金属粉末的制备方法及基本原理(2)
粉末冶金成型

2.高速压制
瑞典开发出粉末冶金用高速压制法。这可能是 粉末冶金工业的又一次重大技术突破。高速压制采 用液压冲击机,它与传统压制有许多相似之处,但关 键是压制速度比传统快500~1000倍,其压头速度高 达2~30m/s,因而适用于大批量生产。液压驱动的 重锤(5~1200kg)可产生强烈冲击波,0.02s内将压 制能量通过压模传给粉末进行致密化。重锤的质量 与冲击时的速度决定压制能量与致密化程度。
(2)生坯强度高
常规工艺的生坯强度约为10~20MPa,温压压坯的强度则为 25~30MPa,提高了1.25-2倍。生坯强度的提高可以大大降 低产品在转移过程中出现的掉边、掉角等缺陷,有利于制备 形状复杂的零件;同时,还有望对生坯直接进行机加工,免 去烧结后的机加工工序,降低了生产成本。这一点在温压烧结连杆制备中表现得尤为明显。
温压成型技术发展趋势: 预合金化粉末的制造技术; • 新型聚合物润滑剂的设计; • 石墨粉末有效添加技术; • 无偏析粉末的制造技术; • 温压系统制备技术。
温压成型技术应用:
温压技术主要适合生产铁基合金零件。同时人们正在 尝试用这种技术制备铜基合金等多种材料零件。由于温压 零件的密度得到了较好的提高,从而大大提高了铁基等粉 末冶金制品的可靠性,因此温压技术在汽车制造 机械制 造、武器制造等领域存在着广阔的应用前景。
6.注射成形技术
Injection molding technology
金属粉末注射成形技术是随着高分子材料的应用 而发展起来的一种新型固结金属粉、金属陶瓷粉和陶 瓷粉的特殊成形方法。它是使用大量热塑性粘结剂与 粉料一起注入成形模中,施于低而均匀的等静压力, 使之固结成形,然后脱粘结剂烧结。
5.注射成形技术
美国开发出一种能在室温下生产全致密零 件而无需后续烧结的粉末冶金工艺。此工艺称 之为“冷成形粉末冶金”。 它采用特殊配制的活化溶液与革新的进料 靴技术,在压力下精确地将粉末注入模中。加 压输送的进料靴使粉末填充更加均匀,而活性 溶液则防止形成氧化物,从而大大促进了冷焊 效应。
冶金工程中的金属材料制备与处理

冶金工程中的金属材料制备与处理冶金工程是研究和应用金属材料的学科,涉及金属材料的制备、加工以及性能改善等方面。
金属材料是冶金工程中的核心,其制备与处理技术的发展对于现代工业的进步有着重要意义。
本文将从金属材料制备的基本原理,常见的制备方法,以及处理技术等方面进行论述。
一、金属材料制备的基本原理金属材料制备过程中的基本原理主要包括金属的途径形成和结晶行为。
金属的形成途径有两种,一种是地质过程,如矿石的形成;另一种是冶金过程,如金属的提取和冶炼。
金属在固态状态下具有晶体结构,通过加热和冷却等方式可以控制其晶体形貌和晶粒尺寸。
二、金属材料制备的常见方法1. 粉末冶金法:粉末冶金法是将金属或合金粉末压制成型,再进行烧结或热处理的一种制备方法。
其优点是可以得到具有高纯度和均匀组织的材料。
粉末冶金法广泛应用于金属粉末冶金制品、金属陶瓷制品和各种复合材料的制备。
2. 液相冶金法:液相冶金法是指将金属或合金在液态下进行熔化和制备的方法。
常见的液相冶金法有熔模铸造法、凝固锭法等。
这些方法可以制备大型和复杂形状的金属制品。
三、金属材料的处理技术金属材料制备完成后,还需要进行一系列的处理技术以改善其性能和使用价值。
常见的处理技术有热处理、表面处理和变形处理等。
1. 热处理:热处理是通过控制金属材料的加热和冷却过程,改变其组织结构和性能的一种方法。
常见的热处理方法包括退火、淬火、回火等。
热处理可以提高金属的硬度、强度和耐腐蚀性能。
2. 表面处理:表面处理是指对金属材料表面进行物理、化学或机械上的处理,以改变其表面特性的方法。
常见的表面处理方法有电镀、喷涂、陶瓷涂层等。
表面处理可以提高金属的耐磨性、耐腐蚀性和装饰性。
3. 变形处理:变形处理是通过塑性变形改变金属材料的组织结构和性能。
常见的变形处理方法有压力加工、轧制、拉伸等。
变形处理可以提高金属的强度、韧性和塑性。
综上所述,冶金工程中的金属材料制备与处理是冶金学的重要内容。
粉末冶金原理知识要点
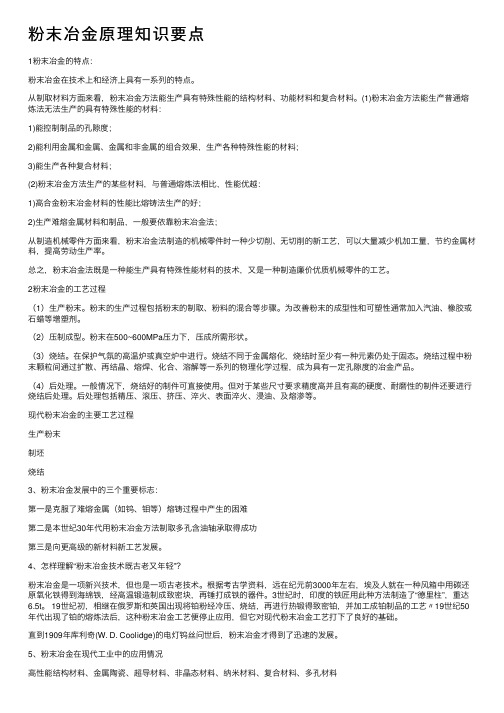
粉末冶⾦原理知识要点1粉末冶⾦的特点:粉末冶⾦在技术上和经济上具有⼀系列的特点。
从制取材料⽅⾯来看,粉末冶⾦⽅法能⽣产具有特殊性能的结构材料、功能材料和复合材料。
(1)粉末冶⾦⽅法能⽣产普通熔炼法⽆法⽣产的具有特殊性能的材料:1)能控制制品的孔隙度;2)能利⽤⾦属和⾦属、⾦属和⾮⾦属的组合效果,⽣产各种特殊性能的材料;3)能⽣产各种复合材料;(2)粉末冶⾦⽅法⽣产的某些材料,与普通熔炼法相⽐,性能优越:1)⾼合⾦粉末冶⾦材料的性能⽐熔铸法⽣产的好;2)⽣产难熔⾦属材料和制品,⼀般要依靠粉末冶⾦法;从制造机械零件⽅⾯来看,粉末冶⾦法制造的机械零件时⼀种少切削、⽆切削的新⼯艺,可以⼤量减少机加⼯量,节约⾦属材料,提⾼劳动⽣产率。
总之,粉末冶⾦法既是⼀种能⽣产具有特殊性能材料的技术,⼜是⼀种制造廉价优质机械零件的⼯艺。
2粉末冶⾦的⼯艺过程(1)⽣产粉末。
粉末的⽣产过程包括粉末的制取、粉料的混合等步骤。
为改善粉末的成型性和可塑性通常加⼊汽油、橡胶或⽯蜡等增塑剂。
(2)压制成型。
粉末在500~600MPa压⼒下,压成所需形状。
(3)烧结。
在保护⽓氛的⾼温炉或真空炉中进⾏。
烧结不同于⾦属熔化,烧结时⾄少有⼀种元素仍处于固态。
烧结过程中粉末颗粒间通过扩散、再结晶、熔焊、化合、溶解等⼀系列的物理化学过程,成为具有⼀定孔隙度的冶⾦产品。
(4)后处理。
⼀般情况下,烧结好的制件可直接使⽤。
但对于某些尺⼨要求精度⾼并且有⾼的硬度、耐磨性的制件还要进⾏烧结后处理。
后处理包括精压、滚压、挤压、淬⽕、表⾯淬⽕、浸油、及熔渗等。
现代粉末冶⾦的主要⼯艺过程⽣产粉末制坯烧结3、粉末冶⾦发展中的三个重要标志:第⼀是克服了难熔⾦属(如钨、钼等)熔铸过程中产⽣的困难第⼆是本世纪30年代⽤粉末冶⾦⽅法制取多孔含油轴承取得成功第三是向更⾼级的新材料新⼯艺发展。
