传动轴的设计及校核
传动轴的设计及校核

第一章轻型货车原始数据及设计要求发动机的输出扭矩:最大扭矩285.0N·m/2000r/min;轴距:3300mm;变速器传动比: 五挡1 ,一挡7.31,轮距:前轮1440毫米,后轮1395毫米,载重量2500千克设计要求:第二章万向传动轴的结构特点及基本要求万向传动轴一般是由万向节、传动轴和中间支承组成。
主要用于在工作过程中相对位置不节组成。
伸缩套能自动调节变速器与驱动桥之间距离的变化。
万向节是保证变速器输出轴与驱动桥输入轴两轴线夹角的变化,并实现两轴的等角速传动。
一般万向节由十字轴、十字轴承和凸缘叉等组成。
传动轴是一个高转速、少支承的旋转体,因断改变的两根轴间传递转矩和旋转运动。
重型载货汽车根据驱动形式的不同选择不同型式的传动轴。
一般来讲4×2驱动形式的汽车仅有一根主传动轴。
6×4驱动形式的汽车有中间传动轴、主传动轴和中、后桥传动轴。
6×6驱动形式的汽车不仅有中间传动轴、主传动轴和中、后桥传动轴,而且还有前桥驱动传动轴。
在长轴距车辆的中间传动轴一般设有传动轴中间支承.它是由支承架、轴承和橡胶支承组成。
传动轴是由轴管、伸缩套和万向此它的动平衡是至关重要的。
一般传动轴在出厂前都要进行动平衡试验,并在平衡机上进行了调整。
因此,一组传动轴是配套出厂的,在使用中就应特别注意。
图 2-1 万向传动装置的工作原理及功用图 2-2 变速器与驱动桥之间的万向传动装置基本要求:1.保证所连接的两根轴相对位置在预计范围内变动时,能可靠地传递动力。
2.保证所连接两轴尽可能等速运转。
3.由于万向节夹角而产生的附加载荷、振动和噪声应在允许范围内。
4.传动效率高,使用寿命长,结构简单,制造方便,维修容易等第三章轻型货车万向传动轴结构分析及选型由于货车轴距不算太长,且载重量2.5吨属轻型货车,所以不选中间支承,只选用一根主传动轴,货车发动机一般为前置后驱,由于悬架不断变形,变速器或分动器输出轴轴线之间的相对位置经常变化,根据货车的总体布置要求,将离合器与变速器、变速器与分动器之间拉开一段距离,考虑到它们之间很难保证轴与轴同心及车架的变形,所以采用十字轴万向传动轴,为了避免运动干涉,在传动轴中设有由滑动叉和花键轴组成的伸缩节,以实现传动轴长度的变化。
轴的设计计算

轴的设计计算轴的计算通常都是在初步完成结构设计后进行校核计算,计算准则是满足轴的强度和刚度要求。
一、轴的强度计算进行轴的强度校核计算时,应根据轴的具体受载及应力情况,采取相应的计算方法,并恰当地选取其许用应力。
对于仅仅承受扭矩的轴(传动轴),应按扭转强度条件计算;对于只承受弯矩的轴(心轴),应按弯曲强度条件计算;对于既承受弯矩又承受扭矩的轴(转轴),应按弯扭合成强度条件进行计算,需要时还应按疲劳强度条件进行精确校核。
此外,对于瞬时过载很大或应力循环不对称性较为严重的轴,还应按峰尖载荷校核其静强度,以免产生过量的塑性变形。
下面介绍几种常用的计算方法:按扭转强度条件计算。
1、按扭转强度估算轴的直径对只受转矩或以承受转矩为主的传动轴,应按扭转强度条件计算轴的直径。
若有弯矩作用,可用降低许用应力的方法来考虑其影响。
扭转强度约束条件为:[]式中:为轴危险截面的最大扭剪应力(MPa);为轴所传递的转矩(N.mm);为轴危险截面的抗扭截面模量();P为轴所传递的功率(kW);n为轴的转速(r/min);[]为轴的许用扭剪应力(MPa);对实心圆轴,,以此代入上式,可得扭转强度条件的设计式:式中:C为由轴的材料和受载情况决定的系数。
当弯矩相对转矩很小时,C值取较小值,[]取较大值;反之,C取较大值,[]取较小值。
应用上式求出的值,一般作为轴受转矩作用段最细处的直径,一般是轴端直径。
若计算的轴段有键槽,则会削弱轴的强度,作为补偿,此时应将计算所得的直径适当增大,若该轴段同一剖面上有一个键槽,则将d增大5%,若有两个键槽,则增大10%。
此外,也可采用经验公式来估算轴的直径。
如在一般减速器中,高速输入轴的直径可按与之相联的电机轴的直径估算:;各级低速轴的轴径可按同级齿轮中心距估算,。
几种轴的材料的[]和C值轴的材料Q2351Cr18Ni9Ti354540Cr,35SiMn,2Cr13,20CrMnTi []12~2012~2520~3030~4040~52160~135148~125135~118118~107107~982、按弯扭合成强度条件校核计算对于同时承受弯矩和转矩的轴,可根据转矩和弯矩的合成强度进行计算。
新版轴的强度校核方法-新版-精选.pdf

另外,实际中,由于减速器输入轴通过联轴器与电动机轴相联结,
则外伸段轴径与电动机轴径不能相差太大, 否则难以选择合适的联轴
器,取
d' min
0.8d电动机轴 ,查表,取 d电动机轴
38mm, 则:
d' min
0.8d电动机轴
0.8 * 38 30.4mm
综合考虑,可取
d' min
32mm
通过上面的例子, 可以看出, 在实际运用中, 需要考虑多方面实
8
依次确定式中的各个参数:
根据减速器输出轴的受力条件,已知:
Ft 8430N Fr 3100N Fa 1800N Fr 2v 3160N Fr1v 787 N Fr 2H 5480N Fr1H 2860N T 1429.49 N m
根据图分析可得:
M H Fr 2H L1 5480 93.5 512400N mm
际因素选择轴的直径大小。
2.2.2 按弯曲强度条件计算:
由于考虑启动、 停车等影响, 弯矩在轴截面上锁引起的应力可视
为脉动循环变应力。
则
ca
其中:
M ≤[ 0 ] 1.7[ -1 ]
W
M 为轴所受的弯矩, N·mm
2
W 为危险截面抗扭截面系数 ( mm3 ) 具体数值查机械设计手册 B19.3-15 ~17.
