金属粉末制备方法分类及其基本原理
金属粉末分类

金属粉末分类
金属粉末的分类可以根据其制备方法、颗粒形状、尺寸、化学成分等不同而有所区分。
以下是一些常见的金属粉末分类方式:
1.根据制备方法分类:金属粉末可以分为气相法金属粉末和液相法金属粉末。
气相法金属粉末是通过物理或化学方法将金属或合金气体冷凝或蒸镀成固态金属颗粒。
液相法金属粉末是通过熔融金属或合金的方法制备而成。
2.根据颗粒形状分类:金属粉末可以分为球形粉末、片状粉末、纤维状粉末,
以及由金属气相化学反应合成的枝晶、纳米线材等。
3.根据尺寸分类:金属粉末可以分为微米级粉末、纳米级粉末和亚微米级粉
末。
4.根据化学成分分类:金属粉末可以分为铜基、铁基、铝基、镁基、镍基、
钴基、钛基、锆基等八大类。
此外,新型金属粉末材料分类包括高熵合金粉末、极细晶粒金属材料、气凝胶金属材料、生物可降解金属粉末材料等。
粉末冶金原理概述
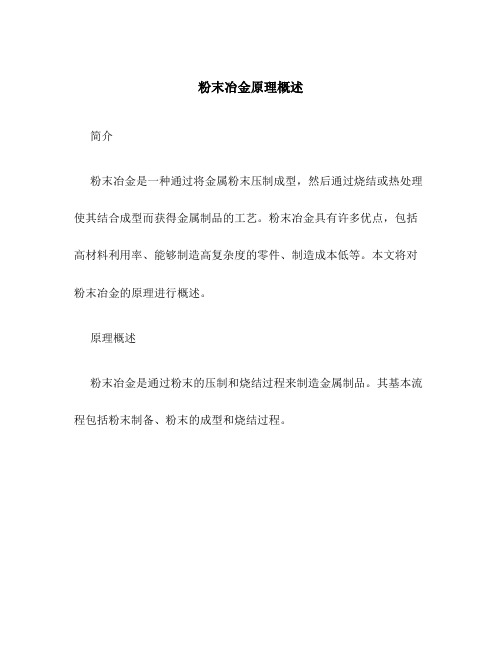
粉末冶金原理概述简介粉末冶金是一种通过将金属粉末压制成型,然后通过烧结或热处理使其结合成型而获得金属制品的工艺。
粉末冶金具有许多优点,包括高材料利用率、能够制造高复杂度的零件、制造成本低等。
本文将对粉末冶金的原理进行概述。
原理概述粉末冶金是通过粉末的压制和烧结过程来制造金属制品。
其基本流程包括粉末制备、粉末的成型和烧结过程。
粉末制备粉末制备是粉末冶金的第一步。
金属粉末可以通过多种方法来制备,包括机械研磨、凝固法、气相法等。
选择合适的粉末制备方法可以控制粉末的粒度、形状和组成,以适应所需的材料特性和制品要求。
粉末成型粉末成型是将金属粉末转化为所需形状的过程。
常见的成型方法包括压制、注塑、挤压等。
其中,压制是最常用的成型方法之一。
通过将金属粉末放入模具中,然后施加高压使其成型。
成型过程中,通过给予粉末适当的压力和温度,使粉末颗粒之间发生塑性变形和结合。
烧结过程烧结是粉末冶金的关键步骤之一。
在烧结过程中,经过成型后的粉末通过加热使其进行结合。
在加热的同时,粉末颗粒之间发生扩散,并形成跨粒界结合。
烧结温度和时间的选择对最终材料的性能和结构有重要影响。
后续热处理在烧结后,通常还需要对金属制品进行后续的热处理。
热处理可以有选择地改变材料的性能和结构,如提高强度、改善耐腐蚀性等。
常见的热处理方法包括固溶处理、时效处理、淬火等。
粉末冶金的优点粉末冶金具有以下优点:1.高材料利用率:由于粉末冶金可以直接利用金属粉末进行成型,因此避免了传统加工中的材料浪费,相比传统冶金方法,粉末冶金材料利用率更高。
2.制造高复杂度零件:粉末冶金可以制造复杂度高的零件,如多孔件、中空件等。
这是传统加工方法无法实现的。
3.制造成本低:粉末冶金不需要进行复杂的加工步骤,相比传统加工方法,制造成本更低。
4.可以利用废料:粉末冶金可以利用废料或回收材料进行制造,提高了资源的利用率。
应用领域粉末冶金广泛应用于各个领域,包括汽车制造、航空航天、船舶制造、化工、电子等。
金属粉末的生产

典型装置
➢以氦气作介质 ➢冷却速度: 10~104℃/s
短金属棒 Ф89mm L250mm
长金属棒 Ф63.5mm L1830mm
旋转电极法
➢ 自耗电极高速旋转(15000~25000r/min) ➢ 粉末纯度高 ➢ 等离子旋转电极雾化制粉法(PREP) ➢ 电子束旋转盘雾化制粉法(EBRD)
雾化法制粉
雾化机理
双流雾化法
用高速气流或高压水流击碎金属液流。
双流雾化形式
➢ 平行喷射 ➢ 垂直喷射 ➢ 互成角度喷射
① V型喷射 ② 锥型喷射 ③ 旋涡环行喷射
双流雾化形式
双流雾化喷嘴结构
气雾化生产铁粉工艺流程
焦炭
废钢
化铁炉 前床 漏包 喷嘴
聚粉器 泵
双锥 混料机
中间料 仓
干燥机
过滤机
➢ 水溶液电解:铜、镍、银、铁、锡 ➢ 熔盐电解 :难熔稀有金属 ➢ 有机电解质电解 ➢ 液体金属阴极电解
氢气还ቤተ መጻሕፍቲ ባይዱW粉
➢ 黄色α相WO3(易挥发) ➢ 蓝色β相WO2.90
➢紫色γ相WO2.72 ➢褐色δ相WO2
WO3 0.1H 2 WO2.90 0.1H 2O WO2.90 0.18H 2 WO2.72 0.18H 2O WO2.72 0.72H 2 WO2 0.72H 2O WO2 H 2 W 2H 2O
CO间接还原
当温度高于570℃时 3Fe2O3 CO 2Fe3O4 CO2 Fe3O4 CO 3FeO CO2 FeO CO Fe CO2 当温度低于570℃时
Fe3O4 4CO 3Fe 4CO2
H298 62.999kJ H298 22.395kJ H298 13.605kJ
粉末冶金的原理
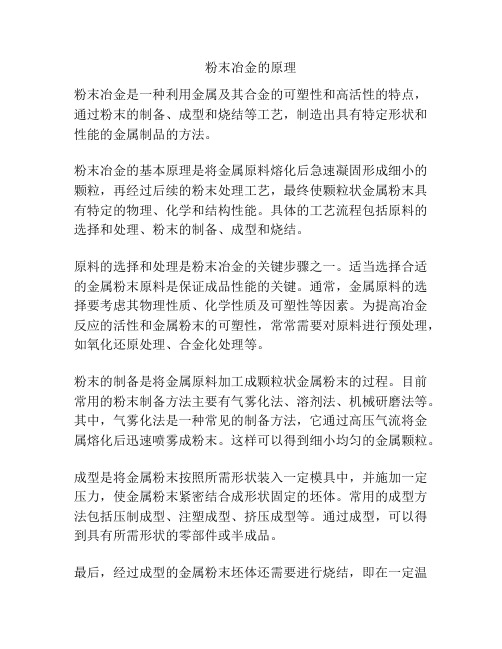
粉末冶金的原理粉末冶金是一种利用金属及其合金的可塑性和高活性的特点,通过粉末的制备、成型和烧结等工艺,制造出具有特定形状和性能的金属制品的方法。
粉末冶金的基本原理是将金属原料熔化后急速凝固形成细小的颗粒,再经过后续的粉末处理工艺,最终使颗粒状金属粉末具有特定的物理、化学和结构性能。
具体的工艺流程包括原料的选择和处理、粉末的制备、成型和烧结。
原料的选择和处理是粉末冶金的关键步骤之一。
适当选择合适的金属粉末原料是保证成品性能的关键。
通常,金属原料的选择要考虑其物理性质、化学性质及可塑性等因素。
为提高冶金反应的活性和金属粉末的可塑性,常常需要对原料进行预处理,如氧化还原处理、合金化处理等。
