螺旋板式换热器工作原理、构造及特点
螺旋板式换热器结构设计

螺旋板式换热器结构设计螺旋板式换热器是一种高效的热交换设备,广泛应用于化工、石油、制药、食品等领域。
其具有换热效率高、能耗低、结构紧凑、占地面积小等优势。
本文将从螺旋板式换热器的结构设计方面进行探讨。
一、基本结构螺旋板式换热器主要由两个纵向平行的金属板组成,它们呈轴线对称排列并向相反方向旋转。
在两个金属板之间,通过搭接或焊接形成交错的通道,形成流体的热交换通道。
1.板式尺寸:板式尺寸的设计应综合考虑流体的流量、压力损失、热传导和换热面积等因素。
对于对称的螺旋板式换热器,一般采用相同的板式,但对小流量、大面积换热器,可采用不同的板式。
2.板式形状:板式的形状直接影响流体的流动状态和热传导效率,在设计中应选用合适的板式形状。
一般采用折弯或贴合成型的方法将金属板加工成波形或直线形态,以减少流体流动的阻力,提高换热效率。
3.板式厚度和材料:板式的厚度和材料确定了板式的刚度和耐腐蚀性。
板式厚度应保证足够的强度和稳定性,一般选择0.4-1.2mm的厚度。
板式材料要选用高强度、优良的耐腐蚀性金属材料,例如不锈钢、钛等。
三、堆叠式结构设计在堆叠式螺旋板式换热器中,多个板式交错组合形成流体的换热通道,其结构设计包括以下几个方面:1.通道宽度:通道宽度的设计应综合考虑换热效率、压力损失和流体的流量大小。
通道宽度越小,换热效率越高,但压力损失也越大。
一般通道宽度为10-15mm。
2.板式堆叠方式:板式堆叠方式有单侧进出口和双侧进出口两种。
单侧进出口适用于流量较大、压力损失小的情况;双侧进出口适用于流量较小、压力损失大的情况。
3.渗漏损失:渗漏损失是指流体在换热通道之间泄漏导致的能量损失。
设计时应注意减小通道之间的渗漏损失,采取相应的措施,如板式之间采用密封条,增加密封面积等。
容积设计是指为螺旋板式换热器设计合理的壳体容积和板式堆叠数目。
在容积设计中,应考虑以下几个方面:1.壳体容积:为保证换热器的性能和运行效率,在设计时应尽量减少壳体的容积,以减少流体的停留时间和热损失。
螺旋板式换热器

目录
• 螺旋板式换热器概述 • 螺旋板式换热器性能特点 • 螺旋板式换热器应用领域 • 螺旋板式换热器设计选型 • 螺旋板式换热器运行维护与保养 • 螺旋板式换热器发展趋势与展望
01 螺旋板式换热器概述
定义与的换热设备,由两张平行的金 属板卷制而成,形成两个均匀的 螺旋通道。
未来发展趋势预测
个性化定制
随着市场需求多样化,螺旋板式换热器将向个性 化定制方向发展。
绿色环保
环保意识的提高将推动螺旋板式换热器向更加环 保的方向发展。
智能化和网络化
随着工业4.0的推进和物联网技术的应用,螺旋板 式换热器将实现智能化和网络化运行。
THANKS FOR WATCHING
感谢您的观看
螺旋板式设计使得设备具有较高的承压能力,可适应较高的工
03
作压力和温度。
操作弹性大、适用范围广
螺旋板式换热器可处 理多种流体介质,包 括液体、气体以及蒸 汽等。
设备处理量可根据需 求进行调整,操作弹 性大。
操作温度范围宽,可 满足不同工艺要求。
易于维护和管理
设备结构简单,维护方便。
螺旋板式换热器具有较长的使用寿命和稳定的性 能,降低了维护成本。 设备运行过程中噪音低,对环境影响小。
02
原理:两种不同温度的流体在螺 旋通道内以逆流或顺流方式进行 热量交换,达到加热或冷却的目 的。
结构组成
螺旋体
由金属板材卷制而成的 螺旋通道,是热量交换
的主要场所。
端盖
密封装置
支承结构
位于螺旋体两端,用于 连接流体进出口管道。
确保流体在螺旋通道内 不泄漏,保证换热效率。
用于支撑螺旋体,保证 其稳定性和安全性。
螺旋板式换热器

螺旋板式换热器螺旋板式换热器:主要由两张平行的薄钢板卷制而成,构成一对相互隔开的螺旋形流道。
冷热两流体以螺旋板为传热面相间流动,两板之间焊有定距柱以维持流道间距,同时也可以增加螺旋板的刚度。
在换热器中心设有中心隔板,使得两个螺旋通道隔开。
在顶部和底部分别焊有盖板或封头和两流体的出、入接管。
一般有一对进出口是设在圆周边上(接管可以为切向或径向),而另外一对则设在圆鼓的轴心上。
螺旋板式换热器是一种高效换热设备,适用汽-汽、汽-液、液-液,对液传热。
它适用于化学、石油、溶剂、医药、食品、轻工、纺织、冶金、轧钢、焦化等行业。
由于用途不同,螺旋板换热器的流道布置和封盖形式有以下几种结构型式。
不可拆式(I型)螺旋板式及可拆式(II型、III型)螺旋板式换热器。
