精益生产讲义培训材料
精益生产课程培训讲义

第一章精益生产的思想和方法企业经营的目的是向社会提供产品和效劳,同时为企业制造利润。
为到达这一目的,企业必须投进人员、材料、设备、资金等资源,并通过对它们的有效使用和优化组合制造出社会所需要的产品。
而利润的上下取决于投进和有效产出1的比例,即生产效率,班组是使产品增值的全然单元,是提高生产效率的主战场。
提高生产效率有以下三种途径:1.投进不变,产出增加;2.产出不变,投进减少;3.投进减少,产出增加。
第一种途径适用于产品的成长期2,即市场对该产品的需求呈上升趋势的时期;第二种途径适用于产品的成熟期或衰退期,即市场对该产品的需求渐趋稳定或下落的时期;第三种途径显然是最理想的,因而难度也是最大的.然而,市场竞争的结果最终将导致第一和第二种途径的失效,从而使企业的经营状况步进低谷。
要防止这种状况,就必须采纳第三种途径。
精益生产的成功有力地证实了这一途径的优越性和有效性。
第一节精益生产的诞生及其特点精益生产方式是继单件生产方式和大量生产方式之后在日本丰田汽车公司诞生的全新生产方式。
精益的“精〞确实是根基指更少的投进,而“益〞指更多的产出。
本世纪中叶,当美国的汽车工业处于开展的顶峰时,以大野耐一为代表的丰田人对美国的大量生产方式进行了完全的分析,得出了两条结论:1.大量生产方式在削减本钞票方面的潜力要远远超过其规模效应所带来的好处2.大量生产方式的纵向泰勒制3组织体制不利于企业对市场的习惯和职工积极性、聪慧和制造力的发扬基于这两点熟悉,丰田公司依据自身面临需求缺乏、技术落后、资金短缺等严重困难的特点,同时结合日本独特的文化背景,逐步创立了一种全新的多品种、小批量、高效益和低消耗的生产方式。
这种生产方式在1973年的石油危机中表达了巨大的优越性,并成为80年代日本在汽车市场竞争中战胜美国的法宝,从而促使美国化费500万美元和5年时刻对日本的生产方式进行考察和研究,并把这种生产方式重新命名为精益生产(LEANPRODUCTION)。
精益生产基础知识培训课件
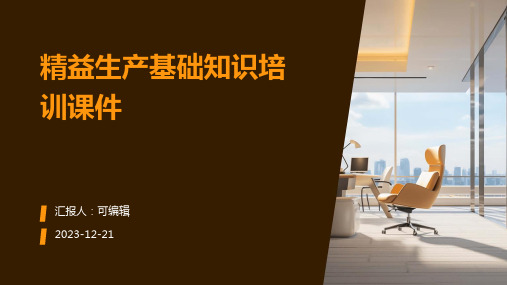
创新。
CHAPTER 05
精益生产的实施与推广
制定实施计划与目标
明确实施目标
制定具体的精益生产实施目标,如降低成本、提高效率、优化流程 等。
制定实施计划
根据目标,制定详细的实施计划,包括时间表、资源分配、责任人 等。
设定可衡量的指标
为确保实施效果,设定可衡量的关键绩效指标(KPI),以便跟踪和 评估。
颜色管理
利用不同颜色的标识来 区分不同的物品或状态
,提高识别效率。
异常管理
及时发现并处理异常情 况,防止问题扩大化。
准时化生产
准时生产
按照客户需求的时间和数 量,准时完成生产任务。
弹性作业
根据生产计划的变化,灵 活调整员工的作业内容和 时间。
流程优化
通过消除浪费、提高效率 等方式,优化生产流程, 降低成本。
自动化与智能化
自动化设备
利用自动化设备代替人工操作,提高 生产效率和质量。
智能化技术
人机协作
在自动化和智能化的基础上,实现人 与机器的协同工作,提高生产效率和 质量。
运用人工智能、大数据等技术手段, 实现生产过程的智能化管理和控制。
CHAPTER 03
精益生产在制造业中的应用
生产线布局优化
消除流水线瓶颈
建立客户反馈机制
及时收集客户反馈,对服务质量进行持续改进,提高客户满意度 和忠诚度。
创新与持续改进
鼓励创新
01
鼓励员工提出创新性的服务流程优化方案,持续改进服务质量
。
实施持续改进
02
对服务流程进行持续改进,提高服务效率和质量。
建立学习型组织
03
构建学习型组织,提高员工技能和素质,推动服务流程优化和
精益生产PPT培训资料
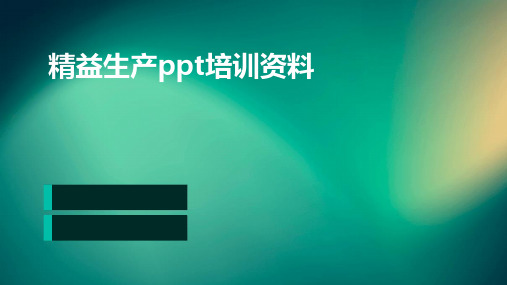
减少浪费