( 2)做出弯矩图 在进行轴的校核过程中最大的难度就是求剪力和弯矩, 画出剪力 图和弯矩图,因此在此简单介绍下求剪力和弯矩的简便方法。 横截面上的剪力在数值上等于此横截面的左侧或右侧梁段上所
3
有竖向外力(包括斜向外力的竖向分力)的代数和 。外力正负号的
规定与剪力正负号的规定相同。 剪力符号: 当截面上的剪力使考虑的
传动轴的设计及校核
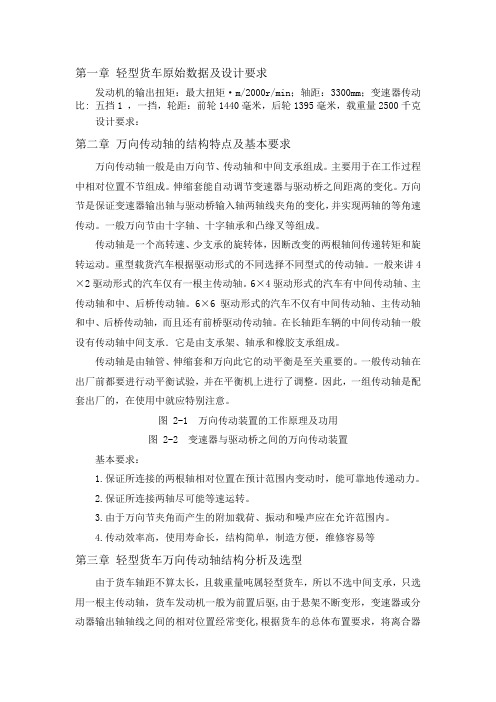
第一章轻型货车原始数据及设计要求发动机的输出扭矩:最大扭矩·m/2000r/min;轴距:3300mm;变速器传动比: 五挡1 ,一挡,轮距:前轮1440毫米,后轮1395毫米,载重量2500千克设计要求:第二章万向传动轴的结构特点及基本要求万向传动轴一般是由万向节、传动轴和中间支承组成。
主要用于在工作过程中相对位置不节组成。
伸缩套能自动调节变速器与驱动桥之间距离的变化。
万向节是保证变速器输出轴与驱动桥输入轴两轴线夹角的变化,并实现两轴的等角速传动。
一般万向节由十字轴、十字轴承和凸缘叉等组成。
传动轴是一个高转速、少支承的旋转体,因断改变的两根轴间传递转矩和旋转运动。
重型载货汽车根据驱动形式的不同选择不同型式的传动轴。
一般来讲4×2驱动形式的汽车仅有一根主传动轴。
6×4驱动形式的汽车有中间传动轴、主传动轴和中、后桥传动轴。
6×6驱动形式的汽车不仅有中间传动轴、主传动轴和中、后桥传动轴,而且还有前桥驱动传动轴。
在长轴距车辆的中间传动轴一般设有传动轴中间支承.它是由支承架、轴承和橡胶支承组成。
传动轴是由轴管、伸缩套和万向此它的动平衡是至关重要的。
一般传动轴在出厂前都要进行动平衡试验,并在平衡机上进行了调整。
因此,一组传动轴是配套出厂的,在使用中就应特别注意。
图 2-1 万向传动装置的工作原理及功用图 2-2 变速器与驱动桥之间的万向传动装置基本要求:1.保证所连接的两根轴相对位置在预计范围内变动时,能可靠地传递动力。
2.保证所连接两轴尽可能等速运转。
3.由于万向节夹角而产生的附加载荷、振动和噪声应在允许范围内。
4.传动效率高,使用寿命长,结构简单,制造方便,维修容易等第三章轻型货车万向传动轴结构分析及选型由于货车轴距不算太长,且载重量吨属轻型货车,所以不选中间支承,只选用一根主传动轴,货车发动机一般为前置后驱,由于悬架不断变形,变速器或分动器输出轴轴线之间的相对位置经常变化,根据货车的总体布置要求,将离合器与变速器、变速器与分动器之间拉开一段距离,考虑到它们之间很难保证轴与轴同心及车架的变形,所以采用十字轴万向传动轴,为了避免运动干涉,在传动轴中设有由滑动叉和花键轴组成的伸缩节,以实现传动轴长度的变化。
轿车传动轴的设计与校核

轿车传动轴的设计与校核汽车传动轴(Drive shaft)是汽车发动机与后轴之间的连接杆件,它的设计与校核对于汽车的性能和安全至关重要。
下面将详细介绍轿车传动轴的设计和校核,并阐述其重要性。
一、轿车传动轴的设计1.传动轴材料选择:传动轴需要承受发动机输出的扭矩和转速,因此需要选择具有高强度和耐疲劳性能的材料。
常用的材料包括碳素钢和合金钢。
2.传动轴的长度和直径:传动轴的长度和直径直接影响其刚度和承载能力。
根据发动机和后桥的布置,需要根据一定的分析和计算确定传动轴的合适长度和直径。
3.传动轴连接形式:传动轴通常是由两个或多个连接件组成的。
连接件通常采用螺纹连接、键式连接或插销连接等形式。
设计时需要考虑连接的强度和可靠性。
4.传动轴的平衡:传动轴在高速运转时会产生振动和失衡力。
为了提高行驶的平稳性和减少振动,传动轴需要进行动平衡。
二、轿车传动轴的校核1.扭矩校核:传动轴需要承受发动机输出的扭矩,并将其传递到后轴。
校核时需要考虑发动机的最大输出扭矩,计算传动轴受力情况并选择合适的材料和尺寸。
2.转速校核:传动轴的转速会影响其受力情况和疲劳寿命。
校核时需要根据发动机的最大转速和后桥的传动比,计算传动轴的转速,并选择合适的材料和尺寸。
3.弯曲校核:传动轴在运行过程中会受到弯曲力的作用。
校核时需要根据传动轴的长度、支撑方式和承载情况,计算传动轴的弯曲应力,并选择合适的材料和尺寸。
4.疲劳寿命校核:传动轴在长时间的运行过程中需要承受来自发动机的扭矩和转速的交替作用,容易产生疲劳破坏。
校核时需要根据传动轴的应力、材料的疲劳强度和工作寿命要求,进行疲劳强度校核。
三、轿车传动轴设计与校核的重要性1.提高传动效率:良好的传动轴设计可以减少能量的损耗,提高传动效率,使汽车在行驶过程中更加经济高效。
2.保证安全性:传动轴承载着发动机输出的扭矩和转速,如果传动轴设计不合理或存在缺陷,可能导致传动轴断裂或失效,严重影响行车安全。
轴的计算校核 计算表
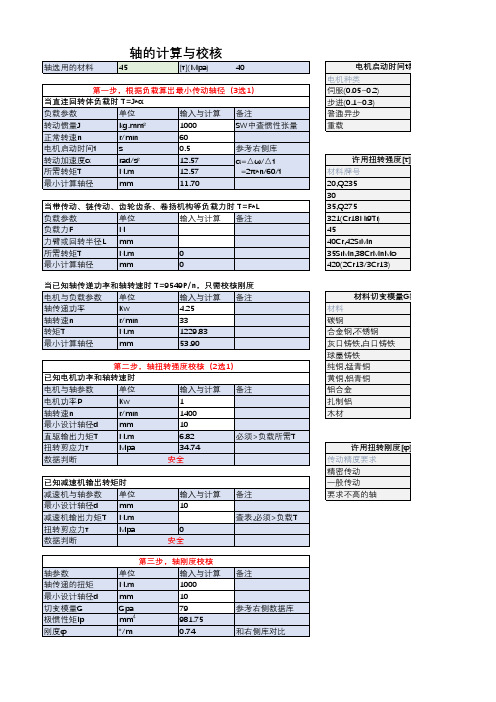
轴传递功率
Kw
பைடு நூலகம்
4.25
轴转速n
r/min
33
转矩T
N.m
1229.83
最小计算轴径
mm
53.90
第二步,轴扭转强度校核(2选1)
已知电机功率和轴转速时
电机与轴参数
单位
输入与计算 备注
电机功率P
Kw
1
轴转速n
r/min
1400
最小设计轴径d mm
10
直驱输出力矩T N.m
6.82
必须>负载所需T
扭转剪应力τ
mm
10
Gpa mm4
79 981.75
°/m
0.74
备注
参考右侧数据库 和右侧库对比
