塑胶件设计准则(较全)
塑胶结构设计规范
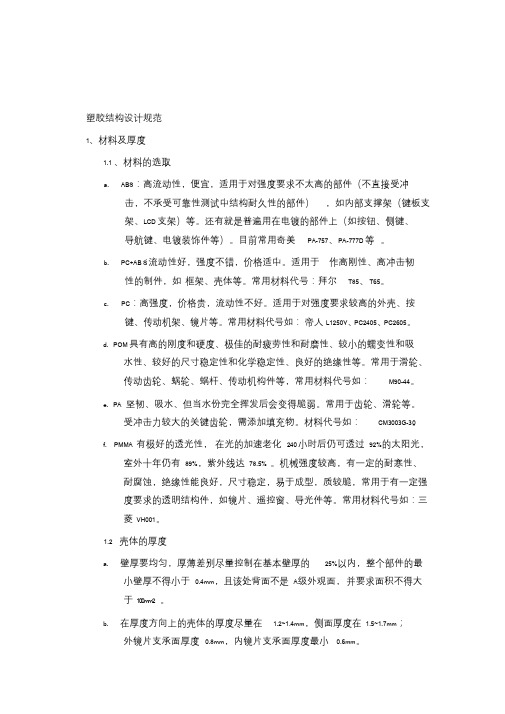
塑胶结构设计规范1、材料及厚度1.1 、材料的选取a. ABS:高流动性,便宜,适用于对强度要求不太高的部件(不直接受冲击,不承受可靠性测试中结构耐久性的部件),如内部支撑架(键板支架、LCD支架)等。
还有就是普遍用在电镀的部件上(如按钮、侧键、导航键、电镀装饰件等)。
目前常用奇美PA-757、PA-777D等。
b. PC+AB:S 流动性好,强度不错,价格适中。
适用于作高刚性、高冲击韧性的制件,如框架、壳体等。
常用材料代号:拜尔T85、T65。
c. PC:高强度,价格贵,流动性不好。
适用于对强度要求较高的外壳、按键、传动机架、镜片等。
常用材料代号如:帝人L1250Y、PC2405、PC2605。
d. POM具有高的刚度和硬度、极佳的耐疲劳性和耐磨性、较小的蠕变性和吸水性、较好的尺寸稳定性和化学稳定性、良好的绝缘性等。
常用于滑轮、传动齿轮、蜗轮、蜗杆、传动机构件等,常用材料代号如:M90-44。
e. PA 坚韧、吸水、但当水份完全挥发后会变得脆弱。
常用于齿轮、滑轮等。
受冲击力较大的关键齿轮,需添加填充物。
材料代号如:CM3003G-3。
0f. PMMA 有极好的透光性,在光的加速老化240小时后仍可透过92%的太阳光,室外十年仍有89%,紫外线达78.5% 。
机械强度较高,有一定的耐寒性、耐腐蚀,绝缘性能良好,尺寸稳定,易于成型,质较脆,常用于有一定强度要求的透明结构件,如镜片、遥控窗、导光件等。
常用材料代号如:三菱VH001。
1.2 壳体的厚度a. 壁厚要均匀,厚薄差别尽量控制在基本壁厚的25%以内,整个部件的最小壁厚不得小于0.4mm,且该处背面不是A级外观面,并要求面积不得大于100mm2 。
b. 在厚度方向上的壳体的厚度尽量在 1.2~1.4mm,侧面厚度在1.5~1.7mm;外镜片支承面厚度0.8mm,内镜片支承面厚度最小0.6mm。
c. 电池盖壁厚取0.8~1.0mm。
d. 塑胶制品的最小壁厚及常见壁厚推荐值见下表。
塑料件设计规则
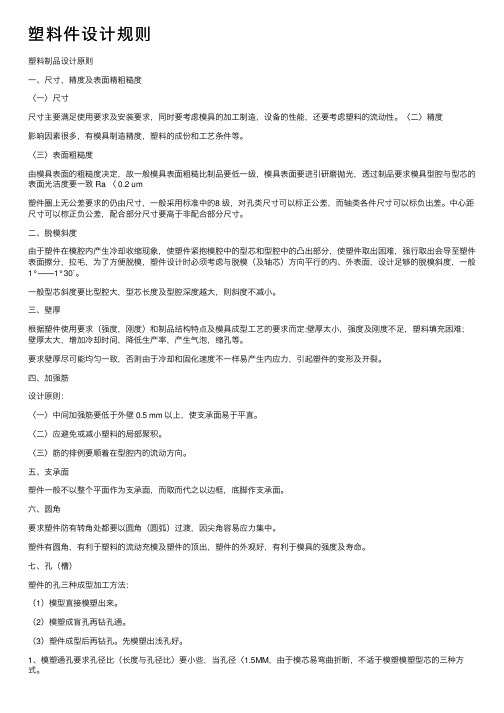
塑料件设计规则塑料制品设计原则⼀、尺⼨,精度及表⾯精粗糙度〈⼀〉尺⼨尺⼨主要满⾜使⽤要求及安装要求,同时要考虑模具的加⼯制造,设备的性能,还要考虑塑料的流动性。
〈⼆〉精度影响因素很多,有模具制造精度,塑料的成份和⼯艺条件等。
〈三〉表⾯粗糙度由模具表⾯的粗糙度决定,故⼀般模具表⾯粗糙⽐制品要低⼀级,模具表⾯要进引研磨抛光,透过制品要求模具型腔与型芯的表⾯光洁度要⼀致 Ra 〈 0.2 um塑件圈上⽆公差要求的仍由尺⼨,⼀般采⽤标准中的8 级,对孔类尺⼨可以标正公差,⽽轴类各件尺⼨可以标负出差。
中⼼距尺⼨可以棕正负公差,配合部分尺⼨要⾼于⾮配合部分尺⼨。
⼆、脱模斜度由于塑件在模腔内产⽣冷却收缩现象,使塑件紧抱模腔中的型芯和型腔中的凸出部分,使塑件取出困难,强⾏取出会导⾄塑件表⾯擦分,拉⽑,为了⽅便脱模,塑件设计时必须考虑与脱模(及轴芯)⽅向平⾏的内、外表⾯,设计⾜够的脱模斜度,⼀般1°——1°30`。
⼀般型芯斜度要⽐型腔⼤,型芯长度及型腔深度越⼤,则斜度不减⼩。
三、壁厚根据塑件使⽤要求(强度,刚度)和制品结构特点及模具成型⼯艺的要求⽽定:壁厚太⼩,强度及刚度不⾜,塑料填充困难;壁厚太⼤,增加冷却时间,降低⽣产率,产⽣⽓泡,缩孔等。
要求壁厚尽可能均匀⼀致,否则由于冷却和固化速度不⼀样易产⽣内应⼒,引起塑件的变形及开裂。
四、加强筋设计原则:〈⼀〉中间加强筋要低于外壁 0.5 mm 以上,使⽀承⾯易于平直。
〈⼆〉应避免或减⼩塑料的局部聚积。
〈三〉筋的排例要顺着在型腔内的流动⽅向。
五、⽀承⾯塑件⼀般不以整个平⾯作为⽀承⾯,⽽取⽽代之以边框,底脚作⽀承⾯。
六、圆⾓要求塑件防有转⾓处都要以圆⾓(圆弧)过渡,因尖⾓容易应⼒集中。
塑件有圆⾓,有利于塑料的流动充模及塑件的顶出,塑件的外观好,有利于模具的强度及寿命。
七、孔(槽)塑件的孔三种成型加⼯⽅法:(1)模型直接模塑出来。
(2)模塑成盲孔再钻孔通。
一文看懂塑胶产品结构设计准则

一文看懂塑胶产品结构设计准则塑胶产品结构设计准则是指在设计塑胶制品时应遵循的一些原则和指导方针,以确保产品具有较好的结构设计、性能和品质。
下面一文将从以下几个方面对塑胶产品结构设计准则进行说明。
一、结构合理性塑胶制品的结构合理性是指在产品的设计中,结构要简洁、紧凑,且能够满足产品的功能要求。
合理的结构设计可以减少零件的数量,简化加工工艺,提高生产效率和降低成本。
此外,结构还应考虑产品的使用要求和使用环境,以确保产品具有较好的使用性能。
二、材料选择在塑胶制品的结构设计中,材料的选择是至关重要的。
合适的材料能够提供较好的强度和耐用性,同时还要满足产品的外观和质感要求。
在材料选择时,要考虑产品的功能要求,包括承受的载荷、环境条件等。
此外,还要考虑材料的加工性能和成本,以确保产品的可制造性和经济性。
三、模具设计塑胶制品的模具设计是确保产品质量和生产效率的重要一环。
模具的设计应考虑产品的结构和外观要求,以及材料的特性和加工工艺。
合理的模具设计可以减少产品的缺陷和变形,提高产品的一致性和精度。
此外,还要注重模具的维护和保养,以延长模具的使用寿命。
四、设计审查设计审查是确保产品设计合理性和质量的重要手段。
设计审查应包括结构设计、材料选择、模具设计等方面。
通过设计审查,可以发现和解决产品设计过程中存在的问题,提高产品的设计质量和可制造性。
五、设计创新在塑胶产品的结构设计中,要注重创新。
创新的设计可以提高产品的竞争力和市场价值。
设计人员应不断学习和积累经验,结合市场需求和技术发展趋势,推进产品的技术创新和结构创新。
总之,塑胶产品结构设计准则是指在设计塑胶制品时应遵循的一系列原则和指导方针。