“I”型结构:两个螺旋流道的两侧完全焊接密封,所以又称为不可拆结构,因而具有较高的密封性。
两流体在流道长均作螺旋流动。
冷流体从外流向中心,热流体从中心流向外,完全是逆流。
由于流体是在单流道中流动,流动分布情况良好,这种形式主要用于液体与液体。
“II”型结构:在这种型式中,一种流体在螺旋流道中进行螺旋流动,另一种则在另一螺旋流道中进行轴向流动。
所以轴向流道的两侧是敞开的,螺旋流道两侧则焊接密封。
这种型式适用于两种介质流率差别很大的情况,通常用作冷凝器、气体冷却器等。
“III”型结构:在这种型式中,一种流体进行螺旋流动,另一种则进行轴向流动和螺旋流动的组合。
适用于蒸汽的冷凝冷却,蒸汽先进入轴流部分,当冷凝后体积减小时,才转入螺旋流道以进一步冷却。
其特点是有一端管板不与外壳相连,可以沿轴向自由伸缩。
这种结构不但完全消除了热应力,而且由于固定端的管板用法兰与壳体连接,整个管束可以从壳体中抽出,便于清洗和检修。
螺旋板换热器的直径一般在1.6m以内,板宽200~1200mm,板厚2~4mm。
两板间的距离由预先焊在板上的定距撑控制,相邻板间的距离为5~25mm。
常用材料为碳钢和不锈钢。
螺旋板换热器的结构及作用

螺旋板换热器的结构及作用
螺旋板换热器是由一组相紧邻的螺旋板组成的一种换热器,它的结构
由内、外壳、螺旋板和锥形中心组成。
其中最重要的是螺旋板,内、外壳
只是它的外部结构,螺旋板的密度和螺距决定了换热效率、流动特性、结
构限制,以及安装在外壳上的锥形中心,消除螺旋板在入口和出口处的速
率变化。
螺旋板换热器用于汽液两相流中的热传递,还可以用于特殊流体的热
传递。
它采用独特的结构设计,从而可以在有限的空间和体积内获得最大
的热传递效率。
它可以更有效地提供更大空间,使得热传递过程更为紧凑。
因此,螺旋板换热器的作用是在液体或汽气流体传递过程中,能够有
效地传递热能,改善换热效率,防止易燃、易爆等物质积聚,减少换热器
大小,优化换热器体积,从而有效降低系统能耗。
螺旋板式换热器

2)偏心距
e1
b1
2
e2
b2
2
3)螺旋体的有效圈数
NY
b1
2
b2
d1
d1
b1
b2 2
2
4 LY 1
b1
b2
2
b1 b2 2
d1-卷辊的直径,LY1-螺旋板有效长度
4)螺旋体的圈数 无外圈板,无半圆筒体 有半圆筒体 有外圈板
螺旋板式换热器
管壳式换热器结构简单,适应性广,但传热效果欠佳,体积大。 从工程应用来看,在某些场合需要高传热效率,紧凑性(超过 700m2/m3)好的换热器,尤其在气—气换热器中,同等传热量和 功率消耗的条件下,其传热面积约为液—液换热器的10倍以上。
高效间壁式换热器:螺旋板式、板式、板翅式、翅片管以及热管 式换热器。
有相变,
p
2G2
2
0.046
deG
0.2
H de
1
3.结构设计
1)中心隔板宽度
W d1 b1 , 或W d2 b2 b-螺旋通道间距,-螺旋板厚度
W d1 b1 , 或W d2 b2
III型 螺旋通道由四张金属板卷制而成,一通道两端全部焊牢, 一侧流体由外缘旋转至中心,然后再由中心旋转至外缘排出;另 一侧流体仅作轴向流动。轴向流动通道截面积较螺旋通道大得多, 适用于流量相差较大的场合(如:气—液换热)。
结构特点及高效换热的原因
传热性能好 流体在螺旋通道内流动产生离心力使通道内外侧流体 之间形成二次流,增加了扰动,在较低的Re数下,流体仍可以处于 湍流状态。其次,等截面通道不存在流动死区,螺旋板片间的定距 柱也可增加流体的扰动。传热系数可达3000W/(m.°C)
螺旋板式换热器结构与性能

螺旋板式换热器结构及性能1、本设备由两张卷制而成,形成了两个均匀的螺旋通道,两种传热介质可进行全逆流流动,大大增强了换热效果,即使两种小温差介质,也能达到理想的换热效果。
2、在壳体上的接管采用切向结构,局部阻力小,由于螺旋通道的曲率是均匀的,液体在设备内流动没有大的转向,总的阻力小,因而可提高设计流速使之具备较高的传热能力。
3、I型不可拆式螺旋板式换热器螺旋通道的端面采用焊接密封,因而具有较高的密封性。
4、II型可拆式螺旋板换热器结构原理与不可拆式换热器基本相同,但其中一个通道可拆开清洗,特别适用有粘性、有沉淀液体的热交换。
5、III型可拆式螺旋板换热器结构原理与不可拆式换热器基本相同,但其两个通道可拆开清洗,适用范围较广。
6、单台设备不能满足使用要求时,可以多台组合使用,但组合时必须符合下列规定:并联组合、串联组合、设备和通道间距相同。