电机启动时间t数据库 电机种类 伺服(0.05~0.2) 步进(0.1~0.3) 普通异步 重载
许用扭转强度[τ]数据库 材料牌号 20,Q235 30 35,Q275 321(Cr18Ni9Ti) 45 40Cr,42SiMn 35SiMn,38CrMnMo 420(2Cr13/3Cr13)
料切变模量G数据库 G(GPa) 79.4 79.4 44 73~76 39 41 26 24~26 0.5
扭转刚度[φ]经验库 [φ](°/m) 0.25~0.5 0.5~1 ≥1
说明: 对于受扭转轴的校核分为扭转强度校核和刚度校核
1,扭转强度校核公式:τ=T/Wt≤[τ] 其中τ的量纲Mpa(N/mm²),T为转矩,量纲N.mm,Wt为扭转截 面系数,量纲mm³,可查询机械设计手册第5版3-105或通过以下 公式计算得到: 实心轴:Wt=πd³/16;空心轴:Wt=π(D4-d4)/(16*D)
传动轴布置及校核方法

传动轴布置及校核方法传动轴是一种用来传递动力和扭矩的装置,广泛应用于各种机械设备中。
在设计传动轴时,需要考虑其布置和校核方法,以确保传动轴的稳定性和安全性。
传动轴的布置方法主要包括以下几个方面:1.位置布置:传动轴的位置布置要考虑到传动装置的种类和布置要求。
通常情况下,传动轴的布置应尽量接近传动元件,如齿轮、链条等,以减小传动误差和部件的松动。
2.路由布置:传动轴的路由布置要尽量保持平直和直线,以减小传动误差和振动。
在实践中,可以通过选择合适的支撑方式、减小布置长度和合理选择径向和轴向间隙等方法来实现。
3.防护布置:传动轴在运行时会产生一定的旋转惯量和振动力,因此需要做好防护措施,以确保人员和设备的安全。
常见的防护方式有安装防护罩、设置安全限位装置等。
校核方法是确定传动轴尺寸和材料的过程,主要包括以下几个步骤:1.力学校核:首先需要根据传动轴所承受的载荷和扭矩进行力学校核。
力学校核可以通过应力分析、变形分析等方法进行。
校核应包括静态强度校核和疲劳强度校核。
2.刚度校核:传动轴在运行时会产生挠度和变形,因此需要根据运行要求和变形限制进行刚度校核。
刚度校核主要通过计算轴的刚度、挠度和变形等参数来确定。
3.动态校核:在一些高速传动轴的设计中,需要考虑其动力学性能。
动态校核主要是通过计算传动轴的固有频率和振动特性来判断传动轴的可靠性。
在动态校核中,通常要考虑传动轴的转动惯量、振动模态等。
4.材料选择:根据传动轴的校核结果,可以确定传动轴的尺寸和材料。
常用的传动轴材料有碳钢、合金钢、不锈钢等,根据不同的工作环境和要求,可以选择合适的材料。
总之,传动轴的布置和校核方法是确保传动轴稳定性和安全性的重要环节。
通过合理的布置和校核,可以保证传动轴在运行过程中的可靠性和长寿命。
在实际应用中,还需要结合具体情况进行分析和计算,并参考相关标准和规范来进行设计。
十字轴式万向节传动轴总成校核规范

十字轴式万向节传动轴总成校核规范十字轴式万向节传动轴总成校核规范十字轴式万向节传动轴总成校核规范1 范围本标准规定了十字轴式万向节传动轴总成校核规范。
本标准适用于发动机、变速器纵置后轮及四轮驱动传动轴的校核计算。
2 规范性引用文件下列文件对于本文件的应用是必不可少的.凡是注日期的引用文件,仅注日期的版本适用于本文件。
凡是不注日期的引用文件,其最新版本(包括所有的修改单)适用于本文件。
QC/T 523 汽车传动轴总成台架试验方法QC/T 29082 汽车传动轴总成技术条件3术语和定义3.1 传动轴总成:由一根或多根实心轴或空心轴管将二个或多个十字轴式万向节连接起来,用来将变速器的输出扭矩和旋转运动传递给驱动桥的装置。
3.2 传动轴临界转速:传动轴失去稳定性的最低转速。
传动轴在该转速下工作易发生共振,造成轴的严重弯曲变形,甚至折断。
3.3 当量夹角:多万向节传动轴的各个万向节输入、输出轴夹角等效转换成单万向节的夹角。
4 校核目的4.1 传动轴总成满足强度要求,能可靠地传递动力;4.2 传动轴总成满足整车耐久要求,使用寿命长。
5 校核要求5.1 校核计算涉及的整车输入参数及需校核参数(见表1)5.2 传动轴最高工作转速m axn ≤0.7kn5.3 轴管的扭转切应力cτ≤[cτ],[cτ]为轴管许用扭转应力,通常取125Mpa5.4 传动轴花键轴扭转应力满足:hτ≤[τ0], 其中[τ] 为花键轴扭转应力,通常为300~350 Mpa5.5 花键齿侧挤压应力满足:yσ≤[yσ],许用挤压应力[yσ]=25~50Mpa5.6 十字轴轴颈根部的弯曲应力wσ≤][wσ,弯曲应力的许用值][wσ为250~350Mpa5.7 十字轴轴颈根部的剪切应力τ≤][τ,剪切应力许用值][τ为80~120Mpa5.8 十字轴滚针轴承的接触应力jσ≤][jσ,接触应力许用值][jσ为3000~3200Mpa5.9 万向节叉弯曲应力wcσ≤,][wcσ弯曲应力许用值][wcσ为50-80Mpa5.10 万向节叉扭转应力bτ≤][bτ,扭转应力许用值][bτ为80-160Mpa5.11 传动轴总成的当量夹角θe <3° 6 校核计算方法6.1 传动轴计算载荷、最高车速确定6.1.1、万向传动轴的计算载荷sT (N.m)的确定对万向节传动轴进行静强度计算时,计算载荷sT 取1se T 和1ss T 的最小值;即s T =min [1se T ,1ss T ]a )按发动机最大转矩和一挡传动比确定qf e se