合理的结构设计、材料选择、模具设计以及设计创新都是塑胶产品结构设计中需要关注的重要方面。
通过遵循这些准则,可以确保塑胶产品具有较好的结构设计、性能和品质。
塑胶件设计准则较全
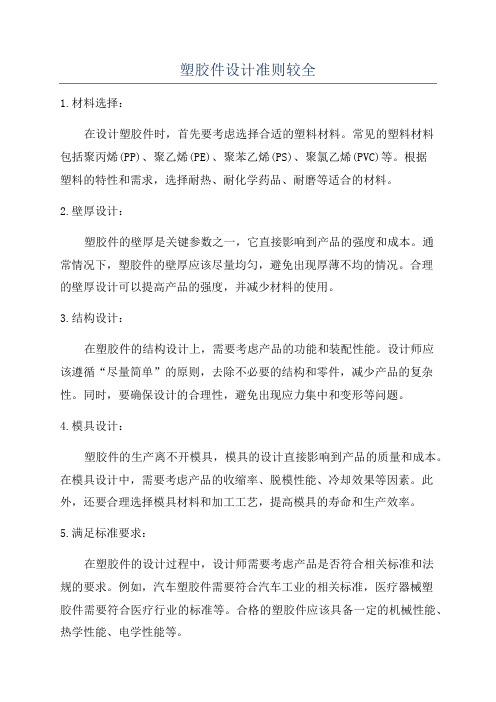
塑胶件设计准则较全1.材料选择:在设计塑胶件时,首先要考虑选择合适的塑料材料。
常见的塑料材料包括聚丙烯(PP)、聚乙烯(PE)、聚苯乙烯(PS)、聚氯乙烯(PVC)等。
根据塑料的特性和需求,选择耐热、耐化学药品、耐磨等适合的材料。
2.壁厚设计:塑胶件的壁厚是关键参数之一,它直接影响到产品的强度和成本。
通常情况下,塑胶件的壁厚应该尽量均匀,避免出现厚薄不均的情况。
合理的壁厚设计可以提高产品的强度,并减少材料的使用。
3.结构设计:在塑胶件的结构设计上,需要考虑产品的功能和装配性能。
设计师应该遵循“尽量简单”的原则,去除不必要的结构和零件,减少产品的复杂性。
同时,要确保设计的合理性,避免出现应力集中和变形等问题。
4.模具设计:塑胶件的生产离不开模具,模具的设计直接影响到产品的质量和成本。
在模具设计中,需要考虑产品的收缩率、脱模性能、冷却效果等因素。
此外,还要合理选择模具材料和加工工艺,提高模具的寿命和生产效率。
5.满足标准要求:在塑胶件的设计过程中,设计师需要考虑产品是否符合相关标准和法规的要求。
例如,汽车塑胶件需要符合汽车工业的相关标准,医疗器械塑胶件需要符合医疗行业的标准等。
合格的塑胶件应该具备一定的机械性能、热学性能、电学性能等。
6.通气设计:塑胶件在注塑过程中需要排除气体,否则会产生气泡和内部缺陷。
因此,在塑胶件的设计中,需要考虑通气的问题。
设计师可以在塑胶件的壁厚较大的地方设置气脱模系统,提高产品的质量。
7.可回收性设计:在现代社会,环保意识日益增强,可回收性成为塑胶件设计的一个重要考虑因素。
设计师应该尽量选择可回收的塑料材料,并设计可分解、可回收利用的产品。
总结起来,塑胶件设计准则涉及到材料选择、壁厚设计、结构设计、模具设计、标准要求、通气设计和可回收性设计等方面。
设计师在进行塑胶件设计时,应根据具体的产品需求和行业要求,合理应用这些准则,确保塑胶件的质量和性能,提高产品的竞争力。
塑胶件设计规范范文
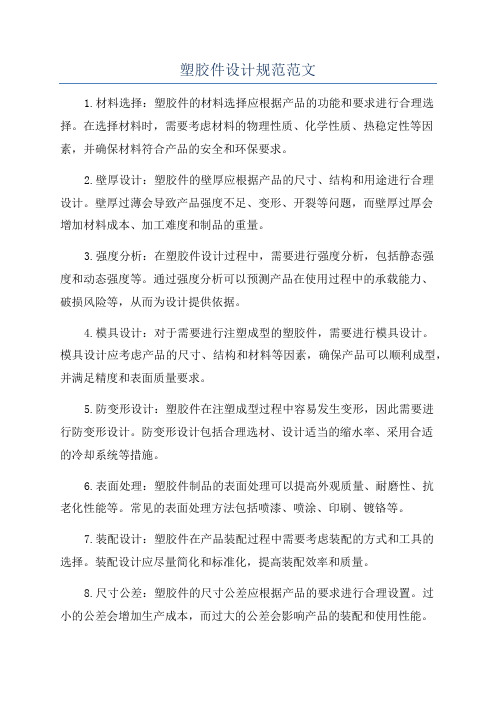
塑胶件设计规范范文1.材料选择:塑胶件的材料选择应根据产品的功能和要求进行合理选择。
在选择材料时,需要考虑材料的物理性质、化学性质、热稳定性等因素,并确保材料符合产品的安全和环保要求。
2.壁厚设计:塑胶件的壁厚应根据产品的尺寸、结构和用途进行合理设计。
壁厚过薄会导致产品强度不足、变形、开裂等问题,而壁厚过厚会增加材料成本、加工难度和制品的重量。
3.强度分析:在塑胶件设计过程中,需要进行强度分析,包括静态强度和动态强度等。
通过强度分析可以预测产品在使用过程中的承载能力、破损风险等,从而为设计提供依据。
4.模具设计:对于需要进行注塑成型的塑胶件,需要进行模具设计。
模具设计应考虑产品的尺寸、结构和材料等因素,确保产品可以顺利成型,并满足精度和表面质量要求。
5.防变形设计:塑胶件在注塑成型过程中容易发生变形,因此需要进行防变形设计。
防变形设计包括合理选材、设计适当的缩水率、采用合适的冷却系统等措施。
6.表面处理:塑胶件制品的表面处理可以提高外观质量、耐磨性、抗老化性能等。
常见的表面处理方法包括喷漆、喷涂、印刷、镀铬等。
7.装配设计:塑胶件在产品装配过程中需要考虑装配的方式和工具的选择。
装配设计应尽量简化和标准化,提高装配效率和质量。
8.尺寸公差:塑胶件的尺寸公差应根据产品的要求进行合理设置。
过小的公差会增加生产成本,而过大的公差会影响产品的装配和使用性能。
9.耐用性设计:塑胶件在使用过程中需要具有一定的耐用性。
耐用性设计包括选择合适的材料、优化结构、进行耐久性测试等。
10.产品标识:塑胶件在制造过程中需要进行产品标识,包括产品型号、批次号、生产厂家等信息。
产品标识有助于产品追溯和质量控制。
请注意,以上只是一些常见的塑胶件设计规范,具体的设计规范还需根据具体产品和行业的要求来确定。
在进行塑胶件设计时,还需充分考虑产品的使用环境、工艺要求和成本等因素,确保产品的质量和可生产性。
塑料件设计准则
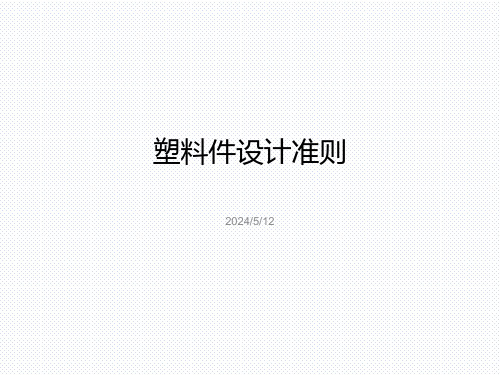
2024/5/12
目录
一. 壁厚均匀原则 二. 加强筋设计原则 三. 倒角原则 四. 拔模原则 五. 形状和结构的简化 六. 避免应力集中 七. 加强刚度的设计 八. 抗变形设计
一.壁厚均匀原则
• 在确定壁厚尺寸时,壁厚均一是一个重要原则。该原则主要是从工艺角度以 及由工艺导致的质量方面的问题而提出来的。均匀的壁厚可使制件在成型过 程中,熔体流动性均衡,冷却均衡。壁薄部位在冷却收缩上的差异,会产生 一定的收缩应力,内应力会导致制件在短期之内或经过一个较长时期之后发 生翘曲变形。
壳体/盒状体 一般≥1.5°;
皮纹面
细皮纹≥3.5° 粗皮纹≥5°
注:皮纹区域在设计数模前必须定义,由客户定义或我们定义客户确认,皮纹状态为客户输入,且必须输入
如出现客户未定义,皮纹面按5°执行,并与客户报警。
四 . 拔模原则
拔模角设计参考 塑胶产品在设计上通常会为了能够轻易的使产品由模具脱离出来而需要在边缘的内侧和外侧各设有一个倾斜角”出模角〔。 若然产品附有垂直外壁并且与开模方向相同的话,则模具在塑料成型後需要很大的开模力才能打开,而且,在模具开启後, 产品脱离模具的过程亦相信十分困难。要是该产品在产品设计的过程上已预留出模角及所有接触产品的模具零件在加工过程 当中经过高度抛光的话,脱模就变成轻而易举的事情。因此,出模角的考虑在产品设计的过程是不可或缺的 因注塑件冷却收缩後多附在凸模上,为了使产品壁厚平均及防止产品在开模後附在较热的凹模上,出模角对应於凹模及凸模 是应该相等的。不过,在特殊情况下若然要求产品於开模後附在凹模的话,可将相接凹模部份的出模角尽量减少,或刻意在 凹模加上适量的倒扣位。 出模角的大小是没有一定的准则,多数是凭经验和依照产品的深度来决定。此外,成型的方式,壁厚和塑料的选择也在考虑 之列。一般来说,高度抛光的外壁可使用1/8度或1/4度的出模角。深入或附有织纹的产品要求出模角作相应的增加,习惯上 每0.025mm深的织纹,便需要额外1度的出模角。