混合组合:一个通道并联,一个通道串联。
螺旋板式换热器的基本参数:1.螺旋板式换热器的公称压力PN规定为0.6,1,1.6、2.5Mpa(即原6、10、16、25kg/cm)(系指单通道的最大工作压力)试验压力为工作压力的1.25倍。
2.螺旋板式换热器与介质接触部分的材质,碳素钢为Q235A、Q235B、不锈钢酸港为SUS321、SUS304、3161。
其它材质可根据用户要求选定。
3.允许工作温度:碳素钢的t=0-+350℃。
不锈钢酸钢的t=-40-500℃。
升温降压范围按压力容器的有关规定,选用本设备时,应通过恰当的工艺计算,使设备通道内的流体达到湍流状态。
(一般液体流速1m/Sec气体流速10m/Sec).设备可卧放或立放,但用于蒸气冷凝时只能立放;用于烧碱行业必须进行整体热处理,以消除应力。
螺旋板式换热器防堵塞原理螺旋板式换热器与一般列管式换热器相比是不容易堵塞的,尤其是泥沙、小贝壳等悬浮颗粒杂质不易在螺旋通道内沉积,主要体现在:1.因为它是单通道杂质在通道内的沉积一形成周转的流还就会提高至把它冲掉;2.因为螺旋通道内没有死角,杂质容易被冲出。
【分类】螺旋板式换热器基本分类__螺旋板式换热器结构性能

【分类】螺旋板式换热器基本分类__螺旋板式换热器结构性能螺旋板式换热器想必大家都有一定的了解和认识,螺旋板式换热器厂家巨威锅炉技术人员来给大家讲解关于螺旋板式换热器基本分类以及结构性能的相关信息。
螺旋板式换热器由两张卷制而成,形成了两个均匀的螺旋通道,两种传热介质可进行全逆流流动,大大增强了换热效果,即使两种小温差介质,也能达到理想的换热效果。
【螺旋板式换热器基本分类】螺旋板换热器分为可拆分螺旋板换热器和不可拆分螺旋板换热器。
不可拆式螺旋板换热器的结构比较简单,螺旋通道的两端全部焊死。
可拆式螺旋板换热器.除螺旋通道两端的密封结构以外,其他与不可拆式完全相同。
为达到机械清洗的目的,可拆式螺旋通道,一端敞开,用平板盖和垫片密封,以防止流体漏到大气中或同一通道内的流体短路。
为了提高螺旋板的承压能力,在板与板之间用定距柱支撑。
筒体上的流体进出口有法向接管和切向接管两种。
中国普遍使用切向接管,它的流体阻力小,杂质容易被冲出。
使用回转支座比较方便,可使换热器立放或卧放。
换热的A、B流体分别流过螺旋板的两侧,其中的一种流体沿螺旋通道由外向内,至中心出口流出;而另一种流体则沿螺旋通道由中心进口,由内向外流出。
两种流体呈纯逆流方式流动。
螺旋板换热器大结构尺寸为:板宽1800毫米,外径1700毫米,传热面积250平方米,板与板之间的距离20毫米。
允许高操作压力可达2.5兆帕。
工作温度由选用的材料而定,材料大多用碳钢、不锈钢、铝、铜和钛。
【螺旋板式换热器结构性能】1、螺旋板式换热器由两张卷制而成,形成了两个均匀的螺旋通道,两种传热介质可进行全逆流流动,大大增强了换热效果,即使两种小温差介质,也能达到理想的换热效果。
2、螺旋板式换热器在壳体上的接管采用切向结构,局部阻力小,由于螺旋通道的曲率是均匀的,液体在设备内流动没有大的转向,总的阻力小,因而可提高设计流速使之具备较高的传热能力。
3、螺旋板式换热器I型不可拆式螺旋板式换热器螺旋通道的端面采用焊接密封,因而具有较高的密封性。
螺旋板式换热器的基本构造

螺旋板式换热器的基本构造螺旋板式换热器与其他种类换热器相比的特点是,传热流道长、流道间距大、耐热温、不易泄漏。
因此它换热效率较高,换热后冷介质的温度容易接近热介质的温度,适于粘稠性物料和含有颗粒性物料的加温或降温处理,但不适于含有纤维性物料换热。
螺旋板式换热器也适用于有机化合物蒸汽的冷凝加工。
二、螺旋板式换热器的基本构造和工作原理螺旋板式换热器是由两张较长的钢板叠放在一起卷制而成的,如图一,每张板上均布地焊有定距柱,它使两张板之间产生一定的间距,形成换热流道,定距柱起到支撑钢板抵抗流体压力的作用,也起到流体在换热流道中流动时增加湍流从而提高换热效率的作用。
相邻两流道流过的两种流体温度不同,它们通过螺旋钢板进行传热,达到换热的目的。
两流道的间距可以相同,也可不同。
流道间距不能太小,也不能太大,太小容易堵塞,太大不利于传热,在制造工艺结构上也难以实现,一般为8-30mm 较为适宜。
图一对于进行换热的两种介质,如果都是液体,在螺旋板式换热器的六道中是按螺旋方向流动的,如图二,并且按逆流的方式流动,所谓逆流是指相邻流道中两种液体流动的方向相反,这样能使两流体在相互传热的流程中始终保持一定的温差,从而可获得较好的效果。