n i ki T T η1max 1=qn 为使用分动器低档时的驱动轴数目k 为液力变矩器变矩系数,k=[(k0-1)/2]+1,k0为最大变矩系数b )按驱动轮最大附着力来确定mm ss i i RGm T ηϕ0'21='2m 汽车最大加速度时的后轴负荷转移系数,取1.2~1.4;ϕ为轮胎与路面间的附着系数,对于越野车,ϕ可取0.8;m i为主减速器从动齿轮到车轮之间的传动比; mη为主减速器主动齿轮到车轮之间的传动效率; 6.1.2 传动轴实际最高转速的确定传动轴实际最高转速m axn (r/min ),按下面方法确定:a )按发动机输入最高转速计算 1max1f g ii Ne Nse = b)按整车最高车速计算Ri V Nse π120max 100020⨯=1f i 为分动器高速档速比,一般为直接档,数值取1 对于传动轴实际最高转速m axn 取1Nse 和2Nse 的最小值,即m axn =min [1se N ,2se N ] 6.2 临界转速的计算:在选择传动轴长度和断面尺寸时,应考虑使传动轴有足够高的临界转速。
传动轴设计及校核作业指导书
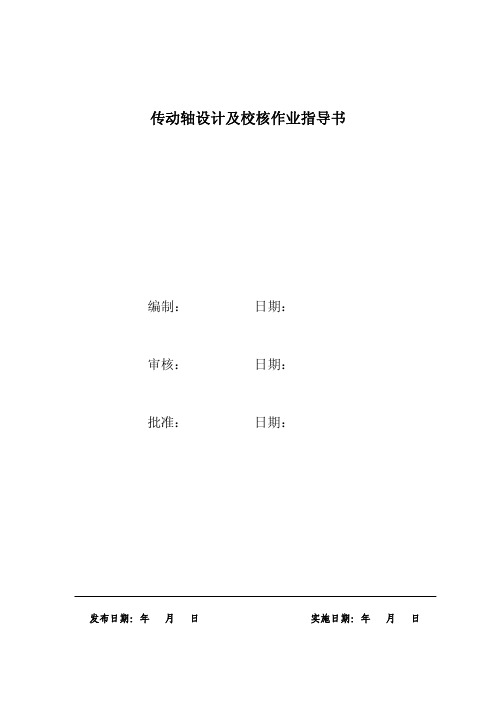
传动轴设计及校核作业指导书编制:日期:审核:日期:批准:日期:发布日期:年 月 日 实施日期:年 月 日前言为使本中心传动轴设计及校核规范化,参考国内外汽车设计的技术规范,结合公司标准和已开发车型的经验,编制本作业指导书。
意在对本公司设计人员在设计过程中起到指导操作的作用,提高设计的效率和成效。
本作业指导书将在本中心所有车型开发设计中贯彻,并在实践中进一步提高完善。
本标准于2011年XX月XX日起实施。
本标准由上海同捷科技股份有限公司第五研发中心底盘总布置分院提出。
本标准由上海同捷科技股份有限公司第五研发中心底盘总布置分院负责归口管理。
本标准主要起草人:张士华一、传动系概述 (3)1.1传动系功能 (3)1.2传动系布置形式 (3)1.3传动系的构成 (7)1.4传动轴的主要结构形式 (8)1.5驱动半轴的紧固方式 (12)二、传动轴的设计流程 (15)2.1传动轴的主要设计流程 (15)2.2传动轴的设计过程及要求 (17)三.传动轴的校核过程 (22)3.1设计校核输入 (22)3.2传动轴校核 (24)3.3结论及分析 (25)3.4传动轴跳动校核 (26)3.5技术文件的编制 (26)3.6传动轴图纸确认 (26)四.试制装车及生产中经常出现的问题 (28)五.参考文献 (28)一、传动系概述1.1 传动系功能A、保证汽车在各种行驶条件下所必需的牵引力与车速,使它们之间能协调变化并有足够的变化范围。
B、使汽车具有良好的动力性和燃油经济性。
C、保证汽车能倒车及左右车轮能适应差速要求。
D、使动力传递能根据需要而顺利接合与分离1.2 传动系的布置形式• 前置后驱动• 前置前驱动• 后置后驱动• 四轮驱动• 中置发动机后轮驱动部分高级轿车也采用前置后驱布置 前置后驱整体桥前置前驱,应用最多前置前驱,应用最多前轮驱动的优点:1、前轮驱动在制造和安装方面都比后轮驱动成本要低很多。
它没有通过驾驶舱下面的驱动轴,也不用制造后桥壳,变速器和差速器被装配在一个壳体中,这样所需的零部件就更少。
传动轴(半轴)跳动校核报告解读

Professional目录1 概述 (1)2 校核目的 (1)3 B35-1车型前传动轴(驱动半轴)运动校核 (1)3.1左传动轴跳动角度校核 (1)3.2 右传动轴跳动角度校核(2WD) (5)3.3右传动轴跳动角度校核(4WD) (9)3.4 前传动轴(驱动半轴)跳动过程中与周边件最小间隙校核 (13)4 B35-1车型后传动轴(驱动半轴)运动校核 (15)4.1 后驱动半轴跳动上极限校核 (16)4.2 后驱动半轴跳动下极限校核 (17)5 B35-1车型中间传动轴运动校核 (17)6 结论 (18)参考文献 (21)传动轴跳动校核报告1概述在车辆行驶过程中,传动轴在跳动极限和转向极限范围,要求传动轴角度关系和伸缩量在允许范围内,以及传动轴在极限状态时与周边零部件具有允许的最小间隙,以保证汽车行驶的安全性。
下面按照有关标准的规定和要求,对B35-1车型进行传动轴跳动校核。
2校核目的2.1传动轴跳动的上下极限位置及最大夹角是否符合设计要求。
2.2传动轴在车辆行驶过程中,与周围部件是否干涉及最小间隙是否满足技术要求。
3B35-1车型前传动轴(驱动半轴)运动校核3.1左传动轴跳动角度校核B35-1车型左传动轴校核主要是分析前驱动半轴在左转跳动上极限、右转跳动上极限、左转跳动下极限、右转跳动下极限四个状态下,驱动半轴角度关系应在允许范围内,以及在极限状态校核驱动半轴与周边零部件具有允许的最小间隙情况。
根据厂家提供图纸的技术要求,固定节最大允许角度46°,移动节最大允许角度为23°,移动节滑移量范围为:-23.0mm~25.9mm。
通过对左传动轴各状态数模的分析测量,得到以下数据。
表1 左传动轴校核参数图1左传动轴移动节的滑移线图由此可见,移动节最大滑移量为-5.5mm小于-23mm,移动节最大夹角为16.8°小于23°,所以左传动轴的移动节满足工作要求。