4、怎样理解“粉末冶⾦技术既古⽼⼜年轻”?粉末冶⾦是⼀项新兴技术,但也是⼀项古⽼技术。
第二章粉末制备

粉末粒度/μm 颗粒形状 聚集状况 表观密度% 冷却速度/K· s -1 偏析程度 氧化物/10
-6
气雾化
100 球形 有一些 55 10
4
水雾化
150 不规则 很少 35 10
5
轻微 120
可忽略 3000
流体压力/MPa
流体速度/m· s 雾化效率
-1
3
100 低
14
100 中等
2)影响二流雾化性能的因素
从制备过程的实质来分:机械破碎法、物 理化学法
固态
粉末
1、金属(合金)→金属粉末:机械粉碎,电化腐蚀 2、金属氧化物(盐类)→金属粉末:还原法 3、金属+非金属化合物 →金属化合物粉末:还原-化合法
金属氧化物+非金属化合物
3 常用的粉末制备方法 3、1 机械粉碎法
碾碎 碾碎机 双辊滚碎机
机 械 粉 碎 法
雾化粉末性能的表征 a.粉末的粒度:平均粒度、粒度分布、可用粉 末收得率 b.粉末形状:松装密度、流动性、压坯密度、 比表面积 c.粉末纯度和结构:化学成分、氧化度、均匀 性、颗粒微观组织结构
A.雾化介质
空气 气体 雾化介质 影响 液体 水 惰性 气体 油
对氧化不严重或再进行还原处理的合 金。(铜、铁、碳钢) 对易氧化的金属粉末制备,含锰、硅、 钒、钛、锆的合金或镍基、钴超合金 能较好地控制颗粒形状和表面氧化 对含有易被还原的氧化物金属合金, 铁、低碳钢、合金钢(由于金属冷却 速度快粉末表面烟花大大减少)
3.2.2离心雾化
离心雾化法—利用机械旋转离心力将金属液流 击碎成细液滴,然后冷却凝结成 粉末 离心雾化法分类:旋转圆盘、旋转坩埚、旋转 电极、旋转网
1)旋转圆盘法
金属粉末的制备方法及基本原理.

金属粉末的制备方法及基本原理1引言金属粉末尺寸小,比表面积大,用其制得的金属零部件具有许多不同于常规材料的性质,如优良的力学性能、特殊的磁性能、高的电导率和扩散率、高的反应活性和催化活性等。
这些特殊性质使得金属粉末材料在航空航天、舰船、汽车、冶金、化工等领域得到越来越广泛的应用。
2金属粉末的制备方法2.1机械法机械法就是借助于机械力将大块金属破碎成所需粒径粉末的一种加工方法。
按照机械力的不同可将其分为机械冲击式粉碎法、气流磨粉碎法、球磨法和超声波粉碎法等。
目前普遍使用的方法还是球磨法和气流磨粉碎法,其优点是工艺简单、产量大,可以制备一些常规方法难以得到的高熔点金属和合金的纳米粉末。
2.1.1球磨法球磨法主要分为滚动球法和振动球磨法。
该方法利用了金属颗粒在不同的应变速率下因产生变形而破碎细化的机理。
其优点是对物料的选择性不强,可连续操作, 生产效率高,适用于干磨、湿磨,可以进行多种金属及合金的粉末制备。
缺点是在粉末制备过程中分级比较困难[3]。
2.1.2气流磨粉碎法气流磨粉碎法是目前制备磁性材料粉末应用最广的方法。
具体的工艺过程为:压缩气体经过特殊设计的喷嘴后,被加速为超音速气流,喷射到研磨机的中心研磨区从而带动研磨区内的物料互相碰撞,使粉末粉碎变细;气流膨胀后随物料上升进入分级区,由涡轮式分级器分选出达到粒度的物料,其余粗粉返回研磨区继续研磨,直至达到要求的粒度被分出为止。
整个生产过程可以连续自动运行,并通过分级轮转速的调节来控制粉末粒径大小(平均粒度在3~8 ym气流磨粉碎法适于大批量工业化生产,工艺成熟。
缺点是在金属粉末的生产过程中,必须使用连续不断的惰性气体或氮气作为压缩气源,耗气量较大;只适合脆性金属及合金的破碎制粉。
2.2物理法物理法一般是通过高温、高压将块状金属材料熔化,并破碎成细小的液滴,并在收集器内冷凝而得到金属粉末,该过程不发生化学变化。
目前研究和使用最多的物理法主要有等离子旋转电极法和气体雾化法。
制备金属粉末的方法

制备金属粉末的方法方法概述金属粉末是一种重要的材料,它具有很多优秀的物理和化学性质,被广泛应用于各种领域。
然而,制备金属粉末的方法并不简单,需要针对不同的金属材料和应用场景,选择合适的制备方法。
目前,常见的制备金属粉末的方法主要包括物理法、化学法和机械法。
各种方法的特点不同,具体应用需要根据实际情况进行选择。
物理法蒸气冷凝法蒸气冷凝法是一种将汽态金属冷凝成固态金属的制备金属粉末的方法。
首先以加热的方式将金属加热到其蒸发温度,然后将蒸气冷却到固态,从而制备出金属粉末。
这种方法适用于硬度高、熔点高、塑性差的金属材料,如钨、铬等。
筛选法筛选法是一种将铸造坯料经过机械破碎后,采用筛分的方法将粉末分离的方法。
这种方法简单、设备成本低,但一次性回收率低,且粒径分布较大。
化学法沉淀法沉淀法是一种将水溶性盐基于反应析出的方法,将金属离子通过反应沉淀成金属粉末。
这种方法适用于生产精度较高、单一元素粉末的制备,如氢氧化钠法制备氧化铁、氯化钴法制备钴粉等。
沉淀法的优点在于制备的粉末粒径均匀,且可以精确控制粒径大小。
气相还原法气相还原法是一种产生气相金属原子,通过气相还原反应制备金属粉末的方法。
以氢气或其他还原剂为还原剂,使金属离子还原成原始金属,从而制备金属粉末。
气相还原法适用于制备高纯度的金属材料,如纯铁粉、二氧化钛粉、二氧化硅粉等。
机械法高能球磨法高能球磨法是一种通过高能球团磨碾金属材料,产生热、化学反应,从而制备金属粉末的方法。
首先将金属粉体加入到高能球磨机中,球体和粉末在磨擦作用下不断碰撞和摩擦,产生高温和高压,使金属粉末发生塑性变形和破碎。
高能球磨法适用于制备高性能的、纯度高的金属材料,如高性能钛合金、纳米钨粉等。
结语以上是制备金属粉末的主要方法,选取合适的方法需要根据材料性质、产品要求等多方面因素考虑。
希望本文能够对大家了解制备金属粉末的方法有所帮助。
粉末的制备

(2)喷嘴结构
•嘴结构应具备以下基本条件; •雾化介质获得尽可能高的出口速度; •雾化介质与金属液流之间形成合理的喷射角度; •金属液流产生最大的紊流;
•金属液流雾化稳定,不会因出口负压造成喷嘴堵塞。
(3)液流性质
金属液的表面张力
金属液的粘度
金属液的的化学组成 金属液的过热温度
