数控线切割机床常见问题39例
电火花线切割机床常见问题及故障说明

•电火花线切割机床常见问题及故障说明(四)三十一、线切割加工中短路处理简法在线切割机床加工过程中,而因排屑不畅造成短路的现象时有发生,特别在加工较厚工件时更为突出。
在操作中,可用溶济渗透清洗的方法消除短路,具体方法是:当短路发生时,先关断自动、高频开关,关掉工作液泵,用刷子蘸上渗透性较强的汽油、煤油、乙醇等溶剂,反复在工件两面随着运动的钼丝向切缝中渗透(要注意钼丝运动的方向)。
直至用改锥等工具在工件下端轻轻地沿着加工的反方向触动钼丝,工件上端的钼丝能随着移动即可。
然后,开启工作液泵和高频电源,依靠钼丝自身的颤动,恢复放电,继续加工。
三十二、断丝后原地穿丝处理断丝后步进电机应仍保持在“吸合”状态。
去掉较少一边废丝,把剩余钼丝调整到贮丝筒上的适当位置继续使用。
因为工件的切缝中充满了乳化液杂质和电蚀物,所以一定要先把工件表面擦干净,并在切缝中先用毛刷滴入煤油,使其润湿切缝,然后再在断点处滴一点润滑油一一这一点很重要。
选一段比较平直的钼丝,剪成尖头,并用打火机火焰烧烤这段钼丝,使其发硬,用医用镊子捏着钼丝上部,悠着劲在断丝点顺着切缝慢慢地每次2-3mm地往下送,直至穿过工件。
如果原来的钼丝实在不能再用的话,可更换新丝。
新丝在断丝点往下穿,要看原丝的损耗程度,(注意不能损耗太大)如果损耗较大,切缝也随之变小,新丝则穿不过去,这时可用一小片细纱纸把要穿过工件的那部分丝打磨光滑,再穿就可以了。
使用该方法可使机床的使用效率大为提高三十三、解决大厚度“紫铜件”切割断丝问题由于紫铜件不同于其它钢材料,当厚度超过50mm时,操作者如仍按加工钢材料工件时使用的电参数来加工,就会发生切割速度慢、电流不稳定、短路频繁、断丝等现象。
要正常加工采取的相应措施主要有:(1)不能使用已经用过较长时间的乳化液,尽量使用新乳化液。
并且最好采用JR-1A、JR-3A、JR-4、南光-I工作液。
因为铜材料粘,旧乳化液中的杂质较难冲掉,还会使紫铜加工时的导电性能受到影响。
线切割故障处理

电火花线切割常见问题的技术论述2010-6-24 1:54:38 苏州市常荣数控设备有限公司1{来源于网络}一、线切割“花丝”现象分析与解决一段时间的切割后,钼丝会出现一段一段的黑斑,黑斑通常有几到十几毫米长,黑斑的间隔通常有几到几十厘米。
黑斑是经过了一段时间的连续电弧放电,烧伤并碳化。
变细变脆和碳化后就很容易断。
黑斑在丝筒上形成一个个黑点,有时还按一定规率排列形成花纹,故称为“花丝”。
二、“花丝”现象的成因因不能有效消电离造成连续电弧放电,电弧的电阻热析出大量碳结成炭精粒,钼丝自己也被碳化。
工件较厚(放电间隙长)、水的介电系数低(恢复绝缘能力差)、脉冲源带有一个延迟灭弧的直流分量(大于10mA)这三者之一是“花丝”现象的基本条件。
放电间隙内带进(或工件内固有)一个影响火花放电的“杂质”是“花丝”现象的诱因。
“花丝”与火花放电加工的拉弧烧伤是同一道理,间隙内的拉弧烧伤一旦形成,工件和电极同时会被烧出蚀坑并结成炭精粒,炭精粒不清除干净就无法继续加工。
细小的炭精粒粘到那里,那里就要拉弧烧伤,面积越来越大,决无自行消除的可能性。
如果工件和电极发生位移,各自与对面都会导致新的拉弧烧伤,一处变两处。
唯一办法是人下手清理,而线切就无能为力了。
三、“花丝”的发生和发展在放电间隙长、蚀除物排出困难、恢复绝缘能力差、火花爆炸无力时,“杂质”很容易产生,电阻热迅速变拉弧烧伤,炭精粒也相拌而成,这个拉弧点随丝运动,其间每个脉冲能量都通过这个拉弧点释放,直到这个拉弧点走出工件,绝缘才有可能恢复,才有可能产生新的火花放电。
钼丝这个点的烧伤炭化(即黑斑)就形成了。
如果间隙内刚才诱发拉弧烧伤的那个点仍顽强存在,极容易与现在接触的钼丝点重复电弧放电,第二个烧伤炭化(即黑斑)点就又形成了。
所以那个点与工件出口的距离往往等于两黑斑间的距离。
自第一个烧伤炭化以后,丝上留了一个炭化点,工件间隙留了一串炭化点,极细的炭精粒播散到水里随时会进入间隙,它们都成了“花丝”的诱发因素。
典型电火花线切割数控机床的故障诊断与维修实例
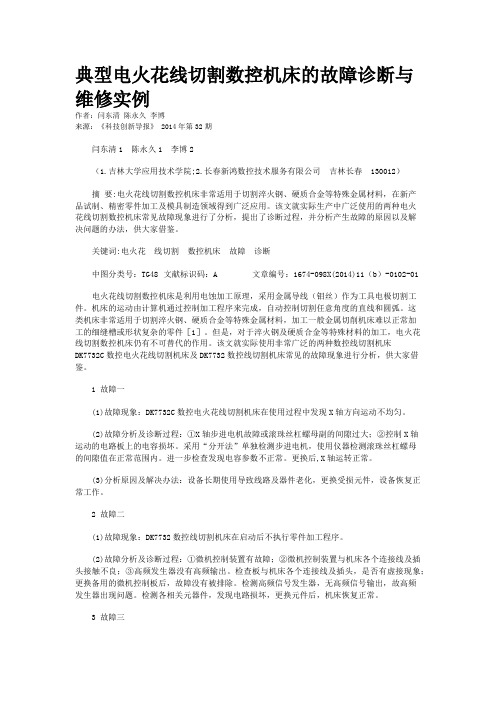
典型电火花线切割数控机床的故障诊断与维修实例作者:闫东清陈永久李博来源:《科技创新导报》 2014年第32期闫东清1 陈永久1 李博2(1.吉林大学应用技术学院;2.长春新鸿数控技术服务有限公司吉林长春 130012)摘要:电火花线切割数控机床非常适用于切割淬火钢、硬质合金等特殊金属材料,在新产品试制、精密零件加工及模具制造领域得到广泛应用。