图2 左传动轴跳动上极限图3 左传动轴左转跳动上极限图4 左传动轴右转跳动上极限图5 左传动轴跳动下极限图6 左传动轴左转跳动下极限1图7 左传动轴右转跳动下极限3.2 右传动轴跳动角度校核(2WD)B35-1车型右传动轴校核主要是分析右传动轴在左转极限跳动上极限、右转极限跳动上极限、左转极限跳动下极限、右转极限跳动下极限四个状态下,传动轴角度关系及伸缩量应在允许范围内,以及在极限状态时右传动轴与周边零部件最小间隙校核。
传动轴布置及校核方法

传动轴布置及校核方法传动轴是机械传动系统中常用的一种零件,主要用于将发动机的动力传递给机械设备。
它是由两个或多个轮毂和中间的轴段组成。
传动轴的布置和校核是确保传动系统正常运转的重要环节。
本文将介绍传动轴布置的基本原则和校核方法。
1.直线布置:传动轴的布置尽量直线,轴段尽量缩短。
直线布置能减小传动轴的弯曲和振动,提高传动效率和传动精度。
同时,采用直线布置还能节省空间,简化传动系统结构。
2.曲线布置:若传动轴无法直线布置(例如传动装置之间相隔较远),可以采用曲线布置。
曲线布置需要考虑轴段的弯曲和转角对传动轴的影响,避免过大的转角和弯曲造成传动轴的过分弯曲和疲劳。
传动轴的校核方法主要包括静力学校核和疲劳校核。
1.静力学校核:静力学校核是指通过计算、分析传动轴在工作负载下的受力情况,来判断传动轴是否具有足够的强度。
静力学校核时需要考虑传动轴的受力情况、材料强度、线性和非线性变形等因素。
常用的静力学校核方法包括弹性力学计算、有限元分析等。
2.疲劳校核:疲劳校核是指通过计算、分析传动轴在长时间循环工作下的疲劳寿命,来判断传动轴是否具有足够的疲劳强度。
疲劳校核时需要考虑传动轴的应力集中情况、材料的疲劳性能、循环载荷和工作条件等因素。
常用的疲劳校核方法包括应力异常修正法、极限剩余应力法、伤害积累理论法等。
在传动轴的校核过程中,需要根据具体的传动方式、传动功率、传动比等因素来选择适当的校核方法和工具。
同时,还需要根据传动轴的实际情况和工作条件,合理选择材料、尺寸和制造工艺,以确保传动轴具有足够的强度、刚度和疲劳寿命。
总之,传动轴布置和校核是机械传动系统设计中重要的环节。
通过合理布置和科学校核,可以保证传动系统的正常运行和稳定工作。
轴的强度校核方法
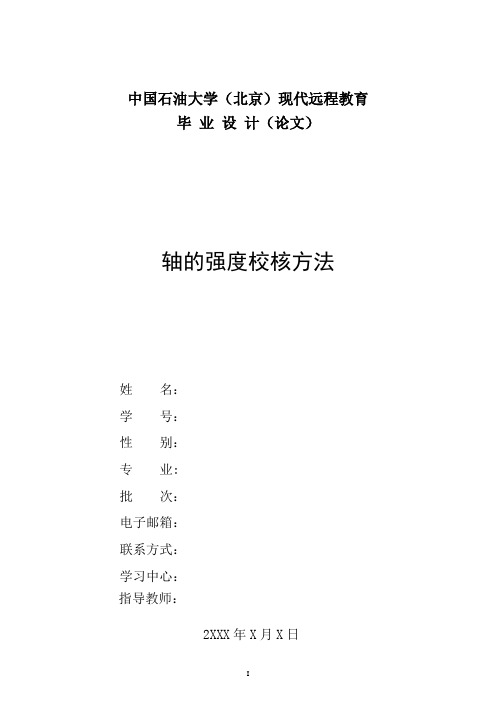
中国石油大学(北京)现代远程教育毕业设计(论文)轴的强度校核方法姓名:学号:性别:专业:批次:电子邮箱:联系方式:学习中心:指导教师:2XXX年X月X日中国石油大学(北京)现代远程教育毕业设计(论文)轴的强度校核方法摘要轴是用来支承回转运动零件,如带轮、齿轮、蜗轮等,同时实现同一轴上不同零件间的回转运动和动力的传递的重要的零件。
为实现机械产品的完整和可靠设计,轴的设计应考虑选材、结构、强度和刚度等要求。
并应对轴的材料或设备的力学性能进行检测并调节,轴的强度校核应根据轴的具体受载及应力情况,采取相应的计算方法,并恰当地选取其许用应力。
最后确定轴的设计能否达到使用要求,对轴的设计十分重要。
本文根据轴的受载及应力情况,介绍了几种典型的常用的对轴的强度校核计算的方法,并对如何精确计算轴的安全系数做了具体的介绍。
当校核结果如不满足承载要求时,则必须修改原结构设计结果,再重新校核。
最后,本文对提高轴的疲劳强度和刚度提出相应改进方法,并对新材料,新技术的应用进行了展望。
关键词:轴;强度;弯矩;扭矩;目录第一章引言 (5)1.1轴类零件的特点 (5)1.2轴类零件的分类 (6)1.3轴类零件的设计要求 (6)1.3.1、轴的设计概要 (6)1.3.2、轴的材料 (6)1.3.3、轴的结构设计 (7)1.4课题研究意义 (9)第二章轴的强度校核方法 (11)2.1强度校核的定义 (11)2.2常用的轴的强度校核计算方法 (11)2.2.1按扭转强度条件计算: (11)2.2.2按弯曲强度条件计算: (13)2.2.3按弯扭合成强度条件计算 (13)2.2.4精确计算(安全系数校核计算) (20)第三章提高轴的疲劳强度和刚度的措施 (25)3.1合理的选择轴的材料 (25)3.2合理安排轴的结构和工艺 (25)3.3国内外同行业新材料、新技术的应用现状 (26)总结 (31)参考文献 (32)第一章引言1.1轴类零件的特点轴是组成各类机械的主要和典型的零件之一,主要起支承传动零部件,传递扭矩和承受载荷的作用。
轴的选择与校核

03
采用先进制造技术
如采用数控加工技术、在线检 测技术、智能制造技术等,提 高轴的制造精度和生产效率。
04
加强人员培训
提高制造人员的技能水平和质 量意识,确保轴的制造过程符 合相关标准和要求。
05
轴的安装、调试与维护保养
安装前的准备工作
检查轴的外观和尺寸, 确保无裂纹、毛刺等 缺陷,尺寸符合设计 要求。
绘制轴力图
将计算得到的支反力按一定比例绘制在轴上 ,形成轴力图,以直观反映轴的受力情况。
轴的强度校核
选择校核截面
根据轴的受力情况和危险截面位置,选择合适的 校核截面。
计算截面应力
利用材料力学中的弯曲应力计算公式,计算校核 截面的应力。
强度条件校核
将计算得到的应力与许用应力进行比较,判断轴 的强度是否满足要求。
轴的热处理
通过淬火、回火、调质等热处理工 艺,提高轴的力学性能和耐磨性。
质量控制关键点
机械加工过程监控
监控加工过程中的切削参数、刀 具磨损、机床精度等,确保加工 质量稳定。
成品检验
对成品轴进行尺寸精度、形位公 差、表面质量等方面的检验,确 保符合设计要求和相关标准。
01
02
毛坯质量检查