塑胶产品结构设计准则
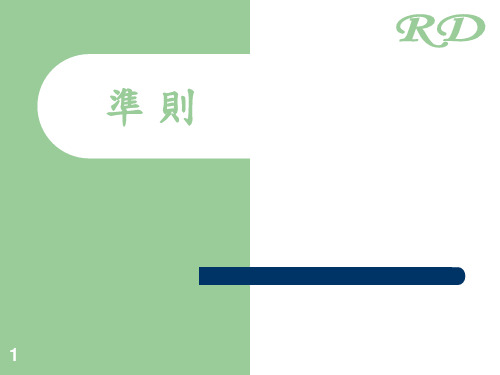
5
壁厚篇 (Wall)
平面准则
在挤压和固化成型过程中,均一的壁厚是非常的重要的。厚胶的地 方比旁边薄胶的地方冷却得比较慢,并且在相接的地方表面 在浇口凝 固后出现收缩痕。更甚者引致产生缩水印、热内应力、挠曲部份歪曲、 颜色不同或不同透明度。若厚胶的地方渐变成薄胶的是无可避免的话, 应尽量设计成渐次的改变,并且在不超过壁厚3:1的比例下。
11
壁厚篇 (Wall)
不同材質的設計要點………………PC;LCP PC 壁厚 壁厚大部份是由负载要求﹑内应力﹑几何形状﹑外型﹑塑料 流量﹑可注塑性和经济性来决定。PC建议最大壁厚:9.5mm 。 若要效果好,则壁厚应不过3.1mm 。在一些需要将壁厚增加使 强度加强时,肋骨和一些补强结构可提供相同结果。PC大部份 应用的最小壁厚在0.75 mm左右,再薄一些的地方是要取决于部 件的几何和大小。短的塑料流程是可以达到0.3 mm 壁厚。 壁厚由厚的过渡到薄的地方是要尽量使其畅顺。所有情况塑 料是从最厚的地方进入模腔内,以避免缩水和内应力。 均一的壁厚是要很重要的。可减少成型后的变型问题。 LCP 壁厚 由于液晶共聚物在高剪切情况下有高流动性,所以壁厚会比 其它的塑料薄。最薄可达0.4mm,一般厚度在1.5mm左右。
(b) 圆角
15
支柱 ( Boss )
支柱突出胶料壁厚是用以装配产品、隔开对象及支撑承托其 它零件之用。空心的支柱可以用来嵌入件、收紧螺丝等。这些应 用均要有足够强度 支持压力 而不致于破裂。 支柱尽量不要单独使用,应尽量连接至外壁或与加强筋一同 使用, 目的: a.是加强支柱的强度 ; b.是使胶料流动更顺畅。 此外,因过高的支柱会导致產品成型时困气,所以支柱高度一般 是不会超过支柱外徑的2.5倍。加强支柱强度的方法,尤其是远离 外壁的支柱,除了可使用加强筋外,三角加强块Gusset plate的 使用亦十分常见。
塑胶件设计准则(一)
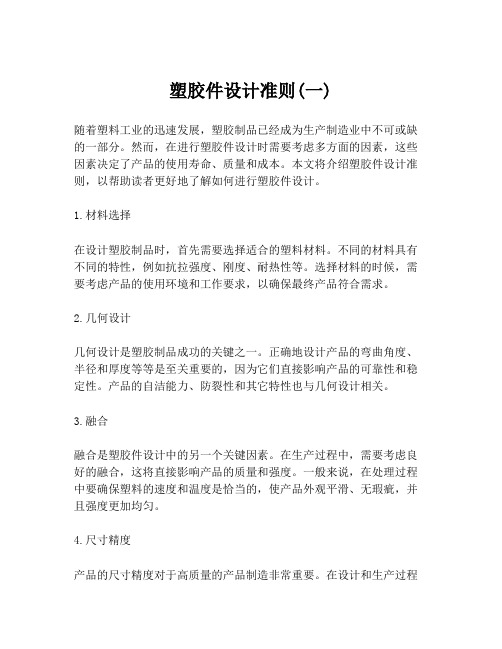
塑胶件设计准则(一)随着塑料工业的迅速发展,塑胶制品已经成为生产制造业中不可或缺的一部分。
然而,在进行塑胶件设计时需要考虑多方面的因素,这些因素决定了产品的使用寿命、质量和成本。
本文将介绍塑胶件设计准则,以帮助读者更好地了解如何进行塑胶件设计。
1.材料选择在设计塑胶制品时,首先需要选择适合的塑料材料。
不同的材料具有不同的特性,例如抗拉强度、刚度、耐热性等。
选择材料的时候,需要考虑产品的使用环境和工作要求,以确保最终产品符合需求。
2.几何设计几何设计是塑胶制品成功的关键之一。
正确地设计产品的弯曲角度、半径和厚度等等是至关重要的,因为它们直接影响产品的可靠性和稳定性。
产品的自洁能力、防裂性和其它特性也与几何设计相关。
3.融合融合是塑胶件设计中的另一个关键因素。
在生产过程中,需要考虑良好的融合,这将直接影响产品的质量和强度。
一般来说,在处理过程中要确保塑料的速度和温度是恰当的,使产品外观平滑、无瑕疵,并且强度更加均匀。
4.尺寸精度产品的尺寸精度对于高质量的产品制造非常重要。
在设计和生产过程中,必须严格控制尺寸精度。
如果精度过低,往往会影响产品的可靠性和性能。
5.模具设计加工模具的质量将直接影响成品的质量。
因此,在设计模具时,需要充分考虑产品的要求,并尽可能减少缺陷的可能性。
从模具材料的选择到处理方法的选定,都必须被考虑到。
综上所述,塑胶件设计准则是非常重要的,可以确保产品质量和性能。
设计师需要仔细考虑产品使用的工作条件,选择适合的材料,并采取正确的几何设计方法。
保证良好的融合、尺寸精度和模具设计,可以使塑料制品达到最高质量标准,从而满足用户的需求。
塑胶件设计准则
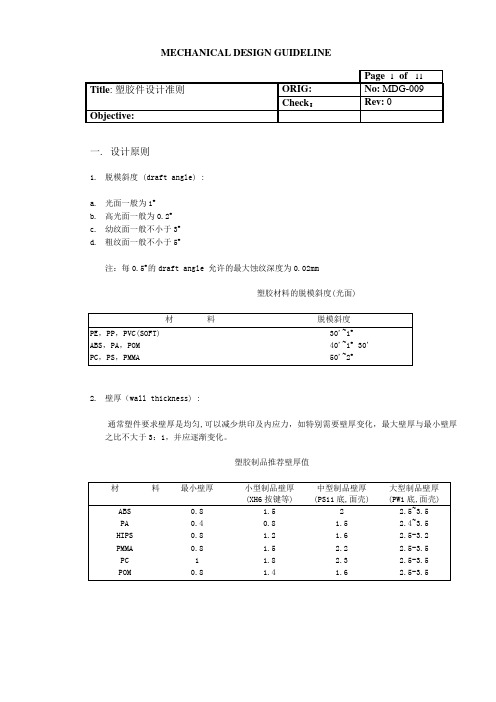
一. 设计原则1.脱模斜度 (draft angle) :a.光面一般为1︒b.高光面一般为0.2︒c.幼纹面一般不小于3︒d.粗纹面一般不小于5︒注:每0.5︒的draft angle 允许的最大蚀纹深度为0.02mm塑胶材料的脱模斜度(光面)2.壁厚(wall thickness) :通常塑件要求壁厚是均匀,可以减少烘印及内应力,如特别需要壁厚变化,最大壁厚与最小壁厚之比不大于3:1,并应逐渐变化。
塑胶制品推荐壁厚值3. 圆角(fillets &Radii):塑件上的锐角易引起应力集中,当塑件内圆角大于1/4壁厚时,内应力急剧下降,在塑件上不采取圆角的地方,最小的圆角 0.2到 0.5mm。
为避免塑件伤人,所有可接触的棱边都需加圆角。
4. 加强筋:(Rib)加强筋可增强塑件的强度及刚度,减少变形,应力集中及缩水。
加强筋要求见下图:5. 止口及叉骨:为防止上,下壳刮手,上,下壳之间必需加叉骨,为增加叉骨强度,叉骨可作成U形,美观线尺寸为0.5mm Min.6. 自攻螺丝柱及防缩水火山口:当螺丝柱直径大于6,为防止螺丝柱底部缩水,可加火山口,请留意烘印。
上下壳螺丝柱配合可采用图示结构。
自攻螺丝柱参考尺寸(材料:ABS)7. PCB定位方式PCB的定位方式分为以下几种:A 螺丝柱猪嘴定位。
当螺丝大于和等于M2.6时,可采用螺丝柱猪嘴定位。
B. 定位柱定位定位柱尺寸为φ1.4 ,PCB定位孔尺寸为φ1.5。