(4)喷射方式
K 1 K
V
2 gK K 1
RT2 [1 ( ) ]
P 1 P2
式中
g—重力加速度
R—气体常数 K—压容比,即Cp/Cv,空气的K值等1.4
T—压缩气体进喷嘴前的温度,K
P1—气体流往环境的压力 P2—使气体流出喷嘴的压力
如果以空气为雾化介质进行雾化,假设T2不变化,将
P1=1大气压,K=1.4代入式上式 ,则可变形为
雾化过程的四种情况
动能交换:雾化介质的动能转变为金属液滴的表面能;
热量交换:雾化介质带走大量的液固相变潜热;
流变特性变化:液态金属的粘度及表面张力随温度的降
低而不断发生变化;
化学反应:高比表面积颗粒(液滴或粉粒)的化学活性 很强,会发生一定程度的化学反应。
气雾化的四个区域
•负压紊流区—高速气流的抽吸作用,在喷嘴中心孔下方形成负压紊流层;
粉末平均粒度及100目以下粉末收得率随雾化盘转速而变化的情况
12000 24000 36000 雾化盘转速,r/min Revolution of atomizing disc 187 154 135 粉末平均粒度,μ m Mean powder particle size 33.0 44.5 56.0 —100 目粉末收得率,% Recovery rate of –100 mech powder
粉末冶金工艺的基本工序(二篇)
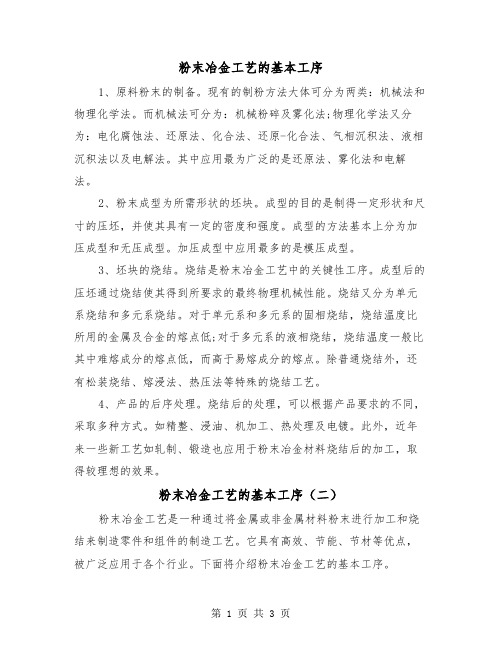
粉末冶金工艺的基本工序1、原料粉末的制备。
现有的制粉方法大体可分为两类:机械法和物理化学法。
而机械法可分为:机械粉碎及雾化法;物理化学法又分为:电化腐蚀法、还原法、化合法、还原-化合法、气相沉积法、液相沉积法以及电解法。
其中应用最为广泛的是还原法、雾化法和电解法。
2、粉末成型为所需形状的坯块。
成型的目的是制得一定形状和尺寸的压坯,并使其具有一定的密度和强度。
成型的方法基本上分为加压成型和无压成型。
加压成型中应用最多的是模压成型。
3、坯块的烧结。
烧结是粉末冶金工艺中的关键性工序。
成型后的压坯通过烧结使其得到所要求的最终物理机械性能。
烧结又分为单元系烧结和多元系烧结。
对于单元系和多元系的固相烧结,烧结温度比所用的金属及合金的熔点低;对于多元系的液相烧结,烧结温度一般比其中难熔成分的熔点低,而高于易熔成分的熔点。
除普通烧结外,还有松装烧结、熔浸法、热压法等特殊的烧结工艺。
4、产品的后序处理。
烧结后的处理,可以根据产品要求的不同,采取多种方式。
如精整、浸油、机加工、热处理及电镀。
此外,近年来一些新工艺如轧制、锻造也应用于粉末冶金材料烧结后的加工,取得较理想的效果。
粉末冶金工艺的基本工序(二)粉末冶金工艺是一种通过将金属或非金属材料粉末进行加工和烧结来制造零件和组件的制造工艺。
它具有高效、节能、节材等优点,被广泛应用于各个行业。
下面将介绍粉末冶金工艺的基本工序。
原料的选取与预处理是粉末冶金工艺的第一个基本工序。
该工序主要包括材料的选择、粉末制备和粉末预处理。
首先,根据工件的要求和使用环境,选择适合的金属粉末或非金属粉末作为原料。
然后,通过机械研磨、化学法或物理法等方法,将原料加工成所需要的粉末。
最后,对粉末进行筛分、干燥和除尘等预处理操作,以提高粉末的质量和工艺性能。
混合是粉末冶金工艺的第二个基本工序。
混合是指将不同种类的粉末按一定比例混合在一起,以得到具有所需成分和性能的混合粉末。
混合可以采用机械混合、湿式混合或干式混合等方法进行。
粉末冶金2 粉末的制备(2)

第2部分粉末的制备(2)PowdermetallurgyprinciplePowderfabricationbyelectrolytic第六章、电解制粉electrolyte(Hydro—metallurgy)Twomethodstoelectrolyte溶液电解:liquidelectrolyte制取Fe、Cu、Ag、Sn、Mo、Pb、Au熔盐电解moltensaltelectrolyte制取Ti、Zr、Be、Ta、Nb、Th、稀有金属及合金rear,metallicalloys Anelectrolyticcelloperationfordepositionofmetalpowders,therawmetalisdissolvedat theanodeanddepositedatthecathode,(Fe,Cu,Au,Ag,Ni,etc.) RelationofmetalionsversusdistancetocathodeC0:ionconcentrationatthecathode,C:ionconcentrationinthesolution Scanningelectronmicrographofelectrolyticcopperpowdershowtypicaldendriticshape Procedureofcopperpowderproductionbyelectrolyticfromsolutionandprocessingparamet ersCathodesCuSO4sol.Anodes(120-150g/L)Electrolyticdeposition,(i=25a/dm2,1.8v,50°C)Cupowderoncathodespickpowder20minintervalWashinganddryingwaterandvacuumMillingandscreen,Cupowder一、电解基本原理及规律BasicMechanism当外加电位=原电池电位时E外=E池,氧化还原平衡oxidation-reductionequilibrium. 