃洛希(C.F.Brush)和劳伦斯(wrence)采用煅烧过的石油焦研制低灰分的炭质电极获得成功。
1899年普利查德(O.G.Pritchard)首先报道了用锡兰天然石墨为原料制造天然石墨电极的方法。
1896年卡斯特纳(H.Y.Gastner)获得了使用电力将炭质电极直接通电加热到高温,而生产出比天然石墨电极使用性能更好的人造石墨电极的专利权。
1897年美国金刚砂公司(Carborundum Co.)的艾奇逊(E.G.Acheson)在生产金刚砂的电阻炉中制造了第一批以石油焦为原料的人造石墨电极,产品规格为22mm×32m mX380mm,这种人造石墨电极当时用于电化学工业生产烧碱,在此基础上设计的“艾奇逊”石墨化炉将由石油焦生产的炭质电极及少量电阻料(冶金焦粒)构成“炉芯电阻”,通电后产生高温,使由石油焦制成的炭质电极在高温下“石墨化”而获得人造石墨电极。
最新石墨电极的原料及制造工艺资料
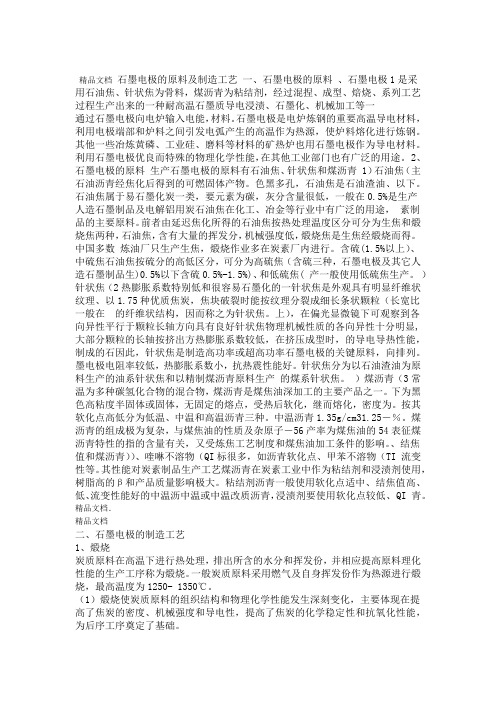
精品文档石墨电极的原料及制造工艺一、石墨电极的原料、石墨电极1是采用石油焦、针状焦为骨料,煤沥青为粘结剂,经过混捏、成型、焙烧、系列工艺过程生产出来的一种耐高温石墨质导电浸渍、石墨化、机械加工等一通过石墨电极向电炉输入电能,材料。
石墨电极是电炉炼钢的重要高温导电材料,利用电极端部和炉料之间引发电弧产生的高温作为热源,使炉料熔化进行炼钢。
其他一些冶炼黄磷、工业硅、磨料等材料的矿热炉也用石墨电极作为导电材料。
利用石墨电极优良而特殊的物理化学性能,在其他工业部门也有广泛的用途。
2、石墨电极的原料生产石墨电极的原料有石油焦、针状焦和煤沥青 1)石油焦(主石油沥青经焦化后得到的可燃固体产物。
色黑多孔,石油焦是石油渣油、以下。
石油焦属于易石墨化炭一类,要元素为碳,灰分含量很低,一般在0.5%是生产人造石墨制品及电解铝用炭石油焦在化工、冶金等行业中有广泛的用途,素制品的主要原料。
前者由延迟焦化所得的石油焦按热处理温度区分可分为生焦和煅烧焦两种,石油焦,含有大量的挥发分,机械强度低,煅烧焦是生焦经煅烧而得。
中国多数炼油厂只生产生焦,煅烧作业多在炭素厂内进行。
含硫(1.5%以上)、中硫焦石油焦按硫分的高低区分,可分为高硫焦(含硫三种,石墨电极及其它人造石墨制品生)0.5%以下含硫0.5%-1.5%)、和低硫焦( 产一般使用低硫焦生产。
)针状焦(2热膨胀系数特别低和很容易石墨化的一针状焦是外观具有明显纤维状纹理、以1.75种优质焦炭,焦块破裂时能按纹理分裂成细长条状颗粒(长宽比一般在的纤维状结构,因而称之为针状焦。
上),在偏光显微镜下可观察到各向异性平行于颗粒长轴方向具有良好针状焦物理机械性质的各向异性十分明显, 大部分颗粒的长轴按挤出方热膨胀系数较低,在挤压成型时,的导电导热性能,制成的石因此,针状焦是制造高功率或超高功率石墨电极的关键原料,向排列。
墨电极电阻率较低,热膨胀系数小,抗热震性能好。