定义
01
浪费是指生产过程中不产生价值的活动或因素,如过度加工、
等待、搬运、库存等。
目的
02
消除浪费,提高生产效率。
步骤
03
通过分析生产过程中的各个环节,找出浪费并采取措施消除或
减少浪费,提高生产效率。
单元化生产
定义
单元化生产是一种将生产线划分为独立的生产单元,每个单元负责特定的产品或工序的生 产方式。
制定具体的目标指标 和时间表,确保目标 的可实现性和可衡量 性。
与员工和利益相关者 沟通,明确精益生产 的期望和要求。
价值流分析
对企业业务流程进行全面梳理, 识别并分析价值流中的浪费和瓶
颈。
运用价值流图等工具,可视化呈 现当前价值流状态,便于发现问
题。
确定关键改善区域,为后续改进 计划提供依据。
制定改进计划
根据价值流分析结果,制定针对性的 改进计划。
对改进计划进行优先级排序,确保资 源合理分配。
确定改进措施、责任人、时间表和预 期成果。
实施改进措施
按照改进计划逐步实施各项措施。 建立跨部门协作机制,确保改进措施的有效执行。
及时跟进并调整计划,确保改进过程中的灵活性。
持续改进与优化
对改进成果进行评估和总结, 确保达到预期目标。
全球化与本地化
全球化战略
随着经济全球化的深入发展,企业将更加注重全球化战略的制定和 实施,以拓展国际市场和提升品牌影响力。
本地化运营
在全球化战略的基础上,企业将更加注重本地化运营,以满足不同 国家和地区的市场需求和文化差异。
跨文化交流与合作
加强跨文化交流与合作,促进不Biblioteka 国家和地区之间的相互理解和合作 共赢。
精益生产篇(培训资料)
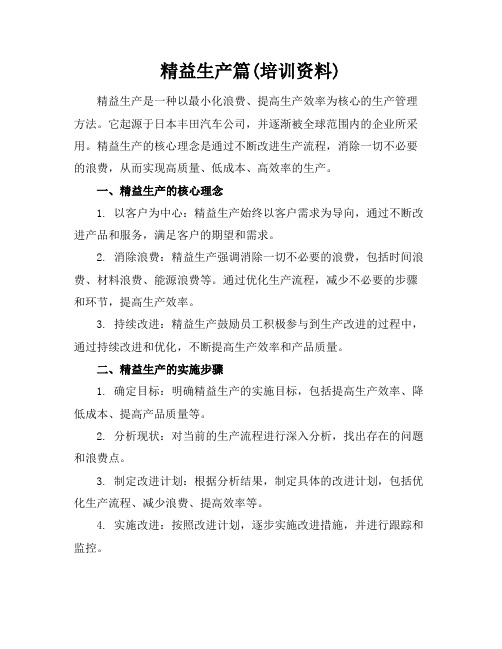
精益生产篇(培训资料)精益生产是一种以最小化浪费、提高生产效率为核心的生产管理方法。
它起源于日本丰田汽车公司,并逐渐被全球范围内的企业所采用。
精益生产的核心理念是通过不断改进生产流程,消除一切不必要的浪费,从而实现高质量、低成本、高效率的生产。
一、精益生产的核心理念1. 以客户为中心:精益生产始终以客户需求为导向,通过不断改进产品和服务,满足客户的期望和需求。
2. 消除浪费:精益生产强调消除一切不必要的浪费,包括时间浪费、材料浪费、能源浪费等。
通过优化生产流程,减少不必要的步骤和环节,提高生产效率。
3. 持续改进:精益生产鼓励员工积极参与到生产改进的过程中,通过持续改进和优化,不断提高生产效率和产品质量。
二、精益生产的实施步骤1. 确定目标:明确精益生产的实施目标,包括提高生产效率、降低成本、提高产品质量等。
2. 分析现状:对当前的生产流程进行深入分析,找出存在的问题和浪费点。
3. 制定改进计划:根据分析结果,制定具体的改进计划,包括优化生产流程、减少浪费、提高效率等。
4. 实施改进:按照改进计划,逐步实施改进措施,并进行跟踪和监控。
5. 持续改进:在实施改进的基础上,不断进行持续改进,提高生产效率和产品质量。
三、精益生产的工具和方法1. 5S管理:通过整理、整顿、清扫、清洁、素养五个步骤,提高生产现场的管理水平。
2. 单件流生产:通过优化生产流程,实现单件流生产,减少库存和浪费。
3. 拉动式生产:根据客户需求,实现按需生产,减少库存和浪费。
4. 标准化作业:制定标准化的作业流程,提高生产效率和产品质量。
5. 持续改进:通过PDCA循环,不断进行持续改进,提高生产效率和产品质量。
四、精益生产的挑战和应对策略1. 变革管理:精益生产需要企业进行全面的变革,包括管理理念、生产流程、员工培训等方面。
企业需要制定明确的变革计划和策略,确保变革的顺利进行。
2. 员工参与:精益生产的成功实施需要员工的积极参与和支持。
精益生产基础培训课件PPT5)
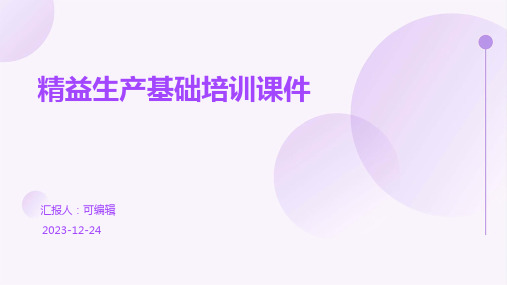