参考PP8XSC. 定位骨定位当PCB尺寸太小时,可在PCB周边开定位缺口,采用定位骨定位。
二. 叉骨设计叉骨即定位骨, 一方面能夠防止底面壳之间產生級位 ( OVER HANG ), 另一方面又能增強抗變形能力。
叉骨一般設置在面殼上, 也有在底殼上設置叉骨, 這要依具体情況而定。
1. 叉骨主要有以下三种形式: A,B,CA 型: 此种形式叉骨強度好 , 推荐使用此种形式叉骨。
B 型: 此种形式叉骨強度較差,用于受力較弱的地方,或由于受尺寸限制,不能采用 A 型及C型叉骨的地方。
塑胶件设计准则[较全]
![塑胶件设计准则[较全]](https://img.taocdn.com/s3/m/b6191537a8114431b90dd846.png)
塑胶件设计准则壁厚(Wall Thickness)基本设计守则壁厚的大小取决于产品需要承受的外力、是否作为其他零件的支撑、承接柱位的数量、伸出部份的多少以及选用的塑胶材料而定。
一般的热塑性塑料壁厚设计应以4mm为限。
从经济角度来看,过厚的产品不但增加物料成本,延长生产周期“冷却时间”,增加生产成本。
从产品设计角度来看,过厚的产品增加引致产生空穴“气孔”的可能性,大大削弱产品的刚性及强度。
最理想的壁厚分布无疑是切面在任何一个地方都是均一的厚度,但为满足功能上的需求以致壁厚有所改变总是无可避免的。
在此情形,由厚胶料的地方过渡到薄胶料的地方应尽可能顺滑。
太突然的壁厚过渡转变会导致因冷却速度不同和产生乱流而造成尺寸不稳定和表面问题。
对一般热塑性塑料来说,当收缩率(Shrinkage Factor)低于0.01mm/mm时,产品可容许厚度的改变达;但当收缩率高于0.01mm/mm时,产品壁厚的改变则不应超过。
对一般热固性塑料来说,太薄的产品厚度往往引致操作时产品过热,形成废件。
此外,纤维填充的热固性塑料于过薄的位置往往形成不够填充物的情况发生。
不过,一些容易流动的热固性塑料如环氧树脂(Epoxies)等,如厚薄均匀,最低的厚度可达0.25mm。
此外,采用固化成型的生产方法时,流道、浇口和部件的设计应使塑料由厚胶料的地方流向薄胶料的地方。
这样使模腔内有适当的压力以减少在厚胶料的地方出现缩水及避免模腔不能完全充填的现象。
若塑料的流动方向是从薄胶料的地方流向厚胶料的地方,则应采用结构性发泡的生产方法来减低模腔压力。
平面准则在大部份热融过程操作,包括挤压和固化成型,均一的壁厚是非常重要的。
厚胶的地方比旁边薄胶的地方冷却得比较慢,并且在相接的地方表面在浇口凝固后出现收缩痕。
更甚者引致产生缩水印、热内应力、挠曲部份歪曲、颜色不同或不同透明度。
若厚胶的地方渐变成薄胶的是无可避免的话,应尽量设计成渐次的改变,并且在不超过壁厚3:1的比例下。
塑胶件设计原则

2.塑件的尺寸精度
影响尺寸精度的因素: ①模具制造精度及其使用后的磨损,
②成型工艺条件的变化,塑料收缩率的波动,
③塑件的形状、脱模斜度及成型后塑件尺寸变化,
④飞边厚度的波动等 。
尺寸精度选用原则:
为了降低模具的加工难度和模具制造成本,在满足塑 件使用要求的前提下应尽量把塑件尺寸精度设计得低一些。
根据塑料收缩率的不同,各种塑料的公差等级分为高、 一般、低精度三种,表3-3。表中未被列出的塑料,可根 据塑件成型后的尺寸稳定性参照上表选择精度等级。选择 精度等级时,应考虑脱模斜度对尺寸公差的影响。
三、塑料制件的表面质量
表面质量包括:表面粗糙度和表观质量。 塑件表面粗糙度的高低,主要与模具型腔表面的粗糙 度有关。目前,注射成型塑件的表面粗糙度通常为 Ra0.02—1.25μm,模腔表壁的表面粗糙度应为塑件的 l/2, 即Ra0.0l~0.63μm。 塑件的表观质量:指塑件成型后的表观缺陷状态。造 成缺陷的因素可能有塑件成型工艺条件、塑件成型原材 料的选择、模具总体设计等。
③PP的尺寸稳定性优于HDPE。④PP的热变形温度高于 HDPE。
HDPE比PP优越的方面:
①HDPE的耐冲击性能比PP强,即使在低温下韧性也好。 ②HDPE适应气候的能力优于PP。
二、塑料制件的尺寸和精度
1.塑件的尺寸
塑件可成型的总体尺寸主要取决于塑料品种的流动性。 在一定的设备和工艺条件下,流动性好的塑料可以成型较 大尺寸的塑件;反之,成型出的塑件尺寸较小。塑件外形 尺寸还受成型设备的限制。从能源、模具制造成本和成型 工艺条件出发,只要能满足塑件的使用要求,应将塑件设 计得尽量紧凑、尺寸小巧一些。
图3—20所示为小型圆柱嵌件与塑件的连接,可供参考。
塑胶产品结构设计准则

confidential
13
三、塑胶产品结构设计准则-支柱 ( Boss )
对于外观件,当有螺丝柱子,需要进行缩水验证,依照上页图示意,塑胶壁厚 1.5 ,螺丝柱子外径3.4,验证结果 NG:(1.8-1.5)/1.5*100%=20% >8%。 外观面有可能会有缩水痕迹。
改善方案如下图:
当缩水验证NG时,可在增加火山口及加深螺丝孔深度来改善。 外观部品综合考虑缩水与螺丝柱子强度,塑胶壁厚要求大于1.3。 适当的辅以三角或十字加强筋方式,可大幅度提高强度和改善料流填充。
confidential
18
四、塑胶产品结构设计准则-洞孔 (Hole)
对于塑胶部品,结合线处强度较弱,受力容易破裂。当通孔处于产品边部,同 时有配合力量要求时,要求孔壁距离外侧壁1.5mm(如因结构原因无法保证 1.5mm, 采用模具设置冷料槽成型后再剪除,但最小要1.0mm),对于卡勾槽尽 量采用盲孔。
10
三、塑胶产品结构设计准则-支柱 ( Boss )
支柱 ( Boss )基本设计守则:
A. 支柱尽量不要单独使用,应尽量连接至外壁或与加强筋一同使用,目的是加 强支柱的强度及使胶料流动更顺畅。
B. 实心支柱的直径大小取壁厚的0.5~0.7倍,当有缩水管理要求时,需使用使用 缩水公式验证。
C. 过高的支柱会导致塑胶部件成型时困气,所以支柱高度一般是不会超过支柱 直径的3倍。过高的支柱要考虑其强度及逃气问题。