粉末的制备是将金属原料加工成颗粒状金属粉末的过程。
目前常用的粉末制备方法主要有气雾化法、溶剂法、机械研磨法等。
其中,气雾化法是一种常见的制备方法,它通过高压气流将金属熔化后迅速喷雾成粉末。
这样可以得到细小均匀的金属颗粒。
成型是将金属粉末按照所需形状装入一定模具中,并施加一定压力,使金属粉末紧密结合成形状固定的坯体。
常用的成型方法包括压制成型、注塑成型、挤压成型等。
通过成型,可以得到具有所需形状的零部件或半成品。
最后,经过成型的金属粉末坯体还需要进行烧结,即在一定温度下对金属粉末进行加热处理,使其颗粒之间发生结晶和扩散,相互融合并形成坚固的金属材料。
烧结可以通过自发热烧结、辅助烧结等方法来实现。
烧结过程中,金属粉末之间的氧化物和杂质也会在高温下被还原和挥发。
通过以上的处理工艺,粉末冶金可以制备出具有复杂形状、高强度、良好磨损性能和耐磨性能的金属制品。
由于粉末冶金具有成本低、能耗少、无需后加工等优势,因此在汽车、航空航天、工具等领域得到广泛应用。
冶金工程中的金属材料制备与处理

冶金工程中的金属材料制备与处理冶金工程是研究和应用金属材料的学科,涉及金属材料的制备、加工以及性能改善等方面。
金属材料是冶金工程中的核心,其制备与处理技术的发展对于现代工业的进步有着重要意义。
本文将从金属材料制备的基本原理,常见的制备方法,以及处理技术等方面进行论述。
一、金属材料制备的基本原理金属材料制备过程中的基本原理主要包括金属的途径形成和结晶行为。
金属的形成途径有两种,一种是地质过程,如矿石的形成;另一种是冶金过程,如金属的提取和冶炼。
金属在固态状态下具有晶体结构,通过加热和冷却等方式可以控制其晶体形貌和晶粒尺寸。
二、金属材料制备的常见方法1. 粉末冶金法:粉末冶金法是将金属或合金粉末压制成型,再进行烧结或热处理的一种制备方法。
其优点是可以得到具有高纯度和均匀组织的材料。
粉末冶金法广泛应用于金属粉末冶金制品、金属陶瓷制品和各种复合材料的制备。
2. 液相冶金法:液相冶金法是指将金属或合金在液态下进行熔化和制备的方法。
常见的液相冶金法有熔模铸造法、凝固锭法等。
这些方法可以制备大型和复杂形状的金属制品。
三、金属材料的处理技术金属材料制备完成后,还需要进行一系列的处理技术以改善其性能和使用价值。
常见的处理技术有热处理、表面处理和变形处理等。
1. 热处理:热处理是通过控制金属材料的加热和冷却过程,改变其组织结构和性能的一种方法。
常见的热处理方法包括退火、淬火、回火等。
热处理可以提高金属的硬度、强度和耐腐蚀性能。
2. 表面处理:表面处理是指对金属材料表面进行物理、化学或机械上的处理,以改变其表面特性的方法。
常见的表面处理方法有电镀、喷涂、陶瓷涂层等。
表面处理可以提高金属的耐磨性、耐腐蚀性和装饰性。
3. 变形处理:变形处理是通过塑性变形改变金属材料的组织结构和性能。
常见的变形处理方法有压力加工、轧制、拉伸等。
变形处理可以提高金属的强度、韧性和塑性。
综上所述,冶金工程中的金属材料制备与处理是冶金学的重要内容。
粉末冶金知识大全
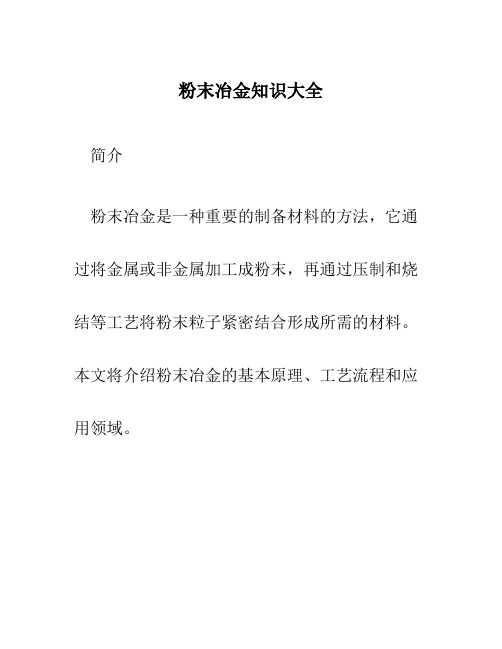
粉末冶金知识大全简介粉末冶金是一种重要的制备材料的方法,它通过将金属或非金属加工成粉末,再通过压制和烧结等工艺将粉末粒子紧密结合形成所需的材料。
本文将介绍粉末冶金的基本原理、工艺流程和应用领域。
1. 粉末制备粉末冶金的第一步是制备粉末。
常见的粉末制备方法包括:•原子熔化法:通过将金属或合金加热到高温,使其熔化后迅速冷却,冷却过程中形成的微细颗粒即为粉末。
•机械研磨法:将金属块或合金块放入球磨机中与球磨介质一起磨碎,经过一定时间后得到所需的粉末。
•物理气相法:通过高温蒸发和凝聚,使金属或合金从气相转变为粉末。
常见的物理气相制备方法有气体凝聚法、物理溅射法等。
2. 粉末冶金工艺粉末冶金包括压制、烧结和后处理等多个工艺步骤。
2.1 压制压制是将制备好的粉末以一定的压力塑造成所需形状的过程。
常见的压制方法有:•静态压制:即将粉末放置在模具中,施加垂直于模具方向的压力,使粉末颗粒之间发生塑性变形,形成一定形状的绿体。
•动态压制:即通过提供一个快速冲击力,使粉末颗粒互相碰撞并发生变形,形成一定形状的绿体。
2.2 烧结烧结是将压制好的绿体在一定温度下进行加热,使粉末颗粒之间发生扩散和结合,形成致密的材料。
常见的烧结方法有:•常压烧结:将绿体放在电炉或气炉中进行加热,使粉末颗粒熔结或固相扩散结合。
•热等静压烧结:在加热的同时施加一定的压力,用于加强绿体的结合。
2.3 后处理烧结完成后,还需要进行一些后处理步骤以提高材料的性能。
常见的后处理方法有:•热处理:通过控制温度和时间,在一定的条件下改变材料的组织结构,提高其硬度、强度等性能。
•表面处理:在材料表面形成覆盖层、涂层或改变表面形貌,以提高耐磨、耐腐蚀等性能。
3. 应用领域粉末冶金在许多领域都有着广泛的应用。
3.1 金属制品粉末冶金可以制备各种金属制品,如汽车零部件、工具等。
由于独特的结构和物理性能,粉末冶金制品具有优异的耐磨、抗拉伸和耐腐蚀等特点。
3.2 陶瓷制品通过粉末冶金技术可以制备出高纯度、高强度的陶瓷制品,如陶瓷刀具、陶瓷齿轮等。
粉末冶金手册

粉末冶金手册粉末冶金是一种将金属或非金属粉末通过压制、烧结等工艺加工成成型品的制造工艺。
粉末冶金具有高效、低成本、可成型性好、材料利用率高等优势,因此在航空航天、汽车工业、电子行业等领域得到广泛应用。