拉动系统
01
02
03
拉动系统
拉动系统是精益生产中的 一种控制方法,通过后工 序向前工序发出需求信号 来拉动生产。
需求信号
需求信号是指后工序根据 实际需要向前工序传递的 信号,前工序根据需求信 号进行生产和调整。
减少浪费
拉动系统有助于减少过量 生产和库存浪费,降低库 存成本和资金占用。
持续改进
持续改进
实施改进措施
总结词
按照计划实施改进措施
详细描述
按照改进计划,逐步实施各项改进措施,确保各项措施的有效执行,并及时解决实施过程中出现的问 题。
持续改进
总结词
不断优化和改进生产流程
详细描述
在实施改进措施后,持续监测生产流程的效率和问题,及时发现并解决新出现的问题,不断优化和改进生产流程 ,实现持续改进的目标。
通过实施5S管理,可以提高生产现场的整洁度和秩序,减少浪费,提高工作效率和产品质 量。
5S管理有助于创造一个安全、有序、高效的工作环境,提升员工的工作满意度和归属感。
快速换模
快速换模技术是精益生产中的一 项重要工具,旨在减少设备或生 产线更换模具或规格的时间和成
本。
通过减少换模时间,可以提高设 备的利用率和生产效率,降低生
单元化生产
单元化生产是将生产线或设备 按照产品族或工艺特点进行分 类和重新布局,以提高生产效 率和灵活性。
通过单元化生产,可以减少产 品在生产线上的移动和等待时 间,降低生产成本和提高产品 质量。
单元化生产需要合理规划和管 理,以确保各单元之间的协调 和配合,实现整体效益的最大 化。
价值流图分析
总结词
了解当前生产流程的效率和问题
详细描述
评估现有生产流程,包括设备、人员、材料、工艺等方面的效率和问题,收集 数据并进行分析,找出瓶颈和浪费。
精益生产知识培训课件

精益生产知识培训课件•精益生产概述•精益生产的工具与方法•精益生产的实施步骤•精益生产的成功案例•精益生产的未来发展与挑战01精益生产概述精益生产是一种以客户需求为导向,通过消除浪费、持续改进和降低成本来提高生产效率和效益的生产方式。
定义关注客户需求、追求价值流优化、强调团队合作、持续改进和创新。
特点定义与特点精益生产的历史与发展起源精益生产起源于日本丰田汽车公司的生产方式,旨在消除浪费、提高效率和效益。
发展随着全球化和市场竞争的加剧,精益生产逐渐成为主流的生产方式,广泛应用于各行各业。
未来趋势随着数字化和智能化的快速发展,精益生产将与工业互联网、大数据等先进技术结合,进一步提高生产效率和灵活性。
价值流流动与平衡拉动系统持续改进精益生产的核心思想01020304识别和优化从原材料到最终产品的整个过程中的所有活动,消除浪费,提高价值。
通过合理安排生产流程,实现顺畅的价值流,提高生产效率。
根据客户需求进行生产和补充,实现准时化生产。
不断寻找和解决浪费问题,持续优化生产过程,提高效率和效益。
02精益生产的工具与方法价值流分析价值流分析是精益生产的核心工具之一,它通过对产品从原材料到最终客户的整个价值流动过程进行系统分析,识别出浪费并制定改进措施。
价值流分析包括对整个生产过程中的所有活动进行记录、评估和优化,旨在消除浪费、降低成本和提高效率。
通过价值流图或其他可视化工具,企业可以全面了解产品从原材料到成品的所有环节,包括供应商、生产、物流和销售等。
5S管理5S管理是一种现场管理方法,包括整理、整顿、清扫、清洁和素养五个方面,旨在提高工作效率、减少浪费和保障安全。
5S管理要求企业保持工作场所整洁有序,减少不必要的物品,标识清楚并易于查找,定期清扫和维护设备,以及培养员工良好的工作习惯和职业素养。
通过实施5S管理,企业可以提高生产效率和产品质量,降低事故风险和减少浪费。
持续改进持续改进是精益生产的核心思想之一,它强调不断优化生产过程、提高产品质量和降低成本。
精益生产基础知识培训课件ppt