塑胶产品结构设计准则
Paul ren
confidential
1
塑胶产品结构设计准则
一. 壁厚 (Thickness) 二. 加强筋(Rib) 三. 支柱 (Boss) 四. 洞孔 (Hole) 五. 扣位(Snap Joint) 六. 出模角(Draft Angle) 七. 螺紋(Screw) 八. 文字(Text) 九. 咬花(Texture)
塑胶产品设计规范
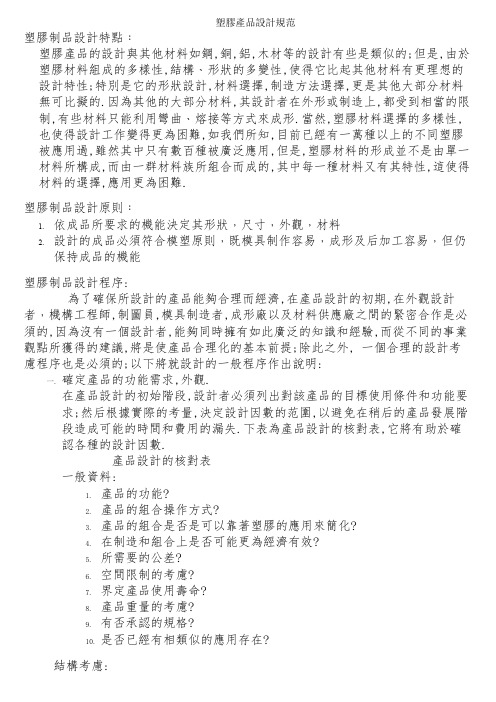
塑膠產品設計規范塑膠制品設計特點﹕塑膠產品的設計與其他材料如鋼,銅,鋁,木材等的設計有些是類似的;但是,由於塑膠材料組成的多樣性,結構﹑形狀的多變性,使得它比起其他材料有更理想的設計特性;特別是它的形狀設計,材料選擇,制造方法選擇,更是其他大部分材料無可比擬的.因為其他的大部分材料,其設計者在外形或制造上,都受到相當的限制,有些材料只能利用彎曲﹑熔接等方式來成形.當然,塑膠材料選擇的多樣性,也使得設計工作變得更為困難,如我們所知,目前已經有一萬種以上的不同塑膠被應用過,雖然其中只有數百種被廣泛應用,但是,塑膠材料的形成並不是由單一材料所構成,而由一群材料族所組合而成的,其中每一種材料又有其特性,這使得材料的選擇,應用更為困難.塑膠制品設計原則﹕1.依成品所要求的機能決定其形狀﹐尺寸﹐外觀﹐材料2.設計的成品必須符合模塑原則﹐既模具制作容易﹐成形及后加工容易﹐但仍保持成品的機能塑膠制品設計程序:為了確保所設計的產品能夠合理而經濟,在產品設計的初期,在外觀設計者﹐機構工程師,制圖員,模具制造者,成形廠以及材料供應廠之間的緊密合作是必須的,因為沒有一個設計者,能夠同時擁有如此廣泛的知識和經驗,而從不同的事業觀點所獲得的建議,將是使產品合理化的基本前提;除此之外, 一個合理的設計考慮程序也是必須的;以下將就設計的一般程序作出說明:一.確定產品的功能需求,外觀.在產品設計的初始階段,設計者必須列出對該產品的目標使用條件和功能要求;然后根據實際的考量,決定設計因數的范圍,以避免在稍后的產品發展階段造成可能的時間和費用的漏失.下表為產品設計的核對表,它將有助於確認各種的設計因數.產品設計的核對表一般資料:1.產品的功能?2.產品的組合操作方式?3.產品的組合是否是可以靠著塑膠的應用來簡化?4.在制造和組合上是否可能更為經濟有效?5.所需要的公差?6.空間限制的考慮?7.界定產品使用壽命?8.產品重量的考慮?9.有否承認的規格?10.是否已經有相類似的應用存在?結構考慮:1.使用負載的狀態?2.使用負載的大小?3.使用負載的期限?4.變形的容許量?環境:1.使用在什麼溫度環境?2.化學物品或溶劑的使用或接觸?3.溫度環境?4.在該種環境的使用期限?外觀:1.外形2.顏色3.表面加工如咬花,噴漆等.經濟因素:1.產品預估價格?2.目前所設計產品的價格?3.降低成本的可能性?二.繪制預備性的設計圖:當產品的功能需求,外觀被確定以后,設計者可以根據選定的塑膠材料性質,開始繪制預備性的產品圖,以作為先期估價,檢討以及原則模型的制作.三.制作原型模型:原型模型讓設計者有機會看到所設計的產品的實體,並且實際的核對其工程設計.原型模型的制作一般有兩種方式,第一種就是利用板狀或棒狀材料依圖加工再接合成一完整的模型,這種方式制作的模型,經濟快速,但是,缺點是量少,而且較難作結構測試;另一種方式,是利用暫用模具,可作少量生產,需花費較高的模具費用,而且所費的時間較長,但是,所制作的產品較類似於真正量產的產品(需要特殊模具機構的部分,可能成形后再以機械加工成形),可做一般的工程測試,而且建立的模具,成形經驗,將有助於產品針對實際模具制作,成形需要而作正確的修正或評估.四.產品測試每一個設計都必須在原型階段,接受一些測試,以核對設計時的計算和假想和實體之間的差異.產品在使用時所需要做的一些測試,大部分都可以籍著原型做有效的測試;此時,面對了所有設計的功能要求,並且能夠達成一個完整的設計評估.模擬使用測試通常在模型產品階段就必須開始,這種型態的測試價值,取決於使用狀態被模擬的程度而定.機械和化學性質的加速化測速通常被視為模型產品評估的重要項目.五.設計的再核對與修正對設計的檢討將有助於回答一些根本的問題:所設計的產品是否達到預期的效果?價格是否合理?甚至於在此時,許多產品為了生產的經濟性或是為了重要的功能和外形的改變,必須被發掘並改善,當然,設計上的重大改變,可能需要做完整的重新評估;假若所有的設計都經過這種仔細檢討,則能夠在這個階建立產品的細節和規格.六.制定重要規格規格的目的在於消除生產時任何的偏差,以使產品符合外觀,功能和經濟的要求,規格上必須明確說明產品所必須符合的要求,它應該包括:制造方法,尺寸公差,表面加工,分模面位置,毛邊,變形,顏色以及測試規格等.七.開模生產當規格被謹慎而實際的訂定之后,模具就可以開始被設計和制作,模具的設計必須謹慎並咨詢專家的意思,因為不適當的模具設計和制造,將會使得生產費用提高,效率降低,並用可能造成品質的問題.八. 品質的控制對照一個已知的標准,訂定對生產產品的規律檢測是良好的檢測作法,而檢測表應該列出所有應該被檢查的項目,另外,相關人員,如品管者或設計者也應與成形廠聯合訂定一個品質管制的程序,以利於在生產的產品能夠符合規格的要求.產品設計細節確定:一.分模線之選定1.不得位于明顯影響外觀的位置2.開模時不形成死角(undercut)的位置3.位于模具易加工的位置4.位于成品后加工容易的位置5.位于不影響尺寸精度的位置(尺寸關系重要的部分盡量放在模具的同一邊)二.脫模斜度脫模斜度是為了便于產品從模具中脫出而設置的。
塑胶产品设计原则

下列所示為各种成形品之實例﹒
外缘有辊纹或及手扭等型类之物 品﹐尽可能留有缘边﹐使"毛刺" 由于软管接头两端有低陷段﹐ 及"浇口"切除加工容易﹒ 因之使用"立式分模之分模线"
電熨斗握把之复雜分模線
图5 (b)