针状焦分为以石油渣油为原料生产的油系针状焦和以精制煤沥青原料生产的煤系针状焦。
石墨电极
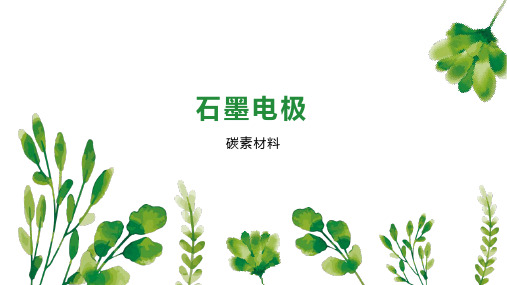
(5)生产所需炭质原料石油焦和煤沥青等为炼油企业和煤化工企业生产加工副产品,原料的质量及其稳定性 难以得到充分的保障,尤其是高功率和超高功率石墨电极生产用针状焦、改质电极沥青和低喹啉不溶物含量专用 浸渍剂沥青,急需我国石油和煤化工加工企业的重视和积极配合。
(2)石墨电极较容易加工,且加工速度明显快于铜电极。比如采用铣削工艺加工石墨,其加工速度较其他金 属加工快2~3倍且不需要额外的人工处理,而铜电极则需要人手挫磨。同样,如果采用高速石墨加工中心制造电 极,速度会更快,效率也更高,还不会产生粉尘问题。在这些加工过程中,选择硬度合适的工具和石墨可减少刀 具的磨损耗和铜电极的破损。如果具体比较石墨电极与铜电极的铣削时间,石墨电极较铜电极快67%,在一般情 况下的放电加工中,采用石墨电极的加工要比采用铜电极快58%。这样一来,加工时间大幅减少,同时也减少了 制造成本。
(2)数控自动成形法:数控自动成形法需要专用的石墨电极成形机,它采用数控方式,有刀具自动调换装置, 可容纳多把刀具。为改善加工环境,加工石墨电极的四周用水幕包围,防止石墨粉尘四处分散。另外也可以用湿 式加工法,由水溶性切削液防止刀具被磨损和石墨粉尘飞散。机床具有高性能过滤装置,可以将切削液和石墨切 屑分离,可保证长时间连续加工,是石墨电极加工的理想专用设备,适合于模具用电极加工。但是其价格较高, 在国内应用还不普遍。
应用
(1)用于电弧炼钢炉
电炉炼钢是石墨电极的使用大户。我国电炉钢产量约占粗钢产量的18%左右,炼钢用石墨电极占石墨电极总 用量的70%~80%。电炉炼钢是利用石墨电极向炉内导入电流,利用电极端部和炉料之间引发电弧所产生的高温热 源来进行冶炼。
石墨电极知识
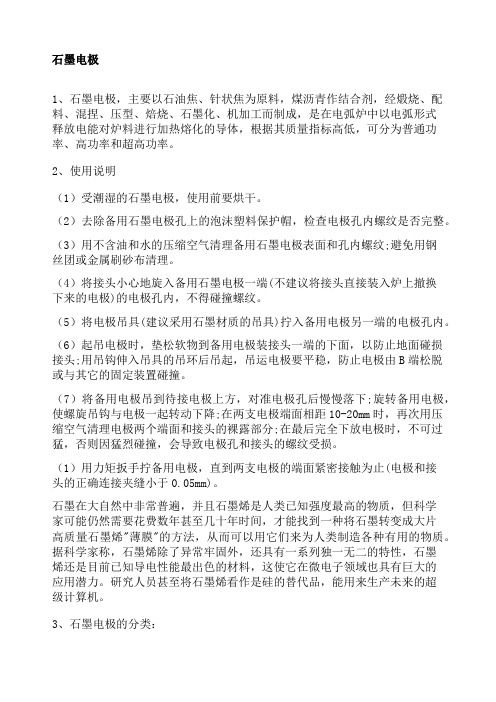
石墨电极1、石墨电极,主要以石油焦、针状焦为原料,煤沥青作结合剂,经煅烧、配料、混捏、压型、焙烧、石墨化、机加工而制成,是在电弧炉中以电弧形式释放电能对炉料进行加热熔化的导体,根据其质量指标高低,可分为普通功率、高功率和超高功率。
2、使用说明(1)受潮湿的石墨电极,使用前要烘干。
(2)去除备用石墨电极孔上的泡沫塑料保护帽,检查电极孔内螺纹是否完整。
(3)用不含油和水的压缩空气清理备用石墨电极表面和孔内螺纹;避免用钢丝团或金属刷砂布清理。
(4)将接头小心地旋入备用石墨电极一端(不建议将接头直接装入炉上撤换下来的电极)的电极孔内,不得碰撞螺纹。
(5)将电极吊具(建议采用石墨材质的吊具)拧入备用电极另一端的电极孔内。
(6)起吊电极时,垫松软物到备用电极装接头一端的下面,以防止地面碰损接头;用吊钩伸入吊具的吊环后吊起,吊运电极要平稳,防止电极由B端松脱或与其它的固定装置碰撞。