本手册将介绍粉末冶金的基本原理、工艺流程、材料选择、设备介绍等内容。
一、粉末冶金的基本原理粉末冶金的基本原理是将金属或非金属物质经过粉碎或原料特殊制备得到的粉末,经过压制成型或注射成型,再经过高温烧结得到所需产品。
这种工艺利用了粉末颗粒之间的相互扭曲和扩散,从而实现了物质的成型。
同时,由于粉末冶金是一种非液态冶金工艺,不需要溶解和凝固过程,避免了材料在液态下的气体、夹杂物等问题,因此可以获得更高的材料纯度和均匀性。
二、粉末冶金的工艺流程粉末冶金的一般工艺流程分为原料制备、混合、成型、烧结和后处理等步骤。
1.原料制备:原料制备阶段主要包括选料和粉末制备。
选料是指根据成品的要求选择合适的原料,如金属、合金、陶瓷或复合材料等。
粉末制备可以通过粉碎、化学方法、电化学方法等得到所需粉末。
2.混合:将所选的原料粉末按照一定比例进行混合。
混合的目的是使各种材料的粒子均匀分散,以获得更高的均匀性。
3.成型:将混合好的粉末通过压制成型,可以使用冷压、热压或注射成型等方法。
成型一般可以分为干压成型和液相成型两种方式。
4.烧结:成型件通过高温烧结,使粉末颗粒之间发生结合,形成致密的材料。
烧结温度和时间根据材料种类、成型件形状等因素确定。
5.后处理:烧结后的材料可以进行表面处理、热处理、加工等工艺。
目的是使产品达到所需的性能和尺寸要求。
三、粉末冶金的材料选择粉末冶金可以应用于各种金属和非金属材料的制备,包括纯金属、合金、陶瓷、塑料等。
在选择材料时需要考虑材料的物理性质、化学性质、应用环境等因素。
例如,对于需要高强度和耐磨性的零件可以选择使用金属粉末冶金制备的合金材料;对于需要绝缘性能和耐高温的零件可以选择使用陶瓷粉末冶金制备的材料。
粉末冶金原理知识要点
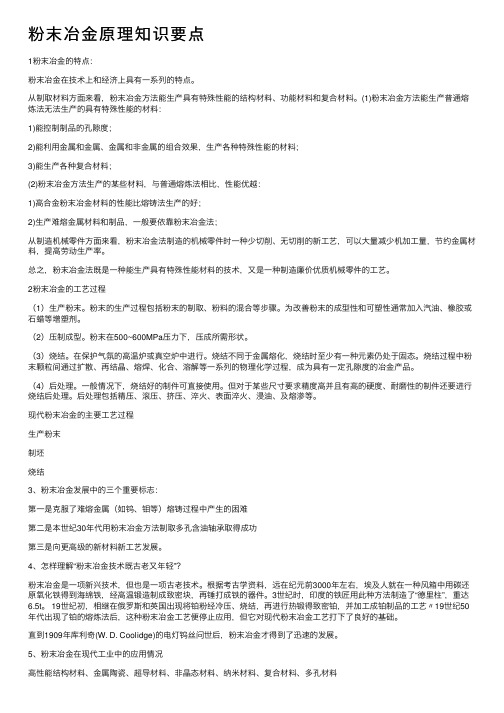
粉末冶⾦原理知识要点1粉末冶⾦的特点:粉末冶⾦在技术上和经济上具有⼀系列的特点。
从制取材料⽅⾯来看,粉末冶⾦⽅法能⽣产具有特殊性能的结构材料、功能材料和复合材料。
(1)粉末冶⾦⽅法能⽣产普通熔炼法⽆法⽣产的具有特殊性能的材料:1)能控制制品的孔隙度;2)能利⽤⾦属和⾦属、⾦属和⾮⾦属的组合效果,⽣产各种特殊性能的材料;3)能⽣产各种复合材料;(2)粉末冶⾦⽅法⽣产的某些材料,与普通熔炼法相⽐,性能优越:1)⾼合⾦粉末冶⾦材料的性能⽐熔铸法⽣产的好;2)⽣产难熔⾦属材料和制品,⼀般要依靠粉末冶⾦法;从制造机械零件⽅⾯来看,粉末冶⾦法制造的机械零件时⼀种少切削、⽆切削的新⼯艺,可以⼤量减少机加⼯量,节约⾦属材料,提⾼劳动⽣产率。
总之,粉末冶⾦法既是⼀种能⽣产具有特殊性能材料的技术,⼜是⼀种制造廉价优质机械零件的⼯艺。
2粉末冶⾦的⼯艺过程(1)⽣产粉末。
粉末的⽣产过程包括粉末的制取、粉料的混合等步骤。
为改善粉末的成型性和可塑性通常加⼊汽油、橡胶或⽯蜡等增塑剂。
(2)压制成型。
粉末在500~600MPa压⼒下,压成所需形状。
(3)烧结。
在保护⽓氛的⾼温炉或真空炉中进⾏。
烧结不同于⾦属熔化,烧结时⾄少有⼀种元素仍处于固态。
烧结过程中粉末颗粒间通过扩散、再结晶、熔焊、化合、溶解等⼀系列的物理化学过程,成为具有⼀定孔隙度的冶⾦产品。
(4)后处理。
⼀般情况下,烧结好的制件可直接使⽤。
但对于某些尺⼨要求精度⾼并且有⾼的硬度、耐磨性的制件还要进⾏烧结后处理。
后处理包括精压、滚压、挤压、淬⽕、表⾯淬⽕、浸油、及熔渗等。
现代粉末冶⾦的主要⼯艺过程⽣产粉末制坯烧结3、粉末冶⾦发展中的三个重要标志:第⼀是克服了难熔⾦属(如钨、钼等)熔铸过程中产⽣的困难第⼆是本世纪30年代⽤粉末冶⾦⽅法制取多孔含油轴承取得成功第三是向更⾼级的新材料新⼯艺发展。
4、怎样理解“粉末冶⾦技术既古⽼⼜年轻”?粉末冶⾦是⼀项新兴技术,但也是⼀项古⽼技术。
第二章粉末制备

粉末粒度/μm 颗粒形状 聚集状况 表观密度% 冷却速度/K· s -1 偏析程度 氧化物/10
-6
气雾化
100 球形 有一些 55 10
4
水雾化
150 不规则 很少 35 10
5
轻微 120
可忽略 3000
流体压力/MPa
流体速度/m· s 雾化效率
-1
3
100 低
14
100 中等
2)影响二流雾化性能的因素
从制备过程的实质来分:机械破碎法、物 理化学法
固态
粉末
1、金属(合金)→金属粉末:机械粉碎,电化腐蚀 2、金属氧化物(盐类)→金属粉末:还原法 3、金属+非金属化合物 →金属化合物粉末:还原-化合法
金属氧化物+非金属化合物
3 常用的粉末制备方法 3、1 机械粉碎法
碾碎 碾碎机 双辊滚碎机
机 械 粉 碎 法
雾化粉末性能的表征 a.粉末的粒度:平均粒度、粒度分布、可用粉 末收得率 b.粉末形状:松装密度、流动性、压坯密度、 比表面积 c.粉末纯度和结构:化学成分、氧化度、均匀 性、颗粒微观组织结构
A.雾化介质
空气 气体 雾化介质 影响 液体 水 惰性 气体 油
对氧化不严重或再进行还原处理的合 金。(铜、铁、碳钢) 对易氧化的金属粉末制备,含锰、硅、 钒、钛、锆的合金或镍基、钴超合金 能较好地控制颗粒形状和表面氧化 对含有易被还原的氧化物金属合金, 铁、低碳钢、合金钢(由于金属冷却 速度快粉末表面烟花大大减少)
3.2.2离心雾化
离心雾化法—利用机械旋转离心力将金属液流 击碎成细液滴,然后冷却凝结成 粉末 离心雾化法分类:旋转圆盘、旋转坩埚、旋转 电极、旋转网
1)旋转圆盘法
金属粉末的制备方法及基本原理.