对于换热的两种介质,一种是液体,另一种是汽(气)体,可按错流方式流动,所谓错流,是指液体按螺旋方向流动,汽(气)体按换热器的轴向直接通过,如图三,这主要是考虑到汽(气)体的特点,适于较大的流量,减少阻力,适用于有机蒸汽冷凝。
根据具体工况,蒸汽也可按螺旋方向流动,但气体由于热容量较小,一般那要按轴向直接通过。
图二图三三、螺旋板式换热器的类型1.不可拆式卷制后的螺旋板式换热器,其两端焊死,它不可拆卸,形成固定结构,流程内部不可触及。
它适用于不易堵塞的流体换热。
不可拆式又有卧式和立式的结构。
2.可拆式卷制后的螺旋板式换热器,每端只将一个流道焊死,而另一个流道开放,然后在端面上加端盖加以密封。
其端盖可以拆卸,从而清理流道内部。
螺旋板式换热器工作原理
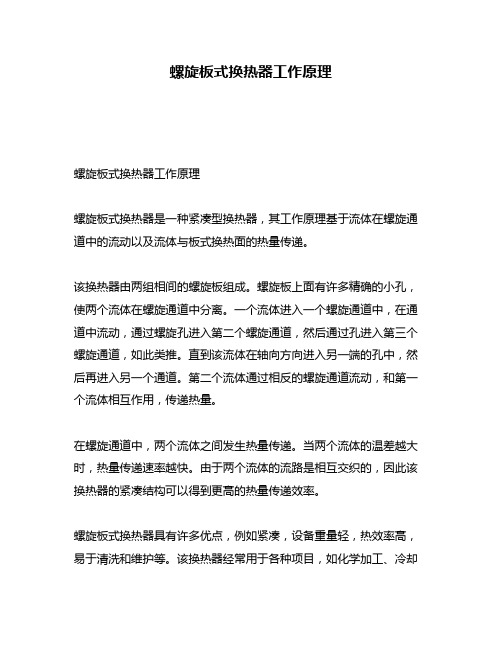
螺旋板式换热器工作原理
螺旋板式换热器工作原理
螺旋板式换热器是一种紧凑型换热器,其工作原理基于流体在螺旋通道中的流动以及流体与板式换热面的热量传递。
该换热器由两组相间的螺旋板组成。
螺旋板上面有许多精确的小孔,使两个流体在螺旋通道中分离。
一个流体进入一个螺旋通道中,在通道中流动,通过螺旋孔进入第二个螺旋通道,然后通过孔进入第三个螺旋通道,如此类推。
直到该流体在轴向方向进入另一端的孔中,然后再进入另一个通道。
第二个流体通过相反的螺旋通道流动,和第一个流体相互作用,传递热量。
在螺旋通道中,两个流体之间发生热量传递。
当两个流体的温差越大时,热量传递速率越快。
由于两个流体的流路是相互交织的,因此该换热器的紧凑结构可以得到更高的热量传递效率。
螺旋板式换热器具有许多优点,例如紧凑,设备重量轻,热效率高,易于清洗和维护等。
该换热器经常用于各种项目,如化学加工、冷却
剂再生,热交换等许多应用领域中。
总之,螺旋板式换热器是一种高效的换热器,具有紧凑、可靠和高效的特点。
它广泛应用于众多领域,并在这些领域中得到了广泛的认可和应用。
2024版板式换热器螺旋板换热器PPT教案

01定义02工作原理板式换热器是一种高效、紧凑的换热设备,由一系列平行排列的金属板组成,板间形成狭窄的流道,冷热流体在板间逆流流动,通过金属板进行热量交换。
板式换热器利用金属板的导热性能,将热量从热流体传递到冷流体。
在板间流道内,冷热流体在流动过程中不断混合,使得温度分布更加均匀,提高了换热效率。
板式换热器定义及工作原理螺旋板换热器定义及工作原理定义螺旋板换热器是一种由两张平行的金属板卷制而成的螺旋状通道,冷热流体在螺旋通道内逆流流动,通过金属板进行热量交换的换热设备。
工作原理螺旋板换热器利用金属板的导热性能,将热量从热流体传递到冷流体。
在螺旋通道内,冷热流体在流动过程中不断混合,使得温度分布更加均匀,提高了换热效率。
同时,螺旋结构使得流体在流动过程中产生旋转流动,增强了流体的湍流程度,进一步提高了换热效率。
应用领域与市场需求应用领域板式换热器和螺旋板换热器广泛应用于化工、石油、制药、食品、轻工等行业的加热、冷却、蒸发、冷凝等工艺过程中。
它们具有结构紧凑、占地面积小、传热效率高、操作灵活等优点,适用于各种规模的工业生产。
市场需求随着工业生产的不断发展,对换热设备的需求也在不断增加。
板式换热器和螺旋板换热器作为高效、紧凑的换热设备,具有广阔的市场前景。
未来市场需求将更加注重设备的传热效率、节能环保、安全可靠等方面的性能提升。
01020304传热板片:是板式换热器主要起换热作用的元件,一般波纹做成人字形,按照流体动力学原理,当板片之间支撑物减少时,流体在流速并不大的情况下,也能产生紊流,并形成许多回流,对传热起到很大的作用。
密封垫片:板式换热器的密封垫片主要是在换热板片之间起密封作用。
板式换热器的泄漏多是因为密封垫片压紧力不足、老化、腐蚀、变形等因素造成的。
压紧装置:压紧装置是板式换热器重要的部件之一,它的作用主要是保证密封垫片的密封性,以及保证设备运行时的紧固性。
导流装置:为了保证流体在换热器中均匀流动,提高传热效率,通常在换热器的进出口设置导流装置。
螺旋板式换热器

螺旋板式换热器螺旋板式换热器是用薄金属板压制成具有一定波纹形状的换热板片,然后叠装,用夹板、螺栓紧固而成的一种换热器。
工作流体在两块板片间形成的窄小而曲折的通道中流过。
冷热流体依次通过流道,中间有一隔层板片将流体分开,并通过此板片进行换热。