(7)将备用电极吊到待接电极上方,对准电极孔后慢慢落下;旋转备用电极,使螺旋吊钩与电极一起转动下降;在两支电极端面相距10-20mm时,再次用压缩空气清理电极两个端面和接头的裸露部分;在最后完全下放电极时,不可过猛,否则因猛烈碰撞,会导致电极孔和接头的螺纹受损。
(1)用力矩扳手拧备用电极,直到两支电极的端面紧密接触为止(电极和接头的正确连接夹缝小于0.05mm)。
石墨在大自然中非常普遍,并且石墨烯是人类已知强度最高的物质,但科学家可能仍然需要花费数年甚至几十年时间,才能找到一种将石墨转变成大片高质量石墨烯"薄膜"的方法,从而可以用它们来为人类制造各种有用的物质。
据科学家称,石墨烯除了异常牢固外,还具有一系列独一无二的特性,石墨烯还是目前已知导电性能最出色的材料,这使它在微电子领域也具有巨大的应用潜力。
研究人员甚至将石墨烯看作是硅的替代品,能用来生产未来的超级计算机。
3、石墨电极的分类:(1)普通功率石墨电极允许使用电流密度低于 17A/厘米2的石墨电极,主要用于炼钢、炼硅、炼黄磷等的普通功率电炉。
高功率石墨电极技术标准完整版
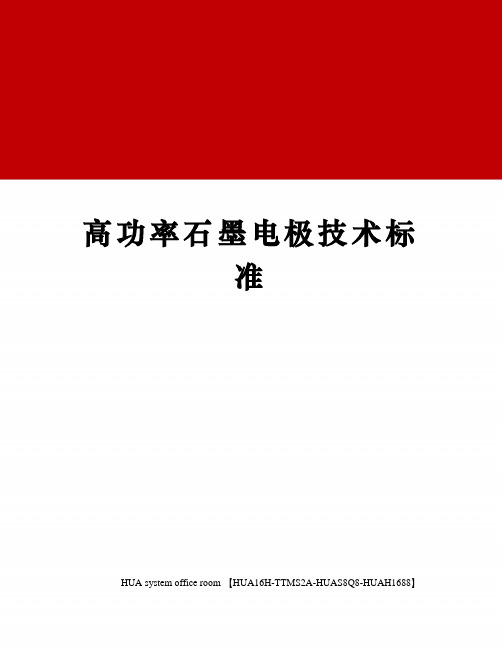
高功率石墨电极技术标准HUA system office room 【HUA16H-TTMS2A-HUAS8Q8-HUAH1688】超高功率石墨电极技术标准1 范围高功率石墨电极的外形、尺寸及允许偏差、技术要求,试验方法、检验规则、包装、标志、储存、运输和质量证明书。
2 引用标准GB/T 1427-1988 炭素材料取样方法GB/T 1429-1985 炭素材料灰分含量测定方法GB/T 3074.1-1982 石墨电极抗折强度测定方法GB/T 3074.2-1982 石墨电极弹性模量测定方法GB/T 3074.4-1982 石墨电极热膨胀系数(CTE)测定方法GB/T 8170-1987 数值修约规则YB/T 119-1997 炭素材料体积密度测定方法YB/T 120-1997 炭素材料电阻率测定方法YB/T 5212-1993 整体石墨电极弹性模量试验声速法YB/T8719-1997 炭素材料及其制品的包装、标志、运输和质量证明书的一般规定。
3 外形、尺寸及允许偏差3.1 电极的直径及长度应符合表1的规定。
表1?㎜3.2 电极的长度允许偏差应符合表2的规定。
表2 ㎜3.3供货中每批允许短尺电极不超过15%。
3.4 电极接头为圆锥形,接头的形状、尺寸按图1(略)和表3的规定3.5 两根电极连接处端面间隙不大于0.4㎜。
表3?㎜4 技术要求4.1 电极和接头理化指标符合表4的规定。
表44.2 表面质量4.2.1 电极表面掉块或孔洞不多于两处,其尺寸应符合表5的规定。
表54.2.2 接头、接头孔及距孔底100 ㎜以内的电极表面,不允许有孔洞和裂纹。
4.2.3 接头和接头孔螺纹的掉块,不多于一处,长度不大于30mm。