金属粉末的制备方法及基本原理1引言金属粉末尺寸小,比表面积大,用其制得的金属零部件具有许多不同于常规材料的性质,如优良的力学性能、特殊的磁性能、高的电导率和扩散率、高的反应活性和催化活性等。
这些特殊性质使得金属粉末材料在航空航天、舰船、汽车、冶金、化工等领域得到越来越广泛的应用。
2金属粉末的制备方法2.1机械法机械法就是借助于机械力将大块金属破碎成所需粒径粉末的一种加工方法。
按照机械力的不同可将其分为机械冲击式粉碎法、气流磨粉碎法、球磨法和超声波粉碎法等。
目前普遍使用的方法还是球磨法和气流磨粉碎法,其优点是工艺简单、产量大,可以制备一些常规方法难以得到的高熔点金属和合金的纳米粉末。
2.1.1球磨法球磨法主要分为滚动球法和振动球磨法。
该方法利用了金属颗粒在不同的应变速率下因产生变形而破碎细化的机理。
其优点是对物料的选择性不强,可连续操作, 生产效率高,适用于干磨、湿磨,可以进行多种金属及合金的粉末制备。
缺点是在粉末制备过程中分级比较困难[3]。
2.1.2气流磨粉碎法气流磨粉碎法是目前制备磁性材料粉末应用最广的方法。
具体的工艺过程为:压缩气体经过特殊设计的喷嘴后,被加速为超音速气流,喷射到研磨机的中心研磨区从而带动研磨区内的物料互相碰撞,使粉末粉碎变细;气流膨胀后随物料上升进入分级区,由涡轮式分级器分选出达到粒度的物料,其余粗粉返回研磨区继续研磨,直至达到要求的粒度被分出为止。
整个生产过程可以连续自动运行,并通过分级轮转速的调节来控制粉末粒径大小(平均粒度在3~8 ym气流磨粉碎法适于大批量工业化生产,工艺成熟。
缺点是在金属粉末的生产过程中,必须使用连续不断的惰性气体或氮气作为压缩气源,耗气量较大;只适合脆性金属及合金的破碎制粉。
2.2物理法物理法一般是通过高温、高压将块状金属材料熔化,并破碎成细小的液滴,并在收集器内冷凝而得到金属粉末,该过程不发生化学变化。
目前研究和使用最多的物理法主要有等离子旋转电极法和气体雾化法。
粉末冶金原理

粉末冶金原理粉末冶金是一种利用金属粉末或者金属粉末与非金属粉末混合后,再经过压制和烧结等工艺制造金属零件的方法。
在粉末冶金工艺中,粉末的特性和原理起着至关重要的作用。
粉末冶金原理主要包括粉末的制备、成型、烧结和后处理等几个方面。
首先,粉末的制备是粉末冶金的第一步。
金属粉末的制备可以通过机械研磨、化学方法和物理方法等多种途径。
机械研磨是指将金属块或者金属棒经过研磨机械的加工,得到所需的金属粉末。
化学方法则是通过化学反应得到金属粉末,而物理方法则是通过物理手段如电解、喷雾等得到金属粉末。
在粉末冶金中,粉末的制备质量直接影响着最终制品的质量和性能。
其次,成型是指将金属粉末进行成型工艺,使其成为所需形状的工件。
成型方法包括压制成型、注射成型、挤压成型等多种方式。
压制成型是将金属粉末放入模具中,再经过压制机械的加工,使其成为所需形状的工件。
注射成型则是将金属粉末与粘结剂混合后,通过注射成型机械将其注射成型。
挤压成型是将金属粉末放入容器中,再通过挤压机械的作用,使其成为所需形状的工件。
成型工艺的精密度和成型质量对于最终产品的质量和性能至关重要。
接下来,烧结是粉末冶金中的关键工艺。
烧结是指将成型后的金属粉末在高温下进行加热处理,使其颗粒间发生结合,形成致密的金属材料。
烧结工艺的温度、压力和时间等参数对于最终产品的致密度、硬度和耐磨性等性能有着重要影响。
最后,后处理是指对烧结后的金属制品进行表面处理、热处理和精加工等工艺。
表面处理可以提高金属制品的耐腐蚀性和美观度,热处理可以改善金属制品的硬度和强度,精加工则可以提高金属制品的精度和表面质量。
总之,粉末冶金原理是一个复杂而又精密的工艺体系,涉及到材料科学、机械工程、化学工程等多个领域的知识。
通过对粉末的制备、成型、烧结和后处理等环节的深入研究和探索,可以不断提高粉末冶金工艺的精度和效率,为制造业的发展和进步提供更加可靠的技术支持。
粉末冶金工艺的基本工序
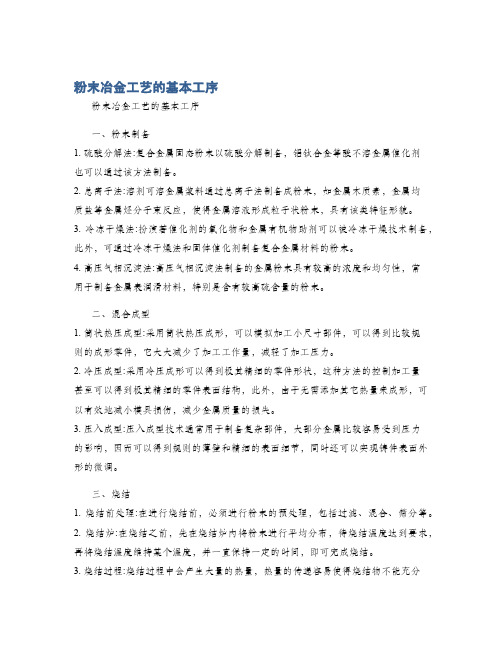
粉末冶金工艺的基本工序粉末冶金工艺的基本工序一、粉末制备1. 硫酸分解法:复合金属固态粉末以硫酸分解制备,铝钛合金等酸不溶金属催化剂也可以通过该方法制备。
2. 总离子法:溶剂可溶金属浆料通过总离子法制备成粉末,如金属木质素,金属均质盐等金属烃分子束反应,使得金属溶液形成粒子状粉末,具有该类特征形貌。
3. 冷冻干燥法:扮演著催化剂的氧化物和金属有机物助剂可以被冷冻干燥技术制备,此外,可通过冷冻干燥法和固体催化剂制备复合金属材料的粉末。
4. 高压气相沉淀法:高压气相沉淀法制备的金属粉末具有较高的浓度和均匀性,常用于制备金属表润滑材料,特别是含有较高硫含量的粉末。
二、混合成型1. 筒状热压成型:采用筒状热压成形,可以模拟加工小尺寸部件,可以得到比较规则的成形零件,它大大减少了加工工作量,减轻了加工压力。
2. 冷压成型:采用冷压成形可以得到极其精细的零件形状,这种方法的控制加工量甚至可以得到极其精细的零件表面结构,此外,由于无需添加其它热量来成形,可以有效地减小模具损伤,减少金属质量的损失。
3. 压入成型:压入成型技术通常用于制备复杂部件,大部分金属比较容易受到压力的影响,因而可以得到规则的薄壁和精细的表面细节,同时还可以实现铸件表面外形的微调。