当外加电位大于原电池cellvoltage电位时,电解发生,阳极氧化anode,阴极cathode还原电极电位的意义:electrode标准电极电位,即离子在浓度等于克离子/升溶液中的还原电位,如:水溶液电解基本原理——电化学原理定义definition:在直流电作用下,在电极上产生氧化与还原的过程称之为电解在阳极anode上失去电子electronlosing,氧化反应oxidationreaction,成为正离子在阴极cathode上金属正离子获得电子electron,obtaining还原成为金属原子电解时,电能转化为化学能——作用与原电池相反reversetoelectriccell,如图所示,化学能——粉末表面能n离子价电数,F=96500库仑,法拉第常数[还]还原物浓度[氧]氧化物浓度T=25ºR=8.3161、电解区,在阴极区,电极电位正着先还原;非标准状态下,电极电位与溶液中离子浓度的关系—涅斯特方程:Insolution,化学位用活度activity表示,纯金属活度Dilutesolution(稀)溶液中,活度activityconcentration,气体的活度等于各分压,所以:1、电极反应(forexampleCuelectrolyte)见图化学体系:Cu粉/Cu离子,CuSO4,H2SO4,H2O/Cu粉,1)硫酸铜水解反应,2)硫酸水解反应,3)阳极氧化反应阳极铜板失去电子,变成离子,进入溶液,即阳极去掉离子,析出氧气。
金属粉末注射成型工艺及研究进展

金属粉末注射成型工艺及研究进展金属粉末注射成型(Metal Powder Injection Molding)是一种将金属粉末与有机增塑剂混合,并经过成型、脱脂与烧结等工艺步骤得到高密度的金属制品的先进制造技术。
自20世纪60年代开始发展以来,金属粉末注射成型技术在汽车、航空航天、医疗器械等领域得到了广泛应用。
本文将着重介绍金属粉末注射成型工艺的基本原理和研究进展。
一、基本原理金属粉末注射成型工艺主要包括以下几个步骤:原料制备、混合、注射成型、脱脂与烧结。
1. 原料制备在金属粉末注射成型过程中,合适的原料对成品制品的性能和质量起着决定性的作用。
通常,金属粉末的粒径要细小,分布要均匀,并具备良好的流动性。
为了提高金属粉末的流动性,往往需要通过表面处理、添加润滑剂等方法进行改性。
2. 混合在混合过程中,金属粉末与有机增塑剂按一定比例进行混合,并通过机械作用使其均匀分散。
混合的目的是为了使金属粉末与增塑剂形成均匀的糊状混合物,便于后续注射成型工艺的进行。
3. 注射成型注射成型是金属粉末注射成型工艺的核心步骤。
通过将混合物注射进注射机的模具腔中,并在一定的压力和温度下进行填充与压实,使其形成所需形状的绿体。
注射成型的优势在于可以制造出复杂且精密的金属件,且生产效率较高。
4. 脱脂与烧结脱脂与烧结是为了最终获得高密度的金属制品。
脱脂过程中,通过热处理将有机增塑剂从绿体中除去,获得无机绿体。
而烧结过程则是将无机绿体在高温下进行热处理,使金属粉末颗粒相互结合,形成致密的金属零件。
二、研究进展金属粉末注射成型技术在近年来获得了许多关注,在工艺、材料以及设备等方面取得了一系列的研究进展。
1. 工艺优化为了提高金属粉末注射成型工艺的效率和品质,研究者们进行了大量的工艺优化研究。
例如,通过调整注射成型参数、优化模具结构以及改变绿体预烧工艺等,可以有效改善成品的性能和质量。
2. 材料开发金属粉末注射成型所使用的金属粉末涉及多种材料,如不锈钢、钴基合金、铁基合金等。
金属粉末注射成型(MIM)简介及基本流程 (2)

材料体系
低合金钢 不锈钢 硬质合金
陶瓷 重合金 钛合金 磁性材料 工具钢
表1 常用的MIM材料及其应用领域
合金牌号、成分
Fe-2Ni、 Fe-8Ni 316L 、17-4PH、 420、 440C
11
第第六六章章:M:IMM制IM造制流程造流程
MIM工艺分类-根据脱脂方式不同:
脱脂方式 溶剂脱脂
热气氛下进行脱脂
脱脂环境 有机溶剂
水 硝酸气体
真空
脱脂工艺 浸泡在溶剂中并加热 (50~70)
浸泡在溶剂中并加热 (40~50) 暴露于硝酸气体中并加热 (120~170C) 加热(25~600C)
方法
热 (一段脱脂)
溶剂 (二段脱脂)
催化 (二段脱脂)
脱脂时间
生坯厚度<10mm, 16 ~ 22 hr 生坯厚度<10mm, 4 ~ 8 hr (第二段热脱需要约6小时追加) 1mm of a Green Part /hr , (第二段热脱需要约6小时追加)
应用领域:
金属注射成形其产品广泛应用于电子信息工程、生物医疗器械、办公设备、汽车、机械、五 金、体育器械、钟表业、兵器及航空航天等工业领域。因此,国际上普遍认为该技术的发展将会 导致零部件成形与加工技术的一场革命,被誉为“当今最热门的零部件成形技术”和“21世纪的 成形技术”
第二章:常用材料
MIM技术适用材料:
水喷粉 x2500倍
第三章:喂料-粘结剂
2.2 结合剂
结合剂又称粘结剂 功能:
粉末冶金原理
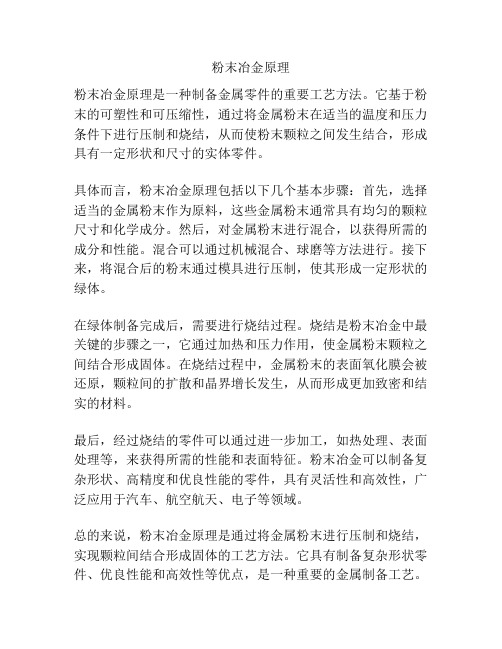
粉末冶金原理
粉末冶金原理是一种制备金属零件的重要工艺方法。
它基于粉末的可塑性和可压缩性,通过将金属粉末在适当的温度和压力条件下进行压制和烧结,从而使粉末颗粒之间发生结合,形成具有一定形状和尺寸的实体零件。
具体而言,粉末冶金原理包括以下几个基本步骤:首先,选择适当的金属粉末作为原料,这些金属粉末通常具有均匀的颗粒尺寸和化学成分。
然后,对金属粉末进行混合,以获得所需的成分和性能。
混合可以通过机械混合、球磨等方法进行。
接下来,将混合后的粉末通过模具进行压制,使其形成一定形状的绿体。
在绿体制备完成后,需要进行烧结过程。
烧结是粉末冶金中最关键的步骤之一,它通过加热和压力作用,使金属粉末颗粒之间结合形成固体。
在烧结过程中,金属粉末的表面氧化膜会被还原,颗粒间的扩散和晶界增长发生,从而形成更加致密和结实的材料。
最后,经过烧结的零件可以通过进一步加工,如热处理、表面处理等,来获得所需的性能和表面特征。
粉末冶金可以制备复杂形状、高精度和优良性能的零件,具有灵活性和高效性,广泛应用于汽车、航空航天、电子等领域。
总的来说,粉末冶金原理是通过将金属粉末进行压制和烧结,实现颗粒间结合形成固体的工艺方法。
它具有制备复杂形状零件、优良性能和高效性等优点,是一种重要的金属制备工艺。
第三章 粉末冶金--概述,粉体制备

2. 粉体的特性