本设备由两张卷制而成,形成了两个均匀的螺旋通道,两种传热介质可进行全逆流流动,大大增强了换热效果,即使两种小温差介质,也能达到理想的换热效果。
在壳体上的接管采用切向结构,局部阻力小,由于螺旋通道的曲率是均匀的,液体在设备内流动没有大的转向,总的阻力小,因而可提高设计流速使之具备较高的传热能力。
基本结构:(1)波纹形状的换热板片(2)夹板(3)夹紧螺栓(4)盖板(5)冷流体进口(6)热流体出口结构图1所示:设计方法:(1)板型选择1、I型不可拆式螺旋板式换热器螺旋通道的端面采用焊接密封,因而具有较高的密封性。
2、II型可拆式螺旋板换热器结构原理与不可拆式换热器基本相同,但其中一个通道可拆开清洗,特别适用有粘性、有沉淀液体的热交换。
3、III型可拆式螺旋板换热器结构原理与不可拆式换热器基本相同,但其两个通道可拆开清洗,适用范围较广。
(2)基本参数1.螺旋板式换热器的公称压力PN规定为0.6,1,1.6、2.5Mpa(即原6、10、16、25kg/cm)(系指单通道的最大工作压力)试验压力为工作压力的1.25倍。
2.螺旋板式换热器与介质接触部分的材质,碳素钢为Q235A、Q235B、不锈钢酸港为SUS321、SUS304、3161。
其它材质可根据用户要求选定。
3.允许工作温度:碳素钢的t=0-+350℃。
不锈钢酸钢的t=-40-500℃。
升温降压范围按压力容器的有关规定,选用本设备时,应通过恰当的工艺计算,使设备通道内的流体达到湍流状态。
(一般液体流速1m/Sec气体流速10m/Sec).设备可卧放或立放,但用于蒸气冷凝时只能立放;用于烧碱行业必须进行整体热处理,以消除应力。
螺旋板式换热器的结构PPT学习教案
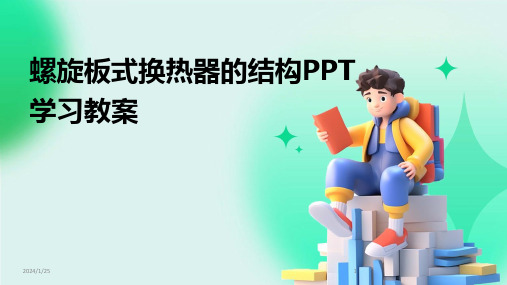
螺旋板式换热器采用薄板卷制,热损失 小,同时能准确地控制板间距,传热系 数较高,容易实现机械化、自动化生产
。
13
性能特点分析
高传热效率
由于流体在螺旋通道内流动时,流体在较低雷诺数下即可 达到湍流状态,同时流体在螺旋通道内流动时存在二次环 流,使得传热效率大大提高。
操作灵活
螺旋板式换热器可适应多种不同的操作条件,如不同的压 力、温度、流量等。
2024/1/25
6
02 螺旋板式换热器 结构组成
2024/1/25
7
主体部分
2024/1/25
螺旋板
由两张平行的金属板卷制而成, 形成螺旋通道,用于热交换。
定距柱
焊接在螺旋板上,保证两张金属 板之间的距离,形成均匀的流道 。
8
连接部分
2024/1/25
法兰
用于连接螺旋板式换热器与其他设备或管道,方便安装和拆卸。
机加工
对螺旋板的边缘进行修整和抛 光,确保表面光洁度和尺寸精 度。
22
质量检测方法与标准
质量检测方法
采用无损检测(如超声波探伤、射线探伤等)和破坏性检测(如拉伸试验、冲击试验等)相结合的方法,对螺旋 板式换热器的质量进行全面检测。
质量标准
参照国家相关标准和行业标准,制定严格的质量检测标准,确保螺旋板式换热器的质量符合设计要求和使用要求 。同时,对于不合格品进行及时的处理和追溯,防止问题扩大和影响产品质量。
适应更多的操作条件。
与热管式换热器相比
03
螺旋板式换热器具有更高的传热效率和更小的压降,同时其结
构也更加紧凑。
15
04 螺旋板式换热器 设计要点与选型 依据
2024/1/25
第4章 螺旋板式

第四章螺旋板式换热器管壳式换热器结构简单,适应性广,但传热效果欠佳,体积大。
从工程应用来看,在某些场合需要高传热效率,紧凑性(超过700m2/m3)好的换热器,尤其在气—气换热器中,同等传热量和功率消耗的条件下,其传热面积约为液—液换热器的10倍以上。
高效间壁式换热器:螺旋板式、板式、板翅式、翅片管以及热管式换热器。
螺旋板式换热器适用于石油化工、制药、食品等轻工业领域的气—气、气—液、液—液对流或冷凝的热交换。
I 型II 型III 型不同型式的螺旋板式换热器一、螺旋板式换热器的构造基本构造:由螺旋形传热板、隔板、头盖以及连接管等部件构成,一般可分为可拆式和不可拆式。
螺旋板式换热器的传热面由两张平行金属板相互间隔一定距离卷成螺旋形而成,两板的内端头焊在同一隔板上,外端头经连接板与壳体焊接,两端再加以密封,形成两个螺旋形流道。
冷热流体分别在各自流道内流动,通过螺旋板进行换热。
中心隔板与螺旋板的焊接结构不可拆式切向缩口的螺旋板式换热器不可拆式切向缩口的螺旋板式换热器三种型式I型两端全部焊牢,冷流体由壳体连接管进入壳体后,沿螺旋通道流至中心,然后从一端面排出;热流体则从另一端进入中心,沿螺旋通道流至外缘,然后从与壳体相连的另一接管排出。