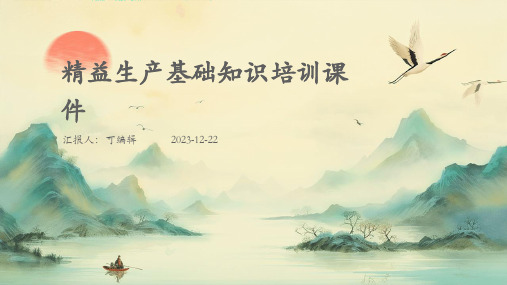
服务成本降低
资源优化
合理配置人力、物力和财力资源,避免浪费。
成本控制
通过精细化管理,降低服务过程中的成本支出。
价值创新
通过创新服务模式和手段,提高服务附加值,实现成本与效益的平衡。
服务效率提高
时间管理
合理安排服务时间,提高服务效率。
团队协作
加强团队之间的沟通与协作,提高工作效率 。
技术应用
利用先进的技术手段,如数字化、智能化等 ,提高服务效率和质量。
价值流分析
定义
价值流分析是一种识别、 测量和分析产品从原材料 到最终客户整个过程中的 所有活动的方法。
目的
通过价值流分析,企业可 以找出过程中的瓶颈和浪 费,并采取措施消除或减 少这些瓶颈和浪费。
步骤
价值流分析包括绘制当前 状态图、绘制未来状态图 、制定实施计划等步骤。
5S管理
定义
步骤
5S管理是一种以整理、整顿、清洁、 清洁检查和素养为主要内容的现场管 理方法。
精益生产的核心思想
01
02
03
04
以客户需求为导向
将客户的需求作为生产的核心 ,确保产品和服务满足客户需
求。
消除浪费
通过消除生产过程中的浪费, 提高生产效率和降低成本。
持续改进
不断寻求改进的机会,持续优 化生产过程和流程。
团队合作
强调团队成员之间的协作和沟 通,共同实现生产目标。
02
精益生产工具与方法
特点
注重客户需求,强调持续改进, 追求卓越品质,降低成本并提高 生产效益。
精益生产的发展历程
01
02
03
起源
起源于日本丰田汽车公司 ,以减少浪费、提高生产 效率为目标。
精益生产培训材料

精益生产培训材料精益生产是一种管理理念,以减少浪费和提高效率为目标,通过优化生产流程和持续改进实现。
针对精益生产的培训材料旨在帮助组织和员工深入了解精益生产的概念和原则,学习应用各种工具和技术来改善生产流程,提高生产效率和质量。
本文将介绍精益生产的基本原理,并提供一些常用的工具和技术示例供参考。
一、精益生产的基本原理1. 将价值观念融入生产过程精益生产的第一个基本原理是将客户价值观念融入整个生产过程。
即以满足客户需求为导向,全面关注产品或服务的质量和交付时间。
了解客户需求,理解客户价值观,可以帮助组织更好地设计和优化生产流程,提供更满意的产品和服务。
2. 削减浪费精益生产的第二个基本原理是削减浪费。
浪费是指在生产过程中不增加价值的任何活动、步骤或资源。
精益生产的目标是通过消除浪费来提高生产效率和质量。
常见的浪费包括过度生产、库存积压、运输等。
通过使用工具和技术来识别和消除浪费,组织可以提高生产效率,节约成本,并提供更高质量的产品和服务。
3. 持续改进精益生产的第三个基本原理是持续改进。
持续改进是一种管理哲学,强调通过团队合作、数据分析和客户反馈来不断优化生产过程。
持续改进需要建立一种学习的文化氛围,鼓励员工提出改进意见和创新思维,并采取措施实施这些改进。
通过持续改进,组织可以不断提高生产效率和质量,赢得市场竞争优势。
二、精益生产的工具和技术示例1. 价值流图价值流图是一种以图形形式显示整个生产过程的工具。
通过绘制原始材料到交付最终产品的完整价值流,可以识别出生产过程中的各种活动和步骤,确定存在的浪费和瓶颈,并提出改进建议。
价值流图可以帮助组织全面了解生产过程,优化流程,消除浪费。
2. Kaizen活动Kaizen是一种通过小步改进来不断提高效率和质量的方法。
Kaizen活动通常由一小组员工组成,通过收集数据、分析问题和制定改进计划来解决生产过程中的具体问题。
Kaizen活动可以帮助组织培养改进意识和团队合作精神,推动持续改进。
精益生产培训讲义(PPT 77页)
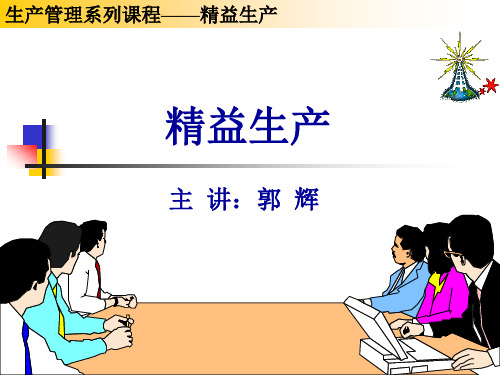
XX钢铁公司
6周预测 每周传真
生管
MRP
90/60/30d 预测