(1)粉体的粒度与粒度分布 ) (2)粉体颗粒的形状 ) (3)粉体的表面特性 (4)粉体的流动性
2. 粉体的特性
(1) 粒度和粒度分布 ) 粉体的粒度:指粉体颗粒的线性尺寸。 粉体的粒度:指粉体颗粒的线性尺寸。 粒度分布:不同粒度的颗粒占全部粉体的百分含量。 粒度分布:不同粒度的颗粒占全部粉体的百分含量。 粉体的粒度和粒度分布主要与粉体的制取方法和工 的粒度和粒度分布主要与粉体 艺条件有关。机械粉碎的粉体一般较粗, 艺条件有关。机械粉碎的粉体一般较粗,气相沉积的粉体 极细。 极细。 粉体的粒度和粒度分布对粉末的压制与烧结过程以及 最终产品的性能有很大影响。例如:在烧结过程中, 最终产品的性能有很大影响。例如:在烧结过程中,与粗 粉压制的压坯相比, 粉压制的压坯相比,细粉压制的压坯在相同的烧结条件下 烧结时更容易收缩。 烧结时更容易收缩。
1. 粉体的制备技术
(1) 机械粉碎法 ) 采用振动球磨和搅动球磨可提高研磨速度。 采用振动球磨和搅动球磨可提高研磨速度。
1. 粉体的制备技术
(2)雾化法 ) 雾化法, 雾化法,利用水流或气流直接击碎液体金属制 取粉末的方法。应用较广泛。 取粉末的方法。应用较广泛。 雾化法可以制取铅、锡、铝、锌、铜、镍、铁 雾化法可以制取铅、 等金属粉体,也可制取黄铜、青铜、合金钢、 等金属粉体,也可制取黄铜、青铜、合金钢、高 速钢、不锈钢等预合金粉体。 速钢、不锈钢等预合金粉体。 雾化法包括: 雾化法包括: 1)二流雾化法;2)离心雾化法;3) 超声波雾化。 二流雾化法; 离心雾化法 离心雾化法; 超声波雾化。 二流雾化法
3.2 粉体的制备与处理
(2)雾化法 ) 2)离心雾化法 ) 离心雾化就是利用机械旋转造成的离心力将 金属液流击碎成细的液滴,然后冷却凝结成粉末。 金属液流击碎成细的液滴,然后冷却凝结成粉末。 常用的有旋转圆盘雾化,旋转水流雾化, 常用的有旋转圆盘雾化,旋转水流雾化,旋 转电极雾化等。 转电极雾化等。
粉末冶金原理

粉末冶金原理粉末冶金新技术摘要本文主要从粉末冶金的基本工艺过程阐述粉末冶金工业今年出现的新工艺,粉末冶金的制粉,成型,烧结等方面论述了粉末冶金的新工艺以及这些工艺的特点及相关应用,论述粉末冶金的新工艺的发展方向关键字:粉末冶金、新技术、粉末冶金工艺1.引言粉末冶金是制取金属或用金属粉末(或金属粉末与非金属粉末的混合物)作为原料,经过成形和烧结,制造金属材料、复合以及各种类型制品的工艺技术。
粉末冶金法与生产陶瓷有相似的地方,因此,一系列粉末冶金新技术也可用于陶瓷材料的制备。
由于粉末冶金技术的优点,它已成为解决新材料问题的钥匙,在新材料的发展中起着举足轻重的作用粉末冶金是一门新兴的材料制备技术。
近代粉末冶金兴起于19世纪末20世纪初。
至20世纪30年代, 粉末冶金整套技术逐步形成, 工业生产初具规模, 对工艺过程及其机理的研究也取得了一定成果。
20世纪中期, 粉末冶金生产技术发展迅速, 产品应用领域不断扩大, 成为现代工业的重要组成部分。
并在此基础上, 为适应科学技术飞速发展对材料性能和成形技术提出的更高要求, 开发了多项粉末冶金新工艺, 包括: 热等静压、燃烧合成、快速凝固、喷射成形、机械合金化、粉末注射成形、温压成形、快速全向压制、粉末锻造、热挤压、爆炸。
2.粉末冶金新技术--制粉2.1雾化法制备金属粉末---低氧含量铁粉生产在无氧气氛中进行, 并包含一些石蜡,这些分解为碳与氢。
碳与铁反应, 形成很薄的富碳表面层。
碳含量使颗粒的延性降低, 但提高了表面的烧结活性。
在粉末压块中, 碳易于扩散到颗粒中心及相邻的颗粒中, 因而可用于生产不需添加石墨的粉末冶金钢。
瑞典IPS钢粉公司每年低氧含量雾化铁粉, 其氧含量低于 (0.015%)。
对于粉末冶金应用来说,这种无氧粉末允许使用便宜的合金元素(铬和锰等)代替镍和铜。
镍作为战略性资源,不但价格昂贵,并且还是一种致癌物, 应尽量避免使用。
这种粉末也很适合于用温压与热等静压工艺来生产高强度部件。
简述粉末冶金基本工艺
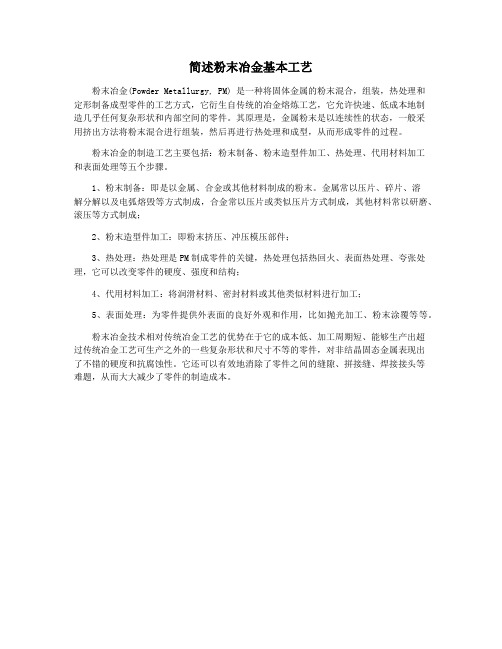
简述粉末冶金基本工艺
粉末冶金(Powder Metallurgy, PM) 是一种将固体金属的粉末混合,组装,热处理和
定形制备成型零件的工艺方式,它衍生自传统的冶金熔炼工艺,它允许快速、低成本地制
造几乎任何复杂形状和内部空间的零件。
其原理是,金属粉末是以连续性的状态,一般采
用挤出方法将粉末混合进行组装,然后再进行热处理和成型,从而形成零件的过程。
粉末冶金的制造工艺主要包括:粉末制备、粉末造型件加工、热处理、代用材料加工
和表面处理等五个步骤。
1、粉末制备:即是以金属、合金或其他材料制成的粉末。
金属常以压片、碎片、溶
解分解以及电弧熔毁等方式制成,合金常以压片或类似压片方式制成,其他材料常以研磨、滚压等方式制成;
2、粉末造型件加工:即粉末挤压、冲压模压部件;
3、热处理:热处理是PM制成零件的关键,热处理包括热回火、表面热处理、夸张处理,它可以改变零件的硬度、强度和结构;
4、代用材料加工:将润滑材料、密封材料或其他类似材料进行加工;
5、表面处理:为零件提供外表面的良好外观和作用,比如抛光加工、粉末涂覆等等。
粉末冶金技术相对传统冶金工艺的优势在于它的成本低、加工周期短、能够生产出超
过传统冶金工艺可生产之外的一些复杂形状和尺寸不等的零件,对非结晶固态金属表现出
了不错的硬度和抗腐蚀性。
它还可以有效地消除了零件之间的缝隙、拼接缝、焊接接头等
难题,从而大大减少了零件的制造成本。
粉末冶金原理课件 PPT
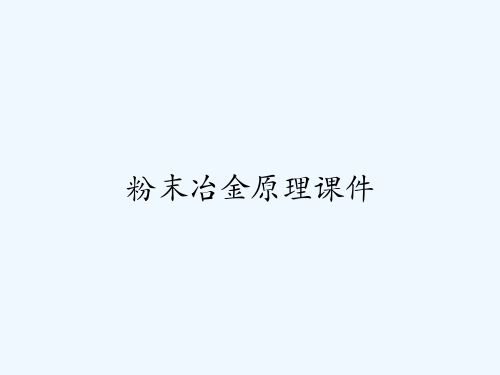
dy k dt y ydy kdt
y
r0
dy
积分 : y 2 2kt
由反应物分数X
4 3
r03
4 3
(r0
y )3
4 3
r03
1
(1
y )3
r0
y r0[1 - (1 - X )1/3]
则 [1 - (1 - X)1/3]
2kt r02
Kt
二、氧化铁还原基本原理
• 1、还原热力学