该文就实际生产中广泛使用的两种电火花线切割数控机床常见故障现象进行了分析,提出了诊断过程,并分析产生故障的原因以及解决问题的办法,供大家借鉴。
关键词:电火花线切割数控机床故障诊断中图分类号:TG48 文献标识码:A 文章编号:1674-098X(2014)11(b)-0102-01电火花线切割数控机床是利用电蚀加工原理,采用金属导线(钼丝)作为工具电极切割工件。
机床的运动由计算机通过控制加工程序来完成,自动控制切割任意角度的直线和圆弧。
这类机床非常适用于切割淬火钢、硬质合金等特殊金属材料,加工一般金属切削机床难以正常加工的细缝槽或形状复杂的零件[1]。
但是,对于淬火钢及硬质合金等特殊材料的加工,电火花线切割数控机床仍有不可替代的作用。
该文就实际使用非常广泛的两种数控线切割机床DK7732C数控电火花线切割机床及DK7732数控线切割机床常见的故障现象进行分析,供大家借鉴。
1 故障一(1)故障现象:DK7732C数控电火花线切割机床在使用过程中发现X轴方向运动不均匀。
(2)故障分析及诊断过程:①X轴步进电机故障或滚珠丝杠螺母副的间隙过大;②控制X轴运动的电路板上的电容损坏。
采用“分开法”单独检测步进电机,使用仪器检测滚珠丝杠螺母的间隙值在正常范围内。
进一步检查发现电容参数不正常。
更换后,X轴运转正常。
(3)分析原因及解决办法:设备长期使用导致线路及器件老化,更换受损元件,设备恢复正常工作。
2 故障二(1)故障现象:DK7732数控线切割机床在启动后不执行零件加工程序。
线切割加工中常见问题及解决办法
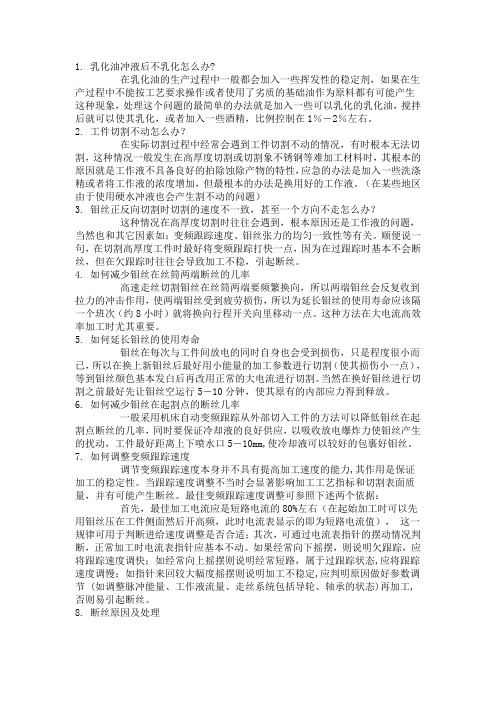
1. 乳化油冲液后不乳化怎么办?在乳化油的生产过程中一般都会加入一些挥发性的稳定剂,如果在生产过程中不能按工艺要求操作或者使用了劣质的基础油作为原料都有可能产生这种现象,处理这个问题的最简单的办法就是加入一些可以乳化的乳化油,搅拌后就可以使其乳化,或者加入一些酒精,比例控制在1%-2%左右。
2. 工件切割不动怎么办?在实际切割过程中经常会遇到工件切割不动的情况,有时根本无法切割,这种情况一般发生在高厚度切割或切割象不锈钢等难加工材料时,其根本的原因就是工作液不具备良好的拍除蚀除产物的特性,应急的办法是加入一些洗涤精或者将工作液的浓度增加,但最根本的办法是换用好的工作液。
(在某些地区由于使用硬水冲液也会产生割不动的问题)3. 钼丝正反向切割时切割的速度不一致,甚至一个方向不走怎么办?这种情况在高厚度切割时往往会遇到,根本原因还是工作液的问题,当然也和其它因素如:变频跟踪速度、钼丝张力的均匀一致性等有关。
顺便说一句,在切割高厚度工件时最好将变频跟踪打快一点,因为在过跟踪时基本不会断丝,但在欠跟踪时往往会导致加工不稳,引起断丝。
4. 如何减少钼丝在丝筒两端断丝的几率高速走丝切割钼丝在丝筒两端要频繁换向,所以两端钼丝会反复收到拉力的冲击作用,使两端钼丝受到疲劳损伤,所以为延长钼丝的使用寿命应该隔一个班次(约8小时)就将换向行程开关向里移动一点。
这种方法在大电流高效率加工时尤其重要。
5. 如何延长钼丝的使用寿命钼丝在每次与工件间放电的同时自身也会受到损伤,只是程度很小而已,所以在换上新钼丝后最好用小能量的加工参数进行切割(使其损伤小一点),等到钼丝颜色基本发白后再改用正常的大电流进行切割。
当然在换好钼丝进行切割之前最好先让钼丝空运行5-10分钟,使其原有的内部应力得到释放。
6. 如何减少钼丝在起割点的断丝几率一般采用机床自动变频跟踪从外部切入工件的方法可以降低钼丝在起割点断丝的几率,同时要保证冷却液的良好供应,以吸收放电爆炸力使钼丝产生的扰动,工件最好距离上下喷水口5-10mm,使冷却液可以较好的包裹好钼丝。
数控线切割机床故障排除三例

过程 中,阻值变化很大 ,进一步排查 ,发现 电液中,绝缘损坏 ,接触不 良导致 步进 电动机
缺相失步。
丝 本身 有锈 点,
优化设计的专用变频器 ,已经很好地 解决了换 向过程 中
断丝问题。④ 钼丝本身的问题。本例就是 设备长时间闲
置导致生锈发生断丝 。加工 中可 以根 据实际断丝发生的
位 置来具体对待 ,快速锁定故障部位。
差, 但是加工完毕还能返 回原点 的几率不大。 根据 图样 ,在该设备上手动输人一段程序 ,加工正
我厂一台 D 73B线切割机床 ,主要 用于加工模具 K70
检查用样板。笔者根据体会 ,将其常见故 障介绍如下。
1 故障一 .