每日订货
精益生产
XX装配厂
周二+周四
每周计划
每日发运 计划
1d1次
5d卷 材
冲压
点焊#1
点焊#2
装配#1
装配#2
发运
4600左 2400右
1100左 600右
1600左 850右
1200左 640右
2700左 平台
1440右
5d 郭 辉 1s
精益生产
清洁
1
2
列队
3
4
5
列队
注塑 1 2 3 4 5
列队
装配 1 2 3 4 5
列队
检查 1 2 3 4 5
该加工车间机器的摆放是依照相同加工功能的原理,这是一个功能区平
面布局图,因此造成它的物料流动的方向是向前向后式,是无序的,存在物 料列队等候的状况。
郭辉
20:15 19
1、库存浪费的解决方法
6
……
郭辉
0 20:16 39
4、标准作业
精益生产
标准作业卡核心控制三个要素: 节拍时间、操作顺序、作业手持。
标准作业卡的目的是作为管理者观察 生产线作业状态的一种管理工具,对于发 现该生产线潜藏的问题点也很有帮助。 另一方面,该车间的监查者通过张贴标准 作业卡,表明了“自己要求工人这样作业” 的强烈意志,因而要对其内容负责。
郭辉
20:15 5
2、精益生产的的诞生
1. 成立于1937年; 2. 1949年陷入经营危机,几近破产; 3. 1957年9月,丰田汽车首次出口美国; 4. 2000年经营利润1万亿日元; 5. 2005年经营利润104亿美元; 6. 2006年成为全球最大的汽车制造商
精益生产知识培训(ppt
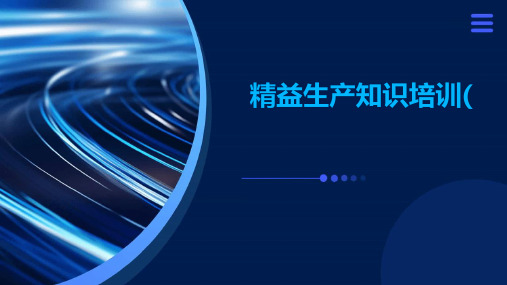
积极引入新技术、新工艺和新设备,提高生产效率和产品质量。
鼓励员工创新
鼓励员工提出改进意见和建议,激发员工的创新精神,促进企业持 续发展。
04
CATALOGUE
精益生产在服务业中的应用
服务流程优化
识别并消除浪费
01
通过对服务流程的全面分析,找出并消除浪费的时间、人力和
资源,提高服务效率。
客户需求导向
精益生产以客户需求为导向,注重满足客户需求和提高客 户满意度,通过快速响应市场需求和灵活调整生产计划, 实现个性化、定制化的生产。
02
CATALOGUE
精益生产的主要工具
5S管理
01
02
03
04
05
整理(Seiri)
整顿(Seiton) 清扫(Seiso)
清洁(Seiketsu 素养(Shitsuke
精益生产的核心思想
消除浪费
精益生产强调消除生产过程中的浪费,包括时间、人力、 物力等方面的浪费,以提高生产效率和降低成本。
持续改进
精益生产强调持续改进和优化生产过程,通过不断改进生 产方法、引入新技术、提高员工技能等方式,不断提高生 产效率和产品质量。
提高效率
精益生产注重提高生产效率,通过优化生产流程、提高设 备利用率、减少停机时间等方式,实现高效、低成本的生 产。
客户反馈机制
建立有效的客户反馈机制,及时了解客户的需求和意见,不断改 进服务,提高客户忠诚度。
持续改进与创新
持续改进
不断寻求改进的机会,通过持续改进提高服务质量和效率。
创新思维
鼓励员工提出创新性的想法和建议,以适应不断变化的市场需求和 客户需求。
跨部门合作
促进不同部门之间的合作,共同寻找改进和创新的机会,推动公司持 续发展。
精益生产基础知识培训课件

5S管理
总结词
5S管理是一种现场管理方法,包括整理 、整顿、清扫、清洁和素养五个方面。
VS
详细描述
5S管理是精益生产的基础,通过规范现 场管理,提高工作效率和减少浪费。整理 和整顿主要是对物品进行分类和标识,保 持工作区域整洁有序。清扫和清洁则是保 持工作区域干净卫生,减少污染和故障。 素养则强调员工遵守规章制度,养成良好 的工作习惯。
详细描述
自动化与智能化可以减少人工干预和人为错误,提高生产过程的稳定性和可靠性。通过引入先进的自动化设备和 智能化系统,企业可以实现生产过程的自动化和智能化,提高生产效率和产品质量。同时,自动化与智能化还可 以降低劳动成本和人力资源的依赖程度。