化气还原,金属热还原,气相还原,
一、金属氧化物还原基本原理
• 1、还原热力学
• 用还原金属氧化物可以获得金属粉末和合 金粉末
• 一种氧化物能否被还原首先要从热力学上 进行判断
• 判断依据:
•
MeO+X=Me+XO
• 根据加和反应可写成:
• 2Me+O2=2MeO
(1)
• 2X+O2=2XO
(2)
• 2现代粉末冶金 • 起源于难熔金属,难熔金属粉末压制、烧结、热锻工艺。1750-1850年,
铂; 1909年钨丝。 • 3含油轴承得发明、硬质合金得生产推动了粉末冶金在机械制造业得
发展 • 4科学技术得发展带动了粉末冶金材料和技术得得发展 • 5粉末冶金制造技术和设备得发展 • 6我国粉末冶金得发展
400
300 200 100
C2 B3
C1 B2
B1
0 0 20 40 60 80 100
还原百分率,%
• (1) Fe2O3还原得多层结构性: • 1)570以上: Fe2O3(芯部) Fe3O4 浮氏体(Fe3O4·FeO 固
溶体) Fe(外层)
• 2)570以下: Fe2O3(芯部) Fe3O4 Fe • (2)反应速度:
粉末的制取方法

六、雾化法
雾化法包括:1)二流雾化法,分气体雾化和水雾化 ;2)离心雾化法,分旋转圆盘雾化、旋转电极雾化 、旋转坩埚雾化等;3)其他雾化法,如转辊雾化、 真空雾化、油雾化等。 二流雾化法是用高速气流或高压水击碎金属液流的 ,离心雾化利用机械旋转的离心力将金属液流击碎 成细的液滴,然后冷却凝结成粉末。
三、气相沉积法
气相沉积法用在粉末冶金中的有以下几种: (1)金属蒸气冷凝,这种方法主要用于制取具有大蒸 气压的金属(如锌、镉等)粉末。这些金属的特点 是有较低的熔点和较高的挥发性,如果将这些金属 蒸气在冷却面上冷凝下来,便可形成很细的球状粉 末。 (2) 羰基物热离解。(3)气相还原,包括气相氢还原和 气相金属热还原。(4)化学气相沉积。
二、还原或还原化合法
金属热还原法主要应用于制取稀有金属(Ta、Nb、Ti 、Zr 、 Th 、U 、Cr等),特别适用于生产无碳金属,也可制取像 Cr-Ni这样的合金粉末。 金属热还原的反应可用一般化学式表示: 式中
根据所讨论的还原过程原理,只有形成化合物的等压位大大
降低的金属才有可能作为金属热还原剂
七、机械粉碎法
(3)球料比 在研磨中还要注意球与料的比例。料太少, 则球与球间碰撞加多,磨损太大;料过多,则磨削面积不够 ,不能很好磨细粉末,需要延长研磨时间,能量消耗增大。 同时,料与球装得过满,使磨筒上部空间太小,球的运动发 生阻碍后球磨效率反而降低。一般在球体的装填系数为 0.4~0.5时,装料量应该以填满球间的空隙稍掩盖住球体表面 为原则。也有建议装料量为磨筒容积的20%的。总之,球与 料不能装得过满。
七、机械粉碎法
金属粉末制备方法分类及其基本原理
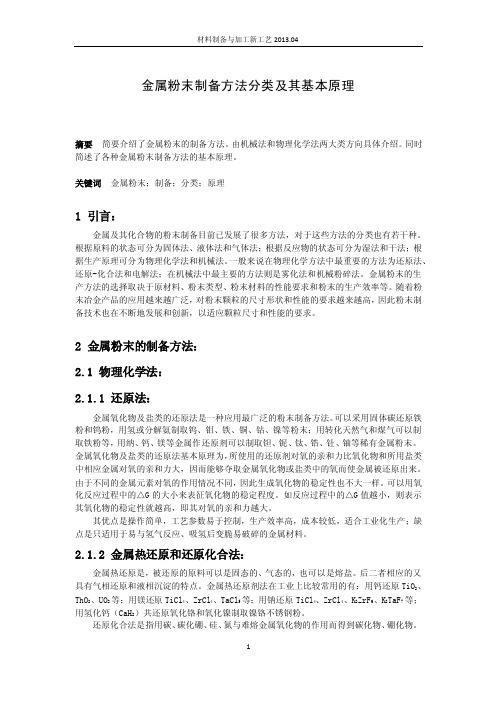
金属粉末制备方法分类及其基本原理摘要简要介绍了金属粉末的制备方法。
由机械法和物理化学法两大类方向具体介绍。
同时简述了各种金属粉末制备方法的基本原理。
关键词金属粉末;制备;分类;原理1 引言:金属及其化合物的粉末制备目前已发展了很多方法,对于这些方法的分类也有若干种。
根据原料的状态可分为固体法、液体法和气体法;根据反应物的状态可分为湿法和干法;根据生产原理可分为物理化学法和机械法。
一般来说在物理化学方法中最重要的方法为还原法、还原-化合法和电解法;在机械法中最主要的方法则是雾化法和机械粉碎法。
金属粉末的生产方法的选择取决于原材料、粉末类型、粉末材料的性能要求和粉末的生产效率等。
随着粉末冶金产品的应用越来越广泛,对粉末颗粒的尺寸形状和性能的要求越来越高,因此粉末制备技术也在不断地发展和创新,以适应颗粒尺寸和性能的要求。
2 金属粉末的制备方法:2.1 物理化学法:2.1.1 还原法:金属氧化物及盐类的还原法是一种应用最广泛的粉末制备方法。
可以采用固体碳还原铁粉和钨粉,用氢或分解氨制取钨、钼、铁、铜、钴、镍等粉末;用转化天然气和煤气可以制取铁粉等,用纳、钙、镁等金属作还原剂可以制取钽、铌、钛、锆、钍、铀等稀有金属粉末。
金属氧化物及盐类的还原法基本原理为,所使用的还原剂对氧的亲和力比氧化物和所用盐类中相应金属对氧的亲和力大,因而能够夺取金属氧化物或盐类中的氧而使金属被还原出来。
由于不同的金属元素对氧的作用情况不同,因此生成氧化物的稳定性也不大一样。
可以用氧化反应过程中的△G的大小来表征氧化物的稳定程度。
如反应过程中的△G值越小,则表示其氧化物的稳定性就越高,即其对氧的亲和力越大。
其优点是操作简单,工艺参数易于控制,生产效率高,成本较低,适合工业化生产;缺点是只适用于易与氢气反应、吸氢后变脆易破碎的金属材料。
2.1.2 金属热还原和还原化合法:金属热还原是,被还原的原料可以是固态的、气态的,也可以是熔盐。
后二者相应的又具有气相还原和液相沉淀的特点。
3d 打印金属粉末的制备方法

3d 打印金属粉末的制备方法1. 引言1.1 概述本文旨在探讨3D打印金属粉末的制备方法。
随着现代制造技术的不断发展,传统的金属加工方式已经无法完全满足人们对于复杂、精密和高强度金属产品的需求。
因此,3D打印技术应运而生,成为一种具有巨大潜力和广泛应用前景的先进加工方式。
1.2 文章结构本文主要分为五个部分:引言、金属粉末的制备方法、方法一: 粉末合金化法、方法二: 激光熔化法以及方法三: 电子束熔化法。
接下来将详细介绍这些内容。
1.3 目的本文旨在探究目前主流的3D打印金属粉末制备方法,并详细介绍每种方法的原理、实验步骤以及结果与讨论。
通过了解这些制备方法,读者可以深入了解3D 打印金属粉末领域的最新发展,并在实际应用中有所借鉴和启发。
同时,本文也希望促进该领域更深入的研究和创新,推动3D打印金属粉末技术的进一步发展。
2. 金属粉末的制备方法:2.1 传统方法介绍:传统的金属粉末制备方法主要包括物理方法和化学方法。
物理方法包括研磨、球磨和喷雾干燥等,这些方法主要通过机械力或热力作用使金属材料在固体状态下生成粉末。