4.2.4 电极表面不允许有横向裂纹。
宽0.3mm~1.0mm的纵向裂纹,其长度不大于电极周长的5%,不多于两条;而宽度小于0.3mm的纵向裂纹不计。
4.2.5 电极表面的黑皮面积:宽度小于电极周长的十分之一,长度小于电极长度的三分之一。
石墨电极简介

• 石墨电极
石墨电极简介:
• 石墨电极是指以石油焦、沥青焦为骨料,煤沥青为黏结剂,经过原材 料煅烧、破碎墨粉、配料、混捏、成型、焙烧、浸烧、石墨化和机械 加工而制成的一种耐高温石墨质导电材料,又称为人造石墨电极。
石墨电极 天然石墨电极
石墨电极的性能
• • • • • 耐高温性能好 稳定性能好 导电性能好 化学稳定性好 导热ቤተ መጻሕፍቲ ባይዱ能特殊
生产工艺:
•
石墨电极工艺流程图
产品展示
• 本 公 司 主 要 销 售 φ 200mm1400mm 普通功率、高功率、超 高功率石墨电极等多种碳素制品, 石墨电极产品体积密度高、抗压 强度大、电阻率低、抗氧化性强。 产品品质经国家碳素材料实验中 心 抽 样 化 验 均 达 到 YB/T40882000 、 YB/T4089-2000 、 YB/T4090-2000标准。
石墨电极的分类
普通功率石墨电极(RP),主要用于炼钢、炼硅、 炼黄麟等的普通功率电炉。
→
高功率石墨电极(HP),主要用于炼钢的高功率 电弧炉。
超高功率石墨电极(UHP),只要用于超高功率 炼钢电弧炉。
产品介绍
普通功率石墨电极
普通功率石墨电极采用中石油 抚顺石化生产的优质石油焦和煤系 沥青为原料,经煅烧、配料、混捏、 压型、焙烧、石墨化、机加工等工 序精制而成。
产品介绍
高功率石墨电极
高功率石墨电极本体采用中石 油抚顺石化生产的优质石油焦、日 本进口油系针状焦和中温沥青为原 料,按照高功率石墨电极生产工艺 经煅烧、配料、混捏、压型、焙烧、 高压浸渍、石墨化、机加工等工序 精制而成,接头采用日本进口针状 焦二浸三烧工艺制成。
石墨电极固定碳含量

石墨电极固定碳含量(原创版)目录1.石墨电极的定义与特点2.石墨电极的制造过程与原料3.石墨电极的应用领域4.石墨电极的优势与替代材料5.石墨电极的未来发展趋势正文石墨电极是一种耐高温的石墨质导电材料,具有低电阻率和耐电弧炉内热梯度的特性。
它主要是以石油焦、沥青焦为骨料,煤沥青为黏结剂,经过多道工序制成。
石墨电极广泛应用于冶金、化工、电子等领域,作为电极来传递电流或产生化学反应。
石墨电极的制造过程分为原料煅烧、破碎磨粉、配料、混捏、成型、焙烧、浸渍、石墨化和机械加工等步骤。
其中,原料的选择和配比对石墨电极的性能具有重要影响。
石墨电极的主要原料为石油焦、沥青焦,这两种原料具有高碳含量、低杂质和较好的耐高温性能。
石墨电极的应用领域十分广泛,主要用于冶金领域中的电炉炼钢和铸铁过程。
在此过程中,石墨电极不仅可以作为电极来传递电流,还可以作为熔炼的反应容器。
此外,石墨电极还被广泛应用于化工领域的石化、电解等过程中。