03
精益生产实施步骤
明确目标与期望
01
目标设定
明确企业实施精益生产的目标,如降低成本、提 高效率、优化流程等。
要点二
增强企业竞争力
通过优化生产和供应链管理,精益生产能够帮助企业获得 竞争优势。
精益生产的优势与局限
01
局限
02
03
04
适用范围有限:精益生产主要 适用于制造业,对于其他行业
可能不太适用。
对员工素质要求高:精益生产 需要员工具备较高的技能和素 质,以及较强的自我管理能力
。
变革阻力:实施精益生产需要 对企业进行深度的变革,可能 会遇到来自员工和管理层的阻
精益生产与传统生产的区别
关注点
精益生产关注价值流 和客户需求,而传统 生产关注产量和效率
。
灵活性
精益生产强调灵活性 和快速响应,而传统 生产更注重稳定性和
计划性。
浪费消除
精益生产通过消除浪 费来提高效益,而传 统生产可能忽略或无
精益生产基础培训讲义

與大量生產思想觀念的變革
四.精益生產的精髓
2.“瘦”,豐田式“瘦型”生產方式 “減肥”運動,剔除多余的機構,富余的人力, 把無效益的事情都砍掉.
四.精益生產的精髓
3.在制品是萬惡之源,提倡在制品向零挑戰.
大量生產把一定量的在制品當作 均衡生產的必要條件
严格把控质量关,让生产更加有保障 。2020 年11月 下午8时 21分20 .11.252 0:21No vember 25, 2020
重规矩,严要求,少危险。2020年11 月25日 星期三8 时21分 55秒20 :21:552 5 November 2020
好的事情马上就会到来,一切都是最 好的安 排。下 午8时21 分55秒 下午8 时21分2 0:21:55 20.11.2 5
(4)不重要也不緊急
馬上辦理
輕
好好規劃
重
馬上辦但只花一點時間
或找人代辦 緩
有空再辦
急
c.工作的時段管理
(1)早上八點至十點: 精力顛峰,適合作規劃 (2)早上十點至十二點:注意力及短暫記憶力最強,
適合腦力激蕩會議,訓練等. (3)下午一點至二點:昏昏欲睡,適合互動溝通工作. (4)下午二點至四點:開始清醒,長期記憶力最淺,適
例:
某日一機臺投入24Hour,其中保養1Hour,機故維修
0.5Hour,待料2Hour.則當日:
24-1-0.5-2
稼動率=
×100%=85%
24
可動率=
24-1-0.5 22
×100%=94%
4.平衡率:
各工序平均工時
平衡率 =
×100%
精益生产培训讲义

精益生产培训讲义第一节:精益生产概述1.1 什么是精益生产?1.2 精益生产的历史和起源1.3 精益生产的核心原则1.4 精益生产的优势和价值第二节:精益生产工具和技术2.1 价值流图2.1.1 价值流图的作用和目的2.1.2 价值流图的绘制过程2.1.3 价值流图的分析和改进2.2 5S整理法2.2.1 5S整理法的概述2.2.2 5S整理法的步骤和注意事项2.2.3 5S整理法的效果和应用2.3 KANBAN2.3.1 KANBAN的概述2.3.2 KANBAN的原理和种类2.3.3 KANBAN的实施和管理2.4 产线平衡2.4.1 产线平衡的作用和目的2.4.2 产线平衡的方法和策略2.4.3 产线平衡的评估和改进第三节:精益生产的实施和管理3.1 精益生产的实施步骤3.1.1 确定目标和范围3.1.2 分析和改善价值流程3.1.3 设计和实施改进方案3.1.4 迭代和持续改进3.2 精益生产管理的关键要素3.2.1 量化和可视化3.2.2 持续培训和培养改进文化3.2.3 激励和奖励系统3.2.4 持续沟通和反馈机制3.3 精益生产管理的挑战和解决方案3.3.1 战略执行和组织文化3.3.2 管理层的支持和领导力3.3.3 