对毛坯的外观、尺寸、化学成分 等进行检查,确保符合设计要求 。
准备安装所需的工具 和材料,如扳手、螺 栓、垫片等。
清理轴的安装表面, 去除油污、锈蚀等杂 质。
安装过程中的注意事项
确保轴的安装位置正确,避免出现偏移或倾斜。
在安装过程中,要轻拿轻放,避免对轴造成撞击 或划伤。 按照规定的拧紧力矩紧固螺栓,防止过紧或过松。
调试方法及步骤
01
安装完成后,进行初步的调试,检查轴是否灵活转动,无卡 滞现象。
传动轴布置及校核方法
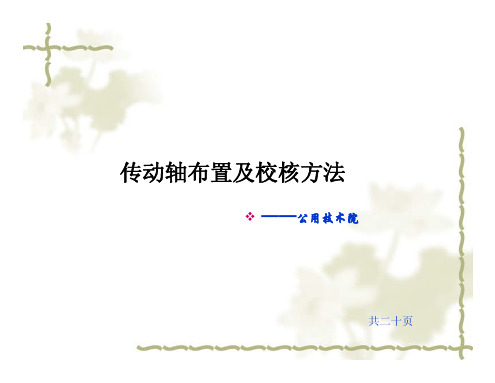
用初选的传动轴长度进行校核,将移动节中心坐标及工作角度和固定 节中心点坐标分别测量出来,将这些点输入厂家提供的梯形图进行比较。 如果不满足要求,需与以上各状态一起进行传动轴长度的调整或发动机姿 态的调整。
(三)其他工况校核
1、Braking at 0.9g.(0.9g的减速度制动) 2、Right turn at 0.9g.(0.9g的加速度向右转弯) 3、Left turn at 0.9g(0.9g的加速度向左转弯) 4、Driving away in first gear.(一档起步) 5、Driving away in rear gear.(倒档起步) 6、Rear crash at 25g. (only for USA market)(25g加速度后碰) 7、Jolt upwards at 3.5g(3.5g加速度向上晃动) 8、Jolt downwards at 4.5g.(4.5g加速度向下晃动)
传动轴布置方法
传动轴布置步骤:
传动轴的布置与动力总成的布置紧密相关,实际上属于同时布置;
一 初步确定传动轴位置
先初步确定动力总成位置
动力总成布置
传动轴布置
考虑因素:
左右:与左右纵梁静、动态间隙
上下:静、动态间隙、行人保护、台阶保护、离地间隙
前后:静、动态间隙、碰撞安全、温度场
通过移动旋转动力总成来满足上述要求;
传动轴布置及校核方法
——公用技术院
共二十页
传动轴基本介绍
传动轴连接差速器与轮胎以传递动力,现多用万向传动轴,即包括两个十字轴万 向节与一根可伸缩的传动轴。万向传动轴应能适应所联两轴夹角及相对位置在一定范 围内的不断变化并且能可靠、稳定、高效地传递动力,保证所联两轴能等速旋转。
轴的强度校核方法

2.2常用的轴的强度校核计算方法进行轴的强度校核计算时,应根据轴的具体受载及应力情况,采 取相应的计算方法,并恰当地选取其许用应力。
对于传动轴应按扭转强度条件计算。
对于心轴应按弯曲强度条件计算。
对于转轴应按弯扭合成强度条件计算。
2.2.1按扭转强度条件计算:这种方法是根据轴所受的扭矩来计算轴的强度, 对于轴上还作用 较小的弯矩时,通常采用降低许用扭转切应力的办法予以考虑。
通常 在做轴的结构设计时,常采用这种方法估算轴径。
实心轴的扭转强度条件为:P TT _WT9550000严w T由上式可得轴的直径为d.nT 为扭转切应力,MPa式中:T 为轴多受的扭矩,N • mmW T 为轴的抗扭截面系数,mm 3n 为轴的转速,r/min P 为轴传递的功率,KW d 为计算截面处轴的直径,mm[T ]为许用扭转切应力,Mpa [片]值按轴的不同材料选取,常用轴的材料及[r ]值见下表:表1 轴的材料和许用扭转切应力空心轴扭转强度条件为:-=dl其中1即空心轴的内径*与外径d之比,通常取1 =0.5-0.6 d这样求出的直径只能作为承受扭矩作用的轴段的最小直径。
例如,在设计一级圆柱齿轮减速器时,假设高速轴输入功率P仁2.475kw, 输入转速n仁960r/min,则可根据上式进行最小直径估算,若最小直径轴段开有键槽,还要考虑键槽对轴的强度影响。
根据工作条件,选择45#钢,正火,硬度HB170-217,作为轴的材料,A0值查表取A0=112,则:P 丨2 475d min - A o 112 15.36mm,厲960因为高速轴最小直径处安装联轴器,并通过联轴器与电动机相连接,设有一个键槽,贝心d m/ =d min (1 7%) =15.36 (1 7%) = 16.43mm另外,实际中,由于减速器输入轴通过联轴器与电动机轴相联结,则外伸段轴径与电动机轴径不能相差太大,否则难以选择合适的联轴器,取d min =0.8d电动机轴,查表,取d电动机轴=38mm,贝卩:d m in = 0.8d电动机轴=0.8* 38 = 30.4mm综合考虑,可取d min' =32mm通过上面的例子,可以看出,在实际运用中,需要考虑多方面实际因素选择轴的直径大小。
- 1、下载文档前请自行甄别文档内容的完整性,平台不提供额外的编辑、内容补充、找答案等附加服务。
- 2、"仅部分预览"的文档,不可在线预览部分如存在完整性等问题,可反馈申请退款(可完整预览的文档不适用该条件!)。
- 3、如文档侵犯您的权益,请联系客服反馈,我们会尽快为您处理(人工客服工作时间:9:00-18:30)。
第一章轻型货车原始数据及设计要求发动机的输出扭矩:最大扭矩285.0N·m/2000r/min;轴距:3300mm;变速器传动比: ?五挡1 ,一挡7.31,轮距:前轮1440毫米,后轮1395毫米,载重量2500千克设计要求:第二章万向传动轴的结构特点及基本要求万向传动轴一般是由万向节、传动轴和中间支承组成。
主要用于在工作过程中相对位置不节组成。
伸缩套能自动调节变速器与驱动桥之间距离的变化。