化学方法则是利用化学反应使金属离子还原生成金属粉末,在这些方法中,溶液固化、沉淀分离和还原制备工艺被广泛采用。
2.2 3D打印金属粉末的意义:与传统的金属加工技术相比,3D打印技术具有更大的灵活性和自由度。
它可以根据设计要求直接将CAD模型转化为实际零部件,无需使用传统的减材成形过程。
因此,利用3D打印技术制备金属粉末具有更高的效率、更低的浪费和更好的成本控制能力。
2.3 目前主流的3D打印金属粉末制备方法:目前主流的3D打印金属粉末制备方法包括粉末合金化法、激光熔化法和电子束熔化法。
粉末合金化法是通过将两种或多种金属粉末混合,并在高温下进行合金反应,从而制备均匀的金属粉末。
该方法可以调整不同金属粉末的比例以获得不同性质的合金粉末,具有较高的生产效率和适用于多种材料的优点。
激光熔化法使用激光束对金属粉末进行扫描和熔化,通过控制激光参数和扫描路径,使得粉末颗粒彼此黏结并形成所需形状的零部件。
金属粉末的制备方法及基本原理
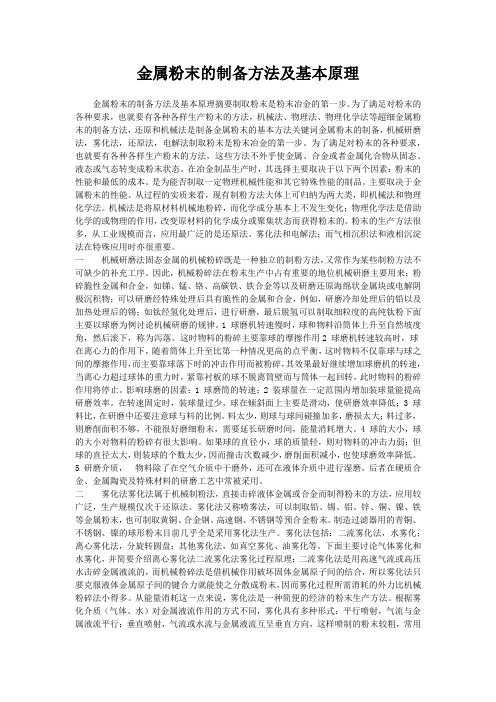
金属粉末的制备方法及基本原理金属粉末的制备方法及基本原理摘要制取粉末是粉末冶金的第一步。
为了满足对粉末的各种要求,也就要有各种各样生产粉末的方法,机械法、物理法、物理化学法等超细金属粉末的制备方法,还原和机械法是制备金属粉末的基本方法关键词金属粉末的制备,机械研磨法,雾化法,还原法,电解法制取粉末是粉末冶金的第一步。
为了满足对粉末的各种要求,也就要有各种各样生产粉末的方法,这些方法不外乎使金属、合金或者金属化合物从固态、液态或气态转变成粉末状态。
在冶金制品生产时,其选择主要取决于以下两个因素:粉末的性能和最低的成本。
是为能否制取一定物理机械性能和其它特殊性能的制品。
主要取决于金属粉末的性能。
从过程的实质来看,现有制粉方法大体上可归纳为两大类,即机械法和物理化学法。
机械法是将原材料机械地粉碎,而化学成分基本上不发生变化;物理化学法是借助化学的或物理的作用,改变原材料的化学成分或聚集状态而获得粉末的。
粉末的生产方法很多,从工业规模而言,应用最广泛的是还原法、雾化法和电解法;而气相沉积法和液相沉淀法在特殊应用时亦很重要。
一机械研磨法固态金属的机械粉碎既是一种独立的制粉方法,又常作为某些制粉方法不可缺少的补充工序。
因此,机械粉碎法在粉末生产中占有重要的地位机械研磨主要用来:粉碎脆性金属和合金,如锑、锰、铬、高碳铁、铁合金等以及研磨还原海绵状金属块或电解阴极沉积物;可以研磨经特殊处理后具有脆性的金属和合金,例如,研磨冷却处理后的铅以及加热处理后的锡;如钛经氢化处理后,进行研磨,最后脱氢可以制取细粒度的高纯钛粉下面主要以球磨为例讨论机械研磨的规律。
1 球磨机转速慢时,球和物料沿筒体上升至自然坡度角,然后滚下,称为泻落。
这时物料的粉碎主要靠球的摩擦作用2 球磨机转速较高时,球在离心力的作用下,随着筒体上升至比第一种情况更高的点平衡,这时物料不仅靠球与球之间的摩擦作用,而主要靠球落下时的冲击作用而被粉碎,其效果最好继续增加球磨机的转速,当离心力超过球体的重力时,紧靠衬板的球不脱离筒壁而与筒体一起回转,此时物料的粉碎作用将停止。
- 1、下载文档前请自行甄别文档内容的完整性,平台不提供额外的编辑、内容补充、找答案等附加服务。
- 2、"仅部分预览"的文档,不可在线预览部分如存在完整性等问题,可反馈申请退款(可完整预览的文档不适用该条件!)。
- 3、如文档侵犯您的权益,请联系客服反馈,我们会尽快为您处理(人工客服工作时间:9:00-18:30)。
金属粉末的制备方法及基本原理
1 引言金属粉末尺寸小 ,比表面积大 ,用其制得的金属零部件具有许多不同于常规材料的性质 , 如优良的力学性能、特殊的磁性能、高的电导率和扩散率、高的反应活性和催化活性等。
这些特殊性质使得金属粉末材料在航空航天、舰船、汽车、冶金、化工等领域得到越来越广泛的应用。
2 金属粉末的制备方法
2.1机械法机械法就是借助于机械力将大块金属破碎成所需粒
径粉末的一
种加工方法。
按照机械力的不同可将其分为机械冲击式粉碎法、气流磨粉碎法、球磨法和超声波粉碎法等。
目前普遍使用的方法还是球磨法和气流磨粉碎法 ,其优点是工艺简单、产量大,可以制备一些常规方法难以得到的高熔点金属和合金的纳米粉末。
2.1.1球磨法
球磨法主要分为滚动球法和振动球磨法。
该方法利用了金属颗粒在不同的应变速率下因产生变形而破碎细化的机理。
其优点是对物料的选择性不强 ,可连续操作 ,生产效率高 ,适用于干磨、湿磨,可以进行多种金属及合金的粉末制备。
缺点是在粉末制备过程中分级比较困难 [3] 。
2.1.2气流磨粉碎法
气流磨粉碎法是目前制备磁性材料粉末应用最广的方法。
具体的工艺过程为 : 压缩气体经过特殊设计的喷嘴后 , 被加速为超音速气流 , 喷射到研磨机的中心研磨区 , 从而带动研磨区内的物料互相碰撞 , 使粉末粉碎变细 ; 气流膨胀后随
物料上升进入分级区 , 由涡轮式分级器分选出达到粒度的物料 , 其余粗粉返回研磨区继续研磨 , 直至达到要求的粒度被分出为止。
整个生产过程可以连续自动运行 , 并通过分级轮转速的调节来控制粉末粒径大小(平均粒度在 3~ 8
μm)。
气流磨粉碎法适于大批量工业化生产 , 工艺成熟。
缺点是在金属粉末的生产过程中 , 必须使用连续不断的惰性气体或氮气作为压缩气源 , 耗气量较大; 只适合脆性金属及合金的破碎制粉。
2.2物理法
物理法一般是通过高温、高压将块状金属材料熔化 , 并破碎成细小的液滴, 并在收集器内冷凝而得到金属粉末 , 该过程不发生化学变化。
目前研究和使用最多的物理法主要有等离子旋转电极法和气体雾化法。
2.2.1 等离子旋转电极法等离子旋转电极法的原理是将金属或合金制成特定规格的棒料 , 然后装入旋转模腔 ,再将等离子枪移至棒料前 , 在等离子束的作用下 , 棒料端部开始熔化 , 形成的液体受到离心力和液体表面张力的双重作用,被破碎成液滴飞离电极棒 ,最终冷凝成球形金属粉末 [4] 。