设备 闲置一段 时间后 ,在未开始放电加工时断丝。
分析解决过程 :主要考虑钼丝传动过程 ( 图 1 , 见 )
从 贮 丝 筒 导 轮 一
一
分析是哪个轴的进给问题 。检查功放板 和信 号板 ,晶体
可能 与钼 丝 的 品 质有 关 ,更 换 钼
丝 后 , 正 常 非 加
6
7
故障现象时有时无 ,是实际处理故 障过 程中最难办 的事情 ,因为不知道故障出现 的时 机,所 以要 变换环境
不断地排查。引起步进电动机 失步 的原因很多 ,比如功
工 过程 中断 丝,
放板 、信号板等 ,另外 ,电磁干扰也是不得 不考虑的问
R H 4 3A 0 G 2 Y 0 3 A的 读 数 头 ,现 能 够 调 整 到 绿 色 灯 亮 , 但 N 系统 依 然 报 警 。利 用 示 波 器 并 参 考 另 外 一 台 正 常 C
数控线切割机报警断丝的故障分析及排除

数控线切割机报警断丝的故障分析及排除技术交流 2010年7月8日作者:刘远槐,高淑芹1 故障现象阿奇夏米尔240机床在正常切割中突出然现自动停机,屏幕出现“3376 WIRE BREAK”(断丝)报警信息,检查电极丝并没有断,只是丝完全处于放松状态。
取消报警信息,重新启动程序加工,几秒钟后又停机并重复出现断丝报警。
将电极丝从工件中退出,空载走丝运行正常。
重新对工件找正运行正常,再次启动加工按钮,立即出现电极丝跳动,几秒钟后又停机,重复显示断丝报警信息。
反复多次,故障依旧。
2 故障分析按照维修手册的提示:当电极丝在制动器皮带上打滑使走丝速度发生变化或走丝编码器的旋转速度与电极丝驱动电机的速度不同步时,屏幕就会显示“WIRE BREAK”(断丝)信息,并自动停机。
由此判定,可能是电极丝回路中某个器件(皮带、滑轮、制动器、导向器、加工头、压丝轮等)故障造成速度不稳,引起走丝与放丝不同步导致出现断丝报警并停机。
3 故障检查①对上下加工头的所有器件进行清洁处理,开机试加工,故障依旧;将加工头与另一台同样机床的加工头交换,故障仍然,说明该故障与加工头无关;②关闭机床电源,用手检查电极丝回路各滑轮的转动状况,并将电极丝穿过上加工头,用手拉动电极丝没有感觉到有明显的阻力点,说明电极丝没有被卡住;③将机床开启在空载走丝状态,用手向上抬平衡臂(放丝电机伺服控制),观察放丝电机旋转加快,说明放丝电机和伺服控制正常;④分别更换放丝电机走丝皮带和制动器皮带,同时调整蓝宝石导丝套、压丝轮后,开机试加工,故障依旧;⑤检查相关保险丝、断路器未发现异常。
至此,所有可能导致故障的因素都逐一排除,究竟是什么原因使走丝的速度不稳定,是否可能是走丝电机和走丝组件的问题?将走丝电机传动组件端盖打开,开机空载运行,观察电机及传动组件的转动情况,电机运转正常,但发现走丝轮与电机轴出现不同步现象,由此判定应该是皮带打滑或者走丝主动轮与电机轴的固定丝锥松动。
(整理)线切割常见问题50例
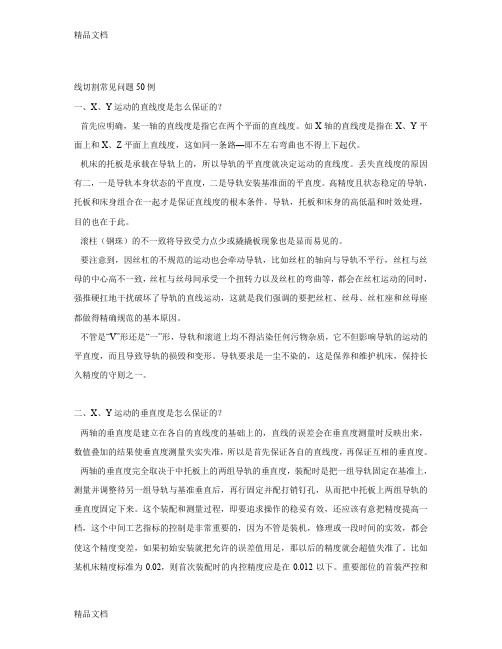
线切割常见问题50例一、X、Y运动的直线度是怎么保证的?首先应明确,某一轴的直线度是指它在两个平面的直线度。
如X轴的直线度是指在X、Y平面上和X、Z平面上直线度,这如同一条路—即不左右弯曲也不得上下起伏。
机床的托板是承载在导轨上的,所以导轨的平直度就决定运动的直线度。
丢失直线度的原因有二,一是导轨本身状态的平直度,二是导轨安装基准面的平直度。
高精度且状态稳定的导轨,托板和床身组合在一起才是保证直线度的根本条件。
导轨,托板和床身的高低温和时效处理,目的也在于此。
滚柱(钢珠)的不一致将导致受力点少或撬撬板现象也是显而易见的。
要注意到,因丝杠的不规范的运动也会牵动导轨,比如丝杠的轴向与导轨不平行,丝杠与丝母的中心高不一致,丝杠与丝母间承受一个扭转力以及丝杠的弯曲等,都会在丝杠运动的同时,强推硬扛地干扰破坏了导轨的直线运动,这就是我们强调的要把丝杠、丝母、丝杠座和丝母座都做得精确规范的基本原因。
不管是“V”形还是“一”形,导轨和滚道上均不得沾染任何污物杂质,它不但影响导轨的运动的平直度,而且导致导轨的损毁和变形。
导轨要求是一尘不染的,这是保养和维护机床,保持长久精度的守则之一。
二、X、Y运动的垂直度是怎么保证的?两轴的垂直度是建立在各自的直线度的基础上的,直线的误差会在垂直度测量时反映出来,数值叠加的结果使垂直度测量失实失准,所以是首先保证各自的直线度,再保证互相的垂直度。
两轴的垂直度完全取决于中托板上的两组导轨的垂直度,装配时是把一组导轨固定在基准上,测量并调整待另一组导轨与基准垂直后,再行固定并配打销钉孔,从而把中托板上两组导轨的垂直度固定下来。
这个装配和测量过程,即要追求操作的稳妥有效,还应该有意把精度提高一档,这个中间工艺指标的控制是非常重要的,因为不管是装机,修理或一段时间的实效,都会使这个精度变差,如果初始安装就把允许的误差值用足,那以后的精度就会超值失准了。