万向节是保证变速器输出轴与驱动桥输入轴两轴线夹角的变化,并实现两轴的等角速传动。
一般万向节由十字轴、十字轴承和凸缘叉等组成。
传动轴是一个高转速、少支承的旋转体,因断改变的两根轴间传递转矩和旋转运动。
重型载货汽车根据驱动形式的不同选择不同型式的传动轴。
一般来讲4×2驱动形式的汽车仅有一根主传动轴。
6×4驱动形式的汽车有中间传动轴、主传动轴和中、后桥传动轴。
6×6驱动形式的汽车不仅有中间传动轴、主传动轴和中、后桥传动轴,而且还有前桥驱动传动轴。
在长轴距车辆的中间传动轴一般设有传动轴中间支承.它是由支承架、轴承和橡胶支承组成。
传动轴是由轴管、伸缩套和万向此它的动平衡是至关重要的。
一般传动轴在出厂前都要进行动平衡试验,并在平衡机上进行了调整。
因此,一组传动轴是配套出厂的,在使用中就应特别注意。
图 2-1 万向传动装置的工作原理及功用图 2-2 变速器与驱动桥之间的万向传动装置基本要求:1.保证所连接的两根轴相对位置在预计范围内变动时,能可靠地传递动力。
2.保证所连接两轴尽可能等速运转。
3.由于万向节夹角而产生的附加载荷、振动和噪声应在允许范围内。
4.传动效率高,使用寿命长,结构简单,制造方便,维修容易等第三章轻型货车万向传动轴结构分析及选型由于货车轴距不算太长,且载重量2.5吨属轻型货车,所以不选中间支承,只选用一根主传动轴,货车发动机一般为前置后驱,由于悬架不断变形,变速器或分动器输出轴轴线之间的相对位置经常变化,根据货车的总体布置要求,将离合器与变速器、变速器与分动器之间拉开一段距离,考虑到它们之间很难保证轴与轴同心及车架的变形,所以采用十字轴万向传动轴,为了避免运动干涉,在传动轴中设有由滑动叉和花键轴组成的伸缩节,以实现传动轴长度的变化。
空心传动轴具有较小的质量,能传递较大的转矩,比实心传动轴具有更高的临界转速,所以此传动轴管采用空心传动轴。
传动轴的长度和夹角及它们的变化范围,由汽车总布置设计决定。
设计时应保证在传动轴长度处在最大值时,花键套与花键轴有足够的配合长度;而在长度处于最小时,两者不顶死。
传动轴夹角大小会影响万向节十字轴和滚针轴承的寿命、万向传动效率和十字轴的不均匀性。
变化范围为3。
传动轴经常处于高速旋转状态下,所以轴的材料查机械零件手册选取40CrNi,适用于很重要的轴,具有较高的扭转强度。
3.1传动轴管选择传动轴管由低碳钢板制壁厚均匀、壁薄(1.5~3.0mm)、管径较大、易质量平衡、扭转强度高、弯曲刚度高、适用高速旋转的电焊钢管制成。
3.2 伸缩花键选择选择矩形花键,用于补偿由于汽车行驶时传动轴两端万向节之间的长度变化。
为减小阻力及磨损,对花键齿磷化处理或喷涂尼龙,外层设有防尘罩,间隙小一些,以免引起传动轴的震动。
花键齿与键槽按对应标记装配,以保持传动轴总成的动平衡。
动平衡的不平衡度由电焊在轴管外的平衡片补偿。
装车时传动轴的伸缩花键一端应靠近变速器,减小其轴向阻力和磨损。
其结构图如下:图 3-1 万向传动轴—花键轴结构简图1-盖子;2-盖板;3-盖垫;4-万向节叉;5-加油嘴;6-伸缩套;7-滑动花键槽;8-油封;9-油封盖;10-传动轴管第四章万向传动轴计算及强度校核4.1传动轴的临界转速长度一定时,传动轴断面尺寸的选择应保证传动轴有足够的强度和足够高的临界转速。
所谓临界转速,就是当传动轴的工作转速接近于其弯曲固有振动频率时,即出现共振现象,以致振幅急剧增加而引起传动轴折断时的转速。
传动轴的临界转速nk(r/min)为,安全系数K取2.0,适用于一般精度的伸缩花键则有(w n 为发动机转速)0.2max =n n k ,4.2传动轴计算转矩 4.3传动轴长度选择根据轴距3300mm ,初选传动轴支承长度C L 为)(6.31470± mm ,花键轴长度应小于支承长度,满足万向节与传动轴的间隙要求,取花键轴长度为mm )5.21448(± 4.4传动轴管内外径确定得3.5188102.11470400028222=⎪⎪⎭⎫ ⎝⎛⨯⨯=+c c d D 又mm d D mm cc 325.1≤-≤初取 mm D c 53=, 则——Lc 为传动轴长度(mm ),即两万向节中心之间的距离;dc 和Dc 分别为传动轴轴管的内、外径(mm )4.5传动轴扭转强度校核由于传动轴只承受扭转应力而不承受弯曲应力,所以只需校核扭转强度,根据公式有[]MPaMPa d D T D c c C c c 3002518.485314.320625165316)(164414=≤=-⨯⨯⨯=-=τπτ)( (c τ为轴管许用扭转应力)上式说明设计参数满足扭转强度要求 4.6花键内外径确定 取安全系数2.27,则h τ——为许用扭转应力K '——为花键转矩分布不均匀系数,取1.3 h D ——花键外径 h d ——花键内径h L ——为花键有效工作长度B ——为键齿宽 0n ——为花键齿数由于花键齿侧许用挤压应力较小,所以选用Lh 较大尺寸的花键,查GB/T1144-2001,取mm d h 46=,mm D h 50=,mm B 9=80=n ,mm L h 041=。
4.7花键挤压强度校核当花键齿面硬度为35HRC 时,许用挤压应力为[]MPa y 50~25=σ 则[]y y σσ<,满足花键挤压强度。