在这些过程中,石墨电极被用作电解槽中的阳极,以产生所需的化学反应。
另外,石墨电极还被用于电子领域中的真空炉、电子束加工等过程中。
相对于其他材料,石墨电极具有显著的优势。
例如,它的密度只有铜的 1/5,热膨胀系数仅有铜的 1/10。
这使得石墨电极在放电加工速度上比铜快 2~3 倍,尤其在薄筋电极的加工上具有明显优势。
此外,石墨电极的重量更轻,可以减轻电极自身的重量,提高电极的使用寿命。
尽管石墨电极具有诸多优点,但随着科技的发展和新材料的出现,石墨电极的替代材料也在逐渐增多。
例如,在一些特殊场合,铜、钨、钼等高熔点金属材料和碳纳米管等新型材料已经逐渐替代石墨电极。
然而,由于石墨电极成本低、性能稳定等优点,目前市场上石墨电极的需求仍然较大。
总的来说,石墨电极作为一种传统的电极材料,在诸多领域具有广泛的应用。
随着科技的进步和市场需求的变化,石墨电极的研发和应用将不断得到拓展和优化。
- 1、下载文档前请自行甄别文档内容的完整性,平台不提供额外的编辑、内容补充、找答案等附加服务。
- 2、"仅部分预览"的文档,不可在线预览部分如存在完整性等问题,可反馈申请退款(可完整预览的文档不适用该条件!)。
- 3、如文档侵犯您的权益,请联系客服反馈,我们会尽快为您处理(人工客服工作时间:9:00-18:30)。
石墨电极石墨电极(graphite electrode)以石油焦、沥青焦为颗粒料,煤沥青为黏结剂,经过}昆捏、成型、焙烧、石墨化和机械加工而制成的一种耐高温的石墨质导电材料。
石墨电极是电炉炼钢的重要高温导电材料,通过石墨电极向电炉输入电能,利用电极端部和炉料之间引发电弧产生的高温为热源,使炉料熔化进行炼钢,其他一些电冶炼或电解设备也常使用石墨电极为导电材料。
2000年全世界消耗石墨电极100万t左右,中国2000年消耗石墨电极25万t左右。
利用石墨电极优良的物理化学性能,在其他工业部门中也有广泛的用途,以生产石墨电极为主要品种的炭素制品工业已经成为当代原材料工业的重要组成部门。
简史早在1810年汉佛莱•戴维(Humphry Davy)利用木炭制成通电后能产生电弧的炭质电极,开辟了使用炭素材料作为高温导电电极的广阔前景,1846年斯泰特(Stair)和爱德华(Edwards)用焦炭粉及蔗糖混合后加压成型,并在高温下焙烧从而制造出另一种炭质电极,再将这种炭质电极浸在浓糖水中以提高其体积密度,他们获得了生产这种电极的专利权。
1877年美国克利夫兰(Cleveland)的勃洛希(C.F.Brush)和劳伦斯(wrence)采用煅烧过的石油焦研制低灰分的炭质电极获得成功。
1899年普利查德(O.G.Pritchard)首先报道了用锡兰天然石墨为原料制造天然石墨电极的方法。
1896年卡斯特纳(H.Y.Gastner)获得了使用电力将炭质电极直接通电加热到高温,而生产出比天然石墨电极使用性能更好的人造石墨电极的专利权。