比如某机床精度标准为0.02,则首次装配时的内控精度应是在0.012以下。
二怎样提高线切割加工机床加工精度
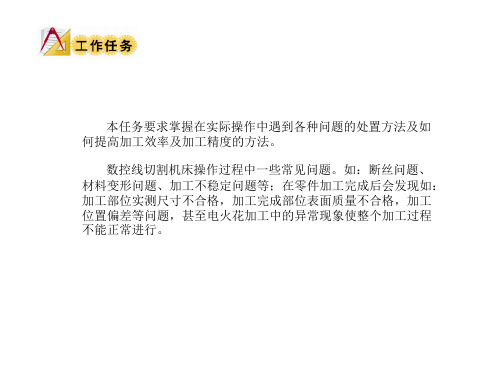
处理方法: ⑴ 调整电参数, 减小电流。(注意:刚切入时电流应适当调小,等
切入后, 工件侧壁面无火花时再增大电流) ⑵ 检查走丝系统部分, 如导轮、轴承、丝筒是否有异常跳动、振
动。 ⑶ 清除氧化皮,毛刺。
3.切割过程中突然断丝。 原因:
选择电参数不当,电流过大。 进给调节不当,忽快忽慢,开路短路频繁。 工作液使用不当, 如错误使用普通机床乳化液, 乳化液太稀,
⑸ 造成加工中不稳定的因素 稳定的加工是这样的:钼丝与工件相近运动,直到间隙被电离击 穿,火花放电会在极效应和热熔效应的作用下形成蚀除,冷却液的爆 炸和清洗作用,使蚀除物被迅速排出带走,新的或介电系数较高的冷 却液使间隙实现消电离恢复绝缘,间隙被扩大,钼丝与工件再作相近 运动。 干扰如上过程的任何因素都会造成加工不稳定。 归纳如下: 1、被切工件厚,蚀除物排出路程过长,水进入困难。 2、材料杂质,致使取样和间隙跟踪失灵失准。 3、水的爆炸,清洗,消电离能力差,有效成分少。 4、运丝速度和轨迹不稳定,间隙鉴别紊乱。 5、材料应力变形,局部弹性大,切缝的细微形变吃掉了放电间隙。 6、变频跟踪松紧不适,超出取样电压与变频速度的线性区较远。 7、坐标运动的阻滞,推力的积累(爬行),使放电间隙产生不确定性, 跟踪失实失准。 8、进电阻抗大或接触不良,取样不稳或距放电点较远。至使间隙辨别 有误。
㈣ 加工过程中材料变形问题 因为材料本身会有应力,切割肯定是打破了原有应力平衡变形后
达成了新的平衡,只是应力有大有小,变形也会大小不一。线切割加 工是同一道理,只是变形小到最终的精度范围以内,加工也就算完成 了。
应力是材料内固有的,随强度和硬度的提高而在加大的,暂时达
成平衡的一种弹性力。所以越是淬火硬的好材料变形越大。这类材料 要求淬火前的反复锻造,均匀组织。并把大量的加工余量和大块的废 料在淬火前就去掉,淬火后所切掉的是达成应力平衡的那一小部分。 这样因线切割造成的变形就会小得多。淬火前没做处理也没去除余量 的时候,也就是拿到的是一个具有强大且完整应力的一块实心料怎么 办?那就只好靠我们线切割自己消除应力,去除余量了。那就是粗切, 算记好留量,设置好夹头,把大部分的余量先去掉。拿到一个形状已 很接近最终工件,已不具有很大变形能力的新的毛坏,如果再附以高 低温的时效处理,材料变形就可算是彻底解决了。
数控线切割机床常见的电气故障及维修

前言随着社会和科学技术的发展,社会生产力的提高,数控设备越来越多地被用到机械加工中来。
了解这些设备的工作原理,及时准确地分析和排除设备故障是我们维修电工必须具备的技能。
数控线切割机床作为现代特种加工的一种重要的设备,它由高频脉冲电源、驱动电源、数控系统及机床电器等几部分组成。
如果不了解工作原理及工作过程,分不清这几者之间的关系对分析和排除机床故障来说将较困难。
本人通过多年对线切割机床的维修,听取了多位线切割操作工的好的建议,吸收了多位电工同行的维修经验,对线切割机床电气故障进行总结和分析,以便让初接触线切割电气维修者少走弯路。
数控线切割机床常见的电气故障及维修线切割数控机床是由高频脉冲对工件形成火花放电,加上切削液的冲洗作用,经数控系统对步进电机的控制拖动来进行加工工件。
线切割机床故障一般常见以下几大类:一是运丝筒故障;二是拖板运行故障;三是高频电源部分故障;四是频繁断丝故障。
由于线切割机床的数控系统,高频电源,驱动电源,机床电器这几部分相互联系,所以在了解了线切割机床工作原理情况下,依据机床电气原理图作全面分析,才能找出故障原因。
下面我以江苏锋陵DK7763型线切割数控机床为例作以分析。
运丝筒故障运丝筒故障主要有运丝筒不换向或丝筒冲出;运丝筒不运转或断丝后不停转。
一运丝筒不换向或运丝筒冲出。
运丝筒不换向是由于丝筒换向开关SQ1或SQ2故障,FU4、FU5其一烧坏使丝筒电机缺相,继电器KA1触点接触不良使丝筒电机缺相等几个原因造成(见附图一)。
丝筒冲出是在运丝筒电机不换向且限位开关SQ3未断开所至(见附图一)。
二运丝筒不运转或断丝后不停转。
此故障原因有多种情况,故障分析较复杂,且若断丝以后丝筒不停转将会使钼丝绕乱而造成不必要的损失。
分析附图一可知若电源和接触器KM2无故障,运丝筒启停是由SB1、KA3、SQ3、SB3、SB4触点决定,SB1、SB3、SB4是常闭或常开按钮,SQ3是限位开关,故障容易排除。
线切割加工中常见的故障及排除方法(zhangyan)