II型流动方式同I型。
通道的两端面交替焊牢,两端各自另加一可拆顶盖密封。
III型螺旋通道由四张金属板卷制而成,一通道两端全部焊牢,一侧流体由外缘旋转至中心,然后再由中心旋转至外缘排出;另一侧流体仅作轴向流动。
轴向流动通道截面积较螺旋通道大得多,适用于流量相差较大的场合(如:气—液换热)。
结构特点及高效换热的原因传热性能好流体在螺旋通道内流动产生离心力使通道内外侧流体之间形成二次流,增加了扰动,在较低的Re数下,流体仍可以处于湍流状态。
其次,等截面通道不存在流动死区,螺旋板片间的定距柱也可增加流体的扰动。
传热系数可达3000W/(m.°C)自洁能力强流道单一,结垢处局部阻力增加,污垢已被冲刷掉。
螺旋板式换热器工作原理、构造及特点

螺旋板式换热器的换热原理、构造原理、特点螺旋板式换热器是用薄金属板压制成具有一定波纹形状的换热板片,然后叠装,用夹板、螺栓紧固而成的一种换热器。
工作流体在两块板片间形成的窄小而曲折的通道中流过。
冷热流体依次通过流道,中间有一隔层板片将流体分开,并通过此板片进行换热。
螺旋板式换热器是一种高效换热器设备,适用汽-汽、汽-液、液-液,对液传热。
它适用于化学、石油、溶剂、医药、食品、轻工、纺织、冶金、轧钢、焦化等行业。
按结构形式可分为不可拆式(Ⅰ型)螺旋板式及可拆式(Ⅱ型、Ⅲ型)螺旋板式换热器。
螺旋板换热器的结构及换热原理决定了其具有结构紧凑、占地面积小、传热效率高、操作灵活性大、应用范围广、热损失小、安装和清洗方便等特点。
两种介质的平均温差可以小至1℃,热回收效率可达99%以上。
在相同压力损失情况下,螺旋板式换热器的传热是列管式换热器的3~5倍,占地面积为其的1/3,金属耗量只有其的2/3。
因螺旋板式换热器是一种高效、节能、节约材料、节约投资的先进热交换设备。
所以目前已广泛用于化工、石化、食品饮料、机械、集中供热、冶金、动力、船舶、造纸、纺织、医药、核工业和海水淡化及热电联产等工业领域,可满足各类冷却、加热、冷凝、浓缩、消毒和余热的回收等工艺的要求。
板式换热器的构造原理、特点:板式换热器由高效传热波纹板片及框架组成。
板片由螺栓夹紧在固定压紧板及活动压紧板之间,在换热器内部就构成了许多流道,板与板之间用橡胶密封。
压紧板上有本设备与外部连接的接管。
板片用优质耐腐蚀金属薄板压制而成,四角冲有供介质进出的角孔,上下有挂孔。
人字形波纹能增加对流体的扰动,使流体在低速下能达到湍流状态,获得高的传热效果。
并采用特殊结构,保证两种流体介质不会串漏。
小结:总体来讲,板式换热器的换热系数要比螺旋板的高,但是螺旋板换热器造价低廉,更加适合工艺要求不严的水水换热!另外板式换热器分为可拆卸和全封闭型,前者可以通过拆卸进行清洗和维修,但是每次拆卸肯定要更换胶条,需要进行二次投资!而后者则应用于介质叫洁净的工况,无法拆卸。
1、螺旋板式换热器的结构

2、板式换热器的特点及应用
优点:(1)传热系数高。 (2)制作方便、金属耗量少、结构紧凑、占地面积小。板式换热 器 单位体积内的换热面积为管壳式的2~5倍。 (3)温度精确控制、末端温差小、热损失小、传热效率高。两种 介质的平均温差可以小至1℃,热回收效率可达99%以上。 (4)拆装方便,利于调节传热面积或流程组合,便于维修和清洗 缺点:(1)流道狭窄,处理量小,流动阻力大。 (2)操作温度受密封垫片材料性能限制而不宜过高。 (3)密封面太多太长,密封任务大,渗漏的可能性也大。 (4)承压能力低。 板式换热器应用 板式换热器广泛应用于化工、冶金、制冷、热回收及自然能源利 用等行业。介质可以是大多数液体、气体以及含固体小颗粒或少量纤 维的物料或具有腐蚀性的流体均能处理。常用在经常需要清洗、工作 环境要求十分紧凑,工作压力在2.5 MPa以下,温度在 -35℃~200℃ 场合。
板式换热器的工作过程示意图
1、板式换热器的基本结构
板式换热器主要由框架和板片两大部分组成。各长方形的 薄金属板片组合部分平行排列,夹紧、组装在框架上面。
板式换热器的结构图
板片的结构
板片由金属薄板用磨具压出不同波纹形状的通道,在板片的四个 角上各开一个圆孔,其中有两个圆孔和板面上的流道相通,另两 个圆孔则不相通。与板面流道相通的园孔在相邻板上是错开的, 以分别形成两流体的通道。常用的波纹形状有水平波纹、人字形 波纹和圆弧形波纹
Ⅱ型可拆式螺旋板换热器
Ⅲ型可拆式螺旋板换热器