1897年美国金刚砂公司(Carborundum Co.)的艾奇逊(E.G.Acheson)在生产金刚砂的电阻炉中制造了第一批以石油焦为原料的人造石墨电极,产品规格为22mm×32m mX380mm,这种人造石墨电极当时用于电化学工业生产烧碱,在此基础上设计的“艾奇逊”石墨化炉将由石油焦生产的炭质电极及少量电阻料(冶金焦粒)构成“炉芯电阻”,通电后产生高温,使由石油焦制成的炭质电极在高温下“石墨化”而获得人造石墨电极。
19世纪末法国人埃鲁(P.L.T.Heroult)发明了直接电弧炉,开始用于冶炼电石和铁合金生产,1899年首次用于炼钢,电弧炉需要一定数量耐高温的导电电极。
虽然1900年前后艾奇逊石墨公司(Acheson Graphite Co.)就出售可连接的电极,但这时只能生产小规格石墨电极,20世纪初期电炉炼钢主要使用以无烟煤为原料的炭质电极或以天然石墨为原料的天然石墨电极。
生产炭质电极或天然石墨电极的工艺比较简单,1910年已经向市场供应直径达610mm的炭质电极。
但是石墨电极的优良性能以及制造工艺的不断改进,大规格石墨电极的大批量生产及售价不断下降,电炉炼钢工业逐渐改用石墨电极,使用炭质电极或天然石墨电极逐渐减少,20世纪60年代以后绝大多数电弧炼钢炉都使用石墨电极。
1914~1918年制成的石墨电极最大直径只有356mm,1924年开始生产直径为406mm的石墨电极,1930年已扩大到457mm,1937年又增加到508mm,不久又生产了直径559mm、610mm、660mm、711mm、762mm的大规格石墨电极。
20世纪80年代世界上最大的电弧炼钢炉使用的石墨电极直径为813mm。
第二次世界大战以后生产石墨电极的原料质量、设备和制造工艺不断改进,随着电炉炼钢输入电功率不断提高的需要,于20世纪60~70年代又研制成功了高功率及超高功率石墨电极。
由于石墨电极质量不断提高及电炉炼钢工艺的改进,每吨电炉钢的石墨电极消耗已由70年代的6~8kg降低到80年代的4~6kg(普通功率电炉),采用超高功率石墨电极的大型电炉每吨钢的电极消耗已降低到2.5kg左右,而超高功率直流电弧炉(只用1根石墨电极)每吨钢的石墨电极消耗可降低到1.5kg左右。
80年代末世界上工业发达国家电炉炼钢工业多数电炉的吨位已提高到80~200t,因此大量使用的是直径550~750mm的高功率或超高功率石墨电极。
品种根据所用原料的不同和成品物理化学指标的区别,石墨电极分为普通功率石墨电极(RP级),高功率石墨电极(HP级)和超高功率石墨电极(UHP级)3个品种。
这是因为石墨电极主要供电弧炼钢炉作为导电材料使用,20世纪80年代国际电炉炼钢工业把电弧炼钢炉按每吨炉容量的变压器输入功率大小分为3类:普通功率电炉(RP炉)、高功率电炉(HP炉)和超高功率电炉(UHP炉)。
20t以上的普通功率电炉每吨炉容量的变压器输入功率一般为300kW/t左右;高功率电炉为400kW/t 左右;把40t以下的电炉输入功率500~600kW/t、50~80t的电炉输入功率400~500kW/t、100t以上的电炉输入功率350~450kW/t称为超高功率电炉。