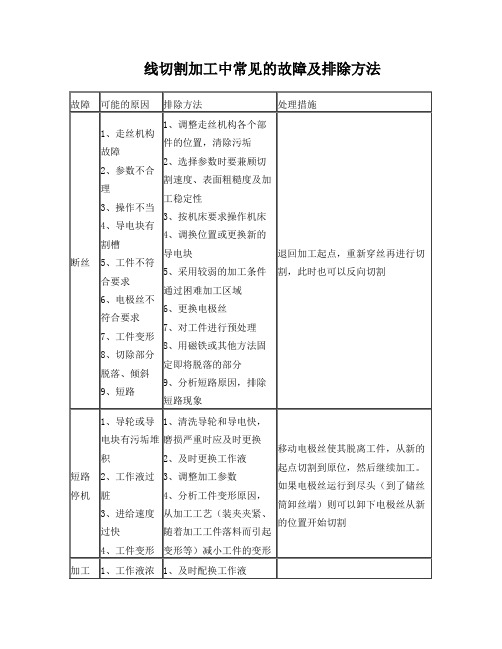
故障
可能的原因
排除方法
处理措施
断丝
1、走丝机构故障
2、参数不Leabharlann 理3、操作不当4、导电块有割槽
5、工件不符合要求
6、电极丝不符合要求
7、工件变形
8、切除部分脱落、倾斜
9、短路
1、调整走丝机构各个部件的位置,清除污垢
2、选择参数时要兼顾切割速度、表面粗糙度及加工稳定性
3、按机床要求操作机床
4、调换位置或更换新的导电块
5、采用较弱的加工条件通过困难加工区域
6、更换电极丝
7、对工件进行预处理
8、用磁铁或其他方法固定即将脱落的部分
9、分析短路原因,排除短路现象
退回加工起点,重新穿丝再进行切割,此时也可以反向切割
短路停机
1、导轮或导电块有污垢堆积
2、工作液过脏
3、进给速度过快
4、工件变形
1、清洗导轮和导电快,磨损严重时应及时更换
2、及时更换工作液
3、调整加工参数
4、分析工件变形原因,从加工工艺(装夹夹紧、随着加工工件落料而引起变形等)减小工件的变形
移动电极丝使其脱离工件,从新的起点切割到原位,然后继续加工。如果电极丝运行到尽头(到了储丝筒卸丝端)则可以卸下电极丝从新的位置开始切割
加工表面粗糙条纹较深
1、工作液浓度不符合要求
2、加工参数不合理
3、钼丝太松或张紧力过小
1、及时配换工作液
2、调整加工参数
3、紧丝或增加配重
切割精度差
1、机床x、y轴反向间隙较大(重复定位精度低)
2、钼丝变细
3、电极丝抖动
4、程序编制错误
1、调整轴承间隙或丝杠间隙
2、更换钼丝
线切割加工中常见问题处理

1.乳化油冲液后不乳化怎么办?在乳化油的生产过程中一般都会加入一些挥发性的稳定剂,如果在生产过程中不能按工艺要求操作或者使用了劣质的基础油作为原料都有可能产生这种现象,处理这个问题的最简单的办法就是加入一些可以乳化的乳化油,搅拌后就可以使其乳化,或者加入一些酒精,比例控制在1%-2%左右。
2.工件切割不动怎么办?在实际切割过程中经常会遇到工件切割不动的情况,有时根本无法切割,这种情况一般发生在高厚度切割或切割象不锈钢等难加工材料时,其根本的原因就是工作液不具备良好的拍除蚀除产物的特性,应急的办法是加入一些洗涤精或者将工作液的浓度增加,但最根本的办法是换用好的工作液。
(在某些地区由于使用硬水冲液也会产生割不动的问题)3.钼丝正反向切割时切割的速度不一致,甚至一个方向不走怎么办?这种情况在高厚度切割时往往会遇到,根本原因还是工作液的问题,当然也和其它因素如:变频跟踪速度、钼丝张力的均匀一致性等有关。
顺便说一句,在切割高厚度工件时最好将变频跟踪打快一点,因为在过跟踪时基本不会断丝,但在欠跟踪时往往会导致加工不稳,引起断丝。
4.如何减少钼丝在丝筒两端断丝的几率?高速走丝切割钼丝在丝筒两端要频繁换向,所以两端钼丝会反复收到拉力的冲击作用,使两端钼丝受到疲劳损伤,所以为延长钼丝的使用寿命应该隔一个班次(约8小时)就将换向行程开关向里移动一点。
这种方法在大电流高效率加工时尤其重要。
5.如何延长钼丝的使用寿命?钼丝在每次与工件间放电的同时自身也会受到损伤,只是程度很小而已,所以在换上新钼丝后最好用小能量的加工参数进行切割(使其损伤小一点),等到钼丝颜色基本发白后再改用正常的大电流进行切割。
当然在换好钼丝进行切割之前最好先让钼丝空运行5-10分钟,使其原有的内部应力得到释放。
6.如何减少钼丝在起割点的断丝几率?一般采用机床自动变频跟踪从外部切入工件的方法可以降低钼丝在起割点断丝的几率,同时要保证冷却液的良好供应,以吸收放电爆炸力使钼丝产生的扰动,工件最好距离上下喷水口5-10mm,使冷却液可以较好的包裹好钼丝。
数控电火花线切割机床常见电气故障及排除方法
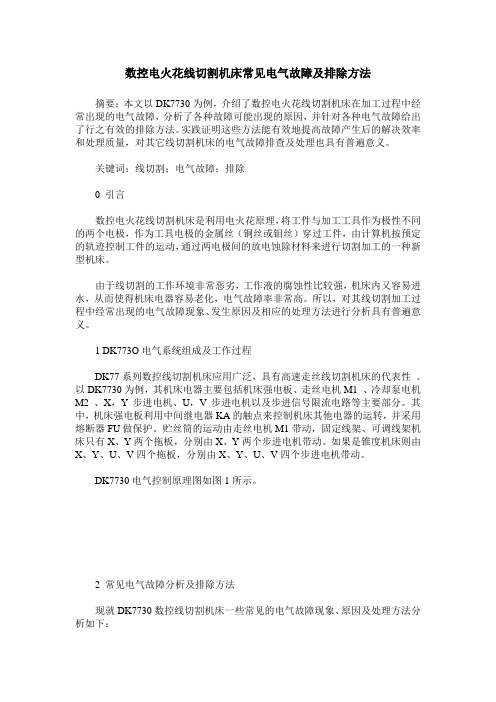
数控电火花线切割机床常见电气故障及排除方法摘要:本文以DK7730为例,介绍了数控电火花线切割机床在加工过程中经常出现的电气故障,分析了各种故障可能出现的原因,并针对各种电气故障给出了行之有效的排除方法。
实践证明这些方法能有效地提高故障产生后的解决效率和处理质量,对其它线切割机床的电气故障排查及处理也具有普遍意义。
关键词:线切割;电气故障;排除0 引言数控电火花线切割机床是利用电火花原理,将工件与加工工具作为极性不同的两个电极,作为工具电极的金属丝(铜丝或钼丝)穿过工件,由计算机按预定的轨迹控制工件的运动,通过两电极间的放电蚀除材料来进行切割加工的一种新型机床。
由于线切割的工作环境非常恶劣,工作液的腐蚀性比较强,机床内又容易进水,从而使得机床电器容易老化,电气故障率非常高。
所以,对其线切割加工过程中经常出现的电气故障现象、发生原因及相应的处理方法进行分析具有普遍意义。