1、螺旋板式换热器的结构
螺旋板式换热器由两张间隔一定的平行薄金属板卷制而成 的。两张薄金属板形成两个同心的螺旋型通道,两板之间 焊有定距柱以维持通道间距,在螺旋板两侧焊有盖板。
十三种类型换热器结构原理及特点(图文并茂)
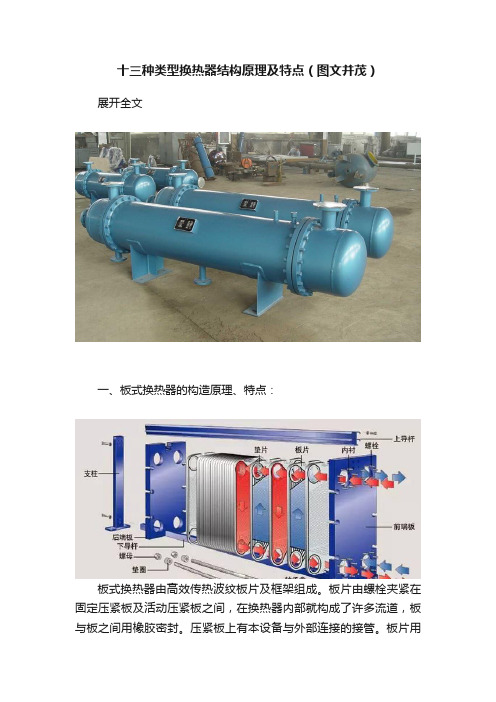
十三种类型换热器结构原理及特点(图文并茂)展开全文一、板式换热器的构造原理、特点:板式换热器由高效传热波纹板片及框架组成。
板片由螺栓夹紧在固定压紧板及活动压紧板之间,在换热器内部就构成了许多流道,板与板之间用橡胶密封。
压紧板上有本设备与外部连接的接管。
板片用优质耐腐蚀金属薄板压制而成,四角冲有供介质进出的角孔,上下有挂孔。
人字形波纹能增加对流体的扰动,使流体在低速下能达到湍流状态,获得高的传热效果。
并采用特殊结构,保证两种流体介质不会串漏。
板式换热器结构图二、螺旋板式换热器的构造原理、特点:螺旋板式换热器是一种高效换热器设备,适用汽-汽、汽-液、液-液,对液传热。
它适用于化学、石油、溶剂、医药、食品、轻工、纺织、冶金、轧钢、焦化等行业。
结构形式可分为不可拆式(Ⅰ型)螺旋板式及可拆式(Ⅱ型、Ⅲ型)螺旋板式换热器。
螺旋板式换热器结构图三、列管式换热器的构造原理、特点:列管式换热器(又名列管式冷凝器),按材质分为碳钢列管式换热器,不锈钢列管式换热器和碳钢与不锈钢混合列管式换热器三种,按形式分为固定管板式、浮头式、U型管式换热器,按结构分为单管程、双管程和多管程,传热面积1~500m2,可根据用户需要定制。
列管式换热器结构图四、管壳式换热器的构造原理、特点:管壳式换热器是进行热交换操作的通用工艺设备。
广泛应用于化工、石油、石油化工、电力、轻工、冶金、原子能、造船、航空、供热等工业部门中。
特别是在石油炼制和化学加工装置中,占有极其重要的地位。
换热器的型式。
管壳式换热器结构图五、容积式换热器的构造原理、特点:钢衬铜热交换器比不锈钢热交换器经济,并且技术上有保证。
它利用了钢的强度和铜的耐腐蚀性,即保证热交换器能承受一定工作压力,又使热交换器出水质量好。
钢壳内衬铜的厚度一般为1.0mm。
钢衬铜热交换器必须防止在罐内形成部分真空,因此产品出厂时均设有防真空阀。
此阀除非定期检修是绝对不能取消的。
部分真空的形成原因可能是排出不当,低水位时从热交换器,或者排水系统不良。
螺旋板换热器的结构及作用
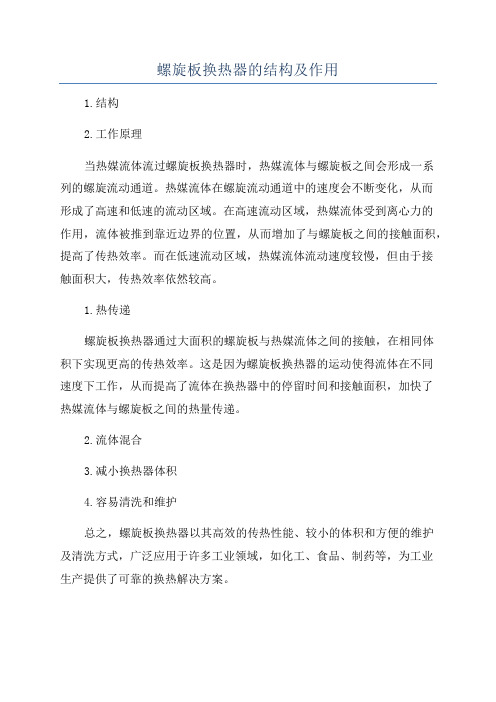
螺旋板换热器的结构及作用
1.结构
2.工作原理
当热媒流体流过螺旋板换热器时,热媒流体与螺旋板之间会形成一系
列的螺旋流动通道。
热媒流体在螺旋流动通道中的速度会不断变化,从而
形成了高速和低速的流动区域。
在高速流动区域,热媒流体受到离心力的
作用,流体被推到靠近边界的位置,从而增加了与螺旋板之间的接触面积,提高了传热效率。
而在低速流动区域,热媒流体流动速度较慢,但由于接
触面积大,传热效率依然较高。
1.热传递
螺旋板换热器通过大面积的螺旋板与热媒流体之间的接触,在相同体
积下实现更高的传热效率。
这是因为螺旋板换热器的运动使得流体在不同
速度下工作,从而提高了流体在换热器中的停留时间和接触面积,加快了
热媒流体与螺旋板之间的热量传递。
2.流体混合
3.减小换热器体积
4.容易清洗和维护
总之,螺旋板换热器以其高效的传热性能、较小的体积和方便的维护
及清洗方式,广泛应用于许多工业领域,如化工、食品、制药等,为工业
生产提供了可靠的换热解决方案。
螺旋板式换热器 标准

螺旋板式换热器标准
螺旋板式换热器是一种高效、紧凑的换热设备,广泛应用于各种工业领域。
其标准设计和制造工艺使其具有较高的传热效率和较低的流体阻力,同时能够适应各种恶劣的工作环境。
螺旋板式换热器的核心部件是由两张平行的金属板卷制而成的螺旋板,相邻的两个螺旋板之间形成了一个曲折的通道,流体通过这个通道时得到了充分的换热。
此外,螺旋板的边缘也卷成了一个半圆形,可以将封头和筒体连接起来,增强了设备的密封性和稳定性。
螺旋板式换热器的优点包括:传热效率高、体积小、重量轻、容易清洗和维修、能够适应高温高压等恶劣工作环境。
同时,由于其特殊的结构,螺旋板式换热器还能够有效地防止介质泄漏和堵塞。
在设计和制造螺旋板式换热器时,需要遵循一定的标准。
首先,设备的材料选择要符合相关标准,如不锈钢、碳钢等。
其次,设备的结构尺寸和参数要符合设计规范,以确保设备的性能和安全性。