牙刷柄之分模线位于制品最大 宽度面上﹐使成形品脱模容易 ﹒再者模具嵌合线与其外形曲 线一致﹐加工容易 ﹒
6.孔
孔為成形品上所必需者﹐良好之位置可得良好之使用﹒孔 在成形品上經由熔合留出者﹐為強度減弱之主要原因﹐必需注 意下列各點﹒ (1) 孔与孔間之距离取用孔徑之兩倍以 上﹒ (2) 孔之周邊肉厚加 厚﹒ (3) 孔与制品邊緣之距离符合孔徑之3倍以 上﹒ (4) 与成形材料流動向成直角之未穿孔﹐孔徑在 1.5mm以下之場合﹐型心銷有彎曲之虞﹐孔深(L)不 能達到孔徑(D)之兩倍﹒ (5) 与突出销配合孔﹐上下孔间有偏心之虞者﹐则可将 任何一侧之孔放大﹒
(7) 組合件旋裝進入方向應如"矢"標所示﹒圖31(a),圖32(a).
(4)﹒ 底肋 底肋与縱肋有相同之作用﹐ 應作同樣之考慮﹐決定其拔模 角度﹒ 使用最多之拔模角度為
較少击起之場合﹐亦得适用 (0.8~1.0) 由於工作上限制 B=1.0~1.8mm
(完整版)塑胶件设计准则(较全)

塑胶件设计准则壁厚(Wall Thickness)基本设计守则壁厚的大小取决于产品需要承受的外力、是否作为其他零件的支撑、承接柱位的数量、伸出部份的多少以及选用的塑胶材料而定。
一般的热塑性塑料壁厚设计应以4mm为限。
从经济角度来看,过厚的产品不但增加物料成本,延长生产周期“冷却时间”,增加生产成本。
从产品设计角度来看,过厚的产品增加引致产生空穴“气孔”的可能性,大大削弱产品的刚性及强度。
最理想的壁厚分布无疑是切面在任何一个地方都是均一的厚度,但为满足功能上的需求以致壁厚有所改变总是无可避免的。
在此情形,由厚胶料的地方过渡到薄胶料的地方应尽可能顺滑。
太突然的壁厚过渡转变会导致因冷却速度不同和产生乱流而造成尺寸不稳定和表面问题。
对一般热塑性塑料来说,当收缩率(Shrinkage Factor)低于0.01mm/mm时,产品可容许厚度的改变达;但当收缩率高于0.01mm/mm时,产品壁厚的改变则不应超过。
对一般热固性塑料来说,太薄的产品厚度往往引致操作时产品过热,形成废件。
此外,纤维填充的热固性塑料于过薄的位置往往形成不够填充物的情况发生。
不过,一些容易流动的热固性塑料如环氧树脂(Epoxies)等,如厚薄均匀,最低的厚度可达0.25mm。
此外,采用固化成型的生产方法时,流道、浇口和部件的设计应使塑料由厚胶料的地方流向薄胶料的地方。
这样使模腔内有适当的压力以减少在厚胶料的地方出现缩水及避免模腔不能完全充填的现象。
若塑料的流动方向是从薄胶料的地方流向厚胶料的地方,则应采用结构性发泡的生产方法来减低模腔压力。
平面准则在大部份热融过程操作,包括挤压和固化成型,均一的壁厚是非常重要的。
厚胶的地方比旁边薄胶的地方冷却得比较慢,并且在相接的地方表面在浇口凝固后出现收缩痕。
更甚者引致产生缩水印、热内应力、挠曲部份歪曲、颜色不同或不同透明度。
若厚胶的地方渐变成薄胶的是无可避免的话,应尽量设计成渐次的改变,并且在不超过壁厚3:1的比例下。
塑料制品设计原则
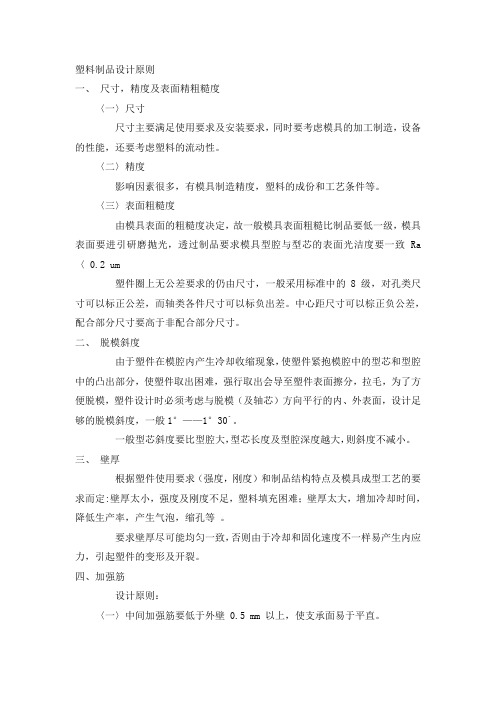
塑料制品设计原则一、尺寸,精度及表面精粗糙度〈一〉尺寸尺寸主要满足使用要求及安装要求,同时要考虑模具的加工制造,设备的性能,还要考虑塑料的流动性。
〈二〉精度影响因素很多,有模具制造精度,塑料的成份和工艺条件等。
〈三〉表面粗糙度由模具表面的粗糙度决定,故一般模具表面粗糙比制品要低一级,模具表面要进引研磨抛光,透过制品要求模具型腔与型芯的表面光洁度要一致 Ra 〈 0.2 um塑件圈上无公差要求的仍由尺寸,一般采用标准中的8 级,对孔类尺寸可以标正公差,而轴类各件尺寸可以标负出差。
中心距尺寸可以棕正负公差,配合部分尺寸要高于非配合部分尺寸。
二、脱模斜度由于塑件在模腔内产生冷却收缩现象,使塑件紧抱模腔中的型芯和型腔中的凸出部分,使塑件取出困难,强行取出会导至塑件表面擦分,拉毛,为了方便脱模,塑件设计时必须考虑与脱模(及轴芯)方向平行的内、外表面,设计足够的脱模斜度,一般1°——1°30`。
一般型芯斜度要比型腔大,型芯长度及型腔深度越大,则斜度不减小。
三、壁厚根据塑件使用要求(强度,刚度)和制品结构特点及模具成型工艺的要求而定:壁厚太小,强度及刚度不足,塑料填充困难;壁厚太大,增加冷却时间,降低生产率,产生气泡,缩孔等。
要求壁厚尽可能均匀一致,否则由于冷却和固化速度不一样易产生内应力,引起塑件的变形及开裂。
四、加强筋设计原则:〈一〉中间加强筋要低于外壁 0.5 mm 以上,使支承面易于平直。
〈二〉应避免或减小塑料的局部聚积。
〈三〉筋的排例要顺着在型腔内的流动方向。
五、支承面塑件一般不以整个平面作为支承面,而取而代之以边框,底脚作支承面。
六、圆角要求塑件防有转角处都要以圆角(圆弧)过渡,因尖角容易应力集中。
塑件有圆角,有利于塑料的流动充模及塑件的顶出,塑件的外观好,有利于模具的强度及寿命。
七、孔(槽)塑件的孔三种成型加工方法:(1)模型直接模塑出来。
(2)模塑成盲孔再钻孔通。
(3)塑件成型后再钻孔。
塑胶件设计

§ 塑件设计
3、塑件结构设计 满足使用要求 好的结构工艺性:是指塑件在满足使用要
求的前提下,其结构应尽可能符合成形工 艺要求,从而简化模具结构,降低生产成 本。
§ 塑件设计
1)塑件结构工艺性设计应遵循的原则:
在保证塑件的使用性能、物理、化学、介电性能与力学 性能等的前提下,尽量选用价格低廉和成形性能较好的 塑料,并力求结构简单、壁厚均匀、成形方便。
在设计塑件时应考虑其模具的总体结构,使模具型腔易 于设计制造,模具抽芯和推出机构简单。
在设计塑件时,应考虑原料的成形工艺性,如流动性、 收缩性等,塑件形状有利于模具分型、排气、补缩和冷 却。
§塑件设计
设计原则: ❖ 应考虑原材料的成型工艺性; ❖ 应考虑模具的总体结构,使模具型腔易于制
造,模具抽芯和推出机构简单; ❖ 在保证塑件使用性能、物理性能与力学性能、