1 DK773O电气系统组成及工作过程DK77系列数控线切割机床应用广泛,具有高速走丝线切割机床的代表性。
以DK7730为例,其机床电器主要包括机床强电板、走丝电机M1 、冷却泵电机M2 、X,Y步进电机、U,V步进电机以及步进信号限流电路等主要部分。
其中,机床强电板利用中间继电器KA的触点来控制机床其他电器的运转,并采用熔断器FU做保护。
贮丝筒的运动由走丝电机M1带动,固定线架、可调线架机床只有X、Y两个拖板,分别由X、Y两个步进电机带动。
如果是锥度机床则由X、Y、U、V四个拖板,分别由X、Y、U、V四个步进电机带动。
DK7730电气控制原理图如图1所示。
2 常见电气故障分析及排除方法现就DK7730数控线切割机床一些常见的电气故障现象、原因及处理方法分析如下:2.1 故障现象:走丝电机M1不正常工作2.1.1 故障现象:M1不能正转启动原因及故障排除(在断电情况下检修):a.SB5、SB6或KA4的触点接触不良。
采用电阻测量法,用万用表检测SB5两端电阻,若接近零则完好,若接近无穷大,则紧固或更换,同理检测KA4的触点。
数控线切割机床常见问题39例
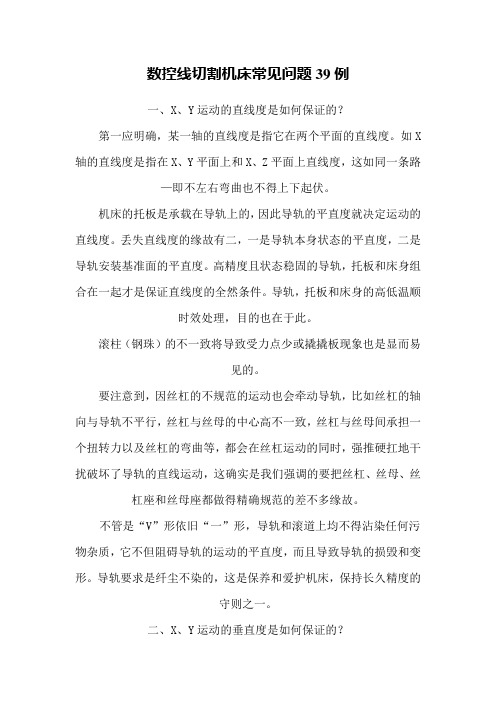
数控线切割机床常见问题39例一、X、Y运动的直线度是如何保证的?第一应明确,某一轴的直线度是指它在两个平面的直线度。
如X 轴的直线度是指在X、Y平面上和X、Z平面上直线度,这如同一条路—即不左右弯曲也不得上下起伏。
机床的托板是承载在导轨上的,因此导轨的平直度就决定运动的直线度。
丢失直线度的缘故有二,一是导轨本身状态的平直度,二是导轨安装基准面的平直度。
高精度且状态稳固的导轨,托板和床身组合在一起才是保证直线度的全然条件。
导轨,托板和床身的高低温顺时效处理,目的也在于此。
滚柱(钢珠)的不一致将导致受力点少或撬撬板现象也是显而易见的。
要注意到,因丝杠的不规范的运动也会牵动导轨,比如丝杠的轴向与导轨不平行,丝杠与丝母的中心高不一致,丝杠与丝母间承担一个扭转力以及丝杠的弯曲等,都会在丝杠运动的同时,强推硬扛地干扰破坏了导轨的直线运动,这确实是我们强调的要把丝杠、丝母、丝杠座和丝母座都做得精确规范的差不多缘故。
不管是“V”形依旧“一”形,导轨和滚道上均不得沾染任何污物杂质,它不但阻碍导轨的运动的平直度,而且导致导轨的损毁和变形。
导轨要求是纤尘不染的,这是保养和爱护机床,保持长久精度的守则之一。
二、X、Y运动的垂直度是如何保证的?两轴的垂直度是建立在各自的直线度的基础上的,直线的误差会在垂直度测量时反映出来,数值叠加的结果使垂直度测量失实失准,因此是第一保证各自的直线度,再保证互相的垂直度。
两轴的垂直度完全取决于中托板上的两组导轨的垂直度,装配时是把一组导轨固定在基准上,测量并调整待另一组导轨与基准垂直后,再行固定并配打销钉孔,从而把中托板上两组导轨的垂直度固定下来。
那个装配和测量过程,即要追求操作的稳妥有效,还应该有意把精度提高一档,那个中间工艺指标的操纵是专门重要的,因为不管是装机,修理或一段时刻的实效,都会使那个精度变差,假如初始安装就把承诺的误差值用足,那以后的精度就会超值失准了。
比如某机床精度标准为0.02,则首次装配时的内控精度应是在0.012以下。
- 1、下载文档前请自行甄别文档内容的完整性,平台不提供额外的编辑、内容补充、找答案等附加服务。
- 2、"仅部分预览"的文档,不可在线预览部分如存在完整性等问题,可反馈申请退款(可完整预览的文档不适用该条件!)。
- 3、如文档侵犯您的权益,请联系客服反馈,我们会尽快为您处理(人工客服工作时间:9:00-18:30)。
数控线切割机床常见问题39例一、X、Y运动的直线度是怎么保证的?首先应明确,某一轴的直线度是指它在两个平面的直线度。
如X 轴的直线度是指在X、Y平面上和X、Z平面上直线度,这如同一条路—即不左右弯曲也不得上下起伏。
机床的托板是承载在导轨上的,所以导轨的平直度就决定运动的直线度。
丢失直线度的原因有二,一是导轨本身状态的平直度,二是导轨安装基准面的平直度。
高精度且状态稳定的导轨,托板和床身组合在一起才是保证直线度的根本条件。
导轨,托板和床身的高低温和时效处理,目的也在于此。
滚柱(钢珠)的不一致将导致受力点少或撬撬板现象也是显而易见的。
要注意到,因丝杠的不规范的运动也会牵动导轨,比如丝杠的轴向与导轨不平行,丝杠与丝母的中心高不一致,丝杠与丝母间承受一个扭转力以及丝杠的弯曲等,都会在丝杠运动的同时,强推硬扛地干扰破坏了导轨的直线运动,这就是我们强调的要把丝杠、丝母、丝杠座和丝母座都做得精确规范的基本原因。
不管是“V”形还是“一”形,导轨和滚道上均不得沾染任何污物杂质,它不但影响导轨的运动的平直度,而且导致导轨的损毁和变形。