各部门协同与合作第四节:精益生产的应用案例分析4.1 公司A的精益生产实施过程和成果4.2 公司B的精益生产实施过程和挑战4.3 公司C的精益生产实施过程和经验分享第五节:精益生产的持续改进5.1 持续改进的重要性和原则5.2 PDCA循环5.3 DMAIC方法5.4 问题解决工具和技术第六节:总结与展望6.1 精益生产的回顾与总结6.2 精益生产的未来发展趋势6.3 精益生产的个人应用和实践建议参考资料:- Womack, J.P., Jones, D.T., and Roos, D. (1990) The Machine That Changed the World, New York: Free Press.- Rother, M. and Shook, J.P. (1998) Learning to See: Value Stream Mapping to Add Value and Eliminate MUDA, Brookline, MA: Lean Enterprise Institute.- Ohno, T. (1988) Toyota Production System: Beyond Large-Scale Production, New York: Productivity Press.第一节:精益生产概述1.1 什么是精益生产?精益生产是一种以提供最大价值为核心的生产管理方法,旨在通过最小化浪费和优化流程,实现高效生产和优质产品。
精益生产基础知识培训课件ppt
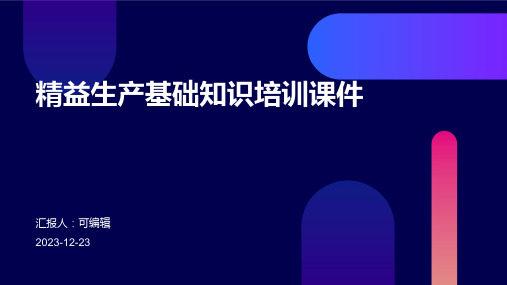
汇报人:可编辑 2023-12-23
目录
• 精益生产概述 • 精益生产工具与方法 • 精益生产实施步骤 • 精益生产案例分析 • 精益生产的未来发展
01
精益生产概述
定义与特点
定义
精益生产是一种以客户需求为导 向,通过消除浪费、持续改进和 优化流程来提高生产效率和降低 成本的制造模式。
智能化生产
通过引入自动化设备和智能机器人,实现生产流程的智 能化,降低人工成本,提高生产线的柔性。
个性化与定制化生产的发展
个性化需求
随着消费者需求的多样化,企业 将更加注重个性化生产,满足不 同客户的定制化需求。
定制化生产
通过引入快速原型制造和3D打印 等技术,实现定制化产品的快速 生产,缩短产品上市时间。
5S管理
总结词
5S管理是一种现场管理方法,包括整理、整顿、清扫、清洁和素养五个方面。
详细描述
5S管理是精益生产中的重要组成部分,它通过规范现场工作环境,提高工作效 率,降低浪费。通过实施5S管理,企业可以营造一个整洁、有序、安全的工作 环境,从而提高员工的工作效率和产品质量。
快速换模
总结词
快速换模是一种减少换线时间、提高生产效率的方法。
减少浪费
总结词
减少浪费是精益生产中最重要的目标之一,它包括减少时间 、人力、物力等方面的浪费。
详细描述
在精益生产中,减少浪费是最核心的目标之一。浪费不仅包 括原材料、能源等物质方面的浪费,还包括时间、人力等资 源方面的浪费。通过消除浪费,企业可以提高效率、降低成 本、提高质量,从而实现可持续发展。
03
精益生产实施步骤
明确目标与期望
目标设定
明确企业实施精益生产的目标,如降 低成本、提高效率、优化流程等。
《精益生产培训资料》课件
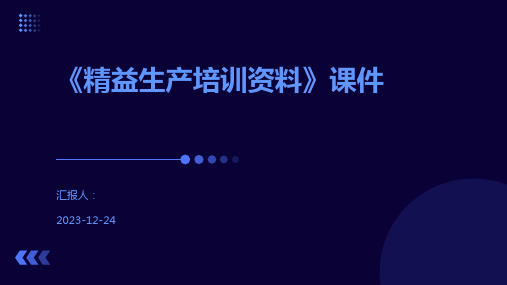
案例三:某机械制造企业的自动化升级改造
总结词
自动化升级改造,提高生产质量和效率
详细描述
某机械制造企业通过自动化升级改造,提高了生产质量和效率。该企业引入了先进的数 控机床和机器人,实现了自动化加工和装配。同时,采用传感器和数据采集系统对生产 过程进行实时监控和反馈控制,确保了产品质量和生产效率的提升。此外,自动化升级