三、烧结1. 烧结前处理:在进行烧结前,必须进行粉末的预处理,包括过滤、混合、筛分等。
2. 烧结炉:在烧结之前,先在烧结炉内将粉末进行平均分布,待烧结温度达到要求,再将烧结温度维持某个温度,并一直保持一定的时间,即可完成烧结。
3. 烧结过程:烧结过程中会产生大量的热量,热量的传递容易使得烧结物不能充分的受热,而出现部分未烧结的现象。
4. 烧结温度控制:因此,在烧结过程中对温度有较为严格的控制要求,烧结室内和外温度的精确控制可以有效地提高烧结率,保证烧结质量。
四、制备复合材料1. 试剂混合法:一般采用试剂混合法,使用试剂使粉末熔化成金属液,将两种粉末液分别滴入容器内,然后混合,固化,再烧结,形成复合材料,其优点是可以快速产生复合材料,但受试剂的影响,使得成型容易受到外界环境的影响。
粉末冶金粉体常见的制备方法及综述1
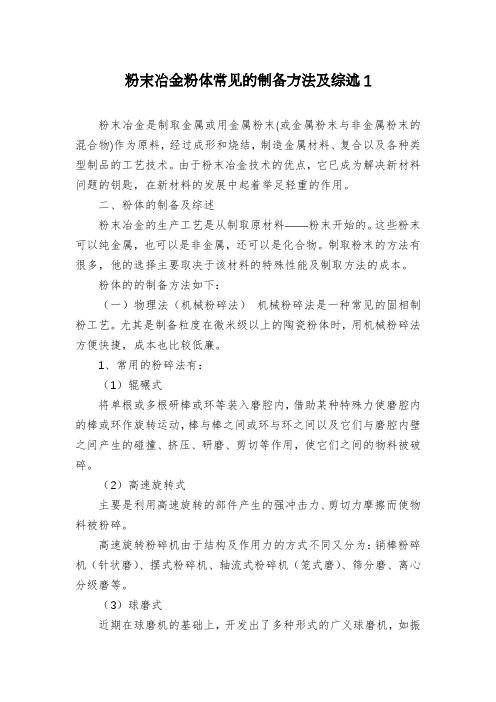
粉末冶金粉体常见的制备方法及综述1粉末冶金是制取金属或用金属粉末(或金属粉末与非金属粉末的混合物)作为原料,经过成形和烧结,制造金属材料、复合以及各种类型制品的工艺技术。
由于粉末冶金技术的优点,它已成为解决新材料问题的钥匙,在新材料的发展中起着举足轻重的作用。
二、粉体的制备及综述粉末冶金的生产工艺是从制取原材料――粉末开始的。
这些粉末可以纯金属,也可以是非金属,还可以是化合物。
制取粉末的方法有很多,他的选择主要取决于该材料的特殊性能及制取方法的成本。
粉体的的制备方法如下:(一)物理法(机械粉碎法)机械粉碎法是一种常见的固相制粉工艺。
尤其是制备粒度在微米级以上的陶瓷粉体时,用机械粉碎法方便快捷,成本也比较低廉。
1、常用的粉碎法有:(1)辊碾式将单根或多根研棒或环等装入磨腔内,借助某种特殊力使磨腔内的棒或环作旋转运动,棒与棒之间或环与环之间以及它们与磨腔内壁之间产生的碰撞、挤压、研磨、剪切等作用,使它们之间的物料被破碎。
(2)高速旋转式主要是利用高速旋转的部件产生的强冲击力、剪切力摩擦而使物料被粉碎。
高速旋转粉碎机由于结构及作用力的方式不同又分为:销棒粉碎机(针状磨)、摆式粉碎机、轴流式粉碎机(笼式磨)、筛分磨、离心分级磨等。
(3)球磨式近期在球磨机的基础上,开发出了多种形式的广义球磨机,如振动球磨、离心球磨、行星磨、离心滚动磨等。
(4)介质搅拌式是依靠磨腔中机械搅拌棒、齿或片带动研磨介质运动,利用研磨介质之间的挤压力和剪切力使物料粉碎。
它实际上是一种内部有动件的球磨机,靠内部动件带动磨介运动来对物料进行粉碎。
搅拌磨早期主要用于染料、油漆、涂料行业浆料分散与混合。
后来经多次改进,逐步发展成为一种新型的高效超细粉碎机。
有时称之为介质磨,也有人称之为“剥片机”。
(5)气流式粉碎机是在高速气流作用下,物料通过本身颗粒之间的撞击,气流对物料的剪切作用以及物料与其它部件的冲击、摩擦、剪切而使物料粉碎。
先后有:扁平式(圆盘式)气流磨、循环式气流磨、对撞式气流磨、流化床气流磨、靶式气流磨、超音速气流磨等。
粉体制备原理与技术

粉体制备原理与技术粉体制备是指将原始材料通过机械、化学和物理方法处理,制成粉末状物质的技术。
粉体制备广泛应用于电子材料、陶瓷材料、金属材料、化工原料、医药、食品等领域。
粉体制备的原理和技术主要包括物理方法、机械方法、化学方法三种。
一、物理方法物理方法主要是利用气态、液态、固态外力(如磨削、撞击等)对物料进行处理,从而达到制备粉末的目的。
物理方法包括:1、凝结法凝结法是将高温金属蒸气通过冷凝器冷却,然后在表面沉积下来,形成一定的粉末形态。
凝结法适用于制备高纯度和特殊结构的金属和非金属材料。
2、气溶胶法气溶胶法是将气态的化学物质喷入高温气氛中,形成微米或亚微米细小颗粒,再利用自由下落或超离心等手段进行收集。
气溶胶法适用于制备特殊形态的粉末,如其形态为球状时,制备涂层材料的效果更佳。
3、溶胶-凝胶法溶胶-凝胶法是在液体介质中形成溶胶,利用物理或化学方法处理形成凝胶,再煅烧得到所需的粉末。
溶胶-凝胶法的特点是制备出的产品纯度高、颗粒尺寸均匀,但生产工艺复杂,成本较高。
二、机械方法机械方法主要是利用机械非均相作用力对原材料进行研磨、切割等处理,破碎成为粉末的方法。
机械方法包括:1、球磨法球磨法是一种通过机械碾磨将原料粉碎成微米甚至纳米级的粉末的方法。
通过球磨法制备出的粉末颗粒尺寸分布范围比较小,形态规则,可形成均匀的合金体系。
2、细化法细化法是通过高频振动、喷射流等力学作用和化学反应过程,使材料粉末实现亚微米级、甚至纳米级的颗粒级细化加工。
三、化学方法化学方法即通过化学反应形成晶体或沉淀,再将其煅烧后得到所需的粉末。
化学方法包括:1、软化化学反应法软化化学反应法是通过添加某些试剂,将反应组分分子分解成无机气相分子,而后这些分子再反应成所需的无机晶体,最后制成粉末。
软化化学反应法适用于制备难度较大的无机晶体粉末。
2、锔合成法锔合成法是先将所需的无机或有机化合物溶解在一定的有机溶剂或水溶剂中,制成溶液,然后将其快速蒸发和烘烤,得到所需的粉末。
粉末冶金原理

粉末冶金原理
粉末冶金是一种通过粉末冶金工艺制备金属、合金、陶瓷和复合材料的方法。
它是一种高效的材料制备技术,具有原料利用率高、产品尺寸精度高、材料组织均匀等优点,因此在航空航天、汽车、电子、机械等领域得到广泛应用。