导轨要求是一尘不染的,这是保养和维护机床,保持长久精度的守则之一。
二、X、Y运动的垂直度是怎么保证的?两轴的垂直度是建立在各自的直线度的基础上的,直线的误差会在垂直度测量时反映出来,数值叠加的结果使垂直度测量失实失准,所以是首先保证各自的直线度,再保证互相的垂直度。
两轴的垂直度完全取决于中托板上的两组导轨的垂直度,装配时是把一组导轨固定在基准上,测量并调整待另一组导轨与基准垂直后,再行固定并配打销钉孔,从而把中托板上两组导轨的垂直度固定下来。
这个装配和测量过程,即要追求操作的稳妥有效,还应该有意把精度提高一档,这个中间工艺指标的控制是非常重要的,因为不管是装机,修理或一段时间的实效,都会使这个精度变差,如果初始安装就把允许的误差值用足,那以后的精度就会超值失准了。
比如某机床精度标准为0.02,则首次装配时的内控精度应是在0.012以下。
重要部位的首装严控和销钉镙钉稳妥有效,加之导轨本身的平直精准,两轴的垂直度就有保证了。
如同直线度一样,丝杠的工作状态也是影响垂直度的重要因素。
与导轨定位面成一定夹角的任何一个外力,都将造成导轨的异动,因为导轨只是导轨,并没有夹死。
所以一旦发现X、Y轴的垂直度超标,要认真判断是导轨自身的形变或错位造成的还是丝杠的运动干扰的。
如果是导轨的导向作用所致,分别在几个位置使丝杠和丝母重复松开再紧固的适配过程,其超标的方向和数值应大体稳定的。
如果是丝杠和丝母运动的干扰所致,将失去方向和数值的规律性。
千万不可盲目把导轨的固定松开,把销钉拨掉,失去判断的任何操作都是无益的。
一旦导轨的固定松开销钉拨掉,就必须重复前面所述首次装调的全过程。
任何测量调整都必须在导轨运动平稳之后再进行,如果突跳和无规律的扭摆,那是导轨太脏或异物,要坚决拭净润滑之后再进行调整,这是必须牢记的。
三、座标位移的误差是怎样产生的?单轴直线度,XY垂直度和系统回差是造成误差的主要原因。
快走丝线切割机,都没实现闭环控制,机械传动系统的回差已成为整机精度的最重要的指标,回差大体来自如下5个方面。
齿轮间隙,主要是步进电机与丝杠间的传动齿轮。
连接键的间隙,特别是丝杠上的大齿轮,点滴的间隙在回差上的反应都是不可忽视的。
电机轴键间隙的影响不仅有回差,还拌有噪音。
丝杠与丝母间的间隙,出厂后丝杠付的轴向传动间隙通常在0.003以下,质差的产品则不太有保证。
丝杠轴承间隙,这个间隙是靠轴承的内外环的轴向调整消除的,但如果轴承质量低劣,会在消除间隙后转动极不灵活,一旦转动轻快了就又有间隙了,所以该处的轴承是不可马虎的。
力矩传递的整体刚性较差,造成柔弱部位的挠性变形使运动变得迟钝滞后,也以间隙的方式体现出来。
以上5个方面,共同造成了系统回差,实际加工中,即使是最简单的封闭图形,也至少有两次排除回差,所以实际加工精度一般在不可消除的回差的两倍左右。
如果系统回差是0.006,那么加工精度在0。
012是有可能的。
两轴的垂直度和各轴的直线度是造成位移失真失准另一主要原因。
位移失真失准就是误差。
只是这个误差的量是随机的,难以估算的。
四、行业标准为什么用切八方来判定机床精度?用切八方判定机床的精度,是一个很好的办法。
它可以很全面地反映出机床座标位移精度,导轮运转的平稳性,X、Y的系统回差和进给与实际位移的保真度。
机床存在的与精度相关的任何毛病在切八方时都被体现出来,是无法人为地掩饰的。
切得的八方应按如下几个方面来分析:与X轴平行的两个直面,尺寸偏小且进给速度慢,说明导轮轴向偏摆抖晃比较大,切缝变大。
与Y轴平行的两个直面,尺寸偏小且进给速度慢,说明导轮径向偏摆抖晃幅度大,切逢度变大。
450两个平行斜面,尺寸偏小,说明Y轴系统回差大,差值约为两倍的回差。
1350两个平行斜面,尺寸偏小,说明X轴系统回差大,差值约为两倍的回差。
450和1350斜面上出现以丝杠螺距为周期的搓板纹,X或Y轴出现进给位移的失真度,说明X或Y轴丝杠推动托板的工作端面出现跳动或失真。
这种纹理和周期的关系只能在450和1350斜面上发现。
450和1350斜面上以电机齿轮为周期的搓板纹,说明电机齿轮的不等分或偏心,这种毛病切直线看不见,切圆也辩不清它的周期关系。
与X轴平行的两直面搓板纹重,说明丝上下运行时在Y轴方向不走一条轨迹。
(上下导轮“V”形槽的延长线不是一条线,所以丝换向为周期的搓板纹。
)与Y轴平行的两直面搓板纹重,说明的上下行时在X方向不走一条道,上下行时张力有较大的差异。
(以丝换向为周期的搓板纹。
)450斜面与1350斜面所夹的角大于或小于900,说明X、Y导轨的垂直度差,它造成四个直面间不垂直但对面能平行,其差值约为该行程内垂直度误差的两倍。
切割面上下两头的不一致,说明上下导轮中有一个其“V”形槽对钼丝的定位作用明显变差。
如上所述,切其它任何形状,都很难把这些都清淅地暴露出来。