重视团队合作和跨部门协作,打破部门壁垒。
特点 追求流程的持续改进,不断消除浪费,提高效率。 采用灵活的生产方式,快速适应市场变化。
精益生产的核心思想
价值
以客户价值为出发点, 识别并创造真正有价值
的流程。
流动
使价值流在生产过程中 连续流动,减少等待和
库存。
拉动
根据客户需求拉动生产 ,避免过量生产和浪费
优化流程
根据总结的经验教训,持续优化生 产流程,提高生产效率和产品质量 。
建立持续改进机制
将精益生产的理念和方法融入日常 工作中,形成持续改进的企业文化 。
04
精益生产案例研究
案例一:某汽车制造企业的精益生产实践
总结词
通过精益生产实践,实现生产效率提升和成本降低
详细描述
某汽车制造企业在精益生产实践中,通过消除浪费、优化流程和提升员工参与度,实现了生产效率提升和成本降 低。具体措施包括采用看板管理、单件流和持续改进等方法,改进了生产线布局和作业流程,减少了等待、搬运 和不良品等浪费现象。
通过持续改进,企业可以不断发 现并解决存在的问题,提高产品
质量和生产效率。
持续改进有助于激发员工的创新 精神,促进企业持续发展。
自动化与机器人
自动化与机器人是现代工业生产中常 用的技术手段,可以提高生产效率、 降低生产成本。
精益生产课程培训讲义
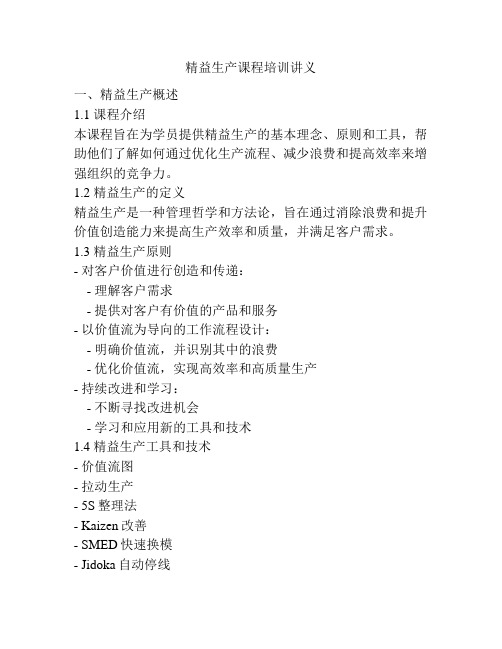
精益生产课程培训讲义一、精益生产概述1.1 课程介绍本课程旨在为学员提供精益生产的基本理念、原则和工具,帮助他们了解如何通过优化生产流程、减少浪费和提高效率来增强组织的竞争力。
1.2 精益生产的定义精益生产是一种管理哲学和方法论,旨在通过消除浪费和提升价值创造能力来提高生产效率和质量,并满足客户需求。
1.3 精益生产原则- 对客户价值进行创造和传递:- 理解客户需求- 提供对客户有价值的产品和服务- 以价值流为导向的工作流程设计:- 明确价值流,并识别其中的浪费- 优化价值流,实现高效率和高质量生产- 持续改进和学习:- 不断寻找改进机会- 学习和应用新的工具和技术1.4 精益生产工具和技术- 价值流图- 拉动生产- 5S整理法- Kaizen改善- SMED快速换模- Jidoka自动停线- 库房管理- TPM全员维护二、精益生产工具的使用2.1 价值流图- 价值流图的定义和作用- 如何绘制价值流图- 分析价值流图,识别浪费,制定改进计划2.2 拉动生产- 拉动生产的原理和好处- 瓶颈理论和平衡生产- 如何实施拉动生产2.3 5S整理法- 5S整理法的目的和原理- 5S五个步骤的具体操作- 维持5S的方法和建议2.4 Kaizen改善- Kaizen改善的概念和原则- PDCA循环的具体步骤- 如何开展改善活动2.5 SMED快速换模- SMED快速换模的意义和原理- SMED步骤的具体操作- 实现快速换模的关键要点2.6 Jidoka自动停线- Jidoka自动停线的目的和原理- 如何实施Jidoka- Jidoka在质量管理中的应用2.7 库房管理- 库房管理的重要性和挑战- 5S在库房管理中的应用- JIT库存管理的原理和实践2.8 TPM全员维护- TPM全员维护的意义和目标- TPM的五大支柱- 如何推动和实施TPM三、精益生产的案例分析3.1 汽车制造业中的精益生产- 丰田生产方式的介绍- 丰田生产系统的成功经验3.2 制造业以外的精益生产应用- 精益服务的原则和案例- 精益医疗的理念和实践- 精益建筑的方法和效果四、精益生产的挑战和解决方案4.1 精益生产的挑战- 文化转变和员工参与- 可持续改进的问题- 管理者的角色和责任4.2 精益生产的解决方案- 培训和教育的重要性- 建立改进文化和激励机制- 在全员参与和持续改进上下功夫五、结语精益生产是一种持续追求卓越的经营理念,其原则和工具可以应用于各个行业和领域。