该方法根据电极转速和等离子弧电流的大小调节控制粉末粒径。
优点是所得粉末球形度好 , 氧含量低 ; 缺点是粉末不易制取 , 每批次的材料利用率不高。
2.2.2气体雾化法气体雾化法是生产金属及合金粉末的主要方法之一。
气体雾化的基本原理是用高速气流将液态金属流破
碎成小液滴并凝固成粉末的过程。
雾化粉末具有球形度高、粉末粒度可控、氧含量低、生产成本低以及适应多种金属粉末的生产等优点 , 已成为高性能及特种合金粉末制备技术的主要发展方向。
喷嘴是气体雾化的关键技术 , 其结构和性能决定了雾化粉末的性能和生产效率。
因此 , 喷嘴结构设计与性能的不断提高决定着气体雾化技术的进步。
从雾化喷嘴结构设计的改进历程可以将雾化技术分为传统雾化技术和新型雾化技术。
2.2.2.1 传统雾化技术
传统雾化技术主要包括超声雾化技术、紧耦合雾化技术和高压气体雾化技术。
超声雾化技术最初由瑞典人发明 , 后由美国 M IT 的 Grant改造完善。
这项技术利用 2~2.5 M a 的超音速气流和 80~100 kHz的脉冲频率 , 气体介质压力为1.4 ~8.2 M Pa, 气流的最高速度 640 m/s, 粉末冷凝速度可达 104~105 K/s 。
用该方法制备的铝粉平均粒度可达到 22 μ m,且粉末呈表面光滑的球状。
该项技术的优点是效率较高, 缺点是只能在金属液流直径小于 5 mm 的情况下才具有较好的效果, 因此, 适用于铝等低熔点金属粉末的生产 , 而对高熔点金属还处于实验阶段。
据报道 , 美国坩埚材料公司( CrucibleMaterials)已引进该项技术进行工业化生产。
紧耦合雾化技术是一种对限制式喷嘴结构进行改造的雾化技术。
由于其气流出口至液流的距离达到最短 [7], 因而提高了气体动能的传输效率。
这种技术目前已被大多数雾化设备
采用。
雾化粉末的特点是微细粉末收得率高 , 粒径小(如铁合金粉末的平均粒度达 10~20 μm), 粒度分布窄 , 冷却速度高。
高的冷却速度有利于快速冷凝合金或非晶合金粉末的生产。
缺点是当雾化气压增加到一定值时 , 导液管出口处将产生正压 , 使雾化过程不能进行 ; 在高压雾化下 , 导液管出口处将产生真空(负压过低), 使金属液流率增加不利于细粉末的产生。
高压气体雾化技术是由美国爱荷华州立大学 Ames实验室的 Anderson 等人提出。
该技术对紧耦合喷嘴结构进行进一步改进 , 将紧耦合喷嘴的环缝出口改为20~ 24 个单一喷孔 , 通过提高气压和改变导液管出口处的形状设计 , 克服紧耦合喷嘴中存在的气流激波 , 使气流呈超声速层流状态 , 并在导液管出口处形成有效的负压[13] 。
这一改进有效提高了雾化效率。
高压气体雾化技术在生产微细粉方面很有成效 , 且能明显节约气体用量。
2.2.2.2新型雾化技术随着微细粉末在高新技术新材料中的应
用 , 需要大量粒径小于
20 μm 或 10 μ m 的金属及合金粉末 , 传统的雾化方法在生产这类粉末时仍然存在不足 : ①细粉末的产出率低(小于20% ); ②气体消耗量大,生产成本高。
为此 ,自20 世纪90 年代,人们对新型雾化技术进行大量的研究 , 并取得了可喜成果。
这些新型雾化技术大大提高了微细粉末的收得率 , 并且正在进入工业化规模应用。
新型雾化技术主要分为层流雾化技术、超声紧耦合雾化技术和热气体雾化技术 3 类。
层
流雾化技术是由德国 Nanoval公司等提出 [14] 。
该技术对常规喷嘴进行了重大改进。
改进后的雾化喷嘴雾化效率高 , 粉末粒度分布窄,冷却速度达106~107 K/s 。
在2.0 M Pa 的雾化压力下 ,以Ar或N2 为介质雾化铜、铝、 316L 不锈钢等 , 粉末平均粒度达到 10 μm。
该工艺的另一个优点是气体消耗量低 , 经济效益显著 , 并且适用于大多数金属粉末的生产。
缺点是技术控制难度大 ,雾化过程不稳定 , 产量小(金属质量流率小于 1 kg/min), 不利于工业化生产。
Nanoval 公司正致力于这些问题的解决。
超声紧耦合雾化技术是由英国 PSI公司提出。
该技术对紧耦合环缝式喷嘴进行结构优化 , 使气流的出口速度超过声速, 并且增加金属的质量流率。
在雾化高表面能的金属如不锈钢时 , 粉末平均粒度可达 20μm 左右, 粉末的标准偏差最低可以降至 1.5 μ m。
该技术的另一大优点是大大提高了粉末的冷却速度 , 可以生产快冷或非晶结的粉末 [7] 。
从当前的发展来看 , 该项技术设备代表了紧耦合雾化技术的新的发展方向 ,且具有工业实用意义 , 可以广泛应用于微细不锈钢、铁合金、镍合金、铜合金、磁性材料、储氢材料等合金粉末的生产。
近年来,英国的PSI公司和美国的 HJF 公司分别对热气体雾化的作用及机理进行了大量的研究。
HJF公司在1.72 M Pa 压力下, 将气体加热至 200~400 ℃雾化银合金和金合金 , 得出粉末的平均粒径和标准偏差均随温度升高而降低 [15] 。
与传统的
雾化技术相比 , 热气体雾化技术可以提高雾化效率 , 降低气体消耗量 , 易于在传统的雾化设备上实现该工艺 ,是一项具有应用前景的技术。
但是, 热气体雾化技术受到气体加热系统和喷嘴的限制 , 仅有少数几家研究机构进行研究。
2.3 物理- 化学法
物理-化学法是指在粉末制备过程中 , 同时借助化学反应和物理破碎 2 种方式而获得粉末的方法。
该方法中最具代表性的是以氢气为反应介质的氢化 -脱氢法( HDH) 。
氢化脱氢法利用原料金属易吸氢增脆的特性 , 在一定的温度下使金属与氢气发生氢化反应生成金属氢化物 , 然后借助机械方法将所得金属氢化物破碎成期望粒度的粉末 , 再将破碎后的金属氢化物粉末中的氢在真空条件下脱除 , 从而得到金属粉末。
氢化脱氢法已被成功用来制取 Ti粉、Zr粉、Hf粉、Ta 粉、 NdFeB 磁粉等金属和合金粉末 , 是一项成熟的工艺技术[19,20] 。
其优点是操作简单 , 工艺参数易于控制 , 生产效率高 , 成本较低 , 适合工业化生产 ; 缺点是只适用于易与氢气反应、吸氢后变脆易破碎的金属材料。