电性能等的前提下,力求结构简单,壁厚均 匀,使用方便。
§ 塑件设计
1、塑件尺寸及其精度 1)塑件尺寸 设计原则:
❖ 受到塑料的流动性制约,流动性好的塑料可以成形较大 尺寸的塑件,反之能成形的塑件尺寸就较小。
§ 塑件设计
❖圆角(不小于0.5~1mm,一般外圆角R=1.5 内圆角R1=0.5 。)
作用: 避免应力集中,提高塑件强度 改善熔体流动情
况、便于脱模模具型腔不易因应力集中而开裂。
§ 塑件设计
❖ 孔的设计(包括通孔、盲孔、异形孔、螺 纹孔) 设计原则: ① 保证足够强度,以满足使用要求; ② 尽量避免侧孔。
§ 塑件设计
❖ 标记符号及表面彩饰
注意事项
①标记符号应放在分型面的平 行方向上,并有适当的斜 度(>10°)以便于脱模。
- 1、下载文档前请自行甄别文档内容的完整性,平台不提供额外的编辑、内容补充、找答案等附加服务。
- 2、"仅部分预览"的文档,不可在线预览部分如存在完整性等问题,可反馈申请退款(可完整预览的文档不适用该条件!)。
- 3、如文档侵犯您的权益,请联系客服反馈,我们会尽快为您处理(人工客服工作时间:9:00-18:30)。
塑胶件设计准则壁厚(Wall Thickness)基本设计守则壁厚的大小取决于产品需要承受的外力、是否作为其他零件的支撑、承接柱位的数量、伸出部份的多少以及选用的塑胶材料而定。
一般的热塑性塑料壁厚设计应以4mm为限。
从经济角度来看,过厚的产品不但增加物料成本,延长生产周期“冷却时间”,增加生产成本。
从产品设计角度来看,过厚的产品增加引致产生空穴“气孔”的可能性,大大削弱产品的刚性及强度。
最理想的壁厚分布无疑是切面在任何一个地方都是均一的厚度,但为满足功能上的需求以致壁厚有所改变总是无可避免的。
在此情形,由厚胶料的地方过渡到薄胶料的地方应尽可能顺滑。
太突然的壁厚过渡转变会导致因冷却速度不同和产生乱流而造成尺寸不稳定和表面问题。
对一般热塑性塑料来说,当收缩率(Shrinkage Factor)低于0.01mm/mm时,产品可容许厚度的改变达;但当收缩率高于0.01mm/mm时,产品壁厚的改变则不应超过。
对一般热固性塑料来说,太薄的产品厚度往往引致操作时产品过热,形成废件。
此外,纤维填充的热固性塑料于过薄的位置往往形成不够填充物的情况发生。
不过,一些容易流动的热固性塑料如环氧树脂(Epoxies)等,如厚薄均匀,最低的厚度可达0.25mm。
此外,采用固化成型的生产方法时,流道、浇口和部件的设计应使塑料由厚胶料的地方流向薄胶料的地方。
这样使模腔内有适当的压力以减少在厚胶料的地方出现缩水及避免模腔不能完全充填的现象。
若塑料的流动方向是从薄胶料的地方流向厚胶料的地方,则应采用结构性发泡的生产方法来减低模腔压力。
平面准则在大部份热融过程操作,包括挤压和固化成型,均一的壁厚是非常重要的。
厚胶的地方比旁边薄胶的地方冷却得比较慢,并且在相接的地方表面在浇口凝固后出现收缩痕。
更甚者引致产生缩水印、热内应力、挠曲部份歪曲、颜色不同或不同透明度。
若厚胶的地方渐变成薄胶的是无可避免的话,应尽量设计成渐次的改变,并且在不超过壁厚3:1的比例下。
下图可供叁考。
转角准则壁厚均一的要诀在转角的地方也同样需要,以免冷却时间不一致。
冷却时间长的地方就会有收缩现象,因而发生部件变形和挠曲。
此外,尖锐的圆角位通常会导致部件有缺陷及应力集中,尖角的位置亦常在电镀过程后引起不希望的物料聚积。
集中应力的地方会在受负载或撞击的时候破裂。
较大的圆角提供了这种缺点的解决方法,不但减低应力集中的因素,且令流动的塑料流得更畅顺和成品脱模时更容易。
下图可供叁考之用。
转角位置的设计应力集中系数与圆弧/壁厚之关系转角位的设计准则亦适用于悬梁式扣位。
因这种扣紧方式是需要将悬梁臂弯曲嵌入,转角位置的设计图说明如果转角弧位R太小时会引致其应力集中系数(Stress Concentration Factor)过大,因此,产品弯曲时容易折断,弧位R太大的话则容易出现收缩纹和空洞。
因此,圆弧位和壁厚是有一定的比例。
一般介乎0.2至0.6之间,理想数值是在0.5左右。
壁厚限制不同的塑胶物料有不同的流动性。
胶位过厚的地方会有收缩现象,胶位过薄的地方塑料不易流过。
以下是一些建议的胶料厚度可供叁考。
热塑性塑料的胶厚设计叁考表热固性塑料的胶厚设计叁考其实大部份厚胶的设计可从使用加强筋及改变横切面形状取缔之。
除了可减省物料以致减省生产成本外,取缔后的设计更可保留和原来设计相若的刚性、强度及功用。
下图的金属齿轮如改成使用塑胶物料,更改后的设计理应如图一般。
此塑胶齿轮设计相对原来金属的设计不但减省材料,消取因厚薄不均引致的内应力增加及齿冠部份收缩引致整体齿轮变形的情况发生。
不同材料的设计要点ABS丙烯腈-丁二烯-苯乙烯共聚物a)壁厚壁厚是产品设计最先被考虑,一般用于注塑成型的会在1.5mm(0.06in)至4.5mm(0.18in)。
壁厚比这范围小的用于塑料流程短和细小部件。
典型的壁厚约在2.5mm(0.1in)左右。
一般来说,部件愈大壁厚愈厚,这可增强部件强度和塑料充填。
壁厚在3.8mm(0.15in)至6.4mm(0.25in)范围是可使用结构性发泡。
b)圆角建议的最小圆角半径是胶料厚度的25%,最适当的半径胶料厚比例在60%。
轻微的增加半径就能明显的减低应力。
PC聚碳酸酯a)壁厚壁厚大部份是由负载要求:内应力、几何形状、外型、塑料流量、可注塑性和经济性来决定。
PC的建议最大壁厚为9.5mm(0.375 in)。
若要效果好,则壁厚应不过3.1mm(0.125 in)。
在一些需要将壁厚增加使强度加强时,肋骨和一些补强结构可提供相同结果。
PC大部份应用的最小壁厚在0.75 mm(0.03 in)左右,再薄一些的地方是要取决于部件的几何和大小。
短的塑料流程是可以达到0.3mm(0.012 in)壁厚。
壁厚由厚的过渡到薄的地方是要尽量使其畅顺。