粉末冶金的基本原理是将金属粉末或合金粉末按一定的成型方法制备成所需形
状的坯料,然后通过烧结或热压等方法将其致密化,最终得到所需的产品。
这种方法可以制备复杂形状的产品,且可以调控产品的性能,因此在一些特殊领域有着独特的优势。
粉末冶金的工艺包括粉末制备、成型和烧结等步骤。
首先是粉末的制备,通常
采用机械球磨、化学法、电化学法等方法制备金属或合金粉末。
然后是成型,通过压制、注射成型等手段将粉末压制成所需形状的坯料。
最后是烧结,将压制好的坯料在一定的温度下进行热处理,使粉末颗粒之间发生扩散与结合,最终形成致密的产品。
粉末冶金的优点之一是可以制备高性能的材料。
由于粉末冶金可以制备复杂形
状的产品,因此可以设计出更加符合工程需求的材料,提高材料的使用性能。
另外,由于粉末冶金可以控制材料的成分和微观结构,因此可以调控材料的力学性能、导热性能、磁性能等,满足不同领域的需求。
除此之外,粉末冶金还可以实现材料的资源化利用。
由于粉末冶金可以利用废料、废料料等再生资源进行材料制备,因此可以减少对原材料的依赖,实现资源的再利用,降低生产成本,减少对环境的影响。
总的来说,粉末冶金是一种高效的材料制备技术,具有制备高性能材料、实现
资源化利用等优点,因此在现代工业中得到了广泛的应用。
随着科技的发展,相信粉末冶金技术会不断完善,为人类社会的发展做出更大的贡献。
粉末的制取方法

六、雾化法
雾化法包括:1)二流雾化法,分气体雾化和水雾化 ;2)离心雾化法,分旋转圆盘雾化、旋转电极雾化 、旋转坩埚雾化等;3)其他雾化法,如转辊雾化、 真空雾化、油雾化等。 二流雾化法是用高速气流或高压水击碎金属液流的 ,离心雾化利用机械旋转的离心力将金属液流击碎 成细的液滴,然后冷却凝结成粉末。
三、气相沉积法
气相沉积法用在粉末冶金中的有以下几种: (1)金属蒸气冷凝,这种方法主要用于制取具有大蒸 气压的金属(如锌、镉等)粉末。这些金属的特点 是有较低的熔点和较高的挥发性,如果将这些金属 蒸气在冷却面上冷凝下来,便可形成很细的球状粉 末。 (2) 羰基物热离解。(3)气相还原,包括气相氢还原和 气相金属热还原。(4)化学气相沉积。
二、还原或还原化合法
金属热还原法主要应用于制取稀有金属(Ta、Nb、Ti 、Zr 、 Th 、U 、Cr等),特别适用于生产无碳金属,也可制取像 Cr-Ni这样的合金粉末。 金属热还原的反应可用一般化学式表示: 式中
根据所讨论的还原过程原理,只有形成化合物的等压位大大
降低的金属才有可能作为金属热还原剂
七、机械粉碎法
(3)球料比 在研磨中还要注意球与料的比例。料太少, 则球与球间碰撞加多,磨损太大;料过多,则磨削面积不够 ,不能很好磨细粉末,需要延长研磨时间,能量消耗增大。 同时,料与球装得过满,使磨筒上部空间太小,球的运动发 生阻碍后球磨效率反而降低。一般在球体的装填系数为 0.4~0.5时,装料量应该以填满球间的空隙稍掩盖住球体表面 为原则。也有建议装料量为磨筒容积的20%的。总之,球与 料不能装得过满。
七、机械粉碎法
金属粉末工艺流程

金属粉末工艺流程一、金属粉末的制备金属粉末工艺流程的第一步是金属粉末的制备。
常见的金属粉末制备方法包括机械研磨法、电解法、气雾化法等。
机械研磨法是将金属块通过机械研磨设备研磨成粉末状;电解法是通过电解过程将金属溶解并在电极上析出成粉末;气雾化法是将金属熔融后,通过高速气流将金属喷射成细小颗粒。
二、金属粉末的分类和筛分经过制备的金属粉末需要进行分类和筛分。
金属粉末的分类是根据其化学成分和粒径等特性进行的,常见的分类有铁粉、铜粉、铝粉等。
筛分是为了去除不符合要求的颗粒和杂质,通常使用筛网进行筛分。
三、金属粉末的成型金属粉末经过分类和筛分后,需要进行成型。
金属粉末成型有多种方法,常见的有压制成型、注射成型和挤压成型等。
压制成型是将金属粉末放入模具中,通过压力使其成型;注射成型是将金属粉末与粘结剂混合后注射到模具中,然后通过加热固化;挤压成型是将金属粉末放入挤压机中,通过挤压使其成型。
四、金属粉末的烧结金属粉末成型后,需要进行烧结。
烧结是将金属粉末在高温下加热,使其颗粒间发生结合,形成致密的金属坯体。
烧结温度和时间根据金属粉末的特性和成型要求而定。
烧结过程中,金属粉末颗粒表面会发生熔化和扩散,从而实现颗粒间的结合。
五、金属粉末的后处理金属粉末烧结后,还需要进行后处理。
后处理包括去除烧结产物表面的氧化物和杂质,以及进行表面处理和喷涂等。
去除氧化物和杂质可以通过化学处理、机械处理等方法实现。
表面处理可以增加金属粉末的抗腐蚀性能和附着力,常见的表面处理方法有镀层、喷涂等。
六、金属粉末的加工和应用经过后处理的金属粉末可以进行加工和应用。
金属粉末加工包括冷挤压、热挤压、冲压、焊接等。
冷挤压和热挤压是将金属粉末通过挤压机进行成型;冲压是将金属粉末放入模具中,通过冲击力使其成型;焊接是将金属粉末与其他金属材料进行连接。
应用方面,金属粉末广泛应用于制造业的各个领域,如汽车制造、航空航天、电子设备等。
金属粉末工艺流程包括金属粉末的制备、分类和筛分、成型、烧结、后处理以及加工和应用等环节。
金属粉末制备方法分类及其基本原理
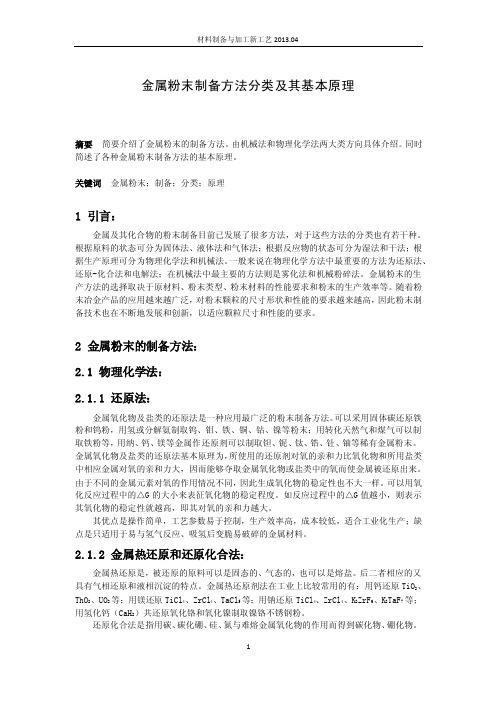