4.8传动轴形位公差确定通过查手册中轴的公差及基本偏差表,确定轴选用配合e7,此配合适用于有明显间隙、易于转动的支承配合,花键根据手册查得dh 为f7,Dh 为a11,B 为d10,由此可确定轴的外径和内径分别为060.0090.053--=C D mm 060.0900.08.48--=c d mm ,花键外径跟内径分别为mmD h 320.0480.050--=,mm d h 025.0050.046--=,80=n ,,mm L h 6.1401±=。
传动轴总成的不平衡是传动系弯曲振动的一个激励源,当高速旋转时,将产生明显的振动和噪声。
万向节中十字轴的轴向窜动、传动轴滑动花键中的间隙、传动轴总成两端连接处的定心精度、高速回转时传动轴的弹性变形、传动轴上点焊平衡片时的热影响等因素,都能改变传动轴总成的不平衡度。
提高滑动花键的耐磨性和万向节花键的配合精度、缩短传动轴长度并增加其弯曲刚度,都能降低传动轴的不平衡度。
为了消除点焊平衡片的热影响,应在冷却后再进行动平衡检验。
传动轴的不平衡度,对于所设计的货车,在1000~4000r/min 时不大于50~100g.cm 。
传动轴总成的径向全跳动不大于0.8mm 。
轴管两端的摆差在其两端不大于0.5mm 。
第五章 十字万向节的设计及校核5.1 结构方案选择十字轴万向节结构简单,强度高,耐久性好,传动效率高,生产成本低,但所连接的两轴夹角不宜太大。
当夹角增加时,万向节中的滚针轴承寿命将下降。
普通的十字轴式万向节主要由主动叉,从动叉,十字轴,滚针轴承及轴向定位件和橡胶封件等组成。
5.2 计算传动轴载荷由于发动机前置后驱,根据表4-1,位置采用:用于变速器与驱动桥之间按发动机最大转矩和一档传动比来确定Tse1=kdTemaxki1ifη/nTss1= G2 m’2φrr/ i0imηm根据富利卡2.0数据,发动机最大转矩Temax=285Nm驱动桥数n=1,发动机到万向传动轴之间的传动效率η=0.85,液力变矩器变矩系数k={(k0 -1)/2}+1=1.615,满载状态下一个驱动桥上的静载荷G2=65%mag=0.65*5000*9.8=31850N,发动机最大加速度的后轴转移系数m’2=1.3,轮胎与路面间的附着系数φ=0.85,车轮滚动半径rr=0.369,主减速器从动齿轮到车轮之间传动比im=1,主减速器主动齿轮到车轮之间传动效率ηm=η发动机η离合器=0.9*0.85=0.765,因为0.195 mag/Temax>16,fj=0,所以猛接离合器所产生的动载系数kd=1,主减速比i0=4.04所以:Tse1=kdTemaxki1ifη/n=185.0 04.4615.12851⨯⨯⨯⨯=1580.6NTss1= G2 m’2φrr/ i0imηm=765.0104.4369 .085.02.1 31850⨯⨯⨯⨯⨯=3878.8N ∵T1=min{ Tse1, Tss1} ∴T1= Tse1=1580.6N5.3 十字轴万向节设计①设作用于十字轴轴颈中点的力为F,则F= T1/2rcosα='3563cos105.6526.1580︒-⨯⨯⨯=12094.1N②十字轴轴颈根部的弯曲应力σw和切应力τ应满足σw =32d1Fsπ(d14-d42)≤[σw]τ=4Fπ(d21-d22)≤[τ]式中,取十字轴轴颈直径d1=38.2mm,十字轴油道孔直径d2=10mm,合力F作用线到轴颈根部的距离s=14mm,[σw]为弯曲应力的许用值,为250-350Mpa,[τ]为切应力的许用值,为80-120 Mpa∴σw =32d1Fsπ(d14-d42)=32×38.2×10-3×7428.561×14×10-3π[(38.2×10-3)4-(10×10-3)4]12094.1=19.094 Mpa<[σw]τ=4Fπ(d21-d22)=4×7428.561π[(38.2×10-3)2-(10×10-3)2=6.959 Mpa<[τ]故十字轴轴颈根部的弯曲应力和切应力满足校核条件③十字轴滚针的接触应力应满足σj =272(1d1+1d)FnLb≤[σj]式中,取滚针直径d0=3mm,滚针工作长度Lb=27mm,在合力F作用下一个滚针所受的最大载荷Fn =4.6FiZ=4.6×7428.5611×44=776.622N,当滚针和十字轴轴颈表面硬度在58HRC以上时,许用接触应力[σj]为3000-3200 Mpa∴σj =272(1d1+1d)FnLb=272[1(38.2×10-3)+1(3×10-3)]×776.62227×10-3=0.875 Mpa<[σj]故十字轴滚针轴承的接触应力校核满足④万向节叉与十字轴组成连接支承,在力F作用下产生支承反力,在与十字轴轴孔中心线成45°的截面处,万向节叉承受弯曲和扭转载荷,其弯曲应力σw 和扭应力τb应满足σw =Fe/W≤[σw]τb =Fa/Wt≤[τb]式中,取a=40mm,e=80mm,b=35mm,h=70mm,查表4-3,取k=0.246,W=bh2/6, Wt=khb2, 弯曲应力的许用值[σw ]为50-80Mpa,扭应力的许用值[τb]为80-160 Mpa∴σw =Fe/W=7428.561×80×10-335×10-3×(70×10-3)26=20.791 Mpa< [σw ]τb =Fa/W t =7428.56×40×10-30.246×70×10-3×(35×10-3)2=14.086 Mpa<[τb ]故万向节叉承受弯曲和扭转载荷校核满足要求⑤ 十字轴万向节的传动效率与两轴的轴间夹角α,十字轴的支承结构和材料,加工和装配精度以及润滑条件等有关。