此外,设备的制造工艺和质量也要符合相关标准,如焊接工艺、无损检测等。
总之,螺旋板式换热器是一种高效、紧凑的换热设备,其设计和制造需要遵循一定的标准。
了解这些标准可以帮助我们更好地了解和使用这种设备,提高其传热效率和安全性。
- 1、下载文档前请自行甄别文档内容的完整性,平台不提供额外的编辑、内容补充、找答案等附加服务。
- 2、"仅部分预览"的文档,不可在线预览部分如存在完整性等问题,可反馈申请退款(可完整预览的文档不适用该条件!)。
- 3、如文档侵犯您的权益,请联系客服反馈,我们会尽快为您处理(人工客服工作时间:9:00-18:30)。
螺旋板式换热器的换热原理、构造原理、特点
螺旋板式换热器是用薄金属板压制成具有一定波纹形状的换热板片,然后叠装,用夹板、螺栓紧固而成的一种换热器。
工作流体在两块板片间形成的窄小而曲折的通道中流过。
冷热流体依次通过流道,中间有一隔层板片将流体分开,并通过此板片进行换热。
螺旋板式换热器是一种高效换热器设备,适用汽-汽、汽-液、液-液,对液传热。
它适用于化学、石油、溶剂、医药、食品、轻工、纺织、冶金、轧钢、焦化等行业。
按结构形式可分为不可拆式(Ⅰ型)螺旋板式及可拆式(Ⅱ型、Ⅲ型)螺旋板式换热器。
螺旋板换热器的结构及换热原理决定了其具有结构紧凑、占地面积小、传热效率高、操作灵活性大、应用范围广、热损失小、安装和清洗方便等特点。
两种介质的平均温差可以小至1℃,热回收效率可达99%以上。
在相同压力损失情况下,螺旋板式换热器的传热是列管式换热器的3~5倍,占地面积为其的1/3,金属耗量只有其的2/3。
因螺旋板式换热器是一种高效、节能、节约材料、节约投资的先进热交换设备。
所以目前已广泛用于化工、石化、食品饮料、机械、集中供热、冶金、动力、船舶、造纸、纺织、医药、核工业和海水淡化及热电联产等工业领域,可满足各类冷却、加热、冷凝、浓缩、消毒和余热的回收等工艺的要求。
板式换热器的构造原理、特点:
板式换热器由高效传热波纹板片及框架组成。
板片由螺栓夹紧在固定压紧板及活动压紧板之间,在换热器内部就构成了许多流道,板与板之间用橡胶密封。
压紧板上有本设备与外部连接的接管。
板片用优质耐腐蚀金属薄板压制而成,四角冲有供介质进出的角孔,上下有挂孔。
人字形波纹能增加对流体的扰动,使流体在低速下能达到湍流状态,获得高的传热效果。
并采用特殊结构,保证两种流体介质不会串漏。
小结:
总体来讲,板式换热器的换热系数要比螺旋板的高,但是螺旋板换热器造价低廉,更加适合工艺要求不严的水水换热!
另外板式换热器分为可拆卸和全封闭型,前者可以通过拆卸进行清洗和维修,但是每次拆卸肯定要更换胶条,需要进行二次投资!而后者则应用于介质叫洁净的工况,无法拆卸。
螺旋板式换热器它是由两张互相平行的薄金属板,卷制成同心的螺旋形通道。
在其中央设置隔板将两通道隔开,两板间焊有定距柱以维持通道间距,螺旋板两侧焊有盖板和接管。
两流体分别在两通道内流动,通过螺旋板进行换热。
(1)总传热系数高由于流体在螺旋形通道内受到惯性离心力的作用和定距柱的干扰,低雷诺数(Re=1400~1800)下即可达到湍流,允许流速大(液体为2m/s,气体为20m/s),故传热系数大。
如水对水换热过程K=2000~3000W/m2•K。
(2)不易结垢和堵塞由于流速较高且在螺旋形通道中流过,有自行冲刷作用,故流体中的悬浮物不易沉积下来。
(3)能利用低温热源由于流道长而且两流体可达到完全逆流,因而传热温差大,能充分利用温度较低的热源。
(4)结构紧凑由于板薄2~4mm,单位体积的传热面积可达到150~500m2/m3。
`主要缺点是操作压强不能超过2MPa,操作温度在300~400℃以下,另外因整个换热器焊为一体,一旦损坏检修困难。
螺旋板换热器直径在1.5m之内,板宽200~1200mm,板厚2~4mm,两板间距5~25mm,可用普通钢板和不锈钢制造,目前广泛用于化工、轻工、食品等行业。
板式和螺旋式的区别,螺旋使用在温度高,压力大,粘度大的场合,而板式用天温度小于160,压力小于1.6MPA,粘度不是很大的场合,螺旋板的传热系数比板换低一半左右,具体得看介质参数来定。
JB-T_4751-2003_螺旋板式换热器JB-T_4751-20
03_螺旋板式换热器.pdf
JB-T_4723-92不可拆式螺旋板换热器型式与基本参数JB-T_4723-92
不可拆式螺旋板换热器型式与基本参数.pdf
YY0_6T40-00--螺旋板换热器螺旋板换热器.
pdf。