金属粉末制备方法分类及其基本原理摘要简要介绍了金属粉末的制备方法。
由机械法和物理化学法两大类方向具体介绍。
同时简述了各种金属粉末制备方法的基本原理。
关键词金属粉末;制备;分类;原理1 引言:金属及其化合物的粉末制备目前已发展了很多方法,对于这些方法的分类也有若干种。
根据原料的状态可分为固体法、液体法和气体法;根据反应物的状态可分为湿法和干法;根据生产原理可分为物理化学法和机械法。
一般来说在物理化学方法中最重要的方法为还原法、还原-化合法和电解法;在机械法中最主要的方法则是雾化法和机械粉碎法。
金属粉末的生产方法的选择取决于原材料、粉末类型、粉末材料的性能要求和粉末的生产效率等。
随着粉末冶金产品的应用越来越广泛,对粉末颗粒的尺寸形状和性能的要求越来越高,因此粉末制备技术也在不断地发展和创新,以适应颗粒尺寸和性能的要求。
2 金属粉末的制备方法:2.1 物理化学法:2.1.1 还原法:金属氧化物及盐类的还原法是一种应用最广泛的粉末制备方法。
可以采用固体碳还原铁粉和钨粉,用氢或分解氨制取钨、钼、铁、铜、钴、镍等粉末;用转化天然气和煤气可以制取铁粉等,用纳、钙、镁等金属作还原剂可以制取钽、铌、钛、锆、钍、铀等稀有金属粉末。
金属氧化物及盐类的还原法基本原理为,所使用的还原剂对氧的亲和力比氧化物和所用盐类中相应金属对氧的亲和力大,因而能够夺取金属氧化物或盐类中的氧而使金属被还原出来。
由于不同的金属元素对氧的作用情况不同,因此生成氧化物的稳定性也不大一样。
可以用氧化反应过程中的△G的大小来表征氧化物的稳定程度。
如反应过程中的△G值越小,则表示其氧化物的稳定性就越高,即其对氧的亲和力越大。
其优点是操作简单,工艺参数易于控制,生产效率高,成本较低,适合工业化生产;缺点是只适用于易与氢气反应、吸氢后变脆易破碎的金属材料。
2.1.2 金属热还原和还原化合法:金属热还原是,被还原的原料可以是固态的、气态的,也可以是熔盐。
后二者相应的又具有气相还原和液相沉淀的特点。
- 1、下载文档前请自行甄别文档内容的完整性,平台不提供额外的编辑、内容补充、找答案等附加服务。
- 2、"仅部分预览"的文档,不可在线预览部分如存在完整性等问题,可反馈申请退款(可完整预览的文档不适用该条件!)。
- 3、如文档侵犯您的权益,请联系客服反馈,我们会尽快为您处理(人工客服工作时间:9:00-18:30)。
金属粉末制备方法分类及其基本原理
摘要简要介绍了金属粉末的制备方法。
由机械法和物理化学法两大类方向具体介绍。
同时简述了各种金属粉末制备方法的基本原理。
关键词金属粉末;制备;分类;原理
1 引言:
金属及其化合物的粉末制备目前已发展了很多方法,对于这些方法的分类也有若干种。
根据原料的状态可分为固体法、液体法和气体法;根据反应物的状态可分为湿法和干法;根据生产原理可分为物理化学法和机械法。
一般来说在物理化学方法中最重要的方法为还原法、还原-化合法和电解法;在机械法中最主要的方法则是雾化法和机械粉碎法。
金属粉末的生产方法的选择取决于原材料、粉末类型、粉末材料的性能要求和粉末的生产效率等。
随着粉末冶金产品的应用越来越广泛,对粉末颗粒的尺寸形状和性能的要求越来越高,因此粉末制备技术也在不断地发展和创新,以适应颗粒尺寸和性能的要求。
2 金属粉末的制备方法:
2.1 物理化学法:
2.1.1 还原法:
金属氧化物及盐类的还原法是一种应用最广泛的粉末制备方法。
可以采用固体碳还原铁粉和钨粉,用氢或分解氨制取钨、钼、铁、铜、钴、镍等粉末;用转化天然气和煤气可以制取铁粉等,用纳、钙、镁等金属作还原剂可以制取钽、铌、钛、锆、钍、铀等稀有金属粉末。
金属氧化物及盐类的还原法基本原理为,所使用的还原剂对氧的亲和力比氧化物和所用盐类中相应金属对氧的亲和力大,因而能够夺取金属氧化物或盐类中的氧而使金属被还原出来。
由于不同的金属元素对氧的作用情况不同,因此生成氧化物的稳定性也不大一样。
可以用氧化反应过程中的△G的大小来表征氧化物的稳定程度。
如反应过程中的△G值越小,则表示其氧化物的稳定性就越高,即其对氧的亲和力越大。
其优点是操作简单,工艺参数易于控制,生产效率高,成本较低,适合工业化生产;缺点是只适用于易与氢气反应、吸氢后变脆易破碎的金属材料。
2.1.2 金属热还原和还原化合法:
金属热还原是,被还原的原料可以是固态的、气态的,也可以是熔盐。
后二者相应的又具有气相还原和液相沉淀的特点。
金属热还原剂法在工业上比较常用的有:用钙还原TiO2、ThO2、UO2等;用镁还原TiCl4、ZrCl4、TaCl5等;用钠还原TiCl4、ZrCl4、K2ZrF6、K2TaF7等;用氢化钙(CaH2)共还原氧化铬和氧化镍制取镍铬不锈钢粉。
还原化合法是指用碳、碳化硼、硅、氮与难熔金属氧化物的作用而得到碳化物、硼化物。
氮化物的方法。
2.1.3 电解法:
电解法是通过电解熔盐或盐的水溶液使得金属粉末在阴极沉积析出的方法。
用电解法几乎可以制取所有金属粉末,生产铜粉、银粉、锡粉尤为适宜。
电解制粉又可分为水溶液电解、有机电解质电解、熔盐电解和液体金属阴极电解。
其优点是制取的金属粉末纯度较高,一般单质粉末的纯度可达 99.7%以上;另外,电解法可以很好的控制粉末的粒度,可以制取出超精细粉末。