所有情况塑料是从最厚的地方进入模腔内,以避免缩水和内应力。
均一的壁厚是要很重要的。
不论在平面转角位也是要达到这种要求,可减少成型后的变型问题。
LCP液晶聚合物a)壁厚由于液晶共聚物在高剪切情况下有高流动性,所以壁厚会比其它的塑料薄。
最薄可达0.4mm,一般厚度在1.5mm左右。
PS聚苯乙烯a)壁厚一般的设计胶料的厚度应不超过4mm,太厚的话会导致延长了生产周期。
因需要更长的冷却时间,且塑料收缩时有中空的现象,并减低部件的物理性质。
均一的壁厚在设计上是最理想的,但有需要将厚度转变时,就要将过渡区内的应力集中除去。
如收缩率在0.01以下则壁厚的转变可有的变化。
若收缩率在0.01以上则应只有的改变。
加强筋一般的设计b)圆角在设计上直角是要避免。
直角的地方有如一个节点,会引致应力集中使抗撞击强度降低。
圆角的半径应为壁厚的25%至75%,一般建议在50%左右。
PA聚酰胺(尼龙)a)壁厚尼龙的塑胶零件设计应采用结构所需要的最小厚度。
这种厚度可使材料得到最经济的使用。
壁厚尽量能一致以消除成型后变型。
若壁厚由厚过渡至薄胶料则需要采用渐次变薄的方式。
b)圆角建议圆角R值最少0.5mm(0.02 in),此一圆角一般均可接受,在有可能的范围,尽量使用较大的R值。
因应力集中因素数值因为R/T之比例由0.1增至0.6而减少了50% ,即由3减至1.5。
而最佳的圆角是为R/T在0.6之间。
PSU聚砜a)壁厚常用于大型和长流距的壁厚最小要在2.3mm(0.09in)。
细小的部件可以最小要有0.8mm(0.03in)而流距应不可超过76.2mm(3in)PBT聚对苯二酸丁二酯a)壁厚壁厚是产品成本的一个因素。
薄的壁厚要视乎每种塑料特性而定。
设计之前宜先了解所使用塑料的流动长度限制来决定壁厚。
负载要求时常是决定壁厚的,而其它的如内应力,部件几何形状,不均一化和外形等。
典型的壁厚介乎在0.76mm至3.2mm(0.03至0.125in)。
壁厚要求均一,若有厚薄胶料的地方,以比例3:1的锥巴渐次由厚的地方过渡至薄的地方。
b)圆角转角出现尖角所导致部件的破坏最常见的现象,增加圆角是加强塑胶部件结构的方法之一。
若将应力减少5%(由3减至1.5)则圆角与壁厚的比例由0.1增加至0.6。
而0.6是建议的最理想表现。
加强筋(Ribs)基本设计守则加强筋在塑胶部件上是不可或缺的功能部份。
加强筋有效地如『工』字铁般增加产品的刚性和强度而无需大幅增加产品切面面积,但没有如『工』字铁般出现倒扣难于成型的形状问题,对一些经常受到压力、扭力、弯曲的塑胶产品尤其适用。
此外,加强筋更可充当内部流道,有助模腔充填,对帮助塑料流入部件的支节部份很大的作用。
加强筋一般被放在塑胶产品的非接触面,其伸展方向应跟随产品最大应力和最大偏移量的方向,选择加强筋的位置亦受制于一些生产上的考虑,如模腔充填、缩水及脱模等。
加强筋的长度可与产品的长度一致,两端相接产品的外壁,或只占据产品部份的长度,用以局部增加产品某部份的刚性。
要是加强筋没有接上产品外壁的话,末端部份亦不应突然终止,应该渐次地将高度减低,直至完结,从而减少出现困气、填充不满及烧焦痕等问题,这些问题经常发生在排气不足或封闭的位置上。
加强筋最简单的形状是一条长方形的柱体附在产品的表面上,不过为了满足一些生产上或结构上的考虑,加强筋的形状及尺寸须要改变成如以下的图一般。
长方形的加强筋必须改变形状使生产更容易加强筋的两边必须加上出模角以减低脱模顶出时的摩擦力,底部相接产品的位置必须加上圆角以消除应力集过份中的现象,圆角的设计亦给与流道渐变的形状使模腔充填更为流畅。
此外,底部的宽度须较相连外壁的厚度为小,产品厚度与加强筋尺寸的关系图a说明这个要求。
图中加强筋尺寸的设计虽然已按合理的比例,但当从加强筋底部与外壁相连的位置作一圆圈R1时,图中可见此部份相对外壁的厚度增加大约50%,因此,此部份出现缩水纹的机会相当大。
如果将加强筋底部的宽度相对产品厚度减少一半(产品厚度与加强筋尺寸的关系图b),相对位置厚度的增幅即减至大约20%,缩水纹出现的机会亦大为减少。
由此引伸出使用两条或多条矮的加强筋比使用单一条高的加强筋较为优胜,但当使用多条加强筋时,加强筋之间的距离必须较相接外壁的厚度大。
加强筋的形状一般是细而长,加强筋一般的设计图说明设计加强筋的基本原则。
留意过厚的加强筋设计容易产生缩水纹、空穴、变形挠曲及夹水纹等问题,亦会加长生产周期,增加生产成本。
产品厚度与加强筋尺寸的关系除了以上的要求,加强筋的设计亦与使用的塑胶材料有关。
从生产的角度看,材料的物理特性如熔胶的黏度和缩水率对加强筋设计的影响非常大。
此外,塑料的蠕动(creep)特性从结构方面来看亦是一个重要的考虑因数。
例如,从生产的角度看,加强筋的高度是受制于熔胶的流动及脱模顶出的特性(缩水率、摩擦系数及稳定性),较深的加强筋要求胶料有较低的熔胶黏度、较低的摩擦系数、较高的缩水率。
另外,增加长的加强筋的出模角一般有助产品顶出,不过,当出模角不断增加而底部的阔度维持不变时,产品的刚性、强度,与及可顶出的面积即随着减少。
顶出面积减少的问题可从在产品加强筋部份加上数个顶出凸块或使用较贵的扁顶针得以解决,同时在顶出的方向打磨光洁亦有助产品容易顶出。
从结构方面考虑,较深的加强筋可增加产品的刚性及强度而无须大幅增加重量,但与此同时,产品的最高和最低点的屈曲应力(bending stress)随着增加,产品设计员须计算并肯定此部份的屈曲应力不会超出可接受的范围。
从生产的角度考虑,使用大量短而窄的加强筋比较使用数个深而阔的加强筋优胜。
模具生产时(尤其是首办模具):加强筋的阔度(也有可能深度)和数量应尽量留有馀额,当试模时发觉产品的刚性及强度有所不足时可适当地增加,因为在模具上去除钢料比使用烧焊或加上插入件等增加钢料的方法来得简单及便宜。
加强筋增强塑胶件强度的方法置于塑胶部件边缘地方的加强筋以下是加强筋被置于塑胶部件边缘的地方可以帮助塑料流入边缘的空间。