故切八方确实是检验机床全面精度的好办法。
但用八方来判定机床精度,一定要注意如下几点:防止切割路线或材料本身的变形。
切割方向和上下面要作好标记。
八方中途不得再调任何一项工艺参数或变频速度。
一次完成,中途不得停机。
要校正钼丝,保证它的垂直度。
不得设置齿隙,间隙补偿。
五、切割效率还能再高吗?切割效率受两大因素的影响,一是丝的载流量(电流),二是切缝中的蚀除物不能及时清除,它的导电作用消耗掉了脉冲能量。
总之,总能量,能量利用率都是切割效率的问题。
?业内就钼材料快速走丝机床的切割效率作过许多的典型试验,结果证明,钼丝载流量达到150A/mm2时,其抗拉强度将被降低到原有强度的1/3~1/4,这个电流值被视作钼丝载流供作切割的极限,以此算来,Ф0.12载流1.74A,Ф0.15载流2.65A, Ф0.18载流3.82A 时即达到了切割钼丝的极限值。
再加大载流量,无疑丝的寿命将是短暂的。
在丝速 10米/秒,北京油脂化工厂的DX-1冷却液,切厚度为50的普通钢,脉宽32MS。
脉间200MS时,用蚀除物的体积来计算切割效率则为5.8mm3/分.A。
用此效率计算,不同粗细的钼丝工作在最大载流量时的面积切割效率为Ф0.12---70.43mm2/分,Ф0.15---90.41mm2/分,.如此算来,丝经加粗即可加大载流量,电流大了效率也可相应提高。
但是,快速往复走丝的线切割是不允许(排丝,挠度,损耗等原因)把丝径加大到0.23以上的.,且因蚀除物排出速度所限,当电流加大到均值8A时,间隙将出现短路或电孤放电,免强维持的短时火花放电也将使钼丝损耗急剧增加,所以一味增粗丝加大电流的办法是不可取的。
.蚀除物在间隙中所呈现的是电阻负载的作用,它短路掉了经钼丝向间隙提供的一部分能量,所以当切割料加厚,蚀除物排出更为困难的时候,能量损失的多,有效的加工脉冲会更少,放电电流变成了线性负载电流,形不成加工而只加热了钼丝,这是能量被损失和断丝的主要原因。
针对影响加工效率的两大主要原因,提高加工速度则应在如下几个方面作相应的努力:加大单个脉冲的能量,即脉冲幅值和峰值电流,为不使丝的载流量负担过大,则应相应加大脉冲间隔,使电流平均值不致增加太多。
保持冷却液的介电系数和绝缘强度,维持较高的火花爆炸力和清洗能力,使蚀除物对脉冲的短路作用减到最小。
提高运丝导丝系统的机械精度,因为窄缝总比宽缝走得快,直缝总比折线缝走得快。
适当地提高丝速,使丝向缝隙内带入的水速加快,水量加大,蚀除物更有效地排出。
增加水在缝隙外对丝的包络性,即让水在丝的带动下起速,起速的水对间隙的清洗作用是较强的。
改善变频跟踪灵敏度,增加脉冲利用率。
减少走丝电机的换向时间,启动更快,增加有效的加工时间。
经上述努力,把切割效率提高到100~120mm2/分钟是可能的,是有实际意的,至于把指标提得更高,则是以牺牲可靠性和连续加工时间作代价的。
六,换向条纹能完全去掉吗?由电蚀原理决定,放电电离产生高温,液内的碳氢化合物被热分解产生大量的碳黑,在电场的作用下,镀覆于阳极。
这一现象在电火花成型加工中被利用作电极的补偿。
而线切割中,一部分被丝带出缝隙,也总有一部分镀覆于工件表面,其特点是丝的入口处少,而丝的出口处多。
这就是产生犬牙状黑白交错条纹的原因。
这种镀层的附着度随工件主体与放电通道间的温差变化,也与极间电场强度有关。
就是说,镀覆碳黑的现象是电蚀加工的伴生物,只要有加工就会有条纹。
碳黑附着层的厚度通常是0.01~2μ,因放电凹坑的峰谷间都有,所以擦掉是很困难的,要随着表面的抛光和凹坑的去除才能彻底打磨干净。
只要不是伴随着切割面的搓板状,没有形状的凸凹仅仅是碳黑的附着,可不必大感烦脑。
因为切割效率,尺寸精度,金属基体的光洁度才是我们所追求的。
为使视觉效果好一些,设法使条纹浅一点,可以从以下几个方面同时着手,即冷却液稍稀些、稍旧一些,加工电压降低一点,变频跟踪更紧一点等。
要彻底没有条纹,则要把产生条纹的条件全部铲除,即丝不换向,液内无乳化的碳氢物改用纯水,这样我们快走丝线切割的主要优越也就没了。
目前去掉换向条纹最有效的办法仍然是多次切割,就沿轮廓线留量0.005~0.02,切割轨迹修正后再切一遍,不留量沿上次轨迹再重复一遍,这样的重复切割,伴随脉冲加工参数的调整,会把换向的条纹完全去除干净,且把加工精度和光洁度都提高一等。
重复切割的最基本条件是机床有足购的重复定位精度和操作的可重复性。
当然还要有操作者的明确思路和准确操作。
七、搓板纹是怎么产生的?随着钼丝的一次换向,切割面产生一次凸凹,在切割面上出现富于规律的搓板状,通常直称为“搓板纹”。
如果不仅仅是黑白颜色的换向条纹,产生有凸凹尺寸差异,这是不能允许的。
应在如下几处找原因:丝松或丝筒两端丝松紧有明显差异,这造成了运行中的丝大幅抖摆,换向瞬间明显的挠性弯曲。