但是电解法制粉耗电量大,制粉成本较高。
电解水溶液可以生产 Cu、Ni、Fe、Ag、Sn、Fe- Ni 等金属(合金)粉末,电解熔盐可以生产Zr、Ta、Ti、Nb 等金属粉末。
2.1.4 羟基法:
将某些金属(铁、镍等)与一氧化碳合成为金属羰基化合物,再热分解为金属粉末和一氧化碳。
这样制得的粉末很细,纯度很高,但成本高。
工业上主要用来生产镍和铁的细粉和超细粉,以及 Fe-Ni、Fe-Co、Ni-Co等合金粉末。
2.1.5 化学置换法:
化学置换法是根据金属的活泼性强弱,用活泼性强的金属将活性较小的金属从金属盐溶液中将其置换出来,将置换所得到的金属(金属粉粒)用其他方法进一步处理细化。
此法主要应用于 Cu、Ag、Au 等不活泼金属粉末的制备。
2.2 机械法:
2.2.1 雾化法:
雾化法属于机械制粉法,是直接击碎液体金属或合金而值得粉末的方法,应用较广泛,规模仅次于还原法。
雾化法又称喷雾法,可以制取铅、锡、铝、铜、镍、铁等金属粉末,也可用于制取青铜、黄铜、碳钢、合金钢等合金粉末的生产。
图1 气体雾化法生产粉末
雾化法一般是利用高压气体、高压液体或高速旋转的叶片,将经高温、高压熔融的金属或合金破碎成细小的液滴,然后在收集器内冷凝而得到超细金属粉末,该过程不发生化学变化。
雾化法是生产金属及合金粉末的主要方法之一。
雾化的方法很多,如双流雾化、离心雾化、多级雾化、超声雾化技术、紧耦合雾化技术、高压气体雾化、层流雾化、超声紧耦合雾化和热气体雾化等。
雾化粉末具有球形度高、粉末粒度可控、氧含量低、生产成本低以及适应多种金属粉末的生产等优点,已成为高性能及特种合金粉末制备技术的主要发展方向,但雾化法具有生产
效率低,超细粉末的收得率不高,能耗相对较大等缺陷。
2.2.2 机械粉碎法:
固体金属的机械粉碎是一种独立的制粉方法,其机理的发展与固体应变的最终状态以及粉碎中裂纹的形成和扩展密切相关。
同时,又作为某些制粉方法不可缺少的补充工序。
例如研磨电解制得的硬脆阴极沉淀物,研磨还原制得的海绵状金属块等。
因此,机械粉碎法在粉末生产中占有重要的地位。
粉碎方式由于物料的性质以及要求的粉碎细度不同,粉碎方式也不同。
按施加外力作用方式不同,物料粉碎一般通过挤压、冲击、磨削和劈裂集中方式进行,各种粉碎设备的工作原理也多以这几种原理为主。
其中,球磨法主要分为滚动球法和振动球磨法。
该方法利用了金属颗粒在不同的应变速率下因产生变形而破碎细化的机理。
其优点是对物料的选择性不强,可连续操作,生产效率高,适用于干磨、湿磨,可以进行多种金属及合金的粉末制备。
缺点是在粉末制备过程中分级比较困难。
图2 高能球磨法制备金属粉末示意图
2.2.3 研磨法:
研磨法是将压缩气体经过特殊喷嘴后,喷射到研磨区,从而带动研磨区内的物料互相碰撞,摩擦成粉;气流膨胀后随物料上升进入分级区,由涡轮式分级器分选出达到粒度的物料,其余粗粉返回研磨区继续研磨,直至达到要求的粒度被分出为止。
由于研磨法采用干法生产,从而省去了物料的脱水、烘干等工艺;其产品纯度高、活性大、分散性好,粒度细且分布较窄,颗粒表面光滑,被广泛地应用于非金属、化工原料、颜料、磨料、保健药品等行业的超细粉碎中。
但研磨法也存在设备制造成本高,在金属粉末的生产过程中,必须使用连续不断的惰性气体或氮气作为压缩气源,耗气量较大,只适合脆性金属及合金的破碎制粉等不足。
3 总结:
随着技术的进步,金属粉末在冶金、化工、电子、磁性材料、精细陶瓷、传感器等方面均得到开发应用,显示了良好的应用前景,且金属粉末呈现出向高纯、超细(纳米)方向发展的趋势。
虽然超细金属粉末的制备方法多种多样,可根据用途和经济技术要求选用不同的方法,但每种方法都有一定的局限性,存在许多需要解决和完善的问题。
当前,制取金属粉末应用最广泛的方法当属还原法、电解法和雾化法;另外在传统生产工艺的基础上进行改进,得到了许多新型的的生产工艺和方法,如超声雾化法、旋转盘雾化法、双辊及三辊雾化法、多级雾化法、等离子旋转电极法、电弧法等。
金属粉末的制取方法中,虽然不少方法已经得到实际应用,但仍存在着两个主要问题,即规模较小和生产成本高。
为了促进金属粉末材料的发展应用,必须对不同的方法加以综合利用,取长补短,开发出生产量更大、成本更低的工艺方法。
参考文献
[1]陈振华,陈鼎.现代粉末冶金原理.北京:化学工业出版社,2013.
[2]崔庚彦,王哲,刘保军.浅谈金属粉末的制备方法.科技信息,2011,4.
[3]陈振华主编。
现代粉末冶金技术.北京:化学工业出版社,2007.
[4]徐瑞东,常仕英,郭忠诚.电解法制备超细铜粉的工艺及性能研究.电子工艺与技术,2006,11:355.
[5]陶珍东,郑少华主编.粉体工程与设备.北京:化学工业出版社,2003.
[6]王树林,李隆秀,韩正文.振动磨的发展与现状.矿山机械,1989,1:2~5.
[7]阎民,郭天德,曹维庆.振动磨理论研究进展.西安理工大学学报,1998,4:417~421.
[8]李征宇.干法超细搅拌球磨机的结构形式特点及其应用.中国粉体技术:2000,4:36.
[9]游峰,范景莲,田家敏等.喷雾干燥和一步氢还原制备各超细钨粉工艺的研究.中国钨业,2008,(6):15~18.
[10]张华诚主编.粉末冶金实用工艺.北京:冶金工业出版社,2004.。