到了20世纪80年代末,经济发达国家大量淘汰50t以下的中小型普通功率电炉,新建的电炉多数是80~150t的超高功率大电炉,并将输入的电功率提高到800kW/t,90年代初期一部分超高功率电炉又进一步提高到1000~1200kW/t。
高功率和超高功率电炉使用的石墨电极在更加苛刻的条件下运行,由于通过电极的电流密度明显增大,结果产生下列问题:(1)因电阻热和炽热气流导致电极温度升高,使得电极及接头的热膨胀量都增加了,同时电极的氧化消耗也提高了。
(2)电极中心部位和电极外圆的温度差增大了,由温度差引起的热应力也相应提高,电极容易产生裂纹和表面剥落。
(3)增大了电磁作用力,引起剧烈的振动,在剧烈振动下,电极因连接松动、脱扣而导致折断的几率增多了。
因此高功率和超高功率石墨电极的物理机械性能必须优于普通功率石墨电极,如电阻率较低,体积密度较大及机械强度较高,热膨胀系数要小,有良好的抗热震性能。
表1列出了20世纪80年代末期3种不同功率电弧炼钢炉的通用标准系列和配用的石墨电极直径。
为了适应炼钢厂大量发展高功率及超高功率电炉的需要,80年代起欧美、日本的炭素厂主要生产两种质量标准的石墨电极,即高功率石墨电极和超高功率石墨电极,普通功率石墨电极因销路不大而很少生产。
直流电弧炉用石墨电极直流电弧炉是20世纪80年代初发展成熟的新型电炉炼钢设备,初期的直流电弧炉是在原来的交流电弧炉基础上改造而成,有的使用3根石墨电极,有的使用2根石墨电极,但80年代中期以后新设计的直流电弧炉多数只用1根石墨电极,与相同功率使用3根石墨电极的交流电弧炉相比,在高温下受到氧化的电极总表面积大大减少,同样以超高功率运行的直流电弧炉,每吨钢的石墨电极的消耗可以降低50%左右,直流电弧炉电流通过电极时不产生趋肤效应及邻近效应,在电极横截面上电流分布均匀,而且直流电弧的稳定性好,运行中机械振动较小,电炉的噪声也较低。
直流电弧炉配用石墨电极的直径也是根据电炉容量和电极允许电流密度计算出来的,对相同输入功率的超高功率电炉而言,使用1根石墨电极的直流炉,电极直径要大一些,如容量为150t的交流电弧炉使用直径600mm的电极,而相同容量的直流电弧炉要使用直径700~750mm的电极,直流电弧炉对石墨电极的质量要求比交流电弧炉使用的还要高一些。
质量指标衡量石墨电极质量的主要指标有电阻率、体积密度、机械强度、线膨胀系数、弹性模量等,石墨电极在使用中的抗氧化性与抗热震性都与以上几项指标有关,产品机械加工的精确度和连接的可靠性也是重要检测项目。
电阻率石墨电极的电阻率是一项重要的物理性能指标,通常用电压降法测量,电阻率的大小可以衡量石墨电极石墨化度的高低,石墨电极的电阻率越低其热导率越高,抗氧化性能越好。
石墨电极使用时的允许电流密度与其电阻率及电极直径有关,石墨电极的电阻率越低,允许电流密度相应提高,但允许电流密度和电极直径的大小成反比,这是因为电极直径越大,电极横截面内中心部位与表层的温差增大,由此产生热应力的提高将引起电极产生裂纹或表面剥落,所以电流密度的增加受到限制。
图1列出了电极直径、允许电流密度与电极品种之间的关系。
体积密度增加体积密度有利于降低孔隙率和提高机械强度,改善抗氧化性能,但如果太大则抗热震性能下降,为此需要采取其他措施弥补这一不足,如提高石墨化温度以增加电极的热导率和采用针状焦为原料降低成品的热膨胀系数。
机械强度石墨电极的机械强度分为抗压、抗折和抗拉3种,主要测定抗折强度,抗折强度是石墨电极在使用时与折断有关的性能指标,在电炉上,当电极和不导电物体接触时,或由于受到塌料的碰撞、强烈振动的破坏作用等原因,石墨电极经常有被折断的危险,抗折强度高的石墨电极不容易被折断。
数根电极串接成电极柱使用时,连接处受到很大的拉力,所以对接头最好规定抗拉强度指标。
弹性模量是反映材料刚度的一个指标,通常石墨电极只测定杨氏弹性模量(纵弹性模量),即材料受到压缩或拉伸时产生单位弹性变形需要的应力,石墨电极的弹性模量与其抗热震性直接有关,石墨电极的弹性模量与其体积密度成正比,并且弹性模量随温度上升而增加。
抗热震性石墨电极的抗热震性表示在温度急剧变化时抵抗热应力破坏的能力,用以下公式表示:R=(κ×S)/(α×E)式中R为抗热震性;S为抗拉强度,MPa;κ为热导率,W/(m•K);α为线膨胀系数,1/℃;E为弹性模量,MPa。
从上式可以看到石墨电极的抗拉强度越高和弹性模量越低,其抗热震性能越好,另一方面石墨电极的热导率越小、热膨胀系数越大则抗热震性越差,电极在温度急剧变化时产生龟裂、表面剥落的可能性越多。
线膨胀系数一般只测定沿电极轴向的线膨胀系数,石墨电极的线膨胀系数与采用原料有关,也与配方的粒度组成、石墨化温度等因素有关。
线膨胀系数小的石墨电极,抗热震性能比较好,所以生产超高功率石墨电极应选用线膨胀系数较低的针状焦为原料,并且石墨化温度应该达到2800~3000℃。
石墨电极的线膨胀系数与测定温度范围有关,中国标准测定温度范围为100~600℃,有些国家的炭素厂对石墨电极的线膨胀系数测定温度范围比较低,有的是20~100℃,有的是30~130℃,因此同样产品在不同温度范围内测定的线膨胀系数不能直接比较。
石墨电极质量的优劣取决于原料性能、工艺技术、管理和生产装备4个方面,极的生产周期需70天以上。
而需要多次浸渍的接头生产周期更长。
(2)能源消耗较高,1t普通功率石墨电极需消耗电力6000kW•h左右,煤气或天然气数千立方米,冶金焦粒及冶金焦粉(二次能源)约1t。
(3)生产石墨电极工序多,需要许多专用机械设备和特殊结构的窑炉,建设投资较大、投资回收期较长。
(4)石墨电极生产过程产生一定数量的粉尘和有害气体,因此需要采取完善的通风降尘及消除有害气体的环境保护措施。
工艺流程生产石墨电极的工艺流程如图2所示,几个主要生产工序如下